中密度纤维板生产工艺设计
5000吨每年PET生产工艺流程设计

This design for the annual output of5000tons of polyethylene terephthalate process preliminary design, the direct polycondensation production methods. The process including esterification, condensation, condensation of three stages. Usingthreekettle process technology.
(3)生产集约化程度不高。装置规模小,生产效率低,生产成本高,缺乏竞争力。企业单线规模除仪化、龙涤、开平和翔鹭等具有单线300~400吨/天能力外,绝大部分为100吨/天、200吨/天能力。在整厂规模上,除仪化、上化、辽化及翔鹭具备20万吨/年以上能力外,大部分在6万吨/年左右和以下,而目前世界聚酯经济规模单厂产能一般在20万吨/年以上。而目前生产能力在6万吨/年以下和采用间歇法工艺路线的小型聚酯装置的生产能力约占我国聚酯总生产能力的50%,造成装置平均生产能力很低,难以发挥规模效益。据测算,小型聚酯装置单位生产能力投资比大型聚酯装置约低20%,而运行能耗增加约30%,损耗多10%以上,而且产品质量较差。
我国的PET生产规模远远落后于国外几个主要生产厂商。进入80年代,我国逐步从国外引进万吨~几十万吨级先进的PET树脂合成装置,质量和产量都有了长足的进展。根据中国防治学会统计,1997年我国生产的PET切片树脂174万吨,其中高黏度包装用(饮料瓶和包装片材等)切片树脂生产能力为22.4万吨,所以生产PET工程塑料级的树脂来源充足。由于制备各种混配改性PET塑料的装置于其他聚合物混配改性用的装置是通用的,国内混配用挤出机等制造业形成一定规模,所以只要市场一旦开拓,国内PET塑料的生产也会快速增长。
大学《家具及木制品加工工艺》试题

《家具及木制品加工工艺》试题2014年10月高等教育自学考试《家具及木制品加工工艺》试题课程代码:04482一、单项选择题(本大题共10小题,每小题1分,共10分)1.锯材是指原木经制材加工所得到的产品。
按锯材年轮切线与宽材面的夹角分类,锯材又分为径切板和( D ).A.边切板 B.平切板 C.竖切板 D.弦切板2.现代家具中最普遍使用的三类五金配件,常被称之为“三大件”的除了暗铰链、滑道(滑轨),还有( A ).A.连接件 B.金属件 C.零配件 D.活动件3.蜂窝空心板质轻,适合制造板式家具,特别适合作( D ).A.弯曲部件 B.折叠部件 C.连接部件 D.活动部件4.单板层积材(LVL)是将较厚的单板接长,再按纹理方向相同组坯后胶合而成的材料,其工艺类似于多层胶合板,所以又称( C ).A.空心板 B.复合板 C.平行胶合板 D.纤维板5.在材料选用方面应力求合理,为充分利用木材,提高木材利用率,应大量采用人造板、人造薄木、弯曲胶合等新材料和( D ).A.新方法 B.新工序 C.新技术 D.新工艺6.涂料涂饰含填孔、染色或着色、涂底漆、涂面漆和( A ).A.涂层干燥 B.涂层打磨 C.涂层抛光 D.涂层打蜡7.锯材宽度受( D )的限制,并具有天然缺陷,如节子、斜纹理等。
A.原木半径 B.原木周长 C.原木体积 D.原木直径8.木材软化处理的方法有蒸煮法、高频加热法、微波加热法和( B ).A.甲醛处理法 B.氨处理法 C.氧处理法 D.氮处理法9.不同颜色、质地的木块、兽骨、金属、岩石、龟甲、贝壳等拼合组成一定的纹样图案,再嵌入或粘贴在木制品表面上的一种装饰方法,即为( A ).A.镶嵌 B.浮雕 C.线雕 D.镶金10.零件在加工之后所得到的尺寸、形状、表面特征等几何参数和图纸上规定的零件的几何参数相符合的程度是( B ).A.加工设备 B.加工精度 C.加工方法 D.加工工艺二、填空题(本大题共10小题,每小题1分,共10分)11.木制品加32212艺学的研究内容包括:木制品材料、木制品结构及木制品加工工艺。
关于人造板的几个技术问题
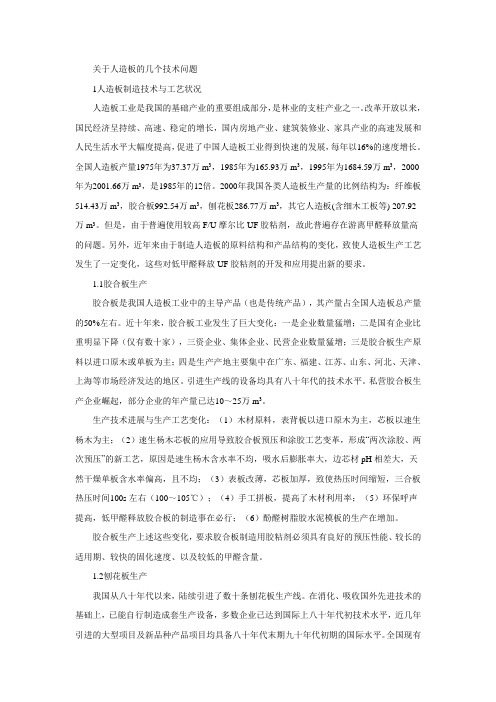
关于人造板的几个技术问题1人造板制造技术与工艺状况人造板工业是我国的基础产业的重要组成部分,是林业的支柱产业之一。
改革开放以来,国民经济呈持续、高速、稳定的增长,国内房地产业、建筑装修业、家具产业的高速发展和人民生活水平大幅度提高,促进了中国人造板工业得到快速的发展,每年以16%的速度增长。
全国人造板产量1975年为37.37万m3,1985年为165.93万m3,1995年为1684.59万m3,2000年为2001.66万m3,是1985年的12倍。
2000年我国各类人造板生产量的比例结构为:纤维板514.43万m3,胶合板992.54万m3,刨花板286.77万m3,其它人造板(含细木工板等) 207.92万m3。
但是,由于普遍使用较高F/U摩尔比UF胶粘剂,故此普遍存在游离甲醛释放量高的问题。
另外,近年来由于制造人造板的原料结构和产品结构的变化,致使人造板生产工艺发生了一定变化,这些对低甲醛释放UF胶粘剂的开发和应用提出新的要求。
1.1胶合板生产胶合板是我国人造板工业中的主导产品(也是传统产品),其产量占全国人造板总产量的50%左右。
近十年来,胶合板工业发生了巨大变化:一是企业数量猛增;二是国有企业比重明显下降(仅有数十家),三资企业、集体企业、民营企业数量猛增;三是胶合板生产原料以进口原木或单板为主;四是生产产地主要集中在广东、福建、江苏、山东、河北、天津、上海等市场经济发达的地区。
引进生产线的设备均具有八十年代的技术水平。
私营胶合板生产企业崛起,部分企业的年产量已达10~25万m3。
生产技术进展与生产工艺变化:(1)木材原料,表背板以进口原木为主,芯板以速生杨木为主;(2)速生杨木芯板的应用导致胶合板预压和涂胶工艺变革,形成“两次涂胶、两次预压”的新工艺,原因是速生杨木含水率不均,吸水后膨胀率大,边芯材pH相差大,天然干燥单板含水率偏高,且不均;(3)表板改薄,芯板加厚,致使热压时间缩短,三合板热压时间100s左右(100~105℃);(4)手工拼板,提高了木材利用率;(5)环保呼声提高,低甲醛释放胶合板的制造事在必行;(6)酚醛树脂胶水泥模板的生产在增加。
《纤维板单位产品综合能耗限额及计算方法》地方标准的研究

《纤维板单位产品综合能耗限额及计算方法》地方标准的研究黄丽;黄军;吴跃锋;龙维【摘要】通过对目前湖南省纤维板实际生产情况的统计与研究,本地方标准切实、合理地规定了湖南省纤维板单位产品综合能耗限额准八值和计算方法.本标准的制定,对加快推进“两型”社会标准化体系建设、促进纤维板生产企业节能降耗具有重要意义.【期刊名称】《湖南林业科技》【年(卷),期】2013(040)001【总页数】4页(P73-75,78)【关键词】地方标准;纤维板;综合能耗;限额;计算方法【作者】黄丽;黄军;吴跃锋;龙维【作者单位】湖南省林产品质量检验检测中心,湖南长沙410004;湖南省林产品质量检验检测中心,湖南长沙410004;湖南省林产品质量检验检测中心,湖南长沙410004;湖南省林业调查规划设计院,湖南长沙410007【正文语种】中文【中图分类】TS653.6目前,我国人造板产业结构、消费结构均处于高能耗阶段,节能技术水平较低、能源管理漏洞较多,能耗大,能源效率明显偏低。
纤维板是人造板行业中最重要的组成部分之一,湖南省纤维板产品以中密度纤维板为主,年产能可达100万m3。
由于缺乏相应的能耗限额的地方标准,难以统计企业能耗、衡量能效,不利于推广节能技术与遏制行业内高能耗、低水平的重复建设。
因此,为了加快推进“两型”社会建设,尽快发挥单位产品能耗限额标准在逐步淘汰落后产能、提高节能技术和管理水平、改善产业环境中的重要作用,制定纤维板生产企业单位产品能耗限额及计算方法的地方标准迫在眉睫。
标准是国民经济和社会发展的重要技术基础,是产业发展和市场竞争的核心要素。
《纤维板单位产品综合能耗限额及计算方法》地方标准的制定,能有效调控湖南省纤维板生产企业的耗能情况,有利于改善纤维板生产行业高能耗、低能效的现状,淘汰落后产能,提高节能技术水平;是规范行业现有产能运行及新产能建设,实现节能减排政策的迫切要求。
《纤维板单位产品综合能耗限额及计算方法》编写是以提高纤维板行业生产能效、降低能耗为目的,以相关国家法律法规、国家标准、行业标准为依据,广泛征求意见,切实符合湖南省实际情况[1-3]。
课程设计--年产10万吨PET生产的工艺设计
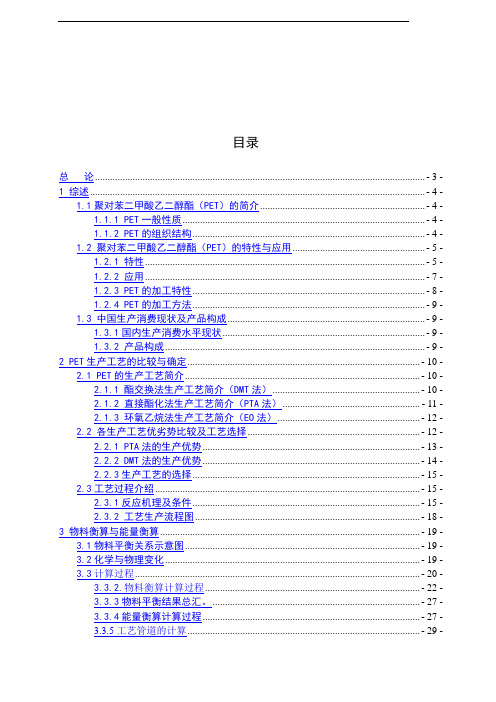
目录总论.................................................................................................................................... - 3 -1 综述...................................................................................................................................... - 4 -1.1聚对苯二甲酸乙二醇酯(PET)的简介.................................................................. - 4 -1.1.1 PET一般性质................................................................................................. - 4 -1.1.2 PET的组织结构............................................................................................. - 4 -1.2 聚对苯二甲酸乙二醇酯(PET)的特性与应用..................................................... - 5 -1.2.1 特性................................................................................................................ - 5 -1.2.2 应用................................................................................................................ - 7 -1.2.3 PET的加工特性............................................................................................. - 8 -1.2.4 PET的加工方法............................................................................................. - 9 -1.3 中国生产消费现状及产品构成............................................................................... - 9 -1.3.1国内生产消费水平现状................................................................................. - 9 -1.3.2 产品构成........................................................................................................ - 9 -2 PET生产工艺的比较与确定............................................................................................. - 10 -2.1 PET的生产工艺简介.............................................................................................. - 10 -2.1.1 酯交换法生产工艺简介(DMT法)........................................................... - 10 -2.1.2 直接酯化法生产工艺简介(PTA法)....................................................... - 11 -2.1.3 环氧乙烷法生产工艺简介(EO法)......................................................... - 12 -2.2 各生产工艺优劣势比较及工艺选择..................................................................... - 12 -2.2.1 PTA法的生产优势....................................................................................... - 13 -2.2.2 DMT法的生产优势....................................................................................... - 14 -2.2.3生产工艺的选择........................................................................................... - 15 -2.3工艺过程介绍.......................................................................................................... - 15 -2.3.1反应机理及条件........................................................................................... - 15 -2.3.2 工艺生产流程图.......................................................................................... - 18 -3 物料衡算与能量衡算........................................................................................................ - 19 -3.1物料平衡关系示意图.............................................................................................. - 19 -3.2化学与物理变化...................................................................................................... - 19 -3.3计算过程.................................................................................................................. - 20 -3.3.2.物料衡算计算过程...................................................................................... - 22 -3.3.3物料平衡结果总汇。
人造板知识要点整理

人造板知识要点整理【题型】名词解释、是非判断、简答题、计算题、作图题、分析题、综合题【名词解释】1分)、相邻层木纹方向互相垂直组坯胶合而成的板材(1分)。
VDG)是指木质人造板在厚度方向上的密度变化,通常表层密度高,芯层密度低,密度高峰值离板材表面有一定距离g/m2);刨花板——固体树脂(即胶粘剂的固体质量)与绝干刨花的质量百分比;纤维板——固体树脂与绝干纤维的质量百分比:已施胶单板组坯后进入热压前需放置的一段时间。
有薄单板经酚醛树脂胶浸渍、干燥,按一定要求组坯后在高温高压下胶合而成的具有较高力学性能、绝缘性能和尺寸稳定性能的板材。
PF;UF,血胶;%)。
(单板层积材组坯一般需进行纵向接长。
接合方式有对接、斜接和指接等。
)重组材:在不打乱木材纤维排列方向、保留木材基本特性的前提下,将小径级树,枝丫材等低质材碾压成“木束”重新组合,制成一种强度高、规格大、具有天然木材纹理结构的新型木材【基本概念】单元(A)×胶粘剂(B1)×添加剂(B2)×产品形状(C)、对称原则2、层间纹理排列原则3、奇数层原则15%左右)湿法(100%以上)半干法(30%以上),鼓式刨片机(单鼓轮刨片机、长材鼓式刨片机)和环式刨片机(双鼓轮刨片机)。
2)、三点定中心法3)、在最小内封闭曲线上寻找最大内切圆国内普遍使用的是喷雾式拌胶机,国外普遍使用的是离心式拌胶机。
旋切时为了保证单板质量,一般要求旋切后角在旋切过程中应随着木段直径的减小而逐渐减小;用作刨花板的原料宜选择密度小强度大的树种;长细比=长度/厚度;滤水时间越长,平均分离程度越高;旋切单板名义厚度取决于卡轴与刀床传动比;普通刨花板和定向刨花板制造过程中工艺要求区别最大的两个工序是刨花制备和铺装;用多层压机、单层压机、连续平压机、连续辊压机压制相同密度的刨花板或纤维板,为了减小成品板的厚度偏差,一般情况下多层压机制造的板子砂削量最大。
旋切1.2mm厚的单甲大于乙,则乙刨花的比表面积大。
木质护墙板的施工工艺设计

木质护墙板的施工工艺木质护墙板的施工工艺(1)材料准备在安装前,需备齐施工材料,以便加快进度。
①木骨架料。
也叫墙筋,一般是用杉木或红、白松木制作,木骨架间距400—600mm,具体间距还须根据面板规格而定。
横向骨架与竖向相同,骨架断面尺寸约(20—45)mm×(40—50)mm,高度及横料长度按设计要求截断,并在大面刨平、刨光、保证厚度尺寸一致。
木料含水率不得大于10%。
②面料板。
多用3—5层的胶合板,若做清漆饰面,应尽量挑选同树种、同纹理、同颜色的胶合板。
③装饰线与压条。
用于墙裙上部装饰造型,压条线形式很多,从材质上分为硬杂木条、白木条、水曲柳木条、核桃木线、柚木线、桐木线等,长度在2—5m。
从用途上分为墙裙压条、墙裙面板装饰线、顶角线、吊顶装饰线、踢脚板、门窗套装饰线(在后面门窗装饰套重点介绍)等。
④冷底子油和油毡。
用于防潮层。
⑤钉子:钉木骨架和面板用。
(2)工具准备。
护墙板施工的主要工具有刨子、磨、榔头、手锯、扁铲、尺、粉线包、裁口刨等。
(3)作业条件。
在施工前,需检查墙面基层质量,合格后可施工。
3.6.4护墙板的装饰施工工艺介绍①抹灰墙面已干燥,含水率在8%—10%以下,墙面应平整。
②干燥后涂刷冷底子油,并贴上油毡防潮层。
(4)施工法①弹线、检查预埋件。
根据施工图上的尺寸,先在墙上画出水平标高,弹出分挡线。
根据线挡在墙上加木橛或预先砌入木砖。
木砖(或木橛)位置应符合龙骨分档尺寸。
木砖的间距,横竖一般不大于400mm,如木砖位置不适用可补设。
②安装木龙骨。
全高型护墙板应根据房间四角和上下龙骨先找平、找直、按面板分块大小由上到下做好木标筋,然后在空当根据设计要求钉横、竖龙骨,先装直龙骨,再装横龙骨。
局部型护墙板根据高度和房间大小,做成龙骨架,整片或分片安装,在龙骨与墙之间铺一层油毡以防潮气。
龙骨间距:一般横龙骨间距400mm,竖龙骨间距可放大到450mm。
龙骨必须与每块木砖钉牢,如果没埋木砖,也可用钢钉直接把木龙骨钉入水泥砂浆面层上。
人造板多层热压机设计的毕业论文
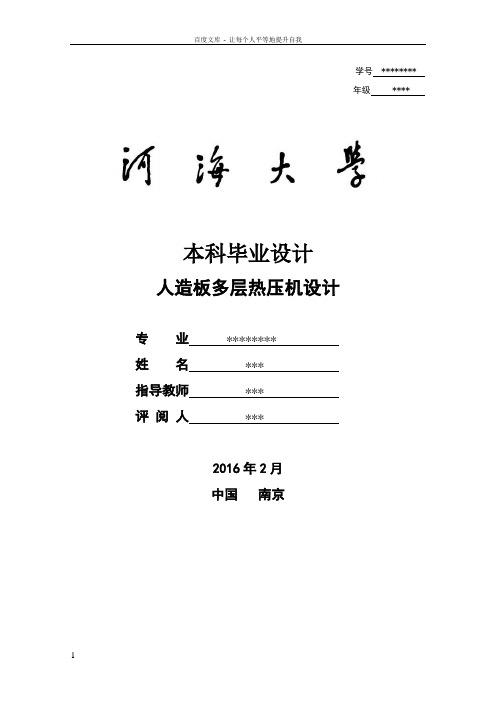
百度文库- 让每个人平等地提升自我学号 ********年级 ****本科毕业设计人造板多层热压机设计专业 ********姓名 ***指导教师 ***评阅人 ***2016年2月中国南京1学术声明:郑重声明本人呈交的毕业设计,是在导师的指导下,独立进行研究工作所取得的成果,所有数据、图片资料真实可靠。
尽我所知,除文中已经注明引用的内容外,本设计(论文)的研究成果不包含他人享有著作权的内容。
对本设计(论文)所涉及的研究工作做出贡献的其他个人和集体,均已在文中以明确的方式标明。
本设计(论文)的知识产权归属于培养单位。
本人签名: *** 日期:I摘要多层热压机是生产胶合板、刨花板、中密度纤维板等人造板的主要设备。
目前设备制造厂生产的热压机已基本定型,为了改进热压机的结构性能和降低制造成本,本文主要对五层侧压式热压机结构进行了设计,并对热压机的重要部件下托板的结构、强度和刚度进行了设计分析和计算,使下托板在结构上更加合理,降低了材料和能源消耗,提高了生产率。
设计主要结合现有的设计理念,在符合设计要求的前提下,设计时热压机的机架整体上主要采用了钢板焊接闭式结构,这种结构制造方便无需大型加工设备,并且,选材主要使用了工字钢、角钢等常用材料,使用钢板焊接的加工工艺,因而,生产工艺性较好,一般机械厂均能制造。
设计中主要使用了CAD、Pro\E等工程制图软件,使用了Pro\E软件进行受力分析。
关键词:侧压式,热压机,结构设计,受力分析IIAbstractThe multi-layered hot press is the production plywood, the shaving board, building board and so on density fiberboard major installations. At present the equipment factory production's hot press has finalized basically, to improve hot press's structure performance and reduce the production cost, this article mainly has carried on the design to five side thrust type hot press structure, and to hot press's important part under carrier's structure, the intensity and the rigidity has carried on the project analysis and calculates, causes the carrier to be more reasonable in the structure, reduced the material and the energy consumption, raised the productivity. The design main union existing design idea, in conforms to under the design requirements premise, in the design in press's rack whole has mainly used the steel plate welding closed type rack, this kind of structure manufacture convenience does not need the large-scale processing equipment, and, the selection has mainly used the I-steel, the angle steel and so on commonly used material, uses processing craft which the steel plate welds, thus, the production technology capability is good, generally the machine shop can make. In the design has mainly used CAD, engineering drawing soft wares Pro \ E and so on, used the software Pro \ E to carry on the stress analysis.Key words: lateral pressure type, thermal-pressing machine, structural design, stress analysisIII目录ABSTRACT (III)1.引言 (6)五层侧压式热压机的发展概况及现状 (6)热压机的特点 (7)热压机的发展带来的机遇和挑战 (8)2.热压机的结构设计 (9)框架结构 (10)柱塞结构 (11)上托板结构 (11)下托板结构 (12)平衡机构简要设计 (13)工作原理 (13)齿轮材质 (15)精度等级 (15)模数 (15)压力角 (15)齿槽宽 (15)40CR(调质) (15)IT7 (15)20° (15)MM (15)齿顶高 (15)齿根高 (15)齿高 (15)齿厚 (15)齿根圆半径 (15)MM (15)MM (15)MM (15)MM (15)MM (15)齿条的设计 (15)材质 (16)精度等级 (16)IV模数 (16)齿形角 (16)齿槽宽 (16)45钢(调质) (16)IT7 (16)20° (16)MM (16)齿顶高 (16)齿根高 (16)齿高 (16)齿厚 (16)齿根圆半径 (16)MM (16)MM (16)MM (16)MM (16)MM (16)轴承的选取 (16)侧压缸支架结构 (19)具体尺寸参阅零件图:BYSJ-06。
五大工艺流程
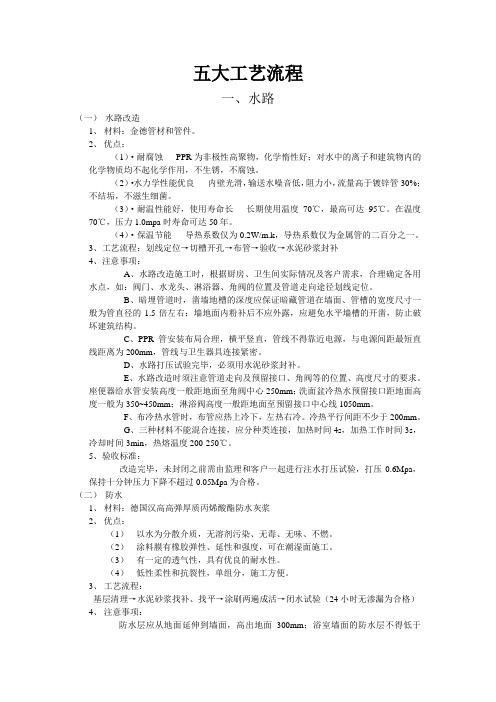
五大工艺流程一、水路(一)水路改造1、材料:金德管材和管件。
2、优点:(1)·耐腐蚀PPR为非极性高聚物,化学惰性好;对水中的离子和建筑物内的化学物质均不起化学作用,不生锈,不腐蚀。
(2)·水力学性能优良内壁光滑,输送水噪音低,阻力小,流量高于镀锌管30%;不结垢,不滋生细菌。
(3)·耐温性能好,使用寿命长长期使用温度70℃,最高可达95℃。
在温度70℃,压力1.0mpa时寿命可达50年。
(4)·保温节能导热系数仅为0.2W/m.k,导热系数仅为金属管的二百分之一。
3、工艺流程:划线定位→切槽开孔→布管→验收→水泥砂浆封补4、注意事项:A、水路改造施工时,根据厨房、卫生间实际情况及客户需求,合理确定各用水点,如:阀门、水龙头、淋浴器、角阀的位置及管道走向途径划线定位。
B、暗埋管道时,凿墙地槽的深度应保证暗藏管道在墙面、管槽的宽度尺寸一般为管直径的1.5倍左右;墙地面内粉补后不应外露,应避免水平墙槽的开凿,防止破坏建筑结构。
C、PPR管安装布局合理,横平竖直,管线不得靠近电源,与电源间距最短直线距离为200mm,管线与卫生器具连接紧密。
D、水路打压试验完毕,必须用水泥砂浆封补。
E、水路改造时须注意管道走向及预留接口、角阀等的位置、高度尺寸的要求。
座便器给水管安装高度一般距地面至角阀中心250mm;洗面盆冷热水预留接口距地面高度一般为350~450mm;淋浴阀高度一般距地面至预留接口中心线1050mm。
F、布冷热水管时,布管应热上冷下,左热右冷。
冷热平行间距不少于200mm。
G、三种材料不能混合连接,应分种类连接,加热时间4s,加热工作时间3s,冷却时间3min,热熔温度200-250℃。
5、验收标准:改造完毕,未封闭之前需由监理和客户一起进行注水打压试验,打压0.6Mpa,保持十分钟压力下降不超过0.05Mpa为合格。
(二)防水1、材料:德国汉高高弹厚质丙烯酸酯防水灰浆2、优点:(1)以水为分散介质,无溶剂污染、无毒、无味、不燃。
中密度纤维板生产线工艺流程

8%%。原木装于通过皮带运输机送载机将小径木、枝桠材等木材原料放在储木台上,入削片机,削片机前装有金属探测器,避免带有金属的木材进入削片机。进入削片机经由螺旋运输机和斗式提升机送人木片储仓的木材被削成规格木片,储存。分别储存软材和硬所以采用两个储仓,由于软材硬材要按比例混合,材木片。由出料装置控根据工艺配比,储仓下部的出料装置能控制出料速度,制出料:或4量,使软硬木片按要求的比例均匀混合。软硬木片之比为3:7
加热压机导热油加热系统的结构与特点热压是汽车内饰生产过程中的一道重要工序,而在板坯热压过程中,加热又是一个重要的工艺条件。目前,对板坯加热的常用方法是利用热压板进行接触加热,即高温热载体流过热压板内部的蛇形通道,对钢制热压板进行加热,热压板升温后再对与之紧密接触的板坯加热,使板坯温度升高。过去,我国汽车内饰企业大多采用蒸汽作为热载体,蒸汽作为热载体具有物理化学性质稳定、来源广泛、价格低廉、无毒无味无污染等特点,但蒸汽用于热压工序时也有几个不易克服的缺点:一是热压工序通常需要较高的温度,一般在160——220℃之间,与此相对应的蒸汽压力为1.6——2.5MPa,因此,需要整个供热系统(包括锅炉、管5 / 21
热压板温度降接触,否则会加速导热油氧化而缩短其使用寿命。
根据规定,导热油用℃以下时热油循环泵才能停止工作。低到80倍的工作压力来制造或选型,所用电机要求防管路及阀门要按1.6所选用的导热油的导热系数要大,比热要高,其闪点和自燃爆。导热油在高温运行时,其化学键容易断裂而氧化裂解生点要高。
导成碳,所以必须在导热油牌号规定的额定工作温度以下使用。
道及其附件与接头等)具有较高的耐压强度,这就使供热系统结构复杂,投资增大,运行管理不便;二是为了保证热压质量,要求热压板面温度尽可能均匀一致,一般要求同一块压板板面上的温差小于3°C,各层热压板之间的温差小于5°C,这就要求载热体在进出热压板时的温度差要尽可能小。采用蒸汽加热时,往往会由于凝结水排故不及时,使热压质量降低;三是蒸汽在热压机中放热后排出的凝结水具有较高的温度(一般在160℃以上),其回收难度较大,若处理不当,则可能造成严重的能源浪费。由于蒸汽加热具有这些不易克服的缺点,所以,近年来越来越多的汽车内饰生产热压机都采用了高温热油供热系统。热油供热的特点热油又称为导热油,属于一种高温有机热载体,热压机采用热油供热时具有以下主要优点:(1)高温低压。热油供热系统采用的是液相封闭循环,导热油在常压下温度可以升高到300以上而不发生气化,例如,HD系列导热油在常压(0. 098MPa)下即可获得330℃的高温,如考虑系统的压力损失及一定的安全系数,热油系统中的最高压力(热油循环泵的出口压力)一般也仅在0.6MPa左右,比具有同样供热温度的蒸汽供热系统的压力低得多。由于具有高温低压的特点,加之热油系统不需要复杂的水处理设施,因此,相对于蒸汽供热系统而言,热油系统结构比较简单,运行、管理也比较方便。这是热油系统的最大的优点。(2)温度均匀。在设计热油系统时,通常在热压机处设置“二次循环”,一方面,可以通过改变二次循环油量调节热油进人热压板时的温度,另一方面,二次循环油量的加人,使通过热压板的油量成倍增加。(3)6 / 21
一、项目名称人造板连续平压生产线节能高效关键技术
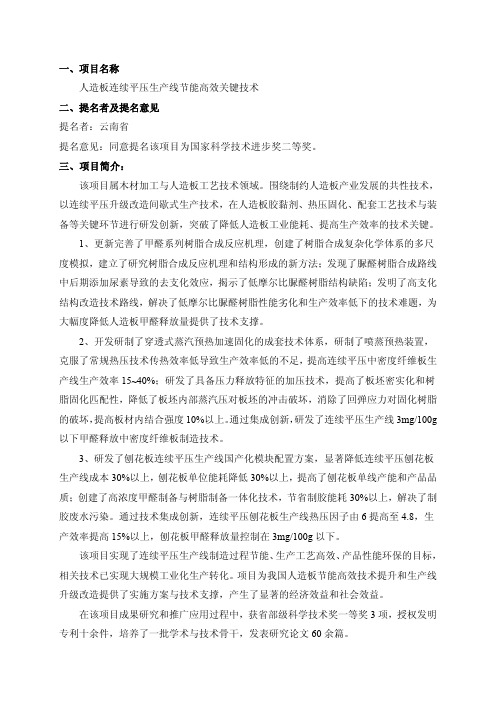
周晓剑,杜官 本,王辉,吴 章康,李君
有权
西南林业 杜官本,邓书
大学
端,李向红
有权
西南林学 杜官本,雷洪
院
有权
西南林业 大学
雷洪,杜官 本,王辉,席
雪冬
有权
东营正和 木业有限
公司
刘保卫,李 杰,刘冬,李
林
有权
东营正和 木业有限
公司
刘保卫,李 杰,刘冬,李
林
有权
东营正和 木业有限
公司
刘保卫,李 杰,刘冬,李
4、国内外重要科技奖励 (1)“甲醛系列树脂人造板胶黏剂合成与应用”获 2018 年高等学校科学研究优秀成 果奖(申报中); (2)“苯酚-尿素-甲醛共缩聚树脂结构形成及控制机理”获 2009 年云南省自然科学 奖一等奖; (3)“节能环保型连续平压刨花板制造成套技术及工业化”获第九届梁希林业科学 技术奖一等奖; (4)“人造板节能高效生产工艺及配套装备关键技术”获 2018 年云南省科技进步奖 一等奖。
在承担国家科技支撑计划课题研究任务“甲醛系树脂低温加速固化技术”过程中,项 目组提出了穿透式蒸汽预热加速固化技术方案,上海人造板机器厂有限公司设计研发了 成套装置,并于 2014 年 12 月在山东茌平县能通密度板有限责任公司实现工业化安装运 行。由于提高产能效果显著,该技术迅速推广至上海人造板机器厂有限公司销售的 20 余条连续平压中密度纤维板生产线。
林
有权
七、主要完成人情况
姓名 杜官本
雷洪 李涛洪 杨志强
刘翔
排名 1
2 3 4 5
行政职务 副校长
副院长 无 无 无
技术职称 教授
教授
副教授 高级工程
师 高级工程
板式家具的产品结构与加工工艺

板式家具的产品结构与加工工艺板式家具,指以人造板为基材,为板件为主体,采用专用的五金连接件或圆木榫连接装配,以表面贴纸或者木皮,经封边、喷漆修饰而制成的家具。
同实木家具相比其主要有两点特征:一是不易变形,可拆卸安装,方便运输和仓储。
二是节约木材资源,提高木材利用率。
板式家具可分为:木皮板式家具、贴纸板式家具、实色板式家具、三聚氰胺类板式家具以及由以上类别的一种两种或多种组成的混合类别板式家具。
一、板式家具的结构1.产品部件自身的结构板式家具部件一般是以人造板为基材,表面进行覆面装饰的构件。
板式家具的主要基材有:中密度纤维板(简称中纤板)、刨花板、胶合板、细木工板、三聚氨胺板等。
目前公司板式产品主要以中纤板为基材,其部件按表面装饰材料可分为以下几种:1)中纤板贴木纹纸或木皮后做透明漆2)中纤板做实色漆,如银珠,白色,蓝色3)中纤板贴热压纸后封PVC边4)中纤板贴三聚氰胺浸渍纸后封PVC边中纤板厚度规格主要有:3,5,9,12,15,18,25mm七种厚度,当板件的设计厚度超过25mm时就需要加厚来实现。
板式家具部件的形式一般可分以下几种:1)实心板:当板件宽度较小时可考虑用实心板,如一些脚、柱类的板件。
2)空心板:当板件宽度较大且两面均为可视面时可考虑空心板内填蜂窝纸,如一些边板、层板类的板件。
3)边部加厚板:当板件宽度较大而只有一面为可视面时可考虑用边部加厚板。
如一些面板、底板类的板件。
4)弯板:当产品部件设计为曲面时就需要压弯板实现。
由多层3mm或5mm 厚的板材加胶在特制的冷压模具中压制而成。
也可只用正反两块3mm或5mm厚的板材,中间夹小木条加胶在模具中压制。
无论用哪种方法压成后其部件的厚度要满足部件的设计厚度。
2.产品部件之间的连接板式家具摒弃了框式家具中复杂的榫卯连接结构,而采用圆孔接合方式。
圆孔的加工主要是由钻头间距为32mm的排钻加工完成的,也就是板式家具结构设计计遵循的“32mm系统”。
《人造板工艺学》教案全套
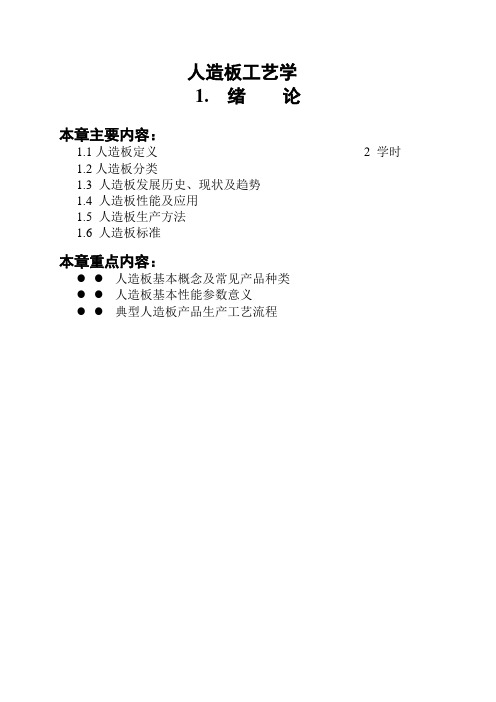
人造板工艺学1. 绪论本章主要内容:1.1人造板定义 2 学时1.2人造板分类1.3 人造板发展历史、现状及趋势1.4 人造板性能及应用1.5 人造板生产方法1.6 人造板标准本章重点内容:●●人造板基本概念及常见产品种类●●人造板基本性能参数意义●●典型人造板产品生产工艺流程1.1 人造板定义人造板是指以木材或其他植物纤维材料为原料,经机械加工分离成各种形状的组元后,再经组合压制成的板材。
人造板=单元(A)×胶粘剂(B1)×添加剂(B2)×产品形状(C)单元(A):单板、竹片、板材、木条、大片刨花、刨花、纤维等。
Lumber, BlockVeneer, StripChip, Flake (Strand), ParticleFiber, Wood woolWood Flour, Wood DustNano-Stuctural Fiber胶粘剂(B1):合成树脂胶——脲醛树脂、酚醇树脂、三聚氰胶树脂、异氨酸脂树脂等。
无机胶粘剂——水泥、石膏、粉煤灰、矿渣等。
添加剂(B2):阻燃剂、防虫剂、防水剂、防腐剂等;产品形状(C):平面状、异状(曲面、弯曲)、表面模压等。
例如:单板×脲醛树脂×平面状=脲醛树脂胶合板单板、木条×脲醛树脂胶×平面状=细木工板刨花×豚醛树脂胶/防水剂=普通刨花板1.2 人造板分类1.2.1 按组成木质(非木质)单元分类(1).以单板、板、片为主的产品(Veneer-based Panel)●●Plywood⎪⎩⎪⎨⎧Thick)layers5or3(Thin:LayersPFUF:sinReBambooWood:MaterialsRaw●●结构胶合板Structural Plywood()()()⎪⎪⎩⎪⎪⎨⎧PlywooddimpregnateIsinReLumberStrandParallelPSLLumberatedminLaGlueGLULAMLumberVeneeratedminLaLVL●●功能胶合板Functional Plywood⎪⎪⎩⎪⎪⎨⎧PlywoodyElectricitstaticAntiPlywoodFireproofFormConcrete●●细木工板Blockboard⎩⎨⎧BlockboardCoreSolidBlockboardCoreHollow(2).以刨花为主的产品(Particle-based Panel)●●Raw MaterialWood, Bamboo, Agricultural Residues●●Adhesive有机合成树脂Synthetic Adhesive——UF, PF无机胶粘剂Inorganic Adhesive——Cement, Gypsum●●Structure➢➢单层结构刨花板:Single-layer particleboard——the density and the size of particle of each layer are uniform in thickness direction.➢➢多层结构刨花板:Multi-layer particleboard——the density and the size of particle of each layer are uneven in thickness direction. Usually smaller particles are formed on the surface while larger particles in the core. Moreover, the interface is obvious. The purpose is to develop adequate strength plus good surface smoothness.➢➢渐变结构刨花板Graduated particleboard——the density and the size of particle of each layer change gradually from the surface to the core. The interface can’t be distinguished.➢➢定向结构板Oriented Strandboard (OSB) ——OSB is mat of three or five alternate layers of strands oriented at 90 degrees utilizing the same principle as plywood.●●DensityLow-density particleboard—ρ<0.5g/cm3Medium-density particleboard—0.5<ρ<0.65g/cm3High-density particleboard—0.65<ρ<0.85g/cm3●●Processing➢➢平压法:Platen-pressed particleboard—the direction of pressure is vertical to the panel surface➢➢挤压法:Extruded particleboard-- the direction of pressure is horizontal to the panel surface, by which the molded products are produced.(3).以纤维为主的产品(Fiber-based Panel)●●Raw MaterialWood, Bamboo, Agricultural Residues●●AdhesiveSynthetic Adhesive——UFInorganic Adhesive——Cement, Gypsum●●DensitySoftboard——ρ<0.4g/cm3Medium-density Fiberbord(MDF)——0.5<ρ<0.8g/cm3Hardboard——ρ>0.8g/cm3●●ProcessingDry Forming——Air as a mediumWet Forming——Water as a mdium1.2.2 按生产过程类型分类根据产品成型时板坯的含水率大小,分成干法、湿法和半干法。
浅谈家具中木材弯曲成型技术的发展

浅谈家具中木材弯曲成型技术的发展北京市木材工业研究所 刘绪林一、引言近年来,“弯曲木”家具已成为我国家具市场中流行的新风尚,生产“弯曲木”家具厂在全国蜂涌而上,由几年前的一、二家发展到现在的一百多家。
“弯曲木”家具能发展成现在的形势,得益于近几年木材弯曲成型技术的发展。
所谓“弯曲木”家具,泛指家具的整体或部件是用弯曲木制成的。
弯曲木的制造技术决定着曲木家具的发展,弯曲木的制造大致分成四类:一是实木弯曲成型;二是多层胶合弯曲成型;三是刨花(纤维)模压弯曲成型;四是中密度纤维板弯曲成型。
这也是当今家具生产中四大木材弯曲成型技术。
其中,实木弯曲是最早应有用于家具制造业中的木材弯曲成型技术,早在160年前,德国木匠Michael.Thonet就制造了第一张实木弯曲成型的椅子。
从那时起,这种工艺在家具制造业中就得到了广泛的应用,第二次世界大战时,这种弯曲木还应用于飞机制造业和高要求的建筑构件上。
本世纪20~30年代,芬兰人阿尔托又首先发明了多层胶合弯曲木,极大地推动了木材弯曲成型技术的发展。
刨花(纤维)模压成型在我国起源于80年代,中密度纤维板弯曲成型技术则是近几年刚刚兴起的一项全新概念的木材弯曲成型技术。
木材弯曲成型技术应用于家具制造,便形成“弯曲木”家具,“弯曲木”家具以其淡雅简洁款式、优美的曲线造型、精细的制作工艺和优质材料等特点闻名于世,以她独具的魅力,成为一种世界性的家具时尚。
进入90年代,弯曲木家具在中国市场上日渐走俏,掀起一股曲木热潮,只有对木材弯曲成型技术及工艺有深入的了解,才能把握和恰当地利用这一新技术,运用到弯曲木家具中,为家具设计开辟一个广阔的设计天地。
二、实木弯曲成型技术实木弯曲的技艺是1830年德国人Michael.Thonet发明的,至今已有160多年的历史。
在已知木材可弯曲成很小曲率半径的技术之前,圆桶及船体已能使用实木弯曲成型了。
采用Thonet工艺,木材可以弯曲成圆形,内曲率半径很小,达到木材厚度的3倍,在某些情况下,还可以更小些,这种弯曲技术最早的产品是椅子。
2.9导热油中密度纤维板多层热压机的基本参数及加热方式
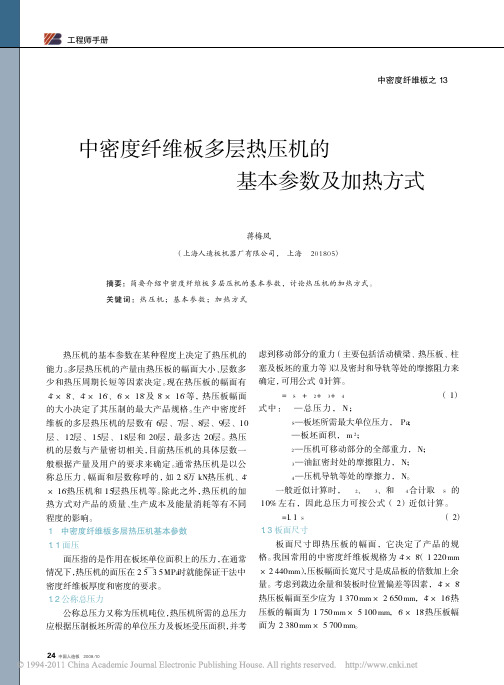
24 中国人造板 2008/10热压机的基本参数在某种程度上决定了热压机的能力。
多层热压机的产量由热压板的幅面大小、层数多少和热压周期长短等因素决定。
现在热压板的幅面有4'×8'、4'×16'、6'×18'及8'×16'等,热压板幅面的大小决定了其压制的最大产品规格。
生产中密度纤维板的多层热压机的层数有6层、7层、8层、9层、10层、12层、15层、18层和20层,最多达20层。
热压机的层数与产量密切相关,目前热压机的具体层数一般根据产量及用户的要求来确定。
通常热压机是以公称总压力、幅面和层数称呼的,如2.8万kN热压机、4'×16'热压机和15层热压机等。
除此之外,热压机的加热方式对产品的质量、生产成本及能量消耗等有不同程度的影响。
1 中密度纤维板多层热压机基本参数1.1 面压面压指的是作用在板坯单位面积上的压力,在通常情况下,热压机的面压在2.5 ̄3.5 MPa时就能保证干法中密度纤维板厚度和密度的要求。
1.2 公称总压力公称总压力又称为压机吨位,热压机所需的总压力应根据压制板坯所需的单位压力及板坯受压面积,并考虑到移动部分的重力(主要包括活动横梁、热压板、柱塞及板坯的重力等)以及密封和导轨等处的摩擦阻力来确定,可用公式(1)计算。
F=P SS +F 2+F 3+F 4 (1)式中:F—总压力,N; P S—板坯所需最大单位压力, Pa; S—板坯面积,m2;F 2—压机可移动部分的全部重力,N;F 3—油缸密封处的摩擦阻力,N;F 4—压机导轨等处的摩擦力,N。
一般近似计算时,F 2、F 3、和F 4合计取PSS的10%左右,因此总压力可按公式(2)近似计算。
F=1.1PSS (2)1.3 板面尺寸板面尺寸即热压板的幅面,它决定了产品的规格。
我国常用的中密度纤维板规格为4'×8'(1 220 mm×2 440 mm),压板幅面长宽尺寸是成品板的倍数加上余量。
- 1、下载文档前请自行甄别文档内容的完整性,平台不提供额外的编辑、内容补充、找答案等附加服务。
- 2、"仅部分预览"的文档,不可在线预览部分如存在完整性等问题,可反馈申请退款(可完整预览的文档不适用该条件!)。
- 3、如文档侵犯您的权益,请联系客服反馈,我们会尽快为您处理(人工客服工作时间:9:00-18:30)。
中密度纤维板生产、基本工艺设计中密度纤维板生产工艺包括生产部分和辅助部分(以木材原料为主)。
生产部分包括原料堆场和备料、热磨施胶干燥、铺装预压热压、后处理、中间储存及砂光工段。
辅助部分有实验室、磨刀间和维修间等。
中密度纤维板生产基本工艺设计. 原料堆场原料堆场是生产工艺的组成部分。
原料在储存过程中,受自然条件的影喻而减少水分和均衡含水率,能减少树脂含量及果胶、淀粉、蛋白等成分,有利于原料质量的稳定,使原料更适于解纤。
而不恰当的原料储存方式和管理方法,不但会造成原料的腐朽变质和浪费,甚至会有火灾的隐患。
在设计中必须根据工厂的生产规模、工艺流程、原料种类、储存季节、场地利用和防火规范要求等来综合考虑原料堆场的储存方式和面积、工艺布局。
原木进场后应按树种和径级以及进场时间的先后顺序分类归堆。
考虑到原料供应的季节性作业和由于市场变化、运输等不可预测的因素,会使原料供应不及时而影响正常生产,为满足企业的正常连续生产必须要有一定的储备量。
对于木材原料来说,原木储存量不能少于1个月的正常生产的需要量。
以3~4个月的生产需要量为最佳。
采用铲车堆垛作业工艺,。
堆积高度按3~5m计算;外购到厂的木片可用简易棚或露天堆场堆放,露天堆场的木片堆积高度可达20~30m。
为避免原料堆垛自燃导致火灾和腐烂变质,堆垛之间要求留有足够的垛间距及通风道。
堆垛间距一般在1~2m,至少不小于0.5m;垛组间距一般在10~15m,垛区间距一般为15~25m。
原料场最好设置在生产区的下风向,堆垛长度方向应与常年主导风向成一个角度,以利通风。
非木材植物纤维原料则在很大程度上受季节影响,必须根据原料收购季节和运输条件等来考虑原料储存期、储存面积及储存方式。
这些原料一般用打捆方式运进料场储存,储存期一般在6个月以上,棉杆、庶渣类的储存量在6~9个月,芦苇、秸秆为7~10个月,竹材一般为2~3个月。
可采取分场地储存,但生产区内至少要储存1~3个月的生产用量。
储存期间的含水率一般控10%~15%为宜。
原禾木堆场应就近备料工段周围布置,并考虑消防通道和消防用水。
原木堆场面积按式(2-1)汁算。
nQS=------------------12Hκ1κ2式中S一原木堆场面积, m2;Q一年需原木数量, m3;n一计划储存月数;H—堆垛高度,取3.0~5.0m;κ1—场地利用系数,取0.6~0.7;κ2—实积系数,取0.35~0.7。
中密度纤维板生产基本工艺设计. (二) 备料备料是中密度纤维板生产的第一道工序,目的是把木材或其他非木材植物纤维原料,按照纤维分离工艺和设备的要求,切成一定规格的碎片并加以净化。
备料包括剥皮、削片、筛选、木片储存和清洗工序。
1.备料工艺流程简述(以木材原料为主)原木装载机将木材原料由厂里的原木堆场运送至备料工段的剥皮生产线上,带皮原木经链条进给运输机送入剥皮机,然后通过运输机送人削片机,在削片机前装有金属探测器,避免带金属的原木损坏刀盘。
进人削片机的木材被削成规格木片,经由运输机械送入木片储仓储存。
在软材、硬材严格按比例混合的情况兄下,采用两个储仓,分别储存软材和硬材木片。
根据工艺配比,由出料装置控制出料量,使软硬木片按要求的比例均匀混合。
中密度纤维板生产所用原料混有大量的树皮以及泥沙、石块甚至金属物,必须采取措予以清除。
因此,木片经运输机送至筛选机进行筛分,在除去过大的和过小的木片和杂物后,将合格木片送至清洗设备,除去泥沙、小碎石、污物及金属块等。
净化后的木片经运输机械送往热磨工段。
2.剥皮工序树皮占树木体积分数的6% ~20%,平均为10% ;占制材板皮的10%,占小径木和枝桠材的13% ~28%,平均为20%以上。
树皮中含有较多的抽提物,当纤维原料中的树皮含量大时,会导致板的强度下降、吸水率提高、板面色色泽不均,从而影响板的质量。
实验得出表2- 3所示的数据,当板子密度为700kg/m3、施胶量为8%时,随着树皮混合比例的增加,板子的强度呈下降趋势;同时也可看出,在混合率一定时,不同长度纤维的板子随着纤维质量的下降也呈下降趋势。
静曲强度/MPa10 24.3 20 15.520 22 18 15中密度纤维板工艺设计规范要求木材原料中树皮含量小于10%(体积分数,下同);木片中树皮含量小于8%。
引进设备的生产工艺,要求木材原料中树皮含量小于8%。
基于国内中密度纤维板生产原料枝桠材和小径木较多、原料的树皮含量大的现实状况,为保证板的质量,需采取控制树皮含量的措施。
控制树皮含量的有效方法之一就是增加剥皮工序。
剥皮工序分人工和机械两种,生产规模较小的生产线,当要求原木剥皮时也往往用人工剥皮。
规模较大的生产线以及引进外国设备生严线,都配套装备有剥皮机。
特别是大型规模的连续平压生产线,要求在筛选前的木片树皮体积分数小于5%,因此必须对原木进行剥皮。
机械剥皮大致有两种采用方式:(1)原木在转筒中酬泼罪目身旦相摩擦使树皮剥落,剥皮能力取决于进给的喂料量和原木在筒中停留的时间。
这种方式适用于比较平直的原木和小径木。
(2)剥皮时主要靠转子转动接触原木,靠与焊在转子上的凸铁块摩擦将树皮剥下来。
这种方式适用于弯曲原木、小径木.(最小直径帕Φ60mm)和大径;对不同树种易于调整。
3.削片工序生产工艺要求在分离成纤维前先将原料切削成一定规格的木片或碎片(指非木材原料的切片).木片或碎片的质量是根据削片的大小、均匀程度而定,要求木片大小合格、均匀。
木片规以长度 15~30mm、宽度15~25mm、厚度3~5mm,含水率大于35%为宜; 禾本科秸秆类原料切成长度为30~50mm为宜。
为获得质量合格的木片,须用机械方法将原料进行切削。
常用的削片机有鼓式削片机和盘式削片机两类,如表2-4.原料适应性广,可切削原木、小径木、主要适用于较平直的原木、小径木原料枝桠材、板皮等加工剩余物及秆状类非木材植物原料可满足中密度纤维板生产要求,也能耗(同等能耗较大能耗较小产量下)4.筛选工序由于工艺要求木片的规惜尺寸妥均匀,为了获得合格均匀的木片,必须将木片中的超大木片分离再碎,将碎屑进行筛除。
常用的筛选机有摆动式平筛和振动式平筛两种。
摆动式平筛的筛体作平面摆动,木片从上方进料口进入,第一层筛出超大木片,第二层筛网将合格木片从该层出料口排出进八生严线,碎屑则通过筛网漏到底部排出。
振动式平筛的筛体作平面振动或垂直振动以达到木片分选的目的。
经筛选后的木片组成应符合表2-5的要求。
表2-5筛选后的木片组成要求表大型木片大于30 不大于8标准木片 16—30 不小于75 木片含水率控制在35%~50%.木片小型木片 6—15 不多于15 中不得混入金属物质5.木片的储存根据工艺设计规范,削片机采用1班生产,料仓必须具有大于16h生产用量的储存量;削片机采用2班生产,料仓必须具有大于8h生产用量的储存量。
生产实践证明,削片机采用.3班生产时,料仓具有大于3h生产用量的储存量才能够满足生产的要求。
料仓装料量的计算公式:G=ΦργV 式中G一装料量, kg;Φ一充满系数, 0.6~0.8:ργ—绝干密度, kg/m3;V一计算容积, m3。
料仓的形式按结构区分,可分为金属结构、混凝土结构、金属与混凝土混合结构;按形状区分,可分为长方形和圆柱形。
木片由料仓上部进入,从底部排出。
防止木片产生“搭桥”现象,在料仓内壁可嵌焊三角铁块,并在出料的倒锥体外壁上安装电动振动。
倒锥体的锥角为55°~60°。
6.木片的运输木片的输送设备主要有带式运输机、螺旋运输机、刮板运输机、埋刮板运输机、斗式提升机和气力输送系统。
带式运输机在运输木材碎料时的速度一般取0.6~1.6m/s。
普通带式运输机倾角一般不大于18°,若超过18°,则须采用特殊皮带如人字皮带,以防木片下滑,这样处理运输机的倾角可以达到26°一28°。
也有倾角达到45°一55°的大倾角皮蒂运输机,但设备投资较高。
螺旋运输机的倾角可以达到30°,且密闭性好,能均匀下料,适用于在不太长的距离内运输散碎物料。
刮板还输机的倾角可以达到45°。
刮板运输机的生产率较低,特别是倾斜运输时,随着倾角的增大,生产率急剧下降。
而埋刮板运输机能弯曲、倾斜和直立提升,不会扬起灰尘,但生产率较低。
斗式提升机用于提升散状物料,工作速度范围为0.8~2.5m/s,运行平稳无噪声,检修方便。
气力输送系统是最为简便的输送木片的设备,一般采用的空气与木片的混合质量比为0.3~0.5,输送风速为22~30m/s。
由于风送过程中木片不断与管壁发生剧烈碰撞,使木片形态变外,影响纤维质量,且原料损耗加大;再加上气力输送系统能耗大,运行成本高,因此绝大部分新建厂,尤其是上规模的厂几乎不采用这种输送方式。
但对灌木类原料如沙柳,其切削木片较细碎,堆积密度低,含水率较低,。
则较适宜用气力系统输送。
一般生产中最常用的是带式运输机、螺旋运输机与斗式提升机相结合的输送方式。
7.木片的清洗中密度纤维板生产所用木片,特别是外购木片混有大量泥沙、石块甚至金属物、泥沙等杂物占质量分数的1%~3%,有的高达5%。
中密度纤维板国家标准规定板的含沙量不得大于0.05% ;而根据IS0 3340标准,要求在热磨机进料口的木片含沙量不得大于0.04%,因此木片清洗是一个重要的环节。
木片通过筛选已去掉了泥沙等杂物的大部分,对于质量要求一般,主要生产中厚板的生产工艺要求是可以满足的,但对于质量要求高,主要生产薄板的生产工艺要求是不够的,必须对筛选后的木片做进一步的清洗。
木片清洗可分为水洗和干洗两种方式。
水洗方法能有效地清除各种杂物,木片质量好,能提高磨浆纤维质量/在清洗的同时进一步加湿木片。
水洗后木片含水率一般在50%以上,有利于纤维分离和板的质量。
根据我国原料的现状,采用水洗比较合适。
但木片水洗耗水量大,又有污水处理问题,且造价较高。
因此,目前除了引进生产线配套有水洗设备,国产生产线甚少采用。
水洗设备较为复杂。
常见的有螺旋脱水式和振动筛脱水式两种。
两种设备的原理和结构类似,只是一种采用螺旋机脱水,另一种采用振动筛脱水。
设备的组成部分大致有搅拌洗涤、重物分离定量排出、滤水排污、沉淀和浮选净化、水循环系统等。
干洗又称风洗,利用风量、风压的调整和机械振动力,将不同重量的杂物与木片分开。
一般原料单一或已除掉树皮的削片,采用此法清洗效果明显。
干洗没有污水产生,但系统的噪声较大,相对水洗其造价较低,但干洗的木片质量不如水洗。
国外干法中密度纤维板生产线多采用此法,我国早期引进生产线也有采用干洗方式,主要在广东一带。
干洗设备常用的有干洗机,又称风洗机。
木片由进料口落人振动器中,通过振动使木片与泥沙等杂物分离。