金属材料疲劳概念
金属材料的形变行为及疲劳机制

金属材料的形变行为及疲劳机制金属材料作为一种重要的结构材料,在现代工业和制造业中扮演着不可或缺的角色。
在机械工程领域中,金属材料的性能是十分重要的。
特别是在长期的使用过程中,金属材料会经历各种形变行为,如塑性变形、弹性变形等,同时也会受到各种外力和环境的影响,从而导致材料的疲劳破坏。
因此,深入研究金属材料的形变机制和疲劳机理对于提高材料的性能和延长材料寿命具有重要意义。
一、金属材料的形变行为及其分类1. 塑性变形在金属材料受到一定的外力作用时,经历一定的应变后,断面积发生明显的变化,称为塑性变形。
塑性变形是指材料在超过弹性限度后,由于材料分子内部结构的移动或重组,而导致材料体积、形状和内部应力等方面发生永久性变化的一种变形方式。
在塑性变形过程中,金属的应力和应变呈现非线性关系,随着应变的增加,应力逐渐增大,直至达到最大极限。
2. 弹性变形当金属受到外力作用时,会发生弹性变形。
弹性变形是指在外力作用消失后,金属能恢复原来的形状和体积的变形方式。
当金属材料受到外力作用时,会在一定范围内出现线性的应力-应变关系。
3. 化学变形在化学作用下,金属那块的外貌、物性或机械性质发作变化的情况下,称之为化学变形。
4. 相变形变相变形变是指金属材料在温度、压力等外界因素的影响下,发生物相转化从而导致断面积等较大的形变的变形方式。
在相变过程中,材料的晶粒会重新排列,导致新的晶粒的形成和原晶粒的破坏。
二、金属材料的疲劳机理金属材料在长期使用过程中,如经历不断的载荷变化,会产生一定的应力水平,从而导致金属的疲劳破坏。
疲劳机理主要分为两种:低周疲劳和高周疲劳。
1. 低周疲劳低周疲劳是指在低频、高应力的作用下,金属材料会逐渐累积一定的变形,终止于断裂。
通常这种疲劳发生在每秒两万次以下的变形下,断裂往往是塑性破坏。
2. 高周疲劳高周疲劳是指在高频、低应力的作用下,金属材料会逐渐累积一定的变形,终止于断裂。
通常这种疲劳发生在每秒两万次以上的变形下,断裂往往是损伤引起的微观裂纹扩展所造成。
材料力学性能第五章_金属的疲劳
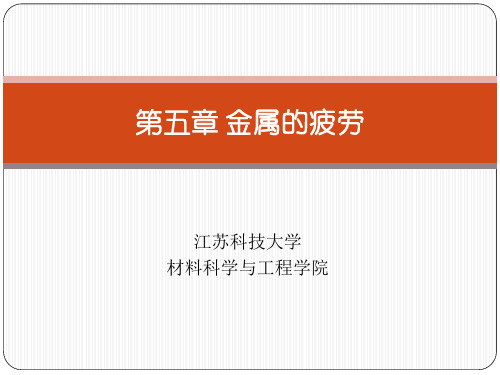
飞机舷窗
高速列车
5.1.3 疲劳宏观断口特征
疲劳断口保留了整个断裂过程的所有痕迹,记载着很多 断裂信息,具有明显的形貌特征,而这些特征又受材料 性质、应力状态、应力大小及环境因素的影响,因此对 疲劳断口的分析是研究疲劳过程、分析疲劳失效原因的 一种重要方法。 疲劳断裂经历了裂纹萌生和扩展过程。由于应力水平较 低,因此具有较明显的裂纹萌生和稳态扩展阶段,相应
疲劳破坏属低应力循环延时断裂,对于疲劳寿命 的预测就显得十分重要和必要。
对缺口、裂纹及组织等缺陷十分敏感,即对缺陷 具有高度的选择性。因为缺口或裂纹会引起应力 集中,加大对材料的损伤作用;组织缺陷(夹杂、 疏松、白点、脱碳等),将降低材料的局部强度, 二者综合更加速疲劳破坏的起始与发展。
18
应力σmax/10MPa
40
20
灰铸铁
0 103 104
105
106
107
循环周次/次
108
109
41
图 几种材料的疲劳曲线
疲劳极限
有水平段(碳钢、合金结构钢、球铁等) 经过无限次应力循环也不发生疲劳断裂,将对应
的应力称为疲劳极限,记为σ-1(对称循环)
无水平段(铝合金、不锈钢、高强度钢等) 只是随应力降低,循环周次不断增大。此时,根 据材料的使用要求规定某一循环周次下不发生断 裂的应力作为条件疲劳极限。 例:高强度钢、铝合金和不锈钢:N=108周次 钛合金:N=107周次
大小:瞬断区大小与机件承受名义应力及材料性质 有关,高名义应力或低韧性材科,瞬断区大;反之。 瞬断区则小。
金属材料疲劳试验变幅疲劳试验

金属材料疲劳试验变幅疲劳试验金属材料疲劳试验是材料科学领域中一项重要的试验方法,用于评估金属材料在长期交变载荷下的耐久性能。
其中,变幅疲劳试验是研究金属材料疲劳寿命的一种方法。
本文将介绍金属材料疲劳试验和变幅疲劳试验的原理、意义以及试验过程。
金属材料疲劳试验是通过施加交变载荷给金属材料,使其在应力循环作用下产生疲劳破坏的试验过程。
疲劳破坏是金属材料在交变载荷下反复加载和卸载过程中,由于材料内部的微观缺陷逐渐扩展导致的失效现象。
疲劳寿命是金属材料在一定的应力水平下进行疲劳试验时,承受指定应力循环次数后发生破坏的时间。
疲劳试验是评估金属材料的耐久性能和确定材料设计寿命的关键方法。
变幅疲劳试验是疲劳试验的一种形式,其原理是通过改变载荷幅值,即载荷的最大值和最小值之间的差值,来评估金属材料的疲劳寿命。
通常情况下,高载荷幅值会导致材料疲劳寿命的显著缩短。
变幅疲劳试验可以通过不同载荷幅值下的疲劳寿命数据,来确定金属材料的疲劳强度曲线,并进行疲劳寿命预测和寿命分析。
变幅疲劳试验的意义在于帮助工程师和科研人员评估金属材料在实际工作条件下的疲劳寿命表现,进而指导材料设计和结构设计。
通过该试验,可以确定材料的疲劳极限,即在多大幅值下材料会发生疲劳破坏,并预测材料在实际使用中的寿命,以保证结构的安全可靠性。
变幅疲劳试验还可以用于研究不同材料及其组织结构对疲劳寿命的影响,从而优化材料的性能。
变幅疲劳试验的试验过程主要包括试样制备、载荷施加和结果分析三个阶段。
需要根据试验目的和要求,制备合适的试样形状和尺寸。
通常情况下,试样应具备代表性,遵循相应的试验标准。
通过载荷施加设备施加不同载荷幅值下的交变载荷给试样,使其发生疲劳破坏。
试验过程中应控制载荷的频率、幅值和加载次数,以便获取准确可靠的试验数据。
对试验结果进行分析,包括疲劳寿命曲线的绘制、疲劳极限的确定以及寿命预测等。
综上所述,金属材料疲劳试验和变幅疲劳试验是评估金属材料疲劳性能的重要方法。
金属疲劳极限

金属疲劳极限金属疲劳极限是指金属材料在连续循环加载下,经过一定次数的循环后发生断裂的最小应力或应变。
它是金属材料在使用过程中的一个重要性能指标,对于保证金属材料的安全可靠性具有重要意义。
金属材料在使用过程中,常常会受到不同程度的力加载。
在循环加载的作用下,金属材料内部会发生微观结构的变化,包括晶粒的滑移、位错的增多、晶界的开裂等。
这些微观结构变化会导致金属材料的力学性能发生变化,最终导致金属材料的断裂。
金属疲劳极限的确定是通过实验来进行的。
实验中,将金属试样置于循环加载的作用下,记录下应力或应变与循环次数的关系曲线。
通过分析曲线的形状和变化趋势,可以确定金属疲劳极限的数值。
金属材料的疲劳寿命与其疲劳极限有密切关系。
疲劳寿命是指金属材料在一定应力水平下能够承受的循环次数。
当金属材料的应力小于疲劳极限时,金属材料的疲劳寿命较长;当金属材料的应力接近或超过疲劳极限时,金属材料的疲劳寿命会急剧下降。
因此,在工程设计中,需要根据金属材料的疲劳极限来确定合理的应力水平,以保证金属材料的使用寿命。
金属疲劳极限的大小与金属材料的组织结构、应力水平、温度等因素有关。
一般来说,晶粒尺寸较细、材料强度较高的金属材料其疲劳极限较高;而材料的强度越低,疲劳极限也会相应降低。
此外,温度对金属材料的疲劳极限也有一定影响,通常情况下,温度升高会导致金属材料的疲劳极限降低。
在实际工程中,为了保证金属材料的安全可靠性,需要对金属材料的疲劳极限进行评估。
评估疲劳极限的方法有很多种,常用的方法包括疲劳试验、数值模拟、统计分析等。
通过这些方法可以对金属材料的疲劳极限进行预测和估计,从而指导工程实践中的设计和材料选择。
金属疲劳极限是金属材料在连续循环加载下发生断裂的最小应力或应变。
它是金属材料在使用过程中的一个重要性能指标,对于保证金属材料的安全可靠性具有重要意义。
在工程实践中,需要对金属材料的疲劳极限进行评估和预测,以保证工程设计的安全性。
金属疲劳

(3)静力破坏通常有明显的塑性变形产生:疲劳破坏通常没有外在宏观的显著塑性变形迹象,哪怕是塑性良好 的金属也这样,就像脆性破坏一样,事先不易觉察出来,这就表明疲劳破坏具有更大的危险性。
相关区别
材料力学是根据静力实验来确定材料的机械性能(比如弹性极限、屈服极限、强度极限)的,这些机械性能没 有充分反映材料在交变应力作用下的特性。因此,在交变载荷作用下工作的零件或结构,如果还是按静载荷去设 计,在使用过程中往往会发生突发性故障。
疲劳破坏与传统的静力破坏有着许多明显的本质区别:
(1)静力破坏是一次最大载荷作用下的破坏:疲劳破坏是多次反复载荷作用下的破坏,它不是短期内发生的, 而是要经历一定的时间,甚至很长时间才发生破坏。
在金属材料中添加各种“维生素”是增强金属抗疲劳的有效办法。例如,在钢铁和有色金属里,加进万分之 几或千万分之几的稀土元素,就可以大大提高这些金属抗疲劳的本领,延长使用寿命。随着科学技术的发展,现 已出现“金属免疫疗法”新技术,通过事先引入的办法来增强金属的疲劳强度,以抵抗疲劳损坏。此外,在金属 构件上,应尽量减少薄弱环节,还可以用一些辅助性工艺增加表面光洁度,以免发生锈蚀。
感谢观看
金属内部结构并不均匀,从而造成应力传递的不平衡,有的地方会成为应力集中区。与此同时,金属内部的 缺陷处还存在许多微小的裂纹。在力的持续作用下,裂纹会越来越大,材料中能够传递应力部分越来越少,直至 剩余部分不能继续传递负载时,金属构件就会全部毁坏。
早在100多年以前,人们就发现了金属疲劳给各个方面带来的损害。但由于技术的落后,还不能查明疲劳破 坏的原因。直到显微镜和电子显微镜相继出现之后,使人类在揭开金属疲劳秘密的道路上不断取得新的成果,并 atigue of metal。金属疲劳是指一种在交变应力作用下,金属材料发生破坏的现象。 机械零件在交变压力作用下,经过一段时间后,在局部高应力区形成微小裂纹,再由微小裂纹逐渐扩展以致断裂。 疲劳破坏具有在时间上的突发性,在位置上的局部性及对环境和缺陷的敏感性等特点,故疲劳破坏常不易被及时 发现且易于造成事故。应力幅值、平均应力大小和循环次数是影响金属疲劳的三个主要因素。
金属材料疲劳

金属材料疲劳金属材料疲劳是指金属在受到循环应力作用下,随着时间的推移逐渐产生裂纹并最终破坏的现象。
疲劳是金属材料的一种重要破坏形式,也是工程实践中不可忽视的问题。
本文将从金属材料疲劳的基本原理、影响因素以及预防措施等方面进行探讨。
首先,金属材料疲劳的基本原理是由于金属在受到交变应力作用下,其晶格结构发生变化,从而引起金属内部的微观损伤,最终导致裂纹的生成和扩展。
这种微观损伤主要包括位错的运动和集聚、晶界的滑移和变形等。
随着循环载荷的不断作用,这些微观损伤逐渐积累,最终导致金属材料的疲劳破坏。
其次,金属材料疲劳受到许多影响因素的制约。
首先是应力水平的大小,循环载荷的幅值越大,金属材料的疲劳寿命就越短。
其次是应力的频率,循环载荷的频率越高,金属材料的疲劳寿命也越短。
此外,温度、环境介质、金属材料的组织结构等因素也会对金属材料的疲劳性能产生重要影响。
为了预防金属材料的疲劳破坏,可以采取一系列的措施。
首先是对金属材料进行合理的设计,尽量避免应力集中和裂纹的敏感区域。
其次是对金属材料进行表面处理,提高其抗疲劳性能。
此外,可以采用合适的工艺控制和热处理手段,提高金属材料的抗疲劳性能。
另外,科学合理地进行应力分析和寿命预测,也是预防金属材料疲劳破坏的重要手段。
总之,金属材料疲劳是一种普遍存在的现象,对于工程实践具有重要的影响。
了解金属材料疲劳的基本原理和影响因素,采取有效的预防措施,对于延长金属材料的使用寿命,提高工程结构的安全性具有重要意义。
因此,我们应该加强对金属材料疲劳的研究和应用,不断提高金属材料的抗疲劳性能,为工程实践提供更加可靠的保障。
通过对金属材料疲劳的基本原理、影响因素和预防措施的探讨,我们可以更加深入地了解金属材料疲劳的本质,为工程实践提供更加可靠的保障。
希望本文能够对相关领域的研究和实践工作有所帮助,推动金属材料疲劳领域的进一步发展。
金属材料疲劳寿命的研究与提高

金属材料疲劳寿命的研究与提高金属材料作为工业生产中不可缺少的一部分,其强度、硬度以及耐久性在很大程度上影响着产品的使用寿命。
然而,由于金属材料长时间的使用和可变的负载,会使金属材料出现疲劳现象,从而缩短其使用寿命。
因此,金属材料疲劳寿命的研究和提高,就成了一个重要的课题。
疲劳现象是指金属材料在经历反复的载荷作用后,其物理、化学性能及结构和外形发生变化、强度、韧性等力学性能等发生退化的现象。
材料疲劳的寿命是通过材料所承受的应力大小以及应力的循环次数来衡量的。
在金属应用方面,疲劳失效是造成很多设备与结构事故的主要原因之一,如:机械设备失效、桥梁倒塌、轮胎爆裂等。
因此,如何提高疲劳寿命就成为了一个十分严峻的挑战。
近年来,对于金属疲劳寿命研究得到了越来越多的关注。
为了让金属材料更加耐久,利用现代制造技术和材料科学,对疲劳寿命的增加进行针对性研究和措施的提出。
目前主要的疲劳寿命提高方法有以下几种:1. 变形处理金属疲劳寿命与其微观组织、组分结构有着密切的关系。
其中制作类似压缩道辊之类的零部件所应用的超声波变压处理技术,可以使材料产生小的塑性变形,从而改善微观组织的结构和性能,并提高了材料的耐久性。
2. 表面处理表面处理是一种简单而且非常有效的提高金属材料疲劳寿命的方法。
例如,通过镀铬、镀镍等金属制成的耐疲劳材料,不仅延缓了加工区域的裂纹,而且具有材料的自润滑性。
另外还有喷砂和拉丝等方法,都可以改善表面质量,防止氢脆现象,从而减少疲劳裂纹的产生。
3. 金属组织优化金属材料的组织和精度对其疲劳性能的影响是显著的。
通过优化金属薄板的组织和晶粒结构,可以提高疲劳强度。
同时采用在液体融合下的熔敷及流行技术,能够有效的降低材料的表面裂纹和疲劳裂纹的开裂阈值,从而提高材料的疲劳寿命。
4. 化学渗透对于不同种类的金属材料,它们的疲劳裂纹出现了在位于金属表面和内部的位置处。
化学渗透可以使底材被渗入的金属改善表面性能并形成非共质形成的结构,从而使其表现出更高的耐久性。
金属疲劳的名词解释

金属疲劳的名词解释金属疲劳是指金属材料在受到周期性或重复加载时,由于内部微观细观结构的缺陷和应力集中等因素,导致局部应力超过其抗力而产生的一种机械性能变化现象。
在实际工程中,金属疲劳是一种重要的失效形式,常常导致机械设备、工程结构和材料元件的突然损坏,因此对金属疲劳的理解和控制具有重要意义。
一、金属疲劳的起因金属疲劳的起因与金属材料的微观细观结构有密切关系。
在金属晶体中存在着晶界、孪晶界、位错、夹杂物等缺陷,这些都是金属疲劳产生的起因。
当金属材料受到外部荷载作用时,缺陷处存在应力集中,容易引发裂纹的形成。
随着荷载的循环,裂纹逐渐扩展,并最终导致材料断裂。
二、金属疲劳的特点1. 循环加载和高频加载。
金属疲劳是因为金属材料在循环加载下产生的疲劳失效,而非稳态加载。
循环加载中的应力水平往往较低,但由于循环次数较多,最终会导致金属材料的损坏。
2. 与应力幅度和寿命的关系。
金属疲劳的寿命与循环应力的幅度密切相关,随着循环应力幅度的增大,金属疲劳的寿命会显著减小。
同时,金属疲劳的寿命还与材料的强度、断裂韧性以及环境因素等有关。
3. 局部疲劳破坏。
金属疲劳是一种局部破坏形式,一般是由于材料表面或内部缺陷的存在而引起的。
在应力集中区域,裂纹会迅速扩展和连接,导致材料的失效。
三、金属疲劳的影响因素1. 循环应力幅度。
金属疲劳的寿命与循环应力的幅度密切相关,一般来说,应力幅度越大,金属疲劳的寿命越短。
2. 材料性能。
金属疲劳的寿命与材料的强度、韧性以及断裂韧性有关。
高强度和高韧性的材料一般具有较长的金属疲劳寿命。
3. 环境条件。
环境条件也是影响金属疲劳寿命的重要因素。
高温、潮湿以及腐蚀介质等会加速金属疲劳的发生和扩展。
四、金属疲劳的防控措施1. 加强材料检测。
在工程设计和加工过程中,对金属材料进行严格的检测,避免使用存在严重缺陷的材料。
2. 强化材料表面处理。
通过表面处理,如表面喷涂、电镀等方式,增加金属材料的表面硬度和耐蚀性,提高金属疲劳的抗性。
金属材料的疲劳极限标准

金属材料的疲劳极限标准1. 引言1.1 疲劳极限的定义疲劳极限是指金属材料在受到交变应力作用下所能承受的疲劳载荷的极限值。
疲劳极限与金属材料的抗疲劳性能密切相关,是评价金属材料抗疲劳性能的重要指标之一。
疲劳极限通常用应力水平表示,即在特定的应力幅值下,金属材料经过一定次数的循环载荷后出现裂纹和破坏的应力值。
疲劳极限是金属材料在实际工程中使用时需要考虑的重要参数,对于确保金属部件在长期使用过程中不会因为疲劳破坏而影响工作安全具有重要意义。
疲劳极限的测定需要进行大量的实验研究和数据分析,以确保结果的准确性和可靠性。
金属材料的疲劳极限还受到多种因素的影响,如材料的化学成分、热处理工艺、表面处理等,需要综合考虑这些因素才能准确评估金属材料的疲劳性能。
1.2 金属材料的疲劳极限金属材料的疲劳极限是指在连续循环加载下,金属材料所能承受的最大变形次数或载荷幅度。
对于金属材料来说,疲劳极限是一项至关重要的性能指标,它直接影响着材料在实际工程中的可靠性和安全性。
金属材料的疲劳极限可以通过实验测试来确定,通常采用旋转弯曲、拉伸、扭转等不同加载方式进行试验。
通过对金属材料进行疲劳测试,可以得到不同载荷条件下的疲劳曲线,从而确定材料的疲劳性能和疲劳寿命。
金属材料的疲劳极限受多种因素影响,包括材料的化学成分、晶粒结构、微观缺陷等。
对于不同类型的金属材料,其疲劳极限标准也有所不同,因此在工程设计和材料选择过程中,需要根据具体的应用要求来确定合适的金属材料及其疲劳极限要求。
疲劳极限的重要性在于可以帮助工程师评估材料的使用寿命和安全性,从而设计出更加可靠和耐久的工程结构。
研究金属材料的疲劳极限标准对于提高材料的抗疲劳性能和延长材料的使用寿命具有重要意义。
2. 正文2.1 金属材料的疲劳损伤金属材料在受到循环载荷作用时,会产生疲劳损伤。
这种损伤是由于金属内部的微观缺陷在受力的作用下逐渐扩展,最终导致材料的破坏。
疲劳损伤的形式主要有裂纹的扩展和表面损伤两种。
金属材料的耐磨性与疲劳性能分析
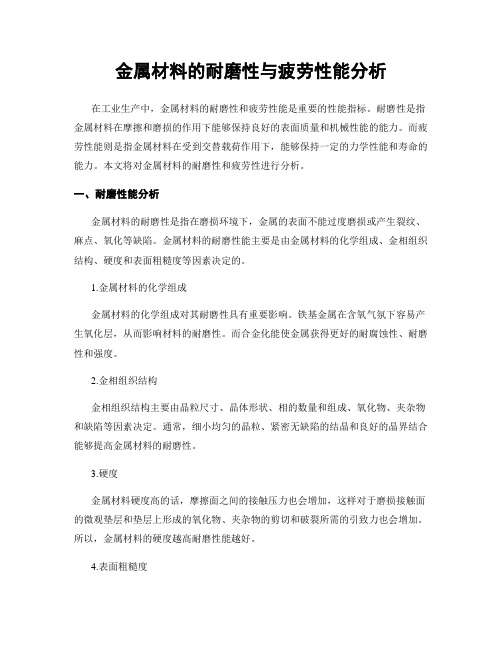
金属材料的耐磨性与疲劳性能分析在工业生产中,金属材料的耐磨性和疲劳性能是重要的性能指标。
耐磨性是指金属材料在摩擦和磨损的作用下能够保持良好的表面质量和机械性能的能力。
而疲劳性能则是指金属材料在受到交替载荷作用下,能够保持一定的力学性能和寿命的能力。
本文将对金属材料的耐磨性和疲劳性进行分析。
一、耐磨性能分析金属材料的耐磨性是指在磨损环境下,金属的表面不能过度磨损或产生裂纹、麻点、氧化等缺陷。
金属材料的耐磨性能主要是由金属材料的化学组成、金相组织结构、硬度和表面粗糙度等因素决定的。
1.金属材料的化学组成金属材料的化学组成对其耐磨性具有重要影响。
铁基金属在含氧气氛下容易产生氧化层,从而影响材料的耐磨性。
而合金化能使金属获得更好的耐腐蚀性、耐磨性和强度。
2.金相组织结构金相组织结构主要由晶粒尺寸、晶体形状、相的数量和组成、氧化物、夹杂物和缺陷等因素决定。
通常,细小均匀的晶粒、紧密无缺陷的结晶和良好的晶界结合能够提高金属材料的耐磨性。
3.硬度金属材料硬度高的话,摩擦面之间的接触压力也会增加,这样对于磨损接触面的微观垫层和垫层上形成的氧化物、夹杂物的剪切和破裂所需的引致力也会增加。
所以,金属材料的硬度越高耐磨性能越好。
4.表面粗糙度金属材料的表面粗糙度也对其耐磨性能有影响。
通常,表面粗糙度越小,表面的揉合层和磨损层也会越小,摩擦阻力也会减小,从而提高了金属材料的耐磨性。
二、疲劳性能分析一般情况下,金属材料的机械件在使用过程中都会遭到交替载荷的作用,这些载荷也就是往复拉伸和压缩的力,造成了所谓的“疲劳断裂”。
疲劳性能是指金属材料在长期使用过程中承受交替载荷作用下,能够保持一定的力学性能和寿命的能力。
金属材料的疲劳性能主要取决于材料的组织结构、载荷的频率、幅值和材料的应力水平。
1.金属材料的组织结构金属材料的组织结构对其疲劳性能有很大影响。
疲劳寿命是一种热态性能,组织结构中的组织成分、晶粒大小、晶界等都会对疲劳寿命产生影响。
金属疲劳例子

金属疲劳例子1. 简介金属疲劳是指金属材料在循环加载下发生持续应力和应变积累导致的破坏现象。
一般来说,金属材料在受到外力作用下都会发生弹性变形,不过当外力反复作用时,即使远远小于金属材料的屈服强度也会导致金属疲劳破坏。
金属疲劳是一种常见的失效形式,特别在机械、航空航天等领域中具有重要的研究价值。
本文主要通过几个金属疲劳的例子来介绍金属疲劳现象、影响因素和预防措施。
2. 金属疲劳的例子2.1 飞机起落架飞机起落架是一个经常受到循环加载的金属构件,其中承受的应力特别大。
由于飞机在起飞性能和安全性要求高,所以起落架的安全性尤为关键。
起落架由多个金属构件组成,例如压铸、锻造等,这些构件经常受到机身的振动和冲击。
金属疲劳在飞机起落架中是一个重要的失效形式。
在某次事故调查中发现,飞机起落架由于长时间的飞行和着陆循环,金属疲劳最终导致了起落架断裂的事故。
为了预防金属疲劳导致的起落架断裂,飞机制造商采用了多种措施。
首先是科学设计,根据飞机的使用情况和受力分析,合理计算起落架的寿命。
其次是周期性的检查和维护,通过定期的检查和维护可以发现金属疲劳的迹象并及时修复或更换受损部分。
另外,飞机制造商还使用了一些技术手段,例如表面处理、改善金属的疲劳性能等。
2.2 汽车曲轴汽车曲轴是发动机中的关键部件之一,也是一个经受循环加载的金属构件。
曲轴通过连杆与活塞相连,将活塞的上下往复运动转化为发动机的旋转运动。
由于发动机运转时,曲轴需要不断承受爆燃冲击力和离心力等循环载荷,使得曲轴容易发生金属疲劳。
在某次事故调查中发现,汽车曲轴发生疲劳断裂最终导致了引擎故障和车辆失控。
为了提高汽车曲轴的疲劳寿命以及减少金属疲劳导致的断裂,曲轴的设计和制造过程中采取了一系列措施。
首先是材料选择,使用高强度、高韧性的材料来增加曲轴的承载能力和抗疲劳性能。
其次是优化曲轴的结构,通过合理的形状和几何参数的选择,减小应力集中区域,从而降低金属疲劳的风险。
金属的疲劳01
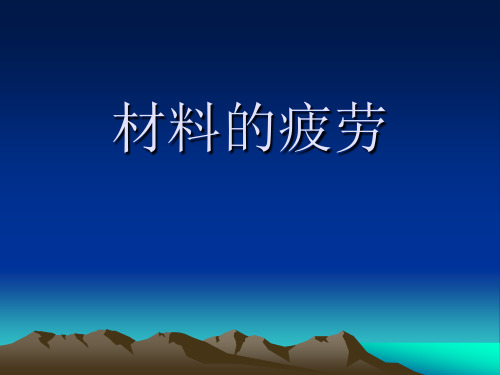
第一章 前言
第二章 疲劳现象
2.1 包辛格(Bauschinger)效
应 在对金属材料做 循环加载试验时发 现,金属材料经过 微量的预变形之后, 如果继续同向加载, 将使其弹性极限升 高,若反向加载将 使其弹性极限降低。
金属在交变应力作用下,其表面出现滑移线或 滑移带,它与静加载的差异在于滑移更不均匀,随 着塑性变形程度的增加,滑移带的数目不甚增加, 但某些带进一步加深、加宽,形成持续滑移带。由 于它具有特殊的位错结构,可以在很低的应力下作 塑性变形,而不产生明显加工硬化,使变形局限在 持续滑移带内进行。随着塑性变形的进一步发展, 持续滑移带内将产生挤出峰勺挤入沟(出现在与表 面相交的滑移带中),再继续加载时,在强烈的滑 移带中沿着凹进的挤入沟将产生显微裂纹,直至最 终发展成为宏观疲劳裂纹。
第三章 疲劳裂纹的萌生
3 . 2 疲劳裂纹萌生的孕育期
第三章 疲劳裂纹的萌生
3 . 2 疲劳裂纹萌生的孕育期
材料的 性能
缺口 尖锐度
孕育期
应力水平
表面 强化效果
第三章 疲劳裂纹的萌生
3 . 3 疲劳裂纹萌生机制
3 . 3 . 1 Wood机制
第三章 疲劳裂纹的萌生
3 . 3 疲劳裂纹萌生机制
3 . 3 . 2 Cottrell和Hull的侵入和挤出模型
第三章 疲劳裂纹的萌生
3 . 3 疲劳裂纹萌生机制
3 . 3 . 3 Zener模型
疲劳裂纹 在晶界萌生
相邻两晶粒为大角度晶界
其中一个晶粒处于 滑移变形的有利方位
变应力反复作用
金属材料的疲劳性能
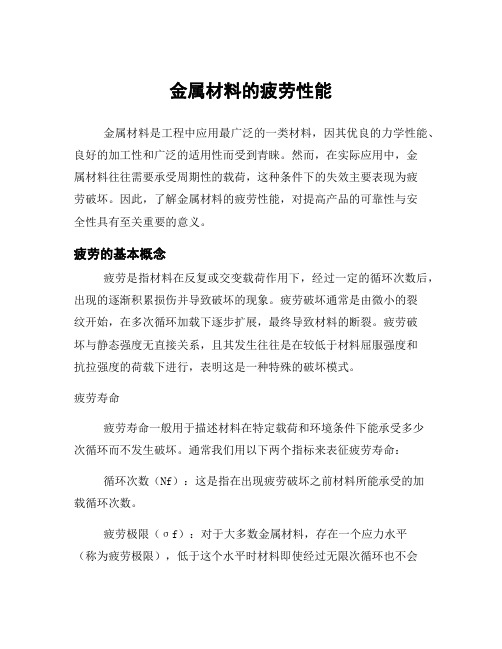
金属材料的疲劳性能金属材料是工程中应用最广泛的一类材料,因其优良的力学性能、良好的加工性和广泛的适用性而受到青睐。
然而,在实际应用中,金属材料往往需要承受周期性的载荷,这种条件下的失效主要表现为疲劳破坏。
因此,了解金属材料的疲劳性能,对提高产品的可靠性与安全性具有至关重要的意义。
疲劳的基本概念疲劳是指材料在反复或交变载荷作用下,经过一定的循环次数后,出现的逐渐积累损伤并导致破坏的现象。
疲劳破坏通常是由微小的裂纹开始,在多次循环加载下逐步扩展,最终导致材料的断裂。
疲劳破坏与静态强度无直接关系,且其发生往往是在较低于材料屈服强度和抗拉强度的荷载下进行,表明这是一种特殊的破坏模式。
疲劳寿命疲劳寿命一般用于描述材料在特定载荷和环境条件下能承受多少次循环而不发生破坏。
通常我们用以下两个指标来表征疲劳寿命:循环次数(Nf):这是指在出现疲劳破坏之前材料所能承受的加载循环次数。
疲劳极限(σf):对于大多数金属材料,存在一个应力水平(称为疲劳极限),低于这个水平时材料即使经过无限次循环也不会发生疲劳破坏。
值得注意的是,并非所有金属都具有明显的疲劳极限,如铝合金等常见金属,其 fatigue limit 不易确定。
疲劳性能影响因素影响金属材料疲劳性能的因素包括但不限于以下几个方面:材料成分金属材料中的化学成分对其疲劳性能有明显影响。
例如,合金元素如镍、钼、铬等可以显著提高钢材的抗疲劳性能。
适当增加合金元素的比例,使得金属晶体结构更加稳定,从而提高了其疲劳强度。
此外,非金属杂质(如硫、磷等)的存在,则会降低材料的疲劳性能。
材料组织材料的微观组织结构直接决定了其机械性能。
在热处理过程中,通过控制冷却速度和温度,可以改变金属材料的相组成与晶粒尺寸,从而优化组织,提高疲劳性能。
例如,细化晶粒可以显著提高金属件的抗疲劳能力。
调质处理后的钢材,相较于退火状态下,会表现出更高的抗疲劳能力。
应力集中在实际使用中,构件往往因为几何形状的不均匀性(如凹坑、切口、焊缝等)而产生应力集中现象。
疲劳断裂的特征分类及基础知识

No.1疲劳与断裂的概念1.疲劳:金属材料在应力或应变的反复作用下发生的性能变化称为疲劳。
2.疲劳断裂:材料承受交变循环应力或应变时,引起的局部结构变化和内部缺陷的不断地发展,使材料的力学性能下降,最终导致产品或材料的完全断裂,这个过程称为疲劳断裂,也可简称为金属的疲劳。
引起疲劳断裂的应力一般很低,疲劳断裂的发生,往往具有突发性、高度局部性及对各种缺陷的敏感性等特点。
No.2疲劳断裂的分类1.高周疲劳与低周疲劳如果作用在零件或构件的应力水平较低,破坏的循环次数高于10万次的疲劳,称为高周疲劳。
例如弹簧、传动轴、紧固件等类产品一般以高周疲劳见多。
作用在零件构件的应力水平较高,破坏的循环次数较低,一般低于1万次的疲劳,称为低周疲劳。
例如压力容器,汽轮机零件的疲劳损坏属于低周疲劳。
2.应力和应变分析应变疲劳——高应力,循环次数较低,称为低周疲劳;应力疲劳——低应力,循环次数较高,称为高周疲劳。
复合疲劳,但在实际中,往往很难区分应力与应变类型,一般情况下二种类型兼而有之,这样称为复合疲劳。
3.按照载荷类型分类弯曲疲劳、扭转疲劳、拉压疲劳、接触疲劳、振动疲劳、微动疲劳。
No.3疲劳断裂的特征宏观:裂纹源→扩展区→瞬断区。
裂纹源:表面有凹槽、缺陷,或者应力集中的区域是产生裂纹源的前提条件。
疲劳扩展区:断面较平坦,疲劳扩展与应力方向相垂直,产生明显疲劳弧线,又称为海滩纹或贝纹线。
瞬断区:是疲劳裂纹迅速扩展到瞬间断裂的区域,断口有金属滑移痕迹,有些产品瞬断区有放射性条纹并具有剪切唇区。
微观:疲劳断裂典型的特征是出现疲劳辉纹。
一些微观试样中还会出现解理与准解理现象(晶体学上的名称,在微观显象上出现的小平面),以及韧窝等微观区域特征。
No.4疲劳断裂的特点(1)断裂时没有明显的宏观塑性变形,断裂前没有明显的预兆,往往是突然性的产生,使机械零件产生的破坏或断裂的现象,危害十分严重。
(2)引起疲劳断裂的应力很低,往往低于静载时屈服强度的应力负荷。
什么是金属疲劳?
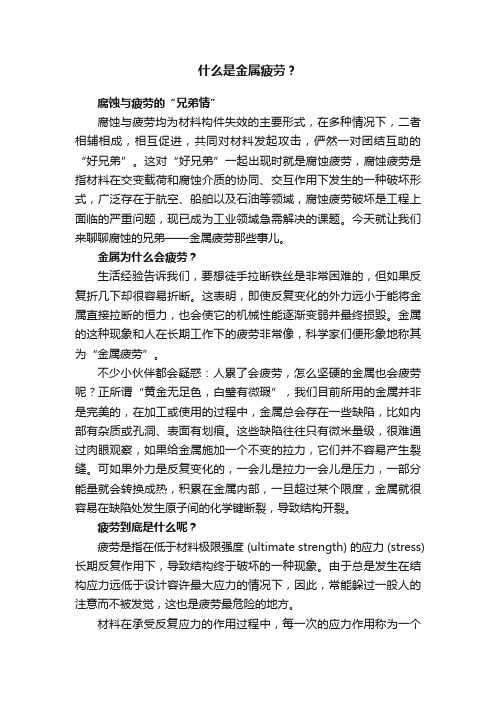
什么是金属疲劳?腐蚀与疲劳的“兄弟情”腐蚀与疲劳均为材料构件失效的主要形式,在多种情况下,二者相辅相成,相互促进,共同对材料发起攻击,俨然一对团结互助的“好兄弟”。
这对“好兄弟”一起出现时就是腐蚀疲劳,腐蚀疲劳是指材料在交变载荷和腐蚀介质的协同、交互作用下发生的一种破坏形式,广泛存在于航空、船舶以及石油等领域,腐蚀疲劳破坏是工程上面临的严重问题,现已成为工业领域急需解决的课题。
今天就让我们来聊聊腐蚀的兄弟——金属疲劳那些事儿。
金属为什么会疲劳?生活经验告诉我们,要想徒手拉断铁丝是非常困难的,但如果反复折几下却很容易折断。
这表明,即使反复变化的外力远小于能将金属直接拉断的恒力,也会使它的机械性能逐渐变弱并最终损毁。
金属的这种现象和人在长期工作下的疲劳非常像,科学家们便形象地称其为“金属疲劳”。
不少小伙伴都会疑惑:人累了会疲劳,怎么坚硬的金属也会疲劳呢?正所谓“黄金无足色,白璧有微瑕”,我们目前所用的金属并非是完美的,在加工或使用的过程中,金属总会存在一些缺陷,比如内部有杂质或孔洞、表面有划痕。
这些缺陷往往只有微米量级,很难通过肉眼观察,如果给金属施加一个不变的拉力,它们并不容易产生裂缝。
可如果外力是反复变化的,一会儿是拉力一会儿是压力,一部分能量就会转换成热,积累在金属内部,一旦超过某个限度,金属就很容易在缺陷处发生原子间的化学键断裂,导致结构开裂。
疲劳到底是什么呢?疲劳是指在低于材料极限强度 (ultimate strength) 的应力 (stress) 长期反复作用下,导致结构终于破坏的一种现象。
由于总是发生在结构应力远低于设计容许最大应力的情况下,因此,常能躲过一般人的注意而不被发觉,这也是疲劳最危险的地方。
材料在承受反复应力的作用过程中,每一次的应力作用称为一个应力周期(cycle),此周期内的材料受力状态,由原本的无应力先到达最大正应力(拉伸应力),然后到达最大负应力(压缩应力),最后回到无应力状态。
金属材料疲劳破坏的机理

一、名词解释1、交变应力:构件中一点应力随着时间变化而变化时,这种应力称为“交变应力”;2、疲劳:在交变应力作用下发生的破坏现象,称为“疲劳失效”或“疲劳破坏”,简称“疲劳”。
疲劳失效与静载作用下的强度失效,有着本质上的差别。
在交变应力作用下,材料的强度性能则不仅与材料有关,而且与应力变化情况、构件的形状和尺寸,以及表面加工质量等因素有着很大关系。
二、疲劳破坏特点1、破坏应力值远低于材料在静载下的强度指标。
2、构件在确定的应力水平下发生疲劳破坏需要一个过程,即需要一定量的应力交变次数。
3、构件在破坏前和破坏时都没有明显的塑性变形,即使在静载下塑性很的材料,也特呈现脆性断裂。
4、同一疲劳破坏断口,一般都明显的两个区域:光滑区域和颗粒区域。
三、疲劳破坏原因以多晶体金属为例,它由很多强弱不等的晶粒所组成,在晶粒边界上或夹杂物处,强度更弱。
在外力作用下,受力较大或强度较弱的晶粒以及晶粒边界上将出现错动的滑移带。
随着应力变化次数的增加,滑移加剧,滑移带变宽,最后沿滑移带裂开,形成裂纹。
这些最初形成的微裂大都是疲劳破坏的发源区,称为“疲劳源”。
再经过若干次应力交变之后,宏观裂纹继续扩展,致使构件截面削弱,类似在构件上作成尖锐的“切口”。
结果,在很低的名义应力(不考虑应力集中时算得的应力),水平下,构件便发生破坏。
裂纹的生成和扩展是一个复杂的过程,它与构件的外形、尺寸、应力交变的类型,以及构件所处的介质等因素有很大关系。
1、应力集中对疲劳极限的影响在构件上截面突变处,如阶梯轴的过渡段、开孔、切槽等处,会产生应力集中现象,即在这些局部区域内,应力有可能达到很高数值。
2、构件尺寸对疲劳极限的影响构件尺寸对疲劳极限有着明显的影响,这是疲劳强度问题与静载强度问题的重要差别之一。
实验结果表明,当构件横截面上的应力非均匀颁布时,构件尺寸越大,疲劳极限越低。
3、构件表面加工质量对疲劳极限的影响粗糙的机械加工,会在构件表面形成深浅不同的刻痕,这些刻痕本身就是初始裂纹。
金属疲劳极限
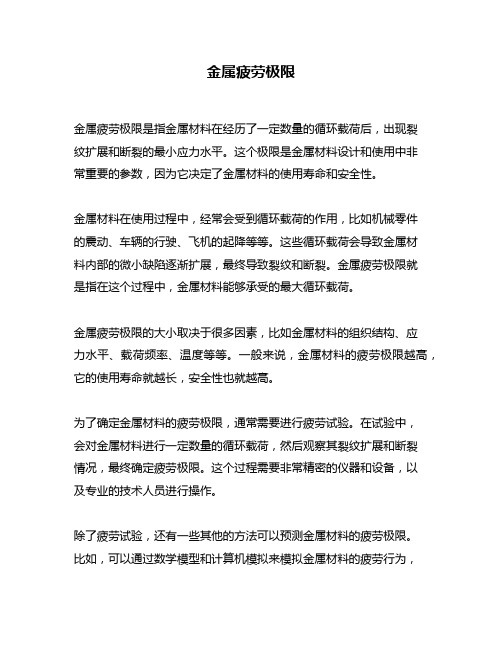
金属疲劳极限
金属疲劳极限是指金属材料在经历了一定数量的循环载荷后,出现裂
纹扩展和断裂的最小应力水平。
这个极限是金属材料设计和使用中非
常重要的参数,因为它决定了金属材料的使用寿命和安全性。
金属材料在使用过程中,经常会受到循环载荷的作用,比如机械零件
的震动、车辆的行驶、飞机的起降等等。
这些循环载荷会导致金属材
料内部的微小缺陷逐渐扩展,最终导致裂纹和断裂。
金属疲劳极限就
是指在这个过程中,金属材料能够承受的最大循环载荷。
金属疲劳极限的大小取决于很多因素,比如金属材料的组织结构、应
力水平、载荷频率、温度等等。
一般来说,金属材料的疲劳极限越高,它的使用寿命就越长,安全性也就越高。
为了确定金属材料的疲劳极限,通常需要进行疲劳试验。
在试验中,
会对金属材料进行一定数量的循环载荷,然后观察其裂纹扩展和断裂
情况,最终确定疲劳极限。
这个过程需要非常精密的仪器和设备,以
及专业的技术人员进行操作。
除了疲劳试验,还有一些其他的方法可以预测金属材料的疲劳极限。
比如,可以通过数学模型和计算机模拟来模拟金属材料的疲劳行为,
从而预测其疲劳极限。
这种方法可以大大节省时间和成本,同时也可以提高预测的准确性。
总之,金属疲劳极限是金属材料设计和使用中非常重要的参数,它决定了金属材料的使用寿命和安全性。
为了确定金属材料的疲劳极限,需要进行疲劳试验或者使用其他预测方法。
在实际应用中,需要根据具体情况来选择合适的金属材料和设计方案,以确保其安全可靠。
79. 如何评估金属材料的疲劳强度?

79. 如何评估金属材料的疲劳强度?79、如何评估金属材料的疲劳强度?在现代工业领域,金属材料的应用极为广泛。
无论是航空航天、汽车制造,还是机械工程等领域,金属材料的性能都直接影响着产品的质量和可靠性。
而疲劳强度作为评估金属材料性能的关键指标之一,其准确评估对于保障产品的安全运行和使用寿命具有至关重要的意义。
那么,究竟什么是金属材料的疲劳强度呢?简单来说,疲劳强度是指金属材料在循环应力或应变作用下,经过一定次数的循环后发生疲劳破坏的最大应力值。
疲劳破坏与常见的静态破坏不同,它往往在应力远低于材料的屈服强度时就可能发生,而且通常没有明显的塑性变形,具有很大的隐蔽性和危险性。
要评估金属材料的疲劳强度,首先需要了解影响其疲劳强度的因素。
材料的化学成分、组织结构、表面状态、加工工艺等都会对疲劳强度产生影响。
例如,合金元素的添加可以改善材料的性能,细化晶粒能够提高疲劳强度;材料表面的粗糙度、残余应力以及存在的缺陷也会显著降低疲劳强度。
此外,加载方式、应力幅、平均应力、加载频率和环境条件等外部因素同样不容忽视。
在实际评估中,常用的方法之一是疲劳试验。
疲劳试验通常包括旋转弯曲疲劳试验、拉压疲劳试验、扭转疲劳试验等。
以旋转弯曲疲劳试验为例,将金属试样安装在旋转弯曲试验机上,使其承受旋转弯曲应力,通过不断增加应力水平,直到试样发生疲劳破坏,记录下此时的应力循环次数和应力值,从而得到材料的疲劳强度。
在进行疲劳试验时,试样的制备和安装至关重要。
试样的形状、尺寸和表面质量应符合相关标准,以确保试验结果的准确性和可比性。
同时,试验设备的精度和稳定性也会对结果产生影响,因此需要定期对设备进行校准和维护。
除了疲劳试验,还可以通过理论分析的方法来评估金属材料的疲劳强度。
常见的理论模型有应力寿命模型(SN 曲线)、应变寿命模型(εN 曲线)等。
这些模型基于材料的力学性能和疲劳损伤机理,通过数学公式来描述疲劳寿命与应力或应变之间的关系。
- 1、下载文档前请自行甄别文档内容的完整性,平台不提供额外的编辑、内容补充、找答案等附加服务。
- 2、"仅部分预览"的文档,不可在线预览部分如存在完整性等问题,可反馈申请退款(可完整预览的文档不适用该条件!)。
- 3、如文档侵犯您的权益,请联系客服反馈,我们会尽快为您处理(人工客服工作时间:9:00-18:30)。
金属材料疲劳概念金属疲劳(Metal Fatigue):许多机械零件,如轴、齿轮、轴承、叶片、弹簧等,在工作过程中各点的应力随时间作周期性的变化,这种随时间作周期性变化的应力称为交变应力(也称循环应力)。
在交变应力的作用下,虽然零件所承受的应力低于材料的屈服点,但经过较长时间的工作后产生裂纹或突然发生完全断裂的现象称为金属的疲劳。
在循环加载下,发生在材料某点处局部的、永久性的损伤递增过程。
经足够的应力或应变循环后,损伤累积可使材料产生裂纹(图1),或使裂纹进一步扩展至完全断裂(图2)。
出现可见裂纹或者完全断裂都叫疲劳破坏。
美国材料试验协会(American Society for Testing Materials, ASTM)将疲劳定义为:“材料某一点或某一些点在承受交变应力和应变条件下,使材料产生局部的永久性的逐步发展的结构性变化过程。
在足夠多的交变次数后,它可能造成裂纹的累积或材料完全断裂”。
法国的J.-V.彭赛列于1839年首先论述了疲劳问题并提出“疲劳”这一术语。
但疲劳研究的奠基人则是德国的A.沃勒。
他在19世纪50~60年代首先得到表征疲劳性能的S-N曲线,并提出疲劳极限的概念。
疲劳研究虽有百余年历史,文献极多,但理论不够完善。
近年来,断裂力学的进展,丰富了传统疲劳理论的内容,促进了疲劳理论的发展。
当前的发展趋势是把微观理论和宏观理论结合起来从本质上探究疲劳破坏的机理。
为什么金属疲劳时会产生破坏作用呢?这是因为金属内部结构并不均匀,从而造成应力传递的不平衡,有的地方会成为应力集中区。
与此同时,金属内部的缺陷处还存在许多微小的裂纹。
在力的持续作用下,裂纹会越来越大,材料中能够传递应力部分越来越少,直至剩余部分不能继续传递负载时,金属构件就会全部毁坏。
早在100多年以前,人们就发现了金属疲劳给各个方面带来的损害。
但由于技术的落后,还不能查明疲劳破坏的原因。
直到显微镜和电子显微镜相继出现之后,使人类在揭开金属疲劳秘密的道路上不断取得新的成果,并且有了巧妙的办法来对付这个大敌。
疲劳特征:疲劳破坏是一种损伤积累的过程,因此它的力学特征不同于静力破坏。
不同之处主要表现为:①在循环应力远小于静强度极限(见材料的力学性能的情况下破坏就可能发生,但不是立刻发生的,而要经历一段时间,甚至很长的时间;②疲劳破坏前,即使塑性材料(延性材料)有时也没有显著的残余变形。
金属疲劳破坏可分为三个阶段:①微观裂纹扩展阶段。
在循环加载下,由于物体内部微观组织结构的不均匀性,某些薄弱部位首先形成微观裂纹,此后,裂纹即沿着与主应力约成45°角的最大剪应力方向扩展。
在此阶段,裂纹长度大致在0.05毫米以内。
若继续加载,微观裂纹就会发展成为宏观裂纹。
②宏观裂纹扩展阶段。
裂纹基本上沿着与主应力垂直的方向扩展。
借助电子显微镜可在断口表面上观察到此阶段中每一应力循环所遗留的疲劳条带。
③瞬时断裂阶段。
当裂纹扩大到使物体残存截面不足以抵抗外载荷时,物体就会在某一次加载下突然断裂。
在疲劳宏观断口上往往有两个区域:光滑区域和颗粒状区域。
疲劳裂纹的起始点称作疲劳源。
实际构件上的疲劳源总是出现在应力集中区,裂纹从疲劳源向四周扩展。
由于反复变形,裂纹的两个表面时而分离,时而挤压,这样就形成了光滑区域,即疲劳裂纹第二阶段扩展区域。
第三阶段的瞬时断裂区域表面呈现较粗糙的颗粒状。
如果循环应力的变化不是稳态的,应力幅不保持恒定,裂纹扩展忽快、忽慢或者停顿,则在光滑区域上用肉眼可看到贝壳状或海滩状纹迹的疲劳弧线(图3)。
循环应力:疲劳破坏是在循环应力或循环应变作用下发生的。
为了便于研究和分析疲劳问题,国际上对循环应力表示法已作出统一规定。
循环应力的每一个周期变化称作一个应力循环。
图4所示的恒幅循环应力由以下诸分量表示:①最大应力σmax,应力循环中最大代数值的应力,以拉应力为正,压应力为负。
②最小应力σmin,应力循环中最小代数值的应力,以拉应力为正,压应力为负。
③平均应力σm,最大应力和最小应力的代数平均值,即σm=(σmax+σmin)/2。
④应力幅σa,最大应力和最小应力的代数差的一半,即σa=(σmax-σmin)/2。
有些国家的文献将σa称作交变应力,但在中国常用交变应力一词表示循环应力。
⑤应力变程Δσ,又称应力范围,是最大应力与最小应力之差,即应力幅的两倍。
⑥应力比R,又称循环特征,是最小应力与最大应力的代数比值,即R=σmin/σmax。
R =-1的应力循环称为对称循环,其最大应力和最小应力绝对值相等,符号相反,且平均应力为零;R=0的应力循环称为脉动循环,其最小应力为零;R等于其他值的应力循环称为非对称循环。
恒幅循环应变的表示法与此类似。
应力循环可以看成两部分应力的组合,一部分是数值等于平均应力σa的静应力,另一部分是在平均应力上变化的动应力σa。
在四个应力分量σmax、σmin、σm、σa中只有两个是独立的。
任意给定两个,其余两个就能确定。
用来确定应力循环的一对应力分量σmax、σmin或σa、σm称为应力水平。
对恒幅循环应力,当给定R或σm时,应力水平可由σmax或σa表示。
产生疲劳破坏所需的循环数取决于应力水平的高低,破坏循环数越大,表示施加的应力水平越低。
疲劳寿命:在循环加载下,产生疲劳破坏所需的应力或应变循环数称为疲劳寿命。
对实际构件,疲劳寿命常以工作小时计。
构件在出现工程裂纹以前的疲劳寿命称为裂纹形成寿命或裂纹起始寿命。
工程裂纹指宏观可见的或可检的裂纹,其长度无统一规定,一般在0.2~1.0毫米范围内。
自工程裂纹扩展至完全断裂的疲劳寿命称为裂纹扩展寿命。
总寿命是二者之和。
因为工程裂纹长度远大于金属晶粒尺寸,故可将裂纹作为物体边界,并将其周围材料视作均匀的连续介质,应用断裂力学方法研究裂纹扩展规律。
为了便于分析研究,常常按破坏循环次数的高低将疲劳分为两类:①高循环疲劳(高周疲劳):破坏循环次数高于104~105的疲劳,一般振动元件、传动轴等的疲劳属此类。
其特点是:作用于构件上的应力水平较低,应力和应变呈线性关系。
②低循环疲劳(低周疲劳):破坏循环次数低于104~105的疲劳,典型实例有压力容器、燃气轮机构件等的疲劳。
其特点是:作用于构件的应力水平较高,材料处于塑性状态。
很多实际构件在变幅循环应力作用下的疲劳既不是纯高循环疲劳也不是纯低循环疲劳,而是二者的综合。
相应地,裂纹扩展也分为高循环和低循环两类。
高循环疲劳裂纹扩展规律可利用线弹性断裂力学方法研究;低循环疲劳裂纹扩展规律一般应采用弹塑性断裂力学方法研究,不过由于问题十分复杂,尚未很好地解决。
安全寿命:实践表明,疲劳寿命分散性较大,高循环疲劳尤其如此,因此必须进行统计分析,考虑存活(概)率(即可靠度)的问题。
具有存活率p(如95%、99%、99.9%)的疲劳寿命N p的含义是:总体(母体)中有p的个体的疲劳寿命大于N p。
而破坏(概)率等于(1-p)。
对应于高存活率或低破坏率的疲劳寿命,在设计上称为安全寿命。
疲劳问题范畴极为广泛。
按材料性质及其工作环境划分,除一般金属疲劳外,还包括有非金属疲劳、高温疲劳、热疲劳(由循环热应力引起)、腐蚀疲劳、擦伤疲劳、声疲劳(由噪声激励引起)、冲击疲劳、接触疲劳等。
金属疲劳寿命预估侧重于力学方面,并且是普遍关注的研究课题。
为了进行疲劳寿命的理论估算和试验,首先必须了解材料的疲劳性能,以此作为理论计算的依据。
其次,疲劳寿命的长短取决于所承受的循环载荷大小,为此还必须编制出供理论分析和全尺寸疲劳试验用的载荷谱。
最后,根据材料的疲劳性能和载荷谱估算出疲劳寿命。
以下分别加以介绍:疲劳性能:材料抵抗疲劳破坏的能力。
高循环疲劳的裂纹形成阶段的疲劳性能常以S-N曲线表征,S为应力水平,N为疲劳寿命。
S-N曲线需通过试验测定,试验采用小型标准试件或实际构件。
若采用小型标准试件,则试件裂纹扩展寿命较短,常以断裂时循环次数作为裂纹形成寿命。
试验在给定应力比R或平均应力σm的前提下进行,根据不同应力水平的试验结果,以最大应力σmax或应力幅σa为纵坐标,疲劳寿命N为横坐标绘制S-N曲线(图5)。
表示寿命的横坐标采用对数标尺;表示应力的纵坐标采用算术标尺或对数标尺。
在S-N 曲线上,对应某一寿命值的最大应力σmax或应力幅σa称为疲劳强度。
疲劳强度一词也泛指与疲劳有关的强度问题。
为了模拟实际构件缺口处的应力集中以及研究材料对应力集中的敏感性,常需测定不同应力集中系数下的S-N曲线。
对试验结果进行统计分析后,根据某一存活率p的安全寿命所绘制的应力和安全寿命之间的关系曲线称为p-S-N曲线。
50%存活率的应力和疲劳寿命之间的关系曲线称为中值S-N曲线,也简称S-N曲线。
当循环应力中的最大应力σmax小于某一极限值时,试件可经受无限次应力循环而不产生疲劳裂纹;当σmax大于该极限值时,试件经有限次应力循环就会产生疲劳裂纹,该极限应力值就称为疲劳极限,或持久极限。
如图5中S-N曲线的水平线段对应的纵坐标就是疲劳极限。
鉴于疲劳极限存在较大的分散性,人们根据现代统计学观点,把疲劳极限定义为:指定循环基数下的中值(50%存活率)疲劳强度。
对于S-N曲线具有水平线段的材料,循环基数取107;对于S-N曲线无水平线段的材料(如铝合金),循环基数取107~108。
疲劳极限可作为绘制S-N曲线长寿命区线段的数据点。