炼油厂含硫污水预处理及综合利用
炼化废水处理技术
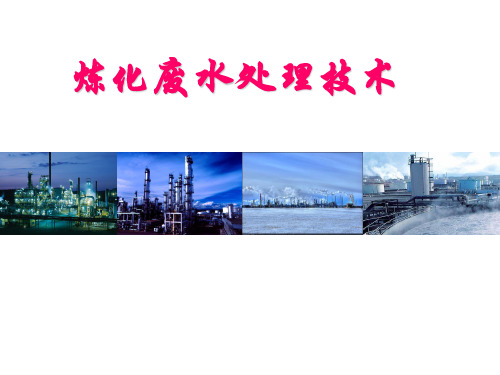
炼化废水分类
低浓度含油废水
水量大,通常为总水量的80%; 污染物浓度较低: 装置产生的低浓度 含油污水
机泵冷却排水 地面冲洗排水 汽包排污水 采样器排水 化验洗涤水蒸汽冷凝水排放 设备放空及清洗排水 办公及其它辅助设施排水等 因装置泄漏等产生的污水
CODcr:500~800mg/L NH3-N:30~50mg/L 硫化物:~ 10mg/L 挥发酚:~ 40mg/L 石油类:300~500mg/L
污染物及处理方法
悬浮油 油(Oil) 分散、乳化油 高氨氮(NH4+-N) 高硫化物 溶解性有机物 (COD、BOD) 低氨氮(NH4+-N) 挥发酚 低硫化物 隔油 浮选、聚结
酸性水汽提
厌氧 生化 缺氧 好氧 普通曝气法 接触氧化法 生物滤池
过滤
悬浮物(SS) 混凝沉淀 气浮
预处理技术
去硫磺回收装置 H2 S 气 脱 气 均 质 储 存
含 硫 污 水
产品碱 精制
碱 洗 污 水
酚、COD 含量高
油 罐 脱 水
油、COD 含量高
原料/成 品油罐
三 泥 滤 液
污水场
油、COD、NH3-N、 酚、S2-等含量很高
COD含量高
水量小污染 物浓度极高
资源浪费; 污水场负荷高、冲击 无法运行; 污染环境。
炼化废水分类 主要高浓度废水 汽提净化水(含硫污水)
水质水量调节破乳沉降除油旋流油水分离浮选净化预处理技术预处理技术20406080100120140160180500010000150002000025000300003500040000450005000055000入口codcr出口codcr20406080100120140160180100020003000400050006000700080009000100001100012000入口油含量出口油含量预处理技术预处理技术集中处理技术集中处理技术炼化废水达标处理工艺轻质油原料沉砂格栅两级隔油生物曝气射流浮选果壳过滤两级浮选废水排放排放排放预处理一级处理二级处理三级处理集中处理技术集中处理技术炼化废水达标处理工艺劣质重油原料多级隔油厌氧酸化两级浮选缺氧a过滤废水排放排放预处理一级处理二级处理三级处理事故污泥回流混凝沉淀炼化废水达标工艺炼化废水达标工艺?乌鲁木齐石化炼油废水处理工艺720含油废水隔油池两级浮选通过25km管线排入485万m的氧化塘炼油废水多级生化炼化废水达标工艺炼化废水达标工艺聚酯废水调节池缺氧酸化池接触氧化池氧化沟沉淀池一沉池两级浮选通过25km管线排入485万m的氧化塘化纤废水达标处理工艺106炼化废水达标工艺炼化废水达标工艺大中型炼化污水处理主体工艺流程应为
炼油厂废水的处理及研究现状

炼油厂废水的处理及研究现状吴勇,周胜(中国市政工程中南设计研究总院有限公司,湖北武汉430010)摘要:近年来中国对废水治理要求日趋严格,诸多地方炼油企业普遍存在处理工艺落后的现象。
为实践节能减排理念、保证国内环保要求,废水处理达标排放已成为了炼油企业重要的环保节能事项。
针对当前国内炼油厂生产的废水现状,文中介绍了含硫废水、含盐废水、碱渣废水等炼油废水的来源和主要污染物,系统论述了炼油企业污水处理厂废水处理现状,即2级和3级处理工艺,并对其研究应用现状进行了分析。
同时,对炼油废水处理趋势和技术路线进行了展望。
关键词:炼油废水;处理工艺;应用现状;趋势与展望中图分类号:X742文献标识码:B文章编号:1671-4962(2023)06-0015-06Treatment and research status of refinery wastewaterWu Yong,Zhou Sheng(Central&Southern China Municipal Engineering Design and Research Institute Co.,LTD,Wuhan430010,China)Abstract:In recent years,the wastewater treatmentrequirements in China have become increasingly strict,and the treatment technologies adopted by many local refineries generally were outdated.In order to practice the concept of energy conservation andemission reduction and ensure domestic environmental protection requirements,wastewater treatment and discharge up to standard had become an important environmental protection and energy saving matter for refineries.In view of the current situation of waste⁃water produced in domestic refineries,this paper introduced the sources and main pollutants of oil refining wastewater such as sulfur wastewater,salt wastewater and alkali slag wastewater,systematically discussed the status quo of wastewater treatment in oil refining wastewater treatment plants(level2and3treatment processes),analyzed the research and application status,and prospected the trend and technical route of oil refining wastewater treatment.Keywords:oil refining wastewater;treatment technology;application status;trend and prospect2016~2022年,中国炼油能力由79.2×108t/a 增至92.4×108t/a,高于美国2022年88.9×108t/a,已跃居为世界第1炼油国。
炼油厂硫磺回收工艺及催化剂的改进和优化

炼油厂硫磺回收工艺及催化剂的改进和优化摘要:本文主要通过对炼油厂硫磺回收工艺及其运行的现状进行分析,来探讨炼油厂硫磺回收工艺及催化剂改进和优化的有效措施,以加强对炼油厂硫磺回收工艺的研究,有效控制炼油厂装置中二氧化硫的排放量,使之符合规定标准,满足我国环境保护政策的要求,从而推动炼油厂的现代化发展,提升经济效益的同时,获取更多的环境效益。
关键词:炼油厂;硫磺回收工艺;催化剂;改进;优化近年来,我国一直致力于环境保护工作,不再以破坏环境为代价来发展经济,越来越重视对污染气体排放的管控,二氧化硫便是其中一项重要管理内容,必须予以高度重视,不容忽视。
随着科学技术的大力发展,有关于环境保护的标准要求也随之改变,有关于石油炼制工业污染排放的规定愈发严格,标准逐渐提高,炼油厂想要取得长远的发展,就应当严格遵循,有效控制装置中的二氧化硫排放量。
为此,炼油厂应当不断地优化硫磺回收工艺及催化剂,控制好二氧化硫的质量浓度,以降低石油炼制所带来的环境污染。
1.炼油厂硫磺回收工艺及其运行现状目前,炼油厂硫磺回收中所采用的是低温水解催化剂,利用低温加氢方式来进行处理。
一级反应器、二级反应器的入口温度,通过热参合换热方式来进行控制。
一级反应器出口高温气体,主要通过电加器辅助加热方式来升温。
现如今,装置酸气中的硫化氢气体主要在百分之五十二左右,烃占有百分之一一点五左右,二氧化碳则占有百分之二十六,氧气占百分之七。
燃烧炉的温度达到了一千一百摄氏度,在监控尾气中二氧化硫的时候,发现其质量浓度一般在每立方米四百至六百毫克[1]。
1.炼油厂硫磺回收工艺及催化剂改进和优化的有效措施1.加强羰基硫水解转化在炼油厂炼油过程中,为了提高硫磺回收工艺水平,减少二氧化硫的排放,应当加强羰基硫水解转化,可从以下方面着手:首先,需要在一反装填充钛基催化剂,催化剂的剂量需要根据反应器的体积大小来确定,一般为反应器的二分之一,或是二分之三,入口温度要符合规定要求。
废水排放预处理管理标准

废水排放预处理管理标准精品汇编资料废水排放预处理管理标准1目的加强和规范炼油厂废水排放与预处理的管理;通过废水的预处理和循环利用;尽可能提高净化污水回用量;减少排污;节约新水;防止环境污染..2范围本标准适用于炼油厂所属各单位..3职责3.1本标准归口安全环保科管理;安全环保科负责本标准的制定、修订..负责废水排放、预处理的管理..3.2总值班室负责异常及紧急状态下废水排放的协调与安排;并组织净化污水的回用工作..3.3技术科应积极推行清洁生产;采用低污染或无污染的清洁生产工艺;合理利用资源和能源减少对环境的影响;负责组织净化污水回用工作的攻关及回用计划的实施..3.4机动科负责环保预处理设施的管理;日常检修、维护与保养具体按设备全过程管理标准执行..3.5厂办负责全厂绿化工作的管理;协调与安排总厂生活服务公司生产服务中心炼油厂绿化环卫队节约新水;使用净化污水绿化厂区..4管理内容和要求4.1废水分类及分布4.1.1含油污水:一车间、常减压、重催、芳烃、加氢精制、焦沥、化工、中心化验室、公用工程一、公用工程二车间生产及油品销售、油品车间洗罐等产生的主要含石油类、硫化物、氨氮等的生产废水..4.1.2含盐污水:一车间、常减压、重催、加氢精制车间油品碱洗或洗罐;公用工程一车间循环水换水等产生的主要含碱、石油类、硫化物、氨氮等的生产废水..4.1.3含硫污水:一车间、常减压、重催、加氢精制、焦沥、芳烃车间生产过程产生的主要含硫化物、氨氮等的生产废水..4.1.4化验废水:中心化验室、公用工程一车间循环水化验室产生的主要含样品、药品、化学药剂的废水..4.1.5生活污水:炼油厂所属办公系统产生的生活污水及厂区澡堂、食堂排放的污水..4.2废水预处理4.2.1各单位应实行清污分流的原则;节约用水;减少排污;在适应工艺及设备要求的情况下减少新水用量;改用净化污水或一水多用..4.2.2技术科应结合各车间实际情况;制定各车间污水回用计划;提高净化污水回用率..4.2.3安环科应对废水排放及预处理进行管理;正常生产时排放污水应达到分级控制规定的排放指标..4.2.4各车间无权随意增加污水排放口或排放点;严禁无组织排放..4.2.5含油污水的预处理1)一车间、焦沥、化工、加氢精制、油品销售、中心化验室、公用工程一、公用工程二车间产生的含油污水通过装置的含油污水排污管线汇往净化水厂炼油工段含油污水系统进行处理..2)常减压、重催、芳烃、油品车间的含油污水通过各车间的隔油池预处理后汇往净化水厂炼油工段含油污水系统进行处理..3)对于含油污水的隔油预处理执行各车间环境管理与作业规程..4.2.6含盐污水的预处理一车间、常减压、重催、加氢精制、公用工程一车间产生的含盐污水通过装置的含盐污水排污管线汇往净化水厂炼油工段含盐污水系统进行处理..4.2.7含硫污水的预处理一车间、常减压、重催、焦沥、加氢精制、芳烃车间生产过程产生的含硫污水直接汇集通过密闭管线排入炼油厂加氢精制车间的污水汽提装置;经脱硫、脱氨后的净化污水部分用于一车间、常减压、重催等装置的回用;剩余的净化污水排入净化水厂炼油工段含盐污水系统或含油污水系统进行处理..具体执行加氢精制车间污水汽提装置的操作规程..4.2.8化验废水的处理分析化验过程多余的分析油样由各岗位收集倒入指定的容器;统一回收利用..具体执行取样油、回收油管理标准..1)化验分析时产生的强酸强碱废液经岗位中和处理后倒入下水系统;防止下水系统腐蚀;大量的强酸强碱废液亦可用容器收集后填写“废弃物排放申报单”一式叁份;报安全环保科和净化水厂;经许可后倒入指定的废渣场..2)化验分析时产生的强氧化剂、有毒溶液要经还原及无毒化处理后排入下水系统;大量的废液用容器收集后填写“废弃物排放申报单”一式叁份;报安全环保科和净化水厂;经许可后倒入指定的废渣场..3)化验分析时产生的浊度低、毒性小的废溶液及清洗水直接排入下水系统..4.2.9生活污水的预处理各单位办公系统的生活污水、厂区澡堂、食堂排放的污水直接排入净化水厂炼油工段生活污水系统进行处理..4.3废水排放4.3.1各车间含油污水和含盐污水达到炼油厂分级控制标准后排放..4.3.2加氢精制车间净化污水达到工艺卡片标准后排放..4.4污水回用4.4.1夏季净化水厂处理后的净化污水回用于厂区绿化..4.4.2加氢精制车间污水汽提装置预处理后的净化污水回用于生产装置.. 4.4.3净化污水只能用于浇灌非食用性经济作物;不得饮用和灌溉食用农作物..4.5地下排污系统的管理4.5.1地下排污系统必须保证畅通、无杂物..严禁因绿化、施工覆盖下水井..4.5.2各车间负责对管理区域内出装置界区第一个下水井前的工业污水、生活污水阴井进行明确标识;检查维护;并做好相关记录..记录见各车间的周检表..4.5.3安全环保科负责炼油厂管理区域地下排污系统的监督管理、检查和维护..4.5.4安全环保科负责对污水排放系统存在的缺陷提出技改方案;并报机动科或技术科审核后对其进行技术改造..4.5.5装置异常状态下;如跑油、冒罐等;具体按装置异常状态环境保护管理标准执行;紧急情况下不可抗力因素造成的污水排放按应急状态处理;具体按应急管理标准执行..4.6分级控制废水排放指标见附录A..4.7废水排放的监测和监督管理4.7.1安全环保科负责设置各车间废水监测采样点;制定炼油厂分级控制废水排放监测委托计划;并监督环境监测部门实施..4.7.2安全环保科负责将污水分析报告单反馈给各车间;并对存在的问题监督有关车间整改..4.7.3各车间接到污水分析报告单后要认真分析原因;对于偶然性超标;当时即可采取预防与纠正措施的填写车间外排污水监测不合格分析跟踪记录见附录B;对于连续性超标;具体按纠正与预防措施管理标准执行..5相关记录5.1J73--226--2002环境保护技术经济指标月报安全环保科填报5.2J73--234--2002工业企业污染物排放季报表季报安全环保科填报5.3J73--235--2002年度排污申报表安全环保科填报5.4J73--236--2002环境统计报表年报安全环保科填报5.5J73--237--2002污染源监测季度报表安全环保科填报5.6J73--238--2002300家重点工业污染源监测季报表安全环保科填报5.7J73--216--2002公司环境监测日报表安全环保科使用5.8J73--217--2002公司污水监测抽查报表安全环保科使用5.9LJ73--001--2002月环保计划统计表安全环保科填写5.10LJ73--002--2002环保综合统计月报表相关车间填报5.11LJ73--003--2002车间外排污水监测不合格分析跟踪记录相关车间填报J6903--001--2002净化水厂工业废水分析数据报表相关车间、安全环5.12JH保科使用6相关文件6.1Q/SYWHL4513--2002环境监测管理标准6.2Q/SYWHL4509--2002环境标识管理标准6.3Q/SYWHL3905--2002生产运行控制标准6.4Q/SYWHL4518--2002装置异常状态环境保护管理标准6.5Q/SYWHL3913--2002应急管理标准6.6Q/SYWHL3913--2002取样油、回收油管理标准6.7Q/SYWHL4201--2002设备全过程管理标准。
炼油厂 含硫污水 汽提塔 流程
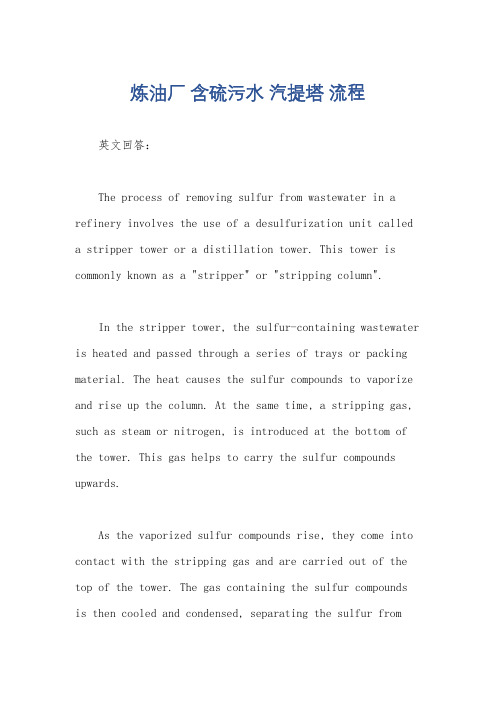
炼油厂含硫污水汽提塔流程英文回答:The process of removing sulfur from wastewater in a refinery involves the use of a desulfurization unit called a stripper tower or a distillation tower. This tower is commonly known as a "stripper" or "stripping column".In the stripper tower, the sulfur-containing wastewater is heated and passed through a series of trays or packing material. The heat causes the sulfur compounds to vaporize and rise up the column. At the same time, a stripping gas, such as steam or nitrogen, is introduced at the bottom of the tower. This gas helps to carry the sulfur compounds upwards.As the vaporized sulfur compounds rise, they come into contact with the stripping gas and are carried out of the top of the tower. The gas containing the sulfur compounds is then cooled and condensed, separating the sulfur fromthe gas. The separated sulfur can be further processed or disposed of properly.The stripped wastewater, now free of sulfur compounds,is collected at the bottom of the tower and sent forfurther treatment or discharge. This process of stripping sulfur from wastewater helps to reduce the environmental impact of sulfur-containing effluents.中文回答:炼油厂中除去含硫污水的流程涉及使用一种称为汽提塔或蒸馏塔的脱硫装置。
含硫污水的有效处理
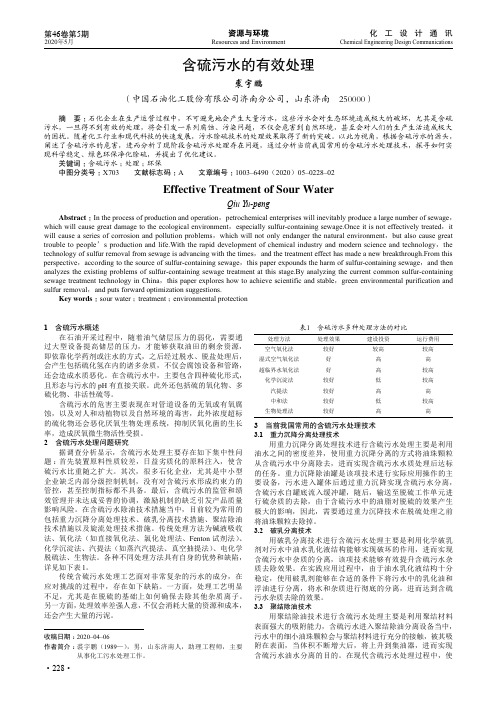
资源与环境化 工 设 计 通 讯Resources and EnvironmentChemical Engineering Design Communications·228·第46卷第5期2020年5月1 含硫污水概述在石油开采过程中,随着油气储层压力的弱化,需要通过大型设备提高储层的压力,才能够获取油田的剩余资源,即依靠化学药剂或注水的方式,之后经过脱水、脱盐处理后,会产生包括硫化氢在内的诸多杂质,不仅会腐蚀设备和管路,还会造成水质恶化。
在含硫污水中,主要包含四种硫化形式,且形态与污水的pH 有直接关联。
此外还包括硫的氧化物、多硫化物、非活性硫等。
含硫污水的危害主要表现在对管道设备的无氧或有氧腐蚀,以及对人和动植物以及自然环境的毒害,此外浓度超标的硫化物还会恶化厌氧生物处理系统,抑制厌氧化菌的生长率,造成厌氧微生物活性受损。
2 含硫污水处理问题研究据调查分析显示,含硫污水处理主要存在如下集中性问题:首先装置原料性质较差,日益劣质化的原料注入,使含硫污水比重随之扩大。
其次,很多石化企业,尤其是中小型企业缺乏内部分级控制机制,没有对含硫污水形成约束力的管控,甚至控制指标都不具备。
最后,含硫污水的监管和绩效管理并未达成妥善的协调,激励机制的缺乏引发产品质量影响风险。
在含硫污水除油技术措施当中,目前较为常用的包括重力沉降分离处理技术、破乳分离技术措施、聚结除油技术措施以及旋流处理技术措施。
传统处理方法为碱液吸收法、氧化法(如直接氧化法、氯化处理法、Fenton 试剂法)、化学沉淀法、汽提法(如蒸汽汽提法、真空抽提法)、电化学脱硫法、生物法。
各种不同处理方法具有自身的优势和缺陷,详见如下表1。
传统含硫污水处理工艺面对非常复杂的污水的成分,在应对挑战的过程中,存在如下缺陷。
一方面,处理工艺明显不足,尤其是在脱硫的基础上如何确保去除其他杂质离子。
另一方面,处理效率差强人意,不仅会消耗大量的资源和成本,还会产生大量的污泥。
石油炼制过程硫及氮资源化回收技术探析

石油炼制过程硫及氮资源化回收技术探析摘要:原油中硫、氧、氮、碳、氢形成的硫化物、氮化物、氧化物、胶质等非烃类化合物约占10~20%,对原油加工的安全、环境、产品质量等有很大影响。
本文分析了石油炼制过程硫及氮资源化回收技术。
关键词:石油炼制;硫;氮;资源化硫、高氮原油的加工带来了新的环保问题,需采取多种措施使其废气、污水排放达到《石油化工企业污染物排放标准》要求,或满足项目所在地污染物排放限值要求。
国家对环保提出了更严格的要求,提高了原油中硫、氮资源的回收率,减少硫氧化物等气体污染物及氨氮等液体污染物的排放,从而最大限度地回收原油中的硫、氮资源。
降低原油加工损耗率,也是节能减排和环保的客观要求。
一、炼化企业主要含硫及氮尾气处理技术1、硫化氢回收技术1)酸性水汽提。
其是以上游工艺装置的含硫污水为原料的集中处理装置,常用的工艺有单塔常压汽提工艺、单塔加压侧线抽氨工艺和双塔加压汽提工艺。
单塔常压汽提工艺产品为净化水及酸性气,单塔加压侧线抽氨工艺与双塔加压汽提工艺产品为净化水、酸性气、液氨。
2)溶剂再生。
它采用上游生产装置脱硫单元(包括循环氢、加氢低分气、干气、液化石油气等脱硫单元)产生的脱硫富胺液为原料,脱硫富胺液采用集中再生处理,主要产品为贫胺液,副产高浓度HS酸性气。
通常采用常规蒸汽加热再2生工艺。
2、二氧化硫回收技术1)可再生湿法烟气脱硫。
该技术可脱除烟气中的二氧化硫,回收高浓度二氧化硫,可直接用于生产液体二氧化硫或硫酸,也可与硫磺回收装置联合生产工业硫磺。
介绍了自主研发的Rasoc工艺等多种可再生湿法烟气脱硫技术,Rasoc工艺是一种资源化(回收)烟气脱硫技术,采用高选择性的专用LAS吸收剂从烟气中回收高浓度SO2酸性气,富吸收剂再生后循环利用,可在多套烟气脱硫装置中实现富吸收剂的集中再生,适用于高质量浓度二氧化硫(大于3000mg/m3)的烟气净化。
2)活性焦干法烟气脱硫。
活性焦烟气处理技术是一种资源(回收)烟气脱硫技术,利用活性焦的吸附催化作用脱除烟气中的SOx、NOx、烟尘,回收利用硫资源。
炼油企业工艺废水分质处理和循环利用
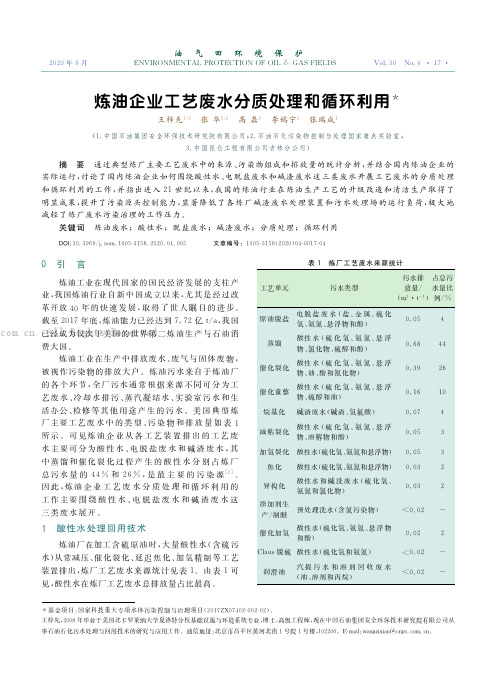
*基金项目:国家科技重大专项水体污染控制与治理项目(2017ZX07402 002 02)。
王梓先,2008年毕业于美国北卡罗莱纳大学夏洛特分校基础设施与环境系统专业,博士,高级工程师,现在中国石油集团安全环保技术研究院有限公司从事石油石化污水处理与回用技术的研究与应用工作。
通信地址:北京市昌平区黄河北街1号院1号楼,102206。
E mail:wangzixian@cnpc.com.cn。
炼油企业工艺废水分质处理和循环利用*王梓先1,2 张华1,2 高磊3 李嫣宁1 张瑞成1(1.中国石油集团安全环保技术研究院有限公司;2.石油石化污染物控制与处理国家重点实验室;3.中国昆仑工程有限公司吉林分公司)摘 要 通过典型炼厂主要工艺废水中的来源、污染物组成和排放量的统计分析,并结合国内炼油企业的实际运行,讨论了国内炼油企业如何围绕酸性水、电脱盐废水和碱渣废水这三类废水开展工艺废水的分质处理和循环利用的工作,并指出进入21世纪以来,我国的炼油行业在炼油生产工艺的升级改造和清洁生产取得了明显成果,提升了污染源头控制能力,显著降低了各炼厂碱渣废水处理装置和污水处理场的运行负荷,极大地减轻了炼厂废水污染治理的工作压力。
关键词 炼油废水;酸性水;脱盐废水;碱渣废水;分质处理;循环利用DOI:10.3969/j.issn.1005 3158.2020.04.005 文章编号:1005 3158(2020)04 0017 040 引 言炼油工业在现代国家的国民经济发展的支柱产业,我国炼油行业自新中国成立以来,尤其是经过改革开放40年的快速发展,取得了世人瞩目的进步。
截至2017年底,炼油能力已经达到7.72亿t/a,我国已经成为仅次于美国的世界第二炼油生产与石油消费大国。
炼油工业在生产中排放废水、废气与固体废物,被视作污染物的排放大户。
炼油污水来自于炼油厂的各个环节,全厂污水通常根据来源不同可分为工艺废水、冷却水排污、蒸汽凝结水、实验室污水和生活办公、检修等其他用途产生的污水。
《2024年油田含油污水处理及回用技术》范文

《油田含油污水处理及回用技术》篇一一、引言随着油田开采的深入,油田含油污水处理问题日益突出。
含油污水的处理不仅关系到油田的正常生产,也直接影响到环境质量。
因此,研究和应用高效的含油污水处理及回用技术,对保障油田可持续发展和环境保护具有重要意义。
本文将重点介绍油田含油污水处理及回用技术的现状、处理流程、技术应用和未来发展方向。
二、油田含油污水处理现状当前,油田含油污水处理面临着诸多挑战。
含油污水中含有大量的油、悬浮物、重金属等有害物质,若直接排放将严重污染环境。
然而,传统的处理方法往往存在处理效率低、能耗高、成本高等问题。
因此,研发高效、低耗、环保的含油污水处理技术已成为当前的研究热点。
三、含油污水处理流程1. 预处理阶段:预处理阶段主要包括隔油池和初级处理设备,用于去除污水中的大颗粒油珠和悬浮物。
隔油池通过重力分离原理,使油珠上浮至水面,便于后续处理。
2. 深度处理阶段:深度处理阶段主要采用物理、化学和生物等方法,进一步去除污水中的油、悬浮物和重金属等有害物质。
常用的技术包括吸附法、氧化法、生物法等。
3. 回用处理阶段:经过深度处理的污水,根据需要可进行回用处理。
回用处理主要包括水质稳定处理和精细过滤等工艺,以提高回用水质,满足特定回用需求。
四、技术应用1. 物理法:物理法主要包括重力分离法、吸附法等。
重力分离法通过油和水的密度差异实现分离;吸附法则利用吸附剂吸附污水中的有害物质,如活性炭等。
2. 化学法:化学法主要采用混凝法、氧化还原法等。
混凝法通过向污水中投加混凝剂,使污染物凝聚成大颗粒便于分离;氧化还原法则通过氧化剂或还原剂破坏污染物的化学结构,降低其危害性。
3. 生物法:生物法主要包括生物膜法、活性污泥法等。
生物膜法利用微生物在生物膜上的生长和代谢作用去除污染物;活性污泥法则利用活性污泥中的微生物吸附和降解有机物。
五、未来发展方向1. 高效低耗技术:研发高效低耗的含油污水处理技术,降低能耗和成本,提高处理效率。
炼油厂污水处理流程

炼油厂污水处理流程炼油厂是一个需要处理大量废水的工业设施。
废水处理是炼油厂保护环境和履行社会责任的重要环节。
在这篇文章中,我们将详细介绍炼油厂污水处理的流程。
1. 污水收集和预处理- 炼油厂污水来源于多个环节,包括冷却水、洗涤废水和生产过程中产生的废水等。
这些废水需要通过管道系统进行收集。
- 在进入污水处理系统之前,废水需要经过初步处理,例如固体分离、调节pH值等,以减少对后续处理设备的负担。
2. 沉淀池- 污水处理系统的第一步是将废水引入沉淀池。
在这个过程中,污水中的悬浮颗粒物会沉淀到底部,形成污泥。
- 沉淀池还可以通过空气进气系统提高氧气的溶解度,促进底部沉淀物中的微生物降解有机废物。
3. 污泥处理- 沉淀池收集到的污泥需要进行处理。
首先,污泥会通过离心分离器进一步去除水分,减少体积。
- 离心分离后的污泥会被送往污泥浓缩池,通过加入化学药剂,将污泥中的水分进一步去除,使其在体积上更加集中。
4. 活性污泥系统- 活性污泥系统是炼油厂常用的废水处理工艺。
它使用微生物处理有机废物。
活性污泥系统一般包括活性污泥池、曝气系统和沉淀池。
- 活性污泥池是微生物的培养基,其中的微生物会分解和降解废水中的有机物质。
- 曝气系统为微生物提供充足的氧气,促进微生物的活动。
曝气系统通常包括潜水泵、曝气管和增氧机等设备。
- 沉淀池用于沉淀处理后的废水,以便去除活性污泥和悬浮物。
5. 膜处理- 膜技术是现代炼油厂污水处理的一种常用方法。
它使用特殊的膜过滤器将废水分离成纯水和浓缩废物。
- 膜过滤器可以有效地去除细菌、病毒和悬浮颗粒等微小颗粒。
- 分离后的纯水可以重复使用或进一步处理,而浓缩废物则需要进行安全处理,以避免对环境造成污染。
6. 消化池和沼气收集- 在污水处理过程中,污泥可以进一步处理以回收能源。
这一步通常涉及到消化池和沼气收集系统。
- 污泥会被送入消化池,通过生物分解产生沼气。
沼气可以被收集并用作燃料或发电。
炼油厂污水处理综合措施

炼油厂污水处理综合措施炼油厂是一种能源生产和深加工企业,其生产过程可能会产生大量的废水。
因此,炼油厂的污水处理是非常必要的。
在此,我将提出炼油厂污水处理的综合措施。
1. 生产过程中污水预处理炼油厂的生产过程会产生大量的废水,因此,在污水放入污水处理系统之前,需要进行初步预处理。
这些预处理措施包括:- 油水分离器:炼油厂废水中经常含有一定量的轻油和重油,使用油水分离器可以将这些油分离出来,减轻后续处理的负担。
- 细菌过滤器:在某些情况下,炼油厂的废水中含有许多微生物,使用细菌过滤器可将其过滤掉,使后续的处理更加有效。
- 混凝剂投加:使用混凝剂能够使废水中的悬浮物聚集在一起,便于后续处理的固液分离。
2. 废水处理过程为了有效地处理炼油厂废水,可以采用以下废水处理技术:- 生化法:生物法是一种通过使用微生物来分解和去除废水中的有机化合物的方法。
这种方法特别适合于高浓度废水的处理。
生化池和活性污泥法是应用广泛的两种生物法。
- 化学凝聚法:化学凝聚法是一种通过将废水中的污染物凝聚在一起而移除它们的方法。
这种方法适用于处理低浓度的污水。
- 膜法:膜法是一种通过将废水通过膜过滤来移除其中的污染物的方法。
这种方法适用于高浓度废水的处理。
3. 净化技术污水处理后,仍有一些难以分解或去除的污染物,比如重金属等。
因此,需要再次进行净化处理。
- 活性炭吸附:活性炭是一种吸附介质,可以使废水中的有机化合物和重金属吸附在表面。
这种方法适用于低浓度污水的净化。
- 沉淀法:对于含有重金属污染物的废水,可以使用化学沉淀将重金属沉淀出来以净化废水。
炼油厂污水处理的综合措施包括预处理、污水处理和净化技术。
采用这些方法,可以有效地净化炼油厂产生的废水,降低其对环境的影响。
石油石化废水处理方法
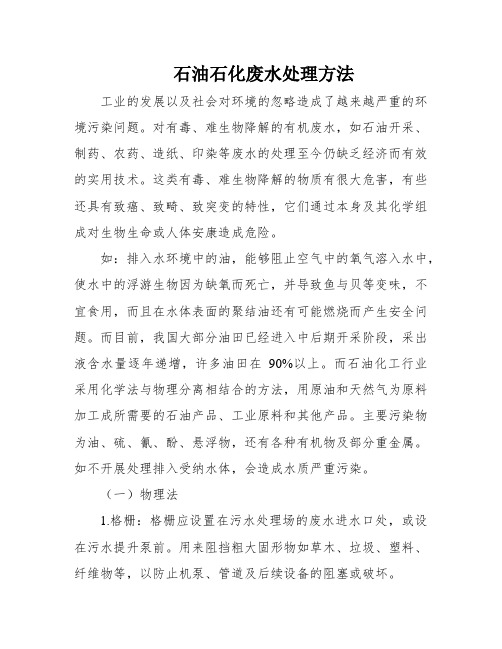
石油石化废水处理方法工业的发展以及社会对环境的忽略造成了越来越严重的环境污染问题。
对有毒、难生物降解的有机废水,如石油开采、制药、农药、造纸、印染等废水的处理至今仍缺乏经济而有效的实用技术。
这类有毒、难生物降解的物质有很大危害,有些还具有致癌、致畸、致突变的特性,它们通过本身及其化学组成对生物生命或人体安康造成危险。
如:排入水环境中的油,能够阻止空气中的氧气溶入水中,使水中的浮游生物因为缺氧而死亡,并导致鱼与贝等变味,不宜食用,而且在水体表面的聚结油还有可能燃烧而产生安全问题。
而目前,我国大部分油田已经进入中后期开采阶段,采出液含水量逐年递增,许多油田在90%以上。
而石油化工行业采用化学法与物理分离相结合的方法,用原油和天然气为原料加工成所需要的石油产品、工业原料和其他产品。
主要污染物为油、硫、氰、酚、悬浮物,还有各种有机物及部分重金属。
如不开展处理排入受纳水体,会造成水质严重污染。
(一)物理法1.格栅:格栅应设置在污水处理场的废水进水口处,或设在污水提升泵前。
用来阻挡粗大固形物如草木、垃圾、塑料、纤维物等,以防止机泵、管道及后续设备的阻塞或破坏。
2.沉淀:沉淀池一般分为平流式、竖立式、辅流式和斜板式沉淀池。
初次沉淀池作为一级处理,是生物处理的预处理设施,在此,将污水中密度较大的悬浮物开展沉淀分离的主要设施。
石油企业常采用沉淀池或沉降罐处理钻井和采油废水,去除其中的悬浮固体物质。
二次沉淀池是生物处理过程必不可少的修建物,在石化企业的污水处理场得到了广泛的采用。
主要是用来去除生物处理过程中发生的污泥,从而得到澄清的处理水,同时为生物处理设备供给一定浓度的回流污泥。
1.隔油:隔油处理主要用于去除含油污水中的悬浮和粗分散油,所以在石油化工业中应用较广,特别是采油废水处理中将隔油装置作为核心设备。
隔油装置一般分为平流式、斜板式和平流斜板组合式三种。
石油开采废水处理一般采用隔油罐,石化废水处理采用隔油池。
炼焦行业脱硫废液产生与利用处置

炼焦行业脱硫废液产生与利用处置摘要:炼焦行业每年产生大量高毒、高腐蚀性、难以被降解的脱硫废液,脱硫废液属于《国家危险废物名录》中的危险废物,含有大量可回收利用的无机盐,也可通过高温燃烧裂解氧化制取硫酸,提盐和制酸是脱硫废液污染防治的达标可行技术和先进技术。
阐述了脱硫废液产生节点和污染特征,分析了脱硫废液利用和处置的主要方式以及存在的问题,针对性的提出了脱硫废液掺煤炼焦、提盐和制酸综合利用的对策建议,可对脱硫废液进行精准管控从而防范环境风险,也对提高脱硫废液的综合利用率有一定的指导作用,还可促进钢铁和炼焦行业的健康发展。
关键词:炼焦行业;脱硫废液;产生;利用;处置1炼焦行业脱硫废液产生与利用处置现状1.1处理技术不成熟在炼焦行业的脱硫废液处理中,存在许多技术难题和技术瓶颈,其中最为突出的问题是处理技术不成熟。
当前,传统的处理方法主要包括化学沉淀法、中和沉淀法和活性炭吸附法等,这些方法虽然已经得到了广泛应用,但是在处理效率、质量和成本方面仍然存在很大的提升空间。
此外,由于脱硫废液的组成比较复杂,其成分之间的相互作用和反应机制也很复杂,因此传统的处理方法往往无法很好地满足废液处理的需求。
另外,随着国家环境保护政策的日益严格,炼焦行业对脱硫废液的处理要求也越来越高,传统的处理技术已经难以满足这种需求。
例如,新颁布的《大气污染防治法》要求企业要对废气进行治理,同时对废水的排放也提出了严格的要求。
这使得炼焦行业需要更加先进、高效、安全和环保的废液处理技术,以达到国家的环保标准。
因此,炼焦行业需要加强技术研发,探索新型的废液处理技术。
目前,国内外已经出现了许多新型的处理技术,例如膜分离技术、生物技术等,这些技术能够更好地满足废液处理的需求,同时也有助于提高处理效率和质量,降低处理成本,并且能够更好地保护环境。
因此,炼焦行业需要加大技术创新力度,积极推广和应用新型的处理技术,以实现废液的高效、安全和环保处理。
1.2资源利用率低炼焦行业的脱硫废液中含有大量的硫酸盐和氨氮等有机物质,这些有机物质具有较高的化学活性和营养价值,可以被利用。
炼油废水处理再利用技术论文

炼油废水处理再利用技术的分析与研究摘要:炼油工业废水主要来自于原油的直接蒸馏、重质油的裂化与蒸馏以及某些馏分的精制等过程中产生的生产废水。
一般是根据废水水质进行分类分流的,包括游离态含油废水、乳化油废水、冷却水、锅炉排水、含硫废水、含碱废水、含酸废水以及一些特殊化合物废水等。
通过对工业废水进行处理,可以达到回收再利用的效果。
关键词:炼油废水处理分析一、简要概况炼油废水主要有含油废水和含碱废水组成,水呈碱性,ph在7.5~8.0含油在100~200mg/l。
开展炼油废水处理成油田同工业用水的研究,将前者只在炼厂内部按技术要求,利用现有设施作简单预处理进行重复利用,既具有经济效益,又具有社会效益。
二、炼油废水产生的机理与特点炼油工业废水主要来自于原油的直接蒸馏、重质油的裂化与蒸馏以及某些馏分的精制等过程中产生的生产废水。
一般是根据废水水质进行分类分流的,包括游离态含油废水、乳化油废水、冷却水、锅炉排水、含硫废水、含碱废水、含酸废水以及一些特殊化合物废水等。
其特点体现在:1.粒径介于100~1000nm的微小油珠易被表面活性剂和疏水固体所包围,形成乳化油,稳定地悬浮于水中,这种状态的油不能用静置法从废水中分离出来。
而大于100μm的呈悬浮状态的可浮油,可以依靠油水相对密度差从水中分离出来。
2.油类污染物排入水体后会形成一层分子膜,污染水体的水质,使水中溶解氧(do)含量下降,并且生成co2,形成h2co3,使ph 值下降,浊度增加。
1)污水量大,废水组分复杂,有机物特别是烃类及其衍生物含量高,并且含有多种重金属。
3.除一般有机物外,主要的污染物还有油脂、酚类、硫化物和氨氮等,其cod含量较高,难降解物质多,而且受碱渣废水和酸洗水的影响,废水的ph变化较大。
三、水处理方案尽管水中都以富含油品为主要特征,但在ph值、矿化度、含油总量、乳化程度、硫化物含量等方面,均存在一定差异。
回收与排放,对水质的要求也不同,炼油废水作为工业水再利用工艺,将不同于作为排放时的处理工艺。
石油炼制生产废水的类别及其对应的处理方式
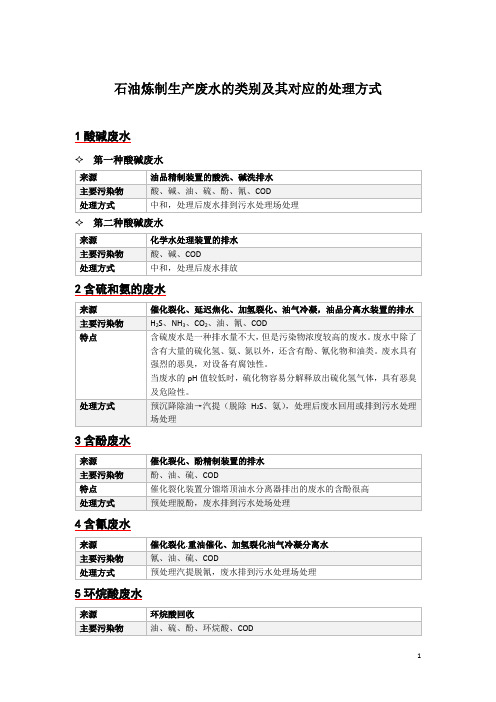
油、SS等
处理方式
在装置预隔油后,均匀排到污水处理场处理
14油轮压舱水
来源
油品运输油船压舱水
主要污染物
油
处理方式
经隔油或隔油浮选后排放
15生活污水
来源
生活辅助设施办公、食堂、浴室等
主要污染物
杂质、BOD5、COD等
处理方式
排到污水处理场处理
16假定净水
来源
末受污染的工业水,无组织排放地面雨水
来源
环烷酸回收
主要污染物
油、硫、酚、环烷酸、COD
处理方式
预处理回收环烷酸,废水排到污水处理场处理
6含氟废水
来源
烷基化氟化钙沉淀池
主要污染物
氟、氟化钙、COD
处理方式
装置内预处理沉淀除渣后排到污水处理场处理
7冷焦和切焦废水
来源
延迟焦化除焦废水
主要污染物
油、焦粉、COD
处理方式
装置内隔油、沉淀、过滤后闭路循环使用
石油炼制生产废水的类别及其对应的处理方式
1酸碱废水
第一种酸碱废水
来源
油品精制装置的酸洗、碱洗排水
主要污染物
酸、碱、油、硫、酚、氰、COD
处理方式
中和,处理后废水排到污水处理场处理
第二种酸碱废水
来源
化学水处理装置的排水
主要污染物
酸、碱、COD
处理方式
中和,处理后废水排放
2含硫和氨的废水
来源
催化裂化、延迟焦化、加氢裂化、油气冷凝,油品分离水装置的排水
12含油含盐废水
来源
原油电脱盐脱水罐排水;生产环烷酸盐类的排水;循环水排污水
主要污染物
油、硫、酚、氰、COD、BOD5、氨氮、盐类、水质稳定剂
炼油厂含硫污水处理副产品——氨水的综合利用
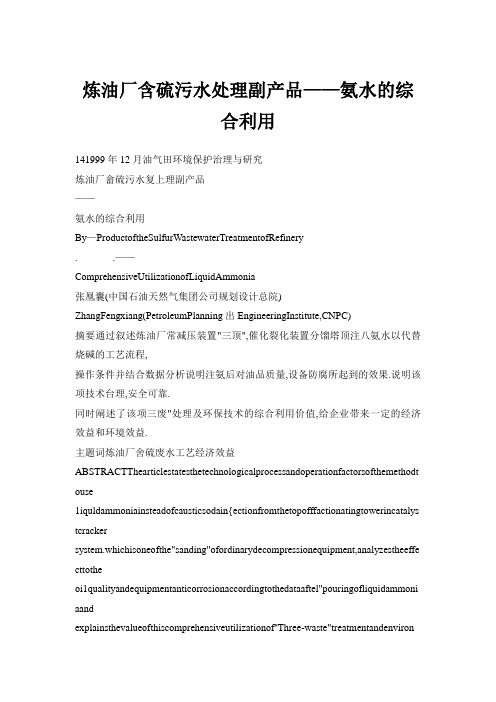
炼油厂含硫污水处理副产品——氨水的综合利用141999年12月油气田环境保护治理与研究炼油厂畲硫污水复上理副产品——氨水的综合利用By—ProductoftheSulfurWastewaterTreatmentofRefinery._______.——ComprehensiveUtilizationofLiquidAmmonia张凰囊(中国石油天然气集团公司规划设计总院)ZhangFengxiang(PetroleumPlanning出EngineeringInstitute,CNPC)摘要通过叙述炼油厂常减压装置"三顶",催化裂化装置分馏塔顶注八氨水以代替烧碱的工艺流程,操作条件并结合数据分析说明注氨后对油品质量,设备防腐所起到的效果.说明该项技术台理,安全可靠.同时阐述了该项三废"处理及环保技术的综合利用价值,给企业带来一定的经济效益和环境效益.主题词炼油厂舍硫废水工艺经济效益ABSTRACTThearticlestatesthetechnologicalprocessandoperationfactorsofthemethodt ouse1iquldammoniainsteadofcausticsodain{ectionfromthetopofffactionatingtowerincatalys tcrackersystem.whichisoneofthe"sanding"ofordinarydecompressionequipment,analyzestheeffe cttotheoi1qualityandequipmentanticorrosionaccordingtothedataaftel"pouringofliquidammoni aandexplainsthevalueofthiscomprehensiveutilizationof''Three-waste"treatmentandenvironmentprotectiontechnology.Themethodcanbringeconomicandenvironmenta1benefittotheente rprises.SUBJECTHEADINGoi1refinery.sulfurouswastewater,technology,economicbenefit1前言国内炼油厂的含硫污水处理装置产生的副产品——稀氨水,对其如何利用的方法有多种.本文介绍燕化炼油厂含硫污水双塔汽提处理装置对副产品氨水的使用情况.结合本厂的实际生产情况,通过在常减压装置,催化裂化装置上的反复试验,确定了利旯j含硫污水处理装置的副产品——稀氨水对三套常减压及两套催化裂化装置分馏塔顶赋合注氢的新工艺这项工艺的实施,对全厂注氨系统进行了改造,合理地利用了氨资源,解决了炼厂设备防腐,减少汽油产品碱洗脱硫的碱用量,从而减少废碱液的处理负担,是一项~举多得的"三废"处理环保技术.2联合注氨工艺技术简述2.1工艺流程特点在全厂含硫污水双塔汽提,常减压装置,催化裂化装置之问建立了一个彼此相关而又相对独立的联合注氨系统.该系统工程主要在全厂增设了两条Dg80的往返氨水线,以形成一个闭路循环.各装置可独立从总循环线上取得一定压力的氨水(各装置不需增设氨水泵),除注氨消耗一部分外,多余部分仍返回系统循环.这样系统及各支路常年循环,因此冬季可防冻凝,保证了全系统安全稳定长周期运行.由于氨水泵出口压力达1_5MPa,在返回线上设置压控阀PIC-204,使其系统压力控制稳定,从而确保各装置注氨量的稳定性.各支路又具有相对独立性,互不影响.实践证明,该项技术台理,安全,稳定,可靠.2.2工艺操作条件根据生产装置试验结果,所注入的氨水浓度在1.5%~3%为宜.浓度越低,注入量越大,否则效果欠佳.浓度过高,注入量小,不易控制,且易形成铵盐结垢.循环氨水压力:泵出口压力=1_5MPa;返窖205压力=0.4MPa(压控自调).两套催化装置的注氨方式.直接注入或收入氨水罐后开计量泵注入:治理与研究油气田环境保护第9卷第4期15注氨压力:0.55~0.8UPa;注氨水量:0.5~0.7m/h.第二,三套常减压装置的注氨方式:直接注八注氨压力:0.5~1.0MPa;注氨水量:初顶:O.O8~O.12/h;常项:0.12~0.15m/h;减项:0.08~0.12in/h;减顶二级:0.05~0.08Ⅲ3/h.常减压蒸馏装置实际注氨量依据三顶水pH值: 75~9.0,铁离子在正常值的范围内进行调整.3联合注氨运行效果分析3.1常减压蒸馏装置☆改变了过去注气氨压力不稳,注气量难以调节的问题.由于注入氨水浓度低,大大减少铵盐结垢现象.☆从表1分析看出,注氨水与注气氨相比"三顶水"中铁离子含量大为降低防腐效果有所改善☆从表2,表3分析可知,联合注氨水后有利于产品脱硫,使直馏汽油中的总硫含量下降,含硫污水中的硫化物含量明显上升,硫化物从油相转入到水相.另外,常减压装置直馏汽油碱洗的碱耗下降了约44%,相应碱渣产率也减少了约5o%,缓和了对污水场的压力.☆不再需要从外部购买工业液氨,降低了消耗,也减少了全厂燃料油生产系统外排到污水场的氨氨负荷.3.2催化裂化装置☆根据表4,表5分析,粗汽油及干气,液态烃中硫化物含量有所下降,相应古硫污水中硫化物含量上升近一倍.以一催化为倒,一催化注氨后汽油中总硫平均降低约20~30mg/L.水中硫化物含量表1三常减压装置联台注氨前后"三顶水pH值,平均铁离子含量变化比较g/L 表2常减压直馏汽油注氨前后比较g/L铜片腐蚀注氨情总硫(mg/L)碱洗前碱洗后250.0注气氨252.0不台格合格260.0221.0注氨水2rJ4J0不合格台格203.5上升约250ag/L.从分析数据不难看出注氨水对催化裂化油,气有一定脱硫效果.从表4可看出注氨水量合适时,对容2008,容201的油水分离不会造成影响.☆有一定的防腐效果,参见表6.其中以掺炼重油的第二套催化分馏塔顶回流罐切水中的铁离子含量下降较明显.☆从第二套催化采样分析,注氨后汽油未经碱洗的铜片腐蚀大部分都台格.因此在正常注氨及侣胄碱洗的条件下,能把住汽油腐蚀合格的质量关.从表3三常减压联台注氨前后三顶水"水质分折数据Ⅲg/L分析项目采样点注氨情况pH碱度油硫化物酚C0D氨氮容102束注氨 6.77~9.23—0.8~4.120~7516.03~20.04m367~0.51433l~5175.6~1&8(初顶水)注氨9.O6~92020.4~58.040~5864.12~108.20,182~l,00497~745l48.6~378容104束注氨6.02~7.680.4~0.650~270l202~24.041.467~2,054154~2994.2~8.4(常顶水)注氨9,O2~9.17l3.6~28.824~5064.12~11O,2L83~2,38436~73785.4~16矗6容201束注氨6.49~8.320.5--0,615~4508.02~l2.025.062~7.6662l0~2502.1~6,3 (减顶水)注氨9.85~10.3625.4~22940~5260l1~3们.68.4l~10.242l~1528l71.6~1715注:表中碱度负值表示酸度161999年12月油气田环境保护治理与研究表4一,二催化装置联合注氨前后吉硫污水水质分析比较ⅡIg几注氨分析项目装置采样点情况0H碱度油硫化物酚COD氰化物氨氨客2008未注氨9.12~9.2421.6~32.41O6~2蜩l20~321l65~253l26O~34240.042~O.1o4223~265(分顶水)注氨8.79~9.1239.6~83.658~14533l~58l256~30l23O3~69270.037~0.074462~826客20]未注氨9.19~9.2344.8~76.025~636l~609225~2953010~37810.044~0.n9325~554(分顶水)注氨9.07~9.4854.0~110130~l7口862~1323322~3443499~43650.064~0.104406~595客301未注氨8.93~9.1吕l25~2285~494007~4809127~18l10234~1360]3010~515:(稳顶水)注氮8.92~9.29728~93640~10419~l1622l28~l4813545~2l0700069~00243248~577(表5催化裂化装置分馏塔顶注氨前后分析数据(平均值)装置一催化(加工蜡油)二催化(掺炼重油船%)注氨情况未注氨联合注氨未注氨联合注氨稳定汽油总硫l78148.5l25.5138.75(~g/L)液烃古H,S(%)24751551干气含S(%)0.800.155O.380.08富气含H,S()0.360.18O.2O0.063表6催化装置注氨前后分馏塔顷回流罐切水数据nu/L注氨项目装置情况pHIFe.'JcL一一催化未挂氨8.54~9.20I5.46~3.10l19.0~20.0窖2008注氨9.20~9.43l1.13~5.68I22.0~25.0=催化未洼氨8.8O~9.72I3.56~9.48l16.0窑201注氨9.24~9.44l1.08~91.58l14.0~16.0目前看,仅靠注氨水,粗汽油不碱洗尚不适合,汽油碱洗还须保留作为产品质量最后把关的手段. ☆汽油碱洗负荷大大降低,注氨水后可使碱浓度降至2.5%以下,且换碱周期由原来的l2~15天延长至36天.目前此项工作正在进一步考核,争取延长碱使用周期,以至达到不退碱或少退碱的目的.3.3确保含硫污水双塔汽提装置平稳运行自联合注氨水投入运行以来,对含硫污水汽提装置来说,改变了以往只开脱硫塔,脱氨塔因氨水无出路而运行不下去的局面.开双塔,对硫化物,氨氮的脱除率有所提高,改善了全厂含硫污水处理后的水质,从而减轻对下游污水处理场的负荷. 3.4减少了污染物排放量,有利于污水净化处理从以上分析可知,联合注氨以后大大减少了汽油碱渣排放量,从而避免了对污水处理场的冲击. 过去有过因碱渣处置不当影响污水场二级生化处理的情况.困此减少碱渣量对提高污水处理水平有着重要意义.另外,由于生产系统不再从外部购买液氨,故流至污水场的纯氨可减少8Ot/a左右,既节省了成本,又有利于污水治理,从而为保证全厂水质达标排放起到积极作用4效益分析从实践来看,常减压——催化裂化联合注氨工艺是可行的,运行效果良好,产生如下经济效益:☆根据目前联合注氨量的计算,如果要达到同样的效果,燕化炼油厂三套常减压装置每年可节省工业液氨100t,按液氨市场价1450元/t计,可节约生产成本14.5万元/a. ☆联合注氨后常减压及催化裂化装置汽油碱洗的用碱量可减少近5O%.据统计至少可节约工业用碱200t/a(浓度4O%),每t碱液按850元计,可节约l7万元/a.☆联合注氨后,全厂可减少一半碱渣,即1000t/a,每t碱渣经提酚处理的费用按4O元计,则相应节约处理费用4万元/a.此外,这些脱酚后的碱渣排至污水场后需加入浓硫酸进行中和处理,根据NaOH(汽油碱洗)生成Na2s,酚钠盐经烟气提酚生成Na2c03,Na2s(污水场加酸中和)生成Na~SO最终无害化,整个流程及有关化学反应计算,每lt浓度为40%的NaOtt液碱经过几次反应最终还需浓度为98%的Hs01t来中和处理.上述节约200t液碱消耗,可相应在污治理与研究油气田环境保护第9卷第4期17水场节约浓度为98%的SO2.00t,这样按硫酸B30 元/t计.可节省费用6.6万元/a.☆联合注氨工程增加一台功率为15kw的氨水泵常年运行按年开工330天计.电耗12万度/a,费用3.6万元/a.综上所述,直接经济效益为38.5万元/a.此外,还有减轻设备腐蚀,延长使用周期的潜在效益和减少污染,保护环境带来的社会效益.5结论☆利用炼油厂含硫污水处理装置的副产氨水对炼油装置进行联合注氨的工艺技术是成功的.该项技术的开发大大减少了炼油过程中废碱渣等污染物的排放量,避免了对下游污水场的冲击.改善了处理水质,有利于环境保护.☆合理地利用炼油厂的氨水资源,节约了成本,有一定的经济效益.☆有利于炼油设备防腐,解决了常减压装置气氨的不足.目前,燕化炼油厂随着宽馏份重整,中压加氢改质和重油催化裂化等装置的投产,全厂含硫含氨污水相应地增加到llOt/h,对双塔汽提处理含硫污水来说会有更多的氨水产生.因此有必要将联合注氨后多出的氨水用于氨精制,生产纯液氨,这是必要的出路目前该厂己建成一套含硫污水单塔汽提侧线出氨及氨精制装置与双塔汽提相配合,不久将投入运行.生产出的液氨纯度可大于99.5%.液氨中总硫含量小于20mg/L,H2S含量小于5IIIg/L,可用于润滑油装置酮苯脱蜡冷冻系统使用.参考文献陈瑞安.石油化工企业清洁生产审计工作指南.北京:中国石化出板社,1998:8刘天齐.石油化工环境保护手册.北京:烃加工出版社.1990:257石油化工设计I主编.石油化工废水治理.北京:石油工业出籁社弹性体征订启事(收稿日期1999—09—17)(赫辑肖翠客)《弹性体》是国内外公开发行的中央级弹性体行业技术性期刊,中国期刊网全文收录辫刊,已被c^.EI.SCI等国际学术界公认的权威检索期刊收录.由中国石油天然气集团公司主管,化工部合成橡胶信息总站主办,吉化集团公司研究院出版,国内外公开发行.本刊理论性,实用性与信息性为特色,主要报道合成橡胶(通用胶和特种胶),胶乳,天然橡胶及其改性,塑料橡胶共混改性与高分子合成材料的科研,生产和加工应用技术.刊登有关弹性体工业的技术开发,技术改造,技术进展,技术评价等方面的专论,综述,预测,以及讲座,外商技术座谈和出国考察报告等.本刊常年开展广告业务,进行厂家介绍和产品宣传,欢迎广为利用.凡2000年订购本刊10份以上者,当年享受在本刊刊登1/2版文字广告的优惠待遇.本刊为季刊,国际标准刊号1005—3174,国内统一刊号22—1105/TQ,每期定价9.00元,全年36.00元,需订阅者可直接与编辑部联系.本编辑部尚有1991—1998各年度《弹性体》合订本,50元/年,欢迎订阅.编辑部地址:吉林省吉林市遵义东路27号邮政编码:132021电话:(0432)39733773977797通过银行汇款:中国工商银行吉林分行吉化办事处帐号:11802490350857。
污水处理工艺方案油田里的污水生意

污水处理工艺方案油田里的污水生意一、项目背景油田开采过程中会产生大量污水,这些污水含有石油、化学物质等多种有害成分,若直接排放,将严重污染环境。
因此,我们必须找到一种高效、环保的污水处理工艺,实现污水的资源化利用。
二、污水处理工艺流程1.预处理:将污水引入调节池,通过搅拌、沉淀等手段,去除污水中的悬浮物和油滴。
2.生物处理:采用好氧生物处理技术,如活性污泥法、生物膜法等,降解污水中的有机物质。
3.深度处理:通过絮凝、过滤、吸附等工艺,进一步净化水质,去除残余污染物。
4.回用或排放:处理后的污水可回用于油田生产,或达到排放标准后排入环境。
三、关键设备与技术1.预处理设备:调节池、搅拌器、沉淀池等。
2.生物处理设备:活性污泥池、生物膜反应器、曝气设备等。
3.深度处理设备:絮凝剂、过滤设备、吸附剂等。
4.自动控制系统:实现设备运行参数的实时监测和自动调节。
四、项目优势1.节能:采用高效节能设备,降低运行成本。
2.环保:实现污水资源化利用,减少环境污染。
3.稳定:工艺成熟,运行稳定,易于维护。
4.灵活:可根据实际需求调整工艺参数,满足不同水质要求。
五、实施方案1.前期调研:收集油田污水水质、水量等相关数据,确定污水处理工艺。
2.设计方案:根据调研结果,设计污水处理工艺流程和设备选型。
3.施工安装:按照设计方案,进行设备安装、调试和运行。
4.运营管理:建立健全运营管理体系,确保污水处理设施稳定运行。
六、项目效益1.经济效益:通过污水资源化利用,降低油田生产成本。
2.社会效益:减少环境污染,提高企业形象。
3.生态效益:保护生态环境,促进可持续发展。
七、风险评估1.技术风险:污水处理技术更新迅速,需关注行业动态,及时调整工艺。
2.市场风险:市场竞争激烈,需提高项目性价比。
3.政策风险:政策变动可能影响项目实施和运营。
这个方案旨在解决油田污水问题,实现污水的资源化利用。
通过采用先进的污水处理工艺,降低运行成本,提高项目效益。
- 1、下载文档前请自行甄别文档内容的完整性,平台不提供额外的编辑、内容补充、找答案等附加服务。
- 2、"仅部分预览"的文档,不可在线预览部分如存在完整性等问题,可反馈申请退款(可完整预览的文档不适用该条件!)。
- 3、如文档侵犯您的权益,请联系客服反馈,我们会尽快为您处理(人工客服工作时间:9:00-18:30)。
PRETREATMENT AND COMPREHENSIVE UTILIZATION OF SOUR WATER IN PETROLEUM REFINERIES
Lin Benkuan Luoyang Petrochemical Engineering Corporation (Luoyang,Henan 471003)
在加工含硫原油时,常减压蒸馏、催化裂化及加氢裂化等工艺装置都要排出大量含硫污水。这 些污水必须经过预处理,才能排至污水处理场,以保证污水处理场的正常运转,并保证最终排出厂 外的污水符合标准的要求。 含硫污水量是制约预处理装置和污水处理场的占地面积、投资和操作费用的关键因素。在炼油 厂的改造扩建工程中,如果处理得当,可能无需另建新装置,只需改造原有装置即可。这样做的结 果,其环保效益和经济效益将十分可观的。现就如何选择预处理工艺、减少含硫污水量及净化水的 综合利用问题进行探讨。
137
焦化分馏塔顶油水分离罐
3 481
33
铂重整柴油加氢高压分离器
15 397
12.615.3
大庆原油
常压塔顶油水分离罐
20
1.0
减压塔顶油水分离罐
52
5.4
催化裂化分馏塔顶
油水分离罐
668
193
催化裂化富气水洗水
156
20
焦化汽油回流罐
1 794
万方数据
file:///E|/qk/lysj/lysj99/lysj9908/990809.htm(第 3/10 页)2010-3-23 4:01:51
炼油设计990809
图1 单塔加压侧线抽出汽提工艺流程 1——汽提塔;2——重沸器;3~5——一、二、三级冷凝器; 6~8——一、二、三级分离器;9——冷却器;10——换热器 2.1.2 双塔加压汽提工艺 双塔加压汽提工艺所回收的硫化氢可作为硫回收装置原料,氨可回用于炼油装置,或作为一般 化肥原料。该工艺操作平稳可靠,国内已应用在含硫污水硫化氢和氨总浓度最高达120 000 mg/L的场 合。其净化水可满足硫化氢不高于50 mg/L和氨不高于100 mg/L的要求。可以根据原料酸性水中硫化 氢和氨的浓度,调整工艺参数或设备结构,以满足对净化水质量的要求。该工艺的流程和设备较复 杂,投资稍多,每吨原料水的蒸汽单耗约230 kg。 2.1.3 CLL氨回收工艺 该工艺是Chemie Linz和Lurge公司(CLL)共同开发的,其流程见图2。
14 365
15 388
2288 512
单塔加压 混合酸性 侧线抽出 水
8 835
16 293
352 408
单塔加压 混合酸性 侧线抽出 水
7 239
9 854
单塔加压 侧线抽出
混合酸性 水
3 000~4 500
6 000~9 000 200~300
65 150
12
68
7
96
<50 <200
由表2可以看出,不论采用哪种汽提工艺,净化水中硫化氢和氨的含量一般都能满足污水处理场 进水质量的要求。
2 含硫污水预处理工艺
含硫污水预处理工艺一般采用空气氧化工艺或蒸汽汽提工艺。空气氧化工艺是用空气中的氧在 一定条件下使含硫污水中的硫化物氧化,一般约90%被氧化为硫代硫酸盐,10%被进一步氧化为硫酸 盐。 该工艺适用于低含硫污水(硫化物含量低于2 000 mg/L)。由于硫化物被空气氧化为盐类,因而污 水中盐含量增加。该法不能起到脱氨及脱氰作用,目前净化水还未回用于工艺装置。同时,净化水 中约90%的硫化物氧化为硫代硫酸盐排至污水处理场,会影响污水处理场生产操作。因此,在国内该 工艺已逐渐被蒸汽汽提工艺所取代。 10多年来,国内炼油界设计科研单位、高等院校以及炼油厂对含硫污水蒸汽汽提工艺做了大量 工作,该技术得到了很大发展。在汽提理论、计算程序、工程设计以及生产操作等方面都取得了可 喜成果,并且开发了适合于不同工况的多种蒸汽汽提工艺。 用蒸汽汽提时,蒸汽起到了加热和降低气相中硫化氢、氨和二氧化碳分压的双重作用,促使它 们从液相进入气相,从而达到净化水质的目的。人们针对气相中硫化氢和氨的出路,开发了以下几 种工艺。 2.1 回收硫化氢和氨的汽提工艺 2.1.1 单塔加压侧线抽出汽提工艺 单塔加压侧线抽出汽提工艺所回收的硫化氢可作为硫回收装置原料,氨可回用于炼油装置,或 作一般化肥原料。该工艺在国内目前多应用于含硫污水中硫化氢和氨总浓度小于50 000 mg/L的场合, 其净化水可满足硫化氢浓度不大于50 mg/L和氨浓度不大于100 mg/L的要求。可以根据含硫污水中硫 化氢和氨的浓度,调整工艺参数和设备结构,以满足对净化水质量的要求。该工艺的流程和设备较 简单,装置操作平稳,投资少,每吨原料水的蒸汽单耗为130~180 kg,其流程见图1。
8.9 114
148
氮化物
24 316
542 3 119 37.8 796 564
0.28 0
10 69 11
20.7 14.5
241
由表1可见,原油中的硫和氮含量高,则污水中硫化氢和氨的含量亦高(如胜利原油)。从加工过 程看,加氢装置和催化裂化装置的含硫污水及其浓度除与原料油的硫、氮含量有关外,还与洗涤水 的用量有关。一般情况下,加工同一种原油时,加氢装置含硫污水中的硫化物和氮化物浓度要比焦 化和催化裂化装置高,而常减压蒸馏装置最低;酚含量则以焦化和催化裂化装置含硫污水最高;减 压蒸馏和焦化装置的含硫污水则油含量最高。 国内炼油厂污水处理场一般对进水的质量要求为硫化氢和氨的质量分数分别不大于50 μg/g和 100 μg/g。因此,催化裂化、延迟焦化和加氢装置(甚至有的常减压蒸馏装置)的含硫污水都必须经 过预处理才能排至污水处理场。 1.2 几套含硫污水汽提装置原料水和净化水的组成 炼油装置的含硫污水可单独或混合后进行汽提,这取决于含硫污水的数量、组成和炼油厂的总 体规划。目前,国内炼油厂大部分都采用混合含硫污水汽提。表2列出了几套汽提装置含硫污水的组 成以及采用的汽提工艺和净化水的组成。
110
柴油加氢精制低压分离罐
8 108
0.5
加氢裂化低压分离罐
4 208
0.3
任丘原油
常压塔顶油水分离罐
6.6
17.7
减压塔顶油水分离罐
8
9.1
催化裂化分馏塔顶
油水分离罐
1 057
155
油
108 208
154 145 210 1 427 231
9 27.8
99 26 287 228 163
炼油设计990809
炼油设计
PETROLEUM REFINERY ENGINEERING 1999年 第29卷 第8期 Vol.29 No.8 1999
炼油厂含硫污水预处理及综合利用
林本宽
摘要:对3种原油采用不同加工过程的含硫污水组成以及几套含硫污水汽提装置的原料水和净化 水组成进行了比较。介绍了空气氧化和蒸汽汽提等含硫污水预处理工艺的原理、流程和特点。对针 对气相中硫化氢和氨的出路而开发的各种蒸汽汽提工艺,如回收硫化氢和氨的汽提工艺(包括单塔加 压侧线抽出汽提工艺、双塔加压汽提工艺、CLL氨回收工艺、美国钢铁公司氨回收工艺),回收硫化 氢而不回收氨的汽提工艺、硫化氢和氨都不回收的汽提工艺以及回收氨的精制工艺等作了详细分 析。最后提出了含硫污水中的氨是否回收的问题,减少催化裂化和油品加氢装置含硫污水量以及净 化水综合利用应采取的措施。 主题词:炼油厂 含硫废水 组成 预处理 汽提 净化 废水 氨 综合利用 环境保护