某型伸缩臂叉装车伸缩臂应力分析
伸缩臂履带起重机带载行驶下臂架应力状态分析
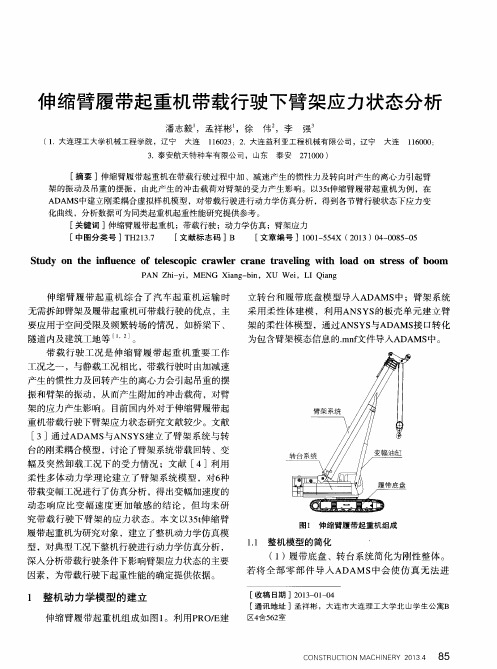
专题研 究
I s
c H
1 . 3 带 载行 驶模 拟
行 ,上述 简化对 结果 影 响较小 ,可 以忽 略 。
Байду номын сангаас
( 2)变 幅油 缸 简 化 为刚性 杆 。在 带载 行 驶 过 程 中 ,变 幅油 缸处 于锁死 状 态 ,且 刚度 较大 ,可 简
化为 刚性 连杆 。
伸 缩臂 履 带起 重 机 的两 侧 履 带分 别 通过 2 个 独 立 的液压 马达 驱动 主动轮 。在直线 行驶 过程 中 ,主 动轮 转速 的增加 和减 小在 整机 上体 现为线 速 度 的增 减 ,在 底 盘 建 立 相 对 地 面 的 移 动 副模 拟 整 机 的移 动 ;在转 向行 驶 时 ,履带 底 盘通过 两侧 履带 的速度
差 实 现转 向 ,转 向半 径及 转 向 角速 度 由式 ( 1)、 ( 2) 决定。
( 3)钢 丝绳 等 效 为 刚性 连杆 ,吊重 以质 量 球 代替 。钢 丝绳 在起 吊重 物过 程 中处 于绷 紧状 态 ,简 化 为刚性 连杆 可 以简化 计算 ,同时对 分析结 果影 响 较小。
2 7 1 0 0 0)
[ 摘要 ] 伸 缩 臂履 带 起重 机 在带 载 行驶 过 程 中加 、减速 产 生 的惯 性 力及 转 向时 产 生 的离 心力 引起 臂 架 的振动 及 吊重 的摆 振 ,由此 产 生 的冲击 载 荷对 臂 架 的受 力产 生 影 响 。以 3 5 t {  ̄ 缩臂 履 带起 重 机 为例 ,在
伸 缩臂履 带起 重机带载行驶 下臂 架应 力状态分析
潘 志毅 ,孟 祥 彬 ,徐
( 1 .大 连 理 工 大 学 机 械 工 程 学 院 ,辽 宁 大连
《2024年度伸缩臂叉装车行走系统优化分析与实验研究》范文

《伸缩臂叉装车行走系统优化分析与实验研究》篇一一、引言随着工程机械的快速发展,伸缩臂叉装车作为重要的物流搬运设备,其行走系统的性能直接关系到工作效率和作业安全。
因此,对伸缩臂叉装车行走系统进行优化分析与实验研究,对于提高设备的整体性能具有重要意义。
本文旨在分析伸缩臂叉装车行走系统的结构特点及性能问题,通过优化设计及实验研究,提高行走系统的动力性、稳定性和经济性。
二、伸缩臂叉装车行走系统结构与性能分析1. 结构特点伸缩臂叉装车行走系统主要由驱动系统、传动系统、行走机构和制动系统等组成。
其中,驱动系统提供动力,传动系统将动力传递给行走机构,实现车辆的行进与转向。
行走机构采用履带式结构,具有较好的地面适应性。
2. 性能问题在实际使用过程中,伸缩臂叉装车行走系统存在动力不足、稳定性差、油耗高等问题。
这些问题主要源于设计不合理、制造工艺落后、使用维护不当等方面。
三、行走系统优化设计1. 动力系统优化为提高动力性能,可采取增加发动机功率、优化传动比、改善燃油供应系统等措施。
同时,采用先进的电控技术,实现动力系统的智能调控。
2. 稳定性优化为提高稳定性,可对履带式行走机构的框架结构进行优化设计,增加支撑面积,降低接地比压。
同时,采用先进的控制算法,实现行驶过程中的动态稳定控制。
3. 经济性优化为降低油耗,可采取轻量化设计、优化液压系统、改进润滑系统等措施。
同时,通过智能管理系统实现油耗的实时监测与控制。
四、实验研究1. 实验方案为验证优化设计的有效性,本文设计了多组对比实验。
首先,对优化前后的行走系统进行性能测试,包括动力性能、稳定性、油耗等指标。
然后,通过实际工况下的使用情况,对比分析优化前后的效果。
2. 实验结果与分析实验结果表明,经过优化设计后,伸缩臂叉装车行走系统的动力性能得到显著提升,稳定性得到有效保障,油耗得到有效降低。
具体数据详见附录中的实验数据表。
五、结论与展望本文通过对伸缩臂叉装车行走系统的优化分析与实验研究,有效提高了设备的动力性、稳定性和经济性。
伸缩臂叉装机研究报告
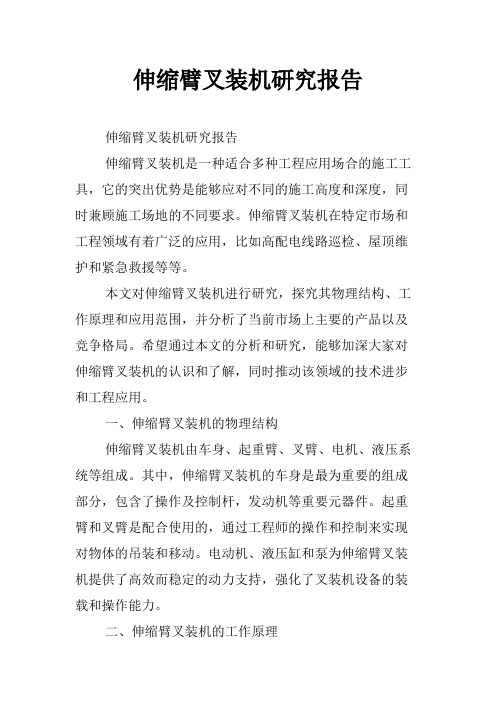
伸缩臂叉装机研究报告伸缩臂叉装机研究报告伸缩臂叉装机是一种适合多种工程应用场合的施工工具,它的突出优势是能够应对不同的施工高度和深度,同时兼顾施工场地的不同要求。
伸缩臂叉装机在特定市场和工程领域有着广泛的应用,比如高配电线路巡检、屋顶维护和紧急救援等等。
本文对伸缩臂叉装机进行研究,探究其物理结构、工作原理和应用范围,并分析了当前市场上主要的产品以及竞争格局。
希望通过本文的分析和研究,能够加深大家对伸缩臂叉装机的认识和了解,同时推动该领域的技术进步和工程应用。
一、伸缩臂叉装机的物理结构伸缩臂叉装机由车身、起重臂、叉臂、电机、液压系统等组成。
其中,伸缩臂叉装机的车身是最为重要的组成部分,包含了操作及控制杆,发动机等重要元器件。
起重臂和叉臂是配合使用的,通过工程师的操作和控制来实现对物体的吊装和移动。
电动机、液压缸和泵为伸缩臂叉装机提供了高效而稳定的动力支持,强化了叉装机设备的装载和操作能力。
二、伸缩臂叉装机的工作原理伸缩臂叉装机的工作原理基于电机动力、液压机械传动和操作结构。
当操作员在车身上调节伸缩臂装配的臂展,此时通过液压支撑系统来掌握起重臂、叉臂呈现出的动作特征,从而实现对外物体的吊装、搬输。
伸缩臂的长度灵活性和臂展的控制是伸缩臂叉装机的关键技术,通过技术的改进和创新,不光方便了工程后期的施工和维修,同时也降低了运输、安装等成本。
三、伸缩臂叉装机的应用范围伸缩臂叉装机是一种多领域、多工种的货物搬运设备,主要应用于以下领域:1、电力行业:高压电线巡检、铁路施工等。
2、清洁行业:城市景区树木种植、草坪修剪和保洁等。
3、建筑行业:电梯维护、楼层施工和屋顶维护等。
4、其他领域:医疗救援、锅炉加水、公路维护等领域。
伸缩臂叉装机在现代工程生产领域广泛应用,为各行业的发展提供了动力支持。
四、当前市场竞争格局在伸缩臂叉装机市场方面,不同公司有自己的特点和竞争策略。
当前市场上已经涌现出了很多品牌和型号的伸缩臂叉装机,包括进口和国产机型。
伸缩臂式叉装车结构设计与工作性能研究开题报告

伸缩臂式叉装车结构设计与工作性能研究开题报告一、研究背景叉装车是一种广泛应用于物流、制造业、农业等领域中的物流运输设备。
叉装车通过液压系统实现货物的提升、运输、放置等功能,因此叉装车的结构和工作性能直接影响着运输效率和货物安全。
传统的叉装车一般采用单臂或双臂固定结构,不能适应不同操作环境和货物尺寸的需求。
而伸缩臂式叉装车则可以通过伸缩臂的伸缩,灵活地适应不同的操作环境和货物尺寸,提高了叉装车的灵活性和工作效率。
因此,本研究拟对伸缩臂式叉装车的结构设计和工作性能进行深入探究。
二、研究内容1. 伸缩臂式叉装车的结构设计伸缩臂式叉装车的伸缩臂结构设计是至关重要的,伸缩臂的伸缩长度和伸缩速度需要兼顾灵活性和安全性。
本研究将进行伸缩臂式叉装车结构设计的优化,包括材料选择、结构形式设计、伸缩臂伸长速度和调节方式等方面的研究。
2. 伸缩臂式叉装车的工作性能测试本研究将对伸缩臂式叉装车的工作性能进行测试,主要包括伸缩臂的承载能力、工作稳定性、操作效率等方面的评估。
通过测试数据的分析和比对,确定伸缩臂式叉装车工作性能的优缺点,为优化叉装车的工作性能提供参考依据。
三、研究方法本研究将采用多种研究方法,包括文献调研、数值模拟、实验测试等。
具体包括以下步骤:1. 对伸缩臂式叉装车的现有研究文献进行调研和综述,了解叉装车的发展历程和现有研究成果。
2. 基于有限元分析方法,对伸缩臂式叉装车的伸缩臂数值模拟,研究伸缩臂的结构形式和工作性能。
3. 进行伸缩臂式叉装车的承载能力、工作稳定性、操作效率等方面的实验测试,获取叉装车的工作性能指标。
四、预期研究成果通过本研究的开展,预期可以获得以下成果:1. 优化的伸缩臂式叉装车结构设计方案,提高叉装车适应不同操作环境和货物尺寸的能力。
2. 伸缩臂式叉装车工作性能的测试数据,较为全面地了解伸缩臂式叉装车的工作性能及其优缺点。
3. 本研究成果可为叉装车工程设计和生产提供参考依据,为提高叉装车的灵活性和工作效率提供技术支持。
《伸缩臂叉装车行走系统优化分析与实验研究》范文
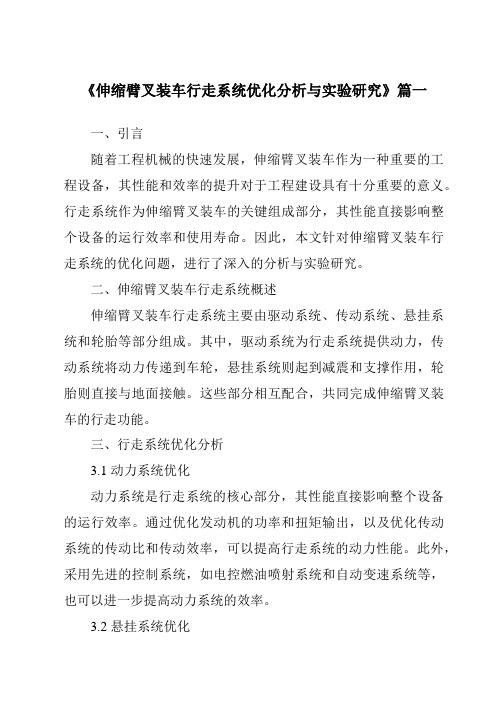
《伸缩臂叉装车行走系统优化分析与实验研究》篇一一、引言随着工程机械的快速发展,伸缩臂叉装车作为一种重要的工程设备,其性能和效率的提升对于工程建设具有十分重要的意义。
行走系统作为伸缩臂叉装车的关键组成部分,其性能直接影响整个设备的运行效率和使用寿命。
因此,本文针对伸缩臂叉装车行走系统的优化问题,进行了深入的分析与实验研究。
二、伸缩臂叉装车行走系统概述伸缩臂叉装车行走系统主要由驱动系统、传动系统、悬挂系统和轮胎等部分组成。
其中,驱动系统为行走系统提供动力,传动系统将动力传递到车轮,悬挂系统则起到减震和支撑作用,轮胎则直接与地面接触。
这些部分相互配合,共同完成伸缩臂叉装车的行走功能。
三、行走系统优化分析3.1 动力系统优化动力系统是行走系统的核心部分,其性能直接影响整个设备的运行效率。
通过优化发动机的功率和扭矩输出,以及优化传动系统的传动比和传动效率,可以提高行走系统的动力性能。
此外,采用先进的控制系统,如电控燃油喷射系统和自动变速系统等,也可以进一步提高动力系统的效率。
3.2 悬挂系统优化悬挂系统的主要作用是减震和支撑,其性能直接影响设备的稳定性和舒适性。
通过优化悬挂系统的结构和参数,如悬挂刚度和悬挂行程等,可以提高设备的稳定性和舒适性。
此外,采用先进的电子控制系统,如电子液压悬挂控制系统等,也可以进一步提高悬挂系统的性能。
3.3 轮胎与地面接触优化轮胎与地面的接触情况直接影响设备的行驶性能和安全性。
通过优化轮胎的结构和材料,如采用更耐磨、更耐压的轮胎材料和更合理的轮胎结构等,可以提高轮胎的使用寿命和抓地力。
此外,采用先进的轮胎管理系统和监测技术,可以实时监测轮胎的状态和磨损情况,及时进行维护和更换。
四、实验研究为了验证上述优化措施的有效性,我们进行了实验研究。
首先,我们分别对优化前后的动力系统、悬挂系统和轮胎与地面接触情况进行了对比实验。
通过实验数据可以看出,经过优化后,设备的动力性能、稳定性和舒适性都得到了显著提高。
伸缩臂的弯曲应力计算公式
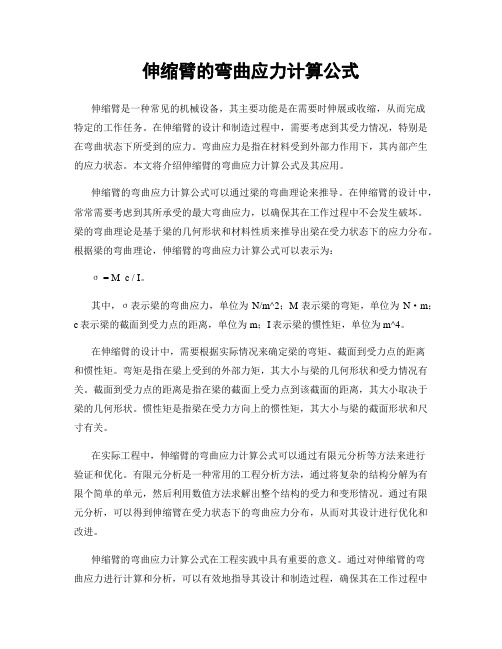
伸缩臂的弯曲应力计算公式伸缩臂是一种常见的机械设备,其主要功能是在需要时伸展或收缩,从而完成特定的工作任务。
在伸缩臂的设计和制造过程中,需要考虑到其受力情况,特别是在弯曲状态下所受到的应力。
弯曲应力是指在材料受到外部力作用下,其内部产生的应力状态。
本文将介绍伸缩臂的弯曲应力计算公式及其应用。
伸缩臂的弯曲应力计算公式可以通过梁的弯曲理论来推导。
在伸缩臂的设计中,常常需要考虑到其所承受的最大弯曲应力,以确保其在工作过程中不会发生破坏。
梁的弯曲理论是基于梁的几何形状和材料性质来推导出梁在受力状态下的应力分布。
根据梁的弯曲理论,伸缩臂的弯曲应力计算公式可以表示为:σ = M c / I。
其中,σ表示梁的弯曲应力,单位为N/m^2;M表示梁的弯矩,单位为N·m;c表示梁的截面到受力点的距离,单位为m;I表示梁的惯性矩,单位为m^4。
在伸缩臂的设计中,需要根据实际情况来确定梁的弯矩、截面到受力点的距离和惯性矩。
弯矩是指在梁上受到的外部力矩,其大小与梁的几何形状和受力情况有关。
截面到受力点的距离是指在梁的截面上受力点到该截面的距离,其大小取决于梁的几何形状。
惯性矩是指梁在受力方向上的惯性矩,其大小与梁的截面形状和尺寸有关。
在实际工程中,伸缩臂的弯曲应力计算公式可以通过有限元分析等方法来进行验证和优化。
有限元分析是一种常用的工程分析方法,通过将复杂的结构分解为有限个简单的单元,然后利用数值方法求解出整个结构的受力和变形情况。
通过有限元分析,可以得到伸缩臂在受力状态下的弯曲应力分布,从而对其设计进行优化和改进。
伸缩臂的弯曲应力计算公式在工程实践中具有重要的意义。
通过对伸缩臂的弯曲应力进行计算和分析,可以有效地指导其设计和制造过程,确保其在工作过程中不会发生破坏。
同时,通过对伸缩臂的弯曲应力进行优化,可以提高其承载能力和使用寿命,从而提高整个机械设备的性能和可靠性。
总之,伸缩臂的弯曲应力计算公式是伸缩臂设计和制造过程中的重要内容。
《2024年度伸缩臂叉装车行走系统优化分析与实验研究》范文
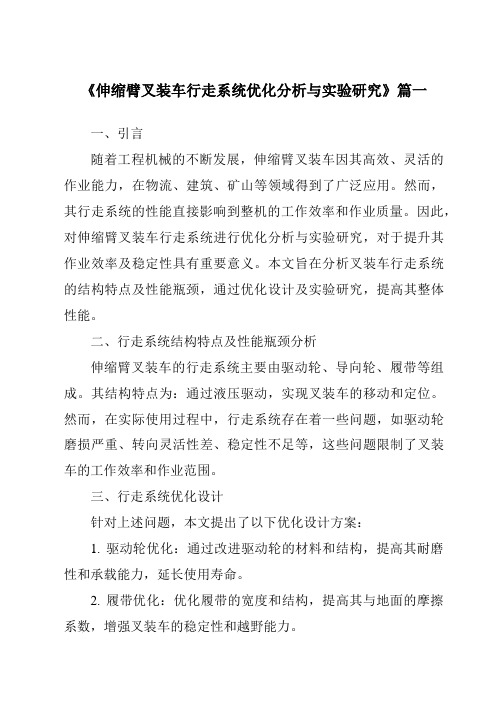
《伸缩臂叉装车行走系统优化分析与实验研究》篇一一、引言随着工程机械的不断发展,伸缩臂叉装车因其高效、灵活的作业能力,在物流、建筑、矿山等领域得到了广泛应用。
然而,其行走系统的性能直接影响到整机的工作效率和作业质量。
因此,对伸缩臂叉装车行走系统进行优化分析与实验研究,对于提升其作业效率及稳定性具有重要意义。
本文旨在分析叉装车行走系统的结构特点及性能瓶颈,通过优化设计及实验研究,提高其整体性能。
二、行走系统结构特点及性能瓶颈分析伸缩臂叉装车的行走系统主要由驱动轮、导向轮、履带等组成。
其结构特点为:通过液压驱动,实现叉装车的移动和定位。
然而,在实际使用过程中,行走系统存在着一些问题,如驱动轮磨损严重、转向灵活性差、稳定性不足等,这些问题限制了叉装车的工作效率和作业范围。
三、行走系统优化设计针对上述问题,本文提出了以下优化设计方案:1. 驱动轮优化:通过改进驱动轮的材料和结构,提高其耐磨性和承载能力,延长使用寿命。
2. 履带优化:优化履带的宽度和结构,提高其与地面的摩擦系数,增强叉装车的稳定性和越野能力。
3. 转向系统优化:通过改进转向系统的液压控制回路,实现更灵活的转向操作,提高工作效率。
四、实验研究为了验证优化设计的有效性,本文进行了以下实验研究:1. 驱动轮耐磨性实验:通过模拟实际工况,对优化前后的驱动轮进行耐磨性测试,对比分析其性能差异。
2. 稳定性实验:在不同工况下,对优化前后的叉装车进行稳定性测试,分析其稳定性的改善情况。
3. 转向灵活性实验:通过对比优化前后叉装车的转向操作时间,评价其转向灵活性的提升程度。
五、实验结果与分析1. 驱动轮耐磨性实验结果:经过耐磨性测试,优化后的驱动轮相比优化前,磨损程度明显降低,使用寿命得到延长。
2. 稳定性实验结果:在不同工况下,优化后的叉装车相比优化前,稳定性有明显提升,特别是在复杂地形条件下,其越野能力得到显著增强。
3. 转向灵活性实验结果:通过对比转向操作时间,优化后的叉装车转向更加灵活,操作更加便捷。
某型伸缩臂叉车稳定性验算
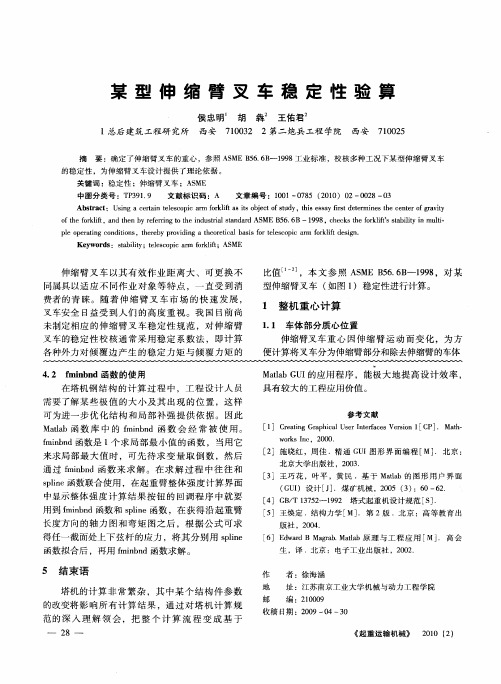
sl e函数联 合使用 ,在起 重 臂整 体 强 度计 算 界 面 pi n
中显示整 体 强 度 计 算 结 果 按 钮 的 回调 程 序 中就 要
[ ]王巧花 ,叶平 ,黄 民 .基于 Mal 3 t b的 图形 用户 界面 a ( U )设 计 [ ] GI J .煤矿机械 ,2 0 ( ) 0— 2 0 5 3 :6 6 . [ ]G / 35 - 19 塔式起重机设 计规范 [ ] 4 B T 172 9 2 s. [ ]王焕定 .结构力学 [ .第 2版 .北京 :高等教育 出 5 M]
[ ]Cet gG ahcl sr ne ae V  ̄i [ P .M t— 1 ra n rpia U e t fcs e o 1 C ] ah i I r n
wo k n r s I c, 20 0. 0
[ ]施晓红 ,周佳 .精通 G I图形界 面编 程 [ .北 京 : 2 U M]
的稳定性 ,为伸缩臂叉车设 计提供了理论 依据。
关 键 词 :稳 定 性 ;伸缩 臂 叉 车 ;A M SE
中图分类号 :T 3 19 P 9 .
文献标识码 :A
文章 编号:10 0 8 ( 00 2— 0 8 0 0 1— 7 5 2 1 )0 0 2 — 3
A s at s gacr i lsoi a,f ki st oj t f td , h sa rt ee nst et f rvy bt c :U i et nt ecpc 1 rl a i b c o u y tiesyfsdtr e h cne o ai r n a e 3 o f s e s n t s i mi e r g t
[ ]E w  ̄ B Marb Ma a 6 d a ga . tb原 理 与工 程应 用 [ .高会 l M]
高空作业平台伸缩臂应力集中分析及局部结构改进
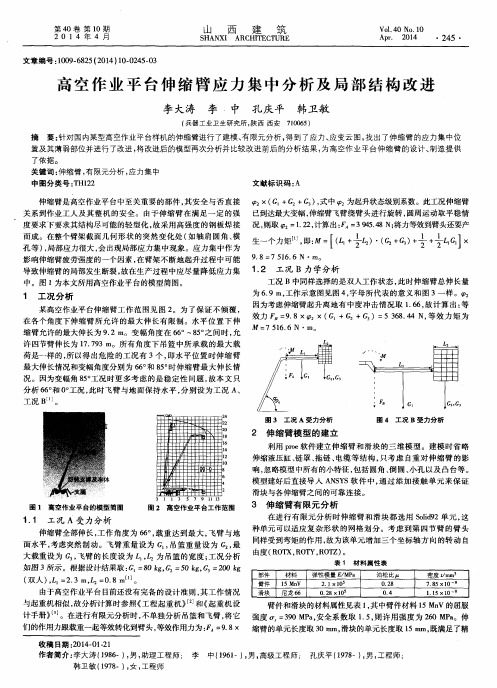
某 高空作业平 台伸缩臂 工作 范 围见 图 2 。为 了保 证不倾 覆 , 在各个 角度下伸缩 臂所 允许 的最 大伸 长有 限制 。水平 位 置下伸 缩臂 允许 的最大伸长为 9 . 2 m。变 幅角度在 6 6 。一 8 5 。 之 间时 , 允 许 四节臂 伸长为 1 7 . 7 9 3 m。所有 角度下 吊篮 中所 承载 的最大 载 荷是一样 的 , 所 以得 出危 险的工况 有 3个 , 即水平 位 置时 伸缩臂 最大 伸长情况和变幅角度分别 为 6 6 。 和8 5 。 时伸缩 臂最 大伸长情 况 。因为变幅角 8 5 。 工况 时更多 考虑 的是稳 定性 问题 , 故 本文 只 分析 6 6 。 和0 。 工况 , 此 时飞臂 与地 面保 持水平 , 分 别设 为工况 A、
置及其 薄弱部位并进行 了改进 , 将改进后 的模型再次分析并 比较 改进前 后的分析 结果 , 为高空作 业平 台伸缩臂 的设计 、 制 造提供 了依据 。
关键词 : 伸缩臂 , 有限元分析 , 应力集 中
中 图分 类 号 : T H1 2 2 文献标识码 : A
伸缩臂是 高空作业平台 中至关 重要 的部 件 , 其安 全与 否直接
( 双 人) , = 2 . 3 m, L 2= O . 8 m… 。
部件 l 材料 表 1 材 料属 性 表 弹性模 量 E / M P a 泊松 比 密度 t / m m
I臂件 J 1 5 M n V
滑块 l尼龙6 6
图 1 高空作业平台的模型简图 图 2 高空作业平台工作范 围
3 伸 缩臂 有 限元分 析
在进 行有 限元分 析 时伸缩 臂 和滑块都 选用 S o l i d 9 2单 元 , 这
《2024年伸缩臂叉装车行走系统优化分析与实验研究》范文

《伸缩臂叉装车行走系统优化分析与实验研究》篇一一、引言随着现代物流和工程机械技术的不断发展,伸缩臂叉装车作为重要的装载和运输设备,其行走系统的性能优化显得尤为重要。
行走系统是伸缩臂叉装车的关键组成部分,直接影响设备的运行效率、稳定性和安全性。
本文针对伸缩臂叉装车行走系统进行优化分析,并开展相关实验研究,以期提升其性能和作业效率。
二、行走系统结构及工作原理伸缩臂叉装车的行走系统主要由驱动系统、传动系统、行走机构和控制系统等部分组成。
其中,驱动系统提供动力,传动系统将动力传递给行走机构,控制系统则负责协调各部分的运行。
行走机构采用履带式设计,具有较好的地面适应性和抓地力,能够在复杂地形中稳定运行。
三、行走系统优化分析1. 动力性能优化:通过改进驱动系统和传动系统的设计,提高行走系统的动力性能。
采用大功率发动机和高效传动装置,提升设备的爬坡能力和载重能力。
2. 稳定性优化:针对履带式行走机构的特性,优化履带的设计和布局,提高设备的稳定性。
通过增加履带的接地压力和调整履带张紧力,降低设备在运行过程中的晃动和振动。
3. 节能性优化:通过改进控制系统的设计,实现行走系统的智能控制和节能运行。
采用先进的控制算法和传感器技术,实现对设备运行状态的实时监测和调控,降低能耗。
四、实验研究为了验证行走系统优化的效果,本文开展了一系列实验研究。
首先,对优化前后的行走系统进行动力性能测试,比较其爬坡能力和载重能力的提升情况。
其次,对设备的稳定性进行实验验证,通过在不同地形条件下运行设备,观察其晃动和振动的程度。
最后,对节能性进行实验评估,记录设备在不同工况下的能耗情况,分析优化后节能效果的显著性。
五、实验结果与分析1. 动力性能实验结果:经过优化后,伸缩臂叉装车的爬坡能力和载重能力均有所提升。
在相同工况下,设备的动力性能得到显著改善,满足更高的作业需求。
2. 稳定性实验结果:优化后的行走系统在不同地形条件下的稳定性得到提高。
某型叉车伸缩臂液压系统稳定性改进

62
2 0 19·6
第50 卷 第 6 期
总第 54 8 期
电磁阀 2 进入蓄能器。同时,举升液压缸无杆腔油压下 降,油箱中的液压油通过单向阀 c 和电磁阀 1 被吸入液 压缸,通过这一过程,举升液压缸内部压力得到平衡,并 且避免了空穴现象的发生。同理,当举升液压缸无杆腔受 到冲击导致活塞杆突然向右侧移动时,蓄能器中储存的 液压油将会弥补有杆腔的压强损失,而对于无杆腔,液压 油将会平稳通过管道流回油箱。 3.2 蓄能器设计
28 MPa,流量为 130 L/min
最大静态可负载压力
22 MPa
叉车行进中产生最大压力
33 MPa
图 2 举升机构液压系统示意图
向阀后进入举升液压缸,导致举升液压缸无杆腔压强大 于有杆腔压强,活塞杆向上运动,从而带动伸缩臂向上抬 升。相反地,当伸缩臂下降时,液压油的回路方向与举升 阶段相反,但是在液压油通过举升液压缸之后,需要有足 够大的压力来打开溢流阀阀门,这样液压油才可以顺利 回到油箱。此外,当需要保持伸缩臂的角度时,举升液压 缸内部压强需要保持恒定,这就需要同时关闭管路 V1 和 V2,从而建立一个封闭系统以实现系统稳定。 1 .2 存在的问题
该型全地形叉车的伸缩臂较长,其举升作业依靠举 升机构举升液压缸来完成。当叉车在行进中发生颠簸时, 伸缩臂会发生振动。叉车在负重情况下前进遇到障碍所 产生的振动会对举升机构举升液压缸产生很大的压力, 甚至会破坏伸缩臂液压系统。
图 1 某型全地形伸缩臂叉车
1 举升机构液压系统
1 .1 功能 图 2 所示为举升机构液压系统示意图。该系统的动
伸缩臂叉车伸缩臂强度测试及臂架间摩擦因数计算研究
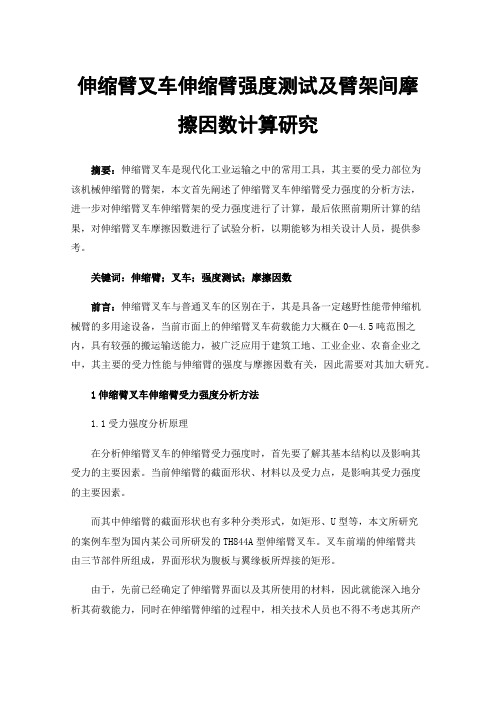
伸缩臂叉车伸缩臂强度测试及臂架间摩擦因数计算研究摘要:伸缩臂叉车是现代化工业运输之中的常用工具,其主要的受力部位为该机械伸缩臂的臂架,本文首先阐述了伸缩臂叉车伸缩臂受力强度的分析方法,进一步对伸缩臂叉车伸缩臂架的受力强度进行了计算,最后依照前期所计算的结果,对伸缩臂叉车摩擦因数进行了试验分析,以期能够为相关设计人员,提供参考。
关键词:伸缩臂;叉车;强度测试;摩擦因数前言:伸缩臂叉车与普通叉车的区别在于,其是具备一定越野性能带伸缩机械臂的多用途设备,当前市面上的伸缩臂叉车荷载能力大概在0—4.5吨范围之内,具有较强的搬运输送能力,被广泛应用于建筑工地、工业企业、农畜企业之中,其主要的受力性能与伸缩臂的强度与摩擦因数有关,因此需要对其加大研究。
1伸缩臂叉车伸缩臂受力强度分析方法1.1受力强度分析原理在分析伸缩臂叉车的伸缩臂受力强度时,首先要了解其基本结构以及影响其受力的主要因素。
当前伸缩臂的截面形状、材料以及受力点,是影响其受力强度的主要因素。
而其中伸缩臂的截面形状也有多种分类形式,如矩形、U型等,本文所研究的案例车型为国内某公司所研发的TH844A型伸缩臂叉车。
叉车前端的伸缩臂共由三节部件所组成,界面形状为腹板与翼缘板所焊接的矩形。
由于,先前已经确定了伸缩臂界面以及其所使用的材料,因此就能深入地分析其荷载能力,同时在伸缩臂伸缩的过程中,相关技术人员也不得不考虑其所产生的摩擦因数,由于该因数会决定伸缩臂伸缩液压缸的选型设计,因此需要对其加大计算。
目前在伸缩臂叉车受力分析方法上有两种,一是结合伸缩臂加载受力部位依照给定材料特性,结合截面形状,求出伸缩臂的整体承载能力。
二是通过加载伸缩臂的方式,来测验伸缩油缸的压力,并对其各个部位的受力情况进行分析,最终得出整体伸缩臂的承载能力。
由于第一种方法存在无法分析伸缩臂危险截面缺陷的问题,且操作难度较高,因此本文则选择第二种方式进行分析[1]。
1.2伸缩臂受力的分析常规伸缩臂叉车伸缩臂的主要受力结构可以分为三个层次,其中第三节以及第二节臂是叉车伸缩臂的主要受力区,一、二、三节臂的受力主要取决于机械链条的拉力,受自身重力与荷载能力、摩擦力、臂间支反力的影响。
《2024年伸缩臂叉装车行走系统优化分析与实验研究》范文
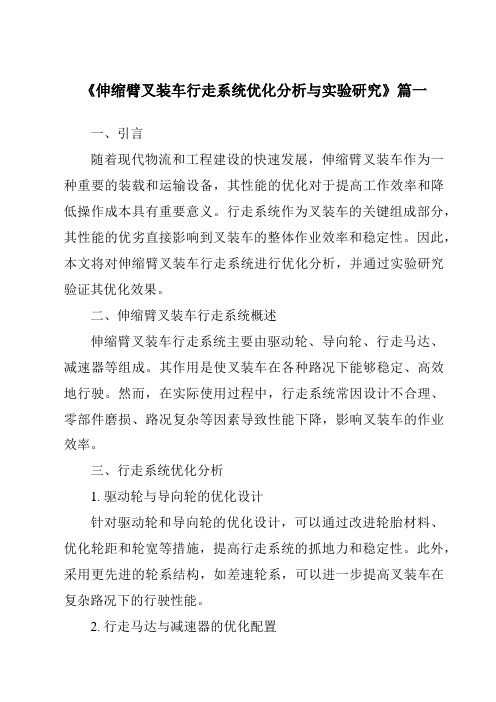
《伸缩臂叉装车行走系统优化分析与实验研究》篇一一、引言随着现代物流和工程建设的快速发展,伸缩臂叉装车作为一种重要的装载和运输设备,其性能的优化对于提高工作效率和降低操作成本具有重要意义。
行走系统作为叉装车的关键组成部分,其性能的优劣直接影响到叉装车的整体作业效率和稳定性。
因此,本文将对伸缩臂叉装车行走系统进行优化分析,并通过实验研究验证其优化效果。
二、伸缩臂叉装车行走系统概述伸缩臂叉装车行走系统主要由驱动轮、导向轮、行走马达、减速器等组成。
其作用是使叉装车在各种路况下能够稳定、高效地行驶。
然而,在实际使用过程中,行走系统常因设计不合理、零部件磨损、路况复杂等因素导致性能下降,影响叉装车的作业效率。
三、行走系统优化分析1. 驱动轮与导向轮的优化设计针对驱动轮和导向轮的优化设计,可以通过改进轮胎材料、优化轮距和轮宽等措施,提高行走系统的抓地力和稳定性。
此外,采用更先进的轮系结构,如差速轮系,可以进一步提高叉装车在复杂路况下的行驶性能。
2. 行走马达与减速器的优化配置行走马达和减速器是行走系统的核心部件,其性能直接影响到叉装车的动力性和能耗。
通过优化马达和减速器的匹配,采用更高效的传动系统,可以降低能耗,提高叉装车的动力性能。
此外,采用先进的控制策略,如智能调速控制,可以进一步提高行走系统的运行效率。
四、实验研究为了验证行走系统优化的效果,我们进行了以下实验研究:1. 模拟实验在模拟不同路况的试验台上,对优化前后的行走系统进行性能测试。
通过对比分析,发现优化后的行走系统在抓地力、稳定性、动力性能等方面均有显著提高。
2. 实地测试在真实工况下,对优化后的伸缩臂叉装车进行实地测试。
测试结果表明,优化后的叉装车在各种路况下均能稳定、高效地行驶,且能耗降低,作业效率得到显著提高。
五、结论通过对伸缩臂叉装车行走系统的优化分析,我们发现通过改进驱动轮和导向轮的设计、优化行走马达和减速器的配置等措施,可以显著提高行走系统的性能。
伸缩臂履带起重机直线行驶工况下臂架应力状态分析_苗明_徐兆亭_苗文博
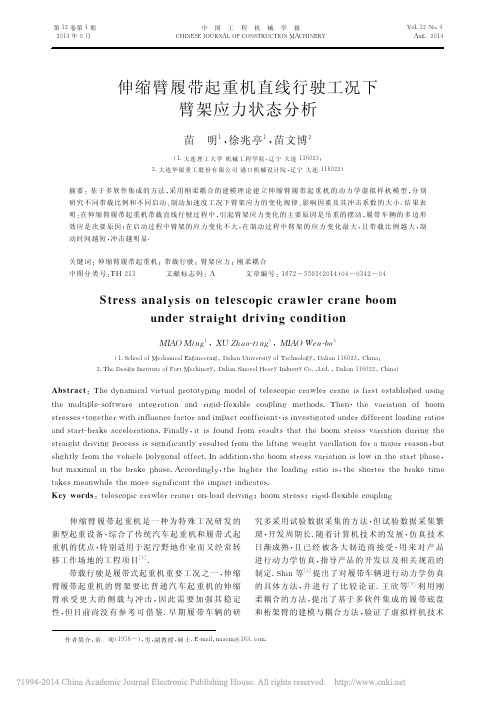
第12卷第4期2014年8月中 国 工 程 机 械 学 报CHINESE JOURNAL OF CONSTRUCTION MACHINERYVol.12 No.4 Aug.2014作者简介:苗 明(1956-),男,副教授,硕士.E-mail:miaom@163.com.伸缩臂履带起重机直线行驶工况下臂架应力状态分析苗 明1,徐兆亭1,苗文博2(1.大连理工大学机械工程学院,辽宁大连116023;2.大连华锐重工股份有限公司港口机械设计院,辽宁大连116022)摘要:基于多软件集成的方法,采用刚柔耦合的建模理论建立伸缩臂履带起重机的动力学虚拟样机模型,分别研究不同带载比例和不同启动、制动加速度工况下臂架应力的变化规律、影响因素及其冲击系数的大小.结果表明:在伸缩臂履带起重机带载直线行驶过程中,引起臂架应力变化的主要原因是吊重的摆动,履带车辆的多边形效应是次要原因;在启动过程中臂架的应力变化不大,在制动过程中臂架的应力变化最大,且带载比例越大,制动时间越短,冲击越明显.关键词:伸缩臂履带起重机;带载行驶;臂架应力;刚柔耦合中图分类号:TH 213 文献标志码:A 文章编号:1672-5581(2014)04-0342-04Stress analysis on telescopic crawler crane boomunder straight driving conditionMIAO Ming1,XU Zhao-ting1,MIAO Wen-bo2(1.School of Mechanical Engineering,Dalian University of Technology,Dalian 116023,China;2.The Design Institute of Port Mechinery,Dalian Sinovel Heavy Industry Co.,Ltd.,Dalian 116022,China)Abstract:The dynamical virtual prototyping model of telescopic crawler crane is first established usingthe multiple-software integration and rigid-flexible coupling methods.Then,the variation of boomstresses,together with influence factor and impact coefficient,is investigated under different loading ratiosand start-brake accelerations.Finally,it is found from results that the boom stress variation during thestraight driving process is significantly resulted from the lifting weight vacillation for a major reason,butslightly from the vehicle polygonal effect.In addition,the boom stress variation is low in the start phase,but maximal in the brake phase.Accordingly,the higher the loading ratio is,the shorter the brake timetakes meanwhile the more significant the impact indicates.Key words:telescopic crawler crane;on-load driving;boom stress;rigid-flexible coupling 伸缩臂履带起重机是一种为特殊工况研发的新型起重设备,综合了传统汽车起重机和履带式起重机的优点,特别适用于泥泞野地作业而又经常转移工作场地的工程项目[1].带载行驶是履带式起重机重要工况之一,伸缩臂履带起重机的臂架要比普通汽车起重机的伸缩臂承受更大的侧载与冲击,因此需要加强其稳定性,但目前尚没有参考可借鉴.早期履带车辆的研究多采用试验数据采集的方法,但试验数据采集繁琐,开发周期长.随着计算机技术的发展,仿真技术日渐成熟,且已经被各大制造商接受,用来对产品进行动力学仿真,指导产品的开发以及相关规范的制定.Shin等[2]提出了对履带车辆进行动力学仿真的具体方法,并进行了比较论证.王欣等[3]利用刚柔耦合的方法,提出了基于多软件集成的履带底盘和桁架臂的建模与耦合方法,验证了虚拟样机技术 第4期苗 明,等:伸缩臂履带起重机直线行驶工况下臂架应力状态分析 在产品开发过程中的有效性.孟祥彬[4]采用路面随机激励的方法,模拟带载行驶工况,取得了较好的结果.本文以75t伸缩臂履带起重机为研究对象,基于多软件集成分别建立地面、履带底盘、转台、臂架和钢丝绳等虚拟样机模型,采用刚柔耦合的方法,在多体动力学仿真软件RecurDyn中对典型工况进行动力学仿真分析,为履带底盘专用伸缩臂设计和带载行驶时相关操作规范的制定提供参考.1 动力学模型的建立伸缩臂履带起重机主要由吊具、臂架系统、变幅油缸、转台系统和履带底盘系统组成,各系统的布局如图1所示.利用Pro/E软件建立转台及上车部分,导入RecurDyn软件中;利用ANSYS软件建立臂架模型,将离散处理后的网格模型导入RecurDyn软件中;在RecurDyn软件中利用trackLM低速履带模块建立履带底盘系统,添加地面和相关联零部件之间的运动副关系.伸缩臂履带起重机基本结构如图1所示.1-吊具;2-伸缩臂;3-变幅油缸;4-转台及上车系统;5-履带底盘系统图1 伸缩臂履带起重机的整机结构图Fig.1 Sketch map of telescopic crawler crane1.1 臂架模型的建立本文所研究的伸缩臂履带起重机的臂架为U型臂,在ANSYS软件中采用shell63单元进行建模,设定材料的弹性模量为2.06×105 MPa,泊松比为0.3,按照U型臂架的厚度分别设定相应的实常数.在第一节臂架的底部耳板的中心、变幅油缸耳板的中心以及第五节臂架头部的耳板中心处均建立一个mass21节点,分别与周围的耳板建立刚性区域,作为与外界刚性体建立转动副的节点,如图2所示.通过RecurDyn软件中的FFlex模块将组装好的柔性体臂架读入到软件中,读入过程要保证前后采用的单位相同,本文采用的单位是mm,kg,N,s.在带载行驶时,变幅油缸处于锁死状态,所以将油缸简化为一圆柱刚体,两端分别与转台和臂架进行铰接.图2 伸缩臂有限元模型Fig.2 Finite element model of the boom1.2 履带底盘模型的建立RecurDyn软件中的履带模块分为两种:高速履带模块和低速履带模块.高速履带模块主要为坦克装甲车等履带设计开发的,低速履带模块主要为履带式工程车辆设计开发的,本文所研究的伸缩臂履带起重机应该采用低速履带模块.根据履带各部件的位置和参数,分别创建履带的驱动轮、支重轮、惰轮、托链轮、履带板和张紧装置,最后在模块中将履带板进行装配.RecurDyn软件可以自动创建驱动轮和履带之间的接触力数学模型以及导向轮和履带之间的作用力模型.调整驱动轮和履带不干涉后,建立相关的约束副,各零件间的约束副关系如表1所示.表1 各零件约束副对应关系Tab.1 Joint relationship of each part约束副类型原零件目标零件转动副驱动轮母体转动副支重轮履带板转动副惰轮张紧器转动副托链轮履带板固定副履带板母体1.3 其他模型的简化建立转台及上车结构采用Pro/E软件建模,输出后缀为.x-t格式后,作为刚体导入到RecurDyn软件中.模型建立时需要对刚体进行合理的简化,在RecurDyn软件中调整刚体的重量及质心位置不变.钢丝绳是起升机构中不可缺少的部分,是用来连接吊具和滑轮组的构件,其特点是只承受拉力,不承受压力.根据其特点,目前多采用Bushing嵌套力连接多段小圆柱来模拟钢丝绳部件之间的约束副,如图3所示. 本文选取的是平直的干土地面,RecurDyn软件根据设定的最大沉陷量、压应力和摩擦系数等计算履带与地面之间的相互作用力.RecurDyn软件343 中 国 工 程 机 械 学 报第12卷 中的地面主要分为硬质地面和软质地面两类,对于不同类型的地面,履带与地面间作用力的计算方法有所不同.图3 钢丝绳模型的简化Fig.3 Simplification of the wire rope 按照以上步骤建立的伸缩臂履带起重机虚拟样机模型如图4所示.图4 伸缩臂履带起重机模型Fig.4 Model of telescopic crawler crane1.4 驱动函数在仿真开始前需要在RecurDyn软件中定义履带的驱动轮速度,需要用到step三次多项式逼近阶跃函数,其基本格式为step(x,x0,h0,x1,h1).其中,x为自变量,可以是时间或时间的某一函数;x0为初始时刻;h0为函数的初始值;x1为终止时刻;h1为函数的终止值,当处于大于x1时刻时,函数值一直为h1.2 仿真算例及结果分析以75t伸缩臂履带起重机起升性能表为参考,选取臂架全伸工况时的起升幅度最小和起升力矩最大两种工况进行仿真分析.由于两种工况下结果曲线类似,下文仅以起升幅度最小工况为例,分别研究在不同带载比例和不同启动和制动加速度工况下,臂架危险区域应力的变化情况.2.1 不同带载比例臂架应力状态分析本文所研究的伸缩臂履带起重机在直线行驶时的行走速度为1.5km·h-1(416.7mm·s-1),驱动轮半径为381mm,所以求得驱动轮角速度为1.1rad·s-1.根据《起重机设计规范》[5],达到最大速度的加速时间为5s,驱动函数为step(time,0,0,5,-1.1)+step(time,35,0,40,1.1),驱动轮转速曲线和履带底盘行驶速度曲线分别如图5和6所示.由图5,6可以看出,虽然驱动轮的角速度是一条光滑的曲线,但由于履带的多边形效应,车辆的整体前进速度并不是光滑的曲线.图5 驱动轮角速度Fig.5 Angular velocity of the driving wheel图6 履带底盘行驶速度Fig.6 Velocity of the crawler chassis 选取带载比例分别为正常起升工况载荷的70%,85%,100%,即7.0t,8.5t,10.0t,不同带载比例下臂架危险区域节点的应力变化曲线如图7所示.由图7可以看出,臂架危险区域的应力整体呈正弦曲线方式波动,这是由起重机直线行驶时吊重的摆动所造成.应力的每一时刻都有微小的波动,并非光滑的曲线,这是由履带底盘行走时的多边形效应造成. 为比较三种带载比例对臂架应力状况的冲击影响,现定义应力冲击系数n1=σmaxσm(1)式中:σmax为最大应力,σm为静平衡时应力.三种带载比例下前5秒为匀加速启动过程,启动过程对臂架应力的影响不大.后5秒为匀加速制443 第4期苗 明,等:伸缩臂履带起重机直线行驶工况下臂架应力状态分析 动过程,制动时冲击系数最大,三种工况均为1.12.但是带载比例越大,制动时应力增加的幅值越大,产生的冲击现象越明显.图7 不同带载比例臂架应力变化Fig.7 Stress variation of boom at different load ratio2.2 不同启动、制动加速度臂架应力状态分析对于伸缩臂履带起重机,起重机操作规范里对其带载行驶比例尚无明确规定,对比上文分析结果,选取85%的带载比例下,加减速时间分别为2,3,5s,即起重机分别经过2,3,5s速度由零加速到正常行驶速度,平稳运行一段时间后,再分别经过2,3,5s速度由正常行驶速度减速到零,对应的加速度分别为!0.21,!0.14,!0.08m·s-2.应力变化曲线如图8所示. 同样定义最大应力与静平衡应力之比为臂架应力冲击系数,参照式(1),经过计算,在启动过程,应力波动不明显,在制动时,对臂架应力的冲击最大,2,3,5s加减速的冲击系数分别为1.17,1.14和1.12,并且加速度越大即加速时间越短冲击越明显,冲击系数越大.3 结论(1)起重机在启动过程中臂架的应力变化不大,在制动过程中臂架的应力变化最大. (2)惯性力导致的吊重摆动是引起臂架应力图8 不同加速度臂架应力变化Fig.8 Stress of boom in different acceleration变化的主要原因,履带底盘的多边形效应是引起臂架应力变化的次要原因.(3)带载比例越大,制动时的加速度越大,制动时间越短,臂架应力的冲击现象越明显.参考文献:[1] 许斌.新型履带式伸缩臂起重机[J].交通世界,2010(7):40-41.XU Bin.New type telescopic crawler crane[J].Traffic World,2010(7):40-41.[2] SHIN S H,YOO W S.Comparative study of dynamic analysistechniques in vehicle simulation[J].KSME Journal,1990,4(2):120-127.[3] 王欣,杜汉平.基于刚柔耦合的履带起重机虚拟样机建模技术[J].中国工程机械学报,2007,5(1):26-31.WANG Xin,DU Hanping.Virtual prototyping for rigid-flexible-coupling crawler crane[J].Chinese Journal ofConstruction Machinery,2007,5(1):26-31.[4] 孟祥彬.伸缩臂履带起重机带载行驶动特性研究[D].大连:大连理工大学,2013.MENG Xiangbin.Research on dynamic characteristics oftelescopic crawler crane traveling with load[D].Dlian:DalianUniversity of Technology,2013[5] 国家标准局.GB/T 3811—2008起重机设计规范[S].北京:国家标准局出版社,2008.The National Standard Office.GB/T 3811-2008Design rules ofcranes[S].Beijing:National Bureau of Standard Press,2008.543。
《2024年度伸缩臂叉装车行走系统优化分析与实验研究》范文

《伸缩臂叉装车行走系统优化分析与实验研究》篇一一、引言随着现代物流和工程机械技术的快速发展,伸缩臂叉装车作为一种重要的装载和运输设备,其性能的优化显得尤为重要。
其中,行走系统作为叉装车的关键组成部分,其性能的优劣直接影响到叉装车的作业效率和稳定性。
因此,对伸缩臂叉装车行走系统进行优化分析与实验研究具有重要的现实意义。
二、伸缩臂叉装车行走系统概述伸缩臂叉装车的行走系统主要由驱动系统、制动系统、转向系统和悬挂系统等部分组成。
驱动系统负责提供动力,制动系统负责车辆制动,转向系统控制车辆的行进方向,而悬挂系统则起到减震和支撑的作用。
这些系统的协同工作,保证了叉装车在各种工况下的稳定性和作业效率。
三、行走系统优化分析1. 驱动系统优化:通过改进电机控制器,提高电机的工作效率和动力输出,同时降低能耗。
此外,采用先进的能量回收技术,将制动过程中的能量回收再利用,提高整体能源利用效率。
2. 制动系统优化:采用先进的液压制动技术,提高制动性能和稳定性。
同时,通过智能控制系统,实现制动力的自动调节,避免因制动力过大或过小而导致的车辆失控或制动距离过长等问题。
3. 转向系统优化:通过优化转向机构的结构设计,提高转向的灵活性和稳定性。
同时,采用电子助力转向技术,减轻驾驶员的转向力度,提高操作舒适性。
4. 悬挂系统优化:通过改进悬挂系统的减震性能,降低车辆在行驶过程中的振动和冲击,提高乘坐舒适性和车辆稳定性。
四、实验研究为了验证上述优化措施的有效性,我们进行了实地实验研究。
实验过程中,我们对优化前后的驱动系统、制动系统、转向系统和悬挂系统进行了全面的性能测试。
实验结果表明,经过优化后,叉装车的动力性能、制动性能、转向灵活性和乘坐舒适性均得到了显著提高。
同时,能耗也得到了有效降低,提高了整体能源利用效率。
五、结论通过对伸缩臂叉装车行走系统的优化分析与实验研究,我们得出以下结论:1. 驱动系统的优化可以提高电机的工作效率和动力输出,降低能耗;同时采用能量回收技术,提高整体能源利用效率。
《2024年度伸缩臂叉装车行走系统优化分析与实验研究》范文

《伸缩臂叉装车行走系统优化分析与实验研究》篇一摘要:本文旨在探讨伸缩臂叉装车行走系统的优化设计及其实际应用效果。
首先,通过对行走系统的工作原理和现有问题进行深入分析,提出优化方案。
其次,通过理论建模和仿真分析,验证优化方案的可行性。
最后,通过实验研究,对优化后的行走系统进行性能评估,并得出结论。
一、引言随着工程机械的不断发展,伸缩臂叉装车作为一种重要的装载设备,其行走系统的性能直接影响到作业效率和安全性。
因此,对行走系统进行优化设计具有重要意义。
本文将重点分析伸缩臂叉装车行走系统的优化设计、理论建模、仿真分析以及实验研究等方面。
二、伸缩臂叉装车行走系统现状分析(一)工作原理伸缩臂叉装车行走系统主要由驱动系统、转向系统、制动系统和悬挂系统等组成。
驱动系统提供动力,转向系统控制行驶方向,制动系统保证安全停车,悬挂系统则起到减震作用。
(二)存在问题当前伸缩臂叉装车行走系统存在能耗高、稳定性差、操作不便等问题,影响了设备的整体性能和使用寿命。
三、行走系统优化设计(一)设计思路针对现有问题,从驱动系统、转向系统和悬挂系统等方面提出优化设计方案。
通过降低能耗、提高稳定性、优化操作等手段,提升行走系统的整体性能。
(二)具体措施1. 驱动系统:采用高效能电机和合理的传动比,降低能耗;2. 转向系统:优化转向控制策略,提高转向稳定性和灵活性;3. 悬挂系统:采用减震性能更好的悬挂装置,提高行驶平稳性。
四、理论建模与仿真分析(一)理论建模根据优化设计方案,建立行走系统的数学模型和物理模型,为后续的仿真分析提供基础。
(二)仿真分析利用仿真软件对优化后的行走系统进行仿真分析,验证其可行性和性能表现。
通过模拟实际工况,对能耗、稳定性、操作性能等指标进行评估。
五、实验研究(一)实验方法与步骤在实验场地进行实际测试,对比优化前后的行走系统在能耗、稳定性、操作性能等方面的表现。
通过数据采集和分析,评估优化效果。
(二)实验结果与分析实验结果表明,优化后的行走系统在能耗、稳定性和操作性能等方面均有显著提升。
《2024年度伸缩臂叉装车行走系统优化分析与实验研究》范文

《伸缩臂叉装车行走系统优化分析与实验研究》篇一一、引言随着现代物流和工程建设的快速发展,伸缩臂叉装车作为重要的物料搬运设备,其性能的优化显得尤为重要。
其中,行走系统作为叉装车的重要组成部分,其性能的优劣直接影响到叉装车的作业效率和作业安全性。
因此,本文旨在通过对伸缩臂叉装车行走系统的优化分析与实验研究,提高其作业性能和安全性。
二、伸缩臂叉装车行走系统概述伸缩臂叉装车的行走系统主要由驱动系统、转向系统和制动系统等组成。
其中,驱动系统负责叉装车的行进和后退;转向系统则控制叉装车的转向;制动系统则保证叉装车在作业过程中的安全性和稳定性。
然而,在实际使用过程中,行走系统可能存在能耗高、响应速度慢、稳定性差等问题。
三、行走系统优化分析1. 驱动系统优化针对驱动系统的能耗高问题,本文提出采用先进的电机控制技术,如矢量控制或直接转矩控制等,以实现电机的高效运行。
此外,通过对电机和传动系统的匹配优化,可以提高叉装车的行进速度和牵引力。
2. 转向系统优化针对转向系统的响应速度和稳定性问题,本文建议采用液压助力转向系统或电动助力转向系统。
这些系统可以通过电子控制技术实现快速、准确的转向响应,提高叉装车的作业效率和安全性。
3. 制动系统优化制动系统的优化主要关注制动性能的稳定性和可靠性。
通过采用先进的制动控制技术和高灵敏度的制动元件,可以保证叉装车在紧急情况下的安全制动。
同时,通过定期的维护和保养,可以保证制动系统的长期稳定运行。
四、实验研究为了验证上述优化措施的有效性,本文进行了实车实验研究。
首先,对优化前后的驱动系统进行能耗对比实验,结果显示优化后的驱动系统在能耗方面有明显降低。
其次,对转向系统的响应速度和稳定性进行测试,结果表明优化后的转向系统具有更快的响应速度和更高的稳定性。
最后,对制动系统的性能进行测试,验证了其稳定性和可靠性的提高。
五、结论通过本文的优化分析与实验研究,我们可以得出以下结论:1. 通过对驱动系统的优化,可以降低伸缩臂叉装车行走系统的能耗,提高其运行效率。
越野式伸缩臂叉装车整机稳定性理论计算方法和试验验证
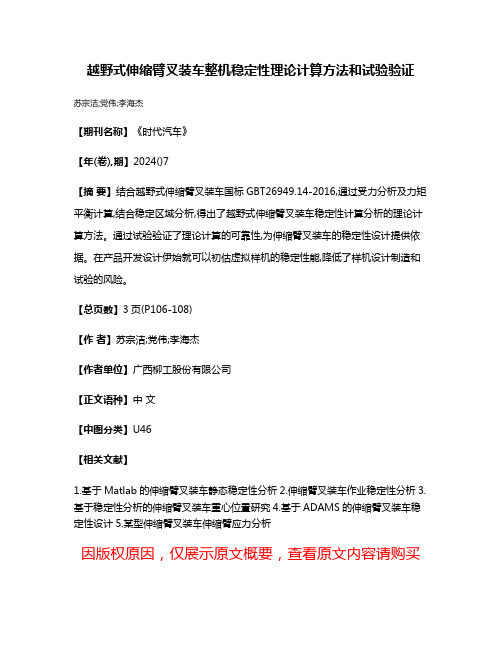
越野式伸缩臂叉装车整机稳定性理论计算方法和试验验证苏宗洁;党伟;李海杰
【期刊名称】《时代汽车》
【年(卷),期】2024()7
【摘要】结合越野式伸缩臂叉装车国标GBT26949.14-2016,通过受力分析及力矩平衡计算,结合稳定区域分析,得出了越野式伸缩臂叉装车稳定性计算分析的理论计算方法。
通过试验验证了理论计算的可靠性,为伸缩臂叉装车的稳定性设计提供依据。
在产品开发设计伊始就可以初估虚拟样机的稳定性能,降低了样机设计制造和试验的风险。
【总页数】3页(P106-108)
【作者】苏宗洁;党伟;李海杰
【作者单位】广西柳工股份有限公司
【正文语种】中文
【中图分类】U46
【相关文献】
1.基于Matlab的伸缩臂叉装车静态稳定性分析
2.伸缩臂叉装车作业稳定性分析
3.基于稳定性分析的伸缩臂叉装车重心位置研究
4.基于ADAMS的伸缩臂叉装车稳定性设计
5.某型伸缩臂叉装车伸缩臂应力分析
因版权原因,仅展示原文概要,查看原文内容请购买。
- 1、下载文档前请自行甄别文档内容的完整性,平台不提供额外的编辑、内容补充、找答案等附加服务。
- 2、"仅部分预览"的文档,不可在线预览部分如存在完整性等问题,可反馈申请退款(可完整预览的文档不适用该条件!)。
- 3、如文档侵犯您的权益,请联系客服反馈,我们会尽快为您处理(人工客服工作时间:9:00-18:30)。
2 1 截面 1—1 .
( )侧移液压缸 在零 位时 b ( )侧移液压缸右移 2 0m c 0 m时
图 2 伸缩 臂水平状态下负载 的横 向作 用位置
图 4 为截面 1 a —1特 征 ,通 过 这些 特征 可 以求 得 1—1截 面 的 近 似 面 积 等 特 性 。 图 4 a中 ,口 =
作条件确定 了 6个研究工况 ,采用工程力学知识建 立伸 缩臂 的力 学模 型 ,通 过分 析约束 和外载 条件确定 了伸缩
臂结构 的危险截面 ,计算 出危 险截 面上盖板 和下底板 处切应 力 、弯 曲应 力和 局部集 中应力 ,最后 采用 第 四强度
理论进行强度计算 ,为伸缩臂叉装 车伸缩臂的结构设计提供 了强度计算方法 。
举 升 载荷 为 5k N;在伸缩 臂 水平 伸 出 50mm状态 4 下 ,最 大举 升载 荷为 2 N 5k 。伸 缩 臂头 部 安 装侧 移 器货 叉 ,货 叉 可 以 在 侧 移 液 压 缸 的作 用 下 横 向移 动 ,以达 到精 确 摆 放货 物 的 目的。根 据设 计 经 验 ,
c i e y C . t . h a e e t i s6 wo kn o d t n n l e w t h e in e p r n e a d a t a o k n o d— h n r o ,L d ,t e p p ri ni e r i g c n i o s i i i t e d s x e i c n cu lw r i g c n i d f i n h g e
yM 1 G 1 0 0 3 1 0 4 0 G l 3 bG A .9 G + . 6 ( A +c )
3
M 1 G l 00 3 l . 6 ( A +G ) G A . 9 G +02 0 G 1 3
F2 攀 ,2 举 F2 攀 yM 1 G 2 0 0 3 :+ . 6 ( A +G ) bG A .9 6 0 6 0 G 2 3 1 M 1 G 2 00 3 l . 6 ( A +6 ) G A . 9 ( +04 0 G 2 : ; 3 bG G 2 0 0 3 1 0 2 0 G 2 : ) M1 A .9 ( + . 6 ( ^ +6 ; 3
srn hte r ,p oiigsrn t ac lt n meh dfrtlh n lrtls o i o m tu tr e in t g oy rvdn te gh c uai to o e a de ec pcb o srcu ed sg . et h l o e e
横 向侧 移 位 置 为 变 量 因素 ,分 为 6个 研 究 工 况 ,
见表 1 。
表 1 伸 缩 臂 各 工 况 状 态
工况 伸缩 臂伸缩状态 控制起重量/ g k 货叉侧 移位置
1 左 移 20 m 0 m
2 3
4
水平全伸
50 o
中置 右移 20mm 0
1 2 约束 与 外载 .
由于伸缩 臂重 心 不 在 伸 缩臂 变 幅平 面 (0 平 z 面 ) 内 ,而且 货叉 可 以通 过液 压 缸 驱 动 左右 侧 移 , 所 以在平 行 于伸缩 臂截 面的平 面 ( 平 面 ) 内伸 缩 臂 受 到 由伸 缩 臂 ( 含货 叉 )重 力 G 、货 叉 重 不 力G ,以及货 物 重 力 G 产生 的偏 载扭 矩 ,如 图 2所
d n t s n o a o c n r td sr s f te d n e o s s c in , a d f al e fr s s e gh c c l t n b u h ig s e s a d l c c n e tae te s o h a g r u e t s r l o n n l p ro t n t a u ai y f a i y m r l o o
某 型 伸 缩 臂 叉装 车 伸 缩 臂应 力分 析
奚 源 陈 志 王 志 丁永 军 闰洪 峰 田 甜
1中国农业机械 化科学研 究院 北京
摘
108 2驻黎阳机械公司军事代表室 郑州 40 0 003 5 00
要 :以北京金轮特种机 械有 限公 司 T 2 0 H 5 6型伸缩臂叉装车伸缩臂为研究对象 ,结合设计经 验和实 际工
依据 图 2和 图 3中伸 缩臂 的受 力状 况可 以计算 出伸 缩臂 在 平 面 内所 受 弯 矩 和平 行 于 xy平 面 o 内所 受扭 矩 ,6种工 况所 对应 的约 束条 件 和载 荷 如
表 2 。
表2 6种工况对应的约束条件和载荷
( A = . N, A =1 . N, 1 1 1 N, =19 N) G 1 4 9k G 2 3 5k G =1. 8k .7k 变 幅 液 压 缩 臂 载 伸 负
液压 缸 驱 动 ,货 叉 的左 右 侧 移 由水 平 方 向 的侧 移 液压 缸 驱 动 ,伸 缩 臂 的整 体 变 幅 运 动 通 过 变 幅 液
压缸驱 动 。
级臂 和货 叉结 构 ,3级 伸缩 臂 的伸 缩 由 1 液 压缸 个 和 2组传 动 链 条 实 现 。在 伸 缩 臂 上 方 I级 臂 尾 部
关键 词 :叉装 车;伸缩臂 ;工况 ;危 险截 面 ;应力 ;分 析
中 图分 类 号 :T 2 2 H 4 文 献 标 识 码 :A 文章 编 号 :10 0 8 ( 0 1 0 0 7 0 0 1— 7 5 2 1 ) 8— 0 2— 4
Abtat aigte e soi bo f e H 56t eade a uatrdb eigG le el pc l - src:T kn l cpc om o 20 lhn l m nfcue yB in o nWh e S ei h te h t T e r j d a Ma
型如 图 1所 示 ,主要 结 构 为 I 臂 、 Ⅱ级 臂 、 Ⅲ 级
间设 置 2条 板 式 传 动 链 条 ,在 Ⅱ、 Ⅲ级 臂 之 间设
置1 条板式传 动链 条 ,由此将 Ⅱ、Ⅲ级臂和链 条
构成 闭 环 传 动 结 构 ,由 液 压 缸 驱 动 链 条 完 成 Ⅱ、
Ⅲ级 臂 的 同 步 伸 缩 。货 叉 上 下 翻 转 通 过 货 叉 俯 仰
收稿 日期 :2 1 0 0—1 2 2— 7
7 一 2
《 起重 运输 机械 》 21 8 0 1( )
1 工 况 分 析
1 1 各 工况 下伸 缩臂 状态 .
T 20 H 56型 伸 缩 臂 叉 装 车 的 伸 缩 臂 能 够 实 现
一
9 ~ 1变 幅 ,在 伸 缩 臂 水 平 全 伸 状 态 下 ,最 大 。 6。
02=0 4= 8 mm , 3= 1 mm , b = 2 6 2 7 mm , h =
一
《 起重运输 机械》 2 1 ( ) 01 8
一
[ ]G / 8 1 20 1 B T3 1- 0 8起重机设计规范 [ ] S. [ ]F M 10 1 9 8欧洲起 重机设 计规范 [ ] 2 E .0 :19 S
作 地 邮 者 :吴 军
址 :河南省 长垣县博 爱南路 6号河南卫华 重型机械 股份有限公司总工办 编 :4 30 540
示 。货叉 侧移 液压 缸 变 幅量 为 一2 0~2 0mm。伸 0 0 缩 臂 等效 受力 图见 图 3 。
4 5 6
在 xy平 面 内 以 伸 缩 臂 根 部 铰 点 为 力 矩 平 衡 o
点,计算可得 F 1 13 2 N,F 2 14 1 k 。 举 = 3 .8k 举 = 7.7 N
t n ,e tb i e ee c p c b o me h n c d l a e n e g n ei g me h n c n w e g i s sa l h st ls o i o m c a ismo e s d o n i e r c a i sk o ld e,d t r n st e d n e o s o s b n e e mi e h a g r u
和 Ⅱ级 臂 头 部 之 间 设 置 液 压 缸 ,在 I、 Ⅱ级 臂 之 疲劳 强度 不一 定按 设 计 规 范 式 ( 1 ) ( 1 ) 进 1 1 、 12
图 1 T 20 H 5 6型伸缩臂 叉装 车
伸缩臂结构 图
参考 文献
行计算 ,因按此计算 出的数值 有可能大于机械零
件 的最 大 抗 拉 、抗 剪 疲 劳 强 度 值 ,应 以不 大 于 机 械零 件 的最大 抗拉 、抗 剪疲 劳强 度值 为 限制 。 当机 械零 件受 具有 不 同应力 循环 特征 值 r 正 的 应力 和 剪 切 应 力 同时 作 用 时 ,设 计 规 范 式 ( 1 ) 18 中的疲 劳安全 系数 n 的取 值 应 以 上述 疲 劳应 力 的 最大 安全 系数 为 准 。
2 危险截面特性计算
由伸缩 臂 约 束 与 受 力 分 析 ,确 定 在 变 幅液 压 缸 铰点 处 、 I级 臂 和 Ⅱ级 臂 搭 接 处 、 Ⅱ级 臂 与 Ⅲ 级 臂搭 接 处 存 在 3个 危 险 截 面 ,危 险 截 面 特 征 如
图 4 。
( )侧移液 压缸左移 20mm a 0
0 前 言
伸缩 臂 叉 装 车 是 一 种 具 有 多 种 作 业 功 能 的 车辆 ,它 将 轮 式 起 重 机 的 伸 缩 臂 式 结 构 与 传 统 叉装 车 的装 卸 功 能 有 机 地 结 合 到 一 起 ,充 分 利 用 了伸 缩 臂 式 结 构 伸 得 高 、伸 得 远 的 特 点 , 可 在底 盘 不 动 的 情 况 下 ,对 离 前 轮 较 远 的 物 资 进 行作业 。 T 2 0 伸缩臂 叉 装 车 伸 缩 臂 结 构 的 三维 造 H 56型
s cin ft e tls o i o m tu t r h o g n y i c n t it n  ̄e a o d t n ,c c lts s e rsrs ,b n e t so ee c p c b o sr cu e tr u h a a s o sr n s a d e r l c n i o s a u a e h a t s e — o h l s a u i l e