衬底制备
Si衬底制作

SiO2+3C=SiC+2CO↑ 总反应式:
2SiC+SiO2=3Si+2CO↑
SiO2+2C=Si+2CO↑
生成的硅由电炉底部放出,浇铸成锭。用此法生产的粗硅 经酸处理后,其纯度可达到99.9%。
2. 三氯氢硅的合成
三氯氢硅是由干燥的氯化氢气体和粗硅粉在合成炉中 (250℃)进行合成的。其主要反应式如下:
Si衬底制备
硅晶片的制备
单晶硅的制备
硅石(SiO2)→工业硅(粗硅) → 高纯的多 晶硅 → 硅单晶
硅晶片的制备
一. 三氯氢硅还原法制备高纯多晶硅
1. 粗硅制备
硅 石 ( SiO2 ) 和 适 量 的 焦 炭 混 合 , 并 在 电 炉 内 加 热 至 1600~1800℃ 可制得纯度为95%~99%的粗硅。其反应式如 下:
硅晶片的制备
反应室
H2
液态三 氯硅烷
制程反 应室
氢和三氯硅 烷
电子级 硅材料
TCS+H2EGS+HCl
载送气体 的气泡
硅晶片的制备
二. Czochralski法直拉单晶硅
直拉法单晶硅工艺过程
引晶:通过电阻加热,将装在石英坩埚中的多晶硅熔化,并保持略高 于硅熔点的温度,将籽晶浸入熔体,然后以一定速度向上提拉籽晶并 同时旋转引出晶体;
SiHCl3沸点低,易燃易爆,全部操作要在低温下进行,一般操作环境温度不 得超过25℃,并且整个过程严禁接触火星,以免发生爆炸性的燃烧。
4. 三氯氢硅的氢还原
提纯SiHCl3和高纯H2混合后,通入1150℃还原炉内进行反应,即可得到硅, 总的化学反应:
SiHCl3+H2=Si+3HCl 生成的高纯多晶硅淀积在多晶硅载体上。
蓝宝石LED衬底工艺流程
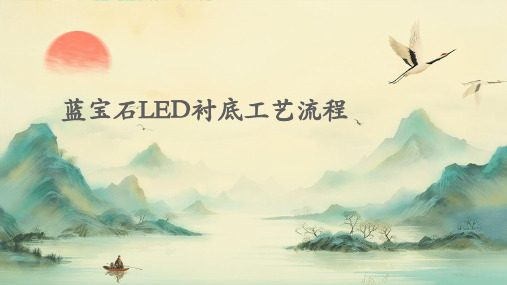
热导
衬底作为芯片散热的主要 通道,将芯片产生的热量 传导至外部。
光学特性
衬底对芯片的光学性能有 影响,如光的吸收、反射 和折射等。
LED衬底材料的种类
蓝宝石
常用作LED衬底材料,具有较高的硬度、化学稳定 性和高热导率。
硅
具有高热导率、低成本和成熟的半导体制造工艺。
碳化硅
具有高热导率、高硬度、高化学稳定性和高抗腐 蚀性。
蓝宝石LED衬底工艺流程
• 引言 • LED衬底概述 • 蓝宝石LED衬底制备工艺流程 • 工艺流程中的关键技术 • 工艺流程中的问题与解决方案 • 结论
01
引言
主题简介
01
蓝宝石LED衬底是LED产业中的重 要组成部分,其工艺流程涉及多 个环节和关键技术。
02
蓝宝石LED衬底具有优异的光学 、热学和机械性能,广泛应用于 照明、显示、背光等领域。
晶体切割
将晶体切割成适当的大小 和形状,以满足后续加工 需求。
切割与研磨的关键技术
切片
抛光
使用刀片或激光将衬底切成适当的大 小。
通过抛光剂和抛光盘对衬底表面进行 抛光,以提高表面光洁度和平整度。
研磨
通过研磨剂和研磨盘对衬底表面进行 研磨,以去除切割痕迹和表面缺陷。
抛光处理的关键技术
选择性抛光
根据衬底表面的不同区域选择不 同的抛光参数,以实现局部抛光。
研究更精确的光刻技术
随着LED芯片尺寸的不断减小,需要更精确的光刻技术来制作更精细 的图案。
发展新型蓝宝石衬底材料
为了满足LED行业的发展需求,需要研究和发展新型蓝宝石衬底材料, 提高其性能和稳定性。
深入研究退火处理技术
退火处理对蓝宝石衬底的性能有很大影响,需要进一步深入研究退火 处理技术,优化退火工艺参数,提高蓝宝石衬底的性能。
半导体工艺(第1章2)衬底材料制备PPT课件

本征吸除:
在晶片内引入一些缺陷,以此吸除在表 面附近的杂质和缺陷;
写在最后
经常不断地学习,你就什么都知道。你知道得越多,你就越有力量 Study Constantly, And You Will Know Everything. The More
国内自造单晶炉设备图如下
直拉法制备单晶硅生长原理
点击视屏
单晶材料中的原生缺陷与有害杂质
硅单晶中存在多种原生缺陷和有害杂质。
宏观缺陷:
孪晶、裂纹、夹杂、位错等
原生缺陷:晶体生长过程中形成的缺陷
微缺陷 :微沉积
➢ 有害杂质是指会影响晶体性质的杂质或杂 质团:施主、受主、重金属、碱金属等。
➢ 孪晶:晶体中有两个或以上生长晶核
(2)晶片平整度:晶片微细加工中,晶片的 翘曲将对图形加工质量产生严重影响。欲 减少翘曲,必须增加晶片厚度、减小晶片 所受的加工应力。
2、器件浅结化对硅材料的要求
➢ 随着器件图形特征尺寸的缩小,器件结深也 越来越浅。
➢ 因此器件特性对硅材料表面质量和界面性质 更为敏感。
➢ 任何表面缺陷都可能引起器件失效或可靠性 降低。
➢ 材料中的缺陷和有害杂质是工艺诱生缺陷 的主要核化中心,因此必须通过单晶生长 过程中的质量控制和后续处理来提高单晶 的质量,使单晶材料趋于完美。
➢ 减少单晶材料缺陷和有害杂质的后续处理 方法通常采用吸除技术。 本征吸除 背面损伤 物理吸除 应力吸除 扩散吸除 吸除技术 溶解度增强吸除 化学吸除
物理吸除过程:
硅单晶体制备
➢多晶硅是制备单晶硅的原始材料 (一)多晶硅制备 多晶硅制备方式主要有三种: ✓ 四氯化硅氢还原法 ✓ 三氯氢硅氢还原法 ✓ 硅烷热分解法
sic衬底制作流程
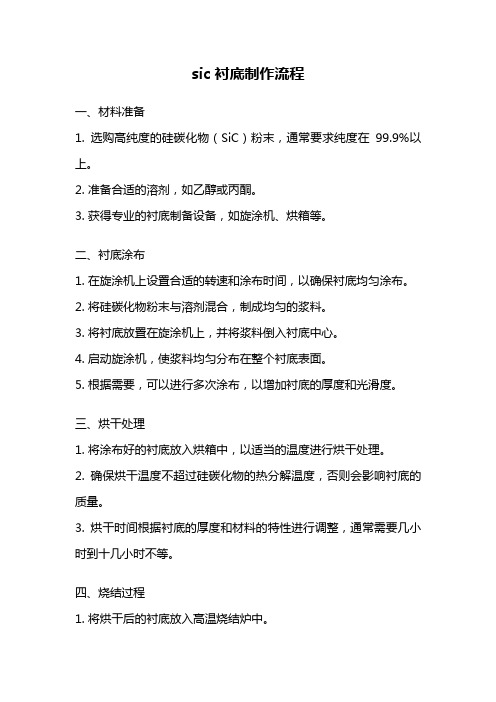
sic衬底制作流程一、材料准备1. 选购高纯度的硅碳化物(SiC)粉末,通常要求纯度在99.9%以上。
2. 准备合适的溶剂,如乙醇或丙酮。
3. 获得专业的衬底制备设备,如旋涂机、烘箱等。
二、衬底涂布1. 在旋涂机上设置合适的转速和涂布时间,以确保衬底均匀涂布。
2. 将硅碳化物粉末与溶剂混合,制成均匀的浆料。
3. 将衬底放置在旋涂机上,并将浆料倒入衬底中心。
4. 启动旋涂机,使浆料均匀分布在整个衬底表面。
5. 根据需要,可以进行多次涂布,以增加衬底的厚度和光滑度。
三、烘干处理1. 将涂布好的衬底放入烘箱中,以适当的温度进行烘干处理。
2. 确保烘干温度不超过硅碳化物的热分解温度,否则会影响衬底的质量。
3. 烘干时间根据衬底的厚度和材料的特性进行调整,通常需要几小时到十几小时不等。
四、烧结过程1. 将烘干后的衬底放入高温烧结炉中。
2. 根据硅碳化物的烧结特性,设置适当的温度和保温时间。
3. 确保烧结过程中的气氛控制,通常采用惰性气体,如氩气。
4. 烧结结束后,待衬底冷却后取出。
五、表面处理1. 根据需要,可以对衬底进行抛光、腐蚀等表面处理,以提高其光滑度和质量。
2. 使用合适的研磨工具和腐蚀剂,对衬底进行处理。
3. 处理后的衬底应经过清洗和干燥,以去除表面的残留物。
六、质量检验1. 对制备好的衬底进行质量检验,包括外观检查、尺寸测量等。
2. 使用适当的仪器和设备,检测衬底的物理和化学性质,如硬度、抗压强度等。
3. 根据相关标准和规范,对衬底的质量进行评估和判定。
4. 如果衬底不合格,需要进行修复或重新制备。
七、包装和存储1. 对合格的衬底进行包装,以防止其受到外界环境的影响。
2. 使用合适的包装材料,如塑料袋、泡沫箱等,将衬底包装好。
3. 在包装上标注衬底的相关信息,如材料、尺寸、批次等。
4. 将包装好的衬底存放在干燥、防尘的环境中,以确保其质量和性能不受损。
总结:sic衬底的制作流程包括材料准备、衬底涂布、烘干处理、烧结过程、表面处理、质量检验以及包装和存储等步骤。
氮化镓衬底工艺流程

氮化镓衬底工艺流程氮化镓(GaN)是近年来发展起来的新型半导体材料,广泛应用于高亮LED、蓝光激光器、高功率场效应管等领域。
其中,GaN晶体的生长过程是至关重要的一步,而衬底是晶体生长的基础,因此GaN衬底的制备工艺显得尤为重要。
本文将从衬底材料、衬底生长、精磨处理和多晶化等方面入手,介绍氮化镓衬底的工艺流程。
一、衬底材料1.1 GaN衬底种类目前,GaN衬底主要有氮化铝衬底(AlN)和氮化硅衬底(SiC)两种。
其中,AlN衬底具有高热导率、热膨胀系数与GaN晶体接近等优点,是制备GaN晶体的一种常用衬底。
而SiC衬底则因其高度匹配的晶格常数,能够有效减小晶格失配引起的缺陷,是制备3~4英寸大尺寸GaN 晶体的优选衬底。
1.2衬底制备AlN衬底的制备流程主要分为以下几个步骤:(1)基底预处理:将去离子水、硝酸和氢氧化钠等用于去除残留金属杂质,保证基底的纯度。
(2)衬底表面处理:利用化学机械抛光(CMP)等方法对基底表面进行处理,达到较好的平整度、粗糙度和表面清洁度。
(3)衬底生长:将生长气氛通过氯化物气相外延法(HVPE)或金属有机化学气相沉积法(MOCVD)等生长工艺,在基底上生长GaN晶体。
SiC衬底的制备流程类似,但具体细节会有所不同。
例如,SiC衬底生长主要采用物理气相沉积法(PVT)等工艺。
二、衬底生长2.1 HVPE生长法HVPE法是制备GaN衬底最常用的生长方式之一,主要流程如下:(1)预处理:将AlN基底经过一定的预热处理,以去除表面吸附水分和氧化物等杂质。
(2)生长室处理:将AlN基底放置于高温、强气流、高氯化镁浓度的生长室中,预热至800~900℃左右后开始生长。
(3)生长过程:利用三氯化铝、氯化镁、氨气等气体在高温、高压下进行反应,形成GaN晶体在AlN衬底上生长。
2.2 MOCVD生长法MOCVD法主要包括以下几个步骤:(1)衬底表面处理:在高温和保护性气氛下,通过物理和化学方法对AlN衬底表面进行处理,如刻蚀和原子层沉积等。
1第一章-硅的晶体结构、环境与衬底制备
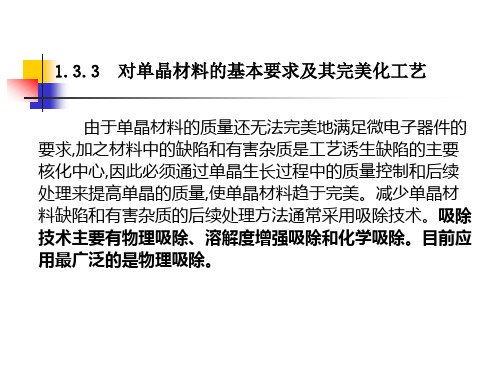
Ⅰ、缺陷密度
由于大直径单晶生长过程中热场控制、生长过程控制更加复杂,以 及装料量的增加,晶体生长时固-液界面扰动、杂质分凝等造成的微区不 匀现象更为严重,从而使晶体缺陷产生的几率增大。 芯片面积的增大,对缺陷密度的要求更加严格。另外,器件尺寸的缩 小,使微缺陷的影响已成为一个不可忽略的重要因素。
Ⅱ、参数的均匀性
大直径单晶生长过程中,掺杂杂质在固-液界面分凝的微区波动 及生长速度的瞬间起伏,将产生单晶电阻率径向和轴向分布的不均 匀性。随着芯片面积的增大和器件图形尺寸的缩小,微区电阻率不 均匀对IC性能的影响更为显著, 影响IC正常工作。
Ⅲ、晶片整度
由于器件尺寸的缩小及芯片面积的增大,在微细加工过程中, 晶片的翘曲将对图形加工质量产生影响,使加工图形畸变变得严重, 即使微小的畸变,只要与加工图形尺寸接近,也会引起器件失效。 晶片的翘曲是影响大直径单晶平整度的主要因素,理论分析表明,晶 片直径愈大、愈容易产生翘曲现象。欲减少翘曲,必须增加晶片厚 度、减小晶片所受的加工应力。
内圆切割法是利用金刚砂的机械磨削作用,将金刚砂粘贴 在刀口,经磨削将单晶棒切割成所需厚度的晶片。磨削过程会 给晶片表面带来不同程度的损伤。损伤层的厚度一般在40- 80μm范围。对于(111)晶面的硅片,为了防止电路制作中埋层 图形畸变,切片时要向最近的〈110〉方向偏3-50。从单晶尾开 始切片,棒尾上翘3-50。主参考面朝外。
1.6.4
超纯气体及化学试剂
(1)超纯气体
气体中的有害杂质除污染晶片外,更为严重的是会破坏器件 结构。例如,氧化过程中,氧气中氮含量过高,将导致在预定时间 内生成的氧化层偏薄,使氧化层耐压下降等现象产生。 微电子加工最常用的化学气体有氧、氮、氢、氩四种气体。 还使用一些特殊气体,例如硅烷、磷烷、四氟化碳、氨气、氯 化氢等,在这些气体中的有害杂质含量只能在10-6数量级。 气体纯度: 气体纯度:VLSI加工中,外延用氢气纯度高达99.99999%。 在使用前,化学气体还需就地进一步提纯。 提纯方法:分子筛、催化剂、玻璃滤球等对气体过滤、去 提纯方法 杂;气体管道、连接附件采用不锈钢管、氟橡胶密封圈等。
sic 衬底制程

sic 衬底制程
SIC(碳化硅)是一种重要的半导体材料,其制造过程就是 sic 衬底制程。
sic 衬底制程是指将硅和碳在高温高压条件下进行反应,形成碳化硅晶体的制造过程。
此外,还需要进行多次退火和化学机械抛光等步骤,最终得到高质量的 sic 单晶衬底。
sic 衬底制程具有以下几个特点。
首先,需要极高的温度和压力才能进行反应,这就需要使用复杂的反应器设备。
其次,反应需要较长的时间,一般需要几个小时到几天不等。
再次,反应的过程中需要控制多个参数,包括温度、压力、反应物浓度等,以确保制备出的 sic 单晶衬底具有高质量的结晶。
sic 衬底制程的应用非常广泛,主要用于制造电力电子、光电子、高温材料等领域的器件。
相对于传统的硅衬底,sic 衬底有着更高的热稳定性和较低的电阻率,能够承受更高的工作温度和电压,因此更加适用于高功率和高频率的电子元件。
同时,sic 衬底的制造难度较大,制造成本也相对较高,因此主要应用于高端市场。
随着半导体技术的不断发展,sic 衬底制程也在不断优化和改进。
目前已经出现了光化学气相沉积(CVD)等新的制备方法,使得sic 单晶衬底的制备更加高效和可控。
未来,随着 sic 衬底制程的进一步发展,相信其应用范围会更加广泛,对半导体产业的发展会起到越来越重要的作用。
- 1 -。
分立器件的工艺流程
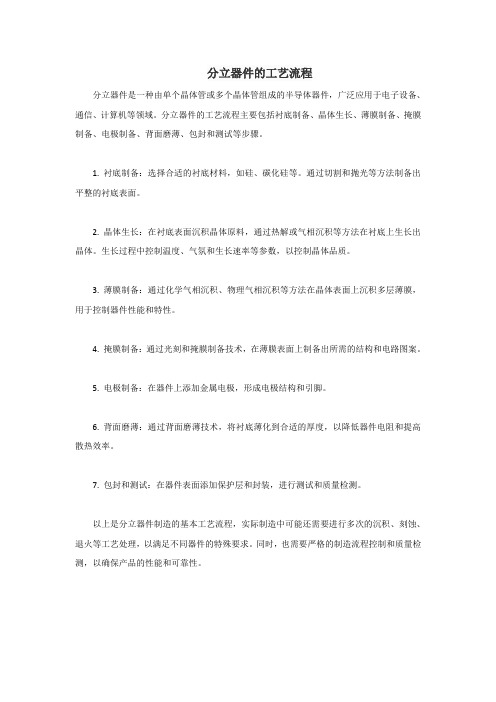
分立器件的工艺流程
分立器件是一种由单个晶体管或多个晶体管组成的半导体器件,广泛应用于电子设备、通信、计算机等领域。
分立器件的工艺流程主要包括衬底制备、晶体生长、薄膜制备、掩膜制备、电极制备、背面磨薄、包封和测试等步骤。
1. 衬底制备:选择合适的衬底材料,如硅、碳化硅等。
通过切割和抛光等方法制备出平整的衬底表面。
2. 晶体生长:在衬底表面沉积晶体原料,通过热解或气相沉积等方法在衬底上生长出晶体。
生长过程中控制温度、气氛和生长速率等参数,以控制晶体品质。
3. 薄膜制备:通过化学气相沉积、物理气相沉积等方法在晶体表面上沉积多层薄膜,用于控制器件性能和特性。
4. 掩膜制备:通过光刻和掩膜制备技术,在薄膜表面上制备出所需的结构和电路图案。
5. 电极制备:在器件上添加金属电极,形成电极结构和引脚。
6. 背面磨薄:通过背面磨薄技术,将衬底薄化到合适的厚度,以降低器件电阻和提高散热效率。
7. 包封和测试:在器件表面添加保护层和封装,进行测试和质量检测。
以上是分立器件制造的基本工艺流程,实际制造中可能还需要进行多次的沉积、刻蚀、退火等工艺处理,以满足不同器件的特殊要求。
同时,也需要严格的制造流程控制和质量检测,以确保产品的性能和可靠性。
hbt工艺流程

hbt工艺流程HBT工艺流程是一种用于制备半导体器件的工艺流程,其全称为Heterojunction Bipolar Transistor,即异质结双极型晶体管。
HBT 工艺流程具有高速、高频、低噪声等特点,在无线通信、微波雷达、光通信等领域有广泛应用。
下面将详细介绍HBT工艺流程的各个步骤。
1. 衬底制备HBT工艺流程的第一步是准备衬底。
衬底可以选择硅、蓝宝石等材料,其选择取决于具体应用需求。
衬底的制备过程包括清洗、抛光等步骤,以保证衬底的表面光洁度和平整度。
2. 区域定义在衬底上进行区域定义是HBT工艺流程的关键步骤之一。
通过使用光刻技术和化学蚀刻技术,将衬底表面划分为不同的区域,用于后续步骤的器件的制备。
3. 材料生长HBT工艺流程中的材料生长是实现异质结的关键步骤。
通过分子束外延、金属有机化学气相沉积等技术,将不同材料层按照特定的序列和厚度生长在衬底上,形成异质结。
4. 掺杂为了调控材料的导电性能,HBT工艺流程中需要对不同区域进行掺杂。
掺杂可以使用离子注入、扩散等技术进行,以改变材料的电子浓度和类型。
5. 制备金属电极HBT工艺流程的下一步是制备金属电极。
通过光刻、金属蒸镀、电子束蒸镀等技术,在相应的区域上制备电极,用于连接器件的外部电路。
6. 薄膜制备HBT工艺流程中的薄膜制备是为了保护器件和提高性能。
通过溅射、化学气相沉积等技术,在器件表面形成一层薄膜,以提高器件的稳定性和可靠性。
7. 电性测试在HBT工艺流程的最后一步,需要对制备好的器件进行电性测试。
通过测试仪器对器件的电流、电压、功率等参数进行测量,以验证器件的性能和工作状态。
总结起来,HBT工艺流程包括衬底制备、区域定义、材料生长、掺杂、制备金属电极、薄膜制备和电性测试等多个步骤。
每个步骤都有其特定的目的和操作方法,通过这些步骤的有序进行,可以制备出高性能的HBT器件。
HBT工艺流程的不断改进和优化,为半导体器件的发展和应用提供了坚实的基础。
叠层太阳能电池工艺流程

叠层太阳能电池工艺流程叠层太阳能电池是一种多层结构的太阳能电池,由不同材料组成的多层薄膜或晶体层叠而成。
其工艺流程主要包括以下几个关键步骤:1.衬底制备:选择合适的衬底材料,常用的有玻璃、金属、聚合物等。
衬底上可能需要进行一系列的前处理,如清洗、抛光等。
2.底层薄膜沉积:在衬底上通过化学气相沉积(CVD)、物理气相沉积(PVD)或溶液法等方法沉积底层薄膜,常见的底层材料有氮化镓(GaN)、氧化锌(ZnO)等。
3.活性层沉积:在底层薄膜表面沉积光电转换的活性层材料。
常用的活性层材料有硅(Si)、硒化铜铟(CIGS)、硫化钙钛矿(perovskite)等。
4.透明导电层沉积:在活性层上方沉积一层透明导电材料,主要用于收集光电转换的电流。
常用的透明导电层材料有氧化锡(SnO2)和氧化铟锡(ITO)等。
5.顶层透明保护层沉积:为了提高太阳能电池的稳定性和抗氧化性,可以在透明导电层上方沉积一层透明保护层。
常用的材料有二氧化硅(SiO2)、氮化硅(SiNx)等。
6.电极制备:在顶层透明保护层上方制备金属电极,常用的金属有铝(Al)、银(Ag)等。
电极通过光电转换层和导电层收集电流,并提供外界接触的导电路径。
7.封装和背板制备:将制备好的太阳能电池进行封装,以保护电池结构和材料不受外界环境的影响。
封装通常包括背板、密封层和玻璃保护面板等。
以上是叠层太阳能电池的基本工艺流程,具体流程和材料的选择可能因不同的技术和制造商而有所差异。
叠层太阳能电池的制备过程较为复杂,需要高精度设备和严密的工艺控制,以确保高效的能量转换和稳定的性能。
硅材料及衬底制备

优化硅衬底的表面质量和完整性,降低缺陷密度和杂质含量。
THANKS FOR WATCHING
感谢您的观看
硅衬底还可用于制造光伏组件,提高光伏发电的效率和可靠 性。
传感器领域的应用
压力传感器
硅材料具有高灵敏度、低滞后性和长期稳定性等特点,可用于制造压力传感器。
温度传感器
硅材料也可用于制造温度传感器,其具有响应速度快、精度高等优点。
其他领域的应用
生物医学
硅材料在生物医学领域中可用于制造 人工关节、牙齿等医疗器件。
硅的化学性质
稳定性
硅在常温下不易与氧、氮、氯等 非金属元素反应。
还原性
硅能够被碳、氢气等还原剂还原。
氧化性
在高温下,硅能够与氧反应生成二 氧化硅。
硅的分类与用途
01
02
03
04
单晶硅
用于制造集成电路、太阳能电 池等。
多晶硅
用于制造太阳能电池、电子器 件等。
纳米硅粉
用于制造涂料、橡胶、塑料等 高分子材料。
上沉积形成非晶硅薄膜。
化学气相沉积法
利用化学反应在衬底上沉积形成 非晶硅薄膜,常用的反应气体为
硅烷和氢气。
物理气相沉积法
利用物理方法将硅原子或分子沉 积在衬底上形成非晶硅薄膜。
04
硅材料及衬底的应用
微电子领域的应用
集成电路
01
硅材料是集成电路制造中最重要的基础材料之一,用于制造芯
片中的晶体管、电容、电阻等元件。
硅材料及衬底制备
contents
目录
• 硅材料基础 • 硅材料制备技术 • 硅衬底制备技术 • 硅材料及衬底的应用 • 硅材料及衬底的发展趋势与挑战
衬底制备与外延工艺

衬底制备与外延工艺一、衬底制备硅是自然界中蕴含最丰富的元素之一,在地壳的含量仅次于氧。
随着现代半导体器件和集成电路技术的发展,硅单晶已成为最重要的集成电路衬底材料,是制作复杂微电子器件的基础。
半导体单晶材料是由多晶材料经过提纯、掺杂和拉制等工序制得,但这些单晶材料还不能直接用于半导体器件的制造。
单晶材料经过切片、研磨、倒角、腐蚀和抛光等工序的加工,获得符合一定标准(厚度、晶向、平整度、平行度和损伤层)的单晶薄片,才可以供给外延或管芯制造使用,这个加工过程一般称为衬底制备。
多晶硅制备单晶硅制备切片研磨倒角定向腐蚀抛光检验衬底晶片其中,由于单晶体具有各向异性的特点,必须按一定的晶向切割才能避免碎片和不影响器件的电参数,同时不同的半导体器件所要求的晶向也往往不同,所以切片前必须确定单晶锭的取向,然后沿某一晶向进行切片。
在制作器件的大圆片上缺口所在的平面,即为定位面;研磨的目的是去除切片的刀痕和损伤层,使晶片表面平整光洁,并达到预期厚度要求,所用的高硬度磨料有金刚石、碳化硅等;倒角即将晶片边缘磨圆,以防止在以后的加工过程中发生崩边,产生碎屑;腐蚀目的是去除表面的加工损伤、应力,并使晶片有一个比较致密和清洁的背面,传统方法是采用氢氟酸和硝酸的混酸溶液;抛光目的是进一步去除加工表面残留的损伤层,以获得平整、光洁、无损伤层并有一定厚度的晶片,方法有机械研磨、化学抛光和两者结合的化学机械抛光。
抛光对于制作器件是最关键的一步,抛光片可直接用于制作器件,也可作为外延的衬底材料。
二、外延外延指在单晶衬底上生长一层新单晶的过程,新生单晶层的晶向取决于衬底,沿着原来的结晶轴方向由衬底向外延伸而成,故名外延。
因此外延生长的结构是衬底与外延层呈一个连续的单晶体,但是衬底与外延层的物质成分不一定相同,晶体结构也不一定相同,当两者材料相同时称为同质外延,例如在硅衬底上外延硅。
虽然抛光片已可直接用于制作器件,但是利用外延可以生产种类更多的材料,使器件设计有了更多的选择。
衬底制备与外延工艺

衬底制备与外延工艺一、衬底制备硅是自然界中蕴含最丰富的元素之一,在地壳的含量仅次于氧。
随着现代半导体器件和集成电路技术的发展,硅单晶已成为最重要的集成电路衬底材料,是制作复杂微电子器件的基础。
半导体单晶材料是由多晶材料经过提纯、掺杂和拉制等工序制得,但这些单晶材料还不能直接用于半导体器件的制造。
单晶材料经过切片、研磨、倒角、腐蚀和抛光等工序的加工,获得符合一定标准(厚度、晶向、平整度、平行度和损伤层)的单晶薄片,才可以供给外延或管芯制造使用,这个加工过程一般称为衬底制备。
其中,由于单晶体具有各向异性的特点,必须按一定的晶向切割才能避免碎片和不影响器件的电参数,同时不同的半导体器件所要求的晶向也往往不同,所以切片前必须确定单晶锭的取向,然后沿某一晶向进行切片。
在制作器件的大圆片上缺口所在的平面,即为定位面;研磨的目的是去除切片的刀痕和损伤层,使晶片表面平整光洁,并达到预期厚度要求,所用的高硬度磨料有金刚石、碳化硅等;倒角即将晶片边缘磨圆,以防止在以后的加工过程中发生崩边,产生碎屑;腐蚀目的是去除表面的加工损伤、应力,并使晶片有一个比较致密和清洁的背面,传统方法是采用氢氟酸和硝酸的混酸溶液;抛光目的是进一步去除加工表面残留的损伤层,以获得平整、光洁、无损伤层并有一定厚度的晶片,方法有机械研磨、化学抛光和两者结合的化学机械抛光。
抛光对于制作器件是最关键的一步,抛光片可直接用于制作器件,也可作为外延的衬底材料。
二、外延外延指在单晶衬底上生长一层新单晶的过程,新生单晶层的晶向取决于衬底,沿着原来的结晶轴方向由衬底向外延伸而成,故名外延。
因此外延生长的结构是衬底与外延层呈一个连续的单晶体,但是衬底与外延层的物质成分不一定相同,晶体结构也不一定相同,当两者材料相同时称为同质外延,例如在硅衬底上外延硅。
虽然抛光片已可直接用于制作器件,但是利用外延可以生产种类更多的材料,使器件设计有了更多的选择。
外延的具体作用有:外延层的掺杂浓度受控于反应气流中的杂质含量,.在外延层与衬底间形成的P-N结杂质分布可接近于理想的突变结;双极型电路的隔离问题可通过外延和隔离扩散技术相结合解决;在重掺的衬底上生长具有较高电阻率的外延层,可以解决器件的击穿电压与串联电阻之间的矛盾、频率与功率之间的矛盾,等等。
外延,扩散,离子注入,衬底制备

7.7 分子束外延(MBE)
MBE:Molecular Beam Epitaxy 原理:在超高真空下,利用薄膜组分元素受热蒸发所 形成的原子或分子束,直接射到衬底表面,形 成外延层。 应用:元素半导体—Si、Ge 化合物半导体-GaAs、GaN、SiGe MBE的特点: ①温度低; ②生长速度低; ③化学组成及掺杂浓度精确可控; ④厚度可精确控制到原子级;
SOI技术的特点与优势
1.速度高 :在相同的特征尺寸下,工作速度可提高 30-40%; 2.功耗低: 在相同的工作速度下,功耗可降低 50 % - 60%; 3.特别适合于小尺寸器件; 4.特别适合于低压、低功耗电路; 5.集成密度高 : 封装密度提高约40%; 6.低成本: 最少少用三块掩模版,减少13%-20% (30%)的工序; 7.耐高温环境: 工作温度300℃-500℃; 8.抗辐照特性好: 是体硅器件的50-100倍。
绪论
外延的分类 ①按工艺分类: 气相外延(VPE):硅的主要外延工艺; 液相外延(LPE):Ⅲ-Ⅴ化合物的外延; 固相外延(SPE):离子注入退火过程; 分子束外延(MBE,Molecular Beam Epitaxy) ②按材料分类 同质外延:外延层与衬底的材料相同,如 Si上外延Si,GaAs上外延GaAs; 异质外延:外延层与衬底的材料不相同,如 Si上外延SiGe 或 SiGe上外延Si; 蓝宝石上外延Si-- SOS(Silicon on Sapphire); 蓝宝石上外延GaN、SiC。 ③按压力分类 常压外延:100kPa ; 低压(减压)外延:5-20kPa。
7.9 外延层电阻率的测量
方法:四探针法、三探针法、电容-电压(CV)法、扩展 电阻法等 扩展电阻法 特点:可以测量微区的电阻率或电阻率分布。 原理:当金属探针与半导体材料呈欧姆接触时,电阻主 要集中在接触点附近的半导体中,而且呈辐射状 向半导体内扩展。 采用探针形式:单探针、两探针、三探针。 下面以右图所示单探 针为例进行原理说明。
《衬底制备》课件

《衬底制备》PPT课件
在这个《衬底制备》的PPT课件中,我将向大家介绍衬底的定义及分类,衬底 制备的重要性,工艺流程和方法,主要衬底生产商及其产品,应用领域以及 发展前景。
衬Hale Waihona Puke 的定义及分类衬底定义衬底是一种用于生长薄膜或器件的基底材料,具有特定的物理和化学特性。
衬底分类
衬底可以根据材料、形状和用途等因素进行分类,常见的有硅衬底、玻璃衬底、金属衬底等。
根据应用需求选择合适的衬 底材料,考虑物理、化学特 性以及成本等因素。
处理和清洗
对衬底进行表面处理和清洗, 去除杂质和表面缺陷,提高 衬底的质量。
薄膜生长
使用化学气相沉积、物理气 相沉积等技术在衬底上生长 所需的薄膜。
主要衬底生产商及其产品
硅衬底
硅衬底是最常见的衬底材料之 一,提供稳定的物理和化学性 能。
液晶显示器、有机发光二极管等显示器件需要稳定的衬底制备技术。
衬底制备的发展前景
1
工艺改进
2
不断改进衬底制备工艺,提高薄膜生
长质量和器件性能。
3
新材料研究
研究新型衬底材料,如柔性衬底、二 维材料衬底等,拓展应用领域。
多功能衬底
开发具有多种功能的衬底材料,满足 不同应用需求。
总结和展望
衬底制备是一项关键的技术,在材料制备和器件制备中起着重要作用。随着 新材料和工艺的不断发展,衬底制备将继续迎来新的突破和应用。
衬底制备的重要性
1 薄膜生长质量
合适的衬底可以提供高质量的薄膜生长环境,影响薄膜的性能和特性。
2 器件性能
衬底的性质和表面特征对器件的性能有着重要影响,如电子器件的导电性能、光学器件 的透明度等。
3 工艺可行性
碳化硅衬底加工过程
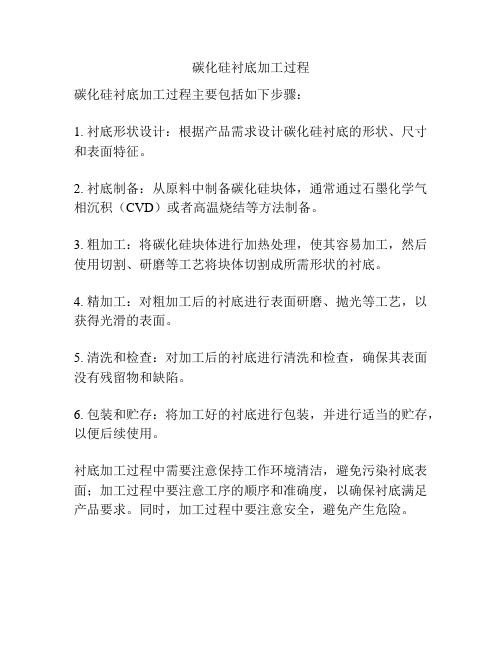
碳化硅衬底加工过程
碳化硅衬底加工过程主要包括如下步骤:
1. 衬底形状设计:根据产品需求设计碳化硅衬底的形状、尺寸和表面特征。
2. 衬底制备:从原料中制备碳化硅块体,通常通过石墨化学气相沉积(CVD)或者高温烧结等方法制备。
3. 粗加工:将碳化硅块体进行加热处理,使其容易加工,然后使用切割、研磨等工艺将块体切割成所需形状的衬底。
4. 精加工:对粗加工后的衬底进行表面研磨、抛光等工艺,以获得光滑的表面。
5. 清洗和检查:对加工后的衬底进行清洗和检查,确保其表面没有残留物和缺陷。
6. 包装和贮存:将加工好的衬底进行包装,并进行适当的贮存,以便后续使用。
衬底加工过程中需要注意保持工作环境清洁,避免污染衬底表面;加工过程中要注意工序的顺序和准确度,以确保衬底满足产品要求。
同时,加工过程中要注意安全,避免产生危险。
- 1、下载文档前请自行甄别文档内容的完整性,平台不提供额外的编辑、内容补充、找答案等附加服务。
- 2、"仅部分预览"的文档,不可在线预览部分如存在完整性等问题,可反馈申请退款(可完整预览的文档不适用该条件!)。
- 3、如文档侵犯您的权益,请联系客服反馈,我们会尽快为您处理(人工客服工作时间:9:00-18:30)。
细颈
放肩
等径
3. 随着单晶的生长,坩埚必须自动 随着单晶的生长, 坩埚必须自动 跟随液面下降而上升,保持液面在 跟随液面下降而上升 , 保持液面在 温度场中的位置不变, 以获得均匀 收尾 温度场中的位置不变, 的电阻率; 同时拉晶速度自动调节 的电阻率;同时拉晶速度自动调节 以保持等径生长。 直拉法生长单晶过
二. 硅单晶制备方法 硅单晶制备方法
直拉法 直拉法CZ CZ* *(Czochralski) 区熔法FZ FZ* *(Float Float-Zone Zone) 中子嬗变掺杂法
多晶硅的性质:
多晶体结构的示意图
1. 化学性质与单晶硅大致相同,与硅有相似的腐蚀方法 化学性质与单晶硅大致相同,与硅有相似的腐蚀方法; 2. 电阻率 电阻率 很高 很高(105~10 ~107 cm), 与N N之间的关系比较复杂。 可进行掺杂,形成 可进行掺杂 ,形成P P型或N 型多晶硅(MOS (MOS的栅极)。 。
如:300K下在纯净硅中掺入 微量的杂质磷原子,使硅的纯 度为99.9999%,其电阻率由21400Ω· cm变为0.2Ω· cm。
T → ni(T) 当硅中掺入Ⅴ族元素(P、As) 时,硅中多数载流子为电子 — — N 型半导体。掺杂浓度用N D(CD)表示。 当硅中掺入Ⅲ族元素(B、Al) 时,硅中多数载流子为空穴 — — P型半导体。掺杂浓度用NA (CA) 表示。 当硅中掺入两种杂质(B、P)时,— — 补偿半导体。 如N D>NA,则补偿后为N型;N A>ND,则补偿后为P型;
15 2010年 4月3日
等径
收尾
16
程示意图
固 过液
基本原理
拉制大直径单晶硅的注意事项 拉制大直径单晶硅的注意事项
1. 晶体旋转方向的选择: 晶体旋转方向的选择:
在拉制单晶时,熔硅中存在着由 在拉制单晶时, 熔硅中存在着由dT/dz和转动引起的热对流, 转动引起的热对流, 会使液面出现波纹和起伏 ,从而造成 会使液面出现波纹和起伏, 从而造成界面杂质过渡区的不平衡 界面杂质过渡区的不平衡 和不稳定, 导致单晶径向电阻率不均匀。为了保证热对流的稳 为了保证热对流的稳 定性,一般采用晶体旋转方向与坩埚旋转方向相反来抑制。
2010年 4月3日
悬浮区熔法
直拉单晶的特点 直拉单晶的特点 1.
3 C、O O含量较高 含量较高,高达 ,高达10 1018 cm-3
原因:熔硅中的C与石英 与石英SiO 2 发生反应生成CO CO,受热 对流影响不易挥发。 对流影响不易挥发。
2. 3.
直拉法适宜拉制直径大、电阻低的硅单晶; 直拉法适宜拉制 直径大、电阻低的硅单晶;
2. 晶体旋转速度的选择
1. 1. 在转化的过程中, 在转化的过程中,界面附近区域(过渡层)中存在着由 界面结晶硅的热流密度和由熔硅界面的热流密度; 两者之差为界面区单位时间内释放的潜能; 2. 随着晶体生长,部分熔硅转化为晶体,使液面不断下降。 随着晶体生长,部分熔硅转化为晶体,使液面不断下降。 3. 为了形成n型或p型衬底材料,拉晶过程中可加入掺杂剂。 型衬底材料,拉晶过程中可加入掺杂剂。
2. 半导体材料按组分划分
Eg大 Eg 大 →高温器件; 元素半导体(如:硅Si Si和锗 和锗Ge) )成本低。
化合物半导体(如:砷化镓GaAs 化合物半导体(如:砷化镓 GaAs 、磷化铟 、磷化铟InP InP) )
二 二.. 半导体材料的基本特性
1.半导体材料的导电能力 1. 半导体材料的导电能力
将多晶硅 多晶硅在 在 真空或惰性气体 真空或惰性气体保护下 保护下加热 加热,使多晶硅熔 ,使多晶硅熔 来拉制单晶硅。 单晶生长过程实际 化,然后利用籽晶 籽晶来拉制单晶硅。 上是硅由液相 固相的转化过程。 该转化过程实现的 条件:液相-固相界面附近存在温度梯度(dT/dz) )。
说明 :
请记录
2010 年4月3 日 17
由于熔硅中的 由于熔硅中的C与石英 与石英(( SiO SiO2 )坩埚反应生成 SiO 和CO ,两者的 挥发受热对流和熔硅外表面氩气的影响变得不稳定,引起液面 波动。采用旋转晶体形成的强迫对流会减少 波动。采用旋转晶体形成的 强迫对流会减少CO 挥发 挥发, , 导致硅 单晶中含O O量过高 量过高。因此, 。因此,单晶的旋转速度要优化选择 单晶的旋转速度要优化选择。 。
半导体工艺原理
主 要内 容
1-1 半导体硅材料 半导体硅材料简介 简介
第1章
硅材料及衬底制备
2010 · 春
XAUT
半导体材料的分类与基本特性 半导体材料硅的结构特征 集成电路对硅材料的要求
半导体硅原材料的提纯 大直径硅单晶的制备方法 半导体单晶材料中的缺陷及有害杂质 杂质吸除技术
单晶棒的整形与定向 晶片加工
2 2/a2 2 2/a2
4 3/3a 2 (min) 2 3/3a 2
4 3/a 2 (max) 2 3/a 2
2. 集成电路技术的发展与硅材料的关系
① 集成电路的特征尺寸逐渐缩小,芯片面积逐渐增大; 集成电路的特征尺寸逐渐缩小,芯片面积逐渐增大; ② 降低生产成本,提高硅晶圆片的直径; ③ 集成电路的器件结构越来越趋向硅圆片的浅表层; 集成电路的器件结构越来越趋向硅圆片的浅表层 ; ④ ④ 集成电路制造应采取尽可能 低的加工温度来完成,需采 用杂质吸除技术。 ⑤ 为满足高性能和高集成度, 为满足高性能和高集成度, 采用多层薄膜结构; 采用多层薄膜结构; ⑥ 对单晶材料的检测分析方法 和测试工具提出高要求。
点 ): 1. 基本要求(6 (6点 : 导电类型 导电类型: N型或P型,μn > μ p ; 电阻率 电阻率: 大小,径向、轴向及微区均匀性和真实性要高; 寿命 寿命: 均匀性和真实性要高; 晶体的完美性 晶体的完美性: 无晶格缺陷和有害杂质沉积; 晶向标识: 标识出反映衬底材料晶向的主、次定位面。 晶向: 双极型器件要求用<111>晶向的单晶;MOS器件要
精馏提纯 多级物化精馏
高纯多晶硅
2. 多晶硅的结构特点与性质
单晶:指在 指在整个晶体内 整个晶体内原子都是周 原子都是周 期性的规则排列 。 多晶:指在晶体内每个局部区域里 原子是周期性的规则排列, 原子是周期性的规则排列 ,可以看成 是由许多取向不同的小单晶体 (晶粒) ) 组成的。在晶粒之间存在一个很薄 的过渡层(晶粒间界),在该层内必须 实现晶向转变。
主要用于VLSI 器件的制作;
2010年 4月3日 18
直拉单晶的发展现状 直拉单晶的发展现状
现有工艺水平,目前国外采用直拉法可生产、研制 现有工艺水平,目前国外采用直拉法可生产、研制 6~18″ ″的硅单晶( 的硅单晶( 150~450mm)
2. 区熔法
制备过程
将预先处好的多晶硅棒和籽晶 粘在一起,竖直固定在区熔炉 的上、下轴之间,以高频感应 的上、下轴之间,以高频感应 线圈等方法加热。 线圈等方法加热。 利用电磁场浮力和熔硅表面的 张力与重力的平衡作用,使所 张力与重力的平衡作用,使所 产生的熔区能稳定地悬浮在硅 棒之间; 真空或氩气、氢气等气氛 在真空或氩气、氢气 等气氛 下,按照特定的工艺条件,使 溶区在硅棒上从头至尾定向移 定向移 动,如此反复多次,使多晶硅 ,如此反复多次,使多晶硅 棒沿籽晶长成单晶硅。 棒沿籽晶长成单晶硅。
ni ( T ) AT 3 / 2e
E g / 2 kT
③导电能力随 光照、外加电场、磁场的作用 ③导电能力随 光照、外加电场、磁场的作用而发生显著变化。 而发生显著变化。
2010 年4月3 日 5
2010年 4月3日
N D=NA— — 补偿型本征半导体。
6
三. 三. 半导体硅材料的结构特征 半导体硅材料的结构特征
2
1-2 大直径硅单晶材料 大直径硅单晶材料的制备 的制备
1-3 衬底制备方法 衬底制备方法
西安理工大学电子工程系
王彩琳
2010年 4月3日
本章参考书::
1. 刘玉岭 刘玉岭 等编,《 等编,《微电子化学技术基础 微电子化学技术基础》 》 ,化学 工业出版社,2005 工业出版社,2005 2. 李乃平 李乃平 主编, 主编,《 《微电子器件工艺》,华中理工 大学出版社 大学出版社, 1995 3. 关旭东 关旭东 编著,《 编著,《硅集成电路工艺基础 硅集成电路工艺基础》 》 ,北京 大学出版社, 大学出版社, 2008 2008 4. 张厥宗 张厥宗 编著,《 编著,《硅单晶抛光片的加工技术 硅单晶抛光片的加工技术》 》, 化学工业出版社 化学工业出版社, ,2005 2005
求用<100>晶向的单晶。
9 2010年 4月3日 10
(解理面)
双原子面内
面间距
a/4
2a/4 2 2/a
2
3a/4 (max) 4 3/3a
2
3a/12 (min) 4 3/3a
2
2/a 2 原子面密度 (min) 晶面间共价 4/a 2 键面密度 可用键密度 2/a 2
2010 年4月3 日
2010 年4月3 日 11
§1.2 大直径单晶材料的制备
一 . 半导体硅的原材料
1. 原材料的提纯
原料(石英石-SiO2) 粗硅 四氯化硅
高温氯化 Si+2Cl2=SiCl 2 (500 ℃~700℃氯化 ) 冷凝后为液态
高温碳还原 SiO2+2C=Si+2CO (1600℃~1800℃)
高纯四氯化硅
①导电能力随温度上升而迅速增加