板材成形过程中的断裂位点
木胶合板的断裂韧性与耐冲击性探究

木胶合板的断裂韧性与耐冲击性探究木胶合板是一种常见的建筑材料,其断裂韧性与耐冲击性是评估其质量和可靠性的重要指标。
本文将探究木胶合板的断裂韧性与耐冲击性,并讨论其相关因素和测试方法。
断裂韧性是描述材料抵抗断裂的能力,与材料的承载能力密切相关。
对于木胶合板来说,其断裂韧性的好坏决定了其在各种应力条件下的稳定性和可靠性。
首先,影响木胶合板断裂韧性的一个因素是胶合剂的类型和质量。
胶合剂是将木材切片粘合在一起的关键组成部分。
优质的胶合剂能够提供较高的粘接强度和耐久性,从而增加木胶合板的断裂韧性。
常见的胶合剂包括酚醛树脂、脲醛树脂和酚醛脲醛树脂等。
选择合适的胶合剂是提高木胶合板断裂韧性的重要步骤。
其次,木胶合板的层压方式和层数也会影响其断裂韧性。
通常,木胶合板是由多层木材切片交替堆叠而成的。
更多的层数可以提高木胶合板的强度和稳定性。
同时,使用交错层压的方式可以减少木材切片之间的裂纹传播,从而提高断裂韧性。
另外,木材的类型和优化处理也会对木胶合板的断裂韧性产生影响。
某些木材具有较高的强度和韧性,例如某些硬木种类。
选择适当的木材种类可以增强木胶合板的整体性能。
同时,木材的优化处理,如干燥和防腐处理,也可以提高其断裂韧性。
除了断裂韧性,木胶合板的耐冲击性也是一个重要的指标。
耐冲击性是指材料在外力冲击下的稳定性和不易破碎的能力。
木胶合板常常用于建筑和家具制造,需要具备一定的耐冲击性,以确保其在使用中不易损坏。
与断裂韧性一样,木胶合板的耐冲击性也受到胶合剂质量、层压方式和木材类型的影响。
优质的胶合剂能够提供较高的粘接强度和耐久性,增加木胶合板的耐冲击性。
合理的层压方式和层数可以减少冲击力传递的路径,从而降低木胶合板的破碎风险。
选择合适的木材类型可以提高木胶合板的整体强度和抗冲击性。
为了评估木胶合板的断裂韧性和耐冲击性,可以采用一些标准化的测试方法。
例如,断裂韧性可以通过冲击试验和弯曲试验来评估。
冲击试验可以模拟材料遭受外力冲击的情况,通过测量冲击力和材料的变形程度来评估其断裂韧性。
中厚板分层缺陷分析解读

近来老有人打电话来,问“什么是钢板的分层(夹层)”,敬请大家看博文《中厚板质量工程师手稿》:分层是钢板(坯)断面出现局部的缝隙,使钢板断面形成局部层状,是钢材中的一种致命性缺陷,钢板不得有分层,见图1。
分层亦称夹层、离层,是钢材的内部缺陷。
钢锭内的气泡、大块的非金属夹杂物、未完全切除的残余缩孔或发生折叠,均可能引起钢材的分层,而不太合理的轧制压下规程又可能使分层加剧。
图1 钢板分层图2 厚板局部分层图3 焊接后钢板分层图4 加工后发现分层根据产生原因的不同,分层所表现的部位形态也不同,有的隐藏在钢材内部,内表面与钢材表面平行或基本平行;也有的延伸到钢材表面,又在钢材表面形成沟纹状的表面缺陷。
概括起来有2种形式:第1种为开口型分层。
这种分层缺陷在钢材的断口上宏观就可发现,一般在钢厂和制造厂里基本上能被复检出来。
第2种为封闭型分层。
这种分层缺陷在钢材的断口中看不到,在制造厂内如果不进行逐张钢板100%超声波探伤,亦难以发现,它是一种处于钢板内部的封闭型分层。
这种分层缺陷从冶炼厂带到制造厂,最后被加工制造成产品出厂。
分层缺陷的存在使分层区钢板承受载荷的有效厚度减少,降低了与分层同方向受载的承载能力。
分层缺陷的边线形状尖锐,对应力作用非常敏感,会引起严重的应力集中。
在运行过程中若有反复的加载、卸载、升温、降温,就会在应力集中区形成很大的交变应力,以致造成应力疲劳。
一、开口型分层某厂生产的板材分层是开口型分层,见图1钢板分层。
从钢板的表面就可以分辨出来。
不需要做实验,图1是某钢厂发运到中南某大型物流企业的板材照片,属于钢厂漏检产品,经销商提出质量异议后,钢厂直接报废了,经销商按废钢价销售给废钢企业使用。
1、分层形貌见图1。
资料显示与钢种关系不大。
2、分层原因分析图5是正常的铸坯凝固过程纵向断面示意图。
图5 正常情况下铸坯凝固过程纵向断面示意图图6 异常情况下铸坯凝固过程纵向断面示意图从图6可以看见,A、B两点造成铸坯搭桥,在C点形成缩孔,产生中心线裂纹或中心疏松,轧制后可能出现分层缺陷。
材料成形中的裂纹
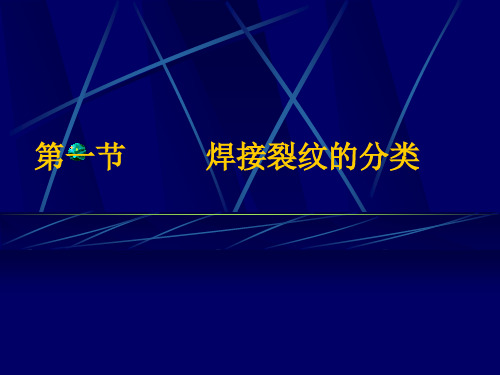
3. 延迟裂纹的开裂机理 充氢钢拉伸试验时出现代现象:
•断裂时,存在一个“上临界应
力σuc”和 “下临界应力σLc”。 •当应力在σuc和σLc之间时,就 会出现由氢引起的延迟断裂 •钢延迟裂纹只是在一定的温 度区间(-100~+100℃)发生, 温度太高则氢易逸出,温度太 低则氢的扩散受到抑制,因此 都不会产生延迟现象的断裂 •延迟裂纹的产生还与钢的组 织具有密切的关系 :低碳(铁 素体)钢和奥氏体钢都不会发 生延迟裂纹 •氢的应力诱导扩散开裂理论
五、多边化裂纹和高温失延裂纹的形成
在热影响区(包括多层焊时前一焊道的热影响区)温度低于固 相线的部位,不存在液态薄膜,也会产生晶间断裂而形成高 温裂纹。这种裂纹大多属于多边化裂纹或高温失延裂纹。 在纯金属或单相奥氏体焊缝或近缝区中,刚凝固的金属存 在很多晶格缺陷,晶格缺陷在高温条件下的扩散聚集形成低 塑性的二次边界(多边化晶界),在收缩应力的作用下由多 边化晶界产生多边化裂纹。 在其它材料的焊接热影响区中,在高温条件下由晶内晶界 的不均匀变形加上晶界的缺陷聚集而失强、失塑导致的晶界 开裂属于高温失延裂纹。
塑性值Pmin相等,此时处于临界状态。
3. 应变按曲线3变化 在固相线Ts附近,焊缝的塑性储备量 △es=Pmin-△e < 0 焊缝应变值△e已超过焊缝金属的最低塑性值 Pmin,此时必然产生裂纹。
四、 影响结晶裂纹的因素及防止措施
是否产生结晶裂纹取决于 1、焊缝金属的脆性温度区间TB 的大小;2、脆性温度区内的最小塑性Pmin;3、脆性温度区内 应变增长率,4、这些因素之间的相互关系。 因此, 从本质上看,影响结晶裂纹的因素主要可归纳为冶 金因素和力的因素 (一) 冶金因素对结晶裂纹的影响 1. 结晶温度区间的影响: 合金状 态图中结晶温度区间越大,脆性温度 区间也越大,结晶裂纹倾向越大
板材单点渐进成形破裂模拟优化与实验验证

板材单点渐进成形破裂模拟优化与实验验证耿佩;崔玉琦;党杰;马晶【摘要】针对渐进成形工艺加工半锥角较小制件侧壁厚度减薄及破裂问题,基于ABAQUS建立渐进成形有限元分析模型,并进行数值模拟与结果分析.对于板材破裂及厚度分布不均现象提出优化方案,并完成数值模拟与实验验证,结果显示,实验加工与数值模拟结果基本一致.最后总结出渐进成形中板材发生破裂的原因、本质及解决方法.%Aiming at the side wall thickness thinning and fracture issues of workpieces with small semi-cone angle during single point incremental forming process,the finite element analysis model of the process has been established on the basis of ABAQUS.The numerical simulation and analysis have been conducted.The optimized proposal for plate fracture and uneven thickness has been put forward.The numerical simulationand experimental verification have been completed.The results show the experimental results agree with the numerical simulation results.Finally,the reason,nature and solution of the plate during single point incremental forming process have been summarized.【期刊名称】《锻压装备与制造技术》【年(卷),期】2017(052)004【总页数】3页(P68-70)【关键词】渐进成形;破裂;实验验证;模拟优化【作者】耿佩;崔玉琦;党杰;马晶【作者单位】西安航空职业技术学院,陕西西安710089;重庆大学材料科学与工程学院,重庆400044;西安航空职业技术学院,陕西西安710089;西安航空职业技术学院,陕西西安710089【正文语种】中文【中图分类】TG386随着现代工业的快速发展,产品更新换代的周期逐渐缩短,对小批量金属板类零件的需求越来越高。
不锈钢薄板轧制过程中的边裂质量问题与控制(共10页)

不锈钢薄板轧制过程中的边裂质量(zhìliàng)问题与控制1.1 概述(ɡài shù)不锈钢(Stainless Steel)是不锈耐酸钢的简称,耐空气、蒸汽、水等弱腐蚀介质(jièzhì)或具有不锈性的钢种称为不锈钢。
不锈钢的耐蚀性随含碳量的增加而降低,因此,大多数不锈钢的含碳量均较低,最大不超过1.2%,有些钢的ωc(含碳量)甚至(shènzhì)低于0.03%(如00Cr12)。
不锈钢中的主要合金元素是Cr(铬),只有当Cr含量达到一定值时,钢材有耐蚀性。
因此,不锈钢一般Cr(铬)含量至少为10.5%。
不锈钢中还含有Ni、Ti、Mn、N、Nb、Mo、Si、Cu等元素。
不锈钢由于其优良的耐蚀性、耐高温性、良好的加工性能、外表美观、耐用等特点,被广泛应用于轻工、家电、建材、包装等工业领域。
由于不锈钢具有加工温度范围窄、高温变形抗力大、表面质量控制困难等生产难点,使得其生产工艺及设备选型与普通碳钢生产相比有许多不同之处。
不锈钢常按组织状态分为马氏体不锈钢、铁素体不锈钢、奥氏体不锈钢、奥氏体-铁素体(双相)不锈钢及沉淀硬化不锈钢等,另外,可按成分分为:铬不锈钢、铬镍不锈钢和铬锰氮不锈钢等。
也可以根据牌号将不锈钢分为200系列、300系列、400系列等。
每种型号的不锈钢都有各自的性能特点,在实际应用中应根据具体使用特性选择合适的不锈钢。
不锈钢薄板是一种价格不高的材料,但是客户对它的表面质量要求非常高。
不锈薄板在生产过程中不可避免会出现各种缺陷,如边裂、划伤、麻点、折痕等,给生产成本以及稳定性造成极大的影响。
1.2 不锈钢薄板轧制过程中的边裂质量问题的定义与表现在不锈钢薄板热连轧生产中,卷板的两个边部出现不同深度的裂口缺陷,俗称边裂或边裂缺陷,其表现形式如图1、图2所示。
图1 某钢铁企业不锈钢热轧薄板(báo bǎn)边裂形貌图2 不锈钢热轧(rè zhá)薄板边裂显微形貌1.3 不锈钢薄板轧制过程(guòchéng)中的边裂质量问题的危害不锈钢薄板轧制过程中,裂边深度严重(yánzhòng)的达5mm~15mm,轻的≤5mm。
金属板材成形开裂的材料影响因素___概述说明

金属板材成形开裂的材料影响因素概述说明1. 引言1.1 概述金属板材成形开裂是制造业中常见的问题,它可能导致产品无法达到设计要求,从而影响生产效率和产品质量。
因此,了解金属板材成形开裂的材料影响因素对于提高生产工艺和产品质量具有重要意义。
1.2 文章结构本文将详细探讨金属板材成形开裂的材料影响因素。
首先,在正文部分我们将介绍相关课题的背景和相关研究现状,然后详细分析不同方面对金属板材成形开裂的影响,并提供了相应的解决方法。
最后,通过总结与展望来回顾本文的主要内容并对未来研究方向进行展望。
1.3 目的本文旨在全面探讨金属板材成形开裂的材料影响因素,通过对相关问题的深入分析和研究,提供有效的解决方案以改善现有生产工艺和产品质量。
通过深入了解这些影响因素,生产企业能够在加工过程中注意到潜在问题并采取必要措施来减少开裂的发生,从而提高生产效率和产品质量。
2. 正文金属板材的成形开裂是一个重要的问题,影响着制造业的发展和产品质量。
在金属板材成形过程中,有许多因素可能导致开裂现象的出现。
本节将详细介绍这些材料影响因素。
首先,质量问题是导致金属板材成形开裂的主要因素之一。
质量问题指的是原始材料本身存在的缺陷或不均匀性。
如果金属板材在制造过程中存在脆性、夹杂物、气孔等缺陷,将增加其易开裂的风险。
此外,如果原始材料在化学成分上存在偏差或含有不合适的合金元素,也会引发开裂问题。
其次,温度对金属板材成形开裂具有重要影响。
温度过高或过低都可能导致开裂现象。
较高温度会使金属变得软化,在变形过程中容易发生撕裂和断裂;而较低温度则容易使金属产生冷脆性,增加了发生开裂的风险。
应变问题也是导致金属板材成形开裂的关键因素之一。
应变是指金属受到外力作用后的形变程度。
如果金属板材在成形过程中受到过大的应变,超过其可承受范围,就会发生裂纹和开裂现象。
此外,应变速率的快慢也对开裂产生影响,较高的应变速率容易导致开裂。
组织结构是影响金属板材成形开裂的重要因素之一。
板材成形技术
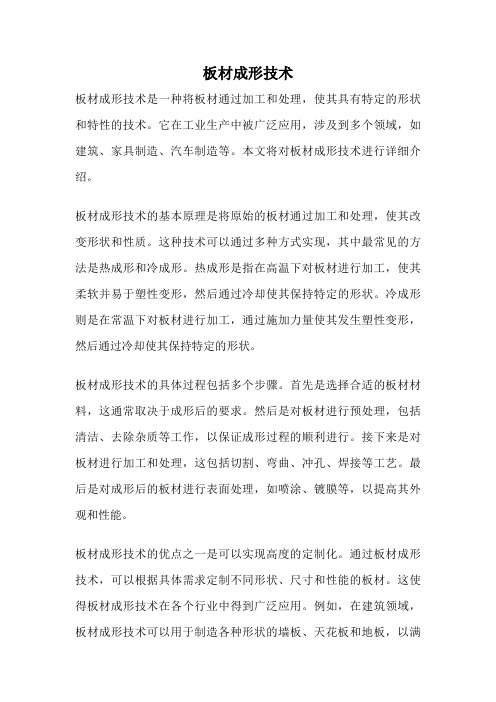
板材成形技术板材成形技术是一种将板材通过加工和处理,使其具有特定的形状和特性的技术。
它在工业生产中被广泛应用,涉及到多个领域,如建筑、家具制造、汽车制造等。
本文将对板材成形技术进行详细介绍。
板材成形技术的基本原理是将原始的板材通过加工和处理,使其改变形状和性质。
这种技术可以通过多种方式实现,其中最常见的方法是热成形和冷成形。
热成形是指在高温下对板材进行加工,使其柔软并易于塑性变形,然后通过冷却使其保持特定的形状。
冷成形则是在常温下对板材进行加工,通过施加力量使其发生塑性变形,然后通过冷却使其保持特定的形状。
板材成形技术的具体过程包括多个步骤。
首先是选择合适的板材材料,这通常取决于成形后的要求。
然后是对板材进行预处理,包括清洁、去除杂质等工作,以保证成形过程的顺利进行。
接下来是对板材进行加工和处理,这包括切割、弯曲、冲孔、焊接等工艺。
最后是对成形后的板材进行表面处理,如喷涂、镀膜等,以提高其外观和性能。
板材成形技术的优点之一是可以实现高度的定制化。
通过板材成形技术,可以根据具体需求定制不同形状、尺寸和性能的板材。
这使得板材成形技术在各个行业中得到广泛应用。
例如,在建筑领域,板材成形技术可以用于制造各种形状的墙板、天花板和地板,以满足不同建筑结构的需求。
在家具制造领域,板材成形技术可以用于制造各种形状和风格的家具,以满足消费者的个性化需求。
板材成形技术还可以提高材料的利用率和生产效率。
传统的板材加工方式往往需要大量的切割和拼接,而板材成形技术可以通过一次成形实现所需形状,减少了材料的浪费和生产过程中的工时。
同时,板材成形技术还可以实现大规模的批量生产,提高了生产效率和产品的一致性。
然而,板材成形技术也存在一些挑战和限制。
首先是对设备和工艺的要求较高。
板材成形需要使用专门的设备和工艺,这需要投入较高的成本,并且对技术人员的要求也较高。
其次,板材成形可能会引起材料的变形和缺陷。
在成形过程中,材料可能会发生变形、开裂等问题,需要采取相应的措施进行修复和调整。
板料成形过程的常见缺陷及产生原因分析

板料成形过程的常见缺陷及产生原因分析起皱和叠料产生原因由于局部压应力过大导致薄板失稳所致,正好与拉裂的产生原因相反两种应力状态容易起皱环向应力: 法向起皱与侧壁起皱失稳当冲压件的周长不断减少,此时只要板料中未受支撑区域的长度与厚度之比较大就会起皱.后果影响零件的精度和美观性影响下一道工序的正常进行起皱和叠料一般解决方法解决办法增加起皱处的法向接触力(有导致其他部位被拉裂的危险)准确预测材料的流动情况产品形状和模具形状增大压边力增加拉延筋数量或者增加高度开裂/减薄产生场合深冲工艺小半径区域,凸模圆角处(材料的抗拉弯强度)侧壁中心(材料延展性,塑性失稳)材料通过拉伸筋进入凹模,流动局部化。
分类——按程度不同分微观拉裂工件中已产生肉眼难以看清的裂纹,一部分材料已失效单纯的拉胀或单纯的弯曲引起局部拉应变过大宏观拉裂工件已出现肉眼可见的裂纹或断裂通常主要由薄板平面内的过度拉胀引起局部拉应变过大开裂/减薄应对措施解决办法改变法向接触力和切向摩擦力的分布,降低拉裂区的拉应变值调整压边力改善润滑条件增加辅助工序(改变产品圆弧或斜度,增加整形)调整拉延筋变换材料或者调整板料尺寸多步拉延回弹及扭曲产生原因二维纯弯曲回弹计算公式弹性回弹: 屈服应力,模具间隙,板料厚度塑性回弹:塑性变形区释放残余应力的卸载过程后果导致冲压件的尺寸和模具的工作表面尺寸不符解决方法调整产品设计(圆角等,产品均衡等)调整模具圆角和尺寸调整工艺方法(变压边力)模具结构方法回弹补偿表面缺陷产生原因滑移线:产品或者模具设计不合理,导致材料弯曲滑移,产生滑移线材料本身:材料单拉应力应变曲线上有屈服点伸长外部约束回弹等原因造成产品扭曲,形成凸凹不平后果(外观零件)影响产品美观表面缺陷应对措施解决办法调整冲压工艺方案,使成形过程中,表面区域的材料滑动和摩擦减小主要不平度要求部位及相关特征造成的回弹影响。
flc板材成形极限

flc板材成形极限FLC板材是一种新型的高分子复合材料,具有优异的力学性能和加工性能,被广泛应用于航空、汽车、船舶等领域。
在成形过程中,FLC板材的成形极限受到多种因素的影响,如材料性能、模具结构、加工工艺等。
下面将对FLC板材的成形极限进行详细的介绍。
一、FLC板材的力学性能FLC板材的力学性能主要包括弹性模量、屈服强度、抗拉强度和延伸率等。
这些性能指标直接影响了成形过程中的变形行为和破裂风险。
由于FLC板材具有优异的综合性能,其成形极限也相对较高。
二、成形极限的测试方法成形极限的测试方法主要包括拉伸试验、压缩试验、弯曲试验和冲压试验等。
其中,冲压试验是最常用的测试方法之一。
在冲压试验中,将试样放置在模具中,通过施加压力来使其变形,直至试样破裂。
通过测量试样的变形量和破裂位置,可以评估材料的成形极限。
三、影响成形极限的因素1.材料性能材料性能是影响FLC板材成形极限的关键因素之一。
材料的弹性模量、屈服强度、抗拉强度和延伸率等性能指标都会影响其成形极限。
一般来说,材料的弹性模量和屈服强度越高,其成形极限也越高。
但是,过高的屈服强度可能会导致材料破裂的风险增加。
因此,在选择材料时,需要综合考虑材料的各项性能指标。
2.模具结构模具结构也是影响FLC板材成形极限的重要因素之一。
模具的结构设计不合理可能会导致材料变形不均匀,从而产生破裂风险。
因此,在模具设计时,需要充分考虑材料的变形特性和模具的结构特点,确保模具结构合理、安全可靠。
3.加工工艺加工工艺也是影响FLC板材成形极限的因素之一。
加工工艺包括加热温度、加热时间、冷却速度等。
不同的加工工艺会导致材料内部结构和性能发生变化,从而影响其成形极限。
因此,在加工过程中,需要选择合适的加工工艺参数,确保材料变形均匀、无破裂现象。
四、提高成形极限的措施1.选择合适的材料选择合适的材料是提高FLC板材成形极限的关键措施之一。
在选择材料时,需要考虑材料的力学性能、加工性能和成本等因素。
钢材压延加工中的断裂与损伤机制
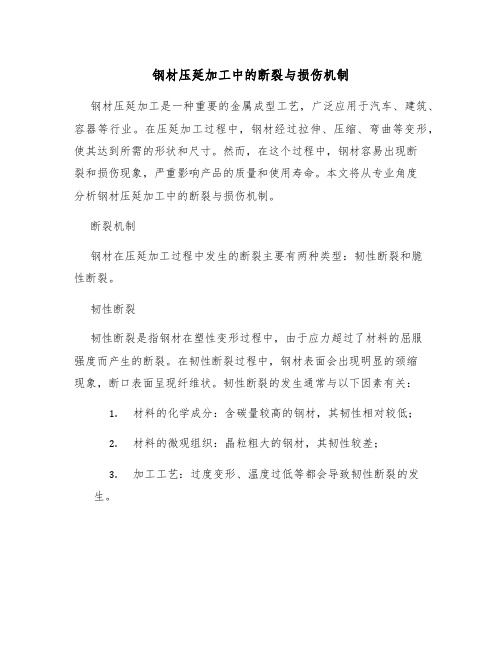
钢材压延加工中的断裂与损伤机制钢材压延加工是一种重要的金属成型工艺,广泛应用于汽车、建筑、容器等行业。
在压延加工过程中,钢材经过拉伸、压缩、弯曲等变形,使其达到所需的形状和尺寸。
然而,在这个过程中,钢材容易出现断裂和损伤现象,严重影响产品的质量和使用寿命。
本文将从专业角度分析钢材压延加工中的断裂与损伤机制。
断裂机制钢材在压延加工过程中发生的断裂主要有两种类型:韧性断裂和脆性断裂。
韧性断裂韧性断裂是指钢材在塑性变形过程中,由于应力超过了材料的屈服强度而产生的断裂。
在韧性断裂过程中,钢材表面会出现明显的颈缩现象,断口表面呈现纤维状。
韧性断裂的发生通常与以下因素有关:1.材料的化学成分:含碳量较高的钢材,其韧性相对较低;2.材料的微观组织:晶粒粗大的钢材,其韧性较差;3.加工工艺:过度变形、温度过低等都会导致韧性断裂的发生。
脆性断裂是指钢材在塑性变形很小或没有塑性变形的情况下发生的断裂。
脆性断裂的特点是断裂过程迅速,没有明显的颈缩现象,断口表面呈现解理状。
脆性断裂的发生通常与以下因素有关:1.材料的化学成分:含碳量较低的钢材,其脆性相对较高;2.材料的微观组织:晶粒细小的钢材,其脆性较差;3.加工工艺:温度过低、变形速度过快等都会导致脆性断裂的发生。
损伤机制钢材在压延加工过程中产生的损伤主要有以下几种形式:表面损伤表面损伤是指钢材表面产生的裂纹、凹坑等缺陷。
表面损伤的主要原因是:1.原材料缺陷:如夹杂物、缩孔等;2.加工过程中的摩擦:导致钢材表面产生划痕;3.温度梯度:在压延过程中,钢材内部和表面温度不一致,导致表面产生应力,从而产生损伤。
内部损伤是指钢材内部产生的裂纹、孔洞等缺陷。
内部损伤的主要原因是:1.材料的不均匀性:如成分不均匀、微观组织不均匀等;2.加工过程中的应力集中:如孔洞、夹杂物等导致的应力集中;3.温度梯度:在压延过程中,钢材内部和表面温度不一致,导致内部产生应力,从而产生损伤。
钢材在压延加工过程中容易发生断裂和损伤,影响产品的质量和使用寿命。
固态成形原理-板料成形原理

(3)剪切断面分析
由于冲裁变形的特点,使冲出的工件断面明显地分成
三个特征区,即圆角带、光亮带与断裂带。
圆角带:
光亮带:
圆角带
光亮带
断裂带:
断裂带
断裂带
圆角带
光亮带
4)凸模与凹模之间的间隙
a)间隙对冲裁件质量的影响 对切断面的要求: 对零件表面的要求: 对尺寸精度的要求: 影响冲裁件质量的因素:
2)弹—塑性弯曲和线性纯塑
性弯曲
切向应力与切向应变的函数关
系为: f ( )
弹性变形范围内(见图1-12(d)
实际应变与工程应变关系:
1 ln1 e1 2 ln1 e2
3 ln 1 e3
体积不变条件:
1 2 3 0
(1)变形板料中一点,其应变或应力状态的几 何表示方法
采用主轴表示法,可将应变分量减少为3个
主条应件,变3分个量主应1 变、中2只、有3两。个由是塑独性立变的形。体一积般不规变
2.2 弯曲
视频
图1-10 弯曲变形过程 1-凸模;2-凹模
变形特点: a)圆角附近部分: 远离圆角的直边部分: 靠近圆角处的直边: (b)在变形区内: 纵向纤维bb: 纵向纤维aa: 应变中性层(图中oo层):
(c)弯曲变形区 变薄因数: (d)变形区的横断面情况: 1)宽板(板宽B与板 厚t之比大于3)弯曲时: 2)窄板(B<3t)弯曲时:
1 板材成形的基本变形方式
1.1 板材成形中的应力应变状态及其几何表示方法 工程应变,主应变为:
e1
l1
l0 l0
e2
b1 b0 b0
e3
t1
t0 t0
在塑性变形中,一般用对数应变(实际应变):
金属板料拉伸成形过程中破裂的研究

金属板料拉伸成形过程中破裂的研究发布时间:2021-09-03T03:17:19.643Z 来源:《学习与科普》2021年8期作者:王洪芬杨佳俊赵博王浥凝[导读] 并提出相应的解决措施,以免出现板材的浪费,造成生产企业的经济损失。
吉林工程技术师范学院摘要:金属板料拉伸主要是利用冲压、拉环或金属模工艺将金属板料做成各种形状。
金属板料拉伸技术在实际生产中的应用是十分广泛的,例如汽车零件的加工,厨房用品的制造等,很多生产厂家都会应用到金属板料拉伸技术。
但是在金属板料拉伸成形的过程中会存在各种因素导致板料出现破裂、起皱等损坏现象,造成板料的浪费。
本文主要对金属板料拉伸成形过程中出现破裂的原因进行分析,给出相应的改进措施,并提出了预防板料破裂的意见。
关键词:金属板料;拉伸成形;破裂研究引言:在实际金属板料拉伸成形的操作中,与冲压成形质量相关的参数比较多,而且这些参数之间又存在很多关联,导致在操作过程中板料容易出现质量缺陷。
技术人员应该对出现的问题进行研究,找出质量缺陷的原因所在,并提出相应的解决措施,以免出现板材的浪费,造成生产企业的经济损失。
1.板料拉伸成形过程中破裂的原因1.1工程应力过大,延展性较差金属板料在拉伸操作时,不断加大工程应力,当达到板料所能承受的最大拉伸应力时,如果持续增加应力,则会导致板料发生断裂,金属板料的断裂强度与断裂时发生的应力值相对应。
板料的延展性是指板料在断裂前能够承受的塑性变形程度的量,大多数的金属在室温的条件下会存在一定的延展性,但是温度下降后,会变为脆性,出现破裂的情况。
有些材料在出现应力误差或温度骤降时,发生局部变形但是不会破裂,这种现象虽然不至于板料的浪费,但是影响其美观和使用性能,也会造成产品利润受损。
1.2模具质量问题,参数执行不准确板料拉伸时,模具的选择与使用会影响板料拉伸成形的质量。
例如模具表面太粗糙;在拉伸的过程中,板料与模具接触不良;模具的凹凸模间隙太小;拉伸筋布置不均匀等问题都容易导致板材破裂。
固态成形原理-板料成形原理

板料成形中,只要板面内两个主应力 1(代数值较大的一 个)、2就可描述(垂直于板面的主应力 3=0 )。设2 / 1=,则称为该点的应力状态参数。在简单加载情况下, 值也为常数。
变形板料中一点的应变状态和应力状态,是完全 对应的。
1
2 3
i i
1
3
2
2 3
i i
2
3
i
2 3
2 1
2 2
2 3
F1,F2 -凸、凹模对板料的 侧压力; P1,P2 -凸、凹模端面与 板料间的摩擦力,其方向与
间隙大小有关,但一般指向 模具刃口; F1、F2-凸、凹模侧面与 板料间的摩擦力。
图3-5 冲裁时作用于材料上的力 1-凹模2-材料3-凸模
视频
冲裁变形过程
冲裁变形过程分为三个阶段: 第一阶段:弹性变形阶段 弯矩M的作用,材料不仅产生 弹性压缩变形而且有穹弯,并 稍有压入凹模腔口。 第二阶段:塑性变形阶段 在塑剪变形的同时还伴有纤维 的弯曲与拉伸。 第三阶段:断裂阶段 当刃口附近应力达到破坏应力 时,先后在凹、凸模刃口侧面 产生裂纹,裂纹产生后沿最大 剪应力方向向材料内层发展, 使材料分离。
(b)应力状态 纵向: 外区受拉应力,内区受压应力。纵 向应力为绝对值最大的主应力。 厚向:
表1-1 立体塑性弯曲时变形区的应力应变状态
(3) 宽板立体纯塑性弯曲时的应力分布与应力中性层位置
1) 外区的三个主应力
(a)微分平衡方程
在板料的纵向剖面内,微体只有、r两个未知主应力的作 用,微体切向应力()对称相等,半径为r处的径向应力 为(r)。
2.2 弯曲
视频
图1-10 弯曲变形过程 1-凸模;2-凹模
变形特点: a)圆角附近部分: 远离圆角的直边部分: 靠近圆角处的直边: (b)在变形区内: 纵向纤维bb: 纵向纤维aa: 应变中性层(图中oo层):
板材成形极限
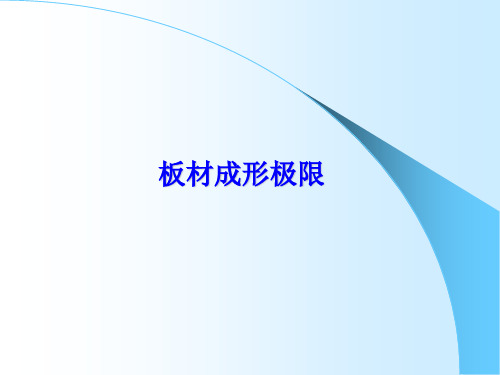
一、拉伸失稳与成形极限
拉伸失稳 是指在拉应力作用下,材料在板平面
方向内失去了塑性变形稳定性而产生缩颈,继 续往下发展,就会发生破裂。
拉伸失稳可分为分散失稳和集中失稳两种。
分散失稳
是指当缩颈刚开始时,在一个比较长的变 形区段中,由于材料性能不均匀或厚度不 均匀等,缩颈在变形区段的各部分 交替产生,此时缩颈 点不断地转移。
集中失稳
由于缩颈的变形程度很小,变形力虽略有下降, 但发展较缓慢,而且由于材料硬化的增强,变 形抗力又有所提高,最薄弱的部位逐渐显示出 来,缩颈逐步集中到某一狭窄区段,这样就形 成了集中失稳 ;
产生集中失稳时,缩颈点已不可能再转移出去, 此时金属产生了不稳定流动,由于这时的承载 面积急剧减小,变形力也就急剧下降,很快就 导致破裂。
3 取 ε2为横坐标,ε1为纵坐标,绘制成形极限曲 线
成形极限 是指材料不发生塑性失稳破坏时的极
限应变值。
成形极限有两种定义:
1 开始产生缩颈的失稳点作为成形极限; 2 将材料破裂点作为成形极限。
成形极限可以看成不是一个点,而是一 个区间。
Байду номын сангаас
二、成形极限曲线 (FLC FLD)
成形极限曲线:是对板材成形性能的一 种定量描述,同时也是对冲压工艺成败 性的一种判断曲线。
ε1和 ε2的极限值。
冲压板材表面坐标网格的制取方法较多, 常用的有照相腐蚀法、电化学浸蚀法 等.网格圆直径一般采用2—7mm
测定板平面内极限应变
1 首先选择破裂处的临界基准网格圆,及其在变 形前后的直径变化;
2 测出变形后的长轴d1和短轴d2的长度时,若基 准网格圆变形前的直径为d0,则可求得板平面 内两个主应变的极限值;1 ln(d1 / d0),2 ln(d2 / d0)
AZ31镁合金板材轧制过程边裂形成原因分析
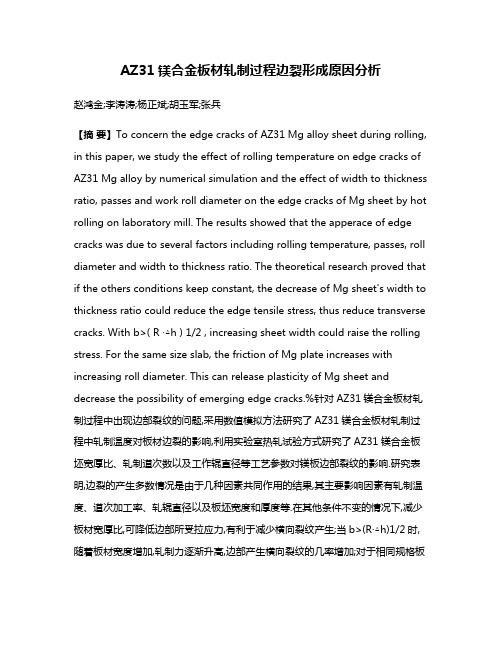
AZ31镁合金板材轧制过程边裂形成原因分析赵鸿金;李涛涛;杨正斌;胡玉军;张兵【摘要】To concern the edge cracks of AZ31 Mg alloy sheet during rolling, in this paper, we study the effect of rolling temperature on edge cracks of AZ31 Mg alloy by numerical simulation and the effect of width to thickness ratio, passes and work roll diameter on the edge cracks of Mg sheet by hot rolling on laboratory mill. The results showed that the apperace of edge cracks was due to several factors including rolling temperature, passes, roll diameter and width to thickness ratio. The theoretical research proved that if the others conditions keep constant, the decrease of Mg sheet's width to thickness ratio could reduce the edge tensile stress, thus reduce transverse cracks. With b>( R ·△h ) 1/2 , increasing sheet width could raise the rolling stress. For the same size slab, the friction of Mg plate increases with increasing roll diameter. This can release plasticity of Mg sheet and decrease the possibility of emerging edge cracks.%针对AZ31镁合金板材轧制过程中出现边部裂纹的问题,采用数值模拟方法研究了AZ31镁合金板材轧制过程中轧制温度对板材边裂的影响,利用实验室热轧试验方式研究了AZ31镁合金板坯宽厚比、轧制道次数以及工作辊直径等工艺参数对镁板边部裂纹的影响.研究表明,边裂的产生多数情况是由于几种因素共同作用的结果,其主要影响因素有轧制温度、道次加工率、轧辊直径以及板坯宽度和厚度等.在其他条件不变的情况下,减少板材宽厚比,可降低边部所受拉应力,有利于减少横向裂纹产生;当b>(R·△h)1/2时,随着板材宽度增加,轧制力逐渐升高,边部产生横向裂纹的几率增加;对于相同规格板坯,随着辊径增大,轧制过程中板坯的宽展量和所受摩擦力逐渐增加,有利于发挥板材塑性从而减小边部裂纹产生的趋势.【期刊名称】《材料科学与工艺》【年(卷),期】2015(023)006【总页数】5页(P93-97)【关键词】AZ31镁合金;边部裂纹;边部拉应力;切边厚度;宽厚比【作者】赵鸿金;李涛涛;杨正斌;胡玉军;张兵【作者单位】江西理工大学材料科学与工程学院,江西赣州341000;江西理工大学材料科学与工程学院,江西赣州341000;江西理工大学材料科学与工程学院,江西赣州341000;江西理工大学材料科学与工程学院,江西赣州341000;江西理工大学材料科学与工程学院,江西赣州341000【正文语种】中文【中图分类】TG335.5+6镁合金是实际应用中质量最轻的金属结构材料,具有密度低,比强度和比刚度高,散热快,电磁屏蔽能力强,阻尼减震性能较好,铸造、切削加工性能优良且尺寸稳定等诸多优点,在航空,3C领域等得到了日益广泛的应用[1-3].但由于常用镁合金具有密排六方晶体结构,其变形性能不及铜和铝.通常,镁板在轧制过程中容易产生边裂现象[4-6],许多学者对此已经做了深入研究.黄志权[7]等研究了轧制温度对AZ31B镁合金板材边裂和组织的影响;马立峰[8]等发现在350℃下,随着压下量的增加,AZ31B镁板边部的损伤也随之增大,边部裂纹出现的次数增多.由于镁板塑性差,轧制时产生边裂是不可避免的问题[9],因此,如何减小边部纹裂的宽度,尽可能的充分利用镁板,是工程技术人员研究的重点.本文从影响板材轧制边裂因素和切边厚度选择等多个角度重点分析了产生裂纹的原因,以及减小边部纹裂的宽度,提高成材率的方法.实验原料为某企业生产的AZ31镁合金连续铸造板坯,原始厚度15 mm,化学成分见表1.板坯在400℃下进行13 h均匀化退火,然后加热到430℃热轧,道次加工率控制在5%~20%.轧制在规格为Φ320 mm×500 mm的二辊轧机上进行,辊速为1.47 rad/s,采用SX-12-10型箱式电阻炉加热.轧制前将轧辊表面温度预热到150℃.轧制时观察板材表面变化及裂纹扩展情况,当板坯按照既定工艺轧制得到3.0、2.0、1.5、1.0 mm样品时,将边部开裂部分切掉,继续轧制,待轧至0.6 mm时观察镁板边部变化.参照相关资料,将AZ31镁合金铸轧板坯应力-应变曲线[10-12]导入Deform-3D软件的材料库中,进行轧制模拟.模拟选取AZ31镁合金板坯宽度和厚度分别为100和15 mm,单道次压下量为1.5 mm;数值模拟板材轧制温度设定为430、400、350、300℃,轧辊温度为150℃,轧机参数同上.2.1 边部裂纹宏观检验出现边部裂纹的AZ31镁合金宏观形貌如图1所示,裂边主要分布在镁合金两侧,裂纹在边部呈现不规则分布,开口较宽,边缘粗糙且开口方向基本垂直于轧制方向;部分裂纹沿轧制方向横向延伸,裂纹延伸至距边部约20 mm;板材侧面裂纹与上表面呈45°夹角.2.2 边裂的主要影响因素影响板材轧制边裂因素较多,板坯成分均匀性、轧制温度、道次加工率、流变应力、轧辊大小、温度以及板坯宽度和厚度等都与边裂有关,但边裂的产生大多数情况是由多种因素共同作用的结果.2.2.1 轧制温度对板材边裂的影响其他条件不变,板坯轧制温度分别为430、400、350和300℃,当4块镁板都出现裂纹后,比较发现,边部裂纹长度随着轧制温度的降低逐渐增长.当轧制温度分别为300、350、400、430℃时对应的边部最大损伤因子依次为0.126、0.123、0.122、0.119,说明随着轧制温度降低,边部损伤因子逐渐增大.COCKCROFT和LATHAM[13]认为对于已知材料,在一定的温度和应变速率下,当损伤因子达到材料的临界损伤因子时材料产生断裂.由此可知,当镁板轧制温度降低时,板材边部开裂趋势增大,这与实验结果相符合.有研究[7]指出,镁合金板坯因温降而引起中部与边部存在较大的温差,致使轧制过程中板坯中部与边部在纵向上存在金属流动量的差异,从而使边部受到附加拉应力的作用,当边部所受的附加拉应力超过其断裂强度极限即产生了边裂.图2为单道次轧制过程中,不同轧制温度下镁板温度场数值模拟结果.当轧制温度为300、350、400、430℃时,镁板中心与边部温度差分别为24、32、39、41℃,轧制温度越高,镁板中心与边部的温度差越大.在一定范围内,镁板塑性随温度的升高逐渐增加,虽然轧制温度低时板材中心与边部温差小,板材边部与心部金属性能相对均匀,但温度低时板材塑性差,轧制过程中很容易产生边裂现象.综上所述,轧制温度越低,板材边部与心部金属性能越均匀,但镁板塑性随温度降低逐渐下降,边部出现裂纹的几率大大增加.2.2.2 道次数对边裂的影响厚度为15 mm原始板坯在430℃下分别采用不同道次进行轧制,保持总加工率(50%)不变,其结果见图3.由图3可以看到,板坯经8道次轧制情况下,板材表面较平整,边部未见有明显裂纹,如图3(a)所示;经6道次轧制时,轧板边部出现长20 mm的断断续续小裂纹,如图3(b)所示;而经3道次轧制时镁板边部裂纹穿透心部,镁板失效,见图3(c).这表明,在总加工率不变的情况下,道次数越少,AZ31镁板边部的损伤也随之增大,同时边部裂纹增多且迅速长大.2.2.3 板坯宽厚比对轧制边裂的影响由采里柯夫公式可知,轧件宽展量与板宽之间存在反比关系,当轧制过程中其他因素不变时,随板材宽度的增加,轧件宽展量逐渐减小.当b<(R·△h)1/2时(其中b为板宽,R为轧辊半径,△h为单道次压下量),宽展量随着板坯宽度的增加逐渐增大;当b>(R·△h)1/2时,宽展量随着板坯宽度的增加逐渐减小;当b=(R·△h)1/2时,宽展量相比于其他条件时最大.同一宽度板材,宽展越大,变形越不均匀,板材越容易开裂;不同宽度板材,随其宽度增加开裂几率逐渐提高.理论上,轧件边部在宽展时,受附加的拉应力,而中间部分受附加压应力,金属的宽展越大,这种应力也愈大.通常,这些应力的存在并不能影响轧件边缘的完整性.但当边部受到的应力超过金属的抗拉强度时,就会产生横向裂纹.因此,在其他条件不变的情况下,b>1.15(R·△h)1/2,随着宽厚比增加,轧辊辊间应力增加[14],板材开裂的几率逐渐上升.2.2.4 工作辊半径对AZ31镁合金板材边裂的影响工作辊半径对板坯轧制过程有明显影响,随着工作辊半径的增加,裂纹长度减小.当工作辊半径从150 mm增加到320 mm,总变形量为86%时,裂纹长度从14.8 mm减少到9.7 mm.由采里柯夫公式可知,当b>(R·△h)1/2时,对于相同规格板坯,随着辊径增大宽展量和板材所受摩擦力逐渐增加,而板材所受摩擦力越大轧制过程中边部塑性越好.对于同一轧件,增加辊径有利于充分发挥板材的塑性,从而减小边部裂纹的长度,由此验证了大辊径轧辊可降低边部裂纹的长度.在实际生产过程中,当b>(R·△h)1/2时,使用半径较大的工作辊可以降低边裂产生的可能性.2.3 切边厚度对轧板边部裂纹扩展的影响综上分析可以看出,影响镁板轧制边裂[9,15-16]的因素较多,如何提高产品成材率,需考虑综合因素.控制裂纹源,切除边部开裂部分可有效提高成材率.经数据分析发现,在本实验条件下,原始板坯热轧至7 mm开始出现裂纹,道次总加工率为53%;继续轧制,表面裂纹不断向心部扩展,且扩展速度较快,待轧至2 mm后,边部裂纹扩展缓慢.图4为轧板切边前宽度、切边后宽度以及切边后继续轧制得到的板宽.按既定工艺获得的3 mm板坯切除边部轧裂部分,切边后样品热轧至1.7 mm出现边裂,继续轧制,原有裂纹扩展量较小,边部出现许多新的细小裂纹;对切边后的2.0、1.5、1.0 mm样品轧至0.6 mm,轧件表面光亮,边部未发现裂纹,轧制后样品宽度分别为101,103,101 mm.综上所述,切边厚度过大,轧制后边部易出现再度边裂现象,切边厚度较薄,轧制后板材宽度相对较窄,降低了成材率.本研究表明待板材轧制1.5 mm左右对其进行切边处理,既提高了成材率又可得到表面质量良好的镁板.由于实验坯料较小,研究结果可能不具备普遍性,但其意义在于验证了提高成材率的可行性,本课题将继续深入探讨影响镁板轧制边裂的主要因素. 有研究[17]指出,镁板抗拉强度随加工道次增加逐渐升高,结合本实验研究结果认为边部所受拉应力与高温抗拉强度满足图5关系曲线.按照既定工艺进行轧制,轧制初期,边部所受拉应力小于轧板高温抗拉强度,轧板表面质量较好;当轧至k 道次,由于宽厚比发生变化以及加工硬化等因素,使得轧板边部所受拉应力大于其高温抗拉强度,镁板出现裂纹,继续轧制,裂纹不断向心部扩展;待轧至(k+l)道次,将轧板边部裂开部分切除而后继续轧制,在(k+l+m)道次又发现新的裂纹.当轧件不采取切边措施,k道次以后边部所受拉应力将始终大于高温抗拉强度,边部裂纹不断向轧板心部扩展.研究认为裂纹的扩展除与上述影响因素有关,还与边部裂纹源有关.在轧制过程中由于边裂的产生,随着轧制的进行,裂纹将不断通过裂纹源扩展,直至边部应力松弛,不足以驱动裂纹向心部扩展.由此可知,在(k+l+m)道次前制品达到所需厚度,则选择(k+l)道次进行切边,在获得光洁镁板的同时又可提高镁板成材率.1)边裂的产生大多数情况是由于几种因素共同作用的结果,其主要影响因素有轧制温度、道次加工率、轧辊直径以及板坯宽度和厚度等.基体成分越不均匀,越容易在轧制过程中形成边部裂纹.2)在其他条件不变的情况下,当b>(R·△h)1/2时,随着板材宽度增加,轧制力逐渐升高,边部产生横向裂纹的几率增加.3)当b>(R·△h)1/2时,对于相同规格板坯,随着辊径增大宽展量和板材所受摩擦力逐渐增加,板材所受摩擦力越大轧制过程中边部塑性越好,因此,增加辊径有利于发挥其塑性减小边部裂纹产生的趋势.【相关文献】[1] MOEMENI S,ZAREI-HANZAKI A,ABEDI H R,et al.The application of shear compression specimen to study shear deformation behavior of AZ31 Mg alloy at hightemperaturesandquasi-staticregime[J]. Experimental Mechanics,2012,52(6):629-636.[2]王欣,杨闯,胡连喜.铸态AZ31镁合金板材等温轧制工艺及组织性能研究[J].材料科学与工艺,2011,19(02):34-37.WANG Xin,YANG Chuang,HU Lianxi.Mechanicalproperties and isothermal rolling process of AZ31 ascast Mg alloyplate[J].MaterialsScienceand Technology,2011,19(2):34-37.[3]赵鸿金,康永林,王朝辉,等.镁合金轴筒件直接挤压铸造的研究[J].特种铸造及有色合金,2005,25 (10):607-609.ZHAO Hongjin,KANG Yonglin,WANG Zhaohui,et al.Magnesiumalloybeam-barrelpartsindirect squeezing casting[J].Special Casting&Nonferrous Alloys,2005,25(10):607-609.[4] ZHANG Dingfei,DAIQingwei,FANGLin,etal. Prediction of edge cracks and plastic-damage analysis of Mg alloy sheet in rolling[J].Transactions of Nonferrous Metals Society of China,2011(05):1112-1117.[5]戴庆伟.镁合金轧制变形及边裂机制研究[D].重庆:重庆大学,2011.[6] XIE H,JIANG Z,YUEN W Y D.Analysis of microstructure effects on edge crack of thin strip during cold rolling[J].Metallurgical and Materials Transactions B,2011,42(6):1244-1252.[7]黄志权,黄庆学,马立峰,等.轧制温度对AZ31B镁合金板材边裂和组织的影响[J].热加工工艺,2014,43(17):1-4.HUANG Zhiquan,HUANG Qingxue,MA Lifeng,et al.Effects of rolling temperature on edge crack and microstructure of AZ31B magnesium alloy plate[J].Hot Working Technology,2014,43(17):1-4.[8]马立峰,庞志宁,马自勇,等.AZ31B宽幅镁合金铸轧板材热轧边裂原因分析[J].材料科学与工程学报,2014,32(05):665-670.MA Lifeng,PANG Zhining,MA Ziyong,et al.Analysis of Hot Rolled Cracks of Casting AZ31B Magnesium Alloy Plate[J].Journal of Materials Science&Engineering,2014,32(05):665-670.[9]马立峰,庞志宁,黄庆学,等.AZ31B镁合金板材轧制边裂与温度场研究[J].稀有金属材料与工程,2014,43:387-392.MA Lifeng,PANG Zhining,HUANG Qingxue,et al. Edge cracks and temperature field of AZ31B magnesium alloy sheet[J].Rare Metal Materials and Engineering,2014,43:387-392.[10]刘祖岩,刘刚,梁书锦.AZ31镁合金应力-应变关系的测定与四维描述[J].稀有金属材料与工程,2007,36(z3):304-307.LIU Zuyan,LIU Gang,LIANG Shujin.Measurement of the stress-strain relationship ofAZ31 magnesium alloy and its four-dimensional description[J].Rare Metal MaterialsandEngineering,2007,36(z3):304-307.[11]方霖.镁合金板材轧制及数值模拟研究[D].重庆:重庆大学,2010.[12]王露萌.AZ31镁合金板材轧制工艺的数值模拟研究[D].哈尔滨:哈尔滨工业大学,2008. [13]COCKCROFT M G,LATHAM D J.Ductility and the workability of metals[J].J Inst Metals,1968,1 (96):33-39.[14]田勇,胡贤磊,王昭东,等.板带材轧制辊间应力分布规律[J].东北大学学报(自然科学版),2009,30(04):539-542.TIAN Yong,HU Xianlei,WANG Zhaodong,et al. Stress distribution on rolls during plate rolling[J]. Journal of Northeastern University(Natural Science),2009,30(04):539-542.[15]WANG Lifei,HUANG Guangsheng,LI Hongcheng,et al.Influence of strain rate on microstructure and formability of AZ31B magnesium alloy sheets[J].Transactions of Nonferrous Metals Society of China,2013,23 (04):916-922.[16]CHEN Shuying,CHANG Guowei,HUANG Yuduo,et al.Effects of melt temperature on as-cast structure and mechanical properties of AZ31B magnesium alloy[J]. Transactions of Nonferrous Metals Society of China,2013,23(06):1602-1609. [17]张兵,袁守谦,张西锋,等.累积复合轧制对镁合金组织和力学性能的影响[J].中国有色金属学报,2008,18(09):1607-1612.ZANG Bing,YUAN Shouqian,ZHANG Xifeng,et al. Effect of accumulative roll bonding on microstructures and mechanical properties of MB2 magnesium[J].The Chinese Journal of Nonferrous Metals,2008,18(09):1607-1612.。
中厚板边裂的形成与控制
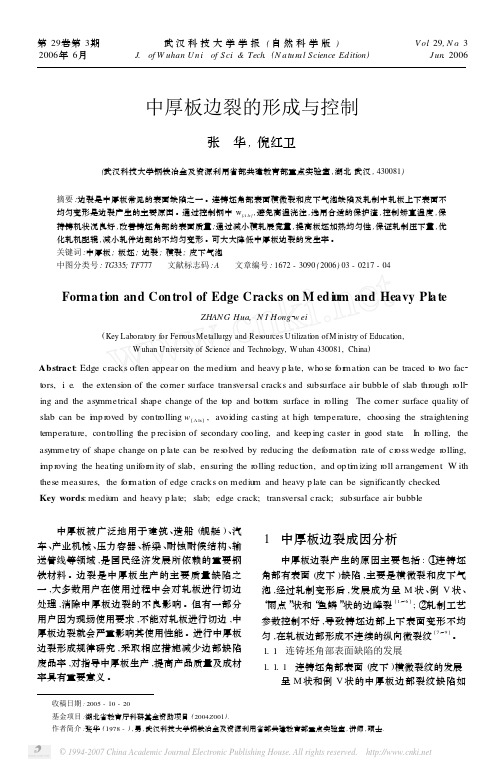
摘要 :边裂是中厚板常见的表面缺陷之一 。连铸坯角部表面横微裂和皮下气泡缺陷及轧制中轧板上下表面不 均匀变形是边裂产生的主要原因 。通过控制钢中 w[A ls] ,避免高温浇注 ,选用合适的保护渣 , 控制矫直温度 , 保 持铸机状况良好 ,改善铸坯角部的表面质量 ;通过减小横轧展宽量 ,提高板坯加热均匀性 ,保证轧制压下量 ,优 化轧机配辊 ,减小轧件边部的不均匀变形 。可大大降低中厚板边裂的发生率 。 关键词 :中厚板 ; 板坯 ; 边裂 ; 横裂 ; 皮下气泡 中图分类号 : TG335; TF777 文献标志码 : A 文章编号 : 1672 - 3090 ( 2006) 03 - 0217 - 04
呈“雨点 ”状和“鱼鳞 ”状的中厚板边部裂纹 缺陷 (见图 2 )一般气体含量较高 [ 10 ] 。钢中气体 含量高 ,与浇铸系统干燥不充分 、保护渣水分含量 较高及水口吹氩量过大等因素有关 [ 10, 11 ] 。
( a)“雨点 ”状 ( b)“鱼鳞 ”状 图 2 铸坯皮下气泡发展而成 的中厚板边部裂纹
轧件展宽后进入纵轧 ,此时轧件头尾部的不 均匀变形部位移到侧边部 ,在随后的纵轧中 ,侧边
© 1994-2007 China Academic Journal Electronic Publishing House. All rights reserved.
2006年第 3期
图 4 毛边中厚板边部基本形状
钢板的大 小 面 源 于 轧 制 时 边 部 的 不 均 匀 变 形 ,且主要发生在轧件横轧展宽过程中 。坯料在 横轧展宽时 ,轧件上面的延伸明显大于下面 ,经多 道次展宽轧制 ,轧件形成大小面双鼓 ,其中线处于 轧件厚度的 1 /3处 ,如图 5所示 。
板材成形过程中的断裂位点

板材成形过程中的断裂位点:综述M. Beatriz Silva1 •Kerim Isik2 •A. Erman Tekkaya2 •Paulo A. F. Martins1摘要:板材成形过程中的断裂通常发生韧性断裂,很少为脆性断裂,操作温度和负载率是典型的过程在两个不同的模式:(1)拉伸(2)平面剪切(分别是断裂力学中相似的模式Ⅰ和Ⅱ)。
在特殊情况下识别每个模式将发生的塑性流动和韧性损伤通过一种分析法描述断裂位点在平面应力条件下来考虑各向异性。
断裂轨迹的特点是通过断裂形成极限线和剪切断裂形成的极限线组成断裂极限图。
实验采用单点增量成形和形成双缺口试样加载拉力,扭转力和平面剪切力支持演示,可以确定1毫米厚AA1050-H111铝片的断裂位点。
韧性断裂和极限断裂研究从比较在截断圆锥形部分由单点增量成形和形成双缺口试样加载拉力得到的断裂试验值之间的关系。
关键词:板材成形;断裂;断裂成形极限图1引言成形能力是板材成形中设置在转给板坯不会被起皱,颈缩或断裂的变形量的极限。
Marciniak是第一个考虑把起皱成形极限,颈缩成形极限和断裂成形极限纳入主应变空间的研究人员(图1a).起皱成形极限位于第二象限左下侧部分,并受多种因素的影响如材料的机械性能,金属板的几何形状,工具的接触条件和应力与应变水平。
把这些因素组合成一般的标准来影响调查特定的板材成形过程是困难的。
Kim和Yang,例如,提供了已发表一份文献的全面概述,并提出了一种基于能量准则来确定起皱的各种金属板材成形过程,如圆柱形,球形,椭圆形的深冲。
颈缩成形极限的特点是一个“V”形曲线[指定为成形极限曲线(FLC)]]表明外观问题和早期断裂源于局部区域变薄可能在金属部件的变形量。
当在主应变空间实验绘制演示不同的加载路径平面应力时,局部颈缩发生的应变轨迹被称为极限成形图(FLD),它最初是根据Keelerde 拉力-拉力区域和Goodwin 延伸的拉力-压力区域提出的。
- 1、下载文档前请自行甄别文档内容的完整性,平台不提供额外的编辑、内容补充、找答案等附加服务。
- 2、"仅部分预览"的文档,不可在线预览部分如存在完整性等问题,可反馈申请退款(可完整预览的文档不适用该条件!)。
- 3、如文档侵犯您的权益,请联系客服反馈,我们会尽快为您处理(人工客服工作时间:9:00-18:30)。
自1990年代中期以来,有几种可供选择的建议关于断裂成形极限。特别是Wierzbicki等人的工作,结合三维度应力 提出了新的断裂模型洛德角参数和偏应力与相关材料的拟合程序建立在主应变空间和有效应变的断裂与应力三维空间的替代形状。
图2 断裂的成形极限线(FFL)a和平面面剪切断裂成形极限线(SFFL)b在主应变空间的示意图
这些来自分析框架的图纸是最近由Isik等人提出的,这表明金属板料成形过程中塑性流动和失败的结果之间断裂力学模式I和II之间的竞争结果,通过广泛的实验测试,确定 AA1050-H111铝片的断裂轨迹,包括在双缺口试样上的拉伸,扭转和平面剪切和在截断圆锥形部分与几何椎体实验的单点增量成形。在模型Ⅰ开裂施加拉力的双缺口试样和SPIF的截断锥部分两者的关系被利用来讨论一些理由,为什么FFLs(或SFFLs)代替FLCs应该考虑材料性能。
关键词:板材成形;断裂;断裂成形极限图
1引言
成形能力是板材成形中设置在转给板坯不会被起皱,颈缩或断裂的变形量的极限。Marciniak是第一个考虑把起皱成形极限,颈缩成形极限和断裂成形极限纳入主应变空间的研究人员(图1a).
起皱成形极限位于第二象限左下侧部分,并受多种因素的影响如材料的机械性能,金属板的几何形状,工具的接触条件和应力与应变水平。把这些因素组合成一般的标准来影响调查特定的板材成形过程是困难的。Kim和Yang,例如,提供了已发表一份文献的全面概述,并提出了一种基于能量准则来确定起皱的各种金属板材成形过程,如圆柱形,球形,椭圆形的深冲。
通过断裂成形极限由两条曲线(指定为断裂位点)相交于第二象限的右上部分和限制应变加载条件下引发裂纹。在Marciniak的最初观点,断裂由平面或平面外(厚度方向)的剪切力引起,但根据作者所知,这种假设和相应的断裂位点描绘在图1a中没有伴随任何的现象模型或实验证据。
图1 金属板材成形在主应变空间的成形极限:a Marciniak的幻想;b 成形极限曲线(FLC)和断裂成形极限线(FFL)的示意图
在塑性流动期间由于体积恒定 ,这表明FFL在主应变空间中是一条斜率为-1从走到右下降的直线(参考图2a中的恒定 的直线)。图2a也显示了2条成比例的加载路线(OC和OF),分别相当于单向拉伸和等轴双向拉伸到断裂点C和F。为了简化表示,断裂的加载路线都是线性的,没有经过方向的改变,在平面应变的条件下期望通过FLC(参考图1a).
颈缩成形极限的特点是一个“V”形曲线[指定为成形极限曲线(FLC)]]表明外观问题和早期断裂源于局部区域变薄可能在金属部件的变形量。当在主应变空间实验绘制演示不同的加载路径平面应力时,局部颈缩发生的应变轨迹被称为极限成形图(FLD),它最初是根据Keelerde拉力-拉力区域和Goodwin延伸的拉力-压力区域提出的。在拉力-压力(左)象限,平面应力塑性理论预测一对平面应变在扩散和发生局部颈缩和主要加载轴发生局部颈缩的角度。在拉力-拉力象限,理论上说颈缩扩散将会发生,但是没有连续的理论解释实验中通常由垂直的最大拉应变形成局部颈缩的发生。这导致Marciniak和Kuczynski假定存在局部变薄区域中发生颈缩。
Atkins表明最主要的断裂轨迹从左到右是和两个条件有关系的,减少厚度的临界量和由McClintock研究和提出图示一条斜率为-1的直线(指定为断裂成形极限线(FFL))的韧性断裂准则。McClintock的韧性断裂准则的工作是基于应力三轴比例rH = r(定义为平均有效应力)的比值,是已知的在基于孔隙增长模型金属成形分析中发挥重要作用。在同一年,Muscat-Fenech等人,由相关的FFL与Ⅰ型断裂韧性和得出结论,相对应FFL的断裂轨迹是由拉力引起的开裂代替由平面剪切引起的开裂(断裂力学模式III),这最初是Marciniak提出的。
板材成形过程中的断裂位点
———————————————————————————————— 作者:
———————————————————————————————— 日期:
ﻩ
板Hale Waihona Puke 成形过程中的断裂位点:综述M. BeatrizSilva1 •KerimIsik2•A.ErmanTekkaya2• Paulo A.F.Martins1
摘要:板材成形过程中的断裂通常发生韧性断裂,很少为脆性断裂,操作温度和负载率是典型的过程在两个不同的模式:(1)拉伸(2)平面剪切(分别是断裂力学中相似的模式Ⅰ和Ⅱ)。在特殊情况下识别每个模式将发生的塑性流动和韧性损伤通过一种分析法描述断裂位点在平面应力条件下来考虑各向异性。断裂轨迹的特点是通过断裂形成极限线和剪切断裂形成的极限线组成断裂极限图。实验采用单点增量成形和形成双缺口试样加载拉力,扭转力和平面剪切力支持演示,可以确定1毫米厚AA1050-H111铝片的断裂位点。韧性断裂和极限断裂研究从比较在截断圆锥形部分由单点增量成形和形成双缺口试样加载拉力得到的断裂试验值之间的关系。
颈缩和断裂的成形极限的关系示意图绘制在图1b,典型的应变加载路径经历急剧变化向平面应变变形后的FLC(参考加载路径OABC和ODE)。这是因为颈缩后,金属的厚度变小开始颈缩和平面应变在纵向上扩展。因此,FLC的可能被视为在所有平面应变加载路径发生急剧变化,因为之前所有的加载路径成为平面应变轨迹( )。
2原理
工作温度和负载率是金属板材成形的典型工序,断裂通常发生韧性断裂,而不是脆性断裂,2个不同的开口模式:(1)拉伸 和(2)平面剪切(分别为Ⅰ和Ⅱ断裂力学)。这种情况下为种模式都会发生塑性流动和显微组织韧性损伤,既在分析框架下断裂位点中平面应力的各向异性。
2.1拉伸断裂
不考虑颈缩前的初始加载历史,发生拉伸断裂大约在恒定厚度方向真实应变 对应的恒定断裂减少厚度 的百分比既 ,其中 是金属的初始厚度, 是断裂的厚度。这断裂减少的厚度 和 的关系是 。