氮碳共渗表面改性技术
齿轮二段碳氮共渗工艺
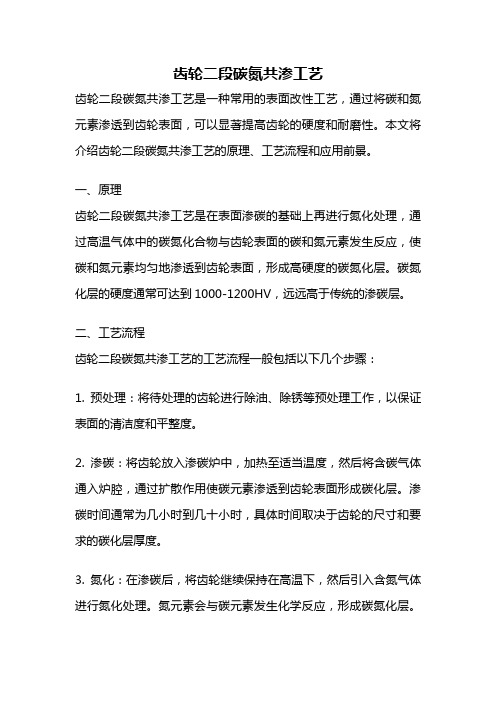
齿轮二段碳氮共渗工艺齿轮二段碳氮共渗工艺是一种常用的表面改性工艺,通过将碳和氮元素渗透到齿轮表面,可以显著提高齿轮的硬度和耐磨性。
本文将介绍齿轮二段碳氮共渗工艺的原理、工艺流程和应用前景。
一、原理齿轮二段碳氮共渗工艺是在表面渗碳的基础上再进行氮化处理,通过高温气体中的碳氮化合物与齿轮表面的碳和氮元素发生反应,使碳和氮元素均匀地渗透到齿轮表面,形成高硬度的碳氮化层。
碳氮化层的硬度通常可达到1000-1200HV,远远高于传统的渗碳层。
二、工艺流程齿轮二段碳氮共渗工艺的工艺流程一般包括以下几个步骤:1. 预处理:将待处理的齿轮进行除油、除锈等预处理工作,以保证表面的清洁度和平整度。
2. 渗碳:将齿轮放入渗碳炉中,加热至适当温度,然后将含碳气体通入炉腔,通过扩散作用使碳元素渗透到齿轮表面形成碳化层。
渗碳时间通常为几小时到几十小时,具体时间取决于齿轮的尺寸和要求的碳化层厚度。
3. 氮化:在渗碳后,将齿轮继续保持在高温下,然后引入含氮气体进行氮化处理。
氮元素会与碳元素发生化学反应,形成碳氮化层。
氮化时间通常较短,一般为几小时。
4. 冷却:将氮化后的齿轮从高温环境中取出,进行冷却处理。
冷却速度的选择会影响到碳氮化层的组织结构和性能。
5. 后处理:对冷却后的齿轮进行清洗、除渣等后处理工作,以保证表面的光洁度和质量。
三、应用前景齿轮二段碳氮共渗工艺具有以下优点:1. 提高齿轮的硬度和耐磨性:碳氮化层比传统的渗碳层硬度更高,能够有效提高齿轮的耐磨性和使用寿命。
2. 提高齿轮的承载能力:碳氮化层的硬度和强度提高了齿轮的承载能力,可以适用于更高负荷和更严苛的工况。
3. 提高齿轮的抗腐蚀性能:碳氮化层能够有效抵御氧化和腐蚀,延长齿轮的使用寿命。
齿轮二段碳氮共渗工艺在各个领域都有广泛的应用,特别是在汽车、航空航天、机械制造等行业中。
例如,在汽车传动系统中,齿轮的耐磨性和承载能力对于提高传动效率和减少噪音都起着重要作用。
齿轮二段碳氮共渗工艺能够满足对于高强度、高耐磨、高精度的齿轮的需求,提高整车的性能和可靠性。
碳氮共渗技术的研究与应用
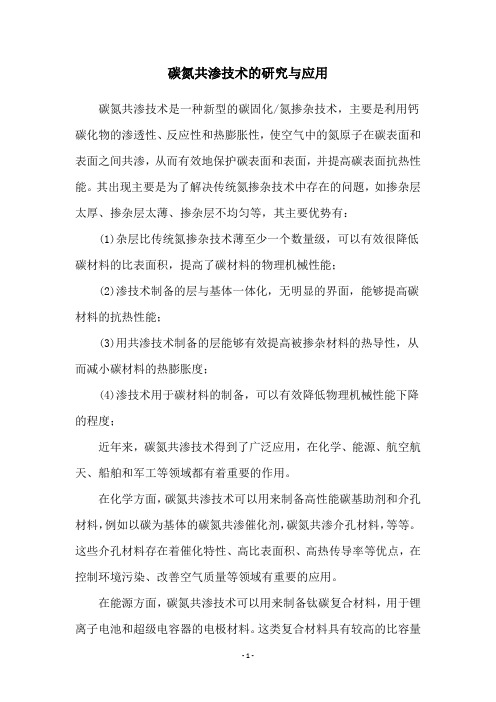
碳氮共渗技术的研究与应用碳氮共渗技术是一种新型的碳固化/氮掺杂技术,主要是利用钙碳化物的渗透性、反应性和热膨胀性,使空气中的氮原子在碳表面和表面之间共渗,从而有效地保护碳表面和表面,并提高碳表面抗热性能。
其出现主要是为了解决传统氮掺杂技术中存在的问题,如掺杂层太厚、掺杂层太薄、掺杂层不均匀等,其主要优势有:(1)杂层比传统氮掺杂技术薄至少一个数量级,可以有效很降低碳材料的比表面积,提高了碳材料的物理机械性能;(2)渗技术制备的层与基体一体化,无明显的界面,能够提高碳材料的抗热性能;(3)用共渗技术制备的层能够有效提高被掺杂材料的热导性,从而减小碳材料的热膨胀度;(4)渗技术用于碳材料的制备,可以有效降低物理机械性能下降的程度;近年来,碳氮共渗技术得到了广泛应用,在化学、能源、航空航天、船舶和军工等领域都有着重要的作用。
在化学方面,碳氮共渗技术可以用来制备高性能碳基助剂和介孔材料,例如以碳为基体的碳氮共渗催化剂,碳氮共渗介孔材料,等等。
这些介孔材料存在着催化特性、高比表面积、高热传导率等优点,在控制环境污染、改善空气质量等领域有重要的应用。
在能源方面,碳氮共渗技术可以用来制备钛碳复合材料,用于锂离子电池和超级电容器的电极材料。
这类复合材料具有较高的比容量和比能量,从而可以提高锂离子电池的安全性和稳定性,改善超级电容器的体积电容量;而且,同时具备较好的高温稳定性和抗潮湿性能,在节能、降耗和环境保护方面发挥着重要的作用。
在航空航天方面,碳氮共渗技术可用来制备碳氮复合材料,其具有优异的抗热、抗衰老性能,同时具有较好的抗氧化性能,因此可以用于航空航天领域中高温材料的制备,有效提升飞行器耐受高温环境的能力,从而提高航空安全性和可靠性。
在船舶领域,碳氮共渗技术可用来制备低密度、耐腐蚀性强、导热性、抗热稳定性好的复合材料,可用于制备船舶中的耐热保温材料,提高船舶的防护性能;而且,它还具有良好的抗氧化和抗磨损性能,从而能够延长船舶的使用寿命,改善船舶的经济效益。
模具钢的渗碳-碳氮共渗改性热处理
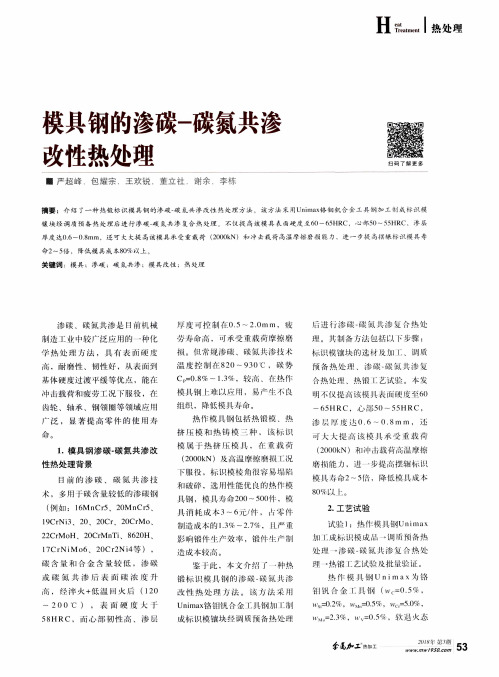
后 进 仃 渗 碳 一臌 氯 j 渗 复 合 热 处 。 j 制 备 方法 也括 以 下 步骤 :
标 lJl 镶 块 的选 材 ^乏加J-、 颅 热 处 、 渗 碳 一碳 氮 渗 复 合热 处 理 、热 锻 I:艺跌验 。 书 发
仪 提 谈 J 面硬 度 6()
~ 65H RC , 一 、 ;50~ 55H R C ,
渗 L J。 度 达 0.6~0.8 111 I11, ¨J 人 尺提 高 眩 懊 j 承 受 重 钺 甜
J 发 u !市lJ O.5~2.0m m,疲 辱 命 高 , fJr承量 重 载 荷 J李僚 磨
损 。 但 常 规 渗碳 、 碳氮 渗{支术 温 度 控 韦I 82()~930 c , 凝势 C =0.8% ~ 1.3% ,较 高 、 热 作 模 钢 上 准 以 J、 J月,易 J :,{ /f 良 细.纵 ,降 低 模 命 。
(1)标 识 模 镶 块 的 选 材 及 加 1: 将 80mm规 格 Unimax材 质棒 料 (wc=0.5%,14's.=0.2% ,
W M = 0 .5% , W c = 5.0 % ,
W =2.3% ,w =0.5%,软 退 火态 l 85HBW ) 加 工至 成 品 标 识 模镶 块 ,如 图 l所 示 。
热 作 儆 锏 U n i n1 a X乃锵 引 饥 合 I JL铡 (Ⅵ’ =().5% ,
- -
0.5.【)% ,
渗氮 渗碳 碳氮共渗

渗氮渗碳碳氮共渗碳氮共渗是一种常见的表面处理技术,通过渗碳和渗氮来改善材料的硬度和耐磨性。
本文将对渗氮、渗碳和碳氮共渗的原理、应用和工艺进行详细介绍。
一、渗氮渗氮是将氮原子渗入材料表面形成氮化物层的过程。
氮原子通过高温处理和氮气氛的作用,渗透到材料表面并与材料中的元素反应,形成硬质氮化物层。
这一薄层氮化物层不仅能提高材料的硬度和抗磨损性能,还能改善材料的耐腐蚀性。
渗氮的主要应用领域包括机械制造、汽车工业、航空航天等。
在机械制造中,渗氮可以增加零件的硬度和耐磨性,延长使用寿命;在汽车工业中,渗氮可以提高引擎零件的耐磨性和抗腐蚀性能;在航空航天领域,渗氮可以增强航空发动机部件的耐高温和耐磨性能。
渗氮的工艺流程一般包括清洗件表面、装配件和炉内预处理、渗氮和回火处理等步骤。
渗氮一般采用封闭式和开放式两种方式进行,根据具体应用需求可以选择合适的渗氮工艺。
二、渗碳渗碳是将碳原子渗入材料表面形成碳化物层的过程。
碳原子通过高温处理和含有碳气体的氛围,渗透到材料表面并在表面与材料中的元素反应,形成硬质碳化物层。
渗碳技术不仅能提升材料的硬度和耐磨性,还可以改善材料的断裂韧性和抗腐蚀性。
渗碳广泛应用于机械零件、钢铁制品等领域。
渗碳后的材料表面硬度高、耐磨性好,适用于制作耐磨零件,如轴承、齿轮等;同时碳化层的外表面与空气隔绝,降低了材料的腐蚀速率,提高了零件的使用寿命。
渗碳的工艺流程包括预处理、渗碳、淬火和回火等。
渗碳一般采用气体渗碳和液体渗碳两种方式进行,具体工艺参数可以根据材料的要求进行选择。
三、碳氮共渗碳氮共渗是将碳原子和氮原子同时渗入材料表面形成碳氮共渗层的过程。
碳氮共渗通过碳氮共渗剂和高温处理,使碳原子和氮原子分别与材料中的元素发生反应,形成硬质碳氮化物层。
碳氮共渗能够同时获得渗碳和渗氮的特性,提高材料的硬度、耐磨性和抗腐蚀性。
碳氮共渗广泛应用于汽车工业、航空航天等领域。
在汽车工业中,碳氮共渗可以提高零部件的硬度和耐磨性,同时还可以提高零部件的抗磨损能力和抗腐蚀性;在航空航天领域,碳氮共渗可以增强发动机部件的抗高温性能和抗腐蚀能力。
表面热处理包括( )。 碳氮共渗
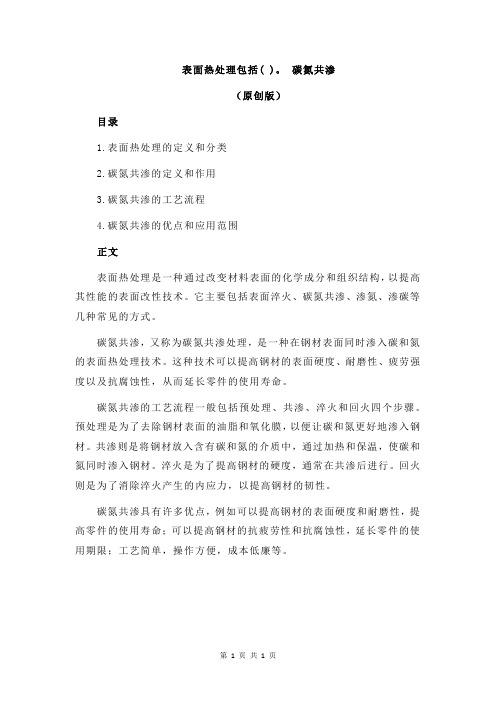
表面热处理包括( )。
碳氮共渗
(原创版)
目录
1.表面热处理的定义和分类
2.碳氮共渗的定义和作用
3.碳氮共渗的工艺流程
4.碳氮共渗的优点和应用范围
正文
表面热处理是一种通过改变材料表面的化学成分和组织结构,以提高其性能的表面改性技术。
它主要包括表面淬火、碳氮共渗、渗氮、渗碳等几种常见的方式。
碳氮共渗,又称为碳氮共渗处理,是一种在钢材表面同时渗入碳和氮的表面热处理技术。
这种技术可以提高钢材的表面硬度、耐磨性、疲劳强度以及抗腐蚀性,从而延长零件的使用寿命。
碳氮共渗的工艺流程一般包括预处理、共渗、淬火和回火四个步骤。
预处理是为了去除钢材表面的油脂和氧化膜,以便让碳和氮更好地渗入钢材。
共渗则是将钢材放入含有碳和氮的介质中,通过加热和保温,使碳和氮同时渗入钢材。
淬火是为了提高钢材的硬度,通常在共渗后进行。
回火则是为了消除淬火产生的内应力,以提高钢材的韧性。
碳氮共渗具有许多优点,例如可以提高钢材的表面硬度和耐磨性,提高零件的使用寿命;可以提高钢材的抗疲劳性和抗腐蚀性,延长零件的使用期限;工艺简单,操作方便,成本低廉等。
第1页共1页。
中碳钢碳氮共渗
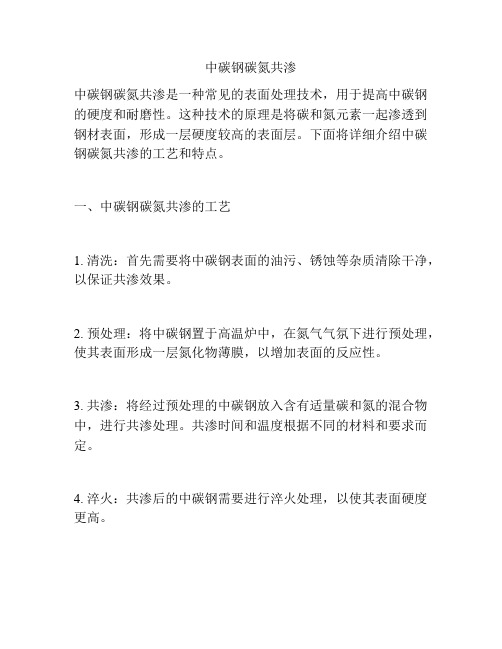
中碳钢碳氮共渗中碳钢碳氮共渗是一种常见的表面处理技术,用于提高中碳钢的硬度和耐磨性。
这种技术的原理是将碳和氮元素一起渗透到钢材表面,形成一层硬度较高的表面层。
下面将详细介绍中碳钢碳氮共渗的工艺和特点。
一、中碳钢碳氮共渗的工艺1. 清洗:首先需要将中碳钢表面的油污、锈蚀等杂质清除干净,以保证共渗效果。
2. 预处理:将中碳钢置于高温炉中,在氮气气氛下进行预处理,使其表面形成一层氮化物薄膜,以增加表面的反应性。
3. 共渗:将经过预处理的中碳钢放入含有适量碳和氮的混合物中,进行共渗处理。
共渗时间和温度根据不同的材料和要求而定。
4. 淬火:共渗后的中碳钢需要进行淬火处理,以使其表面硬度更高。
5. 清洗:最后需要对淬火后的中碳钢进行清洗,去除表面残留物,以达到更好的表面质量。
二、中碳钢碳氮共渗的特点1. 提高硬度:中碳钢碳氮共渗后,表面硬度明显提高,可以达到HRC60以上。
2. 提高耐磨性:由于共渗后表面硬度提高,因此耐磨性也得到了提高。
3. 提高抗腐蚀性:共渗后的中碳钢表面形成了一层致密的氮化物薄膜,可以起到一定的抗腐蚀作用。
4. 易于加工:共渗后的中碳钢表面硬度提高,但内部仍然保持原有的韧性和可加工性。
5. 成本低廉:与其他表面处理技术相比,中碳钢碳氮共渗成本较低。
三、中碳钢碳氮共渗的应用1. 模具制造:模具需要具有较高的硬度和耐磨性,因此中碳钢碳氮共渗技术广泛应用于模具制造领域。
2. 机械制造:机械零部件需要具有较高的硬度和耐磨性,因此中碳钢碳氮共渗技术也常用于机械制造领域。
3. 刀具制造:刀具需要具有较高的硬度和耐磨性,因此中碳钢碳氮共渗技术也广泛应用于刀具制造领域。
总之,中碳钢碳氮共渗是一种常用的表面处理技术,可以提高中碳钢的硬度、耐磨性和抗腐蚀性,广泛应用于模具制造、机械制造和刀具制造等领域。
中温气体碳氮共渗

中温气体碳氮共渗摘要:一、引言二、中温气体碳氮共渗的原理与方法1.碳氮共渗的作用2.中温气体碳氮共渗的特点3.中温气体碳氮共渗的工艺流程三、中温气体碳氮共渗的应用领域四、中温气体碳氮共渗技术的优势与不足五、发展趋势与展望正文:一、引言中温气体碳氮共渗作为一种先进的表面改性技术,在我国得到了广泛的关注与应用。
本文将从其原理、方法、应用领域、技术优势与不足以及发展趋势等方面进行全面阐述,以期为读者提供有关中温气体碳氮共渗技术的全面了解。
二、中温气体碳氮共渗的原理与方法1.碳氮共渗的作用碳氮共渗是一种在金属表面形成碳氮共渗层的表面处理方法。
通过在金属表面引入碳和氮元素,可以提高金属表面的硬度、耐磨性、耐腐蚀性等性能。
在中温条件下进行碳氮共渗,可以获得性能优异的共渗层,满足不同领域对金属材料性能的要求。
2.中温气体碳氮共渗的特点中温气体碳氮共渗具有以下特点:(1)在中温条件下进行,降低了处理过程中的能耗,提高了生产效率。
(2)采用气体作为共渗介质,使得碳氮共渗过程更加稳定,共渗层厚度均匀。
(3)通过控制气体成分和工艺参数,可调节共渗层的性能,满足不同应用场景的需求。
3.中温气体碳氮共渗的工艺流程中温气体碳氮共渗的工艺流程主要包括:预处理、共渗处理、后处理等环节。
预处理主要包括除油、除锈、抛光等,目的是去除金属表面的污物,提高共渗效果。
共渗处理是利用气体介质,在一定的温度和压力下,使碳和氮元素渗入金属表面。
后处理主要包括退火、回火等,目的是调整共渗层的性能。
三、中温气体碳氮共渗的应用领域中温气体碳氮共渗技术广泛应用于以下领域:1.航空航天:发动机零件、轴承、齿轮等部件的表面处理。
2.汽车制造:曲轴、连杆、气门等零件的表面处理。
3.机械制造:各类轴承、齿轮、刀具等产品的表面处理。
4.石油、化工、冶金等领域:阀门、管道、容器等设备的抗腐蚀性能提升。
四、中温气体碳氮共渗技术的优势与不足1.优势:(1)提高金属表面的硬度、耐磨性、耐腐蚀性等性能。
铸铁表面液相微弧放电等离子体碳氮共渗研究
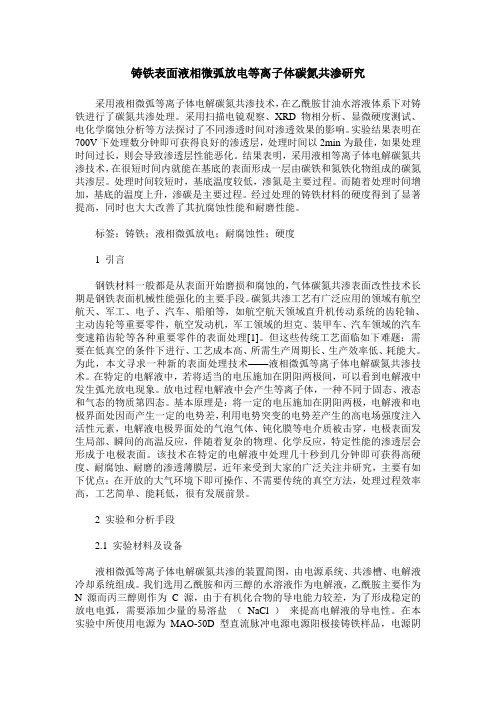
铸铁表面液相微弧放电等离子体碳氮共渗研究采用液相微弧等离子体电解碳氮共渗技术,在乙酰胺甘油水溶液体系下对铸铁进行了碳氮共渗处理。
采用扫描电镜观察、XRD物相分析、显微硬度测试、电化学腐蚀分析等方法探讨了不同渗透时间对渗透效果的影响。
实验结果表明在700V下处理数分钟即可获得良好的渗透层,处理时间以2min为最佳,如果处理时间过长,则会导致渗透层性能恶化。
结果表明,采用液相等离子体电解碳氮共渗技术,在很短时间内就能在基底的表面形成一层由碳铁和氮铁化物组成的碳氮共渗层。
处理时间较短时,基底温度较低,渗氮是主要过程。
而随着处理时间增加,基底的温度上升,渗碳是主要过程。
经过处理的铸铁材料的硬度得到了显著提高,同时也大大改善了其抗腐蚀性能和耐磨性能。
标签:铸铁;液相微弧放电;耐腐蚀性;硬度1 引言钢铁材料一般都是从表面开始磨损和腐蚀的,气体碳氮共渗表面改性技术长期是钢铁表面机械性能强化的主要手段。
碳氮共渗工艺有广泛应用的领域有航空航天、军工、电子、汽车、船舶等,如航空航天领域直升机传动系统的齿轮轴、主动齿轮等重要零件,航空发动机,军工领域的坦克、装甲车、汽车领域的汽车变速箱齿轮等各种重要零件的表面处理[1]。
但这些传统工艺面临如下难题:需要在低真空的条件下进行、工艺成本高、所需生产周期长、生产效率低、耗能大。
为此,本文寻求一种新的表面处理技术——液相微弧等离子体电解碳氮共渗技术。
在特定的电解液中,若将适当的电压施加在阴阳两极间,可以看到电解液中发生弧光放电现象。
放电过程电解液中会产生等离子体,一种不同于固态、液态和气态的物质第四态。
基本原理是:将一定的电压施加在阴阳两极,电解液和电极界面处因而产生一定的电势差,利用电势突变的电势差产生的高电场强度注入活性元素,电解液电极界面处的气泡气体、钝化膜等电介质被击穿,电极表面发生局部、瞬间的高温反应,伴随着复杂的物理、化学反应,特定性能的渗透层会形成于电极表面。
该技术在特定的电解液中处理几十秒到几分钟即可获得高硬度、耐腐蚀、耐磨的渗透薄膜层,近年来受到大家的广泛关注并研究,主要有如下优点:在开放的大气环境下即可操作、不需要传统的真空方法,处理过程效率高,工艺简单、能耗低,很有发展前景。
氮碳共渗表面改性技术
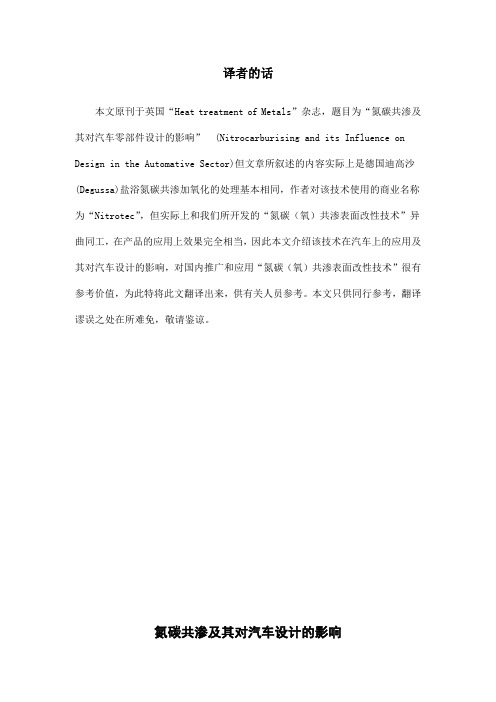
译者的话本文原刊于英国“Heat treatment of Metals”杂志,题目为“氮碳共渗及其对汽车零部件设计的影响” (Nitrocarburising and its Influence on Design in the Automative Sector)但文章所叙述的内容实际上是德国迪高沙(Degussa)盐浴氮碳共渗加氧化的处理基本相同,作者对该技术使用的商业名称为“Nitrotec”,但实际上和我们所开发的“氮碳(氧)共渗表面改性技术”异曲同工,在产品的应用上效果完全相当,因此本文介绍该技术在汽车上的应用及其对汽车设计的影响,对国内推广和应用“氮碳(氧)共渗表面改性技术”很有参考价值,为此特将此文翻译出来,供有关人员参考。
本文只供同行参考,翻译谬误之处在所难免,敬请鉴谅。
氮碳共渗及其对汽车设计的影响C.DAWES Nitrotec服务有限公司(部分选择内部参考)[ 摘要 ]作者回顾了氮碳共渗的发展,这是一种黑色金属材料的化学热处理方法,由于有富氮的化合层形成,因而具有耐磨性和抗腐蚀性,而氮扩散层则提高材料的屈服强度和疲劳强度,特别对细薄件效果显著。
该工艺赋予零件以极高的抗蚀性和漂亮的外观,使氮碳共渗向镀铬提出了挑战。
80年代在汽车工业得到广泛和成功的应用,产品从轮轴轴承到保险杠,使用该工艺可以获得独特的综合性能并能降低成本和减轻重量,由于采用先进的设备和工艺材料可以极大地减少对环境的污染。
一、前言在表面热处理家族中,氮碳共渗独树一帜,这不仅由于它能提供独特的性能结合,而且有着许多的名称和专利,在过去40年里一直引人注目。
该工艺起源于法国的盐浴铁素体处理并于1947年传人英国,当时的贸易名称为“Sulfinuz”,随后经多年探索发现亚硫酸纳能活化氰化物生成氰酸盐,从而导致引入强制通气法并命名为“Tufftride”和“活性氮化”。
这些仅局限于氰化物,采用空气搅拌,将氰化物氧化成氰酸盐,以产生所需要的氮势,而不象“sulfinuz”法那样有表面沉积形成,还需增加一道后处理的清洁工序,另一种易使人混淆的原因是一种被人称之为“液体氮化”的盐浴处理的存在,这种方法是用以氰化物为基盐的盐所产生低含量的氰酸根,用来处理工具钢在表面形成硬的合金氮化物,这种类型的盐浴因其氮势太低,故对非合金钢不起作用。
20CrMo碳氮共渗工艺改进
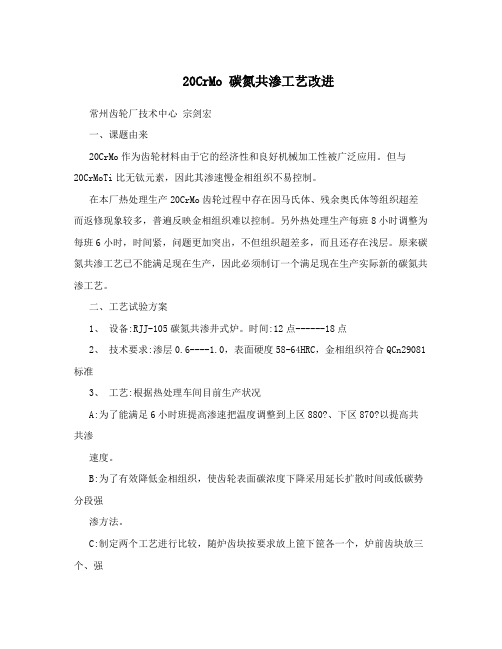
20CrMo 碳氮共渗工艺改进常州齿轮厂技术中心宗剑宏一、课题由来20CrMo作为齿轮材料由于它的经济性和良好机械加工性被广泛应用。
但与20CrMoTi比无钛元素,因此其渗速慢金相组织不易控制。
在本厂热处理生产20CrMo齿轮过程中存在因马氏体、残余奥氏体等组织超差而返修现象较多,普遍反映金相组织难以控制。
另外热处理生产每班8小时调整为每班6小时,时间紧,问题更加突出,不但组织超差多,而且还存在浅层。
原来碳氮共渗工艺已不能满足现在生产,因此必须制订一个满足现在生产实际新的碳氮共渗工艺。
二、工艺试验方案1、设备:RJJ-105碳氮共渗井式炉。
时间:12点------18点2、技术要求:渗层0.6----1.0,表面硬度58-64HRC,金相组织符合QCn29081 标准3、工艺:根据热处理车间目前生产状况A:为了能满足6小时班提高渗速把温度调整到上区880?、下区870?以提高共共渗速度。
B:为了有效降低金相组织,使齿轮表面碳浓度下降采用延长扩散时间或低碳势分段强渗方法。
C:制定两个工艺进行比较,随炉齿块按要求放上筐下筐各一个,炉前齿块放三个、强渗2.5小时取第一个、3.5 小时取第二个、出炉前取第三个。
三、试验结果按工艺规定,正常情况到温后(排气充分),进行强渗、扩散、淬火。
装炉量多煤油滴量和强渗时间应趋上限,反之下限。
为了保证工艺的可靠稳定,本轮试验连续做了12天共12炉,其中1#工艺连续做了6天共6炉,2#工艺连续做了6天共6炉。
具体试验见表、表2四、数据分析从表1是1#工艺的试验数据,从表1金相检验结果可以看出,当扩散时间超过1.25小时残余奥氏体就明显下降(照1),CN化合物1-2级,6炉齿轮全部合格,后面3炉组织更加理想,也就说当扩散时间较充分的情况下,煤油停滴、炉内碳势就有明显下降,那么工件表面的碳浓度下降,表面的碳浓度就可以控制在一合理的范围内(约0.80-1.05C%)。
我们从出炉第三炉前齿块CN化合物级别形态也说明了这问题。
氮碳共渗工艺

氮碳共渗工艺氮碳共渗工艺是一种通过将氮和碳同时渗入材料表面以提高其硬度和耐磨性的表面处理技术。
该工艺在各个领域中得到广泛应用,包括机械制造、汽车工业、航空航天等。
氮碳共渗工艺的基本原理是将材料置于含氮和碳的气氛中,在高温下进行处理。
氮和碳原子会渗入材料表面并与其基体元素发生化学反应,形成氮化物和碳化物的复合层。
这种复合层的硬度和耐磨性优于材料的基体,因此能够显著提高材料的性能。
在氮碳共渗工艺中,温度和渗透时间是关键因素。
通常情况下,温度会控制在800℃到1050℃之间,而渗透时间则根据材料的要求来确定。
较长的渗透时间可以产生更深的渗层,但也会增加处理时间和成本。
因此,在实际应用中需要根据具体情况进行合理的选择。
氮碳共渗工艺的优点之一是能够提高材料的硬度和耐磨性。
由于渗层的硬度高于基体材料,可以有效地延长材料的使用寿命。
此外,渗层还能够提高材料的抗腐蚀性能,增强其耐候性和耐高温性能。
另一个优点是氮碳共渗工艺的适用范围广。
无论是钢材、铁材还是铝材等,都可以通过这种工艺进行表面处理。
而且,氮碳共渗工艺还可以与其他表面处理技术相结合,如氮化、碳化等,进一步提高材料的性能。
然而,氮碳共渗工艺也存在一些限制。
首先,该工艺只适用于可以耐受高温的材料。
对于某些低熔点材料,渗透温度可能会导致材料的变形或损坏。
其次,渗透层的厚度受到限制。
由于渗透是一个表面处理过程,渗透层的厚度通常在几微米到几十微米之间。
对于需要更深的渗层的应用来说,可能需要采用其他处理方法。
总的来说,氮碳共渗工艺是一种有效的表面处理技术,能够显著提高材料的硬度和耐磨性。
它在各个领域中得到广泛应用,并且可以与其他表面处理技术相结合,进一步提高材料的性能。
然而,该工艺也有一些限制,需要根据具体情况进行选择和应用。
通过不断的研究和发展,相信氮碳共渗工艺将在未来得到更广泛的应用。
很全面,渗碳+渗氮+碳氮共渗表面处理工艺

很全面,渗碳+渗氮+碳氮共渗表面处理工艺渗碳与渗氮一般是指钢的表面化学热处理渗碳必须用低碳钢或低碳合金钢。
可分为固体、液体、气体渗碳三种。
应用较广泛的气体渗碳,加热温度900-950摄氏度。
渗碳深度主要取决于保温时间,一般按每小时0.2-0.25毫米估算。
表面含碳量可达0.85%-1.05%。
渗碳后必须热处理,常用淬火后低温回火。
得到表面高硬度心部高韧性的耐磨抗冲击零件。
渗氮应用最广泛的气体渗氮,加热温度500-600摄氏度。
氮原子与钢的表面中的铝、铬、钼形成氮化物,一般深度为0.1-0.6毫米,氮化层不用淬火即可得到很高的硬度,这种性能可维持到600-650摄氏度。
工件变形小,可防止水、蒸气、碱性溶液的腐蚀。
但生产周期长,成本高,氮化层薄而脆,不宜承受集中的重载荷。
主要用来处理重要和复杂的精密零件。
涂层、镀膜、是物理的方法。
“渗”是化学变化,本质不同。
钢的渗碳——就是将低碳钢在富碳的介质中加热到高温(一般为900-950C),使活性碳原子渗入钢的表面,以获得高碳的渗层组织。
随后经淬火和低温回火,使表面具有高的硬度、耐磨性及疲劳抗力,而心部仍保持足够的强度和韧性。
渗碳钢的化学成分特点(1)渗碳钢的含碳量一般都在0.15%-0.25%范围内,对于重载的渗碳体,可以提高到0.25%-0.30%,以使心部在淬火及低温回火后仍具有足够的塑性和韧性。
但含碳量不能太低,,否则就不能保证一定的强度。
(2)合金元素在渗碳钢中的作用是提高淬透性,细化晶粒,强化固溶体,影响渗层中的含碳量、渗层厚度及组织。
在渗碳钢中通常加入的合金元素有锰、铬、镍、钼、钨、钒、硼等。
常用渗碳钢可以分碳素渗碳钢和合金渗碳钢两大类(1)碳素渗碳钢中,用得最多的是15和20钢,它们经渗碳和热处理后表面硬度可达56-62HRC。
但由于淬透性较低,只适用于心部强度要求不高、受力小、承受磨损的小型零件,如轴套、链条等。
(2)低合金渗碳钢如20Cr、20Cr2MnVB、20Mn2TiB等,其渗透性和心部强度均较碳素渗碳钢高,可用于制造一般机械中的较为重要的渗碳件,如汽车、拖拉机中的齿轮、活塞销等。
碳氮共渗的原理及应用
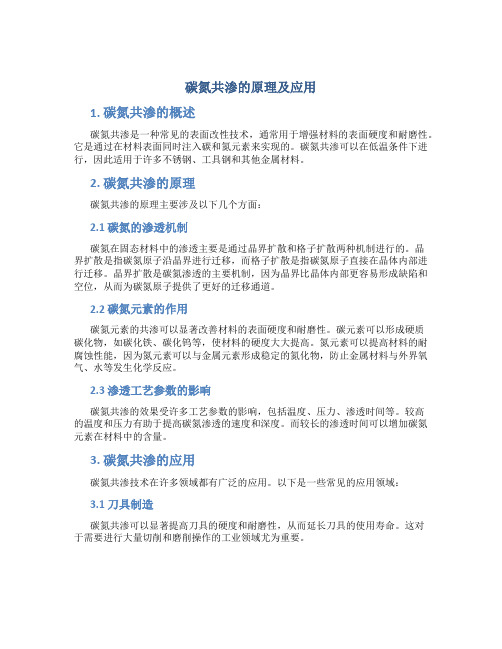
碳氮共渗的原理及应用1. 碳氮共渗的概述碳氮共渗是一种常见的表面改性技术,通常用于增强材料的表面硬度和耐磨性。
它是通过在材料表面同时注入碳和氮元素来实现的。
碳氮共渗可以在低温条件下进行,因此适用于许多不锈钢、工具钢和其他金属材料。
2. 碳氮共渗的原理碳氮共渗的原理主要涉及以下几个方面:2.1 碳氮的渗透机制碳氮在固态材料中的渗透主要是通过晶界扩散和格子扩散两种机制进行的。
晶界扩散是指碳氮原子沿晶界进行迁移,而格子扩散是指碳氮原子直接在晶体内部进行迁移。
晶界扩散是碳氮渗透的主要机制,因为晶界比晶体内部更容易形成缺陷和空位,从而为碳氮原子提供了更好的迁移通道。
2.2 碳氮元素的作用碳氮元素的共渗可以显著改善材料的表面硬度和耐磨性。
碳元素可以形成硬质碳化物,如碳化铁、碳化钨等,使材料的硬度大大提高。
氮元素可以提高材料的耐腐蚀性能,因为氮元素可以与金属元素形成稳定的氮化物,防止金属材料与外界氧气、水等发生化学反应。
2.3 渗透工艺参数的影响碳氮共渗的效果受许多工艺参数的影响,包括温度、压力、渗透时间等。
较高的温度和压力有助于提高碳氮渗透的速度和深度。
而较长的渗透时间可以增加碳氮元素在材料中的含量。
3. 碳氮共渗的应用碳氮共渗技术在许多领域都有广泛的应用。
以下是一些常见的应用领域:3.1 刀具制造碳氮共渗可以显著提高刀具的硬度和耐磨性,从而延长刀具的使用寿命。
这对于需要进行大量切削和磨削操作的工业领域尤为重要。
3.2 汽车制造碳氮共渗可以用于汽车发动机的气缸套等关键部件的表面处理,提高其耐磨性和耐腐蚀性能。
这有助于提高发动机的可靠性和寿命。
3.3 机械制造碳氮共渗可以应用于机械零件的表面硬化处理,从而提高其耐磨性和承载能力。
这对于重载机械设备的制造和使用具有重要意义。
3.4 航空航天领域碳氮共渗可以用于航空航天器材料的表面处理,提高其耐高温和抗氧化性能。
这对于确保航空航天器材料在极端环境下的安全可靠运行具有关键作用。
碳氮共渗_精品文档

碳氮共渗碳氮共渗技术在材料工程领域中扮演着重要的角色。
碳和氮是两个常见的元素,它们的共渗可以显著改善材料的性能,包括硬度、耐腐蚀性、耐磨损性以及高温性能等。
本文将介绍碳氮共渗的基本概念、工艺过程、影响因素以及应用领域。
碳氮共渗是一种将碳和氮同时渗入材料表面的过程。
通过在高温下将含有碳和氮的气体或固体与材料接触,使元素渗透到材料的表层中。
这种共渗过程不仅会增加材料的硬度,还会形成一种称为碳化物或氮化物的新相,从而显著改善材料的性能。
碳氮共渗的工艺过程通常分为几个步骤。
首先,需要选择合适的碳氮源和材料基体。
常用的碳源包括固体碳源,如石墨、金刚石等,以及气体碳源,如甲烷、乙烯等。
而氮源可以是氨气、氮气等。
材料基体通常是金属或陶瓷材料。
在共渗过程中,首先要将材料基体与碳氮源置于高温环境下,通常为800℃至1200℃。
然后,在一定时间内,让碳和氮渗透到材料的表面。
渗透速率受到温度、渗透剂浓度、渗透时间等因素的影响。
碳氮共渗的影响因素非常复杂,包括温度、渗透剂浓度、渗透时间、基体材料等。
温度是影响共渗速率和深度的关键因素。
高温可以提高材料的扩散速率,从而促进共渗的进行。
同时,渗透剂浓度和渗透时间也会直接影响共渗层的厚度和均匀性。
碳氮共渗技术在许多领域中具有广泛的应用。
其中最重要的应用之一是在材料硬度方面的提升。
碳氮共渗可以形成一种称为碳氮化物的新相,具有良好的硬度和耐磨损性。
因此,碳氮共渗被广泛应用于工具钢、汽车发动机零部件、轴承等领域。
此外,碳氮共渗还可以提高材料的耐腐蚀性能,使其更适合在恶劣环境中使用。
总之,碳氮共渗技术是一种重要的材料加工技术,它可以显著改善材料的性能。
通过调整温度、渗透剂浓度和渗透时间等参数,可以实现对共渗层性质的控制。
碳氮共渗在材料硬度、耐磨损性、耐腐蚀性等方面的应用表明,这种技术在工程领域中具有广泛的应用前景。
未来,随着材料科学的进一步发展,碳氮共渗技术将不断优化和创新,为材料工程带来更多的突破和进步。
一种中碳钢表面碳氮共渗改性层及其制备方法[发明专利]
![一种中碳钢表面碳氮共渗改性层及其制备方法[发明专利]](https://img.taocdn.com/s3/m/26e57203dc36a32d7375a417866fb84ae45cc32c.png)
专利名称:一种中碳钢表面碳氮共渗改性层及其制备方法专利类型:发明专利
发明人:应丽霞,谢越,聂重阳,吴云龙,王迪,孙泽贤,王桂香申请号:CN202011252899.8
申请日:20201111
公开号:CN112359385B
公开日:
20220422
专利内容由知识产权出版社提供
摘要:本发明公开了一种中碳钢表面碳氮共渗改性层及其制备方法,属于钢铁表面处理技术领域。
本发明解决了现有阳极液相等离子体渗透电解初期,电流过大易过载,不利于反应时工件温度控制的问题。
本发明将尿素溶解在去离子水形成碳氮源溶液,再取氯化铵颗粒加入到去离子水中形成导电盐溶液。
将碳氮源溶液与导电盐溶液混合形成复合电解液,然后将中碳钢金属试样在复合电解液中进行电解,在其表面快速生成碳氮共渗改性层。
本发明将金属试样作为阳极,利用阳极液相等离子体渗透技术,提高碳氮元素的渗透效率。
通过高电压诱发等离子体辉光放电,促使活性碳氮原子轰击金属表面,最终制备出性能优异的表面碳氮共渗改性层。
申请人:哈尔滨工程大学
地址:150001 黑龙江省哈尔滨市南岗区南通大街145号
国籍:CN
代理机构:哈尔滨市阳光惠远知识产权代理有限公司
代理人:邓宇
更多信息请下载全文后查看。
碳氮共渗 氢脆

碳氮共渗氢脆碳氮共渗是一种表面改性技术,能够提高材料的表面硬度、耐磨性和耐蚀性。
碳氮共渗通常通过高温处理,将气体分子(如氮气和甲烷)渗透到材料表面,从而改善其性能。
碳氮共渗的优点主要有以下几个方面:1.提高表面硬度。
碳氮共渗可以将硬度提高到1000-1500HV,使材料的表面更加耐磨、耐蚀。
2.延长使用寿命。
碳氮共渗处理可以显著延长零件的使用寿命,尤其是那些需要经常接触其他材料或环境的零件。
3.提升工件性能。
碳氮共渗能够提高材料的表面硬度,使其更适用于高温、高压等苛刻工况下的使用。
4.提高效率。
碳氮共渗不需要单独生产新的材料,只需要对现有材料进行表面处理即可,降低了生产成本,提高了效率。
同时,碳氮共渗技术也存在一些缺点,如氢脆问题。
氢脆是由于材料中的氢元素吸收了过多的氢气,导致材料在应力作用下发生裂纹、断裂甚至失效的现象。
氢脆的产生原因主要有两个方面。
一方面是氢气的渗入,另一方面是材料本身的质量和缺陷问题。
碳氮共渗过程中,材料表面的碳和氮被吸入后,可能会和其他物质发生反应,产生氢气。
而材料本身也可能存在一些质量问题和缺陷,如包含氢气的孔洞、裂纹等。
要解决氢脆问题,需要从以下几个方面入手:1.在设计和选择材料时,要考虑到氢脆问题。
选择合适的材料可以减少氢脆的风险。
2.在碳氮共渗前,要进行严格的材料检测,发现问题及时处理。
3.在碳氮共渗过程中,要控制渗入气体的流量和时间,避免过多的氢气被吸入。
4.在碳氮共渗后,要进行低温退火处理,使氢气逸出,减少氢脆的风险。
总之,碳氮共渗技术是一种非常有用的表面处理技术,能够有效提高材料的性能和使用寿命。
但是,氢脆问题也需要引起重视,需要在技术实践中不断加以改进和优化。
只有全面了解和掌握碳氮共渗技术,才能更好地应用于实际生产和工程领域中。
很全面,渗碳+渗氮+碳氮共渗表面处理工艺

很全面,渗碳+渗氮+碳氮共渗表面处理工艺很全面,渗碳+渗氮+碳氮共渗表面处理工艺渗碳与渗氮一般是指钢的表面化学热处理渗碳必须用低碳钢或低碳合金钢。
可分为固体、液体、气体渗碳三种。
应用较广泛的气体渗碳,加热温度900-950摄氏度。
渗碳深度主要取决于保温时间,一般按每小时0.2-0.25毫米估算。
表面含碳量可达0.85%-1.05%。
渗碳后必须热处理,常用淬火后低温回火。
得到表面高硬度心部高韧性的耐磨抗冲击零件。
渗氮应用最广泛的气体渗氮,加热温度500-600摄氏度。
氮原子与钢的表面中的铝、铬、钼形成氮化物,一般深度为0.1-0.6毫米,氮化层不用淬火即可得到很高的硬度,这种性能可维持到600-650摄氏度。
工件变形小,可防止水、蒸气、碱性溶液的腐蚀。
但生产周期长,成本高,氮化层薄而脆,不宜承受集中的重载荷。
主要用来处理重要和复杂的精密零件。
涂层、镀膜、是物理的方法。
“渗”是化学变化,本质不同。
钢的渗碳——就是将低碳钢在富碳的介质中加热到高温(一般为900-950C),使活性碳原子渗入钢的表面,以获得高碳的渗层组织。
随后经淬火和低温回火,使表面具有高的硬度、耐磨性及疲劳抗力,而心部仍保持足够的强度和韧性。
渗碳钢的化学成分特点1)渗碳钢的含碳量一般都在0.15%-0.25%范围内,对于重载的渗碳体,可以提高到0.25%-0.30%,以使心部在淬火及低温回火后仍具有足够的塑性和韧性。
但含碳量不能太低。
否则就不能保证一定的强度。
2)合金元素在渗碳钢中的感化是进步淬透性,细化晶粒,强化固溶体,影响渗层中的含碳量、渗层厚度及构造。
在渗碳钢中通常加入的合金元素有锰、铬、镍、钼、钨、钒、硼等。
常用渗碳钢可以分碳素渗碳钢和合金渗碳钢两大类1)碳素渗碳钢中,用得最多的是15和20钢,它们经渗碳和热处置惩罚后外表硬度可达56-62HRC。
但因为淬透性较低,只适用于心部强度要求不高、受力小、蒙受磨损的小型零件,如轴套、链条等。
表面热处理包括( )。 碳氮共渗
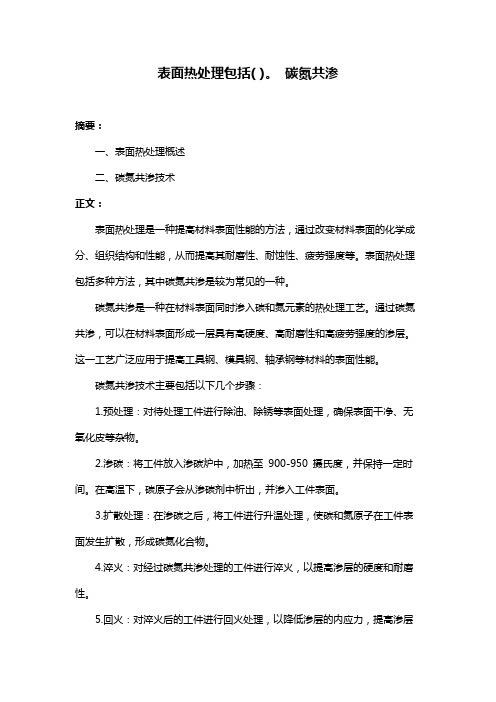
表面热处理包括( )。
碳氮共渗
摘要:
一、表面热处理概述
二、碳氮共渗技术
正文:
表面热处理是一种提高材料表面性能的方法,通过改变材料表面的化学成分、组织结构和性能,从而提高其耐磨性、耐蚀性、疲劳强度等。
表面热处理包括多种方法,其中碳氮共渗是较为常见的一种。
碳氮共渗是一种在材料表面同时渗入碳和氮元素的热处理工艺。
通过碳氮共渗,可以在材料表面形成一层具有高硬度、高耐磨性和高疲劳强度的渗层。
这一工艺广泛应用于提高工具钢、模具钢、轴承钢等材料的表面性能。
碳氮共渗技术主要包括以下几个步骤:
1.预处理:对待处理工件进行除油、除锈等表面处理,确保表面干净、无氧化皮等杂物。
2.渗碳:将工件放入渗碳炉中,加热至900-950 摄氏度,并保持一定时间。
在高温下,碳原子会从渗碳剂中析出,并渗入工件表面。
3.扩散处理:在渗碳之后,将工件进行升温处理,使碳和氮原子在工件表面发生扩散,形成碳氮化合物。
4.淬火:对经过碳氮共渗处理的工件进行淬火,以提高渗层的硬度和耐磨性。
5.回火:对淬火后的工件进行回火处理,以降低渗层的内应力,提高渗层
的韧性。
碳氮共渗技术在工业生产中具有重要意义,可以显著提高材料的表面性能,延长工具、模具等工件的使用寿命。
- 1、下载文档前请自行甄别文档内容的完整性,平台不提供额外的编辑、内容补充、找答案等附加服务。
- 2、"仅部分预览"的文档,不可在线预览部分如存在完整性等问题,可反馈申请退款(可完整预览的文档不适用该条件!)。
- 3、如文档侵犯您的权益,请联系客服反馈,我们会尽快为您处理(人工客服工作时间:9:00-18:30)。
译者的话本文原刊于英国“Heat treatment of Metals”杂志,题目为“氮碳共渗及其对汽车零部件设计的影响” (Nitrocarburising and its Influence on Design in the Automative Sector)但文章所叙述的内容实际上是德国迪高沙(Degussa)盐浴氮碳共渗加氧化的处理基本相同,作者对该技术使用的商业名称为“Nitrotec”,但实际上和我们所开发的“氮碳(氧)共渗表面改性技术”异曲同工,在产品的应用上效果完全相当,因此本文介绍该技术在汽车上的应用及其对汽车设计的影响,对国内推广和应用“氮碳(氧)共渗表面改性技术”很有参考价值,为此特将此文翻译出来,供有关人员参考。
本文只供同行参考,翻译谬误之处在所难免,敬请鉴谅。
氮碳共渗及其对汽车设计的影响C.DAWES Nitrotec服务有限公司(部分选择内部参考)[ 摘要 ]作者回顾了氮碳共渗的发展,这是一种黑色金属材料的化学热处理方法,由于有富氮的化合层形成,因而具有耐磨性和抗腐蚀性,而氮扩散层则提高材料的屈服强度和疲劳强度,特别对细薄件效果显著。
该工艺赋予零件以极高的抗蚀性和漂亮的外观,使氮碳共渗向镀铬提出了挑战。
80年代在汽车工业得到广泛和成功的应用,产品从轮轴轴承到保险杠,使用该工艺可以获得独特的综合性能并能降低成本和减轻重量,由于采用先进的设备和工艺材料可以极大地减少对环境的污染。
一、前言在表面热处理家族中,氮碳共渗独树一帜,这不仅由于它能提供独特的性能结合,而且有着许多的名称和专利,在过去40年里一直引人注目。
该工艺起源于法国的盐浴铁素体处理并于1947年传人英国,当时的贸易名称为“Sulfinuz”,随后经多年探索发现亚硫酸纳能活化氰化物生成氰酸盐,从而导致引入强制通气法并命名为“Tufftride”和“活性氮化”。
这些仅局限于氰化物,采用空气搅拌,将氰化物氧化成氰酸盐,以产生所需要的氮势,而不象“sulfinuz”法那样有表面沉积形成,还需增加一道后处理的清洁工序,另一种易使人混淆的原因是一种被人称之为“液体氮化”的盐浴处理的存在,这种方法是用以氰化物为基盐的盐所产生低含量的氰酸根,用来处理工具钢在表面形成硬的合金氮化物,这种类型的盐浴因其氮势太低,故对非合金钢不起作用。
在50年代后期引入密封淬火炉,由于具有生产效率高的优点,从而导致气体氮碳共渗的开始。
模拟氨气氛,对氮化合金钢进行处理,对碳素钢则无效,但若增加载气包括CO,CO2的含量,则可形成类似于盐浴处理的化合物层,该化合物层含有8%的氮和1%的碳,定义为ε—铁氮化合物,对气体氮碳共渗的早期研究于1961年第一次专利申请而告一段落。
一般的密封淬火炉在570℃工作时形成的化合物层存在不均匀的现象,并且存在易爆炸性,因而其商业应用并没有得到积极响应,然而后10年,衍生了许多商业化的贸易名称,诸如Nitemper,Oxycad,Trinding等等。
到60年代,为消除含氰废物的公害,从而增加成本,同时由于气体氮碳共渗技术的竞争,进而开发了新的盐浴处理技术,如Sursulf,和Tufftride TF1,但二者均没有可以除掉氰化物的后序工序。
到1970年,各种想象的商业名称变得近乎荒谬,在德国曾将认为是低温碳氮处理。
这种状况使得国际材料热处理联合会术语委员会为其作如下定义:铁素体氮碳共渗是一种“热化学处理,它以N和C在黑色金属材料表面进行富集,其中氮占主要成份,表面化合物层以下是扩散区”。
这一定义不排除r′铁氮化合物层的形成,这种氮碳共渗的概念不是以形成单相的ε层为目的的。
图1表明:在铁素体氮碳共渗开成的ε层中,氮是主要元素,在奥氏体碳氮共渗形成的马氏体层中,碳是主要元素。
二、碳和氧的作用碳和氧对ε层的形成和质量分别起作相应的作用。
在盐浴处理中,从氰根图1 氮碳共渗和碳氮共渗的比较到氰酸根碳总是存在的,在用气体处理时,碳仍然存在并与氧结合,渗层中的碳不会影响其技术特性,然而存在于钢表面的渗碳反应确实影响着氮化动力学,因此对ε层的孔隙度有影响。
在对负压处理的研究中发现了氧存在的重要性,在化合物层形成以前通过晶粒边界渗透并将气氛的氧含量从0%增加到2%,可显著地改善渗层的均匀性和增加渗层深度。
大量的实践和数据证明,对不含碳的体系能得到成功的处理结果,但无氧的体系却不能得到满意的渗层。
三、ε层形态的控制用传统的工艺方法不控制氧含量,生成的铁氮化合物层当其厚度超过5-7μm 时,就有孔隙形成,在盐浴处理中,孔隙的形成是盐中溶解铁的介质腐蚀侵蚀的结果,它明显不同于气体氮碳共渗,其孔隙是由氮原于在渗层适当的位置如晶界处结合成氮分子而形成的,因此用盐浴处理比用气体处理形成的疏松少。
为获得最佳的表面结构和化学成份以满足大量的应用要求,还有许多工作有待开发和研究。
图2表示的是三种不同类型的表层形态。
尽管一些应用要求无孔隙的厚的ε层,如图a ;而另一些应用场合则要求得到最佳抗腐蚀性,这样便需要有海绵状孔 隙的表面层,如图b ;对于在润滑条件下 要求耐磨,表层需要有储油特性,这时有 柱状孔隙的表面层是有利的,如图C 。
四、 寻找突破口直到大约10年前,氮碳共渗的应用才有所增加,其主要用来改善零件表面的耐磨性和抗疲劳性能,最著名的例子是曲轴,图5。
主要的商业应用源于用氮碳共渗这一道工序代替至少两个传统工序,从而使其在经济成本上更具竞争力。
开发的关键要素如下:1) 利用氮化后的氧化处理,提高零件 的抗腐蚀性和美化外观。
2) 利用能强化薄板零件的潜力。
3) 将工艺应用于微合金化钢。
4) 提高亚表面硬度以承受点集中负荷应力。
这些氮碳共渗的新观点由于能减轻重量,保护环境,改善安全性,因而对于图2 氮碳共渗所具有的勾层类型( a)无孔隙 (b)海绵状孔隙 (c)柱状孔隙图5 经Tuehdde 处理的Japlx 曲轴汽车行业长期广泛的发展目标起着重要的促进作用。
表1是氮碳共渗与其它工艺的性能比较,由此可看出该工艺具有降低成本的优点,可以代替渗碳淬火与防腐蚀处理二道工序。
表1:各种表面处理性能和成本的比较1、提高抗腐蚀性和美化外观1973年的石油危机导致汽车生产要求减轻车身重量并提高性能;环境保护要求取消有污染的工艺,如镀锌、镀铬,由于氮碳共渗能提高零件的抗腐蚀性和美化工件外观,因而应用得到推广。
研制的氧化工艺和有机密封剂,当用于铁氮化合物层这一特殊的成份和结构上时,显著提高了抗盐腐蚀性并美化工件外观。
Degussa公司率先在盐浴处理后使用后氧化处理,在研制低氰根盐浴过程中,该公司的工人们用氧化盐浴冷却工件并中和氰化物,同时伴随形成了黑色美观的表面,明显地改善了抗盐腐蚀性,这一过程称之为“Tufftride Q”。
然而,由于氧化盐的工作温度为350℃,这一工艺不能充分发挥氮在饱和固溶体中的间隙强化作用,尤其是低碳钢。
为获得最佳抗腐蚀性,应考虑利用表面多孔性并注入防腐蚀的密封剂。
这一过程称之为NITROTEC,其起源于处理的三阶段:氮碳共渗/氧化/保护。
即NITRocarburising/Oxidising/proTECtion。
2、利用薄板零件的强化潜力一般来说,氮碳共渗适用于所有的黑色金属包括铸铁,虽然对不锈钢的处理不太尽如人意,但当对抗磁性和耐磨性要求超过抗蚀性时,仍要采用该工艺。
然而,直到80年代,氮碳共渗应用于薄壁零件才得到认可。
碳钢在氮碳共渗后迅速冷却,在表面ε层下面大多数扩散进入铁点阵中的氮仍保留在饱和固溶体中,因而提高了基体材料屈服强度和疲劳强度。
氮扩散层的性质不取决于共渗介质的类型而是受到扩散层深度和氮碳共渗后冷却速率的控制。
在薄壁区屈服强度的提高最显著,但这种处理对低碳钢不利,当加热温度超过150℃后其强度要降低,因此在使用时必须考虑这二因素。
见图7说明。
3、应用微合金化钢近年来由于IF钢(Interstitial-Free steel)和低合金高强度(HSLA)的出现,因其优良的成型性和深拉特性,引起了人们的极大关注,对这些钢种,用氮碳共渗处理可以获得优良的性能结合,微合金化钢含有少量的强氮化物形成元图7:低碳钢经氮碳共渗淬火后强度分布图素,如Nb 、Ti 、V 等,在氮碳共渗及冷却后,除了铁晶格中氮原子的间隙固溶强化外,还有析出硬化的效应,这种硬化比一般的低碳钢具有更高的抗回火软化能力。
对IF 钢而言,氮化物析出硬化的效果比间隙强化明显,这样与其它钢相比具有更深的表面硬化现象。
如图8所示。
除非加热温度超过500℃,否则不会发 生回火软化现象,很好地满足了加工要求。
利用薄板钢的另一个优点是氮碳共渗后冷却速率的临界值更少,对IF 钢,有时 炉冷便能获得完全淬硬,对减少变形有利。
五、 设计要求与氮碳共渗相结合表2是作者根据自己的经验列出的一些应用实例,因此只代表一小部分应用范围,由于商业竞争的原因,对汽车工业来说不情愿泄漏产品信息,从表2可看出,所有的应用都采用了3个或3个以上氮碳共渗性能的特点i 而尺寸控制是所有设计均需要的,这不足为奇,因为该处理是使用前的最后一道工序,不允许尺离表面的距离 mm图8:570℃,90分钟氮碳共渗后,钢种成份对硬度分布的影响寸改变和校正变形。
表2是设计性能要求对应用的选择1)扭转盘第一个例子是扭转盘,(图10a),厚度约为0.4~0.6mm,用于粘性滑动的差动装置中,(图10b),这些盘装在一壳体内并分别安装在传动轴和壳体上,壳体内充满粘性流动液体,当传动轴相对壳体旋转时,在相邻两盘之间由于速度不同而在粘性液体中产生剪力,并随着速差的增加而增加,于是轴与壳体之间的扭矩加大。
该原理的专利人为Ferguson,由于VisodriveGmbH商业化,用于控制电力机车及四轮载人轿车。
扭转盘原生产工艺为化学镀镍,而现在用氮碳共渗+氧化的处理技术可以大量节约成本,原来加工一个盘,现可以处理40个盘。
2)座位滑动器第二个例子是座位滑动器,图11是由Rockwell国际公司出品的用于RenaultR25 车的座位滑动器。
车辆座位滑轨一般由低碳钢制造并喷漆,在随后的装配过程中要涂抹大量的油脂,无论是司机或乘客,一旦图10 扭转盘(a)粘性控制单元(b)图11 Renault 25 座位滑动器触摸其状苦不堪言,由于淬硬钢球在滑轨上来回移动因而会在导轨上产生凹痕,尽管对手动调节来说影响不是太大,但就目前上市的车辆,其座位均是电动调节,轨迹上任何凹痕的存在,座位调节的平稳性就要受到明显影响,此外,滑动器现已成为安全装置的关键所在,因此对强度有要求。
通常的表面淬硬技术,如碳氮共渗或渗碳,变形太大,而且还需要最后的表面涂层以防腐蚀。
在处理过程中控制给定的Nitrotec 处理的工艺参数,得到特殊的基体硬度分 布,以保证抗压痕产生,并能提高屈服强度,而且表面化合物层还具有耐磨、耐蚀的特点,并能获得黑色悦目的外观。