定向井螺杆泵抽油杆柱力学分析及防磨损措施
抽油机井杆管偏磨原因分析及防治措施

抽油机井杆管偏磨原因分析及防治措施抽油机井杆管是油田开采中的重要设备,其主要作用是将下面的油液抽到地面。
然而,在使用过程中,井杆管常常会出现偏磨现象,这种现象会严重影响设备的正常运行,甚至带来安全隐患。
因此,为了保障油田的正常生产,必须对抽油机井杆管偏磨进行分析和防治。
1、普遍磨损在抽油机井杆管工作的过程中,其表面会产生一定的磨损,这是一种正常的现象。
由于油泥中含有微小颗粒,抽油机井杆管在长时间使用后,其表面会逐渐被磨损。
这类现象普遍存在于使用时间较长的井杆管上。
2、轴向载荷不均轴向载荷不均是导致井杆管偏磨的主要原因之一。
在抽油机运转的过程中,由于油田地质条件和地面装备的差异等原因,井杆管所承受的载荷不是完全均匀的,而是存在一定的偏差。
这种偏差会导致井杆管产生一定的倾斜,从而出现偏磨。
3、水平运动不稳定抽油机井杆管在工作中,其水平方向的运动也很容易产生不稳定的情况。
当井杆管在水平方向上发生偏差时,其表面与钻井孔壁摩擦会增大,这种情况会加速井杆管的磨损,进而导致偏磨的产生。
1、优化井口设备井口设备是导致抽油机井杆管偏磨的重要因素之一。
为了降低其不稳定的运动状态,可以在井口区域安装合适的导向器和限位器,并合理安排布置井口设备。
2、控制水平动态控制抽油机井杆管的水平动态也很有必要。
可以通过在井口区域增加一定的支撑装置来达到控制井杆管垂直度的目的。
3、选择合适的材料为了延长抽油机井杆管的使用寿命,可以选择一些耐磨性能极佳的材料进行制造。
这样能够有效减缓井杆管表面的磨损速度,从而有效防止偏磨的发生。
4、及时维护保养为了保证抽油机井杆管的正常运转,应定期对设备进行维护、保养。
在进行维修时,要及时更换磨损严重的部件,避免设备使用过程中出现安全隐患。
总之,抽油机井杆管偏磨现象的发生对油田开采非常不利,应对该问题进行严肃认真的对待和解决。
利用一些科学的治理措施,能够在一定程度上延长设备的使用寿命,提高工作效率,为油田的生产带来更多的福利。
抽油机井杆管偏磨原因分析及防治措施

抽油机井杆管偏磨原因分析及防治措施一、引言抽油机是油田生产中的重要设备之一,它通过上下运动的井杆管从井下将油液送到地面。
由于井杆管在使用过程中会出现偏磨,导致其使用寿命减少,甚至影响正常的生产运行。
对于抽油机井杆管的偏磨原因进行分析,并提出相应的防治措施是非常重要的。
本文将对抽油机井杆管偏磨原因进行分析,并提出相对应的防治措施。
二、抽油机井杆管偏磨原因分析1. 润滑不良抽油机在运行时,井杆管会不断的上下运动,如果润滑不良,摩擦会增大,从而导致井杆管表面的磨损加剧,造成偏磨。
如果使用的润滑油质量不好,也会加速井杆管的磨损速度。
2. 杂质侵入在油田生产中,井下环境恶劣,很容易有杂质进入井杆管内部,这些杂质会在井杆管与其搭扣的接触部位造成磨损,导致偏磨的发生。
3. 井杆管使用寿命井杆管属于易损耗部件,长时间的使用和摩擦会导致其表面出现磨损,从而形成偏磨。
4. 操作不当在使用抽油机的过程中,如果操作不当,如过度加速或减速,会导致井杆管的磨损速度增加,从而形成偏磨。
5. 环境因素井下环境非常恶劣,地质条件复杂,可能存在地震、岩层崩塌等环境因素,这些都是导致井杆管偏磨的重要原因。
三、抽油机井杆管偏磨的防治措施1. 加强润滑管理针对润滑不良导致的井杆管偏磨问题,可以加强润滑管理,选择优质的润滑油,确保井杆管的良好润滑,减少摩擦,延长井杆管的使用寿命。
2. 定期清理井杆管内部为了防止杂质侵入导致的磨损,应该定期对井杆管内部进行清理,检查井杆管的磨损情况,并及时清除杂质,减少磨损。
3. 规范操作对于抽油机的操作人员,应该接受专业的培训,掌握正确的操作技巧,避免操作不当导致的井杆管磨损。
4. 加强检测定期对井杆管进行检测,发现磨损情况及时进行维修或更换,避免因井杆管磨损加剧导致偏磨。
5. 使用优质材料在制造井杆管时,选择优质的材料,提高井杆管的抗磨性能,延长其使用寿命。
6. 加强环境监测加强井下环境的监测,避免地震、岩层崩塌等环境因素对井杆管的磨损影响。
影响抽油井管杆偏磨的原因分析及治理措施

影响抽油井管杆偏磨的原因分析及治理措施
抽油井管杆偏磨是指管杆表面出现磨损现象,这会导致抽油井的工作效率下降,甚至会造成管杆断裂等严重安全事故。
影响抽油井管杆偏磨的原因主要有以下几个方面:
1. 高速旋转:抽油井的管柱在运行过程中会产生高速旋转的情况,这会导致管杆表面与井壁摩擦,增加了管杆的磨损。
2. 残留砂粒:油井开采过程中,地层中可能存在不同大小的砂粒,这些砂粒会随着油液一起被抽出井口,当油液通过管杆时,砂粒会与管杆表面摩擦,造成管杆偏磨。
3. 腐蚀杂质:井口附近可能存在一些腐蚀性杂质,如盐、酸等,这些杂质会侵蚀管杆表面,加剧管杆的磨损。
为了防止和治理抽油井管杆偏磨问题,可以采取以下几种措施:
1.选用高质量材料:选择耐磨性好的管杆材料,可以延长管杆的使用寿命。
2.安装井壁保护器:在管杆与井壁接触处安装井壁保护器,可以减少管杆与井壁直接接触,降低管杆的磨损程度。
3.定期清洗管杆:定期对管杆进行清洗,去除管杆表面的砂粒和腐蚀杂质,减少管杆的摩擦,并延长管杆的使用寿命。
4.优化设备运行参数:合理调整抽油井的运行参数,如调整抽采流量、减少振动等,可以降低管杆的磨损程度。
5.定期检修管杆:定期对管杆进行检修,发现管杆磨损严重的部位及时更换或修复,确保管杆的安全使用。
抽油井管杆偏磨是一个常见的问题,但通过采取适当的措施,可以有效地延长管杆的使用寿命,提高抽油井的工作效率,保障抽油井的安全运行。
抽油机井杆管偏磨原因分析及防治措施

抽油机井杆管偏磨原因分析及防治措施【摘要】抽油机井杆管的偏磨问题已经引起了广泛关注。
本文从偏磨原因分析和防治措施两个方面展开研究。
在偏磨原因分析部分,我们考虑了油井使用过程中可能出现的摩擦、磨损等因素,并提出了相应的解决方案。
在防治措施部分,我们介绍了采取合适的润滑措施、加强设备维护保养等方式来延长井杆管的使用寿命。
通过对抽油机井杆管偏磨问题的深入研究,可以为相关行业提供有效的指导和帮助。
希望本文的研究成果能够在实际生产中得到有效应用,为抽油机井杆管的维护提供有益参考。
【关键词】抽油机井杆管、偏磨、原因分析、防治措施、研究背景、研究意义、总结、展望1. 引言1.1 研究背景抽油机井杆管偏磨是油田开发中常见的问题,其主要原因包括井杆管与钻杆之间的磨擦,井口环境污染等因素。
对于抽油机井杆管的偏磨现象,不仅会影响油井的正常生产,也会增加油田的维护成本。
对抽油机井杆管偏磨的原因进行深入分析和防治措施的研究具有重要意义。
在油田开发过程中,抽油机井杆管偏磨问题已经引起了油田工程技术人员的高度关注。
但是目前对于抽油机井杆管偏磨的研究还比较有限,缺乏系统性的分析和防治经验的总结。
有必要对抽油机井杆管偏磨的原因进行深入探讨,并提出有效的防治措施,为油田生产提供技术支持和保障。
通过对抽油机井杆管偏磨的研究,可以有效提高油田的生产效率,降低生产成本,延长油田设备的使用寿命,促进油田的可持续发展。
对抽油机井杆管偏磨进行系统研究具有重要的理论和实际意义,对于提高油田生产效率和降低生产成本具有积极的促进作用。
1.2 研究意义抽油机井杆管偏磨是油田开采过程中常见的问题,如果不及时处理会对采油工作造成严重影响。
对于抽油机井杆管偏磨的研究具有重要的意义。
研究抽油机井杆管偏磨可以帮助我们深入了解其发生的原因及规律,从而指导我们采取有效的防治措施。
对抽油机井杆管偏磨进行研究可以提高油田开采效率,减少生产成本,增加经济效益。
随着油田开采技术的不断发展和需求的增加,对抽油机井杆管偏磨进行研究也有助于推动油田开采技术的进步和创新。
抽油机井杆管偏磨原因分析及防治措施

抽油机井杆管偏磨原因分析及防治措施一、引言抽油机井杆管在油田开采过程中扮演着非常重要的作用,它负责输送油气和水等物质,并承受着各种压力和磨损。
随着开采深度的增加和油田设备的老化,井杆管的偏磨现象也逐渐增多,严重影响了油田的生产效率和安全。
针对井杆管的偏磨问题,进行原因分析并提出防治措施,对于保障油田的正常开采具有重要意义。
本文将就抽油机井杆管偏磨的原因进行分析,并提出相应的防治措施。
二、抽油机井杆管偏磨原因分析1. 设备老化抽油机井杆管作为油田开采设备的重要组成部分,经过长期使用后,其表面会出现磨损和腐蚀,从而降低了其耐磨性能。
在这种情况下,井杆管容易出现偏磨现象,影响其使用寿命和运行效率。
2. 弯曲载荷在油田开采过程中,井杆管在输送油气和水的过程中会承受各种弯曲载荷,从而导致其表面受到不均匀的力量作用。
当井杆管承受过大的弯曲载荷时,容易引起局部磨损,最终导致偏磨现象的产生。
3. 润滑不良井杆管的运行会产生大量的摩擦热和磨损颗粒,而润滑不良会加剧磨损进而引发偏磨。
尤其是在重载工况下,井杆管容易出现润滑不良,从而加速了偏磨的发生。
4. 环境因素在油田的工作环境中,会受到各种环境因素的影响,例如沙尘、高温、潮湿等。
这些因素会导致井杆管表面受到腐蚀、磨损等影响,进而导致偏磨现象的产生。
5. 操作不当油田设备的操作不当也是造成井杆管偏磨的一个重要原因。
在操作过程中如果未及时发现和处理异常情况,就会导致井杆管磨损加剧,从而产生偏磨现象。
为了延长抽油机井杆管的使用寿命,必须加强设备维护工作。
定期对井杆管进行清洗和润滑,及时更换磨损严重的部件,保持井杆管的良好状态。
2. 提高材料耐磨性针对设备老化导致的偏磨现象,可以在材料选择上做出改进。
选择更耐磨的材料制作井杆管,提高其抗磨性能,从根本上减轻偏磨的发生。
改进润滑系统设计,加强对井杆管表面的润滑,降低摩擦系数,减少磨损,有利于减轻井杆管的偏磨现象。
4. 加强操作培训提高操作人员的技能水平,加强对设备操作和维护的培训,使其能够及时发现异常情况并采取有效措施,减少人为因素对井杆管偏磨的影响。
影响抽油井管杆偏磨的原因分析及治理措施

影响抽油井管杆偏磨的原因分析及治理措施1. 引言1.1 背景介绍抽油井是油田开发中常见的设备,使用抽油机将地下的原油抽送到地面。
而抽油井管杆作为连接地面和井底的重要部件,承受着巨大的工况压力和摩擦力。
在实际运行中,抽油井管杆常常出现偏磨现象,给井下作业带来了诸多问题。
抽油井管杆偏磨的背后隐藏着许多复杂的原因,包括润滑不足、井底砂粒对管杆的刮擦、井内腐蚀以及管杆过长等。
这些原因导致了管杆表面的磨损加剧,从而影响了抽油井的正常运行。
为了有效解决抽油井管杆偏磨问题,需要采取科学有效的治理措施。
提高润滑效果、使用抗磨涂层、加强管杆的检测和维护、优化管杆长度设计等方法都能在一定程度上减轻管杆偏磨的情况。
通过对影响抽油井管杆偏磨的原因进行分析和治理措施的研究,可以为抽油井的正常运行和维护提供重要的参考,也有助于提高油田开发的效率和生产水平。
【字数:239】1.2 问题提出抽油井管杆偏磨是油田生产过程中常见的问题,其严重影响着抽油井的正常运行。
管杆偏磨不仅会导致生产效率降低,还可能造成设备损坏,增加维护成本。
及时有效地控制管杆偏磨问题对于提高油田生产效率具有重要意义。
抽油井管杆偏磨的问题主要源于多种原因,包括润滑不足、井底砂粒对管杆的刮擦、井内腐蚀、管杆过长等因素。
这些原因相互作用,加剧了管杆的磨损程度,增加了管杆偏磨的风险。
针对这些原因进行深入分析并采取有效的治理措施显得尤为重要。
本文将从影响抽油井管杆偏磨的原因进行分析,结合润滑不足、井底砂粒刮擦、井内腐蚀和管杆过长等因素,探讨管杆偏磨问题的成因及其影响。
将提出相应的治理措施,包括提高润滑效果、使用抗磨涂层、加强管杆的检测和维护以及优化管杆长度设计等方法,以期降低管杆偏磨的风险,保障抽油井的正常运行。
1.3 研究意义抽油井是石油工业中至关重要的设备,管杆偏磨是抽油井在运行中常见的问题,会影响抽油效率并增加维护成本。
对影响抽油井管杆偏磨的原因进行深入分析并提出有效的治理措施具有重要的研究意义。
导致抽油井杆管偏磨的因素分析与治理对策

导致抽油井杆管偏磨的因素分析与治理对策抽油井杆管偏磨是指油井杆管在使用过程中,由于外力作用、磨蚀、腐蚀等因素导致管材表面出现磨损,进而影响井口设备的运行。
以下分析导致抽油井杆管偏磨的因素,并提出相应的治理对策。
1. 油井环境因素:油井环境复杂,存在高压、高温、强腐蚀性物质等因素,这些因素会对井口设备产生严重的腐蚀和磨损。
治理对策:选用耐腐蚀性能好的材料,如镍基合金、高硬度合金等,增加材料的防腐蚀性能,同时定期进行防腐蚀处理。
2. 异物进入井口:油井周围的环境存在大量的沙子、砂石等颗粒物,这些颗粒物可能会进入井口,在摩擦过程中对管材产生磨损。
治理对策:加装滤网或过滤器,防止颗粒物进入井口,定期清理井口周围的杂物。
3. 技术操作不当:操作人员在操作过程中,未掌握正确的操作技巧,如斜孔径向斜向钻进导致抽油杆扭曲;操作不当引起井口设备的过度振动等。
治理对策:加强操作人员的培训,提高其对设备操作的技术水平,制定严格的操作规程。
4. 设备故障:井口设备本身存在一定的设计与制造问题,如磨损、材料不合理、工艺不当等,导致井口设备在工作过程中产生异常磨损。
治理对策:对设备进行定期的检测和维护,发现问题及时修复或更换损坏部件,采用先进的工艺和材料提高设备的耐磨性能。
5. 油井压力过高:油井中的压力、流量等参数超过井口设备的承受能力,导致设备的磨损加剧。
治理对策:合理调整油井参数,控制好井筒内的压力和流量,减少设备的负荷。
6. 油井维护不及时:油井设备的维护保养是预防抽油杆管偏磨的重要措施,如果维护保养不及时,井口设备就容易发生故障,从而导致抽油杆管偏磨。
治理对策:制定完善的维护保养计划,定期对井口设备进行检测、保养和维修,及时更换磨损严重的部件。
抽油井杆管偏磨是一个复杂的问题,需要从多个方面分析和治理。
通过合理选材、加强操作技术、优化设备设计、合理调整油井参数以及及时维护保养,可以有效地减少抽油井杆管偏磨的风险,提高油井的运行效率。
抽油机井杆管偏磨原因分析及治理措施探讨

抽油机井杆管偏磨原因分析及治理措施探讨1. 杆管质量不合格:井杆管的原材料或制造工艺不达标,导致杆管的表面硬度不均匀、抗磨性较差。
此时,可通过加强杆管质量的检验和监控,确保杆管质量合格,并及时更换不合格的杆管。
2. 杆管与井筒之间的摩擦:杆管与井筒之间存在摩擦,加上长时间的运转,会导致杆管的偏磨现象。
治理措施包括:- 加大润滑剂的使用量:在井杆管与井筒的接触处增加合适的润滑剂,以减少摩擦力,并提高润滑效果。
- 优化操作技术:合理控制抽油机的运转速度和工作负荷,避免过大的负荷导致摩擦增大。
- 定期巡检维修:定期进行井下设备的巡检和维修,及时发现并处理存在的问题,以保证设备的正常运转。
3. 井下沙砾堵塞:井底存在大量的沙砾或杂质,容易造成井杆与井筒的摩擦增大,引起杆管的偏磨。
此时,适当采取以下治理措施:- 清洗井筒:定期清洗井筒,清理井底的沙砾和杂质,以减少摩擦。
- 井下过滤器的使用:在抽油机的井下位置设置过滤器,过滤掉大颗粒的杂质,减少其对杆管的磨损。
4. 抽油机安装不规范:抽油机的安装位置不准确或固定不牢固,会导致杆管与井筒之间有较大的摩擦力,引起偏磨。
应采取以下措施进行治理:- 定期检查抽油机的安装情况:确保其位置准确且固定牢固,避免出现倾斜或摇动的情况。
- 加强固定措施:增加安装固定的紧固件,加强抽油机的固定力度,并定期检查其是否松动。
5. 工作环境条件恶劣:井下环境条件差,如温度、湿度较大、粉尘多等,也可能会导致杆管的偏磨现象。
在此类环境下,应采取以下措施:- 加强设备维护:定期检查设备的工作状态和维护情况,确保其正常运转。
- 防护设备的使用:增加防护设备,如防尘罩、防潮罩等,保护设备不受恶劣环境的影响。
针对抽油机井杆管偏磨的原因分析及治理措施,应根据具体的情况进行综合考虑和选择合适的措施进行治理。
定期的巡检和维护工作也是确保设备正常运转和延长使用寿命的重要措施。
抽油机井杆管偏磨原因分析及防治措施

抽油机井杆管偏磨原因分析及防治措施
抽油机井杆管是油田开采过程中使用的重要设备之一。
由于井杆管的长期使用,其表
面会因为各种原因而磨损,从而影响油井的生产效率。
本文将分析抽油机井杆管偏磨的原因,并提出相应的防治措施。
1. 吊卡调整不当:井杆管安装在油井中是需要吊卡协助的,如果吊卡调整不当,会
导致井杆管直线度不够,产生摩擦,从而使井杆管表面磨损。
2. 载荷不均:油井生产过程中由于液体比气体密度大,常常会受到油液的重压,这
种载荷极不均匀,导致井杆管不均匀磨损。
3. 井深过浅:由于油井井深和井杆管直径关系密切,如果井深过浅,就会导致井杆
管的受力不均匀,表面易产生磨损。
4. 氧化:井杆管在油井内长时间暴露在高温高压的环境下,会发生氧化反应,导致
表面变硬,表面松散物质和垃圾附着等情况,从而使井杆管表面磨损加剧。
2. 控制载荷:在油井生产过程中,需要控制载荷均匀性,采取一些措施,比如调整
油液流量,使油液与气体的比例适当,保证混合物的均匀性,从而减少井杆管的磨耗。
3. 选用适当井深:根据井杆管的直径,选择适当的井深,从而保证井杆管受力均匀,避免表面磨损加剧。
4. 做好防腐保护:涂上先进的防腐护理漆或涂覆亚铁氧化物,从而有效抗氧化,可
延长井杆管使用寿命,减少表面磨损。
总之,抽油机井杆管偏磨是油井生产过程中常见问题之一,可对照以上原因和防治措
施进行排查和改进,从而保证井杆管的正常使用和生产效率。
抽油机井杆管偏磨原因分析及防治措施

抽油机井杆管偏磨原因分析及防治措施在油田开发中,抽油机井杆管是连接地表和地下油井的重要设备,其主要作用是将井口与地下油层连接起来,实现油井的抽油作业。
在使用过程中,井杆管常常会出现偏磨现象,导致井杆的寿命减少、生产效率下降,甚至引发事故,因此需要对该问题进行分析和防治措施的研究。
分析抽油机井杆管偏磨的原因。
主要原因可以归纳为以下几点:1. 油井工艺问题:油井开发中,井杆管在井口与地下油层之间会受到巨大的拉力和扭矩,同时水的冲刷和携带垂直向下运动的砂粒对井杆管也会产生冲击和磨损。
如果井口设计不合理,或者井底油层存在砂粒较多的情况,都会加剧井杆管的磨损。
2. 井杆材料问题:抽油机井杆管通常采用碳钢或者合金钢制造,这些材料在使用过程中会受到腐蚀和磨损的影响。
特别是在油水界面处,会产生电化学反应,使得井杆管受到腐蚀。
井杆管在使用过程中还会承受不同程度的冲击和摩擦,导致材料表面的磨损和松动,从而加剧偏磨现象。
3. 润滑不良:井杆管在使用过程中需要润滑剂的保护,以减少磨损和摩擦。
在实际操作中,由于时间限制或者人为疏忽,往往会导致润滑不及时或者不足,从而使井杆管无法得到有效的保护,进而出现偏磨现象。
针对抽油机井杆管偏磨现象,可以采取以下的防治措施:1. 定期检查和维修井口:井口是油井与地表连接的关键部位,其设计是否合理对井杆管的偏磨具有重要影响。
需要定期检查和维修井口,确保井口的结构完整和符合要求,减少井口对井杆管的冲击和磨损。
2. 选择合适的井杆材料:在制造井杆管时,应根据油井的工况和环境条件选择适合的材料,尽量采用抗腐蚀能力较强的合金钢,以减少井杆管的腐蚀和磨损。
3. 合理使用润滑剂:井杆管在使用前应进行润滑处理,选择适当的润滑剂,确保其能够在使用过程中提供足够的润滑效果,减少井杆管的摩擦和磨损。
并且,需要注意及时更换和补充润滑剂,以保证井杆管的持续润滑效果。
4. 加强培训和管理:在油田开发过程中,需要加强对操作人员的培训,增强其对抽油机井杆管偏磨问题的认识和理解,在操作过程中严格按照操作规程进行操作。
导致抽油井杆管偏磨的因素分析与治理对策

导致抽油井杆管偏磨的因素分析与治理对策抽油井是非常重要的石油开采设备,其正常运行对于石油生产具有重要意义。
在日常生产中,我们经常会发现抽油井杆管出现偏磨现象,这不仅会影响井下设备的寿命,还会导致生产能力下降,甚至停产,给整个油田的生产造成严重影响。
对于抽油井杆管偏磨的原因进行深入分析,并提出相应的治理对策,是非常必要的。
本文将对导致抽油井杆管偏磨的因素进行分析,并提出相应的治理对策。
一、导致抽油井杆管偏磨的因素分析1. 抽油井杆管质量问题抽油井杆管是承受地层压力和机械运动力的关键部件,材料的质量直接影响到其抗压性能和耐磨性。
如果材料质量不达标,会导致杆管表面易发生磨损,甚至出现裂纹,从而影响整个井下设备的正常运行。
2. 抽油井杆管运行状态问题抽油井杆管在运行过程中,受到地层压力和机械运动力的作用,很容易出现疲劳破坏,尤其是在井口和井下弯头处,更容易发生偏磨。
如果抽油井杆管在运行过程中出现振动、摆动等异常情况,也会加剧其表面磨损。
3. 润滑不良在抽油井的运行过程中,润滑是非常关键的一环,好的润滑可以降低杆管的磨损。
否则,会导致摩擦增加、磨损加剧,进而导致杆管偏磨。
4. 环境因素抽油井在不同的地质环境中运行,地层的硬度、地质条件、油田开采方式等都会对抽油井杆管的磨损产生影响。
例如在产量较大的地层中运行,地层对杆管的磨损会更加明显。
二、抽油井杆管偏磨的治理对策1. 严格抽油井杆管的质量管理在使用抽油井杆管前,需要严格进行质量检查,选用质量可靠的杆管,并在正常生产中进行定期检测,及时发现问题,进行更换和维修。
2. 加强抽油井杆管的运行状态监测定期对抽油井杆管的运行状态进行监测,一旦发现异常情况,及时采取措施,避免杆管出现过多磨损。
3. 合理选用润滑材料在抽油井杆管的运行中,使用质量可靠的润滑材料,合理注滑,能有效降低杆管磨损程度。
4. 优化抽油井运行环境通过优化井口设计和加强管道支撑,减小抽油井杆管的振动和摩擦力,减少杆管磨损。
抽油机井杆管偏磨原因分析及防治措施

抽油机井杆管偏磨原因分析及防治措施随着石油工业的发展,抽油机在油田开采中发挥着重要作用。
而井杆管是抽油机的重要部件之一,但在实际生产中,井杆管偏磨的问题时有发生,给油田生产带来了很大的困扰。
本文将从井杆管偏磨的原因分析及防治措施做一详细的探讨。
一、井杆管偏磨的原因分析1.井杆管材质选择不当井杆管通常由碳素钢或合金钢制成,但在材质选择不当的情况下,容易造成井杆管的磨损。
在含有酸性气体或盐水的环境下,应选用耐腐蚀的材质,否则容易导致井杆管的腐蚀磨损。
2.井杆管表面硬度不足井杆管表面硬度不足会导致井杆管易受损,表面磨损严重。
这通常与制造过程中的材料选择、加工工艺等有关。
3.井杆管内外径尺寸不准确井杆管内外径尺寸不准确会导致井杆管与其他配件的配合不良,摩擦增大,磨损加剧。
4.井杆管长期使用磨损积累井杆管在长期使用中,由于受到磨损和冲击的影响,表面会出现不同程度的磨损,如果不及时进行修复或更换,就会导致井杆管偏磨。
5.井杆管油膜磨损井杆管在油田生产中,由于运动部件在高速运转时,由于摩擦产生的热量,易造成油膜磨损,进而导致井杆管偏磨。
二、井杆管偏磨的防治措施1.加强材质选择与质量检查在选择井杆管的材质时,应根据具体使用环境选择耐磨耐腐蚀的材质,并加强对原材料的质量检查,确保井杆管的材质符合要求。
2.提高井杆管表面硬度可以通过表面硬化、热处理等工艺,提高井杆管的表面硬度,减小磨损,延长使用寿命。
4.定期检查与维护定期对井杆管进行检查,及时发现磨损或损坏情况,及时进行维护或更换,减小井杆管的磨损程度。
5.加强润滑保养在使用过程中,加强润滑保养,保持井杆管表面油膜的完整性,减小磨损程度。
通过采取以上防治措施,可以有效减缓井杆管的偏磨问题,提高井杆管的使用寿命,保证油田的正常生产。
井杆管偏磨问题的发生主要是由于材质选择不当、表面硬度不足、尺寸不准确、长期使用磨损积累以及油膜磨损等原因所导致。
针对这些问题,提出了加强材质选择与质量检查、提高表面硬度、严格控制尺寸、定期检查与维护以及加强润滑保养等防治措施。
科技成果——定向井井眼抽油井管杆防偏磨技术

科技成果——定向井井眼抽油井管杆防偏磨技术
技术开发单位
中石化江苏油田分公司
适用范围
定向井、水平井
成果简介
油田定向井机抽生产中,油管和抽油杆之间会产生摩擦损坏。
该技术通过改变抽油杆和油管之间的摩擦副和摩擦材料,以减小摩擦系数,并优化杆柱组合以减少抽油杆与油管之间的点接触或面接触,尽可能避免抽油杆柱的受压变形以减小正压力,从而降低抽油杆和油管之间的摩擦损坏。
工艺技术及装备
1、抽油杆柱井下应力检测技术;
2、抽油杆柱三维力学分析与优化设计技术;
3、系列新型防偏磨工具。
市场前景
该技术在实际应用中取得了很好的效果,全面推广后,必将很大程度地减少因管、杆偏磨造成的经济损失,并有利于推动有杆泵抽油技术的进步和发展。
目前中石化股份有限公司共有机械采油井3万多口,油井普遍存在管杆偏磨现象,如果在各油田全面推广防偏磨新技术,每年将减少维护作业费用和管杆更换费用约7亿元,将产生巨大的经济效益,具有广泛的推广应用价值。
抽油机井杆管偏磨机理及防治对策

抽油机井杆管偏磨机理及防治对策归纳了抽油机井杆管磨损的一些主要成因,并对这些成因如井斜、杆管组合、管柱结构及生产参数不合理等进行了分析,且提出了合理防治对策。
标签:井杆管;偏磨;防治;对策1影响抽油机井杆管磨损的因素1.1井身结构原因生产井包括直井和斜井两种,对于斜井这一特殊类型的井,在造斜点一定范围内,油管是弯曲的,由于造斜点距井日较近,抽油泵一般都安在造斜点以下,由于重力等原因,在泵到泵上一段距离内抽油杆与油管必然发生偏磨,导致杆管偏磨。
直井由于目前技术限制,在钻井过程中,随着钻井深度的增加,钻头与井口同度变差,井筒出现自然井斜,造成杆管磨损。
1.2“失稳”对偏磨的影响分析下杆、管在上、下冲程过程中每一点的受力状况。
在上冲程过程中,杆柱每一点受向上的拉力、该点以下杆柱在液体中的重力、该点以下杆柱在上行中与液体的磨擦力、活塞与泵筒的磨擦力。
由于向上的拉力远大于其它向下的阻力,因此,杆柱在向上的拉力作用下向上运动,完成上冲程。
在这个运动过程中,杆柱每一点的合力都是向上,杆柱被拉直,不会发生偏磨现象。
在下冲程过程中,油管每一点的合力都是向下,油管被拉直,不会发生偏磨现象。
杆柱每一点的受该点以下杆柱在液体中的重力,杆柱下行时与液体磨擦产生的向上的阻力,活塞与泵筒磨擦产生的向上的阻力,该点以上杆柱在液体中的重力作用于该点形成的向下的压力。
下冲程时各点受力比较复杂,而且处于变化中,下冲程运动开始时,还受到杆柱向上的惯性力的作用。
各点合力向下,杆柱向下运动。
中性点以下的抽油杆,由于该点以下杆柱的重力较小,不足于克服其它各种向上的阻力,而该点以上杆柱的重力较大,作用于该点形成向下的压力较大,下部杆柱在强大的压力作用下完成下冲程,容易弯曲变形,发生偏磨现象。
由于杆柱的塑性较强,上部的重力不会很快对下部形成压力,而下部杆柱在上冲程的惯性力作用下还在向上运动,大大增加了中下部杆柱的弯曲程度,杆柱发生弯曲的这种现象,我们称为“失稳”。
抽油井井下管杆偏磨因素分析及预防方法
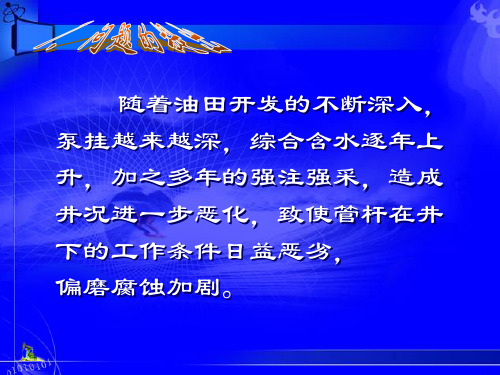
抽油杆本体与油管的偏磨
偏磨多发生在∮19抽油杆, 发生这种偏磨的主要原因是抽 油杆在下冲程时受泵活塞阻力 的影响而发生弯曲,致使杆体 与油管内壁相摩擦,一般表现 在单面磨损。
由于抽油机井在上行程中,抽油 杆受拉,因此不存在弯曲,而在下行 程中,由于抽油杆受压,当压力达到 一定值时,使抽油杆失稳,造成抽油 杆产生屈曲,导致抽油杆与油管偏磨 所以我们重点研究抽油杆在下行程中 的受力状态。
[90,95)
85 5 5.88 105 14 13.33 116 13 11.21 115 17 14.78 421 49 11.64
[95,100]
107 4
3.74 153 10 6.54 127 10 7.87 257 29 11.28 644 53 8.23
74.40%
2.3 抽油杆偏磨深度的统计
[75,80)
173 6
3.47 149 15 10.07 160 14 8.75 152
9 5.92 634 44 6.94
[80,85) [85,90)
242 9
3.72 261 27 10.34 263 30 11.41 230 14 6.09 996 80 8.03
158 8
5.06 203 24 11.82 215 31 14.42 259 25 9.65 835 88 10.54
部位主要集中在抽油杆柱中下部600-
1000m部位。
3.2不同沉没度区间杆管偏磨率的分布规律
年度
项目
2003 2004 2005 2006 总计
总井数(口) 偏磨井数(口)
偏磨率(%) 总井数(口) 偏磨井数(口) 偏磨率(%) 总井数(口) 偏磨井数(口) 偏磨率(%) 总井数(口) 偏磨井数(口) 偏磨率(%) 总井数(口) 偏磨井数(口) 偏磨率(%)
导致抽油井杆管偏磨的因素分析与治理对策
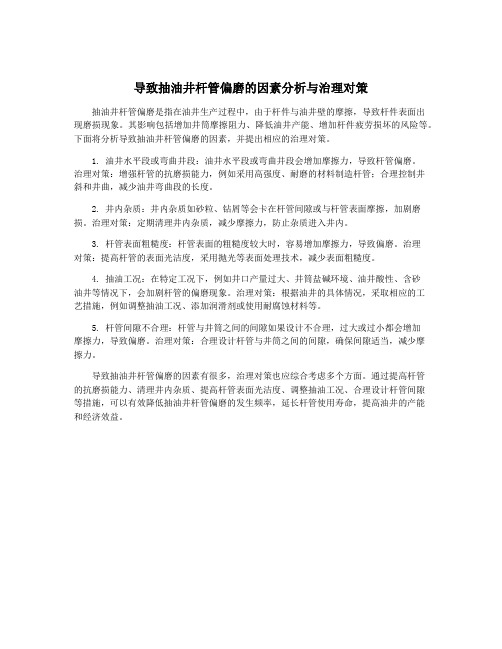
导致抽油井杆管偏磨的因素分析与治理对策抽油井杆管偏磨是指在油井生产过程中,由于杆件与油井壁的摩擦,导致杆件表面出现磨损现象。
其影响包括增加井筒摩擦阻力、降低油井产能、增加杆件疲劳损坏的风险等。
下面将分析导致抽油井杆管偏磨的因素,并提出相应的治理对策。
1. 油井水平段或弯曲井段:油井水平段或弯曲井段会增加摩擦力,导致杆管偏磨。
治理对策:增强杆管的抗磨损能力,例如采用高强度、耐磨的材料制造杆管;合理控制井斜和井曲,减少油井弯曲段的长度。
2. 井内杂质:井内杂质如砂粒、钻屑等会卡在杆管间隙或与杆管表面摩擦,加剧磨损。
治理对策:定期清理井内杂质,减少摩擦力,防止杂质进入井内。
3. 杆管表面粗糙度:杆管表面的粗糙度较大时,容易增加摩擦力,导致偏磨。
治理对策:提高杆管的表面光洁度,采用抛光等表面处理技术,减少表面粗糙度。
4. 抽油工况:在特定工况下,例如井口产量过大、井筒盐碱环境、油井酸性、含砂油井等情况下,会加剧杆管的偏磨现象。
治理对策:根据油井的具体情况,采取相应的工艺措施,例如调整抽油工况、添加润滑剂或使用耐腐蚀材料等。
5. 杆管间隙不合理:杆管与井筒之间的间隙如果设计不合理,过大或过小都会增加摩擦力,导致偏磨。
治理对策:合理设计杆管与井筒之间的间隙,确保间隙适当,减少摩擦力。
导致抽油井杆管偏磨的因素有很多,治理对策也应综合考虑多个方面。
通过提高杆管的抗磨损能力、清理井内杂质、提高杆管表面光洁度、调整抽油工况、合理设计杆管间隙等措施,可以有效降低抽油井杆管偏磨的发生频率,延长杆管使用寿命,提高油井的产能和经济效益。
定向井螺杆泵抽油杆柱力学分析及防磨损措施

目前 , 杆 泵 采 油 技 术 在 直 井 中 的应 用 已经 比较 成 螺 熟” , j但在定 向井 中的应 用还 较 少 , 目前 为止 未 见相 关报 道 。定 向井较直井的井身 结构及 受力情 况更为 复杂 , 柱 的 杆 造斜 段在重力的作用下不可避免地与油管壁发生接触。根据 定 向井的井眼轨迹特性知 , 油杆在做旋 转运 动的过 程中处 抽 于纵横 弯曲状 态 , 这使杆 柱更 易磨损 和断脱。为避 免或 减缓 这种 现象 , 本研 究建立了定 向井螺杆泵抽油杆柱力学模型 , 提 出了合理 布置导 向器及 扶正 器的技术 措施 , 为防止 抽油杆 柱 磨损提供理论指导Mesrs f i u eapr u t e etnpi f h d n sr hnui rg s n ai pm dt p i e n ei y t o om l aue Ln gi paa sa dfc o n o er f o xg d t l i o t t o
D et l p ca t cueo oto e i ci el t a ed t e e ̄a r in ee amnn o u otese i sr tr fcnrl ddr t n w l,i c nla o sv l b a o vn iI lg i n t ̄o t i a y l l u l e o s f p r n ig
维普资讯
第3 4卷 第 4期
20 0 6年 7月
东
北
林
业
大
学
学
报
Vo . 4 No 4 13 .
J OURNALOF N ORT AS O HE T F REs Y UN VE I Y 1 I RST
J1 O 6 u.2 O
式中 : 为泵进 出口压差产生 的反扭矩 ( i) e N・n ; 为转子 偏 心距 ( m) D为转子直径 (n ; m ; i) T为定子 导程(n 。 i) 由于定 向井在造 斜点 以下存 在不 同程 度 的“ 狗腿角 ” 现 象, 必须在抽油杆柱上安装扶 正器 , 以避免抽油杆与油管壁接 触摩擦而损坏 抽 油杆。 由于扶正 器较 短且 与 油管 的 间隙很 小, 对抽油杆来说相 当于活动铰支座 , 取造斜点附近两个相邻 扶正器之间的一跨作为研 究对象 。其 力学模 型如 图 2所 示 , 抽油杆主要受重力 、 体 的摩 擦 阻力 矩 J 主 动力 矩 液 I l f 以及 轴向拉力 等作用 。
抽油机井杆管偏磨原因分析及防治措施

抽油机井杆管偏磨原因分析及防治措施抽油机井杆管是油田采油工程中的重要设备,经常会出现杆管磨损严重的情况。
杆管的磨损会导致泵的工作效率下降,耗能增加,甚至会引发泵杆断裂等严重后果。
因此,对抽油机井杆管的偏磨原因进行分析,并采取相应的防治措施对于油田生产具有重要意义。
一、偏磨原因分析1.1 杆管内部接触磨损抽油杆在工作过程中,会在杆管内部不断向上下运动。
由于摩擦力的存在,在运动过程中,杆管内部接触面处容易发生磨损。
这种磨损在下行时最为明显,其原因是由于井液的黏度随温度升高而下降,而下行过程中,液体上移导致井口液体温度升高,黏度下降,杆管受到井液下压力的影响被向下拉动,从而产生强烈的磨损。
1.2 杆管外部机械磨损由于地形起伏,抽油杆在井筒内不断横向摆动,杆管与井筒之间产生摩擦力,导致杆管外部产生机械磨损。
1.3 杆管与泥浆接触磨损在井筒施工过程中,井壁腐蚀不良,泥浆不充分等原因,会导致泥浆中的细沙、碎石等硬颗粒物料与杆管接触,产生摩擦力,从而导致杆管与泥浆接触部位产生磨损。
1.4 泵口负压磨损当泵口内网目滤芯粘满或泥浆中杂物较多,导致泵口出现明显的噪声,说明抽油杆已被负压拉直而与井筒接触。
此时,抽油杆随泥浆流动运行,容易发生磨损。
二、防治措施2.1 加强井口液体温度调控为了减少下行时杆管内部接触磨损的产生,可采用调整井口液体温度的方法。
根据井口实际温度,通过适时调整泵入口和出口的附加装置,可控制井口液温,降低井下磨损。
2.2 防止杆管外部机械磨损为了防止杆管外部机械磨损,可采用加固井眼的方法。
通过对井眼进行加固,减少地形起伏和杆管摆动的程度,可以有效减少机械磨损。
2.3 采用合适强度的杆管选择合适强度、硬度较高的杆管可有效减少杆管与泥浆接触磨损的程度。
常用的防磨损材料包括金属涂层、碳化硅、氮化硅等。
2.4 如实测量井深度和泵位置在井斜段,由于抽油杆的重量引起呈锯齿形状的橡胶垫圈变形和运动,因此应准确测量井深度和泵位置,以防止泵口于杆管接触后产生磨损。
- 1、下载文档前请自行甄别文档内容的完整性,平台不提供额外的编辑、内容补充、找答案等附加服务。
- 2、"仅部分预览"的文档,不可在线预览部分如存在完整性等问题,可反馈申请退款(可完整预览的文档不适用该条件!)。
- 3、如文档侵犯您的权益,请联系客服反馈,我们会尽快为您处理(人工客服工作时间:9:00-18:30)。
定向井螺杆泵抽油杆柱力学分析及防磨损措施
摘要:定向井本身的井身结构比较特殊,因此在实际作业的过程中采取螺杆泵
抽采方式如果不能采取合理的措施,很容易导致柱杆出现严重的磨损甚至出现卡
死等现象。
为了能够有效消除柱杆在实际抽采作业中出现的磨损等问题,针对抽
油杆造斜点设置了相应的导向器,并在合理的位置配套使用扶正器等相关的措施,在实际确定扶正器合理的位置的时候主要是通过建立模型进行分析计算得出。
这
种方式在抽采现象的应用中得到了广泛应用。
关键词:定向井;螺杆泵;管杆磨损;扶正器
引言
在直井的抽采作业中螺杆泵抽采工艺的应用已经逐渐趋于成熟,但是螺杆泵
抽采工艺在定向井中的应用比较少,对此的相关研究也比较少。
与直井相比较定
向型本身的结构以及井身受力情况都更加复杂,当处于造斜段的时候,感触非常
容易受到重力作用与油管壁发生接触。
根据定向井本身井眼轨迹具体特征可以知道,螺杆泵在抽采作业过程中抽油杆的旋转运动使得在纵横方向上出现了弯曲状态,这样就非常容易导致感度出现损坏或者是断脱等现象。
为了能够最大程度避
免这种现象的出现,本文主要通过建立抽油杆的力学模型,并通过模型分析计算
对导向器以及扶正器的布置方式进行了合理研究。
1 抽油杆柱受力情况分析
螺杆泵的抽油杆在实际作业这个过程中主要是通过地面动力端来进行扭矩传递,并以此来带动驱动轴旋转,驱动头经过减速处理之后通过方卡子将扭矩传递
到光杆上,最终将扭矩传递到抽油杆柱上面。
通过分析可以知道在井口位置抽油
杆柱实际受到的是主动力矩的作用,在旋转作业过程中同时还会受到走向产生的
力F,在举升液体的过程中不会受到一个摩擦力矩,此外,转子与电子之间由于
采取的是过盈配合,因此两者之间也会产生还会产生一个摩擦力,在泵的出口位
置由于会存在一定的压差,因此也会在抽油杆柱上产生的反扭矩。
上述几个参数
可以通过以下计算公式来进行计算。
上述公式中R主要表示的是转子截面半径,m;e主要表示的是转子的偏心距m;主要表示的是在泵进出口产生的压差,Pa;
上述公式中主要表示的是定转子之间在初始状态下的过盈值,mm;n主要表
示的是在螺杆泵在运行过程中的转速,r/min;
上述公式中主要表示的是井下液体动力粘度,Pa·s;主要表示的是油管的内径,m;d主要表的是抽油杆直径,如果都抽油杆本身是空心抽油杆,那么d主
要表示的就是其外径,m。
上述公式中,e主要表示的是转子偏心距,mm;D主要表示的是转子的直径,m;T主要表示的是定子实际的导程,m[1]。
在定向井的抽采过程中,处于造斜点以下的定子都会在不同程度上出现“狗腿角”现象,因此必须要合理的利用扶正器来进行辅助,这样才能有效避免其在转动过程中导致抽油杆与油管壁产生连续摩擦从而出现破坏现象。
而扶正器本身的距
离较短,而且其余油管之间的间隙也非常小,如果在抽油杆上安装扶正器之后,
就相当于为抽油杆设置了一个活动的铰支座,选择造斜点位置附近的两个扶正器
作为主要研究对象,然后来建立起两者之间的力学模型,如下图1所示。
图1 造斜点附近杆柱力学模型
2 杆柱力学模型分析
通过建立有线源分析模型,将油管整体部分以及杆柱作为主要研究对象,将
井底部分作为原点。
在针对井口位置抽油杆柱实际所受到的主动力矩进行计算的
过程中,可以通过将其进一步简化成随着时间而不断变化的旋转角位。
电极所产
生的扭矩主要是通过方卡子来传递到光杆上,而抽油杆在制作上作用的走向力主
要是通过卡子来进行传递,鉴于此,就可以针对井口的边界条件进行进一步简化
之后,将其当成是扭矩角速度的已知边界,而将其他的所有条件都设定为固定边
界[2]。
3 合理布置扶正器及导向器
针对所建立的杆柱模型充分利用ANSYS有限元分析软件进行分析计算,就精
确的计算出杆柱在与油管内部实际产生的变形状况以及两者之间的接触情况进行
精确计算。
在实际针对扶正器及导向器进行合理布置的过程中,接触率以及渗透
量是两个最为主要的依据参数。
利用ANSYS有限元分析软件进行精确计算处理之后,就可以精确的得出接触率以及渗透量。
通过计算可以发现接触力和渗透量之
间呈现出正比例关系,而如果两者接触的地方存在“狗腿角”那么其实际的接触率
以及渗透量要比其他部位都高。
针对计算过程中所产生的最大渗透量位置可以合
理的布置导向器,而针对油管与杆柱存在地方要合理的布置扶正器,在此基础上
再进行详细计算,并针对扶正器位置进行合理调整,充分保证其不存在接触,而
且在接触位置的渗透量不能超过油管壁厚。
如果杆柱在实际作业过程中仅仅存在一个造斜点,为了能够进一步提升杆柱
实际的工作状态,应该完全忽略全角变化率,并相应的设置导向器。
如果杆柱在实际作业过程中会涉及到多个造斜点,而且没25m井段实际的全
角变化率超过了30,则可以针对25m全角变化率非常接近30的时候设置导向器,而针对25m全角变化率超过40的情况,则必须要设置导向器。
针对全角变化率相对比较大的位置设置导向器之后,必须要在间隔为8米的
距离设置一个扶正器,而针对造斜段则必须要严格的按照间隔6米来相应的设置
扶正器[3]。
4 结束语
定向井螺杆泵抽油杆柱在实际作业过程中,造斜段经常会因为重力作用而与
油管之间产生摩擦,非常容易导致杆柱出现损坏现象。
针对抽油杆柱建立相应的
力学模型之后,并通过ANSYS有限元分析软件进行精确计算,最终实现了在抽油
杆柱上合理的布置导向器和扶正器。
参考文献
[1]林骏.水平井螺杆泵举升系统参数优化设计及软件开发[D].燕山大学,2017.
[2]苗新蕾,胥宏峰,孙庆义.定向井螺杆泵采油技术[J].大庆石油学院学报,2006(04):36-38+147.
[3]董世民,张万胜,王强,柴国鸿,苏艳玲.直井地面驱动螺杆泵采油杆管偏
磨机理[J].石油学报,2012,33(02):304-309.。