热等静压(hip)技术在硬质合金及陶瓷材料中的应用
陶瓷粉末热等静压模具
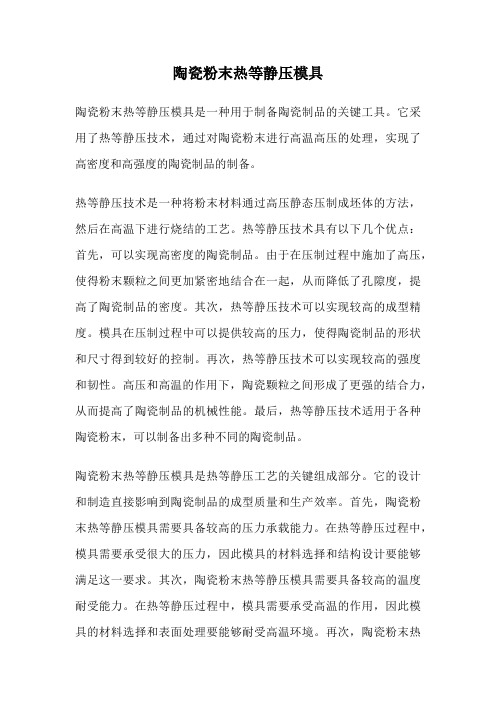
陶瓷粉末热等静压模具陶瓷粉末热等静压模具是一种用于制备陶瓷制品的关键工具。
它采用了热等静压技术,通过对陶瓷粉末进行高温高压的处理,实现了高密度和高强度的陶瓷制品的制备。
热等静压技术是一种将粉末材料通过高压静态压制成坯体的方法,然后在高温下进行烧结的工艺。
热等静压技术具有以下几个优点:首先,可以实现高密度的陶瓷制品。
由于在压制过程中施加了高压,使得粉末颗粒之间更加紧密地结合在一起,从而降低了孔隙度,提高了陶瓷制品的密度。
其次,热等静压技术可以实现较高的成型精度。
模具在压制过程中可以提供较高的压力,使得陶瓷制品的形状和尺寸得到较好的控制。
再次,热等静压技术可以实现较高的强度和韧性。
高压和高温的作用下,陶瓷颗粒之间形成了更强的结合力,从而提高了陶瓷制品的机械性能。
最后,热等静压技术适用于各种陶瓷粉末,可以制备出多种不同的陶瓷制品。
陶瓷粉末热等静压模具是热等静压工艺的关键组成部分。
它的设计和制造直接影响到陶瓷制品的成型质量和生产效率。
首先,陶瓷粉末热等静压模具需要具备较高的压力承载能力。
在热等静压过程中,模具需要承受很大的压力,因此模具的材料选择和结构设计要能够满足这一要求。
其次,陶瓷粉末热等静压模具需要具备较高的温度耐受能力。
在热等静压过程中,模具需要承受高温的作用,因此模具的材料选择和表面处理要能够耐受高温环境。
再次,陶瓷粉末热等静压模具需要具备较好的精度和稳定性。
模具的形状和尺寸要能够满足陶瓷制品的要求,并且在使用过程中要保持稳定的性能。
最后,陶瓷粉末热等静压模具还需要具备较好的耐磨性和寿命。
由于热等静压过程中存在较大的摩擦和磨损,模具的材料选择和表面处理要能够提高其耐磨性和使用寿命。
陶瓷粉末热等静压模具是实现高密度和高强度陶瓷制品制备的重要工具。
通过热等静压技术,可以实现陶瓷制品的高密度、高精度和高性能。
陶瓷粉末热等静压模具的设计和制造对于陶瓷制品的成型质量和生产效率具有重要的影响。
因此,在实际应用中,需要根据具体的工艺要求和陶瓷制品的特点,合理选择和设计陶瓷粉末热等静压模具,以实现最佳的成型效果。
hip在碳化硅烧结中的应用
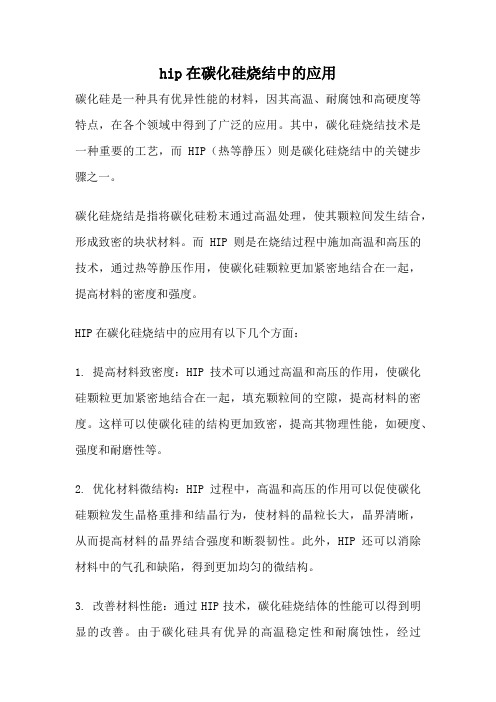
hip在碳化硅烧结中的应用碳化硅是一种具有优异性能的材料,因其高温、耐腐蚀和高硬度等特点,在各个领域中得到了广泛的应用。
其中,碳化硅烧结技术是一种重要的工艺,而HIP(热等静压)则是碳化硅烧结中的关键步骤之一。
碳化硅烧结是指将碳化硅粉末通过高温处理,使其颗粒间发生结合,形成致密的块状材料。
而HIP则是在烧结过程中施加高温和高压的技术,通过热等静压作用,使碳化硅颗粒更加紧密地结合在一起,提高材料的密度和强度。
HIP在碳化硅烧结中的应用有以下几个方面:1. 提高材料致密度:HIP技术可以通过高温和高压的作用,使碳化硅颗粒更加紧密地结合在一起,填充颗粒间的空隙,提高材料的密度。
这样可以使碳化硅的结构更加致密,提高其物理性能,如硬度、强度和耐磨性等。
2. 优化材料微结构:HIP过程中,高温和高压的作用可以促使碳化硅颗粒发生晶格重排和结晶行为,使材料的晶粒长大,晶界清晰,从而提高材料的晶界结合强度和断裂韧性。
此外,HIP还可以消除材料中的气孔和缺陷,得到更加均匀的微结构。
3. 改善材料性能:通过HIP技术,碳化硅烧结体的性能可以得到明显的改善。
由于碳化硅具有优异的高温稳定性和耐腐蚀性,经过HIP处理后的碳化硅材料可以在高温和腐蚀环境下表现出更好的性能,如高温机械性能、耐磨性和耐腐蚀性等。
4. 扩大应用范围:碳化硅材料经过HIP处理后,其性能得到了明显的提升,从而使其在各个领域中的应用范围得到了扩大。
例如,在航空航天、汽车制造、冶金和化工等领域,HIP处理后的碳化硅材料可以用于制造高温结构件、耐磨零部件和耐腐蚀设备等。
HIP在碳化硅烧结中的应用极为重要。
通过HIP技术,可以提高碳化硅材料的致密度、优化材料微结构、改善材料性能并扩大其应用范围。
这为碳化硅材料的发展和应用提供了有力的支撑,也为相关行业的发展带来了广阔的前景。
热等静压技术在金属陶瓷复合材料制备中的应用
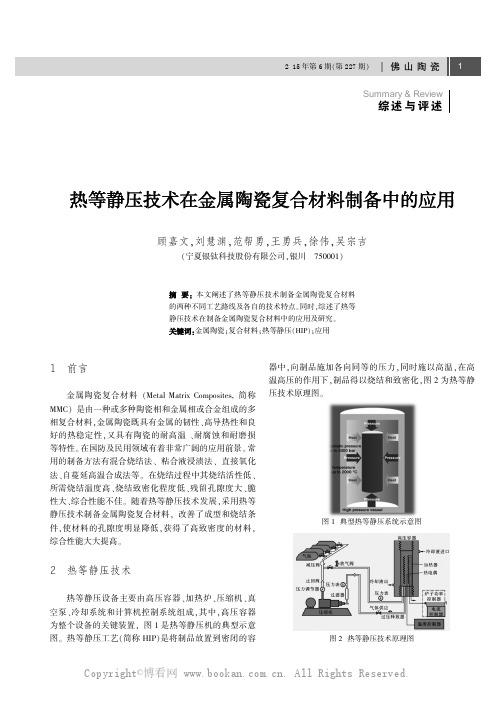
图 2 热等静压技术原理图
Copyright©博看网 . All Rights Reserved.
2 FOSHAN CERAMICS Vol.25 No.6 渊Serial No.227冤
3 制备金属陶瓷复合材料的热等静压工艺
热等静压技术在金属陶瓷复合材料制备中有两种不 同工艺路线袁一种为直接热等静压烧结工艺曰另一种是热 等静压后续致密化工艺遥
热等静压后续致密化制备金属陶瓷复合材料的工艺 路线如图 4 所示遥
粉末制备 寅 压制成型 寅 普通烧结 寅
热等静压后续致密化 寅 后处理 寅 产品 图 4 热等静压后续致密化制备金属陶瓷复合材料的工艺路线
热等静压后续致密化工艺的技术关键如下院 渊1冤 待处理的烧结体基本不含开口气孔袁烧结密度须 达到理论密度的 92%~98%遥 否则仍需选择合适的包套材 料对烧结体进行包封遥 渊2冤 温度的选择原则上为金属基体熔点或合金基体 固溶线绝对温度值的 0.6耀0.9遥 渊3冤 压力选择既能使材料产生塑性流动袁又能保证颗 粒不被压碎遥 渊4冤 保温保压时间选择应使坯体内的蠕变充分进行袁 又不至于造成晶粒长大等不利现象出现袁一般选择 1耀2 h遥 热等静压后续致密化工艺可以减少乃至消除烧结体 中的剩余气孔和缺陷袁愈合内部微裂纹袁从而提高金属陶 瓷复合材料的密度尧强度遥
渊2冤 包套内粉末的振实密度大小直接影响烧结制品 质量袁振实密度低将导致包套收缩量大袁尺寸控制困难袁 且包套易发生破裂遥
渊3冤 粉体均匀性以及金属相尧陶瓷相配比也是影响烧 结制品性能的主要因素遥 由于陶瓷相与金属相的自身不 同特性决定了其在热等静压过程中的变形不同袁因此袁要 想保证得到足够致密的制品袁 必须首先保证陶瓷相与金 属相分布均匀袁 从而使金属相的变形能够完全填充陶瓷 颗粒间的间隙遥
热等静压(HIP)技术在超硬工具制造中的应用
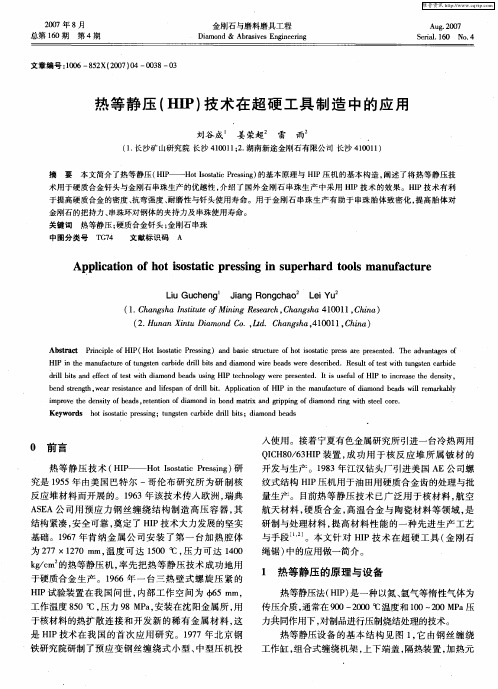
0 前 言
热等 静 压 技 术 ( I— — H tI s t rsn ) HP 0 s ti Pes g 研 o ac i
究是 15 9 5年 由美 国 巴特 尔 一哥伦 布研 究 所 为 研 制 核
入使 用 。接 着 宁夏有 色金属研 究所 引进一 台冷 热两 用 QC 8/ 3 I IH 0 6 HP装置 , 功 用 于 核 反 应 堆 所 属 铍 材 的 成
摘
要
本文简介 了热等静压 ( I—— H tss  ̄ rsig 的基本原理与 H P压机 的基 本构造 , HP o I ti Pes ) o ac n I 阐述了将热等静压技
术用于硬质合金钎头与金 刚石 串珠生产 的优越性 , 绍 了国外金刚石 串珠生产 中采用 H P技 术 的效果 。HP技术有 利 介 I I
Ab t c P n il o I ( o Iot i P es g n ai s u tr o h t ss t rs aep ee t .T ea v na e o sr t r c e f P H t ss t rsi )a d b c t c e f o i t i pes r rsn d h d a t s f a i p H ac n s r u o ac e g
( . h n saIs tt o nn e ac , h nsa4 0 1 , hn ) 1 C ag h ntue fMii Rs r C a gh 10 1 C ia i g e h ( . u nXnuDi o d C . Ld h n sa 4 0 1 , hn ) 2 H n it a n o ,t.C a gh ,10 1 C i a m a
热等静压烧结技术在材料科学与工程专业实验教学中的研究和应用
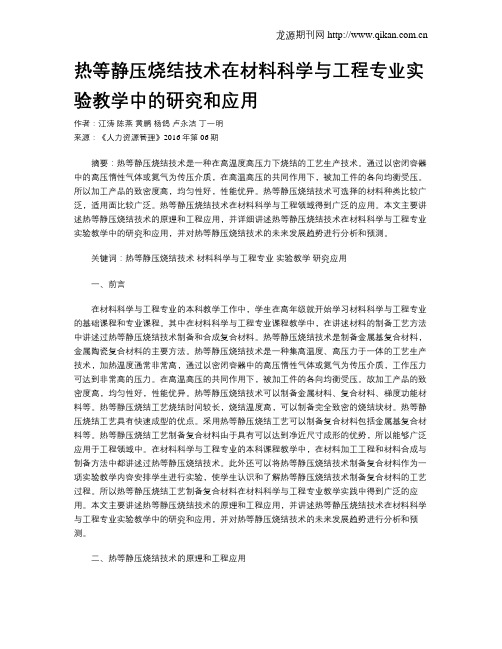
热等静压烧结技术在材料科学与工程专业实验教学中的研究和应用作者:江涛陈燕黄鹏杨鸽卢永洁丁一明来源:《人力资源管理》2016年第06期摘要:热等静压烧结技术是一种在高温度高压力下烧结的工艺生产技术。
通过以密闭容器中的高压惰性气体或氮气为传压介质,在高温高压的共同作用下,被加工件的各向均衡受压。
所以加工产品的致密度高,均匀性好,性能优异。
热等静压烧结技术可选择的材料种类比较广泛,适用面比较广泛。
热等静压烧结技术在材料科学与工程领域得到广泛的应用。
本文主要讲述热等静压烧结技术的原理和工程应用,并详细讲述热等静压烧结技术在材料科学与工程专业实验教学中的研究和应用,并对热等静压烧结技术的未来发展趋势进行分析和预测。
关键词:热等静压烧结技术材料科学与工程专业实验教学研究应用一、前言在材料科学与工程专业的本科教学工作中,学生在高年级就开始学习材料科学与工程专业的基础课程和专业课程。
其中在材料科学与工程专业课程教学中,在讲述材料的制备工艺方法中讲述过热等静压烧结技术制备和合成复合材料。
热等静压烧结技术是制备金属基复合材料,金属陶瓷复合材料的主要方法。
热等静压烧结技术是一种集高温度、高压力于一体的工艺生产技术,加热温度通常非常高,通过以密闭容器中的高压惰性气体或氮气为传压介质,工作压力可达到非常高的压力。
在高温高压的共同作用下,被加工件的各向均衡受压。
故加工产品的致密度高,均匀性好,性能优异。
热等静压烧结技术可以制备金属材料、复合材料、梯度功能材料等。
热等静压烧结工艺烧结时间较长,烧结温度高,可以制备完全致密的烧结块材。
热等静压烧结工艺具有快速成型的优点。
采用热等静压烧结工艺可以制备复合材料包括金属基复合材料等。
热等静压烧结工艺制备复合材料由于具有可以达到净近尺寸成形的优势,所以能够广泛应用于工程领域中。
在材料科学与工程专业的本科课程教学中,在材料加工工程和材料合成与制备方法中都讲述过热等静压烧结技术。
此外还可以将热等静压烧结技术制备复合材料作为一项实验教学内容安排学生进行实验,使学生认识和了解热等静压烧结技术制备复合材料的工艺过程。
热等静压(HIP)技术在金属材料方面的应用

热等静压(HIP)技术在金属材料方面的应用热等静压(HIP)技术于本世纪50年代中期问世。
经过40多年的发展现已成为世界高性能材料生产不可缺少的一项技术,同时也成为新材料开发中的重要高新技术。
我国HIP技术开发始于70年代。
在近30年的发展中,不仅取得不少可喜的成果,而且这些成果已在许多领域中得到了应用。
HIP′99国际会议在北京召开,无疑为我国从事HIP研制人员提供了不可多得的与国际同行进行直接交流的机会,并将有利于我国HIP技术的发展。
为了使广大读者对本届会议内容有一个概略的了解,本文对当前HIP技术在金属材料方面的应用进行了综合评述,其重点在钛合金、高温合金、铍材和难熔金属的应用方面。
1 HIP技术在钛合金方面的应用在近期的应用中,钛合金铸件经HIP致密化处理后最重要的应用仍然在商业方面。
这是由于钛合金铸件可以制备大型、异型的净成形产品,因此大幅度降低部件的制造成本。
HIP处理虽然使合金的强度水平略有下降,但它使材料的塑性及疲劳寿命增加,并使其力学性能的分散度下降,从而提高材料使用性能的可靠性。
Ti-6AI-4V合金是钛合金的主要材料,目前最大的钛合金铸件是美国GE公司的GE90发动机风扇结构件,其外径为1500mm。
Pratt & Whitney公司制造的PW4080发动机过渡罩外径已达1800mm。
由于铸件的尺寸大于目前世界上正在运转的HIP机尺寸,故在此件HIP处理前先把它切开分别进行HIP处理,然后再把它焊合。
为此航空发动机厂要求用HIP处理尺寸为2050mm及超过此尺寸的部件。
鉴于制造2050mm HIP设备的制造费用过高,而且这种大件的数量相对较少,故难以实现。
为了提高钛合金铸件性能,波音公司、洛克希德公司及麦当来、道格拉斯公司作了大量的研究工作。
现已表明,钛精密铸件在HIP后再经过适当的热处理可以使其性能达到锻件的水平(包括疲劳性能及塑性)。
马丁/波音F22空中优势战斗机是HIP钛合金应用的典范,其应用的76个部件约占飞机机架重量的45%,材料为经HIP后的钛合金铸件。
热等静压工艺(HotIsostaticPressing,简写为HIP)是将粉末

(1)陶瓷材料的制材料在高温下发生很多不利的发应或变化; (2)能够在减少甚至无烧结添加剂的条件下,制备出微观结构均匀 且几乎不含气孔的致密陶瓷烧结体; (3)可以减少乃至消除烧结体中的剩余气孔,愈合表面裂纹,从而 提高陶瓷材料的密度、强度; (4)能够精确控制产品的尺寸与形状,而不必使用费用高的金刚石 切割加工,理想条件下产品无形状改变。
后HIP工艺流程图
直接HIP工艺流程图
金属和陶瓷的固结金刚石刀具的烧结铸件质量的修复和改善高性能磁性材料及靶材的致密五热等静压1陶瓷材料的致密化可以在比无压烧结或热压烧结低得多的温度下完成可以有效地抑制材料在高温下发生很多不利的发应或变化
五、热等静压
热等静压工艺(Hot Isostatic Pressing,简写为HIP)是将粉 末压坯或装入包套的粉料装入高压容器中,使粉料经受高温和均衡压 力的作用,被烧结成致密件。 其基本原理是:以气体作为压力介质,使材料(粉料、坯体或烧 结体)在加热过程中经受各向均衡的压力,借助高温和高压的共同作 用促进材料的致密化。 目前,热等静压技术的主要应用有:金属和陶瓷的固结,金刚石 刀具的烧结,铸件质量的修复和改善,高性能磁性材料及靶材的致密 化。
hip热等静压
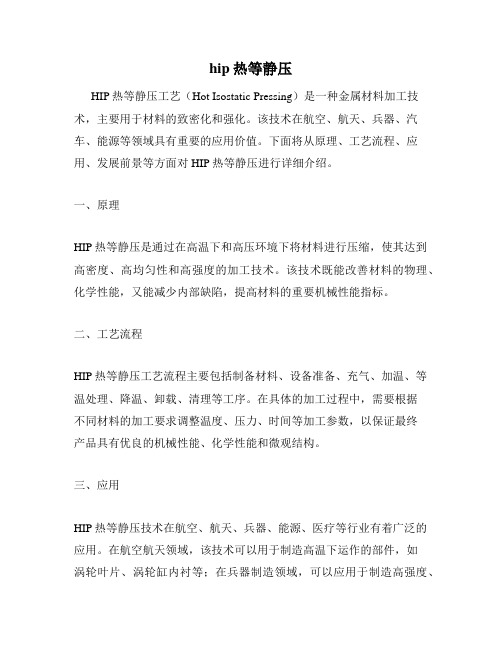
hip热等静压
HIP热等静压工艺(Hot Isostatic Pressing)是一种金属材料加工技术,主要用于材料的致密化和强化。
该技术在航空、航天、兵器、汽车、能源等领域具有重要的应用价值。
下面将从原理、工艺流程、应用、发展前景等方面对HIP热等静压进行详细介绍。
一、原理
HIP热等静压是通过在高温下和高压环境下将材料进行压缩,使其达到高密度、高均匀性和高强度的加工技术。
该技术既能改善材料的物理、化学性能,又能减少内部缺陷,提高材料的重要机械性能指标。
二、工艺流程
HIP热等静压工艺流程主要包括制备材料、设备准备、充气、加温、等温处理、降温、卸载、清理等工序。
在具体的加工过程中,需要根据
不同材料的加工要求调整温度、压力、时间等加工参数,以保证最终
产品具有优良的机械性能、化学性能和微观结构。
三、应用
HIP热等静压技术在航空、航天、兵器、能源、医疗等行业有着广泛的应用。
在航空航天领域,该技术可以用于制造高温下运作的部件,如
涡轮叶片、涡轮缸内衬等;在兵器制造领域,可以应用于制造高强度、
高均匀性的材料,并提高弹头的穿透能力;在能源领域,可以应用于光伏电池、锂离子电池等的制造,以提高其能量密度和循环寿命。
四、发展前景
随着材料科学的不断发展,HIP热等静压技术在材料加工领域将会有更广泛的应用前景。
例如,HIP热等静压技术将可以用于制造高强度的结构材料、高性能的电子材料、大尺寸的功能性陶瓷材料等,推动材料加工技术和材料应用创新,促进工业现代化进程。
综上所述,HIP热等静压工艺是一种重要的材料加工技术,具有广泛的应用前景,为现代工业的发展做出了重要贡献。
热等静压工艺在金属陶瓷制备中的应用-4-7顾嘉文
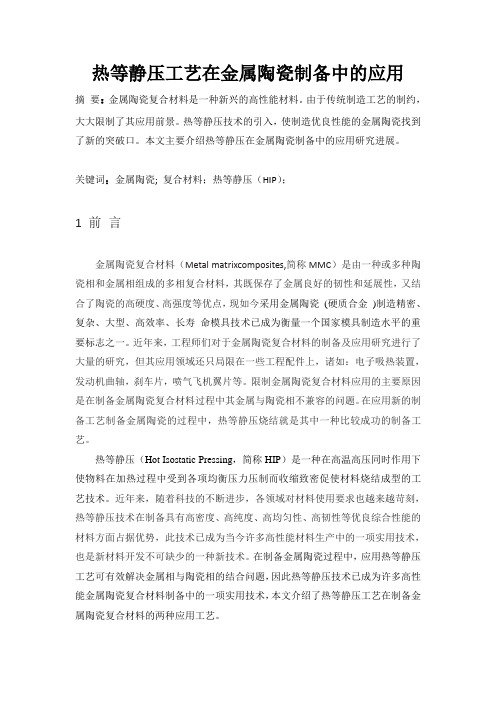
热等静压工艺在金属陶瓷制备中的应用摘要:金属陶瓷复合材料是一种新兴的高性能材料。
由于传统制造工艺的制约,大大限制了其应用前景。
热等静压技术的引入,使制造优良性能的金属陶瓷找到了新的突破口。
本文主要介绍热等静压在金属陶瓷制备中的应用研究进展。
关键词:金属陶瓷; 复合材料;热等静压(HIP);1 前言金属陶瓷复合材料(Metal matrixcomposites,简称MMC)是由一种或多种陶瓷相和金属相组成的多相复合材料,其既保存了金属良好的韧性和延展性,又结合了陶瓷的高硬度、高强度等优点,现如今采用金属陶瓷(硬质合金)制造精密、复杂、大型、高效率、长寿命模具技术已成为衡量一个国家模具制造水平的重要标志之一。
近年来,工程师们对于金属陶瓷复合材料的制备及应用研究进行了大量的研究,但其应用领域还只局限在一些工程配件上,诸如:电子吸热装置,发动机曲轴,刹车片,喷气飞机翼片等。
限制金属陶瓷复合材料应用的主要原因是在制备金属陶瓷复合材料过程中其金属与陶瓷相不兼容的问题。
在应用新的制备工艺制备金属陶瓷的过程中,热等静压烧结就是其中一种比较成功的制备工艺。
热等静压(Hot Isostatic Pressing,简称HIP)是一种在高温高压同时作用下使物料在加热过程中受到各项均衡压力压制而收缩致密促使材料烧结成型的工艺技术。
近年来,随着科技的不断进步,各领域对材料使用要求也越来越苛刻,热等静压技术在制备具有高密度、高纯度、高均匀性、高韧性等优良综合性能的材料方面占据优势,此技术已成为当今许多高性能材料生产中的一项实用技术,也是新材料开发不可缺少的一种新技术。
在制备金属陶瓷过程中,应用热等静压工艺可有效解决金属相与陶瓷相的结合问题,因此热等静压技术已成为许多高性能金属陶瓷复合材料制备中的一项实用技术,本文介绍了热等静压工艺在制备金属陶瓷复合材料的两种应用工艺。
2 热等静压工艺在金属陶瓷制备中的应用热等静压技术在最初期因为设备整体成本较高,其发展一直较为缓慢,为了降低热等静压产品的生产成本,Avure公司的热等静压设备在快速冷却、炉子设计、装卸选择、支持系统和过程控制优化等方面近些年取得了很大进展。
热等静压技术
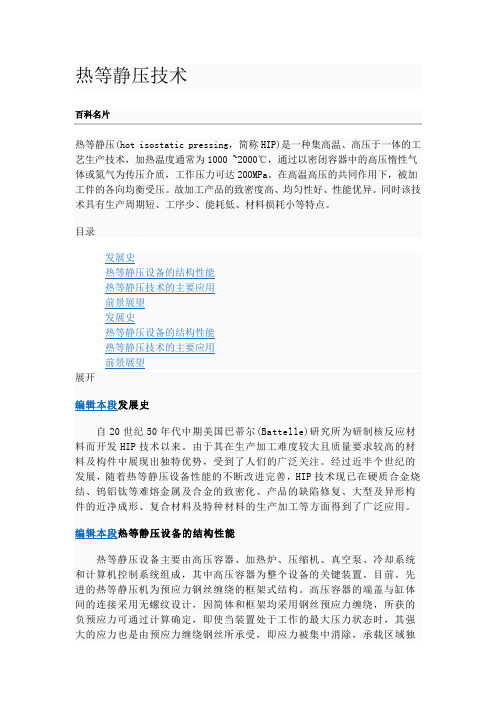
热等静压技术百科名片热等静压(hot isostatic pressing,简称HIP)是一种集高温、高压于一体的工艺生产技术,加热温度通常为1000 ~2000℃,通过以密闭容器中的高压惰性气体或氮气为传压介质,工作压力可达200MPa。
在高温高压的共同作用下,被加工件的各向均衡受压。
故加工产品的致密度高、均匀性好、性能优异。
同时该技术具有生产周期短、工序少、能耗低、材料损耗小等特点。
目录发展史热等静压设备的结构性能热等静压技术的主要应用前景展望发展史热等静压设备的结构性能热等静压技术的主要应用前景展望展开编辑本段发展史自20世纪50年代中期美国巴蒂尔(Battelle)研究所为研制核反应材料而开发HIP技术以来。
由于其在生产加工难度较大且质量要求较高的材料及构件中展现出独特优势,受到了人们的广泛关注。
经过近半个世纪的发展,随着热等静压设备性能的不断改进完善,HIP技术现已在硬质合金烧结、钨铝钛等难熔金属及合金的致密化、产品的缺陷修复、大型及异形构件的近净成形、复合材料及特种材料的生产加工等方面得到了广泛应用。
编辑本段热等静压设备的结构性能热等静压设备主要由高压容器、加热炉、压缩机、真空泵、冷却系统和计算机控制系统组成,其中高压容器为整个设备的关键装置。
目前。
先进的热等静压机为预应力钢丝缠绕的框架式结构。
高压容器的端盖与缸体间的连接采用无螺纹设计,因简体和框架均采用钢丝预应力缠绕,所获的负预应力可通过计算确定,即使当装置处于工作的最大压力状态时,其强大的应力也是由预应力缠绕钢丝所承受,即应力被集中消除,承载区域独立安全。
同时钢丝缠绕还起到防爆和屏障的作用。
因此,这种结构的热等静压机在高温高压(2000摄氏度200MPa)的工作条件下,无需外加任何特殊的防护装置,与老式的螺纹连接结构(端盖与缸体间)的热等静压机相比,不但设备的结构紧凑,而且有效地保证了生产的安全性。
加热炉负责提供热等静压所必需的热量,通常为电阻式加热炉,可视不同温度档的要求,采用不同的电阻材料,如最高工作温度为1450℃条件时可用钼丝加热炉,为2000%条件时可用石墨加热炉。
热等静压高温烧结炉

热等静压高温烧结炉全文共四篇示例,供读者参考第一篇示例:热等静压高温烧结炉是一种先进的工业设备,被广泛应用于金属、陶瓷、硬质合金等材料的制备过程中。
它具有高温、高压和高温度的特点,可以实现材料的高密度、高强度和高硬度,被誉为当今最先进的材料加工工艺之一。
下面将从工作原理、结构组成、应用领域和发展前景等方面对热等静压高温烧结炉进行介绍。
我们来了解一下热等静压高温烧结炉的工作原理。
热等静压高温烧结炉是在高温环境下对粉末材料进行烧结加工的设备,其主要工作原理是通过加热、加压和保持恒温等过程,使粉末材料在高温高压条件下熔融和烧结,最终得到高密度、高强度和高硬度的成品。
在这一过程中,热等静压高温烧结炉能够对原料粉末进行充分的烧结和压实,从而实现优质产品的制备。
热等静压高温烧结炉的结构组成主要包括炉体、加热系统、压力系统、控制系统等部分。
炉体是烧结炉的主体结构,通常由耐高温、耐腐蚀的材料制成,保证了炉体在高温高压条件下的稳定性和耐用性。
加热系统是烧结炉的关键组成部分,通常采用电阻加热、感应加热或火焰加热等方式,能够提供足够的热量以满足烧结工艺的要求。
压力系统则负责提供高压环境,将粉末材料充分压实,保证烧结过程的顺利进行。
控制系统则是烧结炉的智能化核心,能够实现对温度、压力、时间等参数的精准控制,保证产品的质量和稳定性。
热等静压高温烧结炉在金属、陶瓷、硬质合金等材料制备领域具有广泛的应用。
在金属材料领域,热等静压高温烧结炉可以用于制备高强度、高硬度的金属制品,如航空发动机叶片、汽车发动机缸体等。
在陶瓷材料领域,热等静压高温烧结炉可以用于制备陶瓷导热件、陶瓷刀具等高性能陶瓷制品。
在硬质合金领域,热等静压高温烧结炉可以用于制备硬质合金刀具、硬质合金零部件等产品。
热等静压高温烧结炉在提高材料的密度、强度和硬度方面具有重要的应用前景。
未来,随着工业技术的不断发展和对材料性能要求的不断提高,热等静压高温烧结炉将迎来更广阔的发展空间。
等静压技术及其应用

等静压技术及应用1.等静压技术 (1)1.1等静压技术的介绍及发展情况 (1)1.2等静压技术的应用 (3)2.冷等静压技术 (4)2.1冷等静压在陶瓷中的应用 (4)2.2在粉末冶金中的应用 (6)2.3冷等静压技术在食品加工行业中的应用 (7)3.热等静压 (8)3.1热等静压技术在硬质合金中的应用 (9)3.2在粉末冶金中的应用 (11)3.3在陶瓷中的应用 (11)等静压技术1.1等静压技术的介绍及发展情况等静压成形技术是一种利用密闭高压容器内零件受到各向均等的超高压压力状态进行成形的先进制造技术,根据静压力基本方程(p=p+pgh),盛放在密闭容器内的液体,其外加压强p。
发生变化时,只要液体仍保持其原来的静止状态不变,液体中任一点的压强均将发生同样大小的变化。
这就是说,在密闭容器内,施加于静止液体上的压强将以等值同时传到各点,这就是等静压成形的原理。
目前等静压技术的应用领域主要集中在粉末高压固化烧结、扩散连接及组件扩散连接等领域。
其分类也根据产品成形温度的不同分为冷等静压技术(常温,一般使用压力为100~ 630MPa)、温等静压技术(温度一般在80~120℃下,压力为300MPa 左右)热等静压技术(工作温度一般为1000~2200℃,工作压力常为100~200MPa。
)。
等静压技术作为一种先进成形技术,与传统的成形技术相比具有明显的优势,主要集中在:第一.等静压成形的产品,具有密度高而分布均匀、产品内部不存在气泡、成品晶粒间显微孔隙度很低,其力学性能与电性能均比别的成形方法好。
第二.等静压制品几乎无内应力,压坯可以直接进窑烧结,不会翘曲与开裂。
第三.制作长径比(长度与直径之比)很大的产品是轻而易举的事,而其他方法是则是事倍功半或者无法实现。
第四.制作高熔点、高硬度材料的大型产品及形状复杂的产品。
第五.等静压成形的坯体比其他成形方法制得坯体烧成温度低并且不会污染高纯度的压坯材料由于等静压技术有着传统材料成形方法所无法比拟的优点,并且随着新材料新工艺的不断出现,使得等静压设备的需求不断增加,其产品的应用领域不断扩大,特别是1955 年美国巴特尔研究所为了研制核反应堆的材料而开发了热等静压应用技术以来,经过70~80年代,各国开始的高技术热潮也有力地推动了HIP 技术的发展,将热等静压技术作为陶瓷、高温合金、复合材料成形的一种重要的工艺手段。
热等静压技术在材料致密化中的应用

热等静压技术在材料致密化中的应用
热等静压技术(HSP)是一种通过热源和等静压力相结合的方
法来实现材料致密化的技术。
它主要通过以下步骤实现:
1. 材料选择:选择合适的原料或粉末进行制备。
通常选择具有高熔点和高热稳定性的材料,例如陶瓷、金属等。
2. 制备预制坯料:将原料或粉末与一定比例的添加剂混合,并通过压制或其他方法制备成预制坯料。
3. 加热:将预制坯料放置在加热炉中,使用适当的加热方法(例如电加热、燃气加热等)将其加热到一定温度。
4. 施加等静压力:在加热的同时,施加等静压力。
等静压力可以通过液压系统、气压系统等方式施加。
这种等静压力可以有效地减小材料的孔隙度,促进原子或颗粒之间的结合。
5. 热处理和冷却:在施加等静压力的同时,保持高温一段时间,以促进原子或颗粒间的结合,形成致密的材料。
然后,通过适当的冷却方法将其冷却到室温。
热等静压技术在材料致密化中的应用有以下几个方面:
1. 制备高性能陶瓷材料:热等静压技术可以使陶瓷材料的晶界结合更加紧密,孔隙度降低,从而提高陶瓷材料的力学性能和热性能。
2. 制备多孔金属材料:热等静压技术可以用于制备多孔金属材料。
通过控制加热温度和施加等静压力,可以调控金属材料的孔隙度和孔隙分布,从而实现对材料性能的调控。
3. 定向凝固材料制备:在制备定向凝固材料(例如单晶体材料)时,热等静压技术可以通过控制温度和压力,在凝固过程中减小材料中的孔隙度,促进晶粒间的结合,从而提高材料的力学性能和耐热性能。
总而言之,热等静压技术在材料致密化中的应用可以实现对材料性能的调控和提升,广泛应用于陶瓷材料、金属材料等领域。
热等静压技术在金属陶瓷复合材料制备中的应用
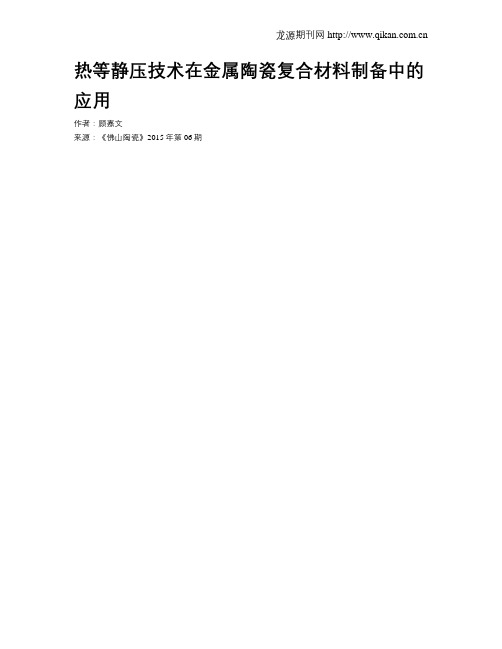
热等静压技术在金属陶瓷复合材料制备中的应用作者:顾嘉文来源:《佛山陶瓷》2015年第06期摘要:本文阐述了热等静压技术制备金属陶瓷复合材料的两种不同工艺路线及各自的技术特点。
同时,综述了热等静压技术在制备金属陶瓷复合材料中的应用及研究。
关键词:金属陶瓷;复合材料;热等静压(HIP);应用1 前言金属陶瓷复合材料(Metal Matrix Composites,简称MMC)是由一种或多种陶瓷相和金属相或合金组成的多相复合材料,金属陶瓷既具有金属的韧性、高导热性和良好的热稳定性,又具有陶瓷的耐高温、耐腐蚀和耐磨损等特性。
在国防及民用领域有着非常广阔的应用前景。
常用的制备方法有混合烧结法、粘合液浸渍法、直接氧化法、自蔓延高温合成法等。
在烧结过程中其烧结活性低、所需烧结温度高、烧结致密化程度低、残留孔隙度大、脆性大、综合性能不佳。
随着热等静压技术发展,采用热等静压技术制备金属陶瓷复合材料,改善了成型和烧结条件,使材料的孔隙度明显降低,获得了高致密度的材料,综合性能大大提高。
2 热等静压技术热等静压设备主要由高压容器、加热炉、压缩机、真空泵、冷却系统和计算机控制系统组成,其中,高压容器为整个设备的关键装置,图1是热等静压机的典型示意图。
热等静压工艺(简称HIP)是将制品放置到密闭的容器中,向制品施加各向同等的压力,同时施以高温,在高温高压的作用下,制品得以烧结和致密化,图2为热等静压技术原理图。
3 制备金属陶瓷复合材料的热等静压工艺热等静压技术在金属陶瓷复合材料制备中有两种不同工艺路线,一种为直接热等静压烧结工艺;另一种是热等静压后续致密化工艺。
3.1 直接热等静压烧结工艺及特点直接热等静压烧结制备金属陶瓷复合材料的工艺路线如图3所示。
直接热等静压烧结工艺制备金属陶瓷复合材料的技术关键如下:(1)包套材质选择,要确保在制备过程中不与原材料粉末发生反应,同时也要考虑到去除的难易程度。
(2)包套内粉末的振实密度大小直接影响烧结制品质量,振实密度低将导致包套收缩量大,尺寸控制困难,且包套易发生破裂。
热等静压(HIP)技术和设备的发展及应用
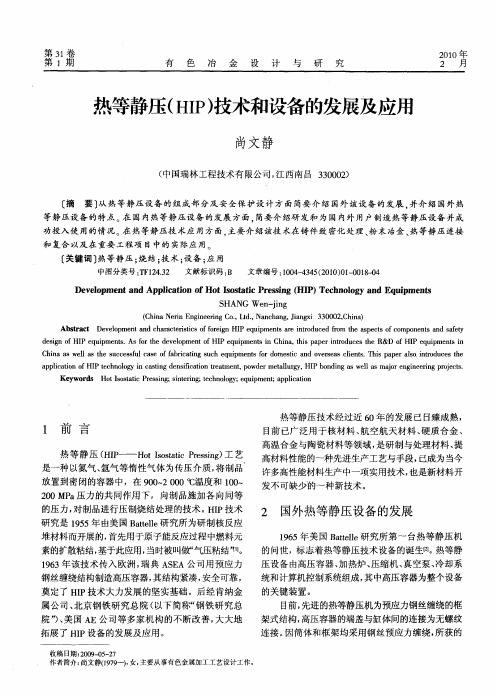
等静压 设备 的特 点。在 国 内热 等静 压设备 的发展 方 面 , 简要介 绍研 发和 为国 内外用 户制造 热等静 压设备 并成 功 投入使 用 的情 况。 热 等静压技 术 应 用方 面 , 介 绍该技 术在 铸件 致 密化处 理 、 末 冶金 、 在 主要 粉 热等 静压连 接
和 复合 以及在 重要 工程 项 目中的 实际应 用
2 国外热等静压设备的发展
16 美 国 B t1 95年 at1 e e研究 所第 一 台热等 静压 机
素的扩散粘结, 基于此应用, 当时被叫做 ‘ 气压粘结 1 。 16 该技 术传 入 欧洲 , 9 3年 瑞典 A E S A公 司用 预 应 力 钢丝缠绕结构制造高压容器, 其结构紧凑, 安全可靠, 奠定了 H P I 技术大力发展的坚实基础 。后经肯纳金 属公司、 北京钢铁研究总院 ( 以下简称“ 钢铁研究总
application热等静压技术经过近60年的发展已日臻成熟1前言目前已广泛用于核材料航空航天材料硬质合金高温合金与陶瓷材料等领域是研制与处理材料提热等静压hiphotisostaticpressing工艺高材料性能的一种先进生产工艺与手段已成为当今是一种以氮气氩气等惰性气体为传压介质将制品许多高性能材料生产中一项实用技术也是新材料开放置到密闭的容器中在9002000oc温度和10o发不可缺少的一种新技术
Ke wo d Ho s sa i P e sn ; it r g tc n lg ; q i me t a p i ai n y rs t o tt rs i g sn ei ; e h oo y e u p n ; p l t l c n c o
热 等静 压技 术经 过近 6 0年 的发展 已 日臻 成 熟 ,
硬质合金低压热等静压烧结工艺
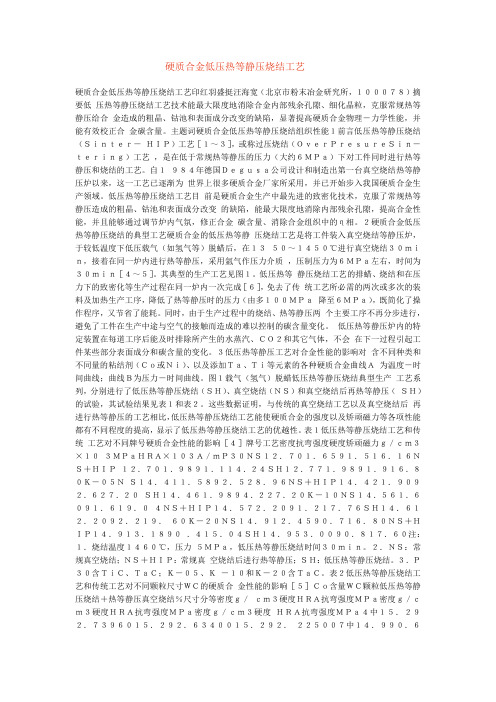
硬质合金低压热等静压烧结工艺硬质合金低压热等静压烧结工艺印红羽盛挺汪海宽(北京市粉末冶金研究所,100078)摘要低压热等静压烧结工艺技术能最大限度地消除合金内部残余孔隙、细化晶粒,克服常规热等静压给合金造成的粗晶、钴池和表面成分改变的缺陷,显著提高硬质合金物理-力学性能,并能有效校正合金碳含量。
主题词硬质合金低压热等静压烧结组织性能1前言低压热等静压烧结(Sinter-HIP)工艺[1~3],或称过压烧结(OverPresureSin-tering)工艺,是在低于常规热等静压的压力(大约6MPa)下对工件同时进行热等静压和烧结的工艺。
自1984年德国Degusa公司设计和制造出第一台真空烧结热等静压炉以来,这一工艺已逐渐为世界上很多硬质合金厂家所采用,并已开始步入我国硬质合金生产领域。
低压热等静压烧结工艺目前是硬质合金生产中最先进的致密化技术,克服了常规热等静压造成的粗晶、钴池和表面成分改变的缺陷,能最大限度地消除内部残余孔隙,提高合金性能,并且能够通过调节炉内气氛,修正合金碳含量、消除合金组织中的η相。
2硬质合金低压热等静压烧结的典型工艺硬质合金的低压热等静压烧结工艺是将工件装入真空烧结等静压炉,于较低温度下低压载气(如氢气等)脱蜡后,在1350~1450℃进行真空烧结30min,接着在同一炉内进行热等静压,采用氩气作压力介质,压制压力为6MPa左右,时间为30min[4~5]。
其典型的生产工艺见图1。
低压热等静压烧结工艺的排蜡、烧结和在压力下的致密化等生产过程在同一炉内一次完成[6],免去了传统工艺所必需的两次或多次的装料及加热生产工序,降低了热等静压时的压力(由多100MPa降至6MPa),既简化了操作程序,又节省了能耗。
同时,由于生产过程中的烧结、热等静压两个主要工序不再分步进行,避免了工件在生产中途与空气的接触而造成的难以控制的碳含量变化。
低压热等静压炉内的特定装置在每道工序后能及时排除所产生的水蒸汽、CO2和其它气体,不会在下一过程引起工件某些部分表面成分和碳含量的变化。
硬质合金烧结方法的新进展

硬质合金烧结方法的新进展1前言烧结是硬质合金生产过程的最后一道工序,也是最基本、最关键的一道工序,烧结前工序中的某些缺陷在一定范围内可以通过调整烧结工艺加以纠正,而由烧结造成的废品一般无法通过以后的工序来挽救,因此烧结工艺和装备选择是否恰当,对烧结产品的质量有着决定性的影响。
长久以来,在实际生产中逐渐形成了多种烧结方法,较为传统的包括氢气烧结、真空烧结、热等静压烧结、真空后续热等静压、烧结热等静压等。
80年代纳米结构问世之后,又逐渐形成了新型烧结方法,如微波烧结、放电等离子烧结等。
下面就这几种烧结技术特别是纳米硬质合金烧结技术做一综合介绍。
2氢气烧结将压坯装在石墨舟中,再充填一定含碳量的氧化铝填料或石墨颗粒填料,通常是装入连续推进式的钼丝炉内,在氢气保护下进行烧结,这个过程就是氢气烧结<1 > 。
氢气烧结的特点是:能够提供还原性气氛;需要预烧结来清除压制时添加的成形剂。
氢气烧结虽然曾在较长时期内被广泛采用,甚至目前还有少数厂家采用它,但经过长期实践,人们发现它存在许多不足。
钼丝刚玉管炉的优点是结构简单、炉子功率小、炉管寿命长,但是炉温控制不准、炉内气氛变化大、产品容易渗碳、脱碳。
另外,其烧结过程是在正压下进行的,产品内部的孔隙不能充分得到消除,留有残余孔隙,一些氧化物杂质也不能较好地挥发排除掉<2 > 。
3真空烧结硬质合金的真空烧结始于上世纪三十年代,而到六十年代才获得较大的发展。
所谓真空烧结,就是在负压的气(汽)体介质中烧结压制的过程。
真空烧结与氢气烧结相比,可以提高炉气纯度,同时负压改善了粘结相对硬质相的润湿性。
真空烧结具有如下优点:(1 )能够更好地排除烧结体中Si、Mg、Ca等微量氧化物杂质,从而提高硬质合金的纯度;(2 )真空下气相的渗碳、脱碳作用大大减少,易于保证最终合金的碳含量,控制合金的组织结构;(3)可以降低烧结温度或保温时间,防止碳化物晶粒的不均匀长大;(4)烧结品残留孔隙比氢气烧结少,可提高合金的密度和机械性能;(5 )烧结时产品不用填料隔开和保护,操作简单,而且产品表面无粘附物和白亮的金属铝沉积物。
烧结态硬质合金的hip处理
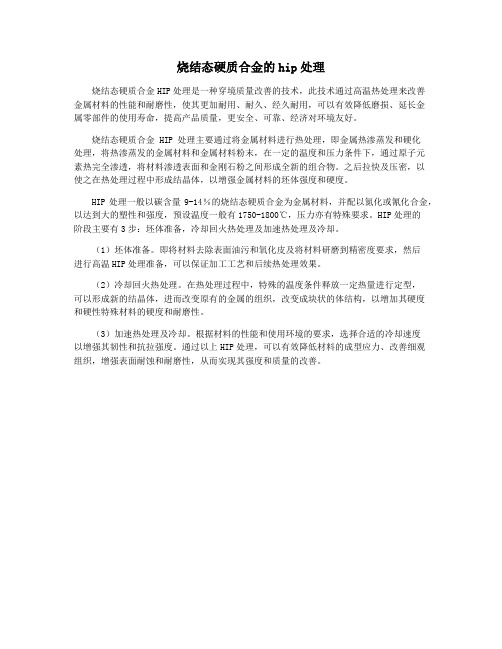
烧结态硬质合金的hip处理
烧结态硬质合金HIP处理是一种穿境质量改善的技术,此技术通过高温热处理来改善
金属材料的性能和耐磨性,使其更加耐用、耐久、经久耐用,可以有效降低磨损、延长金
属零部件的使用寿命,提高产品质量,更安全、可靠、经济对环境友好。
烧结态硬质合金 HIP 处理主要通过将金属材料进行热处理,即金属热渗蒸发和硬化
处理,将热渗蒸发的金属材料和金属材料粉末,在一定的温度和压力条件下,通过原子元
素热完全渗透,将材料渗透表面和金刚石粉之间形成全新的组合物。
之后拉快及压密,以
使之在热处理过程中形成结晶体,以增强金属材料的坯体强度和硬度。
HIP处理一般以碳含量9-14%的烧结态硬质合金为金属材料,并配以氮化或氰化合金,以达到大的塑性和强度,预设温度一般有1750-1800℃,压力亦有特殊要求。
HIP处理的
阶段主要有3步:坯体准备,冷却回火热处理及加速热处理及冷却。
(1)坯体准备。
即将材料去除表面油污和氧化皮及将材料研磨到精密度要求,然后
进行高温HIP处理准备,可以保证加工工艺和后续热处理效果。
(2)冷却回火热处理。
在热处理过程中,特殊的温度条件释放一定热量进行定型,
可以形成新的结晶体,进而改变原有的金属的组织,改变成块状的体结构,以增加其硬度
和硬性特殊材料的硬度和耐磨性。
(3)加速热处理及冷却。
根据材料的性能和使用环境的要求,选择合适的冷却速度
以增强其韧性和抗拉强度。
通过以上HIP处理,可以有效降低材料的成型应力、改善细观
组织,增强表面耐蚀和耐磨性,从而实现其强度和质量的改善。
热等静压处理对Ti(C,N)基金属陶瓷组织和性能的影响
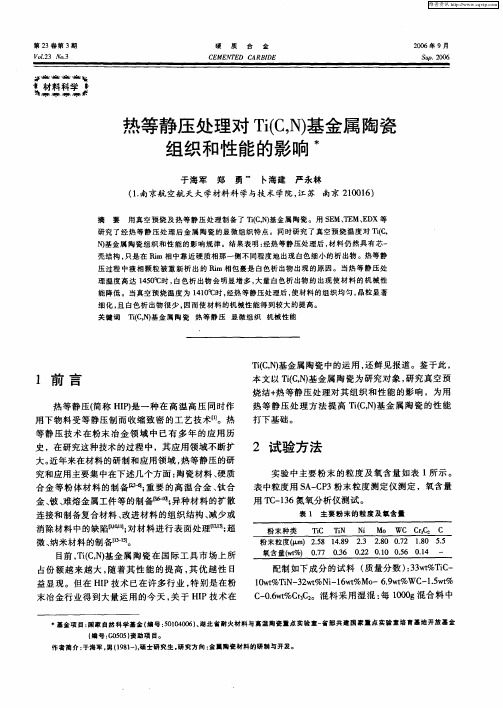
于海军. 郑 勇, 卜海建, 严永林: 热等静 压处理对 T(,】 i N 基金属陶瓷组织和性能的影响 C
・15・ 3
图 1不 同 预烧 温度 所 得 烧 结 体 经 热 等静 压 处 理 后 的 显 微组 织 :
( 13  ̄; )17  ̄; ) 4 0C () 4 0C a 3 0C ( 3 0C ( 1 1 ̄ ; 15  ̄ ) b c d
基 金属 陶瓷 组织 和 性 能 的 影 响 规 律 。结 果表 明 : 经热 等 静 压 处 理 后 , 料 仍 然 具 有 芯 一 材
壳结构 , 只是在 Rm相 中靠近硬质相那 一侧不同程度地 出现 白色细小的析出物。热等静 i
压 过程 中 液 相 颗 粒 被 重 新 析 出 的 Rm 相 包 裹 是 白 色析 出物 出现 的原 因 。 当 热 等 静 压 处 i 理 温 度 高 达 15  ̄时 , 色析 出 物 会 明 显 增 多 , 量 白色 析 出物 的 出现 使 材 料 的 机 械 性 4 0C 白 大 能 降 低 。 当 真空 预 烧温 度 为 1 1  ̄时 , 热 等静 压处 理 后 , 材 料 的组 织 均 匀 , 粒显 著 4 0C 经 使 晶 细 化 , 白 色析 出物 很 少 , 而 使 材 料 的 机 械性 能得 到 较 大 的 提 高 。 且 因
1 w % TN一 2 t Ni 1 w % Mo 69 % W C- .w % 0 t i 3 w% 一6t 一 .wt 15 t
C 06 t r 2 料 采 用 湿 混 : 10 g混合 料 中 一 . %C3 。混 w C 每 00
・基 金 项 目 : 家 自然 科 学 基 金 ( 号 :0 0 0 6 、 北 省 耐 火 材 料 与 高 温 陶 瓷 重 点 实 验 室 一 部 共 建 国 家 重 点 实 验 室 培 育 基 地 开放 基 金 国 编 5140 )湖 省 ( 号 :0 0 ) 助 项 目 。 编 G 55资 作 者 简 介 : 海 军 . (9 1 , 士 研 究 生 . 究方 向 : 属 陶 瓷材 料 的 研 制 与 开 发 。 于 男 18 一) 硕 研 金
- 1、下载文档前请自行甄别文档内容的完整性,平台不提供额外的编辑、内容补充、找答案等附加服务。
- 2、"仅部分预览"的文档,不可在线预览部分如存在完整性等问题,可反馈申请退款(可完整预览的文档不适用该条件!)。
- 3、如文档侵犯您的权益,请联系客服反馈,我们会尽快为您处理(人工客服工作时间:9:00-18:30)。
热等静压(hip)技术在硬质合金及陶瓷材料中的应用热等静压(HIP)技术一直是开发高性能陶瓷材料及复合材料致密制品的主要手段之一。
陶瓷材料、尤其是非氧化物陶瓷材料多为强共价键化合物。
其自扩散系数很小,采用常规烧结工艺难于得到性能优良、形状复杂的致密制品。
在每届国际HIP会议上,陶瓷材料的研究论文都占有主要的位置,下面是1999年北京HIP国际会议关于HIP技术在硬质合金和陶瓷材料中的应用情况介绍。
1硬质合金HIP技术在硬质合金中的应用始于70年代初。
硬质合金经HIP处理后,其抗弯强度与使用寿命大幅度提高,加工后制品的表面光洁度也大大提高,许多采用常规工艺难以生产的部件,在采用HIP技术后也可以顺利生产。
多年的试验研究表明,要想得到全致密的硬质合金产品,并不需要太高(一般只需要几个MPa)的压力。
80年代初开发了一种低压烧结技术, 即低压烧结HIP技术,此项新工艺把硬质合金生产中的脱蜡-烧结-HIP致密化合为一体在同一设备内完成。
由于所需压力成10倍的下降,使HIP设备的制造成本大幅度降低。
几道工序合为一体不但降低了制品的生产成本,同时由于此工艺更加合理而提高了产品的质量。
目前烧结HI技术已成为世界各硬质合金厂生产高质量硬质合金的主要手段。
近年来我国各主要硬质合金生产厂都引进了多台先进的烧结热等静压设备,本届HIP会议发表了数篇有关报道。
其中,株洲硬质合金厂采用平均粒度为08μm的WC粉、钴粉为原料及加入少量VC、Cr3C2制备了HRA≥90、抗弯强度≥3000MPa的系列产品<1>;株洲硬质合金厂还采用烧结HIP工艺生产了外285mm/内66mm×145mm的大件,其单件质量为118kg;他们对采用此工艺与采用常规真空烧结工艺制品的性能进行了比较(表1)<2>表1烧结HIP工艺及常规真空烧结工艺制品性能的比较①烧结工艺密度/gcm3硬度(HRA)抗弯强度/MPa抗压强度/ /MPa晶粒尺寸/μm烧结HIP14228923710555012真空烧结141188 92730468014①合金成分:WC+13Co(质量分数)。
2Si3N4材料Si3N4陶瓷是最主要且应用最广的工程陶瓷材料之一。
由于Si3N4陶瓷材料自身几乎不可能烧结成制品,故在生产Si3N4陶瓷制品时都加入一定数量的烧结助剂如:MgO、Al2O3、Y2O3等。
由于烧结助剂与Si3N4表面SiO2形成低熔点共晶而进行液相烧结,αSi3N4粒子溶于液相后,从液相析出针状βSi3N4,这样的组织结构有利于提高Si3N4 陶瓷材料的力学性能,因而常压烧结Si3N4制品在80年代后得到广泛的应用。
为进一步提高材料的力学性能,近年来大多采用低压HIP烧结技术(又称为气压烧结———GPS),且在加压工艺上各国都进行了大量研究。
清华大学采用先在1800℃、01MPa下烧结2h(材料中含5%Y2O3、3%Al2O3及5%TiC(质量分数)),然后在1900℃、10MPa下烧结2h的工艺,得到了抗弯强度为714MPa,断裂韧性为74MPa·m1/2的材料< 3>。
上海材料所认为,最好的工艺是先在1850℃及1MPa下烧结05~2h,然后进行高压处理(温度为1750~1850℃,压力为150MPa<4>)。
对HIP高压处理致密化的机理研究表明,虽然制品的密度随HIP处理温度的提高而提高,但若预烧工艺选择不当,也可使其中心部位的致密化受到影响。
澳大利亚学者与中国学者的研究结果表明<5>,若在01~1 MPa及1750℃下烧结1h,然后再立即加压至100MPa并保持1h,则可以得到很细的晶粒。
他们对Si3N4/SiC·ZTA·Mg-AT(Mg-Al钛酸盐)等又进行了一系列的试验,得到了同样的结论(表2)。
表2一些陶瓷材料在压力烧结(PS)与高压烧结(SH)后晶粒尺寸等性能的对比<5>材料组成(质量分数)/%烧结条件相对密度/%开孔率/%总气孔率/%平均晶粒尺寸/μmSi3N4Si3N4(90%),CaO(2%),Y2O3( 3%),La2O3(5%)PS(1750℃,2h,N2,0.1MPa)66.533.5 33.59.2±1.8SH(1750℃,2h,N2,100MPa)99.50.30.5 4.9±2.2Si3N4/SiCSi3N4(58.4%),SiC(14.6%),SiO2(3%),Y2O3(9%),La2O3(15%)PS(1750℃,2h,N2,0.1 MPa)73.225.126.81.9±0.4SH(1750℃,2h,N2,100MPa)99.70.000.31.6±0.3ZTAZrO2(15%),Al2O3(85%) PS(1600℃,2h,空气,0.1MPa)97.90.052.050.4±0.1SH(1600℃,2h,100MPa)98.20.001.80.2±0.1O-ATAl2 O3(56.1%),TiO2(43.9%)PS(1550℃,4h,空气,0.1MPa)89.27.010.82.5±0.4SH(1600℃,2h,Ar,Ar,100MPa)91.68.08.41.0±0.4Mg-ATMgO(5%),Al2O3(53.3%) ,TiO2(41.7%)PS(1550℃,4h,空气,0.1MPa)86.68.013 .411.3±1.9SH(1600℃,2h,Ar,100MPa)96.53.53.55 .1±1.2Fe-ATFe2O3(5%),Al2O3(53.3%),TiO2(41.7 %)PS(1550℃,4h,空气,0.1MPa)84.48.615.68.4±0.8SH(1600℃,2h,Ar,100MPa)87.610.312.44.2±2.1Si- ATSiO2(5%),Al2O3(53.3%),TiO2(41.7%)PS(1550℃,4h,空气,0.1MPa)88.35.211.713.3±0.7SH(1600℃,2 h,Ar,100MPa)92.25.97.82.8±0.关于在高压下Si3N4晶粒细化的原因,被认为是由于致密化在更低的温度(αSi3N4完成转变为βSi3N4的温度降低至1400℃)下进行所致。
3SiC陶瓷材料SiC陶瓷材料也是重要的工程陶瓷材料之一。
制备此材料的特点是烧结温度高,材料的全致密化程度仍不理想。
为此,人们进行了大量研究,如选用不同的烧结助剂、降低原材料粉末的粒度和改进烧结工艺等,但收效不大。
(1)加入过量的烧结助剂虽可以使烧结温度降低,但材料的力学性能,尤其是其高温性能降低;(2)高的烧结温度会使材料的晶粒长大、力学性能降低;(3)过高的烧结温度会使一些液相挥发而难以得到全致密的材料。
日本采用包套HIP工艺制备了致密的SiC陶瓷材料,研究了TiC及Si3N4陶瓷颗粒增强和SiC晶须增强的复合陶瓷材料,还研究了不同烧结添加剂(B4C、AlN及Al2 O3)及上述陶瓷材料增强剂对SiC系陶瓷材料烧结致密度、显微组织及力学性能的影响<6> 。
加入Al2O3可在SiC表面生成Al2O3SiO2共晶相,从而可以有效地提高SiC系材料的烧结致密度。
他们采用αSiC的亚微米粉加入3%Al2O3(质量分数),在1850 ℃、200MPa下烧结1h,得到了密度为973%的材料;加入25%Si3N4(体积分数)颗粒增强剂使SiC多相陶瓷材料的抗弯强度达到了625MPa;加入5%SiC(体积分数)晶须材料的断裂韧性值达到了67MPa·m1/2。
上海硅酸盐研究所历时10年开发了“活性”HIP后处理SiC烧结制品的新工艺<7>。
热力学分析表明,许多碳化物(如SiC、TiC和B4C等)在高温、高压氮的作用下不稳定,因此氮气可以作为“活性”HIP后对SiC进行处理的一种典型压力介质(图1)。
SiC材料在高压氮处理后,在材料表面形成Si3N4 ,且使部分内部SiC氮化成Si3N4。
在SiC氮化成Si3N4时,由于产生体积膨胀(约175%),而使材料的气孔率下降,从而使材料表面的气孔和表面缺陷(如裂纹)得以愈合,因此,材料的力学性能大幅度提高。
而采用常规惰性气体作为压力介质时,由于不能改变SiC陶瓷烧结制品的表面组成与结构,因此,当存在表面缺陷时会使材料的力学性能大幅度降低。
图1几种碳化物在1000~2500℃氮化时氮的平衡分压a-多数碳化物;b-SiC及TiC表3列出了SiC系材料在“活性”HIP处理前后,一些力学性能的比较。
从表3可以看到, 经过“活性”HIP处理的材料,其密度有不同程度的提高,其抗弯强度显著提高(有的甚至提高近1倍),其断裂韧性值有的提高50%以上。
在上海硅酸盐研究所研究成果的基础上,日本经验证得到了类似的结果<8>。
表3高压氮处理前后一些材料的性能变化材料氮化处理前氮化处理后密度/g·cm-3抗弯强度/MPaKIC/MPa·m1/2密度/g·cm-3抗弯强度/MPaKIC/MPa·m1/2SiC31466057320100084SiC-2 5%(体积分数)TiC3.453546.53.606907.9SiC-5%(体积分数) SiCw3.135956.73.179208.5SiC-20%(体积分数)Sialon 3.186303.19908Al2O3-20%(质量分数)SiCw-10%(质量分数) SiCp3.707053.751033一般认为,采用热压(HP)工艺可以得到全致密的高性能产品。
试验表明,经过热压的制品在经过高压氮处理后,其力学性能仍可得到大幅度提高(表4)。
对于采用不同工艺制备的Si3N4材料,经高压氮处理后,由于氮部分改变了铝与氧的结合,形成了SiAlON固溶体而提高了Si3N4材料的力学性能(表5)。
表4SiCAlN陶瓷热压后及HIP处理后的力学性能密度/gcm-3抗弯强度/MPa断裂韧性值KI。