石油管道焊缝检测
《石油管道焊缝检测》课件
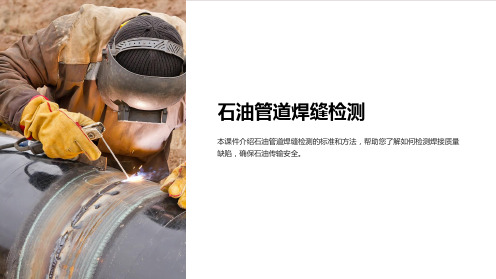
焊缝X射线检测技术
1
优点
可以对不同类型的材料进行检测。
2
应用场景
焊接件、铸造件、铸钢件的内部缺陷。
焊缝磁粉检测技术
优点
可以发现可见缺陷和表面裂纹等不易被其他检测方法发现的缺陷。
应用场景
焊接结构物、车轮轮辋、坦克炮管等缺陷检测。
局限性
只能对磁性部件进行检测。
GB 50253-2015《金属管道焊接规 范》等。
行业标准
P309:管道输送系统焊接质量标 准等。
法律法规
《中华人民共和国安全生产法》 等相关法律法规。
焊缝质量缺陷分类介绍
1
裂纹
2
焊缝或母材中出现的开裂。
3
凹坑
在焊接过程中出现的坑洞或者碳化物。
气孔
焊接时产生的气体在焊缝中形成的圆形 空洞。
检测方法概述
石油管道焊缝检测
本课件介绍石油管道焊缝检测的标准和方法,帮助您了解如何检测焊接质量 缺陷,确保石油传输安全。
石油管道焊缝检测的目的
安全性
防止因焊接质量问题导致石 油泄漏事故。
经济性
保证管道交付质量,减少返 修和重新焊接的成本。
法规要求
符合国家和行业相关的标准 和规定。
石油管道相关标准及规定
国家标准
1 超声波检测
利用声波在材料中的传播 规律进行缺陷检测。
2 X射线检测
利用X射线对材料进行穿 透性检测。
3 磁粉检测
在涂有磁性粉末的零件上, 发现经过磁场拉伸后的铁 磁性裂纹。
焊缝超声波检测技术
优点
• 有非常高的灵敏度。 • 可以在操作难度大的位置检测。
应用场景
• 石化、航天等行业的焊接检测。 • 各种金属或非金属材料的焊缝检测。
油气管道环焊缝检测

图2(e)所示是l0=1500mm,t=7mm,r0=100mm的管道,取测线r=0,θ=0°时,管道内磁场的分 布。可见,较长管道内的磁场分布与较短管子的类似,只是轴向分量和径向分量的平坦部分 更长一些。可以预见当管道很长时,管道内可近似认为是一匀强磁场。
α=0°
α=90°α=0° α=90°
r=0r0,θ=0°
(d)500mm管道测线4上磁场分布
α=0°
α=0°
α=90°
α=90°
r=0r0,θ=0°
磁化角度、不同长度管道内磁场分布;α=0°,15°,30°,45°,60°,75°,90°;r0=100mm;t=7mm;
(a)-(d)l0=500mm,(e)l0=1500mm
(a)500mm管道测线1上磁场分布
α=0°
α=90°α=0° α=90°
r=0.2r0,θ=0°
(b)500mm管道测线2上磁场分布
α=0°
α=90° α=0° α=90°
r=0.2r0,θ=72°
(c)500mm管道测线3上磁场分布
α=0°
α=90°α=0° α=90°
r=0.2r0,θ=144°
等效磁荷法可以有效获得铁磁性材料表面磁荷密度分布,进而方便地求出其周围磁 场分布。本文首次采用等效磁荷法,针对不同的磁化方向计算了非轴向磁化圆柱管状铁 磁性材料表面磁荷密度分布及管内磁场分布并分析了管道内环焊缝处异常磁场产生的 原因及特点。然后设计了一个用于测量管道内磁场的球形载体,测量了某输油气实验管 道内的磁场,以验证上述分析的正确性。最后对所测数据进行处理,通过对管道内环焊 缝处异常磁场的识别和定位而实现对管道环焊缝的识别和定位。
二. 理论分析
采用三维磁体表面磁荷分析方法分析任意方向均匀磁化的铁磁性管道表面的磁荷 密度分布,如式(1)所示。其中,rs 为磁体表面某一点的位置矢量,r’为磁体表面除去 rs 以后剩余表面上任一点的位置矢量,H0为磁化磁场强度,n 为磁体表面 rs处单位法向量, μ 为磁体相对磁导率。
石油天然气钢质管道无损检测-SY-T4109-2013

编号 SGB—1 SGB—2 SGB—3 SGB—4
SGB—5
SGB—6
200
平面
>360~600
>600
SRB对比试块
说明:Φ---被检管线外径; T---被检管线公称壁厚; h---内壁环状矩形槽的槽深; h=10%T且h≤1.5mm。
声能损失
仪器性能的调节
直探头测定,垂直线性,水平线性 斜探头测定,入射点,前沿距离,分辨力,折射角, 灵敏度余量
检测准备
检测面 探头移动区应清除飞溅、锈蚀、油污及其他外部 杂质,检测表面应修磨平整光滑,其表面粗糙度不应 超过6.3μm。焊缝及检测面应经外观检查合格方可进行 检测。
探头移动要求
探头移动区的确定应符合下列规定: 1.采用一次反射法检测时,探头移动区不应小于1.25P, P应按式(6.7.3)计算: P=2KT (6.7.3) 式中:P—跨距(mm); T—板厚(mm); K—声束在工件中的折射角β的正切值(tanβ)。 2.采用直射法检测时,探头移动区不应小于0.75P。
扫查方法
应采用单面双侧直射法和反射波法检测。 扫查灵敏度不应低于评定线灵敏度。 扫查速度不应大于150mm/s,当采用自动报警装臵扫 查时不受此限制;在平行扫查方向上,每个探头的 扫查路径应重叠,其范围至少为探头(压电晶片) 垂直于扫查方向尺寸的10%。
为探测纵向缺欠,探头应垂直焊缝中心线做矩形或 锯齿形扫查,探头前后移动范围应保证能扫查到全 部焊缝截面及热影响区,在保持探头垂直焊缝作前 后移动的同时,应作10°~15°的左右扫查。为观察 缺陷动态波形和区分缺陷信号或伪缺陷信号,确定 缺陷的位臵、方向和形状,可采用前后、左右、转 角、环绕等四种探头基本扫查方式。 检测横向缺欠时,应将波幅曲线灵敏度均提高6dB。 检测时,可在焊接接头两侧边缘使探头与焊接接头 中心线成10°~20°作两个方向的斜平行扫查。
管道焊缝检测方法
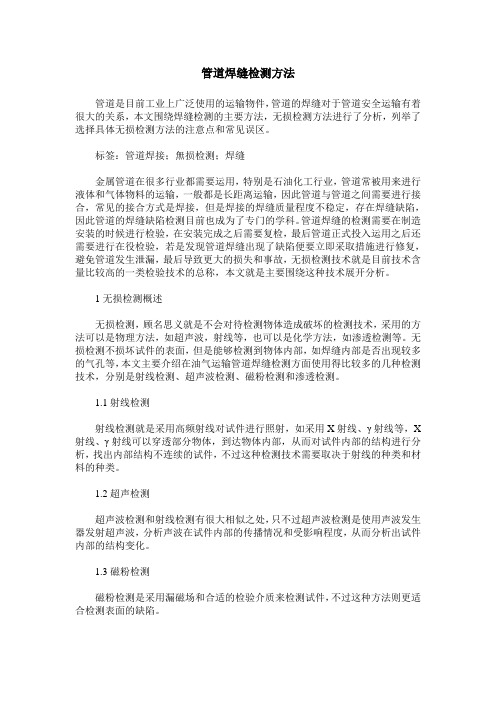
管道焊缝检测方法管道是目前工业上广泛使用的运输物件,管道的焊缝对于管道安全运输有着很大的关系,本文围绕焊缝检测的主要方法,无损检测方法进行了分析,列举了选择具体无损检测方法的注意点和常见误区。
标签:管道焊接;無损检测;焊缝金属管道在很多行业都需要运用,特别是石油化工行业,管道常被用来进行液体和气体物料的运输,一般都是长距离运输,因此管道与管道之间需要进行接合,常见的接合方式是焊接,但是焊接的焊缝质量程度不稳定,存在焊缝缺陷,因此管道的焊缝缺陷检测目前也成为了专门的学科。
管道焊缝的检测需要在制造安装的时候进行检验,在安装完成之后需要复检,最后管道正式投入运用之后还需要进行在役检验,若是发现管道焊缝出现了缺陷便要立即采取措施进行修复,避免管道发生泄漏,最后导致更大的损失和事故,无损检测技术就是目前技术含量比较高的一类检验技术的总称,本文就是主要围绕这种技术展开分析。
1无损检测概述无损检测,顾名思义就是不会对待检测物体造成破坏的检测技术,采用的方法可以是物理方法,如超声波,射线等,也可以是化学方法,如渗透检测等。
无损检测不损坏试件的表面,但是能够检测到物体内部,如焊缝内部是否出现较多的气孔等,本文主要介绍在油气运输管道焊缝检测方面使用得比较多的几种检测技术,分别是射线检测、超声波检测、磁粉检测和渗透检测。
1.1射线检测射线检测就是采用高频射线对试件进行照射,如采用X射线、γ射线等,X 射线、γ射线可以穿透部分物体,到达物体内部,从而对试件内部的结构进行分析,找出内部结构不连续的试件,不过这种检测技术需要取决于射线的种类和材料的种类。
1.2超声检测超声波检测和射线检测有很大相似之处,只不过超声波检测是使用声波发生器发射超声波,分析声波在试件内部的传播情况和受影响程度,从而分析出试件内部的结构变化。
1.3磁粉检测磁粉检测是采用漏磁场和合适的检验介质来检测试件,不过这种方法则更适合检测表面的缺陷。
1.4渗透检测渗透检测需要使用检测液和显像液,先采用检测液从已经在表面看得到缺陷的缺口处注入检测液,之后用显像液将检测液吸至表面,这种检测方法利用的是液体的毛细管渗透作用,也适合于检测表面处的缺陷,和磁粉检测一样不适用于深层缺陷检测。
油气管道环焊缝数字化无损检测技术应用分析常兰川

油气管道环焊缝数字化无损检测技术应用分析常兰川发布时间:2023-05-30T05:50:52.611Z 来源:《工程管理前沿》2023年6期作者:常兰川[导读] 为适应智能化管道建设的迫切要求,油气管道正在向数字化无损检测技术发展。
文章对数字无损检测技术在实际中的应用做了一些探讨,其主要是对AUT和PAUT超声波类检测新技术的应用现状进行了阐述,并提出一些的质量控制措施,以期为油气管道环焊缝数字化无损检测技术的应用完善提供一定的帮助。
徐州东方工程检测有限责任公司 221008摘要:为适应智能化管道建设的迫切要求,油气管道正在向数字化无损检测技术发展。
文章对数字无损检测技术在实际中的应用做了一些探讨,其主要是对AUT和PAUT超声波类检测新技术的应用现状进行了阐述,并提出一些的质量控制措施,以期为油气管道环焊缝数字化无损检测技术的应用完善提供一定的帮助。
关键词:油气管道;环焊缝;数字化无损检测技术引言相对于传统检测方法,数字化无损检测技术在智能化管道施工中有着显著的优越性,其优点是:检测过程的自动化、检测数据的数字化采集,检测结果的实时保存。
在油气管道中,采用了数字无损检测技术,可以有效的保证油气管道的检测质量。
然而,当前的环焊缝数字化无损检测技术依旧存在一定的缺陷,相关建设单位、监管机构、检测机构应对其加以重视,并进行研究与分析,采取措施,有效控制检测质量。
一、数字化无损检测技术(一)AUT检测技术全自动超声检测技术(AUT)是一种能够快速准确的检测管道环向焊接接头缺陷的新型无损检测技术;近年来,AUT技术在长输管道无损检测中得到广泛应用,对于提高无损检测效率、保证无损检测质量、节约工程成本有着重要的意义。
全自动超声检测技术(AUT),采用分区扫查模式,设置不同的延时聚焦方案,通过控制晶片的激发时间,形成不同角度的波束,实现对各自分区的单独扫查,同时辅以B扫通道和TOFD通道,从而实现整个焊缝的整体扫查,检测结果以双门带状图的形式显示。
油气管道环焊缝缺陷排查及处置措施研究
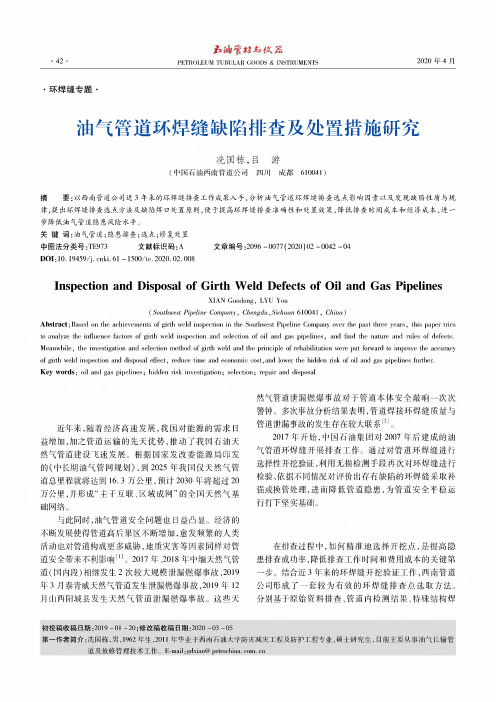
2017年 ,中国石油集团对2007年后建成的油
气管道环焊缝
查工作。通 管道环焊缝 ’
性
证,利用无损检测手段再 环焊缝 '
检验,依
出存有 的环焊缝采取补
换管处理,进而降低管道隐患,为管道安全平稳运
下坚
。
查过程中,
准
点, 高隐
患排查成功率,降低排查工作时间和费用成本的关键第
( 合3年的环焊缝
证工作,西管道
公司形成 套较为有效的环焊缝排查点选取 。
于原始资料排查、管道内检测 、
焊
初投稿收稿日期:2019 -01 -20;修改稿收稿日期:2020 -03 -05 第一作者简介:冼国栋,男,1962年生,2011年毕业于西南石油大学防灾减灾工程及防护工程专业,硕士研究生,目前主要从事油气长输管
道及抢修管理技术工作。E-mail:gdxian@ petrochina. com. cn
步降低油气管道隐患风险水平。
关 键 词:油气管道;隐患排查;选点;修复处置
中图法分类号:TE973
文献标识码:A
文章编号:2096 -0077( 2020) 02 -0042 -04
DOI:10.19459/j. cnki. 61 - 1500/te. 2020. 02. 008
Inspection and Disposal of Girt* Weld Defects of Oil and Gas Pinelines
表1 西南管道公司2018年6月前环焊缝排查情况
开挖 总数
不合格焊口 数量 占开挖总量比例
弯头变壁口
数量
占 合格 例
699
241
34%
119
49%
管道焊缝射线检测程序
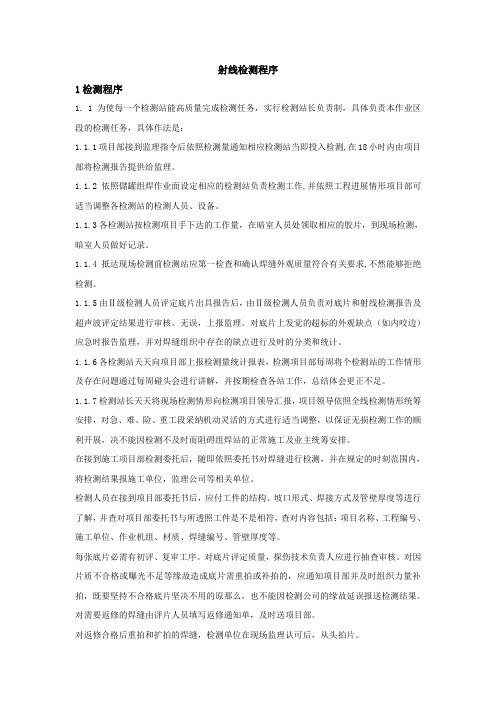
射线检测程序1检测程序1.1为使每一个检测站能高质量完成检测任务,实行检测站长负责制,具体负责本作业区段的检测任务,具体作法是:1.1.1项目部接到监理指令后依照检测量通知相应检测站当即投入检测,在18小时内由项目部将检测报告提供给监理。
1.1.2依照儲罐组焊作业面设定相应的检测站负责检测工作,并依照工程进展情形项目部可适当调整各检测站的检测人员、设备。
1.1.3各检测站按检测项目手下达的工作量,在暗室人员处领取相应的胶片,到现场检测,暗室人员做好记录。
1.1.4抵达现场检测前检测站应第一检查和确认焊缝外观质量符合有关要求,不然能够拒绝检测。
1.1.5由Ⅱ级检测人员评定底片出具报告后,由Ⅱ级检测人员负责对底片和射线检测报告及超声波评定结果进行审核。
无误,上报监理。
对底片上发觉的超标的外观缺点(如内咬边)应急时报告监理,并对焊缝组织中存在的缺点进行及时的分类和统计。
1.1.6各检测站天天向项目部上报检测量统计报表,检测项目部每周将个检测站的工作情形及存在问题通过每周碰头会进行讲解,并按期检查各站工作,总结体会更正不足。
1.1.7检测站长天天将现场检测情形向检测项目领导汇报,项目领导依照全线检测情形统筹安排,对急、难、险、重工段采纳机动灵活的方式进行适当调整,以保证无损检测工作的顺利开展,决不能因检测不及时而阻碍组焊站的正常施工及业主统筹安排。
在接到施工项目部检测委托后,随即依照委托书对焊缝进行检测,并在规定的时刻范围内,将检测结果报施工单位,监理公司等相关单位。
检测人员在接到项目部委托书后,应付工件的结构、坡口形式、焊接方式及管壁厚度等进行了解,并查对项目部委托书与所透照工件是不是相符,查对内容包括:项目名称、工程编号、施工单位、作业机组、材质、焊缝编号、管壁厚度等。
每张底片必需有初评、复审工序。
对底片评定质量,探伤技术负责人应进行抽查审核。
对因片质不合格或曝光不足等缘故造成底片需重拍或补拍的,应通知项目部并及时组织力量补拍,既要坚持不合格底片坚决不用的原那么,也不能因检测公司的缘故延误报送检测结果。
焊缝合格标准

焊缝合格级别及无损检测要点一、长输管道:1.SY0410—98《输油输气管道线路工程施工及验收规范》第7.3.2条:RT执行SY4056—93;UT执行SY4065—93合格级别:输油:P设≤6.4MPa Ⅲ级P设>6.4MPa Ⅱ级输气:P设≤4MPa 一、二级地区Ⅲ级;三、四级地区Ⅱ级P设>4MPa Ⅱ级第7.3.4条:输油管道的探伤比例可任选下面其中之一:100%UT后,对每个焊工或机组每天完成数量的5%作射线复验只进行RT抽查,抽查比例为每个焊工或作业机组每天完成数量的15% 。
第7.3.5条:输气管道的探伤比例:100%UT后,对每个焊工或作业机组每天完成数量的抽查比例:一级地区5%二级地区10%三级地区15%四级地区20%只进行RT抽查,对每个焊工或作业机组每天完成数量的抽查比例:一级地区10%二级地区15%三级地区40%四级地区75%第7.3.6条:抽查时,如每天的焊口数量比例达不到比例要求时,可以每公里为一个检验段,并按规定的比例数随焊随查,均匀的复验、抽查。
第7.3.7条:射线探伤复验,抽查中,有一个焊口不合格,应对该焊工或机组段焊接焊口加倍检查,再不合格,则其余焊口逐个RT探伤第7.3.8条:穿越焊口,钢管与弯头连接的焊口,试压后连头的碰口应进行100%RT。
第7.3.9条:×60及以上级别管材,返修后应按《常压钢制焊接储罐及管道渗透检测技术标准》SY/T0443进行渗透检查。
第7.3.10条:探伤人员应取得相关主管部门颁发的证书。
2.SY0470—2000《石油天然气跨越工程施工及验收规范》第5.3.2条:焊缝外观检查合格之后,应进行无损探伤。
焊缝无损探伤应符合下列规定:跨越管道环向焊缝应进行100%射线探伤。
对射线探伤难度大的个别环向焊缝部位,经有关部门共同商定可用超声波探伤代替射线探伤,但其数量不准超过总数10%。
RT符合SY4056 Ⅱ级合格;UT符合SY4065 Ⅱ级合格二、集输管道:1.SY0466—97《天然气集输管道施工及验收规范》第5.2条无损探伤:第5.2.1条:无损探伤人员必须具备劳动部门颁发的Ⅰ级以上资格证,评片人员具有Ⅱ级及其以上资格;第5.2.2条:焊缝无损探伤必须在外观质量检验合格后进行;第5.2.3条:设计无规定时,管道环缝100%UT,每个焊工所焊的各类焊缝应第5.2.5条:当RT复验不合格,应对该焊工所焊该类焊缝按原射线探伤复验数量补充探伤,仍不合格,停止其工作,并对其于焊工所焊焊缝进行100%RT 复验。
5)长输管道对接焊缝返修后的渗透检测(精)

长输管道对接焊缝返修后的渗透检测向阳施鹏飞(南京佳业检测工程有限公司,江苏南京)以仪征至长岭原油管道工程的渗透检测为例。
仪征至长岭原油管道工程连接仪征首站储油库和湖南长岭炼厂,主要用于进口原油的运输。
全长900公里,主线管道规格为Ø864×11.1材质为:X65。
在管道施工中我检测项目部对X65管材焊口的返修部位、热影响区及返修部位两侧沿焊缝方向各100mm做100%检测。
采用溶剂去除型着色渗透检测法,检测依据的标准为《承压设备无损检测》JB/T4730.5—2005 Ⅰ级合格。
1概述渗透检测是一种以毛细管作用原理为基础的检查表面开口缺陷的无损检测方法,与其它无损检测方法相比,它具有检测方便,设备简单等特点,它检测时不需电源、水源,特别适合野外长距离输送管道的检测工作。
渗透检测伤的缺点是它只能检查表面开口的缺陷,因而在管道无损检测过程中往往与其它无损检测方法配合使用。
2检测对象、比例及检测时机X65管材焊口的返修部位、热影响区及返修部位两侧沿焊缝方向各100mm做100%PT 检测。
返修部位返修完毕后24小时,经RT检测合格,再进行渗透检测。
3检测方法采用溶剂去除型着色渗透检测法。
4器材及要求采用压力喷罐式清洗剂、渗透剂、显像剂,型号DPT-5,在有效期内,喷罐表面无锈蚀和泄漏;试块采用A型铝合金试块和B型镀铬试块。
5系统灵敏度试验在检测现场,使用B型镀铬试块检验操作系统渗透检测灵敏度,灵敏度试块上的人工缺陷在应能清晰的显示3个辐射状裂纹区。
当环境温度低于10℃或高于50℃时,应使用铝合金标准试块,按标准附录B的要求对检测操作方法做出校正。
6检验程序前处理→渗透→去除→显像→观察及评定→后处理。
6.1前处理前处理时野外渗透检测作业的重点,必须使彻底清除妨碍渗透剂渗入缺陷的油脂、涂料、铁锈、水分、检测表面的氧化皮及泥巴污物等。
对被检件进行局部检测时,准备工作范围一般从检测范围向外扩展25mm(根据现场实际情况可增加前处理范围,以免污物对检测面的影响。
油气管道无损检测技术

油气管道无损检测技术管道作为大量输送石油、气体等能源的安全经济的运输手段,在世界各地得到了广泛应用,为了保障油气管道安全运行,延长使用寿命,应对其定期进行检测,以便发现问题,采取措施。
一、管道元件的无损检测(一)管道用钢管的检测埋地管道用管材包括无缝钢管和焊接钢管。
对于无缝钢管采用液浸法或接触法超声波检测主要来发现纵向缺陷。
液浸法使用线聚焦或点聚焦探头,接触法使用与钢管表面吻合良好的斜探头或聚焦斜探头。
所有类型的金属管材都可采用涡流方法来检测它们的表面和近表面缺陷。
对于焊接钢管,焊缝采用射线抽查或100 %检测,对于100 %检测,通常采用X射线实时成像检测技术。
(二)管道用螺栓件对于直径> 50 mm 的钢螺栓件需采用超声来检测螺栓杆内存在的冶金缺陷。
超声检测采用单晶直探头或双晶直探头的纵波检测方法。
二、管道施工过程中的无损检测(一)各种无损检测方法在焊管生产中的配置国外在生产中常规的主要无损检测配置如下图一中的A、B、C、E、F、G、H工序。
我国目前生产中的检测配置主要岗位如下图中的A、C、D、E、F、G、H工序。
图一大口径埋弧焊街钢管生产无损检测岗位配置(二)超声检测全自动超声检测技术目前在国外已被大量应用于长输管线的环焊缝检测,与传统手动超声检测和射线检测相比,其在检测速度、缺陷定量准确性、减少环境污染和降低作业强度等方面有着明显的优越性。
全自动相控阵超声检测系统采用区域划分方法,将焊缝分成垂直方向上的若干个区,再由电子系统控制相控阵探头对其进行分区扫查,检测结果以双门带状图的形式显示,再辅以TOFD (衍射时差法)和B扫描功能,对焊缝内部存在的缺陷进行分析和判断。
全自动超声波现场检测时情况复杂,尤其是轨道位置安放的精确度、试块的校准效果、现场扫查温度等因素会对检测结果产生强烈的影响,因此对检测结果的评判需要对多方面情况进行综合考虑,收集各种信息,才能减少失误。
(三)射线检测射线检测一般使用X 射线周向曝光机或γ射线源,用管道内爬行器将射线源送入管道内部环焊缝的位置,从外部采用胶片一次曝光,但胶片处理和评价需要较长的时间,往往影响管道施工的进度,因此,近年来国内外均开发出专门用于管道环焊缝检测的X 射线实时成像检测设备。
石油管道焊缝缺陷的等级评价
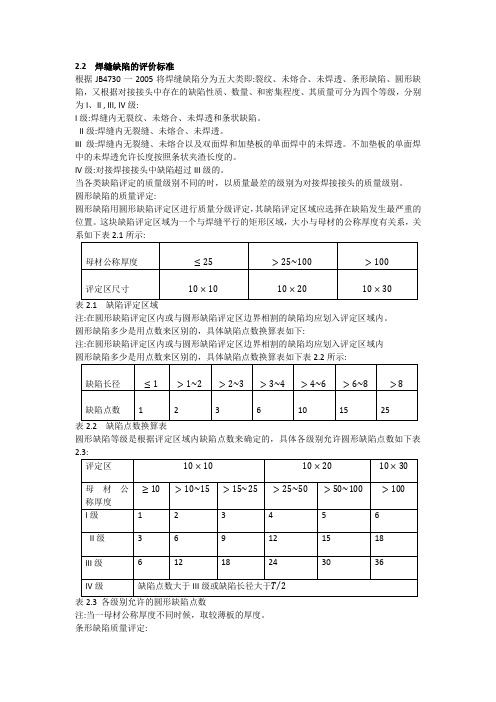
2.2 焊缝缺陷的评价标准根据JB4730一2005将焊缝缺陷分为五大类即:裂纹、未熔合、未焊透、条形缺陷、圆形缺陷,又根据对接接头中存在的缺陷性质、数量、和密集程度、其质量可分为四个等级,分别为I、II , III, IV级:I级:焊缝内无裂纹、未熔合、未焊透和条状缺陷。
II级:焊缝内无裂缝、未熔合、未焊透。
III级:焊缝内无裂缝、未熔合以及双面焊和加垫板的单面焊中的未焊透。
不加垫板的单面焊中的未焊透允许长度按照条状夹渣长度的。
IV级:对接焊接接头中缺陷超过III级的。
当各类缺陷评定的质量级别不同的时,以质量最差的级别为对接焊接接头的质量级别。
圆形缺陷的质量评定:圆形缺陷用圆形缺陷评定区进行质量分级评定,其缺陷评定区域应选择在缺陷发生最严重的位置。
这块缺陷评定区域为一个与焊缝平行的矩形区域,大小与母材的公称厚度有关系,关系如下表2.1所示:注:在圆形缺陷评定区内或与圆形缺陷评定区边界相割的缺陷均应划入评定区域内。
圆形缺陷多少是用点数来区别的,具体缺陷点数换算表如下:注:在圆形缺陷评定区内或与圆形缺陷评定区边界相割的缺陷均应划入评定区域内表2.2 缺陷点数换算表圆形缺陷等级是根据评定区域内缺陷点数来确定的,具体各级别允许圆形缺陷点数如下表注:当一母材公称厚度不同时候,取较薄板的厚度。
条形缺陷质量评定:当存在条形缺陷时,质量评定是按照条形缺陷长度来判定的。
具体各级别对焊接接头允许的条形缺陷长度如下表2.4所示:表2.4 各级别对焊接接头允许的条形缺陷长度级别单个条形缺陷最大长度一组条形缺陷最大长度I 不允许II 在长度为12T的任意选定条形缺陷评定区域内,相邻却鲜见局部超过6L的任一组条形缺陷的累计长度应不超过T,但最小可为4。
III 在长度为6T的任意选定条形缺陷评定区域内,相邻却鲜见局部超过3L的任一组条形缺陷的累计长度不超过T,但最小可为6。
IV 大于III级者注l:L为该组条形缺陷中最长缺陷木身的长度;T为母材公称厚度当母材公称厚度不同时取较薄板的厚度值。
石油天然气钢质管道无损检测_SY_T4109_2013
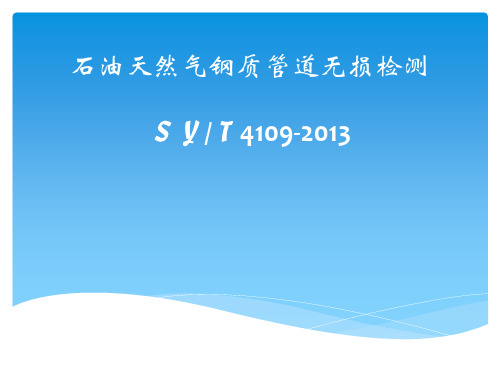
单位:mm
SGB标准试块
表K.1.4 SGB试块适用范围表
编号
SGB—1 SGB—2 SGB—3 SGB—4 SGB—5 SGB—6
弧面半径 mm 30 48 76 120 200 平面
适用管外径范围Φ mm
57~89 >89~140 >140~210 >210~360 >360~600
>600
探头与探伤仪应有良好的匹配性能,在扫查灵敏度 的条件下,探头的始脉冲宽度应小于或等于2.5mm。
检测外径为57㎜~140㎜的对接环焊缝时,探头的接 触面应与管子外表面紧密接触,其边缘与管子外表 面的间隙不应大于0.5mm。
检测准备
检测面 探头移动区应清除飞溅、锈蚀、油污及其他外部
杂质,检测表面应修磨平整光滑,其表面粗糙度不应 超过6.3μm。焊缝及检测面应经外观检查合格方可进行 检测。
小于或等于被检管道焊缝长度的8%, 且任意300㎜内不大于50㎜
Ⅳ
超过Ⅲ级者
检测报告
检05
报告编号 检测日期
规格 板厚 焊接方法 表面状态 检测标准 设备型号 探头型号
单位工程名称:
管道焊缝超声波检测报告
工程编号:
共 页第 页
施工单位
桩号/线位号
mm
材质
㎜
坡口型式
检测部位
检测时间
合格级别
检测面
频率 MHz 晶片尺寸 mm K值
缺陷判定
1 当缺欠反射波只有一个高点,且位于Ⅱ区或Ⅱ区以 上时,应将波幅降低到荧光屏满刻度的80%后,用 6dB法测其指示长度;
2 当缺欠反射波峰值起伏变化,有多个高点,且位 于Ⅱ区或Ⅱ区以上时,应使波幅降低到荧光屏满刻 度的80%,用端点6dB法测其指示长度;
长输石油天然气管道环焊缝的超声检测浅析

长输石油天然气管道环焊缝的超声检测浅析摘要:无损检测作为一项经过实践检测的技术,是保障长输管道焊接质量的重要手段,其可以有效的就管道寿命进行延长。
随着长输管道建设的不断发展,许多先进的无损检测新技术、新工艺在长输管道无损检测施工中得以推广应用,产生了重大的经济效益和社会效益,使长输管道无损检测的发展逐步进入一种良性循环轨道。
本文对当前石油天然气长输管道广泛应用的全自动超声检测系统及天然气管道的环焊缝无损探伤检测技术进行了针对性的探究,并就其检测原理做出了系统的分析论述。
关键词:石油;天然气;长输管道;环焊缝;超声检测;分析中图分类号:p618.13 文献标识码:a 文章编号:伴随国家经济水平的提升,近年来我国天然气、石油行业经历了迅速的发展,从而也加速了石油天然气长输管道的建设发展。
我国目前建设施工的长输管道工程已达到了一定规模,这类长输管道工程的运行正常与否,直接影响着我国及各地区经济的稳步发展,因此加强对其的监管,是维持其正常运行的必然措施。
一、长输管道发展综述管道运输是石油、天然气的一种大规模而且经济的输送方式,作为石油天然气行业产品的主要运输方式,其具有经济、安全和不间断、输送距离远、焊接工作量大、环境条件差、质量要求高的特点。
为了控制工程质量,确保管线的正常安全运行,需要有效的探伤手段来作为质量检测和控制的有效手段。
在长输管道检测技术的发展过程中,主要应用的探伤方法为射线探伤和超声探伤。
近些年来超声检测的发展势头迅猛,尤其在国家“西气东输”工程中发挥了重要的作用,今后超声波探伤将成为发展的必然趋势。
二、环焊缝综述长输管道建设中焊接是主要的工序,焊接的质量会直接关系到建设的速度和使用质量,长输管线环焊缝焊接的缺陷必须采用适当的措施来检测并修复从而保证管道的质量。
长输管线常用焊接方法有焊条电弧焊、自保护药芯焊丝半自动焊、熔化极气体保护焊(sri-i’半自动焊和crc全自动焊)等3 种方式。
大口径油气管道工程焊缝DR检测技术研究

大口径油气管道工程焊缝DR检测技术研究发布时间:2022-10-13T07:41:59.159Z 来源:《工程建设标准化》2022年6月11期作者:王俊李伍林[导读] DR检测技术凭借实时化、数字化、信息化、安全环保等技术优势在长输管道工程焊接检测中的应用范围愈发广泛,王俊李伍林国家管网集团建设项目管理分公司湖北武汉 430040摘要:DR检测技术凭借实时化、数字化、信息化、安全环保等技术优势在长输管道工程焊接检测中的应用范围愈发广泛,对提升焊缝检测质量和效率有积极意义,但检测工艺和成像质量还有很大提升空间。
本文简单对DR检测工艺、透照方式、系统优化、参数设置、管道焊缝检测工艺等多个方面进行了简单阐述,以期为工程检测人员提供相关参考。
关键词:大口径油气管道工程;DR检测技术;检测工艺;探测器;灵敏度;校准实时化、数字化、信息化、安全环保等是射线直接数字成像检测技术(DR)在进行管道工程焊缝检测过程中的显著优势,广泛用于长输管道工程焊接检测工作中。
在检测过程中,我们发现,DR技术虽展现出了高效率、可存储数据、绿色环保等优势,但大口径管道焊缝长焦距透照检测仍受到不小限制,检测成像质量远达不到令人满意效果。
通过优化改进工艺技术和工程,使DR检测工艺技术与大口径长输管道工程焊缝检测的适配度更高,可有效进行大口径管道焊缝中心透照及外透照检测,成像质量得到了质的提升,为油气管道工程DR检测奠定了良好的技术基础。
1 检测工艺技术一般而言,油气管道工程焊缝DR检测工艺可分为以下几个方面:检测透照方式、优化检测系统、设置透照几何参数、校准系统灵敏度、调整检测工艺参数、管道焊缝检测工艺及检测评定。
1.1 检测透照方式基于长输管道工程焊接施工特点的综合考量,为使DR检测灵敏度和效率得到显著提升,单壁单影重心透照检测法为检测管道连续焊口环焊缝实际情况的最优方法,双壁单影外透照检测法则适用于管道连头焊口环焊缝[1]。
在此,需强调的一点是若用双壁单影外透照检测法,为使检测质量得到最可靠保障,射线束中心和环焊缝中线所在垂直面夹角不可超出6°。
石油管道焊缝检测
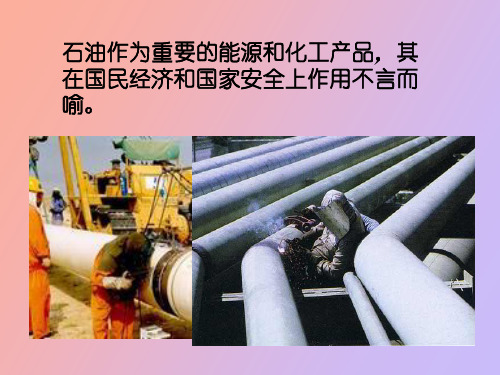
石油管道无损检测
目前石油天然气管道(含集输管道及其站场), 特别是油气长输管道正向着大口径、大壁厚、 高钢级及高压力方向发展,而与之相配套的先 进的焊接和无损检测技术及设备也在广泛采用。 作为无损检测标准,波探伤的部位采取渗 透探伤
渗透检测的工作原理是:工件表面被施涂含有荧光 染料或者着色染料的渗透剂后,在毛细作用下,经 过一定时间,渗透剂可以渗入表面开口缺陷中;去 除工作表面多余的渗透剂,经过干燥后,再在工件 表面施涂吸附介质——显像剂;同样在毛细作用下, 显像剂将吸引缺陷中的渗透剂,即渗透剂回渗到显 像中;在一定的光源下(黑光或白光),缺陷处的 渗透剂痕迹被显示(黄绿色荧光或鲜艳红色),从 而探测出缺陷的形貌及分布状态。
石油管道的焊接——钨极惰性气 体保护(氩弧焊)
氩弧焊的焊接原理 钨极氩弧焊就是把氩气做 为保护气体的焊接。借助产生在钨电极与焊体 之间的电弧,加热和熔化焊材本身(在添加填 充金属时也被熔化),而后形成焊缝金属。钨 电极,熔池,电弧以及被电弧加热的连接缝区 域,受氩气流的保护而不被大气污染。
焊缝检验方法:
射线探伤
利用射线穿透物体来发现物体内部缺陷的探伤 方法。 射线能使胶片感光或激发某些材料发出 荧光。射线在穿透物体过程中按一定的规律衰 减,利用衰减程度与射线感光或激发荧光的关 系可检查物体内部的缺陷。
超声波探伤
超声波探伤操作程序简单、快速,对裂纹、未 熔合危害性缺陷的检测灵敏度高,因此世界上 很多国家对钢结构内部质量的控制采用超声波 探伤,一般已不采用射线探伤。在西气东输中 卫黄河跨越工程中,探伤检测要求比较严格, 对钢结构桁架对接焊缝的无损检测要求采用 100%的超声波探伤,合格后再进行100%的射 线探伤
管道环焊缝射线检测工艺规程(修改版)

管道环焊缝射线检测工艺规程(修改版)管道环焊缝射线检测工艺规程ZJ/GC 01-031.范围本规程规定了射线检测人员资格、所用设备、器材、检测工艺和质量分级等。
本规程适用X射线照相方法和AB级质量要求检查壁厚为2-30mm的低碳钢和低合金钢质石油天然气长输、集输管道及其它石油管线的环向对接焊缝。
2. 规范性引用文件下列文件的条款通过本规程引用而成为本规程的条款。
凡其是注日期的引用文件,其随后所有的修改单(不包括勘误的内容)或修订不适用于本规程。
凡是不注日期的引用文件,其最新版本适用于本规程。
SY4056 石油天然气钢质管道对接焊缝射线照相及质量分级GB4792 放射线卫生防护基本标准GB561 线型象质计GB/T12605 钢管环焊缝熔化焊对接接头射线照相工艺及质量分级ZJ/GD03 现场射线检测安全规定3.检测人员3.1从事射线探伤人员必须经专业技术培训,掌握一定的探伤基础知识和操作技能及安全、卫生防护知识,并持有相关部门颁发的相应资格证书。
3.2 评片人员具备校正视力≦1.0,具能判别出400mm距离处高0.5mm、间距0.5mm的一组印刷字母。
3.3 进行射线检测时,检测人员必须严格遵守国家标准GB4792《放射线卫生防护基本标准》和ZJ/GD03 《现场射线检测安全规定》中的有关规定。
当工作环境不符合本规范工艺要求和安全规定时,检测人员有权拒绝探伤。
4. 设备和器材4.1 公司现有设备及其透照厚度范围见表1。
表14.2 在满足射线穿透力的前提下,宜使用较低管电压,曝光量不低于15mAmin,以提高射线照相灵敏度,如管径小于或等于114mm的对接环缝采用双壁双影法时,可适当提高管电压,以减少曝光时间和增大宽容度。
4.3 胶片和增感屏4.3.1 在满足灵敏度要求的情况下,X射线一般选用J2型胶片,如天津III型、上海A、乐凯等。
4.3.2 射线透照采用铅箔增感屏,不得采用荧光增感屏和荧光金属增感屏。
- 1、下载文档前请自行甄别文档内容的完整性,平台不提供额外的编辑、内容补充、找答案等附加服务。
- 2、"仅部分预览"的文档,不可在线预览部分如存在完整性等问题,可反馈申请退款(可完整预览的文档不适用该条件!)。
- 3、如文档侵犯您的权益,请联系客服反馈,我们会尽快为您处理(人工客服工作时间:9:00-18:30)。
压强度试验.3,焊缝射线照相.4, 超声波探伤.5,磁力探伤.6,渗透 探伤
石油管道无损检测
目前石油天然气管道(含集输管道及其站场),
特别是油气长输管道正向着大口径、大壁厚、 高钢级及高压力方向发展,而与之相配套的先 进的焊接和无损检测技术及设备也在广泛采用。 作为无损检测标准,必须适应和满足这种变化。
射线探伤
利用射线穿透物体来发现物体内部缺陷的探伤
方法。 射线能使胶片感光或激发某些材料发出 荧光。射线在穿透物体过程中按一定的规律衰 减,利用衰减程度与射线感光或激发荧光的关 系波探伤操作程序简单、快速,对裂纹、未
熔合危害性缺陷的检测灵敏度高,因此世界上 很多国家对钢结构内部质量的控制采用超声波 探伤,一般已不采用射线探伤。在西气东输中 卫黄河跨越工程中,探伤检测要求比较严格, 对钢结构桁架对接焊缝的无损检测要求采用 100%的超声波探伤,合格后再进行100%的射 线探伤
石油管道 焊接质量 检测
石油作为重要的能源和化工产品,其 在国民经济和国家安全上作用不言而 喻。
焊接缺陷的危害
焊接缺陷对产品构件,尤其是 压力容器和压力管道在使用中带来了的隐患和 危害是不能低估的 · 由于缺陷的存在,减少了 焊缝的承载面积,削弱了静力拉伸强度。 · 由 于缺陷形成缺口,缺口尖端会发生应力集中和 脆化现象,容易产生裂纹并扩展。 · 缺陷可能 穿透管壁,发生泄漏,影响致密性,留下隐 患。 · 对一些结构件轻者在很大程度上降低产 品的力学性能和缩短产品的使用寿命;重者, 还能产生脆断,导致危及生命财产安全的灾难 性事故,给国民经济带来巨大的损失
thanks
石油管道的焊接——钨极惰性气 体保护(氩弧焊)
氩弧焊的焊接原理
钨极氩弧焊就是把氩气做 为保护气体的焊接。借助产生在钨电极与焊体 之间的电弧,加热和熔化焊材本身(在添加填 充金属时也被熔化),而后形成焊缝金属。钨 电极,熔池,电弧以及被电弧加热的连接缝区 域,受氩气流的保护而不被大气污染。
焊缝检验方法:
渗透探伤
对于不能进行射线探伤和超声波探伤的部位采取渗 透探伤 渗透检测的工作原理是:工件表面被施涂含有荧光 染料或者着色染料的渗透剂后,在毛细作用下,经 过一定时间,渗透剂可以渗入表面开口缺陷中;去 除工作表面多余的渗透剂,经过干燥后,再在工件 表面施涂吸附介质——显像剂;同样在毛细作用下, 显像剂将吸引缺陷中的渗透剂,即渗透剂回渗到显 像中;在一定的光源下(黑光或白光),缺陷处的 渗透剂痕迹被显示(黄绿色荧光或鲜艳红色),从 而探测出缺陷的形貌及分布状态。