掘进机智能控制系统的设计与维护
煤矿智能化掘进系统的开发与应用

煤矿智能化掘进系统的开发与应用摘要:为提升煤矿开采的效率和质量,大部分煤矿企业对于掘进机械的技术水平较为重视,如何提升掘进机械的智能化水平成为相关领域的一项研究热点。
但由于煤矿掘进机械的智能化涉及到的技术领域较多,因此这些机械设备在智能化方面仍有着一定的提升空间。
这就需要对煤矿智能化掘进系统做进一步的深入探究,并将其应用到工程实践当中,充分发挥其优势。
关键词:煤矿;智能化掘进系统;系统开发引言如今在进行煤矿井下作业时,所使用的挖掘设备已经逐渐趋向于智能化,原有的挖掘技术已无法满足现代生产的需求,必须对煤矿井下作业时所使用的设备进行改进与完善,才能够提高煤矿井下作业的工作效率,进一步保证煤矿安全、可持续发展。
1智能掘进的内涵智能化掘进是通过构建多机协同控制系统,实现连续、快速、稳定、安全智能化巷道掘锚运作业。
近期发布的“煤矿智能化建设标准或指导意见”建议掘进工作面的智能化建设总体目标包括有:设备的无线遥控、自主操作与远程控制干预,掘支快速自动平行作业、高效健康除尘、环境危险信息实时监测与预警、多设备的集中协同控制等。
掘进工作面实现这些功能需要依托相关多级的设备、信息、感知等业务的支撑。
智能化掘进是通过构建多机协同控制系统,实现连续、快速、稳定、安全智能化巷道掘锚运作业。
掘进工作面的智能化建设基本任务应当包括:信息自动感知、危险自主判识预警、设备自主运行、远程监视/干预。
掘进工作面实现这些功能需要得到相关软硬件设备、信息、感知等多级业务的支撑。
通过对超前地质信息、巷道环境信息、围岩的探测感知或监控监测(如水文、构造、瓦斯、压力、粉尘、位置与航向、设备扭矩、电流、人机位置等),收集可靠信息并通过数据挖掘、融合、分析、整合等方法,建立相关危险预警模型、自动控制模型、强制干预模型、系统协同模型等数据模型算法,通过即时通讯技术、数字孪生技术、数字边缘云技术,实现灾害危险信息化的评测预警,掘进支护运输设备的自主作业、运行参数的自主优化、多级设备的协同运作、作业信息的动态传输、远程人员的实时干预等。
煤矿井下综合机械化掘进系统智能化建设探讨

煤矿井下综合机械化掘进系统智能化建设探讨摘要:如今在进行煤矿井下作业时,所使用的挖掘设备已经逐渐趋向于智能化,原有的挖掘技术已无法满足现代生产的需求,必须对煤矿井下作业时所使用的设备进行改进与完善,才能够提高煤矿井下作业的工作效率,进一步保证煤矿安全、可持续发展。
关键词:煤矿;井下;综合机械化掘进系统;智能化;建设1 煤矿井下综合机械化掘进系统的智能化首先,煤矿井下综合机械化掘进系统中会使用单机智能控制技术,而该技术中主要包括无线通信系统、人机交互系统、无线遥感系统等。
在综合机械化掘进系统中使用单机智能控制技术可以使各个设备之间能够进行协同工作,而且该系统还可以事先对工作流程进行设定,从而使工作人员运用计算机就能够对各种设备进行控制。
其次,煤矿井下综合机械化掘进系统中还会使用智能结构技术,该技术主要包括自动定位系统、自动截割技术等。
通过使用自动定位系统,可以对井下煤矿作业进行全方位的监控,也可以及时向工作人员发送工作指令,确保各个设备安全稳定运行的同时进一步强化煤矿井下挖掘工作的工作效率。
而使用自动截割技术还可以利用该技术准确地获取截割滚筒的位置,并且利用该技术被截割滚筒的各种参数进行准确分析,最终实现自动截割。
最后,煤矿井下综合机械化掘进系统中还会使用多机协同控制技术,该技术的运用能够对煤矿井下的运输系统进行共同控制,并且还能够使连采机、破碎机等设备都朝着智能化方向发展。
2 煤矿井下综合机械化掘进系统智能化建设2.1 建设远程遥控系统在煤矿井下综合机械化掘进系统智能化建设过程中,使其具备远程遥控器,可以确保在工作过程中实现数据输送的畅通性,对掘进设备可以进行远程遥控。
进一步推动掘进设备,进行自动化截割工作。
除此以外,远程遥控系统的构建还可以进一步明确掘进设备的位置,提升对掘进设备控制的精确度。
2.2 建设综合性的耦合系统综合机械化掘进系统的机制非常复杂,如果在进行煤矿井下作业时,无法发挥综合机械化掘进系统的作用,那么就有可能为煤矿井下掘进工作带来严峻的挑战。
玉溪煤矿工作面掘进机中智能化掘进

收稿日期:2022 06 06作者简介:王㊀凯(1993-),男,山西高平人,助理工程师,从事采掘管理技术工作㊂doi:10.3969/j.issn.1005-2798.2023.01.018玉溪煤矿工作面掘进机中智能化掘进集控系统应用研究王㊀凯(山西兰花科创玉溪煤矿有限责任公司,山西沁水㊀048000)摘㊀要:为加快煤矿智能化建设改造,推动煤矿装备向智能化㊁高端化发展,实现采掘工作面减人作业,在掘进机中建立一套智能化掘进集控系统已成为当前重要的研究趋势㊂为此,以玉溪煤矿工作面掘进机为例,从多个方面开展了掘进机中智能化掘进集控系统的方案设计及关键分系统研究,经过对该集控系统的实际应用得出:该系统运行良好,智能化程度较高,能实现对掘进机设备的自动导航㊁自动坡度追踪和自动截割等功能,系统的综合评分较高,达到了工作面掘进机的智能化掘进作业要求㊂对提高掘进机的作业效率㊁减少作业人员数量㊁提高工作面的作业安全性具有重要意义㊂关键词:煤矿;智能化;掘进;集控系统中图分类号:TD632.2㊀㊀㊀文献标识码:B㊀㊀㊀文章编号:1005 2798(2023)01 0068 03㊀㊀随着煤矿资源的大量开采,采用更加先进的开采设备及系统提高煤矿开采量已成为当前煤矿领域的重要发展方向㊂矿用掘进机是煤矿开采中的重要设备,与采煤机㊁带式输送机等设备共同完成煤矿的开采任务[1]㊂当前市场上通用的掘进机设备智能化程度较低㊁所需作业人员较多,设计智能化集控系统已成为当前煤矿设备智能化升级发展的必然趋势[2]㊂为此,以玉溪煤矿工作面掘进机为例,开展了矿用掘进机中智能化掘进集控系统的总体设计及关键分系统研究,完成了该系统的实际应用及评价,验证了该系统的可靠性及稳定性,提高了掘进机的掘进效率及煤矿开采量,达到了预期效果,实际应用价值较大㊂1㊀集控系统设计的必要性以玉溪煤矿工作面掘进机为例㊂该煤矿采用四六制生产制度,检修班不允许生产,而当前掘进工作面在检修班进行检修㊁防突检测以及前移胶带机尾等工作㊂但在实际掘进过程中存在以下问题:1)㊀当前掘锚一体机机载钻锚装置无法满足防突检测钻孔要求,新购一台成本较高;2)㊀增加带式输送机自移机尾无法实现减人增效;3)㊀掘进断面较大,支护作业规程要求一掘一锚,目前使用手持气动锚杆钻机进行支护作业,掘进机工作一个循环需要分为上下两部分完成,工作效率低且现场作业人员安全系数较低㊂因此,同时考虑先用于煤巷掘进,后期也可在岩巷掘进中使用,计划采购1台智能化EBZ200型悬臂式岩巷掘进机,配套原有的供电㊁运输㊁通风及排水等设备,在1303工作面回风巷中设计一套集成于掘进机设备中的智能化掘进集控系统,以实现掘进工作面的少人化,达到生产安全管理控制的目的㊂2㊀集控系统设计集控系统是整个EBZ200型煤矿掘进机中重要的组成部分,包括井下远程集控中心和地面远程集控中心㊂地面远程集控中心得到井下远程集控中心的授权后,在地面可以实现在井下的全部操作功能㊂井下远程集控中心在紧急情况下可以随时把操控权限切换到井下远程集控中心㊂在掘进机本体中配备了倾角传感器㊁惯性导航仪㊁三维扫描仪㊁红外摄像仪㊁人员接近传感器㊁油温油位传感器㊁语音对讲设备和控制箱等智能化监测监控设备,实现掘进机的工况参数监测㊁数据采集㊁设备精准定位㊁自主导航㊁智能截割㊁环境监测等功能[3]㊂在数据传输和集控方面,主要利用矿方的5G系统,将智能掘进机相关数据接入井下远程集控中心,实现远程控制与监控㊂同时,集控中心的相关数据通过千兆交换机接入井下万兆环网,接入地面远程集控中心㊂通过智能化控制软件,在井下远程集控中心㊁地面远程集控中心能够实时显示掘进工作86面现场的情况,监听现场声音;同时设备工作状态信息可以实时显示在集控中心的显示界面上;现场开放权限后,可以实现掘进工作面设备的井下集控中心或地面集控中心远程操作控制,集控系统网络构架如图1所示㊂图1㊀掘进机中集控系统网络构架3㊀关键分系统设计3.1㊀掘进机车身定位系统掘进机车身定位系统采用三维激光扫描仪与激光陀螺惯性导航融合技术㊂三维激光扫描仪主要通过内置的激光雷达扫描预定的相关标靶,将采集的点云数据发送至GPU图像处理器进行模型构建及计算㊂其中,该定位系统中的CPU处理器通过高速运算将三维激光扫描仪计算数据与激光陀螺惯性导航仪的航姿信息(航向角㊁俯仰角㊁侧倾角㊁加速度等)进行融合处理,得到掘进机车身的姿态及位置信息,其原理如图2所示㊂另外,车身位置信息结合截割臂升降㊁回转㊁伸缩油缸位移传感器通过车载控制器进行截割头相对于巷道的位置信息[4]㊂截割头位置信息是断面自动截割成型的重要数据信息㊂车身姿态和位置信息是进行车身自主纠偏和防碰撞的重要数据信息㊂数据通过构建完毕的掘进机模型可以得出截割机构的俯仰角和回转角㊂图2㊀惯性导航仪原理图3.2㊀断面定义及路径规划设计煤矿巷道断面一般有弧顶㊁平顶㊁斜顶式三种,仅在弧线段数㊁直线段数和直线斜率方面有区别㊂基于以上特性,利用直线按间距分段和弧线按角度分段相结合的方法对断面的轮廓在PLC内进行模型搭建㊂另外,断面自动成形分为逐行扫描阶段和边界扫描阶段㊂逐行扫描完成断面的初成形,边界扫描完成断面的精细化边界修帮㊂控制逐行扫描间96距可以对成形断面的平整度进行调整㊂所设计的断面定义及路径规划如图3所示㊂图3㊀断面定义及路径规划3.3㊀环境监测㊁安全保护关键仪器设备选型设计3.3.1㊀粉尘监测仪器选型设计粉尘传感器主要实现对煤矿井下呼吸性粉尘的在线监测㊂传感器具有呼尘分离效果好算法先进准确度高额定工作电流小传输距离更远等显著特点㊂为此,针对此工作面,在工作面上安装了GCG1000 (X)粉尘浓度传感器,传感器数量根据监测要求确定,粉尘传感器主要技术参数有:①粉尘浓度测量范围为0.1~500mg/m3;②粉尘浓度测量误差不大于ʃ15%.3.3.2㊀甲烷气体监测仪器选型设计矿用低浓度甲烷传感器主要适用于煤矿井下和其它具有爆炸性气体(甲烷混合物㊁煤尘)场合,可用于井下大中型采掘设备和其它机电设备上,连续监测设备附近风流中的瓦斯浓度,也可用于固定场合,当瓦斯浓度达到或超过报警点时,传感器立即发出声㊁光报警信号㊂故选用了GJC4(B)型矿用甲烷传感器,该传感器采用高性能热催化元件㊁微电脑数字技术和新型电子器件,性能稳定,门限准确,反应迅速,精度高㊂使用方式采用人性化设计,软调节技术,操作简单,使用方便㊂其工作温度为(0~40)ħ,测量范围:(0.00%~4.00%)CH4,响应时间ɤ20s,传感器工作电压(9~24)VDC,传感器的传输距离ɤ2km.3.4㊀危险区域人员识别技术分析为提高危险作业区域人员的保护力度,设计了一种危险区域人员识别技术㊂该技术采用在掘进机车身上加装热释红外传感器㊁精准定位等模式,对进入探测范围内的人员进行感应,对进入危险区域人员近感探测,开机前及运行过程中,监测到人员时, 5m范围内停机,声光报警器报警;同时,将误闯信息传递至监控平台上,实现对相关信息的实时显示及报警,危险区域人员识别示意如图4所示㊂4㊀实际应用评价为进一步验证此掘进机中集控系统的综合性能,按照‘全省煤矿智能化建设基本要求及评分方法(试行)“要求,对该系统进行了实际应用及评价打分验证㊂该系统在实际应用过程中,整体运行良好,智能化程度较高,系统可靠性及稳定性较好;建立了在地面以及井下建立远程控制系统,实现一键启动及智能操作;同时,该系统自带瓦斯传感器,增加了粉尘传感器,实现了对井下环境数据智能分析及检测;也实现了整个掘进过程的自主导航㊁坡度追踪和自动截割等功能;通过与锚杆钻车的配合使用,实现全机械化作业,掘进速度满足矿井采掘接替要求㊂经玉溪煤矿相关人员评价,该系统的综合评分为76.34分,相对较高,达到了工作面中掘进机的智能化掘进作业要求㊂图4㊀危险区域人员识别示意5㊀结㊀语以玉溪煤矿工作面掘进机为例,在分析当前煤矿工作面掘进过程中存在问题的基础上,开展了掘进集控系统的总体设计及关键分系统设计研究,并对该系统进行了实际应用评价㊂该集控系统运行良好,智能化程度较高,实现了整个掘进过程的多项自动控制及操作;整个掘进机设备的掘进效率明显提高,达到了预期要求㊂该系统的应用设计有效支撑并完善了掘进机设备及整个工作面的智能化程度,实际应用价值较大㊂参考文献:[1]㊀张㊀朋.综采工作面集控系统的设计分析[J].机械管理开发,2021,36(8):235-236,312.[2]㊀魏永龙,魏永东,徐㊀威.冲击地压孤岛工作面智能化掘进工艺的探索与应用[J].中国矿业,2021,30(S1):113-119.[3]㊀孙㊀健.综采工作面信息化集控系统在平朔矿区的应用[J].露天采矿技术,2021,36(1):79-82. [4]㊀裴新宇.煤矿智能化远程集控系统分析[J].矿业装备,2021(1):116-117.[责任编辑:常丽芳]07。
浅谈煤矿掘进工作中智能化掘进控制系统的运用

浅谈煤矿掘进工作中智能化掘进控制系统的运用摘要:煤矿掘进工作面智能化控制系统的投用,可以减少掘进工作面人员配置,简化掘进施工流程,降低了安全风险,预期效果显著,煤矿企业应大力推广智能化掘进控制系统在掘进工作面运用。
关键词:煤矿;掘进工作;智能化;掘进控制系统一、工作面现状某矿现有快速掘进系统一套,包含EBZ-220T掘探一体机,锚杆钻装机组,迈步自移机尾装置,带式转载机四大部分,安装在16312回风巷掘进工作面,快掘系统掘进时需要8人(主副掘进机司机2人,支护工4人,皮带机司机1人、清煤工1人),工作面工作人员较多,井下巷道空间有限,快速掘进设备整体性强,总长约40米,两侧安全距离较窄,人员现场操作存在安全隐患,危险系数较高,人身伤害事故无法有效避免。
二、配套设备及作用图一惯导图二矿用全自动全站仪掘锚一体机机身安装一台惯导,实现对掘锚一体机的定位和定姿。
在巷道导线点位置安装一台矿用陀螺全站仪,实时动态全自动测量固定和移动目标点的大地坐标。
全自动激光全站仪与惯导技术的定向定位导航系统由硬件和软件两大部分组成。
其中,硬件部分包括全自动跟踪全站仪、反射棱镜、惯性导航设备。
软件部分包括数据实时通讯模块、基于惯导和全站仪的定位模块、基于惯导的定位定姿模块、掘锚一体机三维位姿展示模块、定位定姿数据输出模块、掘进路径导航模块等功能模块。
惯性导航定向定位系统结合惯导实时方位角度数据、全站仪三维坐标实时数据等数据,通过定向定位算法得出掘锚一体机的实时位置与掘锚一体机规划路径的偏差,给出姿态修正数据,实现掘锚一体机定位、定向导航功能,配套设备也随之完成各自的工艺工序。
掘锚一体机三维姿态展示模块安装在集控中心,通过接收定位定姿数据输出模块发送的姿态和位置信息,并结合掘锚一体机的三维模型,实现掘进过程中掘锚一体机的位置和姿态实时三维展示。
定位定姿数据数据输出模块输出的姿态和位置信息,可以作为掘锚一体机定位智能截割和导航的基准数据,通过CAN总线与PLC进行通信。
掘锚机智能化综合控制技术的研究
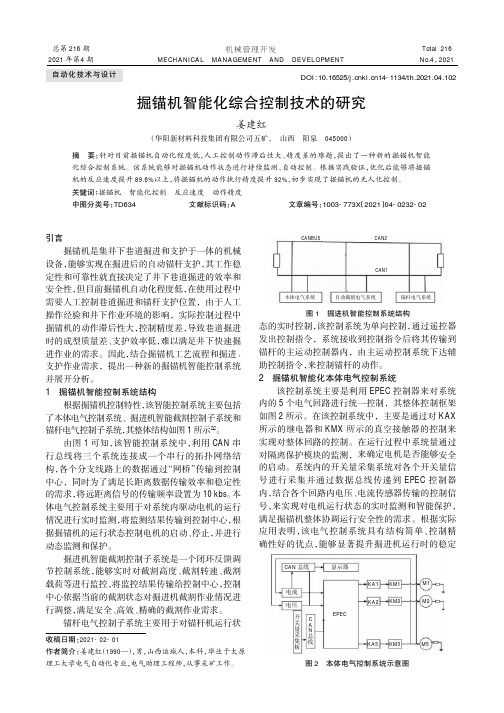
引言掘锚机是集井下巷道掘进和支护于一体的机械设备,能够实现在掘进后的自动锚杆支护,其工作稳定性和可靠性就直接决定了井下巷道掘进的效率和安全性,但目前掘锚机自动化程度低,在使用过程中需要人工控制巷道掘进和锚杆支护位置,由于人工操作经验和井下作业环境的影响,实际控制过程中掘锚机的动作滞后性大,控制精度差,导致巷道掘进时的成型质量差、支护效率低,难以满足井下快速掘进作业的需求。
因此,结合掘锚机工艺流程和掘进、支护作业需求,提出一种新的掘锚机智能控制系统并展开分析。
1掘锚机智能控制系统结构根据掘锚机控制特性,该智能控制系统主要包括了本体电气控制系统、掘进机智能截割控制子系统和锚杆电气控制子系统,其整体结构如图1所示[1]。
由图1可知,该智能控制系统中,利用CAN 串行总线将三个系统连接成一个串行的拓扑网络结构,各个分支线路上的数据通过“网桥”传输到控制中心,同时为了满足长距离数据传输效率和稳定性的需求,将远距离信号的传输频率设置为10kbs 。
本体电气控制系统主要用于对系统内驱动电机的运行情况进行实时监测,将监测结果传输到控制中心,根据掘锚机的运行状态控制电机的启动、停止,并进行动态监测和保护。
掘进机智能截割控制子系统是一个闭环反馈调节控制系统,能够实时对截割高度、截割转速、截割载荷等进行监控,将监控结果传输给控制中心,控制中心依据当前的截割状态对掘进机截割作业情况进行调整,满足安全、高效、精确的截割作业需求。
锚杆电气控制子系统主要用于对锚杆机运行状态的实时控制,该控制系统为单向控制,通过遥控器发出控制指令,系统接收到控制指令后将其传输到锚杆的主运动控制器内,由主运动控制系统下达辅助控制指令,来控制锚杆的动作。
2掘锚机智能化本体电气控制系统该控制系统主要是利用EPEC 控制器来对系统内的5个电气回路进行统一控制,其整体控制框架如图2所示。
在该控制系统中,主要是通过对KAX 所示的继电器和KMX 所示的真空接触器的控制来实现对整体回路的控制。
基于PCC的掘进机监控系统硬件设计
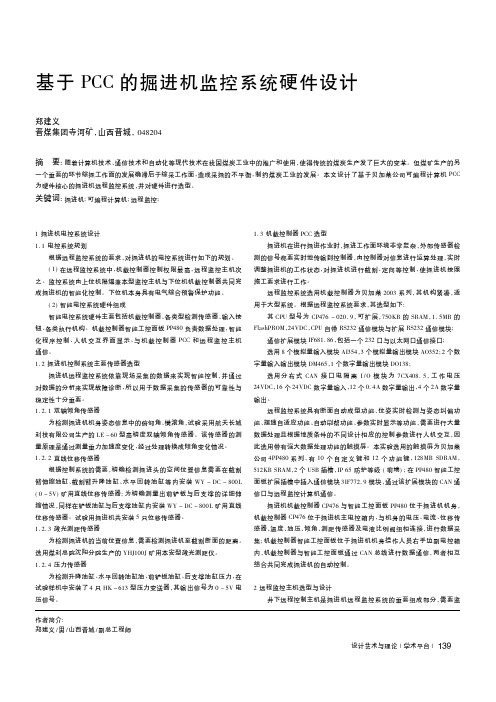
设计艺术与理论|学术平台|139作者简介:郑建义/男/山西晋城/副总工程师基于PCC 的掘进机监控系统硬件设计郑建义晋煤集团寺河矿,山西晋城,048204摘要:随着计算机技术、通信技术和自动化等现代技术在我国煤炭工业中的推广和使用,使得传统的煤炭生产发了巨大的变革。
但煤矿生产的另一个重要的环节综掘工作面的发展确滞后于综采工作面,造成采掘的不平衡,制约煤炭工业的发展。
本文设计了基于贝加莱公司可编程计算机PCC 为硬件核心的掘进机远程监控系统,并对硬件进行选型。
关键词:掘进机;可编程计算机;远程监控;1掘进机电控系统设计1.1电控系统规划根据远程监控系统的要求,对掘进机的电控系统进行如下的规划。
(1)在远程监控系统中,机载控制器控制权限最高,远程监控主机次之。
监控系统由上位机隔爆兼本型监控主机与下位机机载控制器共同完成掘进机的智能化控制。
下位机本身具有电气综合预警保护功能。
(2)智能电控系统硬件组成智能电控系统硬件主要包括机载控制器、各类型检测传感器、输入按钮、各类执行机构。
机载控制器智能工控面板PP480负责数据处理,智能化程序控制、人机交互界面显示、与机载控制器PCC 和远程监控主机通信。
1.2掘进机控制系统主要传感器选型掘进机远程监控系统依靠现场采集的数据来实现智能控制,并通过对数据的分析来实现故障诊断,所以用于数据采集的传感器的可靠性与稳定性十分重要。
1.2.1双轴倾角传感器为检测掘进机机身姿态信息中的俯仰角、横滚角,试验采用航天长城科技有限公司生产的LE -60型高精度双轴倾角传感器。
该传感器的测量原理是通过测量重力加速度变化,经过处理转换成倾角变化情况。
1.2.2直线位移传感器根据控制系统的需要,精确检测掘进头的空间位置信息需要在截割臂伸缩油缸、截割臂升降油缸、水平回转油缸等内安装WY -DC -800L (0-5V )矿用直线位移传感器;为精确测量出前铲板与后支撑的详细伸缩情况,同样在铲板油缸与后支撑油缸内安装WY -DC -800L 矿用直线位移传感器。
智能化技术在掘进机中的应用分析及发展
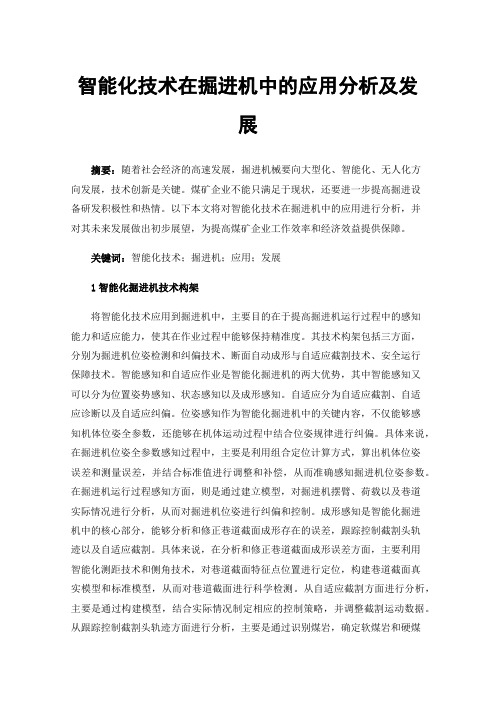
智能化技术在掘进机中的应用分析及发展摘要:随着社会经济的高速发展,掘进机械要向大型化、智能化、无人化方向发展,技术创新是关键。
煤矿企业不能只满足于现状,还要进一步提高掘进设备研发积极性和热情。
以下本文将对智能化技术在掘进机中的应用进行分析,并对其未来发展做出初步展望,为提高煤矿企业工作效率和经济效益提供保障。
关键词:智能化技术;掘进机;应用;发展1智能化掘进机技术构架将智能化技术应用到掘进机中,主要目的在于提高掘进机运行过程中的感知能力和适应能力,使其在作业过程中能够保持精准度。
其技术构架包括三方面,分别为掘进机位姿检测和纠偏技术、断面自动成形与自适应截割技术、安全运行保障技术。
智能感知和自适应作业是智能化掘进机的两大优势,其中智能感知又可以分为位置姿势感知、状态感知以及成形感知。
自适应分为自适应截割、自适应诊断以及自适应纠偏。
位姿感知作为智能化掘进机中的关键内容,不仅能够感知机体位姿全参数,还能够在机体运动过程中结合位姿规律进行纠偏。
具体来说,在掘进机位姿全参数感知过程中,主要是利用组合定位计算方式,算出机体位姿误差和测量误差,并结合标准值进行调整和补偿,从而准确感知掘进机位姿参数。
在掘进机运行过程感知方面,则是通过建立模型,对掘进机摆臂、荷载以及巷道实际情况进行分析,从而对掘进机位姿进行纠偏和控制。
成形感知是智能化掘进机中的核心部分,能够分析和修正巷道截面成形存在的误差,跟踪控制截割头轨迹以及自适应截割。
具体来说,在分析和修正巷道截面成形误差方面,主要利用智能化测距技术和侧角技术,对巷道截面特征点位置进行定位,构建巷道截面真实模型和标准模型,从而对巷道截面进行科学检测。
从自适应截割方面进行分析,主要是通过构建模型,结合实际情况制定相应的控制策略,并调整截割运动数据。
从跟踪控制截割头轨迹方面进行分析,主要是通过识别煤岩,确定软煤岩和硬煤岩,并确定煤岩切割路径,调整掘进机运行轨迹和控制策略,保证巷道截面自动成形。
隧道掘进爆破设计智能系统研究

3、降低施工成本和风险
智能系统的应用能够降低人工设计和操作成本,提高工作效率。智能系统的 精确计算和控制,能够减少炸药用量和浪费,降低施工成本。此外,智能系统能 够精确计算安全距离,提高施工安全性,降低风险。
参考内容
引言
岩石隧道掘进机是一种广泛应用于岩石隧道施工的重要设备,其性能和效率 直接影响到隧道施工的进度和质量。刀盘是岩石隧道掘进机的关键部件之一,其 设计方法的研究对于提高掘进机的整体性能具有重要意义。本次演示将围绕岩石 隧道掘进机刀盘设计方法展开讨论,旨在为掘进机的优化设计和应用提供理论支 持和实践指导。
4、系统整合
智能系统需要实现各硬件设备和软件模块的有机整合,确保系统的稳定性和 高效性。系统整合应考虑各个设备之间的数据传输格式和通讯协议,以及软件模 块之间的接口标准和技术实现方式。通过合理的系统整合,能够提高智能系统的 整体性能和可靠性。
三、爆破设计优化
利用智能系统进行隧道掘进爆破设计的优化,主要包括炸药选择、爆炸效应 控制和安全距离计算等方面。
3、安全距离计算
智能系统能够根据隧道施工安全标准和炸药性能参数,精确计算出爆破作业 的安全距离。通过智能系统的计算,能够确保施工人员和设备在安全范围内进行 作业,提高施工安全性。
四、实际应用与效果
隧道掘进爆破设计智能系统在多项隧道工程中得到了应用,并取得了良好的 效果。在实际工程中,智能系统的应用提高了施工进度和工程质量,同时降低了 施工成本和风险。具体效果如下:
2、硬件设备
隧道掘进爆破设计智能系统主要包括高性能计算机、高清摄像头、无人机等 硬件设备。这些设备能够实现对隧道地质信息的快速采集和处理,提高数据处理 效率。
3、软件设计
智能系统的软件设计是关键环节,主要包括数据采集、处理、分析和存储等 功能。软件设计应采用先进的数据分析和机器学习算法,实现对地质信息的智能 化识别和处理。此外,软件设计还应具备良好的用户界面,方便用户进行数据输 入和结果查看。
掘进机维护保养

EBZ悬臂式纵轴掘进机维护保养三一重型装备有限公司维护保养日常的检查和维修,是为了及时地消除事故的隐患,使机器设备能充分发挥作用,能尽早发现机器各部的异常现象,并采取相应的处理措施是非常重要的。
1.日常检查(即每天工作前检查内容)检查下述各项有无异常现象,并请参照其各部的构造说明及调整方法。
煤尘和水对油脂的清洁度是有直接影响的,应慎重保管和使用其油脂。
特别是对液压系统更应十分注意,避免因粉尘或水的混入而造成液压系统的故障。
3.1 液压系统用油造成液压系统故障的原因,其中70%是由于液压油管理不善,因此,如能充分的注意管理,则可减少液压系统内故障的发生。
有关液压油的管理,务必注意如下各点:3.1.1防止杂物混入液压油内。
3.1.2当发现油质不良时,应尽快更换新油。
3.1.3按规定更换过滤器。
3.1.4保证油箱内所规定的油量。
3.1.5油冷却器内有足够的冷却水通过,以防止油温的异常上升。
3.2 液压系统用油的选定标准所用液压油,必须是适合于高压系统的油类,要选用具有耐磨耗性、抗氧化性、润滑性等特性良好的油类。
当使用环境不低于-5℃时,作为所选用的液压油应该是抗磨液压油或极压抗磨液压油YB-N68。
其质量指标如下:运动粘度:37~43mm2/S(50℃)凝点:≤-25℃粘度指数:≥903.3 液压油的检查按规定的时间(一个月)从油箱内抽取约一升的油样,注入清洁的试管内(数个试管),在分别保管十天后和一个月后与新油相比较,观察其颜色、透明度、杂物的混入程度及沉淀物等的外观检查,再用滤纸过滤液压油,滤出其不纯物。
更严格的检查,则是依据厂家的标准,对粘度、抗氧化、水分的含量、沉淀物、色相、比重、闪点进行检查。
根据检查结果及抽取油样的时间,来决定更换液压油的时间,则更为有利。
3.4 减速机用润滑油的选定标准润滑油对减速机的使用寿命及效率起着重要的作用。
使用润滑油的目的,一方面是向齿轮副、轴承等磨擦表面提供润滑剂,降低磨擦,另一方面又起到散热作用。
针对掘进机故障分析的智能分析系统构建

针对掘进机故障分析的智能分析系统构建作者:李开渊来源:《今日财富》2017年第31期当前,各类机械的信息化水平不断提升,在掘进机械中,使用了更多高效的控制方式及信息化手段,还应用了液压系统,使煤炭开采效率明显提高,事实上,这些增加了掘进机的检修及维护难度。
掘进机的动力,全部来自于内部的电气系统,而液压系统使其具有更强劲的动力。
这两大系统是掘进机的主体部分,故障率也非常高。
专家系统属于计算机程序系统,内部具有很多专业性知识。
它在一定程度上能取代专家角色,具有专家逻辑思维,按照专家的思路来解决某个专门性问题,并全面介紹故障解决方案的内容。
在检修掘进机时,采用该系统,则现场人员技术水平及主观因素,都不会对其产生影响,有利于更快速、高效检修机械,排除故障。
该文对掘进机经常出现的问题进行了研究,在此基础上设计出专家系统,能对现场工作提供强有力的支持,实现生产率的全面提升。
一、掘进机常见故障及分析(一)电气系统常见故障及分析1.PLC不存在输出。
有多种原因会导致这一故障,例如综合保护器出现问题、控制键失效以及线路接线错误等,都会引发这类故障。
在确定PLC有没有输出的时候,可使用状态显示灯,当它发亮时,代表存在输出,如果发暗则代表没有输出。
当PLC不存在输出的时候,要对其状态显示灯进行观察,在此基础上对回路输入状况进行确定,从而找出导致故障的因素。
除此之外,可将输入端进行短接,来判断PLC的输入端是不是已受损。
2.接触器线圈及继电器线圈无法导通。
接触器线圈无法导通的原因为:①接触线圈被烧坏;②未接入交流电源;③继电器受损,不能正常使用。
可使用万用表,来检测上述三类故障。
继电器线圈回路无法导通,其原因为:①继电器线圈被烧坏;②未接入直流电源;③PLC不存在输出。
检测前两个故障原因,可使用万用表,而判断第三个,要对PLC输出端发光管进行观察。
3.接触器不能有效吸合及漏电闭锁不能实现检测。
前一故障的原因是,系统的电压比较低。
悬臂式掘进机智能控制系统关键技术
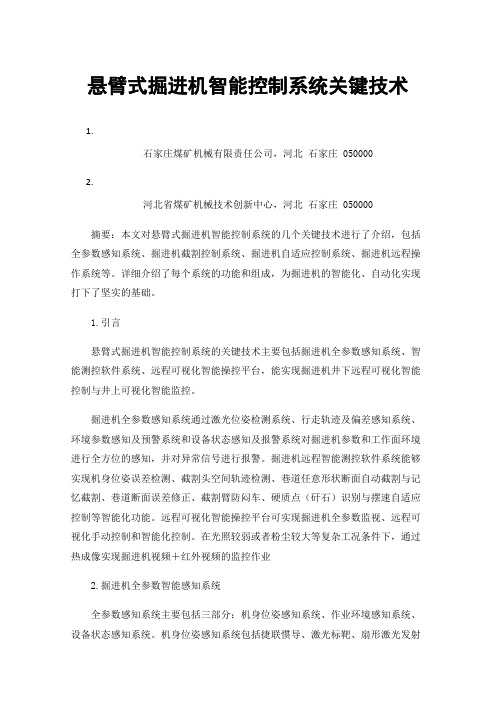
悬臂式掘进机智能控制系统关键技术1.石家庄煤矿机械有限责任公司,河北石家庄 050000 2.河北省煤矿机械技术创新中心,河北石家庄 050000摘要:本文对悬臂式掘进机智能控制系统的几个关键技术进行了介绍,包括全参数感知系统、掘进机截割控制系统、掘进机自适应控制系统、掘进机远程操作系统等。
详细介绍了每个系统的功能和组成,为掘进机的智能化、自动化实现打下了坚实的基础。
1.引言悬臂式掘进机智能控制系统的关键技术主要包括掘进机全参数感知系统、智能测控软件系统、远程可视化智能操控平台,能实现掘进机井下远程可视化智能控制与井上可视化智能监控。
掘进机全参数感知系统通过激光位姿检测系统、行走轨迹及偏差感知系统、环境参数感知及预警系统和设备状态感知及报警系统对掘进机参数和工作面环境进行全方位的感知,并对异常信号进行报警。
掘进机远程智能测控软件系统能够实现机身位姿误差检测、截割头空间轨迹检测、巷道任意形状断面自动截割与记忆截割、巷道断面误差修正、截割臂防闷车、硬质点(矸石)识别与摆速自适应控制等智能化功能。
远程可视化智能操控平台可实现掘进机全参数监视、远程可视化手动控制和智能化控制。
在光照较弱或者粉尘较大等复杂工况条件下,通过热成像实现掘进机视频+红外视频的监控作业2.掘进机全参数智能感知系统全参数感知系统主要包括三部分:机身位姿感知系统、作业环境感知系统、设备状态感知系统。
机身位姿感知系统包括捷联惯导、激光标靶、扇形激光发射器、二维里程检测装置、激光测距仪等。
作业环境感知系统包括防爆摄像仪、热成像仪、毫米波雷达、粉尘传感器等。
设备状态感知系统包括振动传感器、液压油温传感器、流量传感器、位移传感器、电流传感器、电压变送器、智能控制器等机身位姿感知系统能采集掘进机机身在巷道内的位置、方向、姿态,实时显示掘进机的行走轨迹与偏向角、偏距、俯仰角、横滚角、车前距5个掘进机机身位姿参数,准确反映掘进机实际掘进方向与巷道设计中线的偏离情况。
煤矿井下掘进机械的设计和优化研究

煤矿井下掘进机械的设计和优化研究摘要:本研究对煤矿井下掘进机械的设计和优化进行研究,旨在提高掘进机械的效率和安全性。
通过分析掘进机械的工作原理和现有设计,提出了一种基于优化的设计方法,结合了机械设计原理和先进的数值模拟技术。
在此基础上,通过实验验证和性能评估,验证了优化设计的有效性。
研究结果表明,优化设计能够显著提升掘进机械的工作效率和可靠性,对煤矿井下掘进作业具有重要意义。
关键词:煤矿井下;掘进机械;设计;优化;效率;安全性1 引言煤矿井下掘进机械是煤矿开采过程中不可或缺的关键设备。
它们承担着掘进工作、煤炭采取和岩石开采等重要任务,掘进机械的设计和优化对煤矿的安全和生产效率有着重要的影响。
目前,虽然有许多掘进机械的设计方案,但仍存在一些问题和挑战。
一方面,传统的设计方法往往依赖于经验和直觉,缺乏系统性和科学性。
另一方面,井下环境的复杂性和恶劣性增加了掘进机械的运行风险。
因此,本研究对煤矿井下掘进机械的设计和优化方法进行研究,从而提高其工作效率和安全性。
2 煤矿井下掘进机械的工作原理煤矿井下掘进机械是一种用于开采煤炭和岩石的重要设备,其工作原理基于切削和破碎的原理。
掘进机械通过切削或破碎工具,如刀盘、钻头或锤头,对煤炭或岩石进行切削、破碎和分离。
在工作过程中,掘进机械首先通过驱动系统提供动力,使刀盘、钻头或锤头旋转或往复运动。
刀盘或钻头上的切削工具通过旋转或冲击的方式切削或破碎岩石或煤炭。
随着切削或破碎的进行,岩石或煤炭被分离出来,并被传送到后续的运输设备或储存区域。
掘进机械的工作原理涉及多个关键部件和系统。
除了驱动系统和切削工具,还包括供应系统、控制系统和传感器系统。
供应系统负责提供所需的液压或气压能源,以驱动切削工具和其他运动部件。
控制系统通过对驱动系统、切削工具和传感器系统的控制,实现对掘进机械的运行和工作参数的调节和控制。
传感器系统则用于监测和收集关于掘进机械的工作状态、运行参数和环境条件的数据。
浅谈煤矿掘进设备电气系统的控制与维护
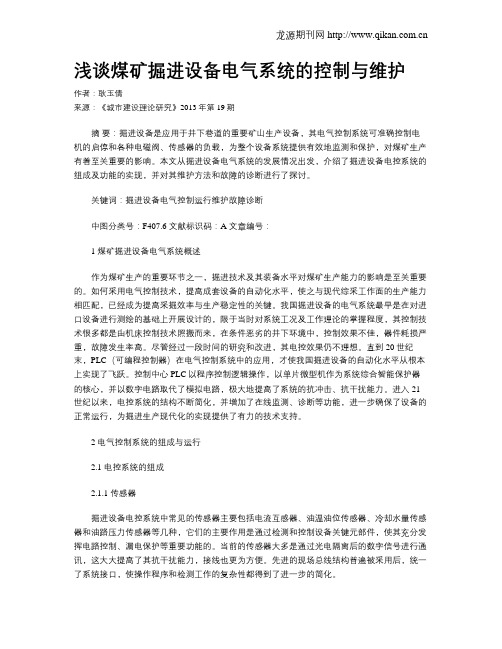
浅谈煤矿掘进设备电气系统的控制与维护作者:耿玉倩来源:《城市建设理论研究》2013年第19期摘要:掘进设备是应用于井下巷道的重要矿山生产设备,其电气控制系统可准确控制电机的启停和各种电磁阀、传感器的负载,为整个设备系统提供有效地监测和保护,对煤矿生产有着至关重要的影响。
本文从掘进设备电气系统的发展情况出发,介绍了掘进设备电控系统的组成及功能的实现,并对其维护方法和故障的诊断进行了探讨。
关键词:掘进设备电气控制运行维护故障诊断中图分类号:F407.6 文献标识码:A 文章编号:1 煤矿掘进设备电气系统概述作为煤矿生产的重要环节之一,掘进技术及其装备水平对煤矿生产能力的影响是至关重要的。
如何采用电气控制技术,提高成套设备的自动化水平,使之与现代综采工作面的生产能力相匹配,已经成为提高采掘效率与生产稳定性的关键。
我国掘进设备的电气系统最早是在对进口设备进行测绘的基础上开展设计的,限于当时对系统工况及工作理论的掌握程度,其控制技术很多都是由机床控制技术照搬而来,在条件恶劣的井下环境中,控制效果不佳,器件耗损严重,故障发生率高。
尽管经过一段时间的研究和改进,其电控效果仍不理想。
直到20世纪末,PLC(可编程控制器)在电气控制系统中的应用,才使我国掘进设备的自动化水平从根本上实现了飞跃。
控制中心PLC以程序控制逻辑操作,以单片微型机作为系统综合智能保护器的核心,并以数字电路取代了模拟电路,极大地提高了系统的抗冲击、抗干扰能力。
进入21世纪以来,电控系统的结构不断简化,并增加了在线监测、诊断等功能,进一步确保了设备的正常运行,为掘进生产现代化的实现提供了有力的技术支持。
2 电气控制系统的组成与运行2.1 电控系统的组成2.1.1 传感器掘进设备电控系统中常见的传感器主要包括电流互感器、油温油位传感器、冷却水量传感器和油路压力传感器等几种,它们的主要作用是通过检测和控制设备关键元部件,使其充分发挥电路控制、漏电保护等重要功能的。
煤矿智能化掘进远程控制系统建设与应用

煤矿智能化掘进远程控制系统建设与应用摘要:煤炭是我国的主要资源之一,综掘是提升巷道掘进效率、降低劳动强度以及缓解采掘接替紧张问题的主要途径之一,但是受掘进工艺制约,综掘工作面往往面临粉尘浓度高、噪音大等问题,作业人员长时间在这种恶劣环境中工作,会给身体健康带来一定威胁。
巷道掘进涉及煤岩开挖、煤矸运输、支护等多个环节,通过综掘、带式输送机及锚杆钻机等配合,各环节虽然基本实现了机械化操作,但是普遍面临自动化程度低、效率不高等问题。
关键词:掘进机;远程控制;智能化引言智能化煤矿掘进工作面人的不安全行为影响因素又包含若干二级影响因素,并对各个影响因素进行了问卷调查。
运用层次分析法分析了一级影响因素,得出个体因素影响程度最大,其次是环境因素。
运用熵权法研究了各个一级影响因素下的二级影响因素的影响权重。
因此,煤矿行业应该根据具体的发展状况,选择科学、合理的技术对综合机械化掘进系统进行智能化建设,使掘进设备具备更加完善的功能,进一步提升掘进效果,保障掘进工作的顺利开展。
1煤矿智能化开采的定义和应用价值煤矿智能化开采是对矿山资源、生产人员、材料设备、外部环境等进行数字化,实现煤矿生产过程中一切信息可以自动采集、实时传输、全程可视、标准运行、自动操作等,使得煤矿生产可以像智能机器一样实现自我识别并进行决策,实现生产系统高效运营,降低企业运营成本,提高生产效益。
这种将煤矿现有生产方式转化成高度网络集成化、数据智能化的生产方式越来越受到煤矿生产企业的重视,成为煤炭产业发展的趋势所在,煤矿智能化开采核心在于采用高新技术和装备,解决煤矿生产、经营问题。
煤矿智能化开采是高新技术与煤炭工业的深度融合,取代井下生产工人的各种作业行为,达到煤矿减人、高效生产的目的。
煤矿智能化开采是新一轮产业变革的产物,是经济社会发展的必然业态,代表了煤矿新的发展方向,开创了煤矿生产新的发展格局,推动了煤矿企业高质量发展。
煤矿智能化开采从根本上改变了煤矿传统的以人为主的生产方式,促进煤矿生产由劳动力密集型向人才技术密集型转变,促进煤矿企业效益提升,确保煤矿企业生产安全。
掘进工作面智能化掘进机关键技术与应用
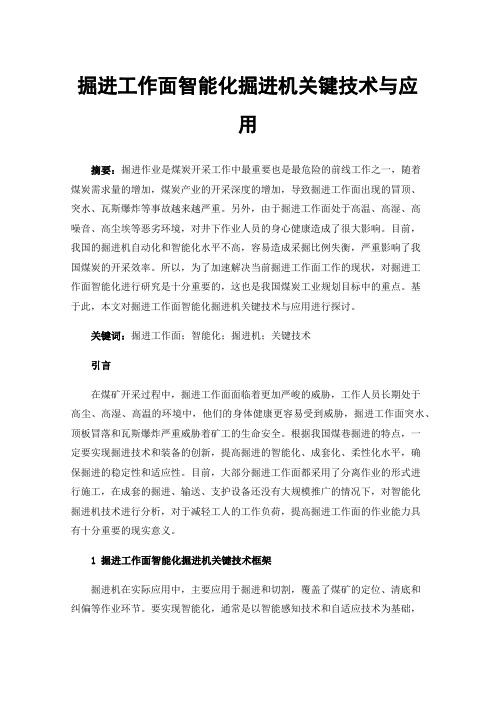
掘进工作面智能化掘进机关键技术与应用摘要:掘进作业是煤炭开采工作中最重要也是最危险的前线工作之一,随着煤炭需求量的增加,煤炭产业的开采深度的增加,导致掘进工作面出现的冒顶、突水、瓦斯爆炸等事故越来越严重。
另外,由于掘进工作面处于高温、高湿、高噪音、高尘埃等恶劣环境,对井下作业人员的身心健康造成了很大影响。
目前,我国的掘进机自动化和智能化水平不高,容易造成采掘比例失衡,严重影响了我国煤炭的开采效率。
所以,为了加速解决当前掘进工作面工作的现状,对掘进工作面智能化进行研究是十分重要的,这也是我国煤炭工业规划目标中的重点。
基于此,本文对掘进工作面智能化掘进机关键技术与应用进行探讨。
关键词:掘进工作面;智能化;掘进机;关键技术引言在煤矿开采过程中,掘进工作面面临着更加严峻的威胁,工作人员长期处于高尘、高湿、高温的环境中,他们的身体健康更容易受到威胁,掘进工作面突水、顶板冒落和瓦斯爆炸严重威胁着矿工的生命安全。
根据我国煤巷掘进的特点,一定要实现掘进技术和装备的创新,提高掘进的智能化、成套化、柔性化水平,确保掘进的稳定性和适应性。
目前,大部分掘进工作面都采用了分离作业的形式进行施工,在成套的掘进、输送、支护设备还没有大规模推广的情况下,对智能化掘进机技术进行分析,对于减轻工人的工作负荷,提高掘进工作面的作业能力具有十分重要的现实意义。
1掘进工作面智能化掘进机关键技术框架掘进机在实际应用中,主要应用于掘进和切割,覆盖了煤矿的定位、清底和纠偏等作业环节。
要实现智能化,通常是以智能感知技术和自适应技术为基础,对掘进工作面进行自动处理[1]。
其中,智能传感主要用于状态和位姿的测量,而自适应则主要用于校正和诊断。
首先,位姿感知是掘进机智能化转型的关键,如动态加载条件下的位姿修正、参数感知等。
在掘进机的位姿参数感应处理中,以组合定位算法为基础,通过对计算和测量的位姿误差进行对比,完成对其进行补正调整,进而确保位姿状态的正确性。
煤矿智能化掘进系统的应用与研究

煤矿智能化掘进系统的应用与研究摘要:改革后,随着智能化矿井建设的发展需要,掘进工作面的机械化程度和技术装备水平与综采机械化的程度相比,差距很大,严重制约了矿井的安全、高效发展。
因此,研究智能掘进的远程控制、在线监测以及自适应截割等技术及应用,对实现“无人则安、人少则安”具有重要的意义,也是满足现代化矿井发展的必然要求。
关键词:掘进机;智能化;远程控制引言在我国的能源结构体系中,煤炭资源占据绝对核心的地位。
为顺应社会经济发展,我国每年会开采大量煤炭资源,以供人们基本生活和工业生产需要。
煤矿开采中掘进机是非常核心和关键的机电装备,其自动化和智能化水平会对煤矿开采过程产生非常重要的影响,通常掘进机的智能化水平越高则煤矿开采效率越高。
近年来,我国在煤矿领域的技术水平虽然得到了很大的提升和发展,但不得不承认,与发达国家相比较,我国在掘进机的自动化和智能化水平上仍然存在很大差距,导致设备性能无法得到充分发挥。
所以如何提升掘进机的智能化水平是当前我国煤矿领域研究的热点问题。
但由于设备智能化控制涉及很多方面的内容,比如机身自主定位、自动截割成型及其控制等,所以在智能化建设方面仍然有很大的提升空间。
本文主要以煤矿中经常使用的悬臂式掘进机为对象,从机身定位、定向以及截割定形层面,对智能化控制技术进行研究,将其应用到工程实践中取得了理想的效果,对于提升掘进机的智能化水平具有一定的现实意义。
1煤矿巷道掘进机智能化关键技术框架巷道掘进机的工作内容通常包含掘进、摆动截割、后退收煤等,涉及纠偏、定位、截割、扫底、收煤等工艺环节。
巷道掘进机的智能化需要利用智能感知技术和自适应技术来达到巷道断面自动成形的目的。
其中,智能感知包含位姿感知、成形感知及状态感知等,自适应作业包含自适应的纠偏、诊断、截割等。
位姿感知是巷道掘进机实现智能化的重点,如机体位姿全参数智能感应、动态荷载下的位姿纠偏等。
在机体位姿全参数智能感应中,需要分析组合定位算法,针对捷联惯导系统位姿计算误差与测量误差进行补正,从而保证位姿参数的准确性。
煤矿掘进工作面自动化智能化改造

煤矿掘进工作面自动化智能化改造摘要:为解决煤矿掘进工作面复杂环境下的安全生产问题,研究了煤矿掘进工作面自动化智能化改造技术路线,并对改造过程中的关键技术进行了分析。
根据实际情况,设计了一套自动化、智能化掘进工作面设备系统。
该系统主要由智能运输系统、智能供电系统等组成。
掘进工作面的自动化智能化改造,实现了煤矿安全生产从“被动”到“主动”的转变,提高了煤矿企业的综合效益。
关键词:煤矿掘进;自动化;智能化1.引言近年来,随着煤炭开采强度的不断加大,矿井开采深度也不断增加,地质条件更加复杂,尤其是煤矿巷道掘进工作面,受地质条件和设备技术条件限制,传统的人工掘进方式已不能满足安全生产需要,且对掘进工作面的人员及设备管理带来极大挑战。
随着智能制造技术的发展及国家对煤矿安全生产的重视程度不断提高,一些煤矿企业已经开始探索从自动化智能化的角度进行开采工作,并取得了一定进展。
2.掘进工作自动化发展现状与改进方向2.1掘进工作自动化发展现状我国煤矿开采行业经过几十年的发展,已经逐步进入到了现代化、自动化和智能化开采的阶段,掘进工作自动化程度已经有了较为明显的提升。
我国煤矿开采行业对于掘进工作进行了大量研究,研发出了一系列不同类型的自动化设备,在掘进机、装岩机、运料车等方面进行了大量研究和应用[1]。
2.2掘进工作自动化改进方向针对上述掘进工作自动化存在的问题,提出改进方向如下:第一,通过网络技术和数字通信技术,构建基于工业以太网的巷道远程控制系统,实现对掘进机、运巷、回风巷道和转载巷道的远程控制。
该系统利用网络技术和数字通信技术将巷道中各个部分联系起来,实现信息互通,将信息采集、传输、处理及反馈等各个环节相互协调,提高煤矿掘进工作自动化水平。
第二,开发基于煤矿井下传感器的巷道环境监测系统,利用井下传感系统对巷道环境进行实时监测,分析巷道环境变化与监测结果,为掘进工作面的自动化改造提供依据,避免因巷道环境因素对掘进工作造成影响。
EBZ220型掘进机使用维护说明书
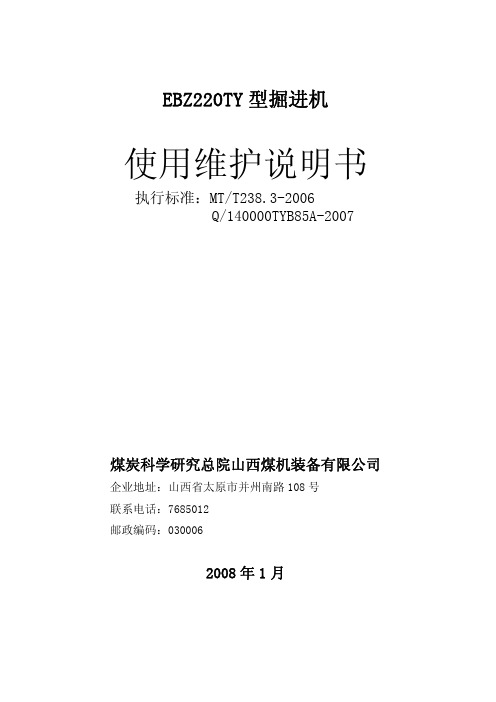
2.6 液压系统
系统额定压力:
油缸回路
25MPa
行走回路
25MPa
装载回路
25MPa
输送机回路
25MPa
系统总流量:
520 L/min
泵站功率
132kw
两联柱塞泵转速
1485 r/min
两联柱塞泵流量
270/80 ml/r
油箱
有效容积
960L
冷却方式 板翅式水冷却器和蛇形管冷却
油缸数量:
8个
多路换向阀的调定压力
1140/660V
额定功率
3kW
防爆等级
H级
转速
1470r/min
G.矿用隔爆型掘进机械防震灯
型号 防爆型式 额定电压 功率 H.瓦斯传感器 型号 防爆型式 电压 I.瓦斯断电仪 型号 防爆型式 电压 J.矿用隔爆型蜂鸣器 型号 防爆型式 额定电压 K.矿用隔爆型控制按钮 型号 防爆型式
DGE20/24B ExdⅠ 24V 20w
主要技术参数21总体参数250mm切割卧底深度200mm龙门高度400mm接地比压0159mpa355kw可经济切割煤岩硬度90mpa可掘巷道断面1028最大可掘高度4835m最大可掘宽度596m适应巷道坡度16机器供电电压1140v牵引力310kn生产能力373mmin22切割机构截割型式纵轴截割功率220160kw截齿形式截齿数量306532rmin32233847365nm最大摆动角度28左右各36平均单刀力5496799423装载机构装载形式三爪星轮液压马达驱动液压马达形式低速大扭矩液压马达液压马达工作压力25mpa液压马达排量2010mlmin液压马达转速40rmin装运能力300铲板宽度30m铲板卧底250mm铲板抬起580mm星轮转速45rmin24运输机构运输形式边双链刮板液压马达驱动液压马达形式低速大扭矩液压马达液压马达工作压力25mpa液压马达排量450mlmin液压马达转速110rmin610mm龙门高度400mm12ms锚链规格1864mm张紧形式黄油缸张紧25行走机构行走形式履带式液压马达分别驱动液压马达形式斜轴式轴向柱塞马达液压马达工作压力25mpa液压马达排量107mlmin行走速度09mmin接地长度32m制动形式摩擦离合器履带板宽度600mm张紧形式黄油缸张紧26液压系统系统额定压力
掘进机智能控制系统的设计与维护

第1期(总第212期)2019年2月机械工程与自动化M E C HA N I C A L ㊀E N G I N E E R I N G㊀&㊀A U T OMA T I O NN o .1F e b .文章编号:1672G6413(2019)01G0208G02掘进机智能控制系统的设计与维护闫㊀肃(山西西山晋兴能源有限责任公司斜沟煤矿,山西㊀兴县㊀033602)摘要:煤矿掘进机的工作环境比较复杂,为使其具有较强的安全性和抗干扰性,设计了一种全新的P L C 控制系统,其中的关键控制器使用S 7G200P L C .介绍了P L C 系统的硬件组成和程序设计流程,并说明了系统维护也是P L C 控制系统设计过程中必要考虑因素.该控制系统具有灵活方便㊁安全可靠㊁自动化程度高等优点,对于矿井下同类型设备的设计具有一定的借鉴意义.关键词:掘进机;控制系统;P L C ;系统维护中图分类号:T D 63+2 2㊀㊀㊀文献标识码:B收稿日期:2018G06G08;修订日期:2018G12G08作者简介:闫肃(1988G),男,山西太原人,大专,从事矿山机电方面的工作.0㊀引言近年来随着煤炭事业的发展,掘进机已经成为煤矿现场工作的必要设备,为了确保掘进机可以在煤矿生产中正常工作,需要进一步设计完善掘进机控制系统的结构和功能,以满足复杂工作环境的各种要求,使其具有环境适应性㊁安全可靠性以及较强的抗干扰性.传统的煤矿掘进机控制系统使用继电器构造,自动化程度低㊁维护困难,难以满足现代化工业4.0的需求.西门子的S 7G200P L C 与其他控制器相比具有接线比较简单㊁编程比较方便㊁安全可靠度高㊁抗干扰性强㊁系统维护方便等优点,采用P L C 可以有效地提高掘进机的实际生产效率,满足煤矿现代化发展需求[1].1㊀掘进机控制要求掘进机控制系统主要包括电机控制㊁P L C 控制㊁显示和保护回路4部分,该控制系统的供电电压为50H z 的交流电压,可以控制掘进机电机的启停及正反转,起到保护电机的作用[2].型号为E B Z 150A 的掘进机在实际生产过程中要实现转载㊁切割和走行等,其中每一个动作都需要相应的电机配合,以满足实际生产的要求.掘进机的具体工作流程为:①前期准备,清除工作现场的无关人员;②启动油泵电机,当油泵油压恒定后会预警切割动作并启动电磁阀;③启动低速和高速截割电机.而掘进机的停机顺序恰好相反,图1为掘进机各电机的具体启动流程.掘进机控制系统应具备如下功能:①漏电检测功能,检测油泵电机和截割电机(低速和高速)等的漏电情况,若有漏电情况发生,会立即启动报警信号;②保护功能,以防各电机过流㊁过载和超温.该控制系统中的P L C 控制程序主要控制油泵和截割电机之间的启动顺序以及低速和高速截割电机之间的互锁;与此同时,该控制系统还设置了急停控制按钮,以便当意外发生时能立即进行停机操作从而起到保护作用.图1㊀掘进机电机启动流程图2㊀掘进机P L C 控制系统设计2.1㊀系统硬件设计掘进机控制系统的硬件包括开关按钮㊁声光报警装置以及功能指示灯等,由于C P U 226模块扩展具有强大的内置功能和灵活的系统配置,故可选择其作为P L C 控制器的处理器.除此之外,为了以后系统的扩展性,在该系统的基础上又分别添加了一个模拟量模块和数字量模块,型号分别为E M 222和E M 231.S 7G200P L C 分别与HM I 人机界面和安装有昆仑通泰组态软件的上位机连接,其功能是使系统具有更加优秀的人机交互功能,降低工人的操作难度,使工作画面更加具体化.其中监控系统能够根据现场情况判断故障,并采取一定的报警措施,可以根据颜色的不同来提示不同等级的故障,通过报警信息工人能够及时地判别出故障的类型以及发生故障的区域,便于及时对设备进行维护和修理,极大地提高了工作效率[3].2.2㊀程序设计P L C 程序设计工作流程如图2所示.从图2中可知掘进机控制系统的具体工作过程为:首先掘进机进行准备工作,系统自查,若一切正常,则可闭合控制系统电源的开关,并进行启动前的预警操作,预警3s 以后便可以对控制油泵的电机进行启动,只有掘进机液压系统的油压保持稳定后才可进行切割预警操作,当延续时长为5s 以后,可以进行切割低速电机的启动操作,再5s 之后可以进行切割高速电机的启动.图2㊀程序设计流程2.3㊀安全性与抗干扰设计由于现场工作环境的复杂性,加强掘进机在安全性能和抗干扰性能方面的设计具有重大意义.掘进机控制系统中的电动机㊁接触器㊁隔离开关等电器元件放置于掘进机的电控箱内,因此电控箱在设计时不仅需要满足尺寸要求,还应该考虑其在结构设计方面的安全性能,使其具有隔爆功能.同时为了确保电控箱柜门的盖子开启之前电路处于开路状态,在电控箱的前门和外壳之间设计了一种机械闭锁装置,同时需要保证电控箱柜门关闭之后机械闭锁解除.除此以外,还需要对控制系统进行防震设计,例如在控制电机上面安装防震垫.为了保证掘进机能够安全无干扰地工作,除了电控箱的隔爆设计以及控制系统的防震设计外,掘进机的P L C 控制系统也需进行相关设计以避免电磁干扰,具体操作有:①对P L C 控制系统进行单独供电设计;②P L C控制系统的信号线与其他动力线独立走线;③P L C 控制系统安装时使用金属柜屏蔽外部电磁干扰[4].3㊀系统维护3.1㊀控制系统维护掘进机控制系统中的电气元件和电缆在工作时很容易被破坏,因此对该控制系统进行定期维护很有必要,具体包括以下两个方面:①各电气元件的检查,首先测试控制系统各接线㊁接触器接点㊁熔断器是否完好;接着测试控制系统照明灯在现场工作中是否正常并同时检查蜂鸣器能否报警;最后测试控制系统停止按钮的灵敏可靠度,并观察其能否进行紧急停机操作;②电缆的检查,首先检查电缆的悬挂和电缆的驰度是否满足实际生产要求并检查其在现场工作中有无滴水或淋水状况发生;接着检查电缆铠装在工作过程中是否被腐蚀,电缆是否接触到油脂类物质,导致电缆的绝缘层受到影响,还应检查电缆铠装承受压力的范围以及各接触点连接的稳定性.3.2㊀电动机的维护掘进机的电动机可以保证工作的正常完成,因此对于该控制系统中电机的定期维护十分重要,具体包括以下两个方面:①工作电压是否满足实际生产要求,电机温度升高是否正常;②检查电机连接件的稳定性和电机的绝缘性,并适时给电机补充润滑油[5].4㊀结语煤矿掘进机所处的工作环境比较恶劣,故应具有耐高温㊁耐腐蚀㊁防震隔爆㊁抗电磁干扰等特点,由于工作环境的复杂性导致掘进机控制系统的硬件㊁程序和安全性与抗干扰设计比较复杂.本文中的控制系统采用S 7G200P L C 控制器,该控制系统具有自动化程度高㊁安全可靠度高㊁智能化程度高等优点,有效地提高了掘进机现场工作的生产率.参考文献:[1]㊀朱文忠.基于P L C 的煤矿掘进机电控系统的可靠性设计与实现[J ].煤矿机械,2013,14(8):73G74.[2]㊀王辉,胡方海,金瓒.智能化技术在掘进机中的应用及发展趋势[J ].煤矿机械,2014,35(12):3G4.[3]㊀梁大海.双巷掘进中E M L 340型连续采煤机的工艺参数探讨[J ].煤炭科学技术,2010,38(5):100G103.[4]㊀刘美俊.西门子P L C 编程及应用[M ].北京:机械工业出版社,2013.[5]㊀唐仲延.连续采煤机掘进工艺研究[J ].煤,2015,24(5):50G51.D e s i g na n dM a i n t e n a n c e o f I n t e l l i g e n t C o n t r o l S ys t e mf o rR o a d h e a d e r Y A NS u(S h a n x i X i s h a n J i n x i n g E n e r g y C o .L t d .,X i e g o uC o a lM i n e ,X i n gx i a n033602,C h i n a )A b s t r a c t :C o a lm i n e r o a d h e a d e rw o r k s i n c o m pl i c a t e d e n v i r o n m e n t ,i n o r d e r t om a k e i tm o r e r o b u s t a n d r e s i s t a n t t o i n t e r f e r e n c e ,a n e wP L C c o n t r o l s y s t e m i s d e s i g n e d i n t h e a r t i c l e ,i nw h i c h t h e k e y c o n t r o l l e r u s e s t h e S 7G200P L C .T h e a r t i c l e i n t r o d u c e s t h e h a r d w a r e ,p r o gr a ma n d s t r u c t u r a l d e s i g n o f t h e P L Cs y s t e m ,a n d e x p l a i n s t h a t s y s t e m m a i n t e n a n c e i s a l s o a n e c e s s a r y c o n s i d e r a t i o n i n t h e d e s i gn p r o c e s s o f t h e P L C c o n t r o l s y s t e m.T h e c o n t r o l s y s t e mh a s t h e a d v a n t a g e s o f f l e x i b i l i t y a n d c o n v e n i e n c e ,s a f e t y a n d r e l i a b i l i t y ,a n d h i g h d e gr e e o f a u t o m a t i o n .I t i s o f p r a c t i c a l s i g n i f i c a n c e f o r t h e d e s i g n o f t h e c o n t r o l s ys t e mo f t h e r o a d h e a d e r .K e y wo r d s :r o a d h e a d e r ;c o n t r o l s y s t e m ;P L C ;s y s t e m m a i n t e n a n c e902 ㊀2019年第1期㊀㊀㊀㊀㊀㊀㊀㊀㊀㊀㊀㊀闫肃:掘进机智能控制系统的设计与维护。
- 1、下载文档前请自行甄别文档内容的完整性,平台不提供额外的编辑、内容补充、找答案等附加服务。
- 2、"仅部分预览"的文档,不可在线预览部分如存在完整性等问题,可反馈申请退款(可完整预览的文档不适用该条件!)。
- 3、如文档侵犯您的权益,请联系客服反馈,我们会尽快为您处理(人工客服工作时间:9:00-18:30)。
掘进机智能控制系统的设计与维护
摘要:近年来随着煤炭事业的发展,掘进机已经成为煤矿现场工作的必要设备,为
了确保掘进机可以在煤矿生产中正常工作,需要进一步设计完善掘进机控制系统的
结构和功能,以满足复杂工作环境的各种要求,使其具有环境适应性、安全可靠性
以及较强的抗干扰性。
传统的煤矿掘进机控制系统使用继电器构造,自动化程度低、维护困难,难以满足现代化工业4.0的需求。
西门子的S7-200PLC与其他控制器相
比具有接线比较简单、编程比较方便、安全可靠度高、抗干扰性强、系统维护方
便等优点,采用PLC可以有效地提高掘进机的实际生产效率,满足煤矿现代化发展
需求。
关键词:掘进机;智能控制系统;设计;维护
1关于控制系统设计问题的研究
首先根据某煤田地质情况以及本煤炭作业工作流程分析与研究,设计的掘进
机控制智能分析系统,必须达到智能化要求,能够实现智能化控制及数据显示功能,从而实现对整个作业流程和运转状况数据的监测和记录,先对掘进机的截割
过程进行分析,搭建断面数据尺寸同作业单位参数之间的数字模型,计算悬臂运
行转角的位置和液压缸位置以及截切头坐标三者之间的相关性。
控制软件表现出截割范围,并给监测系统传送相关数据及视频信息,这些视
频信息分为截切和运行等情况信息,可实现对掘进机的实时监测,从而满足截切
自动成型的要求。
结合地质环境特点把智能技术用于设备当中,以达到节约人力
和时间的目的。
为使系统进入适合的轨道,选用可视化智能监测系统可缩短设备运转时间,
降低能耗。
经过比较选用防爆三相电机和变频技术,经过单片机AVP控制整个截
切流程,并选用VB6.0程序在Window界面显示。
2关于掘进机相关智能设计的要求
控制掘进机系统主要由四部分构成:即PLC、电机、回路保护及显示部分。
该
系统电压是50Hz交流供电电压,能够满足电机进行启停工作及正反转,可以有
效保护电机。
EBZ150A型号的掘进机在进行截割、转载和运行等生产操作时都离
不开电机的支撑,该电机可充分满足工作需求。
掘进机操作一般流程分为:一是准备阶段,要做好工作场地不相关人员的清除
工作;二是启动阶段,当电机被启动后,油泵恒定电压预警引发自动切割后,这时
磁阀被启动;三是低速启动和电机高速截割。
控制掘进机软件系统的主要功能包括:一是漏电状况检测,主要负责对油泵及
电机截割进行漏电检测,如果发生漏电就会引发报警;二是功能保护,用于防止各
电机出现过流和超温、超载等情况。
该系统PLC主要负责对油泵和电机切割顺序
及高低速电机之间的切割互锁;另外,该系统设有急停按钮,确保发生意外时可以
迅速停机,达到保护设备的目的。
3PLC控制系统的设计
3.1硬件系统设计
掘进机系统控制硬件由指示各种功能的信号灯、报警用的声音报警、报警用
的光报警、按钮、开关等组成,由于西门子CPU226控制器能够进行各种功能扩展,灵活、方便,基本能够实现掘进机的智能化控制,所以,本设计采用西门子PLCS7-200的CPU226控制器作为控制核心。
另外,对CPU226进行了功能扩展,
增加了数字模块与模拟模块,分别是西门子Em231与Em222。
西门子S7-200将
与上位机电脑以及HMI触摸屏进行连接,从而达到人机进行交换的最为优秀的应
用系统,它降低了操作人员工作难度,HMI触摸屏更加直观、具体地反映掘进机
的工作状况,控制更加直观。
系统安全监控能够依据采集的现场信息数据进行判断,当出现故障或者危险时,及时发出报警,操作人员根据报警采集的信息能够
准确判断出故障部位及故障性质,这样有利于维修人员快速对故障进行维修,从
而大大提高了掘进机施工效率。
3.2程序控制设计
从中可以看出掘进机在进行智能改装后,其工作流程如下:首先要做掘进机
工作前的准备,进行自检系统以及相应元件检查,判断其是否存在故障,如果系
统元件存在故障,系统将发出故障报警,提醒操作人员处理故障。
当自检结果正
常时,控制人员将启动掘进机,此时掘进机进入准备工作,如果启动油泵电机,
掘进机将进行液压油升压工作,当系统液压稳定后掘进机才能够进行下一步的工作,5s后掘进机进入低速切割程序(启动低速切割电机),再过5s后掘进机进
入高速切割程序(启动高速切割电机)。
3.3抗干扰和安全性设计
由于掘进机施工环境非常复杂,增强、加大掘进机抗干扰及安全性的设计是
非常重要的。
在掘进机系统控制里,各种开换、继电器、PLC、显示器等电子、
电器元件,都安装于掘进机电控柜里,所以,设计的电控柜不仅要达到尺寸要求,在设计的结构上也要满足安全上的需要,必须具备一定的隔爆、防爆的能力。
另
外设计的电控柜,在开门时保证电路断电确保安全,在设计时安装开门传感器,
当开门前由于忘记或者别的原因没有断开控制柜电源,在打开控制柜门时自动断
开控制柜电源,当关闭控制柜门时又能自动接通电源,从而保证工作人员的安全。
另外,控制柜应设计防震装置,确保系统不会因为振动造成系统控制的误操作。
除此之外,掘进机为了能够确保工作时不受干扰,除上述设计采用的电控柜是防
震隔爆外,还有掘进机控制核心PLC程序控制器的选用必须也要具有抗电磁功能,其设计选用内容有:设计PLC程序控制器必须采用独立供电电源;PLC程序控制
器传输信号的线路不能与动力电源线路一起排列,防止交流频率影响信号参数;PLC硬件控制装置必须安装在金属控制柜内,这样可以屏蔽控制柜以外的电磁信号。
4系统维护
4.1控制系统维护
掘进机控制系统中的电气元件和电缆在工作时很容易被破坏,因此对该控制系
统进行定期维护很有必要,具体包括以下两个方面:(1)各电气元件的检查,首先测试
控制系统各接线、接触器接点、熔断器是否完好;接着测试控制系统照明灯在现场
工作中是否正常并同时检查蜂鸣器能否报警;最后测试控制系统停止按钮的灵敏可
靠度,并观察其能否进行紧急停机操作;(2)电缆的检查,首先检查电缆的悬挂和电缆
的驰度是否满足实际生产要求并检查其在现场工作中有无滴水或淋水状况发生;接
着检查电缆铠装在工作过程中是否被腐蚀,电缆是否接触到油脂类物质,导致电缆
的绝缘层受到影响,还应检查电缆铠装承受压力的范围以及各接触点连接的稳定性。
4.2电动机的维护
掘进机的电动机可以保证工作的正常完成,因此对于该控制系统中电机的定期
维护十分重要,具体包括以下两个方面:(1)工作电压是否满足实际生产要求,电机温
度升高是否正常;(2)检查电机连接件的稳定性和电机的绝缘性,并适时给电机补充
润滑油。
结论
煤矿掘进机所处的工作环境比较恶劣,故应具有耐高温、耐腐蚀、防震隔爆、抗电磁干扰等特点,由于工作环境的复杂性导致掘进机控制系统的硬件、程序和安全性与抗干扰设计比较复杂。
本文中的控制系统采用S7-200PLC控制器,该控制系统具有自动化程度高、安全可靠度高、智能化程度高等优点,有效地提高了掘进机现场工作的生产率。
参考文献:
[1]朱文忠.基于PLC的煤矿掘进机电控系统的可靠性设计与实现[J].煤矿机械,2019,14(8):73-74.
[2]王辉,胡方海,金瓒.智能化技术在掘进机中的应用及发展趋势[J].煤矿机
械,2019,35(12):3-4.
[3]梁大海.双巷掘进中EML340型连续采煤机的工艺参数探讨[J].煤炭科学技术,2019,38(5):100-103.。