高强钢的冷冲压成型
高强钢冲压成形过程中的扭曲回弹及补偿研究
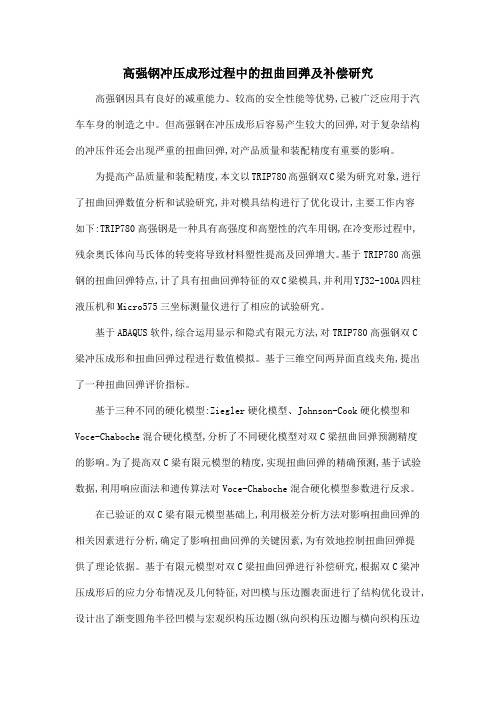
高强钢冲压成形过程中的扭曲回弹及补偿研究高强钢因具有良好的减重能力、较高的安全性能等优势,已被广泛应用于汽车车身的制造之中。
但高强钢在冲压成形后容易产生较大的回弹,对于复杂结构的冲压件还会出现严重的扭曲回弹,对产品质量和装配精度有重要的影响。
为提高产品质量和装配精度,本文以TRIP780高强钢双C梁为研究对象,进行了扭曲回弹数值分析和试验研究,并对模具结构进行了优化设计,主要工作内容如下:TRIP780高强钢是一种具有高强度和高塑性的汽车用钢,在冷变形过程中,残余奥氏体向马氏体的转变将导致材料塑性提高及回弹增大。
基于TRIP780高强钢的扭曲回弹特点,计了具有扭曲回弹特征的双C梁模具,并利用YJ32-100A四柱液压机和Micro575三坐标测量仪进行了相应的试验研究。
基于ABAQUS软件,综合运用显示和隐式有限元方法,对TRIP780高强钢双C 梁冲压成形和扭曲回弹过程进行数值模拟。
基于三维空间两异面直线夹角,提出了一种扭曲回弹评价指标。
基于三种不同的硬化模型:Ziegler硬化模型、Johnson-Cook硬化模型和Voce-Chaboche混合硬化模型,分析了不同硬化模型对双C梁扭曲回弹预测精度的影响。
为了提高双C梁有限元模型的精度,实现扭曲回弹的精确预测,基于试验数据,利用响应面法和遗传算法对Voce-Chaboche混合硬化模型参数进行反求。
在已验证的双C梁有限元模型基础上,利用极差分析方法对影响扭曲回弹的相关因素进行分析,确定了影响扭曲回弹的关键因素,为有效地控制扭曲回弹提供了理论依据。
基于有限元模型对双C梁扭曲回弹进行补偿研究,根据双C梁冲压成形后的应力分布情况及几何特征,对凹模与压边圈表面进行了结构优化设计,设计出了渐变圆角半径凹模与宏观织构压边圈(纵向织构压边圈与横向织构压边圈),并结合渐变圆角半径凹模与纵向织构压边圈进行了综合补偿研究。
研究结果表明:基于渐变圆角半径凹模的回弹角减小了23.8%;基于纵向织构压边圈的回弹角减小了27.9%,基于横向织构压边圈的回弹角减小了21.2%;基于渐变圆角半径凹模和纵向织构压边圈的回弹减小了33.6%。
超高强钢冷冲压三点弯曲与辊压弯曲性
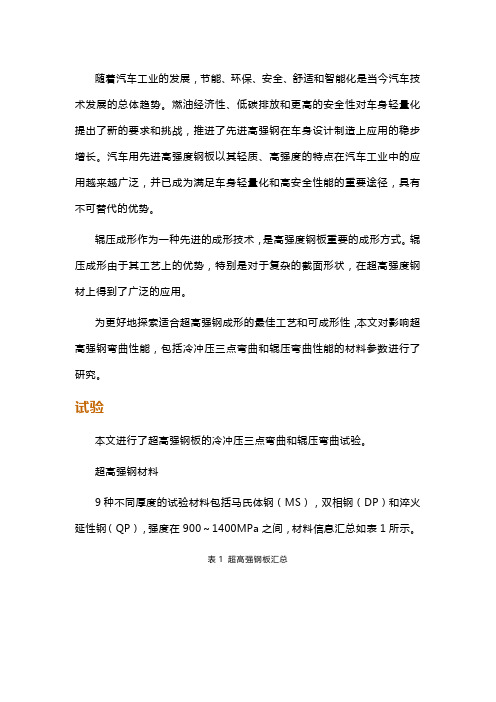
随着汽车工业的发展,节能、环保、安全、舒适和智能化是当今汽车技术发展的总体趋势。
燃油经济性、低碳排放和更高的安全性对车身轻量化提出了新的要求和挑战,推进了先进高强钢在车身设计制造上应用的稳步增长。
汽车用先进高强度钢板以其轻质、高强度的特点在汽车工业中的应用越来越广泛,并已成为满足车身轻量化和高安全性能的重要途径,具有不可替代的优势。
辊压成形作为一种先进的成形技术,是高强度钢板重要的成形方式。
辊压成形由于其工艺上的优势,特别是对于复杂的截面形状,在超高强度钢材上得到了广泛的应用。
为更好地探索适合超高强钢成形的最佳工艺和可成形性,本文对影响超高强钢弯曲性能,包括冷冲压三点弯曲和辊压弯曲性能的材料参数进行了研究。
试验本文进行了超高强钢板的冷冲压三点弯曲和辊压弯曲试验。
超高强钢材料9种不同厚度的试验材料包括马氏体钢(MS),双相钢(DP)和淬火延性钢(QP),强度在900~1400MPa之间,材料信息汇总如表1所示。
表1 超高强钢板汇总设备超高强钢板三点弯曲试验模具,如图1所示。
凸模圆角半径与板料厚度的比值(R/T)被定义为相对弯曲半径。
试验安排本着通过最小数量的试验来获得最小弯曲半径的原则。
本文中的凸模圆角半径均大于1倍料厚。
在特定的三个弯曲角度90°、120°、150°下进行弯曲试验。
图1 三点弯曲模具结构图为评价超高强钢板的辊压性能,采用180°V形截面进行辊压弯曲成形试验。
辊压成形工艺及设备如图2所示。
取4种规格的轧辊进行试验,轧辊半径分别为0.5T、1T、2T和3T,T为板料厚度。
5种弯曲角度54°、90°、126°、144°和180°被用来进行最大弯曲角度的测定。
图2 180°V形截面形状的辊压成形试验设备结果超高强钢板三点弯曲试验最小弯曲半径和最大弯曲角度被用来评估超高强钢的弯曲性能,以外侧表面出现微裂纹作为弯曲极限的标志。
cae回弹补偿的高强度钢冷压成形回弹量集成控制方法
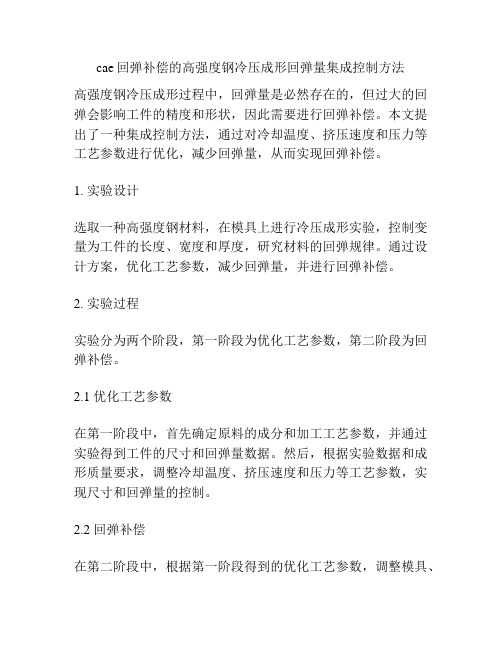
cae回弹补偿的高强度钢冷压成形回弹量集成控制方法高强度钢冷压成形过程中,回弹量是必然存在的,但过大的回弹会影响工件的精度和形状,因此需要进行回弹补偿。
本文提出了一种集成控制方法,通过对冷却温度、挤压速度和压力等工艺参数进行优化,减少回弹量,从而实现回弹补偿。
1. 实验设计选取一种高强度钢材料,在模具上进行冷压成形实验,控制变量为工件的长度、宽度和厚度,研究材料的回弹规律。
通过设计方案,优化工艺参数,减少回弹量,并进行回弹补偿。
2. 实验过程实验分为两个阶段,第一阶段为优化工艺参数,第二阶段为回弹补偿。
2.1 优化工艺参数在第一阶段中,首先确定原料的成分和加工工艺参数,并通过实验得到工件的尺寸和回弹量数据。
然后,根据实验数据和成形质量要求,调整冷却温度、挤压速度和压力等工艺参数,实现尺寸和回弹量的控制。
2.2 回弹补偿在第二阶段中,根据第一阶段得到的优化工艺参数,调整模具、设备和控制系统等部分,实现自动化生产过程。
在生产过程中,通过传感器实时监测工件的尺寸和回弹量,并通过控制系统进行回弹补偿。
具体步骤如下:(1)确定工件的尺寸和回弹量标准值。
(2)通过传感器实时监测工件的尺寸和回弹量。
(3)将实时监测到的数据与标准值进行对比,并计算出回弹量。
(4)根据回弹量调整模具中的压力和温度等参数。
(5)重新进行冷压成形,并再次通过传感器监测工件的尺寸和回弹量。
(6)迭代计算,直到满足要求。
3. 实验结果通过对高强度钢冷压成形回弹量进行集成控制,实现了回弹补偿的目的。
实验结果表明,优化工艺参数后,回弹量得到了明显控制,而回弹补偿方法的应用可以有效减小回弹量,提高工件的成形质量。
超高强度钢板冲压件热成形工艺

超高强度钢板冲压件热成形工艺摘要:随着国民物质生活水平的提高,大家对汽车安全性的要求也越来越强烈,因此,高强度、超高强度钢板在汽车车身上的应用也越来越广泛。
然而,由于高强度、超高强度钢板在常温下强度较高,变形抗力比较大,导致利用常规冷冲压成形的方式很难成形,因此高强度、超高强度钢板热冲压成形技术就应运而生。
目前,高强度钢板热冲压成形零件已经广泛应用于国内外汽车车身的重要零件上。
关键词:热冲压成形;超高强度钢板;模具设计;冷却系统;数值模拟;一、热冲压成形工艺原理首先把常温下强度为500~600MPa的高强度硼合金钢板加热到880~950℃,使之均匀奥氏体化,然后送入内部带有冷却系统的模具内冲压成形,之后保压快速冷却淬火,使奥氏体转变成马氏体,成形件因而得到强化硬化,强度大幅度提高。
比如经过模具内的冷却淬火,冲压件强度可以达到1500MPa,强度提高了250%以上,因此该项技术又被称为“冲压硬化”技术。
实际生产中,热冲压工艺又分为两种,即直接工艺和间接工艺。
直接工艺,下料后,直接把钢板加热然后冲压成形,主要用于形状比较简单变形程度不大的工件。
对于一些形状复杂的或者拉深深度较大的工件,则需要采用间接工艺,先把下好料的钢板预变形,然后再加热实施热冲压,二、热冲压成形工艺的主要影响因素2.1材料热冲压成形工艺中采用的是一种特殊的具有自硬性的硼合金高强度钢板。
和现在的双相钢、相变诱导塑性钢、复相钢、马氏体钢等汽车高强度钢板不同,这些钢板常温下强度就很高,并且通常都采用冷冲压工艺制造零部件,成形前后零件的微观组织没有变化,强度等指标基本上保持不变。
而热成形工艺中使用的硼合金钢板是一种低碳微合金钢,添加了一定量的B元素,提高了钢板的淬火性能,成形后发生相变,强度等指标成倍提高。
另外,还添加了Ti,Cr,Mo,Cu,Ni等多种合金微量儿素,因而提高了材料的屈服强度以及其他力学性能,材料力学性能也很稳定。
典型的热冲压成形钢板22MnB5的下要成分,这种钢板常温下的强度不很高,抗拉强度仅有500700MPa,塑性、可成形性等性能也很好,而通过热成形工艺的加热、成形、冷却后,成形件被淬火,微观组织转变成马氏体,强度、硬度等指标大幅度提高,屈服强度可以达到1000MPa以上,抗拉强度达到1500MPa,硬度可以达到50HRC。
高强钢的冷冲压成型

高强钢的冷冲压成型精益生产、绿色生态高性能润滑剂可提供一种更高性能的膜以保护金属免于断裂、压裂或被焊接到模具上。
好的润滑剂还能够减少摩擦热量,使金属流动不间断并能控制起皱或断裂。
汽车工业的迅猛发展为国民经济和社会发展发挥了重要作用。
但受能源短缺、环境污染等问题的影响,该行业发展之矛盾也日益凸显。
展望未来,该行业的发展只有建立在自然、生态、节能、安全等背景下,其发展才可持续。
在此背景下,汽车轻量化以及高强钢的应用成为了重要发展方向。
但受高强钢板材强度的提高,传统的冷冲压工艺在成型过程中容易产生破裂现象,无法满足高强度钢板的加工工艺要求。
在无法满足成型条件的情况下,目前国际上逐渐研究超高强度钢板的热冲压成形技术。
该技术是综合了成形、传热以及组织相变的一种新工艺,主要是利用高温奥氏体状态下,板料的塑性增加,屈服强度降低的特点,通过模具进行成形的工艺。
但是热成型需要对工艺条件、金属相变、CAE分析技术进行深入研究,目前该技术被国外厂商垄断,国内发展缓慢。
据调查统计,部分汽车品牌高强钢的应用不断扩大,有些车型的车身框架高强度钢的应用已达90%。
一、高强钢特点及成型问题分析根据美国钢铁学院能量部的研究,即使高强度钢降低部分数值其拉伸还是要比传统的冷板困难得多。
高强钢的延展率只有普通钢材的一半(如下图1)同时,当材料被冲压成形时,会变硬,不同的钢材,变硬的程度不同(如下图2)。
一般高强度低合金钢只略有20MPa增加,不到10%。
注意:双相钢的屈服强度有140MPa增加,增加了40%多!金属在成形过程中,会变得完全不同,完全不像冲压加工开始之前。
这些钢材在受力后,屈服强度增加很多。
材料较高的屈服应力加上加工硬化,等于流动应力的大大增加。
因此,开裂、回弹、起皱、工件尺寸、模具磨损、微焊接磨损(如下图3)等成为了高强钢成型过程中的问题焦点。
高强钢屈服强度普通高强钢HSS 210Mpa30KSI比低碳钢含更多的碳和锰高强度低合金钢HSLA 280-550Mpa40-79KSI细晶铁素体与碳和/或者氮析出物,含钛、钒,冲压时,板材屈服强度-YS,仅增加-伊苏只增加20Mpa(3KSI)热处理硬化钢180-280Mpa26-40KSI在冲压加工成形过程中被硬化或者经过烤箱170F(20-30分钟),屈服强度提高70Mpa(10KSI)双相钢350-600Mpa50-86KSI软铁素与岛状马氏体。
高强度钢板冷冲压成形数值模拟研究
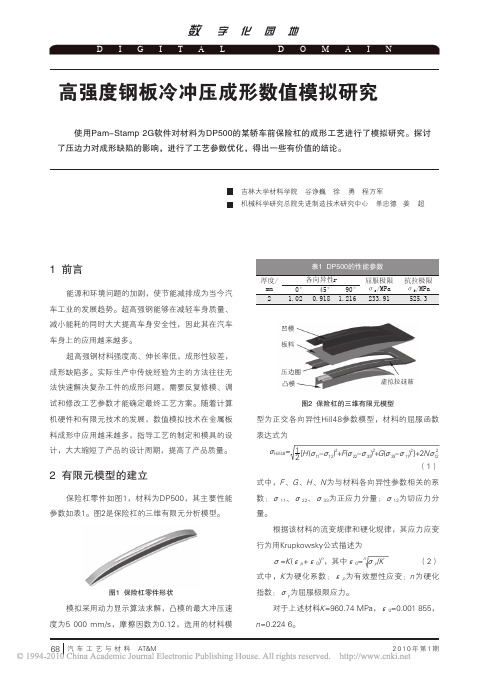
图6 压边力对纵向回弹影响的模拟结果
分明显。对于此类弯曲半径相对较大的细长零件,如 果能够在成形时增大零件两端的压边力,或者再施加 一定的拉力(比如拉弯),可以有效减小纵向回弹 量。
对高强钢前保险杠的成形缺陷规律分析可知,压 边力选为5 000 kN可得到成形质量较好的产品,此时 零件的最大变薄率为18.23%,未出现起皱和拉裂缺 陷,且成形后工件回弹较小。
补充,因此导致B处变薄量增大。随着压边力进一步 增大,B处变薄量加剧,并最终导致此处出现开裂, 如图3c中C处。 3.2 回弹模拟研究
超高强钢冷成形后回弹问题非常显著,回弹是成 形后工件的主要缺陷之一,因此在工艺制定和模具设 计时必须加强对回弹的控制。本文研究了压边力对该 保险杠回弹的影响。
该零件的回弹主要包含截面回弹和纵向回弹两
2010年第1期
汽 车 工 艺 与 材 料 AT&M 69
数 字化园地
D I G I TA L
DOMAIN
种,如图4。分别模拟研究了压边力为1 600 kN、 3 000 kN、4 000 kN、5 000 kN时成形工件的回弹 状况。图5是压边力对截面回弹的模拟结果,可以看 出,随着压边力的增加,截面回弹量明显减小,因此 增大压边力可以有效控制截面回弹,提高截面形状 精度。图6是压边力对纵向回弹的模拟结果,可以看 出,增加压边力也能够减小纵向回弹量,但效果不十
对于此类弯曲半径相对较大的细长零件如果能够在成形时增大零件两端的压边力或者再施加一定的拉力比如拉弯可以有效减小纵向回弹对高强钢前保险杠的成形缺陷规律分析可知压边力选为000kn可得到成形质量较好的产品此零件的最大变薄率为1823未出现起皱和拉结论1压边力对变薄起皱和拉裂等缺陷影响较大
超高强度钢的冷变形成形与力学性能研究

超高强度钢的冷变形成形与力学性能研究超高强度钢是最近研究的热点之一,其应用领域非常广泛,包括航空、汽车、船舶、架桥、建筑和能源等方面。
由于其具有高强度、高韧性、良好的可焊性和强抗环境腐蚀等特点,超高强度钢在工业界中越来越受到关注。
本文对超高强度钢的冷变形成形和力学性能进行探讨。
1. 超高强度钢的冷变形超高强度钢的冷变形是一种非热加工技术,通过对钢材进行冷却处理,使其变得更加硬度和强度,通常采用拉拔工艺。
拉拔是将材料通过一系列套在一起的模具中拉拉过去,使得钢材变形,达到工艺目的。
在这个过程中,为了使钢材变形更加均匀和细腻,需要控制好拉拔速度和拉拔力。
超高强度钢的拉拔变形过程是非常复杂的,需要对几个方面进行研究和掌握。
首先,需要对超高强度钢的成分进行分析,以便确定适合的拉拔变形过程。
钢材中含有各种元素,包括铁、碳、锰、硅、硫和磷等。
不同的元素含量对钢材的力学性能有着不同的影响,因此需要对这些元素进行分析和对比。
其次,需要确定拉拔变形的参数,包括拉拔速度、拉拔力和拉拔力曲线。
这些参数决定了钢材的冷变形程度和成形效果。
为了达到最佳的变形效果,需要对这些参数进行合理的设计和优化。
最后,需要对拉拔变形过程中的微观结构变化进行研究。
这些变化包括晶粒细化、奥氏体结构改变和相变等。
理解这些微观结构变化对于控制和优化拉拔变形过程是非常重要的。
2. 超高强度钢的力学性能超高强度钢具有很好的力学性能,其中包括高强度、高韧性、高耐磨性和高耐蚀性等。
这些性能是由钢材的化学成分、微观结构和物理性质所决定的。
首先,超高强度钢的高强度是由其成分中的碳和其他合金元素共同作用所致。
碳元素可以使钢材硬度增加,而其他合金元素可以提高钢材的强度和韧性。
其次,超高强度钢的高韧性是由奥氏体和贝氏体相的存在所决定的。
奥氏体是一种通过加热和冷却处理得到的钢材结构,具有很好的强度和塑性;贝氏体则是一种通过拉拔变形得到的钢材结构,具有很好的强度和韧性。
超高强度钢防撞梁热成形改冷冲压工艺设计及优化_张旭
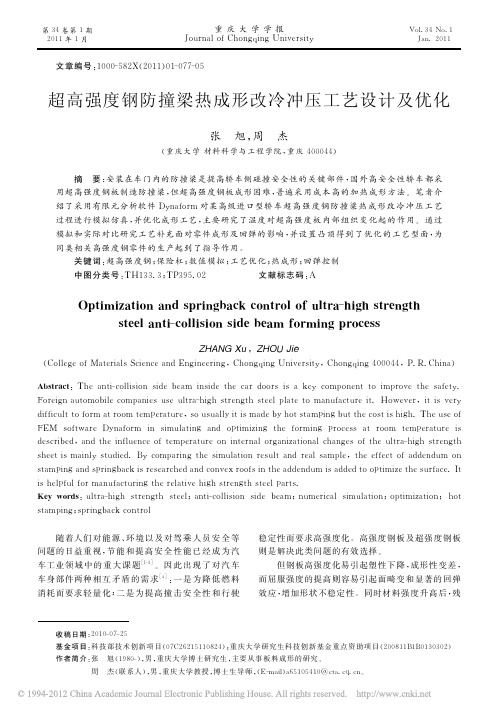
σy = K(εyp +εp)n
模拟和实际对比研究工艺补充面对零件成形及回弹的影响 ,并设置凸顶得到了优化的工艺型面,为
同类相关高强度钢零件的生产起到了指导作用。
关 键 词 :超 高 强 度 钢 ;保 险 杠 ;数 值 模 拟 ;工 艺 优 化 ;热 成 形 ;回 弹 控 制
中 图 分 类 号 :TH133.3;TP395.02
图 2 冷 冲 压 成 形 过 程 中 产 生 破 裂
1 零件的工艺性及其有限元模型
1.1 零 件 工 艺 性 分 析 该 零 件 形 面 如 图 1 所 示 ,为 保 证 乘 员 安 全 性 ,该
防撞梁采用瑞典 SAAB 公司 Docol1200M 型超高强 度钢板,屈服强度达到1 150~1 270 MPa,抗拉强度 大于等于 1 400 MPa。 国 产 时,由 于 前 期 未 采 用 数 值模拟分析,在 采 用 传 统 冷 冲 压 试 制 过 程 中 发 现 零 件尾部发生破 裂 (如 图 2 所 示),而 且 声 音 巨 大。 由 此 可 知 ,该 超 高 强 度 钢 板 在 常 温 下 塑 性 变 形 区 较 小 , 延 伸 性 差 ,成 形 困 难 。 为 克 服 这 一 困 难 ,首 先 对 该 超 高强度钢板进 行 拉 伸 试 验,并 对 比 材 料 在 加 热 前 后 材料的成形性 能,以 确 定 工 艺 参 数。 图 3 是 该 材 料 在各 温 度 梯 度 下 的 应 力 应 变 曲 线,从 图 上 可 以 看 出 ,但 该 材 料 在 常 温 时 即 使 发 生 较 小 应 变 ,其 应 力 增 加 迅 速 ,而 且 容 易 断 裂 ,但 随 着 温 度 的 升 高 其 屈 服 强 度下 降 明 显,当 温 度 达 到 1 000 ℃ 时 其 屈 服 强 度 下 降为720 MPa,而应变相应增加,能有效提高材料的 塑性变形能力。通过图4的微观组织照片可以看出 当温度升高到1 000 ℃时内部的马氏体(明亮部分) 组 织 变 小 ,促 使 材 料 的 塑 性 变 形 能 力 得 到 改 善 ,此 过 程如同淬火工艺能有效提升钢板强度一样。
22MnB5超高强度钢冷冲压成形的数值模拟
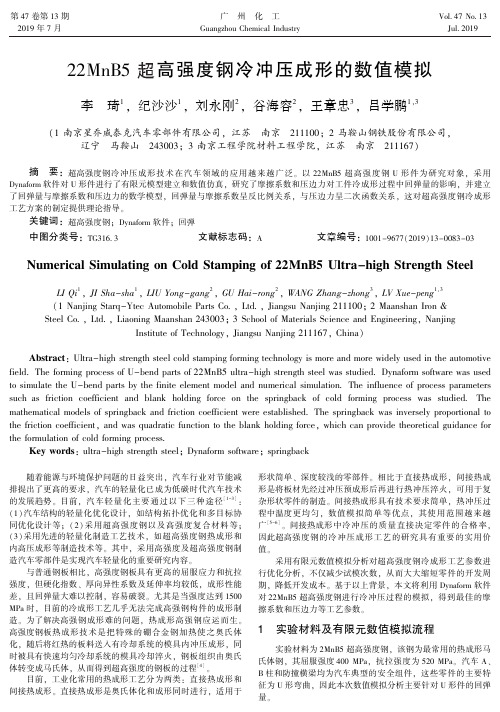
摇 中图分类号: TG316郾 3
摇 文献标志码: A
文章编号: 1001-9677(2019)13-0083-03
Numerical Simulating on Cold Stamping of 22MnB5 Ultra-high Strength Steel
摘摇 要: 超高强度钢冷冲压成形技术在汽车领域的应用越来越广泛。 以 22MnB5 超高强度钢 U 形件为研究对象, 采用
Dynaform 软件对 U 形件进行了有限元模型建立和数值仿真, 研究了摩擦系数和压边力对工件冷成形过程中回弹量的影响, 并建立 了回弹量与摩擦系数和压边力的数学模型, 回弹量与摩擦系数呈反比例关系, 与压边力呈二次函数关系, 这对超高强度钢冷成形 工艺方ቤተ መጻሕፍቲ ባይዱ的制定提供理论指导。
第 47 卷第 13 期 2019 年 7 月
广摇 州摇 化摇 工 Guangzhou Chemical Industry
Vol郾 47 No郾 13 Jul郾 2019
22MnB5 超高强度钢冷冲压成形的数值模拟
李摇 琦1 , 纪沙沙1 , 刘永刚2 , 谷海容2 , 王章忠3 , 吕学鹏1,3
(1 南京星乔威泰克汽车零部件有限公司, 江苏摇 南京摇 211100; 2 马鞍山钢铁股份有限公司, 辽宁摇 马鞍山摇 243003; 3 南京工程学院材料工程学院, 江苏摇 南京摇 211167)
LI Qi1 , JI Sha-sha1 , LIU Yong-gang2 , GU Hai-rong2 , WANG Zhang-zhong3 , LV Xue-peng1,3 (1 Nanjing Starq-Ytec Automobile Parts Co郾 , Ltd郾 , Jiangsu Nanjing 211100; 2 Maanshan Iron & Steel Co郾 , Ltd郾 , Liaoning Maanshan 243003; 3 School of Materials Science and Engineering, Nanjing
高强钢热冲压成型工艺流程 预热处理 冲压成形
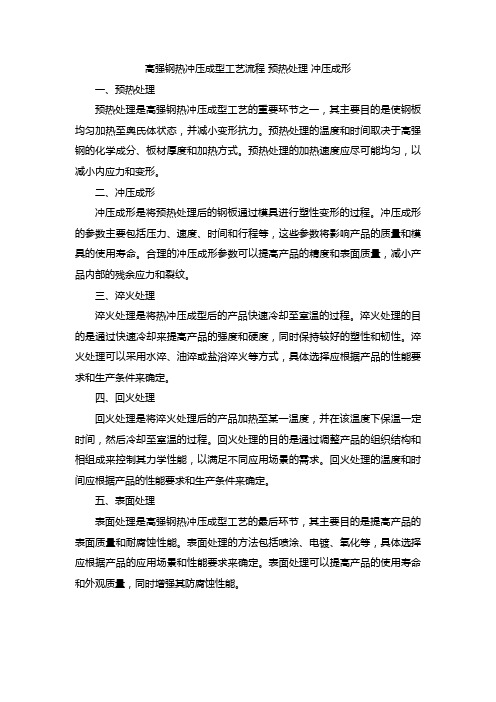
高强钢热冲压成型工艺流程预热处理冲压成形一、预热处理预热处理是高强钢热冲压成型工艺的重要环节之一,其主要目的是使钢板均匀加热至奥氏体状态,并减小变形抗力。
预热处理的温度和时间取决于高强钢的化学成分、板材厚度和加热方式。
预热处理的加热速度应尽可能均匀,以减小内应力和变形。
二、冲压成形冲压成形是将预热处理后的钢板通过模具进行塑性变形的过程。
冲压成形的参数主要包括压力、速度、时间和行程等,这些参数将影响产品的质量和模具的使用寿命。
合理的冲压成形参数可以提高产品的精度和表面质量,减小产品内部的残余应力和裂纹。
三、淬火处理淬火处理是将热冲压成型后的产品快速冷却至室温的过程。
淬火处理的目的是通过快速冷却来提高产品的强度和硬度,同时保持较好的塑性和韧性。
淬火处理可以采用水淬、油淬或盐浴淬火等方式,具体选择应根据产品的性能要求和生产条件来确定。
四、回火处理回火处理是将淬火处理后的产品加热至某一温度,并在该温度下保温一定时间,然后冷却至室温的过程。
回火处理的目的是通过调整产品的组织结构和相组成来控制其力学性能,以满足不同应用场景的需求。
回火处理的温度和时间应根据产品的性能要求和生产条件来确定。
五、表面处理表面处理是高强钢热冲压成型工艺的最后环节,其主要目的是提高产品的表面质量和耐腐蚀性能。
表面处理的方法包括喷涂、电镀、氧化等,具体选择应根据产品的应用场景和性能要求来确定。
表面处理可以提高产品的使用寿命和外观质量,同时增强其防腐蚀性能。
通过以上五个方面的介绍,可以看出高强钢热冲压成型工艺的流程涉及多个环节。
在生产过程中,要保证每个环节的质量和稳定性,以获得高性能的高强钢制品。
cae回弹补偿的高强度钢冷压成形回弹量集成控制方法
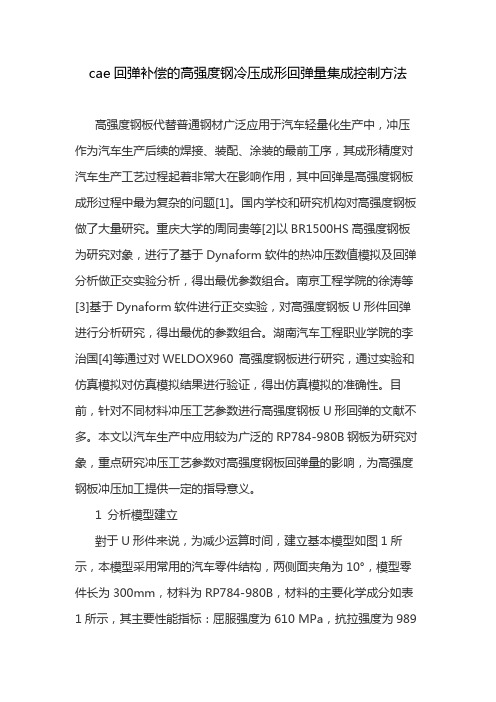
cae回弹补偿的高强度钢冷压成形回弹量集成控制方法高强度钢板代替普通钢材广泛应用于汽车轻量化生产中,冲压作为汽车生产后续的焊接、装配、涂装的最前工序,其成形精度对汽车生产工艺过程起着非常大在影响作用,其中回弹是高强度钢板成形过程中最为复杂的问题[1]。
国内学校和研究机构对高强度钢板做了大量研究。
重庆大学的周同贵等[2]以BR1500HS高强度钢板为研究对象,进行了基于Dynaform软件的热冲压数值模拟及回弹分析做正交实验分析,得出最优参数组合。
南京工程学院的徐涛等[3]基于Dynaform软件进行正交实验,对高强度钢板U形件回弹进行分析研究,得出最优的参数组合。
湖南汽车工程职业学院的李治国[4]等通过对WELDOX960 高强度钢板进行研究,通过实验和仿真模拟对仿真模拟结果进行验证,得出仿真模拟的准确性。
目前,针对不同材料冲压工艺参数进行高强度钢板U形回弹的文献不多。
本文以汽车生产中应用较为广泛的RP784-980B钢板为研究对象,重点研究冲压工艺参数对高强度钢板回弹量的影响,为高强度钢板冲压加工提供一定的指导意义。
1 分析模型建立對于U形件来说,为减少运算时间,建立基本模型如图1所示,本模型采用常用的汽车零件结构,两侧面夹角为10°,模型零件长为300mm,材料为RP784-980B,材料的主要化学成分如表1所示,其主要性能指标:屈服强度为610 MPa,抗拉强度为989MPa,延伸率或伸长率21%),根据U形件弯曲回弹的特点,采用软件计算的最大回弹值作为的变形量。
2 不同工艺参数模拟结果分析通过不同的冲压工艺参数,对模型进行模拟分析,具体分析如下:2.1 摩擦系数对回弹的影响摩擦系数对冲压零件的成形质量和回弹有一定的关联性,当摩擦系数较大时,零件在成形过程中,材料的流动就会变缓慢,从而可以减少成形零件的回弹量,但随着摩擦系数的增大,对零件表面也会造成一定的损伤,影响零件的表面质量,当摩擦系数较小时,其成形结果与之相反。
适用于冷冲压成形的超高强钢性能分析~

适用于冷冲压成形的超高强钢性能分析~车身用钢的发展趋势随着汽车市场对节能、环保、安全、舒适等要求的提高,汽车车身轻量化成为当今汽车技术发展的重要发展方向。
由于高强钢和超高强钢在减轻车身重量的同时,还能提高汽车车身的结构强度及能量吸收能力,因此高强钢和超高强钢在汽车上的应用越来越广泛。
截至目前为止,高强钢和超高强钢仍然是最经济、最有效的轻量化途径之一。
典型的超高强钢应用零件有前、后门左/右防撞杆(梁),前、后保险杠,A柱加强板,B柱加强板,C柱加强板,下边板,地板中通道及车顶加强梁等各种结构件。
高强钢有不同的定义分类方法。
⑴按屈服强度分类:将屈服强度在210~550MPa范围内的钢定义为高强钢(HSS,High Strength Steel),屈服强度在550MPa以上的钢定义为超高强钢(UHSS,Ultra High Strength Steel);⑵按抗拉强度分类:抗拉强度在340~780MPa范围内的钢定义为高强钢(HSS),抗拉强度在780MPa以上的钢定义为超高强钢(UHSS);⑶按照强化机理分类:分为传统高强钢和先进高强钢板,先进高强钢(AHSS,Advanced High Strength Steel)是指通过适当的热处理工艺控制钢的显微组织以得到高强度、高塑性;⑷按其发展历程分类:第一代、第二代和第三代先进高强钢,如图1所示。
图1 高强钢的发展和划分除了钢铁材料之外,铝合金、镁合金、工程塑料、碳纤维及其他轻质材料也加大了在汽车车身上应用研究的力度。
曾有人对2030年时车身的轻量化方案做了预测,不同的轻量化方案下对应着不同的车身用材结构,如图2所示。
不管是哪一种方案,现行车身上用量较大的软钢(抗拉强度340MPa以下)和高强钢(抗拉强度780MPa以下),都将大幅度减少,而超高强钢(抗拉强度在780MPa及以上)的用量将大幅度增加。
图2 2030年时不同轻量化目标下的车身用材结构预测超高强钢冷冲压成形面临的挑战在超高强钢产品开发上,国内外钢厂都进行了大量的工作,日本新日铁、JFE、神户制钢、韩国浦项和瑞典SSAB等钢铁公司已开发出各自的超高强钢产品并在汽车行业得到应用。
高强度钢板冲压成形回弹控制技术

李世 明 ,彭 成 允 ,关 婧 ,李 涛
( 庆理 工 大 学 ,材 料科 学 与工 程 学 院 ,重 庆 ,4 0 5 ) 重 0 0 4
摘 要 :上的使用量在 不断增加 。高 强度钢 板冷冲 压成形 中 ,回弹是不 可
t t e , t g r i p i ba k.The pa r i t od e t an e h he se l he bi ge n s rng c pe n r uc he m i m t odso prng c o r r oc s fs i ba k c ntola e pr e s c ontola e c m pe a i n e hod i c l r nd di o ns to m t n o d—sa p ng f gh sr ng h t e . u m a y ng t i i e t m i or hi t e t se 1S m r i he prncpl a a lc ton ofhot t m p ng f r i nd t a t e ti t i veop e t n a ii n, t pe nd pp i a i -sa i o m ng a he f c or of r sr c t de l m n .I dd to he pa r i t od e t t ps f r s ing c FEM i ulto a om e f c o s w hih nfue e t EM i u a i n n r uc he s e o pr ba k S m a i n nd s a t r c i l nc he F sm l to p e ii r c son.I pr v ng t c ur c fFEM i u a i a be gr al e m o i he a c a y 0 sm l ton c n e ty r duc he tm eofm ou d m a f c ur . e t i l nu a t e K e w or s H i h t e h t e ; S i ba k c nt o ; F y d : g sr ng se l prng c o r l EM i ul to sm a i n
两种先进高强度钢板冷冲压成形的数值模拟
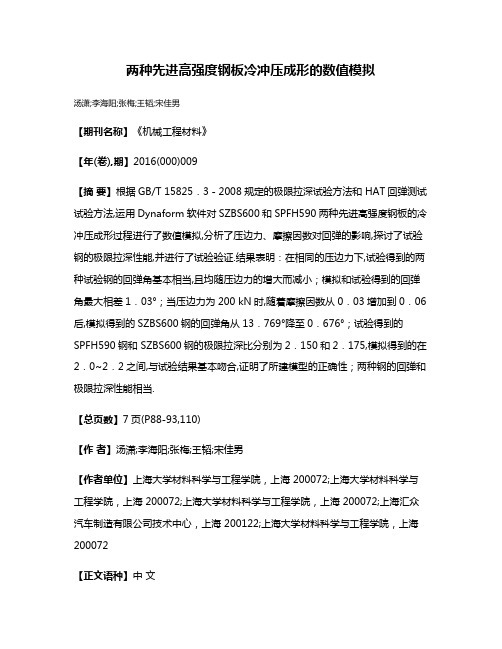
两种先进高强度钢板冷冲压成形的数值模拟汤潇;李海阳;张梅;王韬;宋佳男【期刊名称】《机械工程材料》【年(卷),期】2016(000)009【摘要】根据GB/T 15825.3-2008规定的极限拉深试验方法和 HAT回弹测试试验方法,运用Dynaform软件对SZBS600和SPFH590两种先进高强度钢板的冷冲压成形过程进行了数值模拟,分析了压边力、摩擦因数对回弹的影响,探讨了试验钢的极限拉深性能,并进行了试验验证.结果表明:在相同的压边力下,试验得到的两种试验钢的回弹角基本相当,且均随压边力的增大而减小;模拟和试验得到的回弹角最大相差1.03°;当压边力为200 kN时,随着摩擦因数从0.03增加到0.06后,模拟得到的SZBS600钢的回弹角从13.769°降至0.676°;试验得到的SPFH590钢和 SZBS600钢的极限拉深比分别为2.150和2.175,模拟得到的在2.0~2.2之间,与试验结果基本吻合,证明了所建模型的正确性;两种钢的回弹和极限拉深性能相当.【总页数】7页(P88-93,110)【作者】汤潇;李海阳;张梅;王韬;宋佳男【作者单位】上海大学材料科学与工程学院,上海 200072;上海大学材料科学与工程学院,上海 200072;上海大学材料科学与工程学院,上海 200072;上海汇众汽车制造有限公司技术中心,上海 200122;上海大学材料科学与工程学院,上海200072【正文语种】中文【中图分类】TG386.1【相关文献】1.高强度钢板梁类零件冷冲压成形技术研究 [J], 吴国峰;张云山2.高强度钢板冷冲压成形数值拟研究 [J], 谷诤巍;徐勇;程万军;单忠德;姜超3.论汽车车身的高强度钢板的冷冲压成形差异 [J], 张国峰4.22MnB5超高强度钢防撞梁的冷冲压成形数值模拟 [J], 李琦; 纪沙沙; 王章忠; 吕学鹏5.22MnB5超高强度钢防撞梁的冷冲压成形数值模拟 [J], 李琦; 纪沙沙; 王章忠; 吕学鹏因版权原因,仅展示原文概要,查看原文内容请购买。
汽车用高强钢的成形技术
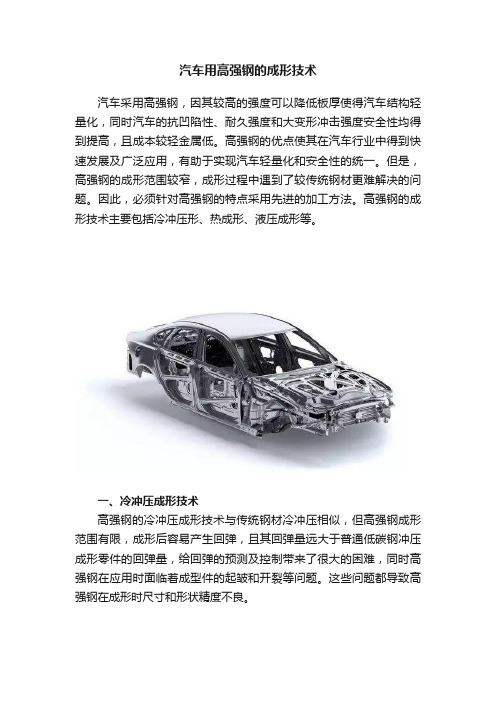
汽车用高强钢的成形技术汽车采用高强钢,因其较高的强度可以降低板厚使得汽车结构轻量化,同时汽车的抗凹陷性、耐久强度和大变形冲击强度安全性均得到提高,且成本较轻金属低。
高强钢的优点使其在汽车行业中得到快速发展及广泛应用,有助于实现汽车轻量化和安全性的统一。
但是,高强钢的成形范围较窄,成形过程中遇到了较传统钢材更难解决的问题。
因此,必须针对高强钢的特点采用先进的加工方法。
高强钢的成形技术主要包括冷冲压形、热成形、液压成形等。
一、冷冲压成形技术高强钢的冷冲压成形技术与传统钢材冷冲压相似,但高强钢成形范围有限,成形后容易产生回弹,且其回弹量远大于普通低碳钢冲压成形零件的回弹量,给回弹的预测及控制带来了很大的困难,同时高强钢在应用时面临着成型件的起皱和开裂等问题。
这些问题都导致高强钢在成形时尺寸和形状精度不良。
二、热冲压成形技术当钢强度超过1000MPa时,一些形状复杂的零件,采用常规的冷冲压工艺难以成形;即使可以采用冷冲压工艺,也有所需冲压力大、成型件易开裂、回弹大等问题,因此热成形技术应运而生。
热冲压成形技术是将硼钢钢板(初始强度为500~600MPa)加热至奥氏体化状态,快速转移到模具中高速冲压成形,在保证一定压力的情况下,制件在模具本体中以大于27℃/s的冷却速度进行淬火处理,保压淬火一段时间,零件成形的同时获得具有均匀马氏体组织。
高强钢热冲压技术将成形和强化分为2个步骤来解决高强钢强度与塑性的矛盾。
其主要优点是:变形抗力小、塑性好、成形极限高、冲压成形性好;回弹易于控制,成形零件尺寸精度高;冲压机吨位要求降低;钢材成形抗力低,模具单位压力小;成形件生产周期短等。
但热冲压技术也存在一些缺点,如设备投资大、模具设计和加工复杂、维护和保养成本高等。
三、液压成形技术液压成形技术是依靠高压液体(水或油)作为传力介质使工件成形的一种塑性加工技术。
液压成形过程中板材通过传力介质的压力作用贴合凸模或凹模成形,是一种柔性加工工艺。
基于热-力耦合和变摩擦因数的高强钢冷冲压成形性
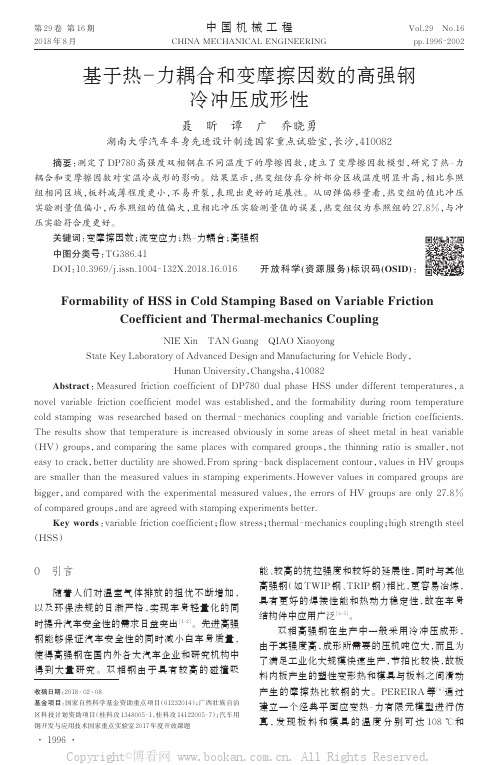
收稿日期:2018-02-08基金项目:国家自然科学基金资助重点项目(61232014);广西壮族自治区科技计划资助项目(桂科攻1348005⁃1,桂科攻14122005⁃7);汽车用钢开发与应用技术国家重点实验室2017年度开放课题0引言随着人们对温室气体排放的担忧不断增加,以及环保法规的日渐严格,实现车身轻量化的同时提升汽车安全性的需求日益突出[1⁃2]。
先进高强钢能够保证汽车安全性的同时减小白车身质量,使得高强钢在国内外各大汽车企业和研究机构中得到大量研究。
双相钢由于具有较高的碰撞吸能、较高的抗拉强度和较好的延展性,同时与其他高强钢(如TWIP 钢、TRIP 钢)相比,更容易冶炼,具有更好的焊接性能和热动力稳定性,故在车身结构件中应用广泛[3⁃5]。
双相高强钢在生产中一般采用冷冲压成形,由于其强度高,成形所需要的压机吨位大,而且为了满足工业化大规模快速生产,节拍比较快,故板料内板产生的塑性变形热和模具与板料之间滑动产生的摩擦热比软钢的大。
PEREIRA 等[6]通过建立一个经典平面应变热-力有限元模型进行仿真,发现板料和模具的温度分别可达108℃和基于热-力耦合和变摩擦因数的高强钢冷冲压成形性聂昕谭广乔晓勇湖南大学汽车车身先进设计制造国家重点试验室,长沙,410082摘要:测定了DP780高强度双相钢在不同温度下的摩擦因数,建立了变摩擦因数模型,研究了热-力耦合和变摩擦因数对室温冷成形的影响。
结果显示,热变组仿真分析部分区域温度明显升高,相比参照组相同区域,板料减薄程度更小,不易开裂,表现出更好的延展性。
从回弹偏移量看,热变组的值比冲压实验测量值偏小,而参照组的值偏大,且相比冲压实验测量值的误差,热变组仅为参照组的27.8%,与冲压实验符合度更好。
关键词:变摩擦因数;流变应力;热-力耦合;高强钢中图分类号:TG386.41DOI :10.3969/j.issn.1004⁃132X.2018.16.016开放科学(资源服务)标识码(OSID):Formability of HSS in Cold Stamping Based on Variable Friction Coefficient and Thermal -mechanics CouplingNIE XinTAN GuangQIAO XiaoyongState Key Laboratory of Advanced Design and Manufacturing for Vehicle Body ,Hunan University ,Changsha ,410082Abstract :Measured friction coefficient of DP780dual phase HSS under different temperatures ,a novel variable friction coefficient model was established ,and the formability during room temperature cold stamping was researched based on thermal ⁃mechanics coupling and variable friction coefficients.The results show that temperature is increased obviously in some areas of sheet metal in heat variable (HV )groups ,and comparing the same places with compared groups ,the thinning ratio is smaller ,not easy to crack ,better ductility are showed.From spring⁃back displacement contour ,values in HV groups are smaller than the measured values in stamping experiments.However values in compared groups are bigger ,and compared with the experimental measured values ,the errors of HV groups are only 27.8%of compared groups ,and are agreed with stamping experiments better.Key words :variable friction coefficient ;flow stress ;thermal⁃mechanics coupling ;high strength steel (HSS)第29卷第16期2018年8月中国机械工程CHINA MECHANICAL ENGINEERINGVol.29No.16pp.1996⁃2002··1996基于热-力耦合和变摩擦因数的高强钢冷冲压成形性——聂昕谭广乔晓勇181℃,这表明高强钢冷冲压产生的热量而导致的温升已经不能忽略。
- 1、下载文档前请自行甄别文档内容的完整性,平台不提供额外的编辑、内容补充、找答案等附加服务。
- 2、"仅部分预览"的文档,不可在线预览部分如存在完整性等问题,可反馈申请退款(可完整预览的文档不适用该条件!)。
- 3、如文档侵犯您的权益,请联系客服反馈,我们会尽快为您处理(人工客服工作时间:9:00-18:30)。
高强钢的冷冲压成型精益生产、绿色生态高性能润滑剂可提供一种更高性能的膜以保护金属免于断裂、压裂或被焊接到模具上。
好的润滑剂还能够减少摩擦热量,使金属流动不间断并能控制起皱或断裂。
汽车工业的迅猛发展为国民经济和社会发展发挥了重要作用。
但受能源短缺、环境污染等问题的影响,该行业发展之矛盾也日益凸显。
展望未来,该行业的发展只有建立在自然、生态、节能、安全等背景下,其发展才可持续。
在此背景下,汽车轻量化以及高强钢的应用成为了重要发展方向。
但受高强钢板材强度的提高,传统的冷冲压工艺在成型过程中容易产生破裂现象,无法满足高强度钢板的加工工艺要求。
在无法满足成型条件的情况下,目前国际上逐渐研究超高强度钢板的热冲压成形技术。
该技术是综合了成形、传热以及组织相变的一种新工艺,主要是利用高温奥氏体状态下,板料的塑性增加,屈服强度降低的特点,通过模具进行成形的工艺。
但是热成型需要对工艺条件、金属相变、CAE分析技术进行深入研究,目前该技术被国外厂商垄断,国内发展缓慢。
据调查统计,部分汽车品牌高强钢的应用不断扩大,有些车型的车身框架高强度钢的应用已达90%。
一、高强钢特点及成型问题分析根据美国钢铁学院能量部的研究,即使高强度钢降低部分数值其拉伸还是要比传统的冷板困难得多。
高强钢的延展率只有普通钢材的一半(如下图1)同时,当材料被冲压成形时,会变硬,不同的钢材,变硬的程度不同(如下图2)。
一般高强度低合金钢只略有20MPa增加,不到10%。
注意:双相钢的屈服强度有140MPa增加,增加了40%多!金属在成形过程中,会变得完全不同,完全不像冲压加工开始之前。
这些钢材在受力后,屈服强度增加很多。
材料较高的屈服应力加上加工硬化,等于流动应力的大大增加。
因此,开裂、回弹、起皱、工件尺寸、模具磨损、微焊接磨损(如下图3)等成为了高强钢成型过程中的问题焦点。
高强钢屈服强度普通高强钢HSS 210Mpa30KSI比低碳钢含更多的碳和锰高强度低合金钢HSLA 280-550Mpa40-79KSI细晶铁素体与碳和/或者氮析出物,含钛、钒,冲压时,板材屈服强度-YS,仅增加-伊苏只增加20Mpa(3KSI)热处理硬化钢180-280Mpa26-40KSI在冲压加工成形过程中被硬化或者经过烤箱170F(20-30分钟),屈服强度提高70Mpa(10KSI)双相钢350-600Mpa50-86KSI软铁素与岛状马氏体。
烘烤硬化-加工时,屈服强度可以增加140Mpa(20KSI)相变诱发塑性钢TRIP 400-800Mpa57-114KSI铁素体和马氏体-同样有贝氏体和残余奥氏体。
合金使点焊更具挑战性。
拉伸翻边高强度钢About 590Mpa84KSI应用时需要较高的剪切边缘延伸度。
铁素体、贝氏体和残余奥氏体。
复相钢350-600Mpa50-86KSI有精细显微结构的铁素体,较高比例的马氏体和贝氏体。
图2基于高强钢的特点和特性,如果不能改变金属流动和减少摩擦,那么高强度钢(HSS)的开裂和质地不均性都可能引起部件报废率的上升。
这种材料所具有的高千磅力每平方英寸(KSI)(测量屈变力的单位)、增强的回弹、加工硬化的倾向以及在升高的成型温度下运行对于模具来说都是一个挑战。
二、高性能润滑技术对高强钢冷冲压成型的重大意义润滑影响成型性这是不争的事实。
因此,高性能润滑剂可提供一种更高性能的膜以保护金属免于断裂、压裂或被焊接到模具上。
好的润滑剂还能够减少摩擦热量,使金属流动不间断并能控制起皱或断裂。
针对这一问题,美国IRMCO公司作为世界知名从事润滑研究制造的专业公司,自三十年前就已成功研发的新型水基润滑技术解决了高强钢的成型问题。
下面,结合多年来的研究和使用从润滑角度并结合该润滑技术的特点谈一下看法和意见。
如下:其一,严酷条件下的润滑保障。
1、由于高强钢的屈服力大,要屈服它比一般板材需要更多的能量,这种能量除了变形以外,很大程度上是板材与模具间推撞(摩擦)。
因此,随着金属在冲压模具中变形温度会不断升高,油基润滑油都会变薄,有些情况下会达到闪点或者烧着(冒烟),润滑失效。
而IRMCO高分子聚合物极温润滑剂中含有抗极压物并具有“热寻性”而且会粘到金属上,随着温度的升高在模具和板材表面形成一个坚韧的保护屏障,从而降低摩擦和温度,以帮助工件更好的延展,以此来控制摩擦和金属流动;同时保护金属不会过热,发黑而拉裂和粘接。
(如下图4)同时,根据实际试验中的问题,我们在实验室里复制现场试验的结果。
不同配方的油基和常规(肥皂)为基础的合成润滑剂,在高强钢上不能正常工作。
废品率和模具磨损(擦伤)失控。
(如下图5)双相钢DP600-UHSS超高强钢试验报告美国绿叶技术实验室对IRMCO产品和汽车行业通过认证的拉伸油以及合成润滑剂,在美国DP780超高强度钢上进行了成型对比实验。
采用了俄亥俄州立大学的茵特拉根(Interlaken)拉伸成型测试法。
这种方法被证实用于测试实际结果非常准确。
IRMCO达到的数值是145 比汽车行业通过认证的拉伸油的115和合成润滑剂的110 超过了25%。
数值越大说明成型能力越好(如下图6)。
2、由于冲压过程中会产生温度,同时由于油的热容量比较大,热扩散比较差。
而IRMCO水基润滑剂因温度产生形成水蒸气带走热量,不但有效的降低了温度,保护了模具,而且因温度所产生的微焊接磨损将得到有效的控制。
同时还可以提高冲次。
其二、工具涂层的性能与润滑剂质量紧密联系。
传统的物理气相沉淀(PVD)和化学气相沉淀涂层(CVD)外部需要润滑发挥最大性能。
IRMCO指出:“热扩散工艺可以减少摩擦磨损的问题。
通过热扩散所产生的碳化钒可以形成耐久性、坚硬的表面,在苛刻的成形和冲压模面时,会极大的提高工具的使用寿命。
如果使用的润滑剂无法承受高温、磨损和先进高强钢的加工硬化性,价值会大幅降低。
因此,使用可满足高强钢需求的润滑剂,是达到涂层使用寿命最大化的关键。
”根据IRMCO技术的先进行及多年的应用经验,高强钢冲压模具无需花费高昂的涂层费用,就可以满足生产需要,并可以延长模具寿命。
从(右图7)可以看出IRMCO润滑技术对模具的保护作用。
冲压三千个工件后,工件表面质量及模具表面得到明显的改观(表面划痕明显减少)。
其三、高性能润滑可以使工件质量更加稳定。
模具间隙及模具的几何设计等是实现工件尺寸精度的重要内容。
因此,这直接关系到对金属材料和润滑剂技术要求。
如果间隙越小、越紧摩擦力越大,对润滑剂的要求也越高,但工件的成型精度也相对越高。
由于IRMCO可以较好的控制摩擦和金属流动,所以可以保证工件质量更加稳定。
三、IRMCO在部分高强钢部件上的应用某大型底盘件企业生产的控制臂(NMS摇臂),板材材质FB780,板材厚度4mm,七工位级进冲压模具,采用IRMCO测试在保证工件质量的同时,同等环境条件下与油基润滑剂比较,模具工作温度下降10-20℃。
在此,需要重点说明的是温度降低意味着摩擦力的减小,这不仅可以保护模具,而且可以提高冲次。
工件图片如下:四、建立在IRMCO 应用下的新的生产工艺流程IRMCO 高性能环保润滑剂不仅可以解决高强钢、重冲、深拉伸等的成型问题,而且可以减少润滑油50%-75%的用量,更重要的是它可以对目前冲压行业的生产工艺带来重大改善和优化,以减少更多能源、资源的消耗和对环境的污染。
优化后的工艺如下:磷化处理一遍常温水洗 冲压成型 焊点焊接面漆喷漆1、冲压成型:IRMCO产品和渗碳模具兼容,所含聚合物的热寻性在冲压温度升高时强力保证润滑膜层。
降低了模具的工作温度,延长了模具寿命,同时可有效提高冲次和工件表面质量。
2、焊点焊接:不需任何处理就可以直接进行焊接,不但不会产生虚焊、假焊,而且不会产生有毒油烟和刺激异味,同时可以减少至少25%的焊接烟雾,不仅极大提高了工作效率的,而且保证了工人的安全和工件洁净并利于搬运,节省手套、棉纱等用量。
3、常温水洗:可以使用26.7~43℃清水进行清洗,大幅度降低能耗;可以使清洁池内沉淀物减少75%和75%的清洗用水;可直接排放,并达到对鱼类无害的标准,污水排放量的减少使处理费用降低。
4、磷化处理:由于易于清洗,可以使工件达到高清洁度,全面提高磷化效果。
5、电泳涂装:IRMCO 产品和电泳漆兼容,同时工件高清洁度增强了电泳涂装的质量。
6、面漆喷漆:IRMCO 产品可以与电烤漆和粉漆完全兼容。
工件的高清洁度提高了喷漆附着力,漆可以喷得更薄,同时喷漆表面无气孔、流淌现象。
六、结束语时至今日,金属成型开始面临新的变化,同时也面临着诸多的问题,美国IRMCO三十年来一直致力于高性能环保润滑剂的开发与研究,在这三十年中她不仅解决了重载、深拉伸以及高强钢等板材工件的成型质量和模具寿命问题,更重要的是为环保以及减少更多资源的消耗做出了重大贡献。
新的调查发现,金属成型润滑剂只占生产总成本的约0.5%,但其直接关联80项费用和影响总成本70%的费用高低,可以消除因用油所带来的至少10%的生产成本的增加,看似一个在生产大天枰上无法称重的物质却决定着整个生产价值链。
无论是工件的成型质量及废品、模具寿命、生产效能、大量的脱脂、清洗以及表面处理所需的能耗、还有生产环境和排污问题等无不与传统油基润滑剂的使用有着直接的关系。
“精益生产、绿色生态”是未来汽车制造的发展趋势。
IRMCO高性能无油润滑技术正是这一进程中不可或缺的重要组成部分,它不仅可以识别生产过程中的浪费,是生产过程的优化者,同时它又不止步于生产过程本身,还有社会效益,并符合公共利益。