复合加工技术在薄壁机匣加工中的应用
高温合金薄壁的机匣加工技术阐述

高温合金薄壁的机匣加工技术阐述在机匣的加工过程中,有很多加工技术被应用。
文章针对高温合金薄壁的机匣加工的相关技术进行详细的阐述和分析,希望通过文章的阐述和分析,能够为我国的机匣加工的发展和创新贡献一份力量。
标签:机匣;变形;切削液;加工方法文章阐述的机匣加工技术以高低压外轴承座的机匣相关组建为例子进行阐述,通过对机匣加工过程中的半精加工、精铣、精加工等加工方式的阐述和分析,来对机匣的相关零件的结构主要特点进行叙述,同时对机匣的材料加工特点进行阐述。
从机匣的加工工艺路线和机匣的加工工艺方法,机匣的加工使用刀具的选择等方面来作机匣加工技术的进一步阐述。
最终阐述相关的机匣加工变形机表面硬化等加工过程中出现的问题,通过阐述来对问题给出相应的处理意见。
1 机匣零部件的结构主要特点和分析机匣零部件材料的特性关于机匣零部件的结构主要特点和分析机匣零部件材料的特性,文章主要从两个方面进行阐述和分析。
第一个方面是机匣的主要结构特点。
第二个方面是机匣材料的材质特性。
1.1 机匣的主要结构特点文章阐述的机匣径向的内外结构都非常的复杂,尤其是内圈的三种形式凹槽数量巨大,同时在机匣零件的下端面以及径向岛屿上还分布着非常多的装配定位孔。
因此在加工这一机匣零件的过程中凹槽的加工量和加工过程中的切削力非常大,这样就会导致在加工的过程中机匣变形,最主要的是零件的很多间接定位尺寸无法保障。
1.2 机匣材料的材质特性文章阐述的机匣加工材质是MSRR7209,在材料领域等同于Inconel 718。
这种材料属于高温合金的一种。
当材料属于毛料的时候是一种固熔的状态,但是当加工成为机匣零件的时候材料显示出一种固熔时效的状态。
Inconel 718为镍铬合金,内部含有非常多的铁元素和钼元素,同时还含有数量极少的铝元素和钛元素。
这种材料的耐腐蚀性能较强,便于高温焊接。
该材料的蠕变断裂的强度温度为700摄氏度。
2 机匣零部件在加工过程中的工艺特性和加工过程中的变形影响关于机匣零部件在加工过程中的工艺特性和加工过程中的变形影响,文章主要从四个方面进行阐述和分析。
航空机匣壳体衬套精密镗削加工吕书森

航空机匣壳体衬套精密镗削加工吕书森发布时间:2021-10-28T07:34:39.153Z 来源:《基层建设》2021年第22期作者:吕书森[导读] 随着我国航空航天事业的蓬勃发展,复合的硬度金属材料广泛应用于航空发动机匣制作中国航发哈尔滨东安发动机有限公司黑龙江省哈尔滨市 150060摘要:随着我国航空航天事业的蓬勃发展,复合的硬度金属材料广泛应用于航空发动机匣制作。
其常用材料有较为普通的镁合金铝合金铜合金等系列,金属技术人员在对机匣零件加工制作时,对人员仪器设备有着精密的部署。
镗削加工技术在机匣加工时增加了零件的精准度,如机匣内孔由于疏忽检查,造成了对零件加工过程中产生的不必要的质量问题。
影响机匣内孔设备如达不到安全使用标准,给日后零件加工的精准度带来隐患,根据以上观点,对航空机匣壳衬套精密镗削进行论述。
关键词:航空机匣壳体;镗削加工;精密加工在我国,航空航天发动机技术有了明显的进步和提升高精密内孔加工技术配合的硬度金属如镁合金、铝合金、铜合金等,用来镗削加工粗糙度的数值决定了内孔品质等级。
对于研发航空机匣壳体加工工艺,使用单品金刚石镗刀设计,让低硬度金属体现出最优良的使用特质。
航空航天发动机,对金属材质有较高的要求,需要零件达到一定的精密等级。
对于材质,更看重其高强度、低密度、硬度强耐高温等方面,世界航空工艺不断突飞猛进,对航空产品的要求度也在不断提升,需要研发制造人员填补工艺技术上的不足之处。
本课题将学习研究实验室的精密和超精密加工工艺方法,并将其转移到航空制造领域,实现精密加工工艺方法在航空领域的工程应用,填补铝镁合金齿轮箱产品加工技术空白,提高航空变速箱制造水平。
1航空机匣壳体衬套加工要求正如常见到的两种加工方法,车削加工和镗削加工法用于航空发动机机匣设备使用,航空发动机对零部件的精度有超高要求,所以对磨削的工艺有着严苛加工制约。
在磨削硬度材质高且表面粗糙的金属时,磨削的加工工艺有了最大化的展现,对于低硬度的金属,磨削工艺无法展现切加工效果有待提升。
复合材料加工技术与应用
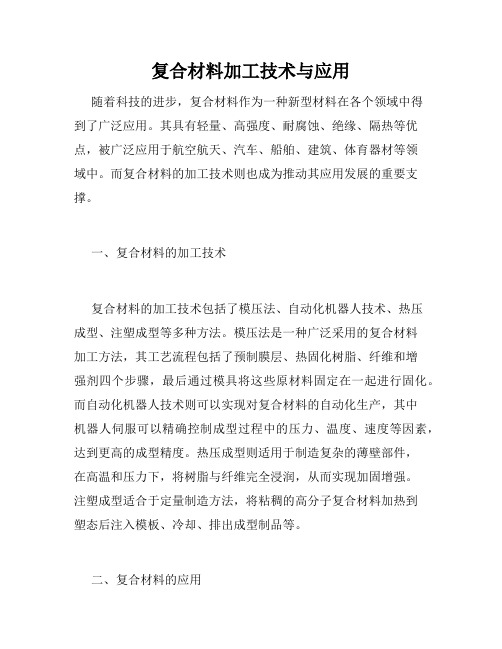
复合材料加工技术与应用随着科技的进步,复合材料作为一种新型材料在各个领域中得到了广泛应用。
其具有轻量、高强度、耐腐蚀、绝缘、隔热等优点,被广泛应用于航空航天、汽车、船舶、建筑、体育器材等领域中。
而复合材料的加工技术则也成为推动其应用发展的重要支撑。
一、复合材料的加工技术复合材料的加工技术包括了模压法、自动化机器人技术、热压成型、注塑成型等多种方法。
模压法是一种广泛采用的复合材料加工方法,其工艺流程包括了预制膜层、热固化树脂、纤维和增强剂四个步骤,最后通过模具将这些原材料固定在一起进行固化。
而自动化机器人技术则可以实现对复合材料的自动化生产,其中机器人伺服可以精确控制成型过程中的压力、温度、速度等因素,达到更高的成型精度。
热压成型则适用于制造复杂的薄壁部件,在高温和压力下,将树脂与纤维完全浸润,从而实现加固增强。
注塑成型适合于定量制造方法,将粘稠的高分子复合材料加热到塑态后注入模板、冷却、排出成型制品等。
二、复合材料的应用复合材料的应用领域丰富多样,特别是其在航空航天领域中的应用广泛。
复合材料具有轻量、高强度、耐腐蚀等优点,可以大幅减轻飞机自身重量,提高飞机性能,降低飞机能耗。
同时,在汽车制造领域中,复合材料的应用能够实现地球友好型设计,使经济性、环保性和性能之间的平衡更加优化。
在建筑领域中,复合材料的应用可以改善建筑结构的强度和耐久性。
三、未来复合材料加工技术的趋势未来的复合材料加工技术将主要围绕着快速成型、非接触加工、精细加工、智能化、柔性生产等方向进行发展。
快速成型技术将逐渐发展出用于复合材料无纸化打印技术、快速切割与铣削技术等,这些新技术可以大幅提高复合材料制造的效率和精度。
非接触式加工技术将更好地解决高精度薄壁零件加工难题。
智能化生产技术则将实现复合材料加工的自动化和智能化,提高生产效率,降低人工纰漏率。
柔性生产则将更好地复合材料制造工艺的灵活度和响应能力,更好地应对客户需求的变化。
综上所述,复合材料加工技术是推动复合材料应用发展的重要支撑,未来复合材料加工技术的发展方向将更加智能、高效、绿色、柔性等,对于提高复合材料在多个领域的应用水平具有重要的促进作用。
车铣复合高效加工薄壁零件

车铣复合高效加工薄壁零件“工欲善其事、必先利其器”,随着装备制造技术的日益发展,数控机床在机械制造行业得到了广泛应用。
相比传统的单刀架数控机床,车铣复合中心凭借双刀架、双主轴的结构优势,通过双刀架同时切削加工,能够提高加工效率、保证产品质量。
下文将以加工零件A 为例,阐述如何使用车铣复合中心高效加工薄壁零件。
零件A的加工特性:◆易变形:零件A为环形零件,单边只有18mm,该零件的毛坯为板材弯曲后焊接成形,从结构和毛坯工艺上分析,该零件在加工过程中易产生变形;◆难加工:该零件的材料为10#钢,因材料很软,在加工过程中不易断屑;◆精度高:该零件的技术要求主要有:内孔相对于外圆的跳动为0.08mm,外圆公差为0.097mm,内孔公差为0.063mm。
零件A的加工工艺和加工结果◆设备简介:EMCO公司的HT690是一台典型的车铣复合中心,该设备具有两套完全独立的主轴系统,上下刀架可分别对主副轴进行加工、上下刀架通过配置动力刀座可用于铣加工、两套主轴之间可以实现工件的自动对接。
图1:设备结构◆工艺过程和结果:在工艺试验中尝试了主副轴均采用卡爪装夹的方法,试验结果内孔变形量0.1~0.2mm,尺寸全部超差。
最终实施的工艺方案是:主轴端采用标准六爪内撑、副轴端采用法兰盘夹具装夹。
从加工结果看,10个零件的内孔变形全部合格,由此可以得出下述结论:副轴端用法兰盘装夹零件的工艺方法是可行的。
◆工艺总结:⑴主轴端采用标准六爪内撑,车削后的外圆变形在0.08~0.1mm之间,该类型的卡爪可沿圆弧方向作微量摆动,这样就与毛坯有了足够长的接触面积,在毛坯变形大的情况下也可以保证主轴端零件的变形量;⑵零件变形主要由三种因素引起:夹变形、前道加工变形、焊疤影响;副轴端采用卡爪装夹的方法只能完全反映零件的变形,无法减小前道工序带来的变形;⑶副轴端采用法兰盘式车夹具,即通过端面螺孔对零件进行夹紧。
该方法使零件仅轴向受力,可消除夹变形影响、减小前道变形和焊疤变形对零件最终变形的影响;⑷对于零件A这样的软质零件,内孔与端面在夹紧过程中相互影响非常明显:手工装夹时,如果前道加工的端面平面度不好或者零件端面与夹具端面贴合不好,都会使端面不平度间接反映到工件的变形上;⑸该设备通过主副轴之间的自动对接,可减少一次装夹时间;自动对接时,副轴带动夹具向主轴移动,直至夹具端面与磁轭端面完全贴合、副轴才会停止移动。
复合材料机匣及其制造方法-概述说明以及解释
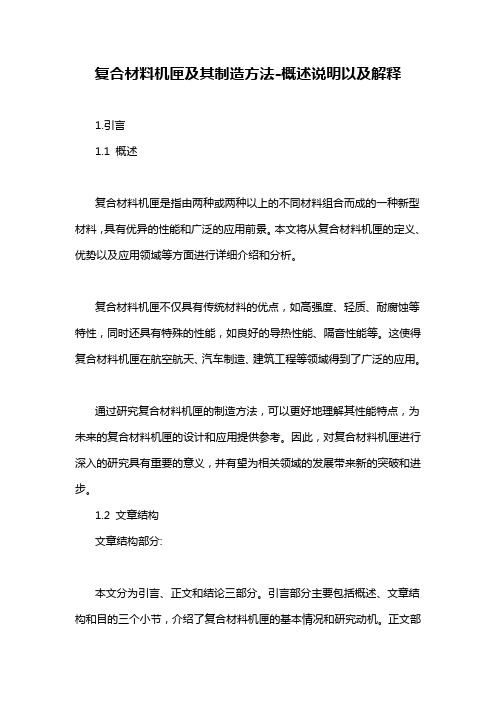
复合材料机匣及其制造方法-概述说明以及解释1.引言1.1 概述复合材料机匣是指由两种或两种以上的不同材料组合而成的一种新型材料,具有优异的性能和广泛的应用前景。
本文将从复合材料机匣的定义、优势以及应用领域等方面进行详细介绍和分析。
复合材料机匣不仅具有传统材料的优点,如高强度、轻质、耐腐蚀等特性,同时还具有特殊的性能,如良好的导热性能、隔音性能等。
这使得复合材料机匣在航空航天、汽车制造、建筑工程等领域得到了广泛的应用。
通过研究复合材料机匣的制造方法,可以更好地理解其性能特点,为未来的复合材料机匣的设计和应用提供参考。
因此,对复合材料机匣进行深入的研究具有重要的意义,并有望为相关领域的发展带来新的突破和进步。
1.2 文章结构文章结构部分:本文分为引言、正文和结论三部分。
引言部分主要包括概述、文章结构和目的三个小节,介绍了复合材料机匣的基本情况和研究动机。
正文部分将深入探讨复合材料机匣的定义、优势和应用领域,详细阐述了复合材料机匣在工程领域的重要性。
结论部分将总结复合材料机匣的重要性,并探讨制造方法对复合材料机匣的影响,以及未来复合材料机匣的发展前景。
整个文章结构清晰,逻辑严谨,为读者全面了解复合材料机匣提供了有效的指导。
1.3 目的:本文旨在探讨复合材料机匣在工业领域的重要性以及其制造方法。
通过深入分析复合材料机匣的定义、优势和应用领域,以及制造方法对其性能的影响,旨在为读者提供关于复合材料机匣的全面认识。
同时,通过展望未来复合材料机匣的发展趋势,为相关领域的研究人员和从业者提供参考和启示,促进复合材料机匣技术的进一步发展和应用。
希望本文能够为相关领域的研究和实践提供有益的信息和思路。
2.正文2.1 复合材料机匣的定义复合材料机匣是一种由不同材料组合而成的机械外壳结构,其中至少包含两种以上不同性质的材料。
这种机匣结构的设计旨在充分发挥各种材料的优势,使整体结构具有更高的强度、刚度、耐磨性和耐腐蚀性。
车铣复合加工方法在铝镁合金机匣中的应用

车铣复合加工方法在铝镁合金机匣中的应用发表时间:2018-10-14T12:17:33.193Z 来源:《电力设备》2018年第19期作者:赵在柱王小伟杨靓[导读] 摘要:车铣复合加工技术是一种先进的机械加工技术,融现代控制技术、精密测量技术应用技术于一体,将过去的传统机械设计和精密制造技术进行优化提升。
(中国航发哈尔滨东安发动机有限公司黑龙江哈尔滨 150066)摘要:车铣复合加工技术是一种先进的机械加工技术,融现代控制技术、精密测量技术应用技术于一体,将过去的传统机械设计和精密制造技术进行优化提升。
航空发动机铝镁合金机匣类零件具有结构复杂、加工余量大、切削温度不能过高和加工工艺性差的特点,通过车铣复合加工技术能有效解决铝镁合金机匣类复杂零件加工难题。
本文对车铣复合加工方法在铝镁合金机匣中的应用进行了分析探讨。
关键词:车铣复合加工;方法;铝镁合金机匣;应用引言车铣复合加工技术融现代控制技术、精密测量技术于一体,将过去的传统机械设计和精密制造技术进行优化提升。
1高性能飞机发动机机匣加工特点概述1.1高性能飞机发动机机匣加工特点。
航空制造技术的飞速发展大大提升了飞机发动机的灵敏性和可靠性,高性能飞机发动机采用的铝镁合金复杂结构使发动机零部件质量大大降低,发动机推重比提高,但也增加了加工的难度。
相应增加。
航空发动机铝镁合金机匣类零件具有结构复杂、加工余量大、切削温度不能过高的特点,其需要五轴联动铣削加工、内腔表面及前后安装边需要借助数控车削加工,前后安装边定位孔、连接孔需要进行钻、扩、镗、铰、铣加工,加工环节多,加工工艺性差,极易引起变形现象,同时造成后续加工工序装夹、找正困难,机匣的加工质量和效率降低。
随着数控机床加工技术的不断发展,趋于多功能和复合加工的技术,实现了机匣件多工序的复合加工,避免了铝镁合金机匣加工过程中二次装夹和找正造成的误差,使加工的自动化程度大大提升。
1.2铣车复合加工技术的发展。
浅谈薄壁机匣零件的高效加工
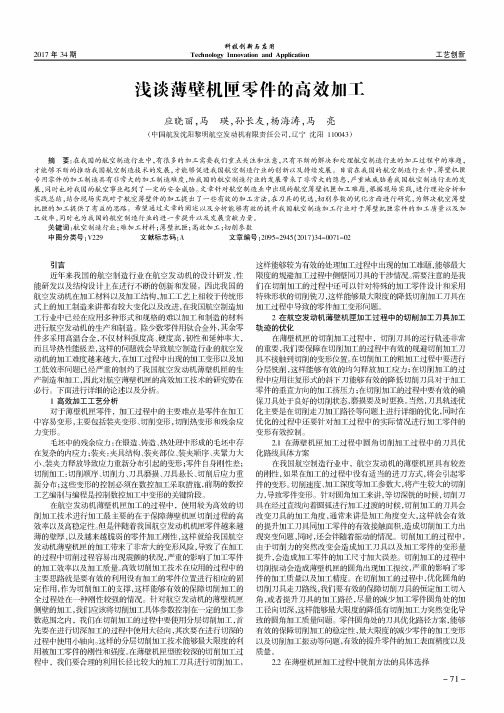
2017年34期科技创新与应用Technology Innovation and Application工艺创新浅谈薄壁机匣零件的高效加工应晓丽,马瑛,孙长友,杨海涛,马亮(中国航发沈阳黎明航空发动机有限责任公司,辽宁沈阳110043)摘要:在我国的航空制造行业中,有很多的加工需要我们重点关注和注意,只有不断的解决和处理航空制造行业的加工过程中的难题,才能够不断的推动我国航空制造技术的发展,才能够促进我国航空制造行业的创新以及持续发展。
目前在我国的航空制造行业中,薄壁机匣专用零件的加工制造具有非常大的加工制造难度,给我国的航空制造行业的发展带来了非常大的隐患,严重地威胁着我国航空制造行业的发展,同时也对我国的航空事业起到了一定的安全威胁。
文章针对航空制造业中出现的航空薄壁机匣加工难题,根据现场实践,进行理论分析和实践总结,结合现场实践对于航空薄壁件的加工提出了一些有效的加工方法,在刀具的优选,切削参数的优化方面进行研究,为解决航空薄壁机匣的加工提供了有益的思路。
希望通过文章的阐述以及分析能够有效的提升我国航空制造加工行业对于薄壁机匣零件的加工质量以及加工效率,同时也为我国的航空制造行业的进一步提升以及发展贡献力量。
关键词:航空制造行业;难加工材料;薄壁机匣;高效加工;切削参数中图分类号:V229 文献标志码:A文章编号院2095-2945 (2017)34-0071-02引言近年来我国的航空制造行业在航空发动机的设计研发、性 能研发以及结构设计上在进行不断的创新和发展。
因此我国的 航空发动机在加工材料以及加工结构,加工工艺上相较于传统形 式上的加工制造来讲都有较大变化以及改进,在我国航空制造加 工行业中已经在应用多种形式和规格的难以加工和制造的材料 进行航空发动机的生产和制造。
除少数零件用钛合金外,其余零 件多采用高温合金,不仅材料强度高、硬度高,韧性和延伸率大,而且导热性能极差,这样的问题就会导致航空制造行业的航空发 动机的加工难度越来越大,在加工过程中出现的加工变形以及力口 工低效率问题已经严重的制约了我国航空发动机薄壁机匣的生 产制造和加工,因此对航空薄壁机匣的高效加工技术的研究势在 必行。
复合加工技术在航空复杂零件加工中的应用.
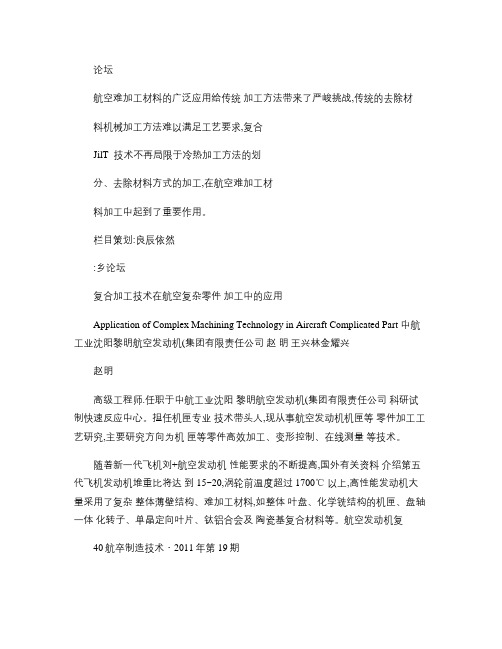
论坛航空难加工材料的广泛应用给传统加工方法带来了严峻挑战,传统的去除材料机械加工方法难以满足工艺要求,复合JilT_技术不再局限于冷热加工方法的划分、去除材料方式的加工,在航空难加工材料加工中起到了重要作用。
栏目策划:良辰依然:乡论坛复合加工技术在航空复杂零件加工中的应用Application of Complex Machining Technology in Aircraft Complicated Part 中航工业沈阳黎明航空发动机(集团有限责任公司赵明王兴林金耀兴赵明高级工程师.任职于中航工业沈阳黎明航空发动机(集团有限责任公司科研试制快速反应中心。
担任机匣专业技术带头人,现从事航空发动机机匣等零件加工工艺研究,主要研究方向为机匣等零件高效加工、变形控制、在线测量等技术。
随着新一代飞机刘+航空发动机性能要求的不断提高,国外有关资料介绍第五代飞机发动机堆重比将达到15~20,涡轮前温度超过1700℃以上,高性能发动机大量采用了复杂整体薄壁结构、难加工材料,如整体叶盘、化学铣结构的机匣、盘轴一体化转子、单晶定向叶片、钛铝合会及陶瓷基复合材料等。
航空发动机复40航卒制造技术・2011年第19期复合加工技术在航空发动机制造领域广泛应用。
解决了复杂结构零件、难加工材料加工难题,如:采用振动钻孔、振动攻丝解决了细长孔加工难题,采用振动光饰解决叶片表面抛光难题;采用镗铣、车铣复合多功能加工中心实现了多工序集中复合加工,减少了工序周转和辅助加工时间,减少了人为干预,提高了自动化加工水平,为加工过程全程序化控制奠定了基础,保证了零件加工质量的稳定性和可靠性。
杂整体薄壁结构、难加工材料零件加工成为发动机制造的关键所在,采用传统的单一加工方法已经难以解决航窄发动机复杂机匣、整体叶盘、整体叶环和盘轴一体化结构复杂零件的加T难题。
航空难加工材料的广泛应用给传统的加工方法带来了严峻的挑战,传统的去除材料机械加工方法难以满足工艺要求,特种加工方法、复合加工技术在航空难加工材料加[Ffl起了蓖要作用。
复合工艺在机匣型面加工中的应用研究

加工内容:该区域直径最大φ900mm,去除材料厚度最大 28mm, 环带宽度最大 50mm,除凸台外的其余材料作为切削余量被去掉,切 削加工量非常大。由于 A 环带圆周上分布有凸台,不能采用连续加 工方式,加工效率低下且刀具消耗极大。
下图 2 中,A 环带为复杂型面加工,B 环带为单一型面加工。
图1 1.2 电火花加工特点
学术论坛
复合工艺在机匣型面加工中的应用研究
李海宁
(中国航发航空科技股份有限公司,四川 成都 610503)
摘要:为了提高外贸某机型高压涡轮机匣的型面电加工效率,解决镍基高温合金材料难加工问题,该文分别通过对石墨电极材料的应 用和采用数控加工与电火花加工两种切削方式相结合的复合加工工艺方法的分析和试验过程的描述,得出采用石墨电极材料进行电加工, 降低电极的消耗,提高加工效率,通过试验,铜电极加工时间为 50 小时,石墨电极加工时间 42 小时,加工效率提高 16%;同时对复合加 工方法的概念引入和应用,充分发挥每种切削方式的优点,相互取长补短,从而获得了综合性价比高、整体加工性能得到提升的优势,从 试验数据看,单独采用数控加工,总切削时间为 40 小时,单独采用电火花加工,总切削时间为 81 小时,而采用复合加工,总切削时间为 20 小时,加工效率提高 50%。从而得出结论为单一简单型面可采用石墨电极材料进行电加工,对于复杂型面可采用复合加工进行电加工来 提高工效。
使用复合循环精密加工薄壁工件
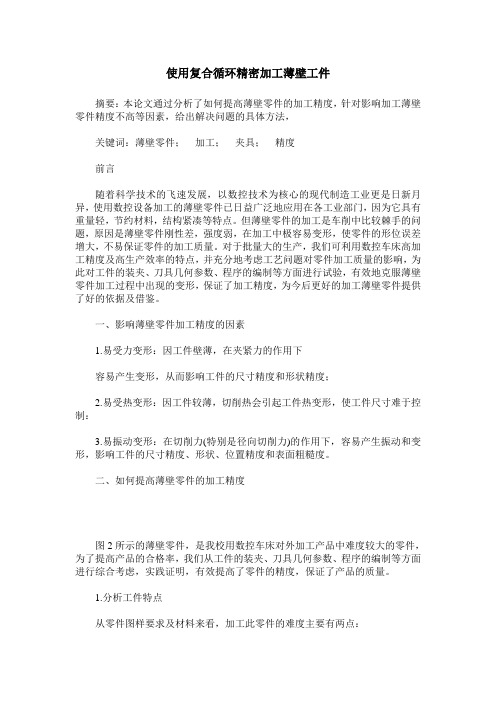
使用复合循环精密加工薄壁工件摘要:本论文通过分析了如何提高薄壁零件的加工精度,针对影响加工薄壁零件精度不高等因素,给出解决问题的具体方法,关键词:薄壁零件;加工;夹具;精度前言随着科学技术的飞速发展,以数控技术为核心的现代制造工业更是日新月异,使用数控设备加工的薄壁零件已日益广泛地应用在各工业部门,因为它具有重量轻,节约材料,结构紧凑等特点。
但薄壁零件的加工是车削中比较棘手的问题,原因是薄壁零件刚性差,强度弱,在加工中极容易变形,使零件的形位误差增大,不易保证零件的加工质量。
对于批量大的生产,我们可利用数控车床高加工精度及高生产效率的特点,并充分地考虑工艺问题对零件加工质量的影响,为此对工件的装夹、刀具几何参数、程序的编制等方面进行试验,有效地克服薄壁零件加工过程中出现的变形,保证了加工精度,为今后更好的加工薄壁零件提供了好的依据及借鉴。
一、影响薄壁零件加工精度的因素1.易受力变形:因工件壁薄,在夹紧力的作用下容易产生变形,从而影响工件的尺寸精度和形状精度;2.易受热变形:因工件较薄,切削热会引起工件热变形,使工件尺寸难于控制:3.易振动变形:在切削力(特别是径向切削力)的作用下,容易产生振动和变形,影响工件的尺寸精度、形状、位置精度和表面粗糙度。
二、如何提高薄壁零件的加工精度图2所示的薄壁零件,是我校用数控车床对外加工产品中难度较大的零件,为了提高产品的合格率,我们从工件的装夹、刀具几何参数、程序的编制等方面进行综合考虑,实践证明,有效提高了零件的精度,保证了产品的质量。
1.分析工件特点从零件图样要求及材料来看,加工此零件的难度主要有两点:(1)主要因为是薄壁零件,螺纹部分厚度仅有4mm,材料为45号钢,批量较大,既要考虑如何保证工件在加工时的定位精度,又要考虑装夹方便、可靠,而我们通常都是用三爪卡盘夹持外圆或撑内孔的装夹方法来加工,但此零件较薄,车削受力点与加紧力作用点相对较远,还需车削M24螺纹,受力很大,刚性不足,容易引起晃动,因此要充分考虑如何装夹定位的问题。
航空发动机典型零件复合加工应用
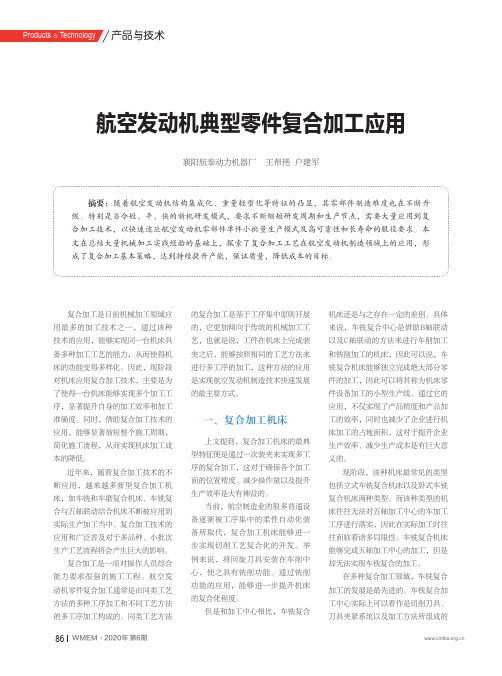
产品与技术襄阳航泰动力机器厂 王帮艳 户建军航空发动机典型零件复合加工应用摘要:随着航空发动机结构集成化、重量轻型化等特征的凸显,其零部件制造难度也在不断升级。
特别是当今短、平、快的新机研发模式,要求不断缩短研发周期和生产节点,需要大量应用到复合加工技术,以快速适应航空发动机零部件单件小批量生产模式及高可靠性和长寿命的服役要求。
本文在总结大量机械加工实践经验的基础上,探索了复合加工工艺在航空发动机制造领域上的应用,形成了复合加工基本策略,达到持续提升产能,保证质量,降低成本的目标。
复合加工是目前机械加工领域应用最多的加工技术之一,通过该种技术的应用,能够实现同一台机床具备多种加工工艺的能力,从而使得机床的功能变得多样化。
因此,现阶段对机床应用复合加工技术,主要是为了使得一台机床能够实现多个加工工序,显著提升自身的加工效率和加工准确度。
同时,借助复合加工技术的应用,能够显著缩短整个施工周期,简化施工流程,从而实现机床加工成本的降低。
近年来,随着复合加工技术的不断应用,越来越多新型复合加工机床,如车铣和车磨复合机床、车铣复合与五轴联动结合机床不断被应用到实际生产加工当中。
复合加工技术的应用和广泛普及对于多品种、小批次生产工艺流程将会产生巨大的影响。
复合加工是一项对操作人员综合能力要求很强的施工工程。
航空发动机零件复合加工通常是由同类工艺方法的多种工序加工和不同工艺方法的多工序加工构成的。
同类工艺方法的复合加工是基于工序集中原则开展的,它更加倾向于传统的机械加工工艺,也就是说,工件在机床上完成装夹之后,能够按照相同的工艺方法来进行多工序的加工,这种方法的应用是实现航空发动机制造技术快速发展的最主要方式。
一、复合加工机床上文提到,复合加工机床的最典型特征便是通过一次装夹来实现多工序的复合加工,这对于确保各个加工面的位置精度、减少操作量以及提升生产效率是大有裨益的。
当前,航空制造业的很多普通设备逐渐被工序集中的柔性自动化装备所取代,复合加工机床能够进一步实现切削工艺复合化的开发。
薄壁类零件加工装夹技术研究
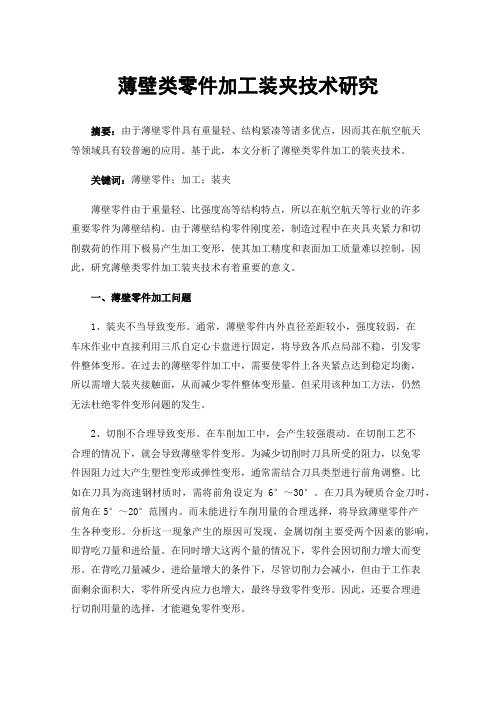
薄壁类零件加工装夹技术研究摘要:由于薄壁零件具有重量轻、结构紧凑等诸多优点,因而其在航空航天等领域具有较普遍的应用。
基于此,本文分析了薄壁类零件加工的装夹技术。
关键词:薄壁零件;加工;装夹薄壁零件由于重量轻、比强度高等结构特点,所以在航空航天等行业的许多重要零件为薄壁结构。
由于薄壁结构零件刚度差,制造过程中在夹具夹紧力和切削载荷的作用下极易产生加工变形,使其加工精度和表面加工质量难以控制,因此,研究薄壁类零件加工装夹技术有着重要的意义。
一、薄壁零件加工问题1、装夹不当导致变形。
通常,薄壁零件内外直径差距较小,强度较弱,在车床作业中直接利用三爪自定心卡盘进行固定,将导致各爪点局部不稳,引发零件整体变形。
在过去的薄壁零件加工中,需要使零件上各夹紧点达到稳定均衡,所以需增大装夹接触面,从而减少零件整体变形量。
但采用该种加工方法,仍然无法杜绝零件变形问题的发生。
2、切削不合理导致变形。
在车削加工中,会产生较强震动。
在切削工艺不合理的情况下,就会导致薄壁零件变形。
为减少切削时刀具所受的阻力,以免零件因阻力过大产生塑性变形或弹性变形,通常需结合刀具类型进行前角调整。
比如在刀具为高速钢材质时,需将前角设定为6°~30°。
在刀具为硬质合金刀时,前角在5°~20°范围内。
而未能进行车削用量的合理选择,将导致薄壁零件产生各种变形。
分析这一现象产生的原因可发现,金属切削主要受两个因素的影响,即背吃刀量和进给量。
在同时增大这两个量的情况下,零件会因切削力增大而变形。
在背吃刀量减少、进给量增大的条件下,尽管切削力会减小,但由于工作表面剩余面积大,零件所受内应力也增大,最终导致零件变形。
因此,还要合理进行切削用量的选择,才能避免零件变形。
3、刀具不合适导致变形。
薄壁零件在车削时,选取合理的刀具至关重要,尤其是对刀具几何角度的选择,不仅会影响切削力的大小,也会影响车削中产生的热变形程度,需关注的是,在薄壁零件的工作表面微观质量的把握也很重要。
某型号薄壁机匣加工技术研究
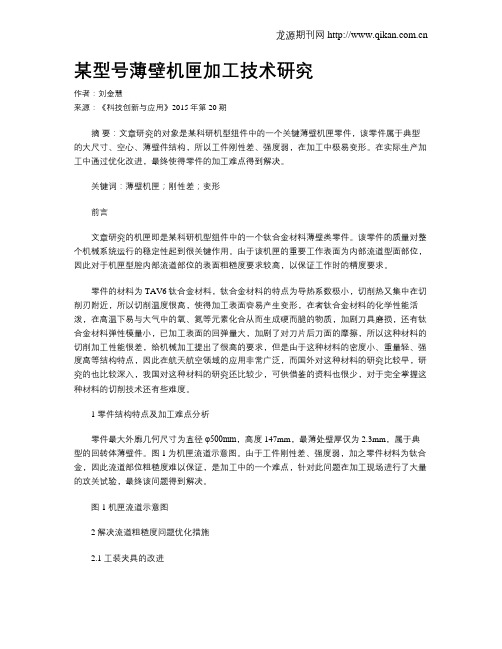
某型号薄壁机匣加工技术研究作者:刘金慧来源:《科技创新与应用》2015年第20期摘要:文章研究的对象是某科研机型组件中的一个关键薄壁机匣零件,该零件属于典型的大尺寸、空心、薄壁件结构,所以工件刚性差、强度弱,在加工中极易变形。
在实际生产加工中通过优化改进,最终使得零件的加工难点得到解决。
关键词:薄壁机匣;刚性差;变形前言文章研究的机匣即是某科研机型组件中的一个钛合金材料薄壁类零件。
该零件的质量对整个机械系统运行的稳定性起到很关键作用。
由于该机匣的重要工作表面为内部流道型面部位,因此对于机匣型腔内部流道部位的表面粗糙度要求较高,以保证工作时的精度要求。
零件的材料为TAV6钛合金材料,钛合金材料的特点为导热系数极小,切削热又集中在切削刃附近,所以切削温度很高,使得加工表面容易产生变形,在者钛合金材料的化学性能活泼,在高温下易与大气中的氧、氮等元素化合从而生成硬而脆的物质,加剧刀具磨损,还有钛合金材料弹性模量小,已加工表面的回弹量大,加剧了对刀片后刀面的摩擦,所以这种材料的切削加工性能很差,给机械加工提出了很高的要求,但是由于这种材料的密度小、重量轻、强度高等结构特点,因此在航天航空领域的应用非常广泛,而国外对这种材料的研究比较早,研究的也比较深入,我国对这种材料的研究还比较少,可供借鉴的资料也很少,对于完全掌握这种材料的切削技术还有些难度。
1 零件结构特点及加工难点分析零件最大外廓几何尺寸为直径φ500mm,高度147mm,最薄处壁厚仅为2.3mm,属于典型的回转体薄壁件。
图1为机匣流道示意图。
由于工件刚性差、强度弱,加之零件材料为钛合金,因此流道部位粗糙度难以保证,是加工中的一个难点,针对此问题在加工现场进行了大量的攻关试验,最终该问题得到解决。
图1 机匣流道示意图2 解决流道粗糙度问题优化措施2.1 工装夹具的改进为保证流道粗糙度满足图纸要求,加工过程中必须保证整个工艺系统的稳定性,因此进行合理的装夹及定位是非常关键的,另外切削时夹紧力不能过大,一定要掌握好零件的夹紧力度。
大型薄壁机匣加工工艺研究
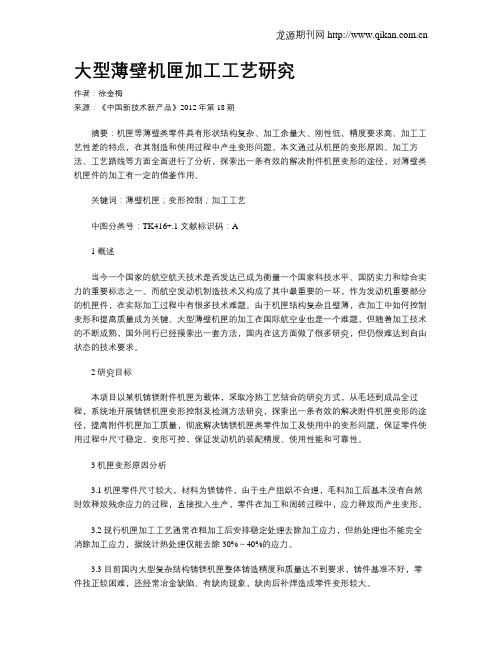
大型薄壁机匣加工工艺研究作者:徐金梅来源:《中国新技术新产品》2012年第18期摘要:机匣等薄壁类零件具有形状结构复杂、加工余量大、刚性低、精度要求高、加工工艺性差的特点,在其制造和使用过程中产生变形问题。
本文通过从机匣的变形原因、加工方法、工艺路线等方面全面进行了分析,探索出一条有效的解决附件机匣变形的途径,对薄壁类机匣件的加工有一定的借鉴作用。
关键词:薄壁机匣;变形控制;加工工艺中图分类号:TK416+.1 文献标识码:A1 概述当今一个国家的航空航天技术是否发达已成为衡量一个国家科技水平、国防实力和综合实力的重要标志之一。
而航空发动机制造技术又构成了其中最重要的一环,作为发动机重要部分的机匣件,在实际加工过程中有很多技术难题。
由于机匣结构复杂且壁薄,在加工中如何控制变形和提高质量成为关键。
大型薄壁机匣的加工在国际航空业也是一个难题,但随着加工技术的不断成熟,国外同行已经摸索出一套方法,国内在这方面做了很多研究,但仍很难达到自由状态的技术要求。
2 研究目标本项目以某机铸镁附件机匣为载体,采取冷热工艺结合的研究方式,从毛坯到成品全过程,系统地开展铸镁机匣变形控制及检测方法研究,探索出一条有效的解决附件机匣变形的途径,提高附件机匣加工质量,彻底解决铸镁机匣类零件加工及使用中的变形问题,保证零件使用过程中尺寸稳定、变形可控,保证发动机的装配精度、使用性能和可靠性。
3 机匣变形原因分析3.1 机匣零件尺寸较大,材料为镁铸件,由于生产组织不合理,毛料加工后基本没有自然时效释放残余应力的过程,直接投入生产,零件在加工和周转过程中,应力释放而产生变形。
3.2 现行机匣加工工艺通常在粗加工后安排稳定处理去除加工应力,但热处理也不能完全消除加工应力,据统计热处理仅能去除30%~40%的应力。
3.3 目前国内大型复杂结构铸镁机匣整体铸造精度和质量达不到要求,铸件基准不好,零件找正较困难,还经常冶金缺陷、有缺肉现象,缺肉后补焊造成零件变形较大。
基于复杂薄壁零件在车铣复合加工工艺探究
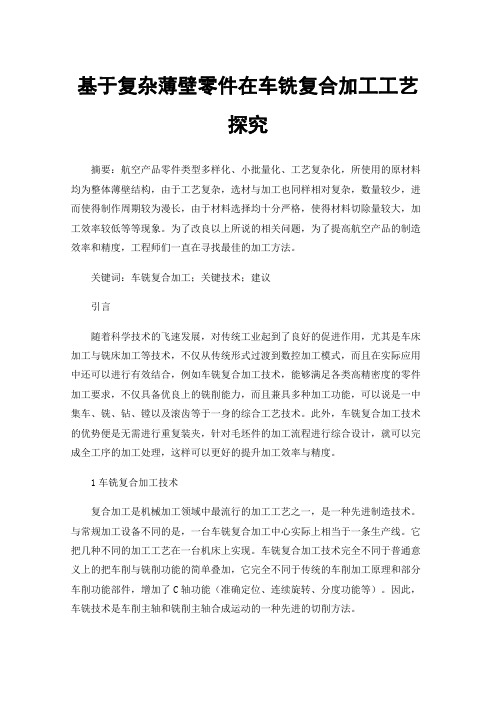
基于复杂薄壁零件在车铣复合加工工艺探究摘要:航空产品零件类型多样化、小批量化、工艺复杂化,所使用的原材料均为整体薄壁结构,由于工艺复杂,选材与加工也同样相对复杂,数量较少,进而使得制作周期较为漫长,由于材料选择均十分严格,使得材料切除量较大,加工效率较低等等现象。
为了改良以上所说的相关问题,为了提高航空产品的制造效率和精度,工程师们一直在寻找最佳的加工方法。
关键词:车铣复合加工;关键技术;建议引言随着科学技术的飞速发展,对传统工业起到了良好的促进作用,尤其是车床加工与铣床加工等技术,不仅从传统形式过渡到数控加工模式,而且在实际应用中还可以进行有效结合,例如车铣复合加工技术,能够满足各类高精密度的零件加工要求,不仅具备优良上的铣削能力,而且兼具多种加工功能,可以说是一中集车、铣、钻、镗以及滚齿等于一身的综合工艺技术。
此外,车铣复合加工技术的优势便是无需进行重复装夹,针对毛坯件的加工流程进行综合设计,就可以完成全工序的加工处理,这样可以更好的提升加工效率与精度。
1车铣复合加工技术复合加工是机械加工领域中最流行的加工工艺之一,是一种先进制造技术。
与常规加工设备不同的是,一台车铣复合加工中心实际上相当于一条生产线。
它把几种不同的加工工艺在一台机床上实现。
车铣复合加工技术完全不同于普通意义上的把车削与铣削功能的简单叠加,它完全不同于传统的车削加工原理和部分车削功能部件,增加了C轴功能(准确定位、连续旋转、分度功能等)。
因此,车铣技术是车削主轴和铣削主轴合成运动的一种先进的切削方法。
2复合加工具有的突出优势2.1缩短产品制造工艺链,提高生产效率车铣复合加工工艺能够在短时间内实现一次装卡完成,亦或是在短时间内完成大部分的加工工序,在时间方面虽短了生产进程。
减少了由于装卡产生的生产辅助时间,减少了产品制造的环节,有效提升生产效率。
2.2减少装夹次数,提高加工精度装卡过程中会改变定位基准,进而产生生产过程中的误差,误差不断积累影响产品的精准性。
复合加工技术在薄壁机匣加工中的应用

复合加工技术在薄壁机匣加工中的应用近年来航空发动机的性能及设计结构在不断改进和提高。
随之而来,发动机机匣零件的材料、结构也发生了很大的变化,越来越多的难加工材料,像钛合金、高温合金、不锈钢、硬质合金以及复合材料等被采用。
机匣设计结构也越来越先进,整体结构机匣、单一机匣所具有的功能也越来越多,因此,机匣零件的制造成形难度也越来越大。
标签:复合加工;机闸加工;铣车随着航空制造技术的发展,新一代飞机发动机的机动性、灵敏性、可靠性大幅提高,高性能飞机发动机大量采用了整体、薄壁复杂结构及难加工材料零件,复杂整体薄壁结构的采用,减轻了发动机零部件的重量,有利于提高发动机推重比,但同时也增加了加工难度。
机匣一般是一个圆柱形或圆锥形的薄壁筒体,主要起承力和包容作用,而且对不同段机匣的要求不一样。
涡轮机匣通常是带有安装边的圆柱形或截锥形壳体,其前后安装边分别与燃烧室机匣和动力涡轮前的中间机匣连接,涡轮机匣上作用有扭矩、轴向力、惯性力和内环压差力等。
近些年,在航空发动机机匣加工领域,具有复杂外型面的整体结构机匣,其外型面的成形加工是普通机械加工工艺所不能实现的,只有应用多轴数控加工技术才能实现复杂外型面的成形加工。
但在加工过程中存在着刀具费用高,加工效率低,设备占用量大。
针对多年来生产中的加工难题,寻求品质的提升、效率的提高、成本降低的途径和方法,运用特种加工技术——电火花加工技术和电解加工技术,同时结合现代数控加工技术,通过对典型结构机匣外型面大量的基础试验研究,取得了良好的加工效果,在保证工艺要求基础上,满足了生产高效益的需求。
1 机匣加工和复合加工技术1.1 机匣电铣加工技术机匣型面的成形,国内通常是通过在多轴数控铣削设备上加工完成的。
该零件外环形面共分二级,分布有二条环形凸缘,下部有1个纵向小凸缘,两个纵向凸缘对称分布。
由于机匣毛坯是自锻件,加工余量很大,且零件材料难切削,为了保证尺寸加工精度和表面加工质量,防止加工后零件变形。
薄壁件复合开孔工装创新设计

薄壁件复合开孔工装创新设计作者:周永龙等来源:《科技创新与生产力》 2018年第11期摘要:针对现有孔加工工装“成本高、使用繁、范围窄”的不足,明确了“分析工艺、综合刀具、钻铣组合”的创新思路,进行工作母盘、工作刀具的设计,探索了新型薄壁件复合开孔工装的实施方式,减少了加工成本,提高了加工效率,增加了适用类型,拓宽了应用范围。
关键词:孔加工;开孔;薄壁件;工装;母盘;刀具中图分类号:TG713 文献标志码:A DOI:10.3969/j.issn.1674-9146.2018.11.091内孔表面是组成机械零件的重要表面之一,在零部件中,内孔表面起到紧固连接、传动、调节质心分布等作用。
孔的类型主要分为紧固连接孔、传动孔、工艺孔等。
其中,紧固连接孔通过各种不同尺寸的螺钉孔、销钉孔或铆钉孔,把零件连接、固定起来;传动孔通过孔与轴的配合类型合理选择,能够让轴和孔之间产生相对运动;工艺孔通过孔的形态与分布,对机械零件本身起到调节、加工的作用,如油孔、减重孔、对定孔等。
孔加工是通过切削设备或成型设备对工件进行加工以产生符合要求的孔的加工过程,包括钻孔、铰孔、镗孔、拉孔、冲孔等方式。
在机械零件中,带孔零件一般要占零件总数的50%~80%,孔的种类也是多种多样的,有圆柱形孔、圆锥形孔、螺纹形孔和成形孔等。
由于孔的种类多样、工件形式各异、加工环境不同,加工方式也不尽相同,对薄板、钣金等薄壁件进行开孔的常用方法是冲孔、钻孔的方式。
冲孔适用于定型薄壁金属件的大批量生产,需要专用机床和模具进行冲压操作,不适应于薄板的单件小批量生产,因此在生产中,对于薄壁件通常采用钻孔加工的方式。
钻孔加工设备可以是手钻、台钻、立式钻床等,刀具一般为麻花钻、锪孔钻,夹具多为弹性夹头。
1 现有薄壁件开孔工装存在的问题图1为市场现有薄壁件开孔工装,其基本结构为成组出现的圆盘刀具,根据开孔的规格大小,选择不同的刀具,在夹紧和传动方式上采用的螺纹旋合夹紧方式,其装配相对复杂耗时,整体表现出“成本高、使用繁、范围窄”的特点[1-2]。
- 1、下载文档前请自行甄别文档内容的完整性,平台不提供额外的编辑、内容补充、找答案等附加服务。
- 2、"仅部分预览"的文档,不可在线预览部分如存在完整性等问题,可反馈申请退款(可完整预览的文档不适用该条件!)。
- 3、如文档侵犯您的权益,请联系客服反馈,我们会尽快为您处理(人工客服工作时间:9:00-18:30)。
复合加工技术在薄壁机匣加工中的应用
摘要:近年来航空发动机的性能及设计结构在不断改进和提高。
随之而来,发动机机匣零件的材料、结构也发生了很大的变化,越来越多的难加工材料,像钛合金、高温合金、不锈钢、硬质合金以及复合材料等被采用。
机匣设计结构也越来越先进,整体结构机匣、单一机匣所具有的功能也越来越多,因此,机匣零件的制造成形难度也越来越大。
关键词:复合加工;机闸加工;铣车
随着航空制造技术的发展,新一代飞机发动机的机动性、灵敏性、可靠性大幅提高,高性能飞机发动机大量采用了整体、薄壁复杂结构及难加工材料零件,复杂整体薄壁结构的采用,减轻了发动机零部件的重量,有利于提高发动机推重比,但同时也增加了加工难度。
机匣一般是一个圆柱形或圆锥形的薄壁筒体,主要起承力和包容作用,而且对不同段机匣的要求不一样。
涡轮机匣通常是带有安装边的圆柱形或截锥形壳体,其前后安装边分别与燃烧室机匣和动力涡轮前的中间机匣连接,涡轮机匣上作用有扭矩、轴向力、惯性力和内环压差力等。
近些年,在航空发动机机匣加工领域,具有复杂外型面的整体结构机匣,其外型面的成形加工是普通机械加工工艺所不能实现的,只有应用多轴数控加工技术才能实现复杂外型面的成形加工。
但在加工过程中存在着刀具费用高,加工效率低,设备占用量大。
针对多年来生产中的加工难题,寻求品质的提升、效率的提高、成本降
低的途径和方法,运用特种加工技术——电火花加工技术和电解加工技术,同时结合现代数控加工技术,通过对典型结构机匣外型面大量的基础试验研究,取得了良好的加工效果,在保证工艺要求基础上,满足了生产高效益的需求。
1 机匣加工和复合加工技术
1.1 机匣电铣加工技术
机匣型面的成形,国内通常是通过在多轴数控铣削设备上加工完成的。
该零件外环形面共分二级,分布有二条环形凸缘,下部有1个纵向小凸缘,两个纵向凸缘对称分布。
由于机匣毛坯是自锻件,加工余量很大,且零件材料难切削,为了保证尺寸加工精度和表面加工质量,防止加工后零件变形。
其外型面加工分层、分块进行,采取合理的走刀路径,采用对称的切削加工余量。
分几次走刀加工到最后尺寸的方法,以减少加工后的变形。
因此,该机匣加工划分三个主要阶段并附加特征工序热处理,以去除材料内应力,防止零件变形。
火花高效放电铣电火花高效放电铣加工技术原理。
电火花高效放电铣借鉴了数控铣削加工方式,采用简单的超长铜管做工具电极,由导向器导向,在工作中电极作高速旋转,在电极与工件之间施加高效高频脉冲电源,电流高达上百安培,对加工区施以冲、浸工作液进行有效冷却排屑,通过专用数控系统控制工件与电极之间的相对运动轨迹,在电极与工件之间产生高效脉冲放电,加工出所需工件的形状,实现零件复杂型面的高效去余量加工。
电火花高效放电铣加工工艺特点。
①可以加工特殊及复杂三维型面的零件。
②加工过程中由于大电流放电作用,增大零件表面的显微裂纹和再铸层厚度。
③脉冲放电持续时间较长,脉冲额率高,增大表面粗糙度值,降低加工精度,材料被加工表面热影响范围太,加工中易产生拉弧烧伤工件表面。
④加工效率比普通电火花加工高,可以达到2000mm3/min。
⑤采用水质工作液,安全无污染并提高加工效率。
⑥与数控加工中心比较,设备的成本相对较低。
1.2 机匣复合加工技术
航空发动机零件的整体化、结构化、轻量化是大推比发动机的重要设计特性之一。
在整体结构零件设计上基本上融合了原来两个单体零件,盘和叶片的加工难度。
车铣复合加工中心适合加工以车削工艺为主,铣削工艺为辅的零件。
五轴车铣复合加工中心的b轴摆头车削技术,对于加工航空发动机零件中一些形状复杂的半封闭型腔凸显出相当大的优势,是近年来发展较快的新技术。
一些机床厂家已经将该项功能作为出售机床的标准配置之一。
2 整体环形机匣铣车复合加工工艺方案
2.1 总体方案
外机匣工艺分析发现,由于该机匣壁厚较薄,属于典型的整体环形机匣,在车加工后会产生一定程度的变形,通常机匣件车加工后,再安排前后安装边及径向安装座孔的加工,这样会造成零件二次装夹找正的困难,二次装夹找正的误差会影响精密定位孔加工的位置度,很难保证加工质量。
航空发动机机匣空间曲面形状较复杂,难
切削材料,零件表面要求无再铸层,无裂纹,加工去除余量大,加工精度要求相对低。
机匣加工要求有足够的加工效率。
这就需要选择适宜的工艺方法,使加工周期缩短,妥善地解决这矛盾,扬长避短,相得益彰。
从理论上讲电火花高效放电铣蚀除机理的电热过程是导致诸多表面裂纹,表面再铸层形成的重要环节。
而且产生过程难于人为控制,且刀具铜电极损耗也较大,为了提高效率必须加大脉宽电流,从而使加工表面再铸层、微裂纹更加加深,表面粗糙度值加大,反之生产效率相对较低,该工艺只适用于加工形状复杂的三维曲面单件加工。
而电解加工是小间隙电化学反应过程,零件表面无冷、热硬化层、无塑性变形、无显微裂纹、无应力、表面粗糙度值低,因此电解加工后零件无中间热处理的周转过程,简化了工艺过程。
2.2 铣车复合加工工艺路线
铣车加工工艺的编制原则:尽量在一次装夹下完成零件多个方向工位的加工。
按照上述的铣车复合工艺编制方法与原则,其工艺路线的设置可采用如下方式:主轴装卡棒料→粗车叶轮外部轮廓→精车外部轮廓→五轴铣削开槽→流道粗加工→流道半精加工→流道精加工→钻孔→背主轴装卡→车削叶轮底部平面→钻孔。
可以看出,一次装卡即完成全部叶轮加工工序,加工效率及精度可以得到大幅提高。
对于具有双刀架的车铣加工中心,双刀塔的设备都具有双通道的控制系统,上下刀架可单独控制,同步加工可以通过代码中的同步语句来实现。
为充分发挥设备的加工能力,可以在加工条
件允许的前提下,通过双刀架的同步操作实现零件的多个工序同时加工。
可以通过上下刀架的同步设置,在粗车外形的同时完成内孔的粗镗加工,从而进一步提高加工效率。
2.3 铣车复合程序的编制
根据铣车复合加工中心数控编程的特点分为铣加工和车加工两种模式,铣加工模式为dm_mill,车加工模式为dm_turn。
在编制五轴联动铣加工程序时,需要激活五轴加工刀尖跟踪功能,数控加工路径前瞻功能g64和加工轴同步协调功能fgroup。
在编制数控车加工程序时,需要使用德马吉五坐标加工中心的平衡功能,在机床屏幕指示的配重位置,按系统提示的重量配置相同重量的配重块,保证车削系统平衡。
采用铣车复合加工技术,实现了车、铣、钻、镗多工序合并加工。
3 结束语
航空发动机机匣空间曲面形状较复杂,难切削材料,零件表面要求无再铸层,无裂纹,加工去除余量大,加工精度要求相对低。
机匣加工要求有足够的加工效率。
这就需要选择适宜的工艺方法,使加工周期缩短,妥善地解陕这矛盾,扬长避短,相得益彰。
对于机匣的加工,采用几种加工工艺相结合的方式,达到优势互补,提高加工的质量和加工的效率,为加工出优质的机匣探索出一条全新的道路。
面对我国加工技术相对落后的情况下,更应探索新的加工方式,开拓进取,创新是永恒的主题。
参考文献
[1]徐斌,刘海波.航空发动机大型机匣电解加工技术研究[a].第二届民用飞机制造技术及装备高层论坛资料汇编(论文集)
[c].2010.
[2]姚宏军,宋秀峰,董顺昌.镁合金航空机匣组合悬挂加工技术研究[a].探索创新交流(第4集)-第四届中国航空学会青年科技论坛文集[c].2010.
[3]丁志伟,陆晓,宣海军.航空发动机复合材料包容机匣的研制
[a].第二届民用飞机制造技术及装备高层论坛资料汇编(论文集)
[c].2010.
[4]李亮.薄壁零件的加工振动分析与加工工艺研究[d].南京航空航天大学,2005.。