在线高精度自动混配煤工艺系统设计
煤炭洗选加工自动化管理系统

煤炭洗选加工自动化管理系统是一种基于现代信息技术和自动化控制技术的煤炭洗选加工过程的智能化管理系统。
该系统通过对煤炭洗煤工艺流程的监测和控制,实现对煤炭质量的有效控制和提升。
本文将从以下几方面对煤炭洗选加工自动化管理系统进行详细介绍。
一、系统架构煤炭洗选加工自动化管理系统包含硬件和软件两部分。
硬件部分主要包括传感器、执行机构、控制器、通信模块等设备。
传感器用于采集煤炭洗选加工过程中的温度、湿度、流量等参数,控制器根据传感器采集的数据进行处理,并通过执行机构控制洗选设备的运行状态。
通信模块用于与上位机进行数据交互。
软件部分主要包括系统监测与控制软件、数据分析与处理软件和用户界面软件等。
系统监测与控制软件用于实时监测洗选过程中的关键参数,并根据预设的洗选规则对洗选设备进行自动控制。
数据分析与处理软件用于对洗选过程中的数据进行分析和处理,提供洗选工艺优化的参考。
用户界面软件则提供给操作人员使用,实现对系统的监控和控制。
二、系统功能煤炭洗选加工自动化管理系统主要具有以下几个功能。
1. 实时监测与控制:系统可以实时监测煤炭洗选加工过程中的温度、湿度、流量等参数,并根据预设的洗选规则对洗选设备进行自动控制,确保洗选过程的稳定运行。
2. 数据采集与存储:系统可以对洗选过程中的关键参数进行采集,并将数据进行存储,便于后续的数据分析和处理。
3. 数据分析与处理:系统可以对洗选过程中的数据进行分析和处理,通过建立模型和算法,提供洗选工艺优化的参考。
4. 故障诊断与维护:系统可以对洗选设备进行实时监测和故障诊断,提前预警并及时进行维护,避免设备故障对洗选工艺的影响。
5. 远程监控与控制:系统可以通过通信模块与上位机进行数据交互,实现对洗选工艺的远程监控和控制,提高管理效率和灵活性。
三、系统优势煤炭洗选加工自动化管理系统相比传统的手工操作和人工监测具有以下几个优势。
1. 提高洗选质量:系统可以实时监测和控制洗选过程中的关键参数,确保洗选质量的稳定和提升。
燃料智能化管理系统——智能配煤掺烧系统(发电企业必备)

发电企业燃料智能化管理系统系列产品之——智能配煤掺烧系统产品定位:智能配煤掺烧系统是武汉博晟信息科技有限公司发电企业燃料智能化管理整体解决方案系列产品之一。
该系列产品立足于为发电企业提供最适合的燃料管理系统,与中国五大发电集团(中国华能集团公司、中国大唐集团公司、中国华电集团公司、中国国电集团公司、中国电力投资集团公司)均有项目合作。
智能配煤掺烧系统参与的管理环节有煤场、掺配、上仓、燃烧、报表。
系统简介:博晟科技智能配煤掺烧管理系统以燃料配煤掺烧精确计算、精益实施、精细管理为目标,系统以配煤掺烧模型为基础,以锅炉设计参数、来煤信息、发电计划、负荷分布、煤场库存、历史掺配评价、设备运行工况等因素为基础生成最经济、最环保、综合最优的掺配方案,系统支持线性、非线性算法(神经网络),提供支持模拟掺配、经济掺配多种方式,基于电厂负荷自动生成掺配列表,形成最优排序,从sis取锅炉数据监控掺配燃煤对锅炉影响,优化掺配模型并对入炉煤质分析,通过定位装置监控斗轮机(堆取料机)实时工况,跟踪掺配执行。
配煤掺烧模型系统提供神经网络算法等多种最优方案求解的算法模型,主要有:最经济方案、最环保方案、综合最优方案。
以设定的目标为优化方向,在保证锅炉稳定燃烧的前提下,进行配比计算。
对求解得到的优化掺配结果,按原则(成本、环保、综合)进行排序。
用户可以在自动计算所得到的原始配方的基础上,自动执行5%调整(也可以设定为其它的调整比例)。
用户可以手工调整原始配方或执行5%调整后得到的各煤种的掺配数量,重新进行计算与比较,得到实用配方。
(1)煤场动态管理通过三维图形方式全面直观的展示煤场数据,动态显示各个煤场中燃煤信息,包括燃燃煤储存指标,煤质构成,燃煤在煤场中的分布,煤场温度、等情况,用图形直观的表示出来。
方便用户随时了解燃煤使用情况,为燃煤采购提供采购依据。
(2)斗轮机调度管理围绕斗轮机调度指令,基于斗轮机编码器,通过无线网络传输斗轮机位置信息到管理中心,对于斗轮机运行工况进行监视。
全自动煤炭采制样系统的设计研究
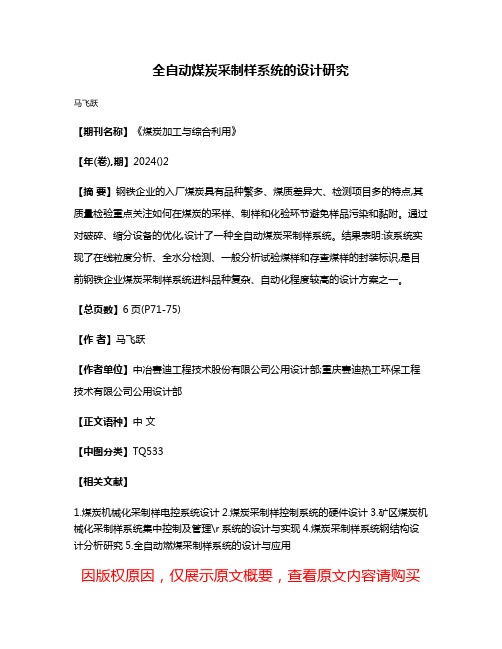
全自动煤炭采制样系统的设计研究
马飞跃
【期刊名称】《煤炭加工与综合利用》
【年(卷),期】2024()2
【摘要】钢铁企业的入厂煤炭具有品种繁多、煤质差异大、检测项目多的特点,其质量检验重点关注如何在煤炭的采样、制样和化验环节避免样品污染和黏附。
通过对破碎、缩分设备的优化,设计了一种全自动煤炭采制样系统。
结果表明:该系统实现了在线粒度分析、全水分检测、一般分析试验煤样和存查煤样的封装标识,是目前钢铁企业煤炭采制样系统进料品种复杂、自动化程度较高的设计方案之一。
【总页数】6页(P71-75)
【作者】马飞跃
【作者单位】中冶赛迪工程技术股份有限公司公用设计部;重庆赛迪热工环保工程技术有限公司公用设计部
【正文语种】中文
【中图分类】TQ533
【相关文献】
1.煤炭机械化采制样电控系统设计
2.煤炭采制样控制系统的硬件设计
3.矿区煤炭机械化采制样系统集中控制及管理\r系统的设计与实现
4.煤炭采制样系统钢结构设计分析研究
5.全自动燃煤采制样系统的设计与应用
因版权原因,仅展示原文概要,查看原文内容请购买。
精细化动力配煤在煤炭中转码头的运用
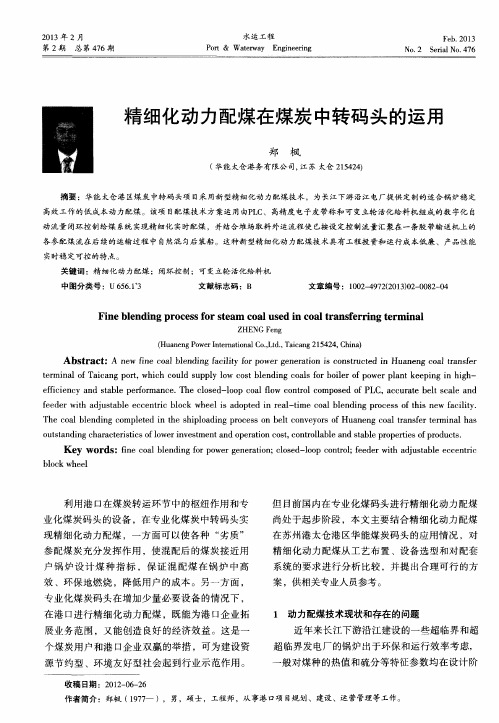
水 运 工 程
Po r t& W a t e r w a y En g i e e i r n g
Fe b. 2 0l 3
第 2期
总第 4 7 6期
N o . 2 S e i r a l No . 4 7 6
■ 精 细 化 动 力 ( 华 配 能 太 煤 仓 港 务 在 有 郑 限 煤 公 司 枫 炭 , 江 苏 中 太 仓 转 2 1 5 4 码 2 4 ) 头 的 运 用
f e e d e r w i t h a d j u s t a b l e e c c e n t r i c b l o c k w h e e l i s a d o p t e d i n r e a l - t i me c o a l b l e n d i n g p r o c e s s o f t h i s n e w f a c i l i t y .
Ke y wo r d s : i f n e c o a l b l e n d i n g f o r p o w e r g e n e r a t i o n ; c l o s e d - l o o p c o n t r o l ; f e e d e r w i t h a d j u s t a b l e e c c e n t r i c
t e r mi n a l o f Ta i c a n g p o r t , wh i c h c o u l d s u p p l y l o w c o s t b l e n d i n g c o a l s f o r b o i l e r o f p o we r p l a n t k e e p i n g i n h i g h -
基于PLC的给煤机控制系统设计

基于 PLC的给煤机控制系统设计摘要:给煤机是火力发电系统的主要配煤设备,在生产过程中实现连续定量供煤,保证高精度的物料配比。
目前,国内给煤机普遍采用继电控制系统,通过硬件逻辑关系实现设备的顺序控制功能。
但由于电路复杂、响应速度慢、控制精度有限、继电器故障率高,给电厂的正常生产运行带来了隐患。
设计了基于PLC 控制器的给煤机自动控制系统,优化了控制结构和外部电路,实现了设备的远程监控和信息通信,降低了操作故障率。
关键词:PLC;给煤机;控制系统;设计1PLC技术概述基本组件、扩展组件、特殊组件是PLC控制系统主要的三个部分。
其中,基本结构分为主流配置和箱体型两种,具体是根据可编程控制器类型的不同进行划分的。
CPU、内存、单电源、编辑器等共同组成了主流配置,其中还包括I/O模板、机架等部分。
其中系统的核心为CPU在系统中影响着整体的规模以及运行速度,同时其他组件的选择和工作也需要以CPU为主。
扩展组件则是在基础组件的基础上,结合实际生产需求增加的部分,例如扩展机箱以及扩展机架等部分,部分系统中还会增加系统I/O的点数。
相比其他组件来说,CPU、外部资源以及内存等能够在扩展配置的配合下形成更好的连接。
另外,我们可以选择使用远程扩展或者当地扩展,这样则能够更好地实现简化系统接线的效果,为后续系统的养护和维修创造良好条件。
部分生产系统中还需要PLC系统满足一些特殊的功能,这部分组件则被称为特殊组件。
我们一般按照功能对特殊组件进行分类,常见的有高速计数器单元、模拟输入与输出单元、成分监测单元等等。
在实际设计过程中,需要我们按照工艺的具体需求选择适合的组件,进而保证生产功能达到实际设计需求。
2系统总体研究与设计2.1系统控制需求分析1)多种操作模式:系统应具有自动控制、手动控制和远程控制模式。
在自动控制模式下,系统根据采集到的参数自动控制电机运行速度,调节供煤量。
当采用手动控制时,可手动完成系统的就地控制,作为设备维护或调整的工作方式。
自动配煤系统简介-II

煤矿用自动装车配煤控制系统简介由于煤矿矿井煤质构造比较复杂,影响煤质的因素较多,造成矿井煤质不稳定,波动性较大,难以符合不同用户的不同需要。
把不同质量的煤相互掺合,从而得到所需要的目标煤质,称为配煤。
对于采用两种煤质的配煤,就是将矸石以一定的比例混入原煤中,使混合后的煤的热值符合用户的要求。
本系统适合两种煤质的配煤,是利用灰分测试仪在线测试混合后煤的灰分,然后动态调节矸石的流量,使混合后的煤符合用户的要求。
对多种煤质的配煤,需重新设计,但原理一样。
一、基本原理在煤的掺合过程中,煤的质和量有以下数学模型A1*Q1+A2*Q2=A3*Q3 -------------①式中各变量的定义:A1-----原煤的产品灰分Q1-----原煤的产品流量A2-----矸石的产品灰分Q2-----矸石的产品流量第 1 页共7 页A3-----配完以后的目标灰分Q3-----配完以后的目标流量,Q3=Q1+Q2由①式可得出:A3=( A1*Q1+A2*Q2)/(Q1+Q2)由于灰分是表示煤中所含杂质的比例,故必须存在A2≥A3≥A1的条件,配煤才有实际意义,只要满足此条件,无论A1、Q1、A2具体的值是多少,都可以通过增加和减少Q2来达到希望的A3,见图1-1。
图1-1第 2 页共7 页第 3 页 共 7 页当A3被指定后,通过指定值和检测值的比较,适时调节矸石流入量,从而达到A3在一个允许的小误差范围内波动,实现配煤自动化。
由此我们可以设计出如图1-2所示的基本系统:图1-2二、系统框图第 4 页共7 页二、系统各单元介绍1.储煤仓储煤仓用来储存待配比的原煤和矸石,本系统最少需要两个储煤仓,分别储存原煤和矸石,如有多个储煤仓轮流使用,效果最好。
2.流量自动调节装置流量自动调节装置是位于储煤仓底部,用来关闭储煤仓和自动调节从煤仓流到传送皮带的煤的流量,由自动控制箱、液压站、液压闸板、位置传感器组成,可受中心站计算机集中控制,能够预置或根据需要自动调节液压闸门的开启位置,由此开启位置中心站计算机可以估算出煤的流量。
焦化智慧配煤系统设计方案

焦化智慧配煤系统设计方案设计方案名称:焦化智慧配煤系统设计方案设计方案概述:焦化智慧配煤系统是一种利用先进的信息技术、人工智能和大数据分析技术,对焦化炉原料煤进行智能化配比的系统。
该系统通过实时监测焦化炉的工艺参数,结合大数据分析,自动调控原料煤的配比比例,以实现最佳燃烧效果和生产效益的最大化。
设计方案详述:1. 系统硬件设施:焦化智慧配煤系统需要配备传感器、数据采集设备、智能控制设备等硬件设施,以实现对焦化炉的参数实时监测和控制。
其中,传感器用于采集焦化炉的温度、压力、流量等工艺参数,数据采集设备用于实时接收并传输这些参数数据,智能控制设备则是对数据进行分析和处理,并根据分析结果进行智能化控制。
2. 数据采集与传输:焦化智慧配煤系统需要建立一个完善的数据采集与传输网络,以确保参数数据能够及时、准确地传输到智能控制设备。
可以采用无线传输技术、以太网等方式进行数据传输,并配备数据传输设备(如路由器)进行数据的接收和传输。
3. 数据分析与建模:通过对焦化炉的工艺参数进行实时监测,并结合历史数据进行大数据分析和挖掘,建立合适的数据模型。
可以利用机器学习算法对数据进行训练和优化,以获取更准确的模型参数,并能够预测炉内煤炭燃烧状况。
同时,还可以利用数据分析技术进行故障诊断和预警,提前发现和处理潜在的问题。
4. 智能化控制:通过建立合适的控制算法,并结合数据模型和实时参数数据,对原料煤的配比比例进行智能化调控。
根据炉内煤炭的燃烧状态,动态调整煤的配比比例,以达到最优燃烧效果和生产效益的最大化。
可以通过控制参数的自动调整,实现对焦化过程的精细调控,提高炉内的煤炭利用率和燃烧效率。
5. 用户界面设计:设计一个直观、简洁的用户界面,方便操作人员进行参数设置和监控。
界面可以显示焦化炉的实时参数数据、数据分析结果等信息,并提供报警和故障诊断功能,以支持对炉内状况的实时监控和处理。
6. 系统集成和优化:焦化智慧配煤系统需要与现有的焦化炉控制系统进行集成,确保两个系统之间的数据传输和交互的稳定和高效。
火电厂数字化煤场智能掺配烧优化系统的设计方案和应用

火电厂数字化煤场智能掺配烧优化系统的设计方案和应用发布时间:2022-10-13T02:15:52.356Z 来源:《当代电力文化》2022年6月11期作者:王博[导读] 系统应用目的是通过最大化且合理的混烧低价煤种,从而降低电厂运行的燃料成本,提高全厂的经济效益;提供混烧状态下的优化运行建议王博中电(商丘)热电有限公司河南省商丘市476000摘要:系统应用目的是通过最大化且合理的混烧低价煤种,从而降低电厂运行的燃料成本,提高全厂的经济效益;提供混烧状态下的优化运行建议,从而保障锅炉混烧的安全,保证排放达标;提供信息化和自动化的煤场管理方法,从而规范燃料调度,保证混烧工作高效进行。
系统实现了煤场的可视化、网络化、数字化的管理,电厂节约了成本,提高了经济效益。
本文主要分析火电厂数字化煤场智能掺配烧优化系统的设计方案和应用。
关键词:数字化煤场;掺配烧,优化;决策模型;煤种引言为降低电厂能耗指标和生产经营成本,提高企业盈利能力,推进优化全过程成本管控工作,围绕节能降耗的要求,采取多项精细智能化管理方式,实现节能、自动化管理。
当锅炉入炉煤种多变、各煤质指标偏离设计值时,将影响锅炉燃烧的经济性和安全性。
数字化煤场智能掺配烧优化系统是一套关于燃煤机组多煤种混烧优化运行的软件系统,系统实现对电厂燃煤从进厂到燃烧的全流程管理,能对堆煤、存煤、配煤、取煤、燃烧、购煤等做出全自动的决策,此外,系统还能够对实现电厂煤场的数字化管理起到重要的支持作用。
1、建立煤场管理系统及多煤种掺配决策系统(1)煤场管理系统。
收集Mogens发电公司的煤场分布数据,结合煤场管理和运营方法,建立适合文发电公司的煤场管理系统,对煤量、热值、煤场数据、堆积场等进行全面有序的管理。
根据煤炭质量、数量、堆积位置,建立能够方便有效地完成煤炭运输人员煤炭运输工作的三维仿真。
结合配煤决策系统,对煤仓中不同煤种和煤质进行实时了解。
(2)各种配煤决策系统。
煤炭调度系统解决方案
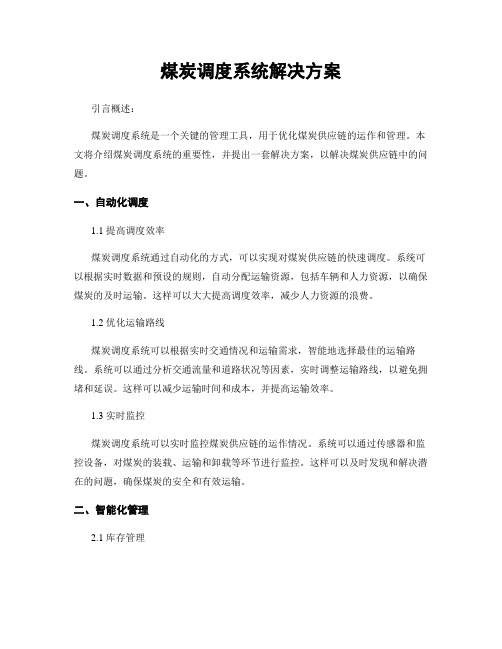
煤炭调度系统解决方案引言概述:煤炭调度系统是一个关键的管理工具,用于优化煤炭供应链的运作和管理。
本文将介绍煤炭调度系统的重要性,并提出一套解决方案,以解决煤炭供应链中的问题。
一、自动化调度1.1 提高调度效率煤炭调度系统通过自动化的方式,可以实现对煤炭供应链的快速调度。
系统可以根据实时数据和预设的规则,自动分配运输资源,包括车辆和人力资源,以确保煤炭的及时运输。
这样可以大大提高调度效率,减少人力资源的浪费。
1.2 优化运输路线煤炭调度系统可以根据实时交通情况和运输需求,智能地选择最佳的运输路线。
系统可以通过分析交通流量和道路状况等因素,实时调整运输路线,以避免拥堵和延误。
这样可以减少运输时间和成本,并提高运输效率。
1.3 实时监控煤炭调度系统可以实时监控煤炭供应链的运作情况。
系统可以通过传感器和监控设备,对煤炭的装载、运输和卸载等环节进行监控。
这样可以及时发现和解决潜在的问题,确保煤炭的安全和有效运输。
二、智能化管理2.1 库存管理煤炭调度系统可以智能地管理煤炭的库存。
系统可以根据实时需求和供应情况,自动计算和调整煤炭的库存量,以确保库存的合理和充足。
这样可以减少库存积压和资金占用,提高资金的利用效率。
2.2 供应链协同煤炭调度系统可以实现煤炭供应链的协同管理。
系统可以与供应商、运输商和客户等各方进行实时的信息交流和协作。
这样可以提高供应链的可见性和协同性,减少信息滞后和误差,提高整个供应链的效率和灵便性。
2.3 数据分析煤炭调度系统可以对煤炭供应链的数据进行分析和挖掘。
系统可以通过采集和整理各种数据,如运输时间、成本、质量等指标,进行数据分析和建模。
这样可以匡助企业了解和优化煤炭供应链的运作情况,提高决策的科学性和准确性。
三、安全保障3.1 风险预警煤炭调度系统可以通过实时监控和数据分析,对潜在的风险进行预警。
系统可以根据历史数据和模型,预测可能浮现的问题,如交通拥堵、车辆故障等。
这样可以提前采取相应的措施,减少风险的发生和影响。
智慧AI选煤系统设计方案
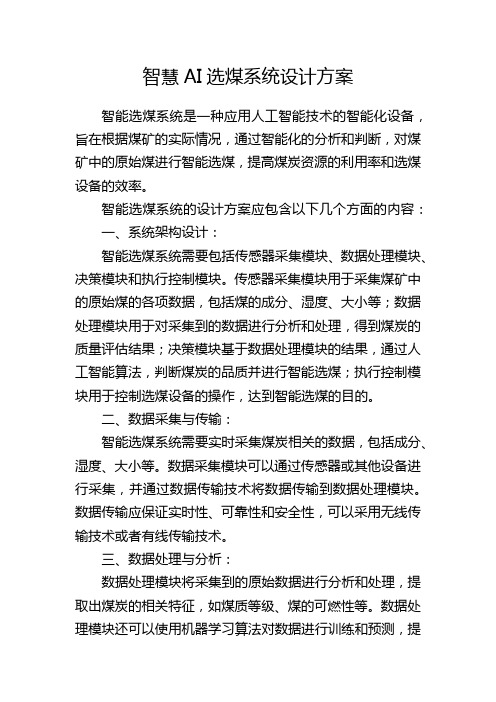
智慧AI选煤系统设计方案智能选煤系统是一种应用人工智能技术的智能化设备,旨在根据煤矿的实际情况,通过智能化的分析和判断,对煤矿中的原始煤进行智能选煤,提高煤炭资源的利用率和选煤设备的效率。
智能选煤系统的设计方案应包含以下几个方面的内容:一、系统架构设计:智能选煤系统需要包括传感器采集模块、数据处理模块、决策模块和执行控制模块。
传感器采集模块用于采集煤矿中的原始煤的各项数据,包括煤的成分、湿度、大小等;数据处理模块用于对采集到的数据进行分析和处理,得到煤炭的质量评估结果;决策模块基于数据处理模块的结果,通过人工智能算法,判断煤炭的品质并进行智能选煤;执行控制模块用于控制选煤设备的操作,达到智能选煤的目的。
二、数据采集与传输:智能选煤系统需要实时采集煤炭相关的数据,包括成分、湿度、大小等。
数据采集模块可以通过传感器或其他设备进行采集,并通过数据传输技术将数据传输到数据处理模块。
数据传输应保证实时性、可靠性和安全性,可以采用无线传输技术或者有线传输技术。
三、数据处理与分析:数据处理模块将采集到的原始数据进行分析和处理,提取出煤炭的相关特征,如煤质等级、煤的可燃性等。
数据处理模块还可以使用机器学习算法对数据进行训练和预测,提高煤质评估的准确性和可靠性。
数据处理模块还可以与数据库进行交互,提高数据的管理和查询效率。
四、决策和控制算法:智能选煤系统的决策和控制模块将根据数据处理模块的结果,使用人工智能算法对原始煤进行智能选煤。
决策和控制算法可以基于历史数据进行训练和优化,以提高选煤的准确性和效率。
决策和控制算法还可以根据不同的选煤要求进行自适应调整,以满足煤矿的实际需求。
五、设备集成与控制:智能选煤系统需要与选煤设备进行集成,并通过执行控制模块对设备进行控制。
设备集成可以通过接口的方式实现,以保证系统的兼容性和扩展性。
控制模块可以实现对设备的远程控制和调整,以满足煤矿现场的实际需求。
六、用户界面设计:智能选煤系统的用户界面需要符合煤矿作业人员的使用习惯和实际需求,界面设计应简洁、直观,并提供必要的操作和信息展示。
原煤预均化堆场智能化控制系统研发与应用

1 煤取料机智能控制系统该厂的煤取料机智能控制系统改造主要分为三项内容:无人值守和智能化巡检、设备在线检测和故障预警以及全自动取料系统,系统架构如图1所示。
图 1 煤取料机智能控制系统架构2 无人值守和智能化巡检无人值守和自动化巡检方面的改造主要保证原煤堆场堆料和取料过程中的人员安全和堆场设备的安全性。
2.1方案架构基于计算机的视觉处理是解决无人值守和智能化巡检的主要途径。
在硬件上安装视频监控系统,实现煤场360°视频捕捉,利用视觉分析技术,对刮板头尾链轮、刮板运行、轨道异物、耙车运行以及人员或车辆进入情况进行实时监控,监控系统架构如图2所示。
图 2 监控系统架构2.2实施方案煤取料机本体安装防爆红外一体机12台,分别监控取料机馈电受电器、两侧耙车行走轮、挡轮、耙车整体运行等情况。
原煤堆棚内安装防爆红外一体机6台,防爆球机4台,辅料堆棚安装枪式摄像机6台,高清球型一体机2台,实现全场360°监控。
摄像机采用防爆型,防护等级IP68,另对取料机机械手臂摄像机镜头加装辅助风自动清洁系统以确保镜头清晰度,可有效防止煤粉、粉尘进入。
搭建智能视频识别平台,通过目标监测、图像分割等深度学习方法,对进入不同区域的人或物进行判定,并通过信号给出不同的处理结果。
完整的视频分析系统还具备在线学习能力,能有效降低误报情况发生。
系统需要视频分析服务器一台并安装视频分析平台软件,软件可定制和二次开发。
刮板上下轨道间安装机械手辅助监控系统,系统由高精度广角摄像头(防爆变焦红外一体机)、3+1 轴机械臂、机械臂底座、巡检轨道、远程中央控制台、无线传输模块、机械手端 PLC、线缆桥架、接收端(机械臂端)电控系统 9 部分组成。
巡检人员在后台通过触摸屏操作实现摄像头的全景观察,并可以对发现的问题进行记录截屏,从而实现取料机刮板系统的全景后台监控。
在堆料机上安装视频监控系统一套,实现堆料机关键部位视频捕捉,对悬臂皮带、电气室、轨道两侧、堆料机两侧、以及人员或车辆进入情况进行实时监控。
西门子全集成称重系统解决方案在焦化配煤系统中的实现

焦化 自动 配 煤 系统 的 主要 功 能 :
于’73 0 L S —0 P C中 ,也可通过 E 2 0 远程 I T 0M / O方式集成于 S — 7 4 0 L /C 0 P CP S7中, 是一款具有 高精 度、高速称重功能的 P C扩 L 展模块 ,具有 与 SMATC s / C 7统一的设计平 台和 通讯功 I I 7P S
焦化 自动 配 煤 系 统 主 要 由称 重 给料机
、
数 据 采 集和 控制 系
。
统
、
电 气 控 制 系 统和 上 位 机 计 算 机
、
软 件 及 网 络等 构 成
图2
皮带 秤 是 称 重 给 料 机 的核 心 部 分
2《 测 )of堕r1《
』堕啦 麟
霉 嚣
焦化 自动 配煤系统 中一般要求 配料秤具 有 05 的精 .%
一
般地讲 , 配料所用的称重给料机的控制
器分为三种模式:单机控制 器、机组控制器和
P C型 控 制 器 。 L 单机控制 器一般采用和皮带秤配套的带控 制功能的积算仪或采用 以单片机技术为基础 的 控制器来实现 , 点是 配置 灵活 , 优 与称重给料 机一一对应 使用 , 一台设备 出现故障不影响其
传 感器 进 行检测 重 量
以 确 定皮 带 上 的 物 料 重 量 ; 装在 尾 部 滚
,
筒 或 旋转 设 备 上 的数 字式 测 速 传 感 器
l
,
该
弓言 ;
在 焦 碳 生 产 工 艺过 程 中
,
速 度 传感 器 的脉 冲输 出正 比 于 皮 带速 度 ; 速 度 信 号 与 重 量 信 号 起送 入 皮 带 给料 机 控 制 器 产 生 并 显 示 累计 量 / 时 流 量 给 瞬
焦化智慧配煤系统设计方案 (2)

焦化智慧配煤系统设计方案设计方案:一、背景介绍:焦化工厂是将煤焦化产物制成高质量焦炭的工艺过程。
而煤的品质对焦化工艺的影响很大,不同煤质的特点和含量对焦炭的质量和产量都有着直接的影响。
因此,智能配煤系统对于优化煤的配比、提高焦炭质量和产量非常重要。
二、系统设计目标:1. 智能化:通过引入先进的人工智能技术,实现智能化的配煤系统,提高煤的配比精准度和效率。
2. 自动化:减少人工操作,提高工作效率,降低人力成本。
3. 实时监测:对于煤质参数进行实时监测,及时反馈煤质的变化情况,使调整更加及时、准确。
4. 提高产能和品质:通过准确的配煤,优化煤质的组成,提高焦炭的质量和产能。
三、系统设计内容:1. 数据采集与监测:设计传感器网络,将各个焦化工序的煤质参数进行实时采集,并传输到数据中心。
2. 数据存储与处理:搭建数据中心,对采集到的煤质参数进行分析和存储,形成历史数据。
3. 智能化算法:通过对历史数据的分析和建模,开发智能化配煤算法。
根据焦炭质量和产能的要求,通过算法计算出最佳的煤质组成。
4. 控制系统:将智能化配煤算法应用在控制系统中,实现自动化控制。
根据焦炭生产的实际需求,自动调整煤的配比。
5. 报警与反馈:当煤质参数超过阈值范围时,系统自动进行报警,并及时反馈给操作人员。
6. 可视化界面:设计直观的可视化界面,显示煤质参数的实时变化情况和系统的运行状态,方便操作人员进行监控和调整。
四、技术支持:1. 人工智能技术:采用机器学习、深度学习等先进技术,对大量的煤质参数数据进行分析和建模,提高配煤精准度和效率。
2. 传感器技术:选择合适的传感器,对煤质参数进行实时监测和采集,确保数据的准确性和实时性。
3. 数据处理技术:利用大数据技术对采集到的煤质参数进行存储、分析和处理,形成有价值的数据,并提供给智能化算法使用。
4. 控制系统技术:采用先进的控制系统技术,将智能化配煤算法嵌入到控制系统中,实现自动化控制。
基于智能燃料管控平台的智能配煤系统设计

基于智能燃料管控平台的智能配煤系统设计
唐士奇;陈静;单存鑫;胡辉;寿志杰
【期刊名称】《今日制造与升级》
【年(卷),期】2024()1
【摘要】基于智能燃料管控平台,研究开发了智能配煤系统,通过配煤规则引擎、智能配煤预测模型、可取煤堆识别、配煤方案综合评价等模块设计,依据当前工况自动生成有效的配煤方案和作业工单,有效提高了电厂机组上煤决策效率,为发电机组提供安全、经济、环保运行提供保障。
相关人员通过在实际燃煤电厂中应用智能配煤系统,验证了该设计的有效性和可行性,取得了良好效果。
【总页数】3页(P62-64)
【作者】唐士奇;陈静;单存鑫;胡辉;寿志杰
【作者单位】江苏射阳港发电有限责任公司;杭州集益科技有限公司
【正文语种】中文
【中图分类】TM621
【相关文献】
1.基于综合智能管控平台的主运皮带集控系统设计
2.基于燃料流程精准管理的智能管控系统设计
3.基于人工智能分析的配网工程全过程数字化管控平台
4.基于物联网技术的配网设备智能巡检管控平台研究与应用
5.基于煤场斗轮机智能集控技术的配煤掺烧专家系统的研究
因版权原因,仅展示原文概要,查看原文内容请购买。
自动化配煤工艺流程图
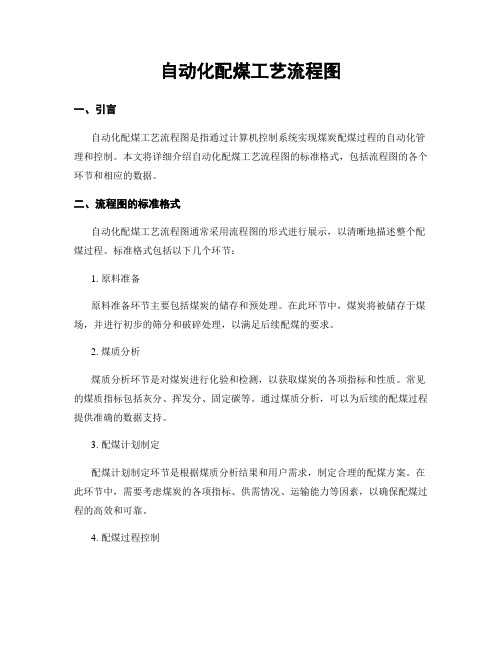
自动化配煤工艺流程图一、引言自动化配煤工艺流程图是指通过计算机控制系统实现煤炭配煤过程的自动化管理和控制。
本文将详细介绍自动化配煤工艺流程图的标准格式,包括流程图的各个环节和相应的数据。
二、流程图的标准格式自动化配煤工艺流程图通常采用流程图的形式进行展示,以清晰地描述整个配煤过程。
标准格式包括以下几个环节:1. 原料准备原料准备环节主要包括煤炭的储存和预处理。
在此环节中,煤炭将被储存于煤场,并进行初步的筛分和破碎处理,以满足后续配煤的要求。
2. 煤质分析煤质分析环节是对煤炭进行化验和检测,以获取煤炭的各项指标和性质。
常见的煤质指标包括灰分、挥发分、固定碳等。
通过煤质分析,可以为后续的配煤过程提供准确的数据支持。
3. 配煤计划制定配煤计划制定环节是根据煤质分析结果和用户需求,制定合理的配煤方案。
在此环节中,需要考虑煤炭的各项指标、供需情况、运输能力等因素,以确保配煤过程的高效和可靠。
4. 配煤过程控制配煤过程控制环节是通过自动化控制系统对配煤过程进行实时监测和控制。
在此环节中,计算机控制系统将根据配煤计划和煤质分析结果,自动调节煤炭的投放量和比例,以确保配煤的准确性和稳定性。
5. 配煤结果检测配煤结果检测环节是对配煤结果进行实时监测和检测,以验证配煤的准确性和合格性。
在此环节中,通过传感器和仪表设备对配煤结果进行监测,并将数据反馈给自动化控制系统,以实现闭环控制。
6. 数据记录和报表生成数据记录和报表生成环节是将配煤过程中的各项数据进行记录和整理,并生成相应的报表。
在此环节中,自动化控制系统将自动记录和保存配煤过程中的各项数据,并生成配煤报表,以供后续分析和评估使用。
三、数据示例为了更好地说明自动化配煤工艺流程图的标准格式,下面给出一个数据示例:1. 原料准备- 煤场储存容量:10000吨- 筛分粒度:50mm- 破碎设备数量:2台2. 煤质分析- 灰分:15%- 挥发分:25%- 固定碳:60%3. 配煤计划制定- 配煤量:500吨/天- 配煤比例:A煤30%、B煤40%、C煤30%- 供需情况:满足用户需求4. 配煤过程控制- 自动化控制系统:PLC控制系统- 控制方式:闭环控制- 投放量调节范围:0-1000吨/小时5. 配煤结果检测- 检测设备:灰分仪、挥发分仪、固定碳仪- 检测精度:灰分±0.5%、挥发分±0.5%、固定碳±1%6. 数据记录和报表生成- 数据记录方式:自动记录- 报表生成频率:每天生成一次- 报表内容:煤质分析报表、配煤结果报表四、结论自动化配煤工艺流程图的标准格式包括原料准备、煤质分析、配煤计划制定、配煤过程控制、配煤结果检测和数据记录与报表生成等环节。
煤炭智慧管控系统设计方案

煤炭智慧管控系统设计方案设计方案:煤炭智慧管控系统背景介绍:煤炭是我国主要的能源来源,但传统的煤炭开采和管理方式存在一系列问题,如煤矿事故频发、煤炭资源浪费等。
为了提高煤炭的开采效率和管理水平,减少安全事故的发生,需要引入先进的信息技术,设计一个煤炭智慧管控系统。
系统目标:1. 提高煤炭开采的效率和质量;2. 降低煤矿事故的发生率;3. 提高煤炭资源的利用率;4. 提高煤炭生产的安全性。
系统功能:1. 煤炭开采监控:通过安装传感器和摄像头等设备,实时监控煤炭开采过程,并将数据传输到中央服务器。
可以监测煤矿的温度、湿度、气体浓度等参数,及时发现异常情况。
2. 煤矿安全预警:根据传感器监测到的数据,系统可以自动分析风险,并发送预警信息,及时采取措施避免事故发生。
例如,当检测到煤矿内气体浓度异常升高时,系统会向相关人员发送紧急警报。
3. 资源管理:系统可以实时统计煤炭的产量、库存等信息,为矿工和管理人员提供准确的数据参考。
通过分析数据,可以合理规划煤炭开采计划,提高资源利用率。
4. 物联网技术应用:系统可以通过物联网技术连接各种设备和传感器,实现设备间的数据共享和自动化控制。
例如,可以实现自动化的运输系统,将煤炭从矿井运送至储存区。
5. 数据分析与挖掘:系统可以对煤炭开采和管理的数据进行分析和挖掘,提供决策支持。
例如,通过分析历史数据,可以预测煤炭开采的潜在风险,并制定相应的管理措施。
系统架构:1. 传感器和设备层:包括温度传感器、湿度传感器、气体浓度传感器、摄像头等设备。
这些设备负责采集煤矿的数据,并将数据传输到中央服务器。
2. 通信网络层:负责设备间的数据传输,可以采用有线或无线通信方式。
可以利用现有的通信网络,如互联网、局域网等。
3. 服务器层:中央服务器负责接收和存储传感器采集的数据,并进行数据处理和分析。
可以使用云计算技术,实现大数据存储和处理。
4. 应用层:用户可以通过手机、电脑等设备访问系统,查看和管理煤炭开采的相关信息。
火电厂数字化煤场智能掺配烧优化系统的设计方案和应用
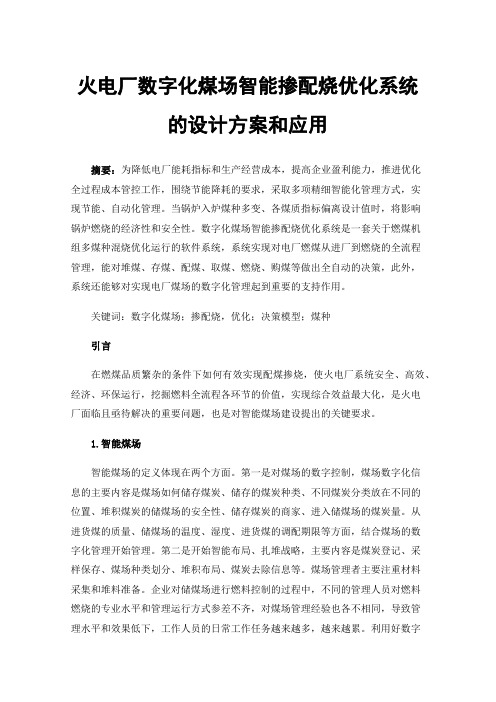
火电厂数字化煤场智能掺配烧优化系统的设计方案和应用摘要:为降低电厂能耗指标和生产经营成本,提高企业盈利能力,推进优化全过程成本管控工作,围绕节能降耗的要求,采取多项精细智能化管理方式,实现节能、自动化管理。
当锅炉入炉煤种多变、各煤质指标偏离设计值时,将影响锅炉燃烧的经济性和安全性。
数字化煤场智能掺配烧优化系统是一套关于燃煤机组多煤种混烧优化运行的软件系统,系统实现对电厂燃煤从进厂到燃烧的全流程管理,能对堆煤、存煤、配煤、取煤、燃烧、购煤等做出全自动的决策,此外,系统还能够对实现电厂煤场的数字化管理起到重要的支持作用。
关键词:数字化煤场;掺配烧,优化;决策模型;煤种引言在燃煤品质繁杂的条件下如何有效实现配煤掺烧,使火电厂系统安全、高效、经济、环保运行,挖掘燃料全流程各环节的价值,实现综合效益最大化,是火电厂面临且亟待解决的重要问题,也是对智能煤场建设提出的关键要求。
1.智能煤场智能煤场的定义体现在两个方面。
第一是对煤场的数字控制,煤场数字化信息的主要内容是煤场如何储存煤炭、储存的煤炭种类、不同煤炭分类放在不同的位置、堆积煤炭的储煤场的安全性、储存煤炭的商家、进入储煤场的煤炭量。
从进货煤的质量、储煤场的温度、湿度、进货煤的调配期限等方面,结合煤场的数字化管理开始管理。
第二是开始智能布局、扎堆战略,主要内容是煤炭登记、采样保存、煤场种类划分、堆积布局、煤炭去除信息等。
煤场管理者主要注重材料采集和堆料准备。
企业对储煤场进行燃料控制的过程中,不同的管理人员对燃料燃烧的专业水平和管理运行方式参差不齐,对煤场管理经验也各不相同,导致管理水平和效果低下,工作人员的日常工作任务越来越多,越来越累。
利用好数字管理系统,引入故障排除方案,建立能源管理库,运用简单的思维方式,有助于收集煤炭,快速投入火炉。
2系统设计流程系统设计原理图如图1所示,系统应能实现时刻监视当前的制粉系统运行状况和锅炉燃烧及排放情况,在预定的优化目标下,通过实时优化程序和专家系统,对制粉系统和燃烧器运行做出优化调整,保证锅炉处于最佳的运行状态。
- 1、下载文档前请自行甄别文档内容的完整性,平台不提供额外的编辑、内容补充、找答案等附加服务。
- 2、"仅部分预览"的文档,不可在线预览部分如存在完整性等问题,可反馈申请退款(可完整预览的文档不适用该条件!)。
- 3、如文档侵犯您的权益,请联系客服反馈,我们会尽快为您处理(人工客服工作时间:9:00-18:30)。
图1常规混配煤中的堆场直混配煤工艺示意图常规混配煤中的筒仓混配煤,也是常规混配煤方式之[2]。
如图2所示为常规混配煤中的筒仓混配煤工艺示意图。
根据图中信息显示,此种混配煤方式,是在现有对取料设备的前提下,将筒仓系统旁路增加到设备中。
若需要对
图1甲醇在汽油中的互溶度与环境温度的关系[1]
艺方案,对于日后提高工作效率和精度性,具有重要的作针对当前在线高精度自动混配煤工艺系统设计应用的现状,本文在研究中通过该对常规混配煤方案的分析,讨了高精度自动混配煤优化方案。
同时,从取料、输送切换。