碳氮共渗与氮碳共渗的区别
渗碳与渗氮的区别

钢的渗碳和渗氮钢的渗碳---就是将低碳钢在富碳的介质中加热到高温(一般为900--950C),使活性碳原子渗入钢的表面,以获得高碳的渗层组织。
随后经淬火和低温回火,使表面具有高的硬度、耐磨性及疲劳抗力,而心部仍保持足够的强度和韧性。
渗碳钢的化学成分特点(1)渗碳钢的含碳量一般都在0.15--0.25%范围内,对于重载的渗碳体,可以提高到0.25--0.30%,以使心部在淬火及低温回火后仍具有足够的塑性和韧性。
但含碳量不能太低,否则就不能保证一定的强度。
(2)合金元素在渗碳钢中的作用是提高淬透性,细化晶粒,强化固溶体,影响渗层中的含碳量、渗层厚度及组织。
在渗碳钢中通常加入的合金元素有锰、铬、镍、钼、钨、钒、硼等。
常用渗碳钢可以分碳素渗碳钢和合金渗碳钢两大类。
(1)碳素渗碳钢中,用得最多的是15和20钢,它们经渗碳和热处理后表面硬度可达56--62HRC。
但由于淬透性较低,只适用于心部强度要求不高、受力小、承受磨损的小型零件,如轴套、链条等。
(2)低合金渗碳钢如20Cr、20Cr2MnVB、20Mn2TiB等,其渗透性和心部强度均较碳素渗碳钢高,可用于制造一般机械中的较为重要的渗碳件,如汽车、拖拉机中的齿轮、活塞销等。
(3)中合金渗碳钢如20Cr2Ni4、18Cr2N4W、15Si3MoWV等,由于具有很高的淬透性和较高的强度及韧性,主要用以制造截面较大、承载较重、受力复杂的零件,如航空发动机的齿轮、轴等。
固体渗碳;液体渗碳;气体渗碳---渗碳温度为900--950C,表面层w(碳)为0.8--1.2%,层深为0.5--2.0mm。
渗碳后的热处理---渗碳工件实际上应看作是由一种表面与中心含量相差悬殊码复合材料。
渗碳只能改变工件表面的含碳量,而其表面以及心部的最终强化则必须经过适当的热处理才能实现。
渗碳后的工件均需进行淬火和低温回火。
淬火的目的是使在表面形成高碳马氏体或高碳马氏体和细粒状碳化物组织。
钢的碳氮共渗5-4讲解

5.4 钢的碳氮共渗1:定义:在钢的表面同时渗入碳和氮的化学热处理工艺称为碳氮共渗。
2:氰化:碳氮共渗可以在气体介质中进行,也可在液体介质中进行.因为液体介质的主要成分是氰盐,故液体碳氮共渗又称为氰化。
3:目的:对低碳结构钢、中碳结构钢以及不锈钢等,为了提高其表面硬度、耐磨性及疲劳强度,进行820—850℃碳氮共渗。
中碳调质钢在570—600℃温度进行碳渗共渗,可提高其耐磨性及疲劳强度,而高速钢在550—560℃碳氮共渗的目的是进一步提高其表面硬度、耐磨性及热稳定性.4:软氮化:根据共渗温度不同,可以把碳氮共渗分为高温(900—950℃)、中温(700—880℃)及低温三种。
其中低温碳氮共渗,最初在中碳钢中应用,主要是提高其耐磨性及疲劳强度,而硬度提高不多(在碳素钢中),故又谓之软氮化。
一、碳和氮同时在钢中扩散的特点同时在钢中渗入碳和氮,如前所述,至少已是三元状态图的问题,故应以Fe-N-C三元状态图为依据。
但目前还很不完善,还不能完全根据三元状态图来进行讨论。
在这里重要讲述一些C、N二元共渗的一些特点。
1.共渗温度不同,共渗层中碳氮含量不同。
氮含量随着共渗温度的提高而降低,而碳含量则起先增加,至一定温度后反而降低。
渗剂增碳能力不同,达到最大碳含量的温度也不同。
2.碳、氮共渗时碳氮元素相互对钢中溶解度及扩散深度有影响。
由于N使y相区扩大,且Ac3点下降,因而能使钢在更低的温度增碳。
氮渗入浓度过高,在表面形成碳氮化合物相,因而氮又障碍着碳的扩散。
碳降低氮在、相中的扩散系数,所以碳减缓氮的扩散。
3.碳氮共渗过程中碳对氮的吸附有影响.碳氮共渗过程可分成两个阶段:第一阶段共渗时间较短(1—3小时),碳和氮在钢中的渗入情况相同;若延长共渗时间,出现第二阶段,此时碳继续渗入而氮不仅不从介质中吸收,反而使渗层表面部分氮原子进入到气体介质中去,表面脱氮,分析证明,这时共渗介质成分有变化,可见是由于氮和碳在钢中相互作用的结果。
金属热处理中渗氮工艺常识

金属热处理中渗氮工艺常识金属热处理中的各种渗氮工艺使氮原子渗入钢铁工件表层内的化学热处理工艺;传统的气体渗氮是把工件放入密封容器中﹐通以流动的氨气并加热﹐保温较长时间后﹐氨气热分解產生活性氮原子﹐不断吸附到工件表面﹐并扩散渗入工件表层内﹐从而改变表层的化学成分和组织﹐获得优良的表面性能。
如果在渗氮过程中同时渗入碳以促进氮的扩散﹐则称为氮碳共渗。
钢铁渗氮的研究始於20世纪初﹐20年代以后获得工业应用。
最初的气体渗氮﹐仅限於含铬﹑铝的钢﹐后来才扩大到其他钢种。
从70年{BANNED}始﹐渗氮从理论到工艺都得到迅速发展并日趋完善﹐适用的材料和工件也日益扩大﹐成为重要的化学热处理工艺之一。
渗入钢中的氮一方面由表及裡与铁形成不同含氮量的氮化铁﹐一方面与钢中的合金元素结合形成各种合金氮化物﹐特别是氮化铝﹑氮化铬。
这些氮化物具有很高的硬度﹑热稳定性和很高的弥散度﹐因而可使渗氮后的钢件得到高的表面硬度﹑耐磨性﹑疲劳强度﹑抗咬合性﹑抗大气和过热蒸汽腐蚀能力﹑抗回火软化能力﹐并降低缺口敏感性。
与渗碳工艺相比﹐渗氮温度比较低﹐因而畸变小﹐但由於心部硬度较低﹐渗层也较浅﹐一般只能满足承受轻﹑中等载荷的耐磨﹑耐疲劳要求﹐或有一定耐热﹑耐腐蚀要求的机器零件﹐以及各种切削刀具﹑冷作和热作模具等。
渗氮有多种方法﹐常用的是气体渗氮和离子渗氮。
气体渗氮:一般以提高金属的耐磨性为主要目的﹐因此需要获得高的表面硬度。
它适用於38CrMnAc等渗氮钢。
渗氮后工件表面硬度可达HV850~1200。
渗氮温度低﹐工件畸变小﹐可用於精度要求高﹑又有耐磨要求的零件﹐如鏜床鏜杆和主轴﹑磨床主轴﹑气缸套筒等。
但由於渗氮层较薄﹐不适於承受重载的耐磨零件。
气体参氮可採用一般渗氮法(即等温渗氮)或多段(二段﹑三段)渗氮法。
前者是在整个渗氮过程中渗氮温度和氨气分解率保持不变。
温度一般在480~520℃之间﹐氨气分解率为15~30%﹐保温时间近80小时。
这种工艺适用於渗层浅﹑畸变要求严﹑硬度要求高的零件﹐但处理时间过长。
最全的渗碳和渗氮区别整理表格
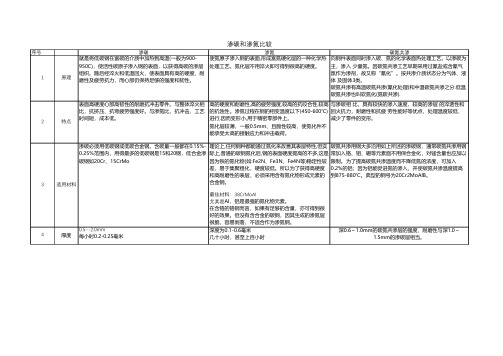
序号渗碳和渗氮比较12特点表面高硬度心部高韧性的耐磨抗冲击零件。
与整体淬火相比,抗挤压、抗弯疲劳强度好。
与渗氮比,抗冲击,工艺时间短,成本低。
高的硬度和耐磨性,高的疲劳强度,较高的抗咬合性,较高的抗蚀性。
渗氮过程在钢的相变温度以下(450-600℃)进行,因而变形小,用于精密零部件上。
氮化层较薄,一般0.5mm、且脆性较高,使氮化件不能承受太高的接触应力和冲击载荷。
渗碳渗氮就是将低碳钢在富碳的介质中加热到高温(一般为900-950C),使活性碳原子渗入钢的表面,以获得高碳的渗层组织。
随后经淬火和低温回火,使表面具有高的硬度、耐磨性及疲劳抗力,而心部仍保持足够的强度和韧性。
使氮原子渗入钢的表面,形成富氮硬化层的一种化学热处理工艺。
氮化层不用淬火即可得到很高的硬度。
原理碳氮共渗向钢件表面同时渗入碳、氮的化学表面热处理工艺。
以渗碳为主,渗入 少量氮。
因碳氮共渗工艺早期采用过氰盐或含氰气氛作为渗剂,故又称“氰化”。
按共渗介质状态分为气体、液体 及固体3类。
碳氮共渗有高温碳氮共渗(氰化处理)和中温碳氮共渗之分.低温碳氮共渗也叫软氮化(氮碳共渗).与渗碳相 比,具有较快的渗入速度,较高的渗层 的淬透性和回火抗力,耐磨性和抗疲 劳性能好等优点,处理温度较低,减少了零件的变形。
3适用材料渗碳必须用低碳钢或低碳合金钢。
含碳量一般都在0.15%-0.25%范围内,用得最多的低碳钢是15和20钢,低合金渗碳钢如20Cr、15CrMo理论上,任何钢种都能通过氮化来改善其表层特性,但实际上,普通的碳钢氮化后,钢的表面硬度提高的不多,这是因为铁的氮化物(如:Fe2N、Fe3N、Fe4N等)稳定性较差,易于集聚粗化,硬度较低。
所以为了获得高硬度和高耐磨性的表层,必须采用含有氮化物形成元素的合金钢。
最佳材料:38CrMoAl尤其是AI,铝是最强的氮化物元素。
在含铬的铬钢而言,如果有足够的含量,亦可得到很好的效果。
但没有含合金的碳钢,因其生成的渗氮层很脆,容易剥落,不适合作为渗氮钢。
渗碳与渗氮的区别
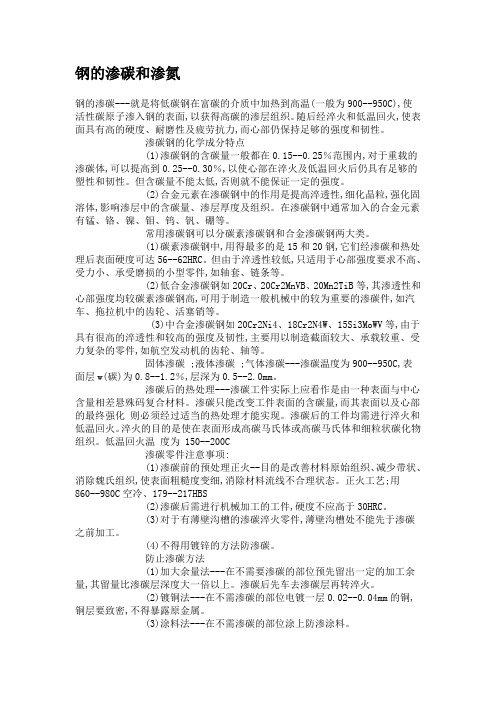
钢的渗碳和渗氮钢的渗碳---就是将低碳钢在富碳的介质中加热到高温(一般为900--950C),使活性碳原子渗入钢的表面,以获得高碳的渗层组织。
随后经淬火和低温回火,使表面具有高的硬度、耐磨性及疲劳抗力,而心部仍保持足够的强度和韧性。
渗碳钢的化学成分特点(1)渗碳钢的含碳量一般都在0.15--0.25%范围内,对于重载的渗碳体,可以提高到0.25--0.30%,以使心部在淬火及低温回火后仍具有足够的塑性和韧性。
但含碳量不能太低,否则就不能保证一定的强度。
(2)合金元素在渗碳钢中的作用是提高淬透性,细化晶粒,强化固溶体,影响渗层中的含碳量、渗层厚度及组织。
在渗碳钢中通常加入的合金元素有锰、铬、镍、钼、钨、钒、硼等。
常用渗碳钢可以分碳素渗碳钢和合金渗碳钢两大类。
(1)碳素渗碳钢中,用得最多的是15和20钢,它们经渗碳和热处理后表面硬度可达56--62HRC。
但由于淬透性较低,只适用于心部强度要求不高、受力小、承受磨损的小型零件,如轴套、链条等。
(2)低合金渗碳钢如20Cr、20Cr2MnVB、20Mn2TiB等,其渗透性和心部强度均较碳素渗碳钢高,可用于制造一般机械中的较为重要的渗碳件,如汽车、拖拉机中的齿轮、活塞销等。
(3)中合金渗碳钢如20Cr2Ni4、18Cr2N4W、15Si3MoWV等,由于具有很高的淬透性和较高的强度及韧性,主要用以制造截面较大、承载较重、受力复杂的零件,如航空发动机的齿轮、轴等。
固体渗碳 ;液体渗碳 ;气体渗碳---渗碳温度为900--950C,表面层w(碳)为0.8--1.2%,层深为0.5--2.0mm。
渗碳后的热处理---渗碳工件实际上应看作是由一种表面与中心含量相差悬殊码复合材料。
渗碳只能改变工件表面的含碳量,而其表面以及心部的最终强化则必须经过适当的热处理才能实现。
渗碳后的工件均需进行淬火和低温回火。
淬火的目的是使在表面形成高碳马氏体或高碳马氏体和细粒状碳化物组织。
各种渗层比较解读

Fe2B
或FeB+Fe2B
渗后
热处理
淬火+低温回火
无
无
淬火+回火
渗层
硬度
56~64HRC
950~1200HV
500~1000HV
58~67HRC
1300~2300HV
常用
渗剂
固:木炭,碳酸盐,粘结剂
优点
比渗氮工艺的渗层厚,可承受重载荷;工艺时间短;渗前不需要调质处理
常用固体渗剂
50%铬铁+
45%Al2O3+5%NH4Cl
常用硼砂盐浴
5%~10%钒粉+
95%~90%无水硼砂+少量中性盐
固体粉末或颗粒
40%~50%钛粉+
55%~45%Al2O3+3%NaF+2%NH4Cl
硼砂盐浴
4%~8%铌粉+
96%~92%硼砂
渗温
/℃
950~1050
900~1000
900~1000
渗氮层的机械性能比渗碳层的好;渗氮温度低,渗后不进行淬火处理,工件变形小;渗氮温度低
与渗氮相比,氮碳共渗的速度快,渗层韧性更高
与渗碳相比处理温度低,变形小,共渗层的机械性能更好
工艺时间短,渗层机械性能好
缺点
硬度和耐磨性不如渗氮层高;渗碳温度高,工件变形大;渗后往往需要淬火处理
渗氮层较薄、且脆性大,不能承受太大的接触应力和高的冲击载荷;渗氮时间长,生产率低,成本较高
8%~15%V2O5+
60%~70%Na2B4O7+1%~3%NaF+Al
常用固体粉末
第十章-模具表面强化技术

*
表面化学热处理技术
二、渗氮(氮化)
(一)气体渗氮
表2 部分模具钢的气体渗氮工艺规范
牌号
处理 方法
渗氮工艺规范
渗氮层 深度/mm
表面硬度
阶段
渗氮温度/℃
时间/h
氨分解率/%
30CrMnSiA
一段
—
500±5
25~30
20~30
0.2~0.3
(一)气体渗氮
(1) 经过渗氮后钢表面形成一层极硬的合金氮化物,渗氮层的硬度一般可达到68~72HRC,不需要再经过淬火便具有很高的表面硬度和耐磨层,而且还可以保持到600~650℃而不明显下降。
(2) 渗氮后钢的疲劳极限可提高15%~35%。这是由于渗氮层的体积增大,使工件表面产生了残余压应力。
(3) 渗氮后的钢具有很高的抗腐蚀能力。
>58HRC
Cr12MoV
760~800HV
*
表面化学热处理技术
二、渗氮(氮化)
(二)离子渗氮
离子渗氮有如下特点:
(1) 渗氮速度快,生产周期短。
(2) 渗氮层质量高。
(3) 工件的变形小。
(4) 对材料的适应性强。
氮碳共渗
提高硬度、耐磨性、抗粘附性、抗蚀性、耐热疲劳性
冷挤模、拉深模、挤压模穿孔针
渗硼
具有极好的表面硬度、耐磨性、抗粘附性、抗氧化性、热硬性、良好的抗蚀性
挤压模、拉深模
碳氮硼三元共渗
提高硬度、强度、耐磨性、耐疲劳性、抗蚀性
挤压模、冲头针尖
盐浴覆层 (TD处理)
提高硬度、耐磨性、耐热疲劳性、抗蚀性、抗粘附性、抗氧化性
很全面,渗碳+渗氮+碳氮共渗表面处理工艺

很全面,渗碳+渗氮+碳氮共渗表面处理工艺渗碳与渗氮一般是指钢的表面化学热处理渗碳必须用低碳钢或低碳合金钢。
可分为固体、液体、气体渗碳三种。
应用较广泛的气体渗碳,加热温度900-950摄氏度。
渗碳深度主要取决于保温时间,一般按每小时0.2-0.25毫米估算。
表面含碳量可达0.85%-1.05%。
渗碳后必须热处理,常用淬火后低温回火。
得到表面高硬度心部高韧性的耐磨抗冲击零件。
渗氮应用最广泛的气体渗氮,加热温度500-600摄氏度。
氮原子与钢的表面中的铝、铬、钼形成氮化物,一般深度为0.1-0.6毫米,氮化层不用淬火即可得到很高的硬度,这种性能可维持到600-650摄氏度。
工件变形小,可防止水、蒸气、碱性溶液的腐蚀。
但生产周期长,成本高,氮化层薄而脆,不宜承受集中的重载荷。
主要用来处理重要和复杂的精密零件。
涂层、镀膜、是物理的方法。
“渗”是化学变化,本质不同。
钢的渗碳——就是将低碳钢在富碳的介质中加热到高温(一般为900-950C),使活性碳原子渗入钢的表面,以获得高碳的渗层组织。
随后经淬火和低温回火,使表面具有高的硬度、耐磨性及疲劳抗力,而心部仍保持足够的强度和韧性。
渗碳钢的化学成分特点(1)渗碳钢的含碳量一般都在0.15%-0.25%范围内,对于重载的渗碳体,可以提高到0.25%-0.30%,以使心部在淬火及低温回火后仍具有足够的塑性和韧性。
但含碳量不能太低,,否则就不能保证一定的强度。
(2)合金元素在渗碳钢中的作用是提高淬透性,细化晶粒,强化固溶体,影响渗层中的含碳量、渗层厚度及组织。
在渗碳钢中通常加入的合金元素有锰、铬、镍、钼、钨、钒、硼等。
常用渗碳钢可以分碳素渗碳钢和合金渗碳钢两大类(1)碳素渗碳钢中,用得最多的是15和20钢,它们经渗碳和热处理后表面硬度可达56-62HRC。
但由于淬透性较低,只适用于心部强度要求不高、受力小、承受磨损的小型零件,如轴套、链条等。
(2)低合金渗碳钢如20Cr、20Cr2MnVB、20Mn2TiB等,其渗透性和心部强度均较碳素渗碳钢高,可用于制造一般机械中的较为重要的渗碳件,如汽车、拖拉机中的齿轮、活塞销等。
碳氮共渗_精品文档

碳氮共渗碳氮共渗技术在材料工程领域中扮演着重要的角色。
碳和氮是两个常见的元素,它们的共渗可以显著改善材料的性能,包括硬度、耐腐蚀性、耐磨损性以及高温性能等。
本文将介绍碳氮共渗的基本概念、工艺过程、影响因素以及应用领域。
碳氮共渗是一种将碳和氮同时渗入材料表面的过程。
通过在高温下将含有碳和氮的气体或固体与材料接触,使元素渗透到材料的表层中。
这种共渗过程不仅会增加材料的硬度,还会形成一种称为碳化物或氮化物的新相,从而显著改善材料的性能。
碳氮共渗的工艺过程通常分为几个步骤。
首先,需要选择合适的碳氮源和材料基体。
常用的碳源包括固体碳源,如石墨、金刚石等,以及气体碳源,如甲烷、乙烯等。
而氮源可以是氨气、氮气等。
材料基体通常是金属或陶瓷材料。
在共渗过程中,首先要将材料基体与碳氮源置于高温环境下,通常为800℃至1200℃。
然后,在一定时间内,让碳和氮渗透到材料的表面。
渗透速率受到温度、渗透剂浓度、渗透时间等因素的影响。
碳氮共渗的影响因素非常复杂,包括温度、渗透剂浓度、渗透时间、基体材料等。
温度是影响共渗速率和深度的关键因素。
高温可以提高材料的扩散速率,从而促进共渗的进行。
同时,渗透剂浓度和渗透时间也会直接影响共渗层的厚度和均匀性。
碳氮共渗技术在许多领域中具有广泛的应用。
其中最重要的应用之一是在材料硬度方面的提升。
碳氮共渗可以形成一种称为碳氮化物的新相,具有良好的硬度和耐磨损性。
因此,碳氮共渗被广泛应用于工具钢、汽车发动机零部件、轴承等领域。
此外,碳氮共渗还可以提高材料的耐腐蚀性能,使其更适合在恶劣环境中使用。
总之,碳氮共渗技术是一种重要的材料加工技术,它可以显著改善材料的性能。
通过调整温度、渗透剂浓度和渗透时间等参数,可以实现对共渗层性质的控制。
碳氮共渗在材料硬度、耐磨损性、耐腐蚀性等方面的应用表明,这种技术在工程领域中具有广泛的应用前景。
未来,随着材料科学的进一步发展,碳氮共渗技术将不断优化和创新,为材料工程带来更多的突破和进步。
碳氮共渗作用
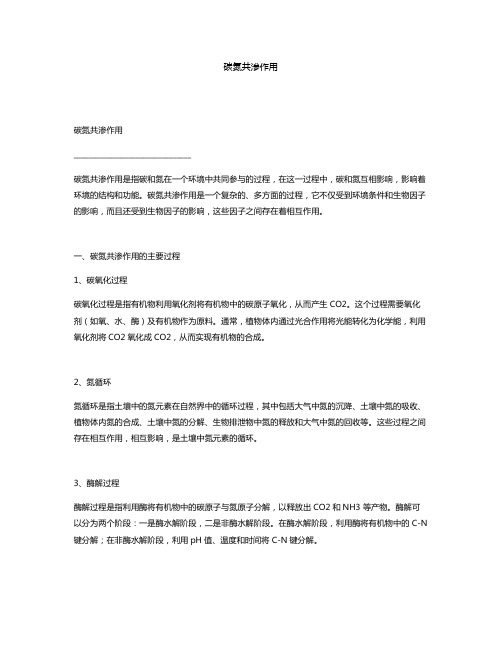
碳氮共渗作用碳氮共渗作用________________________________碳氮共渗作用是指碳和氮在一个环境中共同参与的过程,在这一过程中,碳和氮互相影响,影响着环境的结构和功能。
碳氮共渗作用是一个复杂的、多方面的过程,它不仅受到环境条件和生物因子的影响,而且还受到生物因子的影响,这些因子之间存在着相互作用。
一、碳氮共渗作用的主要过程1、碳氧化过程碳氧化过程是指有机物利用氧化剂将有机物中的碳原子氧化,从而产生CO2。
这个过程需要氧化剂(如氧、水、酶)及有机物作为原料。
通常,植物体内通过光合作用将光能转化为化学能,利用氧化剂将CO2氧化成CO2,从而实现有机物的合成。
2、氮循环氮循环是指土壤中的氮元素在自然界中的循环过程,其中包括大气中氮的沉降、土壤中氮的吸收、植物体内氮的合成、土壤中氮的分解、生物排泄物中氮的释放和大气中氮的回收等。
这些过程之间存在相互作用,相互影响,是土壤中氮元素的循环。
3、酶解过程酶解过程是指利用酶将有机物中的碳原子与氮原子分解,以释放出CO2和NH3 等产物。
酶解可以分为两个阶段:一是酶水解阶段,二是非酶水解阶段。
在酶水解阶段,利用酶将有机物中的C-N 键分解;在非酶水解阶段,利用pH值、温度和时间将C-N键分解。
4、吸收过程吸收过程是指土壤中的微生物利用CO2 和NH3 作为原料,利用有机物中的C-N 键合成有机物。
土壤中存在大量微生物,它们能够将CO2 和NH3 吸收并利用它们合成大量有机物。
二、碳氮共渗作用对土壤肥力的影响1、促进土壤有机物的形成通过碳氮共渗作用,微生物能够将CO2 和NH3 吸收并利用它们合成大量有机物。
这些有机物不仅可以增加土壤的有机质含量,而且还能够促进微生物的生长和多样性,从而促进土壤的肥力。
2、促进根系发育通过碳氮共渗作用,CO2 和NH3 能够被微生物吸收并利用,形成大量有机物。
这些有机物不仅可以增加土壤的含水量,而且也可以促进根系的发育,使根系能够吸收更多的养分,从而促进植物的生长。
渗碳 渗氮、氮碳共渗标准
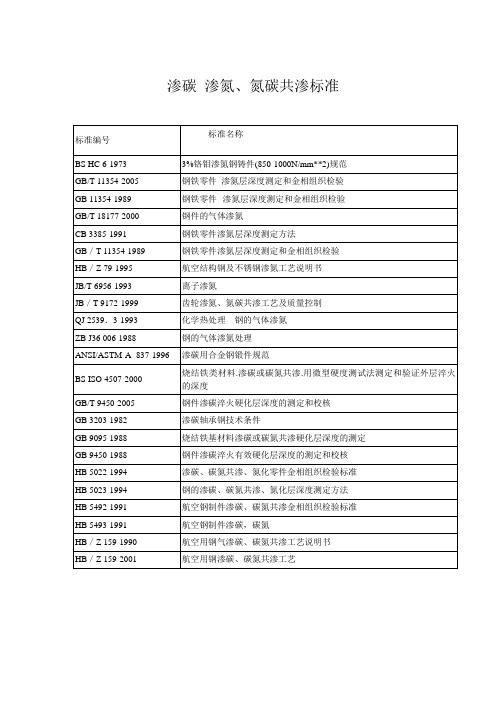
渗碳渗氮、氮碳共渗标准通俗地说,不锈钢就是不容易生锈的钢,实际上一部分不锈钢,既有不锈性,又有耐酸性(耐蚀性)。
不锈钢的不锈性和耐蚀性是由于其表面上富铬氧化膜(钝化膜)的形成。
这种不锈性和耐蚀性是相对的。
试验表明,钢在大气、水等弱介质中和硝酸等氧化性介质中,其耐蚀性随钢中铬含水量的增加而提高,当铬含量达到一定的百分比时,钢的耐蚀性发生突变,即从易生锈到不易生锈,从不耐蚀到耐腐蚀。
不锈钢的分类方法很多。
按室温下的组织结构分类,有马氏体型、奥氏体型、铁素体和双相不锈钢;按主要化学成分分类,基本上可分为铬不锈钢和铬镍不锈钢两大系统;按用途分则有耐硝酸不锈钢、耐硫酸不锈钢、耐海水不锈钢等等,按耐蚀类型分可分为耐点蚀不锈钢、耐应力腐蚀不锈钢、耐晶间腐蚀不锈钢等;按功能特点分类又可分为无磁不锈钢、易切削不锈钢、低温不锈钢、高强度不锈钢等等。
由于不锈钢材具有优异的耐蚀性、成型性、相容性以及在很宽温度范围内的强韧性等系列特点,所以在重工业、轻工业、生活用品行业以及建筑装饰等行业中获取得广泛的应用。
奥氏体不锈钢在常温下具有奥氏体组织的不锈钢。
钢中含Cr约18%、Ni 8%~10%、C约0.1%时,具有稳定的奥氏体组织。
奥氏体铬镍不锈钢包括著名的18Cr-8Ni钢和在此基础上增加Cr、Ni含量并加入Mo、Cu、Si、Nb、Ti等元素发展起来的高Cr-Ni 系列钢。
奥氏体不锈钢无磁性而且具有高韧性和塑性,但强度较低,不可能通过相变使之强化,仅能通过冷加工进行强化。
如加入S,Ca,Se,Te等元素,则具有良好的易切削性。
此类钢除耐氧化性酸介质腐蚀外,如果含有Mo、Cu等元素还能耐硫酸、磷酸以及甲酸、醋酸、尿素等的腐蚀。
此类钢中的含碳量若低于0.03%或含Ti、Ni,就可显著提高其耐晶间腐蚀性能。
高硅的奥氏体不锈钢浓硝酸肯有良好的耐蚀性。
由于奥氏体不锈钢具有全面的和良好的综合性能,在各行各业中获得了广泛的应用。
铁素体不锈钢在使用状态下以铁素体组织为主的不锈钢。
渗碳、渗氮、碳氮共渗

渗碳、渗氮、碳氮共渗三者有什么不同?反映在材料题上具体有什么不一样的效果
渗碳:渗碳后的工件经淬火和低温回火,使表面具有高硬度和耐磨性,而心部仍保持良好的塑性和韧性,从而满足工件外硬内韧的使用要求。
渗氮:零件渗氮后表面形成一层氮化物,不需要淬火就可以具有高的硬度、耐磨性、抗疲劳性和一定的腐蚀性,而且变形也很小。
碳氮共渗:又称氰化。
碳氮共渗是将钢件表面同时渗入碳原子和氮原子,形成碳氮共渗层,以提高工件的硬度、耐磨性和疲劳强度的处理方法。
渗碳淬火、渗氮与碳氮共渗外观区别
三种热处理工艺处理的工件外观上差别不大,都有氧化色。
通过外观观察即可判定其热处理工艺的可能性不大。
渗氮是为什么。
渗碳是因为低碳钢含碳量不够。
那渗氮是为什么。
渗氮,是在一定温度下一定介质中使氮原子渗入工件表层的化学热处理工艺。
常见有液体渗氮、气体渗氮、离子渗氮。
传统的气体渗氮是把工件放入密封容器中,通以流动的氨气并加热,保温较长时间后,氨气热分解产生活性氮原子,不断吸附到工件表面,并扩散渗入工件表层内,从而改变表层的化学成分和组织,获得优良的表面性能。
渗入钢中的氮一方面由表及里与铁形成不同含氮量的氮化铁,一方面与钢中的合金元素结合形成各种合金氮化物,特别是氮化铝、氮化铬。
这
些氮化物具有很高的硬度、热稳定性和很高的弥散度,因而可使渗氮后的钢件得到高的表面硬度、耐磨性、疲劳强度、抗咬合性、抗大气和过热蒸汽腐蚀能力、抗回火软化能力,并降低缺口敏感性。
另外渗碳的最终目的是使渗过碳的工件表面获得很高的硬度,提高其耐磨程度。
很全面,渗碳+渗氮+碳氮共渗表面处理工艺

很全面,渗碳+渗氮+碳氮共渗表面处理工艺很全面,渗碳+渗氮+碳氮共渗表面处理工艺渗碳与渗氮一般是指钢的表面化学热处理渗碳必须用低碳钢或低碳合金钢。
可分为固体、液体、气体渗碳三种。
应用较广泛的气体渗碳,加热温度900-950摄氏度。
渗碳深度主要取决于保温时间,一般按每小时0.2-0.25毫米估算。
表面含碳量可达0.85%-1.05%。
渗碳后必须热处理,常用淬火后低温回火。
得到表面高硬度心部高韧性的耐磨抗冲击零件。
渗氮应用最广泛的气体渗氮,加热温度500-600摄氏度。
氮原子与钢的表面中的铝、铬、钼形成氮化物,一般深度为0.1-0.6毫米,氮化层不用淬火即可得到很高的硬度,这种性能可维持到600-650摄氏度。
工件变形小,可防止水、蒸气、碱性溶液的腐蚀。
但生产周期长,成本高,氮化层薄而脆,不宜承受集中的重载荷。
主要用来处理重要和复杂的精密零件。
涂层、镀膜、是物理的方法。
“渗”是化学变化,本质不同。
钢的渗碳——就是将低碳钢在富碳的介质中加热到高温(一般为900-950C),使活性碳原子渗入钢的表面,以获得高碳的渗层组织。
随后经淬火和低温回火,使表面具有高的硬度、耐磨性及疲劳抗力,而心部仍保持足够的强度和韧性。
渗碳钢的化学成分特点1)渗碳钢的含碳量一般都在0.15%-0.25%范围内,对于重载的渗碳体,可以提高到0.25%-0.30%,以使心部在淬火及低温回火后仍具有足够的塑性和韧性。
但含碳量不能太低。
否则就不能保证一定的强度。
2)合金元素在渗碳钢中的感化是进步淬透性,细化晶粒,强化固溶体,影响渗层中的含碳量、渗层厚度及构造。
在渗碳钢中通常加入的合金元素有锰、铬、镍、钼、钨、钒、硼等。
常用渗碳钢可以分碳素渗碳钢和合金渗碳钢两大类1)碳素渗碳钢中,用得最多的是15和20钢,它们经渗碳和热处置惩罚后外表硬度可达56-62HRC。
但因为淬透性较低,只适用于心部强度要求不高、受力小、蒙受磨损的小型零件,如轴套、链条等。
金属热处理中渗氮工艺常识

离子渗氮:
离子渗氮又称辉光渗氮﹐是利用辉光放电原理进行的。把金属工件作为阴极放入通有含氮介质的负压容器中﹐通电后介质中的氮氢原子被电离﹐在阴阳极之间形成等离子区。在等离子区强电场作用下﹐氮和氢的正离子以高速向工件表面轰击。离子的高动能转变为热能﹐加热工件表面至所需温度。由於离子的轰击﹐工件表面產生原子溅射﹐因而得到净化﹐同时由於吸附和扩散作用﹐氮遂渗入工件表面。
还有以抗蚀为目的的气体渗氮﹐渗氮温度在550~700℃之间﹐保温0.5~3小时﹐氨分解率为35~70%﹐工件表层可获得化学稳定性高的化合物层﹐防止工件受湿空气﹑过热蒸汽﹑气体燃烧產物等的腐蚀。
正常的气体渗般不影响使用。
气体参氮可採用一般渗氮法(即等温渗氮)或多段(二段﹑三段)渗氮法。前者是在整个渗氮过程中渗氮温度和氨气分解率保持不变。温度一般在480~520℃之间﹐氨气分解率为15~30%﹐保温时间近80小时。这种工艺适用於渗层浅﹑畸变要求严﹑硬度要求高的零件﹐但处理时间过长。多段渗氮是在整个渗氮过程中按不同阶段分别採用不同温度﹑不同氨分解率﹑不同时间进行渗氮和扩散。整个渗氮时间可以缩短到近50小时﹐能获得较深的渗层﹐但这样渗氮温度较高﹐畸变较大。
3.氨的分解率
渗氮是其它合金元素与初生态的氮接触而进行(初生态氮的产生,由氨气与加热中的零件接触时零件本身成为触媒而促进氨的分解),虽然在各种分解率的氨气下,皆可渗氮,但一般都采用15~30%的分解率,并按渗氮所需厚度保持4~10小时,处理温度保持在520℃左右。
4.冷却
大部份的工业用渗氮炉都有热交换机,在渗氮工作完成后冷却加热炉及被处理零件。即渗氮完成后,将加热电源关闭,使炉温降低约50℃,然后将氨的流量增加一倍后开启热交换机,此时须注重确认炉内压力为正压。等候导入炉中的氨气安定后,即可减少氨的流量至保持炉内正压为止,当炉温下降至150℃以下时,方可启开炉盖。
渗碳与渗氮,碳氮共渗处理
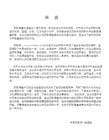
北京基耐尔热处理工艺研究所
1. 等温淬火盐
适用于钢铁材料的150~550℃的盐浴等温淬火,盐浴分级淬火,盐浴本身的流动性好,稳定性好,均匀性好,无老化,适合于连续生产线,单槽、多槽等温淬火和回火。是取代铅浴的理想工艺。...
最后修改日期:2010-03-10
2. 盐浴渗碳
也称无毒原料液体碳氮共渗,盐浴温度在720℃左右,渗层厚度可在0.08~0.3mm方便地进
冲击和重载荷下的零件 表面耐磨、心部韧性、强度都高 30CRNiMoA
精密零件 表面硬度、心部强度都高 38CrMoAlA
对高硬度、高耐磨性要求的氮化件,不宜选用碳钢和一般合金钢。
钢的碳氮
共渗---就是将碳、氮同时渗入工件表层的化学热处理过程(加热温度高于临界温度Ac1或Ac3 ,不宜高于900C,以吸收碳原子为主)。兼有两者的长处,这种工艺有逐步代替渗碳的趋势。主要优点如下:
渗氮用钢---从理论上讲,所有的钢铁材料都能渗氮。但我们只将那些适用可渗氮处理并能获得满意效果的钢才称为渗氮用钢。凡含有Cr、Mo、V、Ti、Al等元素的低、中碳合金结构钢、工具钢、不锈钢(不锈钢渗氮前需去除工件表面的钝化膜,对不锈钢、耐热钢可直接用离子氮化方法处理)、球墨铸铁等均可进行渗氮。
渗氮后零件虽然具有高硬度、高耐磨性和高的疲劳强度,但只是表面很薄的一层(铬钼铝钢于500--540C经35--65h渗氮层深只达0.3--0.65mm) 。必须有强而韧的心部组织作为渗氮层的坚实基底,才能发挥渗氮的最大作用。总的来看,大部分渗氮零件是在有摩擦和复杂的动载荷条件下工作的,不论表面和心部的性能都要求很高。
渗碳零件注意事项:
(1)渗碳前的预处理正火--目的是改善材料原始组织、减少带状、消除魏氏组织,使表面粗糙度变细,消除材料流线不合理状态。正火工艺;用860--980C空冷、179--217HBS
渗碳渗氮的作用及氮碳共渗和碳氮共渗的区别

渗碳:是对金属表面处理的一种,采用渗碳的多为低碳钢或低合金钢,具体方法是将工件置入具有活性渗碳介质中,加热到900--950摄氏度的单相奥氏体区,保温足够时间后,使渗碳介质中分解出的活性碳原子渗入钢件表层,从而获得表层高碳,心部仍保持原有成分. 相似的还有低温渗氮处理。
这是金属材料常见的一种热处理工艺,它可以使渗过碳的工件表面获得很高的硬度,提高其耐磨程度。
渗碳是指使碳原子渗入到钢表面层的过程。
也是使低碳钢的工件具有高碳钢的表面层,再经过淬火和低温回火,使工件的表面层具有高硬度和耐磨性,而工件的中心部分仍然保持着低碳钢的韧性和塑性。
渗碳工件的材料一般为低碳钢或低碳合金钢(含碳量小于0.25%)。
渗碳后﹐钢件表面的化学成分可接近高碳钢。
工件渗碳后还要经过淬火﹐以得到高的表面硬度﹑高的耐磨性和疲劳强度﹐并保持心部有低碳钢淬火后的强韧性﹐使工件能承受冲击载荷。
渗碳工艺广泛用于飞机﹑汽车和拖拉机等的机械零件﹐如齿轮﹑轴﹑凸轮轴等。
渗碳零件的材料一般选用低碳钢或低碳合金钢(含碳量小於0.25%)。
渗碳后必须进行淬火才能充分发挥渗碳的有利作用。
工件渗碳淬火后的表层显微组织主要为高硬度的马氏体加上残余奥氏体和少量碳化物﹐心部组织为韧性好的低碳马氏体或含有非马氏体的组织﹐但应避免出现铁素体。
一般渗碳层深度范围为0.8~1.2毫米﹐深度渗碳时可达2毫米或更深。
表面硬度可达HRC58~63﹐心部硬度为HRC30~42。
渗碳淬火后﹐工件表面产生压缩内应力﹐对提高工件的疲劳强度有利。
因此渗碳被广泛用以提高零件强度﹑冲击韧性和耐磨性﹐借以延长零件的使用寿命。
按含碳介质的不同﹐渗碳可分为固体渗碳﹑液体渗碳﹑气体渗碳和碳氮共渗;渗氮,是在一定温度下一定介质中使氮原子渗入工件表层的化学热处理工艺。
常见有液体渗氮、气体渗氮、离子渗氮。
传统的气体渗氮是把工件放入密封容器中,通以流动的氨气并加热,保温较长时间后,氨气热分解产生活性氮原子,不断吸附到工件表面,并扩散渗入工件表层内,从而改变表层的化学成分和组织,获得优良的表面性能。
软氮化和氮化处理有什么区别
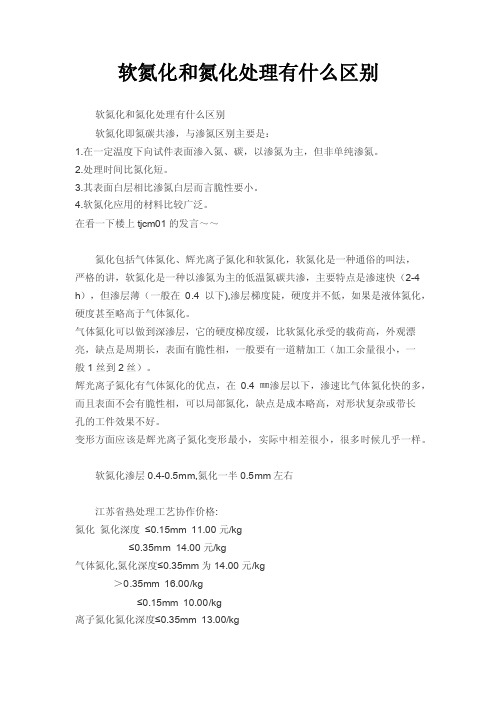
软氮化和氮化处理有什么区别软氮化和氮化处理有什么区别软氮化即氮碳共渗,与渗氮区别主要是:1.在一定温度下向试件表面渗入氮、碳,以渗氮为主,但非单纯渗氮。
2.处理时间比氮化短。
3.其表面白层相比渗氮白层而言脆性要小。
4.软氮化应用的材料比较广泛。
在看一下楼上tjcm01的发言~~氮化包括气体氮化、辉光离子氮化和软氮化,软氮化是一种通俗的叫法,严格的讲,软氮化是一种以渗氮为主的低温氮碳共渗,主要特点是渗速快(2-4 h),但渗层薄(一般在0.4以下),渗层梯度陡,硬度并不低,如果是液体氮化,硬度甚至略高于气体氮化。
气体氮化可以做到深渗层,它的硬度梯度缓,比软氮化承受的载荷高,外观漂亮,缺点是周期长,表面有脆性相,一般要有一道精加工(加工余量很小,一般1丝到2丝)。
辉光离子氮化有气体氮化的优点,在0.4㎜渗层以下,渗速比气体氮化快的多,而且表面不会有脆性相,可以局部氮化,缺点是成本略高,对形状复杂或带长孔的工件效果不好。
变形方面应该是辉光离子氮化变形最小,实际中相差很小,很多时候几乎一样。
软氮化渗层0.4-0.5mm,氮化一半0.5mm左右江苏省热处理工艺协作价格:氮化氮化深度≤0.15mm 11.00元/kg≤0.35mm 14.00元/kg气体氮化,氮化深度≤0.35mm为14.00元/kg>0.35mm 16.00/kg≤0.15mm 10.00/kg离子氮化氮化深度≤0.35mm 13.00/kg>0.35mm 15.00/kg气体氮碳共渗(软氮化) 8.30/kg软氮化即氮碳共渗,氮化是只渗氮.由于软氮化后另件表面的白亮层比氮化后白亮层脆性小,另件的韧性好故称之为"软氮化",软氮化处理后的另件表面硬度有时不比氮化低.对于不同材料软氮化处理后表面硬度在HV500-1200之间.最高硬度接近70HRC渗氮(软氮化)的常见缺陷一、硬度偏低生产实践中,工件渗氮(软氮化)后其表面硬度有时达不到工艺规定的要求,轻者可以返工,重者则造成报废。
- 1、下载文档前请自行甄别文档内容的完整性,平台不提供额外的编辑、内容补充、找答案等附加服务。
- 2、"仅部分预览"的文档,不可在线预览部分如存在完整性等问题,可反馈申请退款(可完整预览的文档不适用该条件!)。
- 3、如文档侵犯您的权益,请联系客服反馈,我们会尽快为您处理(人工客服工作时间:9:00-18:30)。
渗碳:渗碳后的工件经淬火和低温回火,使表面具有高硬度和耐磨性,而心部仍保持良好的塑性和韧性,从而满足工件外硬内韧的使用要求。
渗氮:零件渗氮后表面形成一层氮化物,不需要淬火就可以具有高的硬度、耐磨性、抗疲劳性和一定的腐蚀性,而且变形也很小。
三者比较而言以等离子效果最佳,气体渗氮次之,碳氮共渗最差。
碳氮共渗:又称氰化。碳氮共渗是将钢件表面同时渗入碳原子和氮原子,形成碳氮共渗层,以提高工件的硬度、耐磨性和疲劳强度的处理方法。
等离子氮化由于其温度低、渗氮周期短(温度为500-520℃,时间为12至15小时)组织由ε相、γ相组成,基本不含有脆性ξ相,从而使热应力和组织应力大为降低,变形量小,不易开裂,可作为最终工序。
气体渗氮温度一般为500~560看出温度虽然不高,但时间很长,其热应力就大。组织由ε相、γ相组成,处理不好时有脆性ξ相。
气体软氮化(碳氮共渗)温度常用560-570℃,因该温度下氮化层硬度值最高。氮化时间常为2-3小时,因为超过2.5小时,随时间延长,氮化层深度增加很慢。 可以看出碳氮共渗的温度最高,其组织由ε相、γ相和含氮的渗碳体Fe3(C,N)所组成,所以热应力和组织应力都较前两者大,再者渗层薄,所以不能承受重载。但这种处理也有优点,由于软氮化层不存在脆性ξ相,故氮化层硬而具有一定的韧性,不容易剥落。