球化不良解析与措施
影响球化效果的几方面因素及解决方法

影响球化效果的几方面因素及解决方法1、原材料。
使用废钢方面,由于货源不固定,因而造成成分的波动与偏差,如果是生产铁素体基体材质的铸件,则应选用碳素钢成分的废钢,例如A3钢、45钢等角钢、工字钢等;也可以适度用些不含Cr的合金钢。
在外观方面,最好不得有铁锈、油漆、油圬以及焊缝等,因为铁锈主要是FeO等,在球化反应时会消耗Mg元素,影响球化率;油漆尤其是橘黄色、绿色,是由含Pb约64%和Cr约16.1%的颜料配置而成;焊缝金属一般含有O、H、S、P、Sn、Pb等有害杂质,这些干扰杂质元素,尤其是Pb会进入铁液之中,直接会是石墨形态变异。
尽量少用表面附着较多的煤(煤中S、P含量高)、或铁锈的废钢,以及废钢中夹杂锌、铝、铅、铬、铜等反球化元素,上料工一定要多加注意不能用不明来源的废生铁铸件和玛钢件。
增碳剂一定要保持干燥,受潮后的增碳剂会导致铁水中含O、H等元素增加,造成铁水过度氧化,影响球化效果。
2、出炉温度出炉温度尽量控制在1480-1500℃,在球化包温度较低时,可以适当提高10-30℃。
但最高不能超过1538℃的临界温度。
否则会造成球化反应剧烈(过度烧损球化剂)、夹渣、冷隔等现象。
3、捣包捣包注意:①填充后应进行紧实,使合金之间的空隙或缝隙最小,堆积密度最大;也就是必须分层用力捣实,②必须有覆盖物,覆盖物可以说是千差万别,主要目的是延缓起爆、预处理等,③现场操作操作注意一定要覆盖严实,不要有缝隙,充分体现既覆又盖的目的;④覆盖后的体积最好和处理包凹槽相吻合。
4、扒渣扒渣应迅速和彻底,防止铁水回硫,第二次氧化5、覆盖扒渣后,覆盖足量的保温剂,保证铁水温度下降缓慢,利于浇注。
6、浇注时间尽量在12分钟内完成,以免温度过低和孕育衰退。
与球化剂有关的球铁件缺陷(1)石墨球异化:石墨球异化出现不规则石墨,如团块状、蝌蚪状、蠕虫状、角状或其他非圆球状。
这是由于球状石墨沿辐射方向生长时,局部晶体生长模式和生长速率偏离正常生长规律所致。
实战专家总结球化不良缺陷的13条原因,预防措施该如何做?
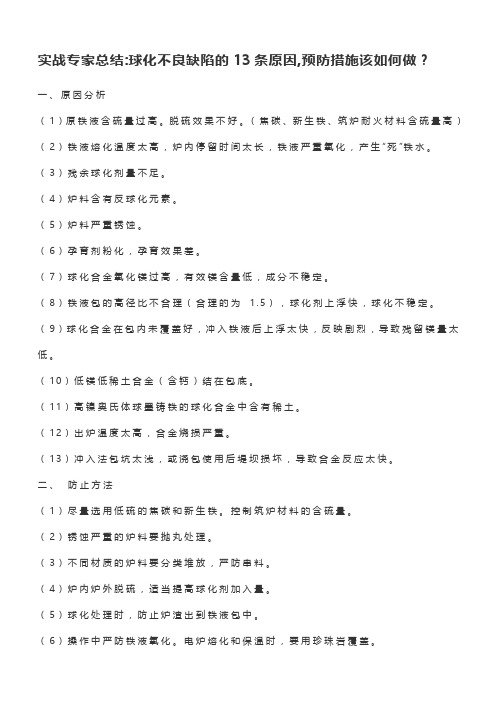
实战专家总结:球化不良缺陷的13条原因,预防措施该如何做?一、原因分析(1)原铁液含硫量过高。
脱硫效果不好。
(焦碳、新生铁、筑炉耐火材料含硫量高)(2)铁液熔化温度太高,炉内停留时间太长,铁液严重氧化,产生“死”铁水。
(3)残余球化剂量不足。
(4)炉料含有反球化元素。
(5)炉料严重锈蚀。
(6)孕育剂粉化,孕育效果差。
(7)球化合金氧化镁过高,有效镁含量低,成分不稳定。
(8)铁液包的高径比不合理(合理的为 1.5),球化剂上浮快,球化不稳定。
(9)球化合金在包内未覆盖好,冲入铁液后上浮太快,反映剧烈,导致残留镁量太低。
(10)低镁低稀土合金(含钙)结在包底。
(11)高镍奥氏体球墨铸铁的球化合金中含有稀土。
(12)出炉温度太高,合金烧损严重。
(13)冲入法包坑太浅,或浇包使用后堤坝损坏,导致合金反应太快。
二、防止方法(1)尽量选用低硫的焦碳和新生铁。
控制筑炉材料的含硫量。
(2)锈蚀严重的炉料要抛丸处理。
(3)不同材质的炉料要分类堆放,严防串料。
(4)炉内炉外脱硫,适当提高球化剂加入量。
(5)球化处理时,防止炉渣出到铁液包中。
(6)操作中严防铁液氧化。
电炉熔化和保温时,要用珍珠岩覆盖。
(7)在保证球化的前提下,尽量降低出炉温度。
(8)注意球化处理操作,调整铁液包的高径比,球化剂和硅铁上面要覆盖铁销或珍珠岩,防止铁液与球化剂作用过分激烈或“结死”包底。
(9)镁球化处理中,加入少量稀土,可中和反球化元素的干扰。
(10)包坑与堤坝按要求,损坏后要及时修复。
(11)使用配比合适、成分稳定的中间合金采用随流孕育和二次孕育。
(12)交界铁液要分离干净。
(13)厚大件球化处理时可冲入一些钼、铜、锑、铋等合金元素。
也可采用重稀土合金球化剂。
(14)使用低镁、低稀土合金,使球化处理反应平缓;减少镁的烧损。
(15)高镍奥氏体球墨铸铁处理用不含稀土的镍镁或硅镁合金。
(16)采用喂丝处理铁水包的出铁量要适当,或适当加高铁水包,留下喂丝时铁液反应空间。
球化过程及主要缺陷分析 文档
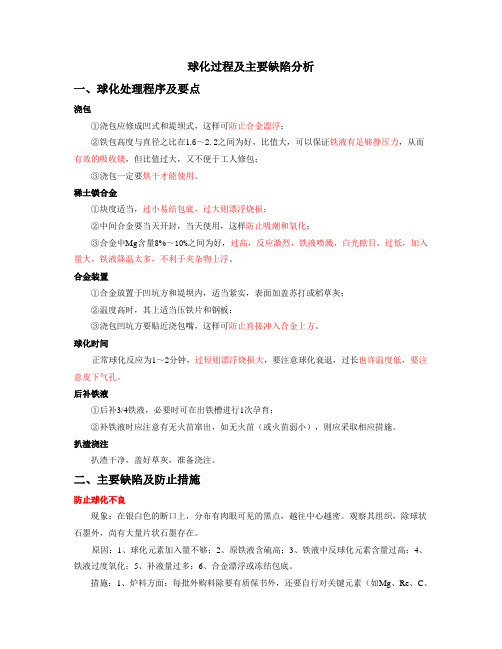
球化过程及主要缺陷分析一、球化处理程序及要点浇包①浇包应修成凹式和堤坝式,这样可防止合金漂浮;②铁包高度与直径之比在1.6~2.2之间为好,比值大,可以保证铁液有足够静压力,从而有效的吸收镁,但比值过大,又不便于工人修包;③浇包一定要烘干才能使用。
稀土镁合金①块度适当,过小易结包底,过大则漂浮烧损;②中间合金要当天开封,当天使用,这样防止吸潮和氧化;③合金中Mg含量8%~10%之间为好,过高,反应激烈,铁液喷溅,白光眩目。
过低,加入量大,铁液降温太多,不利于夹杂物上浮。
合金装置①合金放置于凹坑方和堤坝内,适当紧实,表面加盖苏打或稻草灰;②温度高时,其上适当压铁片和钢板;③浇包凹坑方要贴近浇包嘴,这样可防止直接冲入合金上方。
球化时间正常球化反应为1~2分钟,过短则漂浮烧损大,要注意球化衰退,过长也许温度低,要注意皮下气孔。
后补铁液①后补3/4铁液,必要时可在出铁槽进行1次孕育;②补铁液时应注意有无火苗窜出,如无火苗(或火苗弱小),则应采取相应措施。
扒渣浇注扒渣干净,盖好草灰,准备浇注。
二、主要缺陷及防止措施防止球化不良现象:在银白色的断口上,分布有肉眼可见的黑点,越往中心越密。
观察其组织,除球状石墨外,尚有大量片状石墨存在。
原因:1、球化元素加入量不够;2、原铁液含硫高;3、铁液中反球化元素含量过高;4、铁液过度氧化;5、补液量过多;6、合金漂浮或冻结包底。
措施:1、炉料方面:每批外购料除要有质保书外,还要自行对关键元素(如Mg、Re、C、S、As等)进行检测。
自制合金也要随机抽样化验,并要做到当天熔制当天破碎和使用。
2、熔炼方面:严格按照操作指导书的要求配制铁水,各元素的最终成分应该在一定的变化范围内。
3、处理方面:球化剂不可压得过紧和过松,并且放入包内时间越短越好。
一定要做到定量出液,特别要防止包内进渣,处理后要及时搅拌,扒净浮渣,盖好草灰。
防止皮下气孔现象:经常在铸件上表面的表层内,一般位于表面下0.5m m~3mm处,形成分散细小的圆形或椭圆形光滑孔洞,直径多在1~3mm左右。
东莞球墨铸造厂讲解球墨铸件球化不良、石墨漂浮的缺陷
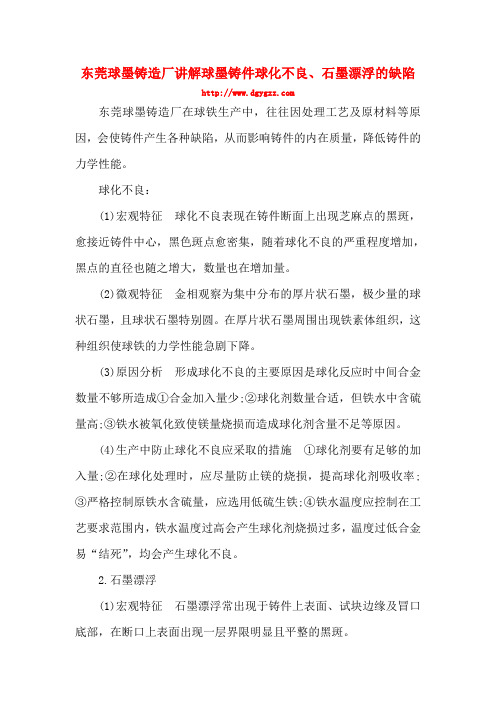
东莞球墨铸造厂讲解球墨铸件球化不良、石墨漂浮的缺陷东莞球墨铸造厂在球铁生产中,往往因处理工艺及原材料等原因,会使铸件产生各种缺陷,从而影响铸件的内在质量,降低铸件的力学性能。
球化不良:(1)宏观特征球化不良表现在铸件断面上出现芝麻点的黑斑,愈接近铸件中心,黑色斑点愈密集,随着球化不良的严重程度增加,黑点的直径也随之增大,数量也在增加量。
(2)微观特征金相观察为集中分布的厚片状石墨,极少量的球状石墨,且球状石墨特别圆。
在厚片状石墨周围出现铁素体组织,这种组织使球铁的力学性能急剧下降。
(3)原因分析形成球化不良的主要原因是球化反应时中间合金数量不够所造成①合金加入量少;②球化剂数量合适,但铁水中含硫量高;③铁水被氧化致使镁量烧损而造成球化剂含量不足等原因。
(4)生产中防止球化不良应采取的措施①球化剂要有足够的加入量;②在球化处理时,应尽量防止镁的烧损,提高球化剂吸收率;③严格控制原铁水含硫量,应选用低硫生铁;④铁水温度应控制在工艺要求范围内,铁水温度过高会产生球化剂烧损过多,温度过低合金易“结死”,均会产生球化不良。
2.石墨漂浮(1)宏观特征石墨漂浮常出现于铸件上表面、试块边缘及冒口底部,在断口上表面出现一层界限明显且平整的黑斑。
(2)微观特征其石墨聚集,呈开花状和枝荔状,有的完全爆裂。
这种组织严重削弱了球铁的力学性能,使材料的强韧性指标明显下降。
(3)原因分析产生石墨漂浮的主要原因为碳硅当量过高(碳当量>4.55%)。
当碳硅当量超过共晶成分,因浇铸温度高,铁水在凝固前就析出石墨,若液态停留一段时间,此时石墨长大并聚集,由于石墨的密度远比铁水轻,聚集石墨易上浮,有时夹杂物也被带到铸件的上表面,从而在铸件上表面产生石墨漂浮;在同等条件下(碳当量相同),铸件愈大,浇铸温度愈高,冷却速度越慢,则铁水在铸型内保持高温液态时间长,石墨有足够的上浮时间,因而石墨漂浮愈严重。
(4)防止石墨漂浮应采取的措施①严格控制碳硅当量,碳不应超过4%,硅不应超过3%,厚大铸件的碳硅量应更低;②提高冷却速度,在壁厚处放置冷铁等;③加入少量强烈阻止石墨化的元素,如加入钼可防止石墨漂浮;④严格控制稀土元素残留量。
球墨铸铁球化不良的预防及改进措施

表1 QT450-10球墨铸铁件性能检验结果
抗拉强度/MPa 屈服强度/MPa 断后伸长率(%) 硬度HBW
试块金相(实测)
产品名
试块编号
称
目标值 实测值
目标 值
实测值 目标值
实测值
目标值
实测值
球化率 (%)
石墨球 铁素体含 大小/级 量(%)
本体球化率(%)
合格
不合格
A102 壳体1
450
275
12.0
(2)孕育作用不强或衰退 孕育衰退产生的原 因主要与孕育剂加入量少或孕育工艺不完善有关。 由于镁的存在是球化的必要条件,而充分的孕育处 理是促进石墨化的保证,因此只讲球化处理而不重 视孕育处理,是生产不出高质量球墨铸铁的。
防止孕育衰退的措施:孕育剂的选用和加入量 要适当,使用含钡、钙的长效孕育剂,采用二次孕 育、随流孕育的复合措施。
163 75
6
80 90(3件) 75~80(2件)
A102复查 壳体1
430
330
5.5
167 75
6
80
—
—
A25
壳体2 ≥450
480 ≥310
345
A25复查 壳体2
480
350
≥10
10.0 160~ 169 12.0 210 160
80 80
6 6
90 91(4件) 85(1件)
85
3 整改措施与效果
铸件球化不良问题出现后,我公司技术、质 量、理化室等部门共同分析,根据生产实际定出了 整改措施。
1)规范操作规程,控制浇注时间。 2)调整开炉次序,第一炉熔炼灰铸铁,利用球 墨铸铁包浇注 (延长浇包的烘烤时间)。
球铁的缺陷和防治
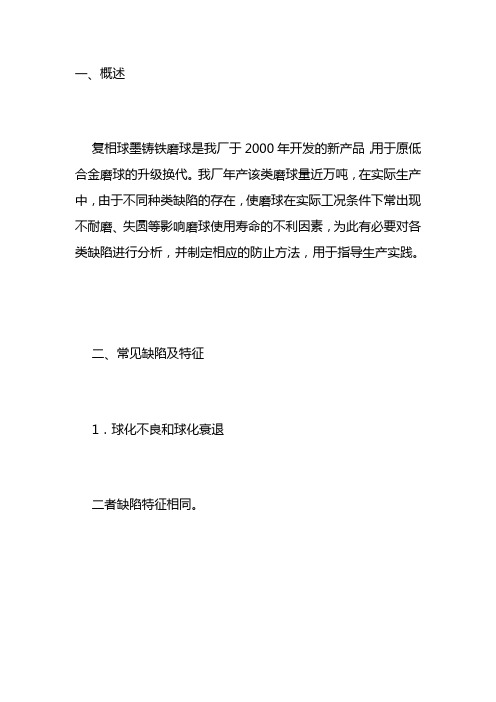
一、概述复相球墨铸铁磨球是我厂于2000年开发的新产品,用于原低合金磨球的升级换代。
我厂年产该类磨球量近万吨,在实际生产中,由于不同种类缺陷的存在,使磨球在实际工况条件下常出现不耐磨、失圆等影响磨球使用寿命的不利因素,为此有必要对各类缺陷进行分析,并制定相应的防止方法,用于指导生产实践。
二、常见缺陷及特征1.球化不良和球化衰退二者缺陷特征相同。
(1)宏观特征铸件断口为银灰色上分布芝麻状黑色斑点,其数量多、直径大,表明程度严重。
若全部呈暗灰色粗晶粒,表明球化不完全。
(2)金相组织集中分布大量厚片状石墨,其数量越多、面积越大,表明程度越严重,球化不完全时呈片状石墨。
(3)产生原因原铁液含硫高,以及严重氧化的炉料中含有过量反球化元素;处理后铁液残留镁和稀土量过低。
铁液中溶解氧量偏高是球化不良的重要原因。
选用低硫焦炭和金属炉料,必要时进行脱硫处理。
另外,应进行废钢除锈,以及增加球化剂中稀土元素用量,严格控制球化工艺。
2.缩孔和缩松特征和产生原因:缩孔产生于铁液温度下降发生一次收缩阶段。
如大气压把表面凝固薄层压陷,则呈现表面凹陷及局部热节凹陷,否则铁液中气体析出至顶部壳中聚集成含气孔的内壁光滑的暗缩孔,有时也与外界相通形成明缩孔,则内表面虽也光滑,但已被氧化。
球墨铸铁共晶凝固时间比灰铸铁长,呈粥状凝固,凝固外壳较薄弱,二次膨胀时在石墨化膨胀力作用下使外壳膨胀,松弛了内部压力。
因此在二次收缩过程中,最后凝固的热节部位内部压力低于大气压,被树枝晶分隔的小熔池处成为真空区,完全凝固后成为孔壁粗糙且排满树枝晶的疏松孔,即缩松缺陷。
宏观缩松产生于热节区残余铁液开始大量凝固的早期,包括了残余铁液的一次收缩和二次收缩,因而尺寸略大且内壁排满枝晶,呈灰暗疏松孔或蝇脚痕状黑点;微观缩松产生于二次收缩末期,共晶团或其集团间的铁液在负压下得不到补缩凝固收缩而成,常见于厚断面处。
3.皮下气孔(1)形貌特征铸件表皮下2~3mm处均匀或蜂窝状分布的球形、椭圆状或针孔状内壁光滑孔洞,直径0.5~3mm,可在热处理和抛丸清理后暴露或机加工时发现,小件中较多。
我公司球化不良问题汇总及措施供大家分享
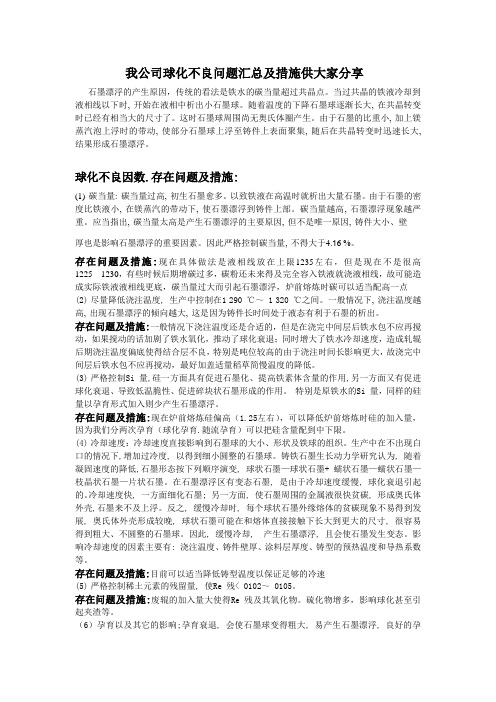
我公司球化不良问题汇总及措施供大家分享石墨漂浮的产生原因,传统的看法是铁水的碳当量超过共晶点。
当过共晶的铁液冷却到液相线以下时, 开始在液相中析出小石墨球。
随着温度的下降石墨球逐渐长大, 在共晶转变时已经有相当大的尺寸了。
这时石墨球周围尚无奥氏体圈产生。
由于石墨的比重小, 加上镁蒸汽泡上浮时的带动, 使部分石墨球上浮至铸件上表面聚集, 随后在共晶转变时迅速长大, 结果形成石墨漂浮。
球化不良因数.存在问题及措施:(1) 碳当量: 碳当量过高, 初生石墨愈多。
以致铁液在高温时就析出大量石墨。
由于石墨的密度比铁液小, 在镁蒸汽的带动下, 使石墨漂浮到铸件上部。
碳当量越高, 石墨漂浮现象越严重。
应当指出, 碳当量太高是产生石墨漂浮的主要原因, 但不是唯一原因, 铸件大小、壁厚也是影响石墨漂浮的重要因素。
因此严格控制碳当量, 不得大于4.16 %。
存在问题及措施:现在具体做法是液相线放在上限1235左右,但是现在不是很高1225---1230,有些时候后期增碳过多,碳粉还未来得及完全容入铁液就浇液相线,故可能造成实际铁液液相线更底,碳当量过大而引起石墨漂浮,炉前熔炼时碳可以适当配高一点(2)尽量降低浇注温度, 生产中控制在1 290 ℃~ 1 320 ℃之间。
一般情况下, 浇注温度越高, 出现石墨漂浮的倾向越大, 这是因为铸件长时间处于液态有利于石墨的析出。
存在问题及措施:一般情况下浇注温度还是合适的,但是在浇完中间层后铁水包不应再搅动,如果搅动的话加剧了铁水氧化,推动了球化衰退;同时增大了铁水冷却速度,造成轧辊后期浇注温度偏底使得结合层不良,特别是吨位较高的由于浇注时间长影响更大,故浇完中间层后铁水包不应再搅动,最好加盖适量稻草简慢温度的降低。
(3)严格控制Si 量,硅一方面具有促进石墨化、提高铁素体含量的作用,另一方面又有促进球化衰退、导致低温脆性、促进碎块状石墨形成的作用。
特别是原铁水的Si 量,同样的硅量以孕育形式加入则少产生石墨漂浮。
球化衰退及球化不良
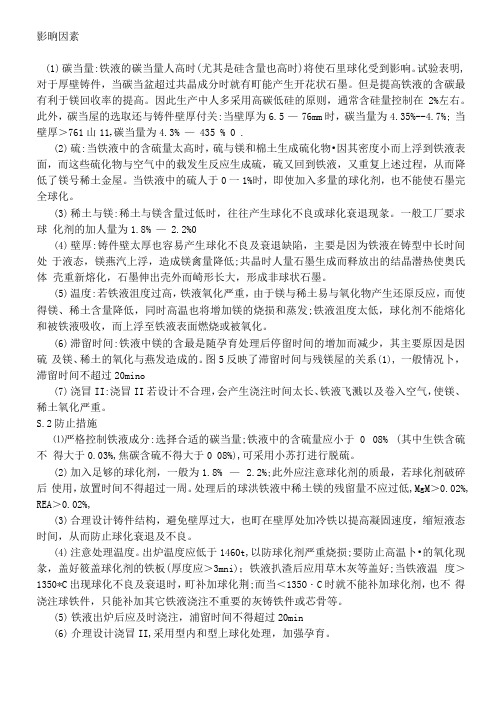
影晌因素(1)碳当量:铁液的碳当量人高时(尤其是硅含量也高时)将使石里球化受到影响。
试验表明, 对于厚壁铸件,当碳当盆超过共晶成分时就有町能产生开花状石墨。
但是提高铁液的含碳最有利于镁回收率的提高。
因此生产中人多采用高碳低硅的原则,通常含硅量控制在2%左右。
此外,碳当屋的选取还与铸件壁厚付关:当壁厚为6.5 —76mm时,碳当量为4.35%--4.7%; 当壁厚>761山117碳当量为4.3% — 435 % 0 .(2)硫:当铁液中的含硫量太高时,硫与镁和棉土生成硫化物•因其密度小而上浮到铁液表面,而这些硫化物与空气中的载发生反应生成硫,硫又回到铁液,又重复上述过程,从而降低了镁号稀土金屋。
当铁液中的硫人于0一1%时,即使加入多量的球化剂,也不能使石墨完全球化。
(3)稀土与镁:稀土与镁含量过低时,往往产生球化不良或球化衰退现彖。
一般工厂要求球化剂的加人量为1.8% — 2.2%0(4)壁厚:铸件壁太厚也容易产生球化不良及衰退缺陷,主要是因为铁液在铸型中长时间处于液态,镁燕汽上浮,造成镁禽量降低;共晶时人量石墨生成而释放出的结晶潜热使奥氏体壳重新熔化,石墨伸出壳外而崎形长大,形成非球状石墨。
(5)温度:若铁液沮度过高,铁液氧化严重,由于镁与稀土易与氧化物产生还原反应,而使得镁、稀土含量降低,同时高温也将增加镁的烧损和蒸发;铁液沮度太低,球化剂不能熔化和被铁液吸收,而上浮至铁液表面燃烧或被氧化。
(6)滞留时间:铁液中镁的含最是随孕育处理后停留时间的增加而减少,其主要原因是因硫及镁、稀土的氧化与燕发造成的。
图5反映了滞留时间与残镁屋的关系(1), 一般情况卜,滞留时间不超过20mino(7)浇冒II:浇冒II若设计不合理,会产生浇注时间太长、铁液飞溅以及卷入空气,使镁、稀土氧化严重。
S.2防止措施⑴严格控制铁液成分:选择合适的碳当量;铁液中的含硫量应小于0 08% (其中生铁含硫不得大于0.03%,焦碳含硫不得大于0 08%),可采用小苏打进行脱硫。
影响球化处理若干因素及应对措施

影响球化处理的若干因素及对策方法。
球墨铸铁定义:球墨铸铁是指铁液在凝固过程中碳以球形石墨析出的铸铁。
影响球化不良、球化衰退的因素有:一.操作原因:1.球化剂未扒平捣实,未按压包要求操作。
对策:将球化剂倒入包坑内,用铁棍扒平捣实,倒入孕育剂后再次扒平捣实,(覆盖1-1.5kg除渣剂)用硅钢片10-15kg覆盖。
2.球化剂未按额定要求称量准确。
对策:保证基本加入量,其重量为20kg/包,并准确称量。
3.出铁时浇包未注意压包方向,铁液直接冲在球化剂上。
对策:必须保证埋包方向靠电炉。
4.出铁速度太慢。
对策:出铁时,前期尽可能快,后期速度开始放缓,以保证铁液的飞溅和铁重的准确性。
5.出铁包残留铁液未倾倒干净。
对策:必须保证每次压包时无铁液残留在包内。
6.出铁量过多。
对策:允许上下波动范围在±50kg,超过该范围必须采取浇注一半后回炉或直接回炉。
7.未及时更换出铁包。
8.对策:要求每炉次更换一次出铁包。
9.未掌握好生产节拍,压球化剂过早或停留时间过长。
对策:需时刻观察造型节拍,不能压包停留时间过长或出铁后等浇注。
10.浇注包内残留铁液过多。
对策:原则上不允许有铁液残留在浇注包内,鉴于各产品重量差异,允许包内残余铁液<30kg。
11.出铁包内渣过多未及时清理。
对策:要求每更换一次球化包就要对包进行一次除渣处理。
12.炉前出铁温度过高。
对策:1)、产品要求浇注温度在1410-1430℃时需增加覆盖用硅钢片18-20kg 或加盖一块钢板。
2)、在压包未知的情况下,如出炉温度过高,反应过快,应减少出铁量或直接回炉处理。
3)、炉前已测得出炉温度过高时应采取打开炉盖,降温到要求温度(依据各产品浇注温度)才可出炉。
二.球化包、浇注原因:1.出铁包、浇包未烘透烘干。
对策:应按照筑包烘包要求进行操作,初次使用的浇包应烫包后才可使用,发现球化时有大量浓烟,浇注包外有大量水蒸汽冒出时,应回炉处理。
2.球化包堤坝太矮或包坑太小。
球墨铸铁件常见缺陷的分析与对策(1)
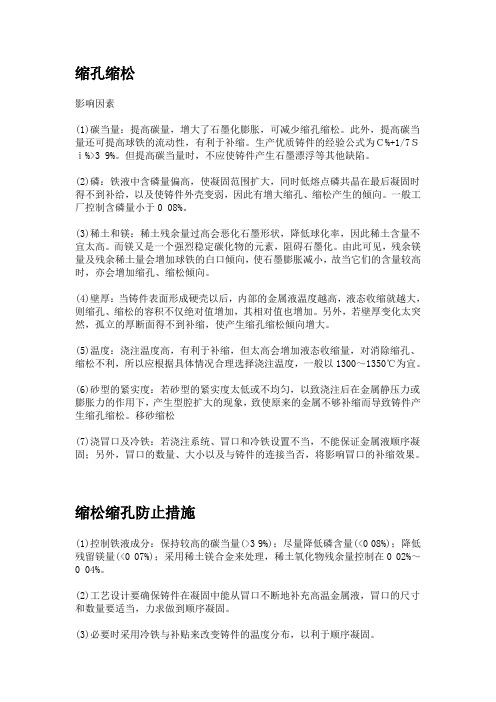
缩孔缩松影响因素(1)碳当量:提高碳量,增大了石墨化膨胀,可减少缩孔缩松。
此外,提高碳当量还可提高球铁的流动性,有利于补缩。
生产优质铸件的经验公式为C%+1/7Si%>3 9%。
但提高碳当量时,不应使铸件产生石墨漂浮等其他缺陷。
(2)磷:铁液中含磷量偏高,使凝固范围扩大,同时低熔点磷共晶在最后凝固时得不到补给,以及使铸件外壳变弱,因此有增大缩孔、缩松产生的倾向。
一般工厂控制含磷量小于0 08%。
(3)稀土和镁:稀土残余量过高会恶化石墨形状,降低球化率,因此稀土含量不宜太高。
而镁又是一个强烈稳定碳化物的元素,阻碍石墨化。
由此可见,残余镁量及残余稀土量会增加球铁的白口倾向,使石墨膨胀减小,故当它们的含量较高时,亦会增加缩孔、缩松倾向。
(4)壁厚:当铸件表面形成硬壳以后,内部的金属液温度越高,液态收缩就越大,则缩孔、缩松的容积不仅绝对值增加,其相对值也增加。
另外,若壁厚变化太突然,孤立的厚断面得不到补缩,使产生缩孔缩松倾向增大。
(5)温度:浇注温度高,有利于补缩,但太高会增加液态收缩量,对消除缩孔、缩松不利,所以应根据具体情况合理选择浇注温度,一般以1300~1350℃为宜。
(6)砂型的紧实度:若砂型的紧实度太低或不均匀,以致浇注后在金属静压力或膨胀力的作用下,产生型腔扩大的现象,致使原来的金属不够补缩而导致铸件产生缩孔缩松。
移砂缩松(7)浇冒口及冷铁:若浇注系统、冒口和冷铁设置不当,不能保证金属液顺序凝固;另外,冒口的数量、大小以及与铸件的连接当否,将影响冒口的补缩效果。
缩松缩孔防止措施(1)控制铁液成分:保持较高的碳当量(>3 9%);尽量降低磷含量(<0 08%);降低残留镁量(<0 07%);采用稀土镁合金来处理,稀土氧化物残余量控制在0 02%~0 04%。
(2)工艺设计要确保铸件在凝固中能从冒口不断地补充高温金属液,冒口的尺寸和数量要适当,力求做到顺序凝固。
(3)必要时采用冷铁与补贴来改变铸件的温度分布,以利于顺序凝固。
铸件球化率不良,最典型的3种解决方法

铸件球化率不良,最典型的3种解决方法1)原铁水含硫量高硫是反球化率元素,它与镁有很强的亲和力,反应生成MgS,而消耗了有效镁,因而导致球化不良,此时需要多加球化剂才能保证球化,生产高品质的球铁,其原始铁液的含硫量,国外一般都控制在0.02%高于此量都必须进行脱硫处理,这样既保证了充分的球化也减少了产生渣孔的危险,同时球化剂的加入量才得以稳定,也确保了残余镁量波动不大,我国的现实情况是,冲天炉的原铁水含硫量一般为0.05-0.06%或以上,中频炉铁水的含硫量一般为0.02-0.035%,但大多数厂家不做脱硫处理,而靠变动球化剂的量来保证球化,其加入量国内各厂差别很大,在0.8-1.8%大范围内波动,而残镁量的范围介于0.03-0.08%常常出现球化不良或过球化现象,含镁量过高造成了铸件渣孔,缩松,反白口缺陷,含镁过高,石墨也会变坏,很多厂为了确保球化良好往往在晶间出现水草状石墨。
要得到好的球化效果,还要注意Mg残/S残的比例合适,壁厚少于15mm的小铸件,范围在2.7-4.0之间,易产生收缩的铸件(特别是热节处无补缩能力时)应控制在2.4-3.0%之间,壁厚在15-30mm 之间的铸件,范围在3.0-4.5%之间,易缩件在2.7-3.5%之间,壁厚大于30mm的厚铸件,范围在3.5-5之间就是说薄铸件镁要低点以免产生白口,热节易生缩松的铸件,镁应低为好,厚铸件镁要高,以弥补镁蒸气逃逸损失,不至于使镁量降低而导致不球化。
原始含硫量过低(<0.005%)也是不所希望的,因这样的原铁液会孕育不良,容易生成碳化物,去年河南某厂采用喂丝工艺生产球铁,原铁水含硫量已低于0.006%,加入的球化剂没减少,因而铸件产生了30%以上的渗碳体,实践证明,球铁原铁液中的硫对球铁铸件的石墨球数和石墨尺寸分布有很大影响,由于石墨球数随硫含量的增加而增加,所以在生产白口倾向较大的薄壁铸件时,采用较高的含硫量,是防止碳化物形成的有效措施。
球化退火的缺陷

球化退火的缺陷
(实用版)
目录
1.球化退火的概念和作用
2.球化退火的缺陷概述
3.球化退火缺陷的具体表现
4.球化退火缺陷的影响和解决方法
正文
球化退火是一种钢铁热处理工艺,其主要目的是通过加热和冷却的过程,使钢铁内部的晶粒结构变得更加均匀,从而提高其性能和可加工性。
然而,这种工艺也存在一些缺陷,可能会影响钢铁的质量和使用效果。
首先,球化退火可能会导致钢铁内部的晶粒过大。
在球化退火的过程中,钢铁会经历一系列的温度变化,如果控制不当,就可能导致晶粒生长过大,从而影响钢铁的性能。
过大的晶粒会使钢铁的强度和硬度降低,使其更容易变形和断裂。
其次,球化退火可能会导致钢铁的表面出现氧化和脱碳现象。
在加热过程中,钢铁表面的氧化物和碳化物可能会被烧掉,从而形成氧化层和脱碳层。
这些层的存在会降低钢铁的硬度和强度,影响其使用寿命。
此外,球化退火还可能会导致钢铁的组织不均匀。
在冷却过程中,如果温度下降过快,就可能导致钢铁内部出现不同的相,从而形成组织不均匀的情况。
这种情况会使钢铁的性能不稳定,影响其使用效果。
对于球化退火缺陷的影响和解决方法,我们可以从以下几个方面进行考虑。
首先,可以通过优化退火工艺,如严格控制加热和冷却的温度和速度,来避免晶粒过大和组织不均匀的问题。
其次,可以在退火后进行表面处理,如喷砂和抛光,来去除氧化层和脱碳层,提高钢铁的表面质量。
【热坛学习】谈谈关于树脂砂球铁件表层球化不良的问题
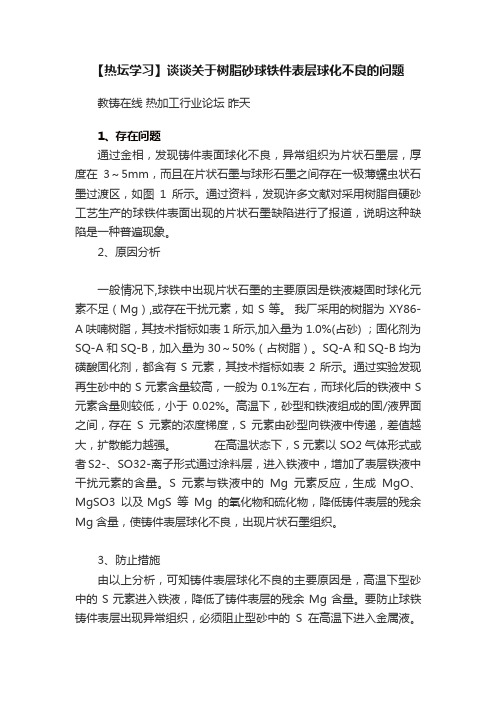
【热坛学习】谈谈关于树脂砂球铁件表层球化不良的问题教铸在线热加工行业论坛昨天1、存在问题通过金相,发现铸件表面球化不良,异常组织为片状石墨层,厚度在3~5mm,而且在片状石墨与球形石墨之间存在一极薄蠕虫状石墨过渡区,如图1所示。
通过资料,发现许多文献对采用树脂自硬砂工艺生产的球铁件表面出现的片状石墨缺陷进行了报道,说明这种缺陷是一种普遍现象。
2、原因分析一般情况下,球铁中出现片状石墨的主要原因是铁液凝固时球化元素不足(Mg),或存在干扰元素,如S等。
我厂采用的树脂为XY86-A呋喃树脂,其技术指标如表1所示,加入量为1.0%(占砂) ;固化剂为SQ-A和SQ-B,加入量为30~50%(占树脂)。
SQ-A和SQ-B均为磺酸固化剂,都含有S元素,其技术指标如表2所示。
通过实验发现再生砂中的S元素含量较高,一般为0.1%左右,而球化后的铁液中S 元素含量则较低,小于0.02%。
高温下,砂型和铁液组成的固/液界面之间,存在S元素的浓度梯度,S元素由砂型向铁液中传递,差值越大,扩散能力越强。
在高温状态下,S元素以SO2气体形式或者S2-、SO32-离子形式通过涂料层,进入铁液中,增加了表层铁液中干扰元素的含量。
S元素与铁液中的Mg元素反应,生成MgO、MgSO3以及 MgS等Mg的氧化物和硫化物,降低铸件表层的残余Mg含量,使铸件表层球化不良,出现片状石墨组织。
3、防止措施由以上分析,可知铸件表层球化不良的主要原因是,高温下型砂中的S元素进入铁液,降低了铸件表层的残余Mg含量。
要防止球铁铸件表层出现异常组织,必须阻止型砂中的S在高温下进入金属液。
可以从三个方面解决这个问题:一是降低型砂中S元素的含量,减少传递源;二是采取措施,阻止S元素由型砂向铁液的传递,从传递过程上解决;第三则是增加铁水中残余Mg含量,抵消S 的影响。
具体有以下几种方法:3.1减少传递源(1)降低再生砂的灼烧减量再生砂中的硫元素与再生砂的灼烧减量有一定的比例关系。
球铁及其球化不良问题探讨分析解读
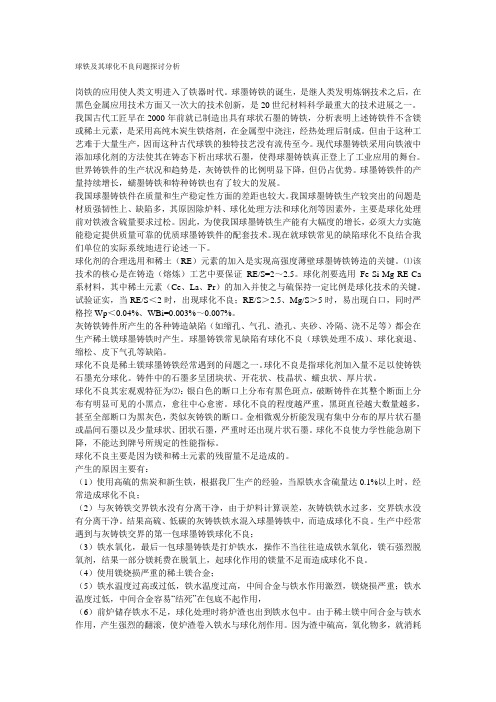
球铁及其球化不良问题探讨分析岗铁的应用使人类文明进入了铁器时代。
球墨铸铁的诞生,是继人类发明炼钢技术之后,在黑色金属应用技术方面又一次大的技术创新,是20世纪材料科学最重大的技术进展之一。
我国古代工匠早在2000年前就已制造出具有球状石墨的铸铁,分析表明上述铸铁件不含镁或稀土元素,是采用高纯木炭生铁熔剂,在金属型中浇注,经热处理后制成。
但由于这种工艺难于大量生产,因而这种古代球铁的独特技艺没有流传至今。
现代球墨铸铁采用向铁液中添加球化剂的方法使其在铸态下析出球状石墨,使得球墨铸铁真正登上了工业应用的舞台。
世界铸铁件的生产状况和趋势是,灰铸铁件的比例明显下降,但仍占优势。
球墨铸铁件的产量持续增长,蠕墨铸铁和特种铸铁也有了较大的发展。
我国球墨铸铁件在质量和生产稳定性方面的差距也较大。
我国球墨铸铁生产较突出的问题是材质强韧性上、缺陷多,其原因除炉料、球化处理方法和球化剂等因素外,主要是球化处理前对铁液含硫量要求过松。
因此,为使我国球墨铸铁生产能有大幅度的增长,必须大力实施能稳定提供质量可靠的优质球墨铸铁件的配套技术。
现在就球铁常见的缺陷球化不良结合我们单位的实际系统地进行论述一下。
球化剂的合理选用和稀土(RE)元素的加入是实现高强度薄壁球墨铸铁铸造的关键。
⑴该技术的核心是在铸造(熔炼)工艺中要保证RE/S=2~2.5。
球化剂要选用Fe-Si-Mg-RE-Ca 系材料,其中稀土元素(Ce、La、Pr)的加入并使之与硫保持一定比例是球化技术的关键。
试验证实,当RE/S<2时,出现球化不良;RE/S>2.5、Mg/S>5时,易出现白口,同时严格控Wp<0.04%、WBi=0.003%~0.007%。
灰铸铁铸件所产生的各种铸造缺陷(如缩孔、气孔、渣孔、夹砂、冷隔、浇不足等)都会在生产稀土镁球墨铸铁时产生。
球墨铸铁常见缺陷有球化不良(球铁处理不成)、球化衰退、缩松、皮下气孔等缺陷。
球化不良是稀土镁球墨铸铁经常遇到的问题之一。
模具热处理常见缺陷及其解决方案
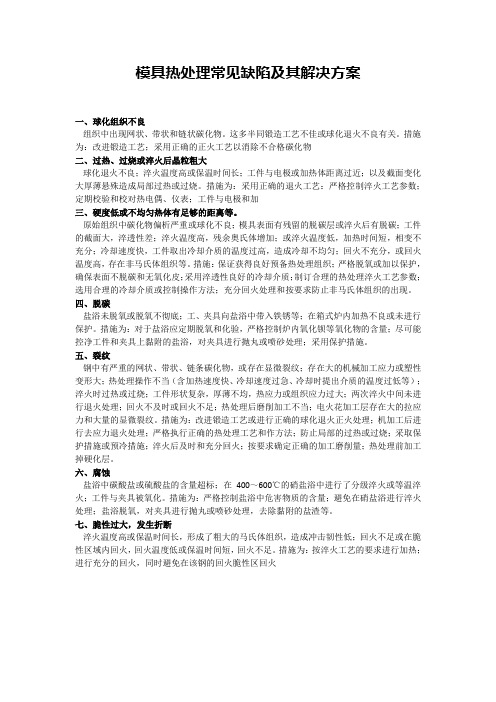
模具热处理常见缺陷及其解决方案一、球化组织不良组织中出现网状、带状和链状碳化物。
这多半同锻造工艺不佳或球化退火不良有关。
措施为:改进锻造工艺;采用正确的正火工艺以消除不合格碳化物二、过热、过烧或淬火后晶粒粗大球化退火不良;淬火温度高或保温时间长;工件与电极或加热体距离过近;以及截面变化大厚薄悬殊造成局部过热或过烧。
措施为:采用正确的退火工艺:严格控制淬火工艺参数;定期校验和校对热电偶、仪表;工件与电极和加三、硬度低或不均匀热体有足够的距离等。
原始组织中碳化物偏析严重或球化不良;模具表面有残留的脱碳层或淬火后有脱碳;工件的截面大,淬透性差;淬火温度高,残余奥氏体增加;或淬火温度低,加热时间短,相变不充分;冷却速度快,工件取出冷却介质的温度过高,造成冷却不均匀;回火不充分,或回火温度高,存在非马氏体组织等。
措施:保证获得良好预备热处理组织;严格脱氧或加以保护,确保表面不脱碳和无氧化皮;采用淬透性良好的冷却介质;制订合理的热处理淬火工艺参数;选用合理的冷却介质或控制操作方法;充分回火处理和按要求防止非马氏体组织的出现。
四、脱碳盐浴未脱氧或脱氧不彻底;工、夹具向盐浴中带入铁锈等;在箱式炉内加热不良或未进行保护。
措施为:对于盐浴应定期脱氧和化验,严格控制炉内氧化钡等氧化物的含量;尽可能控净工件和夹具上黏附的盐浴,对夹具进行抛丸或喷砂处理;采用保护措施。
五、裂纹钢中有严重的网状、带状、链条碳化物,或存在显微裂纹;存在大的机械加工应力或塑性变形大;热处理操作不当(含加热速度快、冷却速度过急、冷却时提出介质的温度过低等);淬火时过热或过烧;工件形状复杂,厚薄不均,热应力或组织应力过大;两次淬火中间未进行退火处理;回火不及时或回火不足;热处理后磨削加工不当;电火花加工层存在大的拉应力和大量的显微裂纹。
措施为:改进锻造工艺或进行正确的球化退火正火处理;机加工后进行去应力退火处理;严格执行正确的热处理工艺和作方法;防止局部的过热或过烧;采取保护措施或预冷措施;淬火后及时和充分回火;按要求确定正确的加工磨削量;热处理前加工掉硬化层。
铸造球铁件,球化过程常见问题及解决方案
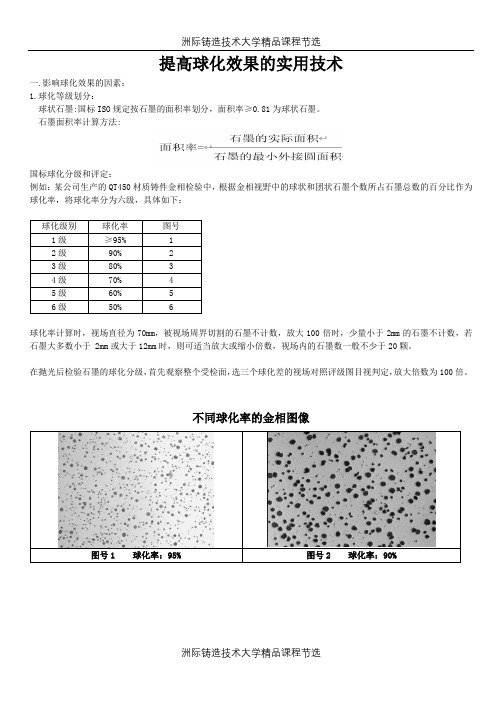
提高球化效果的实用技术一.影响球化效果的因素:1.球化等级划分:球状石墨:国标ISO规定按石墨的面积率划分,面积率≥0.81为球状石墨。
石墨面积率计算方法:国标球化分级和评定:例如:某公司生产的QT450材质铸件金相检验中,根据金相视野中的球状和团状石墨个数所占石墨总数的百分比作为球化率,将球化率分为六级,具体如下:球化率计算时,视场直径为70mm,被视场周界切割的石墨不计数,放大100倍时,少量小于2mm的石墨不计数,若石墨大多数小于 2mm或大于12mm时,则可适当放大或缩小倍数,视场内的石墨数一般不少于20颗。
在抛光后检验石墨的球化分级,首先观察整个受检面,选三个球化差的视场对照评级图目视判定,放大倍数为100倍。
不同球化率的金相图像图号1 球化率:95% 图号2 球化率:90%图号3 球化率:80% 图号4 球化率:70%图号5 球化率:60% 图号6 球化率:50%2.球化可能会出现的问题及解决方案:(1)球化不良:此不良主要体现在炉后成品的残镁分析值低于0.030%(一般标准残镁规格值按照小于0.030%为下限规格值),金相石墨型态一般体现在球状石墨和蠕虫状石墨共存在,或球状石墨、蠕虫状石墨和片状石墨共存在,或蠕虫状石墨和片状石墨共存在,或全部为片状石墨。
控制球化不良的发生,特别注意以下几点:A.添加球化剂重量的核对或喂丝球化线的喂丝长度核对,确保实际加入量与标准规定的相符。
B.三明治球化温度或喂丝温度一般在1480-1530℃。
C.三明治球化反应时间一般控制大于55秒,喂丝球化速度一般控制19-22米/分钟。
D.三明治球化出炉过程确保电炉的先期铁水冲入到球化包的缓冲室,等缓冲室铁水满后,铁水再漫过球化室。
(有很多出炉铁水冲入不当,造成铁水直接冲到球化室的,造成球化反应提前进行,总的球化反应时间短,导致球化不良。
)E.三明治球化需要在球化包之球化室中的球化剂上侧放置覆盖剂,覆盖剂一般为矽钢片,厚度一般控制在0.3-1.0mm,直径或单边长度为10-30mm,要求无油无锈无杂质。
- 1、下载文档前请自行甄别文档内容的完整性,平台不提供额外的编辑、内容补充、找答案等附加服务。
- 2、"仅部分预览"的文档,不可在线预览部分如存在完整性等问题,可反馈申请退款(可完整预览的文档不适用该条件!)。
- 3、如文档侵犯您的权益,请联系客服反馈,我们会尽快为您处理(人工客服工作时间:9:00-18:30)。
2〕预防措施 ① 测球化前首温,管制1530℃↓ ② 针对低温产品,要求出铁温度低时,铁水倒入球化桶内,人 工晃动球化桶让其完全球化反应,且时间不可超过180秒。 ③ 球化剂、覆盖剂填埋松一点。
④ 确保桶内无残余铁水,及按规定进行洗锅,避免球化剂烧损。
FUJIWA MACHINERY INDUSTRY (KUNSHAN) CO., LTD.
每包压包前后均要检查球化室情况,待铁水包冷下来后 应该用棍子将球化室中的渣滓戳干净。
出水如果发现异常立即停止出水,将铁水回炉进行确认 球化。
FUJIWA MACHINERY INDUSTRY (KUNSHAN) CO., LTD.
五、操作细节问题
2、包温过高,球化剂的Mg吸收率低 1)现象
球化包内壁超过温度900℃,内壁通红!(球化包温度也 不能过低,应500℃↑,否则影响浇注温度)。
③ 加球化剂的漏斗放在球化桶上,必须确认漏斗口是否对准球化室;
④ 做一个放料盆的搁架,依照顺序放球化剂、孕育剂、覆盖剂,从料架上依次取 用球化辅料;
⑤ 倒空的球化剂、孕育剂、覆盖剂的空盆,必需放回料架;
⑥ 球化人员必需注意每桶的球化状况;
⑦ 各种料盆,使用喷上不同颜色和原料名称,搁架上贴标签,比如球化剂标识为 绿底黑字。称量球化剂的盆子刷成绿色,且摆的顺序由上而下为球化剂、覆盖 剂、孕育剂;
FUJIWA MACHINERY INDUSTRY (KUNSHAN) CO., LTD.
七、有害元素问题
1)现象 ①要求球化3级以下的球铁件,铸件S控制0.02%↓,要求球化1级的转向节 类0.015%↓。Ti分别控制到0.02%和0.018%↓, ②铁液中过量的硫与球化剂中的Mg反应生成MgO,造成用于球化的镁减 少,造成球化不良
②球化剂的重量偏差
球化反应不激励 易球化衰退
球化反应正常
Si,Mg元素超标
2〕预防措施
① 品证对进料严格把关,并不定期送第三方分析。
②-1称量之前先在辅料挂好相关的标准书。 ②-2依照标准书用电子台称称好规定量,球化剂误差不得超过±0.1kg。 ②-3AT、AC对其进行抽检,并做记录。 ②-4球化前放入电子台称再次确认其重量。 ②-5定期对台称(电子称)进行校验。
FUJIWA MACHINERY INDUSTRY (KUNSHAN) CO., LTD.
二、出炉重量过高或过低,超过标准要求
1)现象:误差超过±10KG 2)原理:铁水超过标准要求,相对球化剂量偏少,炉后 化学成分表现为镁偏低0.025%↓,同时表现为Si也偏低。 3)措施: 1、培训员工,严格按标准执行
绿色盆装球化剂
FUJIWA MACHINERY INDUSTRY (KUNSHAN) CO., LTD.
六、球化剂质量 1)现象
①球化剂粒度较小,或粉末过多 放入高温的球化室后,很快氧化或汽化,使得球化剂的Mg吸收率
降低。 经验证,在同等生产条件下,我司三种球化剂的Mg吸收率如下:
埃肯5922:65-75%,镇江ZDSA-5A:55-65%楚峰6-1:50-60%。 ②球化剂粒度太大
⑧ 称辅料时必须依照此产品的标准书,称辅料时一个产品为一个批次全部称好, 放搁架上;
⑨ 规定向球化桶内倾倒铁水时间不可超过15秒,由取样人员确认及球化人员自主 确认;
FUJIWA MACHINERY INDUSTRY (KUNSHAN) CO., LTD.
五、球化操作细节
加料器对准球化室
球化过程
球化剂的标识
FUJIWA MACHINERY INDUSTRY (KUNSHAN) CO., LTD.
六、球化剂对球化的影响
球化剂和硅铁粒
辅料在台称上确认
添加完球化辅料确认
FUJIWA MACHINERY INDUSTRY (KUNSHAN) CO., LTD.
六球化剂对球化的影响
1〕不良原因
①球化剂纯度偏低 球化反应不激励 易球化不良
FUJIWA MACHINERY INDUSTRY (KUNSHAN) CO., LTD.
一、出水速度
现象:出铁水慢,甚至超过1分钟,特别是最后一包铁水极 易出现此种情况。
原理:镁蒸汽有部分散失到空气中,在铁水中的吸收率低, 炉后化学成分表现为镁偏低,0.025%↓ 措施:
1、培训作业员,保证出水速度。 2、修订标准书,最后一包中可以将球化剂加入量增加0.1%。 3、炉内留0.5T↑起熔铁水。
③少量的Ti就会造成石墨畸变,并且Ti有很强的还原性,会把铁液中的Pb 等有害元素还原出来,对石墨的圆整度造成影响,并且Ti会导致反白口产 生
④铁水保温时间过长,或废钢严重氧化生锈,导致球化剂Mg与O反应,消 耗Mg。 2)预防措施 ①灰铁转球铁时,出空铁水,避免S超标。 ②避免回炉料混料,导致铁水S超标。 ③使用优质废钢(比如08Al)降低球铁的Ti含量。 ④拒绝使用氧化严重的废钢。
九、成分和金相检验控制
1)我们的球化控制方式 ①每一炉原铁水和铸件铁水光谱检查,控制Mg>0.03%→没有监控到每一球化包? ②铁水球化率仪→监控了每一球化包! ③快速金相→取铁豆???有问题!没有每一包检查? ④对于马上直接卖毛坯的铸件,我们没有100%超声波球化率检查! 2)原因 ①每一包的球化失败风险是不一样的。 ②球化剂质量一般时,Mg>0.03%对于壁厚在25mm以下是适宜的,否则不适宜。 ③铁豆子因冷却速度快,而且有时含高S的渣,会造成误判。 3)预防措施 ①每包取浇注包剩余铁水或浇口杯铁水,浇注φ20棒,检验员截断后看棒中心金相。因为有铁
球化反应较正常时冒的白光要更加的剧烈,因为铁水沸 腾严重,甚至溅射出来,导致Mg的吸收率低,炉后化学成分 表现为镁偏低,0.025%↓。 2)措施
连续生产时,如果球化包温度降不下来,使用2个球化包, 交替使用。镁的吸收率在50%以上才是正常的。
或者使用压缩空气,将球化包内腔吹一下。
FUJIWA MACHINERY INDUSTRY (KUNSHAN) CO., LTD.
八、球化室对球化的影响
1〕不良原因 ①球化室过小 装不下球化剂和覆盖剂 铁水当倒入即球
化 球化率不合格 ②球化室过大 铁水易冲到覆盖剂 瞬间球化反应
球化率不合格 2〕预防措施 ① 通过计算制作球化室模型,使之尺寸统一。 ② 一个球化桶最多使用炉数不可超过11炉;且使用过程中要对
球化室内的粘渣清除。
FUJIWA MACHINERY INDUSTRY (KUNSHAN) CO., LTD.
FUJIWA MACHINERY INDUSTRY (KUNSHAN) CO., LTD.
五、操作细节问题
2)、预防措施
① 当浇注机回到轨道时,在浇注线旁做一个标记,浇注机开过标记,马上向球化 桶内加球化辅料;
② 浇注机内做一个装置,剩余铁水不足标准时(根据各产品取不同残余铁水量), 浇注人员按下通知按钮;
⑤铁水熔化后保温时间过长(超过30分钟),使用优质增碳剂、生铁、碳
FUJIWA MACHINERY INDUSTRY (KUNSHAN) CO., LTD.
八、球化室对球化的影响
未使用前的球化室
使用过的球化室
FUJIWA MACHINERY INDUSTRY (KUNSHAN) CO., LTD.
FUJIWA MACHINERY INDUSTRY (KUNSHAN) CO., LTD.
FUJIWA MACHINERY INDUSTRY (KUNSHAN) CO., LTD.
众所周知,我们生产球铁是使用的球方式为三明 法;其中部分产品为保安部品,所以做出合格球化率 的是非常至关重要的事项,才能避免可怕的事情发生, 把合格的产品交到客户手上是我们每个人应尽的职责, 也是我们生存之本!!!
FUJIWA MACHINERY INDUSTRY (KUNSHAN) CO., LTD.
三、铁水温对球化的影响
1)现象 铁水温度高1530℃↑ ,瞬间进行球化反应,导致铁水中镁的
吸收率低,炉后化学成分表现为镁偏低,0.025%↓。 温度过低1480℃↓ ,合金不能迅速熔化,最后球化剂飘在
铁水面上燃烧,镁没有被吸收,被当做渣扒掉。
四、浇注时间长
1)现象 ① 超出浇注管制时间(不要超过10分钟) →球化衰退→球化
率不合格 ② 球化之后铁水中的Mg含量会随着时间减少,导致球化变差;
浇注时间过长,铁水温度低之后,随流孕育剂无法溶解, 导致球化变差(随流孕育剂的熔点一般是1320℃↑).生产过 程违规是超过标准要求的时间还在继续浇注,以及将多余 的铁水倒入废型,将废型浇满导致的球化不良 2)预防措施 ① 利用浇注管制灯(报警灯)进行管制,管制时间为10分钟; ② 管制灯列入浇注每天点检范围内。
FUJIWA MACHINERY INDUSTRY (KUNSHAN) CO., LTD.
产生球化不良的主要方面
一. 出水速度太慢 二. 出水重量过高、过低 三. 铁水温度过高、过低 四. 浇注时间长 五. 操作细节问题 六. 球化剂问题 七. 有害元素问题 八. 球化室对球化的影响 九. 成分和金相检验控制
球化剂颗粒是慢慢从底部浮起来的过程中溶解吸收的,,粒度大的 颗粒浮倒铁水表面才燃烧,没有被吸收。 ③球化剂生产和存储过程中,因时间长、潮湿而氧化。
2)预防措施 ①1~2吨的球化包,球化剂的粒度范围6-25mm比较合理。 ②使用过程中观察球化剂粒度,过大或过小颗粒的球化剂拒绝使用。 ③观察球化剂包装上的生产日期,保存时间超过半年或1年的球化剂拒 绝使用。 ④潮湿的球化剂拒绝使用。