车削螺距为6的梯形螺纹
梯形螺纹各种车削方法之比较

梯形螺纹各种车削方法之比较邓文超【摘要】梯形螺纹广泛用于传动,一般对梯形螺纹的加工精度要求较高,因为其加工精度直接影响其传动精度.在车床上加工梯形螺纹的方法较多,根据所用刀具的不同,螺纹加工精度的不同,加工批量的不同,采用不同的加工方法.【期刊名称】《农机使用与维修》【年(卷),期】2015(000)004【总页数】2页(P67-68)【关键词】低速车削梯形螺纹;高速车削梯形螺纹;旋风切削梯形螺纹【作者】邓文超【作者单位】大连市工贸职业技术学校,辽宁大连116021【正文语种】中文梯形螺纹广泛用于传动,如车床的长丝杠、中小滑板的丝杠、尾座里的丝杠。
一般对梯形螺纹的加工精度要求较高,因为其加工精度直接影响其传动精度。
在车床上加工梯形螺纹的方法较多,主要根据所用刀具的不同,螺纹加工精度的不同,加工批量的不同,采用不同的加工方法。
低速车削梯形螺纹一般采用高速钢车刀,车出的螺纹无论是螺纹牙型,还是表面粗糙度、精度都较高,但生产效率较低。
低速车削螺纹也是初学者首先学习的方法。
根据螺纹螺距的不同,还应选择不同的进刀方法。
1.1 左右切削法当螺纹螺距P≤8 mm,可采用左右切削法的进刀方式(如图1中的a示图)。
左右切削法就是在车刀每次横向进刀时,都必须把车刀向左或向右做微量的移动,即所谓的借刀。
这种切削方法避免了梯形螺纹车刀三个切削刃同时吃刀,可以防止三刃吃刀引起的振动和扎刀现象,但这种方法操作起来不方便,尤其对初学者来说不易掌握,需要反复操作练习实践。
1.2 车直槽法当梯形螺纹的螺距P≤8 mm时,还可采用车直槽法。
车直槽法只能在粗车时使用。
车削时,可先用主切削刃略小于牙槽底宽的矩形螺纹车刀采用直进法车出螺旋槽,直至车至螺纹底径(如图1中的b示图)。
由于矩形螺纹车刀两侧切削刃都带有副偏角,车削时只有主切削刃参加工作,因此,车削省力,不易出现振动和扎刀现象,而且车削时不用借刀,操作较简单易掌握。
精车时,再用梯形螺纹精车刀精车螺纹牙型两侧。
梯形螺纹标准手册
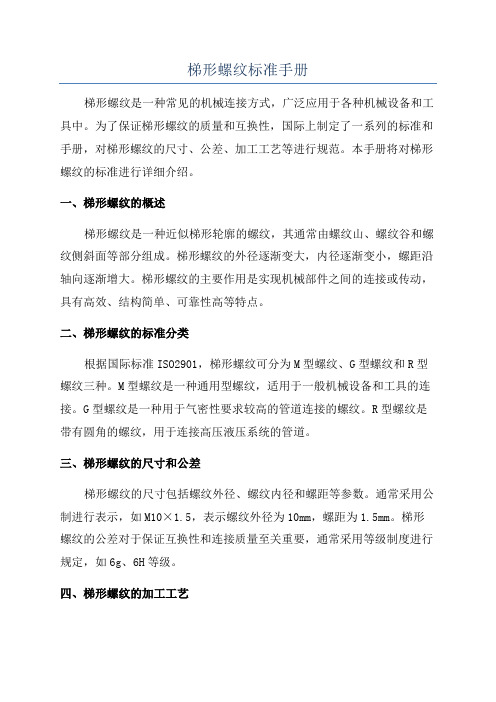
梯形螺纹标准手册梯形螺纹是一种常见的机械连接方式,广泛应用于各种机械设备和工具中。
为了保证梯形螺纹的质量和互换性,国际上制定了一系列的标准和手册,对梯形螺纹的尺寸、公差、加工工艺等进行规范。
本手册将对梯形螺纹的标准进行详细介绍。
一、梯形螺纹的概述梯形螺纹是一种近似梯形轮廓的螺纹,其通常由螺纹山、螺纹谷和螺纹侧斜面等部分组成。
梯形螺纹的外径逐渐变大,内径逐渐变小,螺距沿轴向逐渐增大。
梯形螺纹的主要作用是实现机械部件之间的连接或传动,具有高效、结构简单、可靠性高等特点。
二、梯形螺纹的标准分类根据国际标准ISO2901,梯形螺纹可分为M型螺纹、G型螺纹和R型螺纹三种。
M型螺纹是一种通用型螺纹,适用于一般机械设备和工具的连接。
G型螺纹是一种用于气密性要求较高的管道连接的螺纹。
R型螺纹是带有圆角的螺纹,用于连接高压液压系统的管道。
三、梯形螺纹的尺寸和公差梯形螺纹的尺寸包括螺纹外径、螺纹内径和螺距等参数。
通常采用公制进行表示,如M10×1.5,表示螺纹外径为10mm,螺距为1.5mm。
梯形螺纹的公差对于保证互换性和连接质量至关重要,通常采用等级制度进行规定,如6g、6H等级。
四、梯形螺纹的加工工艺梯形螺纹的加工包括车削、铣削、插削等多种工艺。
车削是最常用的加工方法,通过梯形刀具和螺纹车床进行。
铣削适用于大口径和浅螺距的梯形螺纹加工。
插削是一种高效的加工方法,适用于小口径和深螺距的梯形螺纹加工。
五、梯形螺纹的使用与注意事项使用梯形螺纹时,需要注意以下几点:1.正确选择螺纹尺寸和类型,避免过紧或过松的连接;2.保持螺纹表面的光洁度和粗糙度,以提高螺纹的连接性能;3.注意螺纹的方向和角度,确保正确的连接;4.加强连接的润滑和紧固控制,避免螺纹损坏或松动。
六、梯形螺纹的未来发展趋势随着科技的进步和工业的发展,梯形螺纹将进一步得到改进和应用。
未来的梯形螺纹可能会有更高的密封性、更高的传动效率和更优化的设计。
数控车左右交替法加工大螺距梯形螺纹

数控车左右交替法加工大螺距梯形螺纹作者:吴正平来源:《职业·中旬》2012年第05期螺纹加工目前常用的方法是以车削加工为主,但在实际生产中往往会受到条件的限制而无法正常完成加工任务。
例如在KC6132小型数控车床上用成型梯形螺纹车刀加工Tr55×10长60mm的梯形螺纹。
一、梯形螺纹相关部分尺寸计算大径d=55mm中径d2=d-0.5P=55-0.5×10=50mm小径d3=d-2h3=55-2×5.5=44mm牙高h3=0.5p+ac=0.5×10+0.5=5.5mm螺纹长度为60mm二、螺纹加工指令分析KC6132小型数控车床本身车削刚性较差,在车削螺纹时极易出现闷车现象,因此,在选择加工指令时尤为关键。
在目前的FANUC系统数控车床中,常用的螺纹编程指令有G32、G92、G76三种加工方法。
其中:G32是单一螺纹切削指令,G92螺纹切削固定循环采用直进式进刀方式,G76螺纹切削复式循环采用斜进式进刀方式,由于切削方法的不同,编程方法不同,造成切削力和加工误差也不同。
我们从操作使用上来仔细分析一下。
1.G32螺纹切削使用该指令编程要完成一次切削至少需要4个程序段,用这种方法来加工大螺距的螺纹,程序过长,难以编辑,错误多并大大减少控制系统的存储能力。
2.G92螺纹切削固定循环在切削Tr55×10梯形螺纹时,G92的进刀方式是直进式切削图1,三侧刃同时工作,切削面积大,产生的切削力大,而且排削困难,因此在切削时,不但三切削刃容易磨损,而且极易出现闷车扎刀现象。
3.G76螺纹切削复式循环该指令加工螺纹时的进刀方式是斜进式切削图2,由于粗加工时刀具斜进式切削,始终保持二面同时工作从而减少切削力,切削较流畅不易出现闷车现象。
但在精加工的时候,刀具还是和G92一样采用的直进法,这样又回到了三侧刃口同时切削的情况,从而导致闷车扎刀现象。
综合三种加工指令的特点,常规编程下一般不能在KC6132小型数控车床上完成Tr55×10长60mm的梯形螺纹。
车工理论鉴定题及答案
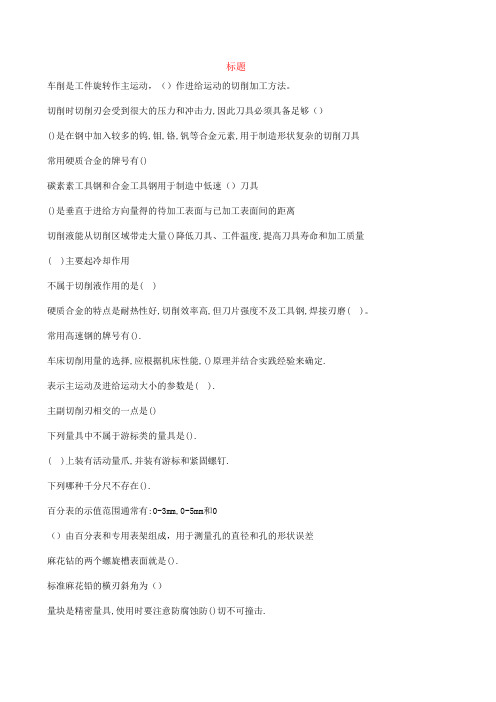
标题车削是工件旋转作主运动,()作进给运动的切削加工方法。
切削时切削刃会受到很大的压力和冲击力,因此刀具必须具备足够()()是在钢中加入较多的钨,钼,铬,钒等合金元素,用于制造形状复杂的切削刀具常用硬质合金的牌号有()碳素素工具钢和合金工具钢用于制造中低速()刀具()是垂直于进给方向量得的待加工表面与已加工表面间的距离切削液能从切削区域带走大量()降低刀具、工件温度,提高刀具寿命和加工质量( )主要起冷却作用不属于切削液作用的是( )硬质合金的特点是耐热性好,切削效率高,但刀片强度不及工具钢,焊接刃磨( )。
常用高速钢的牌号有().车床切削用量的选择,应根据机床性能,()原理并结合实践经验来确定.表示主运动及进给运动大小的参数是( ).主副切削刃相交的一点是()下列量具中不属于游标类的量具是().( )上装有活动量爪,并装有游标和紧固螺钉.下列哪种千分尺不存在().百分表的示值范围通常有:0-3mm,0-5mm和0()由百分表和专用表架组成,用于测量孔的直径和孔的形状误差麻花钻的两个螺旋槽表面就是().标准麻花铅的横刃斜角为()量块是精密量具,使用时要注意防腐蚀防()切不可撞击.万能角度尺在()范围内不装角尺和直尺测量外圆锥体的量具有检验平板两个直径相同圆柱形检验棒()尺等当检验高精度轴向尺寸时,量具应选择检验()、量块、百分表及活动表架。
选好量块组合尺寸后,将量块靠近工件放置在检验平板上,用百分表在量块上校正对准()。
相邻两牙在中径线上对应两点之间的()称为螺距。
M24×1.5-5g6g是螺纹标记,5g表示中径公差等级为(),基本偏差的位置代号为()Tr30×6表示()螺纹,旋向为()螺纹,螺距为()mm。
梯形螺纹的牙型角为()。
梯形螺纹牙形半角误差一般在()蜗杆的工件材料一般选用()。
双线螺纹的螺距主要由分线精度决定,分线误差大,车出的()误差就大。
多线螺纹工件的技术要求中,所有加工表面不准使用锉刀()等修饰。
梯形螺纹的加工及问题处理
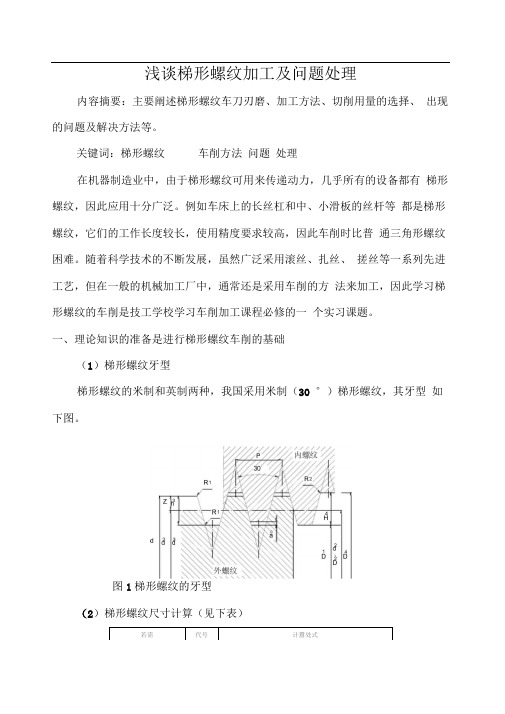
浅谈梯形螺纹加工及问题处理内容摘要:主要阐述梯形螺纹车刀刃磨、加工方法、切削用量的选择、出现的问题及解决方法等。
关键词:梯形螺纹车削方法问题处理在机器制造业中,由于梯形螺纹可用来传递动力,几乎所有的设备都有梯形螺纹,因此应用十分广泛。
例如车床上的长丝杠和中、小滑板的丝杆等都是梯形螺纹,它们的工作长度较长,使用精度要求较高,因此车削时比普通三角形螺纹困难。
随着科学技术的不断发展,虽然广泛采用滚丝、扎丝、搓丝等一系列先进工艺,但在一般的机械加工厂中,通常还是采用车削的方法来加工,因此学习梯形螺纹的车削是技工学校学习车削加工课程必修的一个实习课题。
一、理论知识的准备是进行梯形螺纹车削的基础(1)梯形螺纹牙型梯形螺纹的米制和英制两种,我国采用米制(30 °)梯形螺纹,其牙型如下图。
图1梯形螺纹的牙型(2)梯形螺纹尺寸计算(见下表)(3)梯形螺纹标记梯形螺纹标记由梯形螺纹代号,公差带代号和旋合长度代号组成。
梯形螺纹代号为Tr,单线螺纹用“公称直径x螺距”,多线螺纹用“公称直径x导程(螺距)”表示,左旋时加注LH。
公差带代号只标注中径公差带代号。
当旋长度为N组时,不标注旋合长度代号;当旋合长度为L组时,标注L,并用“-”隔开。
例如:Tr40x7-7H表示公称直径为40mm螺距为7mm中径公差为7H中等旋合长度的右旋梯形内螺纹。
又如:Tr40x14(p7) LH-7e-L表示公称直径为40mm导程为14 mm螺距为7mm中径公差为7e、长旋合长度的左旋梯形外螺纹。
再如:Tr40x7-7e-140表示公称直径为40mm螺距为7mm中径公差为7e、旋合长度为140mm的右旋梯形外螺纹。
二、梯形螺纹车刀的准备是进行梯形螺纹车削的前提梯形螺纹车刀的材料的工作一般包括车刀材料的选择和刀具刃磨等几个 方面的内容,在进行车刀准备时我们应注意以下几个方面的问题:(一)梯形螺纹车刀的材料的选择。
车刀材料的选择是否合理,对车削效率和加工质量有较大的影响。
数控车床梯形螺纹的加工方法及改进研究

科学技术创新2020.29梯形螺纹主要应用于传动机构中作为传导螺纹,梯形外螺纹与内螺纹以成对方式呈现,具有牙型深、螺距较大等特征,在采用数控车床进行加工时易产生较大的切削力与振动问题,加剧刀尖磨损程度、易引发扎刀事故,影响到工件的质量与加工生产进度。
基于此,本文拟针对梯形螺纹的常规加工工艺进行改进,并通过程序调试确保工艺具备可行性。
1梯形螺纹结构与加工方法1.1梯形螺纹。
1.1.1基本结构。
选取一对典型梯形螺纹副作为参照,在该梯形螺纹副的左上方、右上方分别设有螺杆和螺套,两类零件的外形、尺寸与螺纹精度将直接决定零件能否正常旋合。
以梯形螺纹Tr36×6为例(各结构的参数如表1所示),其牙型呈等腰梯形、牙型角为30°,相较于其他螺纹在牙根强度、对中性上占据良好性能优势,其公称直径为36mm 、螺距为6mm 。
左旋螺纹需在尺寸规格后加注“LH ”,右旋螺纹则不标出。
为保障梯形螺纹质量达标,应在加工环节确保牙型的准确度,使螺纹中径与基准轴保持同轴,以中径尺寸定心,在车削加工环节注意控制好中径的尺寸公差与两侧表面粗糙度[1]。
表1梯形螺纹的结构及计算公式1.1.2车刀材料。
在车刀材料选取上,主要选用硬质合金刀片进行梯形螺纹的高速车削,考虑到数控车床存在较严格的加工标准,因此选用材质为YT15硬质合金的可转位机夹刀片,保障刀片在硬度、耐磨性与使用寿命等方面具备良好的性能优势。
在车削加工环节,应注重选用标准刀片,在安装刀具时控制主切削刃与工件轴线保持等高且平行,利用样板进行找正与纠偏处理,使刀头角平分线与工件轴线呈垂直关系,并且将车削深度控制在与牙型高度一致的位置,确保中径尺寸达标。
1.2加工方法。
1.2.1直进法和斜进法。
直进法指车刀沿水平方向间歇进给至牙深部位,考虑到在车削梯形螺纹需利用车刀三刃同时切削,由此将产生较大的切削力、加剧刀具的磨损情况,并且无法保障及时排屑,易出现扎刀问题。
浅谈用宏程序车削大螺距梯形螺纹

浅谈用宏程序车削大螺距梯形螺纹作者:陈廷堡王新国来源:《中国科技纵横》2015年第13期【摘要】数控车床除了能方便的加工普通车床所能加工的所有型面外,还能很方便的加工各种圆弧、螺纹、非圆曲线等,尤其是普通车床上难加工的一些形状特殊复杂的表面,极大地扩展了车工的加工范围。
利用宏程序指令数控车削大螺距梯形螺纹能很好地控制零件的尺寸精度、形位精度、表面质量等要求,提高了加工效率和产品的同一性,是解决出现加工质量不稳定的有效方法之一。
【关键词】宏程序数控车削大螺距梯形螺纹刀1前言现代科学技术的迅猛发展,对机械产品提出了高精度、高复杂性、高效率的要求,大螺距梯形螺纹的加工,一直是一个比较难的机械加工问题。
但随着数控机床的不断发展,利用数控车床加工大螺距的梯形螺纹已经变得很容易。
2 影响零件加工精度的因素2.1加工工件的分析和刀具材料的选用如图1所示梯形螺纹杆,加工材料为:40Gr钢,调制处理、布氏硬度HBS241~286,中等批量加工,为保证加工效率,粗车螺纹刀的材料用YG6X,精车螺纹刀的材料选用YT15。
为了保证质量和提高加工效率,选用数控车床加工。
2.2梯形螺纹在加工中产生误差的现象加工开始,编程指令选用G76复合循环切削指令加工梯形螺纹,前部分的加工螺纹质量能保证,但到中后期开始梯形螺纹的质量出现偏差。
分析超差的现象和原因为:(1)G76指令刀具的进刀方式如图2所示,是沿单边逐渐进刀,车刀单边刀刃参与车削加工。
在梯形螺纹双边刀刃中,为解决切削过程中切削力过大导致振动甚至车刀折断的现象,采用了单边刀具进刀,这极大地改善了刀具的受力状况。
但是,刀具单边刀刃受力较大,刀具两个刀刃受力不均匀,车刀在加工中的受力方式形成悬臂扭曲梁的形态,刀尖产生扭曲倾斜,造成螺纹半角误差。
而且长期以往,不仅车刀单边磨损较大,也容易引起切削力增大,顶弯工件,产生啃刀的现象。
(2)螺纹表面粗糙。
车刀刃口单边受力,磨削不均匀,导致切削参数和工件材料不匹配,系统刚性不足导致切削过程产生振动等。
梯形螺纹基本尺寸

1基本尺寸的名称、代号及关系式列于表1中国第一重型机械集团公司标准梯形螺纹基本尺寸GB /T 5796.3-2005代替GB /T 5796.3-86本标准根据GB /T 5796.1-2005《梯形螺纹第一部分:牙型》和GB 5796.2-2005《梯形螺纹第二部分:直径与螺距系列》规定了梯形螺纹的基本尺寸。
本标准适用于一般用途的机械传动和紧固梯形螺纹联接。
名称代号关系式牙顶间隙;设计牙型上的内螺纹大径;设计牙型上的内螺纹中径;设计牙型上的内螺纹小径;设计牙型上的外螺纹大径(公称直径);设计牙型上的外螺纹中径;设计牙型上的外螺纹小径;基本牙型牙高;设计牙型上的内螺纹牙高;设计牙型上的外螺纹牙高;螺距外螺纹牙顶倒圆角圆弧半径;螺纹牙底倒角圆弧半径;a c D 4D 2D 1d d 2d 3H 1H 4h 3P R 1max R 2maxD 4=d+2a cD 1=d-2H 1=d-Pd 2=D 2=d-H 1=d-0.5P d 3=d-2h 3=d -P -2a c H 1=0.5PH 4=h 3=H 1+a c =0.5P +a c h 3=H 1+a c =P +0.5a c R 1max =0.5a c R 2max =a c表11返回总目录返回分目录后退2各直径基本尺寸列于表2表2基本尺寸mm公称直径d螺距P 中径d 2=D 2大径D 4小径第一系列d 3D 181.57.2508.3006.2006.5001.528.2508.0009.3009.5007.2006.5007.5007.000101.529.2509.00010.30010.5008.2007.5008.5008.0002310.0009.50011.50011.5008.5007.5009.0008.000122311.00010.50012.50012.5009.5008.50010.0009.0002313.00012.50014.50014.50011.50010.50012.00011.000162415.00014.00016.50016.50013.50011.50014.00012.0002417.00016.00018.50018.50015.50013.50016.00014.000202419.00018.00020.50020.50017.50015.50018.00016.00035820.50019.50018.00022.50022.50023.00018.50016.50013.00019.00017.00014.0002435822.50021.50020.00024.50024.50025.00020.50018.50015.00021.00019.00016.00035824.50023.50022.00026.50026.50027.00022.50020.50017.00023.00021.00018.0002835826.50025.50024.00028.50028.50029.00024.50022.50019.00025.00023.00020.000361028.50027.00025.00030.50031.00031.00026.50023.00019.00027.00024.00020.00032361030.50029.00027.00032.50033.00033.00028.50025.00021.00029.00026.00022.000第二系列第三系列9111418222630螺距P 中径d2=D2大径D4第一系列d3D13 6 1032.50031.00029.00034.50035.00035.00030.50027.00023.00031.00028.00024.00036361034.50033.00031.00036.50037.00037.00032.50029.00025.00033.00030.00026.000 371036.50034.50033.00038.50039.00039.00034.50030.00027.00035.00031.00028.00040371038.50036.50035.00040.50041.00041.00036.50032.00029.00037.00033.00030.000 371040.50038.50037.00042.50043.00043.00038.50034.00031.00039.00035.00032.00044371242.50040.50038.00044.50045.00045.00040.50036.00031.00041.00037.00032.000 381244.50042.00040.00046.50047.00047.00042.50037.00033.00043.00038.00034.00048381246.50044.00042.00048.50049.00049.00044.50039.00035.00045.00040.00036.000 381248.50046.00044.00050.50051.00051.00046.50041.00037.00047.00042.00038.00052381250.50048.00046.00052.50053.00053.00048.50043.00039.00049.00044.00040.000 391453.50050.50048.00055.50056.00057.00051.50045.00039.00052.00046.00041.00060391458.50055.50053.00060.50061.00062.00056.50050.00044.00057.00051.00046.0004101663.00060.00057.00065.50066.00067.00060.50054.00047.00061.00055.00049.000第二系列第三系列34384246505565螺距P 中径d2=D2大径D4第一系列d3D1704101668.00065.00062.00070.50071.00072.00065.50059.00052.00066.00060.00054.000 4101673.00070.00067.00075.50076.00077.00070.50064.00057.00071.00065.00059.000804101678.00075.00072.00080.50081.00082.00075.50069.00062.00076.00070.00064.000 4121883.00079.00076.00085.50086.00087.00080.50072.00065.00081.00073.00067.000904121888.00084.00081.00090.50091.00092.00085.50077.00070.00086.00078.00072.000 4121893.00089.00086.00095.50096.00097.00090.50082.00075.00091.00083.00077.0001004122098.00094.00090.000100.500101.000102.00095.50087.00078.00096.00088.00080.000 41220103.00099.00095.000105.000106.000107.000100.00092.00083.000101.00093.00085.000 41220108.000104.000100.000110.500111.000112.000105.50097.00088.000106.00098.00090.000 61422112.000108.000104.000116.000117.000117.000108.00099.00091.000109.000101.00093.00012061422117.000113.000109.000121.000122.000122.000113.000104.00096.000114.000106.00098.00061422122.000118.000114.000126.000127.000127.000118.000109.000101.000119.000111.000103.00061422127.000123.000119.000131.000132.000132.000123.000114.000106.000124.000116.000108.000第二系列第三系列758595105110115125130P d 2=D 2D 4第一系列d 3D 161424132.000128.000123.000136.000137.000137.000128.000119.000109.000129.000121.000111.00014061424137.000133.000128.000141.000142.000142.000133.000124.000114.000134.000126.000116.00061424142.000138.000133.000146.000147.000147.000138.000129.000119.000139.000131.000121.00061624147.000142.000138.000151.000152.000152.000143.000132.000124.000144.000134.000126.00061624152.000147.000143.000156.000157.000157.000148.000137.000129.000149.000139.000131.00016061628157.000152.000146.000161.000162.000162.000153.000142.000130.000154.000144.000132.00061628162.000157.000151.000166.000167.000167.000158.000147.000135.000159.000149.000137.00061628167.000162.000156.000171.000172.000172.000163.000152.000140.000164.000154.000142.00081628171.000167.000161.000176.000177.000177.000166.000157.000145.000167.000159.000147.00018081828176.000171.000166.000181.000182.000182.000171.000160.000150.000172.000162.000152.00081832181.000176.000169.000186.000187.000187.000176.000165.000151.000177.000167.000153.00081832186.000181.000174.000191.000192.000192.000181.000170.000156.000182.000172.000158.00081832191.000186.000179.000196.000197.000197.000186.000175.000161.000187.000177.000163.00020081832196.000191.000184.000201.000202.000202.000191.000180.000166.000192.000182.000168.000第二系列第三系列135145150155165170175185190195P d 2=D 2D 4第一系列d 3D 182036206.000200.000192.000211.000212.000212.000201.000188.000172.000202.000190.000174.00022082036216.000210.000202.000221.000222.000222.000211.000198.000182.000212.000200.000184.00082036226.000220.000212.000231.000232.000232.000221.000208.000192.000222.000210.000194.00024082236236.000229.000222.000241.000242.000242.000231.000216.000202.000232.000218.000204.000122240244.000239.000230.000251.000252.000252.000237.000226.000208.000238.000228.000210.000260122240254.000249.000240.000261.000262.000262.000247.000236.000218.000248.000238.000220.000122440264.000258.000250.000271.000272.000272.000257.000244.000228.000258.000246.000230.000280122440274.000268.000260.000281.000282.000282.000267.000254.000238.000268.000256.000240.000122444284.000278.000268.000291.000292.000292.000277.000264.000244.000278.000266.000246.000300122444294.000288.000278.000301.000302.000302.000287.000274.000254.000288.000276.000256.000第二系列第三系列210230250270290。
数车高级证5(新题库)
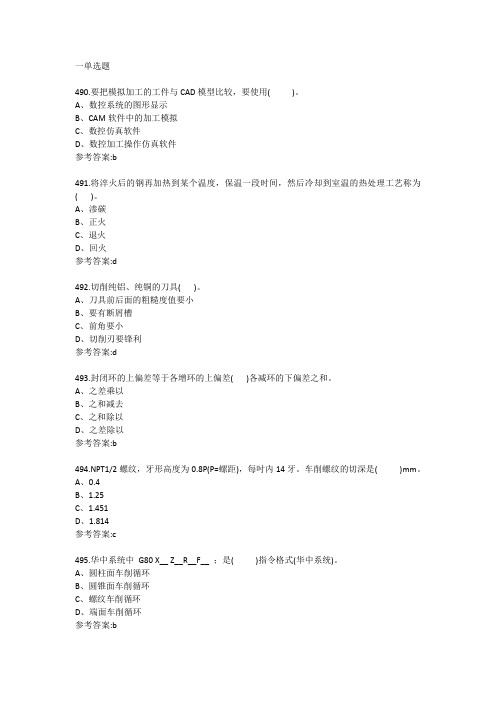
一单选题490.要把模拟加工的工件与CAD模型比较,要使用( )。
A、数控系统的图形显示B、CAM软件中的加工模拟C、数控仿真软件D、数控加工操作仿真软件参考答案:b491.将淬火后的钢再加热到某个温度,保温一段时间,然后冷却到室温的热处理工艺称为( )。
A、渗碳B、正火C、退火D、回火参考答案:d492.切削纯铝、纯铜的刀具( )。
A、刀具前后面的粗糙度值要小B、要有断屑槽C、前角要小D、切削刃要锋利参考答案:d493.封闭环的上偏差等于各增环的上偏差( )各减环的下偏差之和。
A、之差乘以B、之和减去C、之和除以D、之差除以参考答案:b494.NPT1/2螺纹,牙形高度为0.8P(P=螺距),每吋内14牙。
车削螺纹的切深是( )mm。
A、0.4B、1.25C、1.451D、1.814参考答案:c495.华中系统中G80 X__ Z__R__F__ ;是( )指令格式(华中系统)。
A、圆柱面车削循环B、圆锥面车削循环C、螺纹车削循环D、端面车削循环参考答案:b496.进行基准重合时的工序尺寸计算,应从( )道工序算起。
A、最开始第四B、任意C、中间第三D、最后一参考答案:d497.遵守法律法规要求( )。
A、积极工作B、加强劳动协作C、自觉加班D、遵守安全操作规程参考答案:d498.( )的说法属于禁语。
A、“问别人去”B、“请稍候”C、“抱歉”D、“同志”参考答案:a499.在宏程序段R1=R6/R2-R3*COS(R4);中优先进行的运算是( )(SIEMENS系统)。
A、函数:COS(R4)B、乘:R3*C、减:R2 -D、除:R6/参考答案:a500.采用轴向分线法车削M24×4/4的螺纹,第三条螺旋线的起点相对第一条螺旋线应该在轴向平移( )。
A、4B、8C、12D、16参考答案:c501.( )会形成前面磨损。
A、较低的切削速度B、较小的切削厚度C、加工脆性材料D、较高的切削速度参考答案:d502.选用压力表时,其量程应为系统最高压力的( )。
梯形螺纹加工常用的加工方法

梯形螺纹加工常用的加工方法摘要:梯形螺纹的车削在生产实践中非常重要。
本文就梯形螺纹车削过程中车刀的刃磨要求、梯形螺纹的加工方面保证粗加工余量的快速去除和精加工余量的有效预留,从而达到高效、稳定地车削梯形螺纹,一直采用传统的高速钢车刀左右车削法或斜进法加工,不但效率低、刀具易磨损,还经常由于尺寸控制不准,使精加工余量不够出现废品。
本文介绍几种实践中摸索出来的简单实用、效率高的梯形螺纹车削方法,可以提高生产效率,缩短加工时间,保证粗加工余量的快速去除和精加工余量的有效预留,从而达到高效、稳定地车削梯形螺纹。
关键词:梯形螺纹强力切削螺旋升角一、梯形螺纹的相关知识梯形螺纹是利用很广泛的传动螺纹,分为米制和英制两种。
英制梯形螺纹的牙型角为29°,我国常见的是米制梯形螺纹,其牙型角为30°。
1.梯形螺纹标记梯形螺纹的标记由螺纹代号、公差代号及旋合长度代号组成,彼此间用“―”离开。
根据国标规定,梯形螺纹代号由种类代号Tr和螺纹“公称直径×导程”表示,由于标准对内螺纹小径D1和外螺纹大径只规定了一种公差带(4H、4h),规定外螺纹小径d的公差地位永远为h的基础偏差为零。
公差等级与中径公差等级数雷同,而对内螺纹大径D4,标准只规定下偏差(即基础偏差)为零,而对上偏差不作规定,因此梯形螺纹仅标记中径公差带,并代表梯形螺纹公差(由表现公差带等级的数字及表现公差带地位的字母组成)螺纹的旋合长度分为三组,分辨称为短旋合长度(S)、中旋合长度(N)和长旋合长度(L)。
在一般情形下,中等旋合长度(N)用得较多,可以不标注。
梯形螺纹副的公差代号分辨注出内、外螺纹的公差带代号,前面是内螺纹公差带代号,后面是外螺纹公差带代号,中间用斜线分隔。
2.标记示例螺纹代号:单线螺纹:Tr40×6-6h-L;Tr:螺纹种类代号(梯形螺纹);40:公称直径;6:导程(对于单线螺纹而言,导程即为螺距);6h:内螺纹公差代号;L:旋合长度代号。
车工计算题总汇
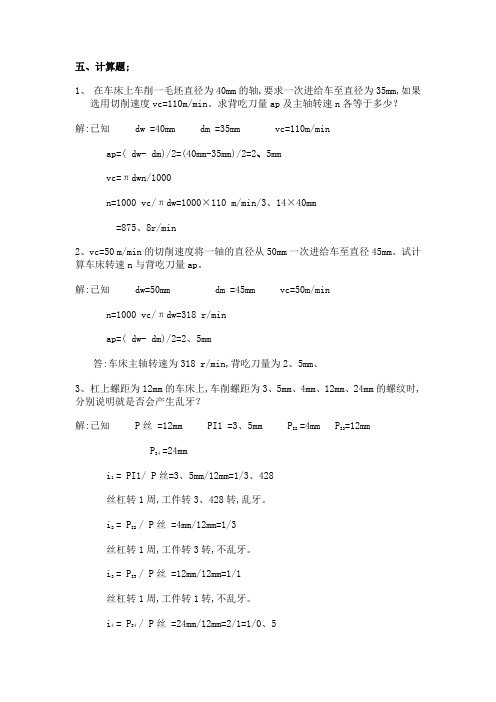
五、计算题;1、在车床上车削一毛坯直径为40mm的轴,要求一次进给车至直径为35mm,如果选用切削速度vc=110m/min。
求背吃刀量ap及主轴转速n各等于多少?解:已知 dw =40mm dm =35mm vc=110m/minap=( dw- dm)/2=(40mm-35mm)/2=2、5mmvc=πdwn/1000n=1000 vc/πdw=1000×110 m/min/3、14×40mm=875、8r/min2、vc=50 m/min的切削速度将一轴的直径从50mm一次进给车至直径45mm。
试计算车床转速n与背吃刀量ap。
解:已知 dw=50mm dm =45mm vc=50m/minn=1000 vc/πdw=318 r/minap=( dw- dm)/2=2、5mm答:车床主轴转速为318 r/min,背吃刀量为2、5mm、3、杠上螺距为12mm的车床上,车削螺距为3、5mm、4mm、12mm、24mm的螺纹时,分别说明就是否会产生乱牙?解:已知 P丝 =12mm PI1 =3、5mm PI2 =4mm PI3=12mmPI4=24mmi1= PI1/ P丝=3、5mm/12mm=1/3、428 丝杠转1周,工件转3、428转,乱牙。
i 2 = PI2/ P丝 =4mm/12mm=1/3丝杠转1周,工件转3转,不乱牙。
i 3 = PI3/ P丝 =12mm/12mm=1/1丝杠转1周,工件转1转,不乱牙。
i 4 = PI4/ P丝 =24mm/12mm=2/1=1/0、5丝杠转1周,工件转0、5转,乱牙。
答:车削螺距为3、5mm、24mm的螺纹会产生乱牙;车削螺距为4mm、12mm的螺纹不会产生乱牙。
4、用450r/min的转速车削Tr50×12内螺纹底孔时,切削速度为多少?解:已知 n=450r/min d=50mm P=12mm根据内螺纹底孔计算公式并代入各值D=d-P=50mm-12mm=38mm按切削速度公式并代入各值。
梯形螺纹标准

梯形螺纹标准梯形螺纹的标记由螺纹代号、公差代号及旋合长度代号组成,彼此间用“—”离开。
根据国标规定,梯形螺纹代号由种类代号Tr和螺纹“公称直径×导程”表示,由于标准对内螺纹小径D1和外螺纹大径只规定了一种公差带(4H、4h),规定外螺纹小径d3的公差地位永远为h的基础偏差为零。
公差等级与中径公差等级数雷同,而对内螺纹大径D4,标准只规定下偏差(即基础偏差)为零,而对上偏差不作规定,因此梯形螺纹仅标记中径公差带,并代表梯形螺纹公差(由表现公差带等级的数字及表现公差带地位的字母组成)螺纹的旋合长度分为三组,分辨称为短旋合长度(S)、中旋合长度(N)和长旋合长度(L)。
在一般情形下,中等旋合长度(N)用得较多,可以不标注。
梯形螺纹副的公差代号分别注出内、外螺纹的公差带代号,前面是内螺纹公差带代号,后面是外螺纹公差带代号,中间用斜线分隔 [2] 。
标记示例螺纹代号:单线螺纹:Tr40×6-6h-L;Tr:螺纹种类代号(梯形螺纹);40:公称直径;6:导程(对于单线螺纹而言,导程即为螺距);6h:外螺纹公差代号;L:旋合长度代号。
左旋螺纹需在尺寸规格之后加注“LH”,右旋则不注出。
例如Tr36×12(6);Tr44×16(8)LH等。
各基本尺寸名称,代号及计算公式如下:牙型角:α=30°螺距P:由螺纹标准确定,牙顶间隙ac P=1.5~5 ac=0.25;P=6~12 ac=0.5;P=14~44 ac=1外螺纹:大径d 公称直径内螺纹:大径D4=d+2ac;中径D2=d2;小径D1=d-P;牙高H4=h3;牙顶宽f=0.366P;牙槽底宽w=0.366P-0.536ac;螺纹升角ψ:tgψ=P/πd2。
梯形螺纹的检测 精简版本
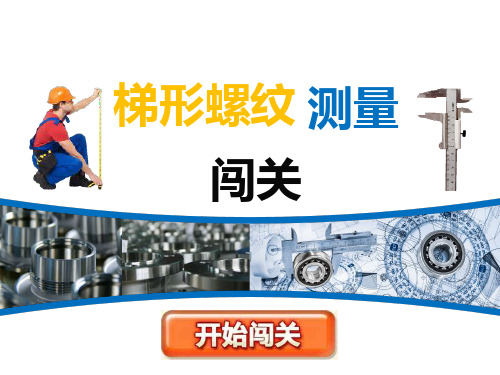
第五关---加工运用案例 单针测量法 T
r 32
x 6 - 7e
三针测量
单针测量
A=(M+d0)/2
23
第五关---加工运用案例 单针测量法 T
r 32
x 6 - 7e
A=(M+d0)/2
用单针测量Tr32×6梯形螺纹,如量得工件实际外径 d0=31.80mm,求单针测量值A。 解:A=(M+d0)/2 =(32.88+31.80)/2 =32.34mm 测量时需考虑公差
第五关---梯形螺纹中径的测量
方法:梯形螺纹主要检测螺纹中径,常用方法 为公法线千分尺及量针,采用三针法测量或者
单针测量。
16
第五关---加工运用案例 梯形螺纹中径公差范围确定
Tr 32 x 6 - 7e d2=d-0.5P =32-0.5x6 =29mm
7e是指中径公差;7 代表公差等级 , e 代表基本偏差,同时 7e 也 表示螺纹小径的公差等级。
实际加工过程中用来检查车床操作手柄是否放对位置!!!
4
第一关---加工运用案例
加工螺距为6MM的梯形螺纹,请问怎么放置手柄位置?
实际的手柄组合:M Ⅳ D 3
5
第一关闯关成功!!!!
第二关---梯形螺纹牙形角、牙高的测量
方法:通过螺纹样板直接测量,如下图所示:
实际加工过程中牙高的用途是什么?
7
梯形螺纹 测量 闯关
梯形螺纹因其螺纹的对中
性好、螺牙强度高,且具有 自锁功能而被广泛应用于各 类传动机构
第一关---梯形螺纹螺距或导程的测量
方法:用钢直尺、游标卡尺或螺纹样板,如下图所示:
用钢直尺测量
用螺纹样板规测量
车工选择题复习卷试题及答案

车工选择题复习卷试题及答案1. 最大圆锥直径与最小圆锥直径之差对圆锥长度之比叫()。
(A)圆锥角(B)圆锥半角(C)锥度(正确答案)(D)斜度答案解析:(C)锥度2. 最大圆锥直径与最小圆锥直径之间的轴向距离叫()。
(A)圆锥角(B)圆锥长度(正确答案)(C)锥度(D)斜度答案解析:(B)圆锥长度3. 锥度C=1∶5,D=32mm,L=40mm,d=()。
(A)20(B)24(正确答案)(C)26(D)28答案解析:(B)244. 圆锥半角α/2与锥度C的关系为()(A)C=2tanα/2(B)C=tanα/2(C)C=2tanα(D)C=tanα(正确答案)答案解析:(D)C=tanα5. 莫氏圆锥分成()个号码。
(A)7(正确答案)(B)6(C)5(D)4答案解析:(A)76. 米制圆锥的锥度是固定不变的,即C=()。
(A)1∶16(B)1∶20(正确答案)(C)1∶12(D)1∶24答案解析:(B)1∶207. 成批加工锥度小,锥体长的工件时,可采用()方法加工圆锥面。
(A)转动小拖板法(B)偏移尾座法(C)靠模车削法(正确答案)(D)成形刀法答案解析:(C)靠模车削法8. 车削圆锥面较短,角度较大,能加工内外圆锥面()。
(A)转动小拖板法(正确答案)(B)偏移尾座法(C)靠模车削法(D)宽刃刀车削法答案解析:(A)转动小拖板法9. ()这种方法操作简单,调整范围大,能保证一定精度。
(A)转动小拖板法(正确答案)(B)偏移尾座法(C)靠模车削法(D)宽刃刀车削法答案解析:(A)转动小拖板法10. 尾座偏移量的计算公式是()。
(A)s= [(D-d)/2L]L0(正确答案)(B)s= (D-d)/2L(C)s= (D-d)/L0(D)s= (D/2L)L0答案解析:(A)s= [(D-d)/2L]L011. 圆锥锥度C的计算公式是()。
(A)s= [(D-d)/2L]L0(B)s= (D-d)/2L(C)s= (D-d)/L0(正确答案)(D)s= (D/2L)L0答案解析:(C)s= (D-d)/L012. 当内锥孔的直径和锥度较大时,车孔后应留铰削余量()mm。
- 1、下载文档前请自行甄别文档内容的完整性,平台不提供额外的编辑、内容补充、找答案等附加服务。
- 2、"仅部分预览"的文档,不可在线预览部分如存在完整性等问题,可反馈申请退款(可完整预览的文档不适用该条件!)。
- 3、如文档侵犯您的权益,请联系客服反馈,我们会尽快为您处理(人工客服工作时间:9:00-18:30)。
车削螺距为6的梯形螺纹【摘要】梯形螺纹的车削不管是在生产实践中,还是在技能训练模块中,是非常重要的。
本文就梯形螺纹车削过程中车刀的刃磨要求、工件的装夹、车刀的装夹和机床的调整以及车削时如何利用梯形螺纹的计算公式从数学方面来保证粗加工余量的快速去除和精加工余量的有效预留,从而达到高效、稳定地车削梯形螺纹。
【关键词】左右车削法梯形螺纹螺旋升角借刀梯形螺纹是螺纹的一种,牙型为等腰梯形,牙型角为30。
内外螺纹以锥面贴紧不易松动。
我国标准规定30°梯形螺纹代号用“Tr”及公称直径×螺距表示,左旋螺纹需在尺寸规格之后加注“LH”,右旋则不注出。
例如Tr36×6;Tr44×8LH等。
梯形螺纹一般作传动用,用以传递准确的运动和动力,所以精度要求比较高,例如车床上的长丝杠和中、小滑板的丝杆等,而且其精度直接影响传动精度和被加工零件的尺寸精度。
梯形螺纹的工件不仅广泛的被用在各种机床上,其螺距和牙型都大,而且精度高,牙型两侧面表面粗糙度值较小,致使梯形螺纹车削时,吃刀深,走刀快,切削余量大,切削抗力大。
这就导致了梯形螺纹的车削加工难度较大,学生在车工技能培训中难于掌握,容易产生扎刀现象,进而使学生对此产生紧张和畏惧的心理,很多操作者都是因为无法快速的去除粗加工余量和将精加工余量留得过多或过少,导致加工速度太慢或将工件报废。
在多年的车工实习教学中,通过不断的摸索、总结、完善,对于梯形螺纹的车削也有了一定的认知,,在此谈谈左右车削法车削梯形螺纹时的几点心得体会。
一、梯形螺纹车刀的刃磨要求。
1.高速钢右旋梯形螺纹粗车刀(以车Tr42×6-7h螺纹为例)。
下图为高速钢右旋梯形螺纹粗车刀,为了便于左右切削并留有精车余量,两侧切削刃之间的夹角应小于牙型角30°,取29°左右。
刀头宽度应小于牙槽底宽W(W=1.93),刀头宽度取1.3mm左右。
为了高效去除大部分切削余量,将刀头磨成圆弧型,以增加刀头强度,并将刀头部分的应力分散。
为了使车刀两条侧切削刃锋利且受力、受热均衡,将前刀面磨成左高右低、前翘的形状,使纵向前角γp=10°-15°、γ右=(3°-5°)+a°、γ左=(3°-5°)-a°、a为螺旋升角;如果是左旋螺纹,则γ右、γ左、相反。
高速钢右旋梯形螺纹粗车刀2.高速钢右旋梯形螺纹精车刀(以Tr42×6螺纹的车刀为例)。
下图为高速钢右旋梯形螺纹精车刀。
为保证牙型角正确,两侧切削刃之间的夹角略大于牙型角,刀头宽度仍可略小于牙槽底宽,略比粗车时宽一些,取1.5mm,以利于螺纹底面和两侧面的加工,并保证两侧面的表面表糙度达到要求,后角均可略取大些,αo前=5°、γ右>(3°-5°)-a°、γ左>(3°-5°)+a°,a为螺旋升角;如是左旋螺纹,则γ右与γ左刚好相反。
高速钢右旋梯形螺纹精车刀二、工件的装夹。
为了提高效率,大余量地车削梯形螺纹,在满足工件技术要求前提下,一般粗、精车都用一夹一顶装夹,个别对中径跳动要求高,不适合一夹一顶加工的工件,也应粗车选择一夹一顶装夹,精车时用两顶尖装夹来保证工件的技术要求。
装夹工件的时候卡盘一定要夹紧,防止产生切削力大于工件夹紧力的情况。
三、车刀的装夹。
1.车刀主切削刃必须与工件轴线等高(用弹性刀杆应高于轴线约0.2mm)同时应和工件轴线平行。
2.刀头的角平分线要垂直与工件的轴线。
用样板找正装夹,以免产生螺纹半角误差。
四、车床的选择和调整。
1.挑选精度较高,磨损较少的机床2.正确调整机床各处间隙,对床鞍、中小滑板的配合部分进行检查和调整、注意控制机床主轴的轴向窜动、径向圆跳动以及丝杠轴向窜动。
3.选用磨损较少的交换齿轮。
五、梯形螺纹的车削方法及测量。
学生练习时,先练习车P=2.5的三角螺纹,采用的是直进法车削,最后练习车P=6的梯形螺纹,采用的是左右车削法,方便学生进行比较。
现以车Tr42×6-7h 螺纹来介绍我是如何指导学生用左右车削法车削梯形螺纹的。
如下图:1.将螺纹大径(略小0.15左右)和两端倒角(2X15°)车好,然后将梯形螺纹粗车刀对到工件外圆上,将中滑板调至零位,同时小滑板朝前进方向消除间隙后对零。
此举目的是方便学生记住刻度,不易出错。
2.以直进法车螺纹。
由于粗车刀刃磨得锋利又耐用,可加大切削深度。
如Tr42×6的螺纹,螺纹牙型高度h3=0.5P+ac ,Ac为间隙量取0.5mm,牙高h3=0.5P+ac=0.5x6+0.5=3.5mm;直径方向为7mm,可第一刀进1.5mm,第二刀1mm,第三刀0.5mm,共计3mm(此时因刀具三刃受力,难以继续采用大切削深度的直进法车削,如继续切削则会产生卡刀现象,开始使用左右借刀法)。
如图所示:3.用游标卡尺测量此时牙顶宽,将测量牙顶宽减去理论牙顶宽(W=2.196≈2.2),再减去所留两侧精车余量(0.2~0.4左右,精车余量以两侧面表面粗糙情况而定,表面光洁时取0.2mm,表面粗糙时取0.4mm),这就是借刀的余量,将这个余量除以2,就是每侧借刀的量。
例如:我现测得牙顶宽为4.4mm,则我应向左边借刀的量是[(4.4-2.2)-0.3]/2=0.95mm。
当我仍以进刀深度为3mm,向左借刀量为0.95mm车时,梯形螺纹刀只有左侧刃在切削,这个时候只有2条切削刃在受力,切削力不会太大。
车完左边借刀的一刀,将小滑板先退后进(消除空行程)对应地在零线右边借刀0.95mm车一刀(也可分两至三刀将借刀量0.95车完),如下图a。
车完后,将小滑板再次对零。
此时刀具就落在车宽了的槽中间,如下图b。
图a图b4.再以直进法车螺纹,由于刀头宽度1.5<W(W=1.93),故可再如前2步分三次进刀将螺纹再车深3mm,如下图C, 然后又先向左借刀。
此时应目测确定借刀量,并通过在螺纹头部试切,看切屑宽度(如车到前一次的侧面,则切屑会变宽),最后确定借刀量,将左侧车好后,以相同借刀量再车右侧面,车到前一次的侧面,左右两边车完后,再次将小滑板对零,如下图d。
图 c图d5.最后又以直进法车螺纹。
第一刀进刀深度为0.5mm,第二刀0.3mm,第三刀0.2mm,第四刀0.1mm。
经过2、3、4、5步的车削螺纹共车深7mm,然后如4步将左侧面借刀至整个侧面车起,同样再将右侧面减刀车起,至此粗车完成。
6.换上螺纹精车刀,将它在螺纹大径上对刀,并将中滑板刻度盘对零。
由于精车刀刀头宽度仍小于牙槽底宽,故精车刀可落到槽底,目测使精车刀处于槽中间,看此时刻度盘值,然后以每次进刀0.1~0.2mm,将总进刀深度车至7~7.4mm(因应车深度为牙高3.5mm,大径小径偏差0~0.419mm,二者之和7+(0~0.419)=(7-7.4)mm),而粗车时已车切削深度7.0mm,,故实际只需进刀0.1~0.2mm。
当牙底车起车平后,又向左侧赶刀,每次0.1~0.05mm,至将左侧面全部车起、车平,然后以低速进0.02mm或走空刀(中、小滑板均不进刀),将左侧车至光洁度达到要求,再将螺纹刀直接退至右边车右侧面,每车一刀就用游标卡尺量一量牙顶宽,当牙顶宽接近2.2mm时,再用三针测量其M值。
当M值合格时,螺纹中径即合格。
三针测量法是测量外螺纹中经的一种比较精密的方法。
适用于测量一些精度要求较高、螺纹升角小于4º的螺纹工件。
测量时把三根直径相等的量针放在螺纹相对应的螺旋槽中,用千分尺量出两边量针顶点之间的距离M,如下图。
例:车Tr42×6-7h梯形螺纹,用三针测量螺纹中径,求量针直径和千分尺读数值M?量针直径dD=0.518P≈3.1mm千分尺读数值M=d2+4.864dD-1.866P=39+4.864×3.1-1.866×6=39+15.08-11.20=42.88mm测量时应考虑公差,则M=42.88-0.118 -0.453为合格。
M值简化读数为42+0.46 +0.43三针测量法采用的量针一般是专门制造的,在实际应用中,有时也用优质钢丝或新钻头的柄部来代替,但与计算出的量针直径尺寸往往不相符合,这就需要认真选择。
要求所代用的钢丝或钻柄直径尺寸,最大不能在放入螺旋槽时被顶在螺纹牙尖上,最小不能放入螺旋槽时和牙底相碰,可根据下表所示的范围内进行选用。
7.至此梯形螺纹加工完毕。
在整个加工过程中,粗加工大约用16~24刀,约需时间15分钟左右,精加工8~12刀左右。
同样约需15分钟(包含测量的时间),而且由于每次车削参加切削的刃不太长,所受的切削力不太大,故切削过程平稳,不会出现扎刀的现象,更不会打刀。
从而保证车梯形螺纹的快速和稳定。
总之,在实践教学中,“左右切削法”这种易懂、易掌握的车削梯形螺纹方法,得到了充分地肯定和好评。
教师能够较形象、较直观地把车削方法讲解和传授给学生,学生普遍也能够较快、较容易地理解和掌握这种车削方法,大大降低了梯形螺纹车削这一课题的教学难度和强度。
但在生产实践中梯形螺纹的车削是相当复杂的,车削过程中不可仅仅应用一种方法去车削,而应融会贯通,因此学生只有掌握和熟练了各种车削方法,才能在车削过程中灵活运用,高效率、高精度、高品质地完成梯形螺纹车削。
参考文献1 车工工艺学('96新版)中国社会劳动保障出版社,1997.52 机械切削工技能机械工业出版社,2004.73 机械工人切削手册(第五版)中国社会劳动保障出版社2003.3。