WIX 维克斯滤清器在线查询
海尔 HWP25-G(WH)管道式中央净水机 使用说明书

市政自来水 0.1MPa~0.4MPa 0.1MPa~0.4MPa
图片区5域℃~38℃
≤90%
环境温度
4℃~40℃
净水流量 额度
总净水量 卫生许可 批准文号
出水水质
8.3L/min 30000L
执行标准
16.6L/min 50000L
33.3L/min 100000L
41.6L/min 130000L
体现海尔真诚、贴心的服务,海尔友情提醒您: 海尔产品安装服务,因用户的安装环境、个性需求不同,安装过程中如需
辅加材料或有特殊服务项目支付材料费,具体付费请参照服务工程师出示的 《服务收费指导价格标准手册》。如服务工程师不按标准收费或服务规范执行 不到位,请拨打海尔全国客服电话4006 999 999或登录海尔自助服务专区 评价、投诉。经核实无误,本次服务“免单”。
维护保养
故障诊断及排除
当产品出现故障时,请采取以下步骤或与当地经销服务网点联系予以排除。
故障现象
产水量下 降很多
原因 滤芯被堵塞 水压过低
解决方法 需要进行清洗或更换滤芯,请与 当地经销服务网点联系
采用增压措施
出水水质差 漏水
滤芯失效
长期停用(停用时 间>3天)
接头损坏
请与当地经销服务网点联系, 及时更换滤芯。
海尔,期待您的参与!
如果您的产品有服务需求,欢迎体验海尔自助服务专区 ,在线安装、报修。
8
环保清单
标记“×”部件在废弃后, 如处理不当,会对环境造成污染,也会造成资源的浪费。
产品中限用物质的名称及含量
部件名称
铅(Pb)
金属件
○
塑料件
○
滤芯组件
○
戴森吸尘器说明书
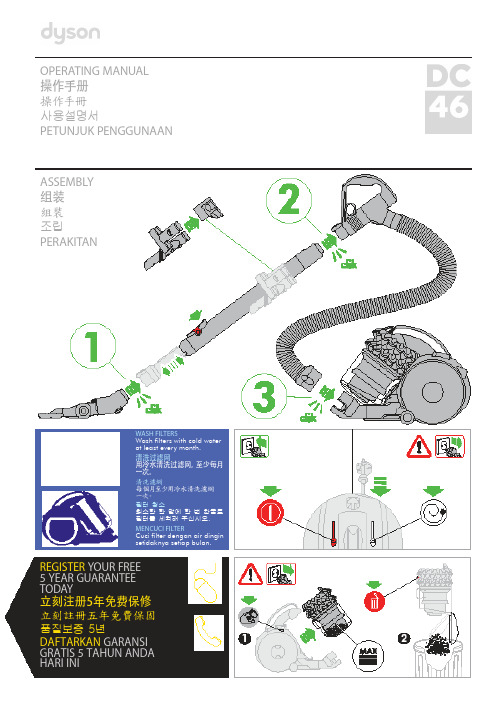
OPERATING MANUAL操作手册操作手冊사용설명서PETUNJUK PENGGUNAANASSEMBLY组装組裝조립PERAKITANWASH FILTERS清洗过滤网清洗濾網필터 청소MENCUCI FILTERREGISTER YOUR FREE5 YEAR GUARANTEE TODAY立刻注册5年免费保修立刻註冊五年免費保固품질보증 5년DAFTARKAN GARANSI GRATIS 5 TAHUN ANDA HARI INIDYSON CUSTOMER CARETHANK YOU FOR CHOOSING TO BUY A DYSON APPLIANCEAfter registering your free 5 year guarantee, your Dyson appliance will be covered for parts and labour for5 years from the date of purchase, subject to the terms of the guarantee.If you have any questions about your Dyson appliance, call the Dyson Helpline with your serial number and details of where/when you bought the appliance.Most questions can be solved over the phone by one of our trained Dyson Helpline staff.Alternatively visit for online help, general tips and useful information about Dyson.戴森客户服务感谢您选择购买戴森产品登记获取 5 年免费保修后,您的戴森产品自购买之日起,将享受 5 年的零件和人工保修服务,但须符合保修条款的规定。
维克斯 'E' 系列泵促进器技术信息说明书

Technical InformationBC442361902253en-0001012Table of ContentsIntroduction (4)Controls (5)Operating Data (6)Displacement,Speed,and Pressure RatingsOverspeed LimitsPVE012Model Number System (8)Shaft Torque Data (8)Performance Curves (9)Installation Dimensions (10)Shaft Options (10)Controls (11)Adjustable Maximum Volume StopLoad Sensing with Pressure LimiterRemote Adjustment CompensatorPVE19/21Model Number System (14)Shaft Torque Data (16)Typical Rear Pumps for Thru-drives (16)Performance Curves (17)PVE19PVE21Installation Dimensions (19)Side Ports and C-type ControlEnd Ports and C-type Control Controls (21)Adjustable Maximum Volume StopLoad Sensing with Pressure LimiterRemote Adjustment CompensatorUnloading ValveShaft Options (24)Thru-drives (25)PVE19/21SAE“A”PVE19/21SAE“B”Application Data (28)34Introduction to PVE Piston PumpsDanfoss PVE piston pumps are inline,variable displacement pumps that are available in three displacement sizes.An assortment of optional controls offer maximum operating flexibility.Pump displacement is varied by means of pressure and/or flow compensator controls.PVE012Section ViewYokeHousingCompensatorValve BlockShaft SealShaftBearingPistonFigure 1.Sectional Views of the PVE PumpsPVE012Section ViewCompensatorFeatures and Benefits•Inline,variabledisplacement pump •Displacement is varied by pressure/flowcompensator controls•Optional controls for maximum operating flexibility•Thru-drive available on PVE 19/21ControlsPressure Compensator Control,“A”OptionThis control automatically varies pump displacement to meet the system flow demand for a constant system pressure.Dis placement starts to reduce to zero within14 bar(200psi)of the com-pensator setting.Power draw-off is minimized, therefore,system relief valves should not be required.Pressure Compensator Control with Maximum Displacement Adjustment As indicated for“A”option above,except there isan independent screw adjustment of maximum displacement from100% (rated)to25%.Load Sensing Compensator and Pressure Limiter,“B”OptionThis compensator provides load sensing control under all pressure conditions up to the desired maximum. It automatically adjusts pump flow in response to a remote pressure signal and maintains outlet pressurePVE with PressureCompensator Arrangedfor Remote Control,“D”Option or“J”OptionExactly the same as the“A”(pressure compensa-tion option)except themachine operator is able tochange the compensatorsetting through the use ofa remote pilot relief valve.Note:Graphic symbolsshown with externalvalve(s)and cylinder toillustrate typical usage.Note:Optional internalbleed orifice diameter is.015’’and is“A”option-control special features.56Displacement,Speed A nd Pressure RatingsModel Number Displacement cm 3/r (in 3/r)Rated Input SpeedMaximum Pressure System Shaft End Pump Cover End Pump (At 0psig Inlet)bar (psi)PVE01225(1.54)–3000210(3000)PVE1941(2.50)–2400210(3000)PVE2145(2.75)–2400186(2700)Pressure Limits Port Pressure RangeInlet**0,2bar to 2,0bar (5in.Hg.vacuum to 30psi)Outlet See Maximum Pressures listed above Drain*0,35bar (5psig)maximum*Integral relief valve protects pump by limiting case pressure peaks to 0,7bar (10psi)above inlet pressure.Flow from valve returned directly to pump inlet.Case drain line required to limit steady-state case pressure.**See page 9for Inlet vs.Speed details.For non-intergrated units onlyPreparation for Start-up Before starting a PVEpump,fill the case through the uppermost drain port with clean system hydrau -lic fluid.The case drain line must be connected to the reservoir below oil level.For multiple pump arrange -ments that include non-PVE sections,the requirements of the non-PVE units must also be considered.MountingDanfoss Hydraulics recom -mends these PVE series piston pumps be mounted horizontally.*Shaded product may not be available7A t Full Flow Conditions Displacement cm /r (in /r)Inlet Pressure/Vacuum*Maximum Speed**rpm PVE21full displacement 45(2.75)5psig 2800PVE19full displacement 41(2.50)0psig 24005in.Hg.21005psig 3100PVE19/21destroked 33(2.00)0psig 27505in.Hg.25005psig 3200PVE19/21destroked 25(1.50)0psig 30005in.Hg.2850PVE012limited to 3000rpm at full displacement and 0psig inlet.*Minimum pressure/vacuum required at pump inlet to operate at displacement and speed listed.**Speeds not listed,but within displacements shown above,may be calculated from values listed.A t Load Sense Standby Condition –“B”O ption ControlsModel Number System Maximum Speed rpm PVE0123600PVE193200PVE213200Pump must be in zero flow,low pressure,standby condition when operated at listed speed.Pump may be damaged if not slowed to normal rated speed before being operated at full flow.Yoke response recorded at rated speed and pressure,0psi inlet,82°C (180°F),SAE 10W oil.Pressure rise was 6900bar (100,000psi)per second.Response DataPVE012PVE19/21ControlT ypeOn Stroke sec.Off Stroke sec.On Stroke sec.Off Stroke sec.Pressure compensator 0.0300.0120.0500.025Load sense compensator0.0400.0120.0600.020Sound Data1200rpm,70bar (1000psi)1500rpm,140bar (2000psi)1800rpm,210bar (3000psi)Model Full Full Full Number Stroke Compensated Stroke Compensated Stroke Compensated System dB(A)Stroke dB(A)dB(A)Stroke dB(A)dB(A)Stroke dB(A)PVE012716576727777PVE19797483858687PVE217573798183*83**2700psiSound level dB(A)per ISO 4412-1standard.81,2Pump SeriesPV –Open Circuit PistonPump3,4,5,6DisplacementE012–25.2cm 3/r (1.54in 3/r)7Input Shaft RotationR –Right-Hand Rotation(cw)L –Left-Hand Rotation(ccw)8,9Front Mounting and Input Shaft01–SAE B 2bolt,Keyed 05–SAE B 2bolt,Splined13t 16/32DP09–SAE B 2bolt,Splined26t 32/64DP10,11Main Ports Location and SizeAU –End ports,SAE o-ring;#20suction,#12pressureAV –End ports,ISO 6149;M42suction,M27pressure12Drain Port Size06–M18metric O-ringport –top (D1)07–M18metric O-ringport –bottom (D2)B –#8SAE O-ring port –top (D1)C –#8SAE O-ring port –bottom (D2)13Diagnostic Pressure Port0–No diagnostic pressureport14ControllerT ypeA –Pressure CompensatorB –Pressure and flowcompensatorC –Electric dual rangepressure Compensator with directional control valveD –Hydraulic remote con -trol pressure compen -satorE –Unloading valve(accumulator Circuits)F –Electric dual rangepressure compensator without directional control valve15,16Pressure Comp./Un -loadingValve Setting00–No pressure compen -sator setting 33–207-214bar(3000-3100psi)17,18Flow Comp.Setting or UnloadValve00–No pressure compen -sator setting 11–9.65-12.41bar(140-180psi)24–22.75-25.51bar(330-370psi)19,20Secondary Compen -sator Setting00–As Given in Code Title 21Control Special Features 0–No Special FeaturesA –Bleed downorifice,LSonlyB –External load-sensingadjustmentG –High rate spring for lowpressure settingJ –Bleed down orifice andhigh rate spring for low pressure setting22Maximum Displace -ment Option1–Standard ajdustment 2–Adjustable maximumdisplacement (set at maximum)23,24Auxiliary Mounting and Output Shaft00–No auxiliary mountingor output shaft25Shaft Seals0–No shaft seal1–Standard shaft seal(nitrile)26,27Special Features00–No special features28,29Paint00–No paint CD –Blue primer30Customer and unit identification0–STD –mark assemblyNumber,full model code and build data Code on plate31Design CodeA –FirstPV E012R 001AU B0B332400A100100CDA712211314252230311,23,4,5,68,910,1115,1617,1819,2023,2426,2728,29Model CodeE Series,PVE012PumpNote:Consult a Danfoss representative for additional settingsPV E 012Shaft Torque DataInput ShaftDesignationThru-drive Option Maximum Input T orque N.m (lb.in.)01SAE “B”straight keyed No 135(1200)05SAE “B”spline 13T ,16/32D.P .,FRMDF No 208(1850)09Special Danfoss 26T for use in rear pump NoN/Aof tandem PVE**-PVE12unitShaft Torque DataPVE012Performance Curves PVE012Oil type:SAE10WOil temperature:49°C(180°F)Inlet pressure:0psiEffective FlowVersus SpeedInput PowerVersus SpeedVolumetric Efficiency Versus Speed9Installation DimensionsPVE012with Pressure CompensatorPVE012Shaft Options#01:SAE“B”Straight Keyed#05:SAE“B”Splined10Adjustmentadjusting rod.Turn theadjusting rod clockwise todecrease maximum pumpdelivery,or counterclock-wise to increase maximumpump delivery,until thedesired setting is obtained.Secure the setting by tight-ening the locknut.To assistinitial priming,the manualadjustment control settingmust be at least40%ofthe maximum flow posi-tion.This control enables maxi-mum pump delivery to beexternally adjusted from25%to100%while main-taining all the standardfeatures of a pressure com-pensated pump.11PVE012Load Sensing withPressure Limiter“A”ControlOptionforrotationcompensator controlR.H.rotatio nthd.SAE O-ringO.D.tubing12PVE012Remote Adjustment CompensatorSee installation dimensionspage10for other details.13141,2Pump SeriesPV –Open Circuit PistonPump3,4,5,6DisplacementE19A –41.0cm 3/r (2.50in 3/r)E21A –45.1cm 3/r (2.75in 3/r)7Input Shaft RotationR –Right-Hand Rotation(cw)L –Left-Hand Rotation(ccw)8,9Front Mounting and Input Shaft01–SAE B 2bolt,Keyed 02–SAE B-B 2bolt,Keyed 04–SAE B 2bolt,tapered 05–SAE B 2bolt,splined13t 16/32DP long shaft08–SAE B-B 2bolt,splined 15t 16/32DP 09–SAE B 2bolt,splined26t 32/64DP10,11Main Ports Locationand SizeAA –Side ports,SAEo-ring;#24suction,#14pressureAB –End ports,SAE o-ring;#24suction,#14pressure AC –Side ports,SAE 4boltflange,Code 61;11/2”suction,1”pressureAD –End ports,SAE 4boltflange,Code 61;11/2”suction,1”pressureAE –Side ports,ISO 6149-1;M48suction,M33pressureAF –End ports,ISO 6149-1;M48suction,M33pressureAS –End ports ISO 61624bolt flange;11/2”suction,1”pressure12Drain Port Size and Location01–#10SAE O-ring port –top (D1)02–#10SAE O-ring port –bottom (D2)06–M18metric O-ringport –top (D1)07–M18metric O-ringport –bottom (D2)13Diagnostic Pressure Port0–No diagnostic pressureport1–#4SAE O-ring port –plugged2–M14metric O-ring port–plugged14ControllerT ypeA –Pressure CompensatorB –Pressure and flowcompensatorC –Electric dual rangepressure compensator with directional control valveD –Hydraulic remote con -trol pressure compen -satorE –Unloading valve(accumulator circuits)F –Electric dual rangepressure compensator without directional control valve15,16Pressure Comp./Un -loadingValve Setting00–No pressurecompensator setting 18–182.7-189.6bar(2650-2750psi)33–206.8-213.7bar(3000-3100psi)17,18Flow Comp.Settingor UnloadValve00–No pressurecompensator setting 11–9.65-12.41bar(140-180psi)14–12.41-15.17bar(180-220psi)24–22.75-25.51bar(330-370psi)19,20Secondary Compen -sator Setting00–No secondary com -pensator setting 04–186.2-193.1bar(2700-2800psi)21Control Special Features 0–No Special Features A –Bleed down orifice B –External load-sensingadjustmentG –High rate spring for lowpressure settingJ –Bleed down orifice andhigh rate spring for low pressure settingPVE19AR01AA10B332400A1AA 1AF CD0A712211314252230311,23,4,5,68,910,1115,1617,1819,2023,2426,2728,29Note:Consult a Danfoss representative for additional settings1522MaximumDisplacement Option1–Standard ajdustment 2–Adjustable maximumdisplacement (set at maximum)23,24Auxiliary Mounting and Output Shaft00–No auxiliary mountingor output shaftAA –SAE A 2bolt w/9T16/32DP external splined shaftAB –2Bolt A (SAE J744-82-2)w/11T 16/32DP ex.splined shaft AC –SAE B 2bolt w/13T16/32DP internal splined coupling AD –SAE B 2bolt w/15T16/32DP internal splined couplingAE –SAE B 2bolt w/26T32/64DP external splined shaft AH –SAE A 2bolt w/9T16/32DP internal splined couplingAJ –SAE A 2bolt w/11T16/32DP internal splined couplingAK –SAE B 2bolt w/26T32/64DP internal splined coupling25Shaft Seals0–No shaft seal1–Flurocarbon shaft seal26,27Special Features00–No special features AA –Auxiliary mountingcover plateAF –Cast iron housing28,29Paint00–No paint CD –Blue primer30Customer and unit identification0–Standard Danfossidentification31Design CodeA –First designPVE19AR01AA10B332400A1AA 1AF CD0A712211314252230311,23,4,5,68,910,1115,1617,1819,2023,2426,2728,29Note:Consult a Danfoss representative for additional settingsShaft Torque Data PVE19/21Typical Rear Pumps for Thru-drives PVE19/21Shaft Torque DataInput Thru-drive MaximumSpline Data Designation Option T orque N.m(lb.in.) 02SAE“BB”straight keyed Y es215(1900)08SAE“BB”spline15T,16/32D.P.,FRSF Y es337(2987)05SAE“B”spline13T,16/32D.P.,FRSF Y es208(1850)01SAE“B”straight keyed No135(1200)09Special Danfoss26T for use in rear pump No N/Aof tandem PVE**-PVE**unitNote:See page22for more details.Typical Rear Pumps for T hru-DrivesModel Code T ypical Rear Pump Model Rear Pump Shaft Code PVE**Thru-drive Coupling AH PVQ10/133PVB5/6Suffix-S214864224V1011(9T/9T Straight)V2062AC PVE0125PVE19/215PVQ20/323864307PVQ40/455(26T/13T Step)V2010or V20201120V(Q)151AD PVE19/218475134PVQ40/458(26T/15T Step)2520V(Q)166AK PVE012PVE19/219627168N/C/26T Straight)PVQ40/451617Inlet pressure:0psiEffective FlowVersus SpeedInput PowerVersus SpeedOverall Efficiency Versus SpeedInlet pressure:0psiInput PowerVersus Speed Overall Efficiency Versus SpeedEffective FlowVersus Speed18PVE19/21with Side PortsMillimeters(inches)19PVE19/21with End Ports Millimeters(inches)20PVE19/21Adjustable Maximum Displacement StopAdjustment Array Loosen the locknut on theadjusting rod.Turn theadjusting rod clockwise todecrease maximum pumpdelivery,or counterclock-wise to increase maximumpump delivery,until thedesired setting is obtained.Secure the setting by tight-ening the locknut.To assistinitial priming,the manualadjustment control settingmust be at least40%ofthe maximum flow position.This control enables maxi-mum pump delivery to beexternally adjusted from25%to100%(it is notrecommended below50%)while maintaining all thestandard features of a pres-sure compensated pump.21PVE19/21PVE19/21Load Sensing with P ressure Limiter Control“B”OptionSee pages19-20for other details and dimensions.PVE19/21Remote Adjustment Compensator Control“D”Option22Unloading Valve Control–“E”OptionWith the unloading valve control the variable pump will unload at a preset pressure.The pump will maintain this no flow,low pressure(approximately14bar(200psi))standby condition,until system pressure drops to about 85%of the preset unloading pressure.The pump will then return on stroke and provide full flow until the preset unloading pressure is reached again. With this control,an efficient accumulator charging circuit is obtained. The pump will provide full flow to fill the accumulator until the maximum charging pressure is reached.The pump then goes to a standby condition until the accumulator pressure drops to85%of the desired maximum. The accumulator is then recharged as the cycle starts over again.A separate right angle check valve must be provided to maintain the accumulator hydraulic charge and prevent back flow when the pumpis unloaded.The check valve’s internal leakage must not exceed five drops per minute.The control port must be connectedto system pressure, downstream of the check valve.Adjustment rangePVE19100-210bar(1500-3000psi)PVE21100-186bar(1500-2700psi)Cut-in pressure is85%of unloading pressure,minimum.Setting Pressures1.Back out accumulatorunloading pressureadjustment screw tobelow desired unloadingpressure.2.Adjust desired standbypressure.3.Set accumulatorpressure by screwingin the accumulatorunloading adjustmentscrew.Accumulatorrecharge(cut-in)pressure is a functionof the maximumaccumulator pressureand is not adjustable.4.Check pressuresettings and re-adjust ifnecessary.2324Shaft OptionsPVE19/216.376.35(0.251)(0.250)No.SAE No.No.04Shaft:T apered Key shaft}PV E19/21S AE“A”T hru-drivesThru-DIM.“A”DIM.“B”DIM.“C”MaxT orque Rating Couplingshaft Spline Data mm(in.)mm(in.)mm(in.)N.m(In.lbs.)Length Dim“D”mm(in.) AA9teeth16/32DP50,812,722,658864224 Flat Root Side Fit(2.00)(0.50)(0.89)(517)62,7(2.47)62,2(2.45)AB11teeth16/32DP50,814,522,6123864325 Flat Root Side Fit(2.00)(0.57)(0.89)(1100)60,9(2.40)60,7(2.39) Note:Couplings,screws and washers must be ordered separately to mount rear pump.“A”O-ring(AS568-042)is included with each thru-drive pump.25PV E19/21S AE“B”T hru-drivesThru-MaxT orque Rating DIM.“A”Couplingshaft Spline Data N.m(In.lbs.)mm(in.)Length Dim“D”mm(in.)AE Special Danfoss26tooth17910,9864307 32/64DP Flat Root Side Fit(1587)(0.43)26T/13T20,6475134(0.81)26T/15T24,9627168(0.98)26T/26T26Support BracketAn optional support bracketshould be used when aheavy second pump ismounted to a thru-drivePVE19/21.The supportbracket(627179),twoscrews(199740),and twowashers(427700)must beordered separately.27Application DataFluid CleanlinessProper fluid conditionis essential for longand satisfactory life of hydraulic components and systems.Hydraulic fluidmust have the correct balance of cleanliness, materials,and ad ditives for protection against wearof components,elevated viscosity,and inclusion of air.Fluid contamination levels according to ISO4406 should not exceed21/18/13 for PVE Piston pumps. Essential information on the correct methods for treating hydraulic fluid is includedin Danfoss publication561“Danfoss Guide to Systemic Contamina tion Control”available from your local Danfoss distributor or by contacting Danfoss Hydraulics. Recommendations on filtration and the selectionof products to control fluid condition are included in561.Recommended cleanlinesslevels,using petroleum oilunder common conditions,are based on the highestfluid pressure levels in thesystem and are coded inthe chart below.Fluidsother than petroleum,severe service cycles,ortemperature extremes arecause for adjustment ofthese cleanliness codes.See Danfoss publication561for exact details.Danfoss products,as anycomponents,will operatewith apparent satisfactionin fluids with highercleanliness codes thanthose described.Othermanufacturers will oftenrecommend levels abovethose specified.Experiencehas shown,however,that life of any hydrauliccomponent is shortenedin fluids with highercleanliness codes thanthose listed below.Thesecodes have been proven toprovide a long,trouble-freeservice life for the productsshown,regardless of themanufacturer.Fire resistant fluidsWater glycol,phosphateester and polyol ester fluidsmay be used with PVEpumps.With the PVE012and PVE19,systempressure and input speedshould not exceed140bar(2000psi)and1800r/min.System temperatureshould not exceed54°C(130°F).Inlet vacuumshould not exceed101,6millibar(3in.Hg.).Hydraulic fluids andtemperature rangesUse antiwear hydraulicoil,or automotive typecrankcase oil designationsSC,SD,SE or SF per SAEJ183FEB80.Select a viscosity gradethat will allow optimumviscosity,between40cSt(180SUS)and16cST(80SUS),to be achieved withinthe optimum performanceenvelope shown.For further information,seeDanfoss Hydraulic Hints andTrouble Shooting Guide.Ordering procedureOrder PVE pumps by thefull model designation.Pump displacement,mounting flange type,direction of rotation,pumpconfiguration,shaft endtype,seals,pressureadjustment range,specificcontrol functions are allspecified in the full modelcode.28Notes29Danfoss Power Solutions is a global manufacturer and supplier of high-quality hydraulic and electric components.We specialize in providing state-of-the-art technology and solutions marine sector.Building on our extensive applications expertise,we work closely with you to ensure exceptional performance for a broad range of applications.We help you and other customers around the world speed up system development,reduce costs and bring vehicles and vessels to market faster.Danfoss Power Solutions –your strongest partner in mobile hydraulics and mobile Go to for further product information.outstanding performance.And with an extensive network of Global Service Partners,we also provide you with comprehensive global service for all of our components.Local address:DanfossPower Solutions GmbH &Co.OHG Krokamp 35D-24539Neumünster,Germany Phone:+4943218710DanfossPower Solutions ApS Nordborgvej 81DK-6430Nordborg,Denmark Phone:+4574882222DanfossPower Solutions (US)Company 2800East 13th Street Ames,IA 50010,USA Phone:+15152396000DanfossPower Solutions Trading (Shanghai)Co.,Ltd.Building #22,No.1000Jin Hai Rd Jin Qiao,Pudong New District Shanghai,China 201206Phone:+862120806201Danfoss can acceptno responsibility for possible errors in catalogues,brochures and other printed material.Danfoss reserves the right to alter its products without notice.This also applies to productsagreed.All trademarks in this material are property of the respective companies.Danfoss and the Danfoss logotype are trademarks of Danfoss A/S.All rights reserved.©Danfoss |September 2022•Cartridge valves •DCV directional control valves•Electric converters •Electric machines •Electric motors •Gear motors •Gear pumps •Hydraulic integrated circuits (HICs)•Hydrostatic motors •Hydrostatic pumps •Orbital motors •PLUS+1®controllers •PLUS+1®displays •PLUS+1®joysticks and pedals•PLUS+1®operator interfaces•PLUS+1®sensors •PLUS+1®software •PLUS+1®software services,support and training •Position controls and sensors•PVG proportional valves •Steering components and systems •TelematicsHydro-Gear Daikin-Sauer-Danfoss。
Sample Filters 76 微纤维过滤芯说明说明书

Microfibre Filter Cartridges efficiently separate suspend -ed liquids from gases. The micro fibers capture the fine liquid droplets suspended in the gas and cause the drop -lets to run together to form large drops within the depth of the filter cartridge. The large drops, forced by the gas, flow to the downstream surface of the filter cartridge, from which the liquid drains by gravity. This process is called “coalescing”. Since the coalesced liquid drains from the cartridge at the same rate that liquid droplets enter the cartridge, the cartridge has an unlimited life when coalescing liquids from relatively clean gases, and the filters operate at their initial retention efficiency even when wet with liquid (see Figure 1). Note that the flow direction is inside-to-outside, to permit the liquid to drip from the outside of the filter to the housing drain.Since the coalesced liquid drips from the downstream surface of the filter cartridge in the presence of filtered gas, it is important to avoid carryover, or entrainment, of liquid droplets by the gas leaving the filter housing. The possibility of entraining coalesced liquid is mini -mized by using an X-Type filter cartridge. The X-Type filter cartridges are constructed of two layers, an inner high-efficiency coalescing layer and an outer layer of coarse glass fibers. The coarse, rapidly-draining outer layer ensures that the liquid drips continuously from the bottom of the filter cartridge and minimizes the chance of liquid carryover. (The small internal volume of some filter housings does not permit use of the thick-wall X-Type cartridges, and therefore Q-Type cartridges must be used.) Re-entrainment of coalesced liquid is also avoided by ensuring that the gas flow rate through the housing is safely below the maximum shown in the flow charts on page 40. For most requirements for removing liquid from gas samples, Grade DX or DQ filter cartridg -es should be used.Coalescing Filtration: Separating Liquids From GasesFigure 1Balston Compressed Air FilterDraining Collected LiquidI f liquid is carried into the filter in slugs rather than dispersed as droplets in the gas, a filter which is prop -erly sized for steady-state conditions can be flooded and permit liquid carryover. If slugging of liquid is expected, a filter with a relatively large bowl should be selected to provide adequate liquid holding capac -ity and provisions should be made to drain the liquid automatically from the bowl of the housing as fast as it accumulates. An automatic float drain can be used if the pressure is in the 10-400 psig (0.69-28 barg) range. Above 400 psig (28 barg), the possibilities are: a constant bleed drain, a valve with automatic timed actuator (supplied by customer), or an exter -nal reservoir with manual valves (see Figure 2). The external reservoir can be constructed of pipe or tubing with sufficient volume to hold all the liquid which is ex -pected to be collected during any period of unattended operation.If the filter is under vacuum, the external reservoir is a practical method of collecting coalesced liquid for manual draining from time to time. If an external vacuum source, such as an aspirator, is available, the liquid may be drained continuously from the housing drain port.Figure 2To drain liquid while filter is operating at pressure or vacuum conditions, closevalve #1, and open valve #2Sample Filter FunctionsCoalescing Filtration:Separating Two Liquid PhasesI n principle, Microfibre Filter Cartridges separate sus-pended droplets of a liquid which is immiscible in anoth-er liquid by the same process as they separate droplets of liquid from a gas. The liquid droplets suspended in the continuous liquid phase are trapped on the fibers and run together to form large drops, which are then forced through the filter to the downstream surface. The large drops separate from the continuous liquid phase by gravity difference, settling if heavier than the continu-ous phase and rising if lighter. The coalescing action of Balston® filters is effective with aqueous droplets sus-pended in oil or other hydrocarbons, and also with oil in water suspensions.In practice, liquid-liquid separations are much more dif-ficult than liquid-gas separations. The specific gravity difference between two liquids is always less than be-tween a liquid and a gas, and therefore a longer phase separation time is needed. Either the filter housing must be oversized or the flow rate greatly reduced to avoid carryover of the coalesced phase. As a rule of thumb, flow rate for liquid-liquid separation should be no more than one-fifth the flow rate for solid- liquid separation shown in the chart on page 77. Even at low flow rates, if the specific gravity difference between the two liquids is less than 0.1 units (for example, if an oil suspendedin water has a specific gravity between 0.9 and 1.1), the separation time for the coalesced phase may be imprac-ticably long. In that case, if there is only a small quantity of suspended liquid, the filter tube can be used until saturated with the suspended liquid and then changed. Another practical problem with liquid-liquid separationsis that small quantities of impurities can act as surface-active agents and interfere with the coalescing action. For that reason it is not possible to predict accurately the performance of a liquid-liquid coalescing filter, and each system must be tested on site. The general guidelines for the system to start testing are to use Grade DX filter cartridges, and flow inside-to-outside at very low flow rates. If the suspended liquid is lighter than the continu-ous phase, the housing should be oriented so that the drain port is up. In general, Microfibre Filter Cartridges should be used for liquid-liquid coalescing in slipstream sampling applications only.Membrane Separation ofSample StreamsA Coalescer Membrane Combination Filter is de-signed to remove entrained liquid and particulate in gas samples for a wide variety of applications, and to prevent contamination or damage to the analyzers and sample system components. Microscopic pores con-tained within the membrane permit molecules of gas or vapor to flow through easily, allowing the composition of the sample gas to remain unchanged. However, even the smallest liquid molecules remain trapped and are unable to flow through the membrane’s small passages under normal operating conditions. This is due to the high surface tension which causes liquid molecules to bind tightly together to form a group of molecules, mov-ing together, which is too large to fit through the pores of the membrane.The membrane is extremely inert, and is recommended for most process liquid applications, with the exception of hydrofluoric acid. It is also recommended for use in systems designed for PPB, PPM, and “percent level” component concentrations, as a result of its very low absorption characteristics. The membrane is strong and durable, but also very soft and pliable. Typically located upstream from the analyzer or component itis protecting, the Coalescer Membrane Combination provides protection even if other sample system com-ponents fail.Removing Gas Bubbles from LiquidsMicrofibre Filter Cartridges readily remove suspended gas bubbles from liquid, eliminating the need for deaera-tion tanks, baffles, or other separation devices. Flow direction through the filter is outside-to-inside. The sepa-rated gas bubbles rise to the top of the housing and are vented through the drain port. If slipstream sampling is used, the separated bubbles are swept out of the hous-ing with the bypassed liquid. Grade DX or Grade DQ is a good choice for gas bubble separation.Sample Filter FunctionsSlipstream or Bypass SamplingI nstrument sample use rates are invariably quite low, yet it is essential to minimize lag time in the sample system. Since analyzers often are located some distance from the sampling point, samples are usu -ally transported to the analyzer at a relatively high flow rate to minimize lag time. The sample is divided at the analyzer, with the analyzer using the portion it requires (usually a very small fraction of the total sample), and the balance recycled to the process, or vented.If the sample filter is located in the low-flow line to the analyzer, it will have good life between filter element changes because the solids loading rate is very low; however, the filter must be carefully selected to avoid introducing unacceptable lag time. If the filter is located in the high-flow portion of the sample system, its effect on sample lag time can be relatively low, but the life between filter changes may be inconveniently short because the element is filtering a much greater volume of material than the analyzer is using.Ideally, a filter should be located at the point where the low-flow stream is withdrawn to the analyzer (Figure 4). This arrangement permits the main volume of the filter to be swept continuously by the high flow rate stream, thus minimizing lag time; at the same time, only the low-flow stream to the analyzer is filtered, thus maximizing filter life.A slipstream filter requires inlet and outlet ports at op -posite ends of the filter element to allow the high flow rate of the by-passed material to sweep the surface of the filter element and the filter reservoir, and a third port connected to the low flow rate line to the analyzer, which allows filtered samples to be withdrawn from the filter reservoir.The Model 95 housings, 31GCFL, 41GCFL, 48S6, 49S6, DFU 8822-11, and DFU 8833-11 are ideal designs for slipstream sampling, since the inlet and the bypass ports are located at opposite ends of the housing, and the bypass port is as large as the inlet port. Larger housings, such as the Model 33S6, Model 45S6, and Model 27/35, can also be used for slipstream sampling, but the relatively small size of the drain port may limit the slipstream rate in some applications.If bubble removal from a liquid is a requirement, this function may be combined with slipstream filtration, since the recommended flow direction for bubble re -moval is outside-to-inside, and the separated bubbles will be swept out of the housing by the bypass stream. In this case, the liquid feed should enter at the bottom of the housing and the bypass liquid exit at the top of the housing.Figure 3Filter cartridge and retainer disc of Model 30 housing may be weighed as a unit for quantita-tive determination of solids in gases.Quantitative Measurement of Solids in GasQuantitative determination of solids in gas, often a requirement in stack gas or other exhaust gas sam -pling, is readily accomplished using a Balston ® Model 30 filter housing. In the Model 30 housing, the filter cartridge is sealed in place by a stainless steel spring acting on a lightweight stainless retainer disc (Figure 3). The retainer disc is pressed firmly into the end of the filter cartridge. When the housing is disassembled, the filter cartridge and retainer disc may be easily removed as a unit. At the beginning of the run, a tare weight is obtained on the filter cartridge-retainer disc assem -bly. When the filter is in service, flow through the filter cartridge is inside-to-outside so that even large solid particles which fall off the filter cartridge are held in the cartridge-disc assembly. At the conclusion of the run with a known volume of gas, the cartridge-disc assem -bly is reweighed, and the increase in weight can be ex -pressed as solids concentration in the gas. Grade DH Filter Cartridges are recommended for high temperature sampling (up to 900°F/482°C). If the sampling or oven-drying temperatures do not exceed 300°F (149°C), Grade DQ may be used.Sample Filter FunctionsA special problem arises in slipstream sampling if the filter is to coalesce and continuously drain suspended liquid from a gas stream or to coalesce liquid droplets from a liquid stream. As noted earlier (see page 32), the coalesced liquid is removed in the form of large drops from the downstream side of the filter. There -fore, the coalescing filter requires two outlet ports, one for the dry gas and one for the liquid drain. To com -bine coalescing and slipstream filtration, a filter hous -ing would need four ports - two for inlet and bypass and two for filtered gas and coalesced liquid - which is not a practical design. Therefore, slipstream -ing plus coalescing requires two stages of filtration (Figure 5). The second (coalescing) stage must be located in the sample line to the analyzer, and should be as small as possible to minimize lag time. If the quantity of suspended liquid is not large, an in-line Disposable Filter Unit (9933-05 or 9922-05) may be considered as a trap for the suspended liquid, to bereplaced when saturated.Figure 5Slipstream Filtration plus coalescing filtrationFigure 4Slipstream or bypass filtrationQuantitative determination of nonvolatile liquids sus -pended in a gas may be accomplished by a procedure similar to the solids determination (see page 68). In the case of liquids, the test is designed so that all the liquid entering the filter cartridge during the test period remains trapped on the fibers; i.e., the sample period is short enough that the filter cartridge does not become saturated and begin to drain liquid.Any convenient filter housing may be used. The filter cartridge should be Grade BQ, to assure quantitative retention of aerosols, no matter what droplet size. With a known gas flow rate and test duration, the increase in weight of the filter cartridge will be a mea -sure of the weight concentration of aerosol in the gas.Considerable care must be taken to obtain a repre -sentative sample of aerosol in gas. If sampling from a large line, the sample probe should enter the pipe from above and if possible, extend into the pipe to avoid picking up liquid clinging to the wall of the pipe. There should be no valves, reducers, or sharp elbows in the sample line upstream from the filter.Quantitative Measurement of Liquids in GasSlipstream Sampling Plus Coalescing FiltrationSample Filter FunctionsA frequently encountered sampling requirement is to analyze the gas composition in the exhaust from absorbers or scrubbers in acid manufacturing plants. The exhaust gas invariably contains droplets of dilute acid, which must be removed from the sample before it enters the analyzer. The recommendations are simi -lar to those for natural gas sample filtration: Grade DQ or DX filter tube, inside-to-outside flow, and two stages of filtration if slipstream sampling is required. Depending upon the composition of the suspended liquid, housings may be stainless steel, PTFE (Model 95T), Monel (Model 95M), or PVDF (DFU 8822-11).Sampling Ambient Air or Other Atmospheric Pressure GasThe filtration requirement for ambient air samplers is usually to remove solid particles or liquid droplets which could deposit on analyzer optical surfaces or cause other calibration problems. Grade DX or DQ filter cartridges are recommended. For low flow rate personal samplers, the compact and lightweight DFU 9933-05-DQ is often used. For higher flow rates, the Model 90 filter holder with Grade DX or DQ filters is recommended.Ambient air sampling systems are often under nega -tive pressure, induced by the sampling pump. If it is necessary to drain coalesced liquid from the system, the external reservoir is often the most convenient method (see Figure 2 on page 66).Sampling WaterMost water analyzers are well protected against the damage or calibration drift caused by solid contami -nation if a 10 micron (LP Grade 30) filter cartridge is used. If long filter life is desired in a system with high solids loading (including most tap water, well water, and cooling water), a two stage LP cartridge system is recommended: LP Grade 10 followed by LP Grade 30.Liquid effluent analyzers usually deal with aqueous streams having a high solids content. In addition, the analyzers are often located in remote areas of the plant and are infrequently serviced. Therefore, the sample filter system must have long life between filter cartridge changes, even in a high solids situation. The general recommendation for this requirement is a two stage filter system, LP Grade 10 filter cartridge followed by LP Grade 30 filter cartridge. The filters should be oversized as much as possible without causing excessive lag time. Plastic filter housings are usually a good choice.Measurements of steam and condensate conductiv -ity, specific ion concentrations, and feedwater additive concentrations are often required in high pressure boiler systems. In a continuous sampling system, the high pressure steam or condensate is cooled to below 100°F (38°C) and then the pressure is reduced to near atmo -spheric pressure for metering to the analyzers. Filtration is required upstream from the pressure reducing valves, to prevent pitting of the valve seats by suspended particles and to eliminate variations in flow rate to the analyzers.A stainless steel filter housing with the appropriate pressure rating and Grade DX or DQ filter cartridge is recommended. Since the analyzer system is often lo -cated some distance from the sampling point, slipstream filtration is usually required. Figure 9 shows a sampling system in operation at a nuclear steam generating facil -ity.Sampling Liquid Effluent StreamsAcid Plant Stack GasFigure 9Model 27 filter with Grade DX filter cartridge protects pressurereducing valves in a steam condensate sampling system.Application RecommendationsOn-Line Process AnalyzersThe variety of filtration requirements for on-line process analyzers precludes making general recommendations above for the required filtration functions. The filter housings most frequently used for process analyzer ap -plications are the Model 95S6 and Model 91S6, which provide the corrosion resistance of Model 316 stainless steel (complies with NACE specification MR-01-75), a pressure rating of 5000 psig (345 barg), have full slipstream sampling capability, and minimum internal volume.Figure 6Model 95S6, 316 stainless steel with 5,000 psig pres-sure rating, is the filter housing most frequently used in process analyzersNatural Gas AnalyzersTo protect gas composition analyzers from liquids and solids, Grade DX or DQ filter tubes are recommended, with inside-out flow direction. If both slipstream sampling and coalescing are required, a two stage system must be used, as described on page 75.The Model 85, 5000 psig (345 barg) rating and Model 37, 4000 psig (276 barg) rating housings comply with NACE specification MR-01-75. For lower pressure ap -plications, any stainless steel housing of appropriate flow capacity may be used.Figure 7Model 85 (left) or Model 37/12 (right) are used for natural gas sample filtration when a h ousing l arger than the Model 95S6 is requiredStack Gas SamplingThe Model 30 housing with Grade DH filter cartridge is used for quantitative determination of solids in stack gas, as described on page 68. The Model 30 may also be used as a beginning-of-the-line filter at stack gas temperature up to 900°F (95°C), to prevent solids from entering the gas sample line. Grade DH is used for this purpose. After the sample is cooled, a coalescing filter with Grade DX tube is used to remove suspended liquids before the sample goes to the analyzer. Flow direction is inside-to-outside. Model 33G or 45G hous -ings are often used in this application to permit a visual check on the liquid level in the filter housing. Since there often is a considerable amount of liquid present at this point, positive steps must be taken to drain the housing to ensure that liquid does not build up and carry downstream to the analyzer.The coalescing filter should be located as close to the analyzer as possible to minimize the chance of con -densation between the filter and the analyzer. Addi -tional precautions which can be taken to avoid down -stream condensation are to cool the sample below ambient temperature upstream from the coalescing filter, and to heat the line.Figure 8Stack gas sample lines usually require a high temperature solids filter at the sample point and a condensate separator immediately upstream from the analyzerApplication Recommendations。
三滤速查表

4.0排量 化油器 新款ACR50 国产四川 进口 进口 1.5T 1.5
SA-120T SA-108P SA-1120H SA-120T SA-147T
SO-114 SO-111 SO-111 SO-110 SO-115 SO-111
SF-190 SF-190 SF-103
SF-368
SUV车
汽油车 柴油车
新款C200
2012款
越野车
SA-1003 SO-415 SF-C18 SA-C149U SO-W03B SF-S1915B SA-1013H SA-C196/196 SO-110 SF-C18 SA-C809P SO-C907 SF-C18 SA-1120H SO-P02/C907 SA-809P SA-1003 SO-415 SA-150P SO-932 SF-420 SA-714 SO-932 SF-C004 SA-150P SO-110 SF-155 SA-C179 SA-1003 SO-110 SI-118 SA-H504 SO-D727/1X SF-190/SF-H0820铝的 SO-D727/1X SA-D004U SA-D100U SA-D299U SO-D727/1X SA-D305U/长形不规则 SO-D718/1K SO-D951 SA-D141U SA-D211U SA-D242U SA-D293U SA-D299U SO-D718/1K SA-D143U SO-D7185X SA-D455 SO-D7185X SO-S8280PO SF-D02 SA-D472U SA-D927U SA-D455/2 SO-D7185X SA-D305 SO-D514 SA-D455 SO-D718/5X SF-D31 SA-D455U SO-D718/5 SA-D455U SO-D718/5 SA-D472U SO-D727/1X
海滩S166T高速沙滤器产品说明书

Your Hayward S166T high-rate sand filter is a high performance, totally corrosion-proof filter that blends superior flow characteristics and features with ease of operation. It represents the very latest in high-rate sand filter technology. It is virtually foolproof in design and operation and when installed, operated and maintained according to instructions, your filter will produce clear, sparkling water with only the least attention and care. HOW IT WORKSYour filter uses special filter sand to remove dirt particles from pool water. The sand is loaded into the filter tank and functions as the permanent dirt removing media. The pool water, which contains suspended dirt particles, is pumped through your piping system and is automatically directed by the patented filter control valve to the top of the filter tank. As the pool water is pumped through the filter sand, dirt particles are trapped by the sand bed, and filtered out. The cleaned pool water is returned from the bottom of the filter tank, through the control valve and back to the pool through the piping system. This entire sequence is continuous and automatic and provides for total recirculation of pool water through your filter and piping system.After a period of time, the accumulated dirt in the filter causes a resistance to flow, and the flow diminishes. This means it is time to clean (backwash) your filter. With the control valve in the backwash position, the water flow is automatically reversed through the filter so that it is directed to the bottom of the tank, up through the sand, flushing the previously trapped dirt and debris out the waste line. Once the filter is backwashed (cleaned) of dirt, the control valve is manually resequenced to Rinse, and then Filter, to resume normal filtering. INSTALLATIONOnly simple tools (screwdriver and wrenches), plus pipe sealant for plastic adapters, are required to install and/or service filter.The filter should be placed on a level concrete slab, very firm ground, or equivalent as recommended by your pool dealer. Position the filter so that the piping connections, control valve and winter drain are convenient and accessible for operation, servicing and winterizing.Your filter is supplied complete with an optional pump mounting base which is pre-drilled for use with Hayward Power-Flo LX series pumps. The pump to filter connecting hoses supplied will accommodate Power-Flo LX pumps used with the mounting base, and Max-Flo or Super Pump installed at surface level. To connect pump to filter:Screw straight adapter, using Teflon pipe sealanttape or Permatex No. 2, securely into pumpdischarge. (Do not overtighten.)Screw elbow adapter, using Teflon pipe sealanttape or Permatex No. 2, securely into opening incontrol valve marked PUMP. (Do not overtighten.)Elbow should point just over RETURN opening. 1.2.a.b.IS166TN2-00PUMP MOUNTINGBASE (S164C)33”(84 cm)SPECIFICATIONSMODEL NUMBER EFFECTIVE FILTRATION AREADESIGN FLOW RATE MAXIMUM WORKINGPRESSURE REQUIRED CLEARANCEMEDIA REQUIRED FT 21.4S166TM 20.13GPM 35LPM 133PSI 50BAR 3.45INCH 18INCH 18MM 457MM 457FILTER SAND*0.45-0.55LBS 100KGS 45ABOVE SIDE TYPE AMOUNT *Also known as No. 20 or No. 1/2 Silica Sand.NOTE: ANSI/NSPI-4 Article V, standard for above-groundand on-ground pools, advises that components such as the filtration system, pumps and heater be positioned so as to prevent their being used as a means of access to the pool by young children.PARTS Model S166TS166T1575XS S166T1575XSN2REF.NO.123456891011121314*15*16*17*18**19**NO.REQ’D.11111111011112112111PART NO.SP071113ECX27081GMX600F GMX600NS SX202S SX164DA SX200Q SX180G SX180H SX164B SX164C ECX1108A SX160Z5SPX1105Z4ECX18028SPX1091Z2N2SABG SX164DAN2KITDESCRIPTIONVari-Flo Control Valve Assembly Pressure Gauge Valve/Tank O-Ring Flange Clamp (Valve-Tank)Sand ShieldLateral Assembly with Center Pipe Filter Tank with Skirt,Complete Lateral Assembly Lateral Gasket Drain CapFilter Support Stand (Skirt)Pump Base5/16”x 3/4”Mounting Screw Kit 1-1/2”Hose1-1/2”Elbow Adapter Hose Clamp1-1/2”Straight Hose Adapter Nature 2CanisterFolding Umbrella Lateral Assembly w/Center Pipe for Nature 2Canister*Furnished with PAK or System only.**Included only on filters supplied with SwimPure CanisterSX164AA17STOP here and load media per instructions (No. 3).Place hose clamps on clear hose and fit hose overstraight and elbow adapters and secure with clamps. Ifit is difficult to fit hose over the adapters, place hose inhot water for several minutes.NOTE:To prevent breakage and damage to pump and control valve, use only pipe sealants specifically formulated for plastics. Do not overtighten fittings or adapters.Loading sand media. Filter sand media is loaded through the top opening of the filter.Loosen flange clamp and remove Filter Control Valve(if previously installed).Cap internal pipe with sand shield to prevent sandfrom entering it. Be sure pipe is securely in place inbottom underdrain hub.We recommend filling tank approximately 1/2 way withwater to provide a cushioning effect when the filtersand is poured in. This helps protect the underdrainlaterals from excessive shock. (Be sure the winterdrain cap is securely in place on drain pipe.) Note:Check to confirm all laterals are in the downposition before loading with sand. (See Figure A onPage 2.)Carefully pour in correct amount and grade of filtersand, as specified. (Be sure center pipe remainscentered in opening). Sand surface should be leveledand should come to about the middle of the filter tank.Remove sand shield from center pipe.NOTE: If your sand filter is equipped with the SwimPure system or you are installing the SwimPure Retrofit Kit, then please follow the steps in the Instruction Sheet included in the SwimPure carton.Assemble Filter Control Valve to filter tank.Wipe filter flange clean.To install clamp, loosely preassemble both halves of theclamp with one screw and one nut, turning the nut twoor three times. Place clamp assembly on the filter neck.Insert filter control valve (with valve/flange O-ring inplace) into the tank neck, taking care that the centerpipe slips into the hole in the bottom of the valve.Install clamp around tank and valve flange andassemble second screw and nut. Tighten both sides ofclamp alternately and evenly. Make sure you tightenjust enough so that the valve may be rotated on thetank for final positioning.Carefully screw the pressure gauge, with pipe tape,into 1/4” tapped hole in valve body. Do not overtighten.Connect pump to control valve opening marked“PUMP” according to the instructions.Tighten both sides of clamp alternately and evenly. Usea correctly sized large screw driver and tighten firmlyto obtain a good seal.Please be sure to place vinyl protector caps over ends ofscrews.Make return to pool pipe connection to control valve opening marked RETURN and complete other necessary plumbing connections, suction lines to pump, waste, etc.Make electrical connections to pump per pump instructions. Be sure all circuits are protected by aproperly-sized ground fault circuit interrupter (GFCI).To prevent water leakage, be sure winter drain cap is securely in place and all pipe connections are tight. NOTE: If you have installed a SwimPure system, then please refer to Step 2 in the SwimPure Instruction Sheet (“Balance the Pool Water”).INITIAL START-UP OF FILTERBe sure correct amount of filter sand media is in tank and that all connections have been made and are secure.Depress Vari-Flo control valve handle and rotate to BACKWASH position. (To prevent damage to control valve seal, always depress handle before turning.)Prime and start pump according to pump instructions allowing the filter tank to fill with water. CAUTION: All suction and discharge valves must be open when starting the pump. Failure to do so could cause severe personal injury and/or property damage.Once water flow is steady out the waste line, run the pump for at least 1 minute. The initial backwashing of the filter is recommended to remove any impurities or fine sand particles in the sand media.Turn pump off, set valve to RINSE position. Start pump and operate until water in sight glass is clear—about 1/2 to 1 minute. Turn pump off, set valve to FILTER position and restart pump. Your filter is now operating in the normal filter mode, filtering particles from the pool water.Adjust pool suction and return valves to achieve desired flow. Check system and filter for water leaks and tighten connections, bolts, nuts, as required.Note the initial pressure gauge reading when the filter is clean. (It will vary from pool to pool depending upon the pump and general piping system). As the filter removes dirt and impurities from the pool water, the accumulation in the filter will cause the pressure to rise and flow to diminish. When the pressure gauge reading is 6-8 lbs.(2.7-3.6 kgs.) higher than the initial “clean” pressure younoted, it is time to backwash (clean) the filter (see BACKWASH under Filter Control Valve Functions). NOTE: During initial clean-up of the pool water, it may be necessary to backwash frequently due to the unusually heavy initial dirt load in the water.CAUTION: To prevent unnecessary strain on piping system and valving, always shut off pump before switching Filter Control V alve positions.To prevent damage to the pump and filter and for proper operation of the system, clean pump strainer and skimmer baskets regularly.FILTER CONTROL VALVE FUNCTIONSFILTER–Set valve to FILTER for normal filtering. Also use for regular vacuuming.BACKWASH–For cleaning filter. When filter pressure gauge rises 6-8 lbs. (2.7-3.6 kgs.) above start-up (clean pressure):Stop the pump, set valve to BACKWASH. Start pump and backwash, approximately 2 minutes or less, depending on dirt accumulation, until water in sight glass is clear. Proceed to RINSE.3.a.b.c.d.4.a.b.c.d.e.f.g.h. 5. 6.1. 7. 2.3.c.4.5.6.RINSE—After backwashing, with pump off, set valve to RINSE. Start pump and operate for about 1/2 to 1 minute. This ensures that all dirty water from backwashing is rinsed out of the filter to waste, preventing possible return to the pool. Stop pump, set valve to FILTER and start pump for normal filtering.WATER—To bypass filter for draining or lowering water level and for vacuuming heavy debris directly to waste.RECIRCULATE—Water is recirculated through the pool system, bypassing the filter.CLOSED—Shuts off flow from pump to filter.VACUUMING—Vacuuming can be performed directly into the filter. When vacuuming heavy debris loads, set valve to WASTE position to bypass the filter and vacuum directly out to waste.WINTERIZINGCompletely drain tank by unscrewing drain cap at base of filter tank. Leave cap off during winter.Depress Vari-Flo control valve handle and rotate so as to set pointer on valve top between any two positions. This will allow water to drain from the valve. Leave valve in this “inactive” position.Drain and winterize pump according to pump instructions.SERVICE & REPAIRSConsult your local authorized Hayward dealer or service center.No returns may be made directly to the factory without theexpressed written authorization of Hayward Pool Products, Inc.PROBLEM SOLVING LISTLOW WATER FLOWSHORT FILTER CYCLES POOL WATER WON’T CLEAR UP Check skimmer and pump strainer baskets for debris.Check for restrictions in intake and discharge lines.Check for air leak in intake line (indicated by bubbles returning to pool).Backwash filter.Check for algae in pool and superchlorinate as required.Be sure chlorine and pH levels are in proper range (adjust as required).Check surface of filter sand for crusting or caking (remove 1”of sand if necessary).Check chlorine, pH and total alkalinity levels and adjust as required.Be sure flow rate through filter is sufficient.Operate filter for longer periods.Be sure Vari-Flo valve is set on “Filter” position.1.2.3.4. 1.2.3. 1.2.3.4.REMEDYPOOL CHEMISTRY GUIDELINESACTION REQUIRED TO CORRECT POOL CHEMISTRY TO RAISETO LOWERSUGGESTED POOL CHEMISTRY LEVELS pHTOTAL ALKALINITYCHLORINE (UNSTABILIZED)CHLORINE (STABILIZED)CHLORINE STABILIZER (Cyanuric Acid)7.2 to 7.6100 to 130 ppm 0.3 to 1.0 ppm 1.0 to 3.0 ppm 40 to 70 ppmAdd Soda AshAdd Sodium Bicarbonate Add Chlorine Chemical Add Chlorine Chemical Add StabilizerAdd Muriatic Acid or Sodium BisulphateAdd Muriatic Acid No action - chlorine will naturally dissipate No action - chlorine will naturally dissipate Dilution - partially drain & refill pool with water that has not been treated with Cyanuric Acid.©2000 Hayward Printed in U.S.A.Rev. 11/00PLEASE REALIZE . . .Pure, clear swimming pool water is a combination of two factors–adequate filtration and proper water chemistry balance.One without the other will not give the clean water you desire.Your filter system is designed for continuous operation.However, this is not necessary for most swimming pools. You can determine your filter operation schedule based on your pool size and usage. Be sure to operate your filtration system longenough each day to obtain at least one complete turnover of your pool water.To properly sanitize your pool, maintain a free chlorine level of 1 to 3 ppm and a pH range of 7.2 to 7.6. Insufficient chlorine or an out of balance pH level will permit algae and bacteria to grow in your pool and make it difficult for your filter to properly clean the pool water.1.2.3.。
Vivitek DU77x-UST 系列用户手册说明书

用户手册DU77x-UST系列1. 常规信息 5版权 (5)免责声明 (5)商标 (5)重要安全信息 (6)使用的符号 (6)一般安全信息 (6)使用的符号 (6)激光警告 (7)3R类激光产品 (7)激光参数 (7)警告标签 (8)一般通知 (9)电源 (9)清洁投影机 (9)管制警告 (9)符号说明 (9)小心激光! (9)阳光警告 (9)2. 开始使用 10包装内容 (10)投影机特点 (11)投影机功能 (11)连接信号源设备 (12)控制键盘 (12)遥控器(SRC) + 功能 (13)工作范围 (14)电池 (14)组合键设置 (14)安装指南 (15)验证安装位置 (15)散热说明 (15)安装注意事项 (16)设置和投影选项 (16)安装投影机 (17)投影距离与投影尺寸 (18)投影机入门指南 (19)1 连接电源和信号源设备 (19)2 开机/关机 (19)3 选择信号源设备 (19)4 调整投影机倾斜角 (20)5 调整投影机图像 (20)3. 屏幕显示(OSD)菜单设置 21OSD菜单控制 (21)OSD导航 (21)输入菜单 (22)自动输入源 (22)HDMI (22)模拟 (23)3D (23)信号开机 (23)图像菜单 (24)图像模式 (24)亮度 (25)ViviBlack (25)色彩管理 (25)高级 (25)图像模式重置 (25)几何调整菜单 (26)宽高比 (26)数码变焦 (26)垂直梯形校正 (26)水平图像平移 (26)垂直图像平移 (26)投影方式 (26)测试图案 (26)控制菜单 (27)直接开机 (27)光源 (27)高海拔 (27)遥控器识别码 (27)网络 (28)设置菜单 (35)节能 (35)音频 (35)屏幕颜色 (35)菜单 (36)按键锁定 (36)安全锁 (36)语言 (36)默认值 (37)信息屏幕 (37)4. 故障排除 38常见问题及解决办法 (38)故障排除提示 (38)LED错误消息 (39)图像问题解答 (39)光源问题 (40)遥控器问题 (40)音频问题 (40)投影机维修 (40)HDM问题解答 (41)5. 规格 42投影机尺寸 (42)投影机数据表 (43)投影机时间表 (44)6. 管制符合性 47FCC警告 (47)加拿大 (47)安全认证 (47)处置和回收 (47)7. RS-232通信 48通信参数设置 (48)操作命令 (48)8. 检修 549. 附錄 551. 常规信息版权本出版物(包括所有照片、插图和软件)受国际版权法律的保护,保留所有权利。
唯特利(Victaulic) W732系列AGS Vic-Strainer Y型过滤器说明书

如需产品安装、维护或支持信息,请参考本文档末的信息。
1.0 产品描述供货尺寸:• 14 – 18"/DN350 – DN450最大工作压力:• 300 psi/2068 kPa/21 bar 应用:• 提供直通流道,压降更低• 有关 732 系列 AGS Vic-Strainer Y 型过滤器的信息,请参见 09.03 号技术文件。
2.0 认证/列名产品的设计和制造依照 Victaulic (唯特利)质量管理体系进行(根据 ISO 9001:2015 获得 LPCB 认证)。
Y 型过滤器20.19-CHI3.0 规格 – 材料本体、卡箍、管端盲板:根据特别需求,可提供符合 ASTM A395 之 65-45-15 等级要求和 ASTM A536 之 65-45-12 等级要求的球墨铸铁。
涂层:橙色瓷漆滤篮:304 型不锈钢孔板14 – 18"/DN350 – DN450: 中心距为 0.234 英寸/6 毫米、过流面积占 40% 的 0.156 英寸/4 毫米直径孔洞。
密封垫圈等级:(请指定选择)1、2Victaulic(唯特利)“E”级 FlushSeal™三元乙丙橡胶(EPDM)三元乙丙橡胶(EPDM)(绿色条纹色码)。
温度范围 –30°F 到 +230°F/–34°C 到 +110°C。
不支持石油或蒸汽应用。
螺栓/螺母:标准:碳钢椭圆颈轨道螺栓,符合 ASTM A449(英制)和 ISO 898-1(公制)Class 9.8 (M10-M16) Class 8.8(M20 及以上)的机械性能要求。
碳钢六角螺母,符合 ASTM A563 Grade B(英制 – 重型六角螺母)和ASTM A563M Class 9(公制 – 六角螺母)的机械性能要求。
轨道螺栓和六角螺母,按照 ASTM B633 ZN/FE5, finish Type III(英制)或 Type II(公制)进行电镀锌处理。
Pierce Arrow PS 系列赶车舵说明书

Recovery Winch Owner’s Manual 1PIERCE ARROW INC.549 U.S. HWY 287 S.HENRIETTA, TEXAS 76365--------------------------------------------------------TOLL FREE 800-658-6301FAX /PierceArrowIncOwner’s Manual:PS SERIES WINCHESCheck out the winchvideos on YouTube.2 Pierce Arrow 800-658-6301Recovery Winch Owner’s Manual 3The PS series winch is a powerful tool and must be used with extreme care. Deviating from the manual’s instructions may cause personal injury. You may lose your warranty if you do not follow the precautions and guidelines outlined in this manual. Keep this manual in a safe place to reference safety and installation instructions, maintenance guidelines and operating recommendations. The owner, operator and installer must read the entire owner manual before operating the winch.Recovery Winch Owner’s ManualShipment Contents1 – Winch1 – P040N Three Prong Remote Control 4 – Winch Mounting Bolts 4 – Lock Washers 1 – Snatch Block1 – Solenoid Assembly 1 – Roller Guide2 – Bolts 2 – Nuts 2 – Washers1 – 7 x 19 Wire Rope 1 – Slip Eye Safety Hook 1 – Owner’s ManualRecommended Tools9/16” Wrench or Socket 17” Wrench Crowbar GlovesSafety Glasses Tree Saver Strap Safety Cut Off Switch First Aid Kit Bow Shackles Chains or StrapsWheel Blocks or Choks Heavy BlanketManual ContentsShipment Contents...................................................... 3Safety Precautions....................................................... 3General Safety Information......................................... 3-4Installation Instructions.............................................. 4Mounting..................................................................... 4Operation................................................................... 4Maintenance.............................................................. 4Specifications............................................................... 5Operation Recommendations..................................... 5Electrical Diagrams ..................................................... 6Parts Diagram ............................................................ 7Warranty .. (8)Safety PrecautionsDRESS PROPERLY• DO NOT wear loose fitting clothing or jewelry.• Tie back long hair.• Wear leather gloves when handling the wire rope.• Wear non-skid footwear during winch operation.• Wear eye and ear protection during operation.KEEP A SAFE DISTANCE• DO NOT step over or under the wire rope.• All onlookers must keep away from the work area.• Never work on or around the winch drum when the winch isoperating.• DO NOT alter your winch in any way. Alterations may weaken thestructural integrity of the winch and void your warranty.• Operate your winch with an unobstructed view.• Read the following safety information carefully beforeattempting to operate your winch. Keep this manual for future reference.General Safety InformationDO NOT MISUSE YOUR WINCH• DO NOT lift items vertically. The winch was designed forhorizontal use only.• DO NOT operate the winch with less than eight wraps on thedrum. The set screw on the drum is not designed to hold pull force of cable.• Avoid continuous pulls from extreme angles. This will cause thewire rope to jam as it piles up on one side.• Use a nylon sling when winching. Hooking the wire rope to itselfwill cause considerable damage to the wire rope.• DO NOT move your vehicle to assist the winch in pulling theload. The combination of the winch and vehicle pulling could overload the wire rope and winch.• Never release the free spool clutch when a load is connected tothe winch.• DO NOT exceed the pulling limitations of this winch.• DO NOT shock loads when winching. A shock load occurs whenincreased force is suddenly applied to the wire rope.• DO NOT use your winch as a hoist.• DO NOT use your winch to lift, support or transport people.• DO NOT alter the warning instruction labels.• DO NOT overheat your winch. Use your winch intermittently.• Only use your winch for direct winching. Do not use your winchfor jerking loads, towing or securing a load.Any damage incurred as a result of such action will void the warranty.• DO NOT winch near electrical power lines.DO NOT ABUSE THE WIRE ROPE• Never carry your winch by the wire rope.• Never yank the wire rope from the winch.• Keep the wire rope from heat or sharp edges.• The cable must be spooled from the bottom of the drum .DO NOT OVERWORK YOUR WINCH• DO NOT maintain power if the motor stalls.• DO NOT exceed maximum line pull ratings.4 Pierce Arrow 800-658-6301• Under a load of 500 lbs (230 kg) re-spool the wire rope. •This will stretch the new wore rope and create a tight wrap around the drum.OPERATION• Apply the parking brake or lock the wheels.• While the clutch is in the OUT position spool the winch cable andconnect to an anchor point.• Check cable rigging before proceeding.• Plug in the winch remote control.• Engage the clutch by shifting it into the IN position. NOTE: Whenthe clutch is engaged your load may begin to drift until the remote is used to recover your load. To ensure safe operation, it is recommended that winch operation take place from the driver’s position.• Start vehicle engine, select neutral or park and maintain idleengine speed.• Using the remote control, press IN or OUT until the vehicle hasbeen retrieved. Regularly check the winch to ensure the cable is winding onto the drum evenly. It is recommended you secure the load using chains or straps at this point.• Detach the load.• Re-spool the wire rope after the winch operation is completed.MaintenanceIt is highly recommended that you regularly use your winch. Simply power the cable out 15 feet, free spool five feet and power in. This will keep all components in good condition so that the winch can be ready when needed. Contact the manufacturer or authorized outlet for technical assistance and repairs.LUBRICATION1. The gearbox has been lubricated using high temperature lithiumgrease at the factory. No internal lubrication is required.2. Lubricate cable periodically using light penetrating oil. Inspect forbroken or worn strands and replace if necessary.BATTERY1. Be sure the battery is in working condition.2. Avoid contact with battery acid.3. Wear eye protection when working around the battery.4. Avoid depleting the battery by running the engine when usingthe winch.5. Check terminals for corrosion and clean or replace as needed.ROPE1. Use aircraft grade cable or approved and rated synthetic rope.1. The life of the rope is directly related to the use and care itreceives.2. Replace damaged or frayed rope with manufacturer’s identicalreplacement part.3. Be sure the rope is in good condition and is properly attached.4. DO NOT use the winch if the rope is frayed.5. DO NOT replace the cable with a cable of lesser strength.6. When the rope is replaced, apply Loctite 7471 primer or 222Threadlocker to the wire rope clamp to prevent the loosening of the screw.WINCH ELECTRICAL CONNECTIONS1. Remove dirt or grease that may have accumulated on theelectrical connections.2. Dielectric grease is recommended on terminals and plugs.SPARE PARTS1. A comprehensive range of spare parts is available. Please contactthe manufacturer, Pierce Arrow at 940-538-5643 for more information.2. DO NOT attempt to disassemble the gearbox. Disassembly mayvoid the warranty. Call Pierce Arrow at 940-538-5643 before repairs are made.• DO NOT overload your winch’s pulling capacity. We recommend the use of a pulley block to double line the wire rope on heavy loads.•DO NOT prolong pulls. The electric winch is designed forintermittent use only. If the motor becomes very hot stop the winch and let it cool down for several minutes.AVOID UNINTENTIONAL STARTING• The winch clutch must be disengaged when not in use and fullyengaged when in use.• Power must be disconnected when not in use.MAINTAIN YOUR WINCH• Before use, you must check your winch carefully.• Damaged equipment must be properly repaired or replaced bythe manufacturer or an authorized service center.• Inspect and maintain the wire rope and winch frequently.• Replace frayed rope strands immediately.• Use only factory approved switches, remote controls andaccessories.• Check the tightness of the mounting bolts and electricalconnections periodically.RE-SPOOL THE WIRE ROPE• Wear leather gloves while re-spooling.• ATTENTION: DO NOT allow the wire rope thread through yourhand.• Keep a slight load on the wire rope while re-spooling. Hold thewire rope with one gloved hand and the remote control in the other.InstallationMOUNTING• Before installation ensure the mounting frame in use is capableof withstanding the winch’s rated capacity.• Ensure the motor, wire rope, drum and gear housing is properlyaligned.• Mount to a flat surface using 3/8” UNC x 1¼” stainless steel boltsand spring washers (PS15000 and PS20000 required grade 10.9 bolts). Your mounting plate must be six millimeters or ¼ inches thick. If your mounting plate is thicker than 1/4 inches, lengthen bolts accordingly.• Mount the roller guide in front of the winch. Do not attach theroller guide to the winch• The cable must be spooled from the bottom of the drumELECTRICAL CONNECTIONS• Connect the black wire to the ground post (1) on the motor. Seediagram on page 5.• Connect the red wire to any terminal on the safety cutoff switch(PS025). Use the other terminal to connect to the vehicle’s battery.• Your solenoid comes pre-wired. See page 5 for diagraminformation. WIRE ROPE PREPARATIONNOTE: The first use of your winch must be a test run during a non-recovery situation. During this trial run begin to recognize the sound of a steady pull, a heavy pull, load jerking or shifting. • Spool the wire rope• Wear leather gloves while spooling. ATTENTION: DO NOT allowthe wire rope thread through your hand.• Unwind the wire rope carefully along the floor to avoid kinking.• Place the end of the wire rope in to the hole on the side of thedrum. The wire rope will protrude ½”- 1”. Tighten the set screw.• Keep a slight load on the wire rope while spooling.• Using the remote control, wrap the wire rope on to the drumuntil the load is recovered. During operation, make sure the wire rope lays smoothly on to the drum without spacing or overlapping.•Spool the wire rope until the red mark appears at five wraps.Recovery Winch Owner’s Manual 5SpecificationsModel Capacity Volts Control DimensionsSpeed Weight Motor Ratio Min. Wire Gauge Gear Train Clutch Brake PS60006,000 lbs 12 VRemote with 12’ lead Cable capacity: 9/32” x 65’Unit: 16.9” x 6.3” x 8.6”Drum: 2.52” x 5.26”Mounting Pattern: 4.5” x 6 5/8”13 fpm55 lbs5.5 hp218:14 gauge Three Stage Planetary Sliding Ring Gear Automatic in the drum PS90009,000 lbs12 VRemote with 12’ lead Cable capacity: 5/16” x 92’Unit: 22” x 6.3” x 8.6”Drum: 2.5” x 8.8”Mounting Pattern: 4.5” x 10”28.2 fpm 84 lbs 5.5 hp 265:14 gauge Three Stage Planetary Sliding Ring Gear Automatic in the drum PS1200012,000lbs 12 V Remote with 12’ lead Cable capacity: 3/8” x 85’Unit: 21.3” x 6.3” x 8.6”Drum:2.52” x 8.82”Mounting Pattern: 4.5” x 10”21.3 fpm 88 lbs 5.5 hp 265:12 gaugeThree Stage Planetary Sliding Ring Gear Automatic in the drum PS2000020,000lbs12 V Remote with 12’ lead Cable capacity: 1/2” x 72’ Unit: 23” x 7.7” x 10.6”Drum: 3.5” x 8.7”Mounting Pattern: 4.5” x 10”20.4 fpm119 lbs 6.8 hp420 : 1 2gaugeThree Stage PlanetarySliding Ring GearAutomatic in the drumLINE PULL (lb.)LINE SPEED (FPM)AMPS 028.2702,00015.41604,00011.52406,0009.2310PS6000LAYERRATED LINE PULL (LBS.)ROPE LENTH ON DRUM (FT.)19,00016.227,32039.335,50068.944,75091.8LINE PULL (lb.)LINE SPEED (FPM)AMPS 028.2802,00014.41804,00010.62406,0008.52808,0007.03309,000 6.5360PS9000LAYERRATED LINE PULL (LBS.)ROPE LENTH ON DRUM (FT.)19,00016.227,32039.335,50068.944,75091.8LINE PULL (lb.)LINE SPEED (FPM)AMPS 021.3652,00011.51756,0007.92308,000 6.528010,000 5.835512,000 4.4390PS12000LAYERRATED LINE PULL (LBS.)ROPE LENTH ON DRUM (FT.)112,0001729,2104138,0307146,89485LINE PULL (lb.)LINE SPEED (FPM)AMPS 023.9682,00012.21006,0007.418510,000 5.127515,000 3.342520,000 2.62530PS20000LAYERRATED LINE PULL (LBS.)ROPE LENTH ON DRUM (FT.)120,00020.4215,48242.44312,58460.18410,55072.166 Pierce Arrow 800-658-6301Electrical DiagramWIRING CHARTConnect the wires to thecorresponding signs.1Field 1Armature Post 2Field 2+12V A -GroundUP DOWN To remote downTo remote upUPDOWN12+-Use the diagram below to customize your wired or wireless remote control connections.Use the diagram below to set up your winch wiring.-WIRING C HART -+11TO BATTERYTO WINCHPOSTIVE TO SAFETY CUT OFF SWITCH GROUNDWINCH POST GROUNDPS025 SAFETY CUT OFF SWITCHPS528NCOMPACT SOLENOID ASSEMBLYParts DiagramPS6000PS9000PS12000PS20000Recovery Winch Owner’s Manual 7Pierce Arrow Product Limited WarrantyPierce Arrow, Inc. warrants to the original purchaser only (whether a wholesale, OEM or retail customer) thatthe goods, equipment, and merchandise manufactured by Pierce Arrow are free from defects in material and workmanship. The Pierce Arrow limited warranty on parts covers such items for a period of one year on mechanical and electrical from the date of shipment by Pierce Arrow. All warranties cover only the product or product parts, and are nontransferable.OBTAINING WARRANTY SERVICEPierce Arrow must be notified promptly in writing, about the defect before any means of repair have been made. The merchandise must be delivered by the purchaser to Pierce Arrow in Henrietta, Texas at the purchaser’s expense. Pierce Arrow reserves the right to repair or replace the merchandise proved to be defective. The purchaser is responsible for the cost of repairs made by Pierce Arrow if the repairs are not covered by the Pierce Arrow warranty.EXCLUSIONSThe Pierce Arrow warranty is not intended to cover normal maintenance parts, including but not limited to: wire rope, oil leakage and remote holdings. Nor is the warranty intended to cover any change or defect due to accident; misuse; improper, inadequate or unauthorized repair; failure to provide maintenance or uses for which the equipment was not intended; and normal deterioration due to weather or road conditions. Reference the owner’s manual for safety, installation, operation and maintenance guidelines.The warranty does not bear the cost of labor, transportation, shipping damages, claimed down time, loss of profit or goodwill, or any other special, incidental, indirect, or consequential damages, concerning or related to any product or part, whether based upon negligence, strict liability, breach of contract, breach of warranty, misrepresentation, or any other legal theory.Merchandise sold by Pierce Arrow, but not manufactured by it, is not warranted by Pierce Arrow and is subject to the manufacturer’s warranty only. The manufacturer’s warranty is available upon request.Pierce Arrow makes no warranty, expressed or implied, to finished products manufactured or supplied by other manufacturers, and supplied from Pierce Arrow to the purchaser, including but not limited to, any vehicle to which our products is affixed to, and any accessories.Merchandise manufactured by Pierce Arrow is not designed or intended for the movement of people and are not to be used in the operation of elevators or other improper uses. Any improper use of the product may void the warranty.Please contact Pierce Arrow with any questions:Pierce Arrow Inc.549 U.S. Highway 287 S.Henrietta, Texas 76365(toll free) 800-658-6301P: 940-538-5643F: 940-538-43828 Pierce Arrow 800-658-6301Revised 05-22-2014。
Valspar水溶胶低VOC擦拭涂料基基础数据表说明书

The data on this sheet represent typical values. Since application variables are a major factor in product performance, this information should serve only as a general guide. Valspar assumes no obligation or liability for use of this information. UNLESS VALSPAR AGREES OTHERWISE IN WRITING, VALSPAR MAKES NO WARRANTIES, EXPRESS OR IMPLIED, AND DISCLAIMS ALL IMPLIED WARRANTIES INCLUDINGWARRANTIES OF MERCHANTABILITY OR FITNESS FOR A PARTICULAR USE OR FREEDOM FROM PATENT INFRINGEMENT. VALSPAR WILL NOT BE LIABLE FOR ANY SPECIAL, INCIDENTAL OR CONSEQUENTIAL DAMAGES. Your only remedy for any defect in this product is the replacement of the defective product, or a refund of its purchase price, at our option.Version 2: Feb 2011 (supersedes all previous revisions) (Continued on reverse)Waterborne Low VOC Wiping Stain BaseTECHNICAL DATA SHEETPRODUCT NUMBERSLWS0750COMPANION PRODUCTSZenith™ Waterborne Wiping Stains LWS075X Series Zenith™ Waterborne Colorants Zenith™ Waterborne LacquerZenith™ Waterborne Pre-catalyzed Lacquer Zenith™ Waterborne Conversion VarnishZenith™ Waterborne Universal Amber SealerDESCRIPTION/USESZenith™ Waterborne Low VOC Wiping Stain Base is a fast drying, direct-to-wood interior stain base that is specially formulated to highlight and enhance thenatural beauty of all types of wood. It is a neutral base used to formulate custom wiping stains. It may also be used to reduce the color strength of Zenith™Waterborne Wiping Stains (LWS0751-LWS0760). It has very little odor, and grain raise is minimal. This product is designed for professional application only. For WoodSubstrates Only.PRODUCT ADVANTAGES• Achieve rich, vibrant colors• Short filled containers for easy tinting • Tintable to any color • HAP’s Free• Ultra-Low VOC • Very low odor •Water cleanupAPPLICATION FEATURES• Very little grain raise • Excellent open time •Fast dry to recoat timesPRECAUTIONSThese products are recommended for professional application and are designed for interior use only. Always pre-test the system on your substrate and under your line conditions to verify suitability to the application and to avoid potential need for costly refinishing. Valspar Wood Finishes products aredesigned to protect and enhance the natural beauty of wood, but cannot eliminate natural discoloration or deterioration of wood as it ages. Additional notes:Do not mix with other finishing systems or deviate from these finishing recommendations. Valspar will not be held liable for finish failures resulting from the mixing of products or deviations from finishing recommendations.PHYSICAL PROPERTIES (objective specifications)Viscosity: N/AWeight Solids: 33.64% Volume Solids: 29.1%Weight/Gallon: 8.9 lbs/gal¹Theoretical Coverage: 466.76 ft/gal @ 1 mil dry Flash Point: 202ºF Closed CupAir Quality Information: VOC: 0.24 lbs/gal of Product AIM VOC : 90.47 g/l VOC Ratio: 0.08 (lbVOC/lb solid)¹ VHAP: 0.0 lb VHAP/lb solid-HAPs Free Photochemically Reactive: NoDry Times (78°F, 50%RH): Air DryTo Touch/Handle: 20-30 minutes To Recoat: 45-60 minutesForce Dry To Flash: 5-8 minutes To Bake: 15 minutes @ 130ºF Cool Down: 10 minutes ambient airShelf life: 2 years from the manufacturing dateReduction: No thinning is recommended.Retarder: If needed to slow dry time, use Zenith™ Waterborne Retarder YXT0700 at a rate of 1-2% (1.2-2.5 oz per gl.) max. *Max VOC after recommended addition of retarder is 250 g/l or 2.1 lbs per gl.Application Equipment:Apply by rag, brush or spray. If spraying use Conventional Air, or HVLP equipment. Use onlyequipment with plastic, stainless steel, or Teflon coated valves and parts.Recommended tip sizes :Conventional Air 0.070-0.086 HVLP 0.070-0.086Note: All information provided is typical (as formulated) and will not represent exact values for every product. For specific Air Quality Data for each product, VOC reports are available upon request.*As allowable within regulatory compliance requirementsFINISHING RECOMMENDATIONSGeneral: Surface must be clean and dust free with moisture content of 6-8% prior to finishing. Remove all dirt, dust, wax and wood marks. Proper sanding and preparation of the wood is critical to achieving consistent results.New Wood: Finish sand surface (150-180 grit) and remove all sanding dust.Painted or Varnished Wood: Remove all paint or varnish then follow new wood instructions.Before using, mix product by hand, or if using mechanical agitation such as an air mixer or drill, mix at slow to moderate speed until there is no material on the bottom of the container. If tinting, colorants must be mixed in with a shaker or mechanical agitation such as an air mixer or drill.Tinting:This product is designed to be tinted with approved, high quality industrial waterborne colorants such asZenith™ High Performance Waterborne colorants or Valspar’s Universal Dye Concentrates (check with your Valspar Distributor for other approved tints).Maximum tint capacity is 12 oz per gallon (9.4% by volume) in a short filled container. Maximum tint load if mixing a custom stain from scratch is 19 oz per gallon (15% by volume). Colorants must be mixed in completely with mechanical agitation before use.Always test the stain for appearance in an inconspicuous area (or scrap sample of the same type of wood) before using. Intermix containers of the same color. Stir well before use and frequently during use. Apply stain by spray, brush or lint-free cloth. Apply an even, wet coat. While product is still wet (approximately 1-3 minutes) wipe off in a circular motion, working the stain into the wood pore. Finally, wipe clean with the grain of the substrate. DO NOT LEAVE THIS PRODUCT ON THE SUBSTRATE WITHOUT WIPING! These stainspenetrate quickly. There is no need to leave them on the substrate longer than a few minutes. Only one coat is recommended.DRYING TIME:Dry touch: 20-30 minutes.Dry to recoat: 45-60 minutes (depending on ambient conditions).Do not apply if the material or substrate temperature is below 60ºF.This product is best applied when surface, material, and air temperatures are between 60-100ºF and when relative humidity is below 50% during application and drying time. Low temperatures, poor air circulation, or high humidity will extend dry times. Abnormal conditions of temperature or humidity may adversely affect product performance.Clean equipment with warm water. If coating has dried, acetone may be required to remove dried film. Keep container closed when not in use to avoid skinning. Do not transfer contents to other containers for storage or disposal. In case of spillage, absorb with inert material such as sand or kitty litter. Dispose of empty cans or unused portion in accordance with local state and federal regulations.Store in a cool, dry place. DO NOT FREEZE! Product should be stored in temperatures between 50°-110°F. Close all containers after use. Do not store near heat or sparks. Spills should be cleaned up with non-sparking tools. See the product MSDS for complete safety information.Always pre-test the system on your substrate and under your line conditions to verify suitability to the application and avoid potential need for costly refinishing. All dry times listed are as tested under ideal indoor environmental conditions of 78°F (26°C) with relative humidity not exceeding 50%. These products are recommended for use under temperature conditions of 60-100°F (16-38°C) and when relative humidity is below 50% during application and drying time. Low temperatures, poor air circulation or high humidity will extend dry times. Valspar strongly recommends against use of these products if temperatures of air, material, or surface to be coated are below 60°F (16°C) or below the dew point. Abnormal conditions of temperature or humidity may adversely affect product performance. Please contact your authorized Valspar Wood Finishes distributor for additional product use recommendations and finishing guidance.MSDS AND CPDS SHEETS AVAILABLE UPON REQUEST。
汽车零部件供应商在华企业清单

德尔福(Delphi)德尔福派克电气系统有限公司上海分公司、广州分公司、白城分公司、长春分公司、上海德科电子仪表有限公司、上海德尔福汽车空调系统有限公司、上海德尔福汽车门锁防盗系统有限公司、上海德尔福汽车排放控制系统有限公司、北京德尔福万源发动机管理系统有限公司、上海德尔福国际蓄电池有限公司、德尔福沙基诺凌云驱动轴有限公司、德尔福(中国)科技研发有限公司、德尔福德科电子(苏州)有限公司、德尔福(上海)汽车转向底盘系统有限公司、德尔福(上海)动力推进系统有限公司伟世通(Visteon)延锋伟世通汽车饰件系统有限公司、上海延锋江森座椅有限公司、伟世通电子(上海)有限公司、延锋伟世通(重庆)汽车饰件系统有限公司、延锋伟世通(北京)汽车饰件系统有限公司、东风伟世通汽车饰件系统控股有限公司李尔(Lear)上海李尔实业交通汽车部件有限公司、武汉友德汽车电器有限公司、江西江铃李尔汽车内饰件有限公司、上海李尔汽车内饰件有限公司、上海松江李尔汽车地毯声学元件有限公司、重庆李尔长安汽车内饰件有限公司、南京李尔新迪汽车内饰系统有限公司、沈阳李尔汽车座椅内饰系统有限公司江森(Johnson Controls)上海延锋江森座椅有限公司、长春富奥-江森自控汽车饰件系统有限公司、沈阳金杯江森自控汽车内饰件有限公司、北京江森自控汽车饰件有限公司天合(TRW)上海天合汽车安全系统有限公司、天合(苏州)汽车电子有限公司、天合(宁波)电子元件紧固装置有限公司、天合汽车底盘系统有限公司、卢卡斯廊重制动系统有限公司、天合汽车部件技术服务(上海)有限公司、天合汽车零部件(上海)有限公司、天合系统咨询服务(上海)有限公司德纳(DANA)天津维克斯滤清器有限公司(TIANJIN WIX)、德纳(无锡)技术有限公司玛格纳(MAGNA)上海龙马神汽车座椅有限公司、顺德多纳勒振华汽车部件有限公司菲特尔莫古(Federal-Mogul)广州辉门冠军火花塞有限公司、安庆帝伯格茨活塞环有限公司、南昌辉门密封件系统有限公司、辉门(青岛)活塞有限公司、上海菲特尔莫古轴瓦有限公司、辉门摩擦产品有限公司博世(Bosch)联合汽车电子有限公司、南京华德火花塞有限公司、无锡欧亚柴油喷射有限公司、杭州博世电动工具有限公司、博世贸易(上海)有限公司、罗伯特?博世(香港)有限公司、博世汽车部件(苏州)有限公司、博世(顺德)燃气用具有限公司、博世华家用电器有限公司、博世包装技术(杭州)有限公司法雷奥(Valeo)上海法雷奥汽车电机雨刮系统有限公司、上海法雷奥汽车电器系统有限公司、法雷奥汽车空调湖北有限公司、法雷奥温岭汽车零部件有限公司、湖北法雷奥车灯有限公司、南京法雷奥离合器有限公司大陆(Continental)上海汽车制动系统有限公司(SABS)、上海康迪汽车制动器有限公司(SABA)弗雷西亚(Faurecia)佛吉亚全兴(武汉)汽车座椅有限公司FGW(Faurecia GSK Wuhan Automotive Seating Co.)、湖北通达爱西亚消声器有限公司采埃孚(ZF)上海采埃孚转向机有限公司、采埃孚汽车变速箱(上海)有限公司、采埃孚转向泵金城(南京)有限公司、柳州ZF机械有限公司、上海伦德福汽车配件有限公司、上海汇众萨克斯减振器有限公司、采埃孚销售服务(上海)有限公司、ZF传动技术(苏州)有限公司、采埃孚贸易有限公司纳铁福(GKN)上海纳铁福传动轴有限公司、吉林北方捷凯传动轴有限公司(JDS)奥托立夫(Autoliv)长春宏光-奥立托夫汽车安全装置有限公司、南京宏光-奥托立夫汽车安全装备有限公司、长春奥托立夫贸鸿汽车安全系统有限公司、上海奥托立夫汽车安全系统有限公司海拉(Hella)长春海拉车灯有限公司、上海广电海拉有限公司(原名为上海海拉车灯有限公司)、北京海拉车灯有限公司、海拉贸易(上海)有限公司(原海拉中国有限公司上海代表处)、海拉灯具研发中心(上海)、海拉电子研发中心(计划)、海拉(广东顺德)贝尔(Behr)上海贝尔汽车空调系统有限公司电装(Denso)烟台首钢电装有限公司、电装电子(天津)有限公司、天津电装汽车电机有限公司、天津阿斯莫上海电装燃油喷射有限公司、天津富奥电装空调有限公司爱信精机(Aisin Seiki)天津爱信汽车零部件有限公司、爱信天津车身零部件有限公司、唐山爱信齿轮有限责任公司、浙江爱信宏达汽车零部件有限公司、高丘六合(天津)工业有限公司、北京艾迪菲导航科技有限公司、杭州爱信伊奈机电有限公司矢崎(Yazaki)重庆矢崎仪表有限公司、天津矢崎汽车配件有限公司、烟台矢崎汽车配件有限公司(福山区)、华南矢崎(汕头)汽车配件有限公司万都(Mando)安徽江淮万都空调公司、万都(哈尔滨)底盘系统有限公司、锦州汉拿电机有限公司莫比斯(Mobis)深圳航盛MOBIS、北京现代MOBIS公司、悦达起亚MOBIS公司。
PetSafe Drinkwell Sedona 宠物饮水字体ountain 用户手册说明书

Product Manual PWW00-15417PetSafe® Drinkwell® Sedona Pet FountainPlease read this entire Product Manual before beginning.WelcomeYou and your pet were made for each other. Our aim is to help you have the bestcompanionship and the most memorable moments together. Your new pet fountain is designed to entice your pet to stay hydrated and healthy.We know that safe pets make happy owners. Before getting started, please take a moment to read through the important safety information. If you have any questions, please don’t hesitate to contact us.Hereinafter Radio Systems Corporation and any other affiliate or Brand of Radio Systems Corporation may be referred to collectively as “We” or “Us”.This is the safety alert symbol. It is used to alert you to potential personal injury hazards.Obey all safety messages that follow this symbol to avoid possible injury or death.WARNING indicates a hazardous situation which, if not avoided,could result in death or serious injury.CAUTION, used without the safety alert symbol, indicates a hazardoussituation which, if not avoided, could result in harm to your pet.NOTICE is used to address safe use practices not related to personal injury. When using electrical appliances, basic safety precautions should always be followed to reduce the risk of fire, electric shock and/or injury to persons, includingthe following:• Read all instructions before using this product.• To reduce the risk of injury, close supervision is necessary when an appliance is used by or near children.• To protect against electric shock, do not place electrical power cord or plug in water or other liquids.• Do not operate any appliance if it has a damaged electrical power cord or plug, or if it is malfunctioning or has been damaged. Call the Customer Care Center immediately for further instructions.• To reduce the risk of electric shock, do not place or store an appliance where it can fall or be pulled into a bathtub or sink.• Always unplug any appliance when not in use, before putting on or taking off parts and before cleaning.• Do not use an appliance for anything other than its intended use.2Customer Care Center +1 (800) 732-2677• If the plug of this device gets wet, turn off the electricity to that electrical outlet.Do not attempt to unplug.• Examine this appliance after installation. Do not plug into electrical outlet if there is water on the electrical power cord or plug.• Do not allow pets to chew on or swallow any parts. If you are concerned your pet may chew the power cord, purchase a cord conduit (a hard plastic protector) at any hardware store.• The plastic fountain parts are BPA-FREE. However, some animals have been known to be sensitive to plastic food and water containers. If your animal shows signs of an allergic reaction to the plastic, please discontinue use until you have consulted with your veterinarian.• The fountain is intended to run continuously (always plugged into an electrical outlet), as long as the water level is maintained and the fountain is cleanedregularly. Be sure to check the water level regularly to help prevent damage to the pump, as your pet will drink the water, and some may evaporate.• Do not attempt repairs on the pump.• Do not pull on the electrical power cord to remove the plug from the electrical outlet.• To unplug, grasp the plug, not the electrical power cord.• To avoid the possibility of the plug or electrical outlet getting wet, the electrical outlet should always be above the level of the fountain.• If an extension cord is necessary, an extension cord with a proper rating should be used.• The electrical use of this appliance is 2.5 watts.• The use of attachments not recommended or sold by the manufacturer may cause an unsafe condition. Do not modify the appliance.• Do not install or store appliance where it will be exposed to weather or temperatures below 40°F.• Read and observe all important notices listed on the appliance and in the packaging.• Never wash the filter with soapy water as the soap residue will seep into the filter and cannot be removed. Only rinse the filter with water.• Use only PetSafe® Brand authorized replacement filters. If unauthorized filters are used, the warranty may be voided.• Do not use outdoors. Do not run dry. For indoor household use only.SAVE THESE INSTRUCTIONS3TABLE OF CONTENTSIn the Box. . . . . . . . . . . . . . . . . . . . . . . . . . . . . . . . . . . . . . . . . . . . . . . . . . . . . . . . . . . . .4 Features. . . . . . . . . . . . . . . . . . . . . . . . . . . . . . . . . . . . . . . . . . . . . . . . . . . . . . . . . . . . . .5 Key Definitions. . . . . . . . . . . . . . . . . . . . . . . . . . . . . . . . . . . . . . . . . . . . . . . . . . . . . . . . .5 Assemble Fountain . . . . . . . . . . . . . . . . . . . . . . . . . . . . . . . . . . . . . . . . . . . . . . . . . . . . .6 Set Up and Add Water. . . . . . . . . . . . . . . . . . . . . . . . . . . . . . . . . . . . . . . . . . . . . . . . . .8 Fountain Disassembly and Cleaning. . . . . . . . . . . . . . . . . . . . . . . . . . . . . . . . . . . . . . .8 Pump Maintenance. . . . . . . . . . . . . . . . . . . . . . . . . . . . . . . . . . . . . . . . . . . . . . . . . . . .10 Fountain Reassembly . . . . . . . . . . . . . . . . . . . . . . . . . . . . . . . . . . . . . . . . . . . . . . . . . .11 The Fountain and Your Environment . . . . . . . . . . . . . . . . . . . . . . . . . . . . . . . . . . . . . .12 General Tips . . . . . . . . . . . . . . . . . . . . . . . . . . . . . . . . . . . . . . . . . . . . . . . . . . . . . . . . .12 Troubleshooting. . . . . . . . . . . . . . . . . . . . . . . . . . . . . . . . . . . . . . . . . . . . . . . . . . . . . . .13 Replacement Parts and Accessories . . . . . . . . . . . . . . . . . . . . . . . . . . . . . . . . . . . . . .14 Customer Care . . . . . . . . . . . . . . . . . . . . . . . . . . . . . . . . . . . . . . . . . . . . . . . . . . . . . . .14 Terms of Use and Limitation of Liability . . . . . . . . . . . . . . . . . . . . . . . . . . . . . . . . . . .15 Warranty . . . . . . . . . . . . . . . . . . . . . . . . . . . . . . . . . . . . . . . . . . . . . . . . . . . . . . . . . . .15Customer Care Center +1 (800) 732-26774FeaturesKey DefinitionsBowl: The plastic bowl is the foundation of the fountain. The bottom of the bowl features four indentations to run the electrical power cord through.Tower: Water is pumped up through the ceramic tower to cycle through the carbon filter and out the top to create a waterfall into the bowl.Filter Housing: The plastic filter housing consists of a lid and base that holds the carbon filter.Rubber Grommet: The rubber grommet comes already installed in the top of the ceramic tower and forms a seal between the filter housing and the tower. Rubber Cap: This rubber seal secures the electrical power cord to the inside of the bowl and prevents leaking.Carbon Filter: The 3-layer filter is made with activated carbon derived from coconut shells. The carbon filter absorbs bad tastes and odors as the water passes through and helps keep the water tasting fresh and more appealing to pets.Foam Filter: The foam filter collects any hair, debris, and pet food before they reach the pump. It is important to use the foam filter as it helps maintain proper pump function.Pump: The small aquarium pump can be partially dismantled for cleaning. The pump is not dishwasher safe! Remove pump from the fountain before cleaning (see“Pump Maintenance” section for detailed instructions). The pump also features aremovable in-line plug for easy attachment and removal.5Note: Rinse all fountain parts with warm water before operating the pet fountain. This will remove any dust or residue that remain in the system from the manufacturing process.1.assembly.2.before use.3.foam filter (1A).4. Take the bowland place thepump inside the(1B) With thebowl positionedis to the right ofsure the pump is5.6Customer Care Center +1 (800) 732-26776.and push all the way down ( 7.post to seal off the bowl (1F).8.9.1Set Up and Add Water1. Place the fountain in desired location. Do not pick up a full fountain by the towerpiece. To properly pick up the fountain, use both hands and grip the sidewalls of the bowl and lift up.2. Fill the fountain by pouring water directly into the bowl. Leave at least ½ inch ofspace between the water level and the rim of the bowl to help control spills and splashing. To protect your floor always use a protective mat, such as a towel or water resistant placemat. This will help protect your floor from splashing or spills caused by your pet.3. Before you plug in the fountain, make sure the electrical power cord, the adapterand your hands are completely dry. Connect the in-line plug and make sure no silver is showing, then plug the adapter into a standard electrical wall outlet. 4. Add water to the bowl as needed. Never let the water level fall below 1 inchfrom the base of the bowl or you might risk pump failure. Replacement pumps are sold separately by calling the Customer Care Center at +1 (800) 732-2677 or visit .Note: Use a soft cloth or sponge to prevent scratching the bowl.CARBON FILTER: Replace carbon filter every two to four weeks.• Always rinse the carbon filter prior to use.• A small amount of carbon dust may be released for the life of the filter, this is normal and is not harmful to your pet.• Replace filters more frequently when using the fountain for multiple pets or pets that produce a lot of saliva.FOAM FILTER: Replace the foam filter every one to two months.• If you do not intend to replace the filter at the time of cleaning, rinse the foam filter thoroughly with fresh water.Filter subscriptions now available! Get fountain filters automatically and conveniently delivered right to your door when you need them. Free shipping and 5% discount included. Visit to sign up or call our Customer Care Center at +1 (800) 732-2677.8Customer Care Center +1 (800) 732-2677PET FOUNTAIN: Array 1.plug (2A).2.tower aside for cleaning (2B 3.cleaning (2C).4.lifting straight up (2D).5.6.straight up to remove (2E).7.a sink.8.cleaning.9.with a new one.11.your pump.water inside the dishwasher.Customer Care Center +1 (800) 732-267710Pump MaintenanceCleaning the pump is essential to the longevity of the fountain, as well as the cleanliness of the water. Clean the pump every two weeks. Warranty may be voided if the pump’s motor is not cleaned regularly.from the Drinkwell ®up (3D 80% water).6. Once the parts are clean you can reassemble the pump for use. a) Replace the impeller.b) Replace the stator.c) Replace the faceplate.top. (4A).2.corner of the square (4B). 3.four notches to choose from.4.and push all the way down.5.post to seal off the bowl (4D).6.dust, which is harmless.7.8.9.10. Place the ceramic tower inside the bowl. Thefilter housing and the tower. Carefully lower thetower until it rests flat (4F).11. Place the fountain in desired location. Do notpick up a full fountain by the tower piece. Toproperly pick up the fountain, use both handsand grip the sidewalls of the bowl and lift up.12. Fill the fountain by pouring water directlyinto the bowl. Leave at least ½ inch of spaceto help control spills and splashing. To protecta towel or water resistant placemat. This willhelp protect your floor from splashing or spillscaused by your pet.13. Before you plug in the fountain, make sure theelectrical power cord, the adapter and yourhands are completely dry. Connect the in-lineplug and make sure no silver is showing,(4GThe Fountain and Your EnvironmentIf you live in a humid environment and have problems with mold or algae, soak all fountain parts in a diluted vinegar solution (20% white vinegar and 80% water)for 10 minutes after regular cleaning. Also, pour the diluted vinegar solution into the pump’s motor cavity. If you have hard water, small white mineral deposits may form on or inside the pump. This can eventually prevent the impeller from turning properly. To avoid replacement or damage to the pump, please take the following precautions:• Clean the pump more frequently.• Clean the pump with a diluted vinegar solution weekly.• Use bottled water instead of tap water.General Tips• When being introduced to the fountain, your pet may be cautious of this new and unusual object. After beginning operation of your fountain, simply allow your pet to adjust at his or her own pace. Some pets may take several days or longer to begin use, while others will start right away.• Your pet may prefer that the fountain be placed away from their normal feeding area. Try placing it in another location, such as a different area of the kitchen or in a bathroom or utility room.• Add ice cubes to the bowl for refreshing, ice-cold running water.12Customer Care Center +1 (800) 732-2677TroubleshootingThe answers to these questions should help you solve most problems you may have with the pet fountain. If they do not, please contact our Customer Care Center at.+1 (800) 732-267713Customer Care Center +1 (800) 732-267714Replacement Parts and AccessoriesReplacement parts or accessories for your fountain can be purchased by visiting or by contacting our Customer Care Center at +1 (800) 732-2677.Filter subscriptions now available! Get fountain filters automatically andconveniently delivered right to your door when you need them. Free shipping and 5% discount included. Visit to sign up or call our Customer Care Center at +1 (800) 732-2677.Customer CareUSA & Canada - Tel: +1 (800) 732-2677Monday - Friday 8 AM – 8 PM / Saturday 9 AM – 5 PMTerms of Use and Limitation of Liability1. Terms of UseThe use of this product is subject to your acceptance without modification of the terms, conditions and notices contained with this product. Use of this product implies acceptance of all such terms, conditions, and notices. If you do not wish to accept these terms, conditions, and notices, please return the product, unused, in its original packaging and at your own cost and risk to the relevant Customer Care location together with proof of purchase for a full refund.2. Proper UseProper Use includes, without limitation, reviewing the entire Product Manualand any specific safety information statements. The specific temperament orsize/weight of your pet may not be suitable for this product. If you are unsure whether this product is appropriate for your pet, please consult your veterinarian or certified trainer prior to use. For products used with pets where training isdesired, Radio Systems Corporation recommends that these training products are not used if your pet is aggressive and accepts no liability for determining suitability in individual cases.3. No Unlawful or Prohibited UseThis product is designed for use with pets only. This product is not intended to harm, injure or provoke. Using this product in a way that is not intended could result in violation of Federal, State or local laws.4. Limitation of LiabilityIn no event shall Radio Systems Corporation or any of its associated companies be liable for (i) any direct, indirect, punitive, incidental, special or consequential damage and/or (ii) any loss or damages whatsoever arising out of or connected with the use or misuse of this product. The Purchaser assumes all risks and liability from the use of this product to the fullest extent permissible by law.5. Modification of Terms and ConditionsRadio Systems Corporation reserves the right to change the terms, conditions and notices governing this product from time to time. If such changes have been notified to you prior to your use of this product, they shall be binding on you as if incorporated herein.WarrantyOne Year Non-Transferable Limited WarrantyThis Product has the benefit of a limited manufacturer’s warranty. Complete details of the warranty applicable to this Product and its terms can be found at .15Radio Systems Corporation10427 PetSafe WayKnoxville, TN 37932+1 (800) 732-2677RE400-1867/2©2019 Radio Systems Corporation。
Solvex 筛芯筛滤器维护指南说明书

Solvex ™ Cartridge FiltersUser GuideRefer to the appropriateValidation Guide or Certificate of Quality for filter specifications.Troubleshooting Decision Tree for The vibrant M and Solvex are trademarks of Merck KGaA,Darmstadt, Germany or its affiliates. All other trademarks are the property of their respective owners. Detailed information on trademarks is available via publicly accessible resources.© 2007- 2018 Merck KGaA, Darmstadt, Germany and/or its affiliates. All Rights ReservedVM_UG3217EN Rev 1 11/2018. Previously published as docu-ment number 00101875PU.For technical assistanceplease visit:/techservice.Worldwide contact information is available at /offices For additional information and documentation please contact: Merck KGaA, Darmstadt, Germany Corporation with General Partners Frankfurter Str . 25064293 Darmstadt, Germany Phone: + 49 6151-72 0For requests from USA and Canada please contact: MilliporeSigmaA subsidiary of Merck KGaA, Darmstadt, Germany 400 Summit DriveBurlington, MA 01803 USA Phone: 1-800-645-5476We provide information and advice to our customers on application technologies and regulatory matters to the best of our knowledge and ability, but without obligation or liability. Existing laws and regulations are to be observed in all cases by our customers. This also applies in respect to any rights of third parties. Our information and advice do not relieve our customers of their own responsibility for checking the suitability of our products for the envisaged purpose.TroubleshootingWettingIf you encounter an integrity test value that is out of specification, the cause may be:• improperly or incompletely wet filter• contaminant or residual on the filter • improper O-ring seal• temperature outside manufacturer’srecommended temperature• system hardware leak (if automatic integritytester is used)Integrity TestingDrying prior to retesting can minimize integrity test failure.If you encounter a problem:• Do not remove the cartridge from its housing(for a post-use test).• Check connections for leaks (if automaticintegrity tester is used).• Ensure that appropriate integrity testspecifications are used for the filter and housing.• Make sure the environmental and/or test fluid temperature is within themanufacturer’s recommended specification.• Make sure an appropriate test fluid is used.Unpacking the Box A Certificate of Quality, included with each filter, provides detailed product properties and performance data. Installing the Filter Before using the filter, verify the catalog number. The catalog number, lot number and serial number are located on top of the cartridge.It is very important that the filter is installed in the housing correctly. The cartridges are shipped double bagged. Carefully tear open the outer bag, then carefully tear open the inner bag. Use the inner bag as a gloveto avoid touching the cartridge with ungloved hands while installing it into the housing. T o ease installation ofthe cartridge into the housing, wet the O-rings with sterile water or fluid to be filtered and gently slide the cartridge into place. For a Code 7 cartridge, after the O-rings are in the socket, twist the cartridge slightly to “lock” it in place. When installing the cartridge, avoid pinching the O-rings or bending the tabs on the Code 7 cartridge. A pre-use integrity test can confirm that the filter is installed in the housing correctly. NOTE: Do not touch a cartridgewith ungloved hands as dirtand oils from skin can affectthe performance of the filter.70/30 IPA Removal FollowingIntegrity Testing1. Set up intallation as shown in Figure 1 and close all valves (V1, V2 andV3).2. Open valves V1 and V2. Flow fluid to be filtered through the filter at theminimum recommended flow rate shown in Table 1. When fluid flowsthrough V2 and all air has been released. Close V2.3. Gradually increase the upstream pressure to 2.8 bar (40 psig). Donot exceed the maximum differential pressure rating (see Certificateof Quality) for the filter unit. Maintain this pressure for a minimum ofone minute to dissolve any residual gas within the filter and to ensuremembrane wetting.4. After one minute, gradually open the downstream valve (V3) andcontinue to flow fluid through the filter at the minimum flow rate shownin Table 1 for five minutes.5. Stop the fluid flow and allow the upstream pressure (P1) to drop to zero.6. Drain the fluid from the housing.Table 1: Minimum Recommended Flow Rates for 5 minutes at 2–5 psi (0.2–0.4 bar)Cartridge Length (in.)70/30 IPA Flow Rate (Lpm)103206309Integrity TesterV1V3Figure 1: Typical installation70/30 IPA Wetting Instructions• The cartridge should be completely dry to ensure complete and adequatewetting of the membrane prior to the procedure.• Use 70/30 IPA (70%/30% isopropanol/purified water).• Moisten the cartridge O-ring with 70/30 IPA to allow ease of insertion into thefilter housing.1. Set up intallation as shown in Figure1 and close all valves (V1, V2 andV3).2. Open V1 and V2. ENSURE THATTHE UNIT IS PROPERLYGROUNDED. USE A NITROGENPRESSURE SOURCE TOMINIMIZE FLAMMABILITY. Flow70/30 IPA through the filter at theminimum recommended flow rateshown in Table 1. When fluid flowsthrough V2 and all air has beenreleased close V2.3. Gradually increase the upstream pressure to 1 bar (15 psig). Do notexceed the maximum differential pressure rating for the filter unit.Maintain this pressure for a minimum of one minute to dissolve anyresidual gas within the filter and to ensure membrane wetting.4. After one minute, gradually open the downstream valve (V3) andcontinue to flow 70/30 IPA through the filter at the minimumrecommended flow rate shown in Table 1 for five minutes.5. Stop the fluid flow and allow the upstream pressure (P1) to drop to zero.6. Drain the wetting fluid from the housing.7. Perform an integrity test.。
Affinia 阿菲尼亚介绍

Pg. 9
Pg. 9
IAM Partner 售后市场伙伴
IAM Long-standing customer relationships 售后市场长期合作的客户
We owned long-standing cooperation customer from 17 years to 40 years in IAM market. The average cooperation time is more than 25 years. 我们在售后市场有着十七年到长达四十多年的忠实客户。平均合作时间已经超过二十五年了。
CEO & President Terry R. McCormack 首席执行官兼总裁 特里-麦考马克
Pg. 2
Pg. 2
Our Company 我们的公司
Argentina 阿根廷 Founded: Dec/01/2004 成立时间:2004年12月01日 Employees: approx. 10,000 全球员工数量:约10,000 International: Locations in 11 countries 全球业务分布:11个国家有分支机构 Revenues: $ 2 billion (year 2010) 全球营业金额:20亿美元(2010年) Global business coverage more than 70 countries. 全球业务覆盖了超过70多个国家 Brazil 巴西 Canada 加拿大 China 中国 India 印度 Mexico 墨西哥 Poland 波兰 Ukraine 乌克兰 USA 美国 Uruguay 乌拉圭 Affinia Group focus on the global on- and off-highway replacement parts and service market. Industry leading brands, worldwide manufacturing and sourcing. 阿菲尼亚集团关注于公路和非公路车辆的配件市场,并致力于成为全球工业品牌、生产和制造的领导者。 Venezuela 委内瑞拉
滤清器对照表
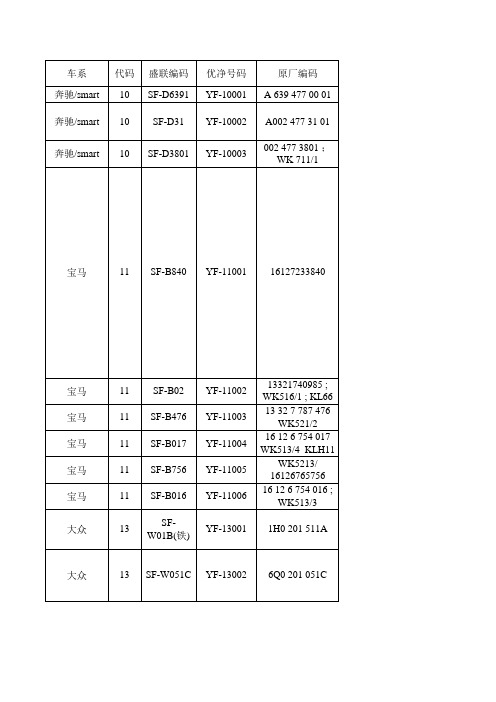
16400-SU100 17040-JN00A、 17040-EW80D 1T040-ED80A
17040-JR50A
17040-9Y00A 17040-2ZS00 16400-4M405
16400-V2700
SF-312
SF-352 SF-377 SF-341 SF-346 SF-376 SF-336 SF-353 SF-311 SF-357 SF-343 SF-3176 SF-417 SF-417B SF-407 SF-403 SF-401 SF-988 SF-309 SF-C05 SF-C7J0
30
福特/悍马/阿 斯顿·马丁/林
30
福特/悍马/阿
斯顿·马丁/林 30
肯
福特/悍马/阿 斯顿·马丁/林
30
福特/悍马/阿 斯顿·马丁/林
30
福特/悍马/阿 斯顿·马丁/林
30
福特/悍马/阿 斯顿·马丁/林
30
福特/悍马/阿 斯顿·马丁/林
30
本田
34
本田
34
本田
34
本田
34
本田
34
SF-G408
SF-G898 SF-G01 SF-G05B SF-F15 SF-F51
36 SF-272 YF-36007 16400-72L00
日产
36
日产
36
日产
36
日产
36
日产
36
日产
36
日产
36
日产
36
三菱
37
三菱
37
三菱
37
三菱
37
三菱
37
三菱
37
三菱
大众公司供应商代码对应表

CShhaannggzhhaoiuKCahiagnegdRaoaAdusttoarAcEcleescstorroineiscsFactory Co.,Ltd.
Shanghai Koito Automotive Lamp Co.,Ltd.
Changshu Automotive Work topack Factory Shanghai SACHS Powertrain Component Systems Co.,Ltd
代码
厂名
5CA 上海尚翔汽车胶管有限公司
5CB 上海华向橡胶制品有限公司智亿工程橡胶分公司
5BZ 上海长辉汽车饰件厂
5CD 上海劳伦茨橡胶制品有限公司 5KJ 上海大和模具塑料厂有限公司
4MA 麦格纳唐纳利(上海)汽车系统有限公司 5CE 上海造漆厂 5EF 上海安谊车轮有限公司
英文名称 Shanghai Shangxiang Automobile Hoses Company Limited Shanghai Huaxiang Rubber Products Co., Ltd. Zhiyi Rubber Branch Shanghai Changhui Automotive Decoration Fty,. Shanghai Senlian Roulunds Rubber Belt Co.,Ltd
马勒滤清器产品表对照表

180 201 511 6Q0 201 051B, S1832B 6Q0 201 051C, 6Q0 201 051 J 1K0 201 051 C, 1K0 201 051 K 1K0 129 620D, 1K0 129 620F, 1KD 129 620B, 1KD 129 620A 191 819 638 8A0 819 439A 1J0 819 644A, 180 819 644 6Q0 819 653, 6RD 820 367, 6Q0 820 367B 1K0 819 644 1H0 819 644 377 819 638 180 819 638 8A0 819 439A 6Q0 820 367B 1K1 819 653A, 1KD 819 644, 1KD 819 653 1H0 819 644A 180 819 638
OX 128/1D ECO OX128/1D机滤芯 OX 254D4 ECO OX254D4机滤芯 OX 396D ECO OX 398D ECO KL 449 KL 460 KL 450/1 KL 450 KL 479 KL 502 LX 1678 LX 1679 LX 1680 LX 1681 LX 1721 LX 1897 LX 1898 LX 1682 LX 1701 LX 1900 LX 1722 LX 1723 LX 1899 LX 2024/1 LX 3184 074环保机滤芯 劲情劲取环保机滤芯 普桑汽油滤 POLO电喷燃油滤 桑塔纳电喷燃油滤(铝) 捷达电喷燃油滤 宝来燃油滤 捷达柴油车柴滤 普桑空滤芯 2000型空滤芯 2VQS空滤芯 B5空滤芯 POLO空滤芯(1.4) 劲情劲取空滤芯 高尔空滤芯 捷达空滤芯(KF2917) 捷达王空滤芯(KF2916) 捷达柴油车空滤芯 宝来空滤芯(1.8) 宝来空滤芯(1.8T) 途安速腾空滤芯 LX2024/1空滤芯 新朗逸空滤芯
唯特利(Victaulic)三通型过滤器W730系列说明书

如需产品安装、维护或支持信息,请参考文档末的信息。
1.0 产品描述供货尺寸:• 14 – 24 英寸/DN350 – DN600最大工作压力:• 可达300 psi/2068 kPa/21 bar 应用:• 提供直通流道,压降更低管道材料:• 碳钢管道制备:• 辊槽,依照25.09号技术文件:先进沟槽系统(AGS )滚槽规格。
2.0 认证/列名产品的设计和制造依照 Victaulic (唯特利)质量管理体系进行(根据 ISO-9001:2015 获得 LPCB 认证)。
Victaulic三通型过滤器W730系列20.11-CHI系统编号位置提交人日期规格部分段落批准人日期3.0 规格 – 材料本体(14 – 24英寸/DN350 – DN600):• 分段焊接碳钢,ANSI标准壁厚,符合ASTM A53,E型或S型,等级:B• 可选:镀锌管端盲板(14 – 24英寸/DN350 – DN600):• 碳钢T型螺栓铰链盖,300-TB级• 可选:镀锌滤篮:不锈钢, 304 型,框架和孔目。
• 14 – 16 英寸/DN350 – DN400:6 x 6 孔目 (0.041英寸金属丝),开口为 0.126英寸• 18 – 24 英寸/DN450 – DN600:4 x 4 孔目 (0.047英寸金属丝),开口为 0.203英寸• 可选:可提供其他尺寸和材质的孔目,详情请联系Victaulic(唯特利)磁体:磁体,特别用于可在工厂添加的润滑油应用和其他情况。
如需详细信息,请联系Victaulic(唯特利)。
其他:可满足特殊需求。
如在推荐、可用性和交付上有特别需求,请联系Victaulic(唯特利)。
注• 进出口之间最大压差不得超过 10 psi/69 kPa。
装配间隙拆除过滤器滤篮所要求的推荐最小清洗间隙1该尺寸为拆除过程中测得中心线至滤篮顶部的尺寸数值5.0 性能W730系列三通型过滤器+60°F/+16°C的水流C V值如下表所示。