硬质合金压制过程中的几个基本知识点
硬质合金挤压工艺流程

硬质合金挤压工艺流程一、原料准备。
咱得先把制作硬质合金的原料准备好呀。
这原料可不是随便凑凑就行的,就像做菜得挑新鲜的食材一样。
硬质合金主要的原料就是碳化钨和钴粉之类的。
这些粉末的粒度那可得严格控制呢。
要是粒度不对呀,就像盖房子用的砖头大小不一,最后盖出来的房子肯定不结实。
碳化钨粉末那可是硬家伙,它得足够细,这样在后面挤压的时候才能更好地成型。
钴粉呢,就像是把这些硬家伙黏在一起的胶水,量也得刚刚好。
二、混合。
原料准备好了,那就得把它们混合均匀啦。
这个过程就像是调面糊一样,得让每一粒粉末都能和其他的粉末亲密接触。
我们会把碳化钨和钴粉放到专门的混合设备里,让它们在里面欢快地翻滚。
这设备一转起来呀,就像是在跳一场粉末的舞蹈。
而且在混合的时候呢,有时候还会加入一些其他的添加剂,比如说润滑剂之类的。
这润滑剂就像是给粉末们穿上了一层滑溜溜的小衣服,这样在挤压的时候它们就更容易从模具里挤出来啦。
三、制粒。
混合好的粉末还不能直接拿去挤压呢,得先制粒。
这就像是把面粉先搓成一个个小团子一样。
制粒的目的就是让粉末形成大小比较均匀的小颗粒。
这些小颗粒可可爱爱的,它们的大小和形状会影响到后面挤压出来的产品的质量。
如果制粒不均匀,那挤压出来的东西可能就会有坑坑洼洼的,就像月球表面一样不平整。
在制粒的时候呀,也是有专门的设备和工艺的,要控制好温度、压力这些参数呢。
四、挤压。
制粒完成后,就到了挤压这个关键的步骤啦。
把那些小颗粒放到挤压机里,然后就像挤牙膏一样把它们从模具里挤出来。
这个模具可就像是一个神奇的模子,决定了挤出来的产品的形状。
比如说要做硬质合金的棒材,那就用对应的圆形模具;要是做板材呢,就用扁平的模具。
挤压的时候呀,压力可得控制好,压力小了,挤不出来或者形状不对;压力大了呢,可能会把模具都给挤坏了,那就麻烦大了。
而且在挤压过程中,粉末之间的结构也在发生变化,它们会变得更加紧密,就像一群小伙伴紧紧地抱在一起。
五、脱脂。
挤压出来的东西里面还含有之前加进去的润滑剂之类的东西呢,这时候就得脱脂了。
硬质合金制造工艺

硬质合金制造工艺
硬质合金制造工艺:
硬质合金烧结成型就是将粉末压制成坯料,再进烧结炉加热到一定温度(烧结温度),并保持一定的时间(保温时间),然后冷却下来,从而得到所需性能的硬质合金材料。
烧结成型是硬质合金制造工艺的主要方法。
硬质合金烧结过程可以分为四个基本阶段:
1:脱除成形剂及预烧阶段,在这个阶段烧结体发生如下变化:
成型剂的脱除,烧结初期随着温度的升高,成型剂逐渐分解或汽化,排除出烧结体,与此同时,成型剂或多或少给烧结体增碳,增碳量将随成型剂的种类、数量以及烧结工艺的不同而改变。
粉末表面氧化物被还原,在烧结温度下,氢可以还原钴和钨的氧化物,若在真空脱除成型剂和烧结时,碳氧反应还不强烈。
粉末颗粒间的接触应力逐渐消除,粘结金属粉末开始产生恢复和再结晶,表面扩散开始发生,压块强度有所提高。
2:固相烧结阶段(800℃--共晶温度)
在出现液相以前的温度下,除了继续进行上一阶段所发生的过程外,固相反应和扩散加剧,塑性流动增强,烧结体出现明显的收缩。
3:液相烧结阶段(共晶温度--烧结温度)
当烧结体出现液相以后,收缩很快完成,接着产生结晶转变,形成合金的基本组织和结构。
4:冷却阶段(烧结温度--室温)
在这一阶段,合金的组织和相成分随冷却条件的不同而产生某些变化,可以利用这一特点,对硬质合金进行热处理以提高其物理机械性能。
硬质合金基本知识简介

硬质合金基本知识简介硬质合金基本知识简介一、硬质合金的基本知识1、硬质合金的定义:由难熔金属的硬质化合物和粘结金属通过粉末冶金工艺制成的一种合金材料。
2、硬质合金的特点:具有高硬度、耐磨、强度和韧度性较好、耐热、耐腐等系列优良性能。
3、硬质合金的用途:广泛应用于金属切削、拉伸、耐磨零件、冲压模具、地质矿山、量具、刃具、圆珠笔尖、军事上穿甲弹头。
4、硬质合金的分类:1)、WC-CO 2)、WC-CO-添加剂3)、WC-CO-TiC 4)、WC-Ni (无磁合金)5、硬质合金的组成元素:W 、WC、Co 、Ni6、硬质合金介于钢、陶瓷之间,与钢相比有以下特点:1)高的硬度、高的耐磨性,低的抗冲击性(决定了硬质合金的使用范围)2)高的抗压性、低的抗弯强度,易断裂3)热膨胀系数低只有钢的三分之一4)耐腐蚀、耐磨性5)高温稳定性二、硬质合金的几个重要指标(物理性能、化学性能、机械性能)1)、比重:Co上升,D下降 D ( density )2)、硬度:Co上升,HRA下降、粒径上升3)、抗弯强度:Co上升,抗弯强度上升4)、抗压强度:Co上升,抗压强度下降5)、冲击韧性:Co上升,冲击韧性上升;粒径大、韧性上升6)、娇顽磁力:与Co含量,晶粒度有关,娇顽磁力可以用来控制合金组织,是生产厂的一项内控指标7)、磁饱和:与Co含量有关,检测Co 含量或已知成分Co量是否存在非磁性8)、弹性模量:硬质合金的弹性模量大。
Co上升,弹性模量下降;晶粒度对弹性模量影响大9)、导热性:WC-Co有较高的导热性。
Co上升,导热率下降10)、热膨胀系数:Co含量的增大而增大,合金热膨胀系数比钢材低很多三判断硬质合金的缺陷1、制粉:1)混料:a、成分b、粒径;2)孔洞:大于40um孔洞为脏划孔(不合格产品)、小于40um孔洞为孔隙(合格产品);3)脱碳:表现为银白色亮点;4)渗碳:石墨夹杂,表现为端口发暗,表面发黑2、成型:1)分层2)裂纹3)未压好:棱角尖锐的三角形、四角形孔洞3、烧结:1)起皮2)鼓泡3)孔洞4)组织不均匀5)变形6)裂纹7)黑心8)过烧9)欠烧Roblloy几种原材料的主要用途锻造模具用原材料:制造汽车产业和机械产业等主要产业所需要各种部材的模锻。
硬质合金压制保压时间 -回复

硬质合金压制保压时间-回复硬质合金压制保压时间的问题是一个涉及到材料科学和工艺学的重要议题。
硬质合金是一种由金属粉末和钎剂混合制备的材料,常用于切削工具、矿山钻头和金属加工等领域。
在硬质合金的制备过程中,压制保压时间起着至关重要的作用,直接影响到最终产品的质量和性能。
本文将一步一步回答硬质合金压制保压时间的问题,从材料选取、工艺设计到最佳保压时间的确定。
第一步:材料选取硬质合金的制备离不开合适的材料选择。
常见的主要成分有钨碳化物和钴。
其中,钨碳化物为硬质合金的硬质相,钴则起到连接硬质相的作用。
合适的材料选取应综合考虑硬度、熔点、热稳定性等因素。
硬度要足够高以保证刀具的耐磨性,熔点不能过低以免影响制备过程,热稳定性要好以防止在高温下发生相反应。
因此,在选择硬质合金材料时,需结合具体应用要求和工艺条件进行综合考虑。
第二步:工艺设计硬质合金的制备过程主要包括混合、压制和高温烧结三个步骤。
工艺设计是决定硬质合金质量和性能的关键因素之一。
压制保压时间在工艺设计中占据重要地位,其目的在于使混合料在压制过程中达到足够的密实度,从而保证烧结后具有良好的物理性能。
保压时间过短会导致材料密实度低,从而降低硬质合金的硬度和耐磨性;保压时间过长则会造成成本和时间上的浪费。
因此,合理确定保压时间对于硬质合金制备非常重要。
第三步:最佳保压时间的确定确定最佳保压时间需要综合考虑材料的固相反应速率、热稳定性以及其他工艺参数的相互作用。
一般来说,保压时间应该充分考虑反应速率和材料的热稳定性,以使得材料颗粒之间得到充分的结合和反应。
实际上,最佳保压时间还受到其他因素的影响,如保压力、压制温度等。
保压时间的确定需要进行多次实验,并根据实验结果进行优化和调整。
总结:硬质合金压制保压时间是一个涉及到材料科学和工艺学的重要议题。
在硬质合金的制备中,合适的材料选取和工艺设计至关重要。
最佳保压时间的确定需要综合考虑材料的固相反应速率、热稳定性,以及其他工艺参数的相互作用。
硬质合金压制保压时间

硬质合金压制保压时间1.引言1.1 概述概述:硬质合金作为一种重要的工程材料,在现代制造业中扮演着重要角色。
其独特的硬度、耐磨性以及高温抗腐蚀性使得它广泛应用于切削工具、矿山设备、粉末冶金等领域。
在硬质合金的制备过程中,压制保压时间是一个关键参数。
本文旨在探讨硬质合金压制保压时间对其性能的影响,以及确定最佳保压时间的方法。
通过对硬质合金的研究,我们了解到压制保压时间是指将混合粉末放入模具中,施加压力并保持一定时间的过程。
在此过程中,粉末颗粒相互间的结合会得到加强,形成致密的结构,从而提高硬质合金的机械性能。
保压时间的长短决定了合金中的气孔、缺陷等问题的解决程度,对硬质合金的性能起着重要作用。
研究表明,过短的保压时间会导致硬质合金中气孔的残留,破坏了其致密性,降低了硬度和抗磨性能。
而过长的保压时间则会使得硬质合金中晶粒长大,从而降低了合金的硬度和强度。
因此,确定适当的保压时间是硬质合金制备过程中必须重视的问题。
在确定最佳保压时间时,首先需要考虑硬质合金的成分、颗粒大小和形状等因素。
此外,还需要考虑硬质合金的用途和要求的性能指标。
通过实验和经验总结,可以根据具体情况确定最佳保压时间,以达到理想的性能。
总之,硬质合金压制保压时间是影响合金性能的关键因素。
不同的保压时间会对合金的致密性、硬度和强度产生不同的影响。
因此,为了获得优质的硬质合金产品,合理选择和控制保压时间至关重要。
在未来的研究中,我们还可以进一步探索保压时间与其他制备参数的相互关系,为硬质合金的制备提供更加准确和有效的指导。
1.2 文章结构文章结构是指文章的组织框架和布局,它对于读者来说非常重要,可以帮助读者更好地理解文章的内容和脉络。
本文的结构分为引言、正文和结论三个部分。
引言部分主要是对硬质合金压制保压时间这个主题进行概述和介绍。
首先,我们会对硬质合金的定义和应用进行简要说明,以便读者了解硬质合金的基本概念。
接着,我们会引出本文的研究重点——硬质合金压制保压时间,并解释为什么这个问题值得研究。
模压成型
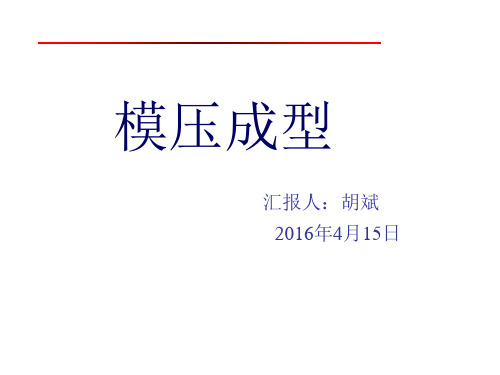
压制废品及其产生的原因
二、裂纹 与分层无本质的区别,都是由于弹性后效产生的弹性张力 大于粉末之间的结合应力的结果,出现在应力集中部位。 与分层不同,裂纹一般是不规则的,无整齐的界面。产生 的原因基本与分层差不多 脱模操作:为了避免脱模时产生裂纹,应该注意:脱模速 度要快,否则会由于已脱模部分横向膨胀而产生裂纹,在 非自动压机,脱模时还应该避免振动和设备本身的振动。
弹性后效
3、弹性后效的决定因素 (1).粉末颗粒间的结合强度越低,弹性后效就会越严重,一 切提高粉末颗粒结合强度的因素,都会导致弹性后效的降 低。 (2).粉末颗粒的接触应力越高,即粉末颗粒的弹性表型越大, 弹性后效就越严重,一切提高粉末颗粒间接触应力的因素, 都会导致弹性后效的增加。 弹性后效产生的弹性张力若大于粉末之间的结合力,会使 粉末之间脱离接触,压坯便会发生分层和裂纹。
2、压制压力 采用限位器压制,当单重增加时,压制高度不变,作用在 压制品上的压力增大,容易分层。 采用恒定压力压制,压力不变,当压制单重增大或混合料 细,制品密度不变,压制高度增加。 压制压力控制:不使压制品分层的最大压力,从而获得最 大的密度和强度(压力过小,易出现未压好的现象)
3、压力计刚性、振动、垂直度、和水平 一般要求压力机有较好的刚性。压机刚性好,当单重波动 时或混合料较干时,压制品高度变化小,制品的密度增加 较大,刚性不好,则压制品高度变大,密度增加较小。 压力机的振动,会使压制品产生裂纹。 压制时上冲头不垂直运动,会使压制品受压不均而分层, 制品两边尺寸发生偏差
圆柱形压块不同部位的密度大小及烧结收缩后的外形
脱模方式及其特点
模压成型的脱模方式可分为:顶出脱模、下拉脱模、和预 载脱模三种方式。 (a).顶出脱模方式及其特点 顶出脱模方式是压坯脱出时,阴模不动,靠下冲头的向上 运动将压坯顶出阴模的脱模 方式:(杠杆压机、凸轮式老 压机) 顶出脱模是靠下冲头的向上运动带动压坯向上运动而使压 坯脱出的,大多是靠杠杆作用产生的,加上下冲头的导向 面很短,压坯顶出很难垂直 上升,整个过程不会太平稳, 所以易造成压坯的脱出裂纹。
硬质合金压制过程中的压力分布

硬质合金压制过程中的压力分布
引起压力分布不匀的主要原因是粉末颗粒之间以及粉末与模壁之间的摩擦力。
压块高度越高,压力分布越不均匀。
实行双向加压或增大压坯直径,能减少压力分布的不均匀性。
四,压块密度分布:越是复杂的压块,密度分布越不均匀;除压力分布的不均匀(压力降)外,装粉方式不正确,使压块不同部位压缩程度不一致,也会造成压块密度不均匀。
1,填充系数:是指压块密度Y压与料粒的松装密度Y松的比值;压缩比:是指粉末料粒填装高度h粉与压块高度h压之比;在数值上填充系数和压缩比是相等的。
K=Y 压÷Y松=h粉÷h压2,为了减少压块密度分布的不均匀性:(1)提高模具的表面光洁度;(2)减少摩擦阻力;(3)提高料粒的流动性;(4)采用合理的压制方式; 3,粉末粒度对压制的影响;(1)粉末分散度越大(松装越小),压力越大。
压块密度越小;有较大的强度值,成型性好。
(2)料粒较粗,压块容易达到较高的压块密度,但其密度分布往往是不均匀的;一般情况下,压块强度随成型剂的加入量而提高。
五,硬质合金压块的弹性后效:1,弹性内应力:粉末颗粒内部和颗粒间接触表面上,由于原子间引力和吸力的相互作用,会产生一个与颗粒受力方向相反,并力求阻止颗粒变形,以便达到与压制压力平衡的作用力叫弹性内应力。
2,弹性后效:在除去压制压力和把压块脱模后,由于弹性内应力的松弛作用而引起压块体积膨胀的现象叫弹性
后效。
3,在许多情况下,压块脱模后发生弹性膨胀是造成压块裂纹和分层的原因。
4,粉末粒度细,颗粒粗糙程度降低,颗粒间结合强度降低(成型不足或含水量大)以及氧化物和杂质含量增加都会增加弹性后效。
料粒干燥太干而变硬,也会增加弹性后效.。
硬质合金基础知识.
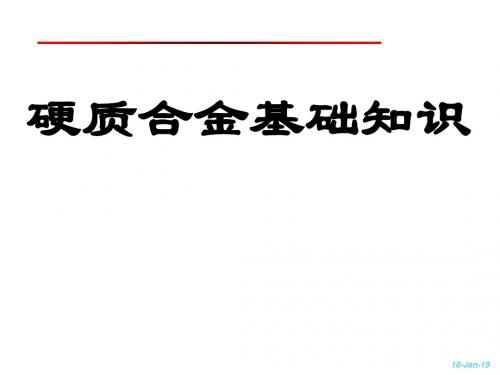
③
18-Jan-19
④ 钢结硬质合金:主要成分是钢,而以TiC或WC作硬质
相组成的一类硬质合金。其显著特点是可热处理与机 加工,是界于工具钢和硬质合金之间的一类中间合金。
M类:奥氏体/铁素体/马氏体不锈钢(如1Cr18Ni9Ti、0Cr19Ni、1Cr17Mo、
0Cr13Al、3Cr13、7Cr17、1Cr18Ni11Si4AlTi、0Cr26Ni5Mo2)、铸钢、锰 钢(40Mn18Cr3、50Mn18Cr4等)、合金钢(含有Ni、Si、Co、Al、Cr、 W、Mo、V、Ti、Nb等合金元素的碳素钢)、合金铸铁、可锻铸铁、易切 钢(Y12、Y15、Y30、Y40Mn等),切削牌号选择W—Co—Ti—Ta(Nb) 类合金,如YW1、YW2、YW3、YS8、YS25、YM101、YM201、YM301、 YC201等;
S类:耐热优质合金即高温合金(Fe基、Fe—Ni基、Ni基、Co基、Ti基合金,
如GH1015、GH2036、GH3128、GH4033、K211、K406、K640、TA2、 TA8、TB1、TB2、TC1~TC6等),除Ti基高温合金外,一般可选用W— Co—Ti—Ta(Nb)类或W—Co类合金,如YS8、YM201、YM301、YG6X、 YG8、YW2、YW3、YD201等;而Ti基高温合金应选用不含Ti的W—Co类 合金,如YG8、YG6X、YG8N、YG6A,理想情况是采用超细晶合金牌号。
18-Jan-19
对W—Co—Ti类合金,YT5、YT14、YT15、YT30、YT05等, 牌号中的数字表示Ti的大致含量。YT5,Ti含量为5%;YT14, Ti含量11.3;YT15,Ti含量12.7;YT30,Ti含量22.5。W—Co 类合金,YG3、YG3X、YG6、YG6X、YG6A、YG8、YG8N等, 数字表示Co含量,YG3,Co是3%,其余类推,X表示细颗粒, A表示加了TaC,N表示加了NbC。对W—Co—Ti—Ta(Nb) 类合金,YW1、YW2、YW3、YS25、YS8等,这些牌号没有规 律可循,只能靠记忆。 新的命名法则是根据牌号的加工范围来命名的,所以,牌号 的选择相对简单,如P类加工,用YC10、YC101、YC201、 YC301、YC35、YC45等,字母Y表示硬质合金,C表示长切屑, 数字表示加工范围,一般以前面两位数字表示,“10”表示精加 工,“20”表示半精加工,“30”表示粗加工,“35”“45”重载粗 加工。M类加工,用YM101、YM201、YM301命名,K类加工, 用YD101、YD201、YD301命名,其字母和数字表示的意义同P 18-Jan-19 类牌号的命名。
硬质合金压制过程中的几个基本知识点

压制过程中的几个基本知识点1、压制过程中粉末的位移与变形1.1 位移粉末装填在刚性模具中时,由于表面不规则,以及相互间的摩擦,颗粒间相互搭架而形成拱桥孔洞的现象叫做“拱桥效应”。
当施加压力时,拱桥效应被破坏,粉末受到压力的作用而发生相对的位移,其位移情况如下图。
1.2 变形粉末在发生位移的同时也发生着变形,变形主要有弹性变形、塑性变形和脆性断裂,基本情况图下图。
2、单位压制压力计算单位压制压力=总压制压力/产品的受压面积,以硬质合金的B 型(20mm ×6.5mm ×5.25mm )试样为例:22.15.620P 单位压制压力注:①单位为KN/mm 2;②收缩系数以 1.2为例,不同的粉末取不同的收缩系数值;③通常情况下,收缩系数随着压制压力的增加而下降,增加压制单重亦可使得收缩系数的下降。
3、弹性后效图压制压力与压坯密度的关系粉末冶金类产品在去除压制压力,将压坯脱模以后,由于弹性内应力的松弛作用而引起压坯体积膨胀的现象,称之为弹性后效,其定量的表示式如下:%100001L L L 式中:δ——压坯高度或直径方向的弹性后效值;L0——压坯脱模前的高度或直径;L1——压坯脱模后的高度或直径。
一般来说,高度方向上的弹性后效要比直径方向上的大得多(即弹性后效具有明显的方向性),脱模的一瞬间是弹性后效最为显著的时刻,是压坯最容易出现分层、裂纹的时刻。
弹性后效是导致压坯出现分层、裂纹废品的主要原因。
其影响因素有以下几点。
①混合料成分的影响:硬度高的粉末在压制时所产生的弹性后效大,弹性后效值随着粉末的硬度提高而提高。
WC-Co 合金混合料的弹性后效值一般比WC-TiC-Co 合金混合料的低。
高钴合金混合料的弹性后效值比低钴混合料的低,粉末氧化物和杂质含量高也会使得弹性后效值提高。
②粉末物理性能的影响:粉末粒度细,颗粒粗糙程度降低,颗粒间结合强度降低,会增加压坯的弹性后效。
混合料的料粒干燥过度变硬时,也会使得弹性后效增加。
硬质合金基础知识ppt
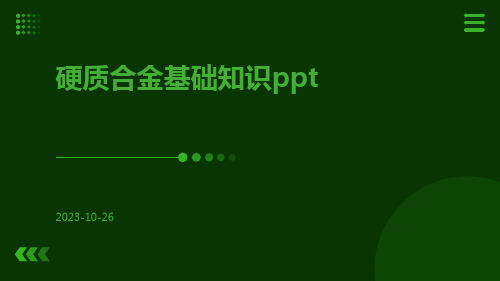
随着科技的进步,各行业对高性能硬质合金产品的需求不断增加。例如,用于航空航天、 汽车、电子等领域的硬质合金产品需要具备更高的强度、硬度、耐磨性和耐腐蚀性。
技术挑战
01
新材料的研发
为了满足各行业对高性能硬质合金的需求,需要不断研发新的硬质合
金材料。这需要对合金成分、制备工艺和热处理制度等进行深入研究
钴粉
粘结剂,提高合金的韧性 。
其他添加剂
如碳化钛、碳化钽等,改 善合金的硬度和耐磨性。
混合制粒
将原料粉末按一定比例混合,使用球磨或搅拌等方法制备均 匀的混合料。
加入适量的润滑剂,如石墨或硬脂酸,提高压制成型时的流 动性。
压制成型
将混合料放入模具中,施加高压,使其成为具有一定形状和尺寸的生坯。 根据产品形状和尺寸选择合适的压制工艺和模具。
它具有高硬度、高耐磨性和耐腐蚀性,广泛用于制造切削工 具、耐磨零件和高温合金等。
硬质合金的组成
硬质合金主要由硬质金属(如钨、钛、钽等)和金属碳化 物(如碳化钨、碳化钛等)组成。
此外,还含有少量其他元素,如钴、铬等,用于改善硬质 合金的性能。
硬质合金的性能特点
高硬度
硬质合金的硬度可达到HRA85~93,仅次 于金刚石。
客户需求变化
随着市场的变化,客户对硬质合金产品的需求也在不断变化。为了满足客户的需求,需要 加强市场调研、了解客户需求变化、及时调整产品策略和服务模式。
05
硬质合金的未来展望
技术创新方向
研发高强度、高韧性硬质合金材料
01
通过优化合金成分、改进生产工艺,提高硬质合金的综合性能
,满足更加严苛的工程应用需求。
低导电性
与金属相比,硬质合金的导电性较低。
硬质合金刀片制造工艺与设备。要点

专业:机械制造及其自动化班级:机制(3)班姓名:XXX时间:2014/7/3目录摘要…………………………………………1. 关键字………………………………………2. 前言…………………………………………3.1 硬质合金的概述1.1 硬质合金1.2 市场概况2 硬质合金的生产工艺2.1 生产原料2.2工艺流程2.3 加工种类2.4 加工种类优缺点对比3 硬质合金性能及其与使用关系3.1 硬度3.2 抗弯刚度3.3 冲击韧性3.4 耐磨性3.5 抗压强度3.6 导热率3.7 线胀系数4 硬质合金的种类及其用途4.1 硬质合金的种类4.2 各种牌号硬质合金的用途5 硬质合金的加工设备5.1 球磨机5.2 制粒设备5.3 自动压机5.4 单体真空脱蜡烧结炉6 国外硬质合金6.1 瑞典6.2 美国6.3 日本6.4 以色列小结…………………………………………... 参考资料……………………………………... 致谢…………………………………………...摘要:硬质合金石由难熔金属的碳化物以铁族金属钴或镍作胶结金属,用粉末冶金方法制造的合金材料。
由于硬质合金具有高硬度、耐磨损、耐腐蚀、耐高温和线胀系数小一系列优点,在现代工业生产中,已成为金属加工、矿山开采、石油钻探,国防军工等不可缺少的重要工具材料。
关键字:硬质合金性能工艺设备前言硬质合金具有很高的硬度、强度、耐磨性和耐腐蚀性,被誉为“工业牙齿”,并且未来高新技术武器装备制造、尖端科学技术的进步以及核能源的快速发展,将大力提高对高技术含量和高质量稳定性的硬质合金产品的需求。
随着国民经济的迅速增长,硬质合金的需求也高速增长。
因此研究并了解硬质合金是十分有意义的事情。
1 硬质合金的概述1.1 硬质合金由难熔金属的硬质化合物和粘结金属通过粉末冶金工艺制成的一种合金材料。
硬质合金具有硬度高、耐磨、强度和韧性较好、耐热、耐腐蚀等一系列优良性能,特别是它的高硬度和耐磨性,即使在500℃的温度下也基本保持不变,在1000℃时仍有很高的硬度。
硬质合金刀具材料基础知
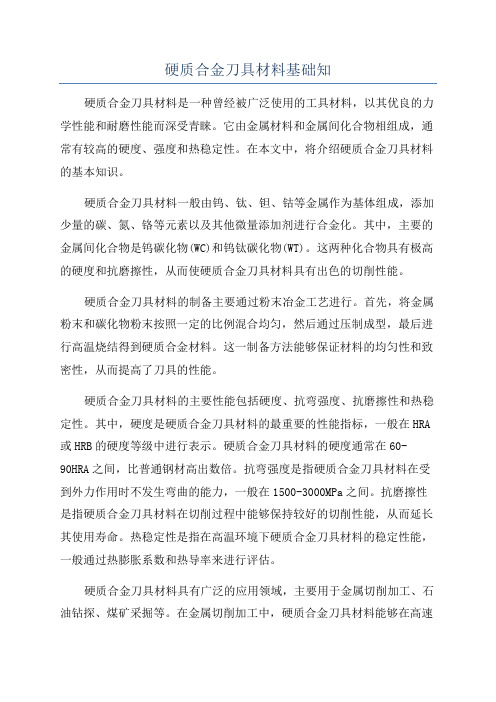
硬质合金刀具材料基础知硬质合金刀具材料是一种曾经被广泛使用的工具材料,以其优良的力学性能和耐磨性能而深受青睐。
它由金属材料和金属间化合物相组成,通常有较高的硬度、强度和热稳定性。
在本文中,将介绍硬质合金刀具材料的基本知识。
硬质合金刀具材料一般由钨、钛、钽、钴等金属作为基体组成,添加少量的碳、氮、铬等元素以及其他微量添加剂进行合金化。
其中,主要的金属间化合物是钨碳化物(WC)和钨钛碳化物(WT)。
这两种化合物具有极高的硬度和抗磨擦性,从而使硬质合金刀具材料具有出色的切削性能。
硬质合金刀具材料的制备主要通过粉末冶金工艺进行。
首先,将金属粉末和碳化物粉末按照一定的比例混合均匀,然后通过压制成型,最后进行高温烧结得到硬质合金材料。
这一制备方法能够保证材料的均匀性和致密性,从而提高了刀具的性能。
硬质合金刀具材料的主要性能包括硬度、抗弯强度、抗磨擦性和热稳定性。
其中,硬度是硬质合金刀具材料的最重要的性能指标,一般在HRA 或HRB的硬度等级中进行表示。
硬质合金刀具材料的硬度通常在60-90HRA之间,比普通钢材高出数倍。
抗弯强度是指硬质合金刀具材料在受到外力作用时不发生弯曲的能力,一般在1500-3000MPa之间。
抗磨擦性是指硬质合金刀具材料在切削过程中能够保持较好的切削性能,从而延长其使用寿命。
热稳定性是指在高温环境下硬质合金刀具材料的稳定性能,一般通过热膨胀系数和热导率来进行评估。
硬质合金刀具材料具有广泛的应用领域,主要用于金属切削加工、石油钻探、煤矿采掘等。
在金属切削加工中,硬质合金刀具材料能够在高速和重负荷下保持切削效果,更高效地完成切削任务。
在石油钻探领域,硬质合金刀具材料具有优异的耐磨性和抗热稳定性,能够适应复杂的地质环境。
在煤矿采掘中,硬质合金刀具材料能够在高硬度的岩石中进行切削,提高采掘效率并减少能量消耗。
总之,硬质合金刀具材料是一种重要的工具材料,具有优异的力学性能和耐磨性能,能够满足各种切削加工和采矿应用的要求。
硬质合金生产工艺
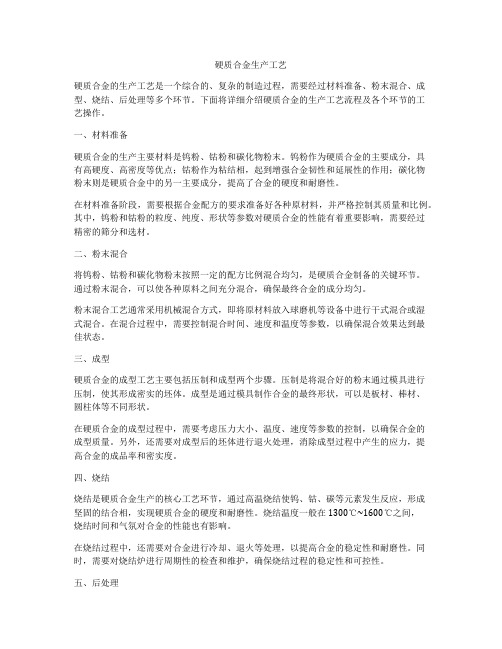
硬质合金生产工艺硬质合金的生产工艺是一个综合的、复杂的制造过程,需要经过材料准备、粉末混合、成型、烧结、后处理等多个环节。
下面将详细介绍硬质合金的生产工艺流程及各个环节的工艺操作。
一、材料准备硬质合金的生产主要材料是钨粉、钴粉和碳化物粉末。
钨粉作为硬质合金的主要成分,具有高硬度、高密度等优点;钴粉作为粘结相,起到增强合金韧性和延展性的作用;碳化物粉末则是硬质合金中的另一主要成分,提高了合金的硬度和耐磨性。
在材料准备阶段,需要根据合金配方的要求准备好各种原材料,并严格控制其质量和比例。
其中,钨粉和钴粉的粒度、纯度、形状等参数对硬质合金的性能有着重要影响,需要经过精密的筛分和选材。
二、粉末混合将钨粉、钴粉和碳化物粉末按照一定的配方比例混合均匀,是硬质合金制备的关键环节。
通过粉末混合,可以使各种原料之间充分混合,确保最终合金的成分均匀。
粉末混合工艺通常采用机械混合方式,即将原材料放入球磨机等设备中进行干式混合或湿式混合。
在混合过程中,需要控制混合时间、速度和温度等参数,以确保混合效果达到最佳状态。
三、成型硬质合金的成型工艺主要包括压制和成型两个步骤。
压制是将混合好的粉末通过模具进行压制,使其形成密实的坯体。
成型是通过模具制作合金的最终形状,可以是板材、棒材、圆柱体等不同形状。
在硬质合金的成型过程中,需要考虑压力大小、温度、速度等参数的控制,以确保合金的成型质量。
另外,还需要对成型后的坯体进行退火处理,消除成型过程中产生的应力,提高合金的成品率和密实度。
四、烧结烧结是硬质合金生产的核心工艺环节,通过高温烧结使钨、钴、碳等元素发生反应,形成坚固的结合相,实现硬质合金的硬度和耐磨性。
烧结温度一般在1300℃~1600℃之间,烧结时间和气氛对合金的性能也有影响。
在烧结过程中,还需要对合金进行冷却、退火等处理,以提高合金的稳定性和耐磨性。
同时,需要对烧结炉进行周期性的检查和维护,确保烧结过程的稳定性和可控性。
五、后处理硬质合金生产完成后,还需要进行后处理工艺,包括抛光、清洗、检测等环节。
生产培训教材系列--硬质合金压制员工培训
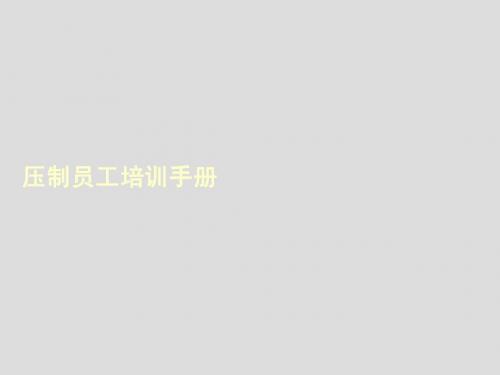
压制员工培训手册
目录
第一章:合金车间情况介绍 第二章:压制原理及操作流程 第三章:压制设备、配件以及常用材料 第四章:烧结员工操作流程 第五章:设备维护 第六章:安全注意事项 第七章:烧结岗位考核关注点以及技能等级提升标准 第八章:生产问题解决、小经验总结
主要是沿压坯的横接面和表面出现裂痕的现象.用32倍显微镜查看. 原因分析:阴模内孔严重变形,压力大于毛坯的承受力.物料过干. 解决措施:阴模内孔抛光,用适当的模具系数压制相对应的牌号.仔细核对毛坯的尺寸、 单重是否在工艺范围内.物料重处理. (c)、未压好:由于压坯内部孔洞尺寸太大,在烧结过程中不能完全消失,使合金内残留 较多的特殊孔洞现象。 原因分析:物料过干粒子太粗,压制单重比工艺要求轻,压制高度比压制工艺要求高,用 错模具等。 解决措施:返回湿磨重做物料,仔细核对产品与压制工艺是否相符,仔细核对模具.
识并盖上桶盖,不得脏化、混料、流失(物料平衡:领料重量=合格产品重量+废刀
板重量+地面料桌面料)。 • • 1.2装模与调试: a.装模:( 详情参考压制作业指导书.每个压制室墙壁上都有粘贴)
•
•
b、调试:检查产品是否有缺陷,发现异常情况应及时处理,不能处理的问题应该及
时向组长或主管汇报。 c、完成调试。在批量生产任何产品之前,应彻底检查毛坯是否存在缺陷。压制常出 现的废品类型:分层、裂纹、未压好、掉边角、痕迹、单重超标、尺寸超标、形状不 符,夹料等(注:见第八节)。进行生产时要隔5-10分钟左右抽查产品是否符合压 制生产工艺要求。压力机上的产品应及时装进舟皿中,不能堆积太多产品在压力机上, 防止产品掉边角。
硬质合金制备过程中的基本原理、烧结工艺及应用

压制成形
压制
1、压制:称量一定量粒料,装入压模中,施加一定压力,保载一段时间再脱模。 2、压胚的干燥:以橡胶作成形剂时,为了完全排除压胚中残留的汽油和水分以
提高压胚强度,和消除压胚中的应力,压胚必须经过干燥。将压胚置于蒸汽干
分类
瞬时液相烧 稳定液相烧结 熔浸 超固相线液相烧结
液相烧结原理
液相烧结的分类
瞬时液相烧结:在烧结中、初期存在液相,后期液相消失的过程。
稳定液相烧结:烧结过程中始终存在液相的烧结过程。 溶浸:采用熔点比压坯或烧结坯组分低的金属或合金,在低熔点组分熔点
或共晶点以上的温度,借熔体的流动性填充其中孔隙空间的烧结方法。
硬质合金制备过程中的基本原理、 烧结工艺及应用
团队成员
硬质合金
是指由难熔金属的硬质化合物和粘结金属通过粉末冶金工艺制成的一种合 金材料。
硬度高、熔点高
性 质
硬度高 热硬性好 耐磨性好
性能
优点
文硬质合金具有 很高的硬度、强 度、耐磨性和耐 腐蚀性,被誉为 “工业牙齿”
硬质合金的分类
钨钴类硬质合金:主要成分是碳化钨(WC) 和粘结剂钴(Co)
液相烧结原理
结果:
固相颗粒表面光滑化和球化 降低颗粒重排列阻力 有利于颗粒间的重排 进一步提高致密化效果
液相烧结原理
小颗粒的溶解速度遵循公式: dr / dt=2DCγLVΩ(r-R)/(kTr2R) 其中,R、r分别为大小晶粒的半径; Ω为固相组分的原子体积;
D为固相组分在液相中的扩散系数;
超固相线液相烧结:液相在粉末颗粒内形成,是一种在微区范围内较普通 液相烧结更为均匀的烧结过程。
硬质合金工艺流程培训
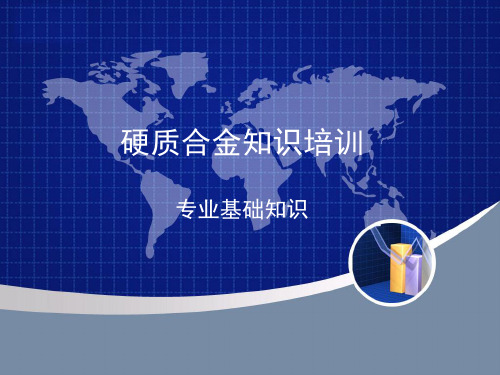
非常规性能
4、抗压强度:表示硬质合金在压缩负荷 下直至破坏时的极限强度,单位为 N/mm2。 • 相同钴含量的合金,WC晶粒度越小, 抗压强度越高。YG硬质合金额抗压强 度大于YT硬质合金。 • 钴含量项目,YT硬质合金的抗压强度 随TiC增加而降低。
非常规性能
5、冲击韧性:即合金的抗冲击强度,表征合 金抗冲击破坏的能力。即硬质合金受冲击 负荷作用而破坏时,试样单位面积所承受 的冲击功,单位为:N•m/cm2。 • 抗冲击强度检测与抗弯强度检测的差别是: 抗冲击强度检测施加载荷速度快、时间短。 • 影响冲击韧性的因素与影响抗弯强度的因 素相似。
3、粘结金属成份对合金材质的影响
粘结金属的量的变动显著影响着合金的性能。 改变粘结金属的加入量是制取不同牌号合金的重要手段之一, 一般控制在±0.2%最好,不能超过±0.5%。 不同含co量还影响着合金的总碳量的波动,含C量高的总 碳变动范围扩大,反之较少。 合金烧结后,由于W与碳溶入钴中形成r 相,r相中c含量 低,则w含量高,相反,当合金碳合量高时, r相中碳含量 也高,而w 含量降低。 烧结温温度与冷动速度对r相成份也有影响, Tr相中W 冷 却速度快,r相中W 含量。
220000
0.13
1492
2、硬质碳化物对硬质合金材质的影响
硬质碳化物对合金材质的影响有①采用不同种类的硬质碳 化物可组成不同系列的合金,WC—CO系,WC—Tac —C o、WC—(Tiw)C—co 等②碳化物的含碳量决定着合金的 碳化量、碳含量的质动将引起合金性能的变化,碳过量时, 产生游离石墨,碳不足时将产生相,都影响合金的强度的下 降。要求控制碳在 ±0.015%这是很难办到。且碳化物的含 碳量与理论值也不相同,主要是制造工艺不同,设备及环境 不同,选用的含碳量的碳化物不同,因此,我们应结合实际 条件来确定的。
硬质合金

硬质合金科技名词定义中文名称:硬质合金英文名称:hardmetal;cemented carbide定义:由作为主要组元的难熔金属碳化物和起黏结相作用的金属组成的烧结材料,具有高强度和高耐磨性。
应用学科:机械工程(一级学科);机械工程(2)粉末冶金(二级学科);粉末冶金材料与制品(三级学科)本内容由全国科学技术名词审定委员会审定公布编辑本层的厚度不过几微米,但是与同牌号的合金刀具相比,使用寿命延长了3倍,切削速度提高25%~50%。
20世纪70年代已出现第四代涂层工具,可用来切削很难加工的材料。
硬质合金是怎样烧结而成的?硬质合金是将这种或多种难熔金属的碳化物和粘接剂金属,用粉末冶金方法制成的金属材料。
编辑本段主要生产国家世界上有50多个国家生产硬质合金,总产量可达27000~28000t-,主要生产国有美国、俄罗斯、瑞典、中国、德国、日本、英国、法国等,世界硬质合金市场基本处于饱和状态,市场竞争十分激烈。
中国硬质合金工业是50年代末期开始形成的,60~70年代中国硬质合金工业得到了迅速发展,90年代初中国硬质合金总生产能力达6000t,硬质合金总产量达5000t,仅次于俄罗斯和美国,居世界第3位。
编辑本段分类与牌号WC刀具①钨钴类硬质合金主要成分是碳化钨(WC)和粘结剂钴(Co)。
其牌号是由“YG”(“硬、钴”两字汉语拼音字首)和平均含钴量的百分数组成。
例如,YG8,表示平均WCo=8%,其余为碳化钨的钨钴类硬质合金。
TIC刀具②钨钛钴类硬质合金主要成分是碳化钨、碳化钛(TiC)及钴。
其牌号由“YT”(“硬、钛”两字汉语拼音字首)和碳化钛平均含量组成。
例如,YT15,表示平均WTi=15%,其余为碳化钨和钴含量的钨钛钴类硬质合金。
钨钛钽刀具③钨钛钽(铌)类硬质合金主要成分是碳化钨、碳化钛、碳化钽(或碳化铌)及钴。
这类硬质合金又称通用硬质合金或万能硬质合金。
其牌号由“YW”(“硬”、“万”两字汉语拼音字首)加顺序号组成,如YW1。
硬质合金制备过程中的基本原理、烧结工艺及应用培训
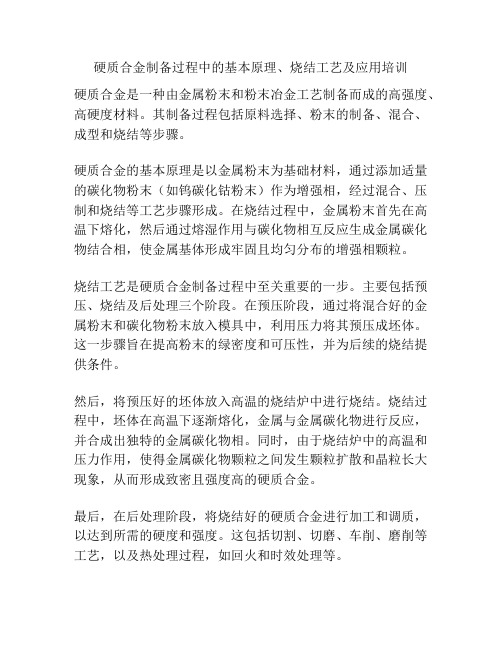
硬质合金制备过程中的基本原理、烧结工艺及应用培训硬质合金是一种由金属粉末和粉末冶金工艺制备而成的高强度、高硬度材料。
其制备过程包括原料选择、粉末的制备、混合、成型和烧结等步骤。
硬质合金的基本原理是以金属粉末为基础材料,通过添加适量的碳化物粉末(如钨碳化钴粉末)作为增强相,经过混合、压制和烧结等工艺步骤形成。
在烧结过程中,金属粉末首先在高温下熔化,然后通过熔湿作用与碳化物相互反应生成金属碳化物结合相,使金属基体形成牢固且均匀分布的增强相颗粒。
烧结工艺是硬质合金制备过程中至关重要的一步。
主要包括预压、烧结及后处理三个阶段。
在预压阶段,通过将混合好的金属粉末和碳化物粉末放入模具中,利用压力将其预压成坯体。
这一步骤旨在提高粉末的绿密度和可压性,并为后续的烧结提供条件。
然后,将预压好的坯体放入高温的烧结炉中进行烧结。
烧结过程中,坯体在高温下逐渐熔化,金属与金属碳化物进行反应,并合成出独特的金属碳化物相。
同时,由于烧结炉中的高温和压力作用,使得金属碳化物颗粒之间发生颗粒扩散和晶粒长大现象,从而形成致密且强度高的硬质合金。
最后,在后处理阶段,将烧结好的硬质合金进行加工和调质,以达到所需的硬度和强度。
这包括切割、切磨、车削、磨削等工艺,以及热处理过程,如回火和时效处理等。
硬质合金的应用非常广泛,常见的应用包括切削工具、矿业工具、电子元件等领域。
由于硬质合金具有极高的硬度、耐磨性和耐腐蚀性,因此在切削加工领域被广泛应用于车削、钻孔、铣削和切割等工艺中。
同时,在矿业工具领域,硬质合金可以用作凿岩钻头、矿山钻头等,因为它的耐磨性和强度能够满足严苛的工况要求。
在电子元件领域,由于硬质合金具有优异的导热性和耐腐蚀性能,因此常用于制造散热器、金属工具接触点等。
总之,硬质合金的制备是一个复杂的过程,包括原料选择、混合、成型和烧结等多个步骤。
通过控制工艺参数和多次迭代优化,可以获得具有优异性能的硬质合金材料,满足不同领域的应用需求。
- 1、下载文档前请自行甄别文档内容的完整性,平台不提供额外的编辑、内容补充、找答案等附加服务。
- 2、"仅部分预览"的文档,不可在线预览部分如存在完整性等问题,可反馈申请退款(可完整预览的文档不适用该条件!)。
- 3、如文档侵犯您的权益,请联系客服反馈,我们会尽快为您处理(人工客服工作时间:9:00-18:30)。
压制过程中的几个基本知识点
1、压制过程中粉末的位移与变形
1.1 位移
粉末装填在刚性模具中时,由于表面不规则,以及相互间的摩擦,颗粒间相互搭架而形成拱桥孔洞的现象叫做“拱桥效应”。
当施加压力时,拱桥效应被破坏,粉末受到压力的作用而发生相对的位移,其位移情况如下图。
1.2 变形
粉末在发生位移的同时也发生着变形,变形主要有弹性变形、塑性变形和脆性断裂,基本情况图下图。
2、单位压制压力计算 单位压制压力=总压制压力/产品的受压面积,以硬质合金的B 型
(20mm ×6.5mm ×5.25mm )试样为例:
22.15.620⨯⨯=P
单位压制压力
注:①单位为 KN/mm 2;②收缩系数以1.2为例,不同的粉末取不
同的收缩系数值;③通常情况下,收缩系数随着压制压力的增加而下降,
增加压制单重亦可使得收缩系数的下降。
3、弹性后效 图 压制压力与压坯密度的关系
粉末冶金类产品在去除压制压力,将压坯脱模以后,由于弹性内应力的松弛作用而引起压坯体积膨胀的现象,称之为弹性后效,其定量的表示式如下:
%1000
01⨯-=L L L δ 式中:δ——压坯高度或直径方向的弹性后效值;
L0——压坯脱模前的高度或直径;
L1——压坯脱模后的高度或直径。
一般来说,高度方向上的弹性后效要比直径方向上的大得多(即弹性后效具有明显的方向性),脱模的一瞬间是弹性后效最为显著的时刻,是压坯最容易出现分层、裂纹的时刻。
弹性后效是导致压坯出现分层、裂纹废品的主要原因。
其影响因素有以下几点。
① 混合料成分的影响:硬度高的粉末在压制时所产生的弹性后效大,弹性后效值随着粉末的硬度提高而提高。
WC-Co 合金混合料的弹性后效值一般比WC-TiC-Co 合金混合料的低。
高钴合金混合料的弹性后效值比低钴混合料的低,粉末氧化物和杂质含量高也会使得弹性后效值提高。
② 粉末物理性能的影响:粉末粒度细,颗粒粗糙程度降低,颗粒间结合强度降低,会增加压坯的弹性后效。
混合料的料粒干燥过度变硬时,也会使得弹性后效增加。
③ 压制压力和压制速度的影响:随着压制压力或压制速度提高,弹性后效值提高。
同时弹性后效还与压坯的直径大小有关,直径越大,弹性后效值越大,因为压制速度过快,压坯中的气体来不及溢出,弹性后效值增加。
④ 成形剂的影响:橡胶、PEG 等做成形剂的压坯强度比石蜡做成形剂的压坯强度大,弹性后效低,成形剂加量不足时,将使得压坯强度降低,弹性后效值增加。
简而言之,一切提高粉末颗粒间结合强度(压坯强度)的因素,都会导致弹性后效值降低。
一切提高粉末颗粒间接触应力的因素,都会导致弹性后效值提高。
4、压制过程中的几个参数
4.1 压缩比
模腔中粉末装填高度与压坯高度的比值称为压缩比。
影响压缩比的主要因素是粉末的装填密度,装填在模腔中的粉末的密度稍大于粉末的松装密度,与振实密度较为接近。
粉末粒度或混合料料粒越细,其松装密度越小,装填体积大,要压制期望密度压坯时的压缩比也越大。
通常情况下,硬质合金混合料的压缩比在2.5~4.0范围内,喷雾料一般在3.5~4.0,机械制粒为2.5~3.0。
4.2 收缩系数
压坯尺寸与烧结后尺寸的比值称为线收缩系数。
它与压制密度有关,在一定范围内,压坯密度越大,收缩系数越小。
通常以不出现分层、裂纹、未压好、钴池时最大密度压坯尺寸和烧结后实际测定的尺寸来确定收缩系数。
由于压坯密度分布的不均匀性,实际上采用平均线收缩系数。
平均线收缩系数可由体收缩系数求得:
3体
线收缩K K =
体积收缩系数K 体=压坯体积V1/合金制品体积V 之比: V V K 1=体
影响收缩系数的因素较多,涉及混合料质量,成型工艺,产品要求等方面。
如混合料的成分,粉末密度,成形剂的种类及加量,成型方式,产品形状、尺寸等,粉末越细,成形剂加量越大,制品形状越复杂,尺寸越大,收缩系数越大。
5、压制废品
5.1分层
沿压块的棱出现,与受压面呈一定角度,形成整齐的分界面叫分层。
造成压块分层的原因是压块中弹性内应力或弹性张力。
如混合料钴含量低,碳化物硬度高,粉末或料粒愈细,成型剂太少或分布不均匀,混合料过湿或过干,压制压力过大,单重过大,压块形状复杂,模具光洁度太差,台面不平,均有可能造成分层。
提高压块强度,减少压块内应力和弹性后效是解决分层的有效方法。
5.2 裂纹
压块中出现不规则局部断裂的现象叫裂纹。
由于压块内部的拉伸应力大于压块的抗张强度。
压块内部拉伸应力来自于弹性内应力。
应注意:影响分层的因素同样影响裂纹。
另外,延长保压时间或多次加压,减少压力,单重,改善模具设计和适当增加模具厚度,加快脱模速度,增加成型剂,提高物料松装密度;可以减少裂纹。
5.3未压好
尽管压块孔隙度可达到40%左右,但由于压制时物料或压力降原因,压坯孔隙是不均匀的;如果局部空隙尺寸太大,烧结中无法消除,叫未压好。
料粒太硬,料粒过粗,物料松装太大;松装料粒在模腔中分布不均匀,单重偏低。
均可能造成未压好(显颗粒)。