钢套箱设计和施工组织方案
有底钢套箱设计与施工要点控制
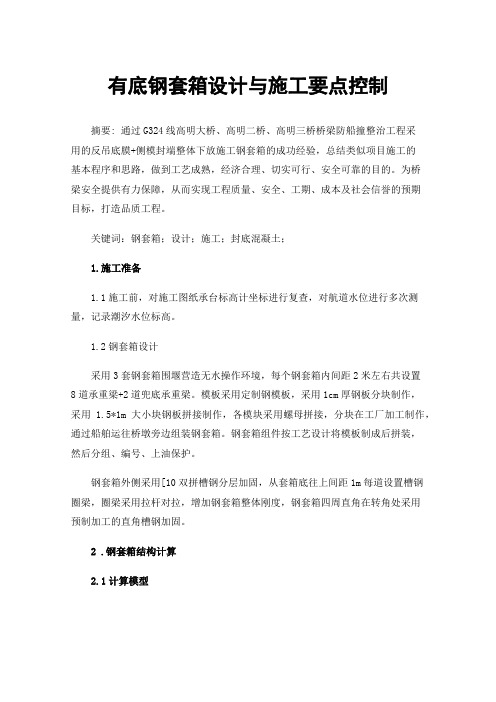
有底钢套箱设计与施工要点控制摘要: 通过G324线高明大桥、高明二桥、高明三桥桥梁防船撞整治工程采用的反吊底膜+侧模封端整体下放施工钢套箱的成功经验,总结类似项目施工的基本程序和思路,做到工艺成熟,经济合理、切实可行、安全可靠的目的。
为桥梁安全提供有力保障,从而实现工程质量、安全、工期、成本及社会信誉的预期目标,打造品质工程。
关键词:钢套箱;设计;施工;封底混凝土;1.施工准备1.1施工前,对施工图纸承台标高计坐标进行复查,对航道水位进行多次测量,记录潮汐水位标高。
1.2钢套箱设计采用3套钢套箱围堰营造无水操作环境,每个钢套箱内间距2米左右共设置8道承重梁+2道兜底承重梁。
模板采用定制钢模板,采用1cm厚钢板分块制作,采用 1.5*1m大小块钢板拼接制作,各模块采用螺母拼接,分块在工厂加工制作,通过船舶运往桥墩旁边组装钢套箱。
钢套箱组件按工艺设计将模板制成后拼装,然后分组、编号、上油保护。
钢套箱外侧采用[10双拼槽钢分层加固,从套箱底往上间距1m每道设置槽钢圈梁,圈梁采用拉杆对拉,增加钢套箱整体刚度,钢套箱四周直角在转角处采用预制加工的直角槽钢加固。
2.钢套箱结构计算2.1计算模型钢套箱采用midas有限元分析软件进行计算,采用三维空间建模,对套箱各个构件赋予各自材料特性,荷载均采用面荷载进行加载,对套箱强度及刚度进行验算。
图2.1-1 钢套箱计算模型2.2荷载及工况分析因为围堰四周设置操作平台,漂浮物及船舶对围堰的撞击可以忽略,围堰受到的主要荷载为自重、静水压力、水流力、浮力等,荷载分项系数为:自重 1.2,外侧静水压力1.4,流水压力1.4,浮力1.0。
2.3计算结果套箱各构件的计算结果如下表:表2.3-1钢套箱计算结果汇总表2.4计算结论从上计算可知,钢套箱强度和刚度是满足规范要求的,结构安全可靠,能满足高明大桥水中承台在各种工况条件下施工的要求。
3.钢套箱制作3.1主要材料配置3.1.1施工所需材料按照结构计算结果及生产计划详细规划进行采购,材料进场时检查外形尺寸及其质量保证书的完整性,进场的材料分类进行堆放,并做好标识。
某铁路特大桥钢套箱施工方案
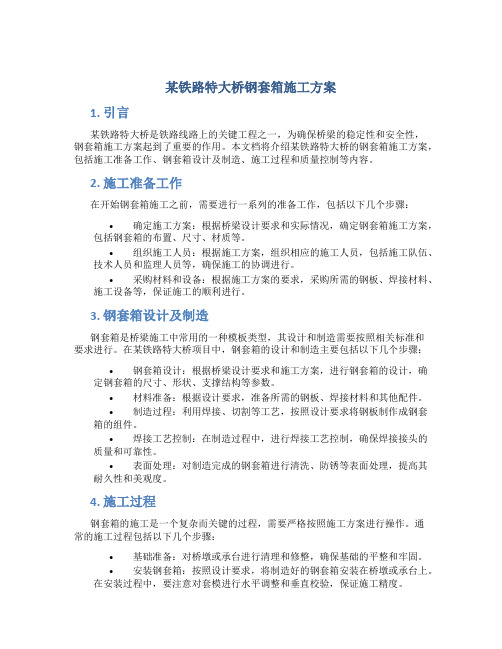
某铁路特大桥钢套箱施工方案1. 引言某铁路特大桥是铁路线路上的关键工程之一,为确保桥梁的稳定性和安全性,钢套箱施工方案起到了重要的作用。
本文档将介绍某铁路特大桥的钢套箱施工方案,包括施工准备工作、钢套箱设计及制造、施工过程和质量控制等内容。
2. 施工准备工作在开始钢套箱施工之前,需要进行一系列的准备工作,包括以下几个步骤:•确定施工方案:根据桥梁设计要求和实际情况,确定钢套箱施工方案,包括钢套箱的布置、尺寸、材质等。
•组织施工人员:根据施工方案,组织相应的施工人员,包括施工队伍、技术人员和监理人员等,确保施工的协调进行。
•采购材料和设备:根据施工方案的要求,采购所需的钢板、焊接材料、施工设备等,保证施工的顺利进行。
3. 钢套箱设计及制造钢套箱是桥梁施工中常用的一种模板类型,其设计和制造需要按照相关标准和要求进行。
在某铁路特大桥项目中,钢套箱的设计和制造主要包括以下几个步骤:•钢套箱设计:根据桥梁设计要求和施工方案,进行钢套箱的设计,确定钢套箱的尺寸、形状、支撑结构等参数。
•材料准备:根据设计要求,准备所需的钢板、焊接材料和其他配件。
•制造过程:利用焊接、切割等工艺,按照设计要求将钢板制作成钢套箱的组件。
•焊接工艺控制:在制造过程中,进行焊接工艺控制,确保焊接接头的质量和可靠性。
•表面处理:对制造完成的钢套箱进行清洗、防锈等表面处理,提高其耐久性和美观度。
4. 施工过程钢套箱的施工是一个复杂而关键的过程,需要严格按照施工方案进行操作。
通常的施工过程包括以下几个步骤:•基础准备:对桥墩或承台进行清理和修整,确保基础的平整和牢固。
•安装钢套箱:按照设计要求,将制造好的钢套箱安装在桥墩或承台上。
在安装过程中,要注意对套模进行水平调整和垂直校验,保证施工精度。
•钢箱槽浇筑:在钢套箱内部进行混凝土的浇筑,形成桥梁的梁体部分。
在浇筑过程中,要注意混凝土的均匀性和浇筑速度的控制。
•后续处理:待混凝土充分凝固后,进行钢套箱的拆除和清理,同时对桥梁进行检验和修整,以保证其满足使用要求。
钢套箱施工方案

钢套箱施工方案钢套箱施工方案1、施工方案的说明由于施工场地为淤泥状填土,施工条件较复杂。
在施工中应密切注意支护效果,认真分析边坡情况,发现问题可根据现场实际情况对本方案作适当调整。
2、施工目标适用、安全、满足下道工序施工要求。
3、施工工艺流程预制钢板沉井校正垂直度位置抽水清理作业面吊装就位加支撑挖土(泥)下沉继续挖土(泥)直至下沉到底加载下沉(1)抽水采用污水泵抽水将施工场地积水抽出排到河中,并随时将施工过程中渗透水抽出。
(2)清理作业面场地积水抽出后,即下人清理作业面,达到沉井吊放要求。
(3)预制钢板沉井制作钢板沉井采用h=8mm钢板预制,1.5m为一节,要求制作标准,水平和垂直方向均符合设计要求,焊缝平齐无渗漏。
(4)吊装就位并校正垂直度及位置场地平整好后,在平整好的场地上放入沉井位置,允许偏差±5cm,定好位置后用吊车将预制好的钢板沉井精确吊放就位,并在吊放过程中,不断调整并校正垂直度,要求垂直度偏差≤0.50%,挖土下沉过程中,用线缀适时的标定垂直以指导施工。
(5)挖土(泥)下沉在就位校正好垂直度后,即挖土(泥)下沉,下沉过程中,应保证下沉均匀、均衡,保证垂直度。
每下沉1m后加支撑一道。
(6)加载下沉当侧阻力较大下沉困难时应用加载下沉的方式,以保证顺利下沉到规定的标高,加载方式采用吊车吊重物加载或堆土加载。
如此进行直至下沉至规定高度在下沉过程中应根据情况及时加支撑。
(7)施工中应注意的问题1)10号墩前期施工中曾经打入木桩,后来产生滑移。
在施工中10号沉井下沉过程中可能会遇到阻碍,应对木桩清除,使其不影响施工。
埋深较浅的桩则可用吊车予以清除。
2)施工完毕后,回填土清除时,应尽可能用吊车将沉井回收,减少材料的浪费。
但再次利用的可能性不大,施工组织上不再安排回收钢板沉井的利用。
二、施工组织计划(一)、劳动力组织根据所承担的工程量所需,劳动力配置如下所示:工种焊工电工技术工人人数4126(二)、设备计划1、主要施工设备一览表序号设备名称设备型号设备功率设备台数1电焊机BX1-300-132手推车33其他若干2、设备进场计划施工中所有设备均在开工前进场。
钢套箱围堰安全施工方案

钢套箱围堰安全施工方案钢套箱围堰是一种用于城市建设和基础设施施工中的一种围堰方式,它能有效地隔离工地和周围环境,保持施工现场的安全和卫生。
钢套箱围堰施工需要严格遵守施工方案,以确保施工过程的安全性。
以下是一份钢套箱围堰安全施工方案的例子:1. 前期准备工作1.1 确定施工现场范围,并与周围居民和企业进行沟通,征得他们的同意和支持。
1.2 安排专业人员进行现场勘察和测量,确定围堰的位置和大小。
1.3 根据勘察结果确定所需的钢套箱数量和规格。
1.4 联系供应商,确保钢套箱及相关器材的按时供应。
2. 施工前的安全措施2.1 制定施工安全计划,明确责任分工和安全要求。
2.2 建立施工现场警示标识,明确施工区域和危险区域。
2.3 培训施工人员,确保他们了解施工规范和安全操作流程。
2.4 确保施工现场的通风、照明和排水设施正常运行。
3. 施工过程中的安全控制3.1 安全设施搭建:根据施工现场布置,搭建围堰的钢套箱,并确保其稳固和牢固。
3.2 钢套箱连接:使用专业工具和固定器材进行钢套箱的连接,以确保其紧密性和稳定性。
3.3 地基处理:在施工现场的地基上进行必要的处理,确保地基平整和稳固。
3.4 挡土墙施工:根据围堰设计方案,以及现场土质条件和坡度要求,进行挡土墙的施工,确保挡土墙的稳定性和密封性。
3.5 环境保护:采取措施防止施工过程中产生的污水、粉尘和噪音对周围环境的影响。
严禁将施工废弃物排放到河流或其他水域中。
3.6 施工区域管控:设立施工区域的出入口,并设置安全警示标识,指示施工区域的边界和危险区域。
4. 施工后的安全控制4.1 定期检查:定期对围堰进行检查和维护,确保其稳定性和安全性。
4.2 清理施工废弃物:及时清理施工现场的废弃物和杂物,保持施工现场的整洁和卫生。
4.3 解体拆除:在施工结束后,根据相关规范和要求,对围堰进行解体和拆除。
本文仅为钢套箱围堰安全施工方案的一个例子,实际施工中需要根据具体情况进行调整和完善。
2024年钢套箱围堰安全施工方案
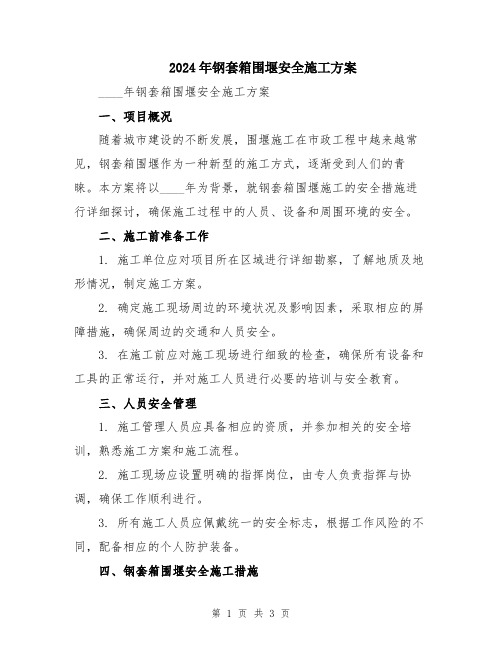
2024年钢套箱围堰安全施工方案____年钢套箱围堰安全施工方案一、项目概况随着城市建设的不断发展,围堰施工在市政工程中越来越常见,钢套箱围堰作为一种新型的施工方式,逐渐受到人们的青睐。
本方案将以____年为背景,就钢套箱围堰施工的安全措施进行详细探讨,确保施工过程中的人员、设备和周围环境的安全。
二、施工前准备工作1. 施工单位应对项目所在区域进行详细勘察,了解地质及地形情况,制定施工方案。
2. 确定施工现场周边的环境状况及影响因素,采取相应的屏障措施,确保周边的交通和人员安全。
3. 在施工前应对施工现场进行细致的检查,确保所有设备和工具的正常运行,并对施工人员进行必要的培训与安全教育。
三、人员安全管理1. 施工管理人员应具备相应的资质,并参加相关的安全培训,熟悉施工方案和施工流程。
2. 施工现场应设置明确的指挥岗位,由专人负责指挥与协调,确保工作顺利进行。
3. 所有施工人员应佩戴统一的安全标志,根据工作风险的不同,配备相应的个人防护装备。
四、钢套箱围堰安全施工措施1. 前期准备:在施工前进行充分的安全交底,让施工人员了解围堰施工的危险性和安全要求,确保每个人都具备安全意识。
2. 施工设备:确保施工设备的齐全、完好,并进行详细检查,如有故障需及时修理或更换。
3. 围堰支撑:严格按照设计要求进行围堰支撑,确保围堰的稳定性,避免倒塌事故的发生。
4. 施工工艺:采用科学合理的施工工艺,避免冲击、振动等对围堰的影响,确保围堰的安全性。
5. 施工作业:所有施工人员必须按照规定进行作业,严禁擅自更改工艺或操作方式,杜绝操作失误导致的事故发生。
6. 安全监控:设置安全监控岗位,对施工现场进行全天候监控,一旦发现异常情况,立即采取相应的应急措施。
7. 废弃物处理:及时清理施工现场产生的废弃物,保持施工现场的整洁,减少安全隐患。
8. 安全培训:定期组织安全培训,提高施工人员的安全意识和应急处理能力,确保他们能够正确应对突发事件。
钢套箱施工方案

撑架桥水中承台施工方案一、执行标准和依据1、编制依据1)《南通市干线公路2013年危桥改造工程招标文件》;2)《公路工程质量检验评定标准》;3)《公路桥涵施工技术规范》;4) 交通部颁布的相关施工技术规范和规程;5)南通市干线公路2013年危桥改造工程《施工图设计》。
2、工程概况撑架桥位于S336线省道K41+741处,位于启东市新港镇。
由于北幅V型撑架桥斜撑杆因严重压缩通航净空,经常受船只碰撞,撑杆撞损严重,砼破损、主筋外露,需进行北幅撑架桥拆除新建,下部构造为Φ1.0m钻孔灌注桩,承台基础。
1#、2#墩处在河道中心,在施工期间主航道需通航。
承台尺寸长7.1m,宽5m,高1.8m (承台底面高程为0.1m,顶面高程为1.9m),一个承台工程量为钢筋8t,混凝土63.9m3。
靠主航道外侧河道水深4.5m左右,内侧水深2.5m左右,河道常水位标高 1.4m,根据现场实际情况,拟采用钢套箱施工,钢套箱尺寸长8m,宽6m,外侧高6.75m,内侧高4.75m,钢板厚度6mm,侧板设置竖肋(12#槽钢)、横向加强板(扁钢)。
二、总体组织安排1、组织机构设置:见组织机构网络图;2、施工现场人力资源配置:(1)管理人员项目经理:朱卫兵技术负责人:陆凤美试验员:钱辉技术员:蔡伟伟安全员:侯江华资料员:蔡伟伟施工负责人:陶林冬施工队长:张新华(2)主要劳动力配置3、原材料⑴、钢套箱:采用6mm厚钢板拼装而成,各项指标达到国家规范要求;⑵、混凝土:采用强制式机械拌合的C30混凝土,使用前已做好原材料检测、配合比设计及配合比验证。
⑶、钢材:采用江苏沙钢集团生产的并经检验合格、监理抽检合格的钢筋。
4、主要检测仪器、施工机具准备:见附表四、质量保证体系1、质量目标:合格率100%,优良率100%.2、质量保证体系网络:见质量保证体系网络图。
五、钢套箱设计1.结构设计⑴、根据常水位 (1.4m)及水深(靠主航道外侧河道水深 4.5m左右,内侧水深2.5m左右),选用钢套箱外侧高度6.75m,内侧4.75m,钢套箱整体焊接成型。
主桥承台钢套箱施工方案3

主桥承台钢套箱施工方案3
一、前言
本文主要介绍了主桥承台钢套箱的施工方案,重点讨论了第三种施工方式的具
体步骤和注意事项,希望能为相关工程施工提供参考和指导。
二、施工方案概述
主桥承台钢套箱是桥梁工程中常见的一种施工方式,能够有效提高工程施工效
率和质量。
本方案主要采用传统的施工工艺,结合现场具体情况,制定了详细的施工方案。
三、施工步骤
1.准备工作:施工前应做好场地清理和安全防护工作,确保施工安全。
2.浇筑底板:首先在承台上浇筑一层混凝土底板,作为钢套箱的基础。
3.安装钢套箱:将预制的钢套箱按照设计要求安装在底板上。
4.浇筑混凝土:在钢套箱内部浇筑混凝土,填满整个空间。
5.拆除钢套箱:待混凝土充分凝固后,拆除钢套箱。
6.收尾工作:完成拆除后,进行清理和整理工作,确保施工场地干净
整洁。
四、注意事项
1.施工过程中,要严格按照设计图纸和施工方案执行,确保工程质量。
2.在浇筑混凝土时,注意控制浇筑速度和浇注方式,避免出现空洞和裂
缝。
3.施工现场应设置专人负责监督,并配备好必要的安全设施和器材。
五、结语
以上就是主桥承台钢套箱施工方案的具体内容,希望能对相关工程的施工提供
一定的帮助。
在施工过程中,要严格按照方案要求执行,确保工程的顺利进行和质量的保障。
钢套箱施工方案

吉莲高速公路A3标禾水河大桥主墩钢套箱设计与施工方案中交二公局第一工程有限公司吉莲高速公路A3标项目经理部二O一一年四月目录第一章工程概况 (1)1.工程概况 (1)1.1承台结构 (1)1.2水文条件 (1)2.钢套箱结构 (1)2.1(2#)主墩钢套箱 (1)2.2(3#)主墩钢套箱 (3)第二章钢套箱施工方案 (6)1.施工综述 (6)2.钢套箱加工 (7)2.1工艺流程 (7)2.2原材料 (8)2.3加工精度 (8)2.4焊缝检验 (9)3.钢套箱拼装 (9)3.1拼装前准备工作 (9)3.2钢套箱拼装 (9)4.钢套箱下放 (9)5钢套箱封底 (10)5.1钢套箱底板封堵 (10)5.2水下封底混凝土浇筑 (11)6钢套箱抽水 (11)6.1钢套箱内抽水 (11)6.2承台钢筋混凝土施工准备工作 (12)第一章工程概况1.工程概况1.1承台结构禾水河大桥2#、3#主墩承台尺寸为10.8m×10.8m×4.2m,采用C30混凝土。
单个承台混凝土方量为490m3。
2#墩承台顶高程为87.7m,底高程为83.5m,封底混凝土厚度1m (C25)。
3#墩承台顶高程为85m,底高程为80.8m,封底混凝土厚度1.5m。
1.2水文条件河水水位是钢套箱封底的重要控制因素,主墩承台封底计划于2011年6月施工,根据目前施工水位(约85.0m),2#墩钢套箱底板位于水面以下2.5m,3#墩钢套箱底板位于水面以下5.7m。
2.钢套箱结构2.1(2#)主墩钢套箱2#主墩钢套箱为单壁结构,单边侧板长10.8m,高度5.2m。
总体布置如图2.1-1~2所示:图2.1-1 2#墩钢套箱立面布置图图2.1-2 2#墩钢套箱平面布置图2.1.1底板底板总厚26.6cm,面板厚6mm,主梁采用2[28b型钢,次梁采用12.6工钢,间距50cm,如图2.1-3所示。
图2.1-3 2#墩钢套箱底板构造图2.1.2壁板仓壁采用单壁结构形式,高度5.2m。
套箱施工方案范文
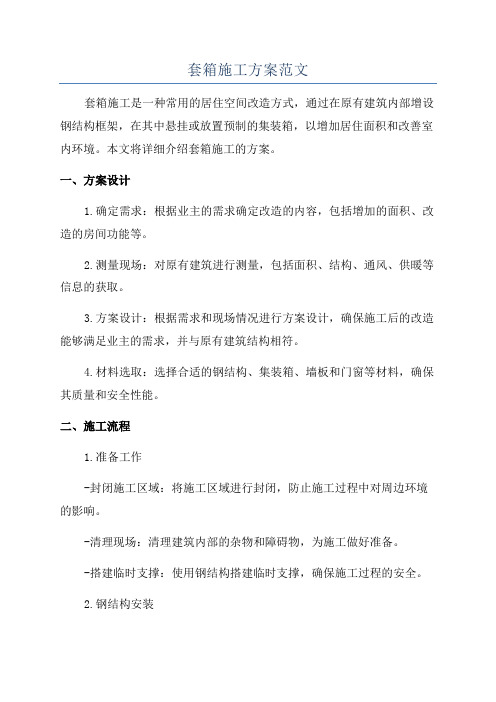
套箱施工方案范文套箱施工是一种常用的居住空间改造方式,通过在原有建筑内部增设钢结构框架,在其中悬挂或放置预制的集装箱,以增加居住面积和改善室内环境。
本文将详细介绍套箱施工的方案。
一、方案设计1.确定需求:根据业主的需求确定改造的内容,包括增加的面积、改造的房间功能等。
2.测量现场:对原有建筑进行测量,包括面积、结构、通风、供暖等信息的获取。
3.方案设计:根据需求和现场情况进行方案设计,确保施工后的改造能够满足业主的需求,并与原有建筑结构相符。
4.材料选取:选择合适的钢结构、集装箱、墙板和门窗等材料,确保其质量和安全性能。
二、施工流程1.准备工作-封闭施工区域:将施工区域进行封闭,防止施工过程中对周边环境的影响。
-清理现场:清理建筑内部的杂物和障碍物,为施工做好准备。
-搭建临时支撑:使用钢结构搭建临时支撑,确保施工过程的安全。
2.钢结构安装-建造钢结构框架:根据设计方案,先进行地面的布置和调整,然后搭建钢结构框架,并进行固定。
-加固钢结构框架:在钢结构框架的主要节点和连接处进行加固,以确保整个结构的稳定性。
3.集装箱安装-集装箱准备:对集装箱进行清理和检查,确保其完好无损和安全使用。
-集装箱运输:使用吊车或起重机将集装箱运送到施工现场。
-集装箱安装:将集装箱放置在钢结构框架内,根据设计方案进行固定和连接。
4.划分空间-墙体建造:根据设计方案,安装墙板,并进行固定和封闭。
-安装门窗:根据需求和设计方案,安装门窗,并确保其安全和密封性能。
5.内部装修-地面处理:根据需求选择合适的地板材料,进行铺设和固定。
-天花板安装:根据设计方案进行天花板的安装和固定。
-水电施工:进行水电设施的施工和布置,包括供水、排水和电气设备等。
-内部装修:根据业主需求进行室内装修,包括墙面装饰、天花板、照明、空调等。
6.环境整治-清理施工垃圾:对施工现场进行清理,清除垃圾和杂物。
-安全检查:对套箱改造后的建筑进行安全检查,确保其稳定性和人员的安全。
承台钢套箱施工方案

承台钢套箱施工方案
1.准备工作
在进行承台钢套箱施工之前,首先需要做好准备工作。
包括测量、确
定承台尺寸和位置、清理施工场地、搭建施工场地的支撑框架等。
2.制作承台钢套箱
3.安装承台钢套箱
在进行承台钢套箱的安装时,需要先确定好其位置和水平度。
将承台
钢套箱放置在准备好的施工场地上,然后使用水平仪进行调整,使其水平
度达到要求。
在安装过程中,需要注意保持承台钢套箱的稳定性和平衡性。
4.进行混凝土浇筑
在承台钢套箱安装完成后,开始进行混凝土的浇筑。
将混凝土倒入承
台钢套箱内,然后使用振动器进行振动,以排除空气和保证混凝土的致密性。
在浇筑过程中,需要注意混凝土的质量和浇筑速度,以避免出现开裂
或渗漏等问题。
5.维护和拆除
在混凝土浇筑完成后,需要对承台钢套箱进行维护。
通常情况下,需
要进行一段时间的养护,以确保混凝土的强度和耐久性。
在养护期间,需
要做好保护措施,以防止外部因素的损害。
一段时间后,混凝土达到设计强度后,可以进行承台钢套箱的拆除。
拆除时,需要使用工具将承台钢套箱撬开,并将其从混凝土中取出。
在拆
除过程中,需要小心操作,以防止损坏混凝土。
总结
承台钢套箱是一种常见的施工方案,用于支撑混凝土浇筑过程中的水
平结构。
在施工过程中,需要做好准备工作、制作钢套箱、安装钢套箱、
进行混凝土浇筑、维护和拆除等步骤。
通过合理的施工方案和细致的操作,可以确保施工质量和工程安全。
钢套箱施工组织设计

12、手砂轮切割机6台,磨光片200块,全部放在C段
13、台式钻床1台,放在C段
(二)6月10日前必须到位的设备和机具
1、震动打桩锤(含控制箱)1套,放在C段
2、柴油抽水机2台,放在C段
2、用两只导管两只漏斗同时压水,从下游向上游浇筑水下砼,砼的标号C30,封底砼顶面高出承台底约50cm,导管的扩散半径按2.2m考虑,共须转移一次导管的位置,压水后注意调节钢护筒内的水头,让护筒内外不造成反压。
六、钢套箱支撑转换
1、封底砼达到7天龄期,且标号达到C25以上后,用抽水机和潜水泵抽干水,将封底砼凿除至承台底。
唐仲凯:负责后勤保障、财务往来
周泽良:负责施工1组,目前在A段负责,进大桥后A段扫尾工程由
何胜龙负责
谭再元:负责施工2组,目前在C段负责,进大桥后C段扫尾工程由
翼目平负责
郑胜勇:负责加工班组
十一、劳动力组织
1、5月份,进场5人,配合项目部做好场地平整、硬化、水、电、住宿等工作。
2、6月份大桥工人40人,其中国内工人30人,本地技术工人10名,分班如下:施工1组和施工2组,每组10人,分别在白天和晚上组织作业,从事套箱安装、下沉等工作,其工人全部用国内工人;加工组20人,从事套箱加工,分白天和晚上两班作业。加工组国内工人10名,本地工人10名。
四、钢套箱安装
1、水位1.5m处(约高出现水位1m),用UPN140槽钢在钢护筒上设置牛腿并搭设平台,平台宽出套箱周边1m,在平台上用全站仪放出钢套箱的设计位置,并在套箱支撑点处用水准仪操平。
2、在护筒顶设置支架,支架离水面的净空7m,用来下放钢套箱
桥梁工程-钢套箱施工技术方案

桥梁工程-钢套箱施工技术方案5.1 方案说明承台套箱以钻孔灌注桩钢护筒为承重体系,在钢护筒插打完成后,以统一标高在钢护筒上焊接平联与承重牛腿,牛腿作为套箱底板主龙骨的承重结构。
在主龙骨上安装次龙骨及面板等,将其作为钻孔平台。
待钻孔灌注桩施工完成后,主龙骨上吊点位置开预留口,便于安装吊点,其余部位进行简单整平修复,即可作为套箱底板。
套箱侧板采用工厂分块制作,集中运输的加工方法。
钢套箱现场拼装完成后,安装下放系统,包括内支撑、下放吊点等,同时割除套箱周边部分钻孔平台,下放系统安装完成后,将套箱整体提升50cm,割除钢护筒剩余平联与承重牛腿,由于套箱总重约200t,套箱下放采用人工配合手摇千斤顶整体下放;在套箱入水前停止下放,检查各个吊点下放距离与平面位置,套箱位置无偏差且各个吊点下放距离调整一致后开始入水;套箱每下放5个行程后对所有吊点的下放距离进行调整,直至套箱下放到位;套箱下放到位后,对套箱平面及空间位置进行测量检查,检验合格后,根据图纸设计位置安装锁定装置,完成套箱下放。
图5.1 类似钢套箱下放5.2 施工工艺流程图5.2 钢套箱施工工艺流程图5.3 套箱加工5.3.1 套箱加工工艺流程图图5.3.1 套箱加工工艺流程图5.3.2 底侧板加工(1)底板加工为加快工序转换效率,提高施工功效,我项目将原钻孔平台顶板用于钢套箱的底板。
在钻孔灌注桩施工完成后,对钻孔平台面板进行修复更换后即可做为套箱底板。
原钻孔平台顶板是按照套箱底板受力形式进行设计的,采用2I40a纵梁作为主龙骨,I14作为次龙骨,次龙骨间采用∠75×50×6加强。
次龙骨上满铺6mm 厚花纹钢板。
整个钻孔平台采用钢护筒作为承重系统,其主龙骨直接搁置在钢护筒牛腿上。
(2)侧板加工套箱侧板加工分为平面板及弧形板两种,均采用工厂定型化加工成型。
平面板分为A、B、 C、D、A1五种型号,其中A型号16块,B型号8块,A1型号2块。
双壁钢套箱围堰施工组织设计

.鹤岗至大连高速公路小沟岭(黑吉界)至抚松段双壁钢套箱围堰专项施工方案编制:复核:审核:中交路桥鹤大高速公路ZT03标段项目经理部.目录1 工程概述 (1)2 技术准备 (1)2.1内业准备 (1)2.2外业准备 (2)3 人员组织 (3)4 材料及制作要求 (4)4.1材料要求 (4)4.2双壁钢套箱制作拼装要求 (4)4.3壁钢套箱制作拼装允许误差 (4)5 主要设备、机具选型 (5)6钢套箱围堰专项施工方案 (5)6.1钢套箱施工工艺流程 (5)6.2双壁钢套箱的设计 (6)6.3钢套箱沉放系统设计及安装 (9)6.3.1 第一层钢套箱拼装下沉 (10)6.3.2钢套箱下沉步骤 (10)6.4钢套箱封底 (11)6.5钢套箱排水 (14)6.6拆除钢套箱悬吊系统及套箱回收 (14)7 钢套箱质量控制及检验标准 (14)7.1双壁钢套箱制作加工 (14)7.2双壁钢套箱沉放 (14)7.3封底混凝土 (15)8 钢套箱施工常见问题与处理措施 (15)围堰抗浮计算 (17)双壁钢套箱施工方案1 工程概述钢套箱顾名思义是套在永久结构外面的临时结构,起到围堰作用。
钢套箱为桥梁基础及下部构造水上施工作业中常用的一类围护结构形式,尤其适合于大河流中的深水基础,能承受较大的水压,保证基础全年施工安全度汛。
特别是在一些施工条件困难或受水文、地形、地质条件限制而无法采用钢板桩、筑岛围堰等围护结构的条件下,钢套箱更显示出了其优越性。
常用的钢套箱分单壁和双壁两种,由于单壁钢套箱刚度差,一般深水基础较少采用,实际工程中大部分情况下采用双壁钢套箱。
钢套箱围堰是一种无底结构,下沉后底部着床或嵌入河床,然后用水下混凝土封底,排水后形成围堰。
钢套箱平面形状可根据承台形状加工成圆形、矩形、也有其他形状。
立面分层,平面分块。
堰壁钢壳由有加劲肋的内外壁板和多层水平桁架所组成。
堰壁底端设刃脚,以利切土下沉。
在堰壁内腔,用隔舱板将其对称地分为若干个密封的隔舱,以利于下沉和排水。
钢套箱下沉施工组织设计

沙田赣江特大桥先桩后堰20#墩钢套箱下沉施工组织设计一、工程概况沙田赣江特大桥20#墩基础承台为圆端形。
采用先桩后堰的施工方案,目前水位标高为11.8m,考虑到施工中不确定因素多,钢套箱设计按施工水位16m左右考虑。
河床覆盖层以砂、砾为主,下伏强风化、弱风化泥质砂岩,该岩不透水,但岩质较软。
二、施工方案根据桥址处的地质水文条件, 通过综合技术经济分析,决定采用先桩后堰法施工。
施工流程为:搭设钻孔平台→孔桩施工→搭设围堰拼装平台→底节钢套箱拼装→吊挂系统设臵→底节钢套箱下水→接第二节钢套箱、下沉→接第三节钢套箱、下沉→封底混凝土施工。
具体施工工艺如下:1、拼装平台搭设待孔桩施工完成后,拆除钻孔区的平台面系和承台范围内的钢管桩,留下平台吊装区的钢管桩。
重新打设钢管桩,在钢管桩上设臵牛腿,牛腿比现场施工水位高50cm处设臵。
在牛腿上搭设横垫梁2I22a,2I22a铺设在横垫梁上,放样出钢套箱刃脚中心线的位臵,要求在搭设拼装平台时,2I22a大致落在钢套箱刃脚中心线位臵上。
为了方便拼装和焊接钢套箱,在拼装工作平台承重梁上可铺设部分木板,现场施工可根据实际情况调节。
(具体见附图 20#墩钢套箱墩拼装下沉)2、底节围堰拼装及下水。
钢套箱按施工设计图纸在钢结构加工厂制造成单元,经检查验收合格后运输至墩位处,逐节进行预拼装,第一节整体预拼完成后,再锁定焊接。
为了防止围堰侧翻,可用倒链内外固定在钢护筒和钢管桩上。
在拼装好后,需全面仔细检查各焊缝有无气孔、夹碴、漏焊等处,并进行油密试验。
确认焊接良好并不漏水后,填写钢套箱验收合格报告,作好下水的准备。
底节钢套箱预拼装完成后锁定焊接时,同时可进行提升系统的施工。
提升系统包括承重梁和扁担梁,利用钢管桩作为承重柱,在钢管桩上设臵单层2I40a作为承重梁,在承重梁上设臵200吨千斤顶。
在千斤顶上设臵扁担梁。
精轧螺纹钢下部和钢套箱连接,上部和扁担梁固定。
利用千斤顶对扁担梁的顶升和下落调整钢套箱的高度。
钢套箱安装施工技术方案

钢套箱安装施工技术方案钢套箱安装施工技术方案一、项目概述随着近年来建设项目的不断推进,钢套箱的应用越来越广泛。
钢套箱不仅具有方便快捷、便于搬迁、结构牢固等特点,而且相对于传统的建筑结构,钢套箱还具有一定的经济性和环保性。
因此,在现代建筑领域中,钢套箱已成为一个不可或缺的建筑元素。
本次施工是在某地区的一个建设项目中使用钢套箱作为办公室的方案。
本文就是介绍这个项目中钢套箱的安装施工技术方案。
二、项目流程1. 了解设计方案。
了解建筑方案、安装设计图纸等相关文件,明确项目要求,确定材料种类和数量。
2. 现场测量和施工准备。
施工前需要从现场实际情况出发,进行测量、划线等工作。
在施工中应使用必要的施工工具和设备,保证施工进度和质量。
3. 安装基础。
在施工前应按照设计图纸要求,为钢套箱的基础进行施工,确保其稳固可靠。
4. 组装钢套箱框架。
按照设计方案要求的尺寸和形状,对钢套箱进行框架的安装,以便后续的操作。
5. 安装墙板和屋面。
按照设计方案要求的尺寸和材料类型,安装钢套箱的墙板和屋面。
6. 安装窗户和门。
根据设计要求,在已安装的墙板上恰当的位置安装窗户,使其更具实用性。
安装门,以便使用和维护。
7. 安装水电管线。
按照设计方案,钻洞并安装相应的水电管线,确保办公区域的使用和设备的正常运转。
8. 内装装修。
对办公室进行必要的内装装修,包括室内墙面的粉刷、家具安装等。
9. 竣工验收。
在安装结束后,对工程进行全面的验收,确保无事故、无质量问题、符合规范等。
三、施工要点1. 基础施工平整根据设计图纸要求,施工前需要对地基进行检查和测量,选择平整的地方施工,避免区域不平导致的倾斜和不稳定。
2. 钢套箱的框架结构要坚固框架结构要保证强度和稳定性,不能出现松动等情况。
同时需要保证框架间的间隙和卡榫,都要正确安装,以确保办公室结构的完整。
3. 墙体和屋面安装要严密钢套箱的墙板和屋面的尺寸要完全符合设计图纸的要求,同时组装要保证尺寸的正确对称。
钢套箱设计与施工方案
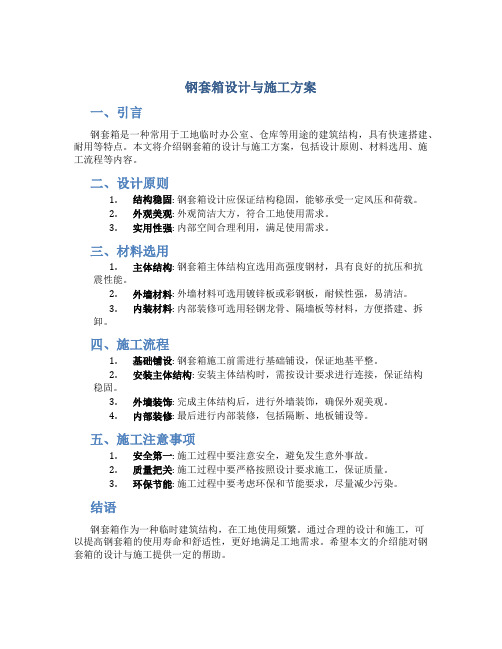
钢套箱设计与施工方案
一、引言
钢套箱是一种常用于工地临时办公室、仓库等用途的建筑结构,具有快速搭建、耐用等特点。
本文将介绍钢套箱的设计与施工方案,包括设计原则、材料选用、施工流程等内容。
二、设计原则
1.结构稳固: 钢套箱设计应保证结构稳固,能够承受一定风压和荷载。
2.外观美观: 外观简洁大方,符合工地使用需求。
3.实用性强: 内部空间合理利用,满足使用需求。
三、材料选用
1.主体结构: 钢套箱主体结构宜选用高强度钢材,具有良好的抗压和抗
震性能。
2.外墙材料: 外墙材料可选用镀锌板或彩钢板,耐候性强,易清洁。
3.内装材料: 内部装修可选用轻钢龙骨、隔墙板等材料,方便搭建、拆
卸。
四、施工流程
1.基础铺设: 钢套箱施工前需进行基础铺设,保证地基平整。
2.安装主体结构: 安装主体结构时,需按设计要求进行连接,保证结构
稳固。
3.外墙装饰: 完成主体结构后,进行外墙装饰,确保外观美观。
4.内部装修: 最后进行内部装修,包括隔断、地板铺设等。
五、施工注意事项
1.安全第一: 施工过程中要注意安全,避免发生意外事故。
2.质量把关: 施工过程中要严格按照设计要求施工,保证质量。
3.环保节能: 施工过程中要考虑环保和节能要求,尽量减少污染。
结语
钢套箱作为一种临时建筑结构,在工地使用频繁。
通过合理的设计和施工,可
以提高钢套箱的使用寿命和舒适性,更好地满足工地需求。
希望本文的介绍能对钢套箱的设计与施工提供一定的帮助。
钢套箱施工方案

隔蒲潭特大桥水中承台钢套箱施工方案隔蒲潭特大桥跨越府河的17#、18#、19#墩为水中墩,17#、18#墩处在河道中心,水深且流速大,采用钢套箱施工。
套箱施工安排在常水位+1m时施工。
17#、18#号墩承台长12.9m,宽9.4m,承台底面高程分别为15.62m 、14.93m,常水位22.29m,以18#墩为例,设置套箱底面标高14.13m,套箱侧板作为承台外模。
钢套箱设计总体设想1.结构设计1.1.根据承台底标高(14.93m)以及常水位 (22.29m),套箱高度至少8.5m,考虑汛期因素,套箱实际高度定为9m。
1.2一般钢套箱隔水模板的形式主要有单壁和双壁两种形式,鉴于单壁模板节省材料、自重轻、加工方便以及装拆方便等优点,采用单壁模板。
1.3由于模板加工精度要求较高,现场加工有难度,故采用工厂加工后运抵现场拼装,因此考虑到运输环节因素,整套模板在平面分成13块小模板。
1.4根据现场起重安装能力,套箱模板在竖向分成3m、3m、3m三节。
详见“钢套箱图”2.钢套箱构造简介根据钢套箱的使用功能,可以将整套套箱分为底模、侧模、内撑、绑定装置以及定位固定装置等五部分。
2.1.侧板部分包括侧板、竖肋,侧面水平加强板、止水带、水平整体加强型钢等五个方面组成。
每节侧板采用10mm厚钢板,竖肋采用8#槽钢@50cm,水平加强板采用100mm宽6mm厚钢板,共布置6道(每60cm一道)组合式侧板的拼装处采用∠75×75×6等边角铁,连接用的螺丝采用T螺栓@20cm,两螺丝间用6mm钢板焊接加强,因连接处是整个侧板薄弱环节,所以用16#型钢进行外围加强,整体型加强型钢设两道,分别处在两节连接的位置上。
详见“钢套箱侧模图”2.2侧板稳定性分析2.2.1.对套箱侧板的受力分析及设计依据如下:套箱作为组合式钢模板,施工中两个阶段受力情况为:下沉就位,封底结束抽干水后,侧板受外部水压力作用;扎钢筋结束,浇注砼过程中,侧板既受外部水压力作用,又受内部砼挤压力作用,但两种力方向相反,可互相抵消一部分力,现假设有第三种情况,即在陆地上进行承台施工,则此时钢模板受内部砼挤压力即为最不利情况受力。
- 1、下载文档前请自行甄别文档内容的完整性,平台不提供额外的编辑、内容补充、找答案等附加服务。
- 2、"仅部分预览"的文档,不可在线预览部分如存在完整性等问题,可反馈申请退款(可完整预览的文档不适用该条件!)。
- 3、如文档侵犯您的权益,请联系客服反馈,我们会尽快为您处理(人工客服工作时间:9:00-18:30)。
西主墩承台双壁钢套箱设计与施工一、工程概况1.1工程简介颗珠山大桥起点桩号为K29+387.929,终点桩号为K31+047.929,全长1660m,桥跨组合为7×50m+(50+139+332+139+50)m+12×50m。
其中主桥长710m,1.2主墩基础结构简介东海大桥VII标西侧主墩桩基有24根,桩径为φ2500mm。
西主墩承台砼方量约4760m3。
一座主墩承台分左右幅、横系梁三部分浇注。
平板车通过栈桥运输至现场,采用履带式吊机或浮吊在钢护筒上设置的临时平台上组拼,然后由悬吊下沉系统下放钢套箱。
钢套箱下放到位后,与护筒固定,抛片石、碎石等进行基底处理,待基底稳定后浇注封底砼,最后进行左右幅承台施工。
方案二:有底钢套箱方案有底钢套箱由侧板、底板和内支撑组成。
钢套箱侧板在加工厂分块加工,然后由平板车通过栈桥运输至现场,采用履带式吊机或浮吊在钢护筒上设置的临时平台上组拼底板和侧板,然后由悬吊下沉系统下放钢套箱至倒挂牛腿上固定。
浇注封底砼,最后分两次施工承台。
无底钢套箱和有底钢套箱方案综合比较见下表。
施工方案综合比较经上述工期、成本、优缺点及套箱构造等方面比选较,西主墩承台拟采用无底双壁钢套箱进行设计与施工。
二、钢套箱设计2.1设计条件2.1.1地质条件根据颗珠山大桥补充地质详勘报告,河床表层为淤泥。
2.1.2水文条件⑴设计高水位:2.15m⑵流速:V=1.2m/s⑶波浪二十年一遇波浪要素表2.1.3设计参数⑴海床面标高:左幅最低海床标高约-3.5m,右幅平均海床标高约-4.5m。
⑵冲刷深度:根据地质水文资料,参考东海大桥IV标的施工经验,本桥位局部冲刷按1m考虑。
⑶钢套箱参数钢套箱设计参数2.2结构计算详见附件——计算书。
2.3钢套箱结构简介双壁钢套箱平面矩形,圆形倒角,内壁平面尺寸为24m×17.4m,外平面尺寸为26m×19.4m,套箱左幅高11m,右幅高10m。
壁厚1.0m,刃脚高为0.8m。
钢套箱竖向分2节,顶节高度为5m,底节高度为5m或6m;平面每节划分为10块,块间设有钢箱或竖向加劲桁片。
2.3.1套箱结构组成钢套箱由壁板、竖向背肋、水平环向桁架、钢箱以及内支撑组成。
2.3.2套箱侧板钢套箱壁板:经计算拟定面板采用6mm钢板。
面板加劲肋:拟采用角钢∠75×75×6,竖向布置间距为20cm~30cm不等。
2.3.3水平环向桁片水平环向桁片是钢套箱主要承重部位,主要承受壁板传递的荷载,通过内支撑传递给钢套箱达到受力平衡,水平桁片沿竖向布置间距为1m。
水平桁片由弦杆和斜杆组成,弦杆为δ10×250mm钢板,斜杆为2∠90×56×6。
2.3.4钢箱内支撑处均设有钢箱,共有12个。
钢箱断面尺寸为1.0m×1.0m,高度方向每50cm设置一道“回形板”,箱内采用钢板加劲。
2.3.5内支撑设置一道内支撑,内支撑采用2[40a,在钢套箱顶部对应于钢箱设置。
三、钢套箱施工3.1概述⑴钢套箱由钢板和型钢焊接而成,套箱壁、分隔舱和钢箱均为水密结构。
双壁钢套箱的主要作用和用途是为承台施工创造一个良好的干施工作业环境,因此,双壁钢套箱施工是主墩基础施工的关键工序之一。
⑵钢套箱施工采用现场分片制作,试拼合格后通过栈桥运输至墩位现场,用墩位处的50t履带吊或浮吊进行吊装组拼,采用钢护筒上的吊装系统下沉钢套箱,水下刚性导管法进行封底砼灌注。
3.2施工工艺流程主墩双壁钢套箱施工工艺框图3.3施工技术要点3.3.1钢套箱制作、试拼装⑴钢套箱在施工现场分片制作,单片重量一般控制在15t以内,根据钢套箱结构设计,每节钢套箱按照10片进行加工。
⑵钢套箱分片制作采用流水作业组织生产,每片钢套箱均在特制的平台和模具上组装焊接成型。
⑶每节钢套箱加工完成后,均进行该节钢套箱整体试拼工作,以检验钢套箱加工误差和加工质量。
3.3.2钢套箱拼装⑴底节钢套箱分片拼装在墩位现场的拼装平台上进行。
拼装平台利用主护筒和钢管桩搭设而成。
钢套箱拼装利用墩位处的50t履带吊或浮吊实施。
⑵以底节钢套箱作为拼装平台拼装顶节钢套箱。
⑶顶节钢套箱拼装焊接完成,焊接横桥向三道内支撑,内支撑随钢套箱一起下沉。
其余内支撑待封底抽水后焊接。
⑷接缝焊接应严格把关,设专职人员现场蹲点,接缝焊接完毕进行渗透检验,以确保焊缝质量。
3.3.3钢套箱下沉⑴钢套箱采用在钢护筒上设置吊装下沉系统,以5t卷扬机为动力进行下沉。
⑵下沉系统设置①钢套箱总重量达285t,采取在钢套箱内壁设置10个下沉吊点,每个吊点按照30t的荷载进行控制设计。
各个吊点上均安装1台5t卷扬机配6轮滑车。
②采用在主护筒上焊接立柱和斜拉杆形成吊装支架。
⑶导向架设置①为了保证钢套箱下沉过程中和下沉到位后,其平面位置和倾斜度满足要求,采取在护筒上设置刚性导向,一个钢套箱共设置12个导向。
②导向架由导向型钢和支腿组成,支腿均由型钢和钢板焊接而成。
③导向架顶标高为+9.0m,底标高为0.0m,总长为9.0m,共设置4个支腿。
④导向架导轨顶至钢套箱内侧的间隙为3cm。
⑤为了避免导向支腿处的护筒产生局部变形,在护筒内设型钢支撑,其位置应与导向架支腿位置相对应。
⑷采用在套箱壁内加水,以抵消部分浮力,以其自重下沉至设计标高。
⑸套箱着床稳定后,立即进行套箱内和套箱外侧的砂袋抛填。
⑹钢套箱的纠偏、调位主要靠钢护筒和导向进行。
3.3.4钢套箱封底⑴锚筋设置:承台砼一次浇注完毕,方量大,为保证封底砼满足承载要求,在封底范围的护筒四周焊接锚固钢筋。
⑵钢套箱封底在钢套箱下沉到位并进行基底处理后进行。
采用刚性导管法灌注水下封底砼,封底净面积为316㎡和343.8㎡,共布设18根导管。
⑶封底砼最大方量为688m3左右,砼采用后场150m3/h的搅拌站集中搅拌供料,配备3辆搅拌运输车通过栈桥运料至现场,直接用输送泵泵送到料斗内进行封底砼灌注。
⑷封底砼方量大,砼配合比拟采用掺加缓凝剂,砼初凝时间为10小时左右,以保证所有封底砼在砼初凝前浇注完成。
四、进度安排和主要机械设备配置4.1进度安排⑴施工周期分析如下:⑵按照上述分析一个主墩承台施工为84天,按照3个月编排计划。
4.2主要机械设备配置根据年度施工计划进度和西主墩钢套箱施工计划进度安排,主要机械设备配置如下:50t履带吊1台,80t浮吊1台,拌和站2座(60m3/h、90m3/h各1座),砼搅拌车3台,砼输送泵2台,潜水设备2套。
五、质量安全保证措施、环境保护和文明施工5.1质量保证措施钢套箱施工是主墩承台施工的前提和保障,我部对钢套箱设计与施工方案进行了反复的讨论、论证,确保施工的可靠性。
建立以项目经理为工程质量第一责任人的工程质量管理机构(见下图),和以项目总工程师负责的工程技术、质检、试验、测量四位一体的质量保证体系,严格施工过程中的质量控制。
质量管理框图5.1.1质量管理机构质量管理组织机构采用定期和不定期相结合的工作方式开展质量检查工作。
项目部质量管理组织机构每旬组织一次质量检查和评比活动,每分项工程施工完毕召开一次质量分析会;作业班组实行上、下工序交接检查制度。
5.1.2质量保证体系⑴监控测量体系首先由测量组加密施工控制网,在监理工程师的协助下对控制网进行全面复测。
现场操作人员熟悉钢套箱施工相关资料,采用一种方法放样,多种方法复核,确保测量结果满足设计要求。
施工测量严格按照规范操作,定期检校仪器,保证仪器良好,作好施工观测记录,确保施工测量程序有效进行,保证工程质量。
⑵质检体系施工过程中每完成一道工序,现场施工技术人员必须填写相关记录表格,尤其对钢套箱的结构尺寸、加工情况等等必须作好详细的记录,对于加工不符合设计要求的钢套箱一律不允许进场。
作业班组实行上下工序交接检查制度,并对关键工序实行跟踪检查,做到预防为主。
5.2安全保证措施5.2.1建立安全生产保证体系“安全生产”是一切施工的前提条件,因此,在整个施工过程中,我们必须始终贯彻落实“安全第一,预防为主”的方针,建立健全的安全生产保证体系。
成立以项目经理为第一责任人的安全生产保障体系,成立安全生产委员会,设置专门的安全管理部门,配备专门的安全管理人员,各作业队选配责任心强的人员任本作业队的兼职安全员,在经理部的领导下,随时随地在工地进行检查,充分发挥监督管理作用。
5.2.2施工安全措施⑴防风浪措施①与国家海洋局东海海区环境预报中心和上海市气象局取得密切联系,建立东海区海洋气候预报网络,及时预报,做到现场施工信息准确。
②根据指挥部建议的避风港位置,及时与相关单位进行联系,并确定避风港位置。
遇有恶劣天气,合理安排水上施工设备顺序进入避风港,人员撤离施工区域。
③经理部安排人员24小时轮流值班,随时接听天气预报,将信息及时反馈到各作业区域。
对施工现场的构件采取加强加固措施。
④接到预报,防风、防台领导小组立即展开工作,统一部署,全体人员进入应急状态,现场停止施工,由抢险小组控制现场,使损失减少到最低限度。
⑵施工船舶安全管理①施工船舶必须持有符合沿海开放海区安全要求的各类有效证书,按规定配齐合格船员、船机、通讯、消防、救生、防污等各类设备必须安全有效。
②严格按照有关规定进行船舶海上管理,确保船舶施工安全。
③配备运输船舶水上甚高频电话系统终端设备,昼夜保持通讯畅通,按规定显示有效的航行、停泊和作业信号。
④遵守“以避(防)为主,以救(抗)为辅,留足余地,自我保护”的原则。
5.3环保措施按照《中华人民共和国环境保护法》以及地方法规和行业企业要求,采取措施控制施工现场的各种粉尘、废水、废气、废渣等对环境的污染和危害。
环境保护坚持“预防为主、防治结合”的方针,努力实现可持续发展战略。
5.4文明施工我们将严格按照招标文件有关章节具体要求和我公司有关文明施工的具体规定,制定严格的项目经理部文明施工管理条例和计划,全体进场员工必须认真遵守、严格执行,坚决做到文明施工,充分体现出我公司现代化施工企业的精神风貌。