油气线结焦原因.
延迟焦化大油气线结焦问题探讨

延迟焦化大油气线结焦问题探讨发布时间:2022-01-14T07:07:43.342Z 来源:《福光技术》2021年24期作者:徐文庆[导读] 在石化生产实践中,影响延迟焦化装置运转的一个重要因素就是焦炭塔大油气管线结焦问题。
山东昌邑石化有限公司山东潍坊 261300摘要:在石化生产实践中,影响延迟焦化装置运转的一个重要因素就是焦炭塔大油气管线结焦问题。
由于大油气管线结焦问题严重,会产生压力降低过大,进而气温升高,同时加速焦粉含量,进一步加剧了大油气管线的结焦问题,容易对石化生产产生影响。
基于此,要探索创新解决大油气管线的结焦问题,其中通过延迟焦化装置生产周期的方式,可以发挥比较理想的效果。
本文基于焦炭大油气管线结焦的危害与实际情况,探索科学的解决策略,旨在进一步提升石化成产效能,提升综合生产效率,进一步发挥延迟焦化设施的重要作用。
关键词:石油化工;延迟焦化;结焦;技术创新1焦化大油气线结焦问题与隐患采用管道方式传输油气,由于路线较长,因此必须使用焊接方式延长管道,但是如果管道之间的焊接质量不满足需求,在外力的压力作用下,可能产生管道的冲击力,而焊口处较为薄弱,内部荷载的增加,会加剧隐藏焊缝或内部焊接口不断扩大,从而导致安全问题[1]。
另外采用管道运输油气时所经过的地质路线较为复杂,由于结焦问题出现,可能造成管道内部应力发生变化,从而产生泄漏并形成隐患。
由于焦化大油气线结焦问题产生,一旦发生造成的危害巨大,不仅关系到周边人员的生命安全,同时还可能造成较大的经济损失。
注重油气的火灾隐患问题是生产环节中的重点,既要防止高温环境下进行查验,同时还要考虑生产中产生的结焦问题。
在大油气线焦化中,如果不采用预防措施,很容易造成较大的经济损失,甚至会发生爆炸事故,并严重污染周边环境,造成的损失难以估量。
油气设备需注重日常检查及管理,不仅要防止油气的易燃易爆,同时还要针对油气的易挥发及窒息性进行潜在危险排查,设备使用必须严格遵守相关标准,并结合实际使用情况加强管理[2]。
重油催化装置反应系统结焦原因与防治
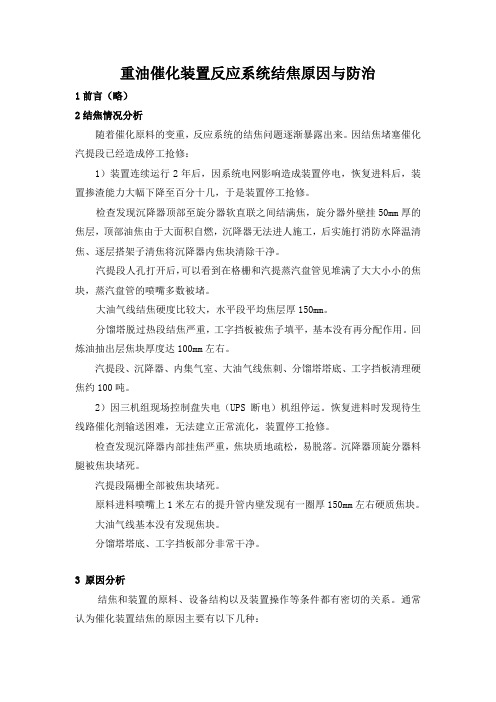
重油催化装置反应系统结焦原因与防治1前言(略)2结焦情况分析随着催化原料的变重,反应系统的结焦问题逐渐暴露出来。
因结焦堵塞催化汽提段已经造成停工抢修:1)装置连续运行2年后,因系统电网影响造成装置停电,恢复进料后,装置掺渣能力大幅下降至百分十几,于是装置停工抢修。
检查发现沉降器顶部至旋分器软直联之间结满焦,旋分器外壁挂50mm厚的焦层,顶部油焦由于大面积自燃,沉降器无法进人施工,后实施打消防水降温清焦、逐层搭架子清焦将沉降器内焦块清除干净。
汽提段人孔打开后,可以看到在格栅和汽提蒸汽盘管见堆满了大大小小的焦块,蒸汽盘管的喷嘴多数被堵。
大油气线结焦硬度比较大,水平段平均焦层厚150mm。
分馏塔脱过热段结焦严重,工字挡板被焦子填平,基本没有再分配作用。
回炼油抽出层焦块厚度达100mm左右。
汽提段、沉降器、内集气室、大油气线焦刺、分馏塔塔底、工字挡板清理硬焦约100吨。
2)因三机组现场控制盘失电(UPS断电)机组停运。
恢复进料时发现待生线路催化剂输送困难,无法建立正常流化,装置停工抢修。
检查发现沉降器内部挂焦严重,焦块质地疏松,易脱落。
沉降器顶旋分器料腿被焦块堵死。
汽提段隔栅全部被焦块堵死。
原料进料喷嘴上1米左右的提升管内壁发现有一圈厚150mm 左右硬质焦块。
大油气线基本没有发现焦块。
分馏塔塔底、工字挡板部分非常干净。
3 原因分析结焦和装置的原料、设备结构以及装置操作等条件都有密切的关系。
通常认为催化装置结焦的原因主要有以下几种:1、原料中未汽化的高沸点物质挂壁后在催化剂作用下炭化生焦。
2、反应油气中重组分在死区冷壁处液化形成“焦核”,逐渐发生缩合生焦。
3.1 原料性质的影响原料中的渣油以VRDS减压渣油为主,原料掺渣比例变化如下表1,渣油性质见表2所示。
VRDS减压渣油中高沸点物质含量在80%以上,随着装置掺渣的增加,原料中高沸点物的比例不断上升,反应产物中高沸点组分相应增加,结焦的趋势增加。
表1 催化原料掺渣变化(略)表2 VRDS渣油性质列表(略)催化装置原料性质变化情况,见下表(略)3.2 设备结构的影响3.2.1 提升管内结焦情况分析从提升管内结焦的位置分析其原因应该是原料油滴穿透现象的结果。
催化裂化油浆结焦原因及对策

催化裂化油浆结焦原因及对策标签:催化裂化;油浆结焦;解决对策在我国炼油厂的催化裂化过程当中,油浆系统当中产生的结焦结垢问题直接影响到了催化裂化设备的正常工作,主要是因为产生大量的结焦结垢物质,直接降低了热换器的热转化效率,同时提高了管道当中材料输送的阻力,进而造成了蜡油渣油的热转换效率降低。
系统内部产生的蒸汽量减少,同时整个反应设备在工作过程当中的能源消耗量加大,油浆当中多余的热量无法及时被排除,进而造成了整个反应系统内部的热平衡性下降,严重的情况下还直接造成油浆输送系统堵塞,进而影响到了整个生产过程的正常进行。
在最近几年发展过程当中,我国炼油厂的催化裂化原材料质量都不是非常理想,外加上在加油的催化裂化技术方面一直是难以攻克的难题。
因此,催化裂化油浆结焦和结垢的问题受到了各大化工企业的广泛关注,必须要采取相应的解决措施来解决这一问题。
1.催化裂化油浆结焦问题分析1.1温度问题的影响从催化裂化的整个反应过程中可以看出,该反应过程中会受到温度的影响,在相同的催化设备当中分馏塔的底部温度越高,那么出现的结焦现象就越明显。
针对己经产生结焦问题来讲,随着温度不断提高整个反应过程的结焦问题就更加明显,就在模拟FCC油浆的结焦单元当中所得出的结论非常明显。
1.2氧含量的影响通过模拟实验分析了FCC油浆当中产生结焦单元的具体原因,通过向试管当中通入一定量的空气或者是氧气,可以看出在不同量的空气和氧气掺入的情况下,对结焦问题的影响比较明显,其中如果空气或者氧气的参与量较大,那么结焦的问题就越严重。
由此可以看出氧气含量的多少对结焦问题的影响非常明显。
1.3固体和电效应影响通过实际的生产过程可以看出,在催化裂化反应过程当中,如果增加油浆内部的沉降器和过滤器设备之后,在产生结焦和结垢的问题上有着明显的缓解。
因此,这一现象也可以得到充分的证明,从中可以得出催化裂化反应过程中油浆当中,所存在的固体杂质对结焦问题的影响比较明显。
延迟焦化装置大油气管线结焦原因分析及改进措施

延迟焦化装置大油气管线结焦原因分析及改进措施颜峰;谢崇亮;范海玲【摘要】The 90 degrees bend was originally designed for the overhead oil vapor lines of a 1.0 MM TPY delayed coking unit,and traditional three point oblique insertion was adopted for the injection of quench oil.The rapid coking was found in the oil vapor line,Within three months,severe coking was found on the surface of overhead vapor lines,and the pressure of the coke drum overhead was increased from 0.17 MPa to 0.27 MPa,and economic benefit and safe operation of the unit were affected.To solve these problems,the form of overhead vapor lines was modified and injection of quench oil was revamped:the form of overhead vapor lines was revamped from 90 degrees bend to four way structure and the injection of quench oil was modified from three point oblique to nozzle structure.In addition,the injection point of quench oil,injection mode of foam removal agent and process parameters were also optimized.After revamping,the coke cleaning cycle of overhead vapor lines was extended to 6 months and online coke cleaning was realized.Safe operation and good economic benefits have been achieved.%某1.0 Mt/a延迟焦化装置焦炭塔顶大油气管线原设计为90°弯头形式,急冷油注入采用传统三点斜插式,在装置运行过程中发现大油气管线结焦速度较快,在3个月内,焦炭塔顶压力由0.17 MPa增加至0.28 MPa,影响装置的安全生产及经济效益.为解决上述问题,对大油气管线形式及急冷油注入方式进行改造:将焦炭塔顶大油气管线形式由90°弯头改为可在线清焦的四通结构,同时将急冷油注入方式由三点斜插式改为喷嘴结构,并对急冷油的注入位置、消泡剂的注入方式及工艺操作参数进行了优化.装置改造后大油气管线的清焦周期延长至6个月,且能够实现在线清焦,实现了安全生产及提高经济效益的综合效果.【期刊名称】《炼油技术与工程》【年(卷),期】2017(047)011【总页数】4页(P31-34)【关键词】延迟焦化;大油气管线;急冷油注入;消泡剂【作者】颜峰;谢崇亮;范海玲【作者单位】中国石油工程建设有限公司华东设计分公司,山东省青岛市266071;中国石油工程建设有限公司华东设计分公司,山东省青岛市266071;中国石油工程建设有限公司华东设计分公司,山东省青岛市266071【正文语种】中文延迟焦化是渣油深度热裂化转化工艺,其特点是对原料的适应性强、工艺成熟、投资低、操作费用少。
焦碳塔大油气线结焦原因分析及预防措施

焦碳xx油气线结焦原因分析及预防措施重油装置xx我国生产的原油一般偏重,总体上说,目前国产原油中的减压渣油约占,部分新增油田开采的原油中减压渣油组分高达,重油加工是提高炼油厂效益和竞争能力的主要手段。
通过重油改质可以使轻油收率大大增加,而延迟焦化作为加工重油的重要手段,是炼油厂不可缺少的重要组成部分,是炼油厂重油平衡的主要手段,如何保证延迟焦化装置的长周期运行是一个十分重要的课题。
焦化装置长周期运行的主要难题在于主要设备管线的结焦问题。
我装置在2011年9月份发生焦炭塔大油气线隔断阀处结焦关不严的情况,可能造成两塔油气互穿。
而且在04年、09年,我装置各发生过一次分馏塔底严重结焦现象,造成辐射泵抽空,过滤器焦子外溢,被迫停厂抢修。
分馏塔底结焦有大部分原因可能是焦子从大油气线带来,所以我认为主要考虑大油气线部分,焦化装置焦炭塔大油气线结焦主要集中在焦炭塔总管部分(两焦炭塔油气汇合处)及两塔隔断阀处。
本文根据我装置实际操作条件,分析大油气线结焦的原因,就结焦原因提出相应的预防措施。
1、大油气线结焦原因分析1.1大油气线油气温度高我装置焦炭塔顶温度大约在405-418度。
由于在新塔预热时,部分油气进入新塔冷凝为凝缩油使进入分馏塔的油气量减少,分馏塔底和蒸发段温度大幅度降低。
提高大油气线油气温度是一个提高塔底及蒸发段温度的重要调节手段,导致有时焦炭塔大油气线温度高于其中油品的临界分解温度,则就可能会发生结焦(临界分解温度是指油品在开始发生分解和缩合的临界状态下的温度)。
1.2系统压力波动由于我厂低压瓦斯管网复杂,使用低压瓦斯的装置较多,使低压瓦斯压力波动频繁。
我装置产出的低压瓦斯由于管网压力高常有外派不畅造成系统压力(低压瓦斯压力)鳖压的现象,正常系统压力为0.08Mp,但是时有系统压力迅速涨至0.12-0.18Mp的情况,而系统压力上涨带动焦炭塔顶压力上涨,通常为0.20-0.24Mp。
在系统压力下降时,焦炭塔压力同时下降,在压力迅速下降的情况下,焦炭塔内线速升高,会有大量泡沫携带入大油气线。
延迟焦化焦炭塔顶大油气线结焦原因及应对措施
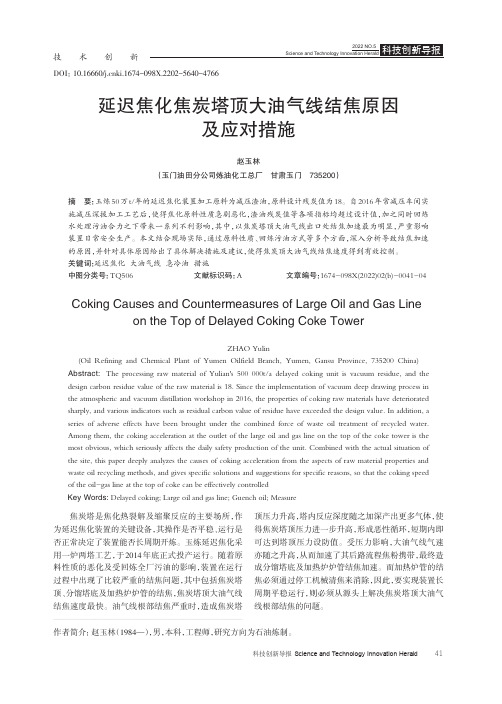
延迟焦化焦炭塔顶大油气线结焦原因及应对措施赵玉林(玉门油田分公司炼油化工总厂甘肃玉门735200)摘要:玉炼50万t/年的延迟焦化装置加工原料为减压渣油,原料设计残炭值为18。
自2016年常减压车间实施减压深拔加工工艺后,使得焦化原料性质急剧恶化,渣油残炭值等各项指标均超过设计值,加之同时回炼水处理污油合力之下带来一系列不利影响,其中,以焦炭塔顶大油气线出口处结焦加速最为明显,严重影响装置日常安全生产。
本文结合现场实际,通过原料性质、回炼污油方式等多个方面,深入分析导致结焦加速的原因,并针对具体原因给出了具体解决措施及建议,使得焦炭顶大油气线结焦速度得到有效控制。
关键词:延迟焦化大油气线急冷油措施中图分类号:TQ506文献标识码:A文章编号:1674-098X(2022)02(b)-0041-04 Coking Causes and Countermeasures of Large Oil and Gas Line on the Top of Delayed Coking Coke TowerZHAO Yulin(Oil Refining and Chemical Plant of Yumen Oilfield Branch,Yumen,Gansu Province,735200China) Abstract:The processing raw material of Yulian's500000t/a delayed coking unit is vacuum residue,and the design carbon residue value of the raw material is18.Since the implementation of vacuum deep drawing process in the atmospheric and vacuum distillation workshop in2016,the properties of coking raw materials have deteriorated sharply,and various indicators such as residual carbon value of residue have exceeded the design value.In addition,a series of adverse effects have been brought under the combined force of waste oil treatment of recycled water. Among them,the coking acceleration at the outlet of the large oil and gas line on the top of the coke tower is the most obvious,which seriously affects the daily safety production of the bined with the actual situation of the site,this paper deeply analyzes the causes of coking acceleration from the aspects of raw material properties and waste oil recycling methods,and gives specific solutions and suggestions for specific reasons,so that the coking speed of the oil-gas line at the top of coke can be effectively controlledKey Words:Delayed coking;Large oil and gas line;Guench oil;Measure焦炭塔是焦化热裂解及缩聚反应的主要场所,作为延迟焦化装置的关键设备,其操作是否平稳、运行是否正常决定了装置能否长周期开炼。
催化结焦原因分析及措施
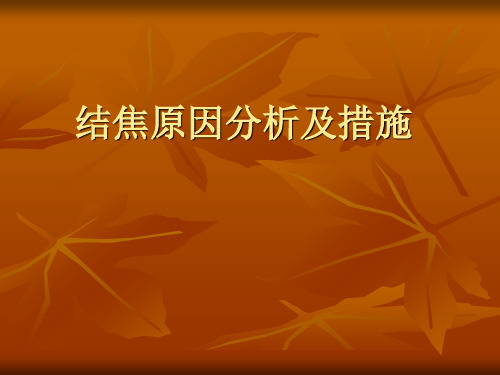
3,喷嘴型式与雾化蒸汽比例
所以进料喷嘴结焦皆与喷嘴型式有关,还与提升 管段的提升效果和雾化蒸汽的比例有关。分布不均, 型式不合理均会引起结焦,采用汽油进预提升段后 干气和油浆明显增加,而达不到其他同类装置的同 一位置回炼汽油可增产液化气的目的。原因是剂油 比不够,新鲜原料裂化温度低。
4,事故状态次数及处理过程
7,沉降器或油气顶部放空结焦
主要在顶部放空和人孔,这些部位虽有防焦蒸汽 松动,但因为设置节流孔尺寸不合适而引起油气的 集聚结焦的。在开停工处理中衬里升温赶空气等步 骤的实施不能正常放空无法顺利完成。
8,大油气管线结焦
结焦一定程度后因油气线速的增加不会继续增加, 对装置运行不会构成影响,若结焦快,突遇停工, 在开工过程中升温快,容易引起的焦炭崩塌,造成 结焦集中堵塞大油气线或进入分馏塔底。 从以上各部结焦状况来看,影响长周期运行和产品 分布的主要是喷嘴结焦和翼阀及料腿内部结焦,影 响事故状态下开停工的是防焦室及油气管线结焦及 旋分器升气管入口背面结焦,翼阀及料腿内部结焦。
口方向朝下,其中有40个向沉降器壁(环管外侧) 口方向朝下,其中有40个向沉降器壁(环管外侧) 呈45 °朝下,另外40个向沉降器中心(环管内侧) 朝下,另外40个向沉降器中心(环管内侧) 呈45°朝下。具体形式与图-2类似,其中倾斜角度 45°朝下。具体形式与图为45°,管嘴长度为90mm,内径为φ14.2,外径为 45°,管嘴长度为90mm,内径为φ14.2,外径为 φ22。。 φ22。。 b) 防焦及松动蒸汽环作用 根据设计,上防焦蒸汽采用3.5Mpa蒸汽,主要是利 根据设计,上防焦蒸汽采用3.5Mpa蒸汽,主要是利 用3.5Mpa蒸汽的高温度来维持沉降器腔内的温度 , 3.5Mpa蒸汽的高温度来维持沉降器腔内的温度 减缓油气冷凝结焦,同时起到将汽提上来的油气赶 到导流锥的作用;其流量由控制阀 控制。
重油催化裂化装置结焦成因及解决策略

重油催化裂化装置结焦成因及解决策略作者:王蓬勃来源:《科学与财富》2019年第07期摘要:随着原料的重质化、劣质化,催化裂化装置和管线结焦已成为制约催化装置长周期平稳运转的重要因素之一,更重要的是这种产生在设备上的焦块会给装置的安全生产带来严重的隐患。
由于结焦而导致的非计划停工给炼厂也带来巨大的经济损失,因此,抑制或减少设备和管线的结焦已成为重油催化裂化装置十分迫切的技术要求。
本文对胜利石化总厂600kt/a 重油催化裂化装置的操作状况和设备结焦原因进行分析,针对装置操作现状提出抑制或减少设备结焦的措施。
关键词:重油催化裂化装置;设备结焦;技术要求;措施1原料性质和主要操作条件1.1 典型原料的性质和组成胜利石化总厂主要加工中间基胜利原油,原油性质较差。
重油催化裂化装置的原料主要为常压渣油,其中大于500℃的减压渣油馏分占62.0%。
由于催化裂化原料的密度大、馏分重、残炭和重金属含量高、饱和分含量低而胶质和沥青质含量高。
因此,该常压渣油的裂化性能较差,裂化后焦炭产率高,这将使设备更易结焦,从而对生产产生不利影响。
1.2 主要操作条件和产物分布胜利石化总厂催化裂化装置的主要操作条件见表1。
产物中裂化气、汽油、轻柴油、油浆和焦炭含量分别为14.54%,40.25%,29.17%,6.10%,8.93%。
2结焦物分析2.1 结焦物的组成胜利石化总厂重油催化裂化装置的结焦主要发生在提升管喷嘴上方区域、沉降器顶部、转油线和分馏塔入口等部位。
其中,提升管喷嘴上方区域和转油线的焦块质地坚硬。
对各部位的结焦物进行分析。
其中,采用元素分析仪测定碳、氢、氮的含量,采用管式炉法测定硫含量,灰分经由马弗炉高温灼烧(900℃下3h)得到。
从分析结果可知,结焦物中灰分含量较高,不同部位的结焦物其灰分含量不同,大致为30%~70%,其他主要为碳、氢、氮和硫等元素,这些元素都是催化裂化原料本身所含的元素,其中含量最多的是碳,若扣除灰分,纯焦的碳含量均在93%以上。
延迟焦化装置焦炭塔周期性切换操作波动的原因及对策

一、焦炭塔切换周期内操作波动的原因分析1.换塔前新塔预热温度偏低焦炭塔的预热过程为:新塔赶空气、试压合格后,关闭脱水隔断阀,缓慢打开新塔瓦斯阀,将老塔油气引入新塔,待新塔压力与老塔压力接近平稳之后,全开新塔瓦斯阀,将底部甩油改去放空,待底部温度上升至170℃以后,再关底部放空阀,全开甩油去甩油罐阀,再逐渐关小瓦斯总阀,建立瓦斯循环,甩油罐甩油去原料罐或分馏塔回炼,在换塔前,新塔底部温度,要求达到330℃以上,塔壁温度在280℃以上。
但是有时预热一段时间后,温度很难升上去,主要是预热的时间不够,新塔不能得到有效的预热循环,造成温度偏低;进料线有焦,焦炭塔的油不能放下来,多数因除焦不净,新塔预热后焦块掉下来堵住进料热偶引起,造成油气循环量小,温度不能上涨;过滤器堵,也会造成焦炭塔预热不畅,焦炭塔底部的油不能放到甩油罐,油气无法进一步的循环,焦炭塔的温度得不到提高。
2.预热速度过快有时受到除焦系统的影响,预热的时间不够,为了抢时间,加快了预热的速度,预热时间从正常时5小时减少到4小时左右,预热时间缩短了近1小时,由于预热不充分,从而导致热量的不均衡,操作的紊乱。
同时速度的加快,油气量变化太快,将影响去分馏塔的油气负荷,蒸发段温度下降较多,上部回流控制阀必须关小才能保证蒸发段温度,由于上部回流量减少与进料的换热少,分馏塔底温度过低,原料进加热炉温度下降,大大加剧了加热炉的热负荷,操作的调整难度加大。
3.油气线结焦,预热油气量不够有时因急冷油注入问题或油气线速过高、焦高太高,引起油气循环线结焦或堵塞,有新塔顶温度上不去的现象。
在新塔预热油,顶温升不高,影响到焦炭塔预热速度,焦炭塔顶压力也超高。
二、优化焦炭塔切换周期内操作的对策1.吹扫彻底,确保预热流程通畅在除焦班进行除焦时,外操现场开汽吹扫进料短管,并检查短管内无焦粒、焦粉方停汽,这样保证了预热时进料短管内无焦堵。
在除焦班除完焦后,要求除焦人员扫尽焦炭塔内壁的焦粉,铲除清理焦炭塔塔底盖焦粉后方可上短管,以保证在预热时无焦粉落入塔底堵塞进料线。
延迟焦化运行常见问题

2.3确定最佳的急冷油注入位置
在早期的设计中,一 般在大油气线出口加 三条急冷油注入线, 管径大多是DN25,斜 插入大油气线中,如 图所示:
• 经过各炼厂焦化装置长 期的经验总结,提出了 一系列行之有效的方法。 如在油气管线上加法兰, 当油气管线结焦时可以 拆掉清焦。有的在油气 出口管线上加过滤器。 还有一种比较好的注入 方法,将急冷油注入油 气刚出焦炭塔的根部, 而且急冷油管线也增大 到DN40,有的采用斜插 式注入,有的采用内置 环行喷雾管注入,均可 有效的防止了油气线结 焦。见图
1.3 加热炉出口温度
加热炉出口温度是焦化反应最关键的操作参数,它 直接影响到焦炭塔内泡沫层的高度。炉出口温度越高,焦 化反应越剧烈,深度越深,泡沫层的高度越低。反之,泡 沫层的高度就越高,易雾沫夹带,使泡沫状焦粉带入油气 管线而引起结焦。图-3表示三种减压渣油炉出口温度与 泡沫层高度的关系。
1.4 加热炉炉管注汽(注水)量
2、掺炼催化油浆使分馏塔底循环过滤器堵塞
• 催化油浆中的催化剂固体粉末除在原料换热器内沉积外, 另一重要沉积点为焦化分馏塔底,由于底循环运转的作用, 该固体粉末最终沉积在底循环过滤器内。自从2003年10 月份掺炼油浆以来,焦化分馏塔底循环过滤器经常堵塞, 导致底循环泵提不起量,常常用蒸汽反吹扫,仍难以奏效, 只好拆开清理,仅11月份就拆开清理3次,拆开后发现过 滤器内含较多焦粉与催化剂粉末混合后的粉状、块状物, 堵塞严重。而在第一开工周期期间(该期间基本未掺炼催 化油浆)该过滤器未曾因堵塞拆开清理过,这进一步验证 了大比例掺炼油浆是导致底循环过滤器堵塞的主要原因。
1.6 焦粉(或泡沫)的夹带
焦炭塔焦粉(或泡沫)的夹带量大小主要与塔内的油 气线速及安全空高有关,在确定焦炭塔直径时一般按 小于允许线速度计算,当装置处理能力提高时,油气 线速增大,容易导致焦粉和泡沫不能沉降而带到油气 线内,导致管线内结焦。
油气线结焦原因.

油气线结焦原因1.前言近年来,由于市场经济的影响和投资的限制,各石油化工公司新建、改扩建延迟焦化装置,给企业带来了可观的经济效益,为企业的发展做出了巨大的贡献。
为了提高经济效益,大部分炼油厂的焦化装置都满负荷生产,有的甚至是超负荷生产,结果带来了一系列的问题,其中之一就是焦炭塔顶大油气线结焦,管线压力降过大,致使装置不能正常运行。
另外分馏塔各抽出线夹带焦粉,设备、管线磨损、腐蚀严重,影响产品质量和操作周期。
这在国内大部分炼油厂都发生过,如上海石化、武汉石化、荆门石化、济南石化、锦西五厂等都发生过油气管线结焦严重的现象。
因此,仔细分析一下原因,找出解决处理的措施是十分必要的。
2.油气线结焦原因焦炭塔顶大油气线结焦的主要原因归纳起来主要有以下三点:2.1焦粉(或泡沫)的夹带焦炭塔焦粉的夹带主要和塔内的油气线速及安全空高有关,在确定焦炭塔直径时一般按允许线速<0.15m/s计算,当装置处理能力提高时,油气线速增大,目前有的焦化装置的操作线速已超过0.15m/s,导致焦粉和泡沫不能沉降而带到出口线。
在确定焦炭塔高度时应留有一定的安全空高,安全空高一般为塔顶切线离泡沫层顶部的距离,一般安全空高为3~5米,国外也有2~3米的设计。
空高越大,焦炭塔的利用率越低,但油气在塔内的停留时间延长,对减少油气线和分馏塔内结焦有利。
国内设计一般在5米左右,但在操作中,由于是满负荷或超负荷运行,使得焦炭塔的安全空高减少,油气在塔内的停留时间缩短,焦粉和大量未完全反应的蜡油被夹带到大油气线内,裂化和缩合反应在大油气线内继续进行,焦粉慢慢越结越多,使得DN350~DN500的管径后来只剩下φ40~φ100的油气流通面积了。
2.2焦粉的沉积一般情况下,延迟焦化装置都设有焦炭塔顶油气线注急冷油措施,如果急冷油的温度、流量选择的合适,则急冷后的油气温度在420℃左右。
如果急冷油的温度偏高或注入量过小,急冷后的油气温度会高于420℃,那么油气在管线内就会有残余反应,若急冷油的注入位置不合适,也会导致冷却效果不理想,油气携带的焦粉不能有效洗涤,使被冷却的油气中的液体未及时排除,停留在出口管线中,并且会有大量的焦粉沉积在管壁上,随着操作时间的延长,焦粉越集越多,最后导致大油气线堵塞,压力降升高,操作难以进行。
焦化分馏塔底抽出线结焦分析及减缓措施

焦化分馏塔底抽出线结焦分析及减缓措施摘要:延迟焦化分馏塔底抽出线结焦是焦化装置普遍存在的一个问题,通过综合当前国内延迟焦化方面的工艺进展及对焦化装置分馏塔底抽出线结焦情况分析,得到影响分馏塔底抽出线结焦的主要因素有辐射注汽量、冷焦吹汽量、消泡剂的作用、焦炭塔平稳操作以及分馏塔底温度等,同时提出了减缓结焦的措施。
关键词:延迟焦化结焦分馏塔底抽出线兰州石化公司炼油厂1.2Mt/a延迟焦化装置,于2005年6月实现投料试车一次成功。
生产过程中发现分馏塔底抽出线结焦严重,在每一个生产周期后期很难建立塔底循环,导致分馏塔底开始结焦,给正常生产带来严重影响。
1、分馏塔底抽出线结焦影响因素分析1.1 辐射注汽量的影响注汽量的大小与原料性质、循环比和处理量等有关,对于新装置,为避免炉管结焦,注汽量较大,但这样加速了油气携带焦粉,增加了焦粉进入分馏塔趋势;另外,为保持辐射炉管内一定的介质流速,当处理量大时就可适当减少注汽量,当处理量小时可适当增大注汽量。
1.2 冷焦小吹汽量的影响焦炭塔在切塔后老塔进行冷焦处理时,由于生焦上部有一定高度的泡沫层和软焦层,如果冷焦时小吹汽量过大,就会有部分泡沫层通过大油气线进入分馏塔底部,加之这时急冷油又切换去了生产塔,不能有效地抑制焦粉和泡沫层进入大油气线和分馏塔。
因此冷焦时吹汽量控制要合理,尤其是高负荷生产和焦炭塔的生焦高度比较高时,应尽量减小小吹汽时蒸汽在塔内的线速。
1.3消泡剂的作用为了降低焦炭塔内泡沫层的高度,防止焦粉通过大油气线携带进入分馏塔底部引起分馏塔底抽出线结焦,一般都要在焦炭塔顶注入消泡剂。
但对消泡剂的加入比例还需要作进一步探索,以节约成本,增加效益。
1.4 焦炭塔平稳操作焦炭塔平稳操作至关重要。
切塔过程中,要通过压缩机控制好系统压力,如果操作不当就会有大量压力损失,会加重焦炭塔内的泡沫生成,打乱分馏塔的温度和压力分布,从而发生泡沫失控导致泡沫溢出,引发焦炭塔冲塔,将大量焦粒带入分馏塔底部,堵塞分馏塔底抽出线。
延迟焦化装置油气线结焦因素分析及解决措施

延迟焦化装置油气线结焦因素分析及解决措施作者:李娜侯勇来源:《中国化工贸易·下旬刊》2018年第10期摘要:120万吨/年延迟焦化装置焦炭塔塔口及油气线结焦严重,严重影响了装置的长周期安全运行。
通过分析结焦的主要原因是焦炭塔塔顶温度控制高,急冷油性质差、急冷油注入量不足、急冷油压力低使喷嘴达到不设计的喷雾效果等原因。
通过优化操作,解决了油气线快速结焦问题。
关键词:延迟焦化;焦炭塔;油气线;结焦;急冷油喷嘴1 前言乌石化公司120万吨/年延迟焦化装置于2011年11月建成投产。
装置采用一炉两塔工艺,设计循环比0.3。
装置加工渣油性质恶劣,金属含量高,导致加热炉炉管及油气线结焦倾向增大,严重影响了装置的长周期安全运行。
2013年检修后,9月23日装置开工正常,焦炭塔安全阀处压力为0.12-0.13MPa,装置运行至2014年10月,焦炭塔安全阀处压力上升至0.22-0.23MPa。
说明油气线已严重结焦。
2 油气结焦的原因分析及预防措施影响油气结焦的因素较多,包括原料性质、加热炉出口温度、焦炭塔顶部温度、油气气速、急冷油注入情况、消泡剂注入情况等。
2.1 塔顶油气温度过高大油气线结焦的原因就是渣油在发生裂化反应的同时,又产生一种副反应即缩合反应。
小分子的烃类缩合成大分子的烃类即会在管线内结焦。
一般来说油品的特性因数 K 值越大则临界分解温度越低,一般在420℃左右。
当原料 K 值增大时,临界温度下降。
另外由于热偶测点挂焦,会导致实际温度高于测量温度。
若焦炭塔大油气线温度高于大油气线内油品的临界温度,则重组分就可能会在大油气线内结焦。
有研究证明油品在临界分解温度范围内最容易发生分解和缩合反应。
因此为了避免大油气管线结焦,焦炭塔顶的操作温度应该低于该油品的临界分解温度。
2013年9月23日装置开工后,按设计要求控制焦炭塔顶部油气温度不大于425℃。
但国内延迟焦化装置普遍控制塔顶温度不大于420℃。
重油MIP催化裂化反应系统结焦原因与防焦措施探讨

图 2 沉降器内的结焦状况
2. 5 CSC 粗旋内壁
CSC 内壁生成了一层类似于保护膜的硬焦,并有明显的“冲 刷”痕迹。这种焦非常坚硬,一般不易脱落,且达到一定厚度后 冲刷与结焦速度 达 到 平 衡,不 会 继 续 增 长。在 正 常 平 稳 生 产 过 程中不会造成危害,但是由于 CSC 设计的小环蒸汽出口设计在 旋分下料锥形段 内 壁 上,结 焦 使 小 环 蒸 汽 出 口 分 布 板 上 的 孔 几 乎完全堵死,影响了 CSC 的汽提分离效果。要防止小环蒸汽进 入升气管的分布板不被结焦堵塞,一定要注意保证 CSC 小环蒸 汽的畅通及一定的流量。
Key words: MIP; FCC; coking; countermeasures
焦炭作为催化裂 化 反 应 产 物 之 一,在 催 化 剂 上 生 焦 是 必 然 的,正常的生焦 是 两 器 热 平 衡 的 热 量 保 证。但 是 在 反 应 器 壁 等 位置上结焦却会 给 带 装 置 的 平 稳 运 行 带 来 极 大 的 安 全 隐 患,据 报道,每年都有大量的催化装置因结焦问题而非计划停工,给生 产带来极大的经济损失[1]。
2. 6 单旋的料腿
清焦前发现六个单旋的料腿有 4 个几乎结焦堵死,其余 2 个下料孔径也已 缩 得 很 小。从 现 场 割 下 来 的 料 内 的 焦 料 看,主 要成粒状物粘附在内壁。这种情况主要是由于绝大部分的催化 剂与油气在 CSC 粗旋中得到了较高的分离,在单旋中只有少量 的催化剂与大量的油气,因此,下料腿得不到很好的“冲刷”,同 时由于温差与温降,此时温度大约在 480 ~ 510 ℃ 。在此温度 下,烃类以热裂化反应为主,且热裂化反应速度较大。热裂化反 应产生不饱和的 热 裂 化 产 物 二 烯 烃,二 烯 烃 很 易 与 稠 环 芳 烃 聚
焦炭塔顶大油气线结焦案例
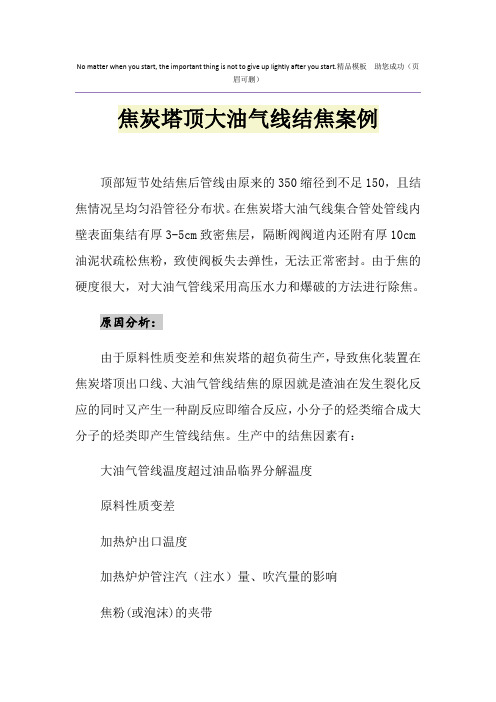
No matter when you start, the important thing is not to give up lightly after you start.精品模板助您成功(页眉可删)焦炭塔顶大油气线结焦案例顶部短节处结焦后管线由原来的350缩径到不足150,且结焦情况呈均匀沿管径分布状。
在焦炭塔大油气线集合管处管线内壁表面集结有厚3-5cm致密焦层,隔断阀阀道内还附有厚10cm 油泥状疏松焦粉,致使阀板失去弹性,无法正常密封。
由于焦的硬度很大,对大油气管线采用高压水力和爆破的方法进行除焦。
原因分析:由于原料性质变差和焦炭塔的超负荷生产,导致焦化装置在焦炭塔顶出口线、大油气管线结焦的原因就是渣油在发生裂化反应的同时又产生一种副反应即缩合反应,小分子的烃类缩合成大分子的烃类即产生管线结焦。
生产中的结焦因素有:大油气管线温度超过油品临界分解温度原料性质变差加热炉出口温度加热炉炉管注汽(注水)量、吹汽量的影响焦粉(或泡沫)的夹带急冷油注入量和位置焦炭塔顶出口线结焦主要和焦炭塔的操作有关,如果急冷油注入点距油气线出口较远,不能雾化直接将刚一出塔的油气温度降低到临界分解温度以下,这样在注急冷油前的一段管线非常容易结焦,特别是油气刚出口的立管上。
采取措施:各炼厂焦化装置在长期的实践中总结了不少经验,提出了许多行之有效的方法。
在油气管线上加法兰,当油气管线结焦时可以拆掉清焦。
在油气出口管线上加过滤器。
将急冷油注入油气刚出焦炭塔的根部,而且急冷油管线也增大到DN40。
采用斜插式注入、内置环型喷雾管注入,均可有效的防止了油气线结焦。
见下图通过进料量和消泡剂控制适宜的气速和泡沫层高度。
另外注入缓焦剂对减少系统结焦也非常有利。
延迟焦化焦炭塔顶大油气线结焦原因及应对措施

延迟焦化焦炭塔顶大油气线结焦原因及应对措施延迟焦化是一种将较重的石油分馏出的高沸点分子转化为更轻的烃类产品的炼油工艺。
在延迟焦化过程中,焦炭塔顶是一个关键的区域,经常会出现大油气线结焦的问题。
大油气线结焦是指进入焦化器的原油在塔顶部分析出的石脑油和沥青油在如石墨、焦炭等表面基质上或其中间形成附着层,堵塞了焦炭塔顶的管道和设备,影响了生产正常运行。
本文将详细阐述延迟焦化焦炭塔顶大油气线结焦的原因及应对措施。
1.原因分析(1)储油桶及补液罐石脑油结油:石脑油中含有大量脂肪酸,它们在高温下容易聚合形成碳质颗粒,导致结焦问题。
(2)塔顶凝析物生成:塔顶凝析物主要由高温下的碳氢化合物形成,这些化合物在高温下变得不稳定,会聚合而生成焦炭。
(3)外界气体侵入:外界空气中的杂质进入焦化塔顶,与原油中的烃类发生化学反应,形成焦炭。
(4)管道淤积:在焦化过程中,管道内会不断积累焦炭、沙粒等杂质,导致堵塞,最终形成焦炭结焦。
2.应对措施(1)优化储油桶和补液罐的结构:增加储油桶和补液罐的容积,减少其中的输送管道,降低原油在这些设备内部的停留时间,以减少结油的机会。
(2)控制塔顶温度:通过合理的调整焦化反应器的温度,控制油气在塔顶的凝析,减少凝析物的生成,减小结焦的风险。
(3)加强塔顶密封:在焦化塔顶和设备之间增加密封装置,减少外界空气和杂质的侵入,降低结焦的可能性。
(4)定期清理管道:定期对焦化塔顶的管道进行清理,及时清除管道中的焦炭、沙粒等杂质,以保持管道畅通。
(5)采用防结焦剂:添加具有防结焦性能的添加剂到原油中,形成稳定的体系,可以有效地防止焦炭结焦的发生。
(6)加强检修和维护:定期对焦化设备进行检修和维护,及时更换老化的设备和部件,保证设备的正常运行,减少结焦风险。
综上所述,延迟焦化焦炭塔顶大油气线结焦问题的解决需要综合运用多种方法和措施,从原料处理、工艺控制、设备维护等各个环节入手。
只有加强科学管理,优化工艺流程,严格执行操作规程,并配合合理的设备维护和清洁措施,才能有效地防止焦炭塔顶大油气线结焦的发生,保证生产的安全、稳定和高效。
焦化部分

主要用于炼铝、炼钢电炉中的电极,冶炼燃料,制造金钢砂,绝缘材料等。
14、石油焦的主要质量指标有哪些
挥发分、硫含量、灰分。
15、延长生焦时间对焦炭的挥发份有何影响?
延长生焦时间,实质就是使生焦时间加长,反应进一步深化,焦床处于高温状态的时间加长,焦床中未反应的重质油进一步参与反应,因而可以降低焦炭的挥发份。
生产中循环比的大小控制是通过调节蒸发段的温度实现的.
37、画出焦化压力与焦炭产率的关系图
38、画出温度与焦炭产率的关系图
39、画出循环比与焦炭产率的关系图
40、焦化循环比大小与产品产量、轻油收率、处理量、单位能耗关系?
循环比
产品产量
轻油收率
单位能耗
处理量
大
小
大
35、操作条件对焦化产品分布有何影响?
操作条件主要是:温度、压力、循环比。
(1)加热炉出口温度:提高温度,则气体、汽油、柴油产率上升,蜡油产率下降,焦炭产率下降。
(2)焦炭塔反应压力:压力提高,气体、汽油、柴油产率上升、焦炭产率上升,蜡油产率下降。
(3)循环比:循环比提高,气体、汽油、柴油产率上升,蜡油产率显著下降,而焦炭则略有增加。
(2)蜂窝状焦-----是含低胶质、沥青质原料生成的石油焦。焦块内小孔呈椭圆形,焦孔内部相互连通,分布均匀,并且是定向的。当沿焦块边部切开时,就能看到蜂窝状结构。
(3)针状焦-----是由芳香烃含量高的热裂化渣油或催化澄清油作原料而生成的石油焦。从外观看,有明显的条纹,焦块内的孔隙是均匀定向呈细长椭圆形,当碰撞时焦块碎裂成针状
36、循环比是根据什么确定的?本装置设计的循环
抑制焦化装置大油气线结焦的对策及分析

延 迟 焦化 工 艺是 重 油加 工 的重要 工 艺 之一 , 在 原 油加 工 中发挥 着重 要 的作 用 … 。在 实 际 生产 中 ,
最 大限度地延 长焦 化装 置 的生产 周期是 各炼 油厂提 高效 益 的一 项有效 途 径 , 在 国 内 同类 装 置 中影 响 而
焦化 装置 长周期运 转 的一个 普遍 问题 是焦炭 塔大油 气线 结焦 问题 。J 。垦 利石 化有 限责 任公 司焦 化装
中图 分 类 号 : E 2 . 2 T 6 43 文 献 标 识 码 : B 文 章编 号 :0 8—0 1 2 1 ) 2—03 0 10 2 X(0 0 0 0 8— 3
An lssa d Co n e me s r so k rLa g la d Ga n k n ay i n u tr a u e fCo e r eOi n sLi e Co i g
r a o s a d t e c re p n i g c u tr a u e .T r u h t e c n r l f e e a co s f c iey e s g e s n , n h o rs o d n o n eme s r s h o g o to v r l a t r ,e e t l a i h o s f v n
1 前 言
管壁, 把焦 炭塔 里没 有进 行完 的反应 继续进行 下去 , 形 成 的这 种结 焦是 比较 少 的 , 长期 积 累 会使 管经 但 变小, 使焦 炭塔 顶压 上 升 , 响生产 。这种 结焦 的主 影 要 原 因是 油气 在焦 炭塔 内线 速度 下 , 生携带 , 产 将焦 炭 塔 内没有反 应完 的泡 沫层 带 到挥发线 , 造成结焦 , 其 次是 由于 油气 长期 处 于高 温 状态 , 有二 次反 应 的
催化裂化装置结焦分析和防结焦措施

催化裂化装置结焦分析和防结焦措施摘要:随着原油价格上涨,原油重质化和劣质化是各炼油企业实现效益最大化的有效方法,由此带来了催化裂化装置结焦问题,目前重油催化裂化装置不可避免的存在结焦问题。
催化裂化结焦主要是由于原料性质变重后,原料喷嘴的雾化效果差,原料油在催化剂上不能完全汽化而产生湿催化剂,这些湿催化剂粘附结焦是引起提升管及沉降器内结焦的主要原因,而油气中重组分油气遇冷凝结,粘附在器壁上,长时间高温条件下发生缩合反应生成焦块,则是油气大管结焦的主要原因。
关键词:催化裂化;结焦;分析1前言催化裂化装置是炼油企业的核心装置,也是影响炼油企业效益的重要装置,如何减少催化裂化装置结焦延长装置运行周期,已成为各炼油企业实现效益最大化的重要手段。
湛江东兴1#催化裂化装置经过数次改造,由蜡油催化裂化改为重油催化裂化,2005年由洛阳设计院对催化装置进行扩能改造后,处理量提高至50万吨/年,设计减渣掺炼比例40%。
随着装置掺渣量的提高,结焦已成为影响装置长周期运行的重要因素,特别是沉降器的结焦长期威胁着装置的安全平稳运行。
1#催化裂化装置于05年3月16日一次性喷油成功后,由于掺渣量大,装置结焦较为严重,见表一。
2007年3月14日按计划进行检修,停工打开沉降器清焦时发现,装置结焦严重,清出的焦炭共约50吨,见图一。
目前1#催化装置沉降器内部结焦也较为严重,本周期运行过程中曾两次出现焦块脱落,造成催化剂循环困难现象。
本文通过分析结焦的原理及部位,结焦的原因,采取相应的防范措施,避免在生产过程中提升管、沉降器、油气大管、分馏塔底及油浆换热系统结焦,确保装置安稳长周期运行。
图一:2007年3月检修时,由沉降器清出的焦块表一:沉降器至气压机入口压力实测数据日期沉降器顶压力Mpa单旋出口压力Mpa油气入分馏塔压力MpaE201顶压力MpaF203压力Mpa气压机入口压力Mpa单旋压降kpa油气大管压降kpa分馏塔压降kpaE201顶至F203压降kpa沉降器至气压机压降kpa2005.6.7 0.245 0.228 0.209 0.194 0.152 0.151 17 19 15 42 94 2005.7.15 0.257 0.238 0.216 0.197 0.166 0.165 19 22 19 31 92 2005.8.1 0.26 0.234 0.199 0.181 0.155 0.154 26 35 18 26 106 2005.8.30 0.272 0.233 0.202 0.178 0.145 0.144 39 31 24 33 128 2005.9.30 0.272 0.234 0.208 0.184 0.142 0.137 38 26 24 42 1352006.1.19 0.266 0.228 0.197 0.174 0.158 0.138 38 31 23 16 128 2006.3.23 0.262 0.227 0.198 0.173 0.148 0.147 35 29 25 25 115 2006.8.28 0.263 0.232 0.206 0.186 0.153 0.152 31 26 20 33 111 2006.11.15 0.263 0.233 0.215 0.187 0.142 0.137 30 18 28 45 126 2007.3检修2007.5.23 0.261 0.252 0.244 0.229 0.209 0.198 9 8 15 20 63 2催化裂化装置结焦原理一般来说结焦的过程可以分为两种,一种为催化裂化反应结焦,催化裂化反应是一个重油脱碳的过程,由低氢碳比的重质油生产高氢碳比的轻质油的过程,因此必然生成一些焦炭,一些易生焦物(烯烃、芳烃、胶质、沥青质)在高温下具有很强的结焦倾向,通过脱氢缩合反应,以催化剂颗粒为结焦中心逐渐长大,最后生成焦。
- 1、下载文档前请自行甄别文档内容的完整性,平台不提供额外的编辑、内容补充、找答案等附加服务。
- 2、"仅部分预览"的文档,不可在线预览部分如存在完整性等问题,可反馈申请退款(可完整预览的文档不适用该条件!)。
- 3、如文档侵犯您的权益,请联系客服反馈,我们会尽快为您处理(人工客服工作时间:9:00-18:30)。
油气线结焦原因
1.前言
近年来,由于市场经济的影响和投资的限制,各石油化工公司新建、改扩建延迟焦化装置,给企业带来了可观的经济效益,为企业的发展做出了巨大的贡献。
为了提高经济效益,大部分炼油厂的焦化装置都满负荷生产,有的甚至是超负荷生产,结果带来了一系列的问题,其中之一就是焦炭塔顶大油气线结焦,管线压力降过大,致使装置不能正常运行。
另外分馏塔各抽出线夹带焦粉,设备、管线磨损、腐蚀严重,影响产品质量和操作周期。
这在国内大部分炼油厂都发生过,如上海石化、武汉石化、荆门石化、济南石化、锦西五厂等都发生过油气管线结焦严重的现象。
因此,仔细分析一下原因,找出解决处理的措施是十分必要的。
2.油气线结焦原因
焦炭塔顶大油气线结焦的主要原因归纳起来主要有以下三点:
2.1焦粉(或泡沫)的夹带
焦炭塔焦粉的夹带主要和塔内的油气线速及安全空高有关,在确定焦炭塔直径时一般按允许线速<0.15m/s计算,当装置处理能力提高时,油气线速增大,目前有的焦化装置的操作线速已超过0.15m/s,导致焦粉和泡沫不能沉降而带到出口线。
在确定焦炭塔高度时应留有一定的安全空高,安全空高一般为塔顶切线离泡沫层顶部的距离,一般安全空高为3~5米,国外也有2~3米的设计。
空高越大,焦炭塔的利用率越低,但油气在塔内的停留时间延长,对减少油气线和分馏塔内结焦有利。
国内设计一般在5米左右,但在操作中,由于是满负荷或超负荷运行,使得焦炭塔的安全空高减少,油气在塔内的停留时间缩短,焦粉和大量未完全反应的蜡油被夹带到大油气线内,裂化和缩合反应在大油气线内继续进行,焦粉慢慢越结越多,使得DN350~DN500的管径后来只剩下φ40~φ100的油气流通面积了。
2.2焦粉的沉积
一般情况下,延迟焦化装置都设有焦炭塔顶油气线注急冷油措施,如果急冷油的温度、流量选择的合适,则急冷后的油气温度在420℃左右。
如果急冷油的温度偏高或注入量过小,急冷后的油气温度会高于420℃,那么油气在管线内就会有残余反应,若急冷油的注入位置不合适,也会导致冷却效果不理想,油气携带的焦粉不能有效洗涤,使被冷却的油气中的液体未及时排除,停留在出口管线中,并且会有大量的焦粉沉积在管壁上,随着操作时间的延长,焦粉越集越多,最后导致大油气线堵塞,压力降升高,操作难以进行。
2.3原料性质变差
随着世界原油的开采,原油的性质越来越差:比重、粘度增大,杂质、重金属含量升高,水和盐的含量增加,这就需要在加工前做好预处理。
众所周知,焦化装置在炼油厂就象我们城市的一个“垃圾桶”,这也是焦化装置的一个特点:能加所有的其它装置无法加工的原料。
这样一来,从油田开采或者输送过来的原料越来越差,进焦化装置的渣油就更差了。
渣油中盐含量增加,在焦炭塔内就容易发泡,泡沫层升高,携带大量的焦粉进入油气管线,焦粉进一步的沉积,造成大油气线结焦。
3. 减少大油气线结焦的几点措施
只有正确的分析,才能找到正确的解决方法。
从以上的分析基本了解了结焦的主要原因,针对油气线结焦问题提出如下措施。
3.1 控制生产负荷
一般情况,设计是严格按着装置的规模和原料性质及产品要求来确定设备的规格、型号的。
原料及处理量一定,所确定的焦炭塔的塔径和高度也就随之而定。
富裕量即操作弹性一般为60%~110%。
如果超过装置的最大弹性范围就会引发一系列的问题,大油气管线结焦就是其中之一。
因此不能盲目的追求大处理量,应根据加工的原料性质对焦炭塔进行核算,使焦炭塔内的气速空高在安全范围之内,或采用缩短生焦时间的办法来增加焦炭塔的处理能力。
3.2 选择适宜的急冷油
常用的急冷油有三种:柴油、中段油和蜡油。
选择急冷油可以从两个
方面考虑:一是急冷效果,就是急冷后的油气温度。
急冷后的油气温度稳定,油气线内残余反应继续的可能性就小,管线结焦的程度越低。
反之则结焦越严重。
用这三种油品作急冷油的急冷效果是柴油>中段油>蜡油。
二是经济效益,用柴油作急冷油,大量的柴油被注入焦炭塔,分离出来的高品质油品又被注入焦炭塔,循环运转,分馏塔分离出来的大量柴油携带的热量无法充分利用,大量的低温位热源只能通过空冷器或水冷器将热量取走。
而用蜡油作急冷油,蜡油不易汽化,急冷后油气易冷凝,造成管线结焦。
综合考虑,选择中段油作为急冷油比较适合。
3.3 确定最佳的急冷油注入位置
在早期的设计中,一般在大油气线出口加三条急冷油注入管线,管径
气温度将低到420℃以下,这样在注急冷油前的一段管线非常容易结焦。
而且管线内结的焦又不能清除,经过长期的经验总结,设计了一种新的注入位置。
将急冷油的注入位置降低到油气线刚刚出焦炭塔的根部,而且急冷油管线也增大到DN40,并采用内置环行喷雾管注入,有效的防止了油气线结焦。
3.4 及时判断管线结焦情况和方便结焦清除的措施
过去焦炭塔顶是安装一支压力表,并在油气出口线的后部,当压力表前的管线结焦后,该压力表的压力仍会是正常值,无法判断结焦情况,经常出现安全阀起跳而压力不高的现象。
本文提出了在安全阀入口增加压力指示,通过该压力表的指示值和出口管道上压力表指示值的差值可明显判断油气出口线的结焦情况,在除焦过程中把管线中的结焦清除。
过去油气出口采用大弯头连接,不方便清焦。
本文提出改用三通或四通连接,上面
比塔底注入的消泡效果明显,塔顶注入应采用特殊的喷头使消泡剂分布均匀。
消泡剂的注入量一般为塔进料的20~50ppm,用柴油稀释到合适的浓度。
注入消泡剂可明显降低泡沫层高度,减少油气中的焦粉夹带,从而减少油出口管线的结焦。
4.小结
焦炭塔是焦化装置的核心设备,在工程设计时不仅要考虑焦炭塔本身结构尺寸、操作温度、操作压力、泡沫层高度、生焦时间等因素,还要考虑到与设备相关的每一个细节,如焦炭塔顶出口线的结构形式等,这样才能保证装置安全、可靠、稳定、长周期的运行。