第八章 聚合过程及聚合反应器
聚合反应工程基础 第八章 聚合过程及聚合反应器

苯乙烯 甲基丙烯酸甲酯
醋酸乙烯酯 丁二烯-苯乙烯
氯丁二烯
氯乙烯
苯乙烯-甲醇 四氟乙烯-水
氯乙烯 偏二氯乙烯
氯乙烯
21
四种聚合方法的比较
比较项目 配方主要成分
聚合场所 聚合机理
生产特点
产物特征
本体聚合
溶液聚合
悬浮聚合
乳液聚合
单体 引发剂
单体 引发剂
溶剂
单体 引发剂
水 分散剂
单体 水溶性引发剂
是不加溶液或分散介质情况下,只有单体在引发剂(有时不加)或光、
热、辐射的作用下进行聚合的方法。
★适用对象
自由基本体聚合反应和离子型聚合反应。
★本体聚合的分类 根据单体与聚合物溶解情况
均相聚合 非均相聚合(沉淀聚合)
根据单体的状态
气相本体聚合 液相本体聚合 固相本体聚合
间歇操作本体聚合 根据操作方式
连续操作本体聚合
按反应性质分
按产物溶解情况分
9
溶液缩聚的特点
反应平稳,有利于热量交换,防止局部过热; 不需要高真空度; 缩聚产物可直接制成清漆、成膜材料、纺丝。
溶剂存在
能用熔融缩聚生产的缩聚物一般不用溶液缩聚生产
使用溶剂后,工艺复杂,需要分离、精制、回收; 生产成本较高。
10
影响溶液聚合的因素 官能团要极少过量(趋势不对称); 反应程度越高,产物相对分子质量越大,但过高,则发生 副反应; 升高温度,反应平衡常数下降(对活性小单体采用高温, 对活性大单体采用低温); 对活性大单体不加催化剂,活性小单体适当加入; 溶剂主要是溶解单体,便于混合、降低黏度、利于换热; 溶解缩聚物有利于链增长,提高产物聚合度。溶剂性质对聚 合影响较大,一要稳定、二要极性大。可以单独使用,也可 混合使用。
第8章 聚合反应工程基础

第八章 1 聚合反应器¾从操作方式来看它能进行间歇、半连续、单釜和多釜连续操作,以满足不同聚合过程的要求。
¾反应釜一般带搅拌装置,且形式多样。
1.1 釜式聚合反应器(聚合釜)(1)釜体(2)搅拌装置基本结构4(3)密封装置(4)传动装置¾封头(1)釜体端部法兰式结构:开式结构、釜盖重包括:上下封头、直立圆筒、接管、法兰、支座等5量较轻,适用压力较低、容积较小的反应釜选用。
闭式、留人孔式结构:闭式结构、无法兰、结构简单、造价较低,适用容积大的反应釜。
6几种搅拌设备筒体的高径比H 1/D 1种类罐内物料类型高径比一般搅拌罐液-固相、液-液相1~1.3¾筒体7气-液相1~2聚合釜悬浮液、乳化液2.08~3.85发酵罐类发酵液1.7~2.5高径比较大?991010反应釜材质:不锈钢、搪瓷11管道颜色标识原料:灰色空气:蓝色氮气:黑色1313水:绿色热介质进出管:红色产物放料管:灰色14141515 传感器:测量反应物的温度、压力或其它参数。
1617 视镜18支座:小型用悬挂式支座,大型用裙式支座或支承式支座。
1920如何有效的排除聚合反应热,保持反应温度?①夹套冷却夹套传热:饱和水蒸汽、热水、冷水、冷冻盐水、热导油等。
22¾蒸汽加热和液体加热的方向?①夹套冷却夹套传热:饱和水蒸汽、热水、冷水、冷冻盐水、热导油等。
压力MPa 温度℃压力MPa 温度℃0010102002001335230.010102.00.200133.50.050111.00.300143.50.100120.00.400151.50.150127.00.520160.0夹套附加内冷管冷却——大型聚合釜或要求低温操作24内冷管——蛇管25③回流冷凝器冷却——反应温度较高,单体沸腾回流移去反应热26回流冷凝器冷却27传热装置——电加热28釜体的保温——高温或低温聚合293133搅拌机顶插式中心安装立式圆筒的三种基本流型径向流流型轴向流切向流36轴向流与搅拌器☆桨式搅拌器(折叶式):结构简单☆叶片用扁钢制成,焊接或用螺栓固定在轮毂上,叶片数是2、3或4 片。
聚合反应工程基础复习提纲
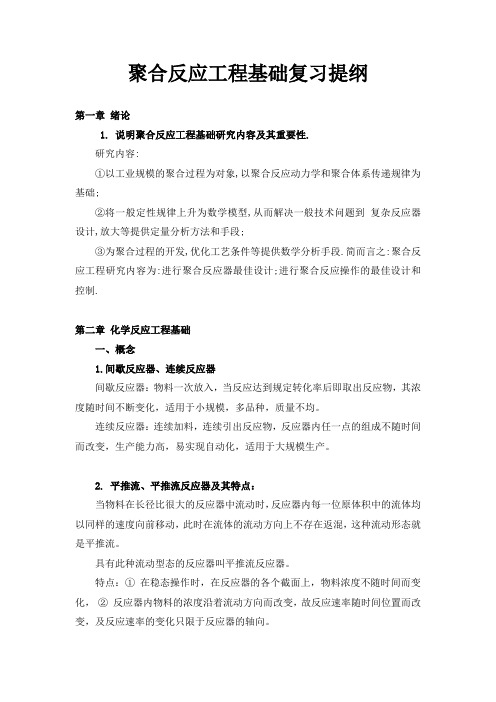
聚合反应工程基础复习提纲第一章绪论1. 说明聚合反应工程基础研究内容及其重要性.研究内容:①以工业规模的聚合过程为对象,以聚合反应动力学和聚合体系传递规律为基础;②将一般定性规律上升为数学模型,从而解决一般技术问题到复杂反应器设计,放大等提供定量分析方法和手段;③为聚合过程的开发,优化工艺条件等提供数学分析手段.简而言之:聚合反应工程研究内容为:进行聚合反应器最佳设计;进行聚合反应操作的最佳设计和控制.第二章化学反应工程基础一、概念1.间歇反应器、连续反应器间歇反应器:物料一次放入,当反应达到规定转化率后即取出反应物,其浓度随时间不断变化,适用于小规模,多品种,质量不均。
连续反应器:连续加料,连续引出反应物,反应器内任一点的组成不随时间而改变,生产能力高,易实现自动化,适用于大规模生产。
2.平推流、平推流反应器及其特点:当物料在长径比很大的反应器中流动时,反应器内每一位原体积中的流体均以同样的速度向前移动,此时在流体的流动方向上不存在返混,这种流动形态就是平推流。
具有此种流动型态的反应器叫平推流反应器。
特点:①在稳态操作时,在反应器的各个截面上,物料浓度不随时间而变化,②反应器内物料的浓度沿着流动方向而改变,故反应速率随时间位置而改变,及反应速率的变化只限于反应器的轴向。
3.理想混合流、理想混合流反应器及其特点:反应器中强烈的搅拌作用使刚进入反应器的物料微元与器内原有物料微元间瞬时达到充分混合,使各点浓度相等,且不随时间变化,出口流体组成与器内相等这种流动形态称之为理想混合流。
与理想混合流相适应的反应器称为理想混合流反应器。
特点:①反应器内物料浓度和温度是均一的,等于出口流体组成②物料质点在反应器内停留时间有长有短③反应器内物质参数不随时间变化。
4.膨胀率:反应中某种物料全部转化后体系的体积变化率5.容积效率:指同一反应在相同的温度、产量、和转化率的条件下,平推流反应器与理想混合反应器所需的总体积比6. 停留时间分布密度函数、停留时间分布函数、平均停留时间停留时间分布密度函数:系统出口流体中,已知在系统中停留时间为 t 到dt 间的微元所占的分率 E(t)dt停留时间分布函数F(t):系统出口流体中,已知在系统中停留时间小于 t 的微元所占的分率 F(t)7.返混指反应器中不同年龄的流体微元间的混合8、宏观流体、微观流体宏观流体:流体微元均以分子团或分子束存在的流体;微观流体:流体微元均以分子状态均匀分散的流体;9.宏观流动、微观流动宏观流体指流体以大尺寸在大范围内的湍动状态,又称循环流动;微观流体指流体以小尺寸在小范围内的湍动状态10.混合时间指经过搅拌时物料达到规定均匀程度所需的时间11.微观混合、宏观混合 P70微元尺度上的均匀化称为宏观混合;分子尺度上的均匀化称为微观混合。
聚合反应器讲解课件

03
聚合反应器的种类与选型
聚合反应器的种类
搅拌釜式反应器
适用于液态物料,通过搅拌实 现混合和传热。
塔式反应器
适用于气态和液态物料的反应 ,通过填料或塔盘实现传质和 传热。
固定床反应器
适用于气态和液态物料的反应 ,催化剂固定在反应器内,通 过反应物在催化剂表面进行反 应。
流化床反应器
适用于固态物料的反应,催化 剂与反应物料混合流动,通过
现代聚合反应器
随着工业技术的发展,现代聚合反应 器逐渐向大型化、连续化、自动化方 向发展,提高了生产效率和产品质量 。
02
聚合反应器的工作原理
聚合反应的原理
聚合反应的分类
根据聚合物的结构和单体种类的不同,聚合反应可分为加聚反应和缩聚反应。加聚反应是 指单体在聚合过程中只生成一种聚合物的反应,而缩聚反应则是指单体在聚合过程中除了 生成聚合物外,还伴有小分子物质(如水、氯化氢等)的生成。
超声波引发聚合
利用超声波的物理作用,可实现聚合反应的高效、快速和均一化, 同时可降低聚合温度,减少能源消耗。
活性自由基聚合
活性自由基聚合是一种新型的聚合方法,具有聚合度高、分子量分布 窄、可控制聚合过程等优点,是高分子合成领域的重要发展方向。
聚合反应器在未来的应用前景
高性能材料制备
01
利用聚合反应器可实现高性能材料的高效、快速和连续化制备
,如高性能聚合物、功能性高分子等。
生物医用材料制备
02
聚合反应器可用于生物医用材料的制备,如生物可降解高分子
材料、组织工程支架材料等。
新材料开发
03
利用聚合反应器可开发新型的高分子材料,如超分子聚合物、
纳米复合材料等。
第八章 聚合过程及聚合反应器

3.管式聚合反应器
优点:结构简单,单位面积所具有的传热面 大,适用作高温、高压的聚合反应器。
缺点: a.易发生聚合物粘壁现象,造成管子堵塞 b.物料粘度大时,压力损失大 c.由于在管子上长度方向上温度、压力、组
分浓度等反应参数不能保持一致,所以反应 器在流动方向上产生参数分布 因此,管式反应器在聚合物生产中时用较少。
自由基溶液聚合选择溶剂时,须注意两方面的问题。 (1)溶剂的活性 溶剂往往并非绝对惰性,对引发
剂有诱导分解作用,链自由基对溶剂有链转移反应。 (2)溶剂对聚合物溶解性能和对凝胶效应的影响
选用良溶剂时,为均相聚合,如果单体浓度不高, 则有可能消除凝胶效应,遵循正常自由基聚合动力 学规律。选用沉淀剂时,则成为沉淀聚合,凝胶效 应显著。
对低粘度系统主要使用平桨式、推进式、涡轮式、 三叶后掠式及布鲁马金式桨叶,当与各类挡板配合 使用时可获得所需的剪切与循环作用。对高粘度体 系主要使用锚式、螺带、带导流筒的螺杆桨叶以及 特殊型式的浆叶。
18
1.釜式聚合反应器
釜式反应器的除热主要是采用夹套和各种内冷构件 (如蛇管、内冷挡板等)。
在使用内冷件时应注意: A.是否产生物料的混合死角 B.是否会引起物料粘附于器壁 C.构件表面和粒子间的凝集 如果夹套和内冷件不除热时,还可以采用 A.单体或溶剂的蒸发 B.使用物料釜外循环冷却 C.冷进料
采用不同的聚合反应器对聚合产物的结构和性能产 生显著的影响。
不同的聚合反应机理对于单体、引发剂(催化剂) 和反应介质的要求各不一致,所以实现这些聚合过 程要采用不同的聚合方法。
2
第一节 工业聚合方法
聚合方法的选择要考虑的因素: 单体的化学特性 传热方式 聚合物的特性 对产品的质量要求(实现大型化、连续化) 聚合反应器的结构与特性
《聚合反应工程》课件

安全与环保实践:在实际操作中,严格按照安全与环保要求进行操作,确保生产过程 的安全与环保。
安全与环保检查:定期对生产现场进行安全与环保检查,及时发现并解决问题,确保 生产过程的安全与环保。
感谢您的观看
汇报人:
应用领域:广泛应 用于建筑、汽车、 电子、医疗等领域
聚合反应工程实验 技术
反应器:用于进行聚合反应的容器,包括搅拌器、加热器等 温度计:用于测量反应温度,确保反应在适宜的温度下进行 压力计:用于测量反应压力,确保反应在适宜的压力下进行 流量计:用于测量反应物料的流量,确保反应物料的供应和排出 真空泵:用于抽真空,确保反应在无氧环境下进行 冷却器:用于冷却反应物料,确保反应物料的温度在适宜的范围内
聚合反应工程安全 与环保
实验前,确保所有设备、仪器和试剂都经过安全检查 实验过程中,穿戴适当的防护装备,如防护眼镜、手套和口罩 实验结束后,及时清理实验现场,确保无残留物 实验过程中,注意观察反应情况,如有异常,及时采取措施
减少废气排放:采用先进的 废气处理技术,如催化燃烧、 吸附等
废水处理:采用先进的废水 处理技术,如生物处理、膜 处理等
聚合反应工程PPT课 件
汇报人:
目录
添加目录标题
聚合反应工程概述
聚合反应工程基础知 识
聚合反应工程实验技 术
聚合反应工程应用实 例
聚合反应工程前沿技 术与发展趋势
添加章节标题
聚合反应工程概述
聚合反应工程是 研究聚合反应过 程及其控制的一 门学科
聚合反应是指由 单体分子通过化 学反应形成高分 子聚合物的过程
聚合反应工程主 要包括聚合反应 机理、聚合反应 动力学、聚合反 应器设计、聚合 反应过程控制等 方面
聚合反应器讲解
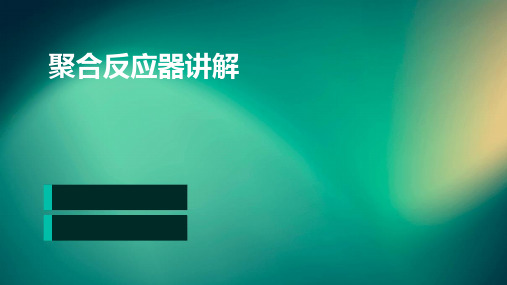
THANKS FOR WATCHING
感谢您的观看
聚合反应器技术的创新与突破
高效能聚合反应器
通过优化反应器的设计,提高聚 合反应的效率,降低能耗和物耗, 实现绿色生产。
聚合反应器智能化
控制
利用人工智能和大数据技术,实 现聚合反应器的智能化控制,提 高生产效率和产品质量。
新型的聚合反应技
术
探索和发展新的聚合反应技术, 如活性聚合、固相聚合等,以适 应高分子材料的多样化和高性能 化需求。
02 聚合反应器的工作原理
聚合反应的原理
聚合反应
指多个小分子通过化学键结合形成大分子的过程。
聚合物的形成
通过重复的链增长和链终止反应,形成高分子量的聚合物。
聚合方式
包括加聚反应和缩聚反应,分别生成碳-碳键和除去小分子。
聚合反应器的操作流程
准备阶段
确保反应器内壁干净、无残留 ,准备好原料和催化剂。
聚合反应器的发展历程
早期阶段
聚合反应器最初的形式为釜式反 应器,以间歇操作为主,规模较
小。
过渡阶段
随着聚合反应技术的发展,连续式 聚合反应器逐渐取代釜式反应器, 实现了聚合反应的连续化、大型化。
现代阶段
随着科技的不断进步,聚合反应器 在技术、材质、设计等方面不断优 化,实现了高效、环保、安全的生 产。
投料阶段
将原料和催化剂按照比例加入 反应器中。
聚合阶段
在一定温度和压力下,原料在 催化剂的后,进行后处理,如 分离、洗涤、干燥等。
聚合反应器的控制要素
温度控制
聚合反应通常需要一定的温度来启动 和维持,控制温度稳定对保证产品质 量和安全性至关重要。
压力控制
聚合过程中,反应器内的压力随反应 进行而变化,需通过调节压力来维持 反应稳定性。
聚合反应器的分类介绍全解
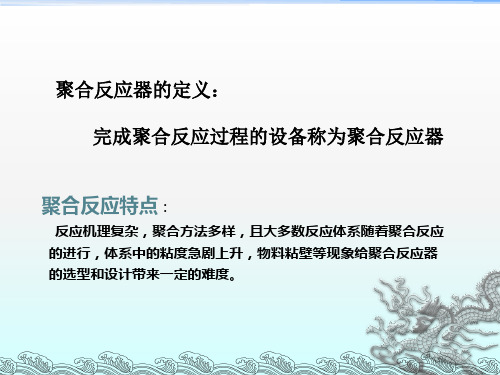
对处理高粘度的聚合体系,如本体聚合或缩聚反应后
期,反应物料的粘度可达500一5000Pa· s,故需采用特殊 型式反应器。该反应器一般采用卧式,主要型式有螺杆型 反应器(如尼龙66的后缩聚反应采用双螺杆)和表面更新型 反应器(如聚酯生产中的后缩聚采用单轴或双轴的表面更 新型圆盘式反应器)。
搅拌釜式反应器
1.管体
是带有夹套的长直圆管,为便于制造安装,常制
成若干段(每段3一5m),各段间用法兰联接。管体顶部可采 用凸形或平板封头,为便于高粘度物料流出,底部多采用锥 形封头。管外装有夹套,内通载热体,管体多采用不锈钢, 夹套可采用普通钢。
管体直径是影响聚合过程的重要因素,在同样聚合温度
和聚合时间下,管径愈小,愈易制取质量均匀、相对粘度较 高的聚合物。这是因为当管径较大时,反应物量增多,引发 剂加入量增多,温度相应增加,低分子物排除困难,并且随
卧式反应器
一、卧式反应器的工作原理 在聚合过程中,有时前后不同阶段物料的特性差异很大, 对反应条件的要求亦不尽相同如聚合前期物料体系粘度低,放 热多,流动较容易,而在聚合后期则往往相反,且希望在反应 进行的同时能去除生成的低分子物,此时在生产中往往采用卧 式反应器。 卧式反应器除需满足一般反应器的要求外,还有以下特殊 要求: 1.物料在反应器内能沿径向充分返混,轴向无返混,尽 量接近平推流。 2.根据聚合动力学理论,为达到预定的聚合度,要尽量 去除体系中生成的小分子,故应在反应器内将反应物料尽可能 展开,形成大面积的薄膜,增加蒸发表面积、且蒸发表面积能 不断更新。
质量,检修时需将釜内物料全部排净。该型式较常用于大型搅拌设备。
3.卧式搅拌反应器
该型式可设臵多个搅拌器,每个搅拌器之间用隔板分开,使物料在反应器 内流动状况类似于多级串联搅拌反应器,从而减少设备台数,降低安装高度。
聚合过程及聚合反应器26页PPT

11、获得的成功越大,就越令人高兴 。野心 是使人 勤奋的 原因, 节制使 人枯萎 。 12、不问收获,只问耕耘。如同种树 ,先有 根茎, 再有枝 叶,尔 后花实 ,好好 劳动, 不要想 太多, 那样只 会使人 胆孝懒 惰,因 为不实 践,甚 至不接 触社会 ,难道 你是野 人。(名 言网) 13、不怕,不悔(虽然只有四个字,但 常看常 新。 14、我在心里默默地为每一个人祝福 。我爱 自己, 我用清 洁与节 制来珍 惜我的 身体, 我用智 慧和知 识充实 我的头 脑。 15、这世上的一切都借希望而完成。 农夫不 会播下 一粒玉 米,如 果他不 曾希望 它长成 种籽; 单身汉 不会娶 妻,如 果他不 曾希望 有小孩 ;商人 或手艺 人不会 工作, 如果他 不曾希 望因此 而有收 益。-- 马钉路 德。
▪
26、要使整个人生都过得舒适、愉快,这是不可能的,因为人类必须具备一种能应付逆境的态度。——卢梭
▪
27、只有把抱怨环境的心情,化为上进的力量,才是成功的保证。——罗曼·罗兰
▪Hale Waihona Puke 28、知之者不如好之者,好之者不如乐之者。——孔子
▪
29、勇猛、大胆和坚定的决心能够抵得上武器的精良。——达·芬奇
▪
30、意志是一个强壮的盲人,倚靠在明眼的跛子肩上。——叔本华
谢谢!
26
《聚合物合成工艺学》复习知识点及思考题

《聚合物合成工艺学》各章重点第一章绪论1.高分子化合物的生产过程及通常组合形式原料准备与精致,催化剂配置,聚合反应过程,分离过程,聚合物后处理过程,回收过程2.聚合反应釜的排热方式有哪些夹套冷却,夹套附加内冷管冷却,内冷管冷却,反应物料釜外循环冷却,回流冷凝器冷却,反应物料部分闪蒸,反应介质部分预冷。
3. 聚合反应设备1、选用原则:聚合反应器的操作特性、聚合反应及聚合过程的特性、聚合反应器操作特性对聚合物结构和性能的影响、经济效应。
2、搅拌的功能要求及作用功能要求:混合、搅动、悬浮、分散作用:1)推动流体流动,混匀物料;2)产生剪切力,分散物料,并使之悬浮;3)增加流体的湍动,以提高传热效率;4)加速物料的分散和合并,增大物质的传递效率;5)高粘体系,可以更新表面,使低分子蒸出。
第二章聚合物单体的原料路线1.生产单体的原料路线有哪些?(教材P24-25)石油化工路线,煤炭路线,其他原料路线(主要以农副产品或木材工业副产品为基本原料)2.石油化工路线可以得到哪些重要的单体和原料?并由乙烯单体可以得到哪些聚合物产品?(教材P24-25、P26、P31)得到单体和原料:乙烯、丙烯、丁烯、丁二烯、苯、甲苯、二甲苯。
得到聚合物:聚乙烯、乙丙橡胶、聚氯乙烯、聚乙酸乙烯酯、聚乙烯醇、维纶树脂、聚苯乙烯、ABS树脂、丁苯橡胶、聚氧化乙烯、涤纶树脂。
3. 合成聚合物及单体工艺路线第三章自由基聚合生产工艺§ 3-1自由基聚合工艺基础1.自由基聚合实施方法及选择本体聚合、乳液聚合、溶液聚合、悬浮聚合。
聚合方法的选择只要取决于根据产品用途所要求的产品形态和产品成本。
2.引发剂及选择方法,调节分子量方法种类:过氧化物类、偶氮化合物,氧化还原体系。
选择方法:(1)根据聚合操作方式和反应温度条件,选择适当分解速度的引发剂。
(2)根据引发剂分解速度随温度的不同而变化,故根据反应温度选择适引发剂。
(3)根据分解速率常数选择引发剂。
- 1、下载文档前请自行甄别文档内容的完整性,平台不提供额外的编辑、内容补充、找答案等附加服务。
- 2、"仅部分预览"的文档,不可在线预览部分如存在完整性等问题,可反馈申请退款(可完整预览的文档不适用该条件!)。
- 3、如文档侵犯您的权益,请联系客服反馈,我们会尽快为您处理(人工客服工作时间:9:00-18:30)。
3.乳液聚合
单体在水介质中,由乳化剂分散成乳液状态进行的
聚合,称为乳液聚合。 乳液聚合是在乳胶粒中进行反应,反应速率高,产 物聚合度高,乳液聚合也是用水作连续相,所以传 热问题也易于解决。但为了稳定乳液,必须在聚合 体系中加入多种配合剂,而又有些配合剂很难从产 物中去除,故乳液聚合的产品适用于制品纯度要求 不高的场合。 乳液聚合时,链自由基处于孤立隔离状态,长链自 由基很难彼此相遇,以致自由基寿命较长,终止速 率较小,因此聚合速率高,且可获得高的分子量。
传热较易,温度容易控制,较少凝胶效应,可以避 免局部过热。 溶液聚合的主要缺点: (1)由于使用溶剂,增加了溶剂的回收与处理设 备; (2)有时溶剂会发生链转移反应,所以产品的分 子量较低: (3)溶剂污染比较严重。
15
4.溶液聚合
选用链转移常数较小的溶剂,容易建立稳态,便于
找出聚合速率、聚合度与单体浓度、引发剂等参数 间的定量关系。 自由基溶液聚合选择溶剂时,须注意两方面的问题。 (1)溶剂的活性 溶剂往往并非绝对惰性,对引发 剂有诱导分解作用,链自由基对溶剂有链转移反应。 (2)溶剂对聚合物溶解性能和对凝胶效应的影响 选用良溶剂时,为均相聚合,如果单体浓度不高, 则有可能消除凝胶效应,遵循正常自由基聚合动力 学规律。选用沉淀剂时,则成为沉淀聚合,凝胶效 应显著。
12
3.乳液聚合
乳液聚合的优点:
(1)以水作分散介质,价廉安全。乳液的粘
度与聚合物分子量及聚合物含量无关,这有 利于搅拌、传热和管道输送,便于连续操作。 (2)聚合速率快,同时产物分子量高,可以 在较低的温度下聚合。 (3)直接采用胶乳的场合,如水乳漆,粘结 剂,纸张,皮革、织物处理剂,以及乳液泡 沫橡胶,更宜采用乳液聚合。
9
2.悬浮聚合
(2)通用性差。只适用于特殊的单体-引发
剂体系。因为悬浮聚合的连续相用水,当使 用的引发剂(或催化剂)遇水会分解时,就 不能采用。
悬浮聚合最常用的反应器为搅拌釜。
10
2.悬浮聚合
悬浮聚合有以下几个优点:
(1)体系粘度低,聚合热容易从粒子经水介
质通过釜壁由夹套冷却水带走,散热和温度 控制比本体聚合、溶液聚合容易得多。产品 分子量及其分布比较稳定。 (2)产品分子量比溶液聚合高,杂质含量比 乳液聚合产品少。 (3)后处理工序比溶液聚合、乳液聚合简单, 生产成本较低,粒状树脂可以直接用来加工。
7
2.悬浮聚合
悬浮聚合是单体以小液滴状悬浮在水中进行的聚合。
单体中溶有引发剂,一个小液滴就相当于本体聚合 的一个单元。从单体液滴转变为聚合物固体粒子, 中间经过聚合物-单体粘性粒子阶段。为了防止粒子 相互粘结在一起,体系中须另加分散剂,以便在粒 子表面形成保护膜。因此悬浮聚合体系一般由单体、 引发剂、水、分散剂四个基本组分组成。 悬浮聚合机理和本体聚合相似,也有均相聚合和沉 淀聚合之分。
强制循环。 为了减轻物料停留在器壁而使传热能力减小,反应 器中装有刮壁装置,轴每转一周,上下的刮片便将 器壁上的聚合物刮掉一次,可以提高传热效率。 此反应器能处理粘度1000Pa.S左右的反应液。
21
1.釜式聚合反应器
22
1.釜式聚合反应器
2)Bethlehem Corp反应器(<100Pa.s)
引发剂外不须加入分散剂、乳化剂等聚合助 剂或溶剂,所以产品的纯度高与其他聚合方 法相比, 工艺流程简单,能耗低,成本低, 对环境的污染小。从反应器的利用率来看, 是所有聚合方法中最高的。
4
1.本体聚合
工业上本体聚合可用间歇法和连续法生产。
生产中关键的问题是反应热的排除。聚合初 期, 转化率不高、体系粘度不大时,散热当 无困难。当转化率提高(如20%-30%)、体 系粘度增大后,散热不易,造成混合、传热 困难,反应情况恶化。如果不能及时带出反 应热,就会使体系温度上升,聚合度下降, 聚合度分布加宽,副反应增加,最后影响到 聚合物的机械强度,严重的则温度失调,引 起爆聚。
1.本体聚合
第二阶段采用的反应器为塔式反应器或特殊
类型的聚合反应器。第二阶段进行薄层聚合, 或以较慢的速度进行。 本体聚合最终因反应前后的温度变化太大 而 使产物的聚合度分布拉宽,产物的性能变差。 从本质上看,本体聚合是一种最简单的聚合 体系,几乎所有的聚合物均可用此法制备, 所以它的通用性很强,有可能发展成为最简 单的工业聚合方法。
33
4.特殊型聚合反应器
在本体聚合和缩聚反应的后期,反应物料的
粘度可达500-1000Pa.s,甚至高达5000Pa.s, 此时上述三类反应器难以适应工艺要求,故 必须使用特殊型聚合反应器,此类反应器主 要用于脱单和后聚合反应器。按反应物料在 反应器内滞留量的大小,可以分为:低滞液 量型反应器和高滞液量型反应器。
16
第二节 聚合反应器
在高分子合成工业中,根据聚合反应体系的
特征和对产品高质量的要求,可以采用多种 型式的聚合反应器。 聚合反应器按其型式可分为釜式、塔式、管 式和特殊型四种。在聚合物产生中约有70% 采用搅拌釜,这是应用最广泛的聚合反应器。 而塔式,特殊型聚合反应器则主要用于高粘 度聚合体系中。
2
第一节 工业聚合方法
聚合方法的选择要考虑的因素: 单体的化学特性 传热方式
聚合物的特性
对产品的质量要求(实现大型化、连续化) 聚合反应器的结构与特性 工业上常用的聚合方法有本体聚合、悬浮聚合、乳
液聚合和溶液聚合。
3
1.本体聚合
本体聚合最大的特点是在聚合过程中,除了
2.塔式聚合反应器
苯乙烯本体聚合塔式反
应器。反应器内物料被 多层搅拌桨缓慢搅动, 以防物料形成沟流,促 进物料形成平推流,并 有助于传热。邻近的桨 叶间有水平的冷却排管 以控制温度。
28
2.塔式聚合反应器
打蛋机型反应器内有两
根带桨叶的搅拌轴,两 轴以相反的方向旋转以 加强搅拌效果。
29
2.塔式聚合反应器
17
1.釜式聚合反应器
釜式聚合反应器是一种形式多变的聚合装置,它广
泛应用于低粘度的悬浮聚合过程,乳液聚合过程。 也能用于高粘度的本体聚合和溶液聚合过程。从操 作方式看它能进行间歇、半连续、单釜和多釜连续 操作,以满足不同聚合过程的要求。为了保证釜中 物料的流动、混合与传热,液滴的分散或固体物料 的均匀悬浮,釜中设有搅拌装置。。 对低粘度系统主要使用平桨式、推进式、涡轮式、 三叶后掠式及布鲁马金式桨叶,当与各类挡板配合 使用时可获得所需的剪切与循环作用。对高粘度体 系主要使用锚式、螺带、带导流筒的螺杆桨叶以及 特殊型式的浆叶。
聚合过程和聚合反应器
第一节
第二节 第三节
工业聚合方法 聚合反应器 聚合反应器选择原则
1
聚合过程及聚合反应器
聚合物生产工业通常由原料准备与精制、引发剂
(催化剂)配制、聚合、分离、后处理及回收等六 个工艺过程组成。聚合物品种不同,生产工艺条件 不同,辅助过程的重要性有所差异,但聚合过程总 是整个工艺过程的核心。而聚合反应器则是核心中 的核心。 采用不同的聚合反应器对聚合产物的结构和性能产 生显著的影响。 不同的聚合反应机理对于单体、引发剂(催化剂) 和反应介质的要求各不一致,所以实现这些聚合过 程要采用不同的聚合方法。
反应器内设有螺杆导流筒,筒外有与螺杆倾
角相反的螺带搅拌桨。 整个反应器用圆盘形挡板分离成两端,挡板 与反应器壁间存在间隙,物料可在各段内分 别循环,并由下至上通过间隙进入另一段。 此反应器也可水平操作,成为卧式反应器。
23
1.釜式聚合反应器(立式)
24
1.釜式聚合反应器(卧式)
25
1.釜式聚合反应器
用于己内酰胺连续缩聚
的VK塔,属于无搅拌 的塔式反应器。塔内装 有多层挡板把塔分割成 多段。由于没有搅拌装 置,使塔中心和塔壁间 的温度差可达数十度, 造成产品质量变差。
30
3.管式聚合反应器
优点:结构简单,单位面积所具有的传热面
大,适用作高温、高压的聚合反应器。 缺点: a.易发生聚合物粘壁现象,造成管子堵塞 b.物料粘度大时,压力损失大 c.由于在管子上长度方向上温度、压力、组 分浓度等反应参数不能保持一致,所以反应 器在流动方向上产生参数分布 因此,管式反应器在聚合物生产中时用较少。
31
3.管式聚合反应器
与管式反应器相似的另一种反应 器是环管式反应器,它在中压法 聚烯烃中得到应用。 两个相互串接的环形管路,并立 在两个垂直的平面内。反应器由 碳钢管、法兰和弯头组成。反应 器内装有轴流泵,使物料在装置 内循环。生成的聚合物经特殊设 计的出料阀借自身的压力排出器 外。为了控制温度,环管外有夹 套,内通冷却介质以移出反应热。 目前环管反应器的容积可达20100m3,管长约为100-150m。
19
1.釜式聚合反应器
釜式聚合反应器最常见的是立式反应器,为了减少
搅拌轴的振动和提高密封性能,将顶伸式搅拌装置 改为底伸式。
顶伸式
底伸式
20
1.釜式聚合反应器
高粘体系采用特殊结构的釜式反应器。 1)Crawford-Russell反应器 反应器采用螺杆+导流筒,使反应物料在釜内进行
18
1.釜式聚合反应器
釜式反应器的除热主要是采用夹套和各种内冷构件
(如蛇管、内冷挡板等)。 在使用内冷件时应注意: A.是否产生物料的混合死角 B.是否会引起物料粘附于器壁 C.构件表面和粒子间的凝集 如果夹套和内冷件不除热时,还可以采用 A.单体或溶剂的蒸发 B.使用物料釜外循环冷却 C.冷进料
釜式反应器的操作条件可在很广的范围内变
化,例如容积可从数立方米0-3Pa .s至上 千Pa .s。