如何用山高样本选择刀具及切削参数
2.6刀具几何参数与切削用量的选择
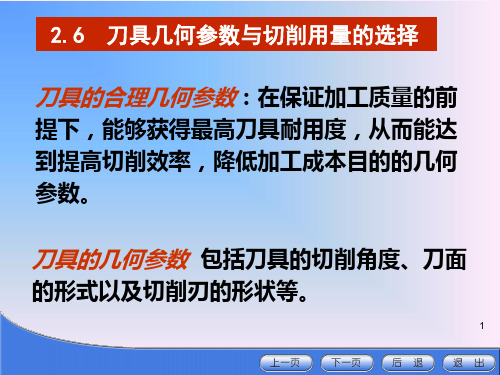
当工件材料强度较大、硬度较高时,由于单位切削力 工件材料强度较大、硬度较高时 切削温度容易升高,为了提高切削刃强度, 大,切削温度容易升高,为了提高切削刃强度,增加 刀头导热面积和容热体积,前角宜取小值。 刀头导热面积和容热体积,前角宜取小值。
10
其他参数的选择
前角的合理数值不是孤立的, 前角的合理数值不是孤立的,还和刀面形状及 刃区参数以及其他角度有关, 刃区参数以及其他角度有关,特别是和刃倾角有密 切关系。 切关系。 例如:带负倒棱的刀具允许采用较大前角; 例如:带负倒棱的刀具允许采用较大前角; 大前角刀具常与负刃倾角相匹配来保证切削刃强度 和抗冲击能力。 和抗冲击能力。 许多先进刀具就是在针对某种加工条件, 许多先进刀具就是在针对某种加工条件,善于 灵活运用这些原则而产生的。 灵活运用这些原则而产生的。
1
为什么要选择刀具合理几何参数? 为什么要选择刀具合理几何参数?
刀具的几何参数对切屑变形、切削力、 刀具的几何参数对切屑变形、切削力、切削 温度和刀具磨损都有显著影响, 温度和刀具磨损都有显著影响,从而影响切削加 工生产率、刀具耐用度、加工质量和加工成本。 工生产率、刀具耐用度、加工质量和加工成本。
7
工件材料
1.加工塑性材料时,切屑呈带状,沿刀具前面流出时 1.加工塑性材料时 切屑呈带状, 加工塑性材料 和前面接触长度较长,摩擦较大, 和前面接触长度较长,摩擦较大,为减小变形和摩 一般都采用正前角 工件材料塑性愈大, 正前角。 擦,一般都采用正前角。工件材料塑性愈大,强度 和硬度愈低时,前角应选得愈大。 和硬度愈低时,前角应选得愈大。
课题2 刀具几何参数的合理选择及切削用量的选择

各位领导,各位老师:你们下午好!我说课的题目是:课题2。
内容是:刀具几何参数的合理选择、刀具切削用量的选择本节是《数控加工工艺与编程基础》人民邮电出版社.于万成主编,第一章第一节的内容。
我主要从教材分析,教法设计,学法指导,教学过程,几点说明等五个方面进行阐述。
一、教材分析:从以下四方面加以分析:1、地位作用:本节主要阐述刀具的几何参数、刀具的几何结构,以及刀具的几何角度对切削用量三要素的影响。
本节知识从理论的角度介绍了刀具的几何参数与工件加工性能之间的联系。
对于生产实践有重要指导意义,也为后续章节的学习奠定了基础,所以本节内容是本章的重点之一。
2、教学目标:根据大纳要求,结合学生特点,我将教学目标定为知识目标,能力目标,思想目标三个方面。
知识目标:1、明确刀具几何参数基本概念;2、会根据加工具体情况正确选择和确定刀具材料、刀具几何参数、切削用量能力目标:(1)培养学生观察、分析及综合归纳刀具几何参数能力。
(2)培养学生主动探究、协作学习的能力。
思想目标:培养学生树立辩证唯物主义的世界观和方法论。
3、重点与难点教学重点:刀具几何参数、切削用量合理选择的基本概念及各参数的功用,之所以将其定义为教学重点,是因为刀具的几何参数相对复杂,难于理解,因此定为教学难点。
教学难点:应用上述功用合理选择刀具几何参数和切削用量,合理的选择刀具几何参数,切削用量,对于工件的加工质量有很大的影响,因此将此定义为教学难点。
4、教材处理:本着突出重点和突破难点的原则,我对教材做如下处理(1)通过直观演示与生产实践相结合方法,引导学生循序渐进,步步深入, 通过观察、分析、归纳总结讲解刀具的材料选择,刀具的几何结构,刀具的几何参数。
(2)通过列举加工实例,结合其斯沃仿真软件的加工的学习,使刀具的几何结构,刀具的几何参数的合理选择,切削用量的合理选择及其影响变得简单易懂。
二、教法设计:主要采用直观演示和启发式教学方法,通过生产实例-创设问题情境-提出问题-探究验证-归纳总结-实践应用等环节,体现“教为主导,学为主体”的教学原则。
如何用山高样本选择刀具及切削参数
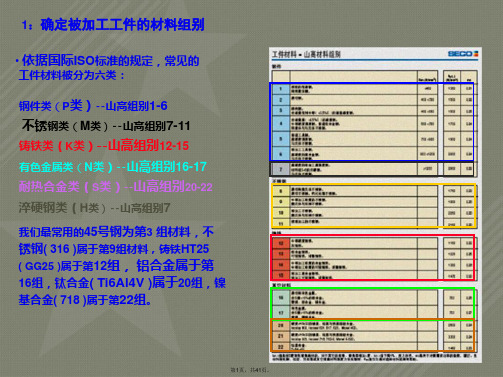
8:常见车削切削问题及解决方法
第11页,共41页。
8:常见车削切削问题及解决方法
第12页,共41页。
How to select the tool & cutting data of MDT tools from the Turning catalogues
MDT标准车刀及切削参数的 基本选择方法
我们最常用的45号钢为第3 组材料,不 锈钢( 316 )属于第9组材料,铸铁HT25 ( GG25 )属于第12组, 铝合金属于第16 组,钛合金( Ti6Al4V )属于20组,镍基 合金( 718 )属于第22组。
第14页,共41页。
2:确定刀杆类型及刀杆尺寸大小、 刀片类型及大小、切削宽度等
铣刀、正方形刀片方肩铣刀、三角形刀 片方肩铣刀等等。 • 按照常规及顺铣的要求,刀盘直径一般
为被加工宽度的1.25倍为佳。
• 刀片的规格及大小主要是依据加工要求
及被加工的余量大小来选择。
• 刀盘齿数的疏与密主要是依据加工的效 率、节拍要求和机床功率、工件夹持刚
性等决定。
比如方肩铣削加工我们一般首选“旋风”
第3页,共41页。
4:您也可以在样本中了解到有关刀杆的其它信息
• 这些信息包括: 刀杆的实际高度尺寸、宽度尺寸、刀杆长度、主偏角、重量、可加工的 最小孔径、刀垫型号、压板型号、锁紧螺钉、扳手规格等等。
第4页,共41页。
5:术语和常用的切削参数计算公式
每分钟切削进给率
F = n*f
( mm/ min )
及被加工的余量大小来选择。
如普通外圆及端面加工及最大达4倍的切 槽刀具用于钛合金Ti6Al4V加工我们可选 刀杆:CFMR2525M03(钛合金加工)
机械加工中数控机床刀具切削参数的选择方法

机械加工中数控机床刀具切削参数的选择方法引言:数控机床作为现代制造业中不可或缺的关键设备, 切削参数的选择直接影响加工质量和效率。
机械加工中,数控机床刀具的切削参数选择是非常重要的一个环节,它直接影响到加工质量、加工效率和刀具寿命。
因此,正确选择切削参数对于提高加工效率和降低加工成本具有重要意义。
本文将介绍机械加工中数控机床刀具切削参数的选择方法。
一、切削速度的选择切削速度是数控机床刀具切削过程中最重要的一个参数,对于切削质量、切削力、切削温度等方面都有直接影响。
选择切削速度主要取决于工件材料的硬度、切削刃口的材料和硬度以及数控机床的能力。
一般来说,硬度较高的材料需要较低的切削速度,而硬度较低的材料则可以选择较高的切削速度。
在合理范围内选择切削速度,不仅可以提高加工效率,还可以保证刀具寿命和加工质量。
切削速度的选择应根据材料和刀具的特性进行调整,经验公式可以作为初步的参考。
二、进给率的选择进给率是切削过程中刀具每单位时间切削的长度,也是衡量切削效率的重要指标。
进给率的选择应考虑切削工艺、切削质量要求以及刀具的特性。
通常情况下,进给率过大容易导致过载,切削力过大,切削质量下降;进给率过小则会浪费加工时间,低效率。
因此,选择合适的进给率对于保持加工质量和提高加工效率至关重要。
在选择进给率时,应考虑切削深度、材料的硬度以及机床的刚性等因素。
三、切削深度的选择切削深度是刀具进入工件的深度,它直接影响加工效率和切削力。
切削深度的选择应根据工件材料的硬度、机床的刚性、刀具的强度等因素综合考虑。
对于硬度较高的材料,一般采用较小的切削深度以减小切削力,避免刀具损坏。
而对于硬度较低的材料,可以适当增加切削深度以提高加工效率。
切削深度的选择过大或过小都会对加工效果带来不利影响,应根据实际情况进行综合考虑。
四、切削角度的选择切削角度是切削刃部分与工件接触的角度。
切削角度的选择要根据切削力、切削声音、加工精度等因素进行综合考虑。
机械加工中的刀具选型与切削参数优化
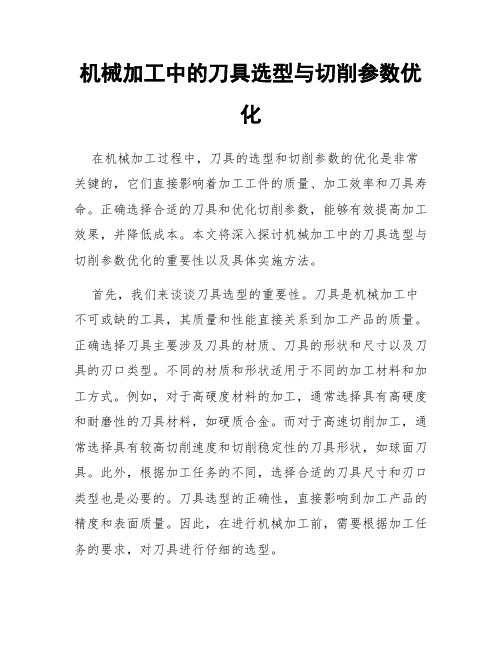
机械加工中的刀具选型与切削参数优化在机械加工过程中,刀具的选型和切削参数的优化是非常关键的,它们直接影响着加工工件的质量、加工效率和刀具寿命。
正确选择合适的刀具和优化切削参数,能够有效提高加工效果,并降低成本。
本文将深入探讨机械加工中的刀具选型与切削参数优化的重要性以及具体实施方法。
首先,我们来谈谈刀具选型的重要性。
刀具是机械加工中不可或缺的工具,其质量和性能直接关系到加工产品的质量。
正确选择刀具主要涉及刀具的材质、刀具的形状和尺寸以及刀具的刃口类型。
不同的材质和形状适用于不同的加工材料和加工方式。
例如,对于高硬度材料的加工,通常选择具有高硬度和耐磨性的刀具材料,如硬质合金。
而对于高速切削加工,通常选择具有较高切削速度和切削稳定性的刀具形状,如球面刀具。
此外,根据加工任务的不同,选择合适的刀具尺寸和刃口类型也是必要的。
刀具选型的正确性,直接影响到加工产品的精度和表面质量。
因此,在进行机械加工前,需要根据加工任务的要求,对刀具进行仔细的选型。
其次,切削参数的优化也是机械加工中必不可少的环节。
切削参数包括切削速度、进给速度和切削深度。
合理的切削参数选取可以提高加工效率和减少成本。
其中,切削速度是刀具切削单位时间内的切削长度,其选择应考虑工件材料和刀具材料的硬度以及刀具的耐磨性。
如果切削速度过高,可能导致刀具磨损严重,甚至断裂。
如果切削速度过低,则会降低加工效率。
进给速度是刀具单位时间内加工给定长度的线速度,其合理选择可以有效减少刀具的磨损和提高加工表面质量。
切削深度指的是刀具在切削过程中切削的最大深度。
合理选择切削深度可以提高加工效率和表面质量。
但是,切削深度过大可能会导致刀具的振动和过度磨损。
因此,在选择切削参数时,需要综合考虑刀具和工件的特性,以及加工工艺要求,采用试切法进行优化。
为了实现刀具选型与切削参数的优化,我们可以采取以下方法:首先,我们可以参考刀具制造商提供的技术文档和刀具目录。
刀具制造商通常会提供刀具材料、形状、尺寸和刃口类型等详细信息,供用户选择。
刀具及切削参数选择
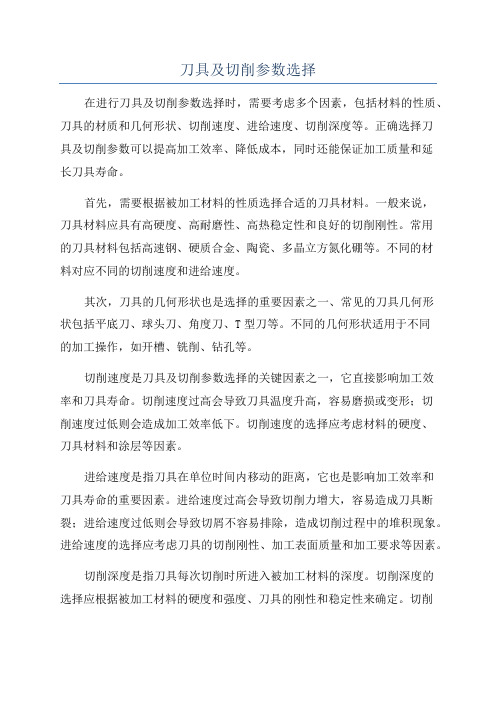
刀具及切削参数选择在进行刀具及切削参数选择时,需要考虑多个因素,包括材料的性质、刀具的材质和几何形状、切削速度、进给速度、切削深度等。
正确选择刀具及切削参数可以提高加工效率、降低成本,同时还能保证加工质量和延长刀具寿命。
首先,需要根据被加工材料的性质选择合适的刀具材料。
一般来说,刀具材料应具有高硬度、高耐磨性、高热稳定性和良好的切削刚性。
常用的刀具材料包括高速钢、硬质合金、陶瓷、多晶立方氮化硼等。
不同的材料对应不同的切削速度和进给速度。
其次,刀具的几何形状也是选择的重要因素之一、常见的刀具几何形状包括平底刀、球头刀、角度刀、T型刀等。
不同的几何形状适用于不同的加工操作,如开槽、铣削、钻孔等。
切削速度是刀具及切削参数选择的关键因素之一,它直接影响加工效率和刀具寿命。
切削速度过高会导致刀具温度升高,容易磨损或变形;切削速度过低则会造成加工效率低下。
切削速度的选择应考虑材料的硬度、刀具材料和涂层等因素。
进给速度是指刀具在单位时间内移动的距离,它也是影响加工效率和刀具寿命的重要因素。
进给速度过高会导致切削力增大,容易造成刀具断裂;进给速度过低则会导致切屑不容易排除,造成切削过程中的堆积现象。
进给速度的选择应考虑刀具的切削刚性、加工表面质量和加工要求等因素。
切削深度是指刀具每次切削时所进入被加工材料的深度。
切削深度的选择应根据被加工材料的硬度和强度、刀具的刚性和稳定性来确定。
切削深度过大会导致切削力增大,容易造成刀具断裂;切削深度过小则会导致加工效率低下。
此外,还需要考虑刀具的冷却方式和切削液的选择。
刀具在切削过程中会产生大量的热量,如果不及时冷却,会导致刀具温度过高,影响刀具寿命。
常见的冷却方式包括气体冷却、液体冷却和固体冷却等。
切削液的选择应考虑被加工材料的性质和切削过程中的润滑和冷却效果。
综上所述,刀具及切削参数选择是一个综合考虑材料性质、刀具几何形状、切削速度、进给速度、切削深度、冷却方式和切削液等多个因素的过程。
刀具及切削参数选择
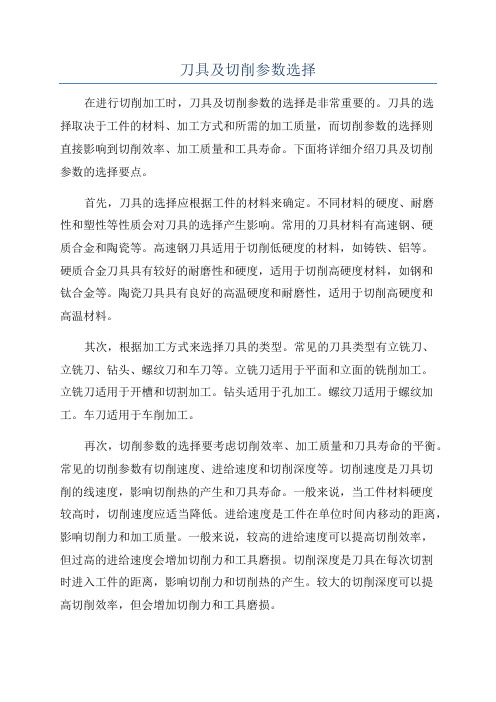
刀具及切削参数选择在进行切削加工时,刀具及切削参数的选择是非常重要的。
刀具的选择取决于工件的材料、加工方式和所需的加工质量,而切削参数的选择则直接影响到切削效率、加工质量和工具寿命。
下面将详细介绍刀具及切削参数的选择要点。
首先,刀具的选择应根据工件的材料来确定。
不同材料的硬度、耐磨性和塑性等性质会对刀具的选择产生影响。
常用的刀具材料有高速钢、硬质合金和陶瓷等。
高速钢刀具适用于切削低硬度的材料,如铸铁、铝等。
硬质合金刀具具有较好的耐磨性和硬度,适用于切削高硬度材料,如钢和钛合金等。
陶瓷刀具具有良好的高温硬度和耐磨性,适用于切削高硬度和高温材料。
其次,根据加工方式来选择刀具的类型。
常见的刀具类型有立铣刀、立铣刀、钻头、螺纹刀和车刀等。
立铣刀适用于平面和立面的铣削加工。
立铣刀适用于开槽和切割加工。
钻头适用于孔加工。
螺纹刀适用于螺纹加工。
车刀适用于车削加工。
再次,切削参数的选择要考虑切削效率、加工质量和刀具寿命的平衡。
常见的切削参数有切削速度、进给速度和切削深度等。
切削速度是刀具切削的线速度,影响切削热的产生和刀具寿命。
一般来说,当工件材料硬度较高时,切削速度应适当降低。
进给速度是工件在单位时间内移动的距离,影响切削力和加工质量。
一般来说,较高的进给速度可以提高切削效率,但过高的进给速度会增加切削力和工具磨损。
切削深度是刀具在每次切割时进入工件的距离,影响切削力和切削热的产生。
较大的切削深度可以提高切削效率,但会增加切削力和工具磨损。
此外,还应考虑冷却润滑剂的选择和使用。
合适的冷却润滑剂可以降低切削热的产生,减小工具磨损,提高加工质量。
综上所述,刀具及切削参数的选择需要考虑工件材料、加工方式和所需加工质量。
合理选择刀具类型和切削参数可以提高切削效率、加工质量和工具寿命。
在实际应用中,还需要根据具体情况进行调整和优化。
解决数控机床技术中的刀具选择和切削参数问题
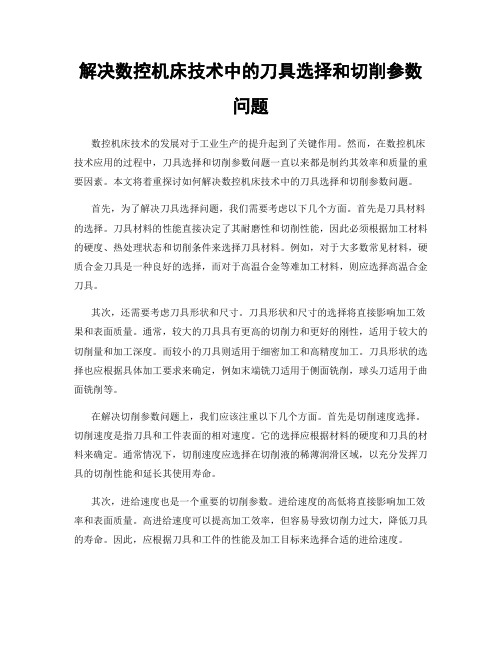
解决数控机床技术中的刀具选择和切削参数问题数控机床技术的发展对于工业生产的提升起到了关键作用。
然而,在数控机床技术应用的过程中,刀具选择和切削参数问题一直以来都是制约其效率和质量的重要因素。
本文将着重探讨如何解决数控机床技术中的刀具选择和切削参数问题。
首先,为了解决刀具选择问题,我们需要考虑以下几个方面。
首先是刀具材料的选择。
刀具材料的性能直接决定了其耐磨性和切削性能,因此必须根据加工材料的硬度、热处理状态和切削条件来选择刀具材料。
例如,对于大多数常见材料,硬质合金刀具是一种良好的选择,而对于高温合金等难加工材料,则应选择高温合金刀具。
其次,还需要考虑刀具形状和尺寸。
刀具形状和尺寸的选择将直接影响加工效果和表面质量。
通常,较大的刀具具有更高的切削力和更好的刚性,适用于较大的切削量和加工深度。
而较小的刀具则适用于细密加工和高精度加工。
刀具形状的选择也应根据具体加工要求来确定,例如末端铣刀适用于侧面铣削,球头刀适用于曲面铣削等。
在解决切削参数问题上,我们应该注重以下几个方面。
首先是切削速度选择。
切削速度是指刀具和工件表面的相对速度。
它的选择应根据材料的硬度和刀具的材料来确定。
通常情况下,切削速度应选择在切削液的稀薄润滑区域,以充分发挥刀具的切削性能和延长其使用寿命。
其次,进给速度也是一个重要的切削参数。
进给速度的高低将直接影响加工效率和表面质量。
高进给速度可以提高加工效率,但容易导致切削力过大,降低刀具的寿命。
因此,应根据刀具和工件的性能及加工目标来选择合适的进给速度。
另外,切削深度也是一个需要考虑的切削参数。
切削深度的选择应根据工件的材料、形状和硬度来进行合理判断。
一般而言,切削深度越大,加工效率越高,但过大的切削深度会增加切削力,影响刀具寿命和表面质量。
因此,在选择切削深度时应综合考虑工艺要求。
最后,还应该注意刀具的冷却和润滑。
切削过程中的高温是导致刀具磨损和断裂的主要原因之一。
因此,通过切削液进行冷却和润滑是非常重要的。
刀具切削参数的选用原则
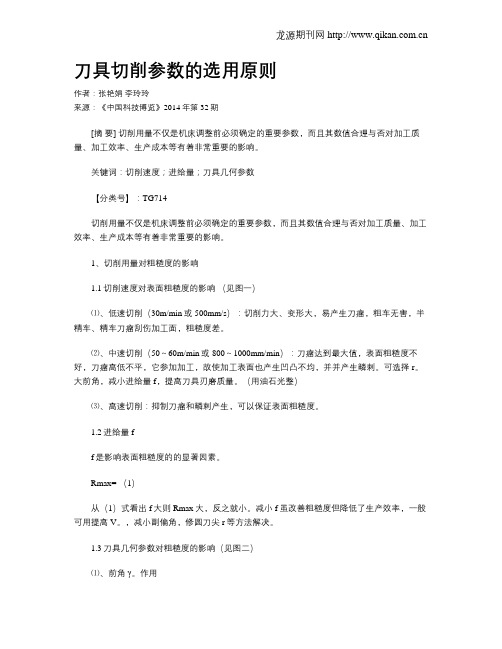
刀具切削参数的选用原则作者:张艳娟李玲玲来源:《中国科技博览》2014年第32期[摘要] 切削用量不仅是机床调整前必须确定的重要参数,而且其数值合理与否对加工质量、加工效率、生产成本等有着非常重要的影响。
关键词:切削速度;进给量;刀具几何参数【分类号】:TG714切削用量不仅是机床调整前必须确定的重要参数,而且其数值合理与否对加工质量、加工效率、生产成本等有着非常重要的影响。
1、切削用量对粗糙度的影响1.1切削速度对表面粗糙度的影响(见图一)⑴、低速切削(30m/min或500mm/s):切削力大、变形大,易产生刀瘤,粗车无害,半精车、精车刀瘤刮伤加工面,粗糙度差。
⑵、中速切削(50~60m/min或800~1000mm/min):刀瘤达到最大值,表面粗糙度不好,刀瘤高低不平,它参加加工,故使加工表面也产生凹凸不均,并并产生鳞刺。
可选择r。
大前角,减小进给量f,提高刀具刃磨质量。
(用油石光整)⑶、高速切削:抑制刀瘤和鳞刺产生,可以保证表面粗糙度。
1.2进给量ff是影响表面粗糙度的的显著因素。
Rmax= (1)从(1)式看出f大则Rmax大,反之就小。
减小f虽改善粗糙度但降低了生产效率,一般可用提高V。
,减小副偏角,修圆刀尖r等方法解决。
1.3刀具几何参数对粗糙度的影响(见图二)⑴、前角γ。
作用使刀具刃口锋利,增大前角γ。
可以用来精加工,但刀具强度减小,切削薄,故散热体积小,刀具磨损快。
在保证刀具强度及寿命的情况下选择大γ前角。
⑵、后角α。
增大α。
,避免刀具后面的摩擦,减小了加工面的硬化,同时也使刀刃锋利,减小了加工表面的硬化。
精加工时应该适度增大α。
≥8°⑶、主偏角Kf,副偏角Kf′,刀尖圆弧减小主偏角Kf则Rmax减小,会使背向力增大,故在实际生产中减少副偏角和增大刀尖r 来使残余金属减少。
切削速度与粗糙度曲线图一副偏角Kf′与表面粗糙度Rmax/um曲线图二2、刀具几何参数的选择几何参数:刀具角度、前面与后面型式、切削刃和刃口型状。
机械制造基础:刀具及切削参数选用
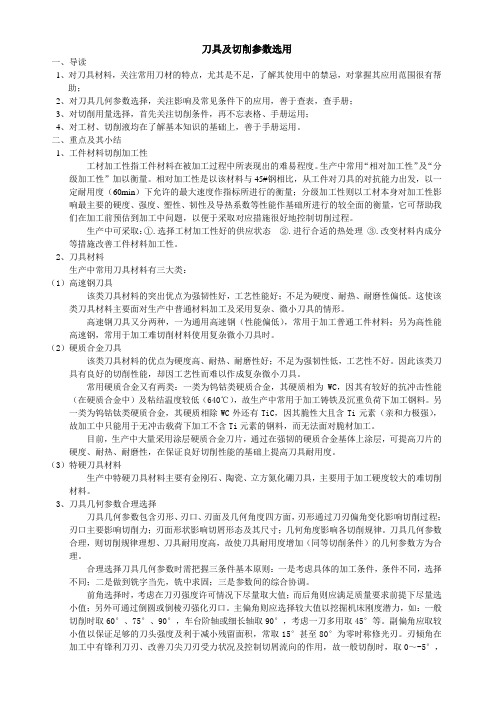
刀具及切削参数选用一、导读1、对刀具材料,关注常用刀材的特点,尤其是不足,了解其使用中的禁忌,对掌握其应用范围很有帮助;2、对刀具几何参数选择,关注影响及常见条件下的应用,善于查表,查手册;3、对切削用量选择,首先关注切削条件,再不忘表格、手册运用;4、对工材、切削液均在了解基本知识的基础上,善于手册运用。
二、重点及其小结1、工件材料切削加工性工材加工性指工件材料在被加工过程中所表现出的难易程度。
生产中常用“相对加工性”及“分级加工性”加以衡量。
相对加工性是以该材料与45#钢相比,从工件对刀具的对抗能力出发,以一定耐用度(60min)下允许的最大速度作指标所进行的衡量;分级加工性则以工材本身对加工性影响最主要的硬度、强度、塑性、韧性及导热系数等性能作基础所进行的较全面的衡量,它可帮助我们在加工前预估到加工中问题,以便于采取对应措施很好地控制切削过程。
生产中可采取:①.选择工材加工性好的供应状态②.进行合适的热处理③.改变材料内成分等措施改善工件材料加工性。
2、刀具材料生产中常用刀具材料有三大类:(1)高速钢刀具该类刀具材料的突出优点为强韧性好,工艺性能好;不足为硬度、耐热、耐磨性偏低。
这使该类刀具材料主要面对生产中普通材料加工及采用复杂、微小刀具的情形。
高速钢刀具又分两种,一为通用高速钢(性能偏低),常用于加工普通工件材料;另为高性能高速钢,常用于加工难切削材料使用复杂微小刀具时。
(2)硬质合金刀具该类刀具材料的优点为硬度高、耐热、耐磨性好;不足为强韧性低,工艺性不好。
因此该类刀具有良好的切削性能,却因工艺性而难以作成复杂微小刀具。
常用硬质合金又有两类:一类为钨钴类硬质合金,其硬质相为WC,因其有较好的抗冲击性能(在硬质合金中)及粘结温度较低(640℃),故生产中常用于加工铸铁及沉重负荷下加工钢料。
另一类为钨钴钛类硬质合金,其硬质相除WC外还有TiC,因其脆性大且含Ti元素(亲和力极强),故加工中只能用于无冲击载荷下加工不含Ti元素的钢料,而无法面对脆材加工。
刀具与切削参数选择
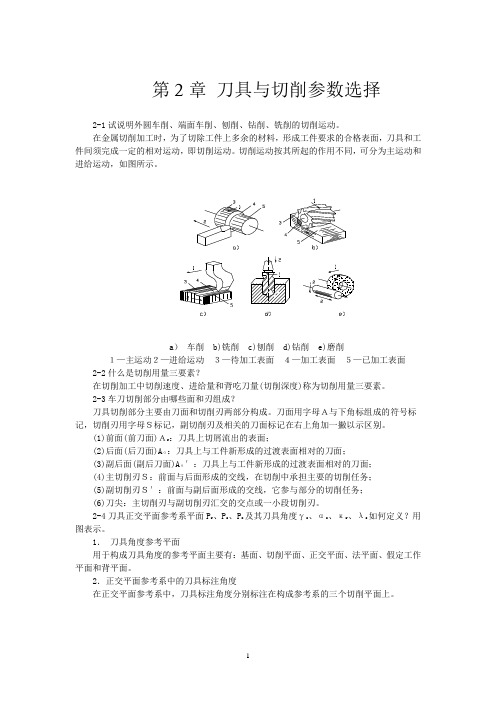
第2章刀具与切削参数选择记,切削刃用字母S标记,副切削刃及相关的刀面标记在右上角加一撇以示区别。
(1)前面(前刀面)Ar:刀具上切屑流出的表面;(2)后面(后刀面)Aα:刀具上与工件新形成的过渡表面相对的刀面;(3)副后面(副后刀面)Aα′:刀具上与工件新形成的过渡表面相对的刀面;(4)主切削刃S:前面与后面形成的交线,在切削中承担主要的切削任务;(5)副切削刃S′:前面与副后面形成的交线,它参与部分的切削任务;(6)刀尖:主切削刃与副切削刃汇交的交点或一小段切削刃。
2-4刀具正交平面参考系平面P r、P s、P o及其刀具角度γo、αo、κr、λs如何定义?用图表示。
1.刀具角度参考平面用于构成刀具角度的参考平面主要有:基面、切削平面、正交平面、法平面、假定工作平面和背平面。
2.正交平面参考系中的刀具标注角度在正交平面参考系中,刀具标注角度分别标注在构成参考系的三个切削平面上。
o o r r s2-7端面车削时,刀尖高(或低)于工件中心时工作角度(前、后角)有何变化?2-8试画图说明切削过程的三个变形区及各产生何种变形?面对已加工表面进行挤压,使已加工表面产生变形,造成纤维化和加工硬化。
2-9切屑有哪些种类?各种切屑在什么情况下形成?由于工件材料性质和切削条件不同,切削层变形程度也不同,因而产生的切屑形态也多种多样。
主要有以下四种类型:带状切屑、节状切屑、粒状切屑、崩碎切屑。
(1)带状切屑它的内表面是光滑的,外表面呈毛茸状。
加工塑性金属时,在切削厚度较小、切削速度较高、刀具前角较大的工况条件下常形成此类切屑。
(2)节状切屑又称挤裂切屑。
它的外表面呈锯齿形,内表面有时有裂纹。
在切削速度较低、切削厚度较大、刀具前角较小时常产生此类切屑。
(3)粒状切屑又称单元切屑。
在切屑形成过程中,如剪切面上的剪切应力超过了材料的断裂强度,切屑单元从被切材料上脱落,形成粒状切屑。
(4)崩碎切屑加工脆性材料,切削厚度越大越易得到这类切屑。
切削参数的选用原则
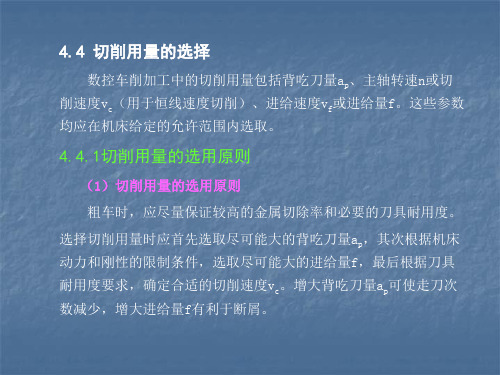
状不同,通常选择外圆、端面或内孔、端面装夹,并力求设计基
准、工艺基准和编程原点的统一。在批量生产中,常用下列方法 划分工序。
(1)按零件加工表面划分工序 即以完成相同型面的那一部分工艺过程为一道工序,对于加工 表面多而复杂的零件,可按其结构特点(如内形、外形、曲面和平 面等)划分成多道工序。 将位置精度要求较高的表面在一次装夹下完成,以免多次定位 夹紧产生的误差影响位置精度。 如图4-19所示工件,按照零件的 工艺特点,将外轮廓和内轮廓的 粗、精加工各放在一道工序内完 成,减少了装夹次数,有利于保
刀路线最短。
(1)先粗后精 指按照粗车一半精车一精车的顺序,逐步提高加工精度。为了 提高生产效率并保证零件的精加工质量, 在切削加工时,应先安排粗加工工序, 在较短的时间内,将精加工前的大部分 加工余量去掉,同时尽量保证精加工的 余量均匀。如图所示。
(2)先近后远 这里所说的远与近,是按加工部位相对于对刀点的距离大小 而言的。在一般情况下,特别是在粗加工时,通常安排离对刀点 近的部位先加工,离对刀点远的部位后加工,以便缩短刀具移动 距离,减少空行程时间。 例如,当加工图4-23所示零件时,对这类直径相差不大的台 阶轴,当第一刀背吃刀量(图4-23中最大背吃刀量可为3mm左右) 未超限度时,宜按Φ 34mm-Φ 36mm-Φ 38mm的顺序先近后远地安排 车削加工。
图4-24为车圆弧的阶梯走刀路线。
图4-25(a)为车圆弧的同心圆弧走刀路线。
图4-24 阶梯走刀路线车圆弧
图4-25
同心圆弧走刀路线车圆弧
图4-27为车圆弧的车锥法切削路线
即先车一个圆锥,再车圆弧。
数控加工技术中的刀具选择与切削参数优化

数控加工技术中的刀具选择与切削参数优化随着科技的不断发展,数控加工技术在工业生产中的应用越来越广泛。
在数控加工中,刀具选择与切削参数优化是关键的环节,能够直接影响加工效率和产品质量。
本文将从刀具选择和切削参数两个方面探讨数控加工技术中的刀具选择与切削参数优化。
一、刀具选择在数控加工中,刀具的选择是非常重要的,不同的刀具适用于不同的加工材料和加工方式。
首先,我们需要考虑加工材料的硬度。
对于硬度较高的材料,应选择硬质合金刀具或陶瓷刀具,以保证刀具的寿命和加工效果。
而对于较软的材料,可以选择高速钢刀具或者硬质合金刀具。
其次,我们还需要考虑加工方式。
对于精密加工,应选择精密刀具,以保证加工精度和表面质量。
而对于高效加工,应选择高效刀具,以提高加工效率。
除了硬度和加工方式,刀具的几何形状也是刀具选择的重要考虑因素。
常见的刀具形状有直刀、球头刀、锥度刀等。
直刀适用于平面加工和开槽加工,球头刀适用于球面加工和曲面加工,锥度刀适用于斜面加工和孔加工。
根据加工需求选择合适的刀具形状,可以提高加工效率和产品质量。
二、切削参数优化切削参数的优化是数控加工中的另一个关键环节。
合理的切削参数能够提高加工效率和延长刀具寿命。
首先,我们需要考虑切削速度。
切削速度是指刀具在单位时间内切削的长度,它直接影响到加工效率和刀具寿命。
一般来说,切削速度应根据加工材料的硬度来确定,硬度较高的材料应选择较低的切削速度,以避免过快磨损刀具。
其次,我们还需要考虑进给速度。
进给速度是指刀具在单位时间内沿工件表面移动的距离,它直接影响到加工的精度和表面质量。
合理的进给速度能够保证加工精度和表面质量,同时提高加工效率。
最后,我们还需要考虑切削深度。
切削深度是指刀具每次进给的深度,它直接影响到加工的粗糙度和加工力。
合理的切削深度能够保证加工粗糙度和加工力在合理范围内,同时提高加工效率。
综上所述,刀具选择与切削参数优化是数控加工技术中的重要环节。
合理的刀具选择和切削参数优化能够提高加工效率和产品质量。
切削用量及刀具几何角度的选择..
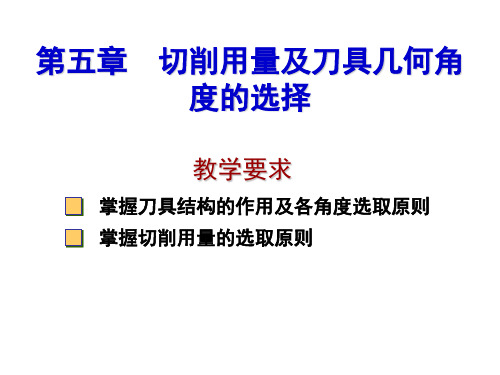
切断刀的标注角度
n
rn
5.3 主偏角、副偏角及其选择
1.主偏角的作用 ⑴影响切削层的形状; ①当切削深度与进给量不变时,主偏角减小,切削厚 度减小,切削宽度增加,从而使单位切削刃长度的 负荷减轻; ②主偏角减小使散热面积增加,刀具耐用度提高。 ⑵影响已加工表面的残留高度; 减小主偏角可以减低工件加工表面的残留面积高度, 提高工件的表面光洁程度; ⑶影响切削分力的比值 增大主偏角,吃刀抗力Fy减小,走刀抗力Fx增大。 (工艺系统的刚性较差时,应选用较大的主偏角)
5.6 切削用量的选择
一、选择切削用量应考虑以下问题: 1.切削用量对加工质量的影响 Fz ①切削深度ap的影响:
171 ap f
0.84
ap增大时,切削力成倍增加,使工艺系统的弹性变形增加,并 易引起振动,从而增高工件表面粗糙度和降低工件精度;
②进给量f的影响:
f增大时,切削力和表面残留面积增加,使工件表面粗糙度增高,使 工件精度下降;
ba1 0.1 ~ 0.3mm; a01 20 ~ 5
5.波形后刀面 优点:增大了切屑卷曲方向的刚度,有利于断屑。
后角的作用及选择
1.后角的作用 ⑴增加后角可减少刀具与已加工表面的摩擦,因此 ①有利于提高工件表面质量; ②有利于提高刀具耐用度; ⑵在同样磨钝标准VB下,增大后角有利于提高刀具耐 用度; ⑶增大后角使切削刃和刀头强度降低,散热体积减小, 从而使刀具耐用度下降。
3.负前角单面型 优点:刃口强度高。 缺点:刃口钝,对切削层的挤压严重。
使用场合: ⑴主要用于硬质合金车刀和铣刀; ⑵切削高强度、高硬度材料和切削淬火钢; ⑶当磨损主要发生在后刀面时。
4.正前角正倒棱 使用场合:适用于高速钢刀具 正倒棱尺寸参数:
山高刀具选择_Tornado

刀具选择 - Tornado (高速)根据应用场合与材料选择立铣刀下图与下一页列出了针对被加工材料的推荐立铣刀类型。
针对每种加工应用,共有三张图表。
•铣槽应用•侧铣(铣轮廓)应用•仿形铣削应用尽量使用首选备选表示了如果你要将同一种型号用于不同的材料组与上述应用时可推荐的铣刀型号。
铣槽* 为获得石墨加工的最佳性能,使用金刚石镀层立铣刀。
** 第17组材料还包括耐磨复合材料。
*** JH410 立铣刀仅用于不稳定工况的切削。
对于未包含在更新样本里的产品,请参阅机加工导航者 2004。
材料山高材料分组编号首选备选软钢1-2JHP-950JH-910-MEGA JH-421JH-120普通钢3-4JHP-950JH-910-MEGA JH-120JH-140工具钢 <48 HRc 5-6JHP-950JH-120JH-140JH-910-MEGA淬硬钢 >48-56 HRc 7JH-120JH-140JH-910-MEGA–淬硬钢 >56-62 HRc 7JH-120JH-140––淬硬钢 >62-65 HRc 7JH-120JH-140––淬硬钢 >65 HRc 7JH-120JH-140––不锈钢8-9JH-910-TRIBON JH-421JH-140–难加工不锈钢10-11JH-910-TRIBONJH-421JH-140–软铸铁12-13JH-910-MEGA JH-120JH-140–硬铸铁14-15JH-910-MEGAJH-120JH-140–Si 含量<16%的铝合金16JH-421/JH-410***JH-440JH-40–Si 含量 >16%的铝合金**17**JH-820JH-830––超级合金20JH-910-TRIBON JH-140––难加工超级合金21JH-910-TRIBONJH-140––钛合金22JH-910-TRIBON JH-140––石墨*JH-910-MEGA*–*–*–*塑料(软)JH-40/JH-410***JH-421JH-440–塑料(硬)JH-421JH-40JH-440–铜合金JH-421/JH-410***JH-440JH-40–刀具选择 - Tornado (高速)侧铣 (铣轮廓)* 为获得石墨加工的最佳性能,使用金刚石镀层立铣刀。
- 1、下载文档前请自行甄别文档内容的完整性,平台不提供额外的编辑、内容补充、找答案等附加服务。
- 2、"仅部分预览"的文档,不可在线预览部分如存在完整性等问题,可反馈申请退款(可完整预览的文档不适用该条件!)。
- 3、如文档侵犯您的权益,请联系客服反馈,我们会尽快为您处理(人工客服工作时间:9:00-18:30)。
2:确定刀盘类型及刀盘直径、刀
片规格及大小、齿数的疏密等
• 刀盘的类型主要是依据加工方式选,基 本可分为“快豹”平面铣削、“八角形 ”平 面铣刀、“六边型”平面铣刀、“双面 八角 形”平面铣刀、“镜面”精加工平面铣 刀、 CBN平面铣刀等等。 • 按照常规及顺铣的要求,刀盘直径一般 为被加工宽度的1.25倍为佳。 • 刀片的规格及大小主要是依据加工要求 及被加工的余量大小来选择。 • 刀盘齿数的疏与密主要是依据加工的效 率、节拍要求和机床功率、工件夹持刚 性等决定。
How to select the tool & cutting data of ISO standard tools from Turning catalogues ISO标准车刀及切削参数的 基本选择方法
1:确定被加工工件的材料组别
• 依据国际ISO标准的规定,常见的 工件材料被分为六类:
钢件类(P类)--山高组别1-6
3:确定最适合的首选刀片 • 根据选定的刀杆型号在样本的相应组别中您可以非常容易地找到首 选刀片的推荐。WNMG080408-M5, TP3000
4:您也可以在样本中了解到有关刀杆的其它信息
• 这些信息包括:
刀杆的实际高度尺寸、宽度尺寸、刀杆长度、主偏角、重量、可加工的 最小孔径、刀垫型号、压板型号、锁紧螺钉、扳手规格等等。
5:术语和常用的切削参数计算公式
每分钟切削进给率 F = n*f ( mm/ min )
F = 每分钟切削进给率
( mm / min )
6:依据选定的刀片确定切削参数
• 根据刚才选择的刀片,您可以很方便地选得适用的切削参数推荐值。 线速度Vc=190m/min,每转进给fz=0.40mm/r,假定工件直径我们已 经知道是D=100mm,那么转速N=604rpm,所以实际的工作进给量 F=604*0.40=242mm/min。
6:加工优化、问题与对策
How to select the face milling tools & cutting data from the Milling catalogues 平面铣刀及切削参数 基本选择方法
1:确定被加工工件的材料组别 • 依据国际ISO标准的规定,常见的 工件材料被分为六类:
钢件类(P类)--山高组别1-6
不锈钢类(M类)--山高组别7-11
铸铁类(K类)--山高组别12-15 有色金属类(N类)--山高组别16-17 耐热合金类(S类)--山高组别20-22 淬硬钢类(H类)--山高组别7 我们最常用的45号钢为第3 组材料,不 锈钢( 316 )属于第9组材料,铸铁HT25 ( GG25 )属于第12组, 铝合金属于第16 组,钛合金( Ti6Al4V )属于20组,镍基 合金( 718 )属于第22组。
LC..1603..
4:您也可以在样本中了解到有关刀杆的其它信息
• 这些信息包括: 刀杆的实际高度尺寸、宽度尺寸、刀杆长度、最大径向有效切深、重 量、刀片宽度、锁紧螺钉、扳手规格等等。
5:依据选定的刀片确定切削参数
• 根据刚才选择的刀 片,您可以很方便 地选得适用的切削 参数推荐值。 线速度 Vc=60 m/min, 每转进给 fz=0.15-0.30 mm/r 假定工件直径我们 已经知道是 D=100 mm,那么 转速 N=190 rpm 所以实际的工作进 给量 F=190*0.25 =47.50 mm/min
3:确定最适合的首选刀片
• 根据选定的刀杆型号在样本的相 应推荐中您可以非常容易地找到 首选刀片的推荐为: LC...1603.. 从样本对航空航天材料性能及分 组的界定,我们可以很方便地知 道该钛合金的可加工性为: 30—35 根据样本上对这种材料不同加工 情况下刀片牌号选择的推荐,我 们可以很方便地确定选择MT 883 或MT CP500为所选刀片,即: LCMR160304-0300-MT 883或 CP500
1:确定被加工工件的材料组别 • 依据国际ISO标准的规定,常见的 工件材料被分为六类:
钢件类(P类)--山高组别1-6
不锈钢类(M类)--山高组别7-11
铸铁类(K类)--山高组别12-15 有色金属类(N类)--山高组别16-17 耐热合金类(S类)--山高组别20-22 淬硬钢类(H类)--山高组别7 我们最常用的45号钢为第3 组材料,不 锈钢( 316 )属于第9组材料,铸铁HT25 ( GG25 )属于第12组, 铝合金属于第16 组,钛合金( Ti6Al4V )属于20组,镍基 合金( 718 )属于第22组。
8:常见车削切削问题及解决方法
8:常见车削切削问题及解决方法
8:常见车削切削问题及解决方法
8:常见车削切削问题及解决方法
8:常见车削切削问题及解决方法
How to seling data of MDT tools from the Turning catalogues MDT标准车刀及切削参数的 基本选择方法
190
7:对切削参数的优化 • 根据山高公司车削刀片断屑槽型的规律我们知道M5只是粗加工的首 选槽型,但是在实际加工时断屑效果的改善还需要优化调整。同样刀 片牌号也完全会因工件的实际工艺状况可以通过优化选择其它牌号得 到更好的加工质量或寿命,如可以选用TM2000、TM4000、TP2500。 实际每转的进给量为Fr=0.40mm,依据每转进给、刀尖圆角与加工所得 表面光洁度之间的关系我们可以预期可能的加工实际光洁度。所以要提 高光洁度您认为应该采用什么措施? 正确的办法应该是加用修光刃刀片而不是简单地降低每齿进给量。
3:确定最适合的首选刀片
• 根据被加工材料在样本的相应组别中您可以非常容易地找到首选 刀片的推荐。SEMX1204AFTN-M15 T350M
4:您也可以在样本中了解 到有关刀盘的其它信息
• 这些信息包括: 刀盘的实际工作直径、最大
直径、刀盘高度、齿数、重
量、安装孔径、备用板手、 适用的刀柄规格等等。
Slotting 铣槽
Contouring 铣边
Circular Ramping Pocket Helical Milling Interpolation 斜线插补铣型腔 螺旋插补
Plunging 插铣
3:确定最适合的首选刀片 • 如我们以加工45钢为例,即山高第4组材料,根据被加工材料在样本的 相应组别中您可以非常容易地找到首选刀片的推荐。 XOMX090308TR-ME06 T350M
How to select the cutting data from the catalogues in Drilling 钻头切削参数的基本选择方法
不锈钢类(M类)--山高组别7-11
铸铁类(K类)--山高组别12-15 有色金属类(N类)--山高组别16-17 耐热合金类(S类)--山高组别20-22 淬硬钢类(H类)--山高组别7 我们最常用的45号钢为第3 组材料,不 锈钢( 316 )属于第9组材料,铸铁HT25 ( GG25 )属于第12组, 铝合金属于第 16组,钛合金( Ti6Al4V )属于20组, 镍 基合金( 718 )属于第22组。
225
6:依切削参数的优化
• 以上切削参数的选择是基于ae/D大于或等于50%的满刀切削状况。当
实际加工中如果径向切削宽度较小、 出现ae/D小于50%的边切削状况 那么依据平均断屑厚度的理论,切削参数必须按照样本的参数修正方 法加以修正、调整。
如: ae=5 mm,则 ae/D = 5/20=25%,fz应该调整为0.13 mm/z,相 应的速度因子为1.30及Vc=1.30*225=292 m/min,转速N=4647 rpm, 所以调整后的实际工作进给为:F=4647*2*0.13=1208 mm/min。
正确的办法应该是加用修光刃刀片而不是简单地降低每齿进给量。
How to select square shoulder milling tools & cutting data from the Milling catalogues 方肩铣刀及切削参数 基本选择方法
1:确定被加工工件的材料组别 • 依据国际ISO标准的规定,常见的 工件材料被分为六类:
2:确定刀盘类型及刀盘直径、刀
片规格及大小、齿数的疏密等
• 刀盘的类型主要是依据加工方式选,基 本可分为“旋风”方肩铣刀、“玉米” 方肩 铣刀、正方形刀片方肩铣刀、三角形刀 片方肩铣刀等等。 • 按照常规及顺铣的要求,刀盘直径一般 为被加工宽度的1.25倍为佳。 • 刀片的规格及大小主要是依据加工要求 及被加工的余量大小来选择。 • 刀盘齿数的疏与密主要是依据加工的效 率、节拍要求和机床功率、工件夹持刚 性等决定。 比如方肩铣削加工我们一般首选“旋风 ”
2:确定刀杆类型及刀杆尺寸大小、
刀片类型及大小、切削宽度等
• 刀杆的类型主要是依据加工方式选,基 本可分为车削(外园、内孔、端面)、 仿形车、切槽(外园、内孔、端面)、 切断、切螺纹等等。 • 刀杆尺寸大小应该越大越好,加工系统 刚性会好,但是也要与机床特性匹配。 • 刀片的类型在满足工艺性的前提下应该 尽可能选择有效可用刃口多的,刀片的 规格及大小、宽度主要是依据加工要求 及被加工的余量大小来选择。 如普通外圆及端面加工及最大达4倍的切 槽刀具用于钛合金Ti6Al4V加工我们可选 刀杆:CFMR2525M03(钛合金加工)
钢件类(P类)--山高组别1-6
不锈钢类(M类)--山高组别7-11
铸铁类(K类)--山高组别12-15 有色金属类(N类)--山高组别16-17 耐热合金类(S类)--山高组别20-22 淬硬钢类(H类)--山高组别7 我们最常用的45号钢为第3 组材料,不 锈钢( 316 )属于第9组材料,铸铁HT25 ( GG25 )属于第12组, 铝合金属于第16 组,钛合金( Ti6Al4V )属于20组,镍基 合金( 718 )属于第22组。