除氟工艺
脱硫废水除氟方法简介及最新工艺推荐

脱硫废水除氟方法简介及最新工艺推荐燃煤电厂在使用燃煤发电的过程中会产生大量的硫氧化物(SOx),例如二氧化硫(SO2),为了去除烟气中的二氧化硫,燃煤电厂会使用排烟脱硫(FGD,FlueGasDesulfurization)设备,凭借抽取大量二价碱土金属工业用水与烟气中的含硫废气进行脱硫反应,再将经过“脱硫”反应后的含有硫酸根的酸性废水处理排放,以下简称为脱硫废水。
所述脱硫废水的成分,含有浓度大于20000mg/L,即20000ppm的硫酸根离子,浓度大于600ppm的氯离子,浓度介于50~200ppm之间的氟离子及浓度介于1000~4000ppm之间的悬浮固体(SuspendedSolid),以下简称SS成分,此外还含有大量金属镁离子。
近年来,各国政府对于环境标准、水质标准的要求日益严厉,中国《综合污水排放标准》规定,对于含50~200ppm氟离子的排放水,以下简称为含氟废水,也要求需要高度净化至氟离子含量降至10ppm以下,才能排入大海。
目前国内外除氟技术主要包括吸附法、离子交换法、电化学法及化学法等。
吸附法除氟技术一般只能用于氟含量小于10mg/L的饮用水除氟处理,且成本高,不适宜用于大水量工业废水除氟领域;离子交换法是利用离子交换树脂的交换能力,去除水中氟离子的一种方法,复合树脂除氟率高,可以再生,不足之处在于其他阴离子存在下会降低去除效率,树脂再生会导致氟浓缩液废弃物,需要再加以处理才能丢弃;电化学法包括电凝聚法和电渗析法,电凝聚法需经固液分离操作,电渗析法中浓缩室的水排放造成污染的缺点也限制了电化学法的实际应用;化学沉淀法除氟技术是工程上常用的工艺之一,脱硫废水与漂白水汇合分别经中继池和缓行槽后依次进入慢混槽和沉淀槽,由沉淀槽排除沉淀污泥进入挤压机处理,分流处理液引入放流池后外排。
该工艺在高氟废水处理中应用较多,其中投加石灰的方法是一种成本较低、应用广泛的除氟方法,但该方法存在一些不足之处,例如由于石灰本身的特点,导致石灰利用率低、加药量大、出水氟离子难以去除到较低水平;混凝沉降法也是常用的除氟工艺,针对脱硫废水,传统混凝沉降方法为添加硫酸铝或液碱,但会形成大量油脂状态、沉降性差的污泥,此种污泥含水率高、固液分离困难,并生成很多粒径细小的颗粒物,造成污染物出水效果不佳,污泥难以回用及堆存占地大等问题,形成了二次固废污染。
除氟工艺
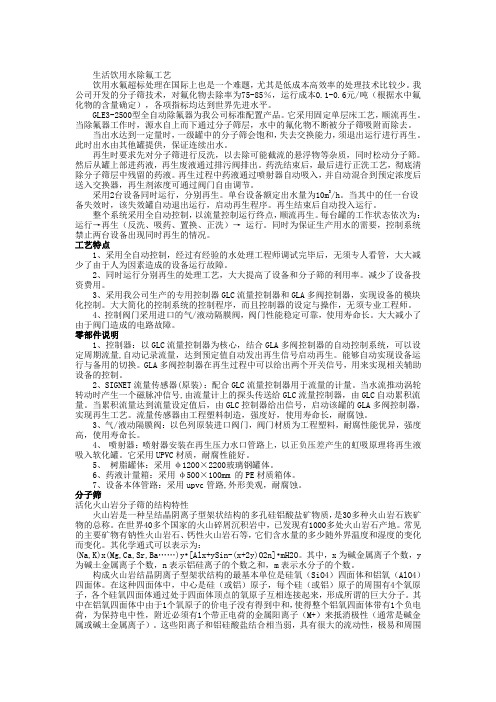
生活饮用水除氟工艺饮用水氟超标处理在国际上也是一个难题,尤其是低成本高效率的处理技术比较少。
我公司开发的分子筛技术,对氟化物去除率为75-85%,运行成本0.1-0.6元/吨(根据水中氟化物的含量确定),各项指标均达到世界先进水平。
GLE3-2500型全自动除氟器为我公司标准配置产品。
它采用固定单层床工艺,顺流再生。
当除氟器工作时,源水自上而下通过分子筛层,水中的氟化物不断被分子筛吸附而除去。
当出水达到一定量时,一级罐中的分子筛会饱和,失去交换能力,须退出运行进行再生。
此时出水由其他罐提供,保证连续出水。
再生时要求先对分子筛进行反洗,以去除可能截流的悬浮物等杂质,同时松动分子筛。
然后从罐上部进药液,再生废液通过排污阀排出。
药洗结束后,最后进行正洗工艺,彻底清除分子筛层中残留的药液。
再生过程中药液通过喷射器自动吸入,并自动混合到预定浓度后送入交换器,再生剂浓度可通过阀门自由调节。
采用2台设备同时运行,分别再生。
单台设备额定出水量为10m3/h。
当其中的任一台设备失效时,该失效罐自动退出运行,启动再生程序。
再生结束后自动投入运行。
整个系统采用全自动控制,以流量控制运行终点,顺流再生。
每台罐的工作状态依次为:运行→再生(反洗、吸药、置换、正洗)→运行。
同时为保证生产用水的需要,控制系统禁止两台设备出现同时再生的情况。
工艺特点1、采用全自动控制,经过有经验的水处理工程师调试完毕后,无须专人看管,大大减少了由于人为因素造成的设备运行故障。
2、同时运行分别再生的处理工艺,大大提高了设备和分子筛的利用率。
减少了设备投资费用。
3、采用我公司生产的专用控制器GLC流量控制器和GLA多阀控制器,实现设备的模块化控制。
大大简化的控制系统的控制程序,而且控制器的设定与操作,无须专业工程师。
4、控制阀门采用进口的气/液动隔膜阀,阀门性能稳定可靠,使用寿命长。
大大减小了由于阀门造成的电路故障。
零部件说明1、控制器:以GLC流量控制器为核心,结合GLA多阀控制器的自动控制系统,可以设定周期流量,自动记录流量,达到预定值自动发出再生信号启动再生。
除氟方法

含氟废水处理大汇总氟是一种微量元素,饮用水含氟量在0.4~0.6mg/L的水对人体无害有益,而长期饮用含量大于1.5mg/L的高氟水则会给人体带来不利影响,严重的会引起氟斑牙和氟骨病。
我国某些地区特殊的地球化学特征使该区域水源含氟量大于1.0mg/L,从而造成地方性氟中毒。
我国有将近l亿人生活在高氟水地区,目前在我国氟受害者多达几千万人。
除个别地区自然因素外,大量的高氟工业废水的排放是主要因素之一。
随着我国工业的迅猛发展,含氟废水的排放量将会增加,因此.含氟废水的排放必须受到严格控制。
某些高浓度含氟工业废水的排放,更对人们身体健康造成很大威胁,所以必须对含氟工业废水加以处理。
1973年颁布的《工业三废排放试行标准》(GBJ4-73)中规定,氟的无机化合物排放标准为10mg/L(以F-计)。
1988年颁布的《污水综合排放标准》(GB8789-88)中规定,新扩改企业对外排放含氟废水,氟化物不得超过10mg/L(向二级污水处理厂排放除外)。
此废水带出物是以氟化钙计,那么1988年的标准比1973年的标准严格了一倍以上。
目前含氟废水的主要处理方法是化学沉淀法和吸附法,这两种方法存在处理后出水很难达标、泥渣沉降缓慢且脱水困难等缺点。
冷冻法、离子交换树脂法、超滤法、电渗析等,因为处理成本高,除氟效率低,多停留在实验阶段,很少推广应用于工业含氟废水治理。
笔者认为,应围绕沉淀法吸附法为主体工艺,后续深处理工艺,提高效率,节约成本,应对含氟废水的特点,开发合理工艺。
化学沉淀法一、Ca(OH)2+PAC+PAM+ 吸收塔法污水处理工艺流程对于高浓度含氟工业废水,一般采用钙盐沉淀法,即向废水中投加石灰,使氟离子与钙离子生成CaF2沉淀而除去。
该工艺具有方法简单、处理方便、费用低等优点,但存在处理后出水很难达标、泥渣沉降缓慢且脱水困难等缺点。
氟化钙在18 ℃时于水中的溶解度为16.3 mg/L,按氟离子计为7.9 mg/L,在此溶解度的氟化钙会形成沉淀物。
除氟工艺

6 吨小时除氟设备2019 年8 月一、设备主要技术参数描述二、工艺流程及简介三、设备报价四、成本核算五、除氟设备照片一、设备主要技术参数描述等相关技术资料(一)除氟设备1.1 目的和依据氟是人体生命必不可少的微量元素之一。
适量的氟能使骨、牙坚固,减少龋齿发病率。
饮用水适宜的氟质量浓度为0.5〜1 mg/L。
当饮用水中氟含量不足时,易患龋齿病;但若长期饮用氟质量浓度高于1 mg/L的水,则会引起氟斑牙病;长期饮用氟质量浓度为2〜6 mg/L 的水会引起氟骨病。
氟长期积累于人体时能深入骨骼生成CaF 2 ,造成骨质松脆,牙齿斑釉,韧带钙化,关节僵硬甚至瘫痪,严重者丧失劳动能力。
氟慢性中毒还可产生软组织损害,甚至肿瘤发生,并有致白血病的危险性。
据近年的资料报道,长期摄入过量的氟化物还有致癌、致畸变反应。
为了防止和减少氟病发生率,控制饮用水中的氟含量是十分必要的。
我国不少地区饮用水源的氟含量较高,目前,全国农村约有7000多万人饮用高氟水(氟含量>1mg/L),水中含氟量最高可达2〜12mg/L,导致不同程度的氟中毒。
如山西南部.山西北部. 东北克山地区,安徽北部、宁夏大部、河北部分地区、天津等。
有效降低饮水中的氟含量,其途径一是选用适宜水源,二是采取饮水除氟,使含量降到适于饮用的范围。
选取适宜水源往往受到自然条件限制,多数情况下采用饮水除氟方式获得洁净饮水。
饮水除氟是通过物理化学作用,将水中过量的氟除去。
1.2 编制依据《中华人民共和国生活饮用水卫生标准》GB5749-2006 《水处理设备制造技术条件》JB2932-1999 ;《水处理设备性能试验总则》GB/T13922.1-1992 ;(2)工程概况1.3 工程说明1.3.1 厂区情况1.3.2 厂址地质及气象条件厂址附近无大的断裂带通过,处于相对稳定地段,适宜建厂。
厂址区域地震基本烈度为切度,地震动峰值加速度为0.05g。
厂址地址为:砂质粘土,抗压强度 1.5kg/cm2以上,无地下水。
室外给水设计 (20)除 氟
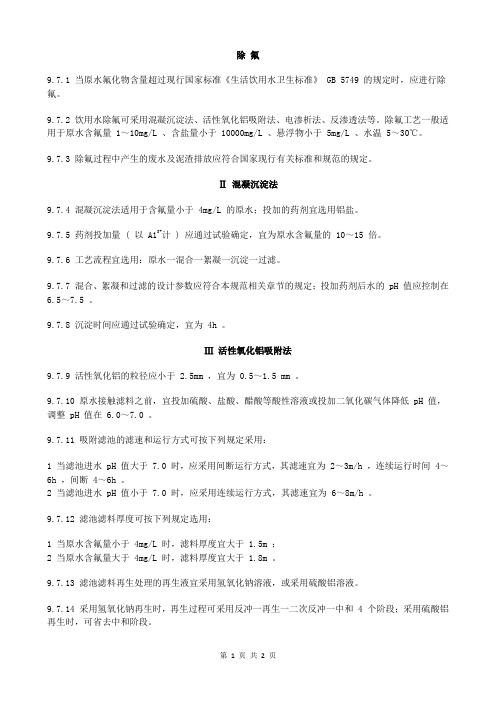
除氟9.7.1 当原水氟化物含量超过现行国家标准《生活饮用水卫生标准》 GB 5749 的规定时,应进行除氟。
9.7.2 饮用水除氟可采用混凝沉淀法、活性氧化铝吸附法、电渗析法、反渗透法等。
除氟工艺一般适用于原水含氟量 1~10mg/L 、含盐量小于 10000mg/L 、悬浮物小于 5mg/L 、水温 5~30℃。
9.7.3 除氟过程中产生的废水及泥渣排放应符合国家现行有关标准和规范的规定。
Ⅱ 混凝沉淀法9.7.4 混凝沉淀法适用于含氟量小于 4mg/L 的原水;投加的药剂宜选用铝盐。
9.7.5 药剂投加量 ( 以 A13+计 ) 应通过试验确定,宜为原水含氟量的 10~15 倍。
9.7.6 工艺流程宜选用:原水一混合一絮凝一沉淀一过滤。
9.7.7 混合、絮凝和过滤的设计参数应符合本规范相关章节的规定;投加药剂后水的 pH 值应控制在6.5~7.5 。
9.7.8 沉淀时间应通过试验确定,宜为 4h 。
Ⅲ 活性氧化铝吸附法9.7.9 活性氧化铝的粒径应小于 2.5mm ,宜为 0.5~1.5 mm 。
9.7.10 原水接触滤料之前,宜投加硫酸、盐酸、醋酸等酸性溶液或投加二氧化碳气体降低 pH 值,调整 pH 值在 6.0~7.0 。
9.7.11 吸附滤池的滤速和运行方式可按下列规定采用:1 当滤池进水 pH 值大于 7.0 时,应采用间断运行方式,其滤速宜为 2~3m/h ,连续运行时间 4~6h ,间断 4~6h 。
2 当滤池进水 pH 值小于 7.0 时,应采用连续运行方式,其滤速宜为 6~8m/h 。
9.7.12 滤池滤料厚度可按下列规定选用:1 当原水含氟量小于 4mg/L 时,滤料厚度宜大于 1.5m ;2 当原水含氟量大于 4mg/L 时,滤料厚度宜大于 1.8m 。
9.7.13 滤池滤料再生处理的再生液宜采用氢氧化钠溶液,或采用硫酸铝溶液。
9.7.14 采用氢氧化钠再生时,再生过程可采用反冲一再生一二次反冲一中和 4 个阶段;采用硫酸铝再生时,可省去中和阶段。
除氟的方法有哪些

随着现代工业的迅速发展,涉氟行业生产过程中会产生大量含氟工业废水,这些废水中通常会含有较多的以氟离子(F-)形态存在的氟元素。
含氟废水来源主要有以下两类:● 以天然含氟矿物为原料直接生产氟化物的传统氟化工生产废水和以含氟工业品为主要或辅助原料的其他工业行业生产废水。
● 半导体行业废水中的氟离子主要来自湿刻蚀工序所使用的刻蚀液,主要物质为氢氟酸和氟化铵,其中的氟离子在清洗环节随纯水进入废水中。
排放标准世界卫生组织规定饮用水中氟含量的上限为1.5mg/L,我国《生活饮用水水质卫生规范》规定饮用水中氟化物含量的限值为1mg/L,而《废水综合排放标准》中氟化物的一级排放标准为氟离子浓度不超过10mg/L。
因此,工业废水中氟离子含量应小于10mg/L。
电镀、铝电解、半导体、钢铁工业、玻璃制造、磷肥生产、热电厂、萤石选矿、氟化盐和氢氟酸等诸多生产过程中都会排出大量的含氟废水,含量都在100mg/L以上,部分行业氟离子含量甚至高达几千mg/L。
所以必须对含氟废水进行处理,达标后才能向外排放。
《电镀污染物排放标准》、《电池工业污染物排放标准》、《电子工业污染物排放标准》规定的排入城镇排水系统的氟化物限值分别为10mg/L、10mg/L和20mg/L。
《城镇污水处理厂污染物排放标准》对氟化物排放没有限制,而《地表水环境质量标准》规定的氟化物限值为1.0 mg/L 和1.5mg/L。
随着污水处理厂排放标准的提高,使得污水处理厂有必要对排放废水进行超深度除氟处理。
目前除氟方法优缺点目前含氟工业废水的水量大、分布广,而且含氟废水组成比较复杂。
工业技术的发展,各行业中产生的含氟废水特点不同,所以导致含氟废水的氟离子浓度差别较大。
但是含氟废水中的氟元素仍然是以氧氟酸、氟硅酸及可溶性氟化物盐的形式存在。
除此之外,由于是工业生产废水,因此含氟废水中除含有氟元素外通常伴随含有无机盐类或有机物等其他污染物,导致其处理较困难。
工业含氟废水常用除氟方法有混凝沉淀法、吸附法、离子交换法、膜过滤法、和电化学法等。
工业炉窑烟气中氟的脱除及综合利用

工业炉窑烟气中氟的脱除及综合利用含氟烟气的处理技术是解决氟污染问题的关键。
废气中的氟化氢和四氟化硅可以通过湿法净化工艺采用水吸收法或碱吸收法脱除。
水吸收法经济实用,但对设备有强烈的腐蚀作用,而碱吸收法可以产生盐类,减轻对设备的腐蚀作用,同时还能回收氟资源。
除此之外,干法吸附也是净化含氟废气的一种重要方法,可以将氟化氢或四氟化硅吸附下来,再循环使用吸附剂。
氟化物是一种常见的污染物,其来源主要包括化学、无机盐和冶金工业。
氟化物具有很高的化学活性和生物活性,对人类、动植物造成危害。
虽然氟也是重要的化工原料,但必须加强对含氟烟气的净化和回收利用,以解决氟污染问题。
气态氟化物包括氟化氢和四氟化硅,它们的化学性质不同。
气态HF为无色、具有强烈的腐蚀性和毒性,易溶于水。
四氟化硅是无色气体,易溶于水,与氟化氢反应生成氟硅酸。
这些性质为净化含氟废气提供了依据。
湿法净化工艺是净化含氟废气的主要方法,可以采用水吸收法和碱吸收法。
水吸收法经济实用,但对设备有强烈的腐蚀作用;碱吸收法可以产生盐类,减轻对设备的腐蚀作用,同时还能回收氟资源。
此外,干法吸附也是一种重要的净化方法,可以将氟化氢或四氟化硅吸附下来,再循环使用吸附剂。
干法吸附工艺是一种净化烟气的方法,它利用固体吸附剂吸附污染物质,如HF、SiF4、SO2等。
通常采用碱性氧化物作吸附剂,利用其固体表面的物理或化学吸附作用,将污染物吸附在固体表面,再利用除尘技术将其除去。
含氟烟气通过装填有固体吸附剂的吸附装置,使氟化氢与吸附剂发生反应,达到除氟的目的。
在含有HF、SO2、CO、NOX、CO2、SiF4等成分的烟气中,氟化氢比其他组分更容易被吸附。
因此,干法除氟通常采用Al2O3、CaO、CaCO3和Fe2O3等吸附剂,其中以Al2O3最为常见。
Al2O3法是一种常用的干法净化技术,用于净化电解铝生产过程中产生的含HF废气。
该技术已经在铝工业中得到广泛应用,且在我国的钢铁企业中也得到了一定的应用。
废水除氟工艺流程

废水除氟工艺流程
废水除氟工艺流程有多种,其中包括石灰法、化学沉淀法、混凝沉淀法等。
具体采用哪种流程需要依据废水中氟离子的含量以及企业的实际情况来决定。
1. 石灰法:通过向废水中加入石灰、石灰乳或氯化钙等含钙化合物,使Ca2+离子与废水中的F-离子生成CaF2,以沉淀形式除去。
这种方法虽然除氟效果很好,但是处理过后的含氟废水还含有一定量的氟离子,需要经过二次处理或多次处理才能达到排放标准。
2. 化学沉淀法:通过在含氟废水中加入一些能够和废水中氟离子产生化学反应,并且能够产生难溶于水的沉淀物质,将氟从水中分离。
常用的沉淀剂包括石灰、电石渣、氯化钙三种。
其中,石灰沉淀法是处理高浓度含氟废水的重要方法,原理是使石灰石溶解后产生的钙离子可以和水中的氟离子反应,生成难溶于水的氟化钙,从而除去水中的氟离子。
3. 混凝沉淀法:通过在含氟废水中加入具有凝聚能力或者是能够和氟化物产生沉淀的物质,使废水中的氟与其生成大量的胶体和难溶物质,然后通过沉淀、泥水分离的方式来去除水体中氟化物的方法。
这种方法相较于化学沉淀法,所需要投入的药剂量比较少,而且处理量更大,经过一次处理后,氟化物浓度就可以低于10mg/L。
此外,还有氧化-吸附法、活性氧化铝吸附法、离子交换法等其他方法。
在实际应用中,企业可以根据自身情况和废水处理要求选择合适的工艺流程。
乙酸钠在除氟工艺上的应用

乙酸钠在除氟工艺上的应用乙酸钠是一种常见的有机酸盐,化学式为CH3COONa。
它在除氟工艺中有着广泛的应用,可以有效地去除水中的氟离子。
本文将从乙酸钠的性质、除氟工艺的原理以及乙酸钠在除氟工艺中的应用等方面进行探讨。
乙酸钠是一种白色结晶粉末,具有较好的溶解性。
它可以在水中迅速溶解,形成乙酸钠溶液。
乙酸钠溶液呈碱性,可以与酸性物质发生中和反应。
这种性质使得乙酸钠在除氟工艺中发挥重要作用。
除氟工艺是一种将水中的氟离子去除的方法。
在一些地区,水中的氟离子含量较高,超过了卫生标准。
高浓度的氟离子对人体健康有一定的影响,因此需要对水进行处理,将其中的氟离子去除。
乙酸钠在除氟工艺中被广泛应用。
乙酸钠除氟的原理是利用乙酸钠溶液对水中的氟离子进行络合作用,形成可溶性的氟化物络合物,从而将氟离子从水中除去。
乙酸钠的碱性可以中和水中的酸性物质,将水中的酸度降低到适宜的范围,为后续的除氟工艺提供条件。
乙酸钠在除氟工艺中的应用可以分为两个步骤。
首先,乙酸钠溶液被加入到待处理的水中,与水中的氟离子发生络合反应。
这个过程需要一定的时间,以确保乙酸钠与氟离子充分反应。
其次,将乙酸钠与水中的络合物一起去除,可以通过沉淀、过滤等方法进行。
这样,就可以将水中的氟离子有效地除去。
乙酸钠在除氟工艺中的应用有许多优点。
首先,乙酸钠是一种廉价且易得的化学品,成本较低。
其次,乙酸钠具有良好的溶解性,可以迅速溶解在水中,与水中的氟离子发生反应。
此外,乙酸钠的碱性可以中和水中的酸性物质,为除氟工艺提供了条件。
因此,乙酸钠在除氟工艺中的应用非常广泛。
除氟工艺是一项重要的水处理技术,可以有效地去除水中的氟离子。
乙酸钠作为其中的一种化学试剂,在除氟工艺中发挥着重要的作用。
乙酸钠可以与水中的氟离子发生络合反应,形成可溶性的氟化物络合物,从而将水中的氟离子除去。
乙酸钠的碱性可以中和水中的酸性物质,为除氟工艺提供条件。
乙酸钠在除氟工艺中应用方便、成本低廉,因此被广泛使用。
铅冶炼除氟工艺

铅冶炼除氟工艺一、介绍铅是一种常见的金属元素,广泛用于电池、建筑材料、汽车零部件等领域。
然而,铅矿石中常常含有氟化物,这对环境和人类健康构成潜在威胁。
因此,铅冶炼过程中除氟工艺的开发和应用变得非常重要。
二、铅矿石中氟化物的问题铅矿石中的氟化物主要存在于矿石中的杂质矿物中,如方解石、萤石等。
这些氟化物在冶炼过程中会释放出氟化氢气体,对环境和人体健康造成危害。
因此,铅冶炼过程中需要采取除氟工艺来降低氟化物含量。
2.1 除氟的原理除氟工艺的基本原理是将铅矿石中的氟化物转化为不挥发的固体物质,从而降低氟化物的含量。
常用的除氟工艺包括氯化法、氟化法和碳酸铵法等。
2.2 除氟工艺的选择选择合适的除氟工艺需要考虑多个因素,包括矿石中氟化物的含量、冶炼设备的特点、工艺的成本和环境影响等。
不同的工艺有不同的适用范围和优缺点,需要综合考虑才能做出最佳选择。
三、氯化法除氟工艺氯化法是一种常用的除氟工艺,其基本原理是利用氯化物将铅矿石中的氟化物转化为氯化物,从而实现除氟的目的。
3.1 氯化法的工艺流程氯化法除氟的工艺流程一般包括以下几个步骤: 1. 矿石预处理:将铅矿石破碎、磨矿,以提高除氟效果。
2. 矿石浸出:将磨碎后的矿石与氯化剂进行浸出反应,将氟化物转化为氯化物。
3. 溶液处理:将浸出液进行加热、沉淀、过滤等处理,以得到含氟较低的溶液。
4. 溶液回收:通过蒸发、结晶等方法,将溶液中的铅和氟分离,以便进行下一步的铅冶炼。
3.2 氯化法的优缺点氯化法除氟工艺具有以下优点: - 除氟效果好:氯化法能够将铅矿石中的氟化物转化为氯化物,从而有效降低氟化物的含量。
- 工艺成熟:氯化法是一种成熟的工艺,已经在铅冶炼行业得到广泛应用。
- 适应性强:氯化法适用于不同类型的铅矿石,具有较广泛的应用范围。
然而,氯化法除氟工艺也存在一些缺点: - 高能耗:氯化法需要进行加热、蒸发等过程,能耗较高。
- 氯化副产物处理:氯化法会产生大量的氯化副产物,需要进行处理和处置,增加了环境压力。
含氟废水处理工艺

含氟废水处理随着现代工业的发展,氟化物的生产企业和使用企业发展越来越多,含氟废水对环境的污染越来越引起国家和相关企业的重视。
我国对含氟废水的排放也制定了相关标准,如在《污水综合排放标准》GB8978 -1996)中规定:污水排放的氟离子浓度的一级标准为≤10mg/L。
所以,含氟废水必须经过处理、达标后,才能排放。
含氟废水分为含有机氟废水和含无机氟废水。
一、含无机氟离子废水处理工艺方法:含氟废水的除氟方法有吸附法、电凝聚法、反渗透法、离子交换法、化学沉淀法和混凝沉降法等。
常用的方法主要有三种:化学沉淀法、混凝沉淀法和吸附法。
化学沉淀法比较简单、处理方便、成本低效果好,主要用于处理高浓度含氟废水。
混凝沉降法一般只适用于含氟较低的废水处理。
吸附法主要适用于水量较小的饮用水的处理。
对含氟浓度高或流量较大的废水,若单独投加钙盐除氟,沉淀速度很慢,而单独使用絮凝剂会增加处理成本,所以常用的是先使用化学沉淀法,再用吸附剂或絮凝剂处理,使氟含量降到10 mg/L 以下。
目前沉淀法较多的是用CaCl 2 沉淀,因为CaCl 2 的溶解度高,能降低CaF 2饱和溶解度的同离子,而且它还是一种中性盐,投加后不会对pH 产生影响,之后再加入混凝剂使生成的CaF 2 小的晶体颗粒变大,降低其比表面积,加速沉淀,从而强化除氟效果。
Ⅰ、氟离子的去除机理去除氟离子的机理主要包含两部分:(1)选择形成合适、难溶的氟化物,使处理工艺从一开始就快速、大量地降低氟离子的浓度(主要氟化钙沉淀);(2)利用同离子效应,通过加入强电解质,进一步有效降低氟离子浓度,使处理后的废水稳定达到排放标准。
Ⅱ、主要方法:1、化学沉淀法:是含氟废水处理最常用的方法,在高浓度含氟废水预处理应用中尤为普遍。
沉淀法系加化学品处理,形成氟化物沉淀物或氟化物在生成的沉淀物上共沉淀,通过沉淀物的固体分离达到氟离子的去除。
因此,其处理效率取决于固液分离的效果。
常用的化学品有石灰、电石渣、磷酸钙盐、白云石或明矾等。
除氟工艺技术

除氟工艺技术除氟工艺技术是一种将氟化物从水和废水中去除的技术。
氟化物通常来自于工业废水、冶炼过程和自然水体中。
高浓度的氟化物会对环境和人类健康产生严重影响,因此除氟工艺技术的开发和应用具有重要意义。
除氟工艺技术有多种方法,包括化学除氟、吸附除氟和膜分离除氟。
化学除氟是指通过化学反应将氟与其他物质结合,形成不溶性或低溶解度的化合物,并从水中去除。
常用的化学除氟剂包括钙、铝、铁、锌等离子,它们与氟离子发生反应生成氟化物沉淀并沉积。
这些离子在废水中通常以溶液或粉末形式添加进入反应槽中,与废水中的氟离子反应,然后通过沉淀与废水分离。
化学除氟方法具有高效、经济的特点,广泛应用于工业废水处理中。
吸附除氟是指使用吸附剂将水中的氟离子吸附到表面上,实现氟离子的去除。
常见的吸附剂有活性炭、离子交换树脂等。
吸附剂的表面具有一定的孔洞结构,能够吸附氟离子,使其从水中被固定下来。
这种方法操作简单,成本较低,适用于小型水处理设备或家庭使用。
膜分离除氟是通过膜的选择性渗透性将水中的氟离子与其他溶质分离。
膜分离方法根据膜的特性可分为反渗透膜、纳滤膜等。
膜分离技术除氟效果较好,但设备复杂,运行成本较高,一般应用于大型工业废水处理系统。
除氟工艺技术的选择取决于废水中氟的浓度、产量、处理要求以及经济性等因素。
除氟工艺技术的发展不断推动着环境保护和可持续发展的进程,在工业生产和生活中发挥着重要作用。
总之,除氟工艺技术是一种将氟化物从水和废水中去除的技术,其方法包括化学除氟、吸附除氟和膜分离除氟。
这些方法各有优缺点,适用于不同的处理情况。
除氟工艺技术的应用为环境保护和可持续发展做出了贡献。
随着科学技术的不断进步,除氟工艺技术也将不断完善,更好地服务于各行各业的废水处理需求。
钙法除氟的排泥量

钙法除氟的排泥量1. 引言氟是一种广泛存在于自然界的元素,但高浓度的氟离子对人体健康有害。
在一些地区,水源中的氟含量超过了国家标准,为了保障人们的健康,需要采取有效的除氟措施。
钙法除氟是一种常用的除氟方法之一,本文将探讨钙法除氟过程中排泥量的相关问题。
2. 钙法除氟原理钙法除氟是利用钙与氟离子之间的化学反应,将水中的氟离子转化为不溶于水的沉淀物,从而达到除氟的目的。
具体过程如下:1.添加钙源:向水中加入钙源,一般使用氢氧化钙(Ca(OH)2),也可以使用生石灰(CaO)等。
2.反应产物:钙源与水中的氟离子反应生成氟化钙(CaF2),氟化钙是一种不溶于水的沉淀物。
3.沉淀分离:沉淀物会自动沉淀到水底部,形成泥浆状物质。
4.排泥处理:将沉淀物从水中分离,即完成了钙法除氟过程。
3. 影响排泥量的因素钙法除氟过程中的排泥量受到多个因素的影响,下面将对其中几个重要因素进行分析。
3.1 钙源种类钙源种类是影响排泥量的关键因素之一。
不同种类的钙源在反应中所产生的沉淀物性质有所不同,从而影响排泥量的大小。
一般来说,氢氧化钙(Ca(OH)2)是常用的钙源,它能够与氟离子充分反应,生成大量的氟化钙沉淀物,因此排泥量较大。
3.2 钙源用量钙源用量是影响排泥量的另一个重要因素。
一般来说,钙源用量越大,反应产生的氟化钙沉淀物的量也越大,排泥量相应增加。
但是,过量的钙源用量并不一定能够提高排泥量,反而可能造成钙源的浪费。
3.3 水质条件水质条件也会对排泥量产生影响。
水中的溶解物质、pH值等因素都可能影响钙法除氟的效果,从而影响排泥量的大小。
一般来说,水中的溶解物质越多,排泥量越大。
4. 排泥量的测定方法为了准确测定钙法除氟过程中的排泥量,需要采用合适的测定方法。
一种常用的方法是通过测量沉淀物的质量来确定排泥量。
具体步骤如下:1.取一定体积的水样,加入适量的钙源,进行钙法除氟过程。
2.将反应后的水样静置一段时间,使沉淀物充分沉淀。
高效除氟剂生产工艺流程

高效除氟剂生产工艺流程英文回答:Efficient Production Process for Defluorination Agents.Defluorination agents are chemicals used to remove fluoride from various substances, such as water or industrial waste. Developing an efficient production process for defluorination agents is crucial for industries that require fluoride removal. In this article, I will outline a production process that combines both chemical reactions and separation techniques to achieve high efficiency.Firstly, the production process starts with the selection of suitable raw materials. The raw materials should have high fluoride affinity and be readily available in large quantities. For example, aluminum oxide and calcium carbonate are commonly used as raw materials for defluorination agents due to their ability to react withfluoride ions.Next, the raw materials undergo a chemical reaction to form the desired defluorination agent. For instance, aluminum oxide can react with hydrochloric acid to produce aluminum chloride, which is an effective defluorination agent. The reaction is typically carried out in a reactor vessel under controlled temperature and pressure conditions.After the chemical reaction, the mixture is subjectedto a separation process to isolate the defluorination agent from the by-products and impurities. One common separation technique is filtration, where the mixture is passedthrough a filter to separate the solid defluorination agent from the liquid phase. The solid product can then be washed and dried to obtain the final defluorination agent.To improve the efficiency of the production process, it is important to optimize the reaction conditions and the separation techniques. This can be achieved through process monitoring and control, as well as continuous improvement efforts. For example, by adjusting the reaction temperatureand concentration of reactants, the yield of the defluorination agent can be maximized. Similarly, by optimizing the filtration process, the separationefficiency can be improved.Furthermore, automation and advanced technologies can be employed to enhance the efficiency of the production process. For instance, automated control systems can monitor and adjust the reaction parameters in real-time, ensuring optimal conditions for the chemical reaction. Additionally, advanced filtration systems, such as membrane filtration, can be used to achieve higher separation efficiency and reduce the need for manual intervention.In conclusion, an efficient production process for defluorination agents involves careful selection of raw materials, chemical reactions, and separation techniques. By optimizing the reaction conditions, improving the separation efficiency, and incorporating automation and advanced technologies, industries can achieve high efficiency in the production of defluorination agents.中文回答:高效除氟剂生产工艺流程。
简述活性氧化铝吸附过滤除氟工艺设计要点
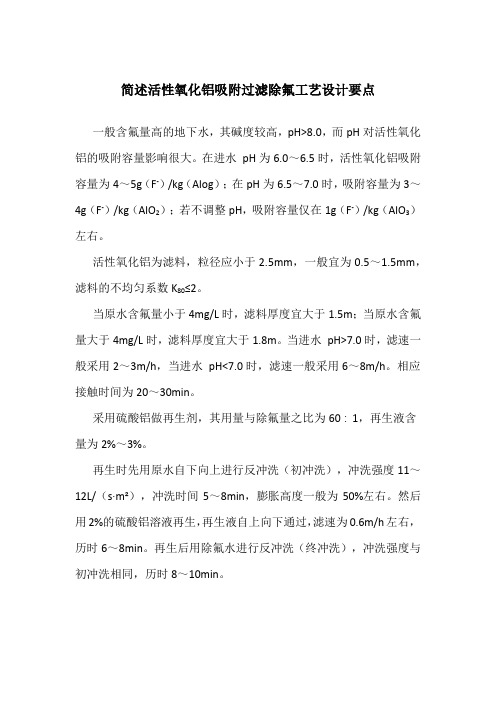
简述活性氧化铝吸附过滤除氟工艺设计要点
一般含氟量高的地下水,其碱度较高,pH>8.0,而pH对活性氧化铝的吸附容量影响很大。
在进水pH为6.0~6.5时,活性氧化铝吸附容量为4~5g(F-)/kg(Alog);在pH为6.5~7.0时,吸附容量为3~4g(F-)/kg(AlO2);若不调整pH,吸附容量仅在1g(F-)/kg(AlO3)左右。
活性氧化铝为滤料,粒径应小于2.5mm,一般宜为0.5~1.5mm,滤料的不均匀系数K80≤2。
当原水含氟量小于4mg/L时,滤料厚度宜大于1.5m;当原水含氟量大于4mg/L时,滤料厚度宜大于1.8m。
当进水pH>7.0时,滤速一般采用2~3m/h,当进水pH<7.0时,滤速一般采用6~8m/h。
相应接触时间为20~30min。
采用硫酸铝做再生剂,其用量与除氟量之比为60∶1,再生液含量为2%~3%。
再生时先用原水自下向上进行反冲洗(初冲洗),冲洗强度11~12L/(s·m²),冲洗时间5~8min,膨胀高度一般为50%左右。
然后用2%的硫酸铝溶液再生,再生液自上向下通过,滤速为0.6m/h左右,历时6~8min。
再生后用除氟水进行反冲洗(终冲洗),冲洗强度与初冲洗相同,历时8~10min。
氧化钙除氟工艺

氧化钙除氟工艺
工艺原理:
氟离子与氧化钙发生如下反应:
Ca(OH)2 + 2F- = CaF2↓ + 2OH-
反应生成的氟化钙(CaF2)难溶于水,可以通过沉淀分离的方式去除。
工艺流程:
1. 加药:将氧化钙溶液(熟石灰乳液)投加到含氟废水中,使之充分混合。
2. 反应:在搅拌条件下,氟离子与氧化钙发生反应生成氟化钙沉淀。
3. 沉淀分离:通过沉淀池或过滤设备将氟化钙沉淀分离。
4. 出水:分离后的出水即为除氟后的产水。
影响因素:
1. 投加量:投加氧化钙的量要适当,过量会导致钙离子残留,不足则除氟效果差。
2. 搅拌:充分搅拌有利于氧化钙与氟离子充分接触反应。
3. pH值:适宜pH值范围为6-8,过高或过低都会影响除氟效率。
4. 温度:较高温度有利于反应进行,但温度过高会引起结垢。
该工艺除氟效率高、操作简便,是常用的除氟方法之一,但沉淀物的处理是需要重视的环节。
除氟工艺及详细说明

除氟工艺及详细说明按照国家污水综合排放标准,氟离子浓度应小于10mg/L;对于饮用水,氟离子浓度要求在1mg/L以下。
目前国内外常用的含氟废水处理方法大致分为两类,即沉淀法和吸附法。
化学沉淀法是通过投加钙盐等化学药品,形成氟化物沉淀或氟化物被吸附于所形成的沉淀物中而共同沉淀。
该方法简单、处理方便,费用低,但石灰溶解度低,只能以乳状液投加,且产生的CaF<SUB>2</SUB>沉淀包裹在Ca(OH)<SUB>2</SUB>颗粒的表面,使之不能被充分利用,因而用量大。
处理后的废水中氟含量一般只能下降到15mg/L,很难达到国标一级标准。
而且存在泥渣沉降缓慢,脱水困难,处理大流量排放物周期长,不适应连续处理连续排放等缺点。
<BR> 吸附法是指含氟废水流经接触床,通过与床中固体介质进行离子交换或化学反应,去除氟化物。
这种方法只适用于低浓度的含氟废水或经其他方法处理后氟化物浓度降至10~20mg/L的废水。
而且接触床的再生及高浓度再生液的处理是整个运行过程中不可缺少的一部分,接触床频繁的再生使运行成本较高; 此外,还有冷冻法、离子交换树脂除氟法、超滤除氟法、电渗析等,但因为处理成本高,除氟效率低,至今多停留在实验阶段,很少推广应用于工业含氟废水治理。
<BR> 絮凝一气浮处理含氟废水新工艺是在传统工艺的基础上,采用絮凝一气浮一吸附相结合的工艺处理含氟废水。
1.基本原理利用铝离子的三种机理来去除氟离子,即:(1)吸附。
铝盐絮凝除氟过程中生成的具有很大表面积的无定性Al(OH)<SUB>3 </SUB>(am)原体对氟离子产生氢键吸附,氟离子半径小,电负(2)离子交换。
氟离子与氢氧根的半径及电荷都相近,铝盐絮凝除氟过程中,投加到水中的A1<SUB>13 </SUB>O<SUB>4 </SUB>(0H)<SUB>14</SUB><SUP>7+</SUP> 等聚阳离子及水解后形成的无定性Al(0H)<SUB>3</SUB>(am)沉淀,其中的OH<SUP>-</SUP>与F<SUP>-</SUP>发生交换,这一交换过程是在等电荷条件下进行的。
吸附除氟工艺方案

吸附除氟工艺方案一、确定工艺流程吸附除氟工艺一般包括以下几个步骤:吸附、再生、循环利用等。
根据不同的水质条件和除氟要求,可以选择不同的工艺流程。
在确定工艺流程时,需要考虑以下因素:1. 水质条件:包括原水中氟的浓度、其他离子成分、pH值等。
2. 除氟要求:需要达到的氟浓度排放标准或使用标准。
3. 吸附剂的特性:不同吸附剂对氟的吸附性能不同,需要根据吸附剂的特性确定工艺流程。
4. 再生和循环利用:需要考虑吸附剂的再生和循环利用,以降低成本和提高环保性。
二、吸附剂选择吸附剂是吸附除氟工艺中的关键因素之一,其选择直接影响除氟效果和工艺成本。
目前常用的吸附剂包括活性氧化铝、活性炭、分子筛、沸石等。
在选择吸附剂时,需要考虑以下因素:1. 吸附性能:要求吸附剂对氟具有较强的吸附性能,同时具有较高的吸附容量。
2. 稳定性:要求吸附剂具有良好的化学和物理稳定性,能够在不同的环境条件下稳定运行。
3. 再生性和循环利用:要求吸附剂具有良好的再生性能,能够循环利用,降低成本。
4. 成本:需要考虑吸附剂的成本,并结合除氟效果和工艺流程进行综合评估。
三、设备配置在确定工艺流程和吸附剂后,需要进行设备配置。
设备配置包括以下几个方面:1. 吸附柱:用于装填吸附剂,实现氟离子的吸附和去除。
2. 再生设备:用于对吸附剂进行再生和循环利用。
3. 监测和控制设备:用于监测水质的氟离子浓度,控制整个工艺流程的运行。
4. 管道和泵:用于连接各个设备和实现水流的输送。
四、操作条件优化在吸附除氟工艺中,操作条件对除氟效果具有重要影响。
因此,需要进行操作条件优化。
优化的操作条件包括以下几个方面:1. pH值:不同pH值条件下,吸附剂对氟的吸附性能不同,需要进行优化选择适当的pH值范围。
2. 流速:水流的流速直接影响吸附剂与氟离子的接触时间和吸附效果,需要进行优化选择适当的流速。
3. 温度:温度对吸附剂的吸附性能具有一定影响,需要进行优化选择适当的温度范围。
- 1、下载文档前请自行甄别文档内容的完整性,平台不提供额外的编辑、内容补充、找答案等附加服务。
- 2、"仅部分预览"的文档,不可在线预览部分如存在完整性等问题,可反馈申请退款(可完整预览的文档不适用该条件!)。
- 3、如文档侵犯您的权益,请联系客服反馈,我们会尽快为您处理(人工客服工作时间:9:00-18:30)。
以上降氟方法、材料都不尽如人意,因此,人们急需寻求一种价格便宜,使用方便,管理简单,寿命长、多功能且出水不增加任何有害物质的材料,来满足降氟改水的需要。山西碧海机械有限公司生产的康华除氟净水滤料(简称BH-1)正好填补了这一空白。
5、 工作原理
BH-1滤料在吸附铝离子后,在表面及孔隙中形成羟基络合离子团,水中的氟离子F—与BH-1滤料的OH—发生离子交换,达到除氟的目的,去除率>95%,总反应式如下:
nF—+F.FAInOH—=F.FAlnF—+nOH—
BH-1滤料结构:BH-1滤料是一种架状构造的含水铝硅酸盐矿物,主要含有Na、Ca以及少数Sr、Ba、K、Mg等金属。BH-1滤料的化学组成,通常用以下式表示:
二、工艺流程简述:
1、原水经给水泵输送至水处理间,进入除氟过滤器1过滤器去除水中的悬浮物,然后进入除氟过滤器2,在进除氟过滤器3,然后再进除氟过滤器4,水流均从下至上通过滤料,降低水中的氟化物含量。过滤速度:5~8m/h。滤层高度≥1600mm。
2、再生:7%硫酸铝溶液至下而上缓缓打入过滤器,浸泡或者循环1小时40分钟,开始排放,2小时之内必须全部放掉。不需清洗即可投入下一个生产周期。
1.2编制依据
《中华人民共和国生活饮用水卫生标准》 GB5749-2006
《水处理设备制造技术条件》 JB2932-1999;
《水处理设备性能试验 总则》 GB/T13922.1-1992;
(2) 工程概况
1.3 工程说明
1.3.1 厂区情况
1.3.2厂址地质及气象条件
厂址附近无大的断裂带通过,处于相对稳定地段,适宜建厂。
饮用水消耗定额(以1吨饮用水计)
序号
名称
技术规格
单位
定额
备注
1
清水
吨
0.3元
2
动力电
度
0.5元
3
再生药品
kg
0.3元
4
四、生活饮用水除氟说明及成本核算
除氟系统是我公司经过多年经验技术研究开发的新型设备.除氟沸石采用顶级沸石,经过活化.煅烧,改性固化,保有量和吸附量大.吸附速度增强.设备全自动控制无需人工操作.滤料自动再生。
11)过滤器系统阀门配电动蝶阀
12、再生液配制槽
1)容积:V=20m3 2) 箱体型式:立式
3) 使用条件:室内布置 4) 设计压力:常压
5) 设计温度:常温 6) 介质种类及浓度:7%硫酸铝溶液
7) 材质:碳钢 8) 箱体顶部设有加料口
9) 配带搅拌装置 10) 配带磁力翻板液位计,并具有高低报警功能
①阴树脂离子交换法:阴树脂去除水中的阴离子能量很大,但对氟离子去除率却非常低,因为阴树脂的选择顺序是:硫酸根>氯根>碳酸氢根>氟,氟排在后面,因此除氟效率非常低,而且价格昂贵,再生极其复杂,很难管理,已经极少使用。
②活性炭吸附法:活性炭具有特别大的比表面积,但其孔径也非常大,后面的氟离子进入孔穴后,前面进入的氟离子容易跑出来,因此对氟离子吸附量非常低,而且没有办法再生,吸附饱和后,只能废弃。运行成本高。
如果硅氧四面体中的硅被铝离子所置换,则形成铝氧四面体。铝是+3价的,这样铝氧四面体的4个顶角中的氧离子有1个得不到中和,因而出现了负电苛。为了中和其电性,相应就有金属阳离子加入。硅氧四面体和铝氧四面体通过其角顶互相连接,便构成了各种形状的三维硅(铝)氧格架状结构,即BH-1滤料结构。由于硅(铝)氧四面体多样性的连接方式,在BH-1滤料结构中便形成了许多孔穴和孔道。
13、 BH-1滤料使用的数量配备理由
每吨BH-1滤料一次饱和可以去除氟1公斤。按照每升水去掉1毫克计算,每吨水要去掉1克,即每吨BH-1滤料一次饱和可以净化1000吨水,每台5吨/小时的除氟设备使用0.3吨BH-1滤料一次饱和可以净化300吨水,每天预计净化500吨水,滤料需要8天再生一次。
(7) 消耗定额
⑤电渗析法。此方法是用电极铝板对水中物质电离的一种除氟方法,除氟干净彻底,出水质量很好,可自动化操作,管理比较容易。缺点是投资高,运行成本太高,电渗析设备被称作电老虎,在当前电费价格下,每吨水成本要3元以上,一般经济条件承担不起。
⑥反渗透法。此法除氟干净彻底,出水质量好,其缺点和电渗析类似,运行成本高,平均产水率低,每净化一吨水,要废弃一吨水,每天3万吨的水厂,要废弃2-3万吨水。因此,反渗透在目前仅适合工业高纯水制备和瓶装水、桶装水,不适合农村饮水安全工程。
3)运行流速:50~60m/h 4)工作压力:0.5MP
5)试验压力:0.75MPa 6)工作温度:0~50℃
7)再生方式:无顶压逆流再生
8)每台过滤器将设有上下两个吊盖人孔。并配备有人孔盖、垫圈、螺栓、螺母
9)过滤器设置窥视孔1个。其厚度足以承受过滤器的工作压力
10)过滤器进水装置采用穹形多孔板,配水采用原沸石垫层。
厂址区域地震基本烈度为Ⅵ度,地震动峰值加速度为0.05g。
厂址地址为:砂质粘土,抗压强度1.5kg/cm2以上,无地下水。
厂址地处暖温带季风区大陆性气候。主要的气象特征值:
最冷月平均气温:-20℃
最热月平均气温:28.8℃
极端温度:最高35.5℃,最低-30.0℃
1.4工艺方案选择
现在常用的饮用水除氟方法较多,主要有阴树脂离子交换法、活性炭吸附法、活性氧化铝吸附法、骨碳(羟基磷酸钙)吸附法、电渗析法、反渗透法等等。
(Na,K )x(Mg ,Ca,Sr,Ba)y{Al(x+2y)Si[n-(x+2y)]O2n}·mH2O
简写MxDy—R。其中:M代表1价阳离子Na、K;D代表2价阳离子Mg ,Ca,Sr,Ba;R代表沸石骨架{Al(x+2y)Si[n-(x+2y)]O2n}·mH2O。
BH-1滤料的结构一般由三维硅(铝)氧格架组成,其基本单元是以硅为中心和周围4个氧离子排列而成的硅氧四面体[Si O4]。
④活性氧化铝吸附法:此方法在一段时间内尤其是在人们没有发现铝离子对人体健康有巨大损害作用以前,我国和世界公认活性氧化铝是最有效的降氟方法。我国目前仍有50%左右的降氟工艺采用活性氧化铝,它也是世界上用得最多的一种降氟剂。但经过多年实践证明,该法存在下述六个问题,一是连续运行时间短,很容易出现假疲劳,运行4~6小时即要间断4~6小时恢复疲劳;二是再生时间长,再生复杂,管理复杂。如用硫酸铝再生,再生时间需要48小时;如用氢氧化钠再生,虽然时间缩短,但需使用盐酸中和,而铝是溶于酸的,稍不注意铝即被酸溶解而进入水中,因此管理要求非常高,工艺繁多,不易操作;三是滤料易出现板结现象,使布水与集水不均匀,严重影响使用寿命。山东省有些地区前些年农村防氟改水采用了活性氧化铝,用一段时间后,滤料基本板结在处理罐内,不但完全失效,而且滤料和罐体形成一体无法分离,造成罐体报废。四是出水水质差,仅能降氟而对水体中有时共存的色度、浊度、重金属离子等有害物质则不能去除。五是惧怕水中共存磷酸盐,因为磷与铝结合非常牢固,无法洗脱,活性氧化铝的表面积一旦被磷酸盐占据,除氟功能即告完结。我国华北地区地下水中普遍含有微量的磷酸盐,而磷酸盐的含量哪怕仅有0.01mg/L,也足以对活性氧化铝构成致命的威胁,这也是华北地区使用活性氧化铝除氟不能成功的主要原因;六是出水有铝离子超标的可能性,我国GB5749-2006《中华人民共和国生活饮用水卫生标准》规定铝离子标准为0.2mg/L,据《直饮水时代》杂志报道,2006年美国和法国科学家经过潜心研究和调查发现,长期饮用铝离子含量超过0.075mg/L的水,就可以造成大脑老化,引起痴呆症、脑中风等,比氟中毒的危害更大。国外发达国家很早以前就对饮用水中铝离子含量有规定。我国是近几年才对铝离子含量做出明确规定的。因此,从发展方向看,铝系除氟材料的前景是可疑的。
④管理极其简便。BH-1再生只需将再生溶液打入交换塔内浸泡即可,不存在活性氧化铝、羟基磷酸钙等需要酸碱中和等复杂操作。
⑤BH-1滤料再生时间短,2小时之内完成。再生简单,再生后不需要清洗就可以投入到下一个运行周期。不需要使用备用罐。节省费用。
⑥使用寿命长。一般除氟材料使用寿命都在一年以内,BH-1可长达3年以上。例如活性氧化铝、羟基磷酸钙等除氟材料除氟量都在700mg/Kg左右,而BH-1却可达到1000mg/Kg 以上。
我国不少地区饮用水源的氟含量较高,目前,全国农村约有7000多万人饮用高氟水 ( 氟含量 >1mg/L) ,水中含氟量最高可达 2~12mg/L,导致不同程度的氟中毒。如山西南部.山西北部.东北克山地区,安徽北部、宁夏大部、河北部分地区、天津等。
有效降低饮水中的氟含量,其途径一是选用适宜水源,二是采取饮水除氟,使含量降到适于饮用的范围。选取适宜水源往往受到自然条件限制,多数情况下采用饮水除氟方式获得洁净饮水。饮水除氟是通过物理化学作用,将水中过量的氟除去。
BH-1滤料结构内部的孔穴和孔道通常都被水分子填充,能在特定温度下而脱除,脱除后留下的孔穴和孔道,变成了如海绵或泡沫状的结构,具有吸附性质。
6、 布置方式
设备成两列布置,每列为独立系统。(见设备平面布置图)
7、 再生用化学药品
硫酸铝
化学成分:AL2(SO4)3
等级:HG 2227-2004 饮用水用
8、 出水指标
降低氟去除率,达到饮用水含量
9、 废水处理
再生废液量少可直接排放不会对周边环境造成污染。
10、 自动化水平
根据装置特点、生产控制要求采用较为先进的仪表控制系统。设计采用全自动控制、盘装表以及批量控制系统、对整个装置进行集中监视、控制及安全保护。确保水质的安全可靠。
11、 除氟过滤器