切削力实验报告
切削力实验报告

篇一:007切削力测量实验报告专业班级姓名学号专业班级姓名学号实验日期实验地点 40号楼一楼实验室成绩实验名称切削力测量实验实验目的本次切削力测量实验的目的在于巩固和深化《机械制造技术基础》课堂所学的有关切削力的理论知识,正确认识切削力直接影响切削热、刀具磨损与使用寿命、加工精度和已加工表面质量等问题。
因此,研究切削力的规律,对于分析切削过程和生产实际是十分重要的。
本次实验在实验老师的指导下,达到如下实验目的:1、了解三向切削力实验的原理和方法;2、进行切削力单因素实验,了解背吃刀量、进给量和切削速度三大切削用量对切削力的影响规律,获得三向切削力实验公式;3、了解在计算机辅助下的、利用三向测力仪进行切削力实验的软、硬件系统构成,以及三向切削测力仪标定的原理和方法。
实验基本原理切削力是机械切削加工中的一个关键因素,它直接影响着机床、夹具等工艺装备的工作状态(功率、变形、振动等),影响着工件的加工精度、生产效率和生产成本等。
切削力的来源有两个:一是切削层金属、切屑和工件表层金属的弹塑性变形所产生的抗力;二是刀具与切屑、工件表面间的摩擦阻力。
影响切削力的因素很多,工件材料、切削用量、刀具几何参数、刀具磨损状况、切削液的种类和性能、刀具材料等都对切削力有较大的影响。
实验基本步骤1、实验指导教师讲解实验的目的和要求;强调实验的纪律、进行安全教育。
2、车床及工件的准备:将圆钢棒材(工件)安装在车床上,利用三爪卡盘和活动顶尖将棒材装夹到位;安装车刀,注意刀尖对准车床的中心高,然后启动车床将工件外圆表面加工平整;3、dj-cl-1型三向切削力实验系统的准备:1)启动切削力实验程序,在“输入实验编号”栏目内,输入年级、专业、班级、组号、实验次数和主题词等,并点击“确定”;2)点击“零位调整”软按钮,调出零位调整界面,进行三向零位调整;3)点击“切削力实验方式向导”软按钮,调出切削力实验方式向导界面,进行实验方式选择:选择切削力单因素实验;4、进行不改变进给量及切削速度,只改变背吃刀量单因素切削力实验;5、进行不改变进给量及背吃刀量,只改变切削速度单因素切削力实验;6、进行不改变背吃刀量及切削速度,只改变进给量单因素切削力实验;7、建立单因素切削力实验综合公式,并输出实验报告。
刀具,切削力实验报告
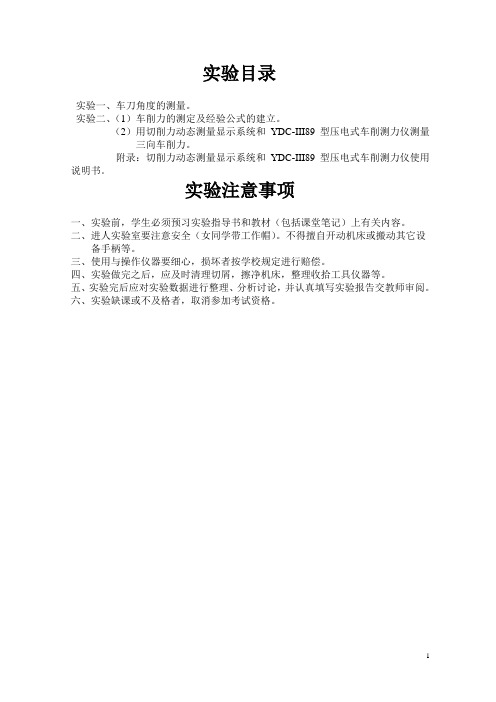
实验目录实验一、车刀角度的测量。
实验二、(1)车削力的测定及经验公式的建立。
(2)用切削力动态测量显示系统和YDC-III89型压电式车削测力仪测量三向车削力。
附录:切削力动态测量显示系统和YDC-III89型压电式车削测力仪使用说明书。
实验注意事项一、实验前,学生必须预习实验指导书和教材(包括课堂笔记)上有关内容。
二、进人实验室要注意安全(女同学带工作帽)。
不得擅自开动机床或搬动其它设备手柄等。
三、使用与操作仪器要细心,损坏者按学校规定进行赔偿。
四、实验做完之后,应及时清理切屑,擦净机床,整理收拾工具仪器等。
五、实验完后应对实验数据进行整理、分析讨论,并认真填写实验报告交教师审阅。
六、实验缺课或不及格者,取消参加考试资格。
实验一车刀角度的测量一、实验目的1.熟悉车刀角度,学会一般车刀角度基准面的确定及角度的测量方法。
2.了解不同参考系内车刀角度的换算方法。
二、实验设备,工具和仪器。
1.车刀量角台(三种型式)。
量角台的构造如图1—1。
(1)台座、(2)立柱、(3)指度片、(4)刻度板、(5)螺钉、(6)夹固螺钉、(7)定位块。
2.各种车刀模型。
A型量γ0 、α0、αo·B型量λs C型量K r、K图1—1车刀量角台三、实验内容车刀标注角度的测量。
用车刀量角台测量外园车刀的γ0 、α0 、λs 、K r、K r·、αo·等角。
(a)量前角:如图1-2,将车刀放置在台座上,调整刻度板4和指度片3使指度片的B边位于车刀主剖面内并与前刀面贴合,则由刻度板上读出γ0。
如果指度片位于横向或纵向剖面,则可测得γf或γp 。
(b)量后角:如图1-3,调整刻度板和指度片使指度片A边位于主剖面内,并与后刀面贴合则由刻度板可测得α0。
同理指度片位于横向或纵向剖面内可测得αf或αp。
调整刻度片位于副剖面内,可测得αo〃。
(c)量刃倾角:如图1-4,调整指度片使之位于切削平面内并使其测量边与主切削刃贴合,则由刻度板读出λs。
金属切削原理实验报告

一、实验目的1. 了解金属切削的基本原理和过程;2. 掌握切削用量对切削力和切削温度的影响;3. 熟悉金属切削实验设备和实验方法;4. 提高对金属切削加工工艺的认识。
二、实验原理金属切削是指用切削工具将金属工件上的多余材料去除,使其达到一定形状、尺寸和表面质量的过程。
金属切削实验主要研究切削用量(切削速度、切削深度、进给量)对切削力和切削温度的影响。
三、实验仪器与设备1. 金属切削实验台;2. 刀具;3. 金属工件;4. 切削力传感器;5. 温度传感器;6. 计算机及数据采集软件。
四、实验步骤1. 安装刀具:将刀具安装在实验台上,确保刀具安装牢固;2. 安装工件:将工件安装在夹具上,调整工件位置,确保工件与刀具对准;3. 设置切削参数:根据实验要求设置切削速度、切削深度和进给量;4. 开启实验台:启动实验台,进行金属切削实验;5. 数据采集:通过切削力传感器和温度传感器采集切削力和切削温度数据;6. 实验结束:关闭实验台,清理实验场地。
五、实验结果与分析1. 切削力与切削速度的关系:在切削深度和进给量不变的情况下,随着切削速度的增加,切削力逐渐增大。
这是因为切削速度提高,切削温度升高,切削材料软化,导致切削力增大;2. 切削力与切削深度的关系:在切削速度和进给量不变的情况下,随着切削深度的增加,切削力逐渐增大。
这是因为切削深度增加,切削面积增大,切削力增大;3. 切削力与进给量的关系:在切削速度和切削深度不变的情况下,随着进给量的增加,切削力逐渐增大。
这是因为进给量增加,切削速度提高,切削力增大;4. 切削温度与切削速度的关系:在切削深度和进给量不变的情况下,随着切削速度的增加,切削温度逐渐升高。
这是因为切削速度提高,切削热增加,切削温度升高;5. 切削温度与切削深度的关系:在切削速度和进给量不变的情况下,随着切削深度的增加,切削温度逐渐升高。
这是因为切削深度增加,切削热增加,切削温度升高;6. 切削温度与进给量的关系:在切削速度和切削深度不变的情况下,随着进给量的增加,切削温度逐渐升高。
切削金属实验总结汇报
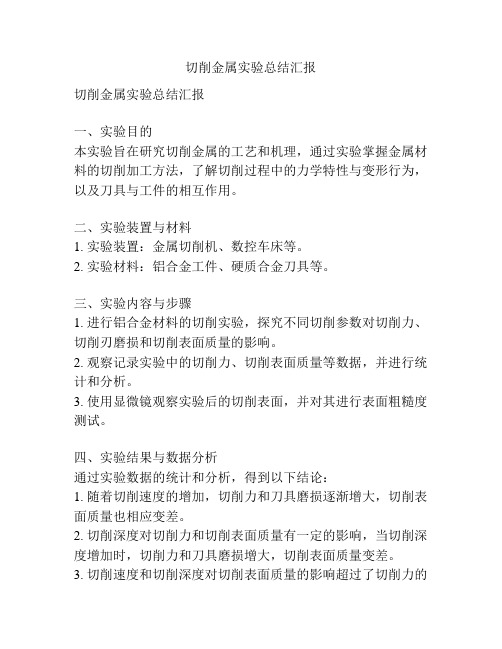
切削金属实验总结汇报切削金属实验总结汇报一、实验目的本实验旨在研究切削金属的工艺和机理,通过实验掌握金属材料的切削加工方法,了解切削过程中的力学特性与变形行为,以及刀具与工件的相互作用。
二、实验装置与材料1. 实验装置:金属切削机、数控车床等。
2. 实验材料:铝合金工件、硬质合金刀具等。
三、实验内容与步骤1. 进行铝合金材料的切削实验,探究不同切削参数对切削力、切削刃磨损和切削表面质量的影响。
2. 观察记录实验中的切削力、切削表面质量等数据,并进行统计和分析。
3. 使用显微镜观察实验后的切削表面,并对其进行表面粗糙度测试。
四、实验结果与数据分析通过实验数据的统计和分析,得到以下结论:1. 随着切削速度的增加,切削力和刀具磨损逐渐增大,切削表面质量也相应变差。
2. 切削深度对切削力和切削表面质量有一定的影响,当切削深度增加时,切削力和刀具磨损增大,切削表面质量变差。
3. 切削速度和切削深度对切削表面质量的影响超过了切削力的影响。
五、实验结论通过本次实验,我们了解了切削金属的工艺和机理,熟悉了金属切削的基本过程,掌握了切削参数对切削力、刃磨损和切削表面质量的影响,进一步认识了机械加工中的金属切削技术,对切削金属领域的应用有了更深入的了解。
六、实验心得体会通过本次实验,我深刻认识到切削金属过程中各个参数的重要性,合理选取切削参数是保证加工效率和加工质量的关键。
同时,我也发现切削金属是一项综合性实践技术,需要我们熟悉材料的性质和刀具的特点,并结合实际情况进行合理的参数调整。
通过实验的反复实践,我不断提高了自己的实践能力和创新思维,对切削金属技术有了更深的认识。
七、展望在今后的学习和工作中,我将继续加强对金属切削工艺和机理的研究,不断提高自己的技术水平,不断完善和创新切削金属的方法和工艺,为我国制造业的发展做出贡献。
同时,我也希望能够与同行交流切削金属技术,在实践中互相学习、共同进步,推动这一领域的发展。
切削力实验
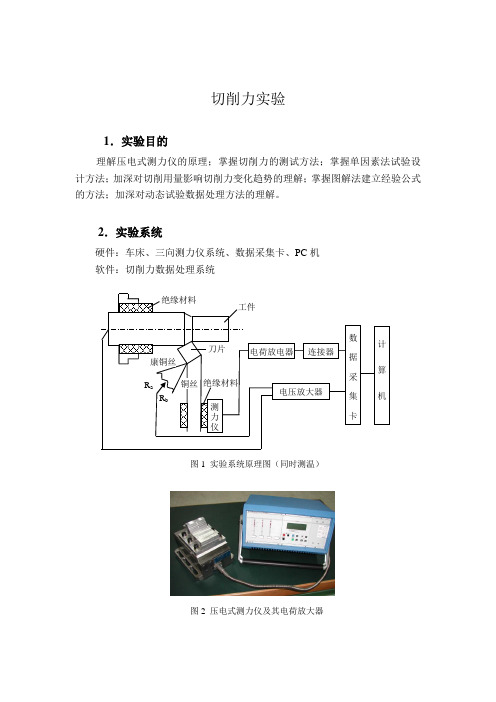
切削力实验
1.实验目的
理解压电式测力仪的原理;掌握切削力的测试方法;掌握单因素法试验设计方法;加深对切削用量影响切削力变化趋势的理解;掌握图解法建立经验公式的方法;加深对动态试验数据处理方法的理解。
2.实验系统
硬件:车床、三向测力仪系统、数据采集卡、PC 机 软件:切削力数据处理系统
图1 实验系统原理图(同时测温)
图2 压电式测力仪及其电荷放大器
图3 信号流程
3.实验过程
1)实验条件范围,准备工件、刀具; 2)单因素法设计实验; 3)实验测试系统,调试;
4)条件下进行切削加工,记录实验数据;
5)数据,获得切削条件与切削力之间的对应数据表; 6)作图法,求切削力经验公式;
7)经验公式分析切削用量对切削力影响的趋势; 8)实验报告。
图4 条件设置界面
图5 三向切削力记录界面(实时改变切削用量)。
数控工艺切削过程模拟实验报告
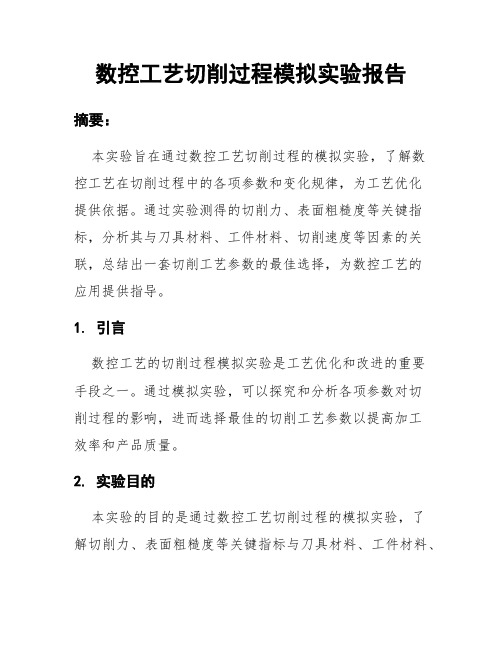
数控工艺切削过程模拟实验报告摘要:本实验旨在通过数控工艺切削过程的模拟实验,了解数控工艺在切削过程中的各项参数和变化规律,为工艺优化提供依据。
通过实验测得的切削力、表面粗糙度等关键指标,分析其与刀具材料、工件材料、切削速度等因素的关联,总结出一套切削工艺参数的最佳选择,为数控工艺的应用提供指导。
1. 引言数控工艺的切削过程模拟实验是工艺优化和改进的重要手段之一。
通过模拟实验,可以探究和分析各项参数对切削过程的影响,进而选择最佳的切削工艺参数以提高加工效率和产品质量。
2. 实验目的本实验的目的是通过数控工艺切削过程的模拟实验,了解切削力、表面粗糙度等关键指标与刀具材料、工件材料、切削速度等因素之间的关系,为优化切削工艺参数提供依据。
3. 实验设备和材料本实验使用的设备为数控加工中心,刀具材料选用硬质合金,工件材料选用无碳钢。
实验中使用的刀具包括铣刀和钻头。
4. 实验内容4.1 实验步骤:1) 将工件固定在数控加工中心工作台上;2) 设定刀具类型、切削速度和进给速度等数控工艺参数;3) 进行模拟切削,记录切削过程中的切削力;4) 完成切削后,测量工件的表面粗糙度。
4.2 实验结果:1) 记录了不同切削参数下的切削力数据;2) 测量了不同切削参数下工件的表面粗糙度。
5. 结果分析通过分析实验得到的数据,绘制切削力与切削速度、切削速度与表面粗糙度之间的关联曲线。
在数控切削过程中,切削力与切削速度呈正相关关系,切削速度与表面粗糙度呈负相关关系。
5.1 切削力与切削速度关系分析实验结果显示,在相同刀具和工件材料的条件下,切削力随着切削速度的增加而增加。
这是因为切削速度的增加会导致刀具与工件之间的摩擦增加,从而导致切削力的增加。
在一定范围内,切削力与切削速度大致呈线性关系。
5.2 切削速度与表面粗糙度关系分析通过实验数据分析,可以看出切削速度与表面粗糙度之间存在着一定的负相关关系。
在其他切削参数相同的情况下,随着切削速度的增加,表面粗糙度逐渐降低。
切削力实验报告

切削力实验报告切削力实验报告引言:切削力实验是机械加工领域中重要的研究内容之一。
通过测量切削力的大小和方向,可以评估刀具性能、优化切削工艺以及提高加工效率。
本实验旨在通过实际操作和数据分析,深入了解切削力的变化规律和影响因素。
实验装置与方法:本次实验采用数控车床进行切削力的测量。
首先,选择适当的刀具和工件材料,并确定切削参数,如进给速度、切削深度和切削速度。
接着,安装刀具和工件,调整好机床的切削参数。
在实验过程中,通过力传感器测量切削力的大小和方向,并将数据记录下来。
最后,根据实验数据进行分析和总结。
实验结果与分析:在实验过程中,我们记录了不同切削参数下的切削力数据,并进行了分析。
首先,我们发现切削速度对切削力有着显著影响。
随着切削速度的增加,切削力呈现出逐渐增加的趋势。
这是因为切削速度增加会导致切削温度升高,材料的塑性变形能力下降,从而增加了切削力的大小。
此外,切削速度的增加也会引起切削过程中的振动,进而增加了切削力的变化幅度。
其次,切削深度也对切削力有着明显的影响。
随着切削深度的增加,切削力呈现出逐渐增加的趋势。
这是因为切削深度的增加会导致切削面积增大,从而增加了切削力的大小。
此外,切削深度的增加也会引起切削过程中的切削力方向的变化,进而影响了切削力的分布情况。
最后,进给速度也对切削力有一定的影响。
我们观察到,随着进给速度的增加,切削力呈现出先增加后减小的趋势。
这是因为进给速度的增加会导致切削过程中的切削面积增大,从而增加了切削力的大小。
然而,当进给速度过大时,切削力会受到切削液的冲击和切削过程中的振动的影响,进而导致切削力的减小。
结论:通过本次实验,我们深入了解了切削力的变化规律和影响因素。
切削速度、切削深度和进给速度都对切削力有着明显的影响。
切削速度的增加会导致切削力的增加,切削深度的增加也会增加切削力的大小,而进给速度的变化则会引起切削力的先增加后减小的变化趋势。
这些实验结果对于优化切削工艺、提高加工效率具有重要的指导意义。
实验二-切削力实验

实验二 切削力实验一、实验目的和要求1. 了解切削测力仪的工作原理和测力方法和实验系统;2. 掌握背吃刀量sp a 进给量f 和切削速度c v 对切削力的影响规律;3. 通过实验数据的处理,建立切削力的经验公式。
二、实验及标定原理三向切削力的检测原理,是使用三向车削测力传感器检测三向应变,三向应变作为模拟信号,输出到切削力实验仪器内进行高倍率放大,再经A/D 板又一次放大之后,转换为数字量送入计算机的。
测力系统首先应该通过三向电标定,以确定各通道的增益倍数。
然后,再通过机械标定,确定测力传感器某一方向加载力值与三个测力方向响应的线性关系。
经过这两次标定,形成一个稳定的检测系统之后,才能进行切削力实验。
测量切削力的主要工具是测力仪,测力仪的种类很多。
有机械测力仪、油压测力仪和电测力仪。
机械和油压测力仪比较稳定、耐用。
而电测力仪的测量精度和灵敏度较高。
电测力仪根据其使用的传感器不同,又可分为电容式、电感式、压电式、电阻式和电磁式等。
目前电阻式和压电式用得最多。
图1 由应变片组成的电桥电阻式测力仪的工作原理:在测力仪的弹性元件上粘贴具有一定电阻值的电阻应变片,然后将电阻应变片联接电桥。
设电桥各臂的电阻分别是R 1、R 2、R 3和R 4,如果R 1/R 2=R 3/R 4,则电桥平衡,即2、4两点间的电位差为零,即应变电压输出为零。
在切削力的作用下,电阻应变片随着弹性元件发生弹性变形,从而改变它们的电阻。
如图1所示。
电阻应变片R 1和R 4在弹性张力作用下,其长度增大,截面积缩小,于是电阻增大。
R 2和R 3在弹性压力作用下,其长度缩短,截面积加大,于是电阻减小,电桥的平衡条件受到破坏。
2、4两点间产生电位差,输出应变电压。
通过高精度线性放大区将输出电压放大,并显示和记录下来。
输出应变电压与切削力的大小成正比,经过标定,可以得到输出应变电压和切削力之间的线性关系曲线(即标定曲线)。
测力时,只要知道输出应变电压,便能从标定曲线上查出切削力的数值。
切削实验报告
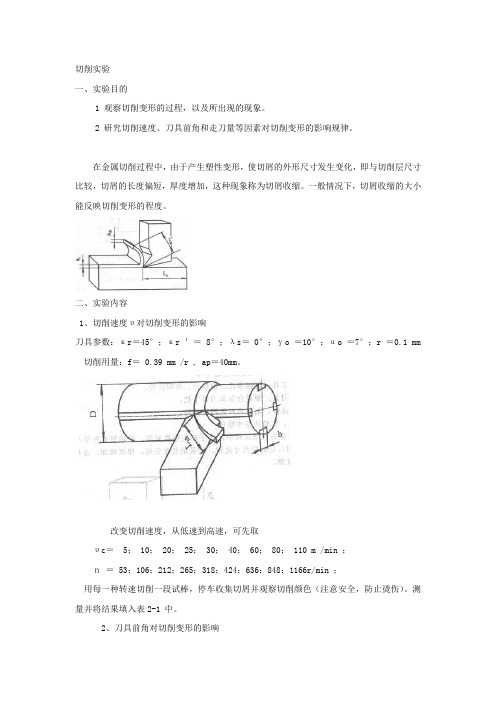
切削实验一、实验目的1 观察切削变形的过程,以及所出现的现象。
2 研究切削速度、刀具前角和走刀量等因素对切削变形的影响规律。
在金属切削过程中,由于产生塑性变形,使切屑的外形尺寸发生变化,即与切削层尺寸比较,切屑的长度偏短,厚度增加,这种现象称为切屑收缩。
一般情况下,切屑收缩的大小能反映切削变形的程度。
二、实验内容1、切削速度υ对切削变形的影响刀具参数:κr=45°;κr '= 8°;λs= 0°;γo =10°;αo =7°;r =0.1 mm 切削用量:f= 0.39 mm /r , ap=40mm。
改变切削速度,从低速到高速,可先取υc= 5; 10; 20; 25; 30; 40; 60; 80; 110 m /min ;n= 53;106;212;265;318;424;636;848;1166r/min ;用每一种转速切削一段试棒,停车收集切屑并观察切削颜色(注意安全,防止烫伤)。
测量并将结果填入表2-1 中。
2、刀具前角对切削变形的影响刀具参数:κr = 45°;κr '= 8°;λs = 0°;αo = 7°; r = 0.1 mm 。
切削用量: f= 0.39 mm /r , ap =40 mm υc= 60 m /min 。
改变车刀前角:γo = 0°; 15°; 30°。
用不同前角的车刀分别切削一段试棒,停车收集切屑并观察切削颜色(注意安全,防止烫伤)。
3、进给量 f 对切削变形的影响刀具参数:κr=45°;κr'=8°;λs=0°;γo=10°;αo=7°;r=0.1 mm 。
切削用量: ap = 40 mm υc= 60 m /min 。
改变进给量: f= 0.2 ; 0.36 ; 0.51 ; 0.66 ( mm/r )。
切削测试实验报告总结(3篇)
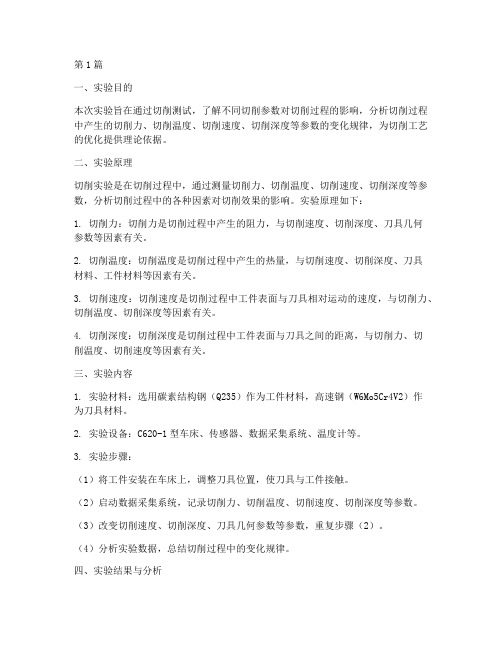
第1篇一、实验目的本次实验旨在通过切削测试,了解不同切削参数对切削过程的影响,分析切削过程中产生的切削力、切削温度、切削速度、切削深度等参数的变化规律,为切削工艺的优化提供理论依据。
二、实验原理切削实验是在切削过程中,通过测量切削力、切削温度、切削速度、切削深度等参数,分析切削过程中的各种因素对切削效果的影响。
实验原理如下:1. 切削力:切削力是切削过程中产生的阻力,与切削速度、切削深度、刀具几何参数等因素有关。
2. 切削温度:切削温度是切削过程中产生的热量,与切削速度、切削深度、刀具材料、工件材料等因素有关。
3. 切削速度:切削速度是切削过程中工件表面与刀具相对运动的速度,与切削力、切削温度、切削深度等因素有关。
4. 切削深度:切削深度是切削过程中工件表面与刀具之间的距离,与切削力、切削温度、切削速度等因素有关。
三、实验内容1. 实验材料:选用碳素结构钢(Q235)作为工件材料,高速钢(W6Mo5Cr4V2)作为刀具材料。
2. 实验设备:C620-1型车床、传感器、数据采集系统、温度计等。
3. 实验步骤:(1)将工件安装在车床上,调整刀具位置,使刀具与工件接触。
(2)启动数据采集系统,记录切削力、切削温度、切削速度、切削深度等参数。
(3)改变切削速度、切削深度、刀具几何参数等参数,重复步骤(2)。
(4)分析实验数据,总结切削过程中的变化规律。
四、实验结果与分析1. 切削力与切削速度的关系:实验结果表明,切削力随切削速度的增加而增大。
这是因为在高速切削过程中,切削刃的磨损加剧,导致切削力增大。
2. 切削力与切削深度的关系:实验结果表明,切削力随切削深度的增加而增大。
这是因为切削深度越大,切削刃所承受的切削阻力越大,从而导致切削力增大。
3. 切削温度与切削速度的关系:实验结果表明,切削温度随切削速度的增加而增大。
这是因为切削速度越高,切削过程中的热量越多,导致切削温度升高。
4. 切削温度与切削深度的关系:实验结果表明,切削温度随切削深度的增加而增大。
切削力测量实验报告
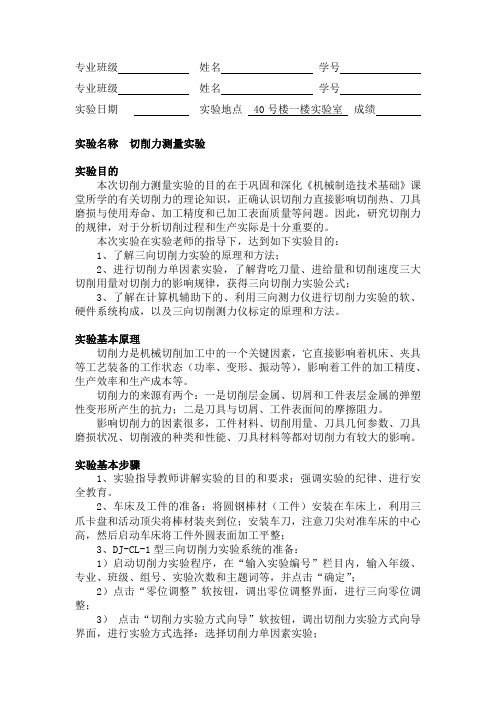
专业班级姓名学号专业班级姓名学号实验日期实验地点 40号楼一楼实验室成绩实验名称切削力测量实验实验目的本次切削力测量实验的目的在于巩固和深化《机械制造技术基础》课堂所学的有关切削力的理论知识,正确认识切削力直接影响切削热、刀具磨损与使用寿命、加工精度和已加工表面质量等问题。
因此,研究切削力的规律,对于分析切削过程和生产实际是十分重要的。
本次实验在实验老师的指导下,达到如下实验目的:1、了解三向切削力实验的原理和方法;2、进行切削力单因素实验,了解背吃刀量、进给量和切削速度三大切削用量对切削力的影响规律,获得三向切削力实验公式;3、了解在计算机辅助下的、利用三向测力仪进行切削力实验的软、硬件系统构成,以及三向切削测力仪标定的原理和方法。
实验基本原理切削力是机械切削加工中的一个关键因素,它直接影响着机床、夹具等工艺装备的工作状态(功率、变形、振动等),影响着工件的加工精度、生产效率和生产成本等。
切削力的来源有两个:一是切削层金属、切屑和工件表层金属的弹塑性变形所产生的抗力;二是刀具与切屑、工件表面间的摩擦阻力。
影响切削力的因素很多,工件材料、切削用量、刀具几何参数、刀具磨损状况、切削液的种类和性能、刀具材料等都对切削力有较大的影响。
实验基本步骤1、实验指导教师讲解实验的目的和要求;强调实验的纪律、进行安全教育。
2、车床及工件的准备:将圆钢棒材(工件)安装在车床上,利用三爪卡盘和活动顶尖将棒材装夹到位;安装车刀,注意刀尖对准车床的中心高,然后启动车床将工件外圆表面加工平整;3、DJ-CL-1型三向切削力实验系统的准备:1)启动切削力实验程序,在“输入实验编号”栏目内,输入年级、专业、班级、组号、实验次数和主题词等,并点击“确定”;2)点击“零位调整”软按钮,调出零位调整界面,进行三向零位调整;3)点击“切削力实验方式向导”软按钮,调出切削力实验方式向导界面,进行实验方式选择:选择切削力单因素实验;4、进行不改变进给量及切削速度,只改变背吃刀量单因素切削力实验;5、进行不改变进给量及背吃刀量,只改变切削速度单因素切削力实验;6、进行不改变背吃刀量及切削速度,只改变进给量单因素切削力实验;7、建立单因素切削力实验综合公式,并输出实验报告。
机械制造工程学实验报告-切削力

2.极差分析:
参加实验的因素取了几个水平,每一水平参加了几次实验,就会导致几个结果,把这些结果相加,就求出了每一因素各同一水平结果之和。本例中主轴转速有四个水平,各进行了四次实验,导致四个结果,把这四个结果相加,就得出各水平分别导致的结果之和,如Kn1=3.12+20.07+22.21+21.06=66.46为主轴转速在2000时切削力结果之和,然后将Kn1等分别写到下表3相应位置。极差是指一组数据中最大值和最小值之差,它是用来划分因素的重要程度的依据,极差越大说明该因素水平所引起实验结果的变化最大,根据极差大小,可以排出因素的主次顺序。经计算,3个主要因素切削深度ap、每齿进给量fx和主轴转速对切削力的影响程度依次为:主轴转速、切削深度、每齿进给量。
1.实验目的
(1)了解多分量切削力测力系统的基本结构及其工作原理。
(2)掌握KISTLER多分量切削力测力系统的基本操作方法。
(3)通过实验得出的数据,分析切削三要素对切削力的影响。
(4)分析实验数据,得出实验结论。
2.实验原理
KISTLER多分量切削力测力系统:
(1)切削力传感器具有高刚度,高固有频率,长寿命,大量程的特点;
1.通过极差分析判断主轴转速、每齿进给量、切削深度对切削力影响程度?
答:从小到大依次是主轴转速、每齿进给量、切削深度。
2.根据多元回归方法,求出切削力的经验公式系数,要求有详细的计算过程。
答:表格如下
序号
X1=logap
X2=logfx
X3=logn
Y=logF
1
X11=-1
X12=2.60
切削量实验报告结果(3篇)

第1篇一、实验目的本次实验旨在探究切削参数(切削深度、进给量、切削速度)对切削量(切削力、切削温度、表面粗糙度)的影响,为实际生产中切削参数的优化提供理论依据。
二、实验内容与方法1. 实验设备:高速切削实验台、电主轴、刀具、测力仪、温度计、表面粗糙度仪等。
2. 实验材料:45号钢。
3. 实验参数:- 切削深度:0.5mm、1.0mm、1.5mm- 进给量:0.2mm/r、0.4mm/r、0.6mm/r- 切削速度:300m/min、400m/min、500m/min4. 实验方法:- 将45号钢材料固定在高速切削实验台上,调整切削参数。
- 使用刀具进行切削实验,记录切削力、切削温度、表面粗糙度等数据。
- 对比不同切削参数下切削量的变化规律。
三、实验结果与分析1. 切削力:实验结果表明,切削力随切削深度、进给量的增加而增大,随切削速度的增加而减小。
在相同切削参数下,切削深度对切削力的影响最为显著。
2. 切削温度:实验结果表明,切削温度随切削深度、进给量的增加而升高,随切削速度的增加而降低。
在相同切削参数下,切削深度对切削温度的影响最为显著。
3. 表面粗糙度:实验结果表明,表面粗糙度随切削深度、进给量的增加而增大,随切削速度的增加而减小。
在相同切削参数下,切削速度对表面粗糙度的影响最为显著。
四、结论1. 切削力、切削温度、表面粗糙度均受到切削参数的影响,其中切削深度的影响最为显著。
2. 在实际生产中,应根据工件材料、加工要求等因素,合理选择切削参数,以获得最佳的切削效果。
3. 高速切削技术具有切削速度高、切削力小、切削温度低等优点,有利于提高加工效率、降低生产成本。
五、实验总结本次实验通过探究切削参数对切削量的影响,为实际生产中切削参数的优化提供了理论依据。
实验结果表明,切削深度、进给量、切削速度对切削力、切削温度、表面粗糙度具有显著影响。
在实际生产中,应根据工件材料、加工要求等因素,合理选择切削参数,以获得最佳的切削效果。
车削加工切削力测量实验报告书附指导书
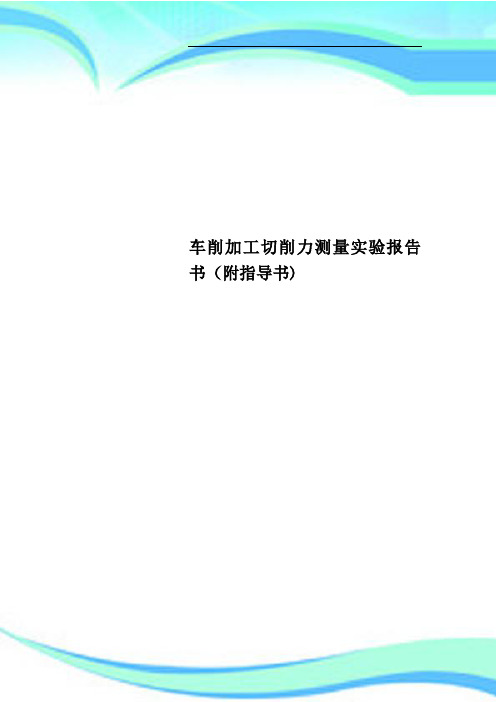
实验系统由下列设备仪器组成
1.微型数控车床KC0628S
2.车床测力刀架系统(图1),包括:
(1)车削测力刀架
(2)动态应变仪
(3)USB数据采集卡
(4)台式计算机
ﻬ3.三向切削力传感器结构与工作原理
三向切削力传感器是一种以电阻式应变片为敏感元件的力传感器。它具有八角扁环型结构(上下环)的弹性元件。八角扁环是用整体钢材加工成八角状结构,从而避免接触面间的摩擦和螺钉夹紧的影响。在八角状弹性元件的适当位置粘贴电阻应变片作为敏感元件。弹性元件受力变形后,导致电阻应变片变形,引起电阻应变片的电阻值变化,见图2。其电阻变化率△R/R与应变△L/L有如下的线性关系:
△R/R=K0*△L/L=K0*ε
式中Ko为电阻应变片的应变灵敏系数,一般Ko=2.0~2.4;
ε—八角状弹性元件的应变。
由于应变片电阻的电阻变化率△R/R是很小的。故此需外接电阻应变仪,将电阻应变片的微小变化量放大,进而转变成电流(电压)的变化量,形成电信号输出。在电阻应变仪的输出端连接计算机数据处理仪,对此信号进行实时采样,A/D转换、形成数字数据流输出,存储,形成实验数据的实时记录文档。
车削加工切削力测量实验报告书(附指导书)
———————————————————————————————— 作者:
———————————————————————————————— 日期:
ﻩ
车削加工切削力测量实验报告书
学号
姓名
小组
时间
成绩
上海大学生产工程实验中心
2014-11
一.实验概述
切削过程中,会产生一系列物理现象,如切削变形、切削力、切削热与切削温度、刀具磨损等。对切削加工过程中的切削力、切削温度进行实时测量,是研究切削机理的基本实验手段和主要研究方法。通过对实测的切削力、进行分析处理,可以推断切削过程中的切削变形、刀具磨损、工件表面质量的变化机理。在此基础上,可进一步为切削用量优化,提高零件加工精度等提供实验数据支持。
切削实训报告

一、实训目的本次切削实训旨在使学生了解和掌握切削加工的基本原理、方法和工艺,熟悉各种切削工具的使用和性能,提高学生的动手能力和实际操作技能。
通过本次实训,使学生能够熟练操作机床,进行简单的零件加工,为后续专业课程的学习和实践打下坚实的基础。
二、实训环境实训地点:XXX机床实训中心实训设备:C620-1型车床、C456型铣床、磨床、万能工具台等实训工具:各种切削刀具、量具、砂轮等三、实训原理切削加工是指利用切削工具对工件进行去除材料的过程。
切削加工的基本原理包括:1. 切削运动:切削运动是切削加工的基本运动,包括主运动和进给运动。
主运动是切削刀具与工件之间相对运动的速度最大的运动,进给运动是切削刀具与工件之间相对运动的速度较小的运动。
2. 切削要素:切削要素包括切削速度、切削深度、进给量、切削刃口形状和材料等。
切削要素的选择直接影响切削加工的质量和效率。
3. 切削力:切削力是切削加工过程中产生的力,包括切削力、进给力、径向力和轴向力。
切削力的计算和合理选择对切削加工的顺利进行至关重要。
四、实训过程1. 车削实训:- 目的:掌握车削加工的基本操作方法,熟悉车床结构及使用方法。
- 过程:首先,进行车床操作前的准备工作,包括检查机床状态、安装刀具、调整工件等。
然后,按照加工要求进行切削,注意切削速度、切削深度和进给量的选择。
最后,进行工件测量和检验。
2. 铣削实训:- 目的:掌握铣削加工的基本操作方法,熟悉铣床结构及使用方法。
- 过程:与车削实训类似,首先进行铣床操作前的准备工作,包括检查机床状态、安装刀具、调整工件等。
然后,按照加工要求进行切削,注意切削速度、切削深度和进给量的选择。
最后,进行工件测量和检验。
3. 磨削实训:- 目的:掌握磨削加工的基本操作方法,熟悉磨床结构及使用方法。
- 过程:与车削、铣削实训类似,首先进行磨床操作前的准备工作,包括检查机床状态、安装刀具、调整工件等。
然后,按照加工要求进行磨削,注意磨削速度、磨削深度和进给量的选择。
实验二车削加工切削力测量实验报告书(大全5篇)
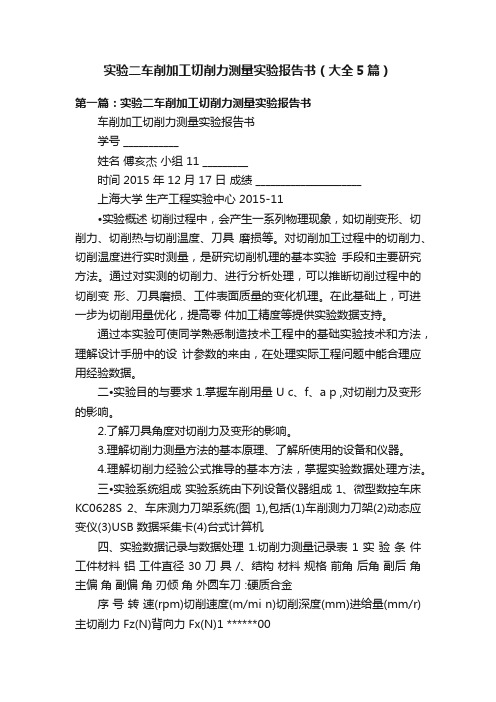
实验二车削加工切削力测量实验报告书(大全5篇)第一篇:实验二车削加工切削力测量实验报告书车削加工切削力测量实验报告书学号 ___________姓名傅亥杰小组 11 _________时间 2015 年 12 月 17 日成绩 _____________________上海大学生产工程实验中心 2015-11•实验概述切削过程中,会产生一系列物理现象,如切削变形、切削力、切削热与切削温度、刀具磨损等。
对切削加工过程中的切削力、切削温度进行实时测量,是研究切削机理的基本实验手段和主要研究方法。
通过对实测的切削力、进行分析处理,可以推断切削过程中的切削变形、刀具磨损、工件表面质量的变化机理。
在此基础上,可进一步为切削用量优化,提高零件加工精度等提供实验数据支持。
通过本实验可使同学熟悉制造技术工程中的基础实验技术和方法,理解设计手册中的设计参数的来由,在处理实际工程问题中能合理应用经验数据。
二•实验目的与要求 1.掌握车削用量 U c、f、a p ,对切削力及变形的影响。
2.了解刀具角度对切削力及变形的影响。
3.理解切削力测量方法的基本原理、了解所使用的设备和仪器。
4.理解切削力经验公式推导的基本方法,掌握实验数据处理方法。
三•实验系统组成实验系统由下列设备仪器组成 1、微型数控车床KC0628S 2、车床测力刀架系统(图1),包括(1)车削测力刀架(2)动态应变仪(3)USB 数据采集卡(4)台式计算机四、实验数据记录与数据处理 1.切削力测量记录表 1 实验条件工件材料铝工件直径 30 刀具 /、结构材料规格前角后角副后角主偏角副偏角刃倾角外圆车刀 :硬质合金序号转速(rpm)切削速度(m/mi n)切削深度(mm)进给量(mm/r)主切削力 Fz(N)背向力 Fx(N)1 ******00主切削力背向力切削深度主切削力背向力切削深度整理采集点并运用 MATLAB 寸数据处理如下:2.请按指数规律拟合主切削力或背刀力和切削深度、进给量的关系,建立切削力的经验公式。
学切削实验报告

一、实验目的本次切削实验旨在通过实际操作,使学生了解和掌握金属切削的基本原理、切削工具的选用和切削参数的确定方法,提高学生对切削工艺的认识,培养学生的实际操作技能和实验分析能力。
二、实验内容1. 实验原理金属切削是利用切削工具将工件表面材料去除,使其达到预定形状和尺寸的过程。
切削过程中,切削力、切削温度、切削液等因素对切削效果产生重要影响。
本实验主要研究以下内容:(1)切削力:切削力是切削过程中产生的力,包括切削主力、切削分力和切削力矩。
切削力的大小与切削速度、切削深度、进给量、工件材料、刀具材料等因素有关。
(2)切削温度:切削温度是切削过程中产生的热量,切削温度的高低对切削效果、刀具磨损和工件表面质量有重要影响。
(3)切削液:切削液在切削过程中具有冷却、润滑、清洗和防锈等作用,对提高切削效果和延长刀具寿命具有重要意义。
2. 实验材料实验材料选用45号钢,其硬度为HB207~255,切前硬度为HRC32~42。
3. 实验设备(1)C620-1型卧式车床(2)M10×1.5高速钢外圆车刀(3)CMM-500型三坐标测量仪(4)精度等级为0.01mm的游标卡尺(5)电子秤4. 实验步骤(1)刀具选用:根据工件材料、加工要求及切削条件,选择合适的刀具。
本实验选用M10×1.5高速钢外圆车刀。
(2)切削参数确定:根据工件材料、加工要求及切削条件,确定切削速度、切削深度和进给量。
本实验切削速度为100m/min,切削深度为2mm,进给量为0.3mm/r。
(3)工件装夹:将工件装夹在C620-1型卧式车床上,确保工件安装牢固。
(4)切削实验:启动C620-1型卧式车床,进行切削实验。
在切削过程中,观察切削现象,记录切削力、切削温度和刀具磨损情况。
(5)测量与分析:使用CMM-500型三坐标测量仪测量工件加工后的尺寸,使用游标卡尺测量刀具磨损量,分析切削效果。
三、实验结果与分析1. 切削力实验过程中,切削力的大小与切削速度、切削深度、进给量等因素有关。
切削正交实验报告

一、实验目的1. 探究不同切削参数对切削过程的影响,包括切削力、切削温度、切削厚度等。
2. 验证正交切削加工的优越性,为实际生产提供理论依据。
3. 优化切削参数,提高加工效率和表面质量。
二、实验原理正交切削是指在切削过程中,切削刃与工件表面垂直或成一定角度的切削方式。
正交切削具有以下特点:1. 切削力较小,切削温度较低。
2. 切屑形成良好,表面质量较高。
3. 切削效率较高,刀具寿命较长。
本实验以300M钢为研究对象,通过正交实验方法,分析不同切削参数对切削过程的影响,并优化切削参数。
三、实验材料及设备1. 实验材料:300M钢2. 实验设备:正交切削实验台、万能工具显微镜、力传感器、热电偶、计算机等四、实验方法1. 实验方案:采用正交实验设计,选取主轴转速、进给量和切削深度三个因素,每个因素选取三个水平,共九个实验方案。
2. 实验步骤:1) 按照实验方案设置切削参数。
2) 利用正交切削实验台进行切削实验。
3) 测量切削力、切削温度、切削厚度等数据。
4) 利用万能工具显微镜观察表面质量。
5) 分析实验数据,得出结论。
五、实验结果与分析1. 切削力分析实验结果表明,主轴转速对切削力的影响较大,进给量和切削深度的影响较小。
随着主轴转速的增加,切削力逐渐减小。
这是由于高速切削时,切削温度升高,切削力降低。
2. 切削温度分析实验结果表明,切削温度随着主轴转速和进给量的增加而升高,切削深度的影响较小。
这是由于高速切削时,切削热量无法及时散发,导致切削温度升高。
3. 切削厚度分析实验结果表明,切削厚度随着主轴转速和进给量的增加而增大,切削深度的影响较小。
这是由于高速切削时,切削速度提高,切削厚度增大。
4. 表面质量分析实验结果表明,正交切削加工的表面质量较好,表面粗糙度较低。
这是由于正交切削具有较小的切削力和切削温度,有利于提高表面质量。
六、结论1. 正交切削加工具有较小的切削力、切削温度和表面粗糙度,有利于提高加工效率和表面质量。
机械加工过程中的切削力分析研究报告

机械加工过程中的切削力分析研究报告摘要:本研究报告旨在对机械加工过程中的切削力进行深入分析研究。
切削力是机械加工中的重要参数,对刀具寿命、加工质量以及加工效率等方面都有着重要影响。
通过对切削力的研究,可以为优化机械加工过程提供理论依据和指导。
一、引言机械加工是制造业中常用的加工方法之一,其过程中切削力的大小和分布对加工结果至关重要。
切削力的研究可以帮助我们更好地了解切削过程中的物理现象,并为优化刀具设计、加工参数选择以及工艺改进提供依据。
二、切削力的形成机理切削力的形成主要与材料的塑性变形、摩擦力、切削区温度以及切削速度等因素相关。
在切削过程中,刀具与工件之间发生相互作用,导致材料的塑性变形和摩擦力的产生。
同时,切削区温度的升高也会影响切削力的大小。
切削速度的增加会导致切削力的增加,但是当切削速度达到一定值后,切削力的增加趋势会减缓。
三、切削力的测量方法切削力的测量方法有多种,常用的方法包括力传感器测量法、应变测量法以及功率测量法等。
力传感器测量法是通过在切削过程中使用力传感器来测量切削力的大小和分布情况。
应变测量法是通过在切削区域放置应变片,测量应变片的应变情况来推算切削力。
功率测量法则是通过测量切削过程中的功率变化来间接计算切削力。
四、切削力的影响因素切削力的大小和分布受多种因素的影响,包括切削速度、进给速度、切削深度、刀具几何形状以及材料性质等。
切削速度的增加会导致切削力的增加,但是同时也会影响切削区温度的升高。
进给速度的增加也会使切削力增加,但是过大的进给速度可能会导致切削力过大,影响加工质量。
切削深度的增加会使切削力增加,但是过大的切削深度可能会导致切削力过大,引起切削振动。
刀具几何形状的设计也会影响切削力的大小和分布情况。
不同材料的性质也会对切削力产生影响。
五、切削力的优化控制为了提高机械加工的效率和质量,需要对切削力进行优化控制。
切削力的优化控制可以通过优化刀具设计、合理选择加工参数以及改进工艺等手段来实现。
山东大学单因素切削力实验报告

切削力单因素实验报告20 年级 智能制造 专业 智能制造 班 2组 第 2次实验 主题词 智能制造机器人指导教师: 实验日期: 实验评分: 一. 实验条件:1. 车床型号 CA61402. 工件参数 工件参数见表1表1 实验工件参数3. 测力传感器型号 DJ-CL03A-201111234. 刀具参数:1) 刀具(刀片)材料 YT152) 刀具几何参数刀具几何参数见表2表2 单因素切削力实验刀具几何参数单位:度二. 实验结果:1. 单因素实验图 改变背吃刀量、改变进给量和改变切削速度的切削力实验图见图1、图2和图3。
3000250020001500 1000 500 0(N) 三 向 切 削力0 0.5 1 1.5 2 2.5 3图1 改变背吃刀量切削力实验图图例(下同) 切向力轴向力径向力2. 单因素实验公式 单因素实验公式见表3表3 单因素实验公式(N) 三 向 切 削 力30002500 2000 1500 1000 5000 0.1 0.2 0.3 0.4 图2 改变进给量切削力实验图(N) 三 向 切 削 力3000 2500 2000 1500 1000 5000 50 100 150 200 250图3 改变切削速度切削力实验图3.单因素实验综合公式:切向力F c =175.93a sp 0.58 f0.64 v c0.52轴向力F f = 2078.44a sp 1.30 f0.72 v c-0.14径向力F sp =12.36a sp 0.55 f-0.17 v c0.12实验评语:三.课后习题1.单因素习题102.单因素习题8四.实验人员:1.参加实验学生:。
- 1、下载文档前请自行甄别文档内容的完整性,平台不提供额外的编辑、内容补充、找答案等附加服务。
- 2、"仅部分预览"的文档,不可在线预览部分如存在完整性等问题,可反馈申请退款(可完整预览的文档不适用该条件!)。
- 3、如文档侵犯您的权益,请联系客服反馈,我们会尽快为您处理(人工客服工作时间:9:00-18:30)。
专业班级姓名学号专业班级姓名学号实验日期实验地点 40号楼一楼实验室成绩实验名称切削力测量实验实验目的本次切削力测量实验的目的在于巩固和深化《机械制造技术基础》课堂所学的有关切削力的理论知识,正确认识切削力直接影响切削热、刀具磨损与使用寿命、加工精度和已加工表面质量等问题。
因此,研究切削力的规律,对于分析切削过程和生产实际是十分重要的。
本次实验在实验老师的指导下,达到如下实验目的:1、了解三向切削力实验的原理和方法;2、进行切削力单因素实验,了解背吃刀量、进给量和切削速度三大切削用量对切削力的影响规律,获得三向切削力实验公式;3、了解在计算机辅助下的、利用三向测力仪进行切削力实验的软、硬件系统构成,以及三向切削测力仪标定的原理和方法。
实验基本原理切削力是机械切削加工中的一个关键因素,它直接影响着机床、夹具等工艺装备的工作状态(功率、变形、振动等),影响着工件的加工精度、生产效率和生产成本等。
切削力的来源有两个:一是切削层金属、切屑和工件表层金属的弹塑性变形所产生的抗力;二是刀具与切屑、工件表面间的摩擦阻力。
影响切削力的因素很多,工件材料、切削用量、刀具几何参数、刀具磨损状况、切削液的种类和性能、刀具材料等都对切削力有较大的影响。
实验基本步骤1、实验指导教师讲解实验的目的和要求;强调实验的纪律、进行安全教育。
2、车床及工件的准备:将圆钢棒材(工件)安装在车床上,利用三爪卡盘和活动顶尖将棒材装夹到位;安装车刀,注意刀尖对准车床的中心高,然后启动车床将工件外圆表面加工平整;3、dj-cl-1型三向切削力实验系统的准备:1)启动切削力实验程序,在“输入实验编号”栏目内,输入年级、专业、班级、组号、实验次数和主题词等,并点击“确定”;2)点击“零位调整”软按钮,调出零位调整界面,进行三向零位调整;3)点击“切削力实验方式向导”软按钮,调出切削力实验方式向导界面,进行实验方式选择:选择切削力单因素实验;4、进行不改变进给量及切削速度,只改变背吃刀量单因素切削力实验;5、进行不改变进给量及背吃刀量,只改变切削速度单因素切削力实验;6、进行不改变背吃刀量及切削速度,只改变进给量单因素切削力实验;7、建立单因素切削力实验综合公式,并输出实验报告。
原始记录1、车床型号 c62402、工件参数工件参数见表13、测力传感器型号 dj-04b-9174、刀具参数:刀具(刀片)材料 yt155、刀具几何参数刀具几何参数见表2表2 单因素切削力实验刀具几何参数6、实验结果:单因素实验图改变背吃刀量、改变进给量和改变切削速度的切削力实验图见图1、图2和图3。
3000 (n) 三向切削力 2500 2000 1500 1000 500 0 0 0.5 11.5 22.5 3 图例(下同)切向力轴向力径向力图 1 改变背吃刀量切削力实验图 3000 (n) 三向切削力 2500 2000 1500 1000 500 0 0 0.1 0.2 0.3 0.4图2 改变进给量切削力实验图 3000 2500 2000 1500 1000 500 0 0 50 100 150 200 250 (n) 三向切削力图3 改变切削速度切削力实验图实验数据处理及结果分析切削用量对切削力的影响很复杂。
加大背吃刀量和进给量都会使切削力增大,但两者的影响程度不同。
背吃刀量加大时,切削力成正比例增大,但进给量加大时,切削力不成正比例增大(略小),所以,在切削加工中,如从切削力和切削功率角度考虑,加大进给量比加大背吃刀量有利。
相比于背吃刀量和进给量,切削速度对切削力的影响较小,但更复杂。
切削铸铁等脆性材料时,因金属的塑性变形很小,切屑与前刀面的摩擦也很小,所以切削速度对切削力的影响不大;切削塑性材料时,当切削速度>27m/min时,积屑瘤消失,切削力一般随切削速度的增大而减小;当切削速度<27m/min时,切削力是受积屑瘤影响而变化的。
当切削速度=5m/min时,积屑瘤开始出现,随着切削速度的提高,积屑瘤逐渐增大,刀具的实际前角增大,故切削力逐渐减小;约在切削速度=17m/min时,积屑瘤最大,切削力最小;当切削速度超过17m/min时,积屑瘤逐渐减小,故切削力逐渐加大。
思考题及实验总结1、影响切削力的因素有哪些?答:2、分析背吃刀量、进给量和切削速度与切削力的关系。
答:实验总结:本组学生在实验前按照实验指导书的要求,认真进行了实验预习,并理解了切削力测量实验的要点;在实验中认真听取指导教师的讲解,积极思考并记录指导教师所讲的实验关键要点;在实际切削力测量实验过程中,严格执行操作规程,很好地完成了实验。
通过该实验,使我们将课堂所学的理论知识更加实际化,达到了理论和实际相结合的实验目的,不仅使我们对切削用量三要素对切削力的影响情况有了最直接的了解,而且使我们掌握了dj-cl-1型三向切削力实验系统测量切削力的使用方法,达到了实验的效果。
教师评语篇二:刀具,切削力实验报告实验目录实验一、车刀角度的测量。
实验二、(1)车削力的测定及经验公式的建立。
(2)用切削力动态测量显示系统和ydc-iii89型压电式车削测力仪测量三向车削力。
附录:切削力动态测量显示系统和ydc-iii89型压电式车削测力仪使用说明书。
实验注意事项一、实验前,学生必须预习实验指导书和教材(包括课堂笔记)上有关内容。
二、进人实验室要注意安全(女同学带工作帽)。
不得擅自开动机床或搬动其它设备手柄等。
三、使用与操作仪器要细心,损坏者按学校规定进行赔偿。
四、实验做完之后,应及时清理切屑,擦净机床,整理收拾工具仪器等。
五、实验完后应对实验数据进行整理、分析讨论,并认真填写实验报告交教师审阅。
六、实验缺课或不及格者,取消参加考试资格。
实验一车刀角度的测量一、实验目的1.熟悉车刀角度,学会一般车刀角度基准面的确定及角度的测量方法。
2.了解不同参考系内车刀角度的换算方法。
二、实验设备,工具和仪器。
1.车刀量角台(三种型式)。
量角台的构造如图1—1。
(1)台座、(2)立柱、(3)指度片、(4)刻度板、(5)螺钉、(6)夹固螺钉、(7)定位块。
2.各种车刀模型。
a型量γ0 、α0、αo b ·型量λs c型量kr 、k 图1—1车刀量角台三、实验内容车刀标注角度的测量。
用车刀量角台测量外园车刀的γ0 、α0 、λs 、 kr 、kr·、αo·等角。
(a)量前角:如图1-2,将车刀放置在台座上,调整刻度板4和指度片3使指度片的b边位于车刀主剖面内并与前刀面贴合,则由刻度板上读出γ0。
如果指度片位于横向或纵向剖面,则可测得γf或γp 。
(b)量后角:如图1-3,调整刻度板和指度片使指度片a边位于主剖面内,并与后刀面贴合则由刻度板可测得α0。
同理指度片位于横向或纵向剖面内可测得αf或αp。
调整刻度片位于副剖面内,可测得αo〃。
(c)量刃倾角:如图1-4,调整指度片使之位于切削平面内并使其测量边与主切削刃贴合,则由刻度板读出λs。
(d)量主偏角、副偏角:如图1-5,将车刀刀杆靠紧定位块.调整刻度板的指度片,使指度片测量边分别与主、副切削刃贴合,由刻度板读出kr和kr〃。
图1—2前角γ0测量图1—3后角量α0的测量图1—4刃倾角λs的测量图1—5主偏角kr、副偏角kr的测量〃实验报告内容实验记录1.主剖面参考系的基本角度(单位:度)计算:3.在所测量刀具中选择刃倾角最大的刀具,计算切深前角γp,进给前角γf。
实验二车削力的测定及经验公式的建立一、实验目的1.了解切削力动态测量显示系统、ydc-iii89型压电式车削测力仪的工作原理和使用方法。
2.了解切削力产生过程。
3.掌握切削深度、进给量等对切削力的影响规律4.通过对实验数据的处理,建立主切削力的经验公式二、实验设备,工具和仪器。
1.工件?60,q235棒料; 2.c6140普通车床;3.ydc-iii89型压电式车削测力仪(含外远圆车刀); 4.sinocer ye5850电荷放大器;5.pci—9118dg/l多功能数据采集卡(a/d转换); 6.计算机;7.切削力动态测量显示系统软件。
三、实验原理(一)测试系统框图(二)ydc-iii89型压电式车削测力仪 1.构成由一个含外圆车刀的整体构件与一个压电石英晶体三维力传感器构成,如图1 切削力单因素实验报告2012 年级机电专业 1 班 3组第 1次实验主题词 yy 一. 实验条件:1. 车床型号 ca61402. 工件参数工件参数见表1表1 实验工件参数实验评分:实验日期:2015-4-15 16:02:44 3. 测力传感器型号 dj-20101124 4. 刀具参数:1) 刀具(刀片)材料 yt152)刀具几何参数刀具几何参数见表2 表2 单因素切削力实验刀具几何参数单位:度二. 实验结果:1. 单因素实验图改变背吃刀量、改变进给量和改变切削速度的切削力实验图见图1、图2和图3。
3000(n) 三向切削力2500 2000 1500 1000 500 0 图1 改变背吃刀量切削力实验图0 0.5 1 1.5 2 2.5 3图例(下同)切向力轴向力径向力系统研制:重庆迪佳科技有限公司共3页第1页3000(n) 三向切削力2500 2000 1500 1000 500 0 0.1 0.2 0.3 0.4 3000 2500 2000 1500 1000 500 0 50 100 150 200 250图3 改变切削速度切削力实验图图2 改变进给量切削力实验图(n) 三向切削力2. 单因素实验公式单因素实验公式见表3表3 单因素实验公式系统研制:重庆迪佳科技有限公司共3页第2页3. 单因素实验综合公式:切向力 fc = 2.56 asp1.43f0.71 vc1.64 轴向力 ff = 0.00 asp1.32 0.10f-1.00 0.20 vc3.59 径向力 fsp = 0.16 aspf vc1.45三. 实验评语:四. 实验人员:1. 指导教师:刘增文,刘逢时2. 参加实验学生:系统研制:重庆迪佳科技有限公司共3页第3页篇四:单因素切削力实验报告切削力单因素实验报告10 年级机制专业 12 班 2组第 1次实验主题词指导教师:实验日期:2013-6-16 15:14:04 实验评分:一. 实验条件:1. 车床型号 ca61402. 工件参数工件参数见表1表1 实验工件参数3. 测力传感器型号4. 刀具参数:1) 刀具(刀片)材料 yt152)刀具几何参数刀具几何参数见表2 表2 单因素切削力实验刀具几何参数单位:度二. 实验结果:1. 单因素实验图改变背吃刀量、改变进给量和改变切削速度的切削力实验图见图1、图2和图3。