环氧氯丙烷的生产技术
环氧氯丙烷工艺技术介绍
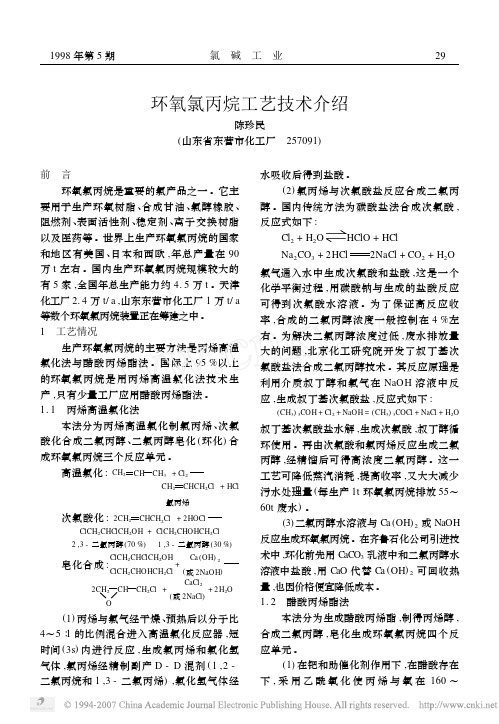
CH2 CHCH2Cl + HCl
氯丙烯
次氯酸化 : 2CH2 CHCH2Cl + 2 HOCl
ClCH2CHClCH2OH + ClCH2CHOHCH2Cl
2 ,3 - 二氯丙醇 (70 %) 1 ,3 - 二氯丙醇 (30 %)
皂化合成 : ClCH2CHClCH2OH + Ca (OH) 2
(CH3) 3CO H + Cl2 + NaO H = (CH3) 3COCl + NaCl + H2O
叔丁基次氯酸盐水解 ,生成次氯酸 ,叔丁醇循 环使用 。再由次氯酸和氯丙烯反应生成二氯 丙醇 ,经精馏后可得高浓度二氯丙醇 。这一 工艺可降低蒸汽消耗 ,提高收率 ,又大大减少 污水处理量 (每生产 1t 环氧氯丙烷排放 55~ 60t 废水) 。
1998 年第 5 期 氯 碱 工 业
29
环氧氯丙烷工艺技术介绍
陈珍民 (山东省东营市化工厂 257091)
前 言
环氧氯丙烷是重要的氯产品之一 。它主
要用于生产环氧树脂 、合成甘油 、氯醇橡胶 、
阻燃剂 、表面活性剂 、稳定剂 、离子交换树脂
以及醋酸丙烯酯法各有优
缺点 。醋酸丙烯酯法在产品收率和原料消耗
及产品成本占有绝对优势 ,是环氧氯丙烷生 产先进工艺 (表 1 是日本鹿岛和昭和电工两 家技术经济指标对比表 ,单位 t/ t·ECH) 。
表 1
项 目
丙烯 (100 %) 氯气 (100 %) 氢氧化钙 (100 %)
(3) 二氯丙醇水溶液与 Ca (OH) 2 或 NaOH 反应生成环氧氯丙烷 。在齐鲁石化公司引进技 术中 ,环化前先用 CaCO3 乳液中和二氯丙醇水 溶液中盐酸 ,用 CaO 代替 Ca (OH) 2 可回收热 量 ,也因价格便宜降低成本。 1. 2 醋酸丙烯酯法
环氧氯丙烷生产原理

环氧氯丙烷生产原理二、主要生产原理1、反应原理1.1、氯化反应原理氯丙烯是丙烯氯化、氯原子在饱和碳键上取代氢原子而合成的。
在氯化过程中丙烯的双键得以保存,产生HCl气体,反应式如下:(1) CH2=CH-CH3+Cl2→CH2=CH-CH2Cl+HCl反应放热约为26.7kcal/mol。
除了主反应外还有许多副反应。
副反应所产生的化合物很多,有丙烯氯化物、三氯丙烷以及热降解产物如芳香烃类、焦油和碳化物等。
主要有在其它碳键上的取代反应生成2-氯丙烯和1-氯丙烯,方程式如下:(2) CH2=CH-CH3+Cl2→CH2=CCl-CH3 +HCl→CHCl=CH-CH3+HCl另外,氯气加成反应生成1,2-二氯丙烷:(3) CH2=CH-CH3+Cl2→ClCH2-CHCl-CH3HCl与氯丙烯继续反应生成1,3-二氯丙烷:(4)CH2=CH-CH2Cl+HCl→ClCH2-CH2-CH2Cl氯丙烯继续氯化进行取代反应,生成1,3-二氯丙烯:(5) CH2=CH-CH2Cl+Cl2→ClCH=CH-CH2Cl+HCl1.2、氯醇化反应原理次氯酸(氯气与水反应生成)与氯丙烯在循环液中混合,在反应器中连续而均匀接触发生反应生成二氯丙醇,生成的二氯丙醇有两种:1,3-二氯丙醇和2,3-二氯丙醇。
反应方程式如下:(1)ClOH + CH2Cl-CH=CH2→ CH2Cl-CHOH-CH2Cl(1,3-二氯丙醇)(2)ClOH + CH2Cl-CH=CH2→ CH2Cl-CHCl-CH2OH(2,3-二氯丙醇)反应为放热反应(216,100kJ/kmol),1,3-二氯丙醇和2,3-二氯丙醇的生成量为1:2。
次氯酸的反应方程式如下:(3)Cl2 +H2O → HOCl + H+ + Cl-(4)HOCl → ClO- + H+优化次氯酸的生成条件、抑制溶液中的游离氯和次氯酸分解,会从总体上提高氯醇化反应的收率。
环氧氯丙烷-甘油安全生产要点

1 工艺简述1.1 环氧氯丙烷生产环氧氯丙烷的主要原料是丙烯、氯气和消石灰。
将气化丙烯和氯气在高温氯化反响器中发展氯化反响,生成粗氯丙烯,经过精制工序精制,得到精氯丙烯。
精氯丙烯与氯气在反响器中发展酸化,生成二氯两醇。
然后再与石灰乳发展皂化反响(环化过程),生成粗环氧氯丙烷,经过精制,得到高纯度环氧氯丙烷。
1.2 合成甘油合成甘油的生产系将精制的环氧氯丙烷在碳酸钠溶液中发展水解,生产粗甘油,经农缩、过滤、蒸馏、脱色及精制得到纯度99.9%的甘油。
本装置所用原料及产品均系易燃、易爆、有毒和强腐蚀性物质,属有毒、有害生产作业岗位。
2 重点部位2.1 丙烯贮罐该贮罐系供应氯化反响器丙烯单体的中间贮罐,不仅具有贮存液化石油气的压力容器的危(wei)险因素,而且排水作业有发生跑料的危(wei)险,曾经有跑料着火的事故教训。
2.2 氯丙烯反响器氯化反响是在高温(470℃)下的放热反响。
反响速度快(2-4 秒),工艺掌握要求严格,一旦投入氯气过量,可造成碳化燃烧。
反响温度太高,则易产生高沸物的副反响及裂解反响,生成的游离碳粘附于设备或者管道内壁以致阻塞管道、设备。
某化工厂曾经有过因氯流量表失灵、投料过量造成停车的事故教训。
2.3 丙烯压缩机由于该机振动较大,易振裂管线焊口使两烯喷出。
喷出并气化的丙烯,如遇有火源,将会造成空中爆炸、着火。
某化工厂压缩机二段出口导淋阀焊口曾经有 3 次震裂的事故实例。
2.4 废油燃烧炉该设备是氯丙烯工序和环氧氯丙烷工序的废油处理装置,用丙烯点火,操作温度是 1250℃,尾气经急冷室冷却,一旦冷却水失控,会造成高温尾气后移而发生火灾。
3 安全要点3.1 丙烯贮罐3.1.1 操作人员发展排水作业时,必需两人在现场监护、操作。
严禁排出丙烯,排水后关严排水阀门。
3.1.2 应定时检查各密封点,严防跑、冒、滴、漏。
3.1.3 应定期对丙烯检测报警仪发展校验检查。
3.2 氯化反响器3.2.1 留意投料配比,严格掌握丙烯和氯气 4:1 的克份子比。
生产环氧氯丙烷的方法
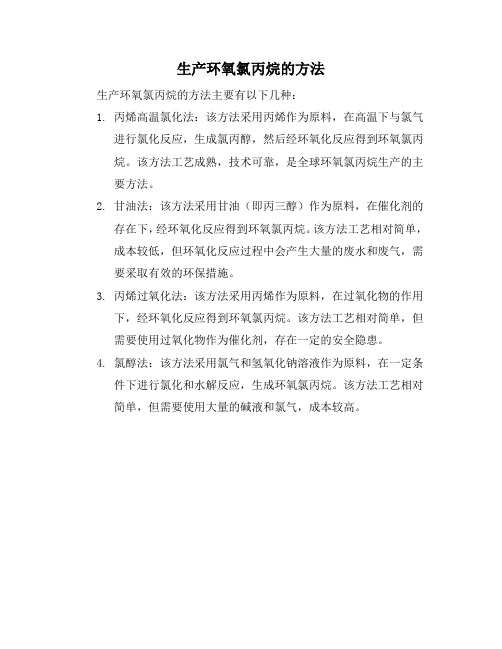
生产环氧氯丙烷的方法
生产环氧氯丙烷的方法主要有以下几种:
1.丙烯高温氯化法:该方法采用丙烯作为原料,在高温下与氯气
进行氯化反应,生成氯丙醇,然后经环氧化反应得到环氧氯丙烷。
该方法工艺成熟,技术可靠,是全球环氧氯丙烷生产的主要方法。
2.甘油法:该方法采用甘油(即丙三醇)作为原料,在催化剂的
存在下,经环氧化反应得到环氧氯丙烷。
该方法工艺相对简单,成本较低,但环氧化反应过程中会产生大量的废水和废气,需要采取有效的环保措施。
3.丙烯过氧化法:该方法采用丙烯作为原料,在过氧化物的作用
下,经环氧化反应得到环氧氯丙烷。
该方法工艺相对简单,但需要使用过氧化物作为催化剂,存在一定的安全隐患。
4.氯醇法:该方法采用氯气和氢氧化钠溶液作为原料,在一定条
件下进行氯化和水解反应,生成环氧氯丙烷。
该方法工艺相对简单,但需要使用大量的碱液和氯气,成本较高。
丙烯高温氯化法生产环氧氯丙烷工艺流程

丙烯高温氯化法生产环氧氯丙烷工艺流程丙烯高温氯化法生产环氧氯丙烷工艺流程,听起来好像很高大上的样子,其实说白了就是把丙烯和氯气混合在一起,然后通过高温加热,让它们发生化学反应,最后生成环氧氯丙烷。
这个过程虽然看起来简单,但是其中蕴含的科学道理可不少呢!我们要准备好原料。
这个原料可不是随便找的,得是纯度很高的丙烯和氯气。
接着,我们要把它们放在一起,然后通过高压泵把它们送入反应器中。
这个时候,反应器里面就会开始冒出一股股白色的烟雾,就像是在下雪一样。
这就是丙烯和氯气在高温下发生化学反应的结果。
我们要让这个反应持续进行下去。
为了达到这个目的,我们会给反应器加热。
一开始的时候,加热的温度还不是很高,就像是在给炉子加煤一样。
但是随着时间的推移,加热的温度越来越高,就像是在给炉子加炭一样。
这个时候,反应器里面的烟雾也变得越来越浓密,就像是在下大雨一样。
我们要等待一段时间,让这个反应充分进行。
这个时间长短取决于反应器的规格和原料的质量。
等到反应充分进行之后,我们就可以停止加热了。
这个时候,反应器里面就会产生一种特殊的气体——氯丙醇。
这种气体有着浓郁的香味,就像是刚刚出炉的面包一样诱人。
我们要把氯丙醇分离出来。
这个过程需要用到一些特殊的设备和技术。
我们要通过冷却器把反应器里的热量散发出去。
我们会把氯丙醇抽出来,放到一个特殊的容器里面进行过滤和分离。
我们就可以得到纯净的环氧氯丙烷了!丙烯高温氯化法生产环氧氯丙烷工艺流程虽然看起来简单粗暴,但是其中蕴含的科学道理可不少呢!只有掌握了这些科学道理,才能够生产出高质量的环氧氯丙烷产品。
所以说啊,要想做好一件事情,就必须要有扎实的理论基础和丰富的实践经验。
只有这样才能够在激烈的市场竞争中立于不败之地!。
环氧氯丙烷工艺流程

环氧氯丙烷工艺流程
一、环氧氯丙烷概述
环氧氯丙烷(氯丙烷)是一种氯代烯烃,具有良好的芳香、开气和易
蒸发性。
大部分环氧氯丙烷由氯乙烯衍生而来,主要用于生产氯丙烷乙醚、酯和烷基胺。
它的化学式为C3H6Cl2,熔点低,容易蒸发分解,分子量165.02、大部分氯丙烷具有典型的乙烯气味,并因其芳香和可溶解性而被
广泛用于化妆品、制药等工业制品中,也可以用于食品、香料和农用产品中。
二、环氧氯丙烷生产工艺
1、水合氯乙烯法:
水合氯乙烯法的原料是氯乙烯,在室温下将氯乙烯和水混合,加入70%的硫酸钠及其它催化剂,在搅拌、加热条件下,经特定的反应温度控制,氯乙烯水解生成氯丙烷及其它混合物,混合物再经过凝固、洗涤、精馏、蒸馏等工艺步骤,将氯乙烯会生成氯丙烷。
2、原子燃料法:
原子燃料法的原料是氯乙烯和氢,一定比例的氯乙烯作为原料放入反
应容器,加热至250℃~400℃之间,水吏林氟烃反应催化剂和氢气混合,放入反应容器,在特定温度和压力下反应1~2小时后,分离产物,再经
过凝固、洗涤、精馏、蒸馏分离得到氯丙烷产物。
3、氯乙烯氯化法:
氯乙烯氯化法的原料是氯乙烯。
环氧氯丙烷工艺流程

环氧氯丙烷工艺流程
环氧氯丙烷是一种重要的有机化工原料,广泛应用于涂料、导电胶、
环氧地坪等领域。
以下是其工艺流程:
1. 原料准备:将氯丙烯、环氧乙烷和氯化铝等原料放入罐中,进行混合。
2. 加热:将罐中原料加热至100℃左右,使其发生反应。
3. 分离:反应后,将产物分为有机相和水相,有机相即为环氧氯丙烷。
4. 精制:采用精馏、萃取等方法对环氧氯丙烷进行精制,提高纯度。
5. 包装:将精制后的环氧氯丙烷装入钢瓶或塑料桶中,密封存储。
需要注意的是,生产过程中要加强安全措施,防止原料泄漏和产生爆
炸等事故。
此外,大型化、自动化是未来环氧氯丙烷生产的发展趋势,有必要加强技术研发和设备更新。
总之,环氧氯丙烷工艺流程简单,但要求控制不同环节的条件,以保
证产品的质量和安全。
未来发展方向为高效、安全、环保的生产方式。
环氧氯丙烷

目前环氧氯丙烷主要生产工艺
丙烯高温氯化法 醋酸丙烯酯法 丙烯醛法 新工艺-甘油法
丙烯高温氯化法
丙烯高温氯化法是工业上生产环氧氯丙烷 的经典方法,由美国Shell公司于1948年首 次开发成功并应用于工业化生产。
目前,世界上90%以上的环氧氯丙烷采用该 方法生产,主要原料是丙烯、氯气和石灰 。其工艺过程主要包括3个反应单元。
③氯化反应
④环氧氯丙烷的合成 主反应:
3 丙烯醛法
Dow 化学开发了丙烯醛制环氧氯丙烷的工艺, 首先将丙烯醛氯化生成2,3-二氯丙醛,然后将 2,3-二氯丙醛加氢生成2,3-二氯丙醇,最后2,3二氯丙醇脱去氯化氢生成ECH。该工艺的原料 丙烯醛是由丙烯催化氧化制取的。
新工艺-甘油法
甘油制环氧氯丙烷最早于1854年由 Berthelot在用盐酸处理粗甘油,然后用碱 液水解时首先发现的,数年后,Reboul提 出这一物质可由二氯丙醇与氢氧化钠经水解 反应直接得到。
组员:王威.邓攀攀.胡益共
什么是环氧氯丙烷 ?
环氧氯丙烷是一种无色有刺激性气味油 状的重要的有机化工原料和精细化工产品 ,用途十分广泛。以它为原料制得的环氧 树脂具有粘结性强,耐化学介质腐蚀、收 缩率低、化学稳定性好、抗冲击强度高以 及介电性能优异等特点,在涂料、胶粘剂 、增强材料、浇铸材料和电子层压制品等 行业具有广泛的应用。
甘油氯化法工艺是将甘油与4%~6%冰醋 酸均匀混合,通入干燥氯化氢气体制成二氯 丙醇,再与氢氧化钠作用制成环氧氯丙烷。
工艺过程可以分为5 个阶段
氯化将甘油和冰醋 酸(按甘油质 量的4%~6% )加入氯化反 应釜中升温至 90 ℃,即开始 通入氯化氢气 体
将氯化后的混 合液用氢氧化 钠中和过量的 氯化氢和催化 剂冰醋酸,并调 节液体的酸碱 度,使二氯丙 醇和其他液体 分离
环氧氯丙烷生产技术改进
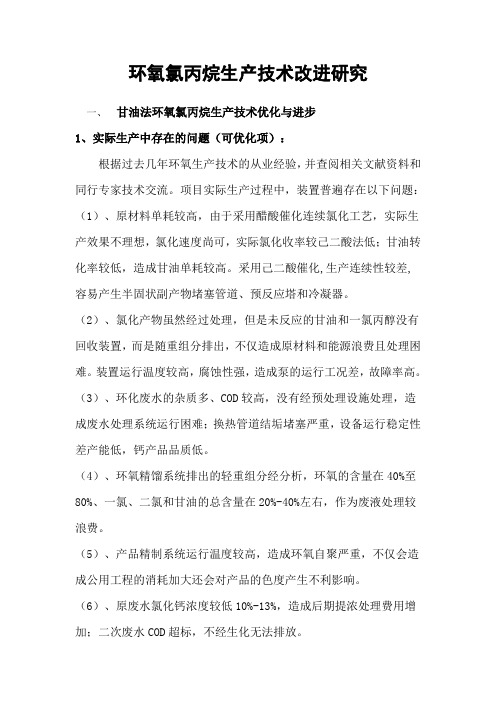
环氧氯丙烷生产技术改进研究一、甘油法环氧氯丙烷生产技术优化与进步1、实际生产中存在的问题(可优化项):根据过去几年环氧生产技术的从业经验,并查阅相关文献资料和同行专家技术交流。
项目实际生产过程中,装置普遍存在以下问题:(1)、原材料单耗较高,由于采用醋酸催化连续氯化工艺,实际生产效果不理想,氯化速度尚可,实际氯化收率较己二酸法低;甘油转化率较低,造成甘油单耗较高。
采用己二酸催化,生产连续性较差,容易产生半固状副产物堵塞管道、预反应塔和冷凝器。
(2)、氯化产物虽然经过处理,但是未反应的甘油和一氯丙醇没有回收装置,而是随重组分排出,不仅造成原材料和能源浪费且处理困难。
装置运行温度较高,腐蚀性强,造成泵的运行工况差,故障率高。
(3)、环化废水的杂质多、COD较高,没有经预处理设施处理,造成废水处理系统运行困难;换热管道结垢堵塞严重,设备运行稳定性差产能低,钙产品品质低。
(4)、环氧精馏系统排出的轻重组分经分析,环氧的含量在40%至80%、一氯、二氯和甘油的总含量在20%-40%左右,作为废液处理较浪费。
(5)、产品精制系统运行温度较高,造成环氧自聚严重,不仅会造成公用工程的消耗加大还会对产品的色度产生不利影响。
(6)、原废水氯化钙浓度较低10%-13%,造成后期提浓处理费用增加;二次废水COD超标,不经生化无法排放。
2、存在问题解决思路和方案:1)、改变生产中的催化剂为己二酸,通过与同业厂家的技术交流,己二酸催化工艺也不是没有问题,主要问题有:堵塞管道及设备(换热器与预反应吸收塔),连续性较差,且控制要求高。
目前大多采取半连续生产状态,备用设备轮换法。
考虑解决方案是采用非填料塔或新鲜甘油吸收;若暂存罐材质用钢衬四氟,高温出料可把换热器省略,省去清理换热器的麻烦。
2)、针对氯化氢、甘油和一氯丙醇没有回收,造成原材料浪费;装置运行温度较高,故障率高的问题,通过工艺装置对比,采用低温蒸馏,氯化氢回收率得到较大提升,同时由于催化剂的改变,甘油转化率提高,暂时舍弃重组分的塔式回收(通过粗甘油精制可知,从重组分中回收甘油需较高的真空-0.098mpa和温度200℃,结果就会造成回收困难,经济性差),而是采用间歇加压反应来彻底转化原料和中间体,通过蒸馏得以回收。
环氧氯丙烷处理工艺
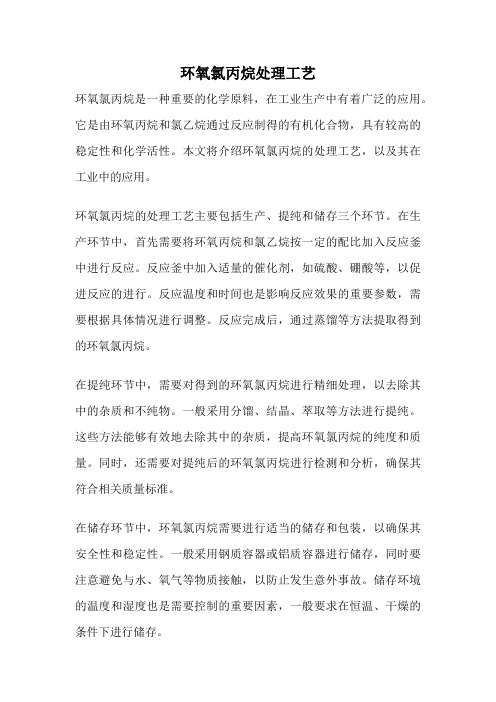
环氧氯丙烷处理工艺环氧氯丙烷是一种重要的化学原料,在工业生产中有着广泛的应用。
它是由环氧丙烷和氯乙烷通过反应制得的有机化合物,具有较高的稳定性和化学活性。
本文将介绍环氧氯丙烷的处理工艺,以及其在工业中的应用。
环氧氯丙烷的处理工艺主要包括生产、提纯和储存三个环节。
在生产环节中,首先需要将环氧丙烷和氯乙烷按一定的配比加入反应釜中进行反应。
反应釜中加入适量的催化剂,如硫酸、硼酸等,以促进反应的进行。
反应温度和时间也是影响反应效果的重要参数,需要根据具体情况进行调整。
反应完成后,通过蒸馏等方法提取得到的环氧氯丙烷。
在提纯环节中,需要对得到的环氧氯丙烷进行精细处理,以去除其中的杂质和不纯物。
一般采用分馏、结晶、萃取等方法进行提纯。
这些方法能够有效地去除其中的杂质,提高环氧氯丙烷的纯度和质量。
同时,还需要对提纯后的环氧氯丙烷进行检测和分析,确保其符合相关质量标准。
在储存环节中,环氧氯丙烷需要进行适当的储存和包装,以确保其安全性和稳定性。
一般采用钢质容器或铝质容器进行储存,同时要注意避免与水、氧气等物质接触,以防止发生意外事故。
储存环境的温度和湿度也是需要控制的重要因素,一般要求在恒温、干燥的条件下进行储存。
除了以上的处理工艺,环氧氯丙烷在工业生产中还有着广泛的应用。
首先,它是一种重要的有机合成原料,可以用于制备各种有机化合物,如醇、醚、酮等。
其次,它还可以用作溶剂和去污剂,在化工、制药、电子等领域有着广泛的应用。
此外,环氧氯丙烷还可以用于制备环氧树脂、聚氨酯等高分子材料,具有良好的机械性能和耐化学性能。
环氧氯丙烷是一种重要的化学原料,在工业生产中具有广泛的应用。
其处理工艺包括生产、提纯和储存三个环节,通过合理的操作和控制,可以得到高纯度、高质量的环氧氯丙烷。
同时,环氧氯丙烷还具有广泛的应用前景,在有机合成、溶剂、高分子材料等领域发挥着重要的作用。
我们应该充分发挥环氧氯丙烷的优势,不断推动其在工业生产中的应用,为促进经济发展和社会进步做出贡献。
甘油法环氧氯丙烷生产工艺

甘油法环氧氯丙烷生产工艺
甘油法环氧氯丙烷生产工艺是一种工业化生产环氧氯丙烷的方法。
下面将介绍甘油法环氧氯丙烷生产工艺的步骤。
首先,制备甘油。
将反应釜加热至50-60摄氏度,然后将适量
的石碱加入,反应4-5小时。
反应完成后,将反应物过滤,得
到甘油。
接下来,进行环氧化反应。
将甘油和氯丙烷加入反应釜中,并加入碱催化剂。
反应温度为70-80摄氏度,反应时间为3-4小时。
反应完成后,得到环氧氯丙烷。
然后,进行环氧烯化反应。
将环氧氯丙烷和双氧水加入反应釜中,加入硫酸固体、催化剂和溶剂。
反应温度为40-50摄氏度,反应时间为2-3小时。
反应完成后,得到环氧氯丙烷。
最后,进行分离和纯化。
将反应物经过冷却和蒸馏,将其中的杂质分离出去,得到纯净的环氧氯丙烷。
然后对得到的产物进行包装,即可得到成品。
甘油法环氧氯丙烷生产工艺具有以下特点:简单易行,反应条件温和,无需大规模设备,且产率高,对环境友好。
这使得甘油法环氧氯丙烷生产工艺成为了一种应用广泛的工业化生产方法。
(整理)甘油法生产环氧氯丙烷

甘油法生产环氧氯丙烷甘油法生产环氧氯丙烷/ | y+ O9 g2 J' S' O概述, Y, r( v3 p) }$ W; S; a3 i. n9 k: r环氧氯丙烷(ECH)别名表氯醇,分子量92.85,是一种易挥发、不稳定的无色油状液体,有与氯仿、醚相似的刺激性气味,密度1.1806 g/cm3,[wiki]沸点[/wiki]115.2 ℃,凝固点-57.2 ℃,折射率1.4382(20℃),[wiki]闪点[/wiki](开杯)40.6 ℃,自燃点415 ℃,微溶于水,能与多种有机溶剂混溶,可与多种有机液体形成共沸物。
7 ]& T$ @0 O- t1 ? M环氧氯丙烷是一种重要的有机化工原料和精细化工产品,用途十分广泛。
以它为原料制得的环氧树脂具有粘结性强,耐化学介质[wiki]腐蚀[/wiki]、收缩率低、化学稳定性好、抗冲击强度高以及介电性能优异等特点,在[wiki]涂料[/wiki]、胶粘剂、增强材料、浇铸材料和[wiki]电子[/wiki]层压制品等行业具有广泛的应用。
此外,环氧氯丙烷还可用于合成硝化甘油**、玻璃钢、电绝缘品、表面活性剂、医药、农药、涂料、胶料、离子交换树脂、增塑剂、(缩)水甘油衍生物、氯醇橡胶等多种产品,用作纤维素酯、树脂、纤维素醚的溶剂,用于生产化学稳定剂、化工染料和水处理剂等。
; y2 x" V5 ~ c( ~; ~, `3 h 工业化的环氧氯丙烷生产方法有基于[wiki]石油[/wiki]原料的丙烯高温氯化法和乙酸丙烯酯法两种,且绝大部分是丙烯路线。
近年来,由于石油价格的飞涨,使得环氧氯丙烷价格上涨且很不稳定,我国每年进口ECH十多万吨,严重制约我国下游产业的发展。
7 d% j: m% I' M' ]) L- q( Y0 G采用甘油法生产ECH,摆脱了以石油资源为原料的依附,又节约了大量的石油资源。
还减少了[wiki]环境[/wiki]污染。
环氧氯丙烷生产技术以及比较分析

环氧氯丙烷生产技术路线1984年美国壳牌公司建成第1座合成甘油生产工厂,环氧氯丙烷作为合成甘油过程的中间体,开始大规模工业生产。
目前,国外环氧氯丙烷的工业化生产方法主要有4种,其中,丙烯高温氯化法是传统的生产方法,至今已有40多年历史,仍是世家上环氧氯丙烷生产的主要方法。
1 丙烯高温氯化法目前,世界90%以上的环氧氯丙烷采用该方法进行生产。
此法生产环氧氯丙烷主要分3步:(1)丙烯在470—500℃高温下氯化生产氯丙烯,副产的1,2—二氯丙烷和1,3—二氯丙烯简称D—D混剂。
要控制好主反应一氯化反应的温度,丙烯与氯气的混合尽可能均匀。
降低温度可抑制析碳反应,但温度偏低有利于加成反应,产品收率相对降低;反之,温度过高,如超过500℃,虽然收率提高,但副作用也加剧,反应器、换热器等严重结碳,影响反应的顺利进行,需停车清碳,实际上还使收率降低。
(2)氯气在水中生成次氯酸,再与氯丙烯反应生成二氯丙醇。
该反应通常称为饱和氯水法,美国Shell、日本鹿岛、意大利Conser等公司均采用此法。
要制取质量分数为4.0%~5.0%的二氯丙醇溶液,必须加大反应过程中的溶液循环量。
氯气可逐级加入,并控制好溶液的酸度,尽量减少副产物的生成量。
(3)二氯丙醇与氢氧化钙发生皂化反应生成环氧氯丙烷。
皂化后的粗ECH经蒸馏后可得到ECH成品。
该法ECH收率为70%~75%。
2 醋酸丙烯酯—丙烯醇法原苏联科学院与日本昭和电工均开发了此法。
原苏联采用先氯化后水解工艺,昭和电工则采用先水解后氯化工艺。
1985年,日本昭和电工公司开始以丙烯为原料经醋酸丙烯酯和丙烯醇生产环氧氯丙烷,从而打破了完全依赖高温氯化法的格局。
该法分4步进行:(1)在钯和助催化剂及醋酸存在下,采用乙酰氧化技术。
使用丙烯与氧在150~190℃反应,生成醋酸丙烯酯:在上述反应条件下,醋酸丙烯醇的选择性大于90%。
(2)醋酸丙烯酯经水解反应制得丙烯醇。
该反应为可逆反应,根据化学平衡原理,醋酸丙烯醇的转化率取决于化学平衡常数。
环氧氯丙烷的合成简介
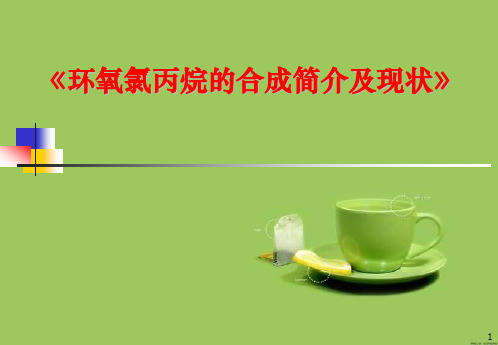
能耗
废水(t/tECH) 成本(万元)
高
40~50 0.9~1.0
较低
20~30 1.0~1.1
30~40%丙烯法
3~7 0.7~0近年来,全球ECH产能增长迅速,2002 年全球产能约 122万 t/a,2011 年产能上升为 206.4万 t/a,到 2012 年达到 248.4 万t/a, 新增产能 42 万t,其中 10 万t的来自于苏威集团新建于泰国的甘
甘油
醋酸 催化剂
分 离 塔
皂 化 塔
精 馏 塔
成品槽
残液
废水
13
2.4 丙烯醛法和丙酮法
(1) Dow化学开发了丙烯醛制环氧氯丙烷的工艺。首先将丙烯醛 氯化生成 2,3-二氯丙醛,然后将 2,3-二氯丙醛加氢生成 2,3二氯丙醇,最后2,3-二氯丙醇皂化生成ECH。 (2) Asahi(日本旭化成)公司和Mitsubishi(日本三菱)公司先
甘油法
丙烯醛和丙酮法
醛和酮转化成醇的选择性较 高。
催化剂价格高,丙烯醛分离 复杂,设备投资费用高。
综上所述,甘油法制备环氧氯丙烷面临着绝好机遇,利用甘油制备 ECH 可摆脱丙烯紧 缺的制约,减少国家对石油的依赖,促进生物质能源产业的顺利发展,具有重大的经济 和社会价值。
15
2.6 各工艺成本比较
项 目 原料1(t/tECH) 原料2(t/tECH) 碱(t/tECH) 投资(3万吨ECH) 安全可靠性 丙烯高温氯化法 0.66(丙烯) 2.1(氯气) 1.10(石灰) 2.5~3亿元 危险、操作 周期短 醋酸丙烯酯法 0.59(丙烯) 0.9 (氯气) 0.70(石灰) 4~5亿元 取决于Pd 催化剂 甘油法 1.20(甘油) 1.0(盐酸) 1.2(液碱) 0.65~0.85亿元 安全可靠
国内外环氧氯丙烷生产应用及市场分析
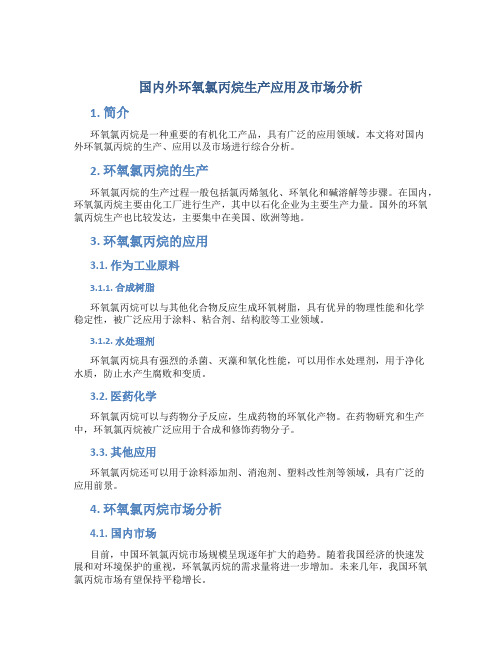
国内外环氧氯丙烷生产应用及市场分析1. 简介环氧氯丙烷是一种重要的有机化工产品,具有广泛的应用领域。
本文将对国内外环氧氯丙烷的生产、应用以及市场进行综合分析。
2. 环氧氯丙烷的生产环氧氯丙烷的生产过程一般包括氯丙烯氢化、环氧化和碱溶解等步骤。
在国内,环氧氯丙烷主要由化工厂进行生产,其中以石化企业为主要生产力量。
国外的环氧氯丙烷生产也比较发达,主要集中在美国、欧洲等地。
3. 环氧氯丙烷的应用3.1. 作为工业原料3.1.1. 合成树脂环氧氯丙烷可以与其他化合物反应生成环氧树脂,具有优异的物理性能和化学稳定性,被广泛应用于涂料、粘合剂、结构胶等工业领域。
3.1.2. 水处理剂环氧氯丙烷具有强烈的杀菌、灭藻和氧化性能,可以用作水处理剂,用于净化水质,防止水产生腐败和变质。
3.2. 医药化学环氧氯丙烷可以与药物分子反应,生成药物的环氧化产物。
在药物研究和生产中,环氧氯丙烷被广泛应用于合成和修饰药物分子。
3.3. 其他应用环氧氯丙烷还可以用于涂料添加剂、消泡剂、塑料改性剂等领域,具有广泛的应用前景。
4. 环氧氯丙烷市场分析4.1. 国内市场目前,中国环氧氯丙烷市场规模呈现逐年扩大的趋势。
随着我国经济的快速发展和对环境保护的重视,环氧氯丙烷的需求量将进一步增加。
未来几年,我国环氧氯丙烷市场有望保持平稳增长。
4.2. 国际市场环氧氯丙烷在国际市场上也有着广阔的应用前景,尤其在工业化发达的国家和地区。
目前,环氧氯丙烷的主要出口国包括美国、欧洲等。
随着全球环境保护意识的增强,对环氧氯丙烷等环保型化工产品的需求将进一步增加。
4.3. 市场竞争态势目前,国内外环氧氯丙烷生产企业较多,市场竞争激烈。
在国内市场,龙头企业占据主导地位,具有规模经济和技术优势。
同时,一些国际大型跨国公司也在我国市场拥有一定的份额。
未来,环氧氯丙烷市场竞争将进一步加剧。
5. 结论环氧氯丙烷作为一种重要的有机化工产品,具有广泛的生产和应用领域。
甘油法制取环氧氯丙烷工艺

甘油法制取环氧氯丙烷工艺生产线,采用的是甘油法生产环氧氯丙烷。
甘油法工艺具有能耗低、无污染、副产物少等优点,同时也能够消化过剩的甘油产能,使得传统的甘油生产企业能够继续保持生产,实现产业链的良性循环。
结论生物柴油的广泛使用带动了甘油产能的过剩,但这也为甘油的利用提供了新的机遇。
甘油法生产环氧氯丙烷具有能耗低、无污染等优点,可以消化过剩的甘油产能,促进产业链的良性循环。
因此,对于传统的甘油生产企业来说,开发甘油法技术是非常有前途的。
同时,政府也应该加大对生物能源的支持力度,推动可再生能源的发展,促进国民经济的可持续发展。
环氧氯丙烷是一种挥发性较高的化学物质,其在不同温度下的饱和蒸汽压可以在表1.2中查看。
由于其易与水蒸气发生反应,因此其蒸汽与空气混合后易形成爆炸性物质。
此外,环氧氯丙烷还具有易燃性,燃烧过程中会产生刺激性的氯化氢及光氯毒物。
在高温下,环氧氯丙烷能自发进行聚合反应,在较低温度下,酸、碱、醇、胺、金属、金属氧化物等物质会引发其聚合反应。
因此,对于ECH的生产、储运及使用都有比较严格的要求,以防止聚合反应可能引发的爆炸。
表1.2中列出了不同温度条件下ECH的饱和蒸汽压数据。
可以看出,随着温度的升高,ECH的饱和蒸汽压也逐渐增大。
作为一种重要的有机化工原料和精细化工产品,环氧氯丙烷的用途十分广泛。
以它为原料制得的环氧树脂具有粘结性强、耐化学介质腐蚀、化学稳定性好、抗冲击强度高以及介质电性能优异等特点,在涂料、胶粘剂、增强材料、浇铸材料和电子层制品等行业具有广泛的应用。
此外,环氧氯丙烷还可用于合成多种产品,如甘油、硝化甘油炸药、玻璃钢、电绝缘品、表面活性剂、医药、农药、涂料、胶料、离子交换树脂、增塑剂、(缩)水甘油衍生物、氯醇橡胶等。
同时,它也是纤维素酯、树脂、纤维素醚的溶剂,用于生产化学稳定剂、化工染料和水处理剂等。
在国内外,环氧氯丙烷的生产现状也十分活跃。
随着科技的不断发展和应用领域的不断拓展,环氧氯丙烷的生产和应用前景也将越来越广阔。
甘油法制取环氧氯丙烷工艺
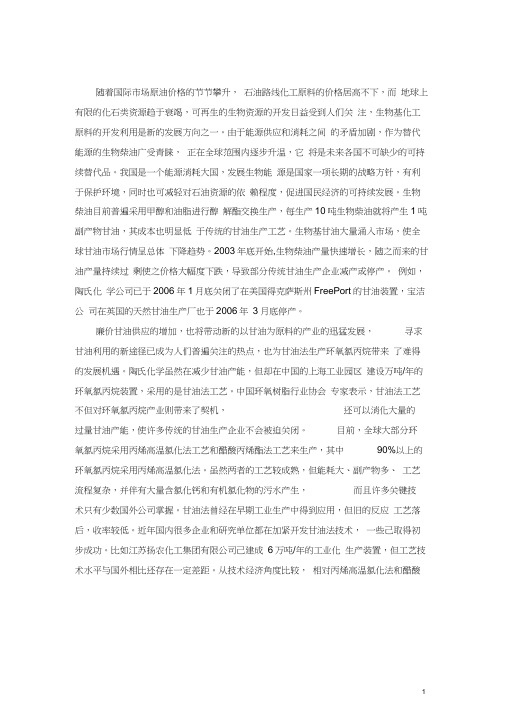
随着国际市场原油价格的节节攀升,石油路线化工原料的价格居高不下,而地球上有限的化石类资源趋于衰竭,可再生的生物资源的开发日益受到人们关注,生物基化工原料的开发利用是新的发展方向之一。
由于能源供应和消耗之间的矛盾加剧,作为替代能源的生物柴油广受青睐,正在全球范围内逐步升温,它将是未来各国不可缺少的可持续替代品。
我国是一个能源消耗大国,发展生物能源是国家一项长期的战略方针,有利于保护环境,同时也可减轻对石油资源的依赖程度,促进国民经济的可持续发展。
生物柴油目前普遍采用甲醇和油脂进行醇解酯交换生产,每生产10吨生物柴油就将产生1吨副产物甘油,其成本也明显低于传统的甘油生产工艺。
生物基甘油大量涌入市场,使全球甘油市场行情呈总体下降趋势。
2003年底开始,生物柴油产量快速增长,随之而来的甘油产量持续过剩使之价格大幅度下跌,导致部分传统甘油生产企业减产或停产。
例如,陶氏化学公司已于2006年1月底关闭了在美国得克萨斯州FreePort的甘油装置,宝洁公司在英国的天然甘油生产厂也于2006年3月底停产。
廉价甘油供应的增加,也将带动新的以甘油为原料的产业的迅猛发展,寻求甘油利用的新途径已成为人们普遍关注的热点,也为甘油法生产环氧氯丙烷带来了难得的发展机遇。
陶氏化学虽然在减少甘油产能,但却在中国的上海工业园区建设万吨/年的环氧氯丙烷装置,采用的是甘油法工艺。
中国环氧树脂行业协会专家表示,甘油法工艺不但对环氧氯丙烷产业则带来了契机,还可以消化大量的过量甘油产能,使许多传统的甘油生产企业不会被迫关闭。
目前,全球大部分环氧氯丙烷采用丙烯高温氯化法工艺和醋酸丙烯酯法工艺来生产,其中90%以上的环氧氯丙烷采用丙烯高温氯化法。
虽然两者的工艺较成熟,但能耗大、副产物多、工艺流程复杂,并伴有大量含氯化钙和有机氯化物的污水产生,而且许多关键技术只有少数国外公司掌握。
甘油法曾经在早期工业生产中得到应用,但旧的反应工艺落后,收率较低。
环氧氯丙烷的生产技术
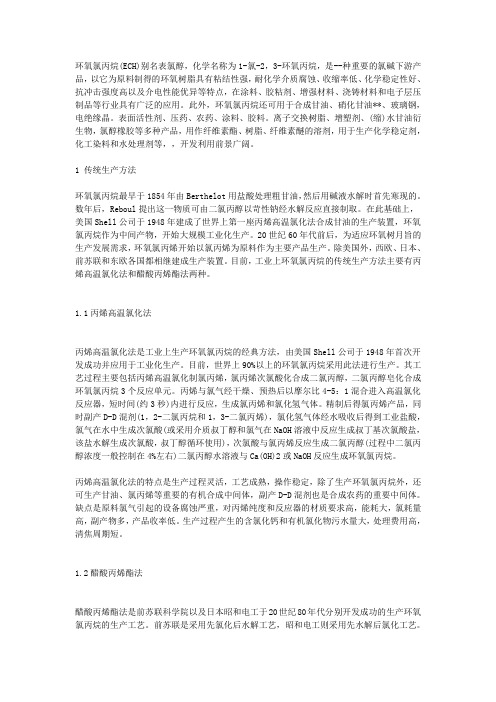
环氧氯丙烷(ECH)别名表氯醇,化学名称为1-氯-2,3-环氧丙烷,是--种重要的氯碱下游产品,以它为原料制得的环氧树脂具有粘结性强,耐化学介质腐蚀、收缩率低、化学稳定性好、抗冲击强度高以及介电性能优异等特点,在涂料、胶粘剂、增强材料、浇铸材料和电子层压制品等行业具有广泛的应用。
此外,环氧氯丙烷还可用于合成甘油、硝化甘油**、玻璃钢,电绝缘晶。
表面活性剂、压药、农药、涂料、胶料。
离子交换树脂、增塑剂、(缩)水甘油衍生物,氯醇橡胶等多种产品,用作纤维素酯、树脂、纤维素醚的溶剂,用于生产化学稳定剂,化工染料和水处理剂等,,开发利用前景广阔。
1 传统生产方法环氧氯丙烷最早于1854年由Berthelot用盐酸处理粗甘油,然后用碱液水解时首先寒现的。
数年后,Reboul提出这一物质可由二氯丙醇以苛性钠经水解反应直接制取。
在此基础上,美国Shell公司于1948年建成了世界上第一座丙烯高温氯化法合成甘油的生产装置,环氧氯丙烷作为中间产物,开始大规模工业化生产。
20世纪60年代前后,为适应环氧树月旨的生产发展需求,环氧氯丙烯开始以氯丙烯为原料作为主要产品生产。
除美国外,西欧、日本、前苏联和东欧各国都相继建成生产装置。
目前,工业上环氧氯丙烷的传统生产方法主要有丙烯高温氯化法和醋酸丙烯酯法两种。
1.1丙烯高温氯化法丙烯高温氯化法是工业上生产环氧氯丙烷的经典方法,由美国Shell公司于1948年首次开发成功并应用于工业化生产。
目前,世界上90%以上的环氧氯丙烷采用此法进行生产。
其工艺过程主要包括丙烯高温氯化制氯丙烯,氯丙烯次氯酸化合成二氯丙醇,二氯丙醇皂化合成环氧氯丙烷3个反应单元。
丙烯与氯气经干燥、预热后以摩尔比4-5:1混合进入高温氯化反应器,短时间(约3秒)内进行反应,生成氯丙烯和氯化氢气体。
精制后得氯丙烯产品,同时副产D-D混剂(1,2-二氯丙烷和1,3-二氯丙烯),氯化氢气体经水吸收后得到工业盐酸,氯气在水中生成次氯酸(或采用介质叔丁醇和氯气在NaOH溶液中反应生成叔丁基次氯酸盐,该盐水解生成次氯酸,叔丁醇循环使用),次氯酸与氯丙烯反应生成二氯丙醇(过程中二氯丙醇浓度一般控制在4%左右)二氯丙醇水溶液与Ca(OH)2或NaOH反应生成环氧氯丙烷。
- 1、下载文档前请自行甄别文档内容的完整性,平台不提供额外的编辑、内容补充、找答案等附加服务。
- 2、"仅部分预览"的文档,不可在线预览部分如存在完整性等问题,可反馈申请退款(可完整预览的文档不适用该条件!)。
- 3、如文档侵犯您的权益,请联系客服反馈,我们会尽快为您处理(人工客服工作时间:9:00-18:30)。
环氧氯丙烷(ECH)别名表氯醇,化学名称为1-氯-2,3-环氧丙烷,是--种重要的氯碱下游产品,以它为原料制得的环氧树脂具有粘结性强,耐化学介质腐蚀、收缩率低、化学稳定性好、抗冲击强度高以及介电性能优异等特点,在涂料、胶粘剂、增强材料、浇铸材料和电子层压制品等行业具有广泛的应用。
此外,环氧氯丙烷还可用于合成甘油、硝化甘油**、玻璃钢,电绝缘晶。
表面活性剂、压药、农药、涂料、胶料。
离子交换树脂、增塑剂、(缩)水甘油衍生物,氯醇橡胶等多种产品,用作纤维素酯、树脂、纤维素醚的溶剂,用于生产化学稳定剂,化工染料和水处理剂等,,开发利用前景广阔。
1 传统生产方法环氧氯丙烷最早于1854年由Berthelot用盐酸处理粗甘油,然后用碱液水解时首先寒现的。
数年后,Reboul提出这一物质可由二氯丙醇以苛性钠经水解反应直接制取。
在此基础上,美国Shell公司于1948年建成了世界上第一座丙烯高温氯化法合成甘油的生产装置,环氧氯丙烷作为中间产物,开始大规模工业化生产。
20世纪60年代前后,为适应环氧树月旨的生产发展需求,环氧氯丙烯开始以氯丙烯为原料作为主要产品生产。
除美国外,西欧、日本、前苏联和东欧各国都相继建成生产装置。
目前,工业上环氧氯丙烷的传统生产方法主要有丙烯高温氯化法和醋酸丙烯酯法两种。
1.1丙烯高温氯化法丙烯高温氯化法是工业上生产环氧氯丙烷的经典方法,由美国Shell公司于1948年首次开发成功并应用于工业化生产。
目前,世界上90%以上的环氧氯丙烷采用此法进行生产。
其工艺过程主要包括丙烯高温氯化制氯丙烯,氯丙烯次氯酸化合成二氯丙醇,二氯丙醇皂化合成环氧氯丙烷3个反应单元。
丙烯与氯气经干燥、预热后以摩尔比4-5:1混合进入高温氯化反应器,短时间(约3秒)内进行反应,生成氯丙烯和氯化氢气体。
精制后得氯丙烯产品,同时副产D-D混剂(1,2-二氯丙烷和1,3-二氯丙烯),氯化氢气体经水吸收后得到工业盐酸,氯气在水中生成次氯酸(或采用介质叔丁醇和氯气在NaOH溶液中反应生成叔丁基次氯酸盐,该盐水解生成次氯酸,叔丁醇循环使用),次氯酸与氯丙烯反应生成二氯丙醇(过程中二氯丙醇浓度一般控制在4%左右)二氯丙醇水溶液与Ca(OH)2或NaOH反应生成环氧氯丙烷。
丙烯高温氯化法的特点是生产过程灵活,工艺成熟,操作稳定,除了生产环氧氯丙烷外,还可生产甘油、氯丙烯等重要的有机合成中间体,副产D-D混剂也是合成农药的重要中间体。
缺点是原料氯气引起的设备腐蚀严重,对丙烯纯度和反应器的材质要求高,能耗大,氯耗量高,副产物多,产品收率低。
生产过程产生的含氯化钙和有机氯化物污水量大,处理费用高,清焦周期短。
1.2醋酸丙烯酯法醋酸丙烯酯法是前苏联科学院以及日本昭和电工于20世纪80年代分别开发成功的生产环氧氯丙烷的生产工艺。
前苏联是采用先氯化后水解工艺,昭和电工则采用先水解后氯化工艺。
其工艺过程主要包括合成醋酸丙烯酯,诺酸丙烯酯水解制烯丙醇,合成二氯丙醇以及二氯丙醇皂化生成环氧氯丙烷4个反应单元。
在钯和助催化剂作用下.丙烯与氧在温度160-180℃、压力0.5-1.0MPa,醋酸存在下反应生成醋酸丙烯醮在温度60-80℃、压力0.1-1.0Mpa下,以强酸性阳离子交换树脂为催化剂,醋酸丙烯酪经水解反应生成烯丙醇,在温度0-10℃,压力0.1-0.3MPa条件下,烯丙醇与氯通过加成反应生成二氯丙醇:二氯丙醇与氢氧化钙发生皂化反应生成环氧氯丙烷。
与传统的丙烯高温氯化法相比较,醋酸丙烯酯法的特点是避免了高温氯化反应,反应条件温和,易于控制,不结焦、操作稳定,丙烯、氢氧化钙和氯气的用量大大减少,反应副产物和含氯化钙废水的排放量也大大减少:开发了丙烯醇的氯化加成反应系统,成功地将氧引入环氧化物中,首次实现了由氧氧化代替氯氧化的技术,减少于醚化副反应,提高了系统的收率;工艺过程无副产盐酸产生;可以较容易获得目前技术还不宫粥到的高纯度烯丙醇。
不足之处是工艺流程长,催化剂寿命短,投资费用相对较高。
丙烯高温氯化法和醋酸丙烯酪法生产环氧氯丙烷的主要技术指标比较见表1所示。
表1丙烯高温氯化法和醋酸丙烯酪法生产环氧氯丙烷的主要技术指标比较针对丙烯高温氯化法传统生产工艺存在的设备腐蚀较为严重,生产能耗大,耗氯量高,副产物多,并且产生大量含氯化钙和有机氯化物废水等不足之处,许多生产厂家对该方法进行了改进。
主要表现在:(1)改变环化反应原料,在环化前先用固体CaCO3代替CaCO,乳液中和二氯丙醇水溶液中的盐酸(1.2%),降低成本,环化反应用CaO代替CaCO3,回收热量降低能耗;(2)改变环化塔。
环化塔由常压改为负压操作,可以使蒸汽消耗降低700kg/t,外排COD 降低了50kg/t,丙烯消耗降低了30kg/t,生产能力却提高了10%-15%。
(3)改进二氯丙醇的合成方法,采用国内碳酸盐法(C12与2%Na2CO3水溶液逆相接触,生成1.8%-2.0%的次氯酸,盐酸被中和,氯丙烯与次氯酸反应)替代国外饱和氯水法(氯丙烯与C12在水相中反应)合成二氯丙醇同时,北京化工研究院利用介质叔丁醇与氯气在NaOH溶液中反应生成叔丁基次氯酸盐,再经水解生成次氯酸和叔丁醇(循环利用),降低了原料消耗和能耗,提高收率,减少了废水排放量。
(4)采用静态混合器对氯化反应器及次氯酸化反应器进行优化,能有效提高二氯丙醇的纯度,减少副产物的生成。
(5)改进环化控制系统。
将氯丙烯反应系统的配比,由原来的丙烯,氯气定值调节改为比值调节控制,有利于反应的操作稳定性,减少结炭,延长装置运行周期,(6)改进蒸汽控制系统。
将原设计的蒸汽定值信率控制改为以原作为显示的塔顶压力作为参比量,自动调节蒸汽流量,使塔顶压力稳定为理想值0.12MPa以下可微调的变值,有利于抑制副反应的发生,防止未反应的二氯丙醇蒸出,增加收率;(7)改进控制碱加入系统。
以塔底排出废水的pH值为控制系统的参比量,调节石灰乳的流量,稳定塔底废水的pH值,使之保持在设定值,这样有助于减轻设备腐蚀和水解反应的发生,节约石灰乳的用量。
(8)改进设备。
增加预分塔来脱除轻组分,采用减压双塔连续精馏工艺来脱重组分,将预分塔顶排出的低沸物中氯丙烯进一步回收,减少了单耗。
在氯丙烯的回收和分离工序中,将原来部分塔的聚丙烯鲍尔环填料改为陶瓷波纹填料,筛板由原来的酚醛胶木板改为陶瓷条梁。
经过这样改造后,减少了设备腐蚀,降低了系统阻力,提高了处理能力,改善了传质效果,提高了质量,减少了消耗。
另外,采用特种环氧树脂独特配方的管件,使之耐盐酸、耐碱及耐二氯丙醇溶液的腐蚀,提高了装置的运行周期。
国内引进的氯丙烯法与国内开发的改进氯丙烯法的工艺参数比较见表2所示。
表2由表2可知,巴陵石化公司引进的氯丙烯法技术优势比较明显,相比之下,国内开发的碳酸盐法原料消耗最高,而经过改进的叔丁基次氯酸盐法技术有所提高,但能耗仍偏高。
2新技术的开发近年来,全球能源的紧缺住要是指石油资源)致使化工原料价格升高,加上人们对环保要求的日益严格,造成环氧氯丙烷现有工业生产技术固有的缺点住口氯丙烯法耗氯高,有机氯化物污水多,醋酸丙烯酯法设备腐蚀严重,反应器材质要求高等)日益明显,因此,国内外生产企业在不断改进现有工业生产技术的同时,不断研究开发出新的生产工艺,具有代表性的有道化学公司开发的丙烯醛法、日本旭川公司开发的丙酮法日本三井东压化学公司开发的有机过氧化氢法、索维尔公司开发的氯丙烯直接环氧化法以及索维尔公司开发的甘油法等。
2.1丙烯醛法丙烯醛法由道化学公司开发成功,该工艺包括丙烯氧化合成丙烯醛,丙烯醛氯化合成2,3-二氯丙醛,二氯丙醛氢化合成二氯丙醇,二氯丙醇皂化制环氧氯丙烷等工序。
丙烯氧化生成丙烯醛和二氯甲烷溶剂混合,冷却后与Cl-起加入氯化反应器,控制反应条件,生成2,3-二氯丙醛,加压时蒸馏回收二氯甲烷溶剂后,再与二氧环己烷溶剂混合,在氧化锆的催化作用下,与H2在反应器中进行加氢反应,生成2,3-二氯丙醇;过量的氢返回循环利用,混合物蒸馏从塔顶除去二氧环己烷溶剂,塔底物料再精馏得到二氯丙醇。
再经过与传统生产工艺一样的皂化、精馏等工序得到环氧氯丙烷产品。
虽然该工艺减少了C12的消耗和有机氯化物污水的排放,但是由于丙烯氧化制丙烯醛工序消耗的能量很高,因此,整个生产工艺的能耗和生产成本均比丙烯高温氯化法高。
2.2丙酮法丙酮法由Asahi公司和Mitsubishi公司分别开发成功。
该工艺包括丙酮氯化取代制1,3-二氯丙酮、二氯丙酮氢化制1,3-二氯丙醇,二氯丙醇皂化等工序。
;Asahi公司利用丙酮和Cl在氯化碘、氯化锂的作用下,在非水相中反应生成1,3-二氯丙酮;再采用异丙醇作为氢化反应的载体,使1,3-二氯丙酮发生转移氢化反应,生成1,3-二氯丙醇,异丙醇被还原成丙酮,返回氯化反应器循环利用。
Mitsubishi公司是使二氯丙酮在-种络合化合物的作用下,在甲苯溶剂中直接氢化反应制得二氯丙醇,然后再经过皂化处理得到环氧氯丙烷。
2.3氯丙烯有机过氧化氢(R00H)氧化法早在1986年,日本三井东压化学公司就使用卤代Ti、烷氧基Ti或Ti羧基化合物负载于SO2的载体为催化剂,开发丁异丙苯过氧化氢为环氧化剂的氯丙烯环氧化合成环氧氯丙烷的技术。
该技术由丙烯间接氧化法合成环氧丙烷的Halcon法“移植”而来。
目前该技术主要采用叔丁基过氧化氢、乙苯过氧化氢、异丙苯过氧化氢、环己烷过氧化氢等烷基过氧化氢(ROOU)为氧源,以生成过氧化物的母体烃类或相应的醇为反应溶剂,并使用负载于SiO2载体上的TI化合物作为催化剂。
一般控制氯丙烯与ROOH的摩尔比为5:1至10:1,反应温度为80-110℃(温度过低,反应不易进行温度过高,则促进ROOH催化分解)当ROOH转化率达到90%时,环氧氯丙烷选择性为80%-90%,产率为70%-80%(相对于ROO印而言。
由于该方法中,ROOH环氧化反应时转变为大量的联产品湘应的醇ROH),因此该工艺是否具有经济性受联产品的市场行情影响较大,另外,由于该工艺过程包括ROOH的制备、环氧化反应、联产品的精馏等工序,流程复杂,一次性投资大,因此目前还没有实现工业化大规模生产。
2.4氯丙烯直接氧化法虽然早在20世纪80年代,英国Interox化学公司就在无催化剂的条件下,利用过氧酸(主要是过乙酸,过丙酸)与氯丙烯进行环氧化反应,成功地合成出环氧氯丙烷。
但是由于过氧酸价格高,生产的安全性、氧源反应后的联产品,催化剂价格等诸多因素的限制,-般只用于附加值高且不易获得的精细化工产品的生产中,用它合成环氧氯丙烷在经济上不合算,为此,人们研究开发出氯丙烯直接环氧化制备环氧氯丙烷的生产工艺。
1999年,索维尔公司以钛硅分子筛为催化剂,直接利用H2O,与氯丙烯进行环氧化反应,成功合成出环氧氯丙烷。