热处理变形的原因及分类
热处理变形的原因

热处理变形的原因在实际生产中,热处理变形给后续工序,特别是机械加工增加了很多困难,影响了生产效率,因变形过大而导致报废,增加了成本。
变形是热处理比较难以解决的问题,要完全不变形是不可能的,一般是把变形量控制在一定范围内。
一、热处理变形产生的原因钢在热处理的加热、冷却过程中可能会产生变形,甚至开裂,其原因是由于淬火应力的存在。
淬火应力分为热应力和组织应力两种。
由于热应力和组织应力作用,使热处理后零件产生不同残留应力,可能引起变形。
当应力大于材料的屈服强度时变形就会产生,因此,淬火变形还与钢的屈服强度有关,材料塑性变形抗力越大,其变形程度越小。
1.热应力在加热和冷却时由于零件表里有温差存在造成热胀冷缩的不一致而产生热应力。
零件由高温冷却时表面散热快,温度低于心部,因此表面比心部有更大的体积收缩倾向,但受心部阻碍而使表面受拉应力,而心部则受压应力。
表里温差增大应力也增大。
2.组织应力组织应力是因为奥氏体与其转变产物的比容不同,零件的表面和心部或零件各部分之间的组织转变时间不同而产生的。
由于奥氏体比容最小,淬火冷却时必然发生体积增加。
淬火时表面先开始马氏体转变,体积增大,心部仍为奥氏体体积不变。
由于心部阻碍表面体积增大,表面产生压应力,心部产生拉应力。
二、减少和控制热处理变形的方法1.合理选材和提高硬度要求对于形状复杂,截面尺寸相差较大而又要求变形较小的零件,应选择淬透性较好的材料,以便使用较缓和的淬火冷却介质淬火。
对于薄板状精密零件,应选用双向轧制板材,使零件纤维方向对称。
对零件的硬度要求,在满足使用要求前提下,尽量选择下限硬度。
2.正确设计零件零件外形应尽量简单、均匀、结构对称,以免因冷却不均匀,使变形开裂倾向增大。
尽量避免截面尺寸突然变化,减少沟槽和薄边,不要有尖锐棱角。
避免较深的不通孔。
长形零件避免截面呈横梯形。
3.合理安排生产路线,协调冷热加工与热处理的关系对于形状复杂、精度要求高的零件,应在粗、精加工之间进行预先处理,如消除应力、退火等。
热处理淬火及变形
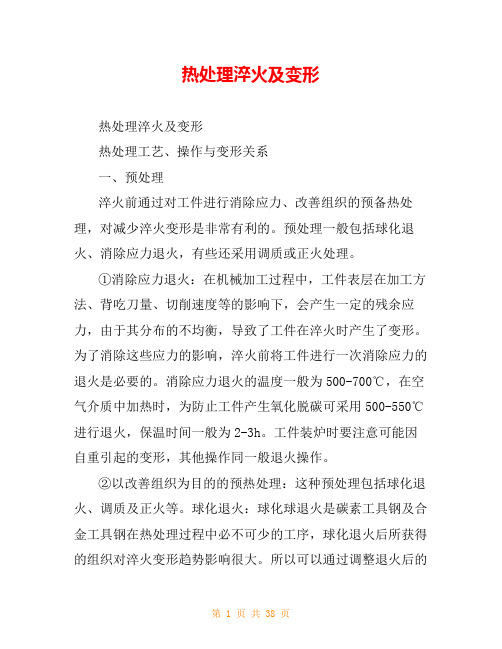
热处理淬火及变形热处理淬火及变形热处理工艺、操作与变形关系一、预处理淬火前通过对工件进行消除应力、改善组织的预备热处理,对减少淬火变形是非常有利的。
预处理一般包括球化退火、消除应力退火,有些还采用调质或正火处理。
①消除应力退火:在机械加工过程中,工件表层在加工方法、背吃刀量、切削速度等的影响下,会产生一定的残余应力,由于其分布的不均衡,导致了工件在淬火时产生了变形。
为了消除这些应力的影响,淬火前将工件进行一次消除应力的退火是必要的。
消除应力退火的温度一般为500-700℃,在空气介质中加热时,为防止工件产生氧化脱碳可采用500-550℃进行退火,保温时间一般为2-3h。
工件装炉时要注意可能因自重引起的变形,其他操作同一般退火操作。
②以改善组织为目的的预热处理:这种预处理包括球化退火、调质及正火等。
球化退火:球化球退火是碳素工具钢及合金工具钢在热处理过程中必不可少的工序,球化退火后所获得的组织对淬火变形趋势影响很大。
所以可以通过调整退火后的组织来减少某些工件有规律的淬火变形。
其他预处理:为减少淬火变形所采用的预处理方法有很多种,如调质处理、正火处理等。
针对工件产生淬火变形的原因及工件所用材料,合理地选用正火、调质等预处理对减少淬火变形是有效的。
但应对正火后引起的残余应力及硬度提高对机加工的不利影响应给予注意,同时调质处理对含WMn等钢可减少淬火时胀大,而对GCr15等钢种的减少变形作用不大。
在实际生产中要注意分清淬火变形产生的原因,即要分清淬火变形是由残余应力引起的还是由组织不佳引起的,只有这样才能对症处理。
若是由残余应力引起的淬火变形则应进行消除应力退火而不用类似调质等改变组织的预处理,反之亦然。
只有这样,才能达到减少淬火变形的目的,才能降低成本,保证质量。
以上各种预处理的具体操作同其他相应操作,此处不赘述。
二、淬火加热操作①淬火温度:淬火温度对工件的淬火变形影响很大。
其影响淬火变形趋势的一般规律如图所示。
薄壁件热处理变形
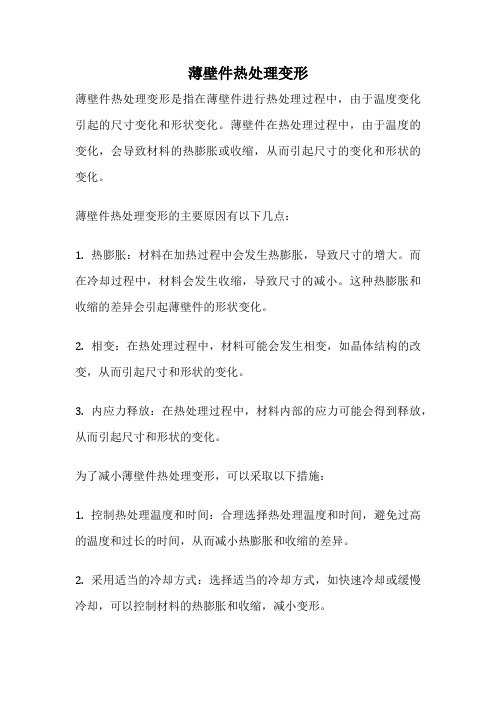
薄壁件热处理变形
薄壁件热处理变形是指在薄壁件进行热处理过程中,由于温度变化引起的尺寸变化和形状变化。
薄壁件在热处理过程中,由于温度的变化,会导致材料的热膨胀或收缩,从而引起尺寸的变化和形状的变化。
薄壁件热处理变形的主要原因有以下几点:
1. 热膨胀:材料在加热过程中会发生热膨胀,导致尺寸的增大。
而在冷却过程中,材料会发生收缩,导致尺寸的减小。
这种热膨胀和收缩的差异会引起薄壁件的形状变化。
2. 相变:在热处理过程中,材料可能会发生相变,如晶体结构的改变,从而引起尺寸和形状的变化。
3. 内应力释放:在热处理过程中,材料内部的应力可能会得到释放,从而引起尺寸和形状的变化。
为了减小薄壁件热处理变形,可以采取以下措施:
1. 控制热处理温度和时间:合理选择热处理温度和时间,避免过高的温度和过长的时间,从而减小热膨胀和收缩的差异。
2. 采用适当的冷却方式:选择适当的冷却方式,如快速冷却或缓慢冷却,可以控制材料的热膨胀和收缩,减小变形。
3. 采用适当的工艺参数:调整热处理的工艺参数,如加热速度、冷却速度等,可以减小薄壁件的变形。
4. 采用适当的夹具和支撑:在热处理过程中,使用适当的夹具和支撑,可以控制薄壁件的形状变化,减小变形。
薄壁件热处理变形是一个复杂的问题,需要综合考虑材料的性质、热处理工艺参数等因素,采取合适的措施来减小变形。
金属材料热加工处理发生形变的因素以及优化方法分析
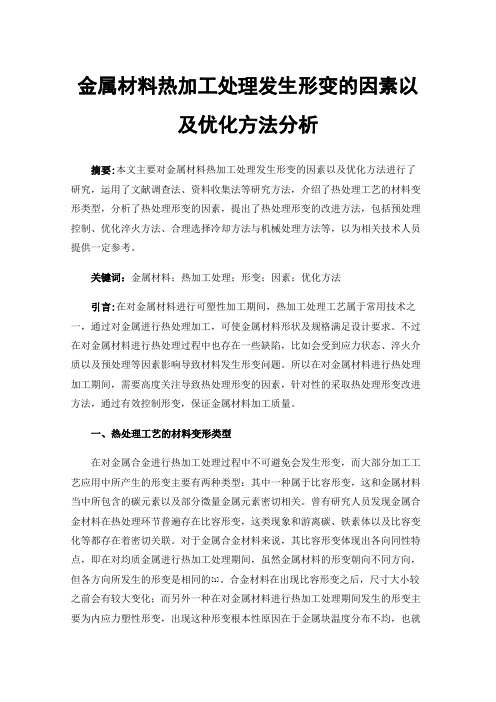
金属材料热加工处理发生形变的因素以及优化方法分析摘要:本文主要对金属材料热加工处理发生形变的因素以及优化方法进行了研究,运用了文献调查法、资料收集法等研究方法,介绍了热处理工艺的材料变形类型,分析了热处理形变的因素,提出了热处理形变的改进方法,包括预处理控制、优化淬火方法、合理选择冷却方法与机械处理方法等,以为相关技术人员提供一定参考。
关键词:金属材料;热加工处理;形变;因素;优化方法引言:在对金属材料进行可塑性加工期间,热加工处理工艺属于常用技术之一,通过对金属进行热处理加工,可使金属材料形状及规格满足设计要求。
不过在对金属材料进行热处理过程中也存在一些缺陷,比如会受到应力状态、淬火介质以及预处理等因素影响导致材料发生形变问题。
所以在对金属材料进行热处理加工期间,需要高度关注导致热处理形变的因素,针对性的采取热处理形变改进方法,通过有效控制形变,保证金属材料加工质量。
一、热处理工艺的材料变形类型在对金属合金进行热加工处理过程中不可避免会发生形变,而大部分加工工艺应用中所产生的形变主要有两种类型:其中一种属于比容形变,这和金属材料当中所包含的碳元素以及部分微量金属元素密切相关。
曾有研究人员发现金属合金材料在热处理环节普遍存在比容形变,这类现象和游离碳、铁素体以及比容变化等都存在着密切关联。
对于金属合金材料来说,其比容形变体现出各向同性特点,即在对均质金属进行热加工处理期间,虽然金属材料的形变朝向不同方向,但各方向所发生的形变是相同的[1]。
合金材料在出现比容形变之后,尺寸大小较之前会有较大变化;而另外一种在对金属材料进行热加工处理期间发生的形变主要为内应力塑性形变,出现这种形变根本性原因在于金属块温度分布不均,也就是在对金属块实现热加工期间,不同的金属块位置有着不同温度,在温度分布不均情况下,使得不同位置有着差异化的冷却速度,在温度逐步下降过程中,不同的金属位置所产生的热胀冷缩效应也是不尽相同的,由此所导致的不良形变即为热应力塑性形变。
201不锈钢热处理变形

201不锈钢热处理变形201不锈钢是一种高强度、耐腐蚀性能优异的不锈钢材料,广泛应用于航空航天、化工、石油、电子等领域。
在使用过程中,不锈钢材料经过热处理会发生一定的变形。
本文将探讨201不锈钢热处理变形的原因及其解决方法。
一、201不锈钢热处理变形的原因热处理是通过改变材料的组织结构和性能来满足特定的使用要求。
201不锈钢在热处理过程中,由于内部应力的释放和晶粒的长大,往往会出现一定程度的变形。
主要原因包括:1. 内应力的释放:在不锈钢材料的加热和冷却过程中,由于热膨胀系数的不同,不同部位的温度变化不一致,导致内部产生应力。
这些内应力在热处理过程中会得到释放,引起材料的变形。
2. 晶粒长大:在热处理过程中,不锈钢材料的晶粒会发生长大,这种长大往往会引起材料的变形。
晶粒长大是因为在高温下,晶界的迁移速度增加,晶粒逐渐长大。
3. 机械应力导致的变形:在热处理过程中,如果材料受到机械应力的作用,也会导致材料的变形。
这种机械应力可以是由于材料本身的形状不均匀或者外部施加的载荷等。
针对201不锈钢热处理变形的问题,可以采取以下解决方法:1. 控制热处理温度和时间:合理控制不锈钢材料的热处理温度和时间,可以减少材料的变形。
通过优化热处理工艺参数,可以使材料内部应力和晶粒长大趋于平衡,减少材料的变形。
2. 采用适当的退火工艺:针对201不锈钢的热处理变形问题,可以采用适当的退火工艺进行处理。
退火可以通过恢复应力、减小晶粒尺寸等方式来减少材料的变形。
3. 加强材料的支撑和固定:在热处理过程中,可以采取合理的支撑和固定措施,防止材料发生变形。
通过加强材料的支撑和固定,可以减少材料的机械应力导致的变形。
4. 优化材料的化学成分:合理控制201不锈钢材料的化学成分,可以改善材料的热处理性能,减少材料的变形。
通过调整材料的合金元素含量和比例,可以降低材料的内应力和晶粒长大的程度。
总结起来,201不锈钢热处理变形是由内应力的释放、晶粒长大和机械应力导致的。
五金弹簧在热处理过程中变形的主要原因与解决

五金弹簧在热处理过程中变形的主要原因与解决一、五金弹簧在热处理过程中变形的主要原因是什么?(1)相信大家经常订弹簧的都知道,弹簧在热处理的时候有时有出现变形的情况,那么出现这个情况的主要原因是什么呢?其实在东莞五金弹簧的常规热处理中,零件形状变化的主要原因是热处理和淬火过程中的热应力和相变应力。
如果加热速度过快,零件与加热炉相比过大,并且每个零件的温度不同,就会导致热变形。
在保温过程中,会释放残余应力,产生变形,零件自重也会导致变形。
(2)在冷却过程中,由于零件不同部位的冷却速度不同,会形成热应力,使零件变形。
即使冷却速度相同,表面冷却总是快,中心冷却总是慢。
因此,第一相变表面使非相变中心发生塑性变形,如果材料表面出现合金成分偏析或脱碳,则相变应力更不均匀,更容易引起零件变形。
另外,如果零件厚度不均匀,冷却速度也会不同。
(3)在锻件热处理中,减少变形的零件按以下方式放置:一是尽量垂直悬挂,二是垂直放置在炉底,三是用两点水平支撑,支点位置在全长的三分之一到四分之一之间,四是,水平放置在耐热钢工具上。
在零件的冷却过程中,淬火介质的种类、冷却性能和淬透性与变形有关。
冷却性能的变化可以通过改变粘度、温度、液体压力、使用添加剂、搅拌等来调节。
淬火油的粘度和温度越高,椭圆变形越小。
静态时,变形较小。
二、哪些方法可以有效地减小变形(1)盐浴淬火;(2)高温油淬火;(3)QSQ方法;(4)解压淬火;(5)一浴三级淬火。
(6)盐浴淬火与高温油淬火相似,都是在马氏体相变温度下淬火,使马氏体相变的均匀性增加。
Qsq为双液淬。
减压淬火是降低淬火介质的液体压力,从而延长蒸汽膜的级数,降低高温区的冷却速度,使零件各部位的冷却速度均匀。
一浴三段淬火结构简单。
首先将零件从淬火温度油中冷却到略高于MS点的温度,然后将其出炉,保存在大气中,使零件的整体温度均匀,然后用油冷却,使马氏体转变均匀进行,变形不规则性大大改善。
热处理变形的原因
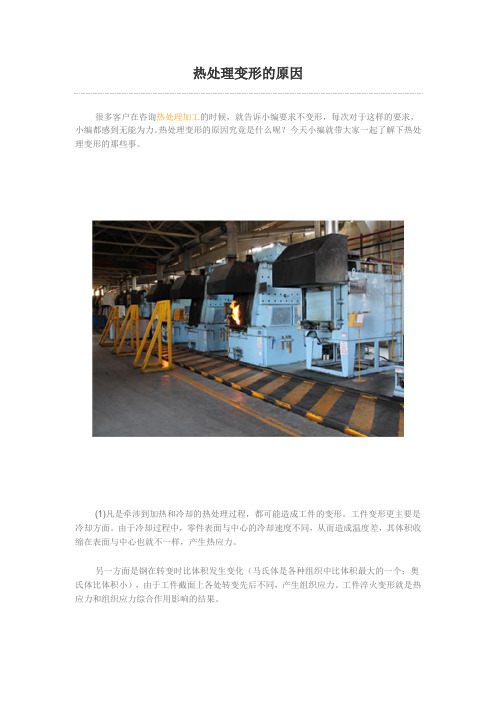
很多客户在咨询热处理加工的时候,就告诉小编要求不变形,每次对于这样的要求,小编都感到无能为力。
热处理变形的原因究竟是什么呢?今天小编就带大家一起了解下热处理变形的那些事。
(1)凡是牵涉到加热和冷却的热处理过程,都可能造成工件的变形。
工件变形更主要是冷却方面。
由于冷却过程中,零件表面与中心的冷却速度不同,从而造成温度差,其体积收缩在表面与中心也就不一样,产生热应力。
另一方面是钢在转变时比体积发生变化(马氏体是各种组织中比体积最大的一个;奥氏体比体积小),由于工件截面上各处转变先后不同,产生组织应力。
工件淬火变形就是热应力和组织应力综合作用影响的结果。
(2)工件的结构形状、原材料质量、热处理前的加工状态、工件的自重以及工件在炉中加热和冷却时的支承或夹持不当,冷却投入方向、方法和冷却时在冷却中的动作不当等也能引起变形。
加热温度高,冷却速快,故淬火变形最为严重。
(3)工件热处理后的不稳定组织和不稳定的应力状态,在常温和零下温度长时间放置或使用过程中,逐渐发生转变而趋于稳定,也会伴随引起工件的变形,这种变形称为时效变形。
时效变形虽然不大,但是对于精密零件和标准量具也不许的。
实际生产中必须予以防止。
(4)热处理过程中产生的内应力有
热应力和相变应力,它们的形成原因和作用是不同的。
这种应力在热处理过程中对变形影响是主要的原因。
钢件热处理变形的原因总结

钢件热处理变形的原因总结
引起热处理变形的因素颇多,总括起来,基本上有三点:
1、固态相变时,各相质量体积的变化必然引起体积的变化,造成零件的胀与缩的尺寸变化;
2、热应力,包括急热热应力和急冷热应力,当它们超过零件在该温度下所具有的屈服极限时,将使零件产生塑性变形,造成零件的形状变化,即歪扭,或称为畸变;
3、组织应力也会引起形状的改变,即畸变。
一般说,淬火工件的变形总是由于以上的两种或三种因素综合作用的结果,但究竟哪一个因素对变形的影响较大,则需要具体情况作具体的分析。
总的来说,体积变化是由相变时比容的改变而引起的。
马氏体的质量体积比钢的其他组成相的质量体积要大,热处理时钢由其他组成相转化为马氏体时,必然引起体积的增加。
而奥氏体的质量体积要比钢的其他组织质量体积要小,在热处理时由其他组成相转变为奥氏体时,则引起体积的减小。
关于形状的变化,歪扭或称为畸变,主要是由于内应力或者外加应力作用的结果。
在加热、冷却过程中,因工件各个部位的温度有差别,相变在时间上有先后,有时发生的组织转变也不一致,而造成内应力。
这种内应力一旦超过了该温度下材料的屈服极限,就产生塑性变形,引起形状的改变。
此外工件内的冷加工残余应力在加热过程中的松弛,以及由于加热时受到较大的外加应力也会引起形状的变化。
在热处理时可能引起体积变化和形状变化的原因见下表。
表中“体积变化原因” 一栏未列入钢因热胀冷缩现象而产生的体积变化,钢由淬火加热温度到零下温度进行冷处理,均随温度的变化而有相应的体积变化,因热胀冷缩而引起的体积变化不均匀乃是热应力产生的原因,而且对变形有相当的影响。
热处理可能引起体积变化和形状变化的原因。
金属材料热处理变形的影响因素与控制策略
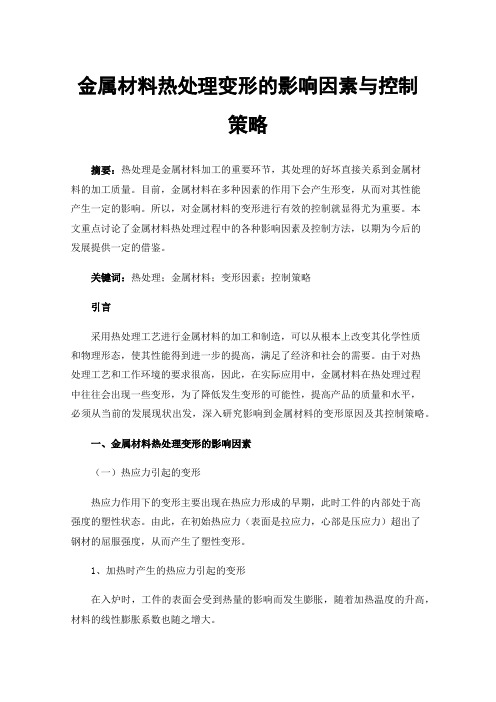
金属材料热处理变形的影响因素与控制策略摘要:热处理是金属材料加工的重要环节,其处理的好坏直接关系到金属材料的加工质量。
目前,金属材料在多种因素的作用下会产生形变,从而对其性能产生一定的影响。
所以,对金属材料的变形进行有效的控制就显得尤为重要。
本文重点讨论了金属材料热处理过程中的各种影响因素及控制方法,以期为今后的发展提供一定的借鉴。
关键词:热处理;金属材料;变形因素;控制策略引言采用热处理工艺进行金属材料的加工和制造,可以从根本上改变其化学性质和物理形态,使其性能得到进一步的提高,满足了经济和社会的需要。
由于对热处理工艺和工作环境的要求很高,因此,在实际应用中,金属材料在热处理过程中往往会出现一些变形,为了降低发生变形的可能性,提高产品的质量和水平,必须从当前的发展现状出发,深入研究影响到金属材料的变形原因及其控制策略。
一、金属材料热处理变形的影响因素(一)热应力引起的变形热应力作用下的变形主要出现在热应力形成的早期,此时工件的内部处于高强度的塑性状态。
由此,在初始热应力(表面是拉应力,心部是压应力)超出了钢材的屈服强度,从而产生了塑性变形。
1、加热时产生的热应力引起的变形在入炉时,工件的表面会受到热量的影响而发生膨胀,随着加热温度的升高,材料的线性膨胀系数也随之增大。
对于热处理变形量小的工件,应首先进行预热,然后逐步升温至更高的温度,以减少加热过程中的热应力。
在低温度和低变形的氮化过程中,缓慢的加热往往是降低变形的一种有效途径。
2、冷却时产生的热应力引起的变形工件在冷却过程中所引起的热应力大于在加热过程中所引起的热应力。
尤其是在盐水中冷却的碳钢件,由于温度和温度的变化,会产生较大的热应力。
(二)组织应力引起的变形1、组织应力引起的变形组织应力导致的变形,是导致材料体积发生改变的重要原因。
由于不同组织的比容,在淬火和冷却时,体积的改变是不可避免的。
该变形特征是,工件的各个部件的大小以相同的速度膨胀或缩小,而不会对工件的外观产生影响。
金属材料热处理变形的影响因素及应对措施
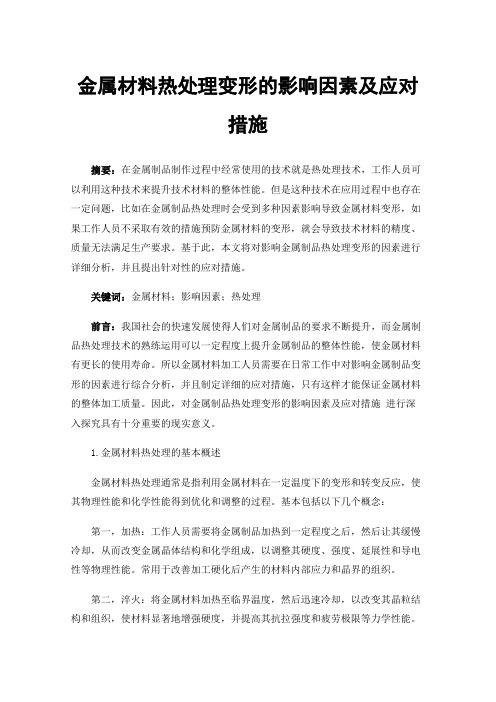
金属材料热处理变形的影响因素及应对措施摘要:在金属制品制作过程中经常使用的技术就是热处理技术,工作人员可以利用这种技术来提升技术材料的整体性能。
但是这种技术在应用过程中也存在一定问题,比如在金属制品热处理时会受到多种因素影响导致金属材料变形,如果工作人员不采取有效的措施预防金属材料的变形,就会导致技术材料的精度、质量无法满足生产要求。
基于此,本文将对影响金属制品热处理变形的因素进行详细分析,并且提出针对性的应对措施。
关键词:金属材料;影响因素;热处理前言:我国社会的快速发展使得人们对金属制品的要求不断提升,而金属制品热处理技术的熟练运用可以一定程度上提升金属制品的整体性能,使金属材料有更长的使用寿命。
所以金属材料加工人员需要在日常工作中对影响金属制品变形的因素进行综合分析,并且制定详细的应对措施,只有这样才能保证金属材料的整体加工质量。
因此,对金属制品热处理变形的影响因素及应对措施进行深入探究具有十分重要的现实意义。
1.金属材料热处理的基本概述金属材料热处理通常是指利用金属材料在一定温度下的变形和转变反应,使其物理性能和化学性能得到优化和调整的过程。
基本包括以下几个概念:第一,加热:工作人员需要将金属制品加热到一定程度之后,然后让其缓慢冷却,从而改变金属晶体结构和化学组成,以调整其硬度、强度、延展性和导电性等物理性能。
常用于改善加工硬化后产生的材料内部应力和晶界的组织。
第二,淬火:将金属材料加热至临界温度,然后迅速冷却,以改变其晶粒结构和组织,使材料显著地增强硬度,并提高其抗拉强度和疲劳极限等力学性能。
第三,固溶处理:这需要工作人员将金属制品的温度保持在一定温度下,使材料中的固溶体或混合物溶解为单一相,然后迅速冷却以避免沉淀形成,从而获得均匀的微观组织结构和化学成分,以增强金属的抗腐蚀性、可加工性和机械性能等。
第四,沉淀强化处理:将金属材料进行固溶处理后,再退火至特定温度下让固溶体于固溶体中析出沉淀相,从而形成分散的硬质相,使材料得到强化。
热处理变形产生的原因及控制方法
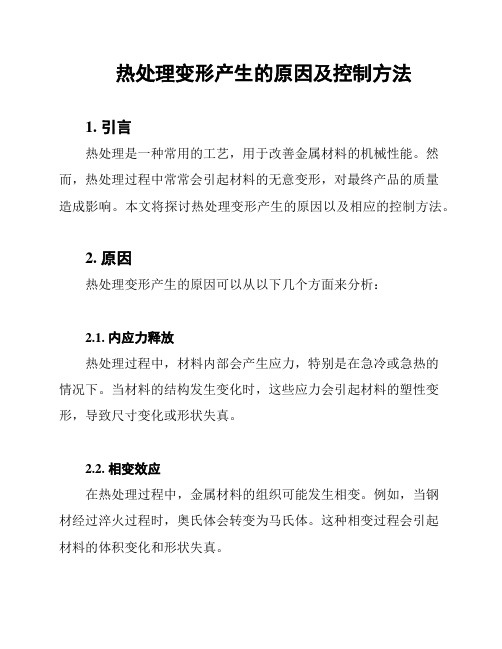
热处理变形产生的原因及控制方法1. 引言热处理是一种常用的工艺,用于改善金属材料的机械性能。
然而,热处理过程中常常会引起材料的无意变形,对最终产品的质量造成影响。
本文将探讨热处理变形产生的原因以及相应的控制方法。
2. 原因热处理变形产生的原因可以从以下几个方面来分析:2.1. 内应力释放热处理过程中,材料内部会产生应力,特别是在急冷或急热的情况下。
当材料的结构发生变化时,这些应力会引起材料的塑性变形,导致尺寸变化或形状失真。
2.2. 相变效应在热处理过程中,金属材料的组织可能发生相变。
例如,当钢材经过淬火过程时,奥氏体会转变为马氏体。
这种相变过程会引起材料的体积变化和形状失真。
2.3. 不均匀加热或冷却如果热处理过程中加热或冷却不均匀,材料的局部温度会存在差异。
这种温度差异会导致材料的非均匀膨胀或收缩,从而引起变形。
3. 控制方法为了减少热处理产生的变形,可以采取以下控制方法:3.1. 控制加热和冷却速率合理控制加热和冷却速率,避免过快或过慢,可以减少材料的变形。
在进行急冷或急热处理时,可以采取预先控制的温度梯度,以缓解内应力的释放。
3.2. 优化工艺参数通过调整热处理过程中的工艺参数,如温度、时间和冷却介质等,可以最大限度地减少材料的变形。
合理选择工艺参数,可以提高材料的均匀性和稳定性。
3.3. 采用合适的支撑结构对于形状复杂的工件,可以采用合适的支撑结构来减少变形。
支撑结构可以提供一定的约束,防止材料发生不受控制的变形。
4. 结论热处理变形是热处理过程中常见的问题,但通过合理的控制方法可以有效减少其影响。
合理控制加热和冷却速率、优化工艺参数以及采用合适的支撑结构都是减少热处理变形的有效途径。
这些控制方法可以提高最终产品的质量和性能。
---以上是关于热处理变形产生的原因及控制方法的内容。
请基于以上内容,进一步完善和添加具体细节,使文档达到800字以上的要求。
热处理变形校正方法

热处理变形校正方法在金属加工行业中,热处理是一个至关重要的环节,它能够改善材料的性能,为产品提供必要的强度和硬度。
然而,热处理过程中往往伴随着变形的问题,这给产品质量带来了挑战。
本文将详细介绍热处理变形校正的方法,帮助读者更好地理解和应对这一工艺难题。
一、热处理变形的原因热处理变形主要是由于材料在加热和冷却过程中,内部应力重新分布所导致的。
当材料暴露在高温环境下,其晶体结构会发生改变,冷却后,这些改变会导致尺寸变化和形状变形。
二、热处理变形校正方法1.预防措施:- 选择合适的材料:不同材料的热处理变形程度不同,选择变形较小的材料是预防变形的有效手段。
- 优化热处理工艺:通过调整加热速度、保温时间、冷却速度等参数,降低热处理变形的风险。
2.变形校正方法:- 机械校正:通过机械力对变形部位进行校正,如锤击、拉伸等,但这种方法仅适用于轻微变形。
- 热校正:利用材料在高温下的塑性变形,对变形部位进行加热至适当温度后进行校正。
这种方法对操作技术要求较高,需防止过度加热导致新的变形。
- 液体校正:将变形部位浸入高温液体中,利用液体的压力和温度对变形进行校正。
此方法适用于复杂形状的零件。
3.数控加工校正:- 采用数控加工技术,根据变形量对零件进行精确加工,以消除变形影响。
这种方法适用于高精度要求的零件。
4.表面处理:- 对变形部位进行表面处理,如喷漆、氧化等,以掩盖或补偿变形。
三、总结热处理变形是金属加工中不可避免的问题,但通过合理的预防措施和校正方法,可以最大限度地降低变形对产品质量的影响。
在实际操作中,应根据具体情况选择合适的校正方法,确保产品达到预期的性能和质量要求。
热处理变形原因与变形控制技术措施论文
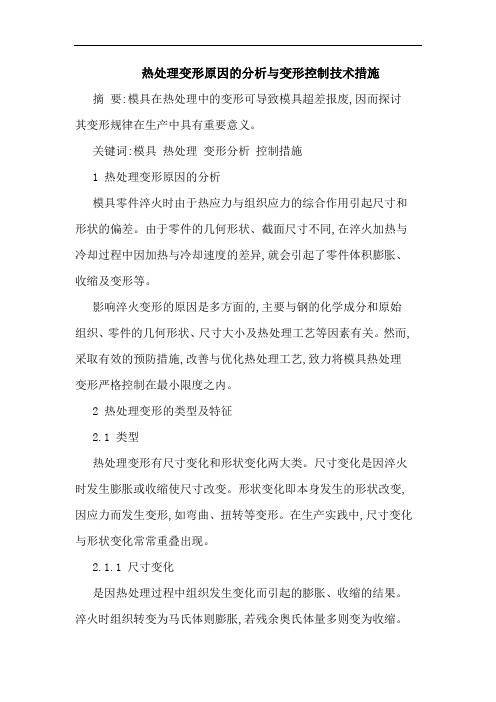
热处理变形原因的分析与变形控制技术措施摘要:模具在热处理中的变形可导致模具超差报废,因而探讨其变形规律在生产中具有重要意义。
关键词:模具热处理变形分析控制措施1 热处理变形原因的分析模具零件淬火时由于热应力与组织应力的综合作用引起尺寸和形状的偏差。
由于零件的几何形状、截面尺寸不同,在淬火加热与冷却过程中因加热与冷却速度的差异,就会引起了零件体积膨胀、收缩及变形等。
影响淬火变形的原因是多方面的,主要与钢的化学成分和原始组织、零件的几何形状、尺寸大小及热处理工艺等因素有关。
然而,采取有效的预防措施,改善与优化热处理工艺,致力将模具热处理变形严格控制在最小限度之内。
2 热处理变形的类型及特征2.1 类型热处理变形有尺寸变化和形状变化两大类。
尺寸变化是因淬火时发生膨胀或收缩使尺寸改变。
形状变化即本身发生的形状改变,因应力而发生变形,如弯曲、扭转等变形。
在生产实践中,尺寸变化与形状变化常常重叠出现。
2.1.1 尺寸变化是因热处理过程中组织发生变化而引起的膨胀、收缩的结果。
淬火时组织转变为马氏体则膨胀,若残余奥氏体量多则变为收缩。
冷处理时因残余奥氏体转变成马氏体又引起膨胀。
马氏体引起的体积膨胀随钢中碳含量增加而变大;其尺寸变化量亦随着增大。
淬火钢回火时马氏体发生分解,而引起收缩;收缩量随马氏体中c%的增多而增大,但若以淬火前的状态为基准,淬火回火后尺寸变化的总合,其结果仍是膨胀。
2.1.2 形状变化是因淬火钢内部的应力及加于外部的力量而引起的。
内部应力是因温度分布不均或因组织转变而引起的。
而外部的力主要是因自重而导致“下垂”。
加热温度越高、保温时间越长,这种因本身重量而引起的“下垂”变形更易发生。
工件加热时,因机械加工或常温加工所产生的残余应力,将发生形状变化。
即使是均匀加热,因钢的屈服点随温度上升而降低之故,此时只要有少许应力存在即发生变形。
因残余应力于外部周围较强。
当温度上升自外部进行时,变形于外部周围特别显著。
金属材料热处理变形原因及防止变形的技术措施

金属材料热处理变形原因及防止变形的技术措施摘要:热处理能改善工件的综合机械机能,但热处理过程引起工件的变形是不可避免的。
任何因素的变化都或多或少地影响工件的变形倾向和形变大小。
在热处理过程中,能够把握工件热处理过程中导致工件变形的主要因素和关键点。
通过分析和实践,改进热处理工艺技术,一定能够在热处理工件的形变问题上得到突破,制定出合理的技术措施,保证热处理产品的质量和合格率。
关键词:金属材料;热处理;变形原因;防止变形技术引言实际工业生产中,仅凭选择材料和成形工艺并不能满足工件所需要的性能,通过对金属材料进行热处理而获得优良的综合性能是必不可少的。
但金属材料的热处理除改善材料的综合性能的积极作用外,在热处理过程中也不可避免地会产生或多或少的变形,而这又是工件生产过程中极力消除和避免的。
因此,需要找出工件热处理过程中发生形变的原因,采取技术措施把变形量控制在符合要求范围内。
1金属材料性能分析在当前的社会生产生活中,金属材料的应用范围十分的广泛。
由于金属材料具有韧性强、塑性好以及高强度的特点,因此其在诸多行业中均有所应用。
当前常用的金属材料主要包括两种:即多孔金属材料以及纳米金属材料。
纳米金属材料:一般情况下,只有物质的尺寸达到了纳米的级别,那么该物质的物理性质和化学性质均会发生改变。
在分析与研究金属材料性能的过程中,主要分析金属材料的如下两种性能:其一,硬度。
一般情况下,金属材料的硬度主要指的是金属材料的抗击能力。
其二,耐久性。
耐久性能和腐蚀性是金属材料需要着重考虑的一对因素。
在应用金属材料的过程中不可避免的会受到各种物质的腐蚀,由此就会导致金属材料出现缝隙等问题。
2金属热处理变形的原因分析在工业生产过程中,各种金属零件早已成为机械制造的必要部分。
在零件的设计、选材中,对综合性能方面也提出了更高要求。
特别是生产过程中,对产品热处理加工后的品质提出了新要求。
但在热处理过程中出现形变等质量问题,一直是热处理过程中难以克服的。
钢的热处理淬火时工件的变形规律

淬火时,工件发生的变形有两类,一是翘曲变形,一是体积变形。
翘曲变形包括形状变形和扭曲变形。
扭曲变形主要是加热时工件在炉内放置不当,或者淬火前经变形校正后没有定型处理,或者是由于工件冷却时工件各部位冷却不均匀所造成,这种变形可以针对具体情况分析解决。
1、引起各种变形的原因及其变化规律(1)由于淬火前后组织变化而引起的体积变形工件在淬火前的组织状态一般为珠光体型,即铁素体和渗碳体的混合组织,而淬火后为马氏体型组织。
由于这些组织体积不同,淬火前后将引起体积变化,从而产生变形。
这种变形只按比例使工件胀缩,但不改变形状。
淬火前后由此而引起的体积变化,可以计算求得。
(2)热应力引起的形状变形热应力引起的变形发生在钢件屈服强度较低,塑性较高,而表面冷却快,工件内外温差最大的高温区。
此时瞬时热应力是表面张应力,心部压应力,心部温度高,屈服强度比表面低很多,易于变形。
因此表现为在多向压应力作用下的变形,即立方体向呈球形方向变化。
由此导致尺寸较大的一方缩小,而尺寸较小的一方则胀大。
(3)组织应力引起的形状变形组织应力引起的变形也产生在早期组织应力最大时刻。
此时截面温度较大,心部温度较高,仍处于奥氏体状态,塑性较好,屈服强度较低。
瞬时组织应力是表面压应力,心部拉应力;其变形表现为心部在多向拉应力作用下的拉长。
由此导致的结果为在组织应力作用下,工件中尺寸较大的一方伸长,而尺寸较小的一方缩短。
2、影响淬火变形的因素(1)影响体积变形和形状变形的因素。
凡是影响淬火前后组织比体积变化的因素均影响体积变形。
(2)其他影响淬火变形的因素。
影响淬火变形的因素有两种,一种是夹杂物和带状组织对淬火变形的影响。
(3)淬火前残存应力及加热冷却不均匀对变形的影响。
淬火前工件内残余应力没有消除,淬火加热装炉不当,淬火冷却不当均引起工件的扭曲变形。
各种热处理工艺造成变形的原因总结

各种热处理工艺造成变形的原因总结引言:热处理工艺是一种常见的金属加工方法,它通过对金属材料进行加热和冷却来改变其结构和性能。
然而,热处理过程中往往会导致材料发生变形,这对于一些精密零件的加工和制造带来一定的困扰。
本文将从各种热处理工艺的角度,总结造成变形的原因,并探讨相应的解决方法。
一、淬火过程中的变形原因淬火是一种通过快速冷却来使金属材料达到高强度和硬度的热处理工艺。
然而,淬火过程中常常会出现变形现象。
造成淬火变形的主要原因有以下几点:1. 冷却速度不均匀:淬火过程中,材料表面和内部的冷却速度不一致,导致应力不均匀分布,从而引起变形。
2. 材料内部组织不均匀:金属材料内部的组织不均匀,如晶粒尺寸、相含量等差异,会导致淬火时的收缩和变形不一致。
3. 冷却介质选择不当:不同的冷却介质对材料的冷却速度有不同的影响,选择不当可能导致应力集中和变形。
解决方法:针对淬火过程中的变形问题,可以采取以下措施:1. 控制冷却速度:通过优化冷却介质的选择和控制冷却速度,使材料表面和内部的冷却速度尽可能一致,减少应力的不均匀分布。
2. 优化材料组织:通过调整材料的化学成分和热处理工艺,使材料内部的组织更加均匀,减少淬火时的收缩和变形差异。
3. 采用适当的淬火工艺:根据材料的特性和要求,选择适当的淬火工艺,控制冷却速度和温度,减少变形的发生。
二、退火过程中的变形原因退火是一种通过加热和缓慢冷却来改善材料的性能和结构的热处理工艺。
然而,退火过程中同样存在变形的问题。
造成退火变形的主要原因有以下几点:1. 温度不均匀:退火过程中,材料的温度分布不均匀,导致应力分布不均匀,从而引起变形。
2. 冷却速度过快:退火结束后,如果冷却速度过快,会导致材料内部的残余应力无法得到充分释放,从而引起变形。
3. 材料内部缺陷:金属材料内部存在各种缺陷,如气孔、夹杂物等,这些缺陷在退火过程中会扩散和移动,导致变形的发生。
解决方法:针对退火过程中的变形问题,可以采取以下措施:1. 控制温度均匀性:通过合理设计加热设备和工艺参数,确保材料的温度分布均匀,减少应力的不均匀分布。
42crmo热处理工变形

42crmo热处理工变形
42CrMo钢的热处理变形是热处理过程中常见的问题之一。
变形主要是由于热处理过程中温度分布不均匀、材料组织转变不均匀等原因导致的。
为了减小42CrMo钢热处理变形,可以考虑以下几个方面:
预热处理:在加热之前,对42CrMo钢材进行预热处理,以避免钢材在加热时因为突然升高的温度而造成变形或者开裂现象。
预加热温度一般为500℃左右,时间不少于1小时。
均匀加热:在加热过程中,要确保42CrMo钢材均匀受热,以避免温度分布不均导致组织转变不均匀,从而引起变形。
控制加热和冷却速度:加热和冷却速度对42CrMo钢热处理变形有重要影响。
应合理控制加热和冷却速度,以减小温度变化引起的应力,从而减小变形。
合理选择淬火介质:淬火介质的选择对42CrMo钢热处理变形也有影响。
应选择淬火冷却速度适宜的淬火介质,以减小淬火过程中产生的热应力,从而减小变形。
回火处理:在淬火后进行回火处理,以消除内应力和稳定组织结构,进一步减小热处理变形。
需要注意的是,热处理变形的控制是一个复杂的过程,需要综合考虑多个因素。
在实际操作中,应根据具体情况进行调整和控制,以达到最佳效果。
模具热处理常见变形原因及控制措施
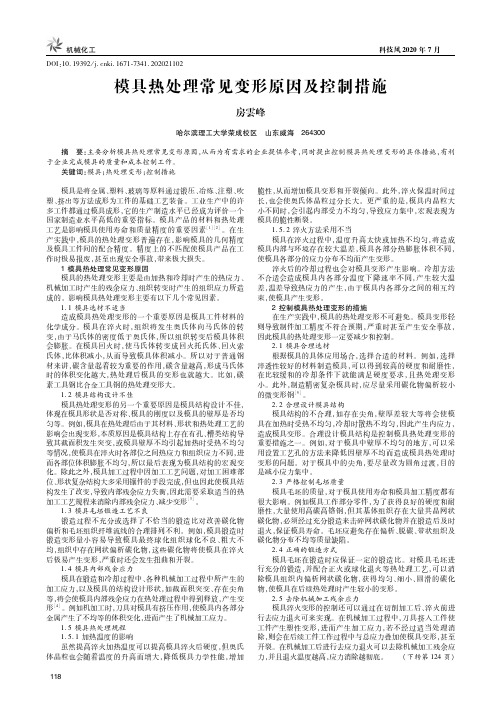
44模具是将金属)塑料)玻璃等原料通过锻压)冶炼)注塑)吹 塑)挤出等方法成形为工件的基础工艺装备# 工业生产中的许 多工件都通过模具成形"它的生产制造水平已经成为评价一个 国家制造业水平高低的重要指标# 模具产品的材料和热处理 工艺是影响模具使用寿命和质量精度的重要因素-$.-). # 在生 产实践中"模具的热处理变形普遍存在"影响模具的几何精度 及模具工件间的配合精度# 精度上的不匹配使模具产品在工 作时极易报废"甚至出现安全事故"带来极大损失#
%模具热处理常见变形原因 模具的热处理变形主要是由加热和冷却时产生的热应力) 机械加工时产生的残余应力)组织转变时产生的组织应力所造 成的# 影响模具热处理变形主要有以下几个常见因素# $&$ 模具选材不适当 造成模具热处理变形的一个重要原因是模具工件材料的 化学成分# 模具在淬火时"组织将发生奥氏体向马氏体的转 变"由于马氏体的密度低于奥氏体"所以组织转变后模具体积 会膨胀# 在模具回火时"使马氏体转变成回火托氏体)回火索 氏体"比体积减小"从而导致模具体积减小# 所以对于普通钢 材来讲"碳含量起着较为重要的作用"碳含量越高"形成马氏体 时的体积变化越大"热处理后模具的变形也就越大# 比如"碳 素工具钢比合金工具钢的热处理变形大# $&) 模具结构设计不佳 模具热处理变形的另一个重要原因是模具结构设计不佳" 体现在模具形状是否对称)模具的刚度以及模具的壁厚是否均 匀等# 例如"模具在热处理后由于其材料)形状和热处理工艺的 影响会出现变形"本质原因是模具结构上存在有孔)槽类结构导 致其截面积发生突变"或模具壁厚不均引起加热时受热不均匀 等情况"使模具在淬火时各部位之间热应力和组织应力不同"进 而各部位体积膨胀不均匀"所以最后表现为模具结构的宏观变 化# 除此之外"模具加工过程中因加工工艺问题"对加工困难部 位)形状复杂结构大多采用镶件的手段完成"但也因此使模具结 构发生了改变"导致内部残余应力失衡"因此需要采取适当的热 加工工艺规程来消除内部残余应力)减少变形-(. # $&( 模具毛坯锻造工艺不良 锻造过程不充分或选择了不恰当的锻造比对改善碳化物 偏析和毛坯组织纤维流线的合理排列不利# 例如"模具锻造时 锻造变形量小容易导致模具最终球化组织球化不良)粗大不 均"组织中存在网状偏析碳化物"这些碳化物将使模具在淬火 后极易产生变形"严重时还会发生扭曲和开裂# $&3 模具内部残余应力 模具在锻造和冷却过程中)各种机械加工过程中所产生的 加工应力"以及模具的结构设计形状"如截面积突变)存在尖角 等"将会使模具内部残余应力在热处理过程中得到释放"产生变 形-3. # 例如机加工时"刀具对模具有挤压作用"使模具内各部分 金属产生了不均等的体积变化"进而产生了机械加工应力# $&5 模具热处理规程 $&5&$ 加热温度的影响 虽然提高淬火加热温度可以提高模具淬火后硬度"但奥氏 体晶粒也会随着温度的升高而增大"降低模具力学性能"增加
影响金属材料热处理变形的因素及减小措施研究

影响金属材料热处理变形的因素及减小措施研究在金属材料加工制造的过程中应用热处理技术,主要的目的是为了促进材料自身性能的提高,确保金属材料可以满意社会经济进展的实际需求。
而热处理过程在提高金属材料性能的同时,也不行避开的产生热处理变形,使工件的尺寸发生偏离,给后续机械加工造成困难,严峻者甚至会使工件报废。
作为热处理工艺员,必需实行切实可行的方法将金属材料热处理的变形掌握在允许的范围之内。
1 金属材料热处理变形影响因素在进行金属材料的热处理时,通常会由于材料自身的密度、结构以及外部因素的影响,而消失冷热分布不匀称的的状况。
一般状况下金属材料的热处理主要分为加热、保温以及冷却三部分内容,由于金属材料受热及冷却时,随着温度的变化,其内部结构的应力也会随之发生转变,从而增加了金属材料变形的几率。
大多数状况下,在进行金属材料的热处理时,都会消失由于材料内部应力分布不匀称而造成的变形,也就是通常所说的内应力塑性变形。
这种变形最显著的特点是,不仅其方向性特别显著,而且发生频率也相对较高。
金属材料内部应力结构会随着金属材料热处理的次数而发生转变,也就是说金属材料进行热处理的次数越多,内应力结构的变化也就越明显,正是由于受到这样的影响,从而导致了金属材料的结构与外形都消失了显著的变化。
但是金属材料内应力塑性变形并不会影响到金属材料本身,这种变化只是针对于材料的内部结构。
在进行内应力塑性变形实际的分析后发觉,导致金属材料内应力产生的因数有许多种,而不同因素引发的变形方式也不同。
在金属材料热处理过程中比较常见的内应力塑性变形主要有组织应力变形和热应力变形两种。
金属材料处于温度环境下进行加热冷却处理时,必需要把握金属材料的热应力变形,否则无法实现金属材料的组织应力变形,也就是说,金属材料自身的淬透性、材料外形以及加热冷却方式直接打算着组织应力变形。
经过分析内应力塑性变形的种类和特点后发觉,虽然在实际的操作过程中,已经把握了对金属材料的加热、保温以及冷却等技术和工艺,但是经过实际的操作发觉,在金属材料热处理的过程中还必需充分的重视正火、淬火、回火以及退火等工艺,才能从根本上保证金属材料热处理的质量与水平不断的提高。
- 1、下载文档前请自行甄别文档内容的完整性,平台不提供额外的编辑、内容补充、找答案等附加服务。
- 2、"仅部分预览"的文档,不可在线预览部分如存在完整性等问题,可反馈申请退款(可完整预览的文档不适用该条件!)。
- 3、如文档侵犯您的权益,请联系客服反馈,我们会尽快为您处理(人工客服工作时间:9:00-18:30)。
一变形的原因
钢的变形主要原因是钢中存在内应力或者外部施加的应力。
内应力是因温
度分布不均匀或者相变所致,残余应力也是原因之一。
外应力引起的变形主要
是由于工件自重而造成的“塌陷”,在特殊情况下也应考虑碰撞被加热的工件,或者夹持工具夹持所引起的凹陷等。
变形包括弹性变形和塑性变形两种。
尺寸
变化主要是基于组织转变,故表现出同样的膨胀和收缩,但当工件上有孔穴或
者复杂形状工件,则将导致附加的变形。
如果淬火形成大量马氏体则发生膨胀,如果产生大量残余奥氏体则相应的要收缩。
此外,回火时一般发生收缩,而出
现二次硬化现象的合金钢则发生膨胀,如果进行深冷处理,则由于残余奥氏体
的马氏体化而进一步膨胀,这些组织的比容都随着含碳量的增加而增大,故含
碳量增加也使尺寸变化量增大。
二淬火变形的主要发生时段1加热过程:工件在加热过程中,由于内应力逐渐
释放而产生变形。
2保温过程:以自重塌陷变形为主,即塌陷弯曲。
3冷却过程:由于不均匀冷却和组织转变而至变形。
三加热与变形
当加热大型工件时,存在残余应力或者加热不均匀,均可产生变形。
残余
应力主要来源于加工过程。
当存在这些应力时,由于随着温度的升高,钢的屈
服强度逐渐下降,即使加热很均匀,很轻微的应力也会导致变形。
一般,工件的外缘部位残余应力较高,当温度的上升从外部开始进行时,
外缘部位变形较大,残余应力引起的变形包括弹性变形和塑性变形两种。
加热时产生的热应力和想变应力都是导致变形的原因。
加热速度越快、工
件尺寸越大、截面变化越大,则加热变形越大。
热应力取决于温度的不均匀分
布程度和温度梯度,它们都是导致热膨胀发生差异的原因。
如果热应力高于材
料的高温屈服点,则引起塑性变形,这种塑性变形就表现为“变形”。
相变应力主要源于相变的不等时性,即材料一部分发生相变,而其它部分
还未发生相变时产生的。
加热时材料的组织转变成奥氏体发生体积收缩时可出
现塑性变形。
如果材料的各部分同时发生相同的组织转变,则不产生应力。
为此,缓慢加热可以适当降低加热变形,最好采用预热。
此外,由于加热中因自重而出现“塌陷”变形的情况非常多,加热温度越高,加热时间越长,“塌陷”现象越严重。
四冷却与变形
冷却不均时将产生热应力导致变形发生。
因工件的外缘和内部存在冷却速
度差异,该热应力是不可避免的,淬火情况下,热应力与组织应力叠加,变形
更为复杂。
加之组织的不均匀、脱碳等,还会导致相变点出现差异,相变的膨
胀量也有所不同。
总之,“变形”是相变应力和热应力共同所致,但并非全部应力都消耗在
变形上,而是一部分作为残余应力存在于工件中,这种应力就是导致时效变形
和时效裂纹的原因。
因冷却而导致的变形表现为以下几种形式:1件急冷初期,急冷的一侧凹陷,然后转为凸起,结果快冷的一面凸起,这种情况属于热应力引起的变形大于相变引起的变形。
2由热应力所引起的变形是钢料趋于球形化(见图1),而由相变应力所引起的变形则使之趋于绕线轴状(见图2)。
因此淬火冷却所致的变形表现为两者的结合(图3),按照淬火方式的不同,表现出不同的变形如图4所示。
3仅对内孔部分淬火时,内孔收缩。
将整个环形工件加热整体淬火时,其外径总是增大,而内径则根据尺寸的不同时涨时缩,一般内径大时,内孔涨大,内径小时,内孔收缩。
五冷处理与变形
冷处理促进马氏体转变,温度较低,产生的变形比淬火冷却要小,但此时产生的应力较大,由于残余应力、相变应力和热应力等的叠加容易导致开裂。
六回火与变形
工件在回火过程中由于内应力的均匀化、减小甚至消失,加上组织发生变化,变形趋于减小,但同时,一旦出现变形,也是很难矫正的。
为了矫正这种变形,多采用加压回火或喷丸硬化等方法。
七重复淬火与变形
通常情况下,一次淬火后的工件未经过中间退火而进行重复淬火,将增大变形。
图5为重复淬火引起的变形,经过重复淬火,其变形累加而趋于球状,容易产生龟裂,但形状相对稳定了,不再容易产生变形了,因此重复淬火前应增加中间退火,重复淬火次数应小于等于2次(不含首次淬火)。
八残余应力与变形
加热过程中,在450℃左右,钢由弹性体转变为塑性体,因此很容易呈上升塑性变形。
同时,残余应力在约高于此温度时也将因再结晶而消失。
因此,快速加热时,由于工件内外部存在温度差,外部达到450℃变成了塑性区,受而内部温度较低处存在残余应力作用而发生变形,冷却后,该区域就是出现变形的地方。
由于实际生产过程中,很难实现均匀、缓慢加热,淬火前进行消除应力退火是非常重要的,除了通过加热消除应力外,对于大型零件采用振动消除应力也是有效的。