散货船优化算法讲解
基于cfd的散货船船体型线自动优化
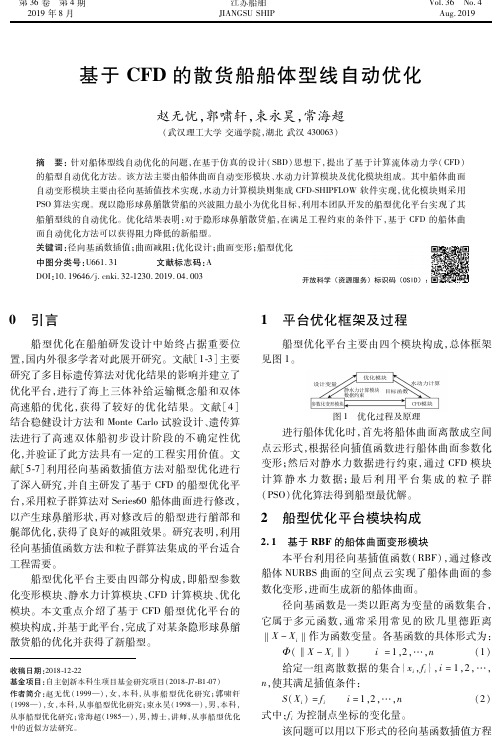
收稿日期:20181222 基金项目:自主创新本科生项目基金研究项目(2018J7B107) 作者简介:赵无忧 (1999—),女,本科,从事 船 型优 化研 究;郭啸 轩 (1998—),女,本科,从事船型优化研究;束永昊(1998—),男,本科, 从事船型优化研究;常海超(1985—),男,博士,讲师,从事船型优化 中的近似方法研究。
∫∫V∫(Px+Qy+Rz)dv=Swe∫t+∫Swl(Pn1 +Qn2 +
Rn3)ds 式中:P、Q、R为变量。
ห้องสมุดไป่ตู้(7)
船体湿表面 Swet与水线 Swl面所围成的部分即为 船体排水体积 V。
静水力数据包括排水体积、浮心纵向位置、湿表
面积等,它们的求法如下。
求解排水体积:P=0,Q=y,R=0
=∫∫V∫(Px+Qy+Rz)dv=Swe∫t+∫Swl(yn2)ds=
0 引言
1 平台优化框架及过程
船型优化在船舶研发设计中始终占据重要位 置,国内外很多学者对此展开研究。文献[13]主要 研究了多目标遗传算法对优化结果的影响并建立了 优化平台,进行了海上三体补给运输概念船和双体 高速船的 优 化,获 得 了 较 好 的 优 化 结 果。 文 献 [4] 结合稳健设计方法和 MonteCarlo试验设计、遗传算 法进行了高速双体船初步设计阶段的不确定性优 化,并验证了此方法具有一定的工程实用价值。文 献[57]利用径向基函数插值方法对船型优化进行 了深入研究,并自主研发了基于 CFD的船型优化平 台,采用粒子群算法对 Series60船体曲面进行修改, 以产生球鼻艏形状,再对修改后的船型进行艏部和 艉部优化,获得了良好的减阻效果。研究表明,利用 径向基插值函数方法和粒子群算法集成的平台适合 工程需要。
双壳散货船分段划分优化
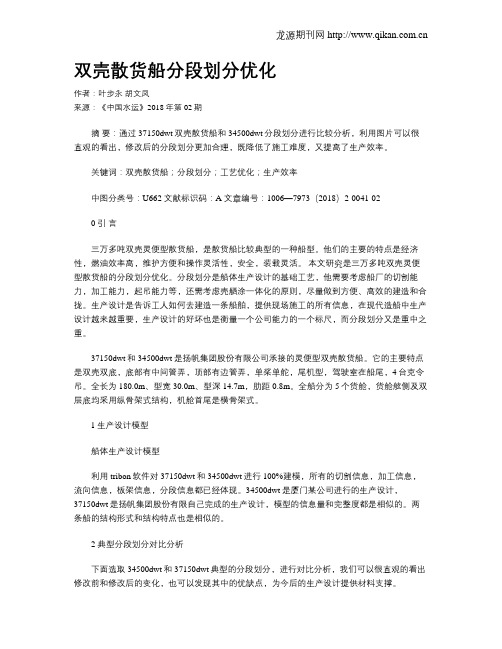
双壳散货船分段划分优化作者:叶步永胡文凤来源:《中国水运》2018年第02期摘要:通过37150dwt双壳散货船和34500dwt分段划分进行比较分析,利用图片可以很直观的看出,修改后的分段划分更加合理,既降低了施工难度,又提高了生产效率。
关键词:双壳散货船;分段划分;工艺优化;生产效率中图分类号:U662 文献标识码:A 文章编号:1006—7973(2018)2-0041-020 引言三万多吨双壳灵便型散货船,是散货船比较典型的一种船型。
他们的主要的特点是经济性,燃油效率高,维护方便和操作灵活性,安全,装载灵活。
本文研究是三万多吨双壳灵便型散货船的分段划分优化。
分段划分是船体生产设计的基础工艺,他需要考虑船厂的切割能力,加工能力,起吊能力等,还需考虑壳舾涂一体化的原则,尽量做到方便、高效的建造和合拢。
生产设计是告诉工人如何去建造一条船舶,提供现场施工的所有信息,在现代造船中生产设计越来越重要,生产设计的好坏也是衡量一个公司能力的一个标尺,而分段划分又是重中之重。
37150dwt和34500dwt是扬帆集团股份有限公司承接的灵便型双壳散货船。
它的主要特点是双壳双底,底部有中间管弄,顶部有边管弄,单桨单舵,尾机型,驾驶室在船尾,4台克令吊。
全长为180.0m、型宽30.0m、型深14.7m,肋距0.8m。
全船分为5个货舱,货舱舷侧及双层底均采用纵骨架式结构,机舱首尾是横骨架式。
1生产设计模型船体生产设计模型利用tribon软件对37150dwt和34500dwt进行100%建模,所有的切割信息,加工信息,流向信息,板架信息,分段信息都已经体现。
34500dwt是厦门某公司进行的生产设计,37150dwt是扬帆集团股份有限自己完成的生产设计,模型的信息量和完整度都是相似的。
两条船的结构形式和结构特点也是相似的。
2 典型分段划分对比分析下面选取34500dwt和37150dwt典型的分段划分,进行对比分析,我们可以很直观的看出修改前和修改后的变化,也可以发现其中的优缺点,为今后的生产设计提供材料支撑。
20500DWT散货船下水方案优化研究
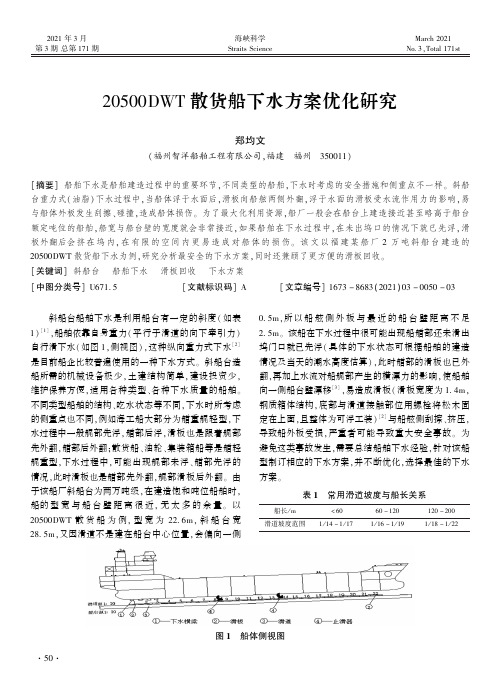
2021年3月第3期总第171期海峡科学Straits ScienceMarch2021No.3,Total171st 20500DWT散货船下水方案优化研究郑均文(福州智洋船舶工程有限公司,福建㊀福州㊀350011)[摘要]船舶下水是船舶建造过程中的重要环节,不同类型的船舶,下水时考虑的安全措施和侧重点不一样㊂斜船台重力式(油脂)下水过程中,当船体浮于水面后,滑板向船舷两侧外翻,浮于水面的滑板受水流作用力的影响,易与船体外板发生刮擦㊁碰撞,造成船体损伤㊂为了最大化利用资源,船厂一般会在船台上建造接近甚至略高于船台额定吨位的船舶,船宽与船台壁的宽度就会非常接近,如果船舶在下水过程中,在未出坞口的情况下就已先浮,滑板外翻后会挤在坞内,在有限的空间内更易造成对船体的损伤㊂该文以福建某船厂2万吨斜船台建造的20500DWT散货船下水为例,研究分析最安全的下水方案,同时还兼顾了更方便的滑板回收㊂[关键词]斜船台㊀船舶下水㊀滑板回收㊀下水方案[中图分类号]U671.5[文献标识码]A[文章编号]1673-8683(2021)03-0050-03㊀㊀斜船台船舶下水是利用船台有一定的斜度(如表1)[1],船舶依靠自身重力(平行于滑道的向下牵引力)自行滑下水(如图1,侧视图),这种纵向重力式下水[2]是目前船企比较普遍使用的一种下水方式㊂斜船台造船所需的机械设备极少,土建结构简单,建设投资少,维护保养方便,适用各种类型㊁各种下水质量的船舶㊂不同类型船舶的结构㊁吃水状态等不同,下水时所考虑的侧重点也不同,例如海工船大部分为艏重艉轻型,下水过程中一般艉部先浮,艏部后浮,滑板也是跟着艉部先外翻,艏部后外翻;散货船㊁油轮㊁集装箱船等是艏轻艉重型,下水过程中,可能出现艉部未浮㊁艏部先浮的情况,此时滑板也是艏部先外翻,艉部滑板后外翻㊂由于该船厂斜船台为两万吨级,在建造饱和吨位船舶时,船的型宽与船台壁距离很近,无太多的余量㊂以20500DWT散货船为例,型宽为22.6m,斜船台宽28.5m,又因滑道不是建在船台中心位置,会偏向一侧0.5m,所以船舷侧外板与最近的船台壁距离不足2.5m㊂该船在下水过程中很可能出现船艏部还未滑出坞门口就已先浮(具体的下水状态可根据船舶的建造情况及当天的潮水高度估算),此时艏部的滑板也已外翻,再加上水流对船艉部产生的横漂力的影响,使船舶向一侧船台壁漂移[3],易造成滑板(滑板宽度为1.4m,钢质箱体结构,底部与滑道接触部位用螺栓将松木固定在上面,且整体为可浮工装)[2]与船舷侧刮擦㊁挤压,导致船外板受损,严重者可能导致重大安全事故㊂为避免这类事故发生,需要总结船舶下水经验,针对该船型制订相应的下水方案,并不断优化,选择最佳的下水方案㊂表1㊀常用滑道坡度与船长关系船长/m<6060~120120~200滑道坡度范围1/14~1/171/16~1/191/18~1/22图1㊀船体侧视图㊃05㊃2021年第3期海峡科学HAI XIA KE XUE1㊀ 散排 下水方案散排 法下水是将下水用的滑板连在一起(滑板串联的数量根据港拖的拖带能力而定),头尾两端分别用高分子聚乙烯绳(俗称防爆缆)固定在甲板缆桩上,船入水全浮后,滑板自然向舷侧外翻㊂待船在江中稳定后,港拖靠近下水船舶,分别将固定滑板的缆绳从船上解开,系到港拖上,再由港拖将滑板拖回坞内㊂等潮水退至最低时将坞门关起,船台吊车辅助回收滑板㊂缆绳的绑扎方案如图2所示㊂图2㊀散排方案(船底部视图)㊀㊀此种方案在船台施工时工程量小,操作工序较简单,人工投入少,船下水后滑板回收也较方便快捷,当天就能回收全部滑板㊂滑板的快速拖离也能为下水船舶靠泊码头争取时间(由于受地理环境影响,船舶下水都在退潮时,如潮水退太低,不利于船只的码头靠泊)㊂但是下水过程中如果整船在未全部滑出坞口时就已全浮或船艏先浮,此时已浮部位下面的滑板就会外翻,再加上水流对船艉部的横漂力作用,很容易造成船舷侧与船台壁刮蹭,导致船体受损㊂2㊀ 整排 下水方案整排 法是将滑板串联在一起,每一串的滑板头尾再用防爆缆分别固定在船的左右舷两侧的缆桩上(滑板的左侧固定在左舷,右侧固定在右舷),阻止滑板在船浮起时外翻㊂待船在江中稳定后,分别依次解开固定滑板的防爆缆,再由港拖将滑板拖回坞内,等待回收㊂缆绳的绑扎方案如图3所示㊂图3㊀整排方案(船底部视图)㊃15㊃HAI XIA KE XUE 海峡科学2021年第3期㊀㊀此种方案的优点是由于滑板不会外翻,所以不管船在哪个位置全浮,都能够保证船舶的下水安全㊂此方案在船台绑扎固定滑板的防爆缆工艺较复杂,如滑板数量多(左㊁右舷滑板各分两串)且多条缆绳共用一个缆桩的话还要注意绑扎顺序㊂船台施工周期较 散排 法长㊂下水后滑板回收较难,因为固定滑板的防爆缆有一半是跨过船底部,滑板拖出时跨船底部分的防爆缆很可能会卡在船底墩位上或与其他防爆缆在水流的作用下相互缠绕,导致滑板不易被拖出㊂如果滑板无法及时拖出,还会影响下水船只靠泊码头和下条船的上船台周期㊂3㊀ 散排 + 整排 下水方案船艉部的部分滑板用 散排 法,艏部剩余的滑板用 整排 法㊂船下水后 散排 部分的滑板可以马上拖出,这种方法可以避免像单一的 整排 法那样,下水后所有滑板积在一起,缆绳又多,易相互缠绕等缺点㊂同时, 散排部分滑板及时拖出也能为 整排 部分滑板的拖带腾出空间和时间㊂缆绳的绑扎方案如图4所示㊂图4㊀ 散排 + 整排 方案(船底部视图)4㊀20500DWT 散货船下水方案的确定根据散货船型的特点及20500DWT 散货船的具体情况分析,采用 散排 + 整排 相结合的方案㊂由于20500DWT 散货船是左右各22片滑板(滑板规格有4m㊁6m㊁8m 长),受港拖的拖带能力限制(一次只能拖10~12片滑板),左右舷滑板各分成2串,每串11片(左㊁右舷滑板各在11~12号处断开),艉部两串滑板用 散排 ,艏部两串滑板用 整排 (如图4)㊂①船艉部由于吃水较深,所以船艉部要滑出坞口后才会艉浮,此时艉部滑板外翻就不会有碰到船台壁的风险㊂船一稳定在江中,由两条港拖同时将艉部滑板先拖回㊂②由于船艏部吃水浅,导致船艏还未滑出坞口就已艏浮,滑板外翻,所以艏部两串滑板用 整排 法,保证下水过程滑板不会与船台壁刮蹭㊂因为只有两串滑板用 整排 法,所以需要跨船底固定的防爆缆较少,缆绳不易被卡住㊂又因艉部滑板已拖出,为艏部滑板腾出了较大的操作空间,所以 整排 部分滑板拖出也较容易㊂5㊀结论20500DWT 散货船及其系列船采用 散排 + 整排 的下水方案,均顺利下水,且滑板回收过程也方便快捷,证明该方案可行㊂该方案的成功应用也可为类似的受水域条件限制的中小型斜船台建造饱和型吨位船时(油轮㊁集装箱船㊁客滚船等)提供一些参考,具体可根据船舶的下水状态及潮水因素等,适当调整滑板 散排 及 整排 数量的比例㊂参考文献:[1]江南造船厂.船舶纵向滑行下水工艺:CB /Z51-1981.[2]黄浩.船体工艺手册(修订本)[M ].北京:国防工业出版社,1989.[3]施功时.关于船舶纵向下水时艉部横漂的分析[J ].造船技术,1986(6):19-24.㊃25㊃。
船装总体优化方案
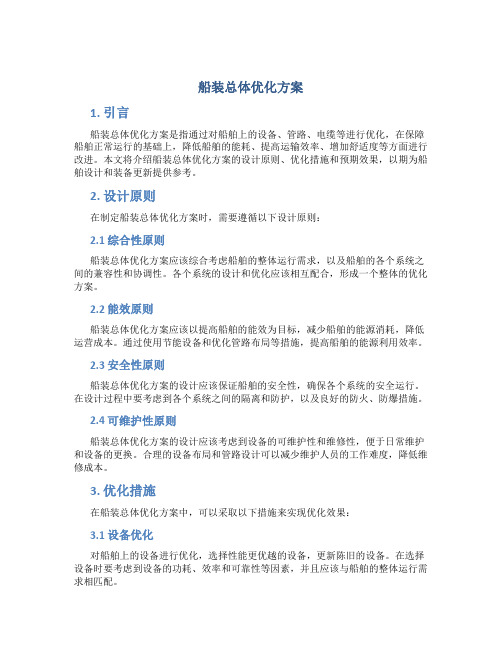
船装总体优化方案1. 引言船装总体优化方案是指通过对船舶上的设备、管路、电缆等进行优化,在保障船舶正常运行的基础上,降低船舶的能耗、提高运输效率、增加舒适度等方面进行改进。
本文将介绍船装总体优化方案的设计原则、优化措施和预期效果,以期为船舶设计和装备更新提供参考。
2. 设计原则在制定船装总体优化方案时,需要遵循以下设计原则:2.1 综合性原则船装总体优化方案应该综合考虑船舶的整体运行需求,以及船舶的各个系统之间的兼容性和协调性。
各个系统的设计和优化应该相互配合,形成一个整体的优化方案。
2.2 能效原则船装总体优化方案应该以提高船舶的能效为目标,减少船舶的能源消耗,降低运营成本。
通过使用节能设备和优化管路布局等措施,提高船舶的能源利用效率。
2.3 安全性原则船装总体优化方案的设计应该保证船舶的安全性,确保各个系统的安全运行。
在设计过程中要考虑到各个系统之间的隔离和防护,以及良好的防火、防爆措施。
2.4 可维护性原则船装总体优化方案的设计应该考虑到设备的可维护性和维修性,便于日常维护和设备的更换。
合理的设备布局和管路设计可以减少维护人员的工作难度,降低维修成本。
3. 优化措施在船装总体优化方案中,可以采取以下措施来实现优化效果:3.1 设备优化对船舶上的设备进行优化,选择性能更优越的设备,更新陈旧的设备。
在选择设备时要考虑到设备的功耗、效率和可靠性等因素,并且应该与船舶的整体运行需求相匹配。
3.2 管路优化对船舶上的管路进行优化,合理布局管道,减少管道的长度和阻力,提高流体传输效率。
同时,选择合适的管道材质和规格,降低压力损失和泄漏风险。
3.3 电气系统优化对船舶的电气系统进行优化,采用节能设备和控制系统,减少能源消耗。
同时,合理布置电缆和开关设备,提高电路的可靠性和安全性。
3.4 舒适度优化考虑到船员的工作和生活环境,对船舶的舒适度进行优化。
例如,在船舶的船舱和公共区域设置合适的空调系统和通风系统,提供舒适的工作和居住环境。
某大型散货船分舱优化的实现方法
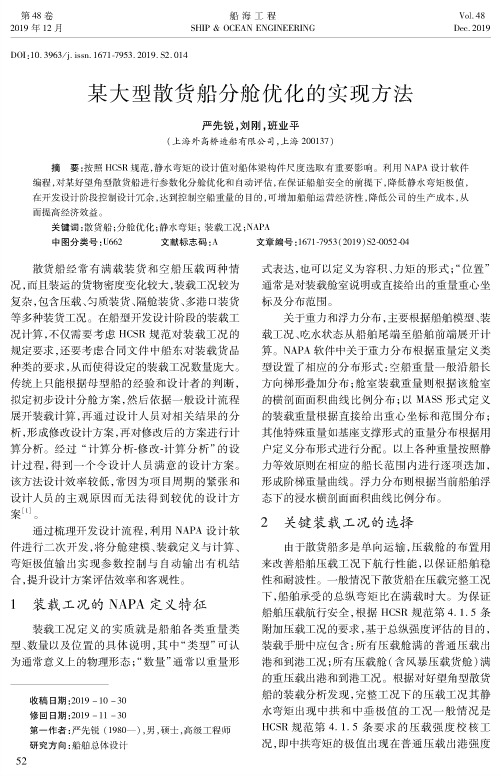
第48卷2019年12月船海工程SHIP&OCEAN ENGINEERIGVol.48Dec.2019DOI:10.3963/j.issn.1671-7953.2019.S2.014某大型散货船分舱优化的实现方法严先锐,刘刚,班业平(上海外高桥造船有限公司,上海200137)摘要:按照HCSR规范,静水弯矩的设计值对船体梁构件尺度选取有重要影响。
利用NAPA设计软件编程,对某好望角型散货船进行参数化分舱优化和自动评估,在保证船舶安全的前提下,降低静水弯矩极值,在开发设计阶段控制设计冗余,达到控制空船重量的目的,可增加船舶运营经济性,降低公司的生产成本,从而提高经济效益$关键词:散货船;分舱优化;静水弯矩;装载工况;NAPA中图分类号:U662文献标志码:A文章编号:1671-7953(2019)S2-0052-04散货船经常有满载装货和空船压载两种情况,而且装运的货物密度变化较大,装载工况较为复杂,包含压载、匀质装货、隔舱装货、多港口装货等多种装货工况。
在船型开发设计阶段的装载工况计算,不仅需要考虑HCSR规范对装载工况的规定要求,还要考虑合同文件中船东对装载货品种类的要求,从而使得设定的装载工况数量庞大。
传统上只能根据母型船的经验和设计者的判断,拟定初步设计分舱方案,然后依据一般设计流程展开装载计算,再通过设计人员对相关结果的分析,形成修改设计方案,再对修改后的方案进行计算分析。
经过“计算分析-修改-计算分析”的设计过程,得到一个令设计人员满意的设计方案。
该方法设计效率较低,常因为项目周期的紧张和设计人员的主观原因而无法得到较优的设计方案⑴o通过梳理开发设计流程,利用NAPA设计软件进行二次开发,将分舱建模、装载定义与计算、弯矩极值输出实现参数控制与自动输出有机结合,提升设计方案评估效率和客观性。
1装载工况的NAPA定义特征装载工况定义的实质就是船舶各类重量类型、数量以及位置的具体说明,其中“类型”可认为通常意义上的物理形态;“数量”通常以重量形收稿日期:2019-10-30修回日期:2019-11-30第一作者:严先锐(1980—),男,硕士,高级工程师研究方向:船舶总体设计式表达,也可以定义为容积、力矩的形式;“位置”通常是对装载舱室说明或直接给出的重量重心坐标及分布范围。
散货船的结构设计特点及施工优化

散货船的结构设计特点及施工优化摘要:散货船是当今世界的三大主流船型之一,且呈现出超大型化的趋势。
散货船共同规范CSR于2006年4月1日作为IACS的统一规范生效,它系统、全面、详细的规定了散货船的结构设计标准。
根据设计经验,文章对散货船结构设计中几个应该注意的问题进行了阐述,同时指出了详细设计中结构设计部分对造船过程中施工工艺考虑不足的现象存在,而这一现象最终造成了船厂在建造过程中存在施工难度大、工艺复杂、焊接量大、变形难以控制、精度不高等问题。
最后文章提出了几种合理改变结构形式的优化方案,来简化船舶建造工艺,降低施工难度和成本,保证精度。
关键词:详细设计;结构特点;结构优化;精度控制全世界每年约有20多亿t的干散货投入到海运市场,占全世界海运量的1/3,散货船作为三大船型之一,其安全性、经济性、环保性是业界关注的焦点。
散货船的结构设计是其安全运营的重要保障,结构设计的是否合理,结构形式是否优化又影响其经济性。
目前国内现状是多数船厂不具备前期的方案设计、详细设计、送审设计的能力,一般都是委托有资质的专业设计院进行前期的详细设计。
而详细设计中的结构设计部分往往是从满足规范要求、满足强度要求来考虑,结构形式往往是参照母型船,对造船过程中的施工工艺考虑往往不够,这样就造成了船厂在建造过程中的施工难度大、工艺复杂、焊接量大、变形难以控制、精度不高。
具备生产设计能力的船厂就需要从船厂的施工角度出发,对于详细设计中工艺性不强的部分进行结构优化,既要满足强度要求,又能大大方便现场施工,降低施工难度,保证精度,同时也降低造船成本。
1 散货船结构设计特点目前投入世界航运市场的散货船多数为典型的单壳结构。
其货舱横剖面如图1所示。
1.1 货舱双层底结构双层底一般采用纵骨架式,设有纵桁、纵骨、横向肋板。
中桁材在货舱区应保持延伸,从船首至船尾应尽可能保持延伸,其结构连续性应在船舶的全厂范围内连续。
旁桁材在货舱区与的平行总体范围内应保持延续,在货舱区与的首端只尾端应尽可能保持延伸。
好望角CAPESIZE散货船优化设计报告
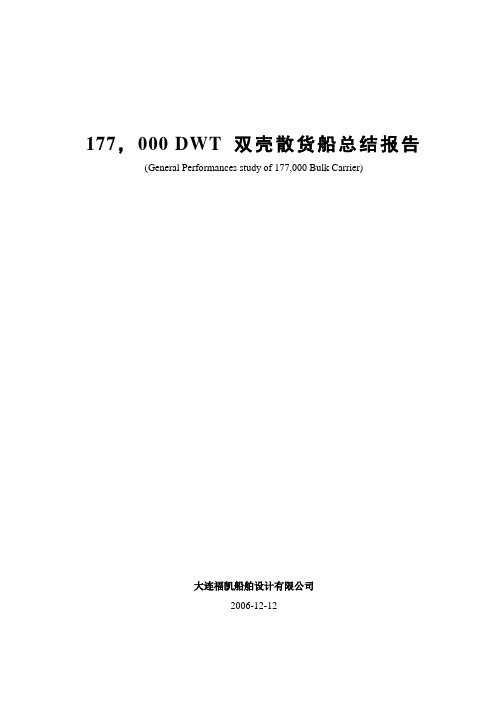
177,000 DWT 双壳散货船总结报告(General Performances study of 177,000 Bulk Carrier)大连福凯船舶设计有限公司2006-12-12摘要:本总结报告根据2006年颁布实施的共同结构规范CSR(Common Structure Rules)要求,对177,000DWT双壳散货船进行开发研究,历时一年多圆满完成各项开发研究工作。
经过母型船分析及设计要素后,优化确定了本船的主尺度。
主要工作包括空船重量、重心位置估算,舱容、航速等计算, 皆满足设计的要求。
并根据最新的共同规范CSR及最新的结构计算软件进行结构的计算和优化。
通过型线设计与优化,得到降低阻力, 提高性能的较佳型线。
该项主要工作是基于母型船线型为基础,然后通过船模试验进行线型优化研究。
根据规范对本船的稳性进行计算, 主要内容包括:静水力计算、舱容计算、干舷计算、完整稳性、谷物稳性及破舱稳性计算。
结构设计以CSR 要求进行计算,并满足永久检测通道的要求,减少检测通道的栏杆, 对本船结构进行修改。
对结构进行三舱段的有限元分析,此类分析在船舶领域属于使用新技术在船舶上面的应用,让船舶结构的应力分析更加准确。
同时在结构计算方面,使用最新的计算软件,且考虑了疲劳和腐蚀因素的影响。
关键词:双壳散货船;总体性能一,开发研究的目的和要求1,在国际共同结构规范CSR (Common Structure Rules) 的生效,所有船长大于150m以上散货船均需要满足此规范,尤其对船体结构要有较大变化,为适应市场需要,在国际市场上占据有利的竞争优势,本公司对174,000DWT好望角型双壳散货船(简称母型船)在深受船东青睐的基础上,开发研究出177,000DWT双壳散货船。
本船在总体性能、线型、船体结构布置和设计等方面皆保证最新规范要求,且满足进入法国敦刻尔克东港的条件。
当前,在国内外此类船型较少的情况下,在开拓国际市场既有一定的竞争力和先进水平。
基于支持向量机的船舶结构优化方法

基于支持向量机的船舶结构优化方法随着船舶的高速发展,对船舶结构的安全性和性能要求也越来越高。
因此,在设计船舶结构时,非常重要的任务是优化船体结构,以获得最佳的结构性能。
支持向量机是一种强大的机器学习算法,可以在最小化结构权重的前提下实现复杂的船体结构优化。
在使用支持向量机(SVM)进行船体结构优化时,首先需要定义目标函数和约束条件。
目标函数可以是船体的稳定性、载荷和阻力等方面,约束条件可以是最小或最大质量、最小或最大刚度和强度等方面。
一旦定义了目标函数和约束条件,就可以通过SVM来确定最佳解。
SVM使用非线性算法将数据映射到高维空间,从而实现分类、回归和优化等任务。
在船体结构优化中,SVM通常是通过尝试许多不同的权重来获得最佳解。
这种优化方法使用一定的权重范围,通过改变权重来获得最佳目标函数值。
这种方法可以在不同的船型、船长和宽度等不同的设计变量下进行优化。
为了有效地使用SVM进行船体结构优化,需要遵循以下步骤:1. 组织数据和定义目标函数与约束条件:收集现有船舶的相关数据,并定义目标函数和约束条件。
2. 运行SVM:使用SVM确定最佳的结构参数和权重,以使目标函数达到最优化。
3. 模型评估:评估所得到的结构参数和权重,与理论及实际工艺进行比较和分析。
该方法的优点包括:1. 精度高:由于SVM被广泛应用于各行各业,它的预测性能非常好,因此在船体结构优化中使用SVM可以提高优化的精度。
2. 可扩展性强:SVM可以根据不同的船型和船长进行调整,并且可以扩展到其他方面的优化。
3. 支持多目标优化:SVM还支持多目标优化,可以将目标函数分为不同的优化目标,分别执行。
总之,基于支持向量机的船体结构优化方法可以帮助设计者获得最佳的船体结构参数和权重,以提高船舶的安全性和性能。
这种方法可以在船舶的不同设计变量下使用,并具有高精度和可扩展性强的优点。
在使用基于支持向量机的船舶结构优化方法之前,需要收集一些相关数据,并对其进行分析。
解析船舶结构优化设计的方法

解析船舶结构优化设计的方法摘要:船舶结构设计对船舶的应用性有着很大的意义。
船舶结构设计的优化方法主要有经典优化设计的数学规划法、多目标模糊优化设计法、基于可靠性的优化设计法、智能型优化设计法等。
在进行具体的船舶结构优化设计时,必须要与实际工程的特点相符合,同时结合计算机技术、现代数学理论等。
本文主要介绍了船舶结构优化设计的几种方法,及其在实现船舶结构的优化、实现船舶的性能最大化中的优缺点。
中国论文网http://www.xzbu关健词:船舶结构;优化;设计方法在船舶结构直接计算中,外载荷(包括波浪压力、砰击载荷、货物压力、晃荡载荷、波浪弯矩、剪力和扭矩等)[1]的计算都依赖于经验公式,不管是采用全船的计算模型还是采用舱段的计算模型,目前情况下很难得到一个完全平衡的外载荷力系。
由于船舶结构是一个复杂的空间结构,直接计算时,有限元模型中节点数、单元数十分庞大,载荷计算的累计误差使得寻求一个完全平衡的外载荷力系的工作更加困难。
在这种情况下,施加合理、合适的边界条件变得十分重要,因为约束点产生的很大的反力严重地影响(改变)了结构的实际受力状态。
边界条件对于计算的结果有重大的影响,而边界条件的确定取决于对结构受力和变形状态的判断以及分析者的经验,其中人为的因素较多。
也许可以认为根据StVenant 原理,由于约束点距离我们最关心的部位较远,对应力分布的计算结果的影响有限,但是这样得到的结果毕竟是不甚合理的。
因此用有限元方法计算船舶结构强度时,为了得到比较准确的变形和应力结果,可能需要特殊的处理方法。
目前的研究中有采用惯性释放的方法[2],此方法用结构的惯性力来平衡外力,由于人为的施加外载荷,虽然在大多数情况下,都经过了节点力的调整,但作用在船体的力系仍然不是平衡力系,根据达朗贝尔原理,利用惯性力使整个力系达到平衡。
也有研究整船有限元模型自动加载技术的[3],这些研究都需要经过节点力的调整和惯性平衡力计算的多次叠代,对船舶要进行浮态调整,实现起来,比较繁琐。
数学建模的船队运输最优化问题
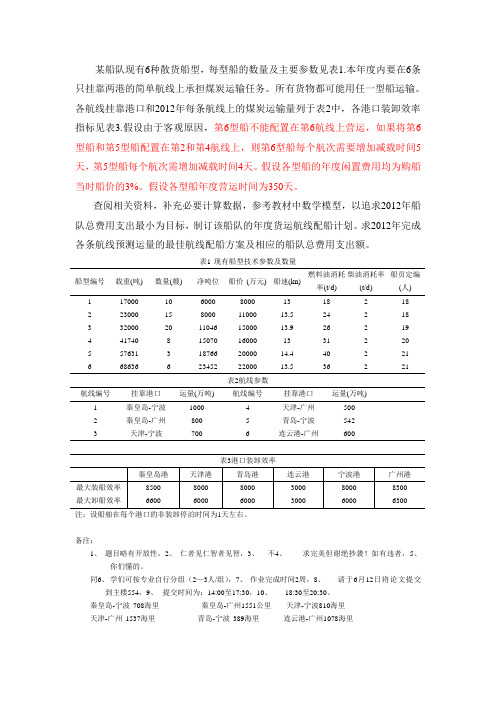
天,第5型船每个航次需增加减载时间4天。假设各型船的年度闲置费用均为购船
当时船价的3%。假设各型船年度营运时间为350天。
查阅相关资料,补充必要计算数据,参考教材中数学模型,以追求2012年船
队总费用支出最小为目标,制订该船队的年度货运航线配船计划。求2012年完成
各条航线预测运量的最佳航线配船方案及相应的船队总费用支出额。
现有船型技术参数及数量船型编号载重吨数量艘净吨位万元船速kn燃料油消耗170001060008000131823000158000110001352432000201104615000139261507016000133118766200001444023452220001353621表2航线参数航线编号挂靠港口运量万吨航线编号挂靠港口运量万吨秦皇岛宁波1000天津广州500秦皇岛广州800青岛宁波542天津宁波700连云港广州600表3港口装卸效率秦皇岛港天津港青岛港连云港宁波港广州港最大装船效率850080008000300080008300最大卸船效率660060006000300060006300注
a62 A62 a63 A63 a64 A64
a65 A65
a66 A66
小写字母代表船数 大写代表船次
各种船往返一次所用的时间
D=2+M/p+M/q+2S/V/24 M:载重量 p:装货率 q:卸货率
S:航线长度 V:船速 2:港口为停靠时间 24:一天 24 小时
1
2
3
4
5
6
秦皇岛-宁 波
11.372
船型编号 载重(吨) 数量(艘)
表1 现有船型技术参数及数量
燃料油消耗 柴油消耗率 船员定编
净吨位 船价 (万元) 船速(kn)
某82000dwt散货船建造技术优化
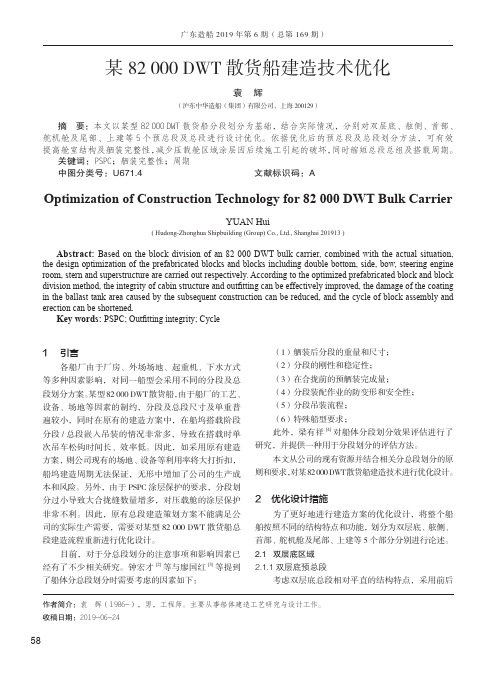
58作者简介:袁 辉(1986-),男,工程师。
主要从事船体建造工艺研究与设计工作。
收稿日期:2019-06-24某82 000 DWT 散货船建造技术优化袁 辉(沪东中华造船(集团)有限公司,上海 200129)摘 要:本文以某型82000DWT 散货船分段划分为基础,结合实际情况,分别对双层底、舷侧、首部、舵机舱及尾部、上建等5个预总段及总段进行设计优化。
依据优化后的预总段及总段划分方法,可有效提高舱室结构及舾装完整性,减少压载舱区域涂层因后续施工引起的破坏,同时缩短总段总组及搭载周期。
关键词:PSPC;舾装完整性;周期中图分类号:U671.4 文献标识码:AOptimization of Construction Technology for 82 000 DWT Bulk CarrierYUAN Hui( Hudong-Zhonghua Shipbuilding (Group) Co., Ltd., Shanghai 201913 )Abstract: Based on the block division of an 82 000 DWT bulk carrier, combined with the actual situation, the design optimization of the prefabricated blocks and blocks including double bottom, side, bow, steering engine room, stern and superstructure are carried out respectively. According to the optimized prefabricated block and block division method, the integrity of cabin structure and outfitting can be effectively improved, the damage of the coating in the ballast tank area caused by the subsequent construction can be reduced, and the cycle of block assembly and erection can be shortened.Key words: PSPC; Outfitting integrity; Cycle1 引言各船厂由于厂房、外场场地、起重机、下水方式等多种因素影响,对同一船型会采用不同的分段及总段划分方案。
基于蚁群算法的长江干散货船中部结构优化设计
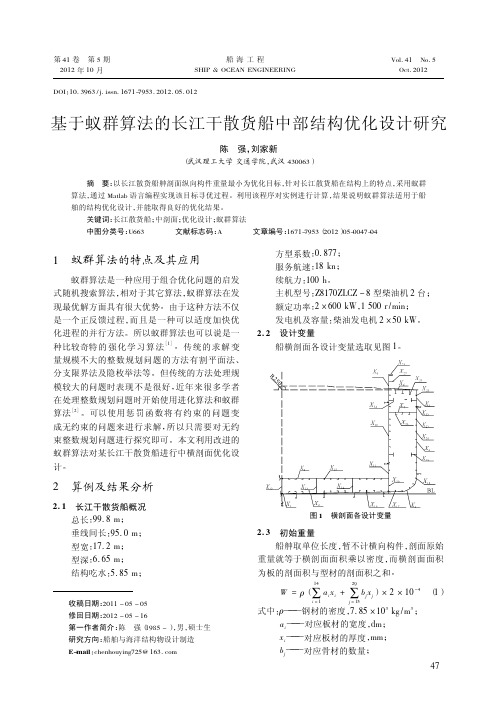
( 8)
的建立根据 CCS《钢质内河船
( 2009 ) A、 B 级航区有关双壳船的 舶建造规范 》 要求确定如下。 2. 4. 1 几何约束条件 1 ) 平板龙骨厚度 x1 应按船中部底板厚度 x2 增加 1 mm; x1 ≥x2 + 1 即 g( X ) 1 = x1 - x2 - 1 ≥0 2 ) 舭列板厚度 x3 应按船中部船底板厚度 x2 增加 0. 5 mm; x3 ≥x2 + 0 . 5 ( 3) 即 g( X ) 2 = x3 - x2 - 0 . 5 ≥0 2. 4. 2 舯横剖面剖面模数和惯性矩约束条件 舯剖面的剖面模数 W 为 W≥KW0
2 算得 10 172. 77 cm ·m;
— —计算剖面的波浪附加弯矩; 式中: M w — | M s + M w | 经计算得 143 826. 663 kN·m。 Wv ≥143 826. 663 ˑ 10 /157 = 9 160. 93 cm2 ·m 此约束包含在 g( X ) 3 及 g( X ) 4 中。 3 ) 各计算工况船体梁剖面中和轴处舷侧外 板及纵舱壁的剪切应力值, 静水计算工况应不大 2 2 于 80 N / mm , 航行计算工况应不大于 91 N / mm 。 各计算工况船体梁剖面中和轴处舷侧外板及 纵舱壁的剪切应力 τ 应按下式计算。 τ i = 0 . 1 K i β i | F ext | S / I / ∑ t ( 9) — —各计算工况的静水剪力极值、 式中: F ext — 航行计 算工况的静水剪力与波浪附加剪力 kN, 叠加的极值, 航行计算工况下和 所有计算工况下的 | F ext | 经计算分别 为 5 027. 699 及 7 123. 587 kN; I— — —剪力极值处船体梁剖面惯性矩, cm2 ·m2 ; S— — —计算剖面位于中和轴以上或以下部分等 cm2 ·m2 ; 值梁横剖面积对中和轴的静矩, — —计算剖 面 中 和 轴 处 舷 侧 外 板 和 纵 ∑t — cm; 舱壁厚度之和, Ki 、 — —舷侧 外 板、 βi — 纵舱壁剪应力修正系 数, 根据剖面型式 K0 、 β0 及 K1 、 β1 0 . 84 、 1 . 00 1 . 20 、 1 . 00 ; 分别为 及 即 g( X ) 6 = 80 IX4 + 80 IX10 - 8 548 . 30S≥0 g( X ) = 80 IX4 + 80 IX10 - 5 983 . 81S ≥0 , 此约 束包含在 g( X ) 6 中; g( X ) = 91 IX4 + 91 IX10 - 6 033 . 24S ≥0 , 此约 束包含在 g( X ) 6 中。 2. 4. 4 船体板屈曲强度约束条件 应不小于其所 甲板或船底板的临界应力 σ cr , 承受的最大总纵弯曲应力。 纵骨架式甲板或船底板格的弹性屈曲应力 σ e 按下式计算。 σ e = 76 ( 100 t / b)
35 000 DWT散货船总体性能优化

35 000 DWT散货船总体性能优化凌乃俊;殷晓俊;张志强;袁野【摘要】通过理论分析、CFD仿真模拟、船模试验三种方法对35 000 DWT散货船进行了型线优化、主机选型及功率点优化.船舶型线优化后阻力明显减少,推进效率显著提高,油耗和EEDI指数大幅降低.【期刊名称】《上海船舶运输科学研究所学报》【年(卷),期】2014(037)001【总页数】7页(P25-30,34)【关键词】型线优化;主机选型;功率点优化【作者】凌乃俊;殷晓俊;张志强;袁野【作者单位】中远船务工程集团有限公司,辽宁大连116600;航运技术与安全国家重点实验室,上海200135;中远船务工程集团有限公司,辽宁大连116600;中远船务工程集团有限公司,辽宁大连116600【正文语种】中文【中图分类】U674.113.10 引言纵观整个航运市场和造船市场,国际油价的快速上涨促使船舶燃油费用日益增加,而航运业的持续低迷又进一步导致新造船价格和二手船价格大幅下滑,航运市场和造船市场的利润空间被大幅压缩。
与此同时,能效设计指数规范(EnergyEfficiency Design Index,EEDI)已于2013-01-01正式生效。
对现有船型进行持续地改进和优化,降低EEDI指数,减少船舶能耗已经迫在眉睫,刻不容缓。
中远船务曾与国外船东签订了2艘35 000 DWT散货船的设计、建造合同,模型试验已顺利完成,航速指标满足合同的要求。
但在新形势下,船东的关注点已经从传统的舱容、载重量开始转向油耗、EEDI指标等要素,为了顺应这一趋势,保持中远船务的市场竞争力,对35 000 DWT散货船进行了优化设计,并再次进行了模型试验。
35 000 DWT散货船的优化设计取得了成功,成为目前市场上同类船型中性能优良的产品,获得船东的高度认可和好评,凭借35 000 DWT散货船的优越性能,中远船务在船市低谷期不断发力,陆续获得了该型船的订单。
万吨级江海直达肥大型散货船线型优化设计

阻力产生的原冈是由于粘性作用和船体后部的减 速运动。使边界层发生分离现象的结果。船体后 部的减速流动情况主要由船舶的后体形状决定。 如果船舶后体的去流段较细长,则沿曲面的流速 变化较缓慢,纵向正压力梯度较小,分离现象可以 推迟,甚至避免,因而粘压阻力可以减小L1]。因而 肥大船型的线型设计有如下基本要求。
结论1万t级江海直达浅吃水肥大型散货船型首尾鳍高开档大的型船7阻力和推进效率伽均高于型船3这些型船的首型差别很小通过尾部线型的不断优化达到了很优秀的水平作为万吨级的散货船其海军常数c479等性能指标已达到优秀的万吨级单桨散货船的水平
第38卷第6期 2009年12月
船海丁程 SHIP&OCEAN ENGINEERING
)8 d、 ̄7I 『l
、
\ \。 \ 、、
…\
)6dWL
\二 才 —、 七
/
f| 扣 r。 }. )4 dWL
l
1/A
‘厂1
100
… {\ | f f f‘一,
)2 dWl.
』
,
∑ 心 \ 么 )I dWL l、7、 \ 、
‘
,
、 ~L 一, {,
3t-
BL
\迨
~≥
!/4Biblioteka Ⅳ 、Ⅲ ⅦⅥ V n m Ⅱl
关键词:球鼻首;双尾鳍;粘压阻力;破波阻力
中图分类号:U674.13
文献标志码:A
文章编号:1671—7953(2009)06—0001—05
江海直达船型为浅吃水肥大船型,常年航行 于江海直达航线,其对船舶的操纵性、稳性和快速 性有较高的要求。目前比较优秀的江海直达船 舶,普遍采用球鼻首型,尾型则有单尾、双尾、双尾 鳍等多种形式。主要根据航行区域水深、港口装 卸条件及船舶吨位大小来确定单机或双机推进。 多年来的研究表明,单机推进的单尾船型较双机 推进的双尾、双尾鳍船型具有更优秀的阻力及推 进性能,因此吨位较大进江航行只到马钢的散货 船,由于航行区域水深条件较好(吃水>9.0 m)、 港口装卸条件较好,通常采用单机推进的单尾船 型;而到武钢的散货船由于航行区域水深及港口 装卸条件受限(吃水<6.0 m)往往采用双机推进 的双尾、双尾鳍船型。这种船型由于吃水受限,往 往吨位在万吨级左右。如何提高双机推进的双 尾、双尾鳍船型的快速性能,直接影响到船舶的经 济性及企业的经济效益。
降低总纵弯矩的散货船分舱优化设计技术研究报告
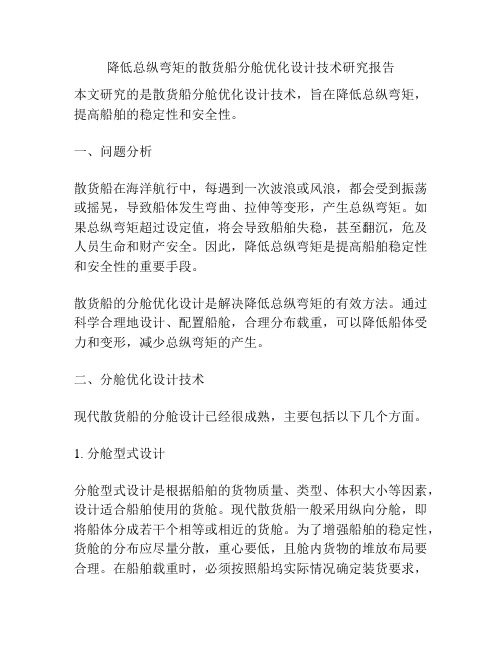
降低总纵弯矩的散货船分舱优化设计技术研究报告本文研究的是散货船分舱优化设计技术,旨在降低总纵弯矩,提高船舶的稳定性和安全性。
一、问题分析散货船在海洋航行中,每遇到一次波浪或风浪,都会受到振荡或摇晃,导致船体发生弯曲、拉伸等变形,产生总纵弯矩。
如果总纵弯矩超过设定值,将会导致船舶失稳,甚至翻沉,危及人员生命和财产安全。
因此,降低总纵弯矩是提高船舶稳定性和安全性的重要手段。
散货船的分舱优化设计是解决降低总纵弯矩的有效方法。
通过科学合理地设计、配置船舱,合理分布载重,可以降低船体受力和变形,减少总纵弯矩的产生。
二、分舱优化设计技术现代散货船的分舱设计已经很成熟,主要包括以下几个方面。
1. 分舱型式设计分舱型式设计是根据船舶的货物质量、类型、体积大小等因素,设计适合船舶使用的货舱。
现代散货船一般采用纵向分舱,即将船体分成若干个相等或相近的货舱。
为了增强船舶的稳定性,货舱的分布应尽量分散,重心要低,且舱内货物的堆放布局要合理。
在船舶载重时,必须按照船坞实际情况确定装货要求,保证货物分配均衡。
2. 舱板设计在分舱型式设计的基础上,还需要对舱板进行设计。
舱板的设计不仅要考虑其强度和承载能力,还要考虑其粘合性和防水性,以避免货物受潮和波浪侵入货舱。
3. 舱底设计舱底设计是为了满足散货船在海洋航行中所遇到的各种复杂海况。
它需要满足良好的强度、刚度、承载力和防波性能等要求。
为了保证船舶的安全性,船底上应设有适当数量和位置的防波碍和刮板,以增强防护能力,从而减少纵向弯曲和拉伸。
4. 均载原则均载原则是指:将货物等分布在船舶的分舱中,尽量使每个货舱的载重均衡。
在航行中,减小总纵弯矩的方法之一是使货物载荷分布均匀地施加到船的前、中、后三个部分,使得纵向重心位置比较靠后,这样可以减小船体受力的不平衡,从而降低总纵弯矩。
三、结论散货船分舱优化设计技术是有效降低总纵弯矩、提高船舶稳定性和安全性的重要手段。
在散货船的分舱设计中,需要考虑分舱型式、舱板、舱底和均载原则等因素。
基于CFD的散货船船体型线自动优化
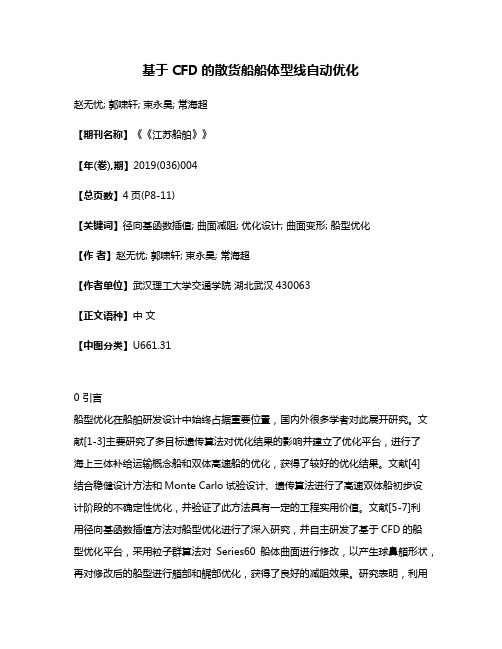
基于CFD的散货船船体型线自动优化赵无忧; 郭啸轩; 束永昊; 常海超【期刊名称】《《江苏船舶》》【年(卷),期】2019(036)004【总页数】4页(P8-11)【关键词】径向基函数插值; 曲面减阻; 优化设计; 曲面变形; 船型优化【作者】赵无忧; 郭啸轩; 束永昊; 常海超【作者单位】武汉理工大学交通学院湖北武汉430063【正文语种】中文【中图分类】U661.310 引言船型优化在船舶研发设计中始终占据重要位置,国内外很多学者对此展开研究。
文献[1-3]主要研究了多目标遗传算法对优化结果的影响并建立了优化平台,进行了海上三体补给运输概念船和双体高速船的优化,获得了较好的优化结果。
文献[4]结合稳健设计方法和Monte Carlo试验设计、遗传算法进行了高速双体船初步设计阶段的不确定性优化,并验证了此方法具有一定的工程实用价值。
文献[5-7]利用径向基函数插值方法对船型优化进行了深入研究,并自主研发了基于CFD的船型优化平台,采用粒子群算法对Series60 船体曲面进行修改,以产生球鼻艏形状,再对修改后的船型进行艏部和艉部优化,获得了良好的减阻效果。
研究表明,利用径向基插值函数方法和粒子群算法集成的平台适合工程需要。
船型优化平台主要由四部分构成,即船型参数化变形模块、静水力计算模块、CFD 计算模块、优化模块。
本文重点介绍了基于CFD船型优化平台的模块构成,并基于此平台,完成了对某条隐形球鼻艏散货船的优化并获得了新船型。
1 平台优化框架及过程船型优化平台主要由四个模块构成,总体框架见图1。
图1 优化过程及原理进行船体优化时,首先将船体曲面离散成空间点云形式,根据径向插值函数进行船体曲面参数化变形;然后对静水力数据进行约束,通过CFD模块计算静水力数据;最后利用平台集成的粒子群(PSO)优化算法得到船型最优解。
2 船型优化平台模块构成2.1 基于RBF的船体曲面变形模块本平台利用径向基插值函数(RBF),通过修改船体NURBS曲面的空间点云实现了船体曲面的参数化变形,进而生成新的船体曲面。
海运物流船舶装载优化方案

海运物流船舶装载优化方案海运物流船舶装载优化方案海运物流是一种非常重要的国际贸易方式,它利用船舶将货物从一个国家运往另一个国家。
然而,船舶的装载过程往往是一个复杂的问题,需要合理安排货物的摆放和分配,以便最大化船舶的装载量。
在本文中,我将提出一些海运物流船舶装载优化方案,以帮助物流企业和船运公司更好地管理和优化船舶的装载过程。
一、货物分类和尺寸测量在装载货物之前,需要对货物进行分类和尺寸测量,以便更好地安排它们的摆放和分配。
货物分类可以按照种类、重量、形状和灵活性等因素进行划分。
货物尺寸测量可以使用激光扫描仪或其他测量工具。
这些数据将有助于确定船舶的最大装载量和货物的最佳摆放方式。
二、舱口、舱间、船壳、船首和船尾的适当分配在船舶装载的过程中,需要将货物适当地分配到舱口、舱间、船壳、船首和船尾等位置。
舱口和舱间通常用于装载大型货物或货物数量较多的集装箱。
船壳和船首用于装载较重的货物,而船尾用于装载较轻的货物。
根据货物的种类和尺寸,对这些位置进行适当的分配,可以最大化船舶的装载量,并确保船舶装载的平衡性和稳定性。
三、货物的紧密堆放在船舶装载的过程中,货物需要紧密堆放,以尽可能地节省空间。
对于一些灵活的货物,可以将它们折叠或叠放起来,以便更好地利用船舶的空间。
对于较大的货物,可以采用固定的支架或绳索,以确保它们的安全性和稳定性。
同时,货物的堆放需要考虑到货物之间的间隙和间隔,以便在需要时方便操作和检查货物。
四、货物的装卸顺序和流程货物的装卸顺序和流程是一个关键的问题,直接影响到船舶的装载效率和货物的安全性。
在装载货物之前,需要制定一份详细的装卸计划,包括货物的数量、种类、尺寸、装卸位置和流程。
在装卸货物的过程中,需要严格按照计划进行,确保货物的顺序和流程合理和稳定。
同时,需要对装卸工人进行培训和管理,以确保他们具备必要的技能和经验,确保货物的安全性和稳定性。
五、船舶的空间利用和容积优化船舶的空间利用和容积优化是一个重要的问题,直接影响到船舶的装载效率和成本。
散货船货舱轮次装载量的优化方法_田佰军

Fx = w ′1 x +w 2 x -ρbx ·[ d -d′+ Δd]
(3)
式中 :w′1 x = w 1 x -ρS x ;Δd = α(x -x f ).
根据材料力学直梁弯曲理论 , 在船体任一剖
面 x 处的剪力 F N x 和弯矩 M x 为
∫x
FNx = Fxdx 0
水深的限制 , 因此要求船舶吃水应满足
d min ≤ d ≤ dmax
即 dmin
Lbp (w ′1 x +w 2 x )d x
∫ ≤ 0
Lbp ρbx d x
∫0
≤ d max
(9)
综上所述 , 在货物装载总量一定时 , 求有约
束条件的船舶静水剪力极小值可归纳为 :
求变量 m i (i = 1 , 2 , 3 , …, n), 使目 标函数
2 0 大 连 海 事 大 学 学 报 第 30 卷
可变重量 ;f x 为单位长度浮力 .固体散货船实际 营运中的装载状态多在压载和满载之间 , 因此其 邦容曲线 , 即船舶浸水横剖面面积曲线的变化近 似直线关系 , 对这一段曲线可采用直壁假设 .对船 舶在不同装载状态下的浸水横剖面面积可作如下 处理 :以横剖面上 z = d′处作为分割线 , 将单位 长度的浮力分为两部分 , 如图 2 所示 , 在吃水 d′
i
≤p
mim1 = p ×S
式中 :S 为 固 体 散 货 在 货 舱 内 所 占 的 底 面 积
(m2 ).
②装载积载因数不大于 0 .56 m3 t 的高密度
固体散货时 , 必须注意货物重量的纵向分配 , 以免
产生过大的应力 .根据“BC 规则” 的规定 , 每一货
57000dwt散货船余量布置设计优化
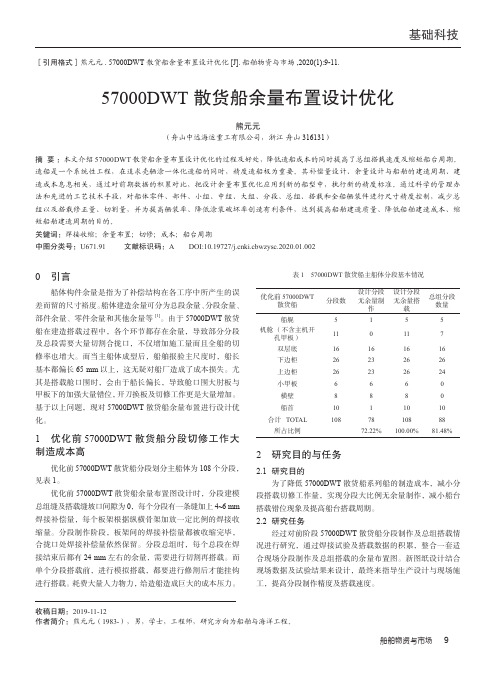
基础科技船舶物资与市场 90 引言船体构件余量是指为了补偿结构在各工序中所产生的误差而留的尺寸裕度。
船体建造余量可分为总段余量、分段余量、部件余量、零件余量和其他余量等[1]。
由于57000DWT 散货船在建造搭载过程中,各个环节都存在余量,导致部分分段及总段需要大量切割合拢口,不仅增加施工量而且全船的切修率也增大。
而当主船体成型后,船舶报验主尺度时,船长基本都偏长65 mm 以上,这无疑对船厂造成了成本损失。
尤其是搭载舱口围时,会由于船长偏长,导致舱口围大肘板与甲板下的加强大量错位,开刀换板及切修工作更是大量增加。
基于以上问题,现对57000DWT 散货船余量布置进行设计优化。
1 优化前57000DWT 散货船分段切修工作大制造成本高优化前57000DWT 散货船分段划分主船体为108个分段,见表1。
优化前57000DWT 散货船余量布置图设计时,分段建模总组缝及搭载缝坡口间隙为0,每个分段有一条缝加上4~6 mm 焊接补偿量,每个板架根据纵横骨架加放一定比例的焊接收缩量。
分段制作阶段,板架间的焊接补偿量都被收缩完毕,合拢口处焊接补偿量依然保留。
分段总组时,每个总段在焊接结束后都有24 mm 左右的余量,需要进行切割再搭载。
而单个分段搭载前,进行模拟搭载,都要进行修割后才能挂钩进行搭载。
耗费大量人力物力,给造船造成巨大的成本压力。
57000DWT 散货船余量布置设计优化熊元元(舟山中远海运重工有限公司,浙江 舟山 316131)摘 要 :本文介绍57000DWT 散货船余量布置设计优化的过程及好处,降低造船成本的同时提高了总组搭载速度及缩短船台周期。
造船是一个系统性工程,在追求壳舾涂一体化造船的同时,精度造船极为重要。
其补偿量设计、余量设计与船舶的建造周期、建造成本息息相关,通过对前期数据的积累对比,把设计余量布置优化应用到新的船型中,执行新的精度标准。
通过科学的管理办法和先进的工艺技术手段,对船体零件、部件、小组、中组、大组、分段、总组、搭载和全船舾装件进行尺寸精度控制,减少总组以及搭载修正量、切割量,并为提高舾装率、降低涂装破坏率创造有利条件,达到提高船舶建造质量、降低船舶建造成本、缩短船舶建造周期的目的。
- 1、下载文档前请自行甄别文档内容的完整性,平台不提供额外的编辑、内容补充、找答案等附加服务。
- 2、"仅部分预览"的文档,不可在线预览部分如存在完整性等问题,可反馈申请退款(可完整预览的文档不适用该条件!)。
- 3、如文档侵犯您的权益,请联系客服反馈,我们会尽快为您处理(人工客服工作时间:9:00-18:30)。
散货船装载过程优化的研究Study on Optimization of Bulk Carrier’s LoadingProcess本文从散货船的安全问题出发,结合散装船舶装卸货过程中的实际情况,提出了通过优化装载方案来控制船舶装货时强度变化的观点,以使整个装货过程中产生的剪力、弯矩对船舶强度的影响尽量最小。
初步建立了散货船装载优化模型,提出了求解该模型的基本思想,并将遗传算法运用于该优化模型的求解。
研究了遗传算法在散货船装载过程优化上的具体实施方法。
采用面向对象的程序设计方法,在Windows平台的Visual C++环境下开发了基于遗传算法的散货船装载过程优化软件。
本文所开发的基于遗传算法的散货船装载过程优化软件,可以作为装载仪中的一个子系统,对各种装货过程进行优选,最后得到一个近似最优的装货方案。
经过优化的装货方案可以大大减小装货过程中所产生的船舶剪力和弯矩最大值。
该软件可以运用于实际生产,通过控制船舶装货环节的船体强度,提高散货船的安全性,延长船舶的使用寿命。
ABSTRACTThis paper particularly analyzes the characteristic of bulk carrier. Present the attitude that controls the vessel’s strength in loading by optimizing the loading scheme. This optimization intends to make the vessel’s Shear Force (SF) and Bending Moment (BM) in loading process to the lowest extent. An optimization modal for loading of bulk carrier is basically established in this paper. Author creatively uses the Genetic Algorithms to get the solution of this optimization modal.The software named “Optimization of Bulk Carrier’s Loading Procession”, which can be inserted to “Stowage System of Bulk Carrier” as a subsystem. This softwarechose the best one approximately from every loading scheme. The optimized scheme can reduce the maximum of SF and BM in loading at most extend. Using the software to optimize the loading process in practice will improve the security of the bulk carrier, and prolong the life span of the bulk carrier.Key Words: Bulk Carrier, Vessel’s Strength, Optimization of Loading Process, Genetic Algorithms.1.4 散货船装卸操作中的强度控制问题从散货船的安全现状可以看出,目前都存在一个共同的问题,即船舶强度问题。
如何才能把营运中的风险降至最低,如何才能提高散货船营运的安全系数,保证人、船、货的安全,延长船舶的使用寿命,这有赖于通过适当的装卸,使装卸过程中产生的剪力、弯矩对船体的潜在损伤降至最低。
这就提出了散货船在装卸过程中的强度控制问题。
[7]散货船在装卸过程中的强度控制的核心,就是要制定较优化的装卸货方案,使整个装卸过程中产生的剪力、弯矩对船舶强度的影响尽量最小。
现有散货船根据SOLAS公约第Ⅶ/11条的规定,均安装了规定的装载仪。
船舶驾驶员通过输入某一状态下的装载货物情况和油水分布情况,就可以得到该状态下的各站号及特殊要求位置的剪力和弯矩值,再将这些数据与规范标准相比较。
通常船舶驾驶员是事先制订一个装卸货方案,再用装载仪去校核,以确定装卸过程中船舶强度是否满足规范要求,如不满足则对原计划进行修改,直到满足规范要求为止。
该装卸方案虽然满足规范要求,但是却未达到优化的程度。
如果能够获得优化方案并以此指导装卸作业,那么货物操作过程中散货船船体的损伤将会大大降低,从而大大减少船体的疲劳,提高散货船的使用寿命,保证船舶安全。
一般来说,由于散货船的装货速度远高于卸货速度,所以装货时对船舶强度的控制就显得比卸货时更加重要。
本文就是从散货船的装载角度出发,在船舶装载仪的基础上引入人工智能的思想,运用遗传算法对船舶的装货过程进行优化,并可在散货船的装载仪中增设一个子系统,对各种装货过程进行优选,最后得到一个近似最优的装货方案,以解决散货船装卸过程中的强度控制问题。
散货船装载过程优化模型的建立在散货船装载过程优化中需要考虑的主要因素仅是船舶纵向强度和船舶的吃水、吃水差限制。
本章首先介绍了静水中船舶纵向强度和浮态的计算方法,再进一步建立了散货船装载过程的优化模型,并初步提出了该模型的求解思路。
装载过程优化模型的建立在散货船的实际装载过程,可以定义为单舱装载方式和多舱装载方式。
单舱装载方式就是装货过程中只有一部装货设备,一次只能对一个货舱进行装货操作;多舱装载方式就是指用两部或两部以上的装货设备对不同的货舱同时进行装货操作的装载方式。
与多舱装载方式相比,采用单舱装载方式时,装货过程中对船舶强度和浮态的控制是比较困难的。
因此对单舱装载方式的优化是非常必要的。
本文仅对单舱装载方式进行了研究,对单舱装载过程建立了优化模型。
2.3.1 建立优化模型的目的。
装载过程优化就是要在已知每个货舱计划装货量的基础上,确定一个优化的装货方案,使得按照这个方案进行装货的整个过程中,船舶产生的剪力、弯矩对船舶强度的影响尽量最小,并且在整个过程中船舶的浮态也能满足规定的要求。
所以,建立装载过程优化模型的目的就是:在尽量减少装货次数的前提下,确定一个能使整个装货过程中船舶的剪力、弯矩尽量小并且使船舶吃水、吃水差始终保持在规定要求以内的装货优化方案。
2.3.2 目标函数的建立2.3.2.1 确立基本变量每个货舱最终要装载的货物重量是已知的,用i V 表示。
船舶总共需要装货的货舱数,用C 表示。
则该航次船舶总装货量为∑=C i i V1。
将每一次装货设备从一个货舱口移动至另一货舱口称之为一次换装作业,而装货设备对全船所有货舱依次完成了一次装货的过程定义为一轮装货作业。
完成整个装货需要的换装次数用J 表示,完成整个装货需要的轮次数用R 表示。
对于有5个货舱和7个货舱的散货船,一般经过两轮装货均可满足优化的要求,即可取R=2。
而对于9个货舱以上的大型散货船,往往需要3轮或以上的装货作业才能满足优化的要求,即R ≥3。
我们假定。
可以看出任意一种装货方案都是由每轮装舱的次序S (Sequence )和每轮各舱的装货数量Q (Quantity )构成。
确定了每轮的装舱次序和每轮的各舱装货量,就确定了一种装货的方案E ,即),(Q S f E = (2-3-1)在装货中为了保证船舶的纵向强度,一般情况下压载水排放位置与装载货舱的位置趋于一致,因此,压载水方案B 是由装货方案所决定的,现定义为)(E t B = (2-3-2)2.3.2.2 目标函数的建立在装货过程中,每个校核站面的剪力、弯矩都是在不断变化的,它们变化是个连续的过程,因而可取每一次换装作业时各个校核站面的剪力ij SF 和弯矩ij BM 其中,i 为校核站面的位置, j 为换装作业的次数。
设各个校核站面的剪力许用值为i ASF ,弯矩许用值为i ABM ,则可设定装货过程中优化模型的目标函数为: )(max )(iij ij ASF SF E g = (2-3-3) )(max )(i ij ij ABM BM E h = (2-3-4)对装货方案E 的优化,理论上就是要求得一个解*E ,使得)(*E g 和 )(*E h 为最小值。
2.3.3 约束条件的设立考虑到港口航道或码头泊位水深的限制和压载水排放要求,散货在装载过程中必须限定船舶吃水和吃水差。
设每次换装作业时船舶的首吃水为Fj d (E),尾吃水为j A d (E),吃水差为j t (E),则装卸过程中约束条件为:⎪⎩⎪⎨⎧<<<<<<21max min max min )()()(T E t T d E d d d E d d j Aj Fj (2-3-5)式中,1T ,2T 分别为装货过程中最大尾倾吃水差和最大首倾吃水差,其中1T 为负值,2T 为正值。
2.3.4 装载过程的优化模型建立最优化模型,有三个基本要素,即决策变量、目标函数和约束条件 ,于是可建立如下装货过程优化模型:min ⎩⎨⎧⎭⎬⎫)()(E h E gs.t. ⎪⎩⎪⎨⎧<<<<<<21max min max min )()()(T E t T d E d d d E d d j Aj Fj (2-3-6)在多目标决策问题中,根据实际情况确定一个目标为主要目标,而把其余目标作为次要目标,并且根据决策者的经验,选取一定的界限值。
这样就将原多目标决策问题转化为在一个新的约束条件下,求主要目标的单目标规划问题[20]。
现将每次换装作业时船舶各个站点的实际剪力占许用剪力的百分比限定在δ以内作为约束条件,就可以把2-3-6式变为下式:min }{)(E hs.t.⎪⎪⎪⎩⎪⎪⎪⎨⎧<<<<<<<δiij j j j ASF SF T E t T d E da d d E df d 21max min max min )()()( (2-4-1)其中,δ可根据船龄及装载条件限定在50%~70%范围内。
2.4 装载过程优化模型求解的基本思路将2-3-1式代入2-3-3和2-3-4式,我们可以将目标函数变为:)(max ),(i ij ij ASF SF Q S g = )(max ),(i ij ij ABM BM Q S h =(2-4-2)求解最优解*E ,也就是求解最优装舱顺序*S 和每轮各舱最优装货量*Q 。