改装车生产过程检验记录表
燃气汽车改装安装及检查记录表

燃气汽车改装安装及检查记录表编号:车牌号码车驾号发动机号充装介质天然气车辆厂牌型号使用区域车辆产权单位使用单位使用单位地址使用联系人联系电话安装项目技术要求安装记录检查结果1、气瓶及文件检查1、气瓶外观应完好无损2、气瓶应具备:合格证、质量证明书、瓶阀合格证3、应具有安装设计图样气瓶外观:良好气瓶编号:气瓶型号:气瓶重量:Kg气瓶容积:L充装介质:天然气工作压力;20 Mpa制造单位:制造日期:年月监检证书编号:合格证编号:质量证明书编号:瓶阀合格证编号:安装设计图号:2、支架安装气瓶安装紧固后在上下左右前后六个方向上应能承受8倍于充满额定工作压力的天然气的气瓶重力的静力,且气瓶与固定座最大位移不超过13mm上:6500N下6500N左:6500N右:6500N前:6500N后:6500N最大位移:mm3、气瓶安装气瓶集成阀与车辆外轮廓边缘的距离应不小于200mm气瓶与排气管的距离大于200mm橡胶垫厚度不小于2mm气瓶集成阀与车辆外轮廓边缘的距离:mm气瓶与排气管的距离mm橡胶垫厚度:mm4、减压阀调节器安装减压阀调节器应安装在震动较小,尽量靠近发动机的位置与发动机间应采用柔性连接5、管路安装刚性高压管路及接头与发动机排气管和传动轴的距离应不小于75mm,固定卡的间距应不大于600mm。
柔性高压软管应使用有弹性的固定卡固定在汽车基础件上,固定卡间距不大于300mm刚性高压管路及接头与发动机排气管和传动轴的距离:mm固定卡间距:mm6、充气阀安装充气阀与高压管线连接应可靠无泄露7、电路安装仿真器(电脑板)7根线,应按照说明书规定,正确连接8、管路气密性试验试验压力为气瓶公称工作压力保压时间不少于5min试验压力:Mpa保压时间:min结果:9、置换处理抽真空、真空度为小于-0.086Mpa。
氮气置换含氧量应小于3%真空度≤Mpa含氧量<10、检漏试验1、进行3-5Mpa天然气低压检漏检验、无泄露2、进行20 Mpa天然气高压捡漏检验、5 min内不得有气体渗漏现象1、试验压力:Mpa结果:2、试验压力:Mpa保压时间:min结果:安装人员日期年月日检查人员日期年月日备注:监检项为安装项目第1、2、3、10项质量保证人:年月日监检员:年月日安装单位(章)年月日。
生产过程检验记录表
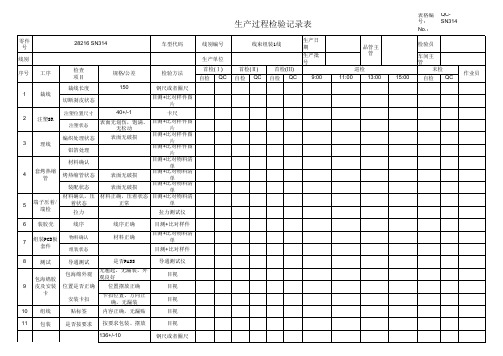
零件 号
28216 SN314
车型代码
线别编号
线别
生产单位
序号 工序
检查 项目
规格/公差
检验方法
首检(Ⅰ) 自检 QC
裁线长度
1
裁线
切断剥皮状态
150
钢尺或者圈尺
目测+比对样件图 片
注塑位置尺寸
40+/-1
卡尺
2 注塑SR
注塑状态
表面无划伤,饱满、 目测+比对样件图
无松动
片
编织处理状态
产品无毛边,变形等 不良
目视+比对样件
不
改
象
合 格
善 状
现
况
Rev 1.0
3
理线
铝箔处理
表面无破损
目测+比对样件图 片
目测+比对样件图 片
材料确认
目测+比对物料清 单
4
套烤热缩 管
烤热缩管状态
表面无破损
目测+比对物料清 单
装配状态
表面无破损
目测+比对物料清 单
材料确认,压 材料正确,压着状态 目测+比对物料清
5
端子压着/ 端检
着状态 拉力
正常
单 拉力测试仪
线束组装1线
首检(Ⅱ)
首检(Ⅲ)
自检 QC 自检 QC
生产日 期 生产批 号
9:00
6 装胶壳
7
组装PCB板 套件
线序 物料确认 组装状态
线序正确 材料正确
目测+比对样件
目测+比对物料清 单
目测+比对样件
车辆检验记录表讲解
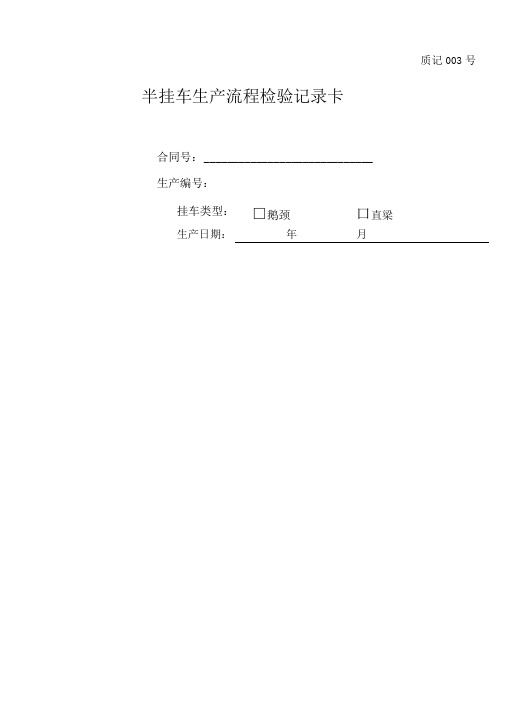
焊接
参数
焊接电流:180-210A
4
推力:
5
弧压:
6
焊缝高度:3-4mm
7
焊缝长度:20-30mm
8
焊缝间距:200-300mm
9
组对间隙小于2mm
10
对称度
腹板相对于翼板对称度1.5
11
垂直度
腹板与翼板垂直度1
12
平面度
前后翼板平面度1
14
鹅颈高度
差
两鹅颈咼度差w1
14
翼板使用
上翼板吃刀面(切
割面)向上
互检
2
压模涂油
涂抹均匀
压孔方向
左右腹板各一,不得相同
压孔数量
不得漏落
工序
序号
检验项目
技术要求
操作者
签字
班长签
字
质检员抽
检签字
判定结
果
备注
纵梁
组焊
工序
1
来料
检验
板材及尺寸符合派工单要求、无残
余氧化铁
上翼
下翼
腹板
宽
厚
翼板厂家、批号
翼板厚度
2
工装
检查
工装定位面干净,无磕碰划伤,油
气缸活动自如
穿刺点
焊补
焊补翼板的穿刺点,并磨平
<7mm
加固板厚度
1
牵引
牵引板厚度:轻型、标准型:6mm;80
吨:8mm;100吨以上:10mm
可测量牵引销
轴线到左右边
梁的距离
牵引销轴线对车架纵向中心平面对称度1
左
右
侧位灯安装板
最前端侧位灯到车辆最前端W2900;
过程检验记录表(自卸车)

5、焊接部分不得有飞溅、焊瘤、虚焊、漏焊以及气
孔等焊接缺陷;
2
底板部分
1、总成焊接不得有飞溅、焊瘤、虚焊、漏焊以及气孔等焊接缺陷,焊缝高度不小于5mm;
2、底板的整体平面度控制在5mm以内;
3、底架中心对角线之差控制在5mm以内;
3
侧板部分
1、总成焊接不得有飞溅、焊瘤、虚焊、漏焊以及气孔等焊接缺陷,焊缝高度不小于4mm;
2、焊接两对角线之差≤3mm,平面度≤2mm;
3、油缸安装孔径与螺栓间隙≤2mm;
6
合厢
1、合厢前必须进行底板及侧板校正,平面度≤5mm
2、厢内控尺寸必须与图纸一致,长宽高误差+-3mm
3、总成对角线之差≤5mm;平面度控制在5mm以内;
4、总成焊接不得有飞溅、焊瘤、虚焊、漏焊以及气孔等焊接缺陷,焊缝高度不小于5mm;
7
副梁
1、总录表(自卸车)
QR-8.2-06-A/0检验员:交验人:生产日期:序号:
产品名称
产品型号
产品编号
序
号
检验项目
技术要求
检验记录
结论
备注
1
底架部分
1、总成焊接不得有飞溅、焊瘤、虚焊、漏焊以及气孔等焊接缺陷,焊缝高度不小于5mm;
2、焊接后两对角线之差≤5mm,纵梁的直线度和平面度控制在3mm以内;
3、侧板上下竖筋及中横筋直线度≤3mm,主板与付板间隙≤4mm;
4
后板部分
1、总成焊接不得有飞溅、焊瘤、虚焊、漏焊以及气孔等焊接缺陷,焊缝高度不小于5mm;
2、焊接两对角线之差≤5mm,平面度≤3mm;
5
前板部分
1、总成焊接不得有飞溅、焊瘤、虚焊、漏焊以及气孔等焊接缺陷,焊缝高度不小于5mm;
过程审核检查记录表
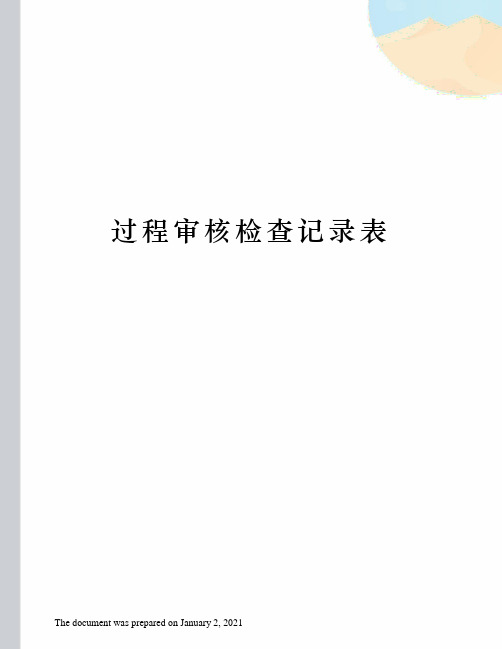
-仓库管理系统
-FIFO 先进先出 / 按照批次投入使用
-有序和清洁
-气候条件
-防损防污防锈
-标识可追溯性/ 检验状态/ 加工工序/ 使用状态
-确保防止混放和混用
-隔离库设置并使用
1.9员工素质是否满足了相应的岗位要求
- 产品/技术规范/特殊的顾客要求
-模块中的零部件的产品特性和加工过程的专业知识
- 工装模具/设备/机器的保养和维修状态包括有计划的维修
2.2.2在批量生产中使用的测量和检验设备能否有效地监控质量要求-可靠性试验、功能试验和耐腐蚀试验
-测量精度/检测设备能力
-数据采集和可评价性
-检测设备的校准证明
2.2.3生产工位和检验工位是否符合要求
-人机工程学
-照明
-有序清洁
-环境保护
-工作环境/零件搬运
-数据采集和可评价性
-检测设备的校准证明
2.2.3生产工位和检验工位是否符合要求
-人机工程学
-照明
-有序清洁
-环境保护
-工作环境/零件搬运
-安全生产
2.2.4在生产文件和检验文件中是否标出全部的重要事项并得到遵守
- 过程参数如压力、温度、时间、速度
-机器/工装模具/辅助器具的数据
-检验规范重要的特性、检验器具、方法、检验频次
-安全生产
2.2.4在生产文件和检验文件中是否标出全部的重要事项并得到遵守
- 过程参数如压力、温度、时间、速度
-机器/工装模具/辅助器具的数据
-检验规范重要的特性、检验器具、方法、检验频次
-过程控制图中的控制限
-机器能力和过程能力的证明
-设备操作指导
-作业指导书
汽车维修过程和检验记录单

汽车维修过程和检验记录单车辆信息:品牌:__________型号:__________车牌号:__________车主姓名:__________维修时间:__________维修过程记录:日期:____________维修人员:____________维修项目:____________维修描述:____________维修费用:____________检验记录单:车辆信息:品牌:__________型号:__________车牌号:__________车主姓名:__________维修时间:__________检验项目:1.车身外观检查:a)前保险杠:__________b)后保险杠:__________c)左前门:__________d)右前门:__________e)左后门:__________f)右后门:__________g)引擎盖:__________h)后备箱:__________i)车顶:__________j)车窗:__________2.发动机检查:a)点火系统:__________b)隔音罩:__________c)冷却系统:__________d)燃油系统:__________e)排气系统:__________f)电气系统:__________3.刹车系统检查:a)刹车片:__________b)刹车盘:__________c)刹车液:__________d)刹车管路:__________e)刹车泵:__________4.悬挂系统检查:a)前悬挂:__________b)后悬挂:__________c)减震器:__________d)悬挂弹簧:__________e)轮胎:__________5.转向系统检查:a)转向器:__________b)轮轴:__________c)轮毂:__________d)轮胎:__________维修结果:1.维修项目:__________2.维修描述:__________3.维修费用:__________维修过程和检验记录单用于记录整个汽车维修过程和检验结果,通过这份记录单,可以清楚地了解到每个维修项目的细节,包括车辆的维修项目、维修描述和维修费用等信息。
汽车关键、特殊工序检验记录表(调试检测)

汽车有限公
关键、特殊工序检验记录表
车型:生产编号:日期:
工序名称检验要求
检验
方式
检查结果备注
调试检测1、前轴制动力:前轴制动力与轴荷的百分
比≥60%, 制动力差≤20%;
2、后轴制动力:当后轴制动力与轴荷的百
分比≥60%时, 制动力差≤24%;当后轴制
动力与轴荷的百分比<60%,制动力差≤
8%;
3、驻车制动力:驻车制动力总和≥该车在
测试状态下整车重量的20%;
4、侧滑量:-5~+5(m/km);
5、前照灯:前照灯远光光束的发光强度≥
18000(cd);前照灯远光光束位置水平方
向偏移量:a、左灯:-17~35(cm/10m)
b、右灯:-35~35(cm/10m);前照灯近光
光束位置水平方向偏移量:-17~35
(cm/10m);
6、排气污染物排放限值:光吸收数≤2.5
(m-1),碳氢化合物(HC)≤1200(ppm),
一氧化碳(CO)CO≤4.0(%)
配置
表、作
业指导
书、目
测、压
力表、
扳手、
手感、
皂液
是否合格:
□
□
□
□
□
□
注:合格打√;不合格打×。
质检员:编号:PG-QR-015-04 版本:A.0。
生产车间过程首检巡检记录表

N/A
1次/2H 目测
目测
一个流确认 装配现场是否按一个流作业,有无产品堆积现象
目测
不合格标识 不良品是否放置在不良品箱(盒)内,不良现象是否标识清楚
目测
NO 标准要求
换线管理 在换线前产线上物料是否清理干净,无物料遗留(含不良品)产线
新品状态确认
量(试)产品有无(临时)生产许可证;临时生产许可证上涉及的 问题点责任部门有无按时间节点完成
外观检查
PVC皮管上的批号正确,印字清晰(记录批次号) 面罩安装方向是否正确,无左右反装,上下反装现象
灯体内无杂物(橡胶碎屑、镀膜磨损物、灯壳飞边等)
检验频率
首检
巡检
检查
首检记录
巡检检查结果与判定
方式 检验结果及相关数据 判定 1.巡检 2.巡检 3.巡检 4.巡检
1件
3pcs/1次 /2H
塞尺
1件
用专用工装封闭灯头部位将灯浸入水中对灯内加压05mpa观看密封部位是否漏水外观整体性是否符合客户标准比对样品胶槽一周有无影响外观的溢胶必要时封样5成品检验外观检查pvc皮管上的批号正确印字清楚记录批次号面罩安装方向是否正确无左右反装上下反装现象灯体内无杂物橡胶碎屑镀膜磨损物灯壳飞边等1件3pcs1次2h1件气密验证1pcs调机气密机胶时气压源目测目测目测目测目测成品外观fqc089a0序号67检验频率项目检验类别主要检验要求及方法首检1件
涂胶重量 气密验证 成品外观
涂胶重量符合标准要求(记录在热熔胶喷涂重量管理表)
封闭式灯具:取标准样件(一只漏气,一只OK)检查气密机工作是否 正常 带漏水孔的灯具:用专用工装封闭灯头部位,将灯浸入水中,对灯 内加压0.5MPa,观察密封部位是否漏水
改装车生产过程检验记录表
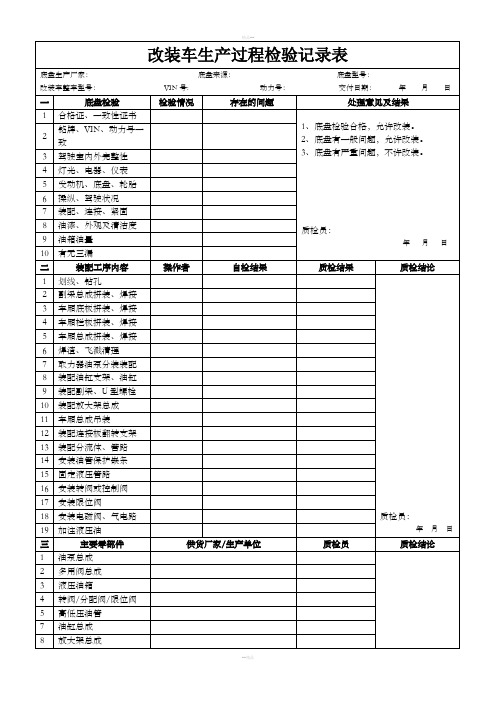
整车外观处理
六
整车性能检验
存在问题
处理意见及结果
质检结论
1
负载 T
质检员:
年 月 日
2
最大举升角度·
3
保压 min
4
自降量 ·`
5
车厢上升时间 S
6
车厢下降时间 s
7
锁启机构试验
8
外廓尺寸 mm
七
最终完善
操作者
存在问题
确认及处理意见
1
整车调试
质检员: 年 月 日
2
油漆完善
3
铆铭牌
4
整车验收
八
终检存在问题
改装车生产过程检验记录表
底盘生产厂家: 底盘来源: 底盘型号:
改装车整车型号: VIN号: 动力号: 交付日期: 年 月 日
一
底盘检验
检验情况
存在的问题
处理意见及结果
1
合格证、一致性证书
1、底盘检验合格,允许改装。
2、底盘有一般问题,允许改装。
3、底盘有严重问题,不许改装。
质检员:
年 月 日
2
铭牌、VIN、动力号一致
3
驾驶室内外完整性
4
灯光、电器、仪表
5
发动机、底盘、轮胎
6
操纵、驾驶状况
7
装配、连接、紧固
8
油漆、外观及清洁度
9
油箱油量
10
有无三漏
二
装配工序内容
操作者
自检结果
质检结果
质检结论
1
划线、钻孔
质检员:
年 月 日
2
副梁总成拼装、焊接
3
车厢底板拼装、焊接
整车装配调整过程控制随车质量记录单

01漏装 02位置装错 03扭紧力矩不够 05松动 07 不平齐、不平整 08磨碰干涉 10定位不准 11扭曲、歪斜、变形 12管路不顺或打折 13装配磕碰、划伤 14润滑油、脂加注量多或少 17怠速高或低 23渗漏 24间隙不均大或小 30粘贴不牢或脱落32装配不牢固不可靠 33未锁紧或锁止不可靠 34发卡或不灵活 35异响 36发动机工作异常 41抖动 42失效 43运动干涉 45 操纵功能不良、失效 54档位不清晰 55性能、功能不良 56机油压力不正常 61温度异常 67接触不良 71指示灯不亮 73零部件尺寸超差 76角度不合适 77龟裂、老化 87问题未排除 91调整不当 92不密封 94示值不准 95气压不正常 101漏紧 114防护不当序号检查调整项目缺陷类型代码返工验证426 平衡轴各密封部位密封良好,不得有渗漏现象。
23 32 73 87427 A、发动机各密封部位无渗漏、变速箱、中、后桥各密封部位无渗漏08 20 2332 73 87 101B、检查变速箱、传动轴、驱动桥安装是否牢固、各密封部位无渗漏428 各润滑脂油嘴安装到位、润滑脂加注量合格05 13 15429 A、变速箱操纵杆万向节叉销锁片应可靠锁止,调节杆锁紧螺母必须锁紧05 08 1333 73 87B、防尘罩无损伤、定位销不松动430 A、变速箱气操纵灵活、可靠、不发卡、档位清晰32 33 34 4554 77 87B、操控电磁阀管线连接正确可靠、防尘罩完好,无龟裂、老化431 A、驾驶室就位后,后挡泥板上气管接口与进气道吻合无明显缝隙、偏歪现象。
08 10 1124 30 87 91B、进气道内密封垫安装可靠432 A、空滤器至发动机进气管与其它部位保证有足够的间隙,不碰磨08 24 8791 101 114B、空滤器支架及支架安装牢靠,管线连接正确,进气道连接正确,密封良好433 A、各座椅调节手柄应操作自如,并能实现其应有的功能要求33 34 4255 87B、安全带安装牢靠,锁止功能有效434 玻璃能够有效推拉、关闭,无发卡、发紧现象、密封良好32 34 42 87 435 后挂衣架及遮阳帘安装位置正确、牢靠,以手感确认牢固性02 20 32436 驾驶室内底板垫应平整无翘曲、皱折、露底等,地板胶垫在左、右门处应压入门口的卡槽内02 07 1120 87441 A、发动机运行平稳无异响游车,机油压力保持正常,最高转速符合发动机最高转速要求,潍柴发动机2480+50rmp,其它车型参数参照调试工艺中要求17 3536 4156 87B、发动机怠速平稳,潍柴要求最低稳定转速在600±50rmp,其它车型参数参照调试工艺中要求442 A、气压低于0.6Mpa时,报警器连续蜂鸣,气压达到0.6Mpa时报警器停止鸣叫。
改装车检查单

外观焊接部位牢固,焊实,无虚焊,漏焊,无夹杂,焊疤表面打磨平整、光滑
总装检查
5.2
钢制零件进行防锈处理
总装检查
5.3
整车喷漆无明显修补痕迹,无漏喷
总装检查
5.4
整车防雨密封
总装检查
6
整车性能要求
6.1
整车通用部分技术参数满足东风“猛士”EQ2050基型车技术要求
总装检查
7
随车工具文件
7.1
随车文件包含产品检验记录单、随车工具清单、使用手册
取消地板固定环及安装孔
车身检查
2.12
腰线以下选用C24全包内饰,腰线以上后部到前圆钢管处截止。配备地垫。
车身检查
2.13
提供安装帘的安装位置标示。
车身检查
2.14
用新结构张紧带总成
内饰检查
2.15
后橡胶垫、侧缓冲垫块用新改进材料及结构
总装检查
2.16
后排座椅取消头枕,增加两点式安全带安装孔
2.16
车身检查
2.6
取消后箱档板支架及后箱档板、后杂货箱,电压变换由后排座椅处移到副驾座椅下,铰链支架台阶处增加挡板
车身检测
2.7
后保险杠左牵引钩采用带限位功能
总装检查
2.8
YY40后置备胎架结构,增加备胎架警告说明牌
总装检查
2.9
采用振序改进后左右前地垫,
内饰检查
2.10
地板优化改进排水孔
车身检查
2.11
3.5
顶盖中间最高点到中后地板凸平面距离982±3mm
车身检查
3.6
轮罩上表面到流水槽上表面高度455±1mm
车身检查
3.7
(完整版)车辆验收记录表

(完整版)车辆验收记录表车辆验收记录表
车辆信息
- 车辆型号:
- 车牌号码:
- VIN码:
- 车辆颜色:
- 发动机号码:
验收时间
- 验收日期:
- 验收人员:
验收项目
1. 车身外观
- 车身漆面:划痕/破损/褪色/起泡- 玻璃:裂纹/破损
- 车灯/车标:损坏/灯泡亮度
- 车窗:打开/关闭顺畅
- 车门/行李箱:
- 异常噪音
- 关闭状态:松动/不合适
- 开启状态:无异常/松动/顺畅
- 刹车灯/转向灯/示宽灯:正常工作
2. 内饰
- 方向盘:松动/异常噪音
- 座椅:
- 松动/异常噪音
- 调节功能:正常工作
- 功能面板:
- 空调控制:正常工作
- 音响:正常工作
- 车载导航:正常工作
- 玻璃:清洁无划痕/脱离
- 操作按钮:正常工作
3. 动力系统
- 发动机:启动/熄火顺畅
- 怠速/加速:正常工作
- 涡轮增压:正常工作
- 排放:无异常/异常噪音
4. 车辆悬挂
- 悬挂系统:
- 正常高度
- 异常噪音
- 异常震动
- 前后减震器:无漏油/异常噪音
5. 刹车系统
- 刹车踏板:正常行程
- 刹车片/刹车盘:磨损程度
- 刹车油:液位
6. 轮胎检查
- 轮胎胎压:正常
- 轮胎纹路:磨损程度- 轮胎裂纹/鼓包:有无
7. 电气系统
- 电瓶:电量
- 灯光:正常工作
- 仪表板:正常显示
- 各种开关:正常工作备注
{备注内容}。
汽车(整车和汽车底盘)工厂检查记录

设备校准:符合不符合检验实施:符合不符合
2)转向系统安装
工艺文件:
人员操作:符合要求不符合要求
检验方式:自检互检抽<巡)检
记录:符合不符合设备校准:符合不符合
3)车轮安装
工艺文件:
车轮动平衡:符合不符合
检验方式:自检互检抽<巡)检
记录:符合不符合设备校准:符合不符合
车速检验台
声级计
漆膜测厚仪
轮胎气压表
扭力扳手<转向系统,车轮)
文件:操作规程:符合不符合运行检查:符合不符合
自行校准规程:符合不符合
校准/检定记录:符合不符合运行检查记录:符合不符合
人员技能/操作:符合基本符合不符合
填写说明:
1.在内打“×”进行选择;不适用写“N.A”.
2.将现场指定实验所选产品地CCC证书复印,附在工厂检查报告4.5条“现场指定实验”后.
设备操作规程符合不符合设备保养程序符合不符合
设备监控记录有没有
夹具结构和精度合格不合格
焊点/焊缝尺寸<含间距)合格不合格
焊点/焊缝外观<均匀、无焊穿、裂缝、夹渣、气泡和虚焊)合格不合格
设备:;型号:;
作业文件号:
电流
电压
速度
冷却温度
控制要求
实测结果
检验方式:自检互检抽<巡)检
检验标准:符合不符合检验文件:符合不符合
4)制动系统
工艺文件:制动液型号:
检泄露:有无排空气:抽真空人工排气
加注设备:定量加注机人工加注符合不符合
人员操作:符合不符合
汽车工厂检查记录表
<整车和汽车底盘)
发布日期:2004/04/08
微车改装生产检验流程卡_2016

新能源微车改装生产检验过程流程卡2870C3315-W车型号:底盘号:VIN码:订单号:电机号:交付日期:一底盘检验检验情况处理意见及结果1 驾驶室及车身2 底盘合格标识3 底盘外观检验员:日期:20 年月日二焊装工序(内容)自检结果操作者专检结果专检结论1 车厢尺寸(长×宽×高)2 底板拼焊3 厢体螺栓焊接4 侧板与顶板拼装5 后门框焊装检验员:日期:20 年月日三装配工序(内容)自检结果操作者专检结果专检结论1 装配紧固螺栓:M142 尾门板制作、安装3 安装锁具4 安装侧围裙5 安装后围裙扭矩按照以下要点执行:M14 螺栓扭矩为135-200N.m;检验员:日期:20 年月日四主要零部件供货厂家主要零部件供货厂家1 后门总成 3 厢内照明灯2 反光标识 4 后尾灯五装涂工序(内容)操作者自检结果专检结果专检结论1 打磨、抛光2 整车刮补腻子3 涂防水胶4 厢内外喷漆5 粘贴反光标识6 喷涂参数7 安装后尾灯、牌照灯8 安装厢内照明灯检验员:日期:20 年月日六整车性能检验存在的问题处理意见及结果1 淋雨试验2 车厢内部尺寸3 整车外廓尺寸检验员:日期:20 年月日七最终完善操作者存在的问题处理意见及结果1 验收整车2 打印铭牌3 铆接铭牌4 打车架VIN码打码员:检验员:日期:20 年月日八终检存在的问题返工返修质量判定总质量:Kg 九检查员:20 年月日合格判定:□合格□不合格说明:1、操作工生产完毕且自检合格后,方可在“操作者”一栏签名;2、检查员专检确认合格后,或返工返修检验确认合格后,方可在“专检结论”一栏打“√”表示合格;3、本卡一车一张,不得多填、漏填、错填。
本卡必须严格按照规定发放、回收,并妥善保管。
- 1、下载文档前请自行甄别文档内容的完整性,平台不提供额外的编辑、内容补充、找答案等附加服务。
- 2、"仅部分预览"的文档,不可在线预览部分如存在完整性等问题,可反馈申请退款(可完整预览的文档不适用该条件!)。
- 3、如文档侵犯您的权益,请联系客服反馈,我们会尽快为您处理(人工客服工作时间:9:00-18:30)。
质检结论
1
负载T
质检员:
年月日
2
最大举升角度·
3
保压min
4
自降量·`
5
车厢上升时间S
6
车厢下降时间s
7
锁启机构试验
8
外廓尺寸mm
七
最终完善
操作者
存在问题
确认及处理意见
1
整车调试
质检员:年月日
2
油漆完善
3
铆铭牌
4
整车验收
八
终检存在问题
返工返修
质量判定
质检员:年月日
九
终检结论
质检员:年月日
3
液压油箱
4
转阀/分配阀/限位阀
5
高低压油管
7
油缸总成
8
放大架总成
9
连接板/翻转支架
10
“U”型螺栓
11
备胎架/锁勾总成
13
油泵、吊架、传动轴
四
装配工艺内容
操作者
自检结果
质检结果
质检结论
1
车厢尺寸:(长Х宽Х高)ХХ(+)
质检员:
年月日
2
驾驶室操作
3
车厢调整
4
翻转机构
5
锁启机构
6
导向立柱(导架)
7
连接板
8
装配油缸支架、油缸
9
装配副梁、U型螺栓
10
装配放大架总成
11
车厢总成吊装
12
装配连接板翻转支架
13
装配分流体、管路
14
安装油管保护嵌条
15
固定液压管路
16
安装转阀或控制阀
17
安装限位阀
18
安装电磁阀、气电路
19
加注液压油
三
主要零部件
供货厂家/生产单位
质检员
质检结论
1
油泵总成
质检员:
年月日
2
多用阀总成
质量安全部主管:年月日
说明:
1、操作工生产完毕并且自检合格后,方可在“操作者”一栏签名。
2、检查员专检合格后,或返工返修确认合格后,方可在专检结果一栏打“√”,合格。
3、本卡一车一张,不得多填、错填、漏填、误填。本卡必须严格按规定发放,回收并妥善保管。
驾驶室内外完整性
4
灯光、电器、仪表
5
发动机、底盘、轮胎
6
操纵、驾驶状况
7
装配、连接、紧固
8
油漆、外观及清洁度
9
油箱油量
10
有无三漏
二
装配工序内容
操作者
自检结果
质检结果
质检结论
1
划线、钻孔
质检员:
年月日
2
副梁总成拼装、焊接
3
车厢底板拼装、焊接
4
车厢栏板拼装、焊接
5
车厢总成拼装、焊接
6
焊渣、飞溅清理
7
取力器油泵分装装配
改装车生产过程检验记录表
底盘生产厂家:底盘来源:底盘型号:
改装车整车型号:VIN号:动力号:交付日期:年月日
一
底盘检验
检验情况
存在的问题
处理意见及结果
1
合格证、一致性证书
1、底盘检验合格,允许改装。
2、底盘有一般问题,允许改装。
3、底盘有严重问题,不许改装。
质检员:
年月日
2
铭牌、VIN、动力号一致
3
8
装配侧后防护装置
9
备胎架及升降机构
10
装配挡泥板、备胎
11
装回复反射器、示廓灯
12
贴反光标识
五
涂装工序内容
操作者
自检结果
质检结果
质检结论
1
清理、打磨、抛光
质检员:
年月日
2
油漆调兑(黏度)
3
整车刮补腻子、打胶
4
喷漆、喷涂厂标字体
5
油漆厚度、附着力
6
油漆光泽度、表面处理
7
整车外观处理
六
整车性能检验
存在问题