铁水预脱硅
炼钢第二讲(1)铁水预处理

17
脱磷剂
氧化剂――――氧气、氧化铁、轧钢铁皮、连铸铁皮等 将铁水中的磷氧化 固定剂――――CaO,Na2CO3; 5NaCO3+4[P]=5(Na2O)+2(P2O5)+5C
3(Na2O)+(P2O5)=(3NaO· P2O5)
使磷稳定地结合在炉渣中 助熔剂――――CaF2,CaCl2。 生产低熔点的化合物,溶于渣中。 18
搅拌能 低 高
供氧 速率 低 高
氧气 比率 低 高
废钢比 低 高
建设投资 低 高
24
脱硫
脱硫原理
钢铁冶炼脱硫,就是要形成稳定的硫化物,并
能与钢或铁水顺利分离。
脱硫基本反应方程式如下:
Mg(g)+[S]=MgS(s) ΔGΘ=- 427367+180.67 T
25
脱硫剂
苏打灰(Na2CO3) 石灰粉(CaO) 电石粉(CaS) 金属镁
铁水“三脱”工艺
铁水三脱预处理( ORP法 )工艺流程
50
49
总用量大约为吨铁水35公斤。配比:CaO42%-Fe2O346%-CaF212%。
预脱磷方法
在高炉出铁沟或出铁槽内进行脱磷; 在铁水包或鱼雷罐车中进行预脱磷; 在专用转炉内进行铁水预脱磷。
19
铁水包喷吹法 优点: 铁水罐混合容易, 浸入 反应动力学条件好 缺点:
吹炼时间长,温降大 渣多
被铁水内部进行脱硫反应,从而达到脱硫的目的。
优点:脱硫效率高、脱硫剂耗量少、金属损耗低等。
38
非卷入型机械搅拌法
特点:在钢包内只设一个简单
的倒T字形耐火材料搅拌棒, 旋转搅拌棒使脱硫剂与铁水混合
进行脱硫。但脱硫时间长,
铁水预处理与炉外精炼
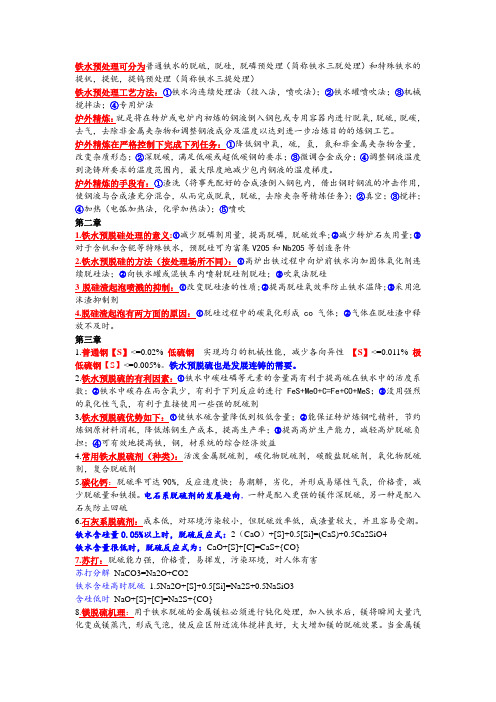
铁水预处理可分为普通铁水的脱硫,脱硅,脱磷预处理(简称铁水三脱处理)和特殊铁水的提钒,提铌,提钨预处理(简称铁水三提处理)铁水预处理工艺方法:①铁水沟连续处理法(投入法,喷吹法);②铁水罐喷吹法;③机械搅拌法;④专用炉法炉外精炼:就是将在转炉或电炉内初炼的钢液倒入钢包或专用容器内进行脱氧,脱硫,脱碳,去气,去除非金属夹杂物和调整钢液成分及温度以达到进一步冶炼目的的炼钢工艺。
炉外精炼在严格控制下完成下列任务:①降低钢中氧,硫,氢,氮和非金属夹杂物含量,改变杂质形态;②深脱碳,满足低碳或超低碳钢的要求;③微调合金成分;④调整钢液温度到浇铸所要求的温度范围内,最大限度地减少包内钢液的温度梯度。
炉外精炼的手段有:①渣洗(将事先配好的合成渣倒入钢包内,借出钢时钢流的冲击作用,使钢液与合成渣充分混合,从而完成脱氧,脱硫,去除夹杂等精炼任务);②真空;③搅拌;④加热(电弧加热法,化学加热法);⑤喷吹第二章1.铁水预脱硅处理的意义:①减少脱磷剂用量,提高脱磷,脱硫效率;②减少转炉石灰用量;③对于含钒和含铌等特殊铁水,预脱硅可为富集V2O5和Nb2O5等创造条件2.铁水预脱硅的方法(按处理场所不同):①高炉出铁过程中向炉前铁水沟加固体氧化剂连续脱硅法;②向铁水罐或混铁车内喷射脱硅剂脱硅;③吹氧法脱硅3脱硅渣起泡喷溅的抑制:①改变脱硅渣的性质;②提高脱硅氧效率防止铁水温降;③采用泡沫渣抑制剂4.脱硅渣起泡有两方面的原因:①脱硅过程中的碳氧化形成co气体;②气体在脱硅渣中释放不及时。
第三章1.普通钢【S】<=0.02% 低硫钢实现均匀的机械性能,减少各向异性【S】<=0.011% 极低硫钢【S】<=0.005%。
铁水预脱硫也是发展连铸的需要。
2.铁水预脱硫的有利因素:①铁水中碳硅磷等元素的含量高有利于提高硫在铁水中的活度系数;②铁水中碳存在而含氧少,有利于下列反应的进行FeS+MeO+C=Fe+CO+MeS;③没用强烈的氧化性气氛,有利于直接使用一些强的脱硫剂3.铁水预脱硫优势如下:①使铁水硫含量降低到极低含量;②能保证转炉炼钢吃精料,节约炼钢原材料消耗,降低炼钢生产成本,提高生产率;③提高高炉生产能力,减轻高炉脱硫负担;④可有效地提高铁,钢,材系统的综合经济效益4.常用铁水脱硫剂(种类):活泼金属脱硫剂,碳化物脱硫剂,碳酸盐脱硫剂,氧化物脱硫剂,复合脱硫剂5.碳化钙:脱硫率可达90%,反应速度快;易潮解,劣化,并形成易爆性气氛,价格贵,减少脱硫量和铁损。
铁水预脱硅

铁水预脱硅铁水预脱硅(desiliconization of hot metal)铁水进入炼钢炉前的降硅处理。
它是发展较早的一种铁水预处理工艺,是分步精炼工艺的发展。
能改善炼钢炉的技术经济指标,降低炼钢费用,也可作为预处理脱磷、脱硫的前处理,可降低脱磷处理剂消耗,进一步生产纯净优质钢。
简史铁水预处理脱硅开始较早,1897年曾有人用平炉进行了脱硅脱磷的预备精炼工业试验,20世纪初进行了混铁炉脱硅,到40年代试验了高炉出铁时的脱硅,中国于50年代曾在鞍山钢铁公司实施过预备精炼炉脱硅和高炉铁水沟脱硅,这些都对改善平炉炼钢的冶炼技术经济指标和提高生产率起了良好的作用。
到了90年代,基于对优质钢材的需求,以及钢铁生产工艺本身节省资源和能量、减少渣量等公害的需要,日本发展了以脱硅、脱磷为目的的铁水预处理。
此后发展成两类预脱硅工艺,一类是作为铁水同时脱磷、脱硫的前工序,以提高其效率,这种铁水进入转炉只需完成脱碳和提高温度,炉渣减少到微量保护渣层的程度,主要生产高纯钢种;另一类是作为降低转炉渣量的措施。
1985年前后日本各大厂曾广泛采用,主要在高炉炉前进行。
后来,由于高炉冶炼低硅铁技术的发展,这类预脱硅方法已较少使用。
原理硅是易氧化元素。
脱硅反应可表示如下:按硅在渣相和金属相问的分配比可表示为式(2):式中L si为硅在渣铁间分配率;C si为硅容量(K si/γ(sio2 ) );a [O]为氧在铁水中活度;f [si]为硅在铁水中活度系数;γ(sio2 )为氧化硅在渣相中的活度系数;K’ Si为反应式(1)的平衡常数。
在碳饱和铁水中硅的活度系数根据各元素相互作用系数按下式计算:按一般炼钢生铁计算,f Si约在7~8之间。
硅容量C si,表示了渣相的溶硅能力。
它与渣中二氧化硅的活度系数,γ(sio2)成反比。
硅容量和渣成分有密切关系。
图1给出了FeO--SiO2--CaO--CaF2渣系的硅容量。
从以上热力学性质可以看出:(1)在一定温度和生铁成分条件下,脱硅能力决定于渣相的硅容量和供氧强度。
铁水预处理技术

3
Northeastern University
各国铁水预处理技术的情况
先进国家铁水预处理已成为钢铁生产的必备工序 ,有的厂铁水实现了100%的预处理。平均约80% 的铁水经过脱硫;日本50%左右的铁水经过脱硅, 40%以上的铁水经过脱磷处理。
4
Northeastern University
我国铁水预处理技术发展过程
50年代初:开始用苏打铺撒法处理高炉铁水 70年代:开始自行开发铁水预处理技术 70年代:武钢二炼钢厂从新日铁引进KR法 1985年:宝钢一炼钢从新日铁引进TDS法投产 1988 年:太钢从国外引进部分关键设备,国内配套建成 了首座铁水三脱预处理站 1998 年:本钢从北美引进铁水包喷吹 CaO+Mg 粒铁水预 脱硫技术 1998年:宝钢从北美引进铁水包喷吹 CaC2+Mg粒铁水预 脱硫技术 近几年:全国有许多钢厂已经或正在建设铁水预处理设备, 但大多以引进为主
[Si] + Fe3O4(s) = SiO2(s) + Fe(l) ΔG3=-275860+156.49T J· mol-1 (3)
吹氧脱硅
[Si] + O2(g) = SiO2 (s) ΔG4=-821780+221.16T J· mol-1
(4)
由ΔG与温度的关系可知,在通常的高炉铁水温度 (1300~1400℃)范围内,ΔG4<ΔG2<ΔG1<ΔG3<0,硅的 氧化反应均为放热反应,且气体脱硅剂比固体脱硅剂的 反应更容易进行。
6
Northeas耗量的关系
7
Northeastern University
铁水预脱硅基本原理
第七章 铁水预处理

8.2 铁水预脱硫工艺
3、铁水预脱硫的优点
铁水中[C]、[Si]较高,fs↑,硫反应能力提高;
铁水中[O]较低,Ls↑,脱硫效率高;
搅拌充分,脱硫剂利用率高,脱硫速度快;
铁水脱硫费用低;
铁水脱硫可提高炼铁炼钢的生产能力、节约工序 能源、降低成本。
实际脱硫过程 扒渣过程
8.2 铁水预脱硫工艺
符合上述条件的典型脱硫剂有:苏打(Na2CO3)、 石灰 (CaO)、食盐(NaCl)、氰氨化钙(CaCN2)、镁(Mg)、碳化 钙(CaC2)等。它们可以单独使用,也可以混合使用。 目前普遍使用的脱硫剂是碳化钙、石灰和镁。其反应为:
CaC2+[S]=CaS+2C石墨
( 1)
8.2 铁水预脱硫工艺
8 .4 铁水预脱磷工艺
3、铁水同时脱硫脱磷 在氧化性条件下,渣铁间的磷硫分配比可表示为:
(%P) 5 lg L P lg lg C P lg f P lg a O [%P] 2 (%S) lg L S lg lg C S lg f S lg a O [%S]
在温度和铁水成分一定时,选择磷容量CP和硫容量CS较大 的渣系,就能得到较大的LP和LS值,实现同时脱磷脱硫。 在一定渣系条件下,可以通过控制熔渣—铁水界面的氧位 来调节LP和LS值的大小,即增大氧位能增大LP和减小LS,反之亦 然。这样,可以根据铁水脱磷和脱硫的程度要求,控制合适的 氧位,有效地实现铁水的同时脱磷脱硫。
log K (1)
2 aCaS aC 19000 log 6.28 aCaC 2 [%S ] f[ s ] T
CaO固 [ S ] C石墨 CaS固 CO气 log log 5.75 aCaO aC [%S ] f[ s ] T (3) 22750 9.63 T aMgS PMg [%S ] f[ s ]
铁水预处理
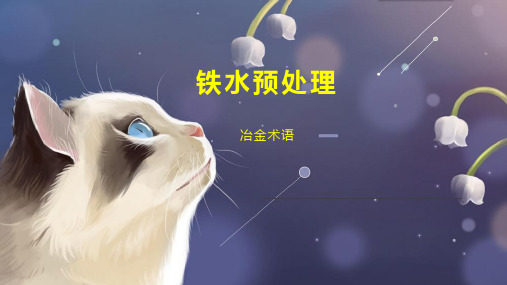
冶金术语
01 工艺简介
03 目的 05 剂
目录
02 分类 04 工艺方法
铁水预处理是指将铁水兑人炼钢炉之前脱除杂质元素或回收有价值元素的一种铁水处理工艺,包括铁水脱硅、 脱硫、脱磷(俗称“三脱”),以及铁水提钒、提铌、提钨等。
我国很多钢厂都采用了铁水预脱硫处理,甚至铁水三脱处理、提钒、提铌、提钨等,尤其是对于生产超低硫、 超低磷钢种的转炉炼钢车间。
工艺简介
铁水预处理是指铁水进入炼钢炉之前采取的冶炼工艺。铁水预处理工艺始于铁水炉外脱硫,1877年,伊顿() 等人用以处理不合格的生铁。铁水预脱硅、预脱磷始于1897年,英国人赛尔(Thiel)等人用一座平炉进行预处理 铁水,脱硅、脱磷后在另一座平炉中炼钢,比两座平炉同时炼钢效率成倍提高。到20世纪初,由于人们致力于炼 钢工艺的改进,所以铁水预处理技术发展曾一度迟缓。直至20世纪60年代,随着炼钢工艺的不断完善和材料工业 对钢材产品质量的要求开趋严格,铁水预处理得到了迅速的发展,并逐步成为钢铁冶金的必要环节。
分类
铁水预脱硅
研究表明,铁水中硅含量为0.3%即可保证化渣和足够高的出钢温度,硅过多反而会恶化技术经济指标。因此, 有必要开展铁水预脱硅处理。
脱硅剂以能够提供氧源的氧化剂材料为主,以调整炉渣碱度和改善流动性的熔剂为辅。如日本福山厂脱硅剂 组成为铁皮0~100%、石灰0~20%、萤石0~10%;日本川崎水岛的脱硅剂为烧结矿粉75%、石灰25%。脱硅生成的 渣必须扒除,否则影响下一步脱磷反应的进行。
(4)抗蚀、焊接和切削性能:钢中硫化物夹杂还会引起坑蚀现象。在钢的焊接过程中,钢中的硫化锰夹杂能 引起热撕裂。硫对钢还有一种很好的影响,即它能改善钢的切削性能。
工艺方法
常用铁水预处理技术

常用铁水预处理技术常用铁水预处理技术铁水预处理基础知识1、什么是铁水预处理?★铁水预处理指铁水兑人炼钢炉之前,为除去某些有害成份或回收某些有益成分的处理过程。
针对炼钢而言,主要是使铁水中硅、磷、硫含量降低到所要求的范围,以简化炼钢过程,提高钢的质量。
铁水预处理具体分为铁水炉外脱硅、脱磷和脱硫,有时脱磷和脱硫同时进行。
对于铁水含有特殊元素提纯精炼或资源综合利用而进行的提钒、提铌、提钨等预处理技术则称为特殊预处理。
2、什么是铁水“三脱”技术?★指铁水兑人炼钢炉之前,进行脱硫、脱硅、脱磷的预处理工艺过程。
3、铁水脱硫的目的是什么?★提高钢质、扩大品种和改善炼钢操作,提高钢的机械、工艺性能。
4、铁水脱硅的目的是什么?⑴减少转炉炼钢渣量、改善操作和提高炼钢经济指标。
硅是氧气转炉炼钢发热的元素,所以为了提高炼钢熔池温度和早化渣,往往希望铁水含硅高一些,但实践证明铁水含硅高时,为了保证转炉渣有较高的碱度,势必增加石灰消耗量,使渣量增多,冶炼时间延长,耗氧量增加,喷溅加剧,铁损增加,并给操作带来困难,从而降低炼钢生产率和增加生产成本。
铁水含硅量一般应控制在0.4%以下的水平。
(2)铁水预脱磷的需要脱硅是铁水预脱磷的先决条件。
铁水预脱磷要求脱磷反应区的氧位高,当加入氧化剂提高氧位时,硅首先就与氧作用而降低铁水中的氧位。
为此,脱磷首先要脱硅,脱磷前控制硅含量一般要求在0.15%以下。
5.铁水脱磷的目的是什么?(1)生产低磷钢、超低磷钢和不锈钢等工艺需要。
磷在钢中对性能的影响,除少数钢种为提高强度或耐大气腐蚀性,要求有一定含磷外,对大多数钢种是有害的,它降低钢的冲击韧性,尤其是低温冲击韧性;磷的枝晶偏析使板材产生带状组织,造成钢板各向异性。
随着新技术材料的发展,对某些品种钢要求磷含量≤0.01%(低磷钢) 或≤0.005%(超低磷钢) 。
用转炉工艺脱磷,虽然有较好的脱磷效果,但达到这种低磷的水平是难以完成的,如采取多次造渣操作,有可能达到,但都存在渣料消耗大,冶炼时间长,热损失大,金属收得率低等问题。
3 铁水预处理技术

3.2 铁水炉外脱硅
铁水预脱硅技术是基于铁水预脱磷技术而发展 起来的。
由于铁水中硅的氧势比磷的氧势低得多,当脱 磷过程加入氧化剂后,硅与氧的结合能力远远大于 磷与氧的结合能力,所以硅比磷优先氧化。这样形 成的SiO2势必会大大降低渣的碱度。 根据以往的研究结果表明,脱磷前必须优先将 铁水硅氧化到远远低于高炉铁水硅含量的0.15%以下, 磷才能被迅速氧化去除。 所以,为了减少脱磷剂用量、提高脱磷效率, 开发了铁水预脱硅技术。
铁水脱硫的情况
国家(地区) 铁水初始硫 (%) 西欧 0.03-0.05 全量脱硫 ≤0.015 ≤0.003 (部分) 50/50 加拿大 0.04-006 全量脱硫 ≤0.015 ≤0.003 (部分) 75/25↑ 美国 0.04-0.06 <0. 003(20%) <0. 005(20%) <0.015(60%) 0/100 Mg+CaO+ CaC2↑ 日本 0.02-0.04 全量脱硫 ≤0.015 ≤0.003 (部分) 75/25↑ CaO+↑(Mg +CaC2) 宝钢 0.025-0.03 <0. 007 (目前) <0. 003 (目标 20%) 100/0↑ CaO+CaC2 +Mg↑
(2) 鱼雷罐车或铁水罐中喷射脱硅剂脱硅
特点:是工作条件好,处理能力大,脱硅效率高且 稳定。
缺点:是占用时间长,温降较大。喷吹分吹氧和喷 粉,粉剂主要使用的是烧结矿粉或集尘粉。 宝钢二炼钢的脱硅就是在铁水“三脱”预处理 站中进行的。宝钢1号高炉采用的是将脱硅剂喷入摆 动流嘴内铁水中的工艺,脱硅剂是烧结机的除尘灰, 脱硅效率高且稳定,鱼雷罐内泡沫渣量比较少,与 不脱硅时相比,鱼雷罐铁水装载量下降不多,在脱 硅剂成分和铁水温度符合要求时,铁水硅含量可由 0.42%脱至0.2%。
铁水预处理“脱硅—脱硫—脱磷”顺序的选择
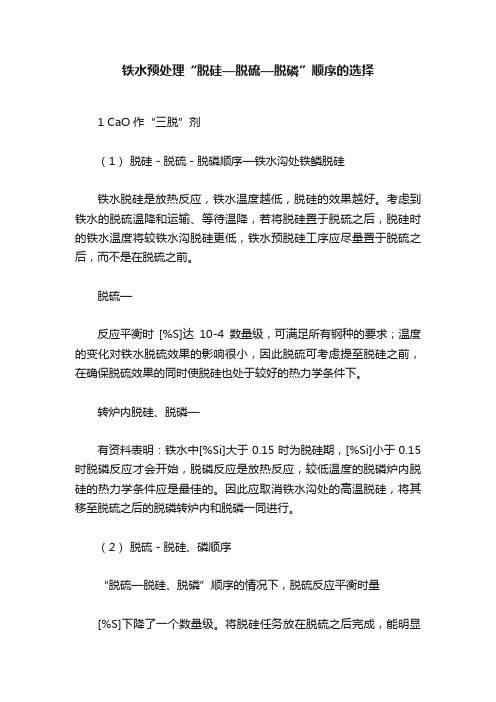
铁水预处理“脱硅—脱硫—脱磷”顺序的选择1 CaO作“三脱”剂(1)脱硅-脱硫-脱磷顺序—铁水沟处铁鳞脱硅铁水脱硅是放热反应,铁水温度越低,脱硅的效果越好。
考虑到铁水的脱硫温降和运输、等待温降,若将脱硅置于脱硫之后,脱硅时的铁水温度将较铁水沟脱硅更低,铁水预脱硅工序应尽量置于脱硫之后,而不是在脱硫之前。
脱硫—反应平衡时[%S]达10-4数量级,可满足所有钢种的要求;温度的变化对铁水脱硫效果的影响很小,因此脱硫可考虑提至脱硅之前,在确保脱硫效果的同时使脱硅也处于较好的热力学条件下。
转炉内脱硅、脱磷—有资料表明:铁水中[%Si]大于0.15时为脱硅期,[%Si]小于0.15时脱磷反应才会开始,脱磷反应是放热反应,较低温度的脱磷炉内脱硅的热力学条件应是最佳的。
因此应取消铁水沟处的高温脱硅,将其移至脱硫之后的脱磷转炉内和脱磷一同进行。
(2)脱硫-脱硅、磷顺序“脱硫—脱硅、脱磷”顺序的情况下,脱硫反应平衡时量[%S]下降了一个数量级。
将脱硅任务放在脱硫之后完成,能明显改善CaO粉剂脱硫的热力学条件。
(3)脱硅、脱磷-脱硫顺序在“脱硅、脱磷—脱硫”顺序的情况下,脱硫反应平衡时[%S]为10-3数量级,而在“脱硅—脱硫—脱磷”顺序下,[%S]为10-4数量级,在“脱硫—脱硅、脱磷”顺序下,[%S]为10-5数量级。
显然“脱硫—脱硅、脱磷”顺序下CaO粉剂脱硫反应的热力学条件更好。
(4)同时“三脱”机理研究表明:用氮氧复合气体作载气喷吹CaO粉同时进行铁水预处理“三脱”反应时,脱硅、脱磷主要是在喷枪附近的高氧势区进行的瞬时接触反应;脱硫则是还原性渣和铁水之间的持久接触反应。
对铁水预处理脱硅来说,脱磷转炉顶吹氧加CaO粉剂脱硅的热力学条件是最优的。
CaO的脱磷能力受铁水温度的影响很大,在其它操作条件允许的情况下,应该尽量在低温下脱磷。
“脱硫-脱硅、脱磷”顺序下,专用脱磷转炉脱磷时铁水的温度较同时“三脱”时低。
综合比较认为:CaO作三脱剂时,脱磷应在脱硫之后,并在专用转炉内进行最佳。
铁水预处理工艺技术操作规程
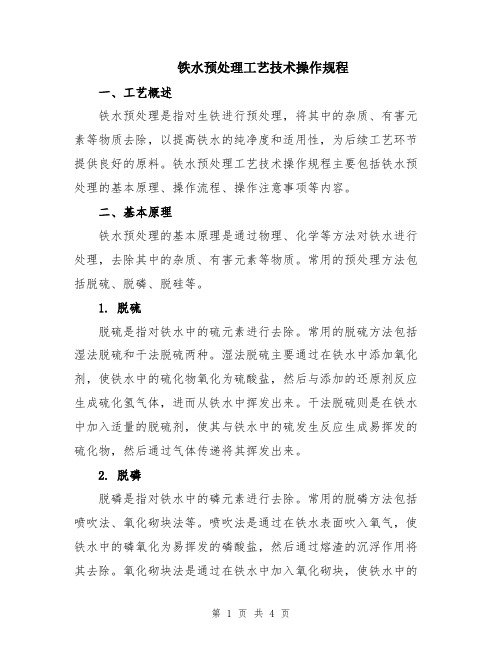
铁水预处理工艺技术操作规程一、工艺概述铁水预处理是指对生铁进行预处理,将其中的杂质、有害元素等物质去除,以提高铁水的纯净度和适用性,为后续工艺环节提供良好的原料。
铁水预处理工艺技术操作规程主要包括铁水预处理的基本原理、操作流程、操作注意事项等内容。
二、基本原理铁水预处理的基本原理是通过物理、化学等方法对铁水进行处理,去除其中的杂质、有害元素等物质。
常用的预处理方法包括脱硫、脱磷、脱硅等。
1. 脱硫脱硫是指对铁水中的硫元素进行去除。
常用的脱硫方法包括湿法脱硫和干法脱硫两种。
湿法脱硫主要通过在铁水中添加氧化剂,使铁水中的硫化物氧化为硫酸盐,然后与添加的还原剂反应生成硫化氢气体,进而从铁水中挥发出来。
干法脱硫则是在铁水中加入适量的脱硫剂,使其与铁水中的硫发生反应生成易挥发的硫化物,然后通过气体传递将其挥发出来。
2. 脱磷脱磷是指对铁水中的磷元素进行去除。
常用的脱磷方法包括喷吹法、氧化砌块法等。
喷吹法是通过在铁水表面吹入氧气,使铁水中的磷氧化为易挥发的磷酸盐,然后通过熔渣的沉浮作用将其去除。
氧化砌块法是通过在铁水中加入氧化砌块,使铁水中的磷与氧化砌块发生反应生成磷酸盐,然后通过熔渣的沉浮作用将其去除。
3. 脱硅脱硅是指对铁水中的硅元素进行去除。
常用的脱硅方法包括湿法脱硅和干法脱硅两种。
湿法脱硅主要是通过在铁水中加入足够量的碱性矿物,使硅与碱性矿物发生反应生成易挥发的硅酸盐,然后通过熔渣的沉浮作用将其去除。
干法脱硅则是在铁水中加入适量的脱硅剂,使其与铁水中的硅发生反应生成易挥发的硅化物,然后通过气体传递将其挥发出来。
三、操作流程铁水预处理的操作流程按照脱硫、脱磷、脱硅的顺序进行,具体步骤如下:1. 脱硫操作流程(1) 检查脱硫设备及周围环境的安全情况。
(2) 开始对铁水进行脱硫前,要先对铁水进行预热,使其温度达到预定的要求。
(3) 进行湿法脱硫时,在预热后的铁水中加入适当的氧化剂,并根据预定的脱硫时间进行搅拌。
宝钢高炉炉前铁水预脱硅技术

宝钢高炉炉前铁水预脱硅技术王天球王士彬(上海宝山钢铁股份有限公司炼铁厂)摘要:本文介绍了宝钢高炉炉前铁水预脱硅技术,并根据现场实际生产数据及操作经验,分析总结出了影响脱硅效果和泡沫渣的诸多因素,通过采取一系列改进措施,使高炉炉前脱硅取得了很大的进步,为炼钢冶炼低磷低硫精品钢提供了优质低硅铁水。
关键词:炉前脱硅脱硅效果泡沫渣影响因素1.概述高炉炉前脱硅主要是为炼钢提供低硅铁水,冶炼高附加值精品钢。
以往铁水预处理都是由炼钢“三脱”来进行的。
由于其工艺复杂,处理时间长,铁水热损失大,渣量大,成本高,八十年代初以来,日本、韩国、台湾等国家和地区相继采用高炉炉前铁水脱硅技术。
其目的在于缩短钢铁冶炼全流程生产时间,降低炼钢熔剂消耗量,为生产低磷低硫高级钢,提高产品竞争力以及改善企业的经济效益提供必要条件。
高炉炉前脱硅所用的方法主要有投撒法和喷吹法两种。
脱硅剂靠自重撒落到铁水表面的称为投撒法,用载气将脱硅剂以一定速度喷入铁水中的称为喷吹法。
这两种方法都有使用实例。
比较而言,投撒法所用的脱硅剂在粒度和种类上可选范围较宽(如烧结矿粉和氧化铁皮等均可应用),其系统工艺流程及设备都比较简单,造价低,但脱硅剂消耗量大,脱硅剂与铁水搅拌不充分,脱硅产生泡沫渣多,脱硅效果欠佳。
日本福山4BF、千叶6BF、韩国光阳4BF等高炉所用的脱硅系统均属于投撒法。
喷吹法脱硅工艺及设备相对要复杂些,所用的脱硅剂粒度、水分等要求也较高,但脱硅剂与铁水的混合较好,反应界面大,有利于脱硅反应进行,脱硅效果较好。
所用的脱硅剂一般为烧结厂除尘灰和出铁厂除尘灰。
喷吹法是目前采用较多的一种炉前脱硅工艺。
日本的千叶5BF、水岛2BF、3BF、4BF、鹿岛2BF、3BF、福山2BF、神户3BF、加古川2BF 以及台湾中钢1BF等均采用了喷吹法脱硅。
宝钢采用铁水预处理技术,有利于调整公司产品结构,冶炼国内、外市场需求量不断增加的低磷、低硫、高纯度、高附加值的钢种,提高公司市场竞争力和经济效益。
脱硅
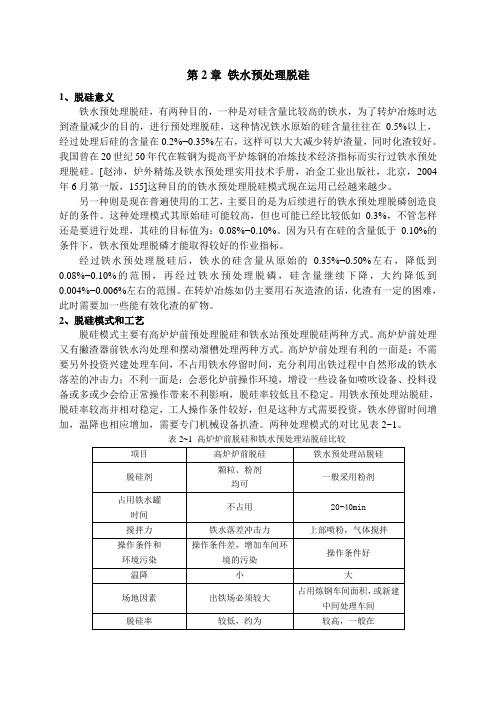
第2章铁水预处理脱硅1、脱硅意义铁水预处理脱硅,有两种目的,一种是对硅含量比较高的铁水,为了转炉冶炼时达到渣量减少的目的,进行预处理脱硅,这种情况铁水原始的硅含量往往在0.5%以上,经过处理后硅的含量在0.2%¬0.35%左右,这样可以大大减少转炉渣量,同时化渣较好。
我国曾在20世纪50年代在鞍钢为提高平炉炼钢的冶炼技术经济指标而实行过铁水预处理脱硅。
[赵沛,炉外精炼及铁水预处理实用技术手册,冶金工业出版社,北京,2004年6月第一版,155]这种目的的铁水预处理脱硅模式现在运用已经越来越少。
另一种则是现在普遍使用的工艺,主要目的是为后续进行的铁水预处理脱磷创造良好的条件。
这种处理模式其原始硅可能较高,但也可能已经比较低如0.3%,不管怎样还是要进行处理,其硅的目标值为:0.08%¬0.10%。
因为只有在硅的含量低于0.10%的条件下,铁水预处理脱磷才能取得较好的作业指标。
经过铁水预处理脱硅后,铁水的硅含量从原始的0.35%¬0.50%左右,降低到0.08%¬0.10%的范围,再经过铁水预处理脱磷,硅含量继续下降,大约降低到0.004%¬0.006%左右的范围。
在转炉冶炼如仍主要用石灰造渣的话,化渣有一定的困难,此时需要加一些能有效化渣的矿物。
2、脱硅模式和工艺脱硅模式主要有高炉炉前预处理脱硅和铁水站预处理脱硅两种方式。
高炉炉前处理又有撇渣器前铁水沟处理和摆动溜槽处理两种方式。
高炉炉前处理有利的一面是:不需要另外投资兴建处理车间,不占用铁水停留时间,充分利用出铁过程中自然形成的铁水落差的冲击力;不利一面是:会恶化炉前操作环境,增设一些设备如喷吹设备、投料设备或多或少会给正常操作带来不利影响,脱硅率较低且不稳定。
用铁水预处理站脱硅,脱硅率较高并相对稳定,工人操作条件较好,但是这种方式需要投资,铁水停留时间增加,温降也相应增加,需要专门机械设备扒渣。
- 1、下载文档前请自行甄别文档内容的完整性,平台不提供额外的编辑、内容补充、找答案等附加服务。
- 2、"仅部分预览"的文档,不可在线预览部分如存在完整性等问题,可反馈申请退款(可完整预览的文档不适用该条件!)。
- 3、如文档侵犯您的权益,请联系客服反馈,我们会尽快为您处理(人工客服工作时间:9:00-18:30)。
铁水预脱硅铁水预脱硅(desiliconization of hot metal)铁水进入炼钢炉前的降硅处理。
它是发展较早的一种铁水预处理工艺,是分步精炼工艺的发展。
能改善炼钢炉的技术经济指标,降低炼钢费用,也可作为预处理脱磷、脱硫的前处理,可降低脱磷处理剂消耗,进一步生产纯净优质钢。
简史铁水预处理脱硅开始较早,1897年曾有人用平炉进行了脱硅脱磷的预备精炼工业试验,20世纪初进行了混铁炉脱硅,到40年代试验了高炉出铁时的脱硅,中国于50年代曾在鞍山钢铁公司实施过预备精炼炉脱硅和高炉铁水沟脱硅,这些都对改善平炉炼钢的冶炼技术经济指标和提高生产率起了良好的作用。
到了90年代,基于对优质钢材的需求,以及钢铁生产工艺本身节省资源和能量、减少渣量等公害的需要,日本发展了以脱硅、脱磷为目的的铁水预处理。
此后发展成两类预脱硅工艺,一类是作为铁水同时脱磷、脱硫的前工序,以提高其效率,这种铁水进入转炉只需完成脱碳和提高温度,炉渣减少到微量保护渣层的程度,主要生产高纯钢种;另一类是作为降低转炉渣量的措施。
1985年前后日本各大厂曾广泛采用,主要在高炉炉前进行。
后来,由于高炉冶炼低硅铁技术的发展,这类预脱硅方法已较少使用。
原理硅是易氧化元素。
脱硅反应可表示如下:按硅在渣相和金属相问的分配比可表示为式(2):式中L si为硅在渣铁间分配率;C si为硅容量(K si/γ(sio2 ) );a [O]为氧在铁水中活度;f [si]为硅在铁水中活度系数;γ(sio2 )为氧化硅在渣相中的活度系数;K’ Si为反应式(1)的平衡常数。
在碳饱和铁水中硅的活度系数根据各元素相互作用系数按下式计算:按一般炼钢生铁计算,f Si约在7~8之间。
硅容量C si,表示了渣相的溶硅能力。
它与渣中二氧化硅的活度系数,γ(sio2)成反比。
硅容量和渣成分有密切关系。
图1给出了FeO--SiO2--CaO--CaF2渣系的硅容量。
从以上热力学性质可以看出:(1)在一定温度和生铁成分条件下,脱硅能力决定于渣相的硅容量和供氧强度。
(2)脱硅过程中随着生铁成分的变化(硅锰等含量下降)f Si下降。
用氧化铁脱硅发生以下反应:[Si]+2(FeO)= (SiO2 )+2Fe (4)此反应可认为分成以下步骤:硅自铁水向渣铁界面转移;渣铁界面的化学反应;二氧化硅从渣铁界面向渣中转移;渣中氧化铁向渣铁界面转移。
成田等人用氧化铁脱硅实验发现:渣中FeO含量大于40%时,铁水中硅向渣铁界面扩散是反应的限制环节。
FeO含量小于10%时,渣中FeO向渣铁界面扩散是反应的限制环节。
FeO含量在10%~40%之间,为两种扩散的混合控制。
按硅在铁水中扩散为控制环节时,反应速度可写成式中K si为铁水中硅的表观传质系数,cm/s;A为渣铁间界面积,cm2;V为铁水体积,cm3;[%Si] 为时间t 时铁水中硅含量;[%Si] *为时间t 时界面硅含量。
若渣铁界面有足够的(FeO)脱硅渣,渣铁处于平衡状态,界面铁水的硅含量[%Si]≈0,则式(5)积分可得式(6):式中[%Si] 0为铁水中起始硅含量。
将实验结果按- d[%Si] / dt 和[%Si] 的关系作图2,可以证实,反应初期脱硅按式(5)3生行,与式(6)的直线式一致。
与[%Si]。
、铁量、渣成分、渣量无关,只受搅拌强度的影响。
按式(6)计算的K si与温度的关系求活化能为15kcal /mol。
此值近似于饱和碳铁水中硅的扩散活化能。
这也说明反应初期铁水中硅的扩散是限制性环节。
反应后半期逐渐偏离直线。
其偏离值相当于式(5)中K si A / V [%Si]*值。
由初期的K si和A/V求[%Si]*,得出各时期的(FeO)%与[%Si]*/[%Si]的关系图3,结果是(%FeO)≥40%[%Si]*/[%Si] =0。
若外延至(%FeO)≈10%时[%Si]*/[%Si] =1。
大贯一雄等人用气体氧喷吹脱硅,实验研究了上浮过程中的反应模型。
将反应分为喷枪前端、上浮过程和顶渣/铁水界面三个区。
枪前端为铁水中Fe、Si、Mn、C与O2的反应区。
后两区均为FeO与铁水中Si、Mn反应区。
喷吹过程顶渣中FeO在5%以下,可以认为与顶渣的反应是受渣中传质控制的。
但大部分反应是在上浮过程中发生的。
对整体来说可按混合控制考虑。
脱硅工艺硅一直作为转炉炼钢的发热元素。
但随着转炉容量增加和冶炼技术的进步,需要由硅提供的热量逐渐减少。
又由于减少渣量对炼钢技术经济指标改善十分有利,所以对铁水含硅量的要求逐渐降低,尤其是需要预处理脱磷脱硫的铁水。
根据不同的冶炼工艺和技术经济条件,大致可分为以下两种情况:(1)对需要脱磷脱硫预处理的铁水,其硅含量分成两种,如果使用苏打系熔剂,则硅含量要求小于0.10%;如果使用石灰系熔剂,则硅含量要求小于0.15%。
因为高于此值时熔剂首先用于脱硅,不能脱磷,不利于提高脱磷渣碱度(脱磷渣碱度CaO/SiO2为3.5~6.0)和脱磷剂利用率。
(2)对直接供给转炉炼钢的铁水,按不同对象钢种(指高温或低温出钢),以[Si]0.5%为基准,改变硅含量对炼钢时铁矿石加入量、炉渣碱度、渣中TFe量和铁收得率、锰铁合金消耗、渣量和喷溅损失等对冶炼成本的影响,得出低温(1610℃±10℃)出钢要求的铁水含硅量以0.20%时成本最低,大于或小于0.2%时都引起成本升高。
高温(1700℃±10℃)出钢要求的铁水含硅量小于0.40%,高于0.40%时则引起成本上升。
脱硅方式按处理场所不同分为在高炉出铁过程中连续脱硅和在铁水罐(或鱼雷车)中间歇处理两种;按加入方法有自然落下的上置法,喷枪在铁水面上的顶喷法和喷枪插入铁水的喷吹法等;按搅拌方法有吹气搅拌、铁水落下流搅拌、喷吹的气粉流搅拌和叶轮搅拌。
脱硅方式的选择主要根据铁水含硅量、要求处理后的含硅量和已有设备限制等条件来确定。
若铁水含硅量大于0.45%~0.50%,应设置高炉炉前脱硅。
若铁水需预处理脱磷、脱硫,需先在铁水罐中脱硅,将含硅量降至0.10%~0.15%以下。
出铁场脱硅有的脱硅剂以皮带或溜槽自然落下加入铁水沟,经铁水落下流将脱硅剂卷入进行反应。
有的铁水沟有落差,脱硅剂高点加入,过落差点有一段反应距离,再设置撇渣器将脱硅渣分离。
硅含量可由0.50%降至0.20%,锰也有下降。
有的脱硅剂以加速添加方式进行。
一种为插入铁水的喷枪,以高速气粉流喷入,喷枪处铁水沟改造为圆形反应坑。
喷枪为横吹4孔;另一种喷枪在铁水面上,以高速气粉流向铁水投射。
有的投射点在铁水沟,该处改造为较宽较深的反应室。
有的投射点在摆动流嘴处。
这些加速添加方式都改善了反应的动力学条件。
同时还需克服喷溅过大、耐火材料侵蚀等问题。
铁水罐脱硅这种脱硅在专门预处理站进行。
采用插入铁水的喷枪脱硅。
脱硅剂粒度为-40~-100目,处理温度低(约1320℃左右),需加氧枪面吹(距铁水面200mm左右),防止温度下降。
当气体氧/固体氧在0.3~0.5范围时,平均脱硅量0.59%,铁水处理后温度基本不变,气体氧用量相当于1.4~2.0m3/t。
若上述比值增至0.6~1.0,平均脱硅量0.48%,则处理后平均升温50℃左右。
与高炉炉前脱硅相比,高炉前脱硅不需增加脱硅时间和工序,热损失少,铁水温降不大。
处理温度较铁水罐脱硅高100℃左右,但铁水罐装入量减少10%~30%,出铁中的硅含量,铁流大小和温度较难控制,影响了脱硅效率的稳定性。
从设备上看,炉前脱硅随出铁沟的设置需多点处理,设备费用高。
但不需新建厂房。
炉前脱硅的过程控制为了给炼钢提供成分稳定的低硅铁水,必须根据出铁时的硅含量和出铁速度确定和控制脱硅剂的输送速度和添加量。
典型的控制系统包括高炉热控制模型预报铁水含硅量,出铁期间硅含量在线快速分析,再根据炼钢要求的含硅量控制脱硅剂加入量。
硅含量的快速分析已开发多种,生产已采用的有两种:一种为将圆片状试样夹在两电极间,其间温差200℃,电极间热电势随硅含量增加而上升。
测量范围是0~1.5%Si,精度σ=0.02%。
插入试样至显示结果需50s。
另一种为固体电解质定硅探头,其结构为Cr•Cr2O3//ZrO2-MoO//SiO2/Si(铁中),用钼丝作高温导线。
当固体电解质外套石英管SiO2与铁水中硅平衡时,有如下关系:[Si]+2[O]=(SiO2) (7)从测定固体电解质/铁水/石英套管间氧的活度得出相应的硅含量,即硅含量与输出电势(毫伏值)的关系。
用此方法控制调节脱硅剂加入量的效果是:目标硅为0.05%~0.12%时,命中率由46%提高至77%,脱硅剂消耗减少30%。
脱硅用耐火材料脱硅渣与高炉渣比较,前者FeO含量高。
原来用Al2O3 - SiC-C 系的铁沟耐火材料在渣线部分侵蚀严重。
因此在渣线部分改变材质,在脱硅剂加入处扩大铁水沟尺寸,铁沟侧壁埋设强制风冷管等。
对高FeO的脱硅渣,由于SiC、C被氧化而受到侵蚀,可用Al2O3- MgO系耐火材料代替,耐侵蚀性主要在于成渣反应生成液相量的大小。
试验证实,当MgO/Al2O3大于1.0时,液相的生成受到抑制,原因在于脱硅渣中FeO与MgO=Al2O3反应生成高熔点矿物。
影响脱硅的因素主要有脱硅剂单耗、处理前含硅量、反应界面积(即铁水与脱硅剂混合状况)、脱硅剂的种类和粒度等。
根据炉前脱硅和铁水罐脱硅的生产数据,温度在1250~1450℃范围内,温度变化对脱硅没有明显影响。
脱硅剂单耗和原始硅含量铁水含硅量大于0.5%时,一般每吨生铁加入脱硅剂10~30kg、脱硅量约0.1%~0.4%,脱硅剂单耗增加,脱硅量增加,但其增加幅度减小。
这与铁水含硅量逐渐降低后脱硅氧效率降低有关。
与硅以外的其他元素(C、Mn等)的氧化有关。
脱硅反应与脱硅剂单耗的关系可用下式表示-ln[Si]f /[Si]0 = KW (8)式中[Si] f 为处理后铁水含硅量;[Si]0 为处理前铁水含硅量;K为比例常数;W为脱硅剂单耗,kg/t。
脱硅氧效率η si可按下式表示η si =与硅反应的氧/ 脱硅剂中的全氧×100%(9)实践证实,铁水原始硅含量对脱硅氧效率影响较大,当[Si]0 >0.5%时;η si在70%以上,当[Si]0降低时,效率急剧变差,当[Si]0=0.2%时,η si约40%。
反应界面积即铁水与脱硅剂的混合。
出铁速度影响着铁水与脱硅剂的混合。
在[Si]0=0.4%~0.6%时,向摆动流嘴处加入25~30kg/t的脱硅剂,当铁流速度由6t/min 提高到9t/min,脱硅率由40%提高到60%。
铁沟上顶部投射法(TIM),喷枪不插入铁水,能改善脱硅的氧效率,尤其是要求终硅量达0.1%~0.2%时,投射法比自然落下法(SFM) η si 提高约10%。