铁水预脱硅
铁水预处理

计算中心
王丽 丽
8 铁水预处理
铁水预处理是指铁水兑入炼钢炉之前进行的各种处理。 铁水预处理是指铁水兑入炼钢炉之前进行的各种处理。 普通铁水预处理包括:铁水脱硫、铁水脱硅和铁水脱磷。 普通铁水预处理包括:铁水脱硫、铁水脱硅和铁水脱磷。 8.1 铁水预脱硫 脱硫剂:石灰粉(CaO)、电石粉( )、电石粉 和金属镁。 1、脱硫剂:石灰粉(CaO)、电石粉(CaC2)和金属镁。 石灰粉: 1)石灰粉: 2CaO(S)+ [S] + 1/2[Si] =(CaS)(S) + 1/2(Ca2SiO4) ) 电石粉: 2)电石粉: CaC2(S)+ [S] ==(CaS)(S) + 2[C] ) 2(S) 电石粉需要以惰性气体密封保存和运输。 电石粉需要以惰性气体密封保存和运输。 金属镁: 3)金属镁: Mg+ [S]=MgS(S) 金属镁活性高,极易氧化,易燃易爆, 金属镁活性高,极易氧化,易燃易爆,所以镁粒必须表面 钝化后才能安全的运输、储存和使用。 钝化后才能安全的运输、储存和使用。
镁在铁水温度下与硫有较强的亲和力。特别是在低温下 镁在铁水温度下与硫有较强的亲和力。 镁脱硫效率极高。用镁脱硫铁水温降小, 镁脱硫效率极高。用镁脱硫铁水温降小,渣量及铁损均 少且不损坏处理罐内衬,也不影响环境。 少且不损坏处理罐内衬,也不影响环境。因而铁水包喷 镁脱硫工艺获得了迅猛的发展。 镁脱硫工艺获得了迅猛的发展。 镁价格昂贵,保存时须防止吸潮。 镁价格昂贵,保存时须防止吸潮。 2、脱硫方法——喷吹法 脱硫方法——喷吹法 —— 此法是用喷枪以惰性气体为载体, 此法是用喷枪以惰性气体为载体,将脱硫剂与气体混合 吹入铁水深部, 吹入铁水深部,以搅动铁水与脱硫剂充分混合的脱硫方 该法可以在鱼雷罐车或铁水包内处理铁水。 法。该法可以在鱼雷罐车或铁水包内处理铁水。
(铁水预处理)炼钢工艺学

水含硫又高的小钢铁厂,还经常被采用。
机械搅拌法
靠旋转沉入铁水中的搅拌器或转动盛铁水的容器使铁水 与脱硫剂搅拌混合。
采用搅拌器和采用转动容器机械搅拌法,均可控制铁水 与脱硫剂的搅拌时间和搅拌强度,用CaC2作脱硫剂能得到 >90%的脱硫效率(单向摇包法搅拌混合较差,脱硫率比双向 摇包法约低10%),可以把铁水中的硫稳定地降低到<0.010%。
1、铁水预脱磷的基本原理
铁水中的磷首先氧化成P2O5,然后与强碱性氧化物结合成 稳定的磷酸盐而去除。
在铁水预脱磷过程中,首先要有适当的氧化剂将溶解于 铁水中的磷氧化,然后采用强有力的固定剂,使被氧化 的磷牢固地结合在炉渣中。
4.4 铁水预脱磷工艺
2、铁水预脱磷方法 ◆ 在高炉出铁沟或出铁槽内进行脱磷 ◆ 在铁水包或鱼雷罐车中进行预脱磷 ◆ 在专用转炉内进行铁水预脱磷
武钢旋转实心搅拌器的KR机械搅拌法,铁水的含硫量 可从0.06%降低到0.005%。实践证明,此类脱硫设备可以用 价廉的石灰进行有效的脱硫。设备最简单,脱硫效率高。
转动容器的回转炉法和摇包法,由于设备复杂,维修费用高 和难于大型化,发展前途不大。
搅拌器法
旋转实心搅拌器的 搅拌法(KR法)
旋转空心搅拌器的搅 拌法(DORA法)
4.5 铁水“三脱”工艺
铁水三脱工艺特点 o 优点: ▪ 可实现转炉少渣冶炼(渣量< 30 kg/t)。 ▪ 铁水脱硫有利于冶炼高碳钢、高锰钢、低磷钢、特殊钢
(如轴承钢、不锈钢)等。 ▪ 可提高脱碳速度,有利于转炉高速冶炼。 ▪ 转炉吹炼终点时钢水锰含量高,可用锰矿直接完成钢水合
金化。 o 缺点: ▪ 铁水中发热元素减少,转炉的废钢加入量减少。 转炉少渣炼钢工艺——铁水预处理将S、P(脱P需先脱Si )
铁水预处理中的硅元素的流动
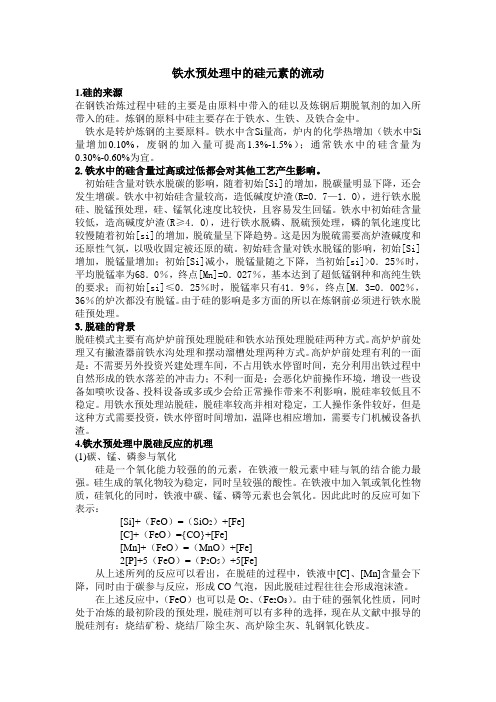
铁水预处理中的硅元素的流动1.硅的来源在钢铁冶炼过程中硅的主要是由原料中带入的硅以及炼钢后期脱氧剂的加入所带入的硅。
炼钢的原料中硅主要存在于铁水、生铁、及铁合金中。
铁水是转炉炼钢的主要原料。
铁水中含Si量高,炉内的化学热增加(铁水中Si 量增加0.10%,废钢的加入量可提高1.3%-1.5%);通常铁水中的硅含量为0.30%-0.60%为宜。
2.铁水中的硅含量过高或过低都会对其他工艺产生影响。
初始硅含量对铁水脱碳的影响,随着初始[Si]的增加,脱碳量明显下降,还会发生增碳。
铁水中初始硅含量较高,造低碱度炉渣(R=0.7—1.O),进行铁水脱硅、脱锰预处理,硅、锰氧化速度比较快,且容易发生回锰。
铁水中初始硅含量较低,造高碱度炉渣(R≥4.0),进行铁水脱磷、脱硫预处理,磷的氧化速度比较慢随着初始[si]的增加,脱硫量呈下降趋势。
这是因为脱硫需要高炉渣碱度和还原性气氛,以吸收固定被还原的硫。
初始硅含量对铁水脱锰的影响,初始[Si]增加,脱锰量增加;初始[Si]减小,脱锰量随之下降,当初始[si]>0.25%时,平均脱锰率为68.0%,终点[Mn]=0.027%,基本达到了超低锰钢种和高纯生铁的要求;而初始[si]≤0.25%时,脱锰率只有41.9%,终点[M.3=0.002%,36%的炉次都没有脱锰。
由于硅的影响是多方面的所以在炼钢前必须进行铁水脱硅预处理。
3.脱硅的背景脱硅模式主要有高炉炉前预处理脱硅和铁水站预处理脱硅两种方式。
高炉炉前处理又有撇渣器前铁水沟处理和摆动溜槽处理两种方式。
高炉炉前处理有利的一面是:不需要另外投资兴建处理车间,不占用铁水停留时间,充分利用出铁过程中自然形成的铁水落差的冲击力;不利一面是:会恶化炉前操作环境,增设一些设备如喷吹设备、投料设备或多或少会给正常操作带来不利影响,脱硅率较低且不稳定。
用铁水预处理站脱硅,脱硅率较高并相对稳定,工人操作条件较好,但是这种方式需要投资,铁水停留时间增加,温降也相应增加,需要专门机械设备扒渣。
1-铁水预处理工艺

3.2 铁水脱磷装置示意图
四、转炉双联法脱磷工艺
日本和歌山制铁所炼钢厂工艺布置示意图
4.1 脱磷转炉
脱磷炉加15%废钢(尺寸稍小些) 脱碳炉加2%废钢(尺寸稍大些) 脱磷炉:废钢与脱碳炉渣一起从料槽加入。 BOFd[p]:[C]:4.7%~3.7% 吹氧时间9min [P]:从0.1%(1000ppm)→降到0.01% (100ppm)周期时间20min 炉龄: 25000炉,炉渣R:≤2,渣量 ~35kg/t,脱磷炉供氧强度是脱碳炉的1/4~1/2。 脱磷炉加入造渣料:BOFd[C]返渣(约占脱碳 炉渣总量的1/2)+石灰 脱磷炉渣:由于碱度≤2,可直接用于筑路 等 半钢温度1300℃左右, 回收煤气,流量为 35000~40000m3/h
五、铁水预处理对纯净钢的意义
铁水含磷、硫可降到低或超低含量水平。 提高转炉生产率、降低成本、节约能耗。 极低碳钢的清洁度。钢中T[O]、[N]、[H]含
量降低。 有利于复吹转炉冶炼高碳钢时的“保碳出钢 技术”。 有效地提高铁、钢、材系统的综合经济效益。
二、铁水脱Si(120t转炉)
铁水脱Si的重要意义: 铁水脱磷的必要条件 利于减少石灰加入量和渣量
铁水脱Si的工艺方法铁水罐脱硅 转炉脱硅
2.1 脱Si剂、脱Si原理
脱硅剂: 氧化剂:氧气,氧化铁皮,精矿粉,烧结矿粉,氧 化铁烟尘 溶剂:石灰,萤石 铁水脱Si化学反应: [Si]+O2(g)=SiO2 [Si]+(2/3)Fe2O3(s)=SiO2(s)+(4/3)Fe [Si]+(1/2)Fe3O4(s)=SiO2(s)+(3/2)Fe [Si]+2(FeO)=SiO2(s)+2Fe
铁水预处理技术

铁水炉外脱硫的经济性也是可观的,如某 铁厂采用铁水炉外脱硫后,高炉碱度从1.25降低 到1.06,焦比降低36kg/t,生产率提高36%。
19
Northeastern University
常 用 铁 水 脱 硫 处 理 方 法 分 类
1982年5月:日本住友公司鹿岛厂 开发的“住友碱精炼 法”—SARP法投产(苏打精炼法)
1982年9月:新日铁君津厂开发的最佳精炼法—ORPD法 投产,以石灰系溶剂进行脱磷脱硫
80年代:以意大利TARANTO 钢厂为代表的欧洲钢铁企 业也进行了铁水三脱试验,但没有推广
80年代:日本住友金属公司和神户钢铁公司分别开发了 采用专用转炉脱磷的SRP法和H炉法
(2)铁水中的碳和硅等能够大大提高硫在铁水中的活 度系数,使硫很容易就能脱到很低水平;
(3)铁水中氧含量较低,硫的分配系数相应有所提高, 有利于脱硫;
17
Northeastern University
(4)铁水炉外脱硫可以在鱼雷车、铁水罐中进行,也可以在 出铁槽中进行,这样可以减少处理投资; (5)铁水处理温度较低,对处理装置的寿命有益; (6)在铁水炉外脱硫的过程中铁水成分的变化比炼钢或钢水 处理过程中钢水成分的变化对最终钢种的影响小。
Hale Waihona Puke 先在铁水沟内加脱氧剂脱硅,然后在鱼雷罐车或铁水 包中喷吹脱硅,即前两种方法的混合。
当铁水含硅量低于0.4%时,可采用简单的铁水沟脱硅法。 当硅含量大于0.4%时,脱硅剂用量增大,泡沫渣严重, 适宜采用脱硅效率高的喷吹法或两段法。若炼钢厂扒渣能 力不足,应采用两段脱硅法,利用挡渣器分离渣铁。 台湾中钢的实践表明使用两步脱硅操作使硅含量下降到 0.15%以下,同时脱磷、脱硫的程度也明显提高。 日本新日铁的在高炉出铁沟和300t鱼雷罐车上采用两段 法进行脱硅处理,处理后硅含量可以达到0.12%。
转炉炼钢操作-铁水预处理

相关知识
四、常见脱硫剂及特点 1.苏打灰
其主要成分为Na2CO3,铁水中加入苏打灰后,与硫作用发生以下3个化学 反应:
用苏打灰脱硫,工艺和设备简单,其缺点是脱硫过程中产生的渣会腐蚀 处理罐的内衬,产生的烟尘污染环境,对人有害。目前很少使用。
相关知识
四、常见脱硫剂及特点 2.石灰粉
其主要成分为CaO,用石灰粉脱方法 2. KR搅拌法
KR法铁水预处理脱硫具体操作要求如下: (1)在处理之前,必须将铁水包内的渣子充分扒除,否则会严重影响 脱硫效果。 (2)处理过程中设置搅拌器的转数一般为90~120r/min,在搅动1~ 1.5min后开始加入脱硫剂,搅动时间约13min左右。 (3)处理完毕后,还需仔细地扒除脱硫渣。 ① KR搅拌法的优点:脱硫效率高、脱硫剂消耗少、金属损耗低。 ② KR搅拌法的缺点:温降大,处理10~15min过程温降约50 ℃,搅拌 过程为了铁水液面波动,液面至包口距离应不小于629mm。
石灰价格便宜、使用安全,但在石灰粉颗粒表面易形成2CaO·SiO2致密层, 限制了脱硫反应进行,因此,石灰耗用量大,致使生成的渣量大和铁损大, 铁水温降也较多。另外,石灰还有易吸潮变质的缺点。
相关知识
四、常见脱硫剂及特点 3.电石粉
用电石粉脱硫,铁水温度高时脱硫效率高,铁水温度低于1300℃时脱硫 效率很低。另外,处理后的渣量大,且渣中含有未反应尽的电石颗粒,遇水 易产生乙炔(C2H2)气体,故对脱硫渣的处理要求严格。在脱硫过程中也容 易析出石墨碳污染环境。电石粉易吸潮生成乙炔(乙炔是可燃气体且易发生 爆炸),故电石粉需要以惰性气体密封保存和运输。
相关知识
三、铁水预脱硫的方法 2. KR搅拌法
这种脱硫方法是以一种外衬耐火材料的搅拌器浸入铁水罐内,利用搅拌 器在铁水中旋转搅动铁水,使铁水产生漩涡,在铁液面中央部分产生一个漩 涡下流坑,同时加入脱硫剂使其在下陷坑中被卷入铁水内部进行脱硫反应 (如图所示),从而得到脱硫的目的。
常用铁水预处理技术

常用铁水预处理技术常用铁水预处理技术铁水预处理基础知识1、什么是铁水预处理?★铁水预处理指铁水兑人炼钢炉之前,为除去某些有害成份或回收某些有益成分的处理过程。
针对炼钢而言,主要是使铁水中硅、磷、硫含量降低到所要求的范围,以简化炼钢过程,提高钢的质量。
铁水预处理具体分为铁水炉外脱硅、脱磷和脱硫,有时脱磷和脱硫同时进行。
对于铁水含有特殊元素提纯精炼或资源综合利用而进行的提钒、提铌、提钨等预处理技术则称为特殊预处理。
2、什么是铁水“三脱”技术?★指铁水兑人炼钢炉之前,进行脱硫、脱硅、脱磷的预处理工艺过程。
3、铁水脱硫的目的是什么?★提高钢质、扩大品种和改善炼钢操作,提高钢的机械、工艺性能。
4、铁水脱硅的目的是什么?⑴减少转炉炼钢渣量、改善操作和提高炼钢经济指标。
硅是氧气转炉炼钢发热的元素,所以为了提高炼钢熔池温度和早化渣,往往希望铁水含硅高一些,但实践证明铁水含硅高时,为了保证转炉渣有较高的碱度,势必增加石灰消耗量,使渣量增多,冶炼时间延长,耗氧量增加,喷溅加剧,铁损增加,并给操作带来困难,从而降低炼钢生产率和增加生产成本。
铁水含硅量一般应控制在0.4%以下的水平。
(2)铁水预脱磷的需要脱硅是铁水预脱磷的先决条件。
铁水预脱磷要求脱磷反应区的氧位高,当加入氧化剂提高氧位时,硅首先就与氧作用而降低铁水中的氧位。
为此,脱磷首先要脱硅,脱磷前控制硅含量一般要求在0.15%以下。
5.铁水脱磷的目的是什么?(1)生产低磷钢、超低磷钢和不锈钢等工艺需要。
磷在钢中对性能的影响,除少数钢种为提高强度或耐大气腐蚀性,要求有一定含磷外,对大多数钢种是有害的,它降低钢的冲击韧性,尤其是低温冲击韧性;磷的枝晶偏析使板材产生带状组织,造成钢板各向异性。
随着新技术材料的发展,对某些品种钢要求磷含量≤0.01%(低磷钢) 或≤0.005%(超低磷钢) 。
用转炉工艺脱磷,虽然有较好的脱磷效果,但达到这种低磷的水平是难以完成的,如采取多次造渣操作,有可能达到,但都存在渣料消耗大,冶炼时间长,热损失大,金属收得率低等问题。
铁水脱硅的工业试验研究

1 前 言
实 现通 过转 炉进 行处 理 。在 2 0 0 9年 9月 份重 钢大 渡
铁水 脱 硅 处 理 是铁 水 预 处 理 的一 个 重 要 环节 , 铁 水 硅 含 量 高将 给转 炉 的正 常 操 作带 来 不 良后 果 ,
口地 区老生产 基地 ,利 用 8t 水包对 硅含 量在 正 常 0铁 范 围 的铁 水 进行 渣 洗 脱硅 的工 业试 验 ,并 对 影 响脱 硅 的 因素进行 分 析 ,实 现脱 硅反 应 的平稳 进行 。
孽● 披 鼋
C S T CHN L l C E O oGY
铁 水 脱 硅 的工 业 试 验 研 究
张杰新 龙 贻菊 胡 昌志
( 重钢股份公司炼钢厂 )
摘
要
本文 总 结 了重钢 铁水 渣洗 脱硅 的工 艺试 验 。分析 了脱 硅 剂加入 量 、原始 硅含 量及 脱硅操 作 等对脱 硅 铁水 脱硅 渣 洗 脱硅 脱 硅效 果
An i d s il e t e i c n z t n p o e s f o tl n C o g i g I n& S e l o L di u u t a s d sl o ia i r c s t n r t i o o h me a h n q n o i r t e . t s mma ie C s r di z n
固体脱硅剂需要升温融化而吸热 ,因此采用 固体脱 硅剂脱硅会导致铁水温有所下降。脱硅剂的理化指 标 见表 1 。
表 1脱硅剂理化指标
・
2 ・ 5
《 铁水脱硅的工业试 验研究 》
根据 表 1设 计 的脱硅剂 在 高炉 出铁过 程 中分批 加人 ,即出铁 5 i后 ,根据 出铁 时 间及铁 水液 面起 mn 泡情 况加 入一定 量 的脱硅 剂 。最后 出铁5 i停 止加 mn 料 ,并在 出铁后 期 加入适 量铝 渣进行 消 泡 。
铁水预处理技术01-02

¾ 历史背景: 60年代,氧枪转炉炼钢的崛起工业的发展给钢铁材料质量和焊接性能
好;抗腐蚀和高温性能好 用户需求:降低钢中杂质:硫、磷含量越低越好! 发展现状:30年代开始,60年代蓬勃发展!
第一章 铁水预处理概述
序,有的厂铁水实现了100%的预处理。平均约80%的铁 水经过脱硫;日本50%左右的铁水经过脱硅,40%以上的 铁水经过脱磷处理。
第一章 铁水预处理概述
• 2. 国外三脱技术的发展
¾ 六类十六种脱硫方法: 摇动法:瑞典的单向偏心摇动铁水罐法,日本神户尼崎铁
厂可逆旋转式DM摇包法。 机 械 搅 拌 法 : 原 西 德 DO(Damage Ostberg) 法 、
受研究者关注。
第一章 铁水预处理概述
• 4. 铁水预处理发展趋势 预脱硫→预脱硅→预脱磷(同时脱磷脱硫);
未来以喷吹法为主; 脱硫剂受原料经济和钢材产品要求而波动; 发展方向:高效、廉价、易得的复合脱硫剂;CaO系、
外预处理技术已在世界各国广泛应用。
第一章 铁水预处理概述
¾ 铁水预处理的必要性和迫切性:
是脱硫反应化学冶金学合理性的必要;
☺高炉: 动力学条件差,脱硫要付出代价;
☺
高炉脱硫:高炉温、焦比高、产量低。
☺转炉: 热力学条件不好,几乎无脱硫能力。
☺炉外: 可创造良好的热力学和动力学条件。
是钢材市场竞争力紧迫性的必要;
RS(Rheinstahl) 法 和 赫 歇 法 、 日 本 新 日 铁 KR(Kambara Reactor)法、千叶NP法。 吹气搅拌法: 新日铁PDS(底喷)法和CLDS(顶喷)法。 钟罩压入法:美国Janes Laughlin公司的镁焦法。 喷 吹 法 : 西 德 Thyssen 的 ATH(斜 插喷 枪 )法; 新日铁的 TDS(顶喷)法。 炉前铁水沟连续脱硫法。
铁水预处理“脱硅—脱硫—脱磷”顺序的选择
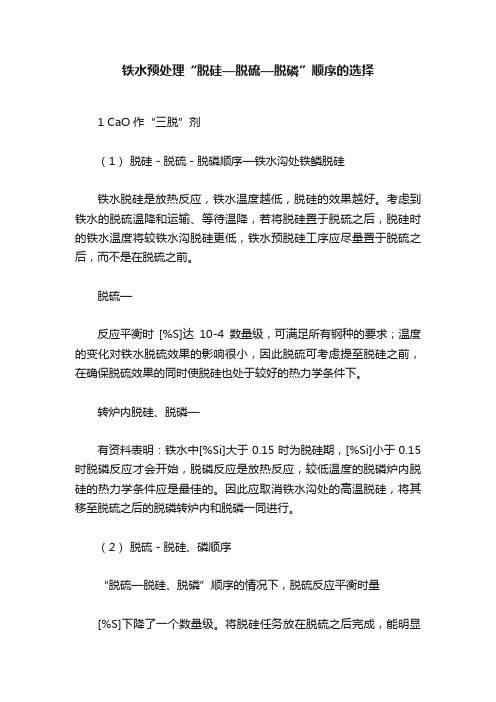
铁水预处理“脱硅—脱硫—脱磷”顺序的选择1 CaO作“三脱”剂(1)脱硅-脱硫-脱磷顺序—铁水沟处铁鳞脱硅铁水脱硅是放热反应,铁水温度越低,脱硅的效果越好。
考虑到铁水的脱硫温降和运输、等待温降,若将脱硅置于脱硫之后,脱硅时的铁水温度将较铁水沟脱硅更低,铁水预脱硅工序应尽量置于脱硫之后,而不是在脱硫之前。
脱硫—反应平衡时[%S]达10-4数量级,可满足所有钢种的要求;温度的变化对铁水脱硫效果的影响很小,因此脱硫可考虑提至脱硅之前,在确保脱硫效果的同时使脱硅也处于较好的热力学条件下。
转炉内脱硅、脱磷—有资料表明:铁水中[%Si]大于0.15时为脱硅期,[%Si]小于0.15时脱磷反应才会开始,脱磷反应是放热反应,较低温度的脱磷炉内脱硅的热力学条件应是最佳的。
因此应取消铁水沟处的高温脱硅,将其移至脱硫之后的脱磷转炉内和脱磷一同进行。
(2)脱硫-脱硅、磷顺序“脱硫—脱硅、脱磷”顺序的情况下,脱硫反应平衡时量[%S]下降了一个数量级。
将脱硅任务放在脱硫之后完成,能明显改善CaO粉剂脱硫的热力学条件。
(3)脱硅、脱磷-脱硫顺序在“脱硅、脱磷—脱硫”顺序的情况下,脱硫反应平衡时[%S]为10-3数量级,而在“脱硅—脱硫—脱磷”顺序下,[%S]为10-4数量级,在“脱硫—脱硅、脱磷”顺序下,[%S]为10-5数量级。
显然“脱硫—脱硅、脱磷”顺序下CaO粉剂脱硫反应的热力学条件更好。
(4)同时“三脱”机理研究表明:用氮氧复合气体作载气喷吹CaO粉同时进行铁水预处理“三脱”反应时,脱硅、脱磷主要是在喷枪附近的高氧势区进行的瞬时接触反应;脱硫则是还原性渣和铁水之间的持久接触反应。
对铁水预处理脱硅来说,脱磷转炉顶吹氧加CaO粉剂脱硅的热力学条件是最优的。
CaO的脱磷能力受铁水温度的影响很大,在其它操作条件允许的情况下,应该尽量在低温下脱磷。
“脱硫-脱硅、脱磷”顺序下,专用脱磷转炉脱磷时铁水的温度较同时“三脱”时低。
综合比较认为:CaO作三脱剂时,脱磷应在脱硫之后,并在专用转炉内进行最佳。
铁水预处理工艺技术操作规程
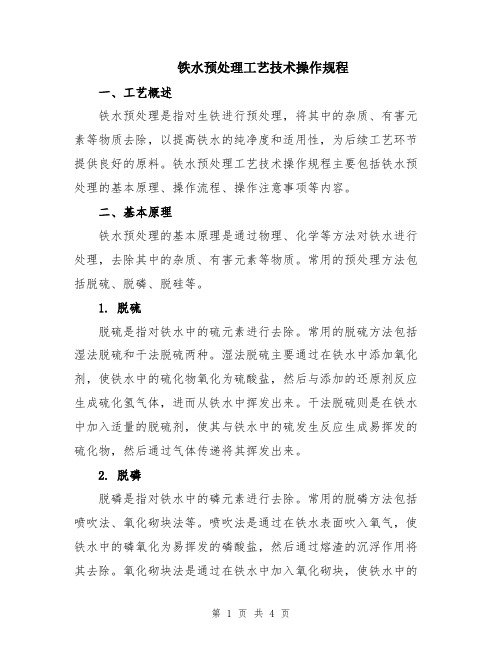
铁水预处理工艺技术操作规程一、工艺概述铁水预处理是指对生铁进行预处理,将其中的杂质、有害元素等物质去除,以提高铁水的纯净度和适用性,为后续工艺环节提供良好的原料。
铁水预处理工艺技术操作规程主要包括铁水预处理的基本原理、操作流程、操作注意事项等内容。
二、基本原理铁水预处理的基本原理是通过物理、化学等方法对铁水进行处理,去除其中的杂质、有害元素等物质。
常用的预处理方法包括脱硫、脱磷、脱硅等。
1. 脱硫脱硫是指对铁水中的硫元素进行去除。
常用的脱硫方法包括湿法脱硫和干法脱硫两种。
湿法脱硫主要通过在铁水中添加氧化剂,使铁水中的硫化物氧化为硫酸盐,然后与添加的还原剂反应生成硫化氢气体,进而从铁水中挥发出来。
干法脱硫则是在铁水中加入适量的脱硫剂,使其与铁水中的硫发生反应生成易挥发的硫化物,然后通过气体传递将其挥发出来。
2. 脱磷脱磷是指对铁水中的磷元素进行去除。
常用的脱磷方法包括喷吹法、氧化砌块法等。
喷吹法是通过在铁水表面吹入氧气,使铁水中的磷氧化为易挥发的磷酸盐,然后通过熔渣的沉浮作用将其去除。
氧化砌块法是通过在铁水中加入氧化砌块,使铁水中的磷与氧化砌块发生反应生成磷酸盐,然后通过熔渣的沉浮作用将其去除。
3. 脱硅脱硅是指对铁水中的硅元素进行去除。
常用的脱硅方法包括湿法脱硅和干法脱硅两种。
湿法脱硅主要是通过在铁水中加入足够量的碱性矿物,使硅与碱性矿物发生反应生成易挥发的硅酸盐,然后通过熔渣的沉浮作用将其去除。
干法脱硅则是在铁水中加入适量的脱硅剂,使其与铁水中的硅发生反应生成易挥发的硅化物,然后通过气体传递将其挥发出来。
三、操作流程铁水预处理的操作流程按照脱硫、脱磷、脱硅的顺序进行,具体步骤如下:1. 脱硫操作流程(1) 检查脱硫设备及周围环境的安全情况。
(2) 开始对铁水进行脱硫前,要先对铁水进行预热,使其温度达到预定的要求。
(3) 进行湿法脱硫时,在预热后的铁水中加入适当的氧化剂,并根据预定的脱硫时间进行搅拌。
铁水预处理中的硅元素的流动
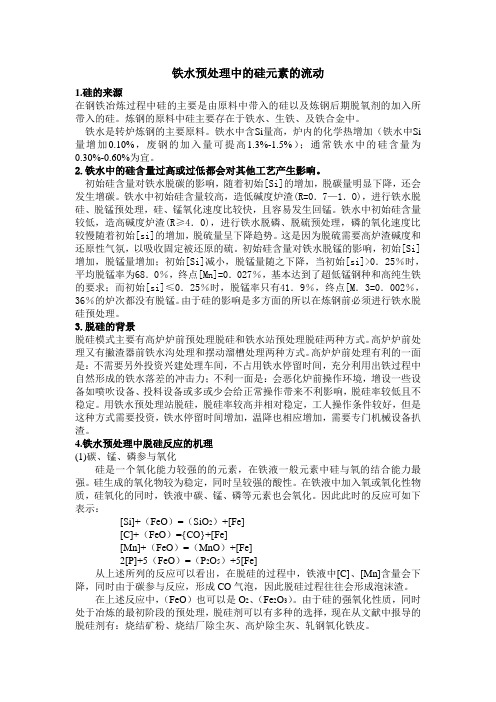
铁水预处理中的硅元素的流动1.硅的来源在钢铁冶炼过程中硅的主要是由原料中带入的硅以及炼钢后期脱氧剂的加入所带入的硅。
炼钢的原料中硅主要存在于铁水、生铁、及铁合金中。
铁水是转炉炼钢的主要原料。
铁水中含Si量高,炉内的化学热增加(铁水中Si 量增加0.10%,废钢的加入量可提高1.3%-1.5%);通常铁水中的硅含量为0.30%-0.60%为宜。
2.铁水中的硅含量过高或过低都会对其他工艺产生影响。
初始硅含量对铁水脱碳的影响,随着初始[Si]的增加,脱碳量明显下降,还会发生增碳。
铁水中初始硅含量较高,造低碱度炉渣(R=0.7—1.O),进行铁水脱硅、脱锰预处理,硅、锰氧化速度比较快,且容易发生回锰。
铁水中初始硅含量较低,造高碱度炉渣(R≥4.0),进行铁水脱磷、脱硫预处理,磷的氧化速度比较慢随着初始[si]的增加,脱硫量呈下降趋势。
这是因为脱硫需要高炉渣碱度和还原性气氛,以吸收固定被还原的硫。
初始硅含量对铁水脱锰的影响,初始[Si]增加,脱锰量增加;初始[Si]减小,脱锰量随之下降,当初始[si]>0.25%时,平均脱锰率为68.0%,终点[Mn]=0.027%,基本达到了超低锰钢种和高纯生铁的要求;而初始[si]≤0.25%时,脱锰率只有41.9%,终点[M.3=0.002%,36%的炉次都没有脱锰。
由于硅的影响是多方面的所以在炼钢前必须进行铁水脱硅预处理。
3.脱硅的背景脱硅模式主要有高炉炉前预处理脱硅和铁水站预处理脱硅两种方式。
高炉炉前处理又有撇渣器前铁水沟处理和摆动溜槽处理两种方式。
高炉炉前处理有利的一面是:不需要另外投资兴建处理车间,不占用铁水停留时间,充分利用出铁过程中自然形成的铁水落差的冲击力;不利一面是:会恶化炉前操作环境,增设一些设备如喷吹设备、投料设备或多或少会给正常操作带来不利影响,脱硅率较低且不稳定。
用铁水预处理站脱硅,脱硅率较高并相对稳定,工人操作条件较好,但是这种方式需要投资,铁水停留时间增加,温降也相应增加,需要专门机械设备扒渣。
铁水预处理方法

本文摘自再生资源回收-变宝网()铁水预处理方法铁水预处理是指将铁水兑人炼钢炉之前脱除杂质元素或回收有价值元素的一种铁水处理工艺,包括铁水脱硅、脱硫、脱磷(俗称“三脱”),以及铁水提钒、提铌、提钨等。
目前我国很多钢厂都采用了铁水预脱硫处理,甚至铁水三脱处理、提钒、提铌、提钨等,尤其是对于生产超低硫、超低磷钢种的转炉炼钢车间。
一、铁水预脱硅研究表明,铁水中硅含量为0.3%即可保证化渣和足够高的出钢温度,硅过多反而会恶化技术经济指标。
因此,有必要开展铁水预脱硅处理。
脱硅剂以能够提供氧源的氧化剂材料为主,以调整炉渣碱度和改善流动性的熔剂为辅。
如日本福山厂脱硅剂组成为铁皮0~100%、石灰0~20%、萤石0~10%;日本川崎水岛的脱硅剂为烧结矿粉75%、石灰25%。
脱硅生成的渣必须扒除,否则影响下一步脱磷反应的进行。
目前铁水预脱硅方法按处理场所不同,可分为高炉出铁场铁水沟内连续脱硅法和铁水罐(或鱼雷罐车)内脱硅两种,其中高炉出铁场是主要炉外脱硅场所。
二、铁水预脱硫除易切削钢外,硫是影响钢的质量和性能的主要有害元素,直接决定着钢材的加工性能和适用性能。
铁水脱硫可在高炉内、转炉内和高炉出铁后脱硫站进行。
高炉内脱硫技术可行,经济性差;转炉内缺少还原性气氛,因此脱硫能力受限;而进入转炉前的铁水中脱硫的热力学条件优越(铁水中[C]、[P]和[Si]含量高使硫的活度系数增大,铁水中比钢液中高3—4倍),性价比高,成为脱硫的主要方式。
三、铁水预脱磷除易切削钢和炮弹钢外,磷是绝大多数钢种的有害元素,显著降低钢的低温冲击韧性,增加钢的强度和硬度,这种现象称为冷脆性。
铁水预脱磷采用的脱磷剂主要由氧化剂、造渣剂和助熔剂组成,其作用在于供氧将铁水中磷氧化成,使之与造渣剂结合成磷酸盐留在脱磷渣中。
目前工业上使用较广的石灰系脱磷剂以为主,配加氧化剂和助熔剂。
铁水预脱磷按处理设备可分为炉外法和炉内法。
炉外法设备为铁水包和鱼雷罐,炉内法设备为专用炉和底吹转炉。
第4章铁水预处理介绍

5
4.2 铁水预处理脱硫
4.2.1 铁水预处理脱硫的意义
铁水炉外脱硫工艺之所以在经济上和技术上是合理可 行的,主要基于以下原因: 1)铁水中含有大量的硅、碳和锰等还原性好的元素,因 此在使用不同类型的脱硫剂,特别是强脱硫剂如钙、镁、 稀土等金属及其合金时,不会发生大量的烧损,以致影响 脱硫反应的进行; 2)铁水中碳和硅等能够大大提高硫在铁水中的活度系数, 使硫很容易就能脱到很低水平; 3)铁水中氧含量较低,硫的分配系数相应有所提高,有 利于脱硫;
6
4.2 铁水预处理脱硫
4)铁水炉外脱硫可以在鱼雷车、铁水罐中进行,也可以 在出铁槽中进行,这样可以减少处理投资; 5)铁水处理温度较低,对处理装臵的寿命有益; 6)在铁水炉外脱硫的过程中铁水成分的变化比炼钢或钢 水处理过程中钢水成分的变化对最终钢种的影响小。
脱硫费用($/kg)
项目 高炉脱硫 铁水预处理脱硫 转炉脱硫 最小值 25 6 43 最大值 30 13 311 条件 低硫焦(S:0.45%)增加焦比进行低S铁水操作 从0.04%脱至0.005%S,从0.02%脱至0.005% 0.047%S铁水和0.074%S废钢,0.005%S铁水和 0.015%S废钢
14
4.2 铁水预处理脱硫
莱茵法的搅拌器是采用铁芯加强的耐火材料制成的倒 T型 搅拌器,处理时转速为60~70转/分。 其特点是:莱茵搅拌器只是部分插入铁水内部,通过搅拌 使罐上部的铁水和熔剂形成涡流搅动,混合接触,并通过 循环流动使整个包内铁水都达到上层脱硫区来实现预处理 的目的。 采用 RS法脱硫时,用熔剂CaC2: 5~ 8 kg/t,处理时间: 10min,脱硫率:70~80%。
19
4.2 铁水预处理脱硫
铁水预处理发展概况及在钢铁生产中的作用

二十世纪八十年代以来,钢铁生产中使用的原材料和燃料的质量变得越来越差。
这一全球化的趋势导致铁水中杂质含量增加,铁水质量下降。
与此同时,钢铁生产企业面临着对洁净钢尤其是对低S、低P的需求不断增长的挑战,如工业输送管道、汽车工业要求高强度、低温韧性、良好的冷成型和焊接性能要求,以及日益增长的低成本生产压力,迫使企业、科研院所开展铁水铁水品质提升或低品质铁水应用技术。
目前主要分为两类,一是通过优化生产设备、提高自动化程度以及提高生产率水平,因炼钢的所有任务放在转炉内完成,所以通过此手段起到的作用有限。
二是把原来在转炉内完成的一些任务在空间和时间上分开,分别在不同的反应器中进行,使冶金反应过程在更适合的环境气氛条件下进行,以提高冶金反应效果,此类技术也被称为铁水预处理。
铁水预处理工艺,对进入转炉冶炼之前的铁水做去除杂质元素的处理,可扩大钢铁冶金原料的来源,提高钢的质量,增加转炉炼钢的品种和提高技术经济指标。
因此,本文旨在通过对铁水预处理技术进行分析总结,并探究其在钢铁生产中的作用,以期能给予研究人员提供参考。
一、铁水预处理铁水预处理被公认为降低钢中杂质含量的最佳工艺,是改善和提高转炉操作的重要手段之一。
其基本目标是将进入转炉的铁水[Si]、[P]、[S]含量脱至成品钢种水品,达到转炉冶炼要求,现代钢铁生产工艺经过技术改造后的基本模式为:高炉炼铁-铁水预处理-转炉冶炼-炉外精炼-连铸连轧。
铁水预处理主要包含预脱硫、预脱硅、预脱磷等。
1.铁水预脱硫铁水预脱硫是指铁水进人炼钢炉前的脱硫处理,铁水脱硫的历史最早可以追溯到1877年英国人在高炉铁水沟脱硫,它是铁水预处理中最先发展成熟的工艺。
在实际生产中炉外脱硫工艺主要有两大类:机械搅拌法和喷吹法。
目前使用最多的是向熔池内喷射镁或镁基脱硫剂的喷吹法,具有脱硫效率高,处理时间短,操作费用低,处理量大,操作比较灵活等优点,可使硫含量降低至0.005%一下,近年来在欧美国家和印度得到积极推广和应用。
- 1、下载文档前请自行甄别文档内容的完整性,平台不提供额外的编辑、内容补充、找答案等附加服务。
- 2、"仅部分预览"的文档,不可在线预览部分如存在完整性等问题,可反馈申请退款(可完整预览的文档不适用该条件!)。
- 3、如文档侵犯您的权益,请联系客服反馈,我们会尽快为您处理(人工客服工作时间:9:00-18:30)。
铁水预脱硅铁水预脱硅(desiliconization of hot metal)铁水进入炼钢炉前的降硅处理。
它是发展较早的一种铁水预处理工艺,是分步精炼工艺的发展。
能改善炼钢炉的技术经济指标,降低炼钢费用,也可作为预处理脱磷、脱硫的前处理,可降低脱磷处理剂消耗,进一步生产纯净优质钢。
简史铁水预处理脱硅开始较早,1897年曾有人用平炉进行了脱硅脱磷的预备精炼工业试验,20世纪初进行了混铁炉脱硅,到40年代试验了高炉出铁时的脱硅,中国于50年代曾在鞍山钢铁公司实施过预备精炼炉脱硅和高炉铁水沟脱硅,这些都对改善平炉炼钢的冶炼技术经济指标和提高生产率起了良好的作用。
到了90年代,基于对优质钢材的需求,以及钢铁生产工艺本身节省资源和能量、减少渣量等公害的需要,日本发展了以脱硅、脱磷为目的的铁水预处理。
此后发展成两类预脱硅工艺,一类是作为铁水同时脱磷、脱硫的前工序,以提高其效率,这种铁水进入转炉只需完成脱碳和提高温度,炉渣减少到微量保护渣层的程度,主要生产高纯钢种;另一类是作为降低转炉渣量的措施。
1985年前后日本各大厂曾广泛采用,主要在高炉炉前进行。
后来,由于高炉冶炼低硅铁技术的发展,这类预脱硅方法已较少使用。
原理硅是易氧化元素。
脱硅反应可表示如下:按硅在渣相和金属相问的分配比可表示为式(2):式中L si为硅在渣铁间分配率;C si为硅容量(K si/γ(sio2 ) );a [O]为氧在铁水中活度;f [si]为硅在铁水中活度系数;γ(sio2 )为氧化硅在渣相中的活度系数;K’ Si为反应式(1)的平衡常数。
在碳饱和铁水中硅的活度系数根据各元素相互作用系数按下式计算:按一般炼钢生铁计算,f Si约在7~8之间。
硅容量C si,表示了渣相的溶硅能力。
它与渣中二氧化硅的活度系数,γ(sio2)成反比。
硅容量和渣成分有密切关系。
图1给出了FeO--SiO2--CaO--CaF2渣系的硅容量。
从以上热力学性质可以看出:(1)在一定温度和生铁成分条件下,脱硅能力决定于渣相的硅容量和供氧强度。
(2)脱硅过程中随着生铁成分的变化(硅锰等含量下降)f Si下降。
用氧化铁脱硅发生以下反应:[Si]+2(FeO)= (SiO2 )+2Fe (4)此反应可认为分成以下步骤:硅自铁水向渣铁界面转移;渣铁界面的化学反应;二氧化硅从渣铁界面向渣中转移;渣中氧化铁向渣铁界面转移。
成田等人用氧化铁脱硅实验发现:渣中FeO含量大于40%时,铁水中硅向渣铁界面扩散是反应的限制环节。
FeO含量小于10%时,渣中FeO向渣铁界面扩散是反应的限制环节。
FeO含量在10%~40%之间,为两种扩散的混合控制。
按硅在铁水中扩散为控制环节时,反应速度可写成式中K si为铁水中硅的表观传质系数,cm/s;A为渣铁间界面积,cm2;V为铁水体积,cm3;[%Si] 为时间t 时铁水中硅含量;[%Si] *为时间t 时界面硅含量。
若渣铁界面有足够的(FeO)脱硅渣,渣铁处于平衡状态,界面铁水的硅含量[%Si]≈0,则式(5)积分可得式(6):式中[%Si] 0为铁水中起始硅含量。
将实验结果按- d[%Si] / dt 和[%Si] 的关系作图2,可以证实,反应初期脱硅按式(5)3生行,与式(6)的直线式一致。
与[%Si]。
、铁量、渣成分、渣量无关,只受搅拌强度的影响。
按式(6)计算的K si与温度的关系求活化能为15kcal /mol。
此值近似于饱和碳铁水中硅的扩散活化能。
这也说明反应初期铁水中硅的扩散是限制性环节。
反应后半期逐渐偏离直线。
其偏离值相当于式(5)中K si A / V [%Si]*值。
由初期的K si和A/V求[%Si]*,得出各时期的(FeO)%与[%Si]*/[%Si]的关系图3,结果是(%FeO)≥40%[%Si]*/[%Si] =0。
若外延至(%FeO)≈10%时[%Si]*/[%Si] =1。
大贯一雄等人用气体氧喷吹脱硅,实验研究了上浮过程中的反应模型。
将反应分为喷枪前端、上浮过程和顶渣/铁水界面三个区。
枪前端为铁水中Fe、Si、Mn、C与O2的反应区。
后两区均为FeO与铁水中Si、Mn反应区。
喷吹过程顶渣中FeO在5%以下,可以认为与顶渣的反应是受渣中传质控制的。
但大部分反应是在上浮过程中发生的。
对整体来说可按混合控制考虑。
脱硅工艺硅一直作为转炉炼钢的发热元素。
但随着转炉容量增加和冶炼技术的进步,需要由硅提供的热量逐渐减少。
又由于减少渣量对炼钢技术经济指标改善十分有利,所以对铁水含硅量的要求逐渐降低,尤其是需要预处理脱磷脱硫的铁水。
根据不同的冶炼工艺和技术经济条件,大致可分为以下两种情况:(1)对需要脱磷脱硫预处理的铁水,其硅含量分成两种,如果使用苏打系熔剂,则硅含量要求小于0.10%;如果使用石灰系熔剂,则硅含量要求小于0.15%。
因为高于此值时熔剂首先用于脱硅,不能脱磷,不利于提高脱磷渣碱度(脱磷渣碱度CaO/SiO2为3.5~6.0)和脱磷剂利用率。
(2)对直接供给转炉炼钢的铁水,按不同对象钢种(指高温或低温出钢),以[Si]0.5%为基准,改变硅含量对炼钢时铁矿石加入量、炉渣碱度、渣中TFe量和铁收得率、锰铁合金消耗、渣量和喷溅损失等对冶炼成本的影响,得出低温(1610℃±10℃)出钢要求的铁水含硅量以0.20%时成本最低,大于或小于0.2%时都引起成本升高。
高温(1700℃±10℃)出钢要求的铁水含硅量小于0.40%,高于0.40%时则引起成本上升。
脱硅方式按处理场所不同分为在高炉出铁过程中连续脱硅和在铁水罐(或鱼雷车)中间歇处理两种;按加入方法有自然落下的上置法,喷枪在铁水面上的顶喷法和喷枪插入铁水的喷吹法等;按搅拌方法有吹气搅拌、铁水落下流搅拌、喷吹的气粉流搅拌和叶轮搅拌。
脱硅方式的选择主要根据铁水含硅量、要求处理后的含硅量和已有设备限制等条件来确定。
若铁水含硅量大于0.45%~0.50%,应设置高炉炉前脱硅。
若铁水需预处理脱磷、脱硫,需先在铁水罐中脱硅,将含硅量降至0.10%~0.15%以下。
出铁场脱硅有的脱硅剂以皮带或溜槽自然落下加入铁水沟,经铁水落下流将脱硅剂卷入进行反应。
有的铁水沟有落差,脱硅剂高点加入,过落差点有一段反应距离,再设置撇渣器将脱硅渣分离。
硅含量可由0.50%降至0.20%,锰也有下降。
有的脱硅剂以加速添加方式进行。
一种为插入铁水的喷枪,以高速气粉流喷入,喷枪处铁水沟改造为圆形反应坑。
喷枪为横吹4孔;另一种喷枪在铁水面上,以高速气粉流向铁水投射。
有的投射点在铁水沟,该处改造为较宽较深的反应室。
有的投射点在摆动流嘴处。
这些加速添加方式都改善了反应的动力学条件。
同时还需克服喷溅过大、耐火材料侵蚀等问题。
铁水罐脱硅这种脱硅在专门预处理站进行。
采用插入铁水的喷枪脱硅。
脱硅剂粒度为-40~-100目,处理温度低(约1320℃左右),需加氧枪面吹(距铁水面200mm左右),防止温度下降。
当气体氧/固体氧在0.3~0.5范围时,平均脱硅量0.59%,铁水处理后温度基本不变,气体氧用量相当于1.4~2.0m3/t。
若上述比值增至0.6~1.0,平均脱硅量0.48%,则处理后平均升温50℃左右。
与高炉炉前脱硅相比,高炉前脱硅不需增加脱硅时间和工序,热损失少,铁水温降不大。
处理温度较铁水罐脱硅高100℃左右,但铁水罐装入量减少10%~30%,出铁中的硅含量,铁流大小和温度较难控制,影响了脱硅效率的稳定性。
从设备上看,炉前脱硅随出铁沟的设置需多点处理,设备费用高。
但不需新建厂房。
炉前脱硅的过程控制为了给炼钢提供成分稳定的低硅铁水,必须根据出铁时的硅含量和出铁速度确定和控制脱硅剂的输送速度和添加量。
典型的控制系统包括高炉热控制模型预报铁水含硅量,出铁期间硅含量在线快速分析,再根据炼钢要求的含硅量控制脱硅剂加入量。
硅含量的快速分析已开发多种,生产已采用的有两种:一种为将圆片状试样夹在两电极间,其间温差200℃,电极间热电势随硅含量增加而上升。
测量范围是0~1.5%Si,精度σ=0.02%。
插入试样至显示结果需50s。
另一种为固体电解质定硅探头,其结构为Cr•Cr2O3//ZrO2-MoO//SiO2/Si(铁中),用钼丝作高温导线。
当固体电解质外套石英管SiO2与铁水中硅平衡时,有如下关系:[Si]+2[O]=(SiO2) (7)从测定固体电解质/铁水/石英套管间氧的活度得出相应的硅含量,即硅含量与输出电势(毫伏值)的关系。
用此方法控制调节脱硅剂加入量的效果是:目标硅为0.05%~0.12%时,命中率由46%提高至77%,脱硅剂消耗减少30%。
脱硅用耐火材料脱硅渣与高炉渣比较,前者FeO含量高。
原来用Al2O3 - SiC-C 系的铁沟耐火材料在渣线部分侵蚀严重。
因此在渣线部分改变材质,在脱硅剂加入处扩大铁水沟尺寸,铁沟侧壁埋设强制风冷管等。
对高FeO的脱硅渣,由于SiC、C被氧化而受到侵蚀,可用Al2O3- MgO系耐火材料代替,耐侵蚀性主要在于成渣反应生成液相量的大小。
试验证实,当MgO/Al2O3大于1.0时,液相的生成受到抑制,原因在于脱硅渣中FeO与MgO=Al2O3反应生成高熔点矿物。
影响脱硅的因素主要有脱硅剂单耗、处理前含硅量、反应界面积(即铁水与脱硅剂混合状况)、脱硅剂的种类和粒度等。
根据炉前脱硅和铁水罐脱硅的生产数据,温度在1250~1450℃范围内,温度变化对脱硅没有明显影响。
脱硅剂单耗和原始硅含量铁水含硅量大于0.5%时,一般每吨生铁加入脱硅剂10~30kg、脱硅量约0.1%~0.4%,脱硅剂单耗增加,脱硅量增加,但其增加幅度减小。
这与铁水含硅量逐渐降低后脱硅氧效率降低有关。
与硅以外的其他元素(C、Mn等)的氧化有关。
脱硅反应与脱硅剂单耗的关系可用下式表示-ln[Si]f /[Si]0 = KW (8)式中[Si] f 为处理后铁水含硅量;[Si]0 为处理前铁水含硅量;K为比例常数;W为脱硅剂单耗,kg/t。
脱硅氧效率η si可按下式表示η si =与硅反应的氧/ 脱硅剂中的全氧×100%(9)实践证实,铁水原始硅含量对脱硅氧效率影响较大,当[Si]0 >0.5%时;η si在70%以上,当[Si]0降低时,效率急剧变差,当[Si]0=0.2%时,η si约40%。
反应界面积即铁水与脱硅剂的混合。
出铁速度影响着铁水与脱硅剂的混合。
在[Si]0=0.4%~0.6%时,向摆动流嘴处加入25~30kg/t的脱硅剂,当铁流速度由6t/min 提高到9t/min,脱硅率由40%提高到60%。
铁沟上顶部投射法(TIM),喷枪不插入铁水,能改善脱硅的氧效率,尤其是要求终硅量达0.1%~0.2%时,投射法比自然落下法(SFM) η si 提高约10%。