铝合金焊缝的电火花铣削工艺研究
金属表面处理的电火花加工技术

金属表面处理的电火花加工技术1. 前言电火花加工技术(Electrical Discharge Machining, EDM)是一种利用连续或断续的电火花放电来去除金属的非接触式加工方法。
该技术在金属表面处理领域具有广泛的应用,特别是在硬质合金、高速钢、淬硬钢等难加工材料的加工上表现出了显著的优势。
本文将从电火花加工的原理、工艺特点、应用领域等方面进行详细探讨。
2. 电火花加工原理电火花加工技术的基本原理是利用高压电源在工件和工具之间产生连续或断续的电火花放电,放电时产生的高温熔化金属和气体,在气压作用下迅速从放电通道中排出,从而达到去除金属的目的。
放电过程中,工件表面和工具表面都会形成一层熔融层,随着后续的冷却和固化,这层熔融层会形成一种特殊的微观结构,对工件的性能产生重要影响。
3. 电火花加工的工艺特点电火花加工具有以下几个显著的工艺特点:(1)非接触式加工:由于加工过程中不直接接触,因此适用于硬质合金、高速钢、淬硬钢等难加工材料的加工。
(2)加工精度高:电火花加工可以达到非常高的加工精度,加工表面质量好,适用于复杂形状的加工。
(3)加工效率:电火花加工的加工效率相对较低,但随着技术的不断发展和设备的更新,加工效率有所提高。
(4)加工变形小:由于是非接触式加工,加工过程中工件的变形较小。
(5)适用范围广:电火花加工适用于各种金属和非金属材料的加工,特别是在难加工材料的加工上具有显著优势。
4. 电火花加工的应用领域电火花加工技术在金属表面处理领域有广泛的应用,主要应用领域包括:(1)模具制造:电火花加工技术在模具制造领域有广泛应用,如冲压模、压铸模、塑料模等。
(2)航空航天:电火花加工技术在航空航天领域中,用于加工难加工材料,如钛合金、镍基高温合金等。
(3)汽车制造:电火花加工技术在汽车制造领域中,用于加工发动机部件、变速箱齿轮等。
(4)微细加工:电火花加工技术在微细加工领域有重要应用,如微细模具制造、微细零件加工等。
铝合金零部件高速铣削工艺研究

铝合金零部件高速铣削工艺研究摘要:本文研究了铝合金零部件的高速铣削工艺,研究内容涵盖了刀具选择、切削速度、进给量、切削深度以及冷却液的选择等方面。
根据铝合金较低的硬度和加工表面要求,选用了单刃、双刃或多刃实心刀具进行高速铣削,并平衡了切削速度、进给量和切削深度之间的关系。
在冷却液的选择方面,建议使用水溶性切削液或喷雾切削液以降低加工温度和摩擦力,并防止铝屑和必要零件产生热膨胀和变形等问题。
通过实验验证了所提出的高速铣削工艺的可行性和有效性。
关键词:铝合金;零部件;高速铣削工艺引言:铝合金是一种轻质高强度材料,广泛应用于航空、汽车、电子等领域中的零部件制造。
高速铣削是一种有效的铝合金加工方法,可以在保证加工质量的前提下提高生产效率。
本文旨在研究铝合金零部件的高速铣削工艺,包括刀具选择、切削速度、进给量、切削深度以及冷却液的选择等方面。
通过对每个因素的分析,确定了高速铣削的工艺参数,最终实现了对铝合金零部件的高速铣削。
一、合理选择刀具在铝合金高速铣削中,刀具的选择是非常重要的。
由于铝合金是一种相对较软的材料,因此可以选择单刃、双刃或多刃实心刀具。
对于单刃刀具而言,由于只有一个刃口,其切削力较大。
然而,单刃刀具比较容易进行切削力的控制,适用于工件形状复杂的加工。
此外,单刃刀具相对简单,对机床的稳定性要求较低。
双刃刀具则具有两个刃口,能够分摊切削力,因此能够减小每个刃口的切削力。
这样一来,双刃刀具在加工过程中对机床的稳定性要求更高。
双刃刀具适用于需要较高精度和表面质量的加工。
多刃实心刀具是指具有多个刃口的刀具,它能够进一步减小切削力,并提高加工效率。
多刃实心刀具适用于大批量生产和高效率加工的情况下。
然而,多刃实心刀具的设计要求更高,对机床的稳定性和刚性要求也更高[1]。
因此,在选择刀具时,需要根据具体的加工要求、工件形状和尺寸、加工精度要求等因素综合考虑。
单刃刀具适用于复杂形状的加工,双刃刀具适用于高精度和表面质量要求较高的加工,而多刃实心刀具适用于大批量和高效率的加工。
铝合金的切削特性分析和工艺技术研究

表 1 铝合金切削性能
铝合金 合金含量 0% ~ 0.5% 铝铜合金 0.5% ~ 5.65% > 5.65% 铝镁合金 镁硅合金 铝硅合金 铝锰合金 铝锌合金 4% ~ 13% < 8% 9.5% ~ 11.5% 切削性能 不好 较好 良好 低劣 优良 优良 低劣 低劣 良好 加入适当 Cu,Mg,切削性改善 冷变形强化,切削性改善 LC4,LC5,LC6,ZL401,ZL402 ZL101,ZL103,ZL104,ZL105,ZL110 冷变形强化,切削性良好 改善措施 冷作处理后,切削性改善 代表合金 LD2 LD5-LD10D ZL202
铝合金本身的材料性能,引起工件在切削加工中出现粘 刀、变形、振动等问题。根据铝合金的切削性能,加工过程 中需合理选择刀具参数、切削参数等,设计恰当的工艺路线, 有效避免或减缓切削过程中的问题,确保工件切削质量。 2.1 刀具材料及刀具参数的选择 铝合金在切削过程中产生的切削力较小,可适于高速
表 2 切削铝合金的刀具材料
(1) 粘刀现象。 铝合金工件硬度小 (最高 120HB 左右) , 塑性较大,切削时工件变形大;切屑与前刀面的摩擦较大, 且接触面积也大;由摩擦和变形产生的热量,使工件表面 金属变软直至溶化。再者,铝合金切屑不容易断裂,热量 不能及时带走,加剧了工件材料的溶化。这样切屑滞留在 切削刃上,容易产生粘刀现象,从而进一步形成积屑瘤, 影响切削过程。ቤተ መጻሕፍቲ ባይዱ(2)切削变形。铝合金件的抗塑性变形能力差,在切 削力的作用下,工件表层容易产生塑性变形。在切削摩擦
钨钴类硬质合金刀具
超细晶粒硬质合金刀具 (聚晶)金刚石刀具 类金刚石碳涂层刀具 陶瓷刀具 聚晶立方氮化硼刀具
除刀具材料外,刀具的几何参数是影响加工质量的一 个重要因素。切削铝合金时,选用较大的刀具前角,一般 12°~ 18°。前角过大,切削刃和刀头强度降低,不利于 刀具散热,影响刀具寿命;前角过小,切屑变形增大,易 断屑,但切屑容易划伤工件已加工表面。粗加工时可适当 减小前角,精加工时可适当增大前角。刀具(副)后角有 利于减小(副)后刀面与工件的摩擦。由于铝合金弹性模 量小、易粘刀,切削摩擦严重,宜选择较大的后角。例如, 切削铸铝合金时,后角可取 12°。对于刃倾角的选择,冲 击较大的连续切削,取较大负值的刃倾角配合较大前角, 保证切削质量;精加工时宜取正刃倾角,防止切屑划伤已 加工表面。 切削时, 选用刀刃锋利的刀具, 前刀前研磨抛光, 选择尽可能小的刀尖圆弧半径,以防止积屑瘤和切削毛刺。 2.2 切削用量的选择 切削用量包括切削速度、进给量和背吃刀量三个切削 要素,表示切削过程中切削运动的大小以及刀具切入工件 的程度,直接影响到切削力、切削热、刀具寿命、工件表 面粗糙度等。对于铝合金这种适于高速切削又容易产生粘 刀、切削变形、振动等问题的材料,合理选择切削用量显 得尤为重要。一般情况下,粗加工时选用较大的切削深度 和进给量。例如,切削 2A12 时,速度可控制在 800r/min 左右;精加工时,切削深度 0.2 ~ 0.5mm,选择较高的切削 速度和较小的进给量。 2.3 切削液的合理选择 铝合金在高速切削下产生大量的切削热,极易使材料
铝合金高速铣削加工的技术与创新研究
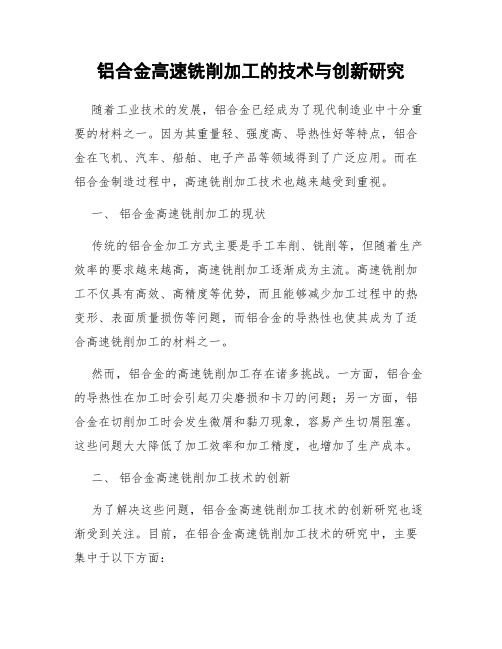
铝合金高速铣削加工的技术与创新研究随着工业技术的发展,铝合金已经成为了现代制造业中十分重要的材料之一。
因为其重量轻、强度高、导热性好等特点,铝合金在飞机、汽车、船舶、电子产品等领域得到了广泛应用。
而在铝合金制造过程中,高速铣削加工技术也越来越受到重视。
一、铝合金高速铣削加工的现状传统的铝合金加工方式主要是手工车削、铣削等,但随着生产效率的要求越来越高,高速铣削加工逐渐成为主流。
高速铣削加工不仅具有高效、高精度等优势,而且能够减少加工过程中的热变形、表面质量损伤等问题,而铝合金的导热性也使其成为了适合高速铣削加工的材料之一。
然而,铝合金的高速铣削加工存在诸多挑战。
一方面,铝合金的导热性在加工时会引起刀尖磨损和卡刀的问题;另一方面,铝合金在切削加工时会发生微屑和黏刀现象,容易产生切屑阻塞。
这些问题大大降低了加工效率和加工精度,也增加了生产成本。
二、铝合金高速铣削加工技术的创新为了解决这些问题,铝合金高速铣削加工技术的创新研究也逐渐受到关注。
目前,在铝合金高速铣削加工技术的研究中,主要集中于以下方面:1. 刀具材料的研究传统的加工刀具主要是碳化钨、硬质合金等,但随着要求越来越高,新型材料的研究也越来越重要。
目前,主要研究的刀具材料包括陶瓷、PCBN、PVD等。
这些新型材料具有优异的耐磨性和热稳定性,能够有效提高铝合金高速铣削加工效率和精度。
2. 切削参数的优化切削参数的优化能够有效提高铝合金高速铣削加工的效率和质量。
近年来,基于神经网络、遗传算法等的自适应优化方法已经广泛使用。
这些方法不仅能够有效地提高铝合金高速铣削加工的效率和精度,而且能够节约时间和人力成本。
3. 刀具表面处理技术的研究刀具表面处理技术的研究也是提高切削效率和精度的一种重要方法。
其中,多种工艺技术的组合,如电化学抛光、光化学处理、喷砂处理和等离子喷涂等工艺,都可以有效地提高刀具表面的抗磨性和硬度。
三、铝合金高速铣削加工技术的应用铝合金高速铣削加工技术的应用越来越广泛,主要涵盖以下几个领域:1. 车身零件的加工高速铣削加工可以实现铝合金车身零件的高效加工,比如汽车车轮和座椅托架等。
铝材电火花线切割加工制造工艺改进—中字牌钼丝
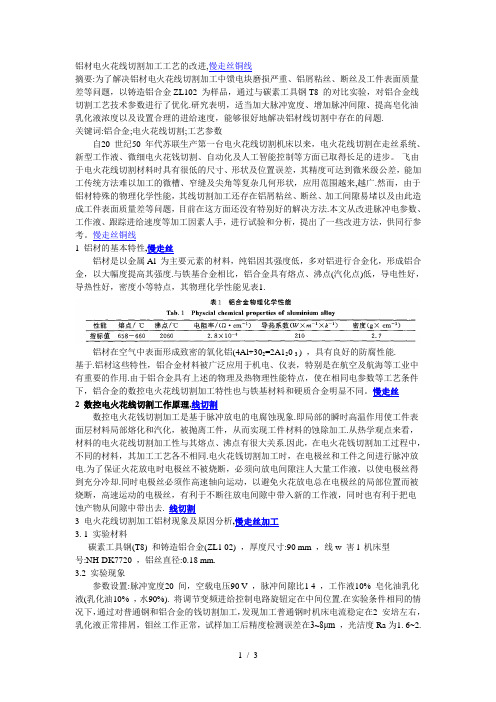
铝材电火花线切割加工工艺的改进,慢走丝铜线摘要:为了解决铝材电火花线切割加工中馈电块磨损严重、铝屑粘丝、断丝及工件表面质量差等问题,以铸造铝合金ZL102 为样品,通过与碳素工具钢T8 的对比实验,对铝合金线切割工艺技术参数进行了优化.研究表明,适当加大脉冲宽度、增加脉冲间隙、提高皂化油乳化液浓度以及设置合理的进给速度,能够很好地解决铝材线切割中存在的问题.关键词:铝合金;电火花线切割;工艺参数自20 世纪50 年代苏联生产第一台电火花线切割机床以来,电火花线切割在走丝系统、新型工作液、微细电火花钱切割、自动化及人工智能控制等方面已取得长足的进步。
-飞由于电火花线切割材料时具有很低的尺寸、形状及位置误差,其精度可达到微米级公差,能加工传统方法难以加工的微槽、窄缝及尖角等复杂几何形状,应用范围越来,越广.然而,由于铝材特殊的物理化学性能,其线切割加工还存在铝屑粘丝、断丝、加工间隙易堵以及由此造成工件表面质量差等问题,目前在这方面还没有特别好的解决方法.本文从改进脉冲电参数、工作液、跟踪进给速度等加工因素人手,进行试验和分析,提出了一些改进方法,供同行参考。
慢走丝铜线1 铝材的基本特性,慢走丝铝材是以金属Al 为主要元素的材料,纯铝因其强度低,多对铝进行合金化,形成铝合金,以大幅度提高其强度.与铁基合金相比,铝合金具有熔点、沸点(汽化点)低,导电性好,导热性好,密度小等特点,其物理化学性能见表1.铝材在空气中表面形成致密的氧化铝(4Al+302=2A120 3 ) ,具有良好的防腐性能.基于.铝材这些特性,铝合金材料被广泛应用于机电、仪表,特别是在航空及航海等工业中有重要的作用.由于铝合金具有上述的物理及热物理性能特点,使在相同电参数等工艺条件下,铝合金的数控电火花线切割加工特性也与铁基材料和硬质合金明显不同。
慢走丝2 数控电火花线切割工作原理,线切割数控电火花钱切割加工是基于脉冲放电的电腐蚀现象.即局部的瞬时高温作用使工件表面层材料局部熔化和汽化,被抛离工件,从而实现工件材料的蚀除加工.从热学观点来看,材料的电火花线切割加工性与其熔点、沸点有很大关系.因此,在电火花钱切割加工过程中,不同的材料,其加工工艺各不相同.电火花钱切割加工时,在电极丝和工件之间进行脉冲放电.为了保证火花放电时电极丝不被烧断,必须向放电间隙注人大量工作液,以使电极丝得到充分冷却.同时电极丝必须作高速轴向运动,以避免火花放电总在电极丝的局部位置而被烧断,高速运动的电极丝,有利于不断往放电间隙中带入新的工作液,同时也有利于把电蚀产物从间隙中带出去.线切割3 电火花线切割加工铝材现象及原因分析,慢走丝加工3. 1 实验材料碳素工具钢(T8) 和铸造铝合金(ZL1 02) ,厚度尺寸:90 mm ,线w 害l 机床型号:NH-DK7720 ,铝丝直径:0.18 mm.3.2 实验现象参数设置:脉冲宽度20 间,空载电压90 V ,脉冲间隙比1 4 ,工作液10% 皂化油乳化液(乳化油10% ,水90%). 将调节变频进给控制电路旋钮定在中间位置.在实验条件相同的情况下,通过对普通钢和铝合金的钱切割加工,发现加工普通钢时机床电流稳定在2 安培左右,乳化液正常排屑,钼丝工作正常,试样加工后精度检测误差在3~8μm ,光洁度Ra为1. 6~2.0 ,切割效益:42.8mm2/min.,慢走丝加工在加工铝合金时,现象如下:(1)电蚀物颗粒较大,工作液易堵塞而导致冷却条件差,电极丝升温快,温度过高,造成短路、烧丝.( 2) 电蚀物容易粘附在电极丝上,导致工件表面粗糙度达不到要求.电极丝直径增大,加工误差增大.(3) 钼丝抖动严重,馈电块磨损出槽.这是由于线切割中有金属转移现象,并且乳化液中含有水和油,所以在加工时放电间隙会产生高温氧化物,使一部分工件材料的氧化物飞溅反粘到电极丝上,使电极丝看上去发白、粗糙.当切割钢铁、铜铁等金属时,由于这些金属的氧化物均为导电物质,放电间隙状态良好,而加工铝及铝合金材料时,铝材的金属氧化物[A1 2O3 ,Al(HO)3]是陶瓷性物质,导电性极差,出现工件切不动,随着电极丝高速往复运动,电蚀物大量粘附在电极丝上,严重影响电极丝放电,造成馈电块磨损严重和断丝。
铝合金材料的铣削加工工艺浅析

维普资讯
进给运 动的切削 加工 方法 。他通 过 铣 刀刀 刃 的切 割和刀 面 的推 挤 , 工件 表 层 的金 属 材 料 变 为 切 把 屑。 由于工件材料 不 同 , 削条件 不 同 , 切 切削 过 程
中的变形 也 不 同 , 因而 产 生不 同 的切 屑 。按 切 屑
件的零点( x坐标) 。在 Y 工作台纵 向) ( 方向, 用工 作 台的 T形槽 固定 多个定位 挡块 , 一般 间 隔 5米左 右, 这些定位挡块的侧定位面必须在一条直线上。 工件的侧面贴上, 确定工件的零点( Y坐标) 。 2 2 工件 夹紧 : .
o ◎ o 铝 点 焊 时 需 要 较 大 的 点 焊 电 流
注释 : 0
最适合
备, 采用高速强力切削来提高效率、 减少塑性变形, 。 适 合 避免出现薄臂处切不断而撕裂现象。同时由于铝合 △ 如 果可 以的话 , 应避 免 ( 别是薄板 ) 特 金材料 比较软 , 进行锯切加工和人工打磨的工序非 常多 , 因此噪音大、 铝粉尘 , 有 需要作好 防护。 2 1 工件定位 : . 在 x( 工作 台横 向) 方向 , 用工作 台 的 T形 槽 固 定一个挡块 , 然后选用 一块合适 长度 的隔板调 整工 2 铝 合 金 材料 的 / -前 准 备 jr n- 铣削是指铣刀旋转作主运动, 工件或铣刀作
c粒 切 状 屑
d崩 切 碎 屑
起 振动 ; 切削 试件 拐角 处 时 , 因切 人角 和 铣削 长 度 的增 加 , 逆铣 的摩擦 效应 也 会 引起 切 削振 动 , 在 并
7075铝合金短电弧铣削加工工艺试验研究

7075铝合金短电弧铣削加工工艺试验研究宋丹; 周建平; 王恪典【期刊名称】《《新疆大学学报(自然科学版)》》【年(卷),期】2019(036)004【总页数】6页(P395-399,405)【关键词】短电弧铣削加工; 7075铝合金; 工艺参数; 正交试验; 极差分析; 方差分析【作者】宋丹; 周建平; 王恪典【作者单位】新疆大学机械工程学院新疆乌鲁木齐830047; 西安交通大学机械工程学院陕西西安710049【正文语种】中文【中图分类】TG6610 引言铝及铝合金具有密度低、强度高、耐腐蚀、耐低温等特点,7075铝合金具有良好的综合性能,被誉为铝合金中最优良的类型,高强度远胜其他种类铝合金,广泛应用于航天航空、船舶、汽车等领域[1,2].对铝合金进行机械加工时,尤其是航空用铝合金,切削量大且多为薄壁件,容易产生加工变形,短电弧加工具有无切削力和去除效率高的特点,对提高7075铝合金的高效高质量有较强的实用意义[3,4].短电弧加工技术的出现,成功解决了低效、噪声大、高污染的加工问题.短电弧铣削加工技术是一种非接触式高效放电加工方式,不受材料本身性能所限制,使难加工材料颇为受益[5].在短电弧铣削加工7075铝合金过程中,工艺效果受多种加工参数影响,其加工效果无法准确控制.已有研究者初步进行了短电弧铣削加工下的工艺研究,如许燕等[6]运用灰色理论将多工艺目标问题转化为单一灰关联度的问题,所得参数组合在保证表面质量的前提下有效提高短电弧加工效率并降低电极损耗率;朱晨光等[7]通过改变脉冲频率和占空比等工艺参数对工件表面变质层做出相关研究,得出频率和占空比较高时工件表面更容易产生裂纹,较低的频率和占空比会使熔化凝固层的厚度提高.本文从工艺试验的角度探讨电源参数对短电弧铣削加工的加工效率、电极损耗等方面的影响规律,以此选取电源工艺参数,对工件加工效率进行合理提高,对刀具损耗进行有效降低.1 实验准备1.1 实验装置及原理短电弧铣削试验采用正极性加工,以防溅液和水成1:200比例的水汽混合物作为极间工作介质,液压为0.1 MPa,气压为0.3 MPa[8].(1)电源: 短电弧新型脉冲电源;(2)试验设备: 新疆大学自主研制的数控短电弧铣削机床;(3)工件:试件尺寸为35 mm×35 mm×10 mm的7075铝合金;(4)工具电极:外径为φ18 mm且内径为φ6 mm的圆柱石墨电极;(5)检测装置:精度为0.02 mm的游标卡尺,精度为0.01 g的电子天平.在进行短电弧铣削加工时,工件与刀具分别接短电弧新型脉冲电源的阳极与阴极,在具有一定气、液比例且带压力的混合工作介质的作用下,阳极和阴极的电极表面之间形成等离子通道,其产生的高热能使得工件材料发生局部熔融和汽化,在混合工作介质的冷却和冲刷作用下,使得材料蚀除的一种加工方法称之为短电弧铣削加工.加工原理如图1所示.图1 短电弧铣削加工原理示意图Fig 1 schematic diagram of short arc milling 1.2 工艺试验在短电弧铣削加工过程中,对加工效果产生影响的工艺参数很多,其影响程度各有不同.实验选取电参数作为主要研究对象,具体设定如表1所示.加工工件7075铝合金的化学成分,如表2所示.表1 工艺参数Tab 1 Process parameters工艺参数A(电压U/V)B(占空比D/%)C(频率F/KHz)水平120550.6水平225751水平335852.3表2 7075铝合金化学成分Tab 2 7075 aluminum alloy chemical composition 元素SiFeCuMnMgCrZnTi其它Al质量分数/%0.2360.51.2-2.00.32.1-2.90.18-0.285.1-6.10.20.05余量2 实验结果分析本次实验采用正交实验进行短电弧铣削加工,MRR和TWR作为加工工艺指标,试验工艺评价指标计算公式如下:式中M为工件蚀除量;T为加工时间.式中m为工具电极损耗量.在开展短电弧铣削加工实验后,根据式(1)和(2)对工件的MRR、TWR进行了测量和计算,结果如表3所示.表3 实验结果Tab 3 experimental results序号工艺参数工艺目标ABCMRR/(g·min−1)TWR/%1 1111.45875.886 2 1321.53385.652 33131.62058.848 4 2321.96398.88 5 2211.88039.716 6 3311.82039.377 7 1230.99577.722 8 2131.69347.441 9 3221.96042.3472.1 极差分析极差分析法计算简单、表达直观、分析易懂.对正交实验进行极差分析,可以有效表现出各因素水平变化所引起的实验结果之间的差异,Rj体现出实验中各因素水平下实验结果的变化程度,Rj越大表明该因素对当前工艺指标影响程度越强[9].第j列的因素极差计算如下:式中,kij(i=1,2,3;j=1,2,3)表示第j因素i水平所对应的工艺指标之和的平均值.将表3中的数据,依照公式(3)对两种工艺指标分别进行处理,两个工艺指标的极差分析结果如表4所示.表4 极差分析结果Tab 4 Range analysis results项目ABC材料去除率K1j4.4814.8385.381 K2j5.6765.3535.186 K3j5.6675.6335.257K1j1.4941.6131.794 K2j1.8921.7841.729 K3j1.8891.8781.752极差Rj0.3980.2650.065电极相对损耗比K1j239.260182.175154.979K2j186.037159.785175.440 K3j140.572223.909235.450K1j79.75360.72551.660 K2j62.01253.26258.480 K3j46.85774.63678.483极差Rj32.89621.26226.823根据以上数据和极差分析方法,各影响因素的水平改变对实验结果的影响是不同的,极差R越大,即该影响因素对工艺指标的影响越大[10].由表4可以看出,对于材料去除率,通过R值的比较:0.398>0.265>0.065,即各因素对MRR影响程度水平为:A(电压)> B(占空比)> C(脉冲频率).通过比较电压因素下Kij的值(1.892>1.889>1.494),即K21>K31>K11,意味着电压(A)取第二水平A2所对应的材料去除率最大;同理比较占空比因素下Kij的值(1.878>1.784>1.613),即K32>K22>K12,即当占空比(B)取第三水平B3所对应的材料去除率最大;最后比较脉冲频率因素下Kij的值(1.794>1.752>1.729),即K23>K13>K33,即频率(C)取第二水平C2所对应的材料去除率最大.对于相对电极损耗比,通过R值的比较:32.896>26.823>21.262,即影响因素对TWR的影响主次水平为A(电压)>C(脉冲频率)>B(电压).由表4数据可以得出,通过比较电压因素下Kij的值(46.857<62.012<79.753),即K31<K21<K11,意味着电压(A)取第二水平A3所对应的相对电极损耗比最小,即电极损耗最小;同理比较占空比(B)Kij的值(53.262<60.752<74.636),即K22<K12<K32,意味着占空比(B)取第二水平B2所对应的相对电极损耗比最小;同理比较频率(C)Kij的值(51.660<58.480<78.483),即K13<K23<K33,所以频率(C)取第一水平C1.2.2 方差分析极差分析法是正交设计中频繁使用的一种方法,但极差分析法的运用有所限制,极差法无法充分利用实验数据所提供的信息.面对误差较大或精度要求较高的实验,单一应用极差分析而忽略实验误差影响,将会直接降低实验结果的可靠性[11].因此,本次实验需要对实验数据采用方差分析做进一步的验证.方差分析步骤如下:(1)偏差平方和计算其中SST为样本总偏差;SSj 为因素偏差和;Kij为j 因素i水平所对应的工艺指标之和;n为实验总次数;m为单个因素的水平数.(2)自由度计算总自由度:dft=n−1.各因素自由度:dfj=m−1 式中,n为实验总次数;m为单个因素的水平数.(3)平均偏差平方和计算(4)利用F-检验准侧判断显著性检验按照上述方差分析求解步骤计算所得结果如表5和表6所示.表5 材料去除率的方差分析Tab 5 Analysis of variance of material removal rate方差来源偏差平方和SS自由度f平均偏差平方和MSF值显著性0.31520.1586.7060.03 B 0.10820.0540.9360.443 C 0.00620.0030.0430.958 A 从表5可以看出,显著性为(0.03<0.443<0.958),故电参数对材料去除率的影响水平为:A>B>C,即电压>占空比>脉冲频率.从表6可以看出,显著性为(0.206<0.352<0.556),故电参数对相对电极损耗比的影响水平为:A>C >B,即电压>脉冲频率>占空比.上述电参数影响水平结果与极差分析所得影响程度结果相同,验证了加工参数影响水平的正确性.表6 相对电极损耗比的方差分析Tab 6 Analysis of variance of relative electrode loss ratio方差来源偏差平方和SS自由度f平均偏差平方和MSF值显著性1626.5642813.2822.0830.206 B 706.1032353.0520.6490.556 C 1166.1592583.081.2480.352 A2.3 综合平衡分析法最终的参数组合是基于两种加工工艺指标的综合评价结果,不能仅仅考虑单一加工工艺指标,必须在单个加工工艺指标的最优参数组合的基础上,使用综合平衡法选择多种工艺指标得出最终的最优组合[12].表7 正交试验优化结果Tab 7 Optimization results of orthogonal test加工工艺指标最优组合主次水平MRRA2B3C2A>B>C TWRA3B2C1B>C>A结合表7中各加工工艺指标的电参数组合,通过极差分析和方差分析所得结果,采用综合平衡法综合考虑加工工艺指标,详细分析过程如下:(1)A因素对应两种工艺指标的值为A2和A3,根据影响因素主次水平可以得出MRR中A因素占主要水平,因此选取A2.(2)B因素对应两种工艺指标的值为B2和B3,根据影响因素主次水平可以得出TWR中B因素占主要水平,因此选取B2.(3)C因素对应两种工艺指标的值为C1和C2,根据影响因素主次水平可以得出TWR中C因素占主要水平,因此选取C1.最终根据上述分析过程,考虑最优加工电参数组合为A2B2C1,即电加工参数:电压25 V,占空比75%,频率0.6 KHz.3 结论本文以材料去除率和电极损耗为工艺指标,采用正交试验法进行7075铝合金短电弧铣削加工试验,采用极差分析与方差分析结合的方法对试验结果进行数据处理与分析,研究了电压、占空比和脉冲频率对加工效率及电极损耗的影响,研究结果表明:以电压为25 V、占空比为75%、脉冲频率为0.6 KHz进行短电弧铣削加工,加工稳定性好,材料去除率约为670.3 mm3·min−1,相对电极损耗较小约为39%.参考文献:【相关文献】[1]周达飞.材料概论(第二版)[M].北京:化学工业出版社,2012.ZHOU D F.Introduction to materials (2nd edition) [M].Beijing: Chemical industry press,2012.(in Chinese)[2]陈芙蓉,李国伟.7075铝合金的研究现状[J].机械制造文摘(焊接分册),2019(1): 1-7.CHEN F R,LI G W.Research status of 7075 aluminum alloy [J].Mechanical manufacturing abstract (welding volume),2019(1):1-7.[3]卢江.短电弧加工机理研究[D].乌鲁木齐: 新疆大学,2011.LU J.Research on mechanism of short arc processing [D].Urumqi: Xinjiang university,2011.(in Chinese)[4]徐成龙,仲梁维.航空铝合金薄壁件加工变形控制研究[J].农业装备与车辆工程,2019,57(3): 113-116.XU C L,ZHONG L W.Research on deformation control of aircraft aluminum alloy thin-wall parts [J].Agricultural equipment and vehicle engineering,2019,57(3): 113-116.(inChinese)[5]许以浩,周建平,许燕,等.基于双闭环PI控制的短电弧加工脉冲电源设计[J].新疆大学学报(自然科学版),2017,34(2): 242-247.XU Y H,ZHOU J P,XU Y,et al.Design of short arc processing pulse power supply based on double closed loop PI control [J].Journal of xinjiang university (natural science edition),2017,34(2): 242-247.(in Chinese)[6]许燕,王博,周建平.镍基高温合金短电弧加工工艺参数优化[J].机床与液压,2018,46(11): 106-110.XU Y,WAN G B,ZHOU J P.Optimization of short arc machining process parameters of nickel-based superalloy [J].Machine tool & hydraulics,2008,46(11): 106-110.(in Chinese) [7]朱晨光,周建平,汪兵兵.镍基高温合金脉冲电弧加工表面完整性研究[J].机床与液压,2015,43(11): 27-29+33.ZHU C G,ZHOU J P,WANG B B.Study on surface integrity of pulse arc machining of nickel-based superalloy [J].Machine tool & hydraulics,2015,43(11): 27-29+33.(in Chinese)[8]ZHOU J P ,LIANG C H,TENG W J,et al.Study on Rules in Material Removal Rate and Surface Quality of Short Electric Arc Machining Process[J].Advanced Materials Research,2008,29(33-37): 1313-1318.[9]邱荣贤.7075铝合金电火花线切割表面完整性影响规律研究[D].长春:长春理工大学,2017.QIU R X.Study on the influence of surface integrity of 7075 aluminum alloy edm[D].Changchun: changchun university of science and technology,2017.(in Chinese)[10]殷静凯,李文斌.电火花线切割加工Cr12MoV的参数优化[J].机械设计与制造,2016(2): 248-250+254.YIN J K,LI W B.Parameter optimization of edm Cr12MoV [J].Mechanical design and manufacturing,2016(2): 248-250+254.(in Chinese)[11]邓鹏.钛合金Ti-6Al-4V电火花线切割参数试验研究[D].太原:太原理工大学,2016.DENGP.Experimental study on parameters of ti-6al-4v edm in titanium alloy [D].Taiyuan: Taiyuan university of technology,2016.(in Chinese)[12]何巍杨.工艺参数对短电弧铣削加工性能影响规律研究[D].乌鲁木齐:新疆大学,2018.HE W Y.Study on the influence of process parameters on the machining performance of short arc milling [D].Urumqi: Xinjiang university,2018.(in Chinese)。
铝合金的切削特性分析和工艺技术分析

铝合金的切削特性分析和工艺技术分析作者:郭改嫄来源:《中国科技博览》2017年第05期[摘要]铝合金作为一种复合金属材料,在人们的工作生活中有着广泛的应用。
但是铝合金材料的切削问题一直也是工艺切割制作中的一个重要问题,只有对铝合金的切削特性做出进一步的科学研究,同时在实际的工艺操作中,采用先进的工具以及合理的参数,才能保证铝合金的切削质量,提高铝合金设备的生产效率。
[关键词]铝合金;特性分析;工艺技术中图分类号:TB 文献标识码:A 文章编号:1009-914X(2017)05-0031-01引言随着我国工业的快速发展,铝合金设备的需求量进一步增大,同时对铝合金原材料进行加工时,工序也变的越来越繁杂,对于切削参数也是要求越来越精确。
因此,在工业中对铝合金材料进行切削时,应该对其切削特性以及工艺参数有更加深入的研究,保证在实际应用中,既能避免资源的浪费,又能保证工艺制作质量。
1、铝合金的切削特性分析受到铝合金本身物理特性的影响,切削的问题主要表现在这三个方面:粘刀现象、切削变形以及切削中的振动问题。
切削时,由于摩擦生热,导致铝合金材料的表面开始受热变软直到熔化。
并且由于铝合金具有很好的延展性,导致切屑不能及时掉落,受热之后就会粘在刀口上,造成粘刀现象;铝合金材料质地软,抗塑性变形能力差[1]。
在切削过程中,受热以及受到应力的作用都会导致工件变形,影响使用,造成资源的浪费;在使用刀具对铝合金材料进行切削时,会出现弹性回复的现象,这是由铝合金弹性模量小的原因造成的。
这就回导致切削刀具、给进系统的振动。
另外,切削中,残留在刀口的切屑在熔化以及脱落的过程中,都会产生不同程度的振动。
2、铝合金切削工艺技术了解到铝合金材料的自身特性,针对切削时出现的三个重要问题,对工艺流程进行设计,合理对刀具以及切削参数进行调整,才能够完成对铝合金材料的顺利切削工作,从而保证工件的质量。
2.1 选择刀具材料及参数由于铝合金相对较软的质地,切削铝合金材料时,需要的切削力度是比较小的。
铝合金化学铣切激光刻型工艺参数研究

铝合金化学铣切激光刻型工艺参数研究王帅东;邹松华;尚洪帅;徐方强;郭志辉;王建波【摘要】在铝合金化学铣切工艺中,传统手工刻型一致性差、精度低,已严重影响部分型号产品的化铣质量,急需采用激光刻型进行替代.本文采用正交实验方法,研究了激光刻型的激光功率、刻型速度、胶层厚度等对刻型效果的影响,得出最佳工艺参数为胶层厚度0.4~0.5 mm,激光功率80 W,刻型速度30 mm/s.【期刊名称】《电镀与精饰》【年(卷),期】2019(041)002【总页数】4页(P39-42)【关键词】铝合金;化学铣切;激光刻型【作者】王帅东;邹松华;尚洪帅;徐方强;郭志辉;王建波【作者单位】天津航天长征火箭制造有限公司,天津300462;天津航天长征火箭制造有限公司,天津300462;天津航天长征火箭制造有限公司,天津300462;天津航天长征火箭制造有限公司,天津300462;天津航天长征火箭制造有限公司,天津300462;天津航天长征火箭制造有限公司,天津300462【正文语种】中文【中图分类】TG5铝合金化学铣切是利用含有某些化学元素的化学溶液对铝合金表面进行溶解和腐蚀加工,其基本过程为:在清洗除油的铝合金零件表面涂覆能够抵抗腐蚀溶液作用的可剥性保护胶,经室温或高温固化后进行刻型,然后将需要铣切加工部位的胶层去除,再把零件浸入腐蚀溶液中,对裸露的表面进行腐蚀加工。
化学铣切加工精度高,但也存在成本高、生产周期长、环境污染严重等问题[1]。
实施化学铣切前,需在铝合金表面刻型出需要铣切的图案或形状。
目前,刻型的方法有手工刻型和激光刻型等,手工刻型成本低,但效率低、精度差,激光刻型精度高,效率快。
国外对于激光刻型研究较多。
PRIMA公司的LASERDYNE高精度多轴激光加工系统已用于我国航空发动机薄壁零件表面激光刻型等诸多加工领域[2]。
我国相关制造企业也引进了西班牙TORRESLASER激光刻型机,并成功用于航空蒙皮类零件的化铣加工[3]。
铝合金模具材料的电火花加工条件
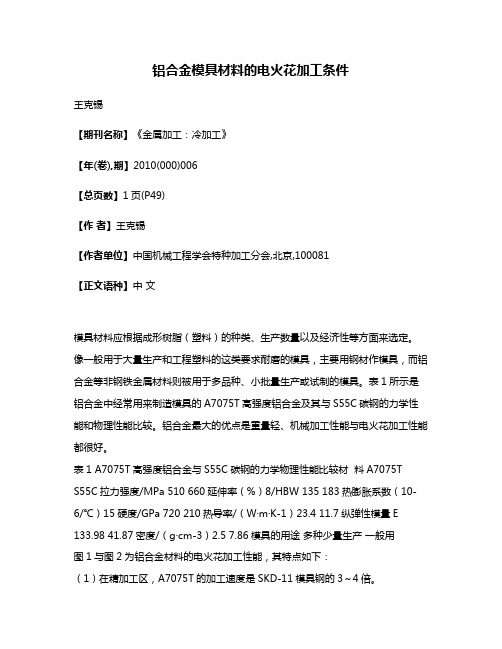
铝合金模具材料的电火花加工条件王克锡【期刊名称】《金属加工:冷加工》【年(卷),期】2010(000)006【总页数】1页(P49)【作者】王克锡【作者单位】中国机械工程学会特种加工分会,北京,100081【正文语种】中文模具材料应根据成形树脂(塑料)的种类、生产数量以及经济性等方面来选定。
像一般用于大量生产和工程塑料的这类要求耐磨的模具,主要用钢材作模具,而铝合金等非钢铁金属材料则被用于多品种、小批量生产或试制的模具。
表1所示是铝合金中经常用来制造模具的A7075T高强度铝合金及其与S55C碳钢的力学性能和物理性能比较。
铝合金最大的优点是重量轻、机械加工性能与电火花加工性能都很好。
表1 A7075T高强度铝合金与S55C碳钢的力学物理性能比较材料A7075TS55C拉力强度/MPa 510 660延伸率(%)8/HBW 135 183热膨胀系数(10-6/℃)15硬度/GPa 720 210热导率/(W·m·K-1)23.4 11.7纵弹性模量E 133.98 41.87密度/(g·cm-3)2.5 7.86模具的用途多种少量生产一般用图1与图2为铝合金材料的电火花加工性能,其特点如下:(1)在精加工区,A7075T的加工速度是SKD-11模具钢的3~4倍。
(2)电极损耗非常小,是 SKD-11的1/2以下。
图1 铝合金与SKD11的加工速度特征(3)加工表面粗糙度值低,在粗加工中比SKD-11大约低30% ~40%,但在精加工区中比 SKD-11大约低6%(见表2)。
(4)粗加工的扩大量(超切)比SKD-11大约低30%,尤其因加工速度快,在使用铝合金作模具材料时能在较短时间内完成模具加工任务,而且还可使用与铜打钢(Cu-St)相同的加工条件。
如果电极损耗率与钢铁类材料相等,那么脉宽时间就可缩短25%,因此,可进一步提高加工速度。
另外,表2是同样放电条件下,A7075T铝合金与S55C碳钢加工表面粗糙度比较。
电火花线切割LY12硬铝实验分析

加工作用,同时还会因短路电流过大,容易造成 WEDM 断丝和电源部件损坏,这种 状态是电加工中严禁的状态,一般电加工机床数控系统都会对其严密监控。
图 1.1 加工间隙放电波形 2. 多线电火花线切割加工效率实验 表 2-1 电火花线切割加工效率实验参数表 试验参数 参数数值 脉宽 14us 脉间 4 5 6us 进给速度 3 步/s 电极丝 D=0.18mm 表面涂有金刚砂的钼丝 丝速 5.8m/s 材料厚度 50mm 切割材料 LY12 硬质铝合金 电解液 工业电解液
T1 U 放电切割时其极间加工脉冲电压电流呈爬坡时增加, 当间隔比及其他 条件一定时, 一定时间与范围内脉宽越大的其电压电流所需爬坡时间越小,一段 时间内能量对电压电流的积分值越大, 故产生脉冲能量越大, 故脉冲宽度为 24us 时加工效率要高于脉冲宽度为 14us 时;当脉冲宽度继续增加,工件时初速度继 续增大且切缝深度越深蚀除物排屑越困难;导致当脉冲宽度 34us 时工件去除速 度无法跟上蚀除物排出速度,导致切片无法顺利切下。 表 2-2 电火花线切割加工效率实验参数表 试验参数 数值 脉宽 24us 间隔比 8us 进给速度 4 5 6 步/s 电极丝 钼丝 D=0.18mm 丝速 5.8m/s 材料厚度 50mm 切割材料 LY12 硬质铝合金 电解液 工业电解液
电火花线切割 LY12 硬铝实验分析 1. 1 实验研究背景 电火花线切割加工在非传统材料的加工中被广泛采用, 非传统材料的加工是电火 花加工的一种独特应用。 电火花加工的适用条件只要工件具有的导电性,即只要 工件是导电的,其加工过程不受工件硬度、韧性与脆性的限制,因此适合加工难 切削材料,例如模具钢、硬质合金、高温合金、石墨或者导电性陶瓷与等材料。 电火花线切割加工是一种非接触式加工, 在加工过程中不受切削力与切削变形的 影响。 在加工过程中电极丝张紧力通过张力控制装置保持恒定,本套机器采用的 是重锤张紧, 避免由于电极丝的振动而产生的工件加工精度误差。电极丝材料通 常为黄铜、涂锌铜、钼、钨等,电极丝的直径通常为 0.02-0.3mm,微细切割时 电极丝直径可达 20-30um,因此线切割加工可以使工件的拐角半径可以很小,可 以满足精密加工的要求。 加工复杂精密工件以及通孔类零件时线切割加工技术的 优异特性得到了很好地展现。 电火花线切割可用于加工冲压模具,间距细小的引 线框模具,微细机械零件,上下异形模具等。电火花成型加工中用的许多特殊形 状的电极都是由电火花线切割方法加工, 比如在航空航天领域中的闭式整体涡轮 叶盘加工所需要的成型电极大部分是采用电火花线切割加工。 电火花线切割加工 也广泛应用于模具、微电子、航空航天和医疗器械等领域。 按照电极丝的运行方向和运丝速度大小等特点,人们把线切割机床分为两类:一 类是往复走丝线切割机床,另一类是单向走丝线切割机床。往复走丝线切割机 床又分为快走丝线切割机床和中走丝线切割机床。 该类型机床的电极丝可以双向 运行循环使用,其走丝速度一般为 8-10 m/s,加工效率可达到 180 mm2/min, 加工工件的的最佳表面质量可以达到粗糙度 Ra =1.2-1.25 µm,多次切割可达到 Ra = 0.8 µm 左右,尺寸精度一般在 0.01mm 左右。往复走丝线切割机床是我国 独创的线切割加工模式,其加工精度和表面质量虽然不及单向走丝线切割机床, 其价格优势使其广泛应用在中小企业中。 单向走丝线切割机床一些关键技术被借 鉴于中走丝线切割机床, 其加工质量要优于快走丝线切割机床;单向走丝线切割 机床顾名思义即电极丝朝单一方向运行加工后不再使用,其走丝速度一般低于 0.2m/s,切割效率最快可达 500 mm2/min,最佳表面粗糙度可达 Ra < 0.05 µm。 这是国外生产和使用的主要机种。 据统计目前国内外的电火花线切割机床在电加 工机床中所占的比例已大于 60%。值得指出的是,单向走丝电火花线切割机床由 于其加工工件表面质量好、加工精度高等特点,在电加工行业被誉为“皇冠上的 明珠” ,因此研究单向走丝线切割加工更具有深远的意义。 1.2 电火花加工机理 每个脉冲放电的微观过程是电场力、磁力、热力、流体动力、电化学和胶体化学 等综合作用的过程。这一过程大致可以分为四个连续阶段:极间介质的电离、击 穿,形成放电通道;介质热分解,电极材料馆化、汽化热膨胀;电极材料的抛出;极 间介质的消电离。 (1)极间介质的电离、击穿,形成放电通道 当脉冲电压施加于电极与工件之间时,两极间形成一个电场。工件与电极的微观 表面凹凸不平,极间距离又很小,因而极间电场强度很不均勻,两极间离得最近的 突出或尖端处的电场强度最大。电场强度最大的地方发生电子发射,电子从阴极 表面逸出,电场的存在使电子不断加速,电子高速向阳极运动,在运动过程中,电 子撞击放电介质的中性分子和原子,产生碰撞电离,形成正负粒子,导致带电粒子 急速增多。 当电子到达阳极时,介质被击穿,产生火花放电,形成导通通道,随后电
铝合金的电火花线切割加工工艺
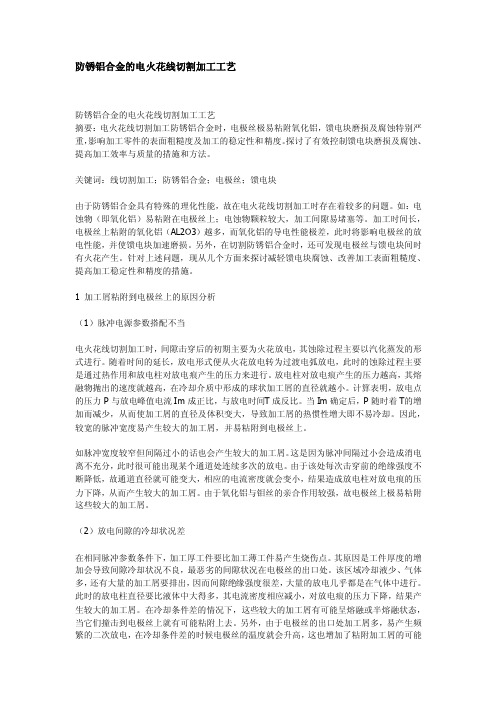
防锈铝合金的电火花线切割加工工艺防锈铝合金的电火花线切割加工工艺摘要:电火花线切割加工防锈铝合金时,电极丝极易粘附氧化铝,馈电块磨损及腐蚀特别严重,影响加工零件的表面粗糙度及加工的稳定性和精度。
探讨了有效控制馈电块磨损及腐蚀、提高加工效率与质量的措施和方法。
关键词:线切割加工;防锈铝合金;电极丝;馈电块由于防锈铝合金具有特殊的理化性能,故在电火花线切割加工时存在着较多的问题。
如:电蚀物(即氧化铝)易粘附在电极丝上;电蚀物颗粒较大,加工间隙易堵塞等。
加工时间长,电极丝上粘附的氧化铝(AL2O3)越多,而氧化铝的导电性能极差,此时将影响电极丝的放电性能,并使馈电块加速磨损。
另外,在切割防锈铝合金时,还可发现电极丝与馈电块间时有火花产生。
针对上述问题,现从几个方面来探讨减轻馈电块腐蚀、改善加工表面粗糙度、提高加工稳定性和精度的措施。
1 加工屑粘附到电极丝上的原因分析(1)脉冲电源参数搭配不当电火花线切割加工时,间隙击穿后的初期主要为火花放电,其蚀除过程主要以汽化蒸发的形式进行。
随着时间的延长,放电形式便从火花放电转为过渡电弧放电,此时的蚀除过程主要是通过热作用和放电柱对放电痕产生的压力来进行。
放电柱对放电痕产生的压力越高,其熔融物抛出的速度就越高,在冷却介质中形成的球状加工屑的直径就越小。
计算表明,放电点的压力P与放电峰值电流Im成正比,与放电时间T成反比。
当Im确定后,P随时着T的增加而减少,从而使加工屑的直径及体积变大,导致加工屑的热惯性增大即不易冷却。
因此,较宽的脉冲宽度易产生较大的加工屑,并易粘附到电极丝上。
如脉冲宽度较窄但间隔过小的话也会产生较大的加工屑。
这是因为脉冲间隔过小会造成消电离不充分,此时很可能出现某个通道处连续多次的放电。
6061铝合金的电火花加工

6061铝合金的电火花加工A.PRAMANIK;A.K.BASAK;M.N.ISLAM;G.LITTLEFAIR【期刊名称】《中国有色金属学报:英文版》【年(卷),期】2015(025)009【摘要】在不同脉冲时间和导线张力下,研究6061铝合金电火花线切割加工过程中材料的去除率、切口/狭缝宽度、表面光洁度和线电极磨损,通过改变脉冲时间和导线张力,在电火花线切割加工机床上进行了8次实验。
结果表明,随着脉冲时间的延长,材料的去除率增加,但导线张力不影响材料的去除率。
较高的导线张力有利于促进加工工艺的稳定性,产生较低的线电极磨损和更好的表面光洁度。
随着脉冲时间的变化,表面粗糙度没有明显变化。
在所有加工条件下,表面外观非常相似。
加工后表面包含凝固熔融材料、飞溅材料和气泡。
由于热量输入的增加,脉冲时间的延长增大了线电极的磨损。
线电极的磨损产生了斜槽,该斜槽正面的切口宽度比底部的宽。
较高的电极损耗会产生较高的锥度。
【总页数】9页(P2866-2874)【作者】A.PRAMANIK;A.K.BASAK;M.N.ISLAM;G.LITTLEFAIR【作者单位】[1] Department of Mechanical Engineering, Curtin University, Bentley, WA 6102, Australia;[2] Adelaide Microscopy, the University of Adelaide, Adelaide, SA 5005, Australia;[3] School of Engineering, Deakin University, Waurn Ponds 3220, Australia【正文语种】中文【中图分类】TG146因版权原因,仅展示原文概要,查看原文内容请购买。
- 1、下载文档前请自行甄别文档内容的完整性,平台不提供额外的编辑、内容补充、找答案等附加服务。
- 2、"仅部分预览"的文档,不可在线预览部分如存在完整性等问题,可反馈申请退款(可完整预览的文档不适用该条件!)。
- 3、如文档侵犯您的权益,请联系客服反馈,我们会尽快为您处理(人工客服工作时间:9:00-18:30)。
砂 轮 磨 削。 Fra bibliotek关键词 : 电火 花铣 削 ; 焊 缝处 理 ; 铝 合金 焊缝 中图分 类号 : T G 6 6 1 文献标 识码 : A 文章 编号 : 1 0 0 9 — 2 7 9 X( 2 0 1 3 ) 0 5 — 0 o 1 8 — 0 3
S t u d y o n EDM - mi l l i n g f o r Al u mi n u m AH o y We l d i n g J o i n t
火花铣 削铝合金 焊缝 的加 工 效率进 行 了研 究。结果表 明 : 铣 削工 艺影 响焊缝 力 学性 能 , 电火花铣 削
工 艺与砂轮 磨 削工 艺处 理 的焊缝 抗拉 性 能相 当;砂 轮 磨 削焊缝表 面为各 向异性 划痕 沟槽 式 分布 ,
电火花铣 削焊缝 表 面为 各 向 同性较 均 匀凹坑 ; 同等 尺 寸要 求下 , 电 火花铣 削工 艺 的尺 寸精 度 高 于
a c c u r a c y .A t l a s t ,t h e p r o c e s s i n g e f i f c i e n c y f o E D M- mi l l i n g o n a l u mi n u m a l l o y w e l d i n g j o i n t s i s r e s e a r c h e d . T h e r e s u l t s s h o w t h a t mi l l i n g p r o c e s s e s e f f e c t e d m e c h a n i c l a p r o p e r t i e s f o w e l d i n g j o i n t s , t h e E D M— mi l l i n g p r o c e s s a n d g r i n d i n g m i l l i n g p r o c e s s i s s i mi l r a o n t e n s i l e p r o p e r t i e s o f w e l d i n g j o i n t s . he T s u r f a c e o f w e l d i n g j o i n t s g r i n d e d a p p e a r t h a t a l u m i n u m l a l o y h a v e s o me a n i s o t r o i c s c r a t c h ro g o v e
《 电加工与模具) 2 0 1 3 年第 5 期
设计 ・ 研 究
铝 合 金 焊 缝 的 电火 花 铣 削 工 艺研 究
郭豫 鹏 , 宋 云龙 , 韦 东波 , 狄 士 春
(哈尔 滨工业 大学 机 电工程 学 院 , 黑 龙 江哈尔 滨 1 5 0 0 0 1)
摘要 : 以铝合 金 焊缝 的 电 火花铣 削 工艺 为研 究对 象 , 利 用 电 火花 铣 削技 术对铝 合金 焊 缝 凸起 进 行 了处理 . 并 与经砂 轮 磨 削 处理 的 焊缝进 行 了力 学性 能 、 表 面 形貌 、 尺寸 精度 的对 比 , 最后 对 电
w e l d i n g j o i n t p r o t r u b e r a n c e s a r e t r e a t e d w i t h E D M- mi l l i n g . T h e w e l d i n g j o i n t s b y E MD— m i l l i n g re a
Gu o Yu p e n g , S o n g Yu n l o n g , We i Do n g b o, Di S h i c h u n
( Ha r b i n I n s t i t u t e o f T e c h n o l o g y , H a r b i n 1 5 0 0 0 1 , C h i n a) A b s t r a c t : B a s e d o n t h e t e c h n o l o g y o f e l e c t i r c a l d i s c h a r g e ma c h i n i n g m i l l i n g( E D M- m i l l i n g ) , he t
c o mp re a d wi t h t h o s e b y g r i n d i n g mi l l i n g ,i n me c h a n i c a l p r a p e r t i e s ,s u r f a c e mo r p h o l o y ,d g i me n t i o n a l