塑性成形技术的现状及发展趋势
装备制造业之塑性成形技术

装备制造业之塑性成形技术装备制造业是国民经济中的重要支柱产业之一,其发展与创新对于国家经济以及军事安全具有重要的战略意义。
而塑性成形技术是装备制造行业中的一项重要成果,在提高装备品质、降低生产成本以及提升市场竞争力等方面发挥着至关重要的作用。
塑性成形技术是指将金属等材料通过加热并施加一定的压力使其发生塑性变形,从而获得所需要的产品形状的一种制造技术。
塑性成形技术包括很多种形式,比如挤压、拉伸、冲压、滚压、压铸等,不同的成形方式可以适用于不同材料的制造,同时也会对产品的性能产生不同的影响。
塑性成形技术的应用范围非常广泛,可以在航空、汽车、机械、能源、建筑等多个领域中得到应用。
比如在航空航天领域中,许多零部件使用的铝合金、钛合金等材料就是通过塑性成形技术加工而成。
在汽车制造中,钣金冲压技术、汽车车轮轧辊技术等都是塑性成形技术的应用,让汽车生产更快、更便宜、更环保。
在机械制造领域中,CNC数控机床等设备也是利用塑性成形技术来制造的。
塑性成形技术的好处是显而易见的。
首先,采用塑性成形技术可以大幅度降低材料的浪费,保证物料的利用率。
其次,成形的过程中可以大大提高材料的强度、硬度和韧性等性能,使其具有更优异的物理性能。
最后,采用塑性成形技术可以大幅度节省制造成本,提高制造效率,节约人力资源。
然而,塑性成形技术也有其自身的难点和挑战。
首先,在材料的选择、加工方法的确定、生产设备的运行等方面都需要高度的技巧和经验。
其次,在实际应用中还需要充分考虑诸如材料的质量稳定性、生产成本等问题。
因此,塑性成形技术的应用需要专业技术人员在其运用前对其加工原理、机械构造和效果等进行充分的研究和了解。
总之,塑性成形技术在装备制造行业中占据着重要的位置。
它不仅可以使装备产品的品质得到大幅提升,而且还能够提高生产效率、降低生产成本、实现资源的实际应用。
在这个全球化的时代,如何不断创新、精益求精,才能在激烈的国际市场中占据一席之地。
塑性成形技术不仅是一种装备制造技术,更是一种精神和实践。
微塑性成形技术的现状及研究进展

微塑性成形技术的现状及研究进展摘要:目前我国伴随科技的发展对微小型化的需求越来越大,这也促进了时代的进步和人民生活水平的提高。
微塑性成形技术占有很重要的地位。
文章主要介绍了微塑性成形技术的背景和意义,并综述了微塑性成形技术的尺度效应和摩擦尺度效应现象,阐明了其技术的研究领域。
关键词:微塑性成形;尺度效应;摩擦随着科技的飞速发展及人们对多功能电子产品小型化的需求,微细加工的技术迅速成为当前的研究和应用热点。
微塑性成形(Micro-forming)技术[1],是指利用材料的塑性变形来生产至少在两维方向上尺寸处于几mm以下零件的技术。
这一技术继承了传统塑性加工技术的高生产率、最小或零材料损失、产品力学性能优秀和误差小的特点,可批量成形各种复杂形状的微小零件。
微制造技术的发展来源于产品微细化的要求,越来越多的用户希望随身用的多功能电子器件体积小型化、功能集成化[2],而在医疗器械、传感器及电子器械等医疗、工业控制等行业也需要制造出更微小的零件[3],以期得到更高的功能要求。
因此,微塑性成形技术有很强的在短时间内得到快速的发展。
一、微塑性成形的尺度效应在成形工艺中,描述材料变形行为的主要参数是流动应力和变形曲线(即应力应变变化关系),因为这些参数直接影响到成形力、工具载荷、局部变形行为以及充模情况等。
根据相似原理将标准样件等比缩小设计,进行的拉伸和镦粗试验表明:由于尺度效应的影响,随着样件尺度的减小,流动应力也呈现减小的趋势。
晶粒尺度对材料应力应变关系已经在宏观成形工艺中得到充分的研究,为了研究微细成形中特有的尺度效应现象,在这些试验中,不同尺度样件的晶粒尺度保持相同的,所以可以肯定实验中观测到的流动应力减小现象与晶粒尺度的变化无关,主要是由尺度微小化引起的。
对于流动应力减小的现象,通常可以用表面层模型解释对于流动应力减小的现象,通常可以用表面层模型解释,如图1所示。
表面层模型认为在小尺度的情况下,材料变形已经不符合各向同性连续体的变化规律,在小尺度情况下(根据晶粒尺度与制件局部变形尺度的比率判断),表面晶粒增多,表面层变厚。
非合金钢板的超塑性成形技术研究及其应用潜力

非合金钢板的超塑性成形技术研究及其应用潜力超塑性成形是一种通过在高温条件下对材料应力施加的加工方法,可以使非合金钢板也能够实现高度塑性变形。
本文将探讨非合金钢板超塑性成形技术的研究现状以及其在实际应用中的潜力。
首先,我们将介绍非合金钢板超塑性成形技术的研究现状。
非合金钢板由于其较低的碳含量以及少量的合金元素,通常具有较低的塑性,限制了其在成形过程中的应用。
然而,通过对非合金钢板进行超塑性成形的研究,可以改善其塑性特性,使其具备更广阔的应用前景。
目前,非合金钢板超塑性成形技术的研究主要集中在以下几个方面。
首先,研究人员通过调整非合金钢板的化学成分,改变晶体结构,提高材料的塑性。
其次,采用热处理方法,通过控制加热温度和时间,使非合金钢板获得更高的塑性。
此外,研究人员还探索了不同的成形方法,如等温拉伸、等温压缩、等温缩径等,以实现非合金钢板的超塑性变形。
在实际应用中,非合金钢板超塑性成形技术具有广阔的潜力。
首先,超塑性成形可以极大地提高材料的成形能力,使非合金钢板能够制造出更复杂的形状和结构。
这对于一些应用场景,如汽车、航空航天以及能源领域的零部件制造具有重要意义。
其次,超塑性成形技术可以减少材料在成形过程中的应力和变形,降低材料的变形硬化率,从而改善零部件的成形质量和机械性能。
此外,超塑性成形还可以降低材料的成形温度,减少能源消耗,降低生产成本。
然而,在实际应用中,非合金钢板超塑性成形技术还面临一些挑战。
首先,超塑性成形需要非常严格的加工条件和设备配置,包括高温环境、复杂的工艺参数控制等。
这增加了生产成本和困难。
其次,非合金钢板超塑性成形技术的研究还相对较少,需要进一步的实验研究和理论探索。
此外,超塑性成形后的材料往往会出现晶界滑移和晶界扩散现象,可能会影响材料的综合性能和寿命。
为了克服这些挑战,进一步开展非合金钢板超塑性成形技术的研究是非常必要的。
首先,可以通过优化材料的化学成分,改善非合金钢板的塑性特性。
金属塑性成形课件

2023-11-06•金属塑性成形概述•金属塑性成形工艺•金属塑性成形设备•金属塑性成形技术的发展趋势•金属塑性成形过程中的缺陷与质量控制目•金属塑性成形实例分析录01金属塑性成形概述金属塑性成形是一种使金属材料发生塑性变形,以获得所需形状、尺寸和性能的加工方法。
金属塑性成形广泛应用于机械制造、航空航天、汽车、电子等领域,是一种重要的材料加工技术。
金属塑性成形的定义金属塑性成形可以制造出复杂形状的零件,并且能够获得较高的精度和表面质量。
与切削加工相比,金属塑性成形具有更高的材料利用率和更低的能耗。
金属塑性成形过程中材料的变形是均匀的,因此可以避免应力集中和裂纹等缺陷。
金属塑性成形的特点03金属塑性成形的基本原理包括应力状态、屈服准则、塑性流动规律等。
金属塑性成形的基本原理01金属塑性成形的原理是基于金属的塑性变形规律,即在外力作用下,金属材料会发生形状和尺寸的变化。
02在金属塑性成形过程中,材料的变形受到应力状态、变形温度、变形速度等因素的影响。
02金属塑性成形工艺自由锻工艺自由锻是利用冲击力或静压力使金属坯料变形,并施加外力将其锻造成所需形状和尺寸的锻造方法。
定义特点流程应用自由锻具有较大的灵活性,可以生产形状各异的锻件,但生产效率较低,适用于单件或小批量生产。
自由锻的流程包括坯料准备、加热、变形和锻后冷却。
自由锻主要用于大型锻件和难变形材料的加工,如轴、轮毂、法兰等。
模锻工艺模锻是利用模具使金属坯料变形,并施加外力将其锻造成所需形状和尺寸的锻造方法。
定义模锻具有较高的生产效率,且能获得较为精确的形状和尺寸,但模具制造成本较高。
特点模锻的流程包括坯料准备、加热、放入模具、变形、锻后冷却和修整。
流程模锻广泛应用于中小型锻件的生产,如齿轮、轴套、法兰等。
应用板料冲压工艺板料冲压是利用冲压机将金属板料变形,并施加外力将其冲制成所需形状和尺寸的加工方法。
定义板料冲压具有较高的生产效率,且能获得较为精确的形状和尺寸,但模具对材料的厚度和硬度有一定要求。
装备制造业之塑性成形技术

装备制造业之塑性成形技术随着现代工业的不断发展,各类装备制造业在实现高效生产和优质产品方面面临着日益严峻的挑战。
然而,塑性成形技术作为一种重要的制造工艺,正逐渐成为解决这些问题的关键。
本文将介绍塑性成形技术在装备制造业中的应用及其优势,并分析其未来发展趋势。
一、塑性成形技术在装备制造业中的应用1. 金属板材的压力成形金属板材压力成形技术是制造高强度、高精度零部件的重要手段。
通过将金属板材置于模具中,并施加压力,使金属板材发生弯曲、拉伸或冲裁等变形过程,从而得到所需形状的零部件。
该技术广泛应用于航空航天、汽车、电子等领域,并且可以生产出具有优良机械性能和表面质量的产品。
2. 金属管材的拉伸和冲压成形金属管材的拉伸和冲压成形技术主要用于制造管道、管接头和其他金属管材零部件。
通过控制拉伸和冲压力度,使金属管材在变形过程中逐渐改变截面形状,从而得到满足需求的产品。
该技术在石油化工设备、船舶制造等行业中得到广泛应用。
3. 塑性挤压技术塑性挤压技术是将金属坯料通过模具挤压成型,用于制造复杂截面的金属材料。
该技术具有高效率、节能和资源利用率高的特点,并且可以生产出优质的零部件。
在航空航天、铁路交通等领域,塑性挤压技术已成为制造高性能轻质构件的重要工艺。
二、塑性成形技术的优势1. 精度高塑性成形技术可以通过精确的模具设计和控制,实现对材料的精细加工,从而获得高度精密的零部件。
与传统加工工艺相比,塑性成形技术具有更低的工艺损失和变形量,可以提供更高的制造精度和表面质量。
2. 材料利用率高塑性成形技术将材料的变形过程与材料的剪切、挤压和拉伸等工艺相结合,可大幅提高材料的利用率。
与传统切削加工相比,塑性成形技术减少了材料废料的产生,并可在一次成形中得到复杂形状的零部件。
3. 生产效率高塑性成形技术具有高效率、批量生产的优势。
通过合理的设备配置和工艺优化,可以实现自动化、连续化生产,从而大幅提高生产效率。
此外,塑性成形技术还可以快速响应市场需求,缩短产品的开发周期。
超塑性成形的发展状况

超塑性成形的发展状况第一篇:超塑性成形的发展状况超塑性成形的发展状况摘要:金属材料的超塑性是指金属在特定条件下,具有更大的塑性。
本文主要介绍了超塑性成形的主要发展历程,超塑性成形的主要应用,非金属材料的超塑性研究和国内外的发展现状。
关键词:超塑性金属材料成形一、绪论近年来,高温合金和钦合金的使用不断增加,尤其是在宇航飞行器及其发动机生产中。
这些合金的特点是:流变杭力高,可塑性低,具有不均匀变形所引起机械性能各向异性的敏感性,难于机械加工及成木高昂。
如采用普通热变形锻造时,机械加工的金属损耗达80%左右,如采用超塑性成形方法,就能改变锻件肥头大耳的落后状况。
金属材料的超塑性是指金属在特定条件(晶粒细化.极低的变形速度及等温变形)下,具有更大的塑性。
如低碳钢拉伸时延伸率只有30~40%,塑性好的有色金属也只有60~70%,但超塑性状态。
一般认为塑性差的金属延伸率在100~200%范围内,塑性好的金属延伸率在500~2000%范围内。
要使超塑性出现,必须满足某些必要条件。
首先必须使金属具有0.25-2.5μm的极细晶粒,即必须小于一般晶粒大小的十分之一。
其次,当温度达金属熔点一半以上时,具有一般晶粒金属的晶粒便开始长大,而这时细晶粒金属的晶粒保持稳定。
因此,超塑性除要求有极细的晶粒度外,还必须具有高的延伸率和低的屈服应力,并以低的变形速率在高于熔点一半的温度下进行加工。
二、超塑性成形的发展早在1920年,德国W.Rosenhain等人将冷轧后的Zn-Al-Cu三元共晶合金的铝板慢速弯曲的时候,发现这种脆性材料被弯成180°而未出现裂纹,它和普通晶体材料大不相同。
他们推断这种负荷速度有密切依赖关系的异常现象,可能是由于加工产生了非晶质。
1934年,英国C.E.pearson初次对共晶合金的异常弯曲进行了详细研究。
这种合金的挤压材料很脆,容易破裂,可是C.E.pearson将其缓慢拉伸,得到了伸长率为2000%的试样。
塑料成型技术现状与发展

塑料成型技术现状与发展
随着社会经济的快速发展,塑料制品在人们的生活中发挥着越来越重要的作用。
而塑料成型技术作为塑料制品生产的重要环节,也在不断地发展与变革。
本文将探讨塑料成型技术的现状与发展趋势。
目前,塑料成型技术主要包括注塑成型、吹塑成型、挤塑成型、压塑成型、旋转成型等几种。
其中,注塑成型是最为常见的一种,其优点在于可以生产出高精度、大批量的塑料制品。
吹塑成型则适合生产大型、空心的塑料制品,如瓶子、桶等。
挤塑成型则适用于生产长条形的塑料制品,如管子、线缆等。
随着科技的发展,塑料成型技术也在不断地改进和创新。
比如,目前已经出现了3D打印技术,可以直接将数字模型转化为实物,而且可以生产出复杂形状的塑料制品。
此外,还有电子束成型技术、激光成型技术等,这些新兴技术的出现,为塑料成型技术的发展带来了新的机遇与挑战。
但是,塑料污染也成为了当前亟需解决的问题。
因此,塑料成型技术在未来的发展中,需要更加注重环保和可持续发展的理念。
比如,推广可降解塑料的生产和使用,采用环保的生产工艺和清洁能源等,都是值得尝试的方向。
总之,塑料成型技术在未来的发展中,需要更加注重环保与可持续发展的理念,同时也需要不断地创新和改进,以应对社会的需求和挑战。
- 1 -。
塑料成型技术现状与发展
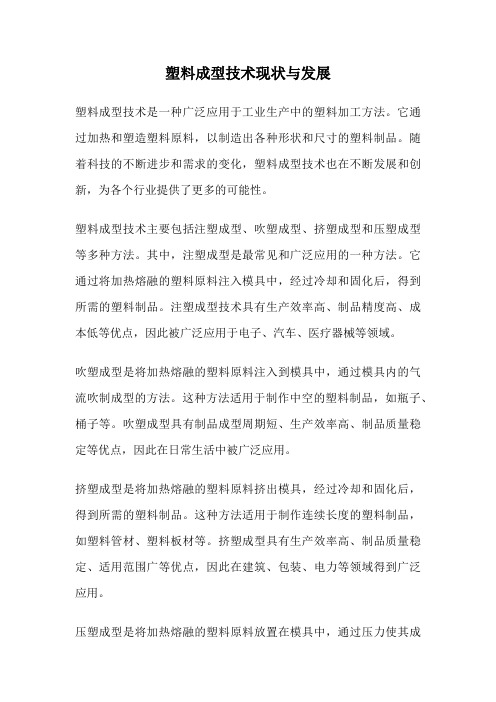
塑料成型技术现状与发展塑料成型技术是一种广泛应用于工业生产中的塑料加工方法。
它通过加热和塑造塑料原料,以制造出各种形状和尺寸的塑料制品。
随着科技的不断进步和需求的变化,塑料成型技术也在不断发展和创新,为各个行业提供了更多的可能性。
塑料成型技术主要包括注塑成型、吹塑成型、挤塑成型和压塑成型等多种方法。
其中,注塑成型是最常见和广泛应用的一种方法。
它通过将加热熔融的塑料原料注入模具中,经过冷却和固化后,得到所需的塑料制品。
注塑成型技术具有生产效率高、制品精度高、成本低等优点,因此被广泛应用于电子、汽车、医疗器械等领域。
吹塑成型是将加热熔融的塑料原料注入到模具中,通过模具内的气流吹制成型的方法。
这种方法适用于制作中空的塑料制品,如瓶子、桶子等。
吹塑成型具有制品成型周期短、生产效率高、制品质量稳定等优点,因此在日常生活中被广泛应用。
挤塑成型是将加热熔融的塑料原料挤出模具,经过冷却和固化后,得到所需的塑料制品。
这种方法适用于制作连续长度的塑料制品,如塑料管材、塑料板材等。
挤塑成型具有生产效率高、制品质量稳定、适用范围广等优点,因此在建筑、包装、电力等领域得到广泛应用。
压塑成型是将加热熔融的塑料原料放置在模具中,通过压力使其成型的方法。
这种方法适用于制作大型、复杂形状的塑料制品,如汽车外壳、家电外壳等。
压塑成型具有制品强度高、制品表面光滑等优点,因此在汽车、电子等领域得到广泛应用。
随着科技的不断进步和需求的变化,塑料成型技术也在不断发展和创新。
一方面,随着新型材料的涌现,塑料成型技术得到了更多的应用。
例如,高性能塑料、环保塑料等新型材料的使用,使得塑料制品在耐高温、耐腐蚀等方面有了更好的性能。
另一方面,随着数字化技术的应用,塑料成型技术也向着智能化、自动化方向发展。
例如,通过机器人技术实现自动化生产,通过模具设计软件进行数字化设计等,都使得塑料成型技术更加高效和精确。
随着人们对环境保护意识的增强,塑料成型技术也面临着挑战和发展。
集成计算材料工程在精确塑性成形中的应用现状与发展趋势

集成计算材料工程在精确塑性成形中的应用现状与发展趋势发布时间:2022-08-28T05:07:37.884Z 来源:《科技新时代》2022年第1月2期作者:李雪[导读] 集成计算材料工程通过模型化与计算实现对材料制备、李雪2302231981****0727摘要:集成计算材料工程通过模型化与计算实现对材料制备、加工和服役等过程的定量描述,成为实现力、热、电、磁、声场等单一/耦合外场作用下高性能构件精确塑性成形先进而有效的研究手段,近年来在精确塑性成形领域得到越来越广泛的应用。
对集成计算材料工程在塑性成形过程多尺度建模和起皱类缺陷预测方面的相关研究现状、主要进展及未来发展趋势进行了综述。
首先论述了模型在精确塑性成形领域中的应用现状,并分析了不同尺度模型间信息的传递方式;在此基础上讨论了利用集成计算材料工程研究制约精确塑性成形的起皱缺陷的预测方法,对比分析了目前主要的失稳起皱模型的准确性;最后对集成计算材料工程在精确塑性成形中的未来发展趋势进行了展望。
关键词:集成计算材料工程;塑性成形;多尺度建模;失稳起皱;断裂塑性成形是通过外力或者耦合其他外场作用使材料产生永久不可恢复的形状改变和性能提高,进而获得满足宏观形状尺寸和微观组织性能要求的构件的过程。
该过程是一个集材料、几何和边界条件非线性为一体的复杂制造过程。
在成形过程中材料的微观组织会发生显著的改变,而微观组织决定了服役性能,因此,通过塑性成形有望实现构件的形性一体化成形,即高性能构件精确塑性成形。
高性能构件精确塑性成形是材料加工与先进制造领域的重点发展方向之一。
对于以轻质材料难变形和复杂形状难成形为特征的高性能构件,其塑性成形往往还涉及材料在声、热、电、力等多能场耦合作用下更加复杂的变形机制。
在该过程中,材料宏观形状与性能改变的本质是细微观的位错运动和组织结构演化,这意味着该过程中同时存在多尺度的耦合变形,仅通过试验或者理论分析方法系统分析多尺度的耦合变形及其机制与规律存在较大局限性甚至不可能。
先进材料超塑成形技术

先进材料超塑成形技术先进材料超塑成形技术是一种利用特殊的工艺方法和控制技术,将金属材料在高温和高应变率条件下通过塑性变形成型的一种先进制造技术。
超塑成形技术能够制备出复杂几何形状的零件,并且具有优异的力学性能和表面质量。
本文将对超塑成形技术的原理、应用、发展现状和未来发展进行探讨。
超塑成形技术的原理主要是利用材料在高温和高应变率条件下的特殊塑性行为。
在高温下,材料的塑性变形能力会显著增强,可以实现超塑性变形。
高应变率条件下,由于材料的快速变形速率,可以避免材料的回弹和微观缺陷的形成,从而得到理想的成形零件。
超塑成形技术通常需要在高温下进行,因此需要使用专门设计的设备和控制系统来保持合适的温度和应变率。
超塑成形技术在航空航天、汽车制造、医疗器械等领域具有广泛的应用前景。
在航空航天领域,超塑成形技术可以制造出轻量化的结构件,提高整体效能并减少燃料消耗。
在汽车制造领域,超塑成形技术可以制造出复杂形状和轻质的车身零件,提高车辆的安全性能和燃油经济性。
在医疗器械领域,超塑成形技术可以制造出精密的植入器械和医疗设备,提高治疗效果和患者的生活质量。
目前,超塑成形技术已经得到了广泛的研究和应用。
一些国家和地区已经建立了专门的研究中心和实验室,对超塑成形技术进行深入研究,并推动其产业化发展。
在实践中,超塑成形技术已经成功应用于一些特定领域的生产工艺中,取得了较好的成果。
然而,超塑成形技术还存在一些挑战和限制。
首先,高温和高应变率条件下材料容易发生晶粒长大和孔洞形成等缺陷,导致材料的力学性能下降。
其次,超塑成形技术的设备和工艺复杂,生产周期长,需要大量的热能和人工操作。
此外,超塑成形技术还需要对材料的力学性能和塑性变形行为进行深入研究,以满足不同应用领域对材料的要求。
未来,超塑成形技术的发展方向主要包括材料的改进、工艺的优化和设备的突破。
首先,需要开发出具有优异力学性能和高温稳定性的超塑性材料。
其次,需要改进超塑成形工艺,提高生产效率和产品质量。
金属塑性成形的研究现状与发展趋势
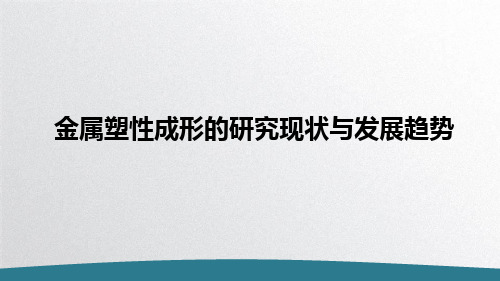
4 自由锻造
5 模型锻造
6 冲压
2
特点及优势
2.特点与优势
生产效率高
适用范围广
特点与优势
节约材料
力学性能好
2.特点与优势
(1)生产效率高:现代金属塑性成形都是靠机械完成,只需要几个简单的动 作,使得生产效率大幅提高。
(2)节约材料:是一种少切削甚至无切削的加工方式,对金属材料的利用率 较高,基本不会造成浪费。
上海交通大学牵头,通过汽 车覆盖件成形过程的“合理选材、 优化工艺、稳健设计”,建立了 汽车覆盖件精益成形技术体系。
图2 汽车覆盖件精益成形的技术体系
3.2 局部加载精确塑性成形一体化制造技术
西北工业大学牵头,研究薄壁轻量化构件和大型复杂构件精确塑性成 形技术发展中的关键问题,解决航空、航天和高技术发展中面临的迫切的塑 性成形技术难题。
金属塑性成形的研究现状与发展趋势
目 1、概述
3、研究现状
2、应用现状
录 2、特点与优势 4、发展趋势
1
概述
1.概述
一、金属塑性成形(压力加工) 金属材料在外力作用下产生塑性变形,获得具有一定形状尺寸和性能的毛坯或零
件的生产方法。
图1 汽车机盖冲压件
1.概述
二、基本生产方式
1扎制
2 挤压
3拉拔
2.特点与优势
(3)适用范围广:金属塑性成形在此方面则有其独特的优势,可加工出复杂 部件,有利于企业产品的创新,可以应用在各种机械产品上。
(4)力学性能好:据计算,一般的金属塑性成形后,强度极限最大可提高 120%,硬度最大可提高150%,弹性极限能提高300%。
3
研究现状
3.1 汽车覆盖件精益成形技术
精密塑性近净成形技术的发展现状及趋势
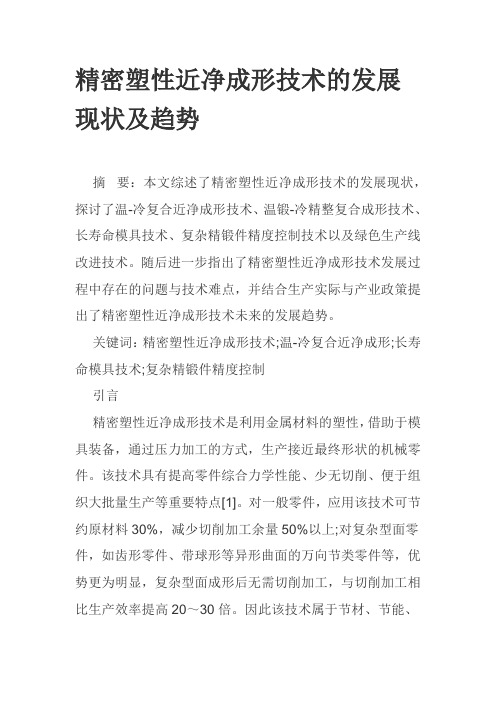
精密塑性近净成形技术的发展现状及趋势摘要:本文综述了精密塑性近净成形技术的发展现状,探讨了温-冷复合近净成形技术、温锻-冷精整复合成形技术、长寿命模具技术、复杂精锻件精度控制技术以及绿色生产线改进技术。
随后进一步指出了精密塑性近净成形技术发展过程中存在的问题与技术难点,并结合生产实际与产业政策提出了精密塑性近净成形技术未来的发展趋势。
关键词:精密塑性近净成形技术;温-冷复合近净成形;长寿命模具技术;复杂精锻件精度控制引言精密塑性近净成形技术是利用金属材料的塑性,借助于模具装备,通过压力加工的方式,生产接近最终形状的机械零件。
该技术具有提高零件综合力学性能、少无切削、便于组织大批量生产等重要特点[1]。
对一般零件,应用该技术可节约原材料30%,减少切削加工余量50%以上;对复杂型面零件,如齿形零件、带球形等异形曲面的万向节类零件等,优势更为明显,复杂型面成形后无需切削加工,与切削加工相比生产效率提高20~30倍。
因此该技术属于节材、节能、高效、短流程(减少加工工序、缩短工艺路线)的绿色制造技术,在汽车工业、工程机械等行业具有广泛的应用前景。
塑性近净成形技术的水平已成为衡量一个国家制造水平的重要标志[2]。
近年来,德、日等国在数值仿真技术应用研究、自动化生产、模具寿命、应用领域及提高锻件精度等方面都有长足的发展。
我国50年代开始塑性净成形技术的理论与应用研究,但发展缓慢,其主要原因为:没有形成适合国情的关键技术,生产与模具装备相对落后。
由于锻造模具工况环境比较恶劣,所承受工作载荷、热应力大,导致模具寿命较低,常用的模具材料H13、3Cr2W8V和H11,国内锻模平均寿命只有4000-5000件左右,使得锻件的生产成本偏高,竞争力减弱,严重制约着精密塑性近净成形技术的发展。
1 精密塑性近净成形技术的发展现状(1)温-冷复合近净成形过程中数值模拟技术温冷复合近净成形技术是20世纪70年代发展起来的一种精密锻造成形工艺,其既能够有效降低变形抗力,还结合了冷加工的成形精度[3]。
塑性成形技术的若干发展趋势

塑性成形技术的若干发展趋势引言随着科学技术的发展,塑性成形技术越来越呈现出技术融合的趋势。
一方面,塑性成形技术的进步需要从相关学科的发展中吸取自身发展的动力,如在塑性变形机理的研究中要利用材料科学和力学的进步来深化对于塑性成形中材料组织性能演化规律的认识,以便更好地解释和预测热成形过程中回复、再结晶以及流动应力的变化,塑性成形中的织构演化和塑性各向异性、损伤的演化和破裂准则;在塑性成形工艺优化中,需要利用计算数学和计算力学中的新方法等等。
另一方面,科学技术的发展也为塑性成形技术不断开辟新的应用领域,如微制造中用塑性成形工艺部分地取代起源于集成电路制造工艺的光刻、腐蚀等技术,可以降低成本、减少环境污染。
这种技术融合的趋势对于从事塑性成形理论研究和技术开发的科技人员提出了新的要求和挑战。
下面就我个人所关心的某些相关问题作一些探讨,希望与各位专家共同切磋,并有机会开展合作。
1. 数值模拟:从变形到组织性能经过几十年的发展,塑性成形模拟技术已经进入普及应用的阶段。
利用模拟技术已经能够解决十分复杂的工程问题,为企业带来了巨大的经济效益。
国外一些大公司已经将成形模拟作为模具设计、制造流程中必经的一个环节。
模拟技术在我国也逐步得到推广,国外开发的冲压成形模拟软件Dynaform、AutoForm,体积成形模拟软件DEFORM等在我国已拥有大量用户,我国自行研发的模拟软件、如FASTAMP等也已得到推广应用。
以前,模具调试和锻压生产中出现缺陷时,只能采用工艺试验和试凑法摸索解决方案;而现在,人们首先会借助于数值模拟技术探索改进方案,然后再通过实验进行验证,这就大大地节省了人力、物力和时间的消耗。
然而,现有的塑性成形模拟技术还远远不能满足研究和生产所提出的实际要求。
现有的商业软件对一般成形过程中的应变和应力分布已经能给出比较精确的结果,但是对于预测工件在成形过程中的组织性能变化则无能为力。
这直接影响到模拟技术的应用效果。
有色金属塑性加工发展趋势
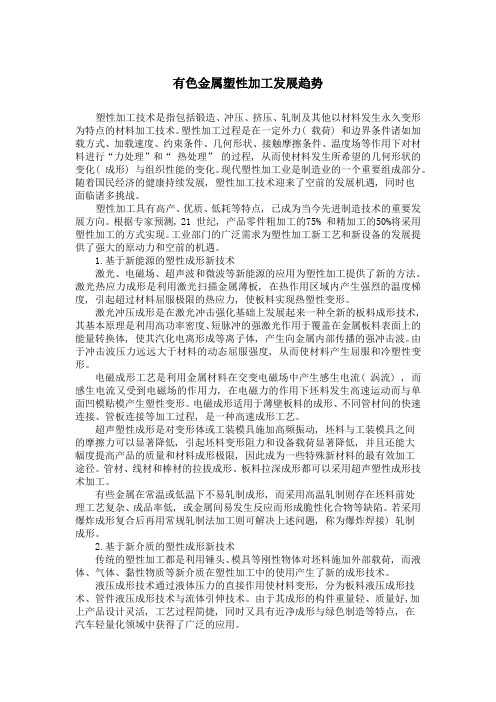
有色金属塑性加工发展趋势塑性加工技术是指包括锻造、冲压、挤压、轧制及其他以材料发生永久变形为特点的材料加工技术。
塑性加工过程是在一定外力( 载荷) 和边界条件诸如加载方式、加载速度、约束条件、几何形状、接触摩擦条件、温度场等作用下对材料进行“力处理”和“热处理”的过程, 从而使材料发生所希望的几何形状的变化( 成形) 与组织性能的变化。
现代塑性加工业是制造业的一个重要组成部分。
随着国民经济的健康持续发展, 塑性加工技术迎来了空前的发展机遇, 同时也面临诸多挑战。
塑性加工具有高产、优质、低耗等特点, 已成为当今先进制造技术的重要发展方向。
根据专家预测, 21 世纪, 产品零件粗加工的75% 和精加工的50%将采用塑性加工的方式实现。
工业部门的广泛需求为塑性加工新工艺和新设备的发展提供了强大的原动力和空前的机遇。
1.基于新能源的塑性成形新技术激光、电磁场、超声波和微波等新能源的应用为塑性加工提供了新的方法。
激光热应力成形是利用激光扫描金属薄板, 在热作用区域内产生强烈的温度梯度, 引起超过材料屈服极限的热应力, 使板料实现热塑性变形。
激光冲压成形是在激光冲击强化基础上发展起来一种全新的板料成形技术, 其基本原理是利用高功率密度、短脉冲的强激光作用于覆盖在金属板料表面上的能量转换体, 使其汽化电离形成等离子体, 产生向金属内部传播的强冲击波。
由于冲击波压力远远大于材料的动态屈服强度, 从而使材料产生屈服和冷塑性变形。
电磁成形工艺是利用金属材料在交变电磁场中产生感生电流( 涡流) , 而感生电流又受到电磁场的作用力, 在电磁力的作用下坯料发生高速运动而与单面凹模贴模产生塑性变形。
电磁成形适用于薄壁板料的成形、不同管材间的快速连接、管板连接等加工过程, 是一种高速成形工艺。
超声塑性成形是对变形体或工装模具施加高频振动, 坯料与工装模具之间的摩擦力可以显著降低, 引起坯料变形阻力和设备载荷显著降低, 并且还能大幅度提高产品的质量和材料成形极限, 因此成为一些特殊新材料的最有效加工途径。
精密微塑性成形技术的现状及发展趋势论文

精密微塑性成形技术的现状及发展趋势论文精密微塑性成形技术的现状及发展趋势论文引言微塑性成形技术主要是采用塑性变形的方式进行形成微型零件的工艺方法,在多种复杂形状微小零件作用下能够达到微米量级,所以在微型零件的制造上较为适用。
微塑性成形技术并非是传统塑性成形工艺的简单等比例缩小,其作为新的研究领域对实际的发展有着重要促进作用,故此加强这一领域的理论研究就有着实质性意义。
1 精密微塑性成形原理特征及方法分析1.1 精密微塑性成形原理特征分析科技的发展带来了生产的效率提升,在微塑性成形技术的发展过程中经历了不同时期的进步,传统的成形工艺按照比例微缩到微观领域在参数上的适应性就失去了。
而微塑性成形技术在现阶段已经成了多种学科交叉的边缘技术,实际成形中的润滑以及摩擦也与此同时发生了一些变化,所以宏观摩擦学当中的摩擦理论就不能有效适应。
但由于微小尺度下秒面积与体积的增大,所以在摩擦力就对成形造成的影响逐渐扩大,那么润滑就是比较关键的因素。
从实际的成形原理来看,在工件进行微缩化的过程中,此时在摩擦力上就会随之加大,压力的加大那么封闭润滑包中的润滑油压强也随之加大,这样就支持以及对成形的载荷实现了传递,进而对摩擦也减小了。
在工件的尺寸不断的微小化过程中,开口润滑包面积减少幅度不是很大,但在封闭润滑包的面积减少幅度就相对比较大,采用固体润滑剂的过程中由于不存在润滑剂溢出的状况所以就对摩擦系数的影响也较小。
1.2 精密微塑性成形方法分析微塑性成形工艺及方法的相关研究主要是在微冲压以及微体积成形方面,其中的微体积成形主要是进行的微连接器以及顶杆和叶片等微型的期间精密形成。
以螺钉为例,其最小的尺寸只有0.8 微米,而微成形胚料的最小直径是0.3 微米,在模压成形的微结构构建沟槽的最小宽度能够达到二百纳米。
另外在微冲压成形这一方法上最为重要的就是进行的薄板微深拉伸以及增量成形等方法。
微型器件的微塑性成形技术属于新兴的研究领域,在成形的方法上主要就是实现毫米级的微型器件精密微成形,在微塑性成形技术的不断发展下,这一技术会进一步的优化。
金属塑性成形综述
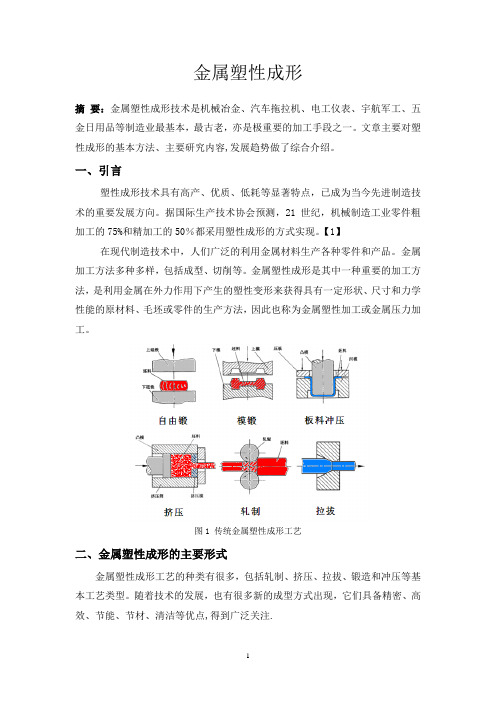
金属塑性成形摘要:金属塑性成形技术是机械冶金、汽车拖拉机、电工仪表、宇航军工、五金日用品等制造业最基本,最古老,亦是极重要的加工手段之一。
文章主要对塑性成形的基本方法、主要研究内容,发展趋势做了综合介绍。
一、引言塑性成形技术具有高产、优质、低耗等显著特点,已成为当今先进制造技术的重要发展方向。
据国际生产技术协会预测,21世纪,机械制造工业零件粗加工的75%和精加工的50%都采用塑性成形的方式实现。
【1】在现代制造技术中,人们广泛的利用金属材料生产各种零件和产品。
金属加工方法多种多样,包括成型、切削等。
金属塑性成形是其中一种重要的加工方法,是利用金属在外力作用下产生的塑性变形来获得具有一定形状、尺寸和力学性能的原材料、毛坯或零件的生产方法,因此也称为金属塑性加工或金属压力加工。
图1 传统金属塑性成形工艺二、金属塑性成形的主要形式金属塑性成形工艺的种类有很多,包括轧制、挤压、拉拔、锻造和冲压等基本工艺类型。
随着技术的发展,也有很多新的成型方式出现,它们具备精密、高效、节能、节材、清洁等优点,得到广泛关注.2。
1 体积成型金属体积成型是指对金属块料、棒料或厚板在高温或室温下进行成形加工的方法,主要分为热态金属体积成型和冷温态金属体积成型.热态金属变形过程可分为热锻、轧制、挤压、拉拔、辗压等工艺技术;冷温态变形过程可分为冷锻、冷精轧、冷挤压、冷拔、冷辗扩等工艺.2.2 板材成型所谓板材成型是指用板材、薄壁管、薄型材等作为原材料进行塑性加工的成形方法。
在忽略板厚的变化时,可视为平面变形问题来处理,板材成型可分为:冲裁、弯曲、拉延、胀形、翻边、扩孔、辊压等工艺技术。
2。
3 粉末态金属成形随着制粉技术的发展,其应用领域不断扩展,对于复杂形状的机械零件来说,它具有高效、精密成形的特点,但成本较高,机械性能不如整体金属材料。
粉末态金属成形的工艺过程为制粉、造型、压实、烧结、精锻。
2.4半固态金属材料成形70年代开发研究的新技术,原金属材料作过特殊前处理,当材料加热到一定温度时可使30%的金属材料处于融溶状态,其余70%的金属材料呈均匀细颗粒组织的固态。
塑性成形新技术及应用

塑性成形新技术及应用塑性成形是一种常见的加工方法,广泛应用于各行各业。
随着科技的发展和技术的进步,塑性成形也不断创新和改进,出现了许多新技术和应用。
首先,说到塑性成形的新技术,我们可以提到热成形技术。
热成形是一种通过控制金属的温度来实现形状改变的方法。
相比于常规的冷成形,热成形能够提高材料的塑性和可变形性,从而获得更复杂的形状和更高的尺寸精度。
热成形技术主要包括热锻、热轧、热拉伸等,广泛应用于航空航天、汽车制造、机械加工等领域。
其次,还可以提到微成形技术。
微成形是一种针对微米尺度工件的加工技术,主要通过微纳加工设备和精密控制技术来实现。
与传统的宏观成形相比,微成形具有尺寸小、精度高、工艺复杂等特点。
微成形技术在微机电系统(MEMS)、生物医学器械、微型传感器等领域有着广泛应用,如微型机械零件的制造、微流控芯片的加工等。
另外,值得一提的是增材制造技术在塑性成形中的应用。
增材制造技术是一种基于逐层堆叠的三维打印技术,通过逐层堆叠材料来构建复杂的工件形状。
在塑性成形中,增材制造可以实现一些传统加工方法无法完成的形状和结构,具有设计自由度高,制造成本低,能耗低等优势。
增材制造技术被广泛应用于航空航天、医疗器械、汽车制造等领域,如航空发动机叶片的制造、医学植入物的制备等。
除了以上所介绍的新技术,塑性成形还有许多其他的应用。
在汽车制造领域,塑性成形广泛应用于汽车车身板的制造。
汽车车身板材多采用薄板和超高强度钢,能够通过塑性成形来实现复杂的车身形状和结构。
在航空航天领域,塑性成形被用于制造飞机的轻质结构件,如航空发动机叶片、机翼等。
在电子设备制造领域,塑性成形被用于制造外壳、内部零件等。
在医疗器械领域,塑性成形被用于制造人工关节、骨刺钉等。
总而言之,塑性成形作为一种重要的加工方法,不断创新和改进,出现了许多新技术和应用。
热成形技术、微成形技术和增材制造技术都是其中的新技术,它们为塑性成形带来了更多的发展机遇和应用领域。
金属塑性成形技术的发展方向及问题探讨
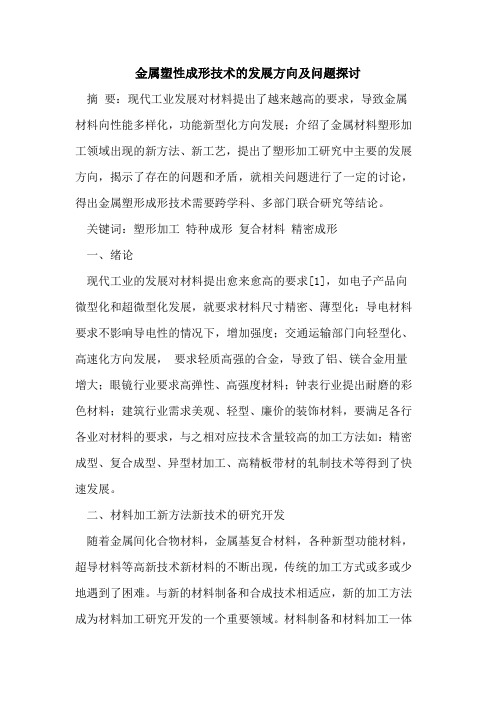
金属塑性成形技术的发展方向及问题探讨摘要:现代工业发展对材料提出了越来越高的要求,导致金属材料向性能多样化,功能新型化方向发展;介绍了金属材料塑形加工领域出现的新方法、新工艺,提出了塑形加工研究中主要的发展方向,揭示了存在的问题和矛盾,就相关问题进行了一定的讨论,得出金属塑形成形技术需要跨学科、多部门联合研究等结论。
关键词:塑形加工特种成形复合材料精密成形一、绪论现代工业的发展对材料提出愈来愈高的要求[1],如电子产品向微型化和超微型化发展,就要求材料尺寸精密、薄型化;导电材料要求不影响导电性的情况下,增加强度;交通运输部门向轻型化、高速化方向发展,要求轻质高强的合金,导致了铝、镁合金用量增大;眼镜行业要求高弹性、高强度材料;钟表行业提出耐磨的彩色材料;建筑行业需求美观、轻型、廉价的装饰材料,要满足各行各业对材料的要求,与之相对应技术含量较高的加工方法如:精密成型、复合成型、异型材加工、高精板带材的轧制技术等得到了快速发展。
二、材料加工新方法新技术的研究开发随着金属间化合物材料,金属基复合材料,各种新型功能材料,超导材料等高新技术新材料的不断出现,传统的加工方式或多或少地遇到了困难。
与新的材料制备和合成技术相适应,新的加工方法成为材料加工研究开发的一个重要领域。
材料制备和材料加工一体化是一个发展趋势,为降低新材料的成本使之达到商业化应用,新的廉价的加工方法的开发是至关重要的。
有观点认为,未来新材料在应用方面的竞争,很大程度取决于它的加工方法是否容易和廉价,换言之,就是材料加工技术方面的竞争。
材料加工新技术不断出现,尤其是针对复合材料的加工方面更为突出。
主要有:1.喷射成型技术喷射成形技术作为一种生产工程材料的加工技术,其独创之处是金属或合金自熔融状态经一步工艺直接制成接近最终产品的形状,并具有良好的组织性能。
用喷射成形方法生产铅合金板坯和各种形状的锻造坯料,可以省去以往从液态金属到固体坯料之间的铸造、热轧开坯,进一步简化工艺,大大降低了能耗和成本。
装备制造业之塑性成形技术

装备制造业之塑性成形技术在装备制造业中,塑性成形技术是一项重要的制造工艺,它通过对金属材料的塑性变形来实现对零件的成形。
塑性成形技术具有高效、精确、经济的特点,广泛应用于各个领域,如汽车制造、航空航天等。
本文将对塑性成形技术的概念、工艺流程以及在装备制造业中的应用进行论述,并重点介绍了其在汽车制造领域中的应用。
一、塑性成形技术概述塑性成形技术是利用材料在塑性变形过程中体积不变的特性,通过外力作用将材料加工成所需形状的一种成形工艺。
它能够更好地满足装备制造业对高强度、轻质材料的需求,并能够减少加工工序和材料浪费。
塑性成形技术包括热挤压、热轧、锻造、拉伸等多种方法,每种方法都有其适用的材料和成形形式。
二、塑性成形技术的工艺流程塑性成形技术的工艺流程一般包括材料准备、装配和调整、塑性成形、材料处理和成品制备等环节。
首先,需要选择合适的材料,并对其进行加热、退火等预处理,以提高材料的可塑性。
然后在成形装置中安装和调整模具,确保其能够进行准确的成形。
接下来,将加热后的材料放入成形装置中,通过外力的作用,使其发生塑性变形,并按照设计要求形成所需的零件形状。
最后,对成形后的零件进行处理和制备,如清洗、涂层等,以保证其质量和性能的稳定。
三、塑性成形技术在装备制造业中的应用1. 汽车制造领域塑性成形技术在汽车制造领域中得到了广泛的应用。
例如,汽车车身的制造中,通过冲压工艺将钢板进行成形,制作出车身外壳等零部件。
这种工艺具有高效、精确的特点,能够满足汽车制造行业对高强度、轻质材料的需求,并能够大批量生产,提高生产效率。
2. 航空航天领域在航空航天领域,塑性成形技术被广泛应用于飞机和火箭等装备的制造过程中。
例如,利用锻造技术可以制造出高强度、耐高温的发动机零部件,以提高发动机的性能和寿命。
此外,通过冲压工艺可以制造出轻质、高强度的飞机蒙皮和结构零件等。
3. 电子设备制造领域在电子设备制造领域,塑性成形技术也有着广泛的应用。
- 1、下载文档前请自行甄别文档内容的完整性,平台不提供额外的编辑、内容补充、找答案等附加服务。
- 2、"仅部分预览"的文档,不可在线预览部分如存在完整性等问题,可反馈申请退款(可完整预览的文档不适用该条件!)。
- 3、如文档侵犯您的权益,请联系客服反馈,我们会尽快为您处理(人工客服工作时间:9:00-18:30)。
塑性成形技术的现状及发展趋势
塑性成形技术具有高产、优质、低耗等显著特点,已成为当今先进制造技术的重要发展方向。
据国际生产技术协会预测,21 世纪,机械制造工业零件粗加工的75 %和精加工的50 %都采用塑性成形的方式实现。
工业部门的广泛需求为塑性成形新工艺新设备的发展提供了强大的原动力和空前的机遇。
金属及非金属材料的塑性成形过程都是在模具型腔中来完成的。
因此,模具工业已成为国民经济的重要基础工业。
新世纪,科学技术面临着巨大的变革。
通过与计算机的紧密结合,数控加工、激光成型、人工智能、材料科学和集成制造等一系列与塑性成形相关联的技术发展速度之快,学科领域交叉之广泛是过去任何时代无法比拟的,塑性成形新工艺和新设备不断地涌现,掌握塑性成形技术的现状和发展趋势,有助于及时研究、推广和应用高新技术,推动塑性成形技术的持续发展。
实施塑性成形技术的最终形式就是模具产品,而模具工业发展的关键是模具技术进步,模具技术又涉及到多学科的交叉。
模具作为一种高附加值产品和技术密集型产品,其技术水平的高低已成为衡量一个国家制造业水平的重要标志之一。
1 塑性成形技术的现状
精密成形技术对于提高产品精度、缩短产品交货期、减少切削加工和降低生产成本均有着重要意义。
近10年来,精密成形技术都取得了突飞猛进的发展。
精冲技术、冷挤压技术、无飞边热模锻技术、温锻技术、超塑性成形技术、成形轧制、液态模锻、多向模锻技术发展很快。
例如电机定转子双回转叠片硬质合金级进模的步距精度可达2μm ,寿命达到1亿次以上。
集成电路引线框架的20~30工位的级进模,工位数最多已达160个。
自动冲切、叠压、铆合、计数、分组、转子铁芯扭斜和安全保护等功能的铁芯精密自动叠片多功能模具。
新型轿车的大尺寸覆盖件成形、大功率汽车的六拐曲轴成形。
700mm汽轮机叶片精密辊锻和精整复合工艺,楔横轧汽车、拖拉机精密轴类锻件。
除传统的锻造工艺外,近年来半固态金属成形技术也日趋成熟,引起工业界的普遍关注。
所谓半固态成形,是指对液态液相共存的半固态坯料进行各种成形加工。
它具有节省材料、降低能耗、提高模具寿命、改善制件性能等一系列优点,并可成形复合材料的产品,被誉为21世纪新兴金属塑性加工的关键技术。
此外,在粉末冶金和塑料加工方面,金属粉末锻造成形,金属粉末超塑性成形,粉末注射成形、粉末喷射和喷涂成形以
及塑料注射成形中热流道技术,气体辅助技术和高压注射的成功应用,大大扩充了现代精密塑性成形的应用范围。
2现代模具工业的发展趋势
传统的模具制造技术,主要是根据设计图纸,用仿型加工,成形磨削以及电火花加工方法来制造模具。
而现代模具不同,它不仅形状与结构十分复杂,而且技术要求更高,用传统的模具制造方法显然难于制造,必须借助于现代科学技术的发展,采用先进制造技术,才能达到它的技术要求,表1列出了传统模具与现代模具制造的技术水平。
当前,整个工业生产的发展特点是产品品种多、更新快、市场竞争剧烈。
为了适应市场对模具制造的短交货期,高精度、低成本的迫切要求,模具将有如下发展趋势:
(1) 愈来愈高的模具精度。
10年前,精密模具的精度一般为5μm ,现在已达2~3μm ,不久1μm精度的模具即将上市。
随着零件微型化及精度要求的提高,有些模具的加工精度要求在1μm以内,这就要求发展超精加工。
(2) 日趋大型化模具。
这一方面是由于用模具成形的零件日渐大型化,另一方面也是由于高生产率要求的一模多腔(现在有的已达一模几百腔)所致。
(3) 扩大应用热流道技术。
由于采用热流道技术的模具可提高制件的生产率和质量,并能大幅度节约制件的原材料,因此热流道技术的应用在国外发展较快,许多塑料模具厂所生产的塑料模具50 %以上采用了热流道技术,甚至达到80 %以上,效果十分明显。
热流道模具在国内也已生产,有些企业使用率上升到20 %~30 %。
(4) 进一步发展多功能复合模具。
一副多功能模具除了冲压成形零件外,还担负着叠压、攻丝、铆接和锁紧等组装任务,这种多功能复合模具生产出来的不再是单个零件,而是成批的组件,可大大缩短产品的生产及装配周期,对模具材料的性能要求也越来越高。
(5) 日益增多高挡次模具。
大致可分三个层次,一是用于汽车、飞机、精密机械的微米级(μm)精密加工;二是用于磁盘、磁鼓制造的亚微米级(0. 01μm)精密加工;三是用于超精密电子器件的毫微米级(0. 001μm)精密加工。
目前,超精密加工已进入纳米级(011~100nm)精度阶段。
这将使模具的技术含量不断提高,使中、高档模具比例将不断增大。
(6) 进一步增多气辅模具及高压注射成型模具。
随着塑料成形工艺的不断改进和发展,为了提高注塑件质量,气辅模具及高压注射成型模具将随之发展。
(7) 增大塑料模具比例。
随着塑料原材料的性能不断提高,各行业的零件将以塑代钢,以塑代木的进程进一步加快,使塑料模具的比例日趋增大。
同时,由于机械零件的复杂程度和精度的逐渐提高,对塑料模具的制造要求也越来越高。
(8) 增多挤压模及粉末锻模。
由于汽车、车辆和电机等产品向轻量化发展,如以铝代钢,非全密度成形,高分子材料、复合材料、工程陶瓷、超硬材料成形和加工。
新型材料的采用,不仅改变产品结构和性能而且使生产工艺发生了根本变革,相应地出现了液态(半固态)挤压模具及粉末锻模。
对这些模具的制造精度要求是高的。
(9) 日渐推广应用模具标准化。
模具标准化及模具标准件的应用将极大地影响模具制造周期,且还能提高模具的质量和降低模具制造成本。
因此,模具标准件的应用在“十五”期间必将得到较大的发展。
(10) 大力发展快速制造模具。
目前是多品种小批量生产时代,21 世纪,这种生产方式占工业生产的比例将达到75 %以上。
由此,一方面是制品使用周期缩短,
另一方面花样变化频繁,要求模具的生产周期愈短愈好。
因此,开发快速成型模具将越来越引起人们的重视和关注。
3 当代塑性成形技术的研究方向
国内塑性成形技术与国外相比还有一定的差距,加入WTO之后,为了塑性成形技术逐步达到国际水平,需在如下六方面不断研究,不断提高:
(1) 塑性成形
有限元分析金属流动;数值仿真金属流动;成形工艺过程模拟,预测缺陷;纳米材料(超细、微细晶粒)成形,微观视塑法;快速原型成形。
模具设计
计算机辅助设计;反(逆)向工程;并行工程;快速设计;协同设计;人工智能;基于知识的工程;基于事例的推理;基于模型的推理;集成化技术;网络化技术;多学科多功能综合技术;特征技术。
(3) 模具结构
标准化模具;模块单元组合模具;基于Web的CAPP体系结构;纳米模具。
(4) 模具材料
A1基本材料:新型模具材料(冷作、热作) ;钢结硬质合金。
B1表面工程技术:热扩渗技术;热喷涂与热喷焊技术;复合电镀与复合电刷镀技术;化学镀技术;物理气相及化学气相沉积技术;高能束(激光束、离子束、电子束)技术;稀土表面工程技术;纳米表面工程技术。
(5) 模具制造
数控;电火花;线切割;超精加工;高速铣削;计算机集成制造系统;快速模具制造;柔性制造系统;敏捷制造系统;虚拟制造系统;智能制造系统;协同制造系统;精益生产体系;绿色制造系统;信息管理系统。
(6) 绿色环保技术
无色热锻润滑剂(削除乌烟肮脏) ;拉深润滑剂(可完全挥发的) ;无噪声技术;消震、隔震技术。