集散型计算机控制系统
08第八章 计算机集散控制系统

但是集中型计算机控制存在三个主要问题:
①.集中的脆弱性:集中控制使危险也集中, 一旦计算机系统发生故障,将导致生产过程 的全面瘫痪; ②.计算机的负荷:由于计算机控制回路多, 计算机的负荷过重,导致控制性能降低; ③ .系统开发周期和人才利用:由于计算机 控制的应用面越来越广,计算机控制系统的 规模和复杂性越来越大,造成开发周期增加, 人力资源难以组织。
进入20世纪70年代后,随着大规模集成电路 的问世,微处理器诞生,以及控制技术﹑显示 技术﹑计算机技术﹑通信技术等进一步发展, 产生了新型的计算机控制系统——集散控制系 统,它按控制功能或按区域分散配置若干个控 制站,每个控制站可控制几个﹑十几个或几十 个回路,从而实现了控制功能分散,使得危险 也得以分散。系统中使用多台屏幕显示器进行 监视﹑操作和管理,系统中各控制站通过完全 双重化的数据通信系统连接起来。
这一阶段的代表产品有美国Honeywell公 司的TDC2000,它是一个具有许多微处理器的 分级控制系统,以分散的控制设备来适应分散 的过程对象,并将它们通过数据高速公路与基 于CRT的操作站相连接,互相协调,实现对工 业过程的控制和监视,达到掌握全局的目的。 系统克服了集中型计算机控制系统的致命弱点, 实现了控制系统的功能分散﹑负荷分散,从而 危险也分散。这个阶段比较著名的产品还有 Bailey公司的NetWork90,Foxboro公司的 Spectrum,日本横河的CENTUM 等。
1975年,美国 Honeywell公司首次向世界 范围推出TDC2000系统,随之世界各大仪表制 造公司也推出各自的集散控制系统,从而使过 程控制进入集散控制系统时期。集散控制系统 的发展大体可分为三个阶段,每个阶段的技术 重点表现如下:
第一阶段:1975~1980年, 以微处理器 为基础的过程控制单元,实现多种控制功能算 法,并实现分散控制:采用带显示器的操作站, 与过程控制单元分离,实现集中监视﹑集中操 作﹑信息综合管理;采用较先进的冗余通信系 统﹑用同轴电缆做传输媒质,实现控制单元与 操作站的通信。
集散型控制系统
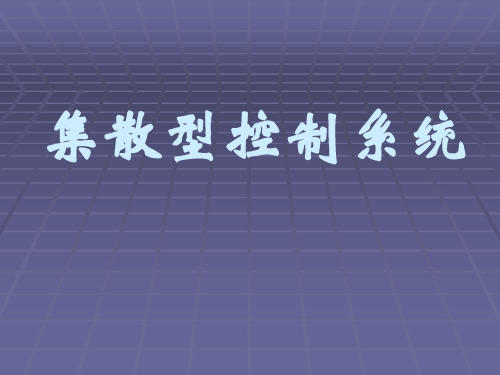
现场总线(Fieldbus)的概念
•现场总线是安装在生产过程区域的现场设备/仪表与控制室内的
自动控制装置/系统之间的一种串行、数字式、多点通信的数据总 线。
•现场总线是以单个分散的、数字化、智能化的测量和控制设备
作为网络节点,用总线相连接,实现相互交换信息,共同完成自 动控制功能的网络系统与控制系统。
现场总线的分类
•基金会现场总线(FF):主要用于过程自动化、楼宇自动化 •PROFIBUS: 有全球最多的供货厂商数;国际化、开放式、不
依赖于设备生产商的现场总线标准;ห้องสมุดไป่ตู้泛适用于各种自动化领域。
•LonWorks:是以单个分散的、数字化、智能化的测量 •CAN (Control Area Network): 低成本,高互连;特别适合
传统的现场级与车间级自动化监控及信息集成系统
缺点:
•信息集成能力不强: 控制器获取信息量有限,大量的数据如
设备参数、故障及故障纪录等数据很难得到。底层数据不全、信 息集成能力不强,不能完全满足CIMS系统对底层数据的要求。
•系统不开放、可集成性差、专业性不强:不同厂家产品之
间缺乏互操作性、互换性,因此可集成性差。这种系统很少留出 接口,允许其它厂商将自己专长的控制技术,如控制算法、工艺 流程、配方等集成到通用系统中去。
集散型控制系统
集散控制系统的概念 集散控制系统的发展历史 集散控制系统的现状 集散控制系统的发展趋势 集散控制系统的特点 集散控制系统的组成 集散控制系统的工作原理 国产化DCS的发展目标
集散控制系统的概念
集散控制系统(Distributed Control System简 称DCS)也叫分布控制系统。它是利用计算机技术对 生产过程进行集中监测、操作、管理和分散控制的 一种新型控制技术。是由计算机技术、信号处理技 术、测量控制技术、通讯网络技术、CRT技术、图形 显示技术及人机接口技术相互渗透发展而产生的。 它是相对于集中式控制系统而言的一种新型计算机 控制系统,是在集中式控制系统的基础上发展、演 变而来的。在系统功能方 面,集散控制系统(DCS) 和集中式控制系统的区别不 大,但在系统功能的实现方 法上却完全不同。
20__集散控制系统

三、 DCS实例-PCS7过程控制系统
SIMATIC PCS 7是一种新型过程控制系统。它提出了一种全 集成自动化(Totally Integrated Automation, TIA)理念,具 有统一的数据管理、通信和组态功能。 PCS 7 采用了TIA 系列的标准硬件和软件,基本部件包括自 动化系统、分布式I/O、操作员站、工程师站和通信网络。
同智能调节器一样,PLC的高可靠性和不断增强的功能, 使它既可以在小型控制系统中担当控制主角,又可以作 为大型集散控制系统中最基层的一种控制单元
> 硬件结构-集中操作监控级
集中操作监控级是面向现场操作员和系统工程师的。
集中操作监控级以操作监视为主要任务-把过程参数的信息集中 化,对各个现场控制站的数据进行收集,并通过简单的操作,进 行工程量的显示、各种工艺流程图的显示、趋势曲线的显示以及 改变过程参数(如设定值、控制参数、报警状态等信息);另一 个任务是兼有部分管理功能:进行控制系统的组态与生成。
注意:控制仪表和运行人员在地理上的集中,控制器分别完 成各控制任务,故障影响不大——运行管理的集中,仍然分 散控制; 采用气动单元组合仪表、电动单元组合仪表和组件组装式仪 表。
过程控制系统的发展史
过程控制系统的发展史
过程控制系统的发展史
3. 50年代末60年代初:集中控制方式
计算机进入过程控制领域,一台计算机控制全厂的生产过程, 整个系统控制任务的集中。 特点:控制集中、管理集中 缺点:受硬件水平限制,计算机可靠性低,一旦发生故障, 全厂生产瘫痪。
控制器;
运行人员分布在全厂各处; 适用于规模不太大、工艺过程不太复杂的企业。
过程控制系统的发展史
集中型计算机控制系统
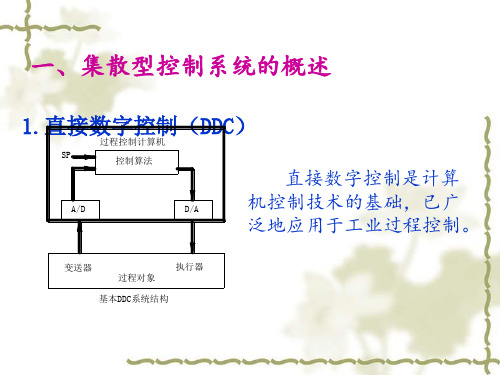
计算机控制器混合控制系统、 监督计算机控制系统SCC
❖ 计算机控制器混合控制系统
CRT操作台
对于老工厂技术改造
中央计算机
尤为可取。特别随着可编
{
设定值
程控制器的发展,与计算
调
调
节
节
器
器
机形成混合控制系统已普 遍应用于老企业中。
特点:
①自主性; ②可靠性; ③协调性; ④友好型; ⑤适应性、灵活性和可扩充性; ⑥在线性。
结构:
①现场装置管理层次的直接控制级; (过程级)
②过程管理级; ③产品管理级; ④工厂总体管理和经营管理级。
入
中央计算机
入
Di 子
Do 子
系
系
统
统
﹛ 被测变量
过程对象
操作变量
集中型计算机控制系统
﹛
缺点:
集中型计算机控制
系统将大量功能集于一 身,把危险也集中了。 一旦计算机发生故障, 将导致生产过程的全面 瘫痪。为了增强可靠性, 一方面要设计高可靠性 的计算机,一方面引入 双重计算机概念。
三、分层计算机控制系统
其实质是四C技术: 计算机、控制器、通信和CRT现实技术。
它以微处理机为核心,把微型计算机、 工业控制计算机、数据通信系统。现实操作 装置、过程通道、模拟仪表灯有机地结合起 来,采用组合组装式结构组成系统,对生产 过程进行集中监视、操作、管理和分散控制 的一种新型控制技术。
它即不同于分散的仪表控制系统,又不 同于集中式计算机控制系统,而是吸收了两 者的有点,在它们的基础上发展起来的一门 系统工程技术,具有显著的优越性。
DCS系统简介及应用
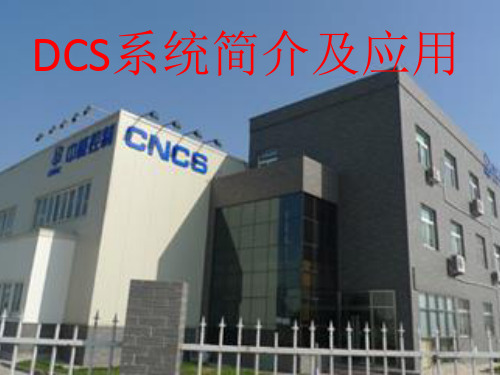
DCS应用情况
高桥石化公司炼油厂1#常减压装置采用SPECTRUM 系 统与FOX-300 上位机,除对全装置实现常规控制外,开 发了常压塔计算机集成优化系统,实现了基于动态内回 流的常压塔测线产品质量的在线计算、多测线产品质量 及收率的智能化协调控制与最佳回流取热分配控制,并 利用人工智能方法构造上级协调系统,开发了常压塔整 体智能决策与优化专家系统。该项目突破传统思维模式, 代之以信息流、物料流和能量流为主干分解方法,充分 发挥了DCS信息采集功能、通信功能和运算功能强的优 势,并以此为依托,开发和实施了高质量的数学模型和 优化控制软件。该系统在现场长时间投用以来,性能可 靠,提高轻油收率。
二、我国石油化工工业DCS应用情况
截止到1990年,中国石油化工总公司范围内 用于过程控制的大小不同规模的DCS共122套, 其中已投用的90 套,在建的32套。除4套为国产 外,其余均为国外引进产品。 石化总公司的122套DCS,用于炼油专业的27 套,化工专业的47套,化纤专业的18套,化肥专 业的13套,公用工程、三剂生产等系统14套,另 有3套用于中试装置。除此3套外,其余119套 DCS分别用在25个企业的71个生产厂。
缺点(与FCS比较)
• • • • • 浪费一次性投资 浪费安装费用 浪费维护费用 控制准确度与可靠性不高 用户的选择性不多
dcs自动控制系统
典型的dcs系统架构
DCS系统简介及应用
一、DCS控制系统应用概况
集散控制系统(Total Distributed Control System,DSC)是20世纪70年代中期发展起来 的以微处理器为基础的分散型计算机控制系 统。它是控制技术(Control)、计算机技术 (Computer)、通信技术(Communication)、 阴极射线管(CRT)图形显示技术和网络技术 相结合的产物。该装置时利用计算机技术对 生产过程进行集中监视、操作、管理和分散 控制的一种全新的分布式计算机控制系统。
计算机控制系统—集散控制系统(工业仪表自动化)

1. 主控卡 2. 数据转发卡 3. I/O卡 ➢ 集线器Hub ➢ 接线端子板
控制站硬件总貌
电源
机笼 机笼 机笼
Hub1 Hub2
机柜
接线端子板
02
操作站(OS)
由工业PC、CRT、键盘、鼠标、打印机等组成的人机接口设备,是操作人员完成工艺过程监 视、操作、记录等管理任务的操作平台。(Operator Station,简称OS)。
01
02
02
03 JX-300XP基本构架
03
03
03
03
04
04
04
注意事项 ➢ 插拔卡件(模块)等操作前,必须正确佩戴防静电手腕带和防静电手套; ➢ 对卡件操作时,持拿边缘部分,禁止直接触碰焊点等; ➢ 禁止转动机柜; ➢ 保管好软件狗等实训物品; ➢ 注意人身及设备安全;
03
➢ 高速、可靠、开放的通讯网络 SCnet II ➢ 分散、独立、功能强大的控制站 ➢ 多功能的协议转换接口 ➢ 全智能化设计 ➢ 任意冗余配置 ➢ 简单、易用的组态手段和工具 ➢ 丰富、实用、友好的实时监控界面 ➢ 事件记录功能 ➢ 安装方便,维护简单,产品多元化、正规化
CONTENTS
PLC
系统结构示意图
智能仪表
02
控制站(CS)
实现对物理位置、控制功能都相对分散的现场生产过程进行控制。主要硬件设备称为控制站。 (Control Station,简称CS)。
包 括 数 据 采 集 站 ( DAS ) 、 逻 辑 控 制 站 ( LCS ) 和 过 程 控 制 站 (PCS)三种类型。 ➢ 数据采集站:提供对模拟量和开关量信号的基本监视功能。 ➢ 逻辑控制站:提供马达控制和继电器类型的离散逻辑功能。 ➢ 过程控制站:简称控制站,是传统意义上集散控制系统的控制
第1章 集散控制系统的概述_1

☞集散控制系统是 20 世纪 70 年代中期发展起来的、以微处理器为基础的、实行集中管理、分散控集散控制系统第一章 绪论制的计算机控制系统。
由于该系统在发展初期以实行 分散控制 为主,因此又称为分散型控制系统或分 布式控制系统(Distributed Control System,DCS), 简称为集散系统或DCS。
TPS系统结构图☞集散控制系统是控制技术 (Control) 、 计 算 机 技 术 (Computer) 、 通 信 技 术 (Communication) 、 阴 极 射 线管(CRT)图形显示技术和 网络 技术(Network)相 结合 的产物,是一种操作显示集 中、控制功能分散、采用分 级分层体系结构、局部网络 通信的计算机综合控制系 统,其目的在于控制或控制 管理一个工业生产过程或工 厂。
1☞集散控制系统自问世 以来,发展异常迅速 , 几经更新换代,技术 性能日臻完善,并以 其技术先进、性能可 靠、构成灵活、操作 简便和价格合理的特 点,赢得了广大用 户,巳被广泛应用于 石油、化工、电力、 冶金和轻工等工业领 域。
1集散控制系统产生的背景20 世纪 60 年代初,人们开始将电子计算机用于过程控 制,试图利用计算机所具有的能执行复杂运算、处理速度 快、集中显示操作、易于通信、易于实现多种控制算法、易 于改变控制方案、控制精度高等特点,来克服常规模拟仪表 的局限性。
一台计算机控制着几十甚至几百个回路,整个生产过程 的监视、操作、报警、控制和管理等功能都集中在这台计算 机上。
一旦计算机的公共部分发生故障时,轻则造成装置或整个 工厂停工,重则导致设备的损坏甚至发生火灾、爆炸等恶性事 故,这就是所谓“危险集中”。
(2)集中型计算机控制系统 (1)直接数字 控制DDC的控制过程是:计算机首先 通过模数输入转换器 (A/D)按一 定周期,循环实时采集多个生产过 程被控参数的信息,然后按照控制 算法运算后,其结果通过数模转换 器 (D/A)依次进入控制执行器, 构成一个闭环回路。
计算机集散型控制系统简介
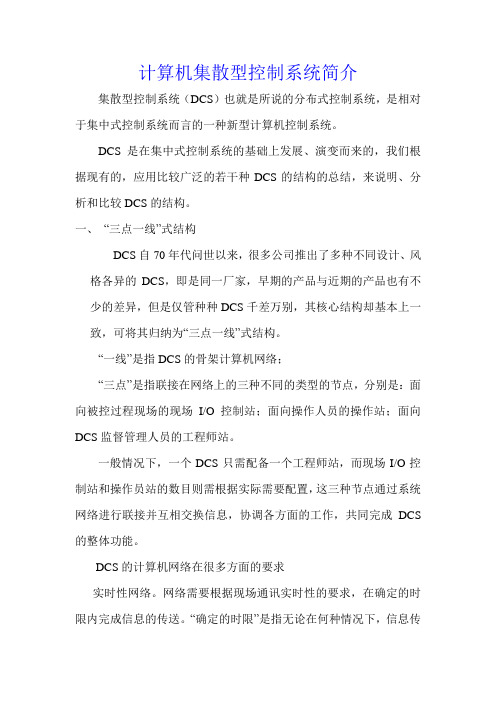
计算机集散型控制系统简介集散型控制系统(DCS)也就是所说的分布式控制系统,是相对于集中式控制系统而言的一种新型计算机控制系统。
DCS是在集中式控制系统的基础上发展、演变而来的,我们根据现有的,应用比较广泛的若干种DCS的结构的总结,来说明、分析和比较DCS的结构。
一、“三点一线”式结构DCS自70年代问世以来,很多公司推出了多种不同设计、风格各异的DCS,即是同一厂家,早期的产品与近期的产品也有不少的差异,但是仅管种种DCS千差万别,其核心结构却基本上一致,可将其归纳为“三点一线”式结构。
“一线”是指DCS的骨架计算机网络;“三点”是指联接在网络上的三种不同的类型的节点,分别是:面向被控过程现场的现场I/O控制站;面向操作人员的操作站;面向DCS监督管理人员的工程师站。
一般情况下,一个DCS只需配备一个工程师站,而现场I/O控制站和操作员站的数目则需根据实际需要配置,这三种节点通过系统网络进行联接并互相交换信息,协调各方面的工作,共同完成DCS 的整体功能。
DCS的计算机网络在很多方面的要求实时性网络。
网络需要根据现场通讯实时性的要求,在确定的时限内完成信息的传送。
“确定的时限”是指无论在何种情况下,信息传送度能在这个时限内完成,而这个时限则是根据被空过程的实时性要求确定的。
系统的拓扑结构。
大致可分为星型,总线型和环型三种。
目前应用最广泛的是环网和总线网。
二、DCS的系统网络SNET各种网络解决碰撞的技术:一种是TOKEN RING(对于环型网)或TOKEN PASSING(对于总线型网)方式;另一种解决碰撞的技术是载波侦听与碰撞检测技术,即CSMA/CD 方式.DCS的基础硬件:DCS由三种节点组成:现场I/O控制站、操作员站、和工程师站,通过局域网络互联在一起形成一个系统。
对于局域网来说,所有的节点都没有什么本质的和原则的区别,它们都是具有自己特定的网络地址,都可以通过局域网接收和发送数据。
集散控制系统

集散控制系统(Distributed control system)是以微处理器为基础的对生产过程进行集中监视、操作、管理和分散控制的集中分散控制系统,简称DCS系统。
是相对于集中式控制系统而言的一种新型的计算机控制系统,它是在集中式控制系统的基础上发展、演变而来的。
它是一个由过程控制级和过程监控级组成的以通信网络为纽带的多级计算机系统,综合了计算机(Computer)、通信(communication)、显示(CRT)和控制(Control)等4C技术,其设计原则是分散控制、集中操作、分级管理、分而自治和综合协调,大大提高了系统的可靠性。
DCS由上而下形成多级控制结构,即过程控制级、集中监控级和生产管理级,采用网络方式实现各级间的信息传递。
DCS既不同于分散的常规仪表控制系统,又不同于集中式计算机控制系统,而是吸收了两者的优点,在它们的基础上发展起来的一门系统工程技术,具有很强的生命力和显著地优越性。
1975年12月,美国霍尼韦尔(HoneyWell)公司推出TDC-2000集散控制系统,成为最早提出集散控制系统设计思想的开发商。
从而开始了DCS的初创阶段(1975-1980)这个时期的系统的特点是:比较注重控制功能的实现,系统的设计重点是现场控制站;系统的人机界面功能则相对较弱,在实际中只用CRT操作站进行现场工况的监视,使得提供的信息也有一定的局限;在功能上更接近仪表控制系统;各个厂家的系统均由专有产品构成,包括高速数据通道、现场控制站、人机界面工作站及各类功能性的工作站等,不仅系统的购买价格高,系统的维护运行成本也高。
可以说,DCS的这个时期是超利润时期,其应用范围也受到一定的限制。
第二阶段(1980-1985)是DCS的成熟期。
这一时期的DCS系统最大的特点是引入了局域网作为系统骨干,按照网络节点的概念组织过程控制站、中央操作站、系统管理站及网关,使得系统的规模、容量进一步增加,系统的扩充有更大的余地,也更加方便在功能上,这个时期的DCS逐步走向完善,除回路控制外,还增加了顺序控制、逻辑控制等功能,加强了系统管理站的功能,可实现一些优化控制和生产管理。
计算机集散控制系统的特点

计算机集散控制系统的特点
(1)自主性
在集散控制系统中,每一个分散过程控制装置都是一个自治的小系统,它完成数据的采集、信号处理、计算及数据输出等功能。
集散控制系统的各部分是各自独立的自治系统,但是,在系统中它们又是互相协调工作的。
(2)人-机界面
集散控制系统的人-机界面由操作管理装置来实现。
操作人员可以通过操作管理装置可以监视工业现场的生产情况,按预先设定的控制策略设计各个控制回路,并对各回路的控制器参数进行整定;还可以实现各状态量的监视及组态操作。
极大的方便了操作人员的操作,便于集中操作和管理。
(3)系统适应性和可扩充性好
集散控制系统的硬件和软件系统均采用标准化、模块化设计思路,具有灵活的组配方案,用户可以根据生产需要来改变系统的配置,在生产流程发生改变时可以很方便地扩大或缩小系统地规模。
(4)通信网络具有开放性
在集散控制系统中,系统通信网络是dcs 的骨架,是DCS 的基础和核心,对于DCS 整个系统的实时性、可靠性
和扩充性,起着决定性的作用。
DCS数据通信网络的实现需要相应的网络协议。
系统网络的发展有一个过程,历经了RS232,RS485协议等直至当今的开放式网络协议。
(5)运行安全可靠
集散控制系统的结构采用容错设计,在任何一个环节出现故障的情况下,仍然可以保持系统的正常运行。
系统的硬件包括操作站、控制站、通信网络及其他一些关键设备均采用双重或多重冗余设计;系统软件采用模块化设计结构,进行组态修改时可以在线下载,而不影响其他程序的运行。
系统还设有完善的自诊断功能,整个系统运行安全可靠。
集散控制

计算机集散控制系统随着生产规模的扩大,信息量的增多,控制和管理的关系日趋密切。
对于大型企业生产的控制和管理,不可能只用一台计算机来完成。
于是,人们研制出以多台微型计算机为基础的集散控制系统(DCS)。
它采用分散控制、集中操作、分级管理、分而自治和综合协调的设计原则,自下而上可以分为若干级,如过程控制级、控制管理级、生产管理级和经营管理级等。
DCS 又称分布或集散式控制系统。
第一章第一节集散控制系统基本概念集散控制系统(DCS)是以微处理器为基础的集中分散型控制系统集散控制系统主要特性集中管理、分散控制DCS 作一个比较完整的定义(1) 以回路控制为主要功能的系统。
(2) 除变送和执行单元外,各种控制功能及通信、人机界面均采用数字技术。
(3) 以计算机的CRT、键盘、鼠标,轨迹球代替仪表盘形成系统人机界面。
(4) 回路控制功能由现场控制站完成,系统可有多台现场控制站,每台控制一部分回路。
(5) 人机界面由操作员站实现,系统可有多台操作员站。
(6) 系统中所有的现场控制站、操作员站均通过数字通信网络实现连接。
二、基本结构集散控制系统是采用标准化、模块化和系列化设计,由过程控制单元、过程接口单元、管理计算机以及高速数据通道等五个主要部分组成。
基本结构如图所示。
(1) 过程控制单元(Process Control Unit,PCU),又叫现场控制站。
它是DCS 的核心部分,对生产过程进行闭环控制,可控制数个至数十个回路,还可进行顺序、逻辑和批量控制。
(2) 过程接口单元(Process Interface Unit,PIU),又叫数据采集站。
它是为生产过程中的非控制变量设置的采集装置,不但可完成数据采集和预期处理,还可以对实时数据作进一步加工处理,供CRT 操作站显示和打印,实现开环监视。
(3) 操作员站(Operating Station,OS)是集散系统的人机接口装置。
除监视操作、打印报表外,系统的组态、编程也在操作站上进行。
集散型控制系统综述

集散型控制系统综述一、集散型控制系统概述集散型控制系统又名分布式计算机控制系统(Distributed Control System)~11 DES.其实质是利用计算机技术对生产过程进行集中监视、操作、管理和分散控制的一种新型控制技术。
它是由计算机技术、测量处理技术、信号处理技术、通讯网络技术以及人机接口技术相互发展、渗透而产生的。
整个系统概括起来是由集中管理部分、分散控制监渊部分和通讯部分组成。
其中集中管理部分叉分为工程师站、操作站和管理计算机。
工程师站主要用于组态和维护,操作站则用于监视和操作,管理计算机用于全系统的信息管理和优化控制。
分散控制检测部分按功能可分为控制站、监测站或现场控制站.用于控制和监{鲥。
通讯部分用于连接集散型控制系统的各个分布部分完成指令、数据及其它信息的传递.集散型控制系统软件部分是由实时多任务操作系统、数据库及其它信息软件,组态软件和各种应用软件组成.利用组态软件就可以生成用户所需要的各种实用系统。
集散塑控嗣系统具有通用性强、系统组态灵活、控嗣功能完善、数据处理方便、显示操作集中、人机界面好、安装规范化、调试方便、运行安全可靠的特点.它能够适应工业生产过程控嗣的各种需要,能提高生产自动化水平和管理水平,提高产品质量,降低能源和原材料消耗,提高劳动生产率.保证生产安全,促进工业技术发展.创造最佳的经济效益和社会效益。
二、集散型控制系统的组成用于控制和监督工艺的数字式集散型控制系统主要由以下三个部分组成:①工艺接口,②数字通信系统;③操作工接口。
(1)工艺接口—现场控制站及监测站工艺接口主要由现场控制站及现场监工艺接口主要由现场控制站及现场监测站组成。
现场控制站是以微处理机为基础的设备,能用于接受和输送4一20mA信号并履行控制功能。
现场控制站的作用是采集现场信息,进行数据处理,对现场进行自动控制。
其控制功能分为两类:即反馈控制功能和顺序控制功能。
反馈控制功能依靠称为内部议表沟软件来实现,实质上是各种已编好的可提供各种用途的子程序。
集散控制系统原理及应用

该工业自动化生产线采用集散控 制系统实现了生产流程的自动化 控制和智能化管理。
系统还能够根据实际生产需求调 整设备参数和生产计划,提高了 生产效率和产品质量,降低了人 工干预和生产成本。
感谢您的观看
THANKS
发展历程
经历了模拟仪表、工业控制计算机、集中式数字控制系统、集散控 制系统等多个阶段。
发展趋势
随着物联网、云计算、大数据等技术的发展,集散控制系统将向智 能化、网络化、集成化方向发展。
集散控制系统的基本组成
中央计算机系统
包括主控计算机、操作员站、工程师站等, 负责系统的监控、操作和优化。
通信网络
连接中央计算机系统和分散控制单元,实现 数据传输和共享。
通过中央计算机系统实 现生产过程的监控、操 作和优化。
采用多台微处理器分散 控制,提高系统的可靠 性和灵活性。
建立高速通信网络,实 现各节点之间的信息传 输和数据共享。
支持多种通信协议和软 件接口,便于系统集成 和升级。
集散控制系统的历史与发展
起源
20世纪70年代初期,随着计算机和通信技术的发展,集散控制系 统开始出现。
该化工厂采用集散控制系统对生产过程 进行集中监控和分散控制,实现了生产 流程的自动化和智能化。
案例二:某电力企业的集散控制系统应用
详细描述
该电力企业采用集散控制系统对 电网进行实时监测和调控,确保 了电网的稳定运行和安全供电。
通过集散控制系统的数据采集和 传输功能,实现了对电网设备的 远程监控和维护,降低了运维成 本和人力投入。
兼容性问题
不同品牌的集散控制系统之间可能存 在兼容性问题,导致信息互通和数据
共享方面存在障碍。
成本较高
集散控制系统的建设和维护成本较高, 对企业来说是一笔不小的投入。
集散型控制系统介绍

集散型控制系统介绍12020年4月19日本答案仅供参考。
第1章绪论1.1 什么是过程计算机控制系统?它由哪几部分组成?经过具体示例说明。
答:它是指由被控对象、测量变送装置、计算机和执行装置构成,以实现生产过程闭环控制的系统,它综合了计算机过程控制和生产工艺过程。
例如温度控制系统。
1.2 计算机控制工业生产过程有哪些种类型?答:计算机控制工业生产过程一般有五种类型:操作指导控制系统;直接数字控制系统;监督控制系统;集散控制系统;现场总线控制系统。
1.3 计算机控制系统的硬件一般有哪几大主要组成部分?各部分是怎样互相联系的?其中过程通道有几种基本22020年4月19日类型?它们在系统中起什么作用?答:计算机控制系统的硬件一般包括:主机、外部设备、过程输入输出设备。
两个过程通道,一个是输入通道,另一个为输出过程通道。
输入过程通道包括:A/D通道----把模拟信号转换成数字信号后再输入;DI通道-----直接输入开关量信号或数字量信号。
输出过程通道包括:D/A通道----把数字信号转换成模拟信号后再输出;DO通道-----直接输出开关量信号或数字量信号。
1.4 直接数字控制系统的硬件由哪几部分组成?答:直接数字控制系统的硬件主要有计算机(主机)、过程输入输出通道、操作台和计算机辅助设备组成。
如下图所示。
32020年4月19日42020年4月19日1.5 数字PID 控制算法有几种形式?各有什么特点?答:数字PID 控制算法有位置式、增量式、速度式三种形式。
PID 位置式根据偏差计算阀门的位置,PID 增量式根据偏差计算阀门的变化;PID 速度式根据偏差变化程度计算阀门的变化。
1.6 试推导计算机控制系统PI 控制算法的位置式、增量式和速度式。
答:模拟PI 控制算法为])(1)([)(0⎰+=tI p dt t e T t e k t u 其中,p k ----比例增益I T ----积分时间常数在采样周期相当短暂时,用矩形法近似代替积分项∑⎰=≈ki t i Te dt t e 00)()(,其中T 为采样周期,k 为采样序号。
集中型计算机控制系统

D/A
直接数字控制是计算 机控制技术的基础,已广 泛地应用于工业过程控制。
变送器 过程对象 基本DDC系统结构
执行器
DDC控制过程是: 计算机首先通过模数输入转换器(A/D) 按一定周期,循环实时采集多个生产过程 被控参数的信息,然后按照控制算法运算 后,其结果通过数模转换器(D/A)依次进 入控制执行器,构成一个闭环回路。 DDC比起模拟仪表控制的主要优点在于: 很容易在计算机中实现PID和其他复杂 的运算规律,并且保持了数字化的精度。
过程对象
集中型计算机控制系统
﹛
﹛
被测变量
操作变量
三、分层计算机控制系统
集中型计算机控制系统暴露了集中控制 的重大缺陷,促使控制系统向分散化发展 。出现了分层计算机控制系统: 计算机控制器混合控制系统、 监督计算机控制系统SCC
• 计算机控制器混合控制系统
CRT操作台
中央计算机 设定值
调 节 器
调 节 器
过程对象
监督计算机控制系统
四、集散型控制系统
集散型控制系统(DCS): 集中分散性计算机控制系统。又称为分布式 计算机控制系统 。
其实质是四C技术: 计算机、控制器、通信和CRT现实技术。
它以微处理机为核心,把微型计算机、 工业控制计算机、数据通信系统。现实操 作装置、过程通道、模拟仪表灯有机地结 合起来,采用组合组装式结构组成系统, 对生产过程进行集中监视、操作、管理和 分散控制的一种新型控制技术。 它即不同于分散的仪表控制系统,又不 同于集中式计算机控制系统,而是吸收了 两者的有点,在它们的基础上发展起来的 一门系统工程技术,具有显著的优越性。
二、集中型计算机控制系统
一台计算机上实现的功能:过程监视、 数据收集、数据处理、数据存储、报警和 登录、过程控制。此外,还可以实现生产 调度和工厂管理的部分功能。
集散控制系统(DCS)基础培训课件

当前集散控制系统面临的挑战和机遇
与其他系统的集成和互操作性 面临的机遇
工业4.0和智能制造的推动
当前集散控制系统面临的挑战和机遇
云计算、大数据等技术的应用 市场需求增长和定制化服务的机会
发展趋势预测:智能化、网络化等方向
智能化
01
02
利用人工智能和机器学习技术提高系统自适 应性和智能化水平
实现故障预测和自主维护,减少人工干预
在楼宇自动化领域,DCS可用 于楼宇照明、空调、安防等系
统的集中管理和控制。
CHAPTER 02
硬件组成与功能实现
控制器类型及其特点
01
02
03
PLC型控制器
采用可编程逻辑控制,适 用于中小型控制系统,具 有编程灵活、易于维护等 特点。
专用控制器
针对特定控制需求设计, 具有高性能、高可靠性等 特点,适用于大型和复杂 控制系统。
实时曲线显示
将采集到的数据以曲线形式实时 展曲线查询
提供历史曲线查询功能,可查看 过去一段时间内的数据变化趋势
。
报表生成与打印
根据用户需求生成各类报表,如 日报、周报、月报等,并支持打
印功能。
CHAPTER 05
系统集成与调试维护方法
DCS与其他系统集成策略探讨
执行情况检查与记录
阐述如何对DCS系统维护保养的执行情况进行检查和记录,包括保养计划的执行情况、保 养效果的评估等方面的内容。同时,强调建立完善的维护保养档案的重要性。
CHAPTER 06
发展趋势与新技术应用前景
当前集散控制系统面临的挑战和机遇
面临的挑战 系统复杂性和维护成本增加
对安全性和可靠性的更高要求
混合型控制器
集散控制系统(DCS)
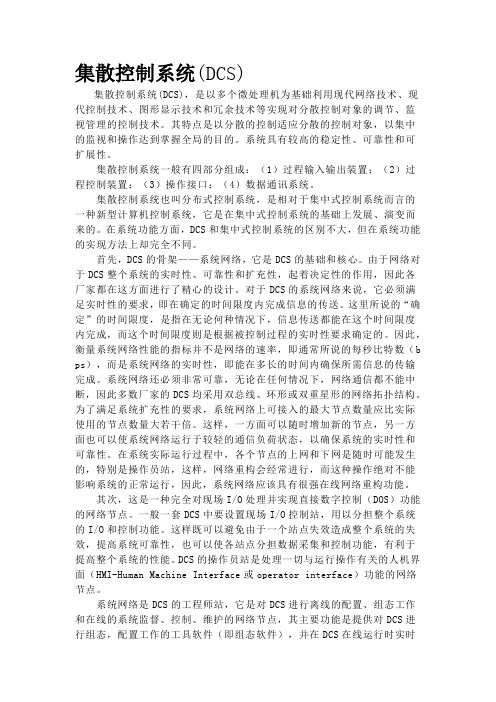
集散控制系统(DCS)集散控制系统(DCS),是以多个微处理机为基础利用现代网络技术、现代控制技术、图形显示技术和冗余技术等实现对分散控制对象的调节、监视管理的控制技术。
其特点是以分散的控制适应分散的控制对象,以集中的监视和操作达到掌握全局的目的。
系统具有较高的稳定性、可靠性和可扩展性。
集散控制系统一般有四部分组成:(1)过程输入输出装置;(2)过程控制装置;(3)操作接口;(4)数据通讯系统。
集散控制系统也叫分布式控制系统,是相对于集中式控制系统而言的一种新型计算机控制系统,它是在集中式控制系统的基础上发展、演变而来的。
在系统功能方面,DCS和集中式控制系统的区别不大,但在系统功能的实现方法上却完全不同。
首先,DCS的骨架——系统网络,它是DCS的基础和核心。
由于网络对于DCS整个系统的实时性、可靠性和扩充性,起着决定性的作用,因此各厂家都在这方面进行了精心的设计。
对于DCS的系统网络来说,它必须满足实时性的要求,即在确定的时间限度内完成信息的传送。
这里所说的“确定”的时间限度,是指在无论何种情况下,信息传送都能在这个时间限度内完成,而这个时间限度则是根据被控制过程的实时性要求确定的。
因此,衡量系统网络性能的指标并不是网络的速率,即通常所说的每秒比特数(b ps),而是系统网络的实时性,即能在多长的时间内确保所需信息的传输完成。
系统网络还必须非常可靠,无论在任何情况下,网络通信都不能中断,因此多数厂家的DCS均采用双总线、环形或双重星形的网络拓扑结构。
为了满足系统扩充性的要求,系统网络上可接入的最大节点数量应比实际使用的节点数量大若干倍。
这样,一方面可以随时增加新的节点,另一方面也可以使系统网络运行于较轻的通信负荷状态,以确保系统的实时性和可靠性。
在系统实际运行过程中,各个节点的上网和下网是随时可能发生的,特别是操作员站,这样,网络重构会经常进行,而这种操作绝对不能影响系统的正常运行,因此,系统网络应该具有很强在线网络重构功能。
什么是DCS

什么是DCS名称:DCS,全称:DistributedControlSystem,定义:DCS是分散控制系统(DistributedControlSystem)的简称,国内一般习惯称为集散控制系统。
它是一个由过程控制级和过程监控级组成的以通信网络为纽带的多级计算机系统,综合了计算(Computer)、通讯(Communication)、显示(CRT)和控制(Control)等4C技术,其基本思想是分散控制、集中操作、分级管理、配置灵活、组态方便。
系统的主要技术概述系统主要有现场控制站(I/O站)、数据通讯系统、人机接口单元(操作员站OPS、工程师站ENS)、机柜、电源等组成。
系统具备开放的体系结构,可以提供多层开放数据接口。
硬件系统在恶劣的工业现场具有高度的可靠性、维修方便、工艺先进。
底层汉化的软件平台具备强大的处理功能,并提供方便的组态复杂控制系统的能力与用户自主开发专用高级控制算法的支持能力;易于组态,易于使用。
支持多种现场总线标准以便适应未来的扩充需要。
系统的设计采用合适的冗余配置和诊断至模件级的自诊断功能,具有高度的可靠性。
系统内任一组件发生故障,均不会影响整个系统的工作。
系统的参数、报警、自诊断及其他管理功能高度集中在CRT上显示和在打印机上打印,控制系统在功能和物理上真正分散,DCS·整个系统的可利用率至少为99.9%;系统平均无故障时间为10万小时,实现了核电、火电、热电、石化、化工、冶金、建材诸多领域的完整监控。
“域”的概念。
把大型控制系统用高速实时冗余网络分成若干相对独立的分系统,一个分系统构成一个域,各域共享管理和操作数据,而每个域内又是一个功能完整的DCS系统,以便更好的满足用户的使用。
网络结构可靠性、开放性及先进性。
在系统操作层,采用冗余的100Mbps以太网;在控制层,采用冗余的100Mbps工业以太网,保证系统的可靠性;在现场信号处理层,12Mbps 的PROFIBUS总线连接中央控制单元和各现场信号处理模块。
计算机集散控制系统

0103 1120 1001 1011
PV跟踪+预置 无过去方式再启动 常规PID
SLOT2输出 信息来自SLOT2输出 PV
信息来自SLOT1
绝对值报警 非温度变量
线性 Xxx.x
平方根处理 反作用控制
正在用输出指示 B方式
数据监测
• 模拟量输入
模拟量输入有的来自变送器,有的直接来自检测元件。这 些信号进入系统后都要经过模数转换、特性化处理、格式 选择、源选择和报警检查等。特性化处理有四种:热电偶、 热电阻、线性和开平方。
• 该系统将若干台微机分散应用于过程控制,全部信息通过通信网络由 上位管理计算机监控,实现最优化控制,整个装置继承了常规仪表分 散控制和计算机集中控制的优点,克服了常规仪表功能单一,人-机 联系差以及单台微型计算机控制系统危险性高度集中的缺点,既实现 了在管理、操作和显示三方面集中,又实现了在功能、负荷和危险性 三方面的分散 。
2 xx.xx
5
3 x.xxx
6
7
特性显示 线性
J型热电偶 K型热电偶 T型热电偶 S型热电偶
平方根 铂电阻 辐射高温计
0 1
控制方程
0
0 A方程
1
1 B方程
组态字及其功能说明
控制作用 正在用 反作用
输出指示 正在用 反作用
: • 串级控制系统流程如图
PV
O 蒸
TT x
SLOT2 01 SP
PID
集散系统的组成
• 现场控制级 又称数据采集装置主要是对过程变量进行数据采集和预 处理,而且对实
时数据进一步加工处理,供CRT显示和打印机打印,从而实现开环监视,并将 采集到的数据传输到监控计算机。
- 1、下载文档前请自行甄别文档内容的完整性,平台不提供额外的编辑、内容补充、找答案等附加服务。
- 2、"仅部分预览"的文档,不可在线预览部分如存在完整性等问题,可反馈申请退款(可完整预览的文档不适用该条件!)。
- 3、如文档侵犯您的权益,请联系客服反馈,我们会尽快为您处理(人工客服工作时间:9:00-18:30)。
Distribution control system一、A brief introduction of the distributed control systemDistributed control system, also called distributed control system, is a new computer control system for centralized control system. It is a centralized decentralized control system based on multi processor based, is currently in process control, especially in large and medium-sized production device to control the application of the most and the highest reliability control system. In the traditional process control introduction of computer technology, using software composed of various functional modules, instead of the past conventional instrument function, to realize the control of production process of pressure, temperature, liquid level, flow, composition and mechanical quantities such as parameters, and the screen of CRT display, communication applications linked network technology component system. The features of DCS field control station of distributed control, real-time data transmission through the cable sent to the control room operator station, realize the centralized monitoring and management, decentralized control, the control function, load and risk diversification.Distributed control system of information management is "set", "scattered" is to control function, DCS system can realize decentralized control and centralized monitoring and management can be realized. In the aspect of system function, DCS and centralized control systems are not very different, but in the realization of system functions methods are completely different. Centralized control system only needs a computer and the I / O devices and CRT, keyboard, printer, etc. peripheral equipment can be complete system functionality and DCS would normally have to by the four basic parts: the system network, I / O control station, operator station and engineer station. In DCS, the field I/O control station, operator station and engineer station is composed of independent computers, respectively, to complete data acquisition and control; monitoring, alarm and recording; system configuration, system management and other functions. These specific features of the computer are referred to as "nodes", and all of these nodes and through network system connected together, become a complete and unified system, in order to achieve decentralized control and centralized monitoring, centralized operation. DCS system is with the modern large-scale industrial production automation continued to rise and process control requirements of increasingly complex emerges as the times require comprehensive control system, it is the product of computer technology, system control technology, network communication technology and multimedia technology combined, can provide window friendly interface and powerful communication function. Is a sophisticated equipment to complete process control and management.二、The history of the development of distributed control systemDCS since its inception in 1975, has experienced thirty years of development. In thirty years, although DCS has not been a major change in the structure of thesystem, but after the continuous development and improvement, its function and performance have been greatly improved. In general, DCS is toward more open, more standardized, more products in the direction of development. As the field of process automation computer control system, the traditional DCS is only a narrow concept. If you thought that only the production process of the DCS automation system, it leads to the wrong conclusion, because now the computer control system has been greatly expanded. It not only includes the DCS in the past contains a variety of content, also drill down to the field of every measurement equipment, implementing agencies, to the development to the production management and enterprise management. Traditional DCS now only refers to this part of the production process control automation, and industrial automation system concept, should be targeted to enterprise wide solutions, namely total solution level. Only from this point of view put forward and solve problems, to really play the computer automation of its function.After entering ninety age, computer technology, more and more new technologies were applied to the DCS. PLC is a kind of logic control of electronic equipment is developed, which is mainly used to replace inflexible and cumbersome relay logic. After entering the field bus technology in the mid ninety's development is very rapid, that some people have to predict: FCS based on field bus control system will replace the DCS as the protagonist. But the field bus can not replace the DCS. The reasons are as follows:1.Low speed network characteristics of the 1 field bus, so that the number of meters each bus did not reach a rational number. In practical application, a H1 bus can only be installed about 8 instruments. As a result, the field bus save cable advantage is very limited.2.field bus standards are not unified, no one has an absolute advantage, the user can choose.3.field bus is still not well solve the intrinsic safe danger zone problem.三、The main technical overview of systemThe system mainly has the field control station (I/O station), data communication system, man-machine interface unit (operator station and engineer station of OPS ENS), power supply cabinet, etc.. The system has an open architecture that can provide multi open data interface. In the harsh industrial field hardware system with high reliability, convenient maintenance, advanced technology. Finished the bottom software platform with powerful processing function, and provide convenient configuration complex control system and user is special and advanced control algorithm of the support ability of independent development, easy configuration and easy to use. Support a variety of fieldbus standards in order to adapt to future expansion needs. The design of the system with self diagnosis function and diagnosis to the appropriate redundancy configuration module level, high reliability. The occurrence of either component fault in the system, will not affect the operation of the system. System parameters, alarm, self diagnose and other managementfunctions is highly concentrated in the CRT display and print to the printer, control system on the physical function and truly decentralized, utilization rate of at least 99.9% of the whole system; system mean time to failure of 100000 hours, the realization of the complete monitoring of nuclear power, thermal power, thermal power, petrochemical, chemical, metallurgy, building materials and many other fields. The concept of "domain". The large scale control system with high-speed real time redundant network is divided into several relatively independent system, a system composed of a domain, the domain sharing data management and operation, and each domain is a functional integrity of the DCS system, in order to better meet the user's use. The network structure reliability, openness and advanced. In the operating system layer, the redundancy of 100Mbps Ethernet; in the control layer, using redundant100Mbps Ethernet and ensure the system reliability; in the field of signal processing layer and 12mbps PROFIBUS bus connecting central control unit and the signal processing module. The structure of Client/Server standard.Some DCS operationlayer using Client/Server open structure and reliable operating system. Operating system with WINDOWS NT operating system; the control station adopts mature embedded real-time multi task operating system QNS control system to ensurereal-time, safety and reliability. Control configuration software standard. The control system uses IEC611313 standard configuration tools, can achieve any monitoring and control requirements. Scalable and scalable, secure economy.The level of DCS system and management of a total of four levels: 1) direct control level (process control level): process control level is the basis for the distributed control system (DCS), main functions include: process data acquisition, direct digital control, equipment monitoring, system test and diagnosis and implementation running is safe and reliable. At this level, the process control computer known as the scene control station, and all kinds of field device directly connected (such as instrumentation, actuator etc.). The implementation of continuous monitoring, control and batch control of control object. At the same time it up withthe second layer is connected to the computer, control and management of information receiving level, to transfer control device of the characteristics of information and the collected real-time data. 2) the process management level: at this level the process management computer to realize comprehensive monitoring equipment operating process, simulation screen display and control circuit configuration and parameter modification, for all building electromechanical equipment operation process optimization processing, report on the operation, trend chart display. To achieve the overall optimization within the unit can, and to generate commands to the lower level. In this layer, the main function is to optimize process control, adaptive control, loop real-time data to simulate the picture monitor. 3) hierarchical management level: set the parameters according to the characteristics of the coordinated control system of building automation, intelligent building of the electrical equipment, is the overall coordinator. It can plan the system structure and operation mode of scale control system of each unit in the use of energy, according to the situation of the users. This is what needs the high level of building automation system.4) property management: building property management level resides in thebuilding automation system of the highest level, the scope of its management is very wide, these functions are integrated into the software system, through a comprehensive plan, under different conditions, combined with a variety of conditions and energy allocation, in order to achieve the optimal solutions to these problems. In this level, the need to achieve the integration of intelligent building automation equipment and public security automation system.四、The characteristics of distributed control system(1) the high reliability of the DCS system to control the spread of the computer implementation, the system uses fault-tolerant design of the structure, so a computer malfunction will not cause the loss of other systems. In addition, due to relatively simple task undertaken by each computer system can according to need to achieve the function with specific structure and software of special computer, so that the reliability of each computer system has also been improved.(2) open DCS using open, standardization, modularization and serialization design, each computer system using the LAN communication, to achieve information transmission, when the need to change or expand the system functionality, will add computer conveniently connected into the network system of communication or from the network discharge, almost does not affect the work of other computer systems. (3) flexibility through the configuration software according to the different process of application objects were software and hardware configuration, which determine the measurement and control signals and inter connections, from the control algorithm library choose the appropriate control law and basic graphics from the graphics libraries call components required for various monitoring control and alarm screen, thus convenient to constitute the control system.(4) easy maintenance function single small or micro dedicated computer, with characteristics of simple and convenient maintenance, when a local or a computer failure can in does not affect the online replacement of the operation of the whole system, rapid troubleshooting.(5) through the communication network data transfer coordination between the various stations, sharing, and coordination of the whole information system, to complete the overall function and optimization of control system.(6) control function complete control algorithm rich, set continuous control, sequence control and batch control in one, advanced control cascade, feedforward and decoupling, adaptive and predictive control can be realized, and can easily add the special control algorithm required. Very flexible forms of DCS, managed by a dedicated computer station, operator station and engineer station, recording station, field control station and data acquisition station, etc., but also by the universal server, industrial control computer and a programmable controller. At the bottom of the process control level by the general decentralized field control station, data acquisition station, data acquisition and control, and through the data communications network transmission to the monitoring computer production level. Production control level centralized management of the data from the process control level, such asoptimizing calculation, statistics, fault diagnosis and alarm etc.. With the development of computer technology, DCS and higher performance according to need the computer equipment through the network connection to achieve more senior management functions, such as scheduling, storage management, energy management etc.五、Distributed and centralized system is differentDistributed control system (DCS), also called the distributed system, a new type of computer is compared with the centralized control system of the control system, which is a centralized control system based on the development and evolution of the. In the aspect of system function, DCS and centralized control systems are not very different, but in the realization of system functions methods are completely different. Firstly, the framework of DCS system network, it is the foundation and core of DCS. As the network of the system for real-time DCS, reliability and scalability, plays a decisive role, so the manufacturers have been careful in this area of design. For the DCS system network, it must meet the requirements of real-time transmission of information, is completed within defined time limits. Here said the "OK" time limit, is that in any case, information transmission can be completed within the time limit, and the time limit is under the control of the process of real time demand. Therefore, measure system network performance index and the network is not rate, which is often referred to as bits per second number (BPS), but the real-time network system, which can ensure the long time to complete the required information transmission. The network system also must be very reliable, in any case, the communication can not be interrupted, the network topology so most manufacturers of DCS were doublebus ring or dual star. In order to meet the system requirements, the maximum number of nodes in the system can access the network should be several times larger than the number of nodes actually used. In this way, one can always add new nodes, on the other hand, it can also make the system running on the network communication load lighter, to ensure the real-time and reliability of the system. In the actual operation of the system, each node of the Internet and the net is that may occur at any time, especially the operator station, so that network reconfiguration will often, and this operation must not affect the system's normal operation. Therefore, network system should have a strong online network reconfiguration functions.Secondly, this is a complete on-site I/O processing and Realization of direct digital control (DOS) function of network nodes. A general DCS to set the field I/O control station, I/O and control functions to share the entire system. This can be avoided due to the failure of a site caused by the failure of the whole system, improve the system reliability, the site also allows sharing of data acquisition and control functions, is conducive to improve the performance of the whole system. The DCS operator station is to deal with all the relevant operation interface (HMI-Human Machine or Interface operator interface) network node function.Network system is the DCS Engineer Station, it is to DCS off-line configuration, configuration and online system supervision, control, maintenance ofthe network node, its main function is to provide to the DCS configuration, configuration software tools (software) and in DCS run on-line real time monitoring DCS network each node operation, system engineer can through the engineer station timely adjustment of system configuration and some system parameters set, the DCS in the best working condition at any time. Different with the centralized control system, all DCS are required to have system configuration function, it can be said that no system configuration functions of the system can't be called DCS.。