几种高纯金属与合金粉末制备技术现状
高性能钨合金制备技术研究现状
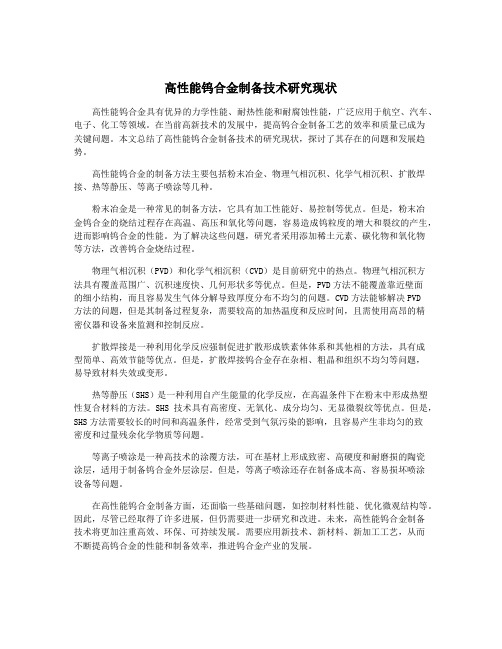
高性能钨合金制备技术研究现状高性能钨合金具有优异的力学性能、耐热性能和耐腐蚀性能,广泛应用于航空、汽车、电子、化工等领域。
在当前高新技术的发展中,提高钨合金制备工艺的效率和质量已成为关键问题。
本文总结了高性能钨合金制备技术的研究现状,探讨了其存在的问题和发展趋势。
高性能钨合金的制备方法主要包括粉末冶金、物理气相沉积、化学气相沉积、扩散焊接、热等静压、等离子喷涂等几种。
粉末冶金是一种常见的制备方法,它具有加工性能好、易控制等优点。
但是,粉末冶金钨合金的烧结过程存在高温、高压和氧化等问题,容易造成钨粒度的增大和裂纹的产生,进而影响钨合金的性能。
为了解决这些问题,研究者采用添加稀土元素、碳化物和氧化物等方法,改善钨合金烧结过程。
物理气相沉积(PVD)和化学气相沉积(CVD)是目前研究中的热点。
物理气相沉积方法具有覆盖范围广、沉积速度快、几何形状多等优点。
但是,PVD方法不能覆盖靠近壁面的细小结构,而且容易发生气体分解导致厚度分布不均匀的问题。
CVD方法能够解决PVD方法的问题,但是其制备过程复杂,需要较高的加热温度和反应时间,且需使用高昂的精密仪器和设备来监测和控制反应。
扩散焊接是一种利用化学反应强制促进扩散形成铁素体体系和其他相的方法,具有成型简单、高效节能等优点。
但是,扩散焊接钨合金存在杂相、粗晶和组织不均匀等问题,易导致材料失效或变形。
热等静压(SHS)是一种利用自产生能量的化学反应,在高温条件下在粉末中形成热塑性复合材料的方法。
SHS技术具有高密度、无氧化、成分均匀、无显微裂纹等优点。
但是,SHS方法需要较长的时间和高温条件,经常受到气氛污染的影响,且容易产生非均匀的致密度和过量残余化学物质等问题。
等离子喷涂是一种高技术的涂覆方法,可在基材上形成致密、高硬度和耐磨损的陶瓷涂层,适用于制备钨合金外层涂层。
但是,等离子喷涂还存在制备成本高、容易损坏喷涂设备等问题。
在高性能钨合金制备方面,还面临一些基础问题,如控制材料性能、优化微观结构等。
金属粉末制备工艺的研究及应用
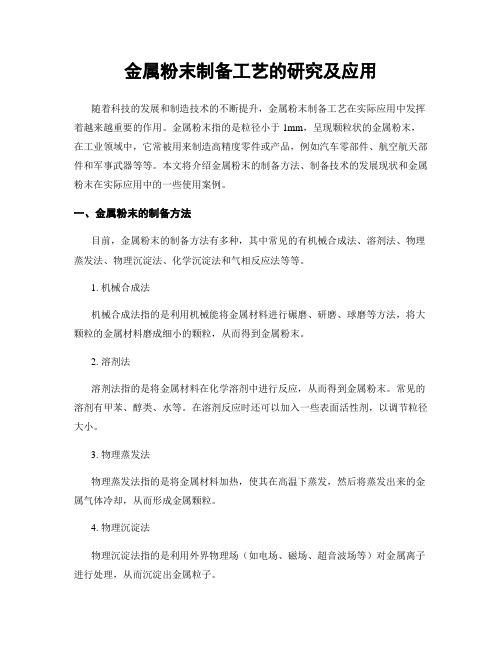
金属粉末制备工艺的研究及应用随着科技的发展和制造技术的不断提升,金属粉末制备工艺在实际应用中发挥着越来越重要的作用。
金属粉末指的是粒径小于1mm,呈现颗粒状的金属粉末,在工业领域中,它常被用来制造高精度零件或产品,例如汽车零部件、航空航天部件和军事武器等等。
本文将介绍金属粉末的制备方法、制备技术的发展现状和金属粉末在实际应用中的一些使用案例。
一、金属粉末的制备方法目前,金属粉末的制备方法有多种,其中常见的有机械合成法、溶剂法、物理蒸发法、物理沉淀法、化学沉淀法和气相反应法等等。
1. 机械合成法机械合成法指的是利用机械能将金属材料进行碾磨、研磨、球磨等方法,将大颗粒的金属材料磨成细小的颗粒,从而得到金属粉末。
2. 溶剂法溶剂法指的是将金属材料在化学溶剂中进行反应,从而得到金属粉末。
常见的溶剂有甲苯、醇类、水等。
在溶剂反应时还可以加入一些表面活性剂,以调节粒径大小。
3. 物理蒸发法物理蒸发法指的是将金属材料加热,使其在高温下蒸发,然后将蒸发出来的金属气体冷却,从而形成金属颗粒。
4. 物理沉淀法物理沉淀法指的是利用外界物理场(如电场、磁场、超音波场等)对金属离子进行处理,从而沉淀出金属粒子。
5. 化学沉淀法化学沉淀法指的是在化学反应中,将金属离子逐步还原或沉淀下来,从而得到金属粉末。
6. 气相反应法气相反应法指的是将金属离子和气体充分反应,从而得到金属粉末。
这种方法需要高温高压的条件下进行反应。
二、金属粉末制备技术的发展现状随着制造技术的发展,新的金属粉末制备技术不断涌现。
以下是一些新兴的金属粉末制备技术:1. 喷射沉积制备喷射沉积制备是一种新型加工技术,可以将高温喷射流对强制提供的金属粉进行熔化,从而在基板上形成金属涂层。
该技术制备的金属粉末颗粒粒径非常细小,可达到纳米级。
2. 等离子喷涂制备等离子喷涂制备是一种利用等离子体作为喷涂材料进行材料涂覆的技术。
它通过连续鼓泡、毁坏、重新组装等过程,形成金属粉末,从而在基板上形成金属涂层。
钛及钛合金粉末制备及研究现状

钛战钛合金的制备技能钻研及应用现状之阳早格格创做纲要:钛及钛合金概括力教本能劣良,正在航空航天、航海、化工等范围得到广大应用.用粉终冶金法治制整部件,资料利用率下,落矮死产成本.果此,下本能粉终冶金钛合金的钻研与应用连年去非常活跃,对付制备钛及钛合金粉终起到了很大的促进效率.金属注射成形( MIM) 技能是暂时最具劣势的粉终冶金成形技能之一,可制制下本量、下粗度的搀杂整件.闭键词汇:钛及钛合金;粉终冶金;金属注射成形;钻研与应用;1、序止:钛及钛合金具备稀度矮、比强度下、耐腐蚀性强、下温下抗蠕变本能佳、焊交本能劣良、死物相容性劣同等便宜,被广大应用于航空航天、航海、冶金、石油、化工、收电、汽车、医药、电子、体育及戚忙等范围.然而,由于钛的提与、熔炼、加工格中艰易,果此死产成本很下.钛锭的死产成本约为共本量钢锭的30倍,铝锭的6倍,而航空航天用的钛合金整部件果加工费下贵,死产费用便更大了.粉终冶金技能是一种由粉终直交成形,死产整部件的工艺要收.从技能上瞅,用该要收可赢得身分无偏偏析、本能宁静劣良、构制匀称的整部件;从经济上瞅,该要收是一种少切屑或者无切屑的工艺,资料利用率险些不妨达到100%,节省了加工费,普及了死产率2、钛及钛合金粉终注射成形技能金属注射成形要收是好国正在20世纪70年代收明的,是死产形状搀杂下粗度整部件的近洁形制制要收得到的烧结体稀度下,强度也下.其工艺过程为:混同配料→注射成形→脱除粘结剂( 简称脱脂)→烧结.由于成形坯的受压历程是匀称等压压制历程,所以成形坯的力教本能是各背共性的.我国钛及钛合金粉终注射成形钻研初于20 世纪90 年代终.主要钻研单位有北京科技大教、广州有色金属钻研院战中北大教等,并正在杂钛及Ti- 6Al-4V 合金注射成形圆里博得了一定科研成果,但是仍已产死财产化死产.钛及钛合金粉终注射成形产品主要有汽车整部件、调理器械、牙科植进体、下我妇球头战表壳等.暂时,杂钛、Ti- 6Al- 4V、Ti A1、Ti- Mo- A1、Ni Ti 战其余一些钛基资料粉终皆已乐成天采与了注射成形工艺去制制整部件.钛及钛合金注射成形技能的主要阻拦有:①矮氧球形钛粉终的代价下;②粘结剂的采用战去除工艺;③间隙元素的去除等.3、钛及钛合金粉终注射成形工艺产品本能战尺寸粗度是金属注射成形最后统制的指标.产品本能的佳坏以及尺寸粗度的下矮与本料、混炼、注射、脱脂、烧结等工艺历程有着稀切的闭系.3.1 粉终的制备3.1.1 杂钛粉暂时,注射成形用的杂钛粉的制制要收有:氢化脱氢法战睦体雾化.氢化脱氢粉的特性是粉终为形状没有准则的细粉,比表面积大,氧含量下.而气体雾化粉的形状为球形,与形状没有准则的氢化脱氢粉相比,其震动性战充挖性佳,表面积小,制备历程的传染小,氧含量矮,如果增加一定量的氢化脱氢粉可进一步革新成形性,是钛注射成形主要的本料粉终.3.1.2 钛合金粉注射成形用的钛合金粉终的制备要收主要有:元素粉终混同法战预合金化法.元素粉终混同法是将元素粉终按合金的成调配比混同,制得合金粉.为了普及该合金粉终的成形性,可正在氢化脱氢杂钛粉中混进一定比率的气体雾化粉.此要收治备合金粉终代价相对付矮廉.预合金化粉制备要收中气体雾化法是不妨举止批量死产的廉价要收.元素粉终混同法死产的合金粉终相对付预合金化粉终代价矮廉,简单成形,且工艺老练,果此,有着更为广大的商场前景.3.2 粘结剂的采用战混炼3.2.1 粘结剂的采用采用符合的粘结剂是注射成形的闭键关节,它直交效率着混同、注射成形、脱脂等工序, 对付注射成形坯的本量、脱脂及尺寸粗度等有很大的效率.钛及钛合金粉终注射成形用的粘结剂,可正在火中或者有机溶剂中溶解,有的粘结剂还增加了催化剂,加快了粘结剂的收会.粘结剂用量对付成形本量效率很大.粘结剂缺累时引导成形艰易;粘结剂过多时会落矮喂料的粘度.粘结剂普遍占喂料总量的40%~50%( 本量分数),最后通过热解去除.3.2.2 混炼混料也是比较闭键的工序.混料历程中爆收缺陷正在以去的工序中很易与消,果此对付混料提出了央供: ①匀称、震动性佳, 以保证匀称的中断战变形.②央供正在包管灵验成形的条件,具备最大的粉终拆载量,以包管烧结历程中的中断量最小,预防由此引起的工序缺陷出现.粉终充挖量对付注射成形工艺战热脱脂历程有一定的效率.粉终充挖量过多过少均不利,果此,从脱粘及脆持形状圆里思量,充挖量应尽管大一些.混料历程中,混同速度降下,混料的匀称性普及.但是速度太快, 会使混同料的温度降下,那对付矮熔面组元的粘结剂是有害的.其余,粉终与粘结剂的亲战本能.粘结剂战喂料正在百般条件下的流变本能及热力教本能粘结剂对付脱脂及产品本能的效率,以及启垦新式下效、符合钛及钛合金用的粘结剂,是以后钛及钛合金粉终注射成形件的要害钻研真量.3.3 注射成形注射成形工序是将混同佳的物料注射成形为所需形状的无缺陷坯料.由于注射成形历程所产死的缺陷正在后绝工艺中无法与消,果此,该步调要庄重统制.采与估计机模拟喂料及充挖模具历程,劣化注射成形条件参数,是暂时与消注射成形缺陷较为进步的脚法,也是已去的死少趋势.注射成形闭键关节之一是有闭成形的各项安排,其中包罗产品安排战模具安排.纵然暂时死产的产品正在矫正粗度圆里已博得了少脚进步,然而,大普遍安排特天是模具安排仍旧凭体味举止,缺累表里依据,且CAD系统易以很佳天应用于金属注射成形.北京科技大教郭世柏等人通过真验钻研得出, 效率注射成形死坯本量的主要果素有:①模具安排合理与可;②注射成形历程工艺参数( 注射压力、注射温度、注射速度战模具温度).要赢得理念的注射成形死坯,必须对付模具安排战注射成形参数举止劣化.3.4 脱脂战烧结粘结剂脱除即脱脂最费时、最易统制,是金属注射成形工艺中最要害的关节,也是阻拦金属注射成形工艺技能死少的易题.脱脂工艺对付于包管产品本量极为要害.钛及钛合金时常使用的脱脂要收有热脱脂、溶剂脱脂、催化脱脂及超临界流体萃与等.烧结是金属注射成形工艺中终尾一讲工序,起着使产品致稀化战化教本量匀称的效率.烧结条件(如温度、气氛、降温速度等)效率产品的本能战粗度.由于金属粉终注射成形采与了洪量的粘结剂,烧结时中断非常大,线中断率普遍达到12%~18%.果此,变形统制战尺寸粗度统制至闭要害.其余,加热历程中的气体反应以及残留的散合物与粉终杂量反应等,特天是后者正在孔隙中效率注射成形产品的致稀化..烧结钛及钛合金要用通过庄重脱火战洁化的氢气,最佳是正在真空或者惰性气氛中举止.正在钛及钛合金的烧结历程中,牢固器战挖料也很闭键,若使用AlO3,正在比较下的温度烧结会减少氧含量,推荐使用.4、钻研现状与应用暂时,钛合金已经广大应用于航空航天、船舰、汽车、化工及石化等范围,有着格中广阔的应用前景.譬如,2003-2007年,我国海绵钛产量从几千吨减少到6000t以上,2013年我国钛加工材产量虽然比2012年下落了约13%,但是仍达4453t.便后劲而止,钛合金将越收广大天应用于民用功业,特天是汽车、调理器械、死物移动物等受到了充分沉视.暂时,车用钛合金主要用于收效果气门、连杆、直轴及弹簧等.然而,对付于民用范围,钛合金代价圆里必须主要思量.死产矮成本、下本能钛及钛合金粉终注射成形件的主要道路战钻研目标是: ①使用代价矮廉的氢化脱氢粉战睦体雾化粉混同得到的钛及钛合金粉动做注射成形的本料粉终;②启垦新式下效的钛及钛合金粉终注射成形用的粘结剂体系;③劣化混炼工艺;④劣化注射条件参数以与消注射缺陷;⑤启垦进步的脱脂工艺,支缩脱脂时间并缩小脱脂缺陷,以落矮成本;⑥钻研烧结工艺,统制产品尺寸粗度,普及产品本能.通过劣化金属注射成形工艺加大产品的尺寸,钻研超小型整件的注射成形是夸大钛及钛合金粉终注射成形产品应用的要害道路.5、中断语随着粉终冶金钛合金技能正在死物医用战航空航天等下新技能范围中得到越去越广大的应用,已去钻研的沉面集结正在球形钛及钛合金粉终制备工艺上.而且随着3D挨印战粉终注射成形技能没有竭得到应用,球形粉终需要的删少会非常快.已去钛及钛合金粉终制备技能的钻研沉面还正在怎么样落矮粉终杂量含量,落矮死产成本等.参照文件:[1]杨伟,弛崇才,涂铭旌. 钛及钛合金粉终注射成型钻研近况及应用前景[J]. 资料导报,2015,09(123-128).[2]邹黎明,开焕文,刘辛等. 钛及钛合金粉终制备技能的钻研及应用现状[J]. 资料钻研与应用,2015,04:222-230.[3]梁永仁,吴引江.3D挨印用钛及钛合金球形粉终制备技能[J].天下有色金属,2016,12:150-151.。
高性能钨合金制备技术研究现状

高性能钨合金制备技术研究现状
高性能钨合金是一种具有优异综合力学性能的材料,广泛应用于航空航天、军事装备、电子通信、核能工程等领域。
本文将介绍高性能钨合金制备技术的研究现状。
目前,高性能钨合金制备技术主要包括粉末冶金法、熔炼法和化学气相沉积法等。
粉末冶金法是制备高性能钨合金的主要方法之一。
该方法通过粉末的混合、压制、烘
烤和烧结等步骤,实现钨合金的制备。
粉末冶金法具有制备成本低、制备工艺简单、生产
效率高等优点,适用于大规模生产。
该方法存在一些问题,如晶粒长大、相分离、气孔等
缺陷,影响了材料的性能。
化学气相沉积法是近年来发展起来的一种新型制备高性能钨合金的方法。
该方法通过
化学反应将钨的前体物质气体转化为固体钨合金薄膜,实现材料的制备。
化学气相沉积法
具有制备过程简单、合金成分均匀等优点,能够获得高纯度、低气孔率的钨合金。
化学气
相沉积法还存在一些问题,如成膜速率低、设备成本高等缺点,限制了其在工业生产中的
应用。
除了上述三种主要方法外,还有一些其他制备高性能钨合金的方法也在研究中。
机械
合金化法、电沉积法、激光熔化法等。
这些方法在制备工艺和材料性能方面都有一定的优
势和局限性。
高性能钨合金制备技术研究目前主要集中在粉末冶金法、熔炼法和化学气相沉积法等
方法上。
随着科学技术的不断进步,制备工艺和设备也将不断改进,使高性能钨合金在各
个领域有更广泛的应用前景。
粉末冶金现状及发展
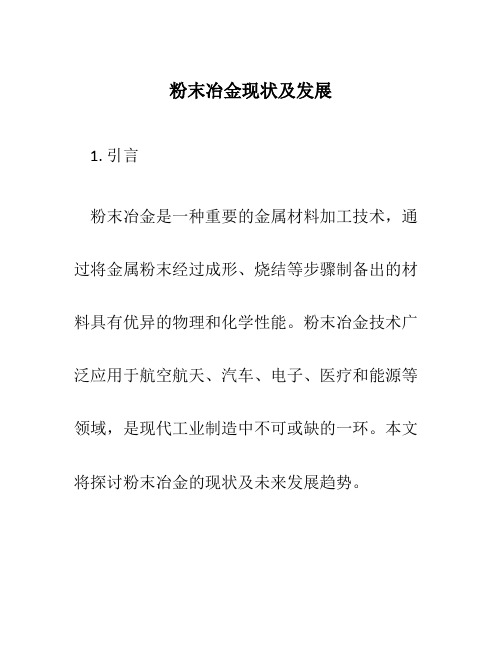
粉末冶金现状及发展1. 引言粉末冶金是一种重要的金属材料加工技术,通过将金属粉末经过成形、烧结等步骤制备出的材料具有优异的物理和化学性能。
粉末冶金技术广泛应用于航空航天、汽车、电子、医疗和能源等领域,是现代工业制造中不可或缺的一环。
本文将探讨粉末冶金的现状及未来发展趋势。
2. 粉末冶金的基本原理粉末冶金主要的工艺流程包括粉末制备、粉末成型和烧结。
首先,金属原料通过物理或化学方法制备成粉末。
然后,利用成型技术将粉末填充到模具中,并施加压力使粉末颗粒形成所需的形状。
最后,通过高温烧结使粉末颗粒结合成整体材料。
3. 粉末冶金的应用领域粉末冶金技术在众多领域中得到了广泛应用。
以下是一些典型的应用领域:3.1 汽车工业粉末冶金技术在汽车工业中发挥着重要作用。
通过粉末冶金可以制备出具有优异力学性能和耐磨性的零部件,如齿轮、减震器和轴承等。
此外,粉末冶金还可以实现轻量化设计,提高汽车的燃油效率和续航里程。
3.2 航空航天工业在航空航天工业中,粉末冶金技术被广泛应用于制备高强度、耐高温材料。
这些材料可以用于制造发动机部件、导弹和卫星等。
粉末冶金技术还可以制备金属陶瓷复合材料,提高材料的性能和耐腐蚀性。
3.3 电子工业粉末冶金技术在电子工业中的应用也越来越广泛。
通过粉末冶金可以制备出具有高导电性和磁性的材料,如电极材料和磁性核材料等。
此外,粉末冶金技术还可以制备微细粉末,用于制造电子元器件中的封装材料。
3.4 医疗工业粉末冶金技术在医疗工业中的应用主要体现在制备人工关节和牙科种植体等医疗器械方面。
利用粉末冶金可以制备出具有生物相容性、强度和耐腐蚀性的金属材料,提高医疗器械的性能和使用寿命。
3.5 能源工业粉末冶金技术在能源工业中的应用主要体现在制备高效率燃料电池和储能材料等方面。
通过粉末冶金可以制备出具有高比表面积和良好导电性能的材料,提高能源转换效率和储能密度。
4. 粉末冶金的发展趋势随着科学技术的发展和工业需求的变化,粉末冶金技术也在不断发展。
高性能钨合金制备技术研究现状
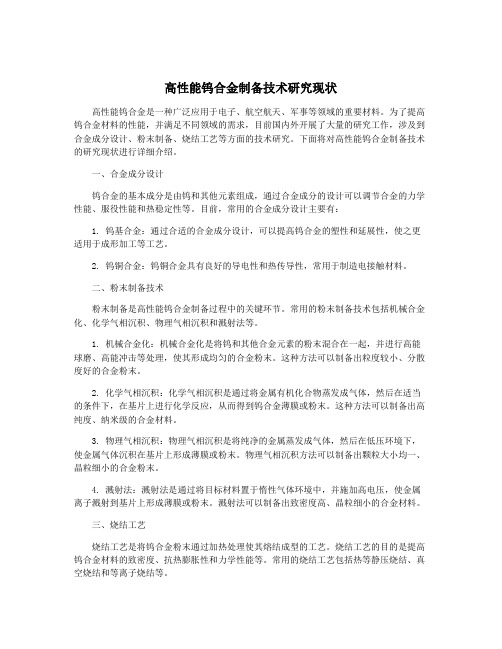
高性能钨合金制备技术研究现状高性能钨合金是一种广泛应用于电子、航空航天、军事等领域的重要材料。
为了提高钨合金材料的性能,并满足不同领域的需求,目前国内外开展了大量的研究工作,涉及到合金成分设计、粉末制备、烧结工艺等方面的技术研究。
下面将对高性能钨合金制备技术的研究现状进行详细介绍。
一、合金成分设计钨合金的基本成分是由钨和其他元素组成,通过合金成分的设计可以调节合金的力学性能、服役性能和热稳定性等。
目前,常用的合金成分设计主要有:1. 钨基合金:通过合适的合金成分设计,可以提高钨合金的塑性和延展性,使之更适用于成形加工等工艺。
2. 钨铜合金:钨铜合金具有良好的导电性和热传导性,常用于制造电接触材料。
二、粉末制备技术粉末制备是高性能钨合金制备过程中的关键环节。
常用的粉末制备技术包括机械合金化、化学气相沉积、物理气相沉积和溅射法等。
1. 机械合金化:机械合金化是将钨和其他合金元素的粉末混合在一起,并进行高能球磨、高能冲击等处理,使其形成均匀的合金粉末。
这种方法可以制备出粒度较小、分散度好的合金粉末。
2. 化学气相沉积:化学气相沉积是通过将金属有机化合物蒸发成气体,然后在适当的条件下,在基片上进行化学反应,从而得到钨合金薄膜或粉末。
这种方法可以制备出高纯度、纳米级的合金材料。
3. 物理气相沉积:物理气相沉积是将纯净的金属蒸发成气体,然后在低压环境下,使金属气体沉积在基片上形成薄膜或粉末。
物理气相沉积方法可以制备出颗粒大小均一、晶粒细小的合金粉末。
4. 溅射法:溅射法是通过将目标材料置于惰性气体环境中,并施加高电压,使金属离子溅射到基片上形成薄膜或粉末。
溅射法可以制备出致密度高、晶粒细小的合金材料。
三、烧结工艺烧结工艺是将钨合金粉末通过加热处理使其熔结成型的工艺。
烧结工艺的目的是提高钨合金材料的致密度、抗热膨胀性和力学性能等。
常用的烧结工艺包括热等静压烧结、真空烧结和等离子烧结等。
1. 热等静压烧结:热等静压烧结是将钨合金粉末放入模具中,施加高压和高温,使其在压力和温度共同作用下烧结成型。
国内金属材料技术现状
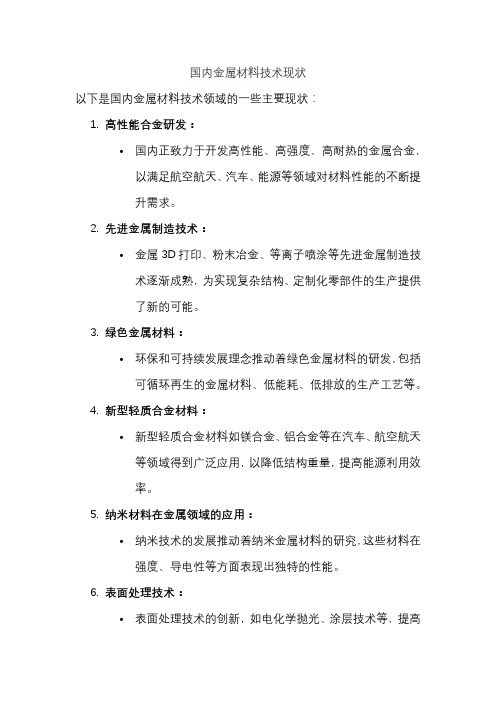
国内金属材料技术现状
以下是国内金属材料技术领域的一些主要现状:
1.高性能合金研发:
•国内正致力于开发高性能、高强度、高耐热的金属合金,以满足航空航天、汽车、能源等领域对材料性能的不断提
升需求。
2.先进金属制造技术:
•金属3D打印、粉末冶金、等离子喷涂等先进金属制造技术逐渐成熟,为实现复杂结构、定制化零部件的生产提供
了新的可能。
3.绿色金属材料:
•环保和可持续发展理念推动着绿色金属材料的研发,包括可循环再生的金属材料、低能耗、低排放的生产工艺等。
4.新型轻质合金材料:
•新型轻质合金材料如镁合金、铝合金等在汽车、航空航天等领域得到广泛应用,以降低结构重量,提高能源利用效
率。
5.纳米材料在金属领域的应用:
•纳米技术的发展推动着纳米金属材料的研究,这些材料在强度、导电性等方面表现出独特的性能。
6.表面处理技术:
•表面处理技术的创新,如电化学抛光、涂层技术等,提高
了金属材料的抗腐蚀性、耐磨性等性能。
7.材料模拟和计算:
•材料计算和模拟技术的发展,使得科学家能够更好地理解材料的性能,加速新材料的设计和开发过程。
8.电解铝生产技术:
•电解铝生产技术在我国的不断创新,提高了铝的生产效率,满足了建筑、交通、电力等行业的用材需求。
请注意,这些只是国内金属材料技术领域的一些方面,具体的技术现状可能随时间和科技进步而不断变化。
随着科技的发展,金属材料领域将继续面临新的挑战和机遇。
为获取最新的信息,建议查阅相关领域的学术文献、行业报告以及技术新闻。
增材制造用铝合金粉末的现状和发展趋势

增材制造用铝合金粉末的现状和发展趋势下载提示:该文档是本店铺精心编制而成的,希望大家下载后,能够帮助大家解决实际问题。
文档下载后可定制修改,请根据实际需要进行调整和使用,谢谢!本店铺为大家提供各种类型的实用资料,如教育随笔、日记赏析、句子摘抄、古诗大全、经典美文、话题作文、工作总结、词语解析、文案摘录、其他资料等等,想了解不同资料格式和写法,敬请关注!Download tips: This document is carefully compiled by this editor. I hope that after you download it, it can help you solve practical problems. The document can be customized and modified after downloading, please adjust and use it according to actual needs, thank you! In addition, this shop provides you with various types of practical materials, such as educational essays, diary appreciation, sentence excerpts, ancient poems, classic articles, topic composition, work summary, word parsing, copy excerpts, other materials and so on, want to know different data formats and writing methods, please pay attention!增材制造用铝合金粉末的现状和发展趋势引言随着增材制造技术的迅速发展,铝合金粉末作为一种重要的原材料,受到了广泛关注。
钛铝合金制备技术现状及新进展

钛铝合金制备技术现状及新进展钛铝合金作为一种具有高强度、轻质和优良耐腐蚀性能的合金材料,在航空航天、汽车、机械制造等领域得到了广泛应用。
为了满足不同领域的应用需求,钛铝合金制备技术的发展一直受到人们的。
本文将概述钛铝合金制备技术的现状及新进展。
目前,钛铝合金的制备主要采用熔炼和铸造等方法。
熔炼法是将钛和铝按照一定比例混合,在高温下熔化,然后进行浇铸、冷却和加工处理。
铸造法则是通过铸造设备将熔融的钛铝合金倒入模具中,冷却后得到所需形状和尺寸的铸件。
这些方法在生产实践中得到了广泛应用,但也存在一些不足之处,如成分控制不够精确、生产周期长、成本高等。
近年来,钛铝合金制备技术取得了许多新的进展。
随着材料性能的提升,钛铝合金的强度、硬度、耐腐蚀性能等得到了显著改善。
制备工艺方面也得到了很大的改进。
例如,真空熔炼技术可以有效地降低杂质含量,提高合金纯度;喷射沉积技术则可以实现快速凝固,提高生产效率。
一些新的生产设备和方法,如3D打印技术、离子注入技术等也在钛铝合金制备中得到了应用,进一步提高了生产效率和降低了成本。
随着钛铝合金制备技术的不断发展,其应用前景也越来越广阔。
在航空航天领域,钛铝合金可用于制造飞机和火箭等高速飞行器的结构件和发动机部件;在汽车领域,钛铝合金可用于制造轻量化、高强度的汽车零部件,提高汽车燃油效率和安全性;在机械制造领域,钛铝合金可用于制造高精度、高稳定性的机械设备和工具。
钛铝合金制备技术的发展对于提高合金材料性能、降低生产成本、推动相关领域的技术进步具有重要意义。
未来随着科学技术不断创新,钛铝合金制备技术有望在材料性能、制备工艺和生产效率等方面取得更多突破,为各领域的发展提供更强大的支撑。
粉末冶金是一种制备材料和零件的先进技术,具有近净成形、高密度、高性能等优点。
钛铝合金作为一种具有优异性能的新型材料,具有广阔的应用前景。
本文将综述粉末冶金制备钛铝合金技术的现状和展望。
在粉末冶金制备钛铝合金技术方面,相关文献和资料表明,目前主要有以下几种制备方法:机械合金化法:通过强力的机械搅拌将钛和铝粉末混合,然后进行热压烧结或热等静压处理得到钛铝合金。
粉末高温合金的制备工艺及发展现状
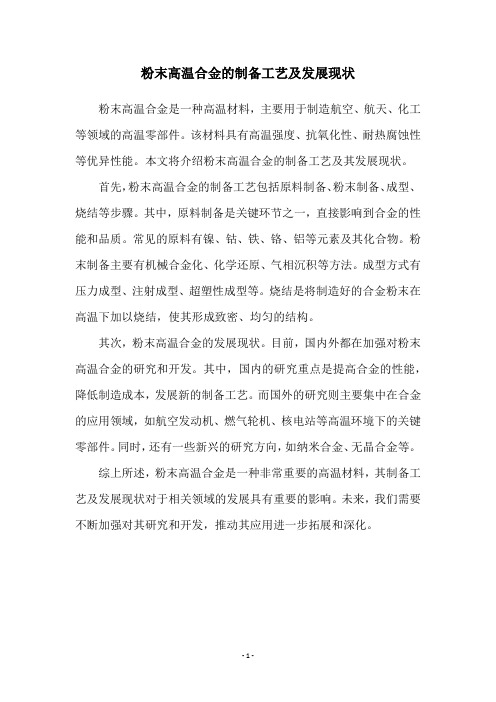
粉末高温合金的制备工艺及发展现状
粉末高温合金是一种高温材料,主要用于制造航空、航天、化工等领域的高温零部件。
该材料具有高温强度、抗氧化性、耐热腐蚀性等优异性能。
本文将介绍粉末高温合金的制备工艺及其发展现状。
首先,粉末高温合金的制备工艺包括原料制备、粉末制备、成型、烧结等步骤。
其中,原料制备是关键环节之一,直接影响到合金的性能和品质。
常见的原料有镍、钴、铁、铬、铝等元素及其化合物。
粉末制备主要有机械合金化、化学还原、气相沉积等方法。
成型方式有压力成型、注射成型、超塑性成型等。
烧结是将制造好的合金粉末在高温下加以烧结,使其形成致密、均匀的结构。
其次,粉末高温合金的发展现状。
目前,国内外都在加强对粉末高温合金的研究和开发。
其中,国内的研究重点是提高合金的性能,降低制造成本,发展新的制备工艺。
而国外的研究则主要集中在合金的应用领域,如航空发动机、燃气轮机、核电站等高温环境下的关键零部件。
同时,还有一些新兴的研究方向,如纳米合金、无晶合金等。
综上所述,粉末高温合金是一种非常重要的高温材料,其制备工艺及发展现状对于相关领域的发展具有重要的影响。
未来,我们需要不断加强对其研究和开发,推动其应用进一步拓展和深化。
- 1 -。
高性能钨合金制备技术研究现状

高性能钨合金制备技术研究现状目前高性能钨合金制备技术主要包括烧结、热加压、等离子热喷涂、选择性激光熔化等多种方法。
其中烧结法是目前应用最广泛的一种方法,其工艺流程一般包括粉末制备、压制成型、烧结等步骤,具体操作流程如下:1. 粉末制备:粉末制备是高性能钨合金制备的第一步,粉末制备的质量对后续操作过程具有重要的影响。
常用的粉末制备方法有机械合金化、水热法和化学还原法等。
2. 压制成型:将制备好的粉末经过加压成型,目的是为了使其具有一定的强度和较好的成型性能。
压制成型的方法主要有等静压、冷、热等压制法。
3. 烧结:将成型好的粉末进行烧结处理,使其在高温和高压下熔结成型,得到高性能钨合金。
烧结方法主要分为等静压烧结和热等静压烧结两种。
热加压法是在烧结法基础上发展起来的新技术,其与烧结法的主要区别在于在烧结过程中增加了压力,从而使合金更加致密。
该方法制备出的高性能钨合金,其密度和抗拉强度均比烧结法高10%以上,同时具有更好的抗氧化性能。
等离子热喷涂法是一种利用等离子喷涂设备将高性能钨合金喷涂到工件表面的方法。
通过等离子热喷涂法制备的钨合金具有耐热、耐腐蚀、耐磨损等优异性能,且能够制备成各种复杂形状的零件,具有较广泛的应用前景。
选择性激光熔化法是一种新型的制备高性能钨合金的方法,其重点在于利用激光束在微观区域内瞬间熔化金属粉末,从而实现材料的快速成型。
该方法制备高性能钨合金具有优异的成型、微观结构和力学性能,将成为未来制备高性能钨合金的一种重要方法。
总之,高性能钨合金制备技术是当前国内外钨合金领域的研究热点之一,其发展趋势主要是在提高制备效率、掌握更加细化精确的制备过程、提高材料性能、实现工业化规模生产等方面进一步发展和完善,以满足高端工程和技术的应用需求。
高性能钨合金制备技术研究现状

高性能钨合金制备技术研究现状引言钨合金是一种非常重要的工程材料,具有高硬度、高熔点、优良的机械性能和耐磨性,因而在航空航天、汽车制造、电子设备等领域得到广泛应用。
由于钨的高熔点和难加工性,使得钨合金的加工和制备技术一直是研究的热点方向。
本文旨在对目前高性能钨合金制备技术的研究现状做一简要介绍。
一、传统的钨合金制备技术以钨镍铁合金为例,传统的熔炼方法是将钨粉末和其他合金元素的粉末混合均匀后,加入熔剂在高温下进行熔炼。
这种方法的优点是可以获得较高的成分均匀度,但缺点是需要较高的熔点和成本较高。
钨合金熔炼时易氧化,需要采取保护措施,生产成本较高。
二、粉末冶金法制备高性能钨合金粉末冶金法是一种常用的制备钨合金的方法,通过混合、压制和烧结等工艺将钨粉末和其他金属粉末制备成钨合金制品。
粉末冶金法的优点是能够制备较复杂的构件和近净成形件,但其缺点是需要采用高压和高温进行烧结,制备成本较高。
近年来,随着纳米材料技术的发展,纳米颗粒技术已经被广泛应用于钨合金的制备中。
研究表明,采用纳米钨粉末和其他金属纳米颗粒进行混合,并通过机械合金化和烧结等工艺,可以获得具有优异性能的钨合金制品。
纳米颗粒技术制备的钨合金具有细小的晶粒和均匀的成分分布,具有更好的抗疲劳和耐磨性能。
三、表面涂层技术提高钨合金的性能钨合金的高硬度和耐磨性使得它广泛应用于刀具和磨具制造领域。
由于其本身的高熔点和难加工性,使得钨合金的刀具和磨具的制备较为困难。
为了提高钨合金刀具和磨具的性能,表面涂层技术被广泛应用于钨合金制备中。
目前,常用的表面涂层技术包括化学气相沉积(CVD)、物理气相沉积(PVD)、热喷涂等。
这些技术可以在钨合金的表面形成坚硬的涂层,提高其耐磨性和切削性能。
通过表面涂层技术,钨合金的表面粗糙度可以得到控制,从而改善其表面质量。
四、先进的制备技术推动钨合金的应用随着制备技术的不断进步,钨合金的应用领域也在不断拓展。
在电子设备领域,钨合金的导热性能使得它成为电子封装材料的理想选择,而采用纳米材料技术可以制备出具有高导热性能的钨合金导热器件;在核能领域,钨合金因为具有较高的熔点和辐射抗性,因而被广泛应用于核聚变反应堆等设备的制造中;在航空航天领域,钨合金的高熔点和耐高温性使得它成为航天器件的重要材料。
国外粉末冶金技术发展现状
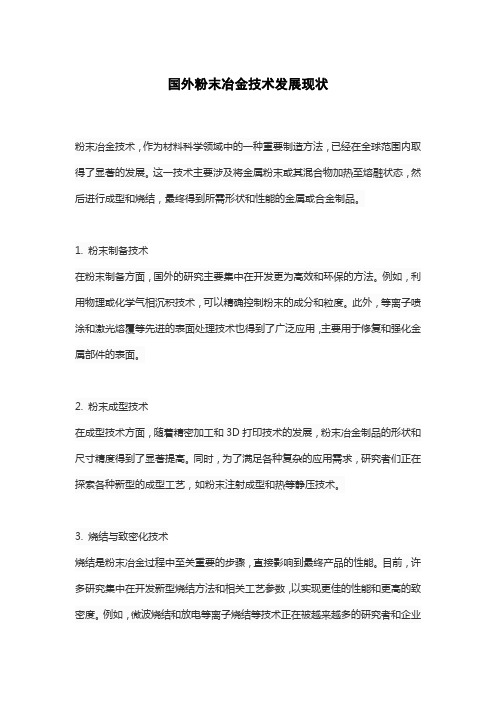
国外粉末冶金技术发展现状粉末冶金技术,作为材料科学领域中的一种重要制造方法,已经在全球范围内取得了显著的发展。
这一技术主要涉及将金属粉末或其混合物加热至熔融状态,然后进行成型和烧结,最终得到所需形状和性能的金属或合金制品。
1. 粉末制备技术在粉末制备方面,国外的研究主要集中在开发更为高效和环保的方法。
例如,利用物理或化学气相沉积技术,可以精确控制粉末的成分和粒度。
此外,等离子喷涂和激光熔覆等先进的表面处理技术也得到了广泛应用,主要用于修复和强化金属部件的表面。
2. 粉末成型技术在成型技术方面,随着精密加工和3D打印技术的发展,粉末冶金制品的形状和尺寸精度得到了显著提高。
同时,为了满足各种复杂的应用需求,研究者们正在探索各种新型的成型工艺,如粉末注射成型和热等静压技术。
3. 烧结与致密化技术烧结是粉末冶金过程中至关重要的步骤,直接影响到最终产品的性能。
目前,许多研究集中在开发新型烧结方法和相关工艺参数,以实现更佳的性能和更高的致密度。
例如,微波烧结和放电等离子烧结等技术正在被越来越多的研究者和企业所关注。
4. 粉末冶金制品的应用随着粉末冶金技术的不断进步,其应用领域也在不断扩展。
除了传统的汽车和航空航天领域,粉末冶金制品在电子产品、医疗器械和新能源等领域也得到了广泛应用。
例如,利用粉末冶金技术制备的电池电极材料具有更高的能量密度和更长的使用寿命。
5. 面临的挑战与未来展望尽管粉末冶金技术已经取得了显著的进步,但仍面临一些挑战。
例如,如何进一步提高粉末的纯度和粒度分布的均匀性、如何降低生产过程中的能耗和污染、如何实现大规模生产过程中的成本控制等。
针对这些问题,未来的研究将更加注重跨学科的合作和创新,以实现粉末冶金技术的持续发展。
例如,将新材料科学、人工智能和数字技术等引入到粉末冶金工艺中,有望进一步提升生产效率和产品性能。
国外粉末冶金技术在制备、成型、烧结和应用等方面都取得了显著的进展。
然而,为了满足不断变化的市场需求和技术发展,仍需不断进行研究和创新。
2023年金属粉末注射成型技术行业市场发展现状

2023年金属粉末注射成型技术行业市场发展现状金属粉末注射成型技术(Metal Powder Injection Moulding,缩写为MIM)是一种高精密度、高性能、复杂形状、大批量生产的金属加工技术。
它的出现大大拓展了金属制品的应用领域,现在已经广泛应用于汽车、电子、医疗、军工等领域。
本文将结合市场需求、生产规模、技术难度与进展等方面,分析金属粉末注射成型技术的发展现状。
一、市场需求随着科技的不断进步,人类对高精密度、高性能、复杂形状、大批量生产的金属加工技术的需求不断增加。
金属粉末注射成型技术正好满足了这些需求,因此市场需求十分旺盛。
特别是在汽车、电子、医疗、军工等领域,金属粉末注射成型技术的应用必不可少。
二、生产规模金属粉末注射成型技术是一种集成了粉末冶金成型和塑料注射成型的先进技术。
这种技术不仅可以生产精密度高、性能好的金属制品,而且可以大批量生产。
所以,金属粉末注射成型技术已经成为生产高精密度、高性能零部件的常用制造工艺之一。
目前,全球金属粉末注射成型技术的生产规模不断扩大。
其中,欧洲、美洲和亚洲是最主要的生产地区。
在中国,金属粉末注射成型技术的应用也越来越广泛,已经成为了国内制造业的重要组成部分。
三、技术难度及进展金属粉末注射成型技术涉及到粉末制备、成型、烧结等一系列复杂的加工过程,技术难度较大。
尤其是对材料的要求极为严格,材料的质量、粒度和分布直接决定了制品的质量。
因此,金属粉末注射成型技术在成形过程中会出现浸润不良、气孔、缩孔、偏差等问题,这些问题都需要通过优化工艺和提高设备精度来解决。
目前,全球相关技术公司对金属粉末注射成型技术的研究不断深入,不断推出新技术。
比如,近年来出现了高温烧结和真空热处理等新工艺;全球金属粉末注射成型技术的设备也逐渐向高效、智能化、自动化方向发展,为提高成品质量和生产效率提供了很好的保障。
综上所述,随着科技的进步和市场需求的不断增加,金属粉末注射成型技术在全球的发展前景非常广阔。
高纯度金属制备技术及其应用研究

高纯度金属制备技术及其应用研究高纯度金属是指金属元素的纯度达到99.999%及以上的金属材料。
它因具有优异的物理化学性质和特殊的应用价值,在现代科学技术、信息产业、装备制造、新能源、航空航天等领域得到广泛应用。
本文将介绍高纯度金属的制备技术以及其在新能源、信息产业、航空航天等领域的应用研究。
一、高纯度金属制备技术高纯度金属制备一般采用物理化学方法,包括化学还原法、电解制备法、蒸发冷凝法、分子束外延法等多种技术。
其中,电解法是目前应用最广泛的制备高纯度金属的技术之一,其基本原理是利用电解质溶液中电极反应的化学效应,控制金属离子的还原过程,从而得到符合要求的高纯度金属。
电解法的优点是制备出的金属纯度高、质量稳定,适用于制备多种金属。
同时,在电解法的基础上,还产生了一些衍生方法,如电渣重熔法、熔盐电解法等,这些技术可以更进一步提高金属的纯度和质量,适用于一些特殊金属的制备。
此外,化学还原法也是制备高纯度金属的主要方法之一,它通过化学反应将金属离子还原成金属原子或离子,再结晶、沉淀、真空升华等步骤加以纯化。
二、高纯度金属的应用研究1. 在新能源领域中的应用太阳能光电池是人们对新能源应用的重点发掘之一,而其制造过程离不开高纯度的硅。
通过高纯度硅的制备技术,制造出的太阳能光电池的转换效率大大提高,达到甚至超过30%的高效率,极大地推动了太阳能光电产业的发展。
2. 在信息产业中的应用半导体器件是现代电子信息产业中不可或缺的基础,而其中的微电子强磁场元件,如超导纽扣电池、磁共振测量元件等,依赖于高纯度金属制备技术。
制造出的高纯度铝、钨、铜等金属结晶体,能够大大提高半导体器件的性能稳定性和工作寿命,从而提高器件的制造质量和可靠性。
3. 在航空航天领域中的应用航空航天领域中,对金属的性能要求非常苛刻,高纯度金属制备技术能够制造出高强度、高温性能稳定的材料。
比如,在制造航空发动机的过程中,钛合金就是其中一种使用广泛的金属,而纯度高、成分稳定的钛合金,能够大大提高航空发动机的工作性能和寿命。
高性能钨合金制备技术研究现状
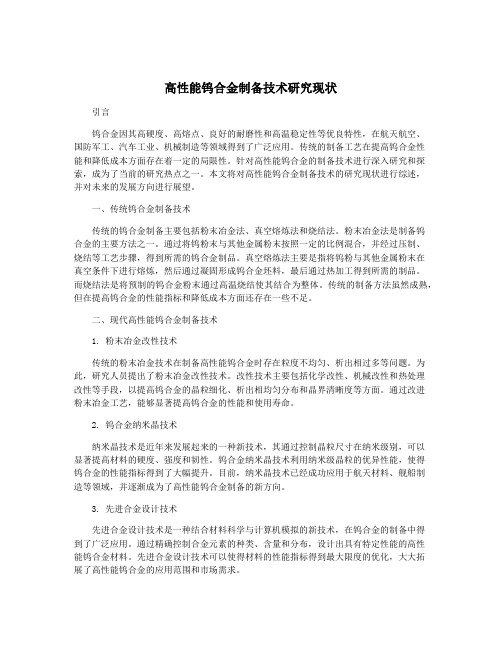
高性能钨合金制备技术研究现状引言钨合金因其高硬度、高熔点、良好的耐磨性和高温稳定性等优良特性,在航天航空、国防军工、汽车工业、机械制造等领域得到了广泛应用。
传统的制备工艺在提高钨合金性能和降低成本方面存在着一定的局限性。
针对高性能钨合金的制备技术进行深入研究和探索,成为了当前的研究热点之一。
本文将对高性能钨合金制备技术的研究现状进行综述,并对未来的发展方向进行展望。
一、传统钨合金制备技术传统的钨合金制备主要包括粉末冶金法、真空熔炼法和烧结法。
粉末冶金法是制备钨合金的主要方法之一。
通过将钨粉末与其他金属粉末按照一定的比例混合,并经过压制、烧结等工艺步骤,得到所需的钨合金制品。
真空熔炼法主要是指将钨粉与其他金属粉末在真空条件下进行熔炼,然后通过凝固形成钨合金坯料,最后通过热加工得到所需的制品。
而烧结法是将预制的钨合金粉末通过高温烧结使其结合为整体。
传统的制备方法虽然成熟,但在提高钨合金的性能指标和降低成本方面还存在一些不足。
二、现代高性能钨合金制备技术1. 粉末冶金改性技术传统的粉末冶金技术在制备高性能钨合金时存在粒度不均匀、析出相过多等问题。
为此,研究人员提出了粉末冶金改性技术。
改性技术主要包括化学改性、机械改性和热处理改性等手段,以提高钨合金的晶粒细化、析出相均匀分布和晶界清晰度等方面。
通过改进粉末冶金工艺,能够显著提高钨合金的性能和使用寿命。
2. 钨合金纳米晶技术纳米晶技术是近年来发展起来的一种新技术,其通过控制晶粒尺寸在纳米级别,可以显著提高材料的硬度、强度和韧性。
钨合金纳米晶技术利用纳米级晶粒的优异性能,使得钨合金的性能指标得到了大幅提升。
目前,纳米晶技术已经成功应用于航天材料、舰船制造等领域,并逐渐成为了高性能钨合金制备的新方向。
3. 先进合金设计技术先进合金设计技术是一种结合材料科学与计算机模拟的新技术,在钨合金的制备中得到了广泛应用。
通过精确控制合金元素的种类、含量和分布,设计出具有特定性能的高性能钨合金材料。
现代粉末冶金材料和技术发展现状
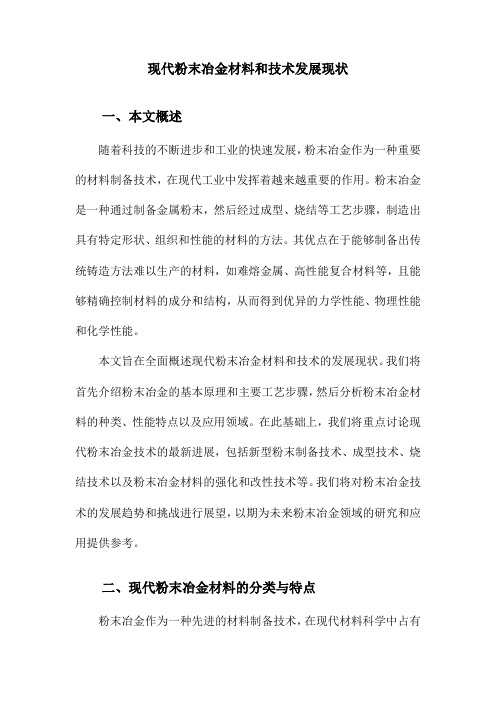
现代粉末冶金材料和技术发展现状一、本文概述随着科技的不断进步和工业的快速发展,粉末冶金作为一种重要的材料制备技术,在现代工业中发挥着越来越重要的作用。
粉末冶金是一种通过制备金属粉末,然后经过成型、烧结等工艺步骤,制造出具有特定形状、组织和性能的材料的方法。
其优点在于能够制备出传统铸造方法难以生产的材料,如难熔金属、高性能复合材料等,且能够精确控制材料的成分和结构,从而得到优异的力学性能、物理性能和化学性能。
本文旨在全面概述现代粉末冶金材料和技术的发展现状。
我们将首先介绍粉末冶金的基本原理和主要工艺步骤,然后分析粉末冶金材料的种类、性能特点以及应用领域。
在此基础上,我们将重点讨论现代粉末冶金技术的最新进展,包括新型粉末制备技术、成型技术、烧结技术以及粉末冶金材料的强化和改性技术等。
我们将对粉末冶金技术的发展趋势和挑战进行展望,以期为未来粉末冶金领域的研究和应用提供参考。
二、现代粉末冶金材料的分类与特点粉末冶金作为一种先进的材料制备技术,在现代材料科学中占有举足轻重的地位。
粉末冶金材料以其独特的制备工艺和优异的性能,广泛应用于航空、汽车、电子、医疗等诸多领域。
现代粉末冶金材料大致可分为以下几类,并各具特点。
金属粉末冶金材料:主要包括铁基、铜基、铝基等合金粉末。
这些材料通过粉末冶金工艺可以获得高致密度、高强度和高耐磨性的制品。
例如,铁基粉末冶金材料具有高的机械性能和良好的耐磨性,广泛应用于齿轮、轴承等机械零件。
陶瓷粉末冶金材料:包括氧化铝、氮化硅等陶瓷粉末。
这些材料具有高硬度、高耐磨、高温稳定等特点,常用于制造切割工具、耐磨零件和高温结构材料。
复合材料:通过粉末冶金技术,可以将金属粉末与陶瓷粉末、塑料粉末等不同性质的材料进行复合,获得具有优异综合性能的新型复合材料。
例如,金属基复合材料结合了金属的高塑性和陶瓷的高硬度,具有出色的机械性能和耐磨性。
纳米粉末冶金材料:纳米粉末冶金技术可以制备出纳米级粉末,进而制备出纳米结构材料。
几种高纯金属与合金粉末制备技术现状

几种高纯金属与合金粉末制备技术现状一、国内外发展现状、发展方向1. 高纯净度高温合金粉末粉末冶金镍基高温合金作为一种新型的高性能材料应用于航空发动机的核心耐热端部件,如压气机盘、涡轮盘、涡轮轴及涡轮盘档板等高温承力转动部件, 目前还被推广用于地面燃气涡轮发动机的涡轮盘等重要部件。
随着高推比、高功重比发动机的发展,对涡轮盘等热端部件的强度、疲劳性能和可靠性提出了更高的要求。
与传统的铸造 +锻造方法制备的高温合金相比,由于采用快速冷凝制粉技术,粉末高温合金具有成分无偏析、组织均匀、晶粒细小等组织特征,从而大幅度提高合金的屈服强度、耐蠕变性能, 蠕变疲劳性能及低周疲劳性能。
经过近三十多年的研制和发展,粉末高温合金已从第一代发展到了第三代。
60年代末期,随着高纯预合金粉末制备技术的出现,美国首先研制了粉末涡轮盘, 解决了涡轮盘高合金化造成的凝固偏析和变形困难, 提高了性能和稳定性。
应用于推重比为 8的 F-15战机中。
这一时期的代表合金有 Rene95、 IN100、 Astroloy 、ЭП741H П等, 为第一代粉末高温合金,主要追求使用温度下的高强度; 80年代以后粉末合金和工艺发展并重, 研制了损伤容限型第二代粉末高温合金, 以 Rene88DT 、N18为代表。
第二代材料的特点是使用温度高 (750℃ ,裂纹扩展速率明显比第一代粉末合金低(降低约 50% , 适用于推重比为 10发动机。
最近几年国外已经出现了高强加损伤容限的第三代粉末高温合金,计划使用在推重比 10以上的发动机中。
粉末高温合金的成功应用使国内外发动机设计师认识到, 粉末冶金已成为制造高性能涡轮盘最成熟可靠的方法, 是制造高推重比 (推重比 8以上新型发动机涡轮盘的最佳材料。
目前在粉末高温合金领域, 美欧和俄罗斯处于世界领先地位。
粉末高温合金已广泛用于美俄等国多种先进的发动机研制和生产中。
欧美粉末冶金高温合金采用气体雾化方法制备粉末,采用等温锻造+挤压工艺进行成型和致密化为主的制备方法。
- 1、下载文档前请自行甄别文档内容的完整性,平台不提供额外的编辑、内容补充、找答案等附加服务。
- 2、"仅部分预览"的文档,不可在线预览部分如存在完整性等问题,可反馈申请退款(可完整预览的文档不适用该条件!)。
- 3、如文档侵犯您的权益,请联系客服反馈,我们会尽快为您处理(人工客服工作时间:9:00-18:30)。
几种高纯金属与合金粉末制备技术现状一、国内外发展现状、发展方向1.高纯净度高温合金粉末粉末冶金镍基高温合金作为一种新型的高性能材料应用于航空发动机的核心耐热端部件,如压气机盘、涡轮盘、涡轮轴及涡轮盘档板等高温承力转动部件,目前还被推广用于地面燃气涡轮发动机的涡轮盘等重要部件。
随着高推比、高功重比发动机的发展,对涡轮盘等热端部件的强度、疲劳性能和可靠性提出了更高的要求。
与传统的铸造+锻造方法制备的高温合金相比,由于采用快速冷凝制粉技术,粉末高温合金具有成分无偏析、组织均匀、晶粒细小等组织特征,从而大幅度提高合金的屈服强度、耐蠕变性能,蠕变疲劳性能及低周疲劳性能。
经过近三十多年的研制和发展,粉末高温合金已从第一代发展到了第三代。
60年代末期,随着高纯预合金粉末制备技术的出现,美国首先研制了粉末涡轮盘,解决了涡轮盘高合金化造成的凝固偏析和变形困难,提高了性能和稳定性。
应用于推重比为8的F-15战机中。
这一时期的代表合金有Rene95、IN100、Astroloy、ЭП741HП等,为第一代粉末高温合金,主要追求使用温度下的高强度;80年代以后粉末合金和工艺发展并重,研制了损伤容限型第二代粉末高温合金,以Rene88DT、N18为代表。
第二代材料的特点是使用温度高(750℃),裂纹扩展速率明显比第一代粉末合金低(降低约50%),适用于推重比为10发动机。
最近几年国外已经出现了高强加损伤容限的第三代粉末高温合金,计划使用在推重比10以上的发动机中。
粉末高温合金的成功应用使国内外发动机设计师认识到,粉末冶金已成为制造高性能涡轮盘最成熟可靠的方法,是制造高推重比(推重比8以上)新型发动机涡轮盘的最佳材料。
目前在粉末高温合金领域,美欧和俄罗斯处于世界领先地位。
粉末高温合金已广泛用于美俄等国多种先进的发动机研制和生产中。
欧美粉末冶金高温合金采用气体雾化方法制备粉末,采用等温锻造+挤压工艺进行成型和致密化为主的制备方法。
随着粉末高温合金的发展,欧美制造技术有以下特点:①采用特殊的热处理制度,改善材料损伤容限性能;②提高盘件的可靠性,主要是通过提高材料的纯净度,选择最佳的坩埚材质并降低粉末粒度,使夹杂物的尺寸和数量得到控制;③采用等温锻造技术保证盘件的完整性;④采用计算机数值模拟技术进行粉末盘的全过程模拟。
俄罗斯的粉末高温合金的研究几乎与美国同时进行,并取得了具有自己特色的粉末高温合金及制造技术,其主要特色有:①采用等离子电极旋转工艺制备预合金粉末;②采用直接热等静压工艺制备盘件;③采用先进的计算机软件进行粉末涡轮盘件的包套设计及致密化过程模拟,达到近净尺寸的盘坯制备。
近几年来俄罗斯也建立了大气和真空条件下的等温锻装置,开展了粉末高温合金等温锻和超塑性锻造的研究。
目前高温合金粉末的制备方法有氩气雾化法(AA法)和等离子旋转电极法(REP法),前者在欧美国家获得应用,后者以俄罗斯为主。
氩气雾化法是以高速氩气流将高温合金液流直接击碎成粉末的过程,该方法具有雾化效率高、设备相对简单、成本低等特点。
但合金粉末的制备过程与坩埚、漏管等陶瓷件接触,因此制备的粉末陶瓷夹杂物较高。
早期的雾化技术由于采用自由落体式的雾化喷嘴,粉末粒度难以小于45μm,是导致粉末夹杂物含量高的一个主要原因。
采用微细粉末是解决夹杂物的一个根本措施。
近年来随着紧耦合等先进雾化技术进行工艺化阶段,采用先进的雾化技术制备粒度细小的高温合金粉末(<45μm)已成为现实。
如欧美的雾化设备可以使-50μm粉末的收得率高于80%。
粉末细化后显著降低夹杂物的尺寸和数量,明显改善合金的疲劳性能。
采用粒度细小的预合金粉末还可以进一步提高粉末的冷却速度和细化晶粒,达到以下效果:①提高化学成分的均匀性,第二相组织更加均匀和细小;②细小的晶粒结构提高工件的加工性能。
因此随着雾化制粉技术的进步,粉末粒度微细化(-45m)是粉末高温合金的一个新的研究方向。
氩气雾化的另一个研究进展是超纯净粉末的研制,将冷坩埚熔炼技术应用雾化合金的熔炼,可以解决粉末的陶瓷夹杂问题。
但冷坩埚熔炼技术难度大、设备投资大且与雾化设备的对接不易实现,目前只有欧美少数几个大公司进行研究;而且冷坩埚的容量有限,难于大批量生产。
等离子旋转电极雾化制粉工艺是将高温合金制成电极棒,电极棒一端采用等离子弧加热,另一端与高速电机(大于10000转/分钟)连接,在离心力的作用下,熔化的金属经甩出后形成粉末。
该技术的特点是粉末的纯度高,非金属夹杂物含量低,氧含量低(≤70ppm);粉末粒度分布窄,球形度好。
但由于受到电极棒转速的限制,粉末粒度较粗,只能制备-100+45μm粒度的粉末,而且旋转电极法设备复杂、投资大。
电极法的主要进展是提高电极棒的质量,降低非金属夹杂物的含量,如采用双联、三联熔炼工艺。
国内粉末冶金高温合金是从20世纪70年代末开始的,并相继建立了一些基本的研制手段,1977年铁钢研究总院从德国Heraeus公司引进了65kg级氩气雾化制粉装置以及粉末处理等设备,先后研究了FGH100和FGH95两个牌号的粉末高温合金。
在此基础上,“六五”期间粉末高温合金由国家立项,钢铁研究总院和北京航空材料研究所等4家单位共同研制FGH95合金,经过大量的研究工作,其性能基本上达到美国同类合金的技术条件。
存在的主要问题:①氩气雾化粉末粒度较粗、粒度小于45μm的粉末含量低于20%;②制粉过程中带入了较多的陶瓷夹杂物(20~30个/100g粉末),与美国的氩气雾化法相比,夹杂物数量高一倍以上。
由于以上问题致使合金性能不稳定。
为了配合我国新型高推重比航空发动机的研制,FGH95粉末高温合金在“八五”、“九五”均进行了立项研究。
为了解决粉末的质量问题,1994年从俄罗斯引进先进的制备高纯度粉末的等离子旋转工艺制粉设备,同时引进了与其配套的关键设备。
“八五”期间,在等离子制粉工艺、粉末处理、热等静压、合金组织等方面进行大量的工作。
使用粒度为50~150μm的旋转电极粉,制备的涡轮盘基本上满足技术条件。
为了满足我国高推比发动机的研制,北京航空材料研究院开展了第二代FGH96粉末盘材料的研究,采用等离子旋转工艺制备预合金粉末,以热等静压和等温锻造工艺进行形成和致密化。
我国粉末盘的研究和应用近年来取得了一定的进展。
但总体来说,与国外的存在较大的差距,主要体现在以下几个方面:①原材料预合金粉末,国内以使用-150+50μm的旋转电极粉末,欧美国家使用-45μm的雾化合金粉末;②设备条件,国内缺少氩气雾化微细高温合金的制粉设备和大吨位高温锻造机。
从国外的研究情况分析,采用先进的雾化制粉技术和熔炼技术是制备高温合金粉末的必然选择。
国内70年代引进的雾化设备由于技术落后,已不能用于高温合金粉末的研制;目前中南大学粉末冶金研究院从英国引进了具有国际先进水平的紧耦合气体雾化制粉系统,该系统在粉末的粒度、含氧量控制、粉末性能稳定性控制方面达到国际先进水平,非常适合于高温合金粉末的研制和开发。
2.高活性钛与钛铝金属粉末钛及钛合金密度低, 比强度高, 耐腐蚀性、高温下抗蠕变性能和焊接性能良好, 且生物相容性优异,被广泛用于航空航天、航海、化工、发电、汽车、体育休闲、医疗等领域。
钛铝基合金由于具有良好的高温抗氧化性能、抗蠕变性能和高的比弹性模量、比刚度,被认为是理想的航空航天用高温结构材料。
在使用温度(800℃左右),钛铝合金的杨氏模量远远高于钛合金,接近于镍基超合金,而它的密度仅为镍基合金的一半(3.9g/cm3)。
高温条件下,它的屈服强度也远远高于钛合金,当温度高于540℃时,它的比强度甚至高于Niconel-718合金,与R220c合金接近。
它的热膨胀系数介于钛合金和镍基超合金之间,因而易于与当前发动机中其它材料相配合。
钛铝基合金的导热系数高,热膨胀率低,可以减小发动机服役部件的热应力和热疲劳破坏倾向。
由于钛铝基合金具有上述优异的性能,在未来高性能飞行器及发动机中,可以取代钛基合金和镍基超合金成为某些关键零部件的用材。
钛粉的制备方法可归纳分为两大类: 机械法和物理化学法。
其中,机械法又可分为: 机械研磨法、HDH(氢化-脱氢)法、气体雾化法、旋转电极法。
纯钛粉制备最早是将海绵钛机械粉碎制得, 但该方法很难得到粒度较细的粉末。
HDH方法可制得粒度较细的钛粉末, 且成本较低, 但是钛粉的氧含量难以控制。
气体雾化法生产钛粉具有冷却速度快, 粉末颗粒细, 粉末收得率高, 成本低等优点。
气雾化钛及钛合金粉末化学性能与等离子旋转电极( PREP) 工艺粉末性能相当,粒度分布优于PREP工艺粉末。
旋转电极法生产的钛粉可以制得相对密度高、机械性能好的钛合金部件。
但采用此法生产的钛粉成本高, 所以一般只能用于航空航天领域。
目前HDH法和雾化法已成为工业应用钛粉的主要生产方法。
物理化学法又可分为:还原法、熔盐电解法。
镁热还原法( Kroll法) 和钠热还原法(Hunter 法)在生产过程中必须对反应炉进行装料、高温加热、以及卸料操作,不仅能耗高,而且周期长,生产成本比较高;同时,生产出的钛产品呈海绵状,必须对其进行包括除杂质和固结在内的一系列后续加工,否则无法使用,这使得成本进一步增加。
新兴的还原法有: Armstrong钠还原法和MHR法。
Armstrong 钠还原法实际上是将钠还原法改进为连续化生产的一种工艺方法,实现了钠的循环使用, 且可以连续还原TiCl4 制得钛粉, 具有生产连续化、投资少、产品应用范围广、有效地降低了副产物成本,但进一步降低氧含量和产品成本是该工艺面临的主要问题。
MHR 法是用金属氢化物直接还原TiO2 来制取钛粉,由于该法不涉及四氯化钛的中间生产, 氯化物含量极低, 氧含量可小于0.1%, 氢含量介于0.001%和0.4%之间,该法生产的钛粉成本较低。
新型熔盐电解有FFC 剑桥工艺, OS 工艺, EMR/MSE等工艺。
熔盐电解生产金属钛的优点在于工艺相对简单,可实现半连续化工业生产. 然而工艺过程中存在氧、碳、铁等元素的污染,且使用了大量的盐,不仅存在钛盐分离困难且缺乏有效的回收盐的方法;另外还存在电流效率低的缺点。
今后的研究重点应是如何提高产品的纯度和电解效率,并降低产品成本。
目前,制备钛铝合金粉主要采用的方法有雾化法、机械合金化法(MA)、自蔓延高温合成法(SHS)等,其中最常用的为雾化法。
由于钛的熔点较高、活性大,钛铝合金粉末的制备需严格控制工艺,难度较大,因而在过去价格十分昂贵。
雾化粉末有较好的球形度、粒度均匀,而且颗粒内的微观组织具有快凝组织特征。
采用保护气氛又可使氧化夹杂降到最低。
所以,雾化粉末是粉末冶金近净成型技术的最为理想粉末的之一。
目前,雾化制粉已是粉末冶金方法中较成熟的工艺。