马钢冷轧乳化液的应用与优化
乳化液系统对冷轧版型控制影响
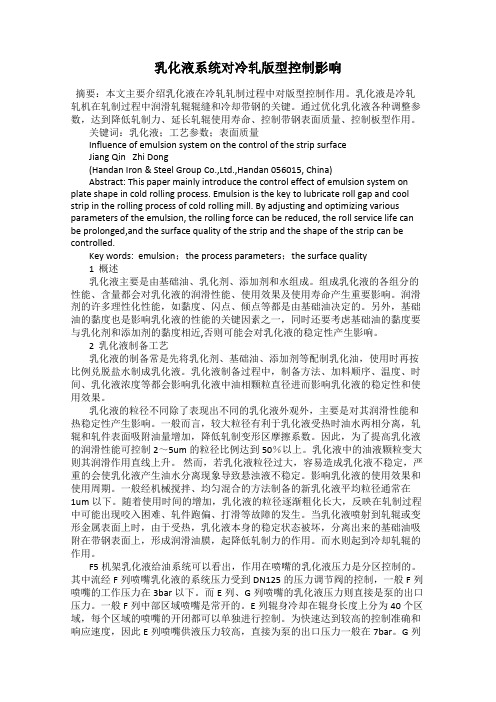
乳化液系统对冷轧版型控制影响摘要:本文主要介绍乳化液在冷轧轧制过程中对版型控制作用。
乳化液是冷轧轧机在轧制过程中润滑轧辊辊缝和冷却带钢的关键。
通过优化乳化液各种调整参数,达到降低轧制力、延长轧辊使用寿命、控制带钢表面质量、控制板型作用。
关键词:乳化液;工艺参数;表面质量Influence of emulsion system on the control of the strip surfaceJiang Qin Zhi Dong(Handan Iron & Steel Group Co.,Ltd.,Handan 056015, China)Abstract: This paper mainly introduce the control effect of emulsion system on plate shape in cold rolling process. Emulsion is the key to lubricate roll gap and cool strip in the rolling process of cold rolling mill. By adjusting and optimizing various parameters of the emulsion, the rolling force can be reduced, the roll service life can be prolonged,and the surface quality of the strip and the shape of the strip can be controlled.Key words: emulsion;the process parameters;the surface quality1 概述乳化液主要是由基础油、乳化剂、添加剂和水组成。
组成乳化液的各组分的性能、含量都会对乳化液的润滑性能、使用效果及使用寿命产生重要影响。
可逆冷轧机乳化液系统改造与优化

可逆冷轧机乳化液系统改造与优化摘要:近年来,我国的工业化进程有了很大进展,轧机的应用也越来越广泛。
本文基于金泰包装1200mm可逆冷轧机乳化液系统,通过对供乳方式、循环设备、加热方式及磁过滤器等设备进行改进,有效解决了薄规格边部热擦伤、乳化液寿命低、过滤精度差等问题,改善了带钢板面质量,适应了产品结构调整的需要。
关键词:冷轧;乳化液;改造引言轧机是钢板带厂的关键设备,为钢板带厂下游工序提供重要保障,签于其在钢板带生产中的重要作用,对该设备的维护、检修及故障的快速处理也显得越来越重要。
卷取机张力的稳定性直接影响带材的质量和成品率,尤其在带材被拖动动态升降速的过程中,更要保持张力的恒定以免出现断带。
所以本文着重对该轧机卷取机的张力控制系统进行简单的阐述,并对常见的张力故障加以分析、总结,以提高设备维护水平,提高产品质量和成品率。
1乳化液斑特征乳化液斑多出现在轧机的头部,也就是重卷的尾部,在重卷或平整时可清楚观察到:距尾部50m左右时开始出现(时多时少,50m只是一个大致的平均数,严重时通条都存在),起始是在带钢的边部和中部浪形区,沿带钢纵向呈条状或细长条状;随着带钢到尾部距离的缩短,斑迹的密度增大,在距尾部30m时大量出现,呈一定间距平行条状排列,有的整个区域上下表面均产生乳化液斑,斑迹的形状、大小基本一致。
斑迹大多呈黄褐色,轻者呈黄色,重者呈灰黑色,斑迹无法用擦拭物擦除。
2金泰包装 1200mm乳化液循环系统存在的问题1)乳化液箱采用老式的蒸汽盘管的加热方式,里面铺设复杂的加热蒸汽管道,容易在蒸汽管道缝隙造成油泥沉淀和板结,清理困难,蒸汽加热效率低。
2)控制温度、液位的各路控制阀门的启闭都分别需要岗位工人从轧机操作台跑到乳化液站来进行人工调节,如果指标不稳定,就会经常造成过润滑、欠润滑、乳化液浓度波动大等问题,出现薄规格产品糊边、变形区温度过高引起的粘辊或钢带断裂等事故。
3)污油箱存在着循环“死角”,容易形成大量的浮油,极大地降低了乳化液的使用寿命和质量,常时间的开启磁过滤器,不仅增加了油耗,还造成了润滑不足。
乳化液新技术在冷轧生产线上的应用
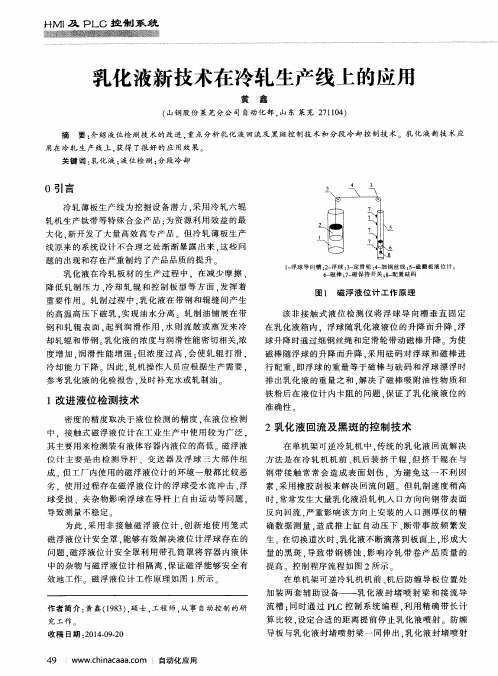
1改进液位测技术
密 度 的精 度取 决 于 液 位 检 测 的精 度 , 在 液 位 检 测 中 .接 触 式磁 浮 液 位 计 在 工 业 生 产 中使 用 较 为 广 泛 , 其 主要 用来 检 测 装 有 液 体 容 器 内液 位 的 高低 。磁 浮 液
素. 采 用 橡 胶 刮 板 来 解 决 回流 问题 但 轧 制 速 度 稍 高
时. 常 常 发 生 大 量乳 化 液 沿 轧 机 入 口方 向 向 钢 带 表 面
反向回流 . 严 重 影 响 该 方 向上 安 装 的入 口测 厚 仪 的精
为此. 采用 非接触磁 浮液位 计 . 创 新 地 使 用 笼 式
磁 浮液 位计安 全罩 . 能够有效解决液位计 浮球存在 的
问题 . 磁 浮 液位 计 安全 罩 利用 带 孔 筒 罩 将 容 器 内液 体 中 的杂 物 与磁 浮 液位 计 相 隔 离 . 保 证 磁 浮 能 够 安 全 有 效地 工 作 磁 浮 液 位 计 工作 原理 如 图 1 所 示
用在 冷轧 生产 线上 . 获 得 了很 好 的 应 用 效 果 。
关键 词 : 乳化 液 ; 液位检 测 ; 分 段 冷 却
0引 言
冷 轧 薄 板 生 产 线 为挖 掘设 备 潜 力 , 采 用 冷 轧 六 辊 轧机生产钛带等特殊合金 产品 ; 为 资 源 利 用 效 益 的 最 大化 . 新 开 发 了 大量 高效 高 专 产 品 。但 冷 轧 薄 板 生 产 线 原 来 的 系 统设 计 不合 理 之 处 渐 渐 暴 露 出 来 , 这些 问 题 的 出现 和 存 在 严 重 制 约 了产 品 品质 的提 升 。 乳 化 液 在 冷 轧 板 材 的生 产 过 程 中 ,在 减 少 摩 擦 、 降低轧 制压力 、 冷却轧 辊和控制 板型 等方面 , 发 挥 着 重 要 作 用 轧 制 过 程 中 . 乳 化 液 在 带 钢 和 辊 缝 间产 生 的高 温 高 压 下 破 乳 , 实 现 油 水 分 离 。 轧 制 油 铺 展 在 带 钢和轧 辊表面 . 起到润 滑作用 , 水 则 流 散 或 蒸 发 来 冷 却轧辊和带钢 。 乳 化 液 的浓 度 与 润 滑 性 能 密切 相 关 , 浓
轧制乳化液的工业试验及应用
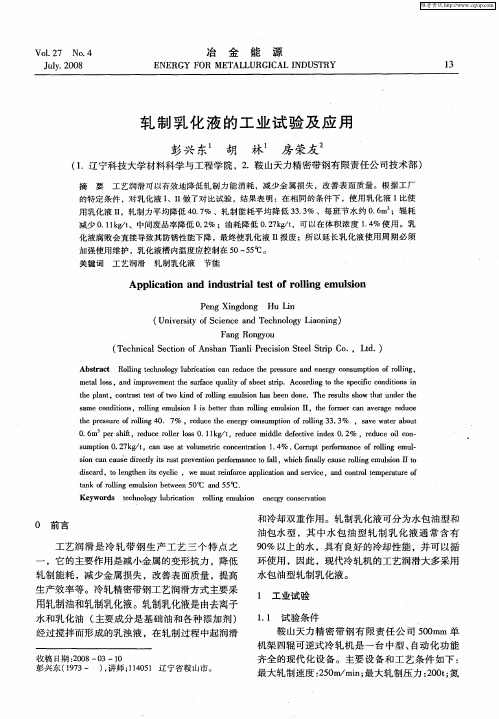
me a s ,a d i r v me t h u fc u l y o h e a p tll s n mp o e n e s ra e q ai fs e ts .Ac o d n o t e s e i c c n i o s i o t t c r i gt p cf o d t n n h i i t e p a t o tatt s o i d o ol g e lin h e n d n .T e rs l h w a n e h h l n ,c nr s e t ft k n frl n mu so a b e o e h ut s o t tu d rt e wo i s e s h s me c n i o s ol g e lso s b t r ̄ a l n muso I h o me B v rg e u e a o dt n ,rl n mu in I i et t n r l g e l in I ,t e f r re B a e a e rd c i i e h o i
维普资讯
Vo . 7 No 4 12 .
冶
金
能
源
1 3
J l. 0 8 uy 2 0
E RGY F T 工URG C NDUS RY NE OR ME AI I AL I r
轧 制 乳 化 液 的 工 业 试 验 及 应 用
Ap l a in a d i d sra e to ol g e lin p i t n n u t il s fr l n muso c o t i
乳化液控制系统在冷轧可逆轧机上的应用
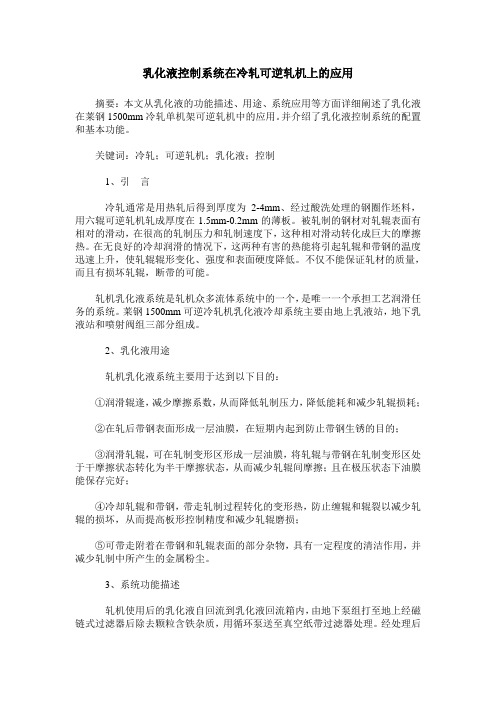
乳化液控制系统在冷轧可逆轧机上的应用摘要:本文从乳化液的功能描述、用途、系统应用等方面详细阐述了乳化液在莱钢1500mm冷轧单机架可逆轧机中的应用。
并介绍了乳化液控制系统的配置和基本功能。
关键词:冷轧;可逆轧机;乳化液;控制1、引言冷轧通常是用热轧后得到厚度为2-4mm、经过酸洗处理的钢圈作坯料,用六辊可逆轧机轧成厚度在1.5mm-0.2mm的薄板。
被轧制的钢材对轧辊表面有相对的滑动,在很高的轧制压力和轧制速度下,这种相对滑动转化成巨大的摩擦热。
在无良好的冷却润滑的情况下,这两种有害的热能将引起轧辊和带钢的温度迅速上升,使轧辊辊形变化、强度和表面硬度降低。
不仅不能保证轧材的质量,而且有损坏轧辊,断带的可能。
轧机乳化液系统是轧机众多流体系统中的一个,是唯一一个承担工艺润滑任务的系统。
莱钢1500mm可逆冷轧机乳化液冷却系统主要由地上乳液站,地下乳液站和喷射阀组三部分组成。
2、乳化液用途轧机乳化液系统主要用于达到以下目的:①润滑辊逢,减少摩擦系数,从而降低轧制压力,降低能耗和减少轧辊损耗;②在轧后带钢表面形成一层油膜,在短期内起到防止带钢生锈的目的;③润滑轧辊,可在轧制变形区形成一层油膜,将轧辊与带钢在轧制变形区处于干摩擦状态转化为半干摩擦状态,从而减少轧辊间摩擦;且在极压状态下油膜能保存完好;④冷却轧辊和带钢,带走轧制过程转化的变形热,防止缠辊和辊裂以减少轧辊的损坏,从而提高板形控制精度和减少轧辊磨损;⑤可带走附着在带钢和轧辊表面的部分杂物,具有一定程度的清洁作用,并减少轧制中所产生的金属粉尘。
3、系统功能描述轧机使用后的乳化液自回流到乳化液回流箱内,由地下泵组打至地上经磁链式过滤器后除去颗粒含铁杂质,用循环泵送至真空纸带过滤器处理。
经处理后的乳化液在净油箱里存放,净乳液由工作泵送到轧机冷却润滑使用,在工作泵出口总管设筒式自清洗过滤器和板式换热器,当乳化液温度高于轧机使用要求时,采用板式换热器对乳化液进行冷却处理,使其温度降至轧机所要求的温度。
乳化液浓度对板带钢冷轧润滑性能的影响研究

乳化液浓度对板带钢冷轧润滑性能的影响研究1.绪论1.1 研究背景和意义1.2 相关研究概述1.3 研究内容和目的2.理论分析2.1 乳化液的基本概念和组成2.2 乳化液中浓度的概念和作用2.3 钢板冷轧润滑机理的分析2.4 浓度对润滑性能的理论作用原理3.实验设计3.1 实验方案设计3.2 实验材料和设备选择3.3 实验方法和步骤3.4 实验数据处理和分析4.实验结果4.1 实验数据统计结果4.2 浓度对钢板冷轧润滑性能的影响结果分析4.3 不同浓度乳化液润滑性能的比较与探讨5.结论与展望5.1 研究结论5.2 研究创新点5.3 其他问题与展望5.4 实验的局限性和不足点1.绪论1.1 研究背景和意义板带钢冷轧工艺是工业生产中常见的一种加工方式。
在板带钢冷轧过程中,为减少材料表面损伤和摩擦损失,在轧制过程中广泛应用润滑技术。
目前,乳化液润滑技术已成为钢板冷轧的主要润滑方式之一。
乳化液是指由油、水、乳化剂等物质组成的稳定混合物,是钢板冷轧润滑的重要介质。
乳化液的浓度可以影响到钢板冷轧的润滑效果、减小轧制压力、降低表面温度,提高钢品表面质量等。
因此,研究乳化液浓度对板带钢冷轧润滑性能的影响,对提高钢板冷轧润滑技术的效率和质量具有重要意义。
1.2 相关研究概述国内外学者对乳化液浓度对板带钢冷轧润滑性能的研究已有较深入的探讨。
例如,对于在高温下进行的板带钢冷轧润滑,如何调节乳化液浓度才能够达到最佳润滑效果和减小表面质量问题,学者们展开了很多的研究,如使乳化液的油水比为3:7时,其润滑效果为最佳。
再如,国外学者曾研究乳化液浓度对板材表面质量的影响,得出乳化液浓度在1%~6%之间对钢板表面质量的影响形式为“U”形,在浓度为3%时表现最佳。
然而,考虑到钢品工艺参数的多样性和原材料质量的差异,乳化液浓度对板带钢冷轧润滑性能的影响尚需进一步的研究。
1.3 研究内容和目的本文将就乳化液浓度对板带钢冷轧润滑性能的影响进行研究。
乳化液在冷轧润滑过程中的应用分析
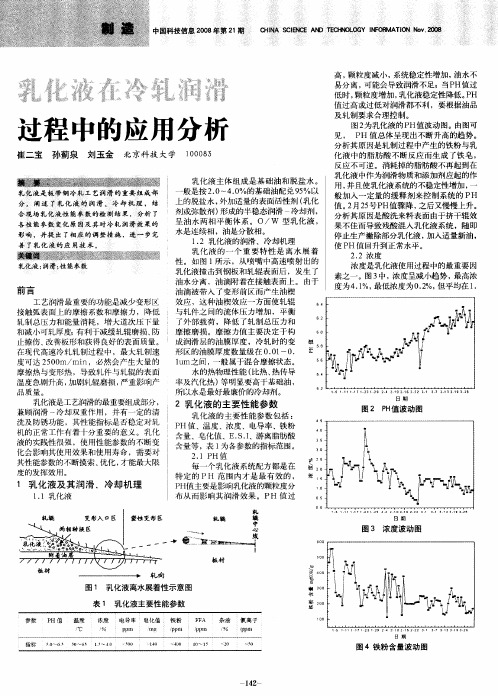
乳化液 ; . 能参数 漓 }性
前 言
工艺 润 滑 最 重要 的功 能 是 减 少 变 形 区 接 触 弧 表 面上 的摩 擦 系数 和 摩 擦 力 , 降低 轧 制 总 压 力和 能 量 消 耗 ,增 大 道 次 压 下 量 和 减 小 可轧 厚 度; 利 于 减缓 轧 辊 磨 损 、 有 防 止擦伤、 改善 板 形 和 获 得 良好 的 表 面 质 量 。 在现代高速 冷轧轧制过程 中,最大#  ̄J LI 速 度 可 达 2 0 m/ i 5 0 r n,必 然 会 产 生 大 量 的 a 摩 擦 热 与 变形 热 ,导 致 轧 件 与 轧 辊 的 表 面 温 度 急剧 升 高 , 剧 轧 辊 磨 损 , 重影 响 产 加 严
轧
日 期
图 2 H值波动图 P
1 乳 化 液及 其 润滑 冷却 机 理
1 1乳 化 液 .
轧 蟪
◆ 谚 謦
板料
警
日 期
裳
}
图 3 浓度波动 图
图 1 乳化液离水展着性示意图
表 1 乳化液 主要性能参数
参数 P 值 H 温度
i  ̄ C
浓度 电 导率 皂化值 铁粉
一
乳化液 是 板带 钢 冷轧工 艺漓滑 的重要组 成部 分 ≯嘏 遂 乳 化 液 讷 讽蒲 - 却 机 理 纯 冷
合 现 场 乳 化液 性 能 参 数 的 检 测 结 果 , 析 了 分
各 性能 参数变化原 因及 其对冷 轧 润滑效果 的 影响 ,并提 了相应 的调整措 施 ,进一 步完
品质量 。
高, 颗粒度减小 , 系统稳定性增加 , 油水不 易分离 , 可能会导致润滑不足;当P H值过 低时 , 颗粒度增加 , 乳化液稳 定性 降低。 H P 值过高或过低对润滑都不利 ,要根据油品 及轧制要求合理控制。 图2 为乳化液的P H值波动图。由图可 见 , PH值总体呈现 出不断升高的趋势 。 分析其原 因是轧制过程 中产生的铁粉与乳 化 液 中的 脂肪 酸不断 反应 而生成 了铁 皂 , 反应 不可逆 。消耗掉的脂肪酸不再起到在 乳化液 中作为润滑物质和添加剂应起的作 用, 并且使乳化液系统的不稳定性增加 , 一 般加 入一定量的缓释剂 来控制系统的 PH 值 。 月2 号P 2 5 H值骤降, 之后又慢慢上升 。 分析其原 因是酸洗来料表面 由于挤干辊效 果 不 佳 而 导 致 残 酸 混 入 乳 化 液 系 统 ,随 即 停止生产撇除部分乳化液 , 加入适量新油, 使P H值 回升到正常水平 。 2 2浓 度 . 浓度是乳化液 使用过程 中的最重要 因 素之一 。图3 , 中 浓度呈减小趋势 , 最高浓 度为 4 1 最低浓度为 02 但平均在 1 .%, .%, .
关于冷轧中乳化液的技术指标
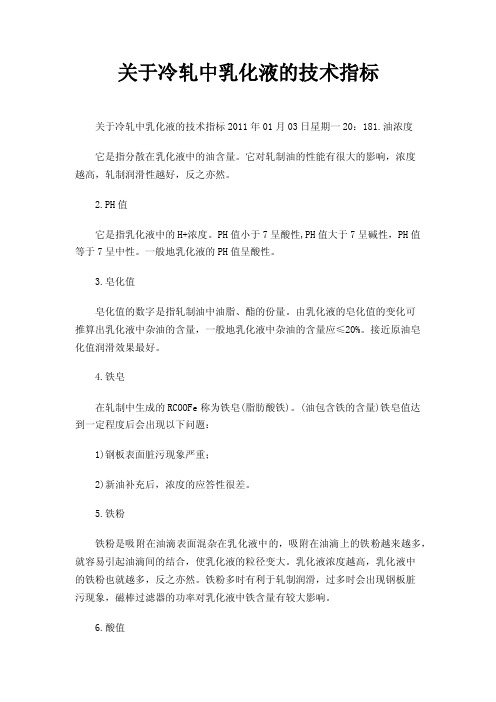
关于冷轧中乳化液的技术指标关于冷轧中乳化液的技术指标2011年01月03日星期一20:181.油浓度它是指分散在乳化液中的油含量。
它对轧制油的性能有很大的影响,浓度越高,轧制润滑性越好,反之亦然。
2.PH值它是指乳化液中的H+浓度。
PH值小于7呈酸性,PH值大于7呈碱性,PH值等于7呈中性。
一般地乳化液的PH值呈酸性。
3.皂化值皂化值的数字是指轧制油中油脂、酯的份量。
由乳化液的皂化值的变化可推算出乳化液中杂油的含量,一般地乳化液中杂油的含量应≤20%。
接近原油皂化值润滑效果最好。
4.铁皂在轧制中生成的RCOOFe称为铁皂(脂肪酸铁)。
(油包含铁的含量)铁皂值达到一定程度后会出现以下问题:1)钢板表面脏污现象严重;2)新油补充后,浓度的应答性很差。
5.铁粉铁粉是吸附在油滴表面混杂在乳化液中的,吸附在油滴上的铁粉越来越多,就容易引起油滴间的结合,使乳化液的粒径变大。
乳化液浓度越高,乳化液中的铁粉也就越多,反之亦然。
铁粉多时有利于轧制润滑,过多时会出现钢板脏污现象,磁棒过滤器的功率对乳化液中铁含量有较大影响。
6.酸值酸值的数值表示轧制油中脂肪酸的量。
1)脂肪酸的优点:酸基对钢板表面有较强的附着力,因此它对润滑性和防锈性都很好。
2)脂肪酸的缺点:脂肪酸过多,将会促进油箱以及管道的腐蚀,此外还将生成大量铁油泥,使钢板表面及轧机机组的脏污急剧增加。
7.电导率一般指乳化液的导电能力,是电阻的倒数。
(离子高则容易油水分离!)8.温度温度是个管理项目,它对性能有很大的影响。
1)温度较低时容易出现的问题:①润滑不良,轧制力升高,振动现象多发;②容易产生轧后钢板表面脏污现象;③钢板表面水分蒸发困难,钢板容易生锈。
2)温度较高时容易出现的问题:①乳化不安定,附着量增加,容易产生打滑现象;②蒸汽大量产生,污染工作环境。
乳化液在轧制过程中的润滑和冷却乳化液在冷轧中的主要作用是润滑和冷却。
在轧制过程中,轧制变形区产生的高温使乳化液产生油水分离,油吸附在轧辊与钢板表面形成油膜,起到润滑作用。
乳化液润滑冷轧铝板表面缺陷分析

乳化液润滑冷轧铝板表面缺陷分析乳化液作为润滑剂在冷轧铝板表面中起着至关重要的作用,能够有效地降低摩擦系数和延长轧辊的使用寿命。
但是,在实际生产过程中,乳化液的使用也会引起一些表面缺陷,如泡沫、异色、花印等问题,严重影响铝板表面质量。
因此,本文将对乳化液润滑冷轧铝板表面缺陷进行分析和探讨,以期对于乳化液的正确使用和表面质量的提升提供一些参考和帮助。
一、缺陷种类与特征1、泡沫缺陷泡沫缺陷是最常见的表面缺陷之一,其主要特征为涂层表面出现不规则的气泡,严重时会影响铝板表面的质量。
通常泡沫缺陷的成因是由于乳化液在使用过程中,乳化剂的稳定性不足,表面张力较小,容易产生泡沫。
此外,还可能是由于空气污染、杂质等因素引起的。
2、异色缺陷异色缺陷是指涂层表面明显出现色差现象,主要是因为乳化剂、添加剂等的不同,导致涂层颜色变化,对于铝板表面的美观性和涂层掩盖力有着很大的影响。
3、花印缺陷花印缺陷是指涂层表面出现明显的桔皮状和波纹状纹路,这是由于乳化液分散性不均匀,导致涂层中局部的乳化液浓度过高或过低所引起,极大地降低了铝板表面的质量。
二、缺陷成因分析1、泡沫缺陷成因分析泡沫缺陷的成因主要可归为以下几点:(1)乳化剂稳定性差:乳化剂在使用过程中,容易受到环境变化的影响,其稳定性会发生改变,从而导致乳化液泡沫化现象的发生。
(2)表面张力小:乳化液属于表面活性剂的范畴,表面张力小的情况下,其表面上的液体分子就更容易发生聚集,产生气泡和泡沫。
(3)污染:乳化液在使用过程中会受到空气、尘埃等污染物的影响,从而使得泡沫的产生加剧。
2、异色缺陷成因分析异色缺陷的成因主要可归为以下几点:(1)乳化剂不同:乳化剂的配方不同,其对于铝板表面的涂层颜色也会产生不同的影响,导致出现异色缺陷。
(2)添加剂杂质:添加剂杂质的含量会影响涂料的颜色稳定性,从而引起铝板表面的质量问题。
3、花印缺陷成因分析花印缺陷的成因主要可归为以下几点:(1)乳化液分散性不均匀:乳化液在冷轧过程中不易完全分散开来,会留下一些局部的浓度差异,从而引起花印的产生。
乳化液应用及问题研究
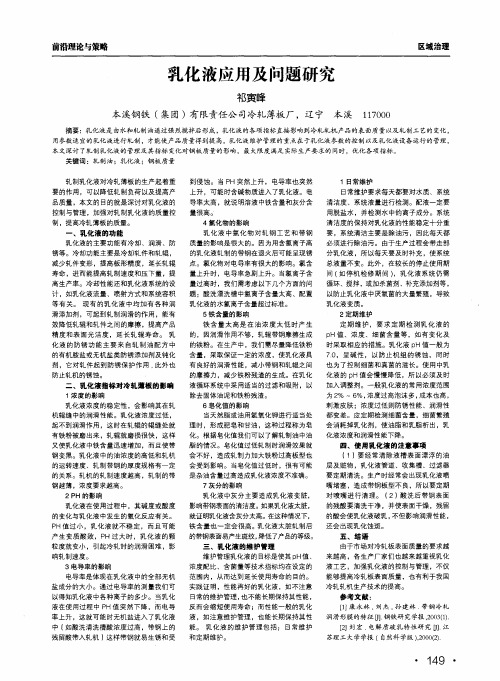
到侵蚀。当PH突然上升.电导率也突然 上升,可能时含碱物质进入了乳化液。电 导率太高,就说明溶液中铁含量和灰分含 量很高。
4氯化物的影响 乳化液中氯化物对轧钢工艺和带钢 质量的影响是很大的。因为用含氯离子高 的乳化液轧制的带钢在退火后可能呈现锈 点。氯化物对电导率有很大的影响。氯含 量上升时,电导率急剧上升。当氯离子含 量过高时,我们需考虑以下几个方面的问 题:酸洗漂洗槽中氯离子含量太高、配置 乳化液的水氯离子含量超过标准。 5铁含量的影响 铁含量太高是在油浓度太低时产生 的,因润滑作用不够,轧辊带钢摩擦生成 的铁粉。在生产中,我们需尽量降低铁粉 含量,采取保证一定的浓度,使乳化液具 有良好的润滑性能,减小带钢和轧辊之间 的摩擦力。减少铁粉残渣的生成。在乳化 液循环系统中采用适当的过滤和吸附,以 除去固体油泥和铁粉残渣。 6皂化值的影响 当天然脂或油用氢氧化钾进行适当处 理时,形成肥皂和甘油,这种过程称为皂 化。根据皂化值我们可以了解轧制油中油 脂的情况。皂化值过低轧制时润滑效果就 会不好,造成轧制力加大铁粉过高板型也 会受到影响。当皂化值过低时,很有可能 是杂油含量过高造成乳化液浓度不准确。 7灰分的影响 乳化液中灰分主要造成乳化液变脏, 影响带钢表面的清洁度。如果乳化液太脏, 就证明乳化液含灰分太高。在这种情况下. 铁含量也一定会很高。乳化液太脏轧制后 的带钢表面易产生斑纹,降低了产品的等级。 三、乳化液的维护管理 维护管理乳化液的目标是使其pH值、 浓度i§gl:k.、含菌量等技术指标均在设定的 范围内,从而达到延长使用寿命的目的。 实践证明。性能再好的乳化液,如不注意 日常的维护管理,也不能长期保持其性能, 反而会缩短使用寿命;而性能一般的乳化 液,如注意维护管理.也能长期保持其性 能。乳化液的维护管理包括:日常维护 和定期维护。
冷轧乳化液吹扫系统的改进
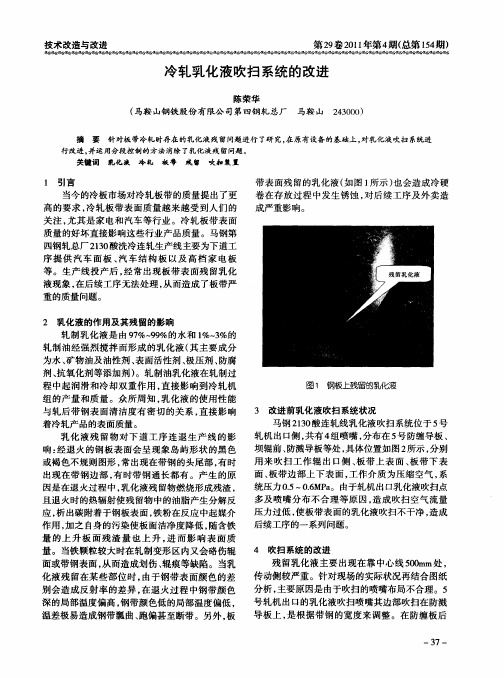
行改进 。 并运 用分段控制 的方 法消除 了乳化液残 留问题 。 关键词
1 引言
当今 的冷板 市场 对冷 轧 板 带 的质 量 提 出 了更
高的要求 , 冷轧板带表面质量越来越受到人们的 关注, 尤其是家 电和汽车等行业 。冷轧板带表面 质量的好坏直接影响这些行业产品质量 。马钢第 四钢 轧 总厂 23 酸洗 冷 连轧 生产 线 主要 为下 道 工 10 序 提供 汽 车面 板 、 汽车结 构板 以及 高档家 电板 等 。生产线投产后 , 经常出现板带表面残 留乳化 液现象 , 在后续工序无法处理 , 从而造成了板带严 重 的质 量 问题 。
带表 面 残 留的 乳化 液 ( 图 l 示 ) 会造 成 冷 硬 如 所 也 卷在存放 过程 中发生锈蚀 , 对后续工序及外卖造 成 严重 影 响 。
2 乳化液的作用及其残留的影响 轧 制 乳 化 液 是 由 9%~ 9 7 9 %的水 和 l 3 %~ %的 轧制油经强烈搅拌 而形成的乳化 液( 主要成分 其 为水 、 矿物油及 油性剂 、 表面活性剂 、 极压剂 、 防腐 剂、 抗氧化剂等添加剂 ) 。轧制油乳化液在轧制过 图 1 钢板上残 留的乳化液 程中起润滑和冷却 双重作用 , 直接影 响到冷轧机 组 的产量和质 量。众所周知 , 乳化液 的使用性能 与轧后带钢表面清洁度有 密切 的关 系 , 直接影响 3 改进前 乳化 液 吹扫 系统状 况 马钢 2 3 酸连 轧 线 乳化 液 吹 扫 系统 位 于 5 10 号 着 冷 轧产 品 的表面 质量 。 共有 4 组喷嘴 , 分布在 5 防缠导板 、 号 乳 化液 残 留物 对下 道工序 连退生 产线 的影 轧机 出口侧 , 防溅导板等处 , 具体位置如 图2 所示 , 分别 响 : 退 火 的钢 板 表 面会 呈 现 象 岛 屿 形 状 的 黑 色 坝辊前 、 经 板带上表 面 、 板带下 表 或褐色不规则图形 , 常出现在带钢的头尾部 , 有时 用来 吹扫工作 辊 出 口侧 、 面、 板带边部上下表面 , 工作介质为压缩空气 , 系 出现在带钢边部 , 有时带钢通长都有 。产生的原 .~06 P 。 因是 在退 火 过 程 中 , 化 液残 留物燃 烧 形 成残 渣 , 乳 统 压力 05 .M a 由于 轧机 出 口乳 化 液吹 扫点 造 且退火时的热辐射使残留物 中的油脂产生分解反 多及喷嘴分布不合理等原 因, 成吹扫空气流量 压力过低 , 使板带表面的乳化液吹扫不干净 , 造成 应 , 出碳附着于钢板表面 , 析 铁粉在反应中起媒介 作用 , 加之 自身的污染使板面洁净度 降低 , 随含铁 后续工序 的一系列问题 。 量 的上 升板 面残 渣 量也 上升 , 而影 响表 面质 进 量。当铁颗粒较大时在轧制变形 区内又会硌伤辊 4 吹扫 系统 的 改进 残 留乳化液主要出现在靠 中心线 50 m处 , 0r a 面或带钢表面 , 从而造成划伤 、 辊痕等缺 陷。当乳 化液残 留在某些 部位时 , 由于钢带表 面颜色 的差 传 动侧较严重 。针对现场的实际状况再结合图纸 主要原因是 由于吹扫的喷嘴布局不合理。5 别会造成反射率的差异 , 在退火过程 中钢带颜色 分析 , 号轧机 出口的乳化液吹扫喷嘴其边部吹扫在防溅 深的局部温度偏高 , 钢带颜色低的局部温度偏低 , 是根据带钢 的宽度来调整。在防缠板后 温差极易造成钢带瓢 曲、 跑偏甚至断带。另外 , 板 导板上 ,
冷轧机组乳化液的研究与应用

浓度 持续 下降 ( 正 常加油 ,
下水道及废乳化液收集槽乳化液增加 冷却水变 自或乳化液 电导率升高
系统泄漏 冷却器泄漏
堵漏 堵漏
液位正常 )
浓度上升 P H升高
E S I 突然下降
皂化值 上升
乳化液水解
杂油泄漏
检查细菌
,
添加杀菌剂或稳定剂
部分排放并加油
电导率 上升 电导率上升
电导率不变
碱性清洗剂泄漏 配制水 p H上升
细菌水解 酸洗挟带 配制水 p H下降 配制水 电导率高 冷却器泄漏 酸洗挟带 酸洗挟带 杂油泄漏 酸洗挟带 杂油泄漏 酸洗挟带 , ,水质 ,部分排放并加油 检查细菌.添加杀菌剂或稳定剂 检查酸洗线挤干辊 控制水质 ,部分排放并加油 控制水质 ,部分排放并加油 堵漏 .部分排放并加油 检查 酸洗线挤干辊 检查 酸洗线挤干辊 检修液压及润滑系统 检查酸洗线挤干辊 检修淮压及润滑系统 检查 酸洗线挤干辊 开动磁性分离器 开动磁性分离器 部分排放并加油 部分排放并加油
常见问题 现象 原 因 解决方法
一
、
1 润滑 作 用
良好 的润 滑可 有 效 降 低 摩 擦 力 , 良 好 的挥 发 性 可 降低 退 火 时 间 。 正 常平 稳 的轧 制 需要 轧 制 油提供 均 衡 稳定 的润 滑 , 即 轧 制油 除必 须 保 证 稳 定 的 物 理 和 化学 特 性 外 ,还 必 须 保 持 数 量 上 的 ,即 吸 附 量 的 稳 定 。 由 于轧 制 油 通 过 分 散 于 乳化 液 中进 行应用 。
P H下降
电导率上升
,
氯离子升高
轧 制 过程 中工 件 发 生 变 形 所 产 生 的 氯离子不变 大 量 的 热 ,也 需 要 由乳 化 液 带 走 ,正确 电导率升高 P H不变 ,冷却水变 白 P H降低 ,氯离子升高 控 制 乳 化 液 的 流量 和喷 射 部 份 ,可 以有 氯离子升高 P H降低 ,电导率升高 效 控 制 板 温 ,并 调 节 板 形 。 在 应 用 乳 化 酸值下降 皂化值下降 液 的 冷 却 功 能 时 ,除 板 温 的 控 制 外 ,可 酸值上降 皂化值上升 ,p H下降 以 通 过乳 化液 流量 的位 置 的控 制 ,使 轧 皂 化值 下降 其它指标 无明显变化 皂化 值上升 酸值上升 ,p H下降 辊 的不 同部 份 产 生不 同程 度 的热 胀 冷缩 , 铁含鼍上升 , 达到 控 制板形 的 目的 。 灰分上升 / 乳化液的冷却性能与油品的应用浓 E S I 下降 , 度 成 反 比 ,浓 度越 高 ,冷 却 能 力 越 低 。 E S I 上升 P H上升 其关 系 如图 1 所示 。 l 温度上升 泡沫减少 ,漂油增加 l 温度下降 轧制力上升 .… 3 乳化 液 的清 洗性 能 乳化液的清洗 主要包括对板面进行 过 程 中 ,除 产 生 铁 粉 外 ,还 会 产 生 各 种 清 洗 ,对 轧 辊 和机 架 进 行 清 洗 。 在 轧 制 高 粘 性 的铁 皂 体 、油 品在 高 温 高 压 下 产 生 的聚 合 物 。这 些 异 物 是 影 响 板 面 清 洁 度 的主 要 因素 。 二 、乳化液成分及主要功能控制 乳 化 液 的性 能 或 稳 定 性 的 变化 ,除 温度 的因素外 ,基本是 由是 内部各组分 变 化 所 造 成 的。 表 1 列 出 了乳 化 液 的一 般 组分 及 含量 。 . 乳 化 液 的 性 能 或性 能稳 定 性 对 轧 制 或 润 滑 的影 响可 以从 两 个方 面 进行 描 述 。 乳 化 液 的皂 化 值 、酸值 、p H值 的变 化 会 图 1 导 致 轧 制 油 物 理 和 化 学 性 能 的 变化 ;乳 表1 乳 化液 各项指 标 测试要 求 化 液 的其 它指标 , 如 浓度 、 温 度 、电导 率 、 项目 对轧制润滑的影响 测试 频度 氯 离子 及 p H值 等指 标 的变化 会 引起参 与 浓度 轧制油的数量 I 一 2次 / 班 润 滑 的轧 制 油 的数 量上 的变 化 。这 里 p H P H 轧制油的数量及物化性能 I 一 2次 / 班 值 的 变化 对 两 方 面都 有 所影 响 。一 般 在 电导率 轧制油的数量 I - 2次 / 班 乳 化 液 应 用 一 段 时 间 后 ,乳 化 液 会 逐 渐 氯离子 轧制油的数量 1 次/ 周 处 于一 种 代 谢 平 衡 ,其 皂 化 值 、酸 值 、 酸值 轧制油的物化性能 1 - 2次 / 周 灰 分 、铁 含 量 等 会保 持 相 对稳 定 ,每 周 皂化值 轧制油的物化性能 I - 2次 / 周 至两 次 的测 试 就 基 本 可 以 控 制 。对 于 铁含量 轧制油的数量 I - 2次 / 周 浓度、 温度 、 电导率 等则 由于 频繁 的加水 、 灰分 轧制油的数量 I - 2次 / 周 加 油 的影 响 而 不 断 变 化 ,并 且 会 造 成 轧 E S I 轧制油的数量 1 - 2次 / 周 制 润滑 较 大的变 化 , 因此 必 须高 频测试 。
乳化液的应用

乳化液的应用述了乳化液的分类、应用和保养,并介绍了乳化液的性能以及乳化液系统的组成。
使用一种乳化液能在一个轧程内实现90%的压下率,将 3.00x505mm的坯料轧制至0.30x505mm的成品,不经脱脂直接退火后带钢表面仍保持光洁的表面。
【关键词】乳化液可逆式冷轧机一.概述现代冷轧板带轧机设备朝着大型化、高速化和连续化的方向发展,以满足日益不断增长的市场对冷轧板带的数量和质量的要求。
生产工艺、设备技术的提高,对冷轧工艺润滑、冷却剂(即轧制油)的要求也越来越高。
可以说,冷轧工艺润滑、冷却已成为现代冷轧技术中一个非常重要的课题。
轧制油在轧机中的作用如同人体中血液般重要。
轧制油的优劣是能否正常发挥轧机生产能力的关键。
早期的轧机或采用植物油如菜仔油、棕榈油,或采用动物油如牛脂,或采用矿物油如锭子油,或采用上述油脂的混合油直接供轧机润滑用,轧制冷却则由另一套冷却水系统完成。
采用这种润滑方式的优点是具有良好的润滑性能,但由于润滑油的冷却性能较差,需增加冷却水供应系统及润滑油回收分离系统等。
使系统变得复杂,增加了设备投资,又不利于润滑系统的管理。
故适用于轧制速度较低的轧机轧制极薄带钢,难轧合金,精密合金及部分重有色金属等。
随着现代冷轧技术的进步,越来越多的轧机采用乳化液作工艺润滑、冷却,甚至是新建的轧制0.10mm的极薄带轧机。
乳化液的发展越来越受人关注。
一种性能优良的乳化液应具备以下特点:1)较好的润滑性能,可降低辊缝中的摩擦系数,从而降低了轧制压力和轧制能耗,有利于发挥轧机的最大轧制能力,轧制更薄的产品,获得板形更好、尺寸偏差更精的带材;2)适当的冷却性能,可降低辊缝中带钢与轧辊的温度,有利于提高轧制速度,发挥轧机的最大生产能力,获得更高的经济效益;3)良好的清洁性,保证退火后的带钢具有光洁的表面,降低产品的次品率;4)良好的防锈蚀能力,使带钢在轧制后可贮存较长时间而无需涂防锈油。
又可作为酸洗后的预涂油;并可防止轧制设备受腐蚀而降低使用寿命;5)其他性能,如稳定性,抗泡性,抵抗杂油性能和控制细菌滋生性能等。
冷轧机组乳化液的研究与应用

冷轧机组乳化液的研究与应用作者:蔡卫娟刘海法来源:《中国新技术新产品》2013年第22期摘要:本文主要介绍了莱钢可逆冷轧机组的乳化液的作用、性能,成分及主要功能。
论述了影响乳化液使用的常见原因及处理方法。
关键词:乳化液;性能;功能;处理方法中图分类号:TG33 文献标识码:A一、乳化液作用1 润滑作用良好的润滑可有效降低摩擦力,良好的挥发性可降低退火时间。
正常平稳的轧制需要轧制油提供均衡稳定的润滑,即轧制油除必须保证稳定的物理和化学特性外,还必须保持数量上的,即吸附量的稳定。
由于轧制油通过分散于乳化液中进行应用。
2 冷却性能轧制过程中工件发生变形所产生的大量的热,也需要由乳化液带走,正确控制乳化液的流量和喷射部份,可以有效控制板温,并调节板形。
在应用乳化液的冷却功能时,除板温的控制外,可以通过乳化液流量的位置的控制,使轧辊的不同部份产生不同程度的热胀冷缩,达到控制板形的目的。
乳化液的冷却性能与油品的应用浓度成反比,浓度越高,冷却能力越低。
其关系如图1所示。
3 乳化液的清洗性能乳化液的清洗主要包括对板面进行清洗,对轧辊和机架进行清洗。
在轧制过程中,除产生铁粉外,还会产生各种高粘性的铁皂体、油品在高温高压下产生的聚合物。
这些异物是影响板面清洁度的主要因素。
二、乳化液成分及主要功能控制乳化液的性能或稳定性的变化,除温度的因素外,基本是由是内部各组分变化所造成的。
表1列出了乳化液的一般组分及含量。
乳化液的性能或性能稳定性对轧制或润滑的影响可以从两个方面进行描述。
乳化液的皂化值、酸值、pH值的变化会导致轧制油物理和化学性能的变化;乳化液的其它指标,如浓度、温度、电导率、氯离子及pH值等指标的变化会引起参与润滑的轧制油的数量上的变化。
这里pH值的变化对两方面都有所影响。
一般在乳化液应用一段时间后,乳化液会逐渐处于一种代谢平衡,其皂化值、酸值、灰分、铁含量等会保持相对稳定,每周一至两次的测试就基本可以控制。
对于浓度、温度、电导率等则由于频繁的加水、加油的影响而不断变化,并且会造成轧制润滑较大的变化,因此必须高频测试。
冷轧乳化液系统使用与改进
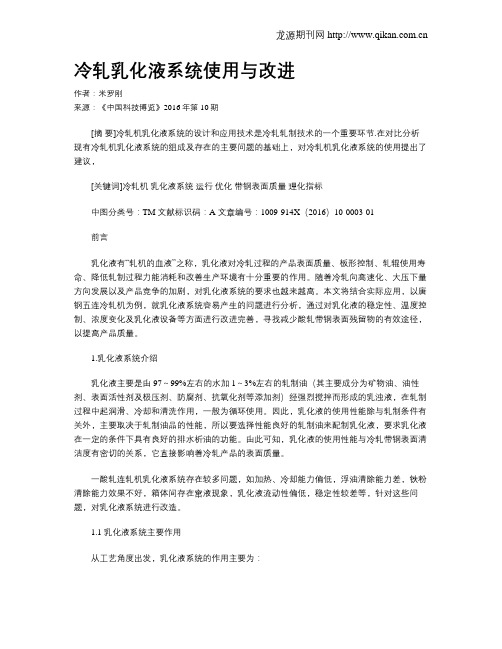
冷轧乳化液系统使用与改进作者:米罗刚来源:《中国科技博览》2016年第10期[摘要]冷轧机乳化液系统的设计和应用技术是冷轧轧制技术的一个重要环节.在对比分析现有冷轧机乳化液系统的组成及存在的主要问题的基础上,对冷轧机乳化液系统的使用提出了建议,[关键词]冷轧机乳化液系统运行优化带钢表面质量理化指标中图分类号:TM 文献标识码:A 文章编号:1009-914X(2016)10-0003-01前言乳化液有“轧机的血液”之称,乳化液对冷轧过程的产品表面质量、板形控制、轧辊使用寿命、降低轧制过程力能消耗和改善生产环境有十分重要的作用。
随着冷轧向高速化、大压下量方向发展以及产品竞争的加剧,对乳化液系统的要求也越来越高。
本文将结合实际应用,以唐钢五连冷轧机为例,就乳化液系统容易产生的问题进行分析,通过对乳化液的稳定性、温度控制、浓度变化及乳化液设备等方面进行改进完善,寻找减少酸轧带钢表面残留物的有效途径,以提高产品质量。
1.乳化液系统介绍乳化液主要是由97~99%左右的水加1~3%左右的轧制油(其主要成分为矿物油、油性剂、表面活性剂及极压剂、防腐剂、抗氧化剂等添加剂)经强烈搅拌而形成的乳浊液,在轧制过程中起润滑、冷却和清洗作用,一般为循环使用。
因此,乳化液的使用性能除与轧制条件有关外,主要取决于轧制油品的性能,所以要选择性能良好的轧制油来配制乳化液,要求乳化液在一定的条件下具有良好的排水析油的功能。
由此可知,乳化液的使用性能与冷轧带钢表面清洁度有密切的关系,它直接影响着冷轧产品的表面质量。
一酸轧连轧机乳化液系统存在较多问题,如加热、冷却能力偏低,浮油清除能力差,铁粉清除能力效果不好,箱体间存在窜液现象,乳化液流动性偏低,稳定性较差等,针对这些问题,对乳化液系统进行改造。
1.1 乳化液系统主要作用从工艺角度出发,乳化液系统的作用主要为:1)润滑:冷轧过程中,乳化液中的润滑油吸附在轧辊和带材的表面上形成一层很薄的油膜,为轧制提供必要的润滑。
冷轧轧制油使用说明及安全说明书书
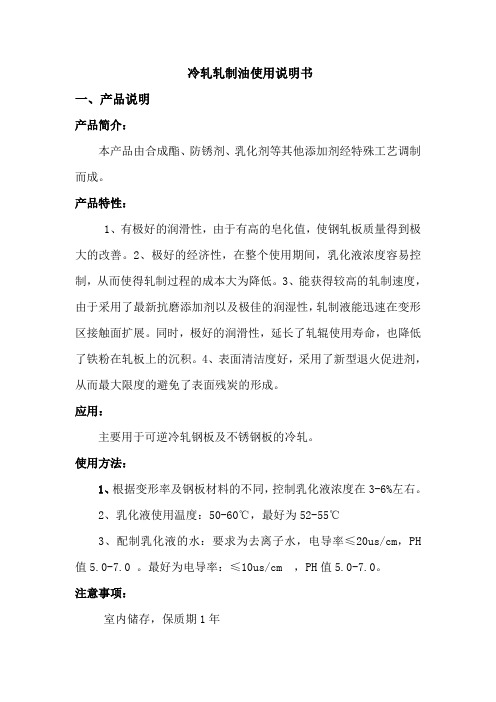
冷轧轧制油使用说明书一、产品说明产品简介:本产品由合成酯、防锈剂、乳化剂等其他添加剂经特殊工艺调制而成。
产品特性:1、有极好的润滑性,由于有高的皂化值,使钢轧板质量得到极大的改善。
2、极好的经济性,在整个使用期间,乳化液浓度容易控制,从而使得轧制过程的成本大为降低。
3、能获得较高的轧制速度,由于采用了最新抗磨添加剂以及极佳的润湿性,轧制液能迅速在变形区接触面扩展。
同时,极好的润滑性,延长了轧辊使用寿命,也降低了铁粉在轧板上的沉积。
4、表面清洁度好,采用了新型退火促进剂,从而最大限度的避免了表面残炭的形成。
应用:主要用于可逆冷轧钢板及不锈钢板的冷轧。
使用方法:1、根据变形率及钢板材料的不同,控制乳化液浓度在3-6%左右。
2、乳化液使用温度:50-60℃,最好为52-55℃3、配制乳化液的水:要求为去离子水,电导率≤20us/cm,PH 值5.0-7.0 。
最好为电导率:≤10us/cm ,PH值5.0-7.0。
注意事项:室内储存,保质期1年包装:170kg/桶二、轧机和乳化液系统清洗A设备准备阶段1、检查所有相关设备,包括排液泵,注入泵,溢流口及管道,脱盐水管道等,保证正常使用。
B乳化液切换清洗从一种乳化液切换到另一种乳化液,由于配方的机制不同,不能相互滥用,必须进行清洗,以使乳化液的影响降到最低,保证新乳化液的功能。
乳化液切换清洗过程如下:1、将轧机收集槽内的乳化液全部打回乳化液箱2、排放乳化液3、清洗乳化液全部循环系统的淤泥(包括轧机周围,收集槽、管道、过滤器、乳化液箱等)4、淤泥清洗完毕后,在乳化液箱中注入足够配制水5、循环2-5小时,清洗所有设备和附属设备6、排放清洗水7、在乳化液箱中注入足够的配制水,升温至35-45℃8、配制合适0.5%浓度的新乳化液9、循环2-5小时,充分清洗所有设备和附属设备10、排放乳化液,准备新乳化液的配制C乳化液的配制在完成必要的清洗工作后,可以进行乳化液的配制。
浅析乳化液在冷轧带钢生产中的应用
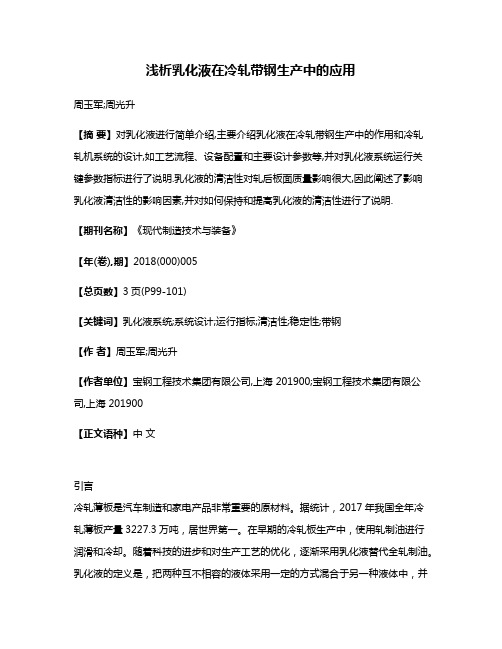
浅析乳化液在冷轧带钢生产中的应用周玉军;周光升【摘要】对乳化液进行简单介绍,主要介绍乳化液在冷轧带钢生产中的作用和冷轧轧机系统的设计,如工艺流程、设备配置和主要设计参数等,并对乳化液系统运行关键参数指标进行了说明.乳化液的清洁性对轧后板面质量影响很大,因此阐述了影响乳化液清洁性的影响因素,并对如何保持和提高乳化液的清洁性进行了说明.【期刊名称】《现代制造技术与装备》【年(卷),期】2018(000)005【总页数】3页(P99-101)【关键词】乳化液系统;系统设计;运行指标;清洁性;稳定性;带钢【作者】周玉军;周光升【作者单位】宝钢工程技术集团有限公司,上海 201900;宝钢工程技术集团有限公司,上海 201900【正文语种】中文引言冷轧薄板是汽车制造和家电产品非常重要的原材料。
据统计,2017年我国全年冷轧薄板产量3227.3万吨,居世界第一。
在早期的冷轧板生产中,使用轧制油进行润滑和冷却。
随着科技的进步和对生产工艺的优化,逐渐采用乳化液替代全轧制油。
乳化液的定义是,把两种互不相容的液体采用一定的方式混合于另一种液体中,并形成相对平衡的系统状态。
分散相通常以小直径的液滴形式存在于连续相中。
在冷轧带钢生产中,将轧制油投加至脱盐水中并进行搅拌和加热,使其混合均匀,供轧机使用。
1 乳化液简述根据乳化液的定义可知,若分散相为油,连续相为水,形成O/W型乳化液(水包油型);若分散相为水,反之形成油包水型乳化液(W/O)。
冷轧轧机生产中的乳化液,通常由基础油、乳化剂和添加剂等组成。
其中,基础油以矿物油为主。
添加剂包括乳化稳定剂、极压机、防锈剂、防腐剂、抗氧剂和杀菌剂等。
常用的冷轧乳化液分为稳定型乳化液、半稳定型乳化液和不稳定性乳化液三大类。
(1)稳定型乳化液,稳定指数ESI一般大于0.6,特点是乳化效率高、乳化液颗粒分布均匀、稳定性好,且退火后带钢板面清洁性好。
(2)半稳定型乳化液,特点是润滑性较好,清洁性较稳态型差,在退火前需要进行脱脂清洗。
乳化液各项性能对冷轧板的实际影响

乳化液各项性能对冷轧板的实际影响一、浓度浓度是分散在乳化液当中的油含量,它对轧制油的性能有很大影响。
浓度过大使润滑状态处于良好状态,容易引起打滑现象浓度高附着力越强,乳化液不稳定,附着力越大……对于钢板轧制有不利的影响浓度过低,摩擦系数升高,压力增大,容易引起热划伤,板面黑等润滑不足的现象.二、PH值PH值是指乳化液中的氢离子的浓度,7以下为酸性,7以上碱性。
正常乳化液PH值控制在5.4~6.2之间为弱酸性,太低或太高都会带来不利影响。
PH值偏低的原因可能来自于酸性,漂洗不够等PH值过高原因:1.酸洗漂洗水过碱性2.乳化液配制水偏碱性3.轧机周围冲洗碱液进入乳液4.加热器蒸汽泄漏5.冷却器循环水泄漏或其它自来水等PH值过高对轧钢带来负面影响破坏油膜,压力过大,板面发黑等杂油混入温度正常50~60度可以发挥乳化液最佳状态过低:板黑,压力大钢的变形量小易断带等过高:冷却不好过热易氧化钢板等三、皂化值:数值是反映轧制油中的润滑成份高低、皂化值高润滑性能越好反之越差皂化值变动原因:轧机泄露液压油、齿轮油进入乳液中,皂化值下降,润滑不足等现象同时消耗油量加大成本上升。
四、铁粉:铁粉过多钢板表面赃污(个人认为50-150,据实际情况而定)铁粉过低对润滑不好,因为少量铁粉对润滑油帮助;铁粉过多,以磁过滤器除掉(不要除太多,以免把油的成分带走太多,对润滑不利)五、酸值:脂肪酸的含量脂肪酸对钢板表面有附着力,对润滑性能和防锈性有良好作用。
如果太多的话对轧机和板面带来污染。
六、氯离子:乳化液中氯过多,给油直接破乳,对轧钢带来压力大,不好控制,极易断带。
钢板表面氯过高前几道次压力大、发黑等给乳化液中的氯离子含量增大。
氯离子升高的原因:加热器、冷却器、泄露漂洗不净,自来水进入等。
七、电导率:纯水不带电导率,杂质越多电导率越高乳化液中电导率越高、杂质越多,有化学反应,对油成分破坏对轧钢带来不必要的影响,多走滤布,定期除杂油等,控制好电导率。
- 1、下载文档前请自行甄别文档内容的完整性,平台不提供额外的编辑、内容补充、找答案等附加服务。
- 2、"仅部分预览"的文档,不可在线预览部分如存在完整性等问题,可反馈申请退款(可完整预览的文档不适用该条件!)。
- 3、如文档侵犯您的权益,请联系客服反馈,我们会尽快为您处理(人工客服工作时间:9:00-18:30)。
(4)机架内的保洁。分厂针对轧机内油泥积累较多,每周检修时提前半小时停机进行热水冲洗
轧机。每月清理乳化液返回槽sl~s3,将其底部沉淀积累的油泥清除,防止通过喷嘴喷射到设备上 造成二次污染。争取做到每季度让专业清理队伍对轧机进行全面清理后,进行热水冲洗。
233
《第十八届全国薄板宽带生产技术信息交流会》论文集
4优化系统工艺参数,提高润滑能力,改善清洁度‘
(1)浓度是润滑的最重要因素,在一定范围内提高S1~¥2浓度,加强润滑可改善带钢表而清 洁度。乳化液浓度在2.O%浓度轧制3.0~O.8 mm产品,表面反射率不足50%,浓度提高至2.8%~ 3.0%,其他条件不变,反射率可提高至50%~60%。 (2)温度在工艺润滑中具有举足轻重的地位,乳化液温度必须严格控制在工艺要求范围内,温 度过高或过低都不利于润滑及清洁度。温度过低利于细菌的繁殖,造成乳化液腐败,同时,较低的 温度不利于轧制油中极压添加剂等成分发挥作用而影响润滑。温度过高则分子热运动加剧,乳化液 颗粒度会逐渐变大,稳定性下降,老化过程加快。辊面温度同样起着重要作用,现场发现,刚换辊 后轧制的带钢普遍较黑,而在轧制300~400t以后,辊面温度及状态均较为理想,带钢表面也亮起 来。对润滑油的有关理论普遍认为变形区温度有一最佳范围利于轧制油润滑性能的发挥,冷辊刚上 机时温度过低,影响润滑,故清洁度较低。 (3)颗粒度的影响。颗粒度是油滴在水相中成正态分布,其分布概率最大粒径称为颗粒度。有 良好的颗粒度分布是润滑良好的基础。颗粒度过大,则乳化液不稳定,油易析出:颗粒度过小,则乳 化液过稳定,油膜不易形成,造成润滑不足。pH值、杂油、剪切作用等因素均可影响颗粒度分布, 进而影响润滑和清洁度。还有一点从在生产中一也不容忽视,即新配制的乳化液颗粒度较大,往往 需要1~3个班的连续运行才能够获得理想的颗粒度分布,在这之前轧出的带钢一般清洁度都不能让 人满意。在大量加油后,乳化液的颗粒度同样会有所增大,轧出的带钢表而残油量大,板而较黑。 为此分厂对乳化液操作人员有明确规定,加油、加水必须遵循少量多次的原则。乳化液浓度勤检查, 及时补油补水。
Abstract
This article introduced the construction and function of emulsion system in the used the emulsion system for the low cleanliness of the strip in production,take measure activity during the production
和油泥粘度大,流动性差,其喷射到轧机上极易黏附在轧机内,日集月累后机架内设备上积累了大 量油泥,在外界力量作用下松动落到轧辊或钢板上,极易造成辊印和板面缺陷,见图3。
图3
(3)轧后板面残留物多,板面清洁度差,给后道工序的生产造成影响。板而残留物主要来自冷
轧过程。在高温、高压的轧制变形区内,带钢与轧辊磨损产生大量直径l~3岬的铁粉微粒,这些
高。
3
针对生产过程中出现的问题,优化工艺参数,制定相应措旌
因为S3槽乳化液浓度过高,不仅不能起到清洗带钢表面的作用,反而污染了带钢表面降低了
其清洁度。首先针对F3、F4机架间乳化液窜流问题,进行设备改进。在F3、F4机架间底部的乳化
232
《第十八届全国薄板宽带生产技术信息交流会》论文集
液收集盘之间焊接一块高500ram的钢板以挡住乳化液窜流,再在S3槽中架设一潜水泵,将s3槽 内高浓度的乳化液抽入到S1、S2槽后,补水稀释后降低浓度。通过以上措施,逐步将S3槽乳化液 浓度控制在O.5%。 热划伤、乳化液及板面清洁度差说明乳化液在某种条件下润滑能力不好,不能满足生产的需要。 所谓的热划伤是钢板冷轧时,在工作辊与钢板的摩擦表面偶尔产生的表面损伤。在高速轧制的过程 中,压下量达到一定数值,因轧制变形功过大而产生大量的热能,这时,润滑油膜破裂,带钢与轧 辊易发生局部粘结,并在轧辊表面不均匀扩展,带材表面变得粗糙进一步扩展开裂。一般说来,只 有在大压下量和乳化液没有充足润滑的轧制条件下,摩擦表面温度达到临界温度时,才会产生这种 缺陷。研究和分析产生热划伤条件的理论很多,其中最为实用的是佐藤提出的,如图4所示的理论, 用油膜厚度当量和钢板表面温度两个坐标表示产生热滑伤的条件,并将实验点作曲线,成为能定量 控制产生热滑伤的界限。
230
《第十八届全国薄板宽带生产技术信息交流会》论文集
图1
图2
23l
《第十八届全国薄板宽带生产技术信息交流会》论文集
(2)在冷轧轧制过程中,在辊缝区内润滑条件不好,其高温、高压的轧制变形区内,带钢与轧
辊磨损产生大量直径在1---'3岬的铁粉微粒,这些铁粉颗粒很大一部分由乳化液冲刷进入乳化液系
统。这些铁粉为活性铁带有大量的电荷,其在乳化液中的轧制油滴相互吸引形成铁皂和油泥,铁皂
用s3槽乳化液。针对的主要是出口厚度为O.5mm,(含)以下的带钢,这些规格压下率较大,多在
70%以上,所以对轧制过程中的乳化液的润滑能力要求较高,在轧制时,根据产品规格、合同要求 等选择不同模式。
2乳化液系统使用过程中出现的问题
(1)-B钢1捍酸轧机组设计为4机架6辊UCM轧机,其产品等级主要为CQ、DQ、DDQ和HSLA, 轧机入口厚度范围为1.5~5.5mm,出口为0.3~2.5mm,设计最大压下率为80%,实际在生产中常 常超过最大设计。与其它同类轧机相比,4机架冷连轧机单位负荷较高,特别是F3,在轧制一些极 限规格时相对压下率可以达到45~50%,润滑不好的情况下,F3工作辊特别是下工作辊极易出现 划伤,见图1。这种轧辊上的划伤发生时,同时也发生在带钢表面,造成带钢表面大量无手感短线 状热划伤。见图2
PL-TCM.analyzed factors during
and hot scratch in the initial stages of PL-TCM put
to
solve the problem
to
hot scratch,improve the
cleanliness of strip from Key words
1乳化液系统的组成及作用
1.1循环系统 循环系统是整个乳化液系统核心之一,分为3个清洁槽S1~S3和3个与之相对应的返回槽sl-s3 及相关管路。S1、s2体积为200m3,配有磁性分离器,3个大功率搅拌器,蒸汽加热系统和一套溢 流吹扫;s3体积为80m3除了有以上设备还配有一套撇油器,撇除泄漏到乳化液中的杂油。sl、s2 体积为50m3,s3体积为10m3,配有一套蒸汽加热器和搅拌器:S1~S3配有5台喷射泵,sl~s3 配有5台返回泵;正常工作时,四用一备。 1.2喷射系统 喷射系统主要作用是将乳化液喷射到F1~F4入口带钢与工作辊接触的辊缝区进行润滑、F4入
1.3相关辅助设备 为保证乳化液系统稳定的运行,除了以上这些工作设备外,还有大量的辅助设备。@30m3原 油槽,储存原油,保证乳化液浓度。②10m3预配槽,将轧制油配成15%,便于轧制油充分乳化。
⑨50m3热水槽,冲洗轧机油泥,保证机架内的清洁度。④霍夫曼过滤器,乳化液系统共有两套过 滤器;S1、S2共有一套,S3共用一套。霍夫曼过滤器的主要作用是过滤乳化液中粒径较大的杂质, 保证乳化液的清洁。 1.4乳化液系统的使用 sl槽乳化液浓度为2.0~2.5%,S2槽乳化液浓度为3.0~3.5%:S3浓度为O.5%左右,一般使 用在F4小压下的情况下,其主要的作用是对轧后钢板清洗,所以浓度要求越低越好。乳化液系统 共有4种使用模式SPl~"SP4:SPl模式为机架F1~F4全部使用s1槽,F4机架工作辊使用光辊, 轧机出口厚度为厚规格,但对板面粗糙度有特殊要求冷轧卷;SP2模式为机架F1~F4全部使用S2 槽,F4、机架工作辊使用光辊,在这种模式下主要是针对一些压下率较大且热卷屈服强度较高的钢种, 如硅钢,高强度低合金钢等;SP3模式为轧机使用较多的模式机架F1~F3使用Sl槽,F4机架工作 辊使用毛辊,主要针对常规厚规格的冷轧卷,。SP4模式为F1~F3使用S2槽高浓度乳化液,F4使
PL-TCM in the MASTEEL.
cold rolling,emulsion,cleanliness,measurement
0
引言
1捍冷轧线是马钢“十五”重点技改项目,引进日本三菱一日立技术,连轧机采用日立的4机架
6辊UCM轧机。与轧机本体设备一同引进的还有轧机冷却润滑系统一乳化液系统。马钢l撑冷轧的 乳化液系统分为循环系统、喷射系统及相关辅助设备。在所有冷轧带钢加工过程中都要涉及润滑和 冷却的问题。这是因为冷轧时带钢的变形抗力大、表而质量要求高,摩擦的影响很明显的缘故。因 此,为了降低轧制压力,减小摩擦的影响,冷轧过程中广泛采用乳化液进行冷却和润滑,乳化液为 低浓度的8L¥0油与脱盐水混合物。冷轧过程中的冷却和润滑是实现塑性变形和获得良好板形以及减 少能源消耗的关键之一,同时也降低了轧后板面残留物,为下道工序生产创造了良好的条件。
钢 板 表 面 温 度 ℃
油膜厚度当量,
图4
∥Ⅲ
根据上图可以定性的说,带钢表面温度越低,润滑油膜越厚,产生热划伤的概率越小。这样, 从防治热划伤的角度出发,可以采用降低带钢表面温度和增大润滑油膜厚度的策略。在轧机乳化液 流量一定的前提下,最主要的防止喷嘴的堵塞,使轧辊有局部冷却盲区而造成该处局部温升过高导 致热划伤。为此分厂根据投产以来的经验,规定每周检修时施减少喷嘴堵塞情况的发生。其次,通过现场大量 调查分析,发现热划伤主要出现F3机架下表面,主要原因是因为本机组入口原料为CSP所生产,非 常规热轧,决定了其硬度较高,其次冷轧机为4机架,带钢通过前两机架大压下后,带钢加工硬化 程度已经很大,这是对润滑的条件要求更为苛刻,若没有良好的润滑条件就会出现划伤。在和轧制 油生产厂家确定热划伤原因后,共同调整轧制油配方。调整的方向主要为提高轧制油的皂化值、提 高辊缝区油膜厚度和油膜的承压能力。经过几次配方的调整后,乳化液已经基本稳定,满足了生产 需要,成功解决了薄规格热划伤问题。