中间轴式变速器设计
中型货车变速器设计(三轴式)
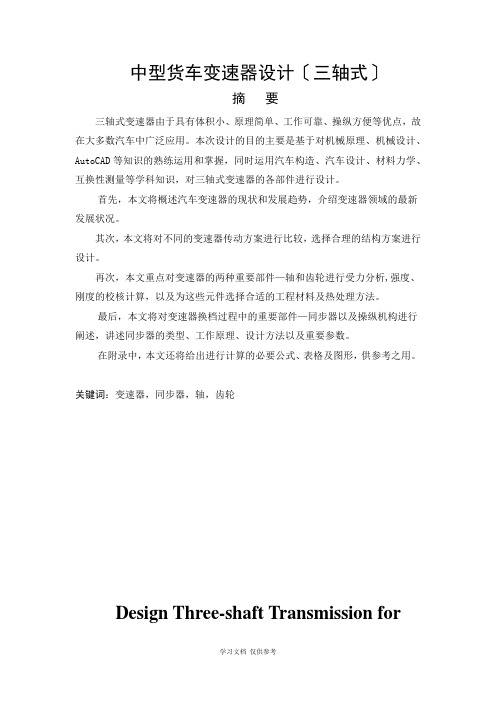
中型货车变速器设计〔三轴式〕摘要三轴式变速器由于具有体积小、原理简单、工作可靠、操纵方便等优点,故在大多数汽车中广泛应用。
本次设计的目的主要是基于对机械原理、机械设计、AutoCAD等知识的熟练运用和掌握,同时运用汽车构造、汽车设计、材料力学、互换性测量等学科知识,对三轴式变速器的各部件进行设计。
首先,本文将概述汽车变速器的现状和发展趋势,介绍变速器领域的最新发展状况。
其次,本文将对不同的变速器传动方案进行比较,选择合理的结构方案进行设计。
再次,本文重点对变速器的两种重要部件—轴和齿轮进行受力分析,强度、刚度的校核计算,以及为这些元件选择合适的工程材料及热处理方法。
最后,本文将对变速器换档过程中的重要部件—同步器以及操纵机构进行阐述,讲述同步器的类型、工作原理、设计方法以及重要参数。
在附录中,本文还将给出进行计算的必要公式、表格及图形,供参考之用。
关键词:变速器,同步器,轴,齿轮Design Three-shaft Transmission forMedium-duty TruckAuthor: Li BijunTutor:Lei ZhengbaoAbstractThree-shaft transmission is widely used most vehicle for its particular advantages ,such as small dimension ,simply theory ,good stability, conveniently operation .The purpose of my paper is based on the skillful of using mechanic theory ,mechanic design, AutoCAD. Meanwhile, my paper is incorporated structure of vehicle, design of vehicle, mechanic of materials, and survey of interchangeability. I will design the parts of three-shaft transmission.At first, I will give a summary of the current situation and the tendency of development of the vehicle transmission, and introduce the latest development state in the field of the transmission.The second, I will compare the transmitting scheme of different transmission, and choose a better structure scheme.Next, I will do some mechanic analyses, strength, stiffness check of the shafts and gears, which are the important parts of the transmission, and choose appropriate materials and heat treatment.At last, I will introduce the operation mechanism and the synchronizer, which plays an important role in changing gear. I will give an account of the type, operation, design procedure and major parameter of the synchronizer.At the supplement, I will write some thing like formula, tableau graph and so on. It may be helpful for the future design.Key words: Transmission, Synchronizer, Shaft, Gear目录1 绪论 (1)1.1变速器的设计意义及背景 (1)1.2变速器的现状及发展趋势 (2)1.3变速器的设计方法和研究内容 (5)2 变速器结构方案的设计 (6)2.1两轴式和三轴式变速器 (6)2.2齿轮安排 (7)2.3换档结构方式 (8)2.4倒档的结构方案及倒档轴的位置 (8)3 变速器轴的设计 (10)3.1轴的设计 (10)3.2轴的受力分析与校核计算 (13)4 变速器齿轮的设计 (21)4.1齿轮传动的失效形式 (21)4.2 变速器齿轮设计步骤 (22)4.3各档齿轮齿数的分配 (26)4.4 齿轮的材料及其选择原则 (31)4.5圆柱齿轮强度的简化计算方法 (33)5 同步器设计 (39)5.1惯性式同步器 (39)5.2同步器工作原理 (42)5.3同步器的主要参数确实定 (42)6 变速器操纵机构 (46)6.1操纵机构的功用 (46)6.2 换档位置图 (46)6.3变速杆的布置 (46)6.4锁止装置 (47)结论 (51)致谢 (52)参考文献 (53)附录 (54)1 绪论1.1变速器的设计背景及目的现代汽车的动力设置,几乎都采用往复活塞式内燃机。
车辆工程毕业设计101九档双中间轴变速器
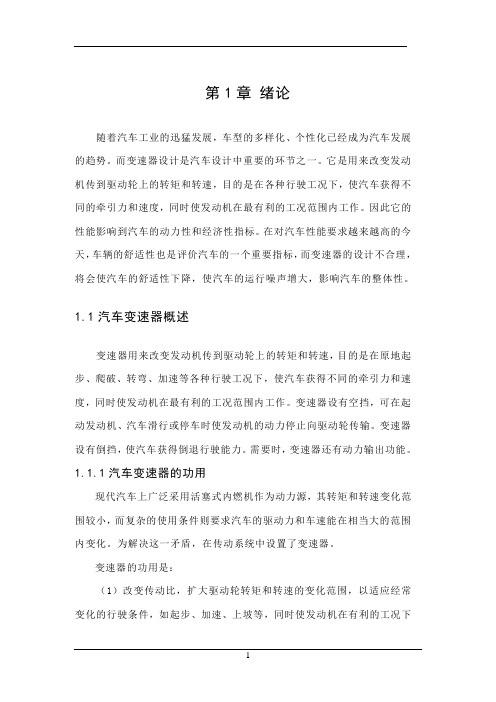
第1章绪论随着汽车工业的迅猛发展,车型的多样化、个性化已经成为汽车发展的趋势。
而变速器设计是汽车设计中重要的环节之一。
它是用来改变发动机传到驱动轮上的转矩和转速,目的是在各种行驶工况下,使汽车获得不同的牵引力和速度,同时使发动机在最有利的工况范围内工作。
因此它的性能影响到汽车的动力性和经济性指标。
在对汽车性能要求越来越高的今天,车辆的舒适性也是评价汽车的一个重要指标,而变速器的设计不合理,将会使汽车的舒适性下降,使汽车的运行噪声增大,影响汽车的整体性。
1.1汽车变速器概述变速器用来改变发动机传到驱动轮上的转矩和转速,目的是在原地起步、爬破、转弯、加速等各种行驶工况下,使汽车获得不同的牵引力和速度,同时使发动机在最有利的工况范围内工作。
变速器设有空挡,可在起动发动机、汽车滑行或停车时使发动机的动力停止向驱动轮传输。
变速器设有倒挡,使汽车获得倒退行驶能力。
需要时,变速器还有动力输出功能。
1.1.1汽车变速器的功用现代汽车上广泛采用活塞式内燃机作为动力源,其转矩和转速变化范围较小,而复杂的使用条件则要求汽车的驱动力和车速能在相当大的范围内变化。
为解决这一矛盾,在传动系统中设置了变速器。
变速器的功用是:(1)改变传动比,扩大驱动轮转矩和转速的变化范围,以适应经常变化的行驶条件,如起步、加速、上坡等,同时使发动机在有利的工况下工作;(2)在发动机旋转方向不变的前提下,使汽车能倒退行驶;(3)利用空挡,中断动力传递,以使发动机能够起动、怠速,并便于变速器换挡或进行动力输出。
1.1.2汽车变速器的分类汽车变速器按传动比变化方式不同,可分为有级式、无级式和综合式三种。
(1)有级式变速器应用最为广泛,它采用齿轮传动,具有若干个定值传动比。
按所用轮系形式不同,有级式变速器又可分为有轴线固定式变速器和轴线旋转式变速器两种。
目前,轿车和轻、中型货车变速器的传动比通常有3-5个前进挡和一个倒挡;在重型货车用的组合式变速器中,则有更多挡位。
双中间轴变速箱工作原理

双中间轴变速箱工作原理说起来这双中间轴变速箱啊,可真是个有意思的东西,咱今儿就聊聊它的工作原理,也让大伙儿见识见识这机械里的门道。
咱先说说啥是双中间轴变速箱。
都知道那传统的手动变速箱,里头有输入轴、中间轴、输出轴,三根轴里头,中间轴算是挑大梁的,可咱们今儿说的这个双中间轴变速箱,嘿,它有两根中间轴,你说神奇不神奇?这两根中间轴啊,长得一模一样,就像俩双胞胎似的。
它们的好处在哪儿呢?就在于能把功率给分流了。
你想啊,同样一份活儿,一个人干累,两个人干不就轻松多了嘛。
这变速箱也一样,原先一根中间轴得扛的功率,现在两根轴一分,每根轴就只要扛一半了,这不就轻松多了嘛。
这样一来,变速器的尺寸、质量都能减小,咱开车的时候也感觉更轻快。
再说说它的主轴和主轴齿轮,那设计得可真是巧妙。
主轴齿轮在主轴上能浮动,就像小船在水上漂似的,这样一来,两个中间轴齿轮对主轴齿轮施加的径向力就大小相等、方向相反,相互抵消了。
主轴呢,就只需要承受扭矩,不用受弯矩的罪了。
这就像是咱们挑担子,如果两边重量一样,肩膀就不容易疼,道理是一样的。
这样一来,主轴和轴承的受力情况就大大改善了,变速箱的可靠性和耐用性也就提高了。
还有啊,这主轴换挡的方式也挺逗,它是用滑移齿套换挡的。
你想象一下,那滑移齿套就像个调皮的孩子,在主轴齿轮上滑来滑去,找到合适的位置就“咔嚓”一声,和主轴齿轮的内接合齿啮合上了,动力就这么传递过去了。
这变速箱挡位还多,各档间速比的级差小,换挡的时候那叫一个轻便,就像是咱们骑自行车换档似的,轻轻一拨就过去了。
我记得有一次啊,我和老王一块儿去修车厂,看到师傅在修这个双中间轴变速箱。
老王就好奇地问:“这变速箱咋这么复杂呢?”师傅就笑了,说:“复杂是复杂了点儿,但你可别小看它,它可是能大幅度降低变速箱总成噪音,提高变速箱承载能力的。
”老王一听,就瞪大了眼睛,说:“这么神奇?”师傅就点点头,说:“可不是嘛,这机械里的门道多了去了,咱们啊,还得慢慢学。
汽车设计--3变速器设计
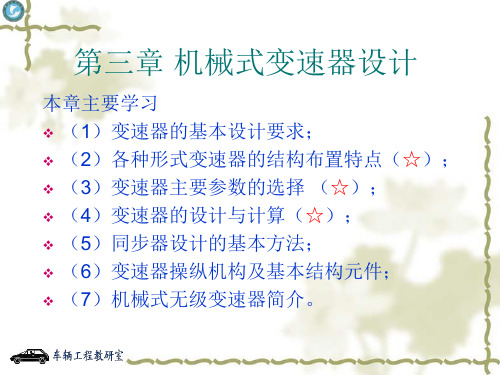
直齿:b=Kcm, Kc为齿宽系数,取为4.5~8.0 斜齿:b= Kcmn,Kc取6.0~8.5
5、变位系数的选择原则
◎采用变位的原因:
1)避免齿轮产生根切 2)配凑中心距 3)通过变位影响齿轮的强度,使用平稳性,耐磨性、抗胶
合能力及齿轮的啮合噪声。 ◎变位齿轮的种类:高度变位和角度变位。 1)高度变位:齿轮副的一对啮合齿轮的变位系数的和为零。
1、变速器的传动比范围: 指变速器最低挡传动比与最高挡传动比的比值。 2、最高挡传动比的选取: 直接挡1.0,超速挡0.7~0.8。
3、最低挡传动比选取:
影响因素:
发动机的最大转矩、最低稳定转速;
驱动轮与路面间的附着力; 主减速比与驱动轮的滚动半径;
Ft max Ff Fi max
汽车的最低稳定车速。
1、中间轴式变速器
❖ 多用于FR,RR布置的 乘用车和商用车上
❖ 能设置直接挡,直接挡 效率高
❖ 一挡传动比能设计较大
❖ 一轴与输出轴转向相同 (挂前进档时)
❖ 零件多,尺寸、质量大
2、两轴式变速器
❖ 结构简单、紧凑、轮廓 尺寸小
❖ 中间挡位传动效率高、 噪音低(少了中间轴、 中间传动齿轮)
❖ 不能设置直接挡,高挡 位时噪音高(轴承齿轮 均承载),且效率略比 三轴式低
第三章 机械式变速器设计
本章主要学习 ❖ (1)变速器的基本设计要求; ❖ (2)各种形式变速器的结构布置特点(☆); ❖ (3)变速器主要参数的选择 (☆); ❖ (4)变速器的设计与计算(☆); ❖ (5)同步器设计的基本方法; ❖ (6)变速器操纵机构及基本结构元件; ❖ (7)机械式无级变速器简介。
车辆工程毕业设计101九档双中间轴变速器
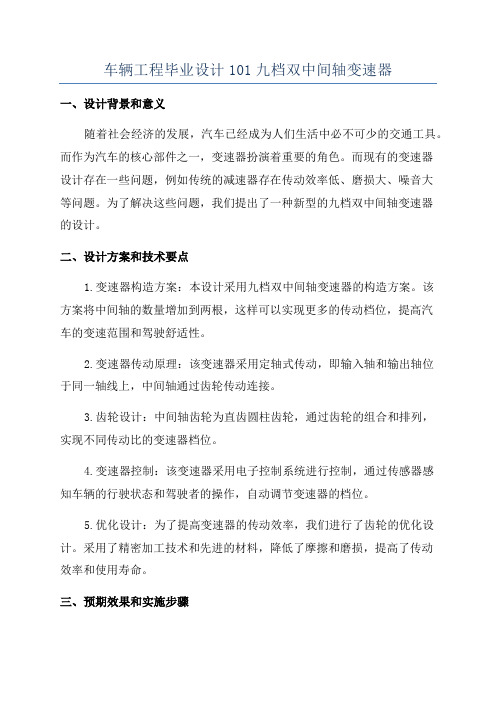
车辆工程毕业设计101九档双中间轴变速器一、设计背景和意义随着社会经济的发展,汽车已经成为人们生活中必不可少的交通工具。
而作为汽车的核心部件之一,变速器扮演着重要的角色。
而现有的变速器设计存在一些问题,例如传统的减速器存在传动效率低、磨损大、噪音大等问题。
为了解决这些问题,我们提出了一种新型的九档双中间轴变速器的设计。
二、设计方案和技术要点1.变速器构造方案:本设计采用九档双中间轴变速器的构造方案。
该方案将中间轴的数量增加到两根,这样可以实现更多的传动档位,提高汽车的变速范围和驾驶舒适性。
2.变速器传动原理:该变速器采用定轴式传动,即输入轴和输出轴位于同一轴线上,中间轴通过齿轮传动连接。
3.齿轮设计:中间轴齿轮为直齿圆柱齿轮,通过齿轮的组合和排列,实现不同传动比的变速器档位。
4.变速器控制:该变速器采用电子控制系统进行控制,通过传感器感知车辆的行驶状态和驾驶者的操作,自动调节变速器的档位。
5.优化设计:为了提高变速器的传动效率,我们进行了齿轮的优化设计。
采用了精密加工技术和先进的材料,降低了摩擦和磨损,提高了传动效率和使用寿命。
三、预期效果和实施步骤1.预期效果:九档双中间轴变速器相比传统变速器,具有更广泛的变速范围和更平滑的传动过程,提高了汽车的性能和驾驶舒适性。
2.实施步骤:首先,进行变速器的整体设计,包括尺寸和重量等方面的考虑。
然后,进行齿轮的设计和制造,确保齿轮的精度和耐用性。
最后,进行变速器的安装和测试,检验其性能和可靠性。
四、结论本设计提出了一种九档双中间轴变速器的设计方案,通过优化设计和控制系统的引入,可以提高变速器的传动效率和换档平稳性。
预计该变速器可以在实际应用中获得良好的性能表现。
发动机功率48KW 中间轴 五档变速器课程设计讲解
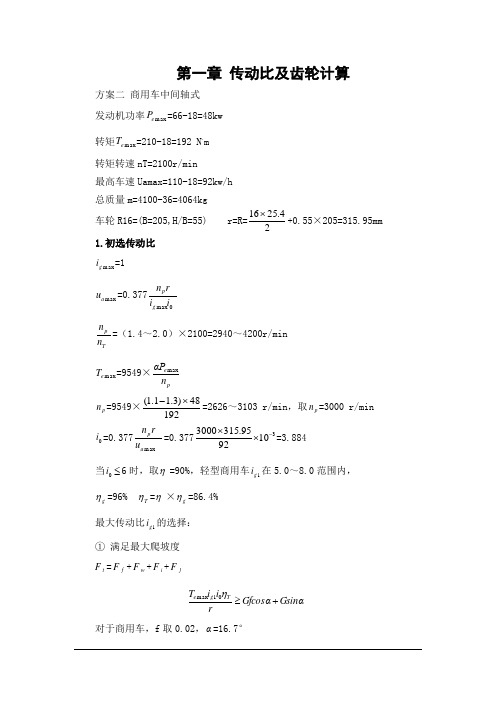
第一章 传动比及齿轮计算方案二 商用车中间轴式 发动机功率max e P =66-18=48kw 转矩max e T =210-18=192 N .m 转矩转速nT=2100r/min 最高车速Uamax=110-18=92kw/h 总质量m=4100-36=4064kg 车轮R16=(B=205,H/B=55) r=R=24.2516 ⨯+0.55×205=315.95mm 1.初选传动比m ax g i =1max a u =0.377max i i r n g pTp n n =(1.4~2.0)×2100=2940~4200r/minmax e T =9549×pe n αP maxp n =9549×19248)3.11.1( ⨯-=2626~3103 r/min ,取p n =3000 r/min0i =0.377maxa p u rn =0.3773109295.3153000-⨯⨯=3.884当0i ≤6时,取η=90%,轻型商用车1g i 在5.0~8.0范围内,g η=96% T η=η×g η=86.4% 最大传动比1g i 的选择: ① 满足最大爬坡度 t F =f F +w F +i F +j FGsin αGfcos αri i T Tg e +≥η01max对于商用车,f 取0.02,α=16.7°∴()T e g i T sin αfcos αGr i η0max 1+≥=()%4.86884.31927.1671602.031595.08.94064⨯⨯︒+︒⨯⨯⨯⨯sin .cos =5.44② 满足附着条件t F =f F +i F201max z Tg e f ri i T ≤ηφ,即T e z g i T r f i η0max 21≤φ=%4.86884.319231595.08.08.94064⨯⨯⨯⨯⨯=15.62在沥青混凝土干路面,φ=0.7~0.8,取φ=0.8 由以上两式得,5.44≤1g i ≤15.62 ∵轻型商用车1g i =5.0~8.0 ∴取1g i =7 各档传动比的确定 五档5g i =1,为直接挡按等比级数原则,一般汽车各挡传动比大致符合如下关系:q i i i i i i i i g g g g g g g g ====54433221式中:q —常数,也就是各挡之间的公比;因此,各挡的传动比为41q i g =,32q i g =,23q i g =,q i g =441g i q ==1.627所以各挡传动比与Ι挡传动比的关系为2g i =4.307,3g i =2.647,4g i =1.6272.初选中心距A初选中心距时,可根据下述经验公式31max g e A i T K A η=式中:A —变速器中心距(mm );A K —中心距系数,商用车:A K =8.6~9.6; max e T —发动机最大转矩(N .m );1i —变速器一挡传动比;g η—变速器传动效率,取96%。
(毕业设计)中型专用汽车变速器设计说明书

摘要变速器用来改变发动机传到驱动轮上的转矩和转速,目的是在原地起步、爬坡、转弯、加速等各种行驶工况下,使汽车获得不同的牵引力和速度,同时使发动机在最有利的工况范围内工作。
所以变速器的结构设计的合理性直接影响到汽车动力性和经济性。
设计要求达到换挡迅速、省力、方便、有较高的工作效率、工作噪声低。
因此变速器在汽车中得到广泛应用。
本次设计的是五个前进档加一个倒档的中型专用车的变速器。
为了使该变速器应用范围更加的广泛,应用到不同工程上,使得本变速器带有取力器。
变速器采用中间轴式,换档形式采用的是同步器和滑移齿轮换档,使的换档方便,可靠。
操纵机构设有自锁和互锁装置。
先利用已知参数确定各挡传动比,再后确定齿轮的模数、压力角、齿宽等参数。
由中心矩确定箱体的长度、高度和中间轴及二轴的轴径,然后对中间轴和各挡齿轮进行校核。
在设计过程中,利用CAXA绘图,运用MATALAB软件编程。
最后绘制装配图及零件图。
通过本次设计,使所设计的变速器工作可靠,传动效率更高。
关键词:变速器,同步器,齿轮,取力器AbstractTo change the engine used to spread transmission of torque and wheel speed, the aim of starting in place, climb, turn and accelerate a variety of driving conditions, different vehicle traction and speed, while the engine in the most favorable range conditions.Therefore, the reasonability of the structure design of a transmission gearbox directly affects the vehicle's dynamic performance. It is usually required shifting gears rapidly and conveniently, saving force, and having a higher working efficiency and low working noises.The design of the five forward file plus a reverse of the transmission medium-sized special vehicle. In order to make the transmission more broad range of applications, application to a different project, make a check of the power transmission device. Transmission use of the middle axis, shifting the form of using the synchronizer gear shift and sliding to make the shift easy and reliable. Manipulation of institutions with self-locking and interlocking devices.Using the given basic parameters, it was firstly determined the transmission ratio of each shift, the shaft center distances, the gear modulus, the gear pressing angles and widths, and so on. And then the general dimension of the gearbox, including its length, width and height , and then on the intermediate shaft and the block to check gear. During the design process, using CAXA mapping, the use of software programming MATALAB. The final assembly drawing and components drawing Fig.Through this design, so that the design of the transmission of reliable, efficient transmission.Key words:Transmission,,Synchronizer,Gear,Take out of power目录第一章前言 (1)第二章变速器结构概述 (2)第三章变速器各主要参数的设计计算 (3)3.1变速器传动比的确定 (3)3.2中心距的初步确定 (4)3.3轴的直径的初步确定 (4)3.4齿轮模数的确定 (5)3.5齿轮压力角的选择 (5)3.6各档齿轮齿数的分配 (5)3.7变位系数的选择 (7)3.8齿轮齿宽的设计计算 (7)3.9变速器同步器的设计计算 (8)第四章变速器中间轴的校核 (11)4.1中间轴常啮合齿轮处进行校核 (11)4.2对中间轴四挡齿轮处进行校核 (12)4.3对中间轴三挡齿轮进行校核 (13)4.4对中间轴二挡齿轮处进行校核 (13)4.5对中间轴一档挡齿轮处进行校核 (14)第五章变速器各档齿轮强度的校核 (16)5.1齿轮弯曲应力计算 (16)5.1.1二轴一挡直齿轮校核 (16)5.1.2倒挡直齿轮校核 (16)5.1.3二轴二挡斜齿轮校核 (17)5.1.4二轴三挡斜齿轮校核 (17)5.1.5二轴四挡斜齿轮校核 (17)5.1.6二轴常啮合斜齿轮校核 (18)5.1.7中间轴一档齿轮校核 (18)5.1.8中间轴二档齿轮校核 (18)5.1.9中间轴三档齿轮校核 (18)5.1.1.0中间轴四档齿轮校核 (19)5.1.1.1中间轴常啮合齿轮校核 (19)5.2齿轮接触应力计算 (19)5.2.1 二轴一挡直齿轮校核 (20)5.2.2二轴二挡斜齿轮校核 (20)校核 (21)5.2.3 二轴三挡斜齿轮Z7校核 (21)5.2.4二轴四挡斜齿轮Z5校核 (22)5.2.5二轴常啮合斜齿轮Z35.2.6中间轴一档齿轮校核 (22)5.2.7中间轴二档齿轮校核 (23)5.2.8中间轴三档齿轮校核 (23)5.2.9中间轴四档齿轮校核 (23)5.2.1.0中间轴常啮合齿轮校核 (24)5.2.1.1倒档齿轮校核 (24)第六章变速器操纵机构的设计 (25)第七章变速器轴承的选择 (26)第八章取力器的设计与计算 (27)8.1取力器的布置 (27)8.2取力器齿轮、轴和轴承的参数选择和强度计算 (28)第九章结论 (31)参考文献 (32)致谢 (33)附录一 (34)外文翻译 (34)附录二 (43)第一章前言变速器是传动系的重要部件,它的任务就是充分发挥发动机的性能,使发动机发出的动力有效而经济地传到驱动轮,以满足汽车行驶上的各项要求。
中间轴式变速器设计

目录1.概述 (2)2 中间轴式变速器设计 (3)2.1传动方案和零部件方案的确定 (3)2.1.1传动方案初步确定 (4)2.1.2零部件结构方案 (4)2.2 主要参数的选择和计算 (5)2.2.1 先确定最小传动比 (5)2.2.2 确定最大传动比 (6)2.2.3 挡位数确定 (7)2.2.4 中心距A (8)2.2.5 外形尺寸设计 (8)2.2.6 齿轮参数 (9)3 变速器的设计计算 (14)3.1轮齿设计计算 (14)3.1.1 齿轮弯曲强度计算 (14)3.1.2 轮齿接触应力 (17)3.2 轴设计计算 (19)3.2.1 轴的结构 (19)3.2.2 确定轴的尺寸 (19)3.2.3 轴的校核 (20)图1:中间轴式变速器2 中间轴式变速器设计2.1传动方案和零部件方案的确定作为一辆前置后轮驱动的货车,毫无疑问该选用中间轴式多挡机械式变速器。
中间轴式变速器传动方案的共同特点如下。
(1)设有直接挡;(2)1挡有较大传动比;(3)档位搞的齿轮采用常啮合传动,档位低的齿轮(1挡)可以采用或不采用常啮合齿轮川东南;(4)除1挡外,其他档位采用同步器或啮合套换挡;(5)除直接挡外,其他档位工作时的传动效率略低。
2.1.1传动方案初步确定(1)变速器第一轴后端与常啮合主动齿轮做成一体,第2轴前端经滚针轴承支撑在第1轴后端的孔内,且保持两轴轴线在同一条直线上,经啮合套将它们连接后可得到直接挡。
档位搞的齿轮采用常啮合齿轮传动,1挡采用滑动直齿轮传动。
(2)倒档利用率不高,而且都是在停车后在挂入倒档,因此可以采用支持滑动齿轮作为换挡方式。
倒挡齿轮采用联体齿轮,避免中间齿轮在最不利的正负交替对称变化的弯曲应力状态下工作,提高寿命,并使倒挡传动比有所增加,装在靠近支承出的中间轴1挡齿轮处。
2.1.2零部件结构方案2.1.2.1齿轮形式齿轮形式有直齿圆柱齿轮、斜齿圆柱齿轮。
两者相比较,斜齿圆柱齿轮有使用寿命长、工作时噪声低的优点;缺点是制造工艺复杂,工作时有轴向力。
双中间轴变速器结构特点

缺点
制造成本高
重量较大
双中间轴变速器的制造成本相对较高,因 为其结构复杂,需要高精度的加工和装配 。
由于双中间轴变速器有两个中间轴和相关 零部件,其重量相对较大,可能会对车辆 的燃油经济性产生一定影响。
变速器尺寸大
传动效率略有降低
由于双中间轴变速器的结构特点,其整体 尺寸较大,可能会对车辆的布局和空间产 生一定影响。
同步器的作用
同步器的作用是在换挡过程中使主、从动齿轮的转速同步,以减小齿轮间的冲击和磨损。同步器通过摩擦片和花 键轴的结合,实现转速的同步。
动力传递路径
动力传递路径
双中间轴变速器的动力传递路径包括输入轴、主中间轴、副 中间轴和输出轴。发动机的动力通过输入轴传递到主中间轴 ,再经过副中间轴传递到输出轴,最终驱动车辆前进或后退 。
小型轻量化
随着汽车工业的发展和消费者对车辆性能要求的 提高,双中间轴变速器将趋向于小型轻量化设计 ,以减小车辆的整备质量,提高车辆的动力性和 燃油经济性。
智能化控制
随着信息技术和智能控制技术的发展,双中间轴 变速器将趋向于采用智能化控制技术,实现变速 器的自动控制和智能调节,提高变速器的操控性 能和响应速度。
双中间轴变速器结构特点
目录
CONTENTS
• 引言 • 双中间轴变速器结构 • 双中间轴变速器的工作原理 • 双中间轴变速器的优缺点 • 双中间轴变速器的应用与发展趋势
01 引言
CHAPTER
变速器概述
01
变速器是汽车传动系统的重要组 成部分,用于改变发动机和驱动 轮之间的转速和转矩,以适应不 同的行驶条件和需求。
பைடு நூலகம்
VS
传动效率
双中间轴变速器的传动效率主要受到齿轮 和轴承的摩擦损失、同步器的摩擦损失等 因素的影响。为了提高传动效率,需要优 化齿轮和轴承的设计,选择合适的润滑油 ,并定期进行维护和保养。
变速器设计(详细过程完整版).
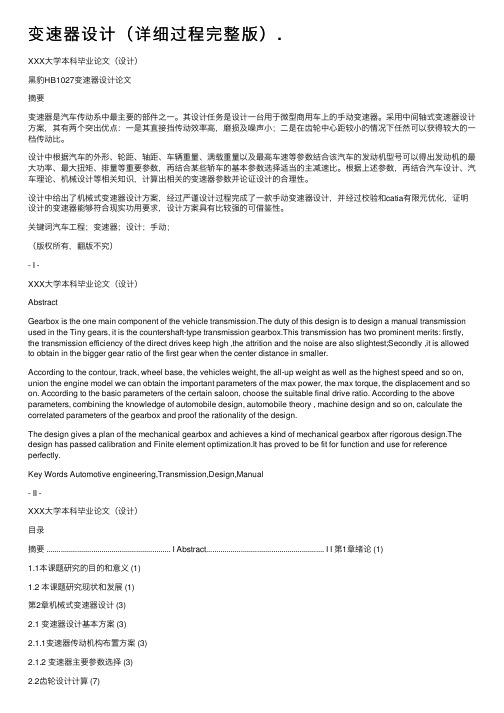
变速器用齿轮有直齿圆柱齿轮和斜齿圆柱齿轮两种。
4、轴的结构分析
第一轴通常与齿轮做成一体,其长度决定于离合器总成的轴向尺寸。第一轴的花健尺寸与离合器从动盘毂的内花键统一考虑, 目前一般都采用齿侧定心的矩形花健,键齿之间为动配合。
第二轴制成阶梯式的以便于齿轮安装,从受力及合理利用材料来看,也是需要的。各截面尺寸不应相差悬殊,轴上供磨削用的 砂轮越程槽处的应力集中会引起轴断裂。[4]
-4本设计是针对黑豹HB1027变速器设计,为五档手动中间轴式机械式变速器,因此,初步选取传动比范围为 5.0,最高档为超 速档,次高档为直接挡,传动比为1.0。 2、变速器各挡传动比的确定 选择最低档传动比时,应根据汽车最大爬坡度、驱动车轮与路面的附着力、汽车的最低稳定车速以及主减速比和驱动车轮的滚 动半径等来综合考虑、确定。
Key Words Automotive engineering,Transmission,Design,Manual
- II -
XXX大学本科毕业论文(设计)
目录
摘要 ............................................................. I Abstract.......................................................... I I 第1章绪论 (1)
长期处于主导变速器市场的地位,各方面技术经过长期市场考验,通过逐步积累,技术已经相当成熟。
2.手动变速器传动效率较高,理论上比自动变速器更省油。
3.手动变速器结构简单,制造工艺成熟,市场需求大,能够产生生产规模效益,生产成本低廉。
4.维修方便,维修成本便宜。
5.可以给汽车驾驶爱好者带来更多的操控快感。[1]
轻型货车中间轴式五挡变速器设计

工有一定难度。从零件的尺寸和形状位置要求来看主要保证工件的表面粗糙度。
对于端面及齿面的加工,采用数控车床进行粗车和精车可以达到加工要求;
粗糙度要求较高的加工表面在粗车和精车之后通过精磨达到最终加工要求;
内孔的光洁度及尺寸公差要求均较高,可以用先粗车,后精车,最后精磨,从而达到加工要求;
最后采用强力喷丸机及电镀磷化处理提高工件的使用性能及耐磨性。
1.7检验说明
在直接档齿轮的加工过程中,要进行如下的检验:齿坯加工后的检验,热处理后的检验和最终检验。前两项为中间检验,是针对各加工项目进行的;最终检验是作全面的检查。为了保证检验准确,检验前工件要清洗干净。
齿坯的检验:齿坯的加工质量,在很大程度上影响齿轮的加工质量,尤其是对定位基准,要仔细的检查齿轮加工完后的精度和表面粗糙度。不合格的齿坯不能流到下一道工序。成批生产时,一般要全部检查,大量生产时,齿坯质量稳定时可做部分抽检。
4、心部硬度为513HV;
5、强力喷丸处理(磨齿后);
6、表面电镀磷化处理;
7、应除去加工时产生的毛刺,夹角平滑;
8、热处理:渗碳淬火表面硬度650~800HV;以大端齿根部为准,渗碳层厚度为0.7~1.1mm;心部硬度 513HV。
深入探索固定轴式(两轴式和中间轴式)变速器

深入探索固定轴式(两轴式和中间轴式)变速器相信各位老司机们应该都了解变速器的功用了,那么变速器有什么设计要求呢?变速器的基本设计要求;1)保证汽车有必要的动力性和经济性。
2)设置空挡,切断发动机的动力传输。
3)设置倒挡,使汽车能倒退行驶。
4)设置动力输出装置。
5)换挡迅速、省力、方便。
6)工作可靠。
变速器不得有跳挡、乱挡及换挡冲击等现象发生。
7)变速器应有高的工作效率。
8)变速器的工作噪声低。
了解了以上设计要求,那么我们是否了解机械式变速器的传递原理呢?它就是利用齿轮啮合改变传动比。
两轴式变速器多用于发动机前置前驱汽车。
比较经典的应用有桑塔纳、捷达、富康。
两轴式变速器有结构简单、轮廓尺寸小、布置方便、中间挡位传动效率高和噪声低等优点。
两轴式变速器不能设置直接挡,一挡速比不可能设计得很大。
结构特点:(1)输出轴与主减速主动齿轮成一-体;(2)除倒挡外,其它挡均用常啮合齿轮传动;(3)同步器多数装在输出轴上;(4)各前进挡均经过一对齿轮传递动力;(5)只有两个轴。
中间轴式变速器多用于发动机前置后驱的型式汽车。
结构特点:(1)第一轴和第二轴的轴线在同一直线上,可以布置直接挡;(2)除直接挡外其他各挡均经过两对齿轮传递动力,故在中心距不大的情况下,可以提高传动比;(3)一挡有较大的传动比;(4)挡位高的齿轮采用常啮合齿轮传动,挡位低的齿轮(一挡)可以采用或不采用常啮合齿轮传动;(5)除一挡以外,其他挡位采用同步器或啮合套换挡;(6)除直接挡以外,其他挡位工作时的传动效率略低。
微型货车中间轴式手动变速器设计分析

微型货车中间轴式手动变速器设计分析张雪文【摘要】分析了微型货车中间轴式手动变速器的设计方案,并以四速变速器为例进行设计分析,可为汽车相关从业人员提供参考.【期刊名称】《汽车零部件》【年(卷),期】2011(000)001【总页数】4页(P70-73)【关键词】微型货车;中间轴式手动变速器【作者】张雪文【作者单位】益阳职业技术学院,湖南益阳,413049【正文语种】中文1 确定传动方案微型货车中间轴式手动变速器传动方案特点如下:(1)一挡有较大的传动比;(2)设有直接挡;(3)挡位高的齿轮采用长啮合齿轮传动,挡位低的齿轮(一挡)可以采用长啮合齿轮传动;(4)除一挡以外,其他挡位采用同步器或啮合套换挡;(5)除直接挡以外,其他挡位工作时间的传动效率略低。
传动方案初步确定:变速器第一轴后端与长啮合主动齿轮做成一体,第2轴前端经轴承支撑在第1轴后端的孔内,且保持两轴线在同一直线上,经长啮合套将他们连接后可得到直接挡。
挡位高的齿轮采用常啮合齿轮传动,一挡采用滑动直齿齿轮传动。
倒挡采用支持滑动齿轮作为换挡方式。
倒挡齿轮采用联体齿轮。
2 确定零部件结构方案2.1 齿轮形式齿轮形式为直齿圆柱齿轮、斜齿圆柱齿轮。
变速器中的长啮合齿轮均采用斜齿圆柱齿轮。
直齿圆柱齿轮仅用于低挡和倒挡。
2.2 换挡机构形式变速器一挡、倒挡采用轴向滑动直齿齿轮换挡;常啮合齿轮可用移动啮合套换挡;二挡以上都采用同步器换挡。
2.3 变速器轴承变速器第1轴、第2轴的后部轴承以及中间前、后轴承,按直径系列一般选用中系列球轴承圆柱滚子轴承。
滚针轴承、滑动轴套用于齿轮与轴不固定连接。
3 主要参数的选择和设计计算目前,微型货车一般选用4~5个换挡变速器。
汽车大多数时间是以最高挡行驶的,即用最小传动比的挡位行驶。
3.1 确定最小传动比itmin传动系最小传动比可由变速器最小传动比ig和主减速器传动比i0的乘积来表示通常变速器最小传动比ig取决于传动系最小总传动比itmin和主减速器传动比i0,而汽车最高车速时变速器传动比最小,则根据公式式中:ua为汽车行驶车速,km/h;n为发动机转速,r/min;r为车轮半径,m;ig为特指最高挡传动比。
专项设计——中间轴式变速器(DOC)
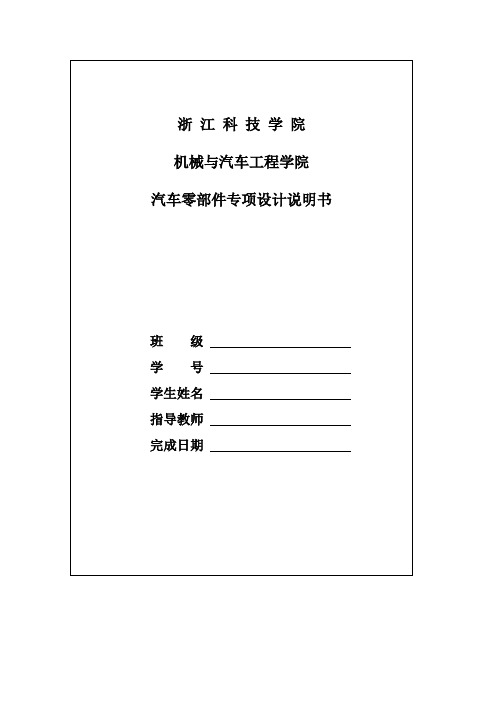
目录1 概述 (1)1.1专项设计题目,任务与分析 (1)1.1.1设计题目:微型面包车变速器 (1)1.1.2设计功用分析 (2)1.1.3 变速器的功用 (2)1.1.4变速器主要参数的选择与计算 (2)2 变速器的方案设计 (3)2.1 传动方案和零部件方案确定 (3)2.1.1传动方案确定 (3)2.1.2 零、部件结构方案分析 (4)2.2 变速器主要参数的选择 (5)2.2.1档数 (5)2.2.2 传动比范围 (5)2.2.3 最低档传动比计算 (5)2.2.4 其他各档传动比初选 (6)2.2.5 中心距A的确定 (7)2.2.6 外形尺寸 (7)2.2.7 齿轮参数选择 (7)2.2.7.5 各档齿轮齿数的分配 (10)3 齿轮参数选择 (16)3.1 各档齿轮参数 (16)3.2齿轮的校核 (20)3.2.1 齿轮的损坏形式 (20)3.2.2 齿轮加工方法及材料 (20)3.2.3 计算各轴的转矩 (21)3.2.4 齿轮弯曲强度计算 (21)3.2.5轮齿接触应力σj (25)3.2.6计算各挡齿轮的受力 (30)4 轴的强度计算 (32)4.1 选择轴的材料 (32)4.2 初选轴的直径 (33)4.3.1 变速器在一档工作时二轴和中间轴的刚度 (34)4.3.2 变速器在二档工作时二轴和中间轴的刚度 (37)4.3.3 变速器在三档工作时二轴和中间轴的刚度 (38)4.3.4 变速器在四档工作时二轴和中间轴的刚度 (40)4.4 轴的强度计算 (40)4.4.1 各轴的支反力 (41)4.4.2各轴的强度校核 (43)4.5 轴承选择与校核 (46)4.5.1 变速器轴承选择 (46)4.5.2 中间轴轴承型号 (46)4.5.3 各挡时的支撑反力 (46)4.5.4 计算各挡时的当量轴承载荷 (47)4.5.5 按路程系数F(各挡行驶里程占行驶里程的百分比)计算各挡轴u承的总当量载荷P (48)m4.5.6根据各轴承的总当量载荷P和承载容量C,按下式计算其寿命Lm(h) (48)课程设计总结 (49)参考文献 (50)微型面包车变速器的设计摘要:变速器是改变汽车运转速度或牵引力的装置,由许多直径大小不同的齿轮组成。
CA10TA190M双中间轴变速器的设计-开题报告

毕业设计(论文)开题报告(或9档)倍档组合式机械变速器。
增加倍档组合式变速器最大输入扭矩和最低档传动比的技术难点是副变速器低档齿轮的强度容量不足,超出齿轮轮齿的承载能力。
解决的办法是将由一个轮齿承受的载荷分流给几个轮齿来承担。
这样一来,输入齿轮扭矩不变,每个轮齿的负荷将等于同时接触齿数的平均数值。
倍档组合式变速器的副变速器功率分流方法有两种:一种是采用行星齿轮系的传动方法,这种结构非常紧凑,体积小而扭矩容量大,直到现在仍广泛应用;另一种功率分流的方法是采用双中间轴传动结构。
双中间轴传动最大工艺难点是保证主传动齿轮能和所啮合的双中间轴齿轮的轮齿同时接触问题,解决的办法是用浮动主传动齿轮的方法来消除齿轴对位的制造误差,确保轮齿同时接触,达到功率分流的目的。
与此相适应的换档同步器也有一定的浮动量。
图1 双中间轴倍档组合式变速器双中间轴倍档组合式变速器具有如下优点:1)由于一轴和二轴上各档齿轮同时与两根中间轴上对应的齿轮相啮合,功率分流,从理论上讲,每对齿轮上传递的扭矩为1/2,这就使每对齿轮传递的扭矩减少50%,使变速器的中心距、齿轮模数和宽度可以减小,从而减小变速器的质量和尺寸,特别是长度尺寸。
2)由于二轴从动齿轮在轴上处于径向浮动状态,两根中间轴的轴心线均匀分布在以二轴理论轴心为圆心、以中心距为半径的圆柱面上,所以二轴上各档齿轮及一轴齿轮在与两根中间轴上的对应齿轮相啮合产生的径向力达到平衡,即互相抵消。
二轴不承受径向力,只传递扭矩,这样二轴可以设计得细一些,结构可以简单一些,其后轴承可以选择较小的规格,这也有助于减小变速器的质量和尺寸。
3)由于二轴齿轮的径向浮动和二轴的铰接式浮动的结果,使得齿轮在啮合时能自动抵消一部分制造和装配误差,啮合质量优于单中间轴。
啮合区容易达到设计要求,实际使用情况也证实了这点。
这就有利于降低啮合噪声和提高耐用度。
4)由于双中间轴倍档组合式变速器可以明显地减小变速器的质量和轴向尺寸,利用这种优点,可提高变速器的最大传递功率和扭矩,扩大使用范围。
双中间轴变速器结构特点

11、换档机构及二轴齿轮定位
3
2
1、滑套 2、二轴齿轮
4
α 3、卡簧
4、花键垫
5、调整垫 6、二轴
5
注:α=35°
6
1
➢主轴上的滑套通过渐开线花键套在主轴上,移动滑套使滑套的接合齿与主轴齿轮 的内接合齿啮合传递动力。
➢滑套和主轴齿轮内接合齿端处于相同大小的锥角α=35°。由于主轴和主轴齿轮处 于浮动状态,所以挂档时,这两个锥面能起到一定的自动定心和同步作用。
17、取力机构
取力轴
法士特双中间轴变速器普遍采用在变速器后端副箱加长轴处取力
18、后取力控制机构
定位环
1.范围档拨叉轴 2.范围档气缸 3.后盖壳体 4.范围档气缸活塞 5.O型密封圈 6.定位环 7.O型密封圈 8.六角尼龙锁紧螺母
为实现停车取力,必须将副变速器处于空档位置。为解决这一问题, 9.空档位置气缸 10.导销 11.空档位置气缸活塞 12.13.O型密封圈
全同步器
速比代号
名义输入扭矩 (×10N·m)
3.
E T (O) —20 0 13
伊顿 双中间轴
超速档
前进挡 数量
设计级别
额定输 出扭矩
目录
一、双中间轴变速器特点介绍 二、双中间轴变速器编号规则 三、双中间轴变速器典型结构
三、典型结构
1、变速箱主副箱基本结构
副箱 主箱
双中间轴结构,功率分流,
每个中间轴、中间轴两端的轴 承及中间轴上的齿轮只承受总 动力的1/2,输入轴及主轴上的 轮齿也承受总动力的1/2 ,这 样主轴所受的力大小相等,方 向相反,主轴只承受扭矩,不 承受弯矩。消除了主轴变形引 起的齿轮啮合区的破坏,降低 了变速器齿轮啮合的噪音,提 高了齿轮的寿命。可延长变速 器使用奉命,使其工作更加可 靠。
中心轴四档变速器设计

中心轴四档变速器设计一、目的意义21世纪,汽车工业已经成为中国经济发展的主要支柱产业之一,汽车企业对各部件的设计需求逐渐旺盛。
随着汽车工业的发展迅猛,车型的多样化、个性化已经成为汽车发展的主要趋势。
而变速器设计是汽车设计中重要的环节之一,变速器在汽车传动系中扮演着至关重要的角色。
它是用来改变发动机传到驱动轮上的转矩和转速,目的是在各种行驶工况下,使汽车获得不同的牵引力和速度,同时使发动机在最有利的工况范围内工作。
因此它的性能影响到汽车的动力性和经济性指标。
可以说,变速器是伴随着汽车工业出现的必然产物,是汽车上的必需品。
在完成了最基本的传动功能之外,我们对变速器的要求也是越来越高,汽车的性能、使用寿命、能源消耗、振动噪声等在很大程度上取决于变速器的性能。
由此可见,对汽车的变速器进行研究具有十分重要的意义。
二、研究的基本内容,拟解决的主要问题(1)基本数据的确定;(2)传动方案的确定;(3)变速器主要零件结构方案的确定;(4)变速器主要参数的选择;(5)变速器齿轮的设计计算及弯曲强度接触强度校核(6)同步器主要尺寸的确定;(7)轴的设计及校核轴承选择以及寿命计算;(8)变速箱体的设计。
拟解决的主要问题:(1)变速器倒档齿轮齿数的计算,及校核;(2)变速器轴的设计与校核;(3)变速器轴承选用哪一种可以既满足工作条件又可以获得较长的使用寿命;(4)变速器同步器的选择和主要参数计算。
三、变速器的设计要求(1)保证汽车有必要的的动力性和经济性;(2)设置不同挡位,满足用来调整与切断发动机动力向驱动轮的传输并使汽车能倒退行驶;(3)工作可靠,汽车行驶过程中,变速器不得有跳挡、乱挡,以及换挡冲击等现象出现;(4)工作效率高,噪声小;结构简单、方案合理;(5)在满载及冲击载荷件下,使用寿命长为保证变速器具有良好的工作性能,对变速器又提出如下的设计要求:(1)正确的选择变速器的档位数和传动比,并使之与发动机参数及主减速比做优化匹配,以保证汽车具有良好的动力性与燃料经济性;(2设置空挡,以保证汽车在必要时能将发动机与传动系长时间分离;设置倒档,使汽车可以倒退行驶;(3)操作简单、准确、轻便、迅捷;(4)传动效率高、工作平稳、无噪声或低噪声;(5)制造工艺性好、造价低廉、维修方便;(6)贯彻零件标准化、部件通用化和变速器总成系列化等设计要求,遵守有关标准和法规(7)需要时应设置动力输出装置;(8)体积小、质量小、承载能力强、使用寿命长、工作可靠四、选取发动机本设计采用大众的EA211 发动机五、传动方案采用中间轴式变速器五、齿轮和轴尺寸详见中心轴四档变速器设计.xlsx。
- 1、下载文档前请自行甄别文档内容的完整性,平台不提供额外的编辑、内容补充、找答案等附加服务。
- 2、"仅部分预览"的文档,不可在线预览部分如存在完整性等问题,可反馈申请退款(可完整预览的文档不适用该条件!)。
- 3、如文档侵犯您的权益,请联系客服反馈,我们会尽快为您处理(人工客服工作时间:9:00-18:30)。
目录1.概述 .................................................................................... 错误!未定义书签。
2 中间轴式变速器设计 (2)2.1传动方案和零部件方案的确定 (2)2.1.1传动方案初步确定 (2)2.1.2零部件结构方案 (3)2.2 主要参数的选择和计算 (4)2.2.1 先确定最小传动比 (4)2.2.2 确定最大传动比 (5)2.2.3 挡位数确定 (6)2.2.4 中心距A (7)2.2.5 外形尺寸设计 (7)2.2.6 齿轮参数 (8)3 变速器的设计计算 (13)3.1轮齿设计计算 (13)3.1.1 齿轮弯曲强度计算 (13)3.1.2 轮齿接触应力 (16)3.2 轴设计计算 (18)3.2.1 轴的结构 (18)3.2.2 确定轴的尺寸 (18)3.2.3 轴的校核 (19)图1:中间轴式变速器2 中间轴式变速器设计2.1传动方案和零部件方案的确定作为一辆前置后轮驱动的货车,毫无疑问该选用中间轴式多挡机械式变速器。
中间轴式变速器传动方案的共同特点如下。
(1)设有直接挡;(2) 1挡有较大传动比;(3)档位搞的齿轮采用常啮合传动,档位低的齿轮(1挡)可以采用或不采用常啮合齿轮川东南;(4)除1挡外,其他档位采用同步器或啮合套换挡;(5)除直接挡外,其他档位工作时的传动效率略低。
2.1.1传动方案初步确定(1)变速器第一轴后端与常啮合主动齿轮做成一体,第2轴前端经滚针轴承支撑在第1轴后端的孔内,且保持两轴轴线在同一条直线上,经啮合套将它们连接后可得到直接挡。
档位搞的齿轮采用常啮合齿轮传动,1挡采用滑动直齿轮传动。
(2)倒档利用率不高,而且都是在停车后在挂入倒档,因此可以采用支持滑动齿轮作为换挡方式。
倒挡齿轮采用联体齿轮,避免中间齿轮在最不利的正负交替对称变化的弯曲应力状态下工作,提高寿命,并使倒挡传动比有所增加,装在靠近支承出的中间轴1挡齿轮处。
2.1.2零部件结构方案2.1.2.1齿轮形式齿轮形式有直齿圆柱齿轮、斜齿圆柱齿轮。
两者相比较,斜齿圆柱齿轮有使用寿命长、工作时噪声低的优点;缺点是制造工艺复杂,工作时有轴向力。
变速器中的常啮合齿轮均采用斜齿圆柱齿轮。
直齿圆柱齿轮仅用于抵挡和倒挡。
2.1.2.2换挡机构形式此变速器换挡机构有直齿滑动齿轮、移动啮合套换挡和同步器换挡三种形式。
采用轴向滑动直齿齿轮换挡,会在轮齿端面产生冲击,齿轮端部磨损加剧并过早损坏,并伴有噪声,不宜用于高档位。
为简化机构,降低成本,此变速器1挡、倒挡采用此种方式。
常啮合齿轮可用移动啮合套换挡。
因承受换挡冲击载荷的接合齿齿数多,啮合套不会过早被损坏,但不能消除换挡冲击。
目前这种换挡方法只在某些要求不高的挡位及重型货车变速器上应用。
因此不适合用于本设计中的变速器,不采用啮合套换挡。
使用同步器能保证换挡迅速、无冲击、无噪声,得到广泛应用。
虽然结构复杂、制造精度要求高、轴向尺寸大,但为了降低驾驶员工作强度,降低操作难度,2挡以上都采用同步器换挡。
2.1.2.3变速器轴承变速器轴承常采用圆柱滚子轴承、球轴承、滚针轴承、圆锥滚子轴承、滑动轴套等。
变速器第1轴、第2轴的后部轴承以及中间轴前、后轴承,按直径系列一般选用中系列球轴承或圆柱滚子轴承。
中间轴上齿轮工作时产生的轴向力,原则上由前或后轴承来承受都可以;但当在壳体前端面布置轴承盖有困难的时候,必须由后端轴承承受轴向力,前端采用圆柱滚子轴承承受径向力。
滚针轴承、滑动轴套用于齿轮与轴不固定连接,有相对转动的地方,比如高档区域同步器换挡的第2轴齿轮和第2轴的连接,由于滚针轴承滚动摩擦损失小,传动效率高,径向配合间隙小,定位及运转精度高,有利于齿轮啮合,在不影响齿轮结构的情况下,应尽量使用滚针轴承。
2.2 主要参数的选择和计算目前,货车变速器采用4~5个挡或多挡,多挡变速器多用于重型货车和越野汽车。
因此挡位数大致在4~5个,需要通过计算传动比范围后最后确定。
2.2.1 先确定最小传动比传动系最小传动比可由变速器最小传动比和主减速器传动比的乘积来表示= 3-1通常变速器最小传动比取决于传动系最小传动比和主减速器传动比,而根据汽车理论,汽车最高车速时变速器传动比最小,则根据公式=0.3773-2式中:为汽车行驶速度,km/h; n为发动机转速,r/min; r为车轮半径,m; 特指为最高档传动比。
可得=0.3773-3轻型车轮胎尺寸根据GB/T2977-1997《载重汽车轮胎系列》可选用7.50R20,即轮胎名义宽度7.5in,轮辋名义直径16in,轮胎扁平率为90~100,在此取90,则轮胎直径可以算为r=≈0.435(m)汽车给定的最大车速为100km/h,发动机转速为2566.3r/min,代入③式得=4. 23另外,为了满足足够的动力行呢,还需要校核最高档动力因数。
一般汽车直接挡或最高档动力因数取值范围如下表所示本设计汽车总质量为7000t,为中型货车,可选取=0.06,最小传动比与最高档动力因数有如下关系=η 3-4式中:为直接挡或最高档时,发动机发出最大扭矩时的最大车速,km/h,此时可近似取=。
其它参数见下表。
小传动比为=4.11。
若按变速器直接挡=1,则=4.11,该车采用单级主减速器,主减速器传动比 ,满足要求。
2.2.2 确定最大传动比确定传动系最大传动比,要考虑三方面问题,最大爬坡度或1挡最大动力因数、附着力和汽车最低稳定车速。
传动系的最大传动比通常是变速器1挡传动比与主减速器传动比的乘积,即= 3-5 当汽车爬坡时车速很低,可以忽略空气阻力,汽车的最大驱动力应为=+ 3-6各表达式展开为η3-7 则3-8≥()η各参数见下表计算参数表一般货车最大爬坡度为30%,即 ≈16.7°。
代入3-8式计算可得 ≥4.50。
1挡传动比还应满足附着条件= η 3-9对于后轮驱动汽车,最大附着力有如下公式= = = 3-10式中: 为后轴质量,查表得满载时取值范围为 =(65%-70%) ,选取65.3% ,即满载时后轴质量为4571kg将式3-9代入式3-10求得η 取 ,计算可得 。
结合上面已经计算数值 ≥4.23。
故c 初步取 =4.5,即变速器传动比范围是1~4.5,传动系最大传动比 =18.495。
2.2.3 挡位数确定增加变速器挡位数能够改善汽车的动力性和经济性。
挡位数越多,变速器的结构越复杂,使轮廓尺寸和质量加大,而且在使用时换挡频率也增高。
在最低挡传动比不变的条件下,增加变速器的挡位数会使变速器相邻的低挡与高挡之间的传动比比值减小,换挡容易进行。
在确定汽车最大和最小传动比之后,应该确定中间各挡的传动比。
实上上,汽车传动系各挡传动比大体上是按照等比级数分配的。
因此,各挡传动比的大致关系为q i i iig g g g ==3221式中:q 为各挡之间的公比。
当挡位数为n 时,有 11-=n g i q对于本变速器,挡位数暂定为4,则11-=n g i q =35.4=1.65<1.8一般挡数选择要求如下。
1)为了减小换挡难度,相邻档位之间的传动比比值在1.8以下。
2)高挡区相邻档位之间的传动比比值要比抵挡相邻挡位之间的比值小。
即本例满足要求,确定挡位数为4,则=4.5,==2.72,=q=1.65,=1.2.2.4 中心距A对于中间轴式变速器,中间轴与第2轴之间的距离称为变速器中心距A。
变速器中心距是一个基本参数,对变速器的外形尺寸、体积和质量大小、齿轮的接触强度都有影响。
中心距越小,齿轮的接触应力越大,齿轮的寿命越短。
因此,最小允许中心距应当由保证轮齿有必要的接触强度来确定。
初选中心距A时,可根据下面的经验公式计算A=η3-11式中:为中心距系数,货车为为发动机最大转矩,;为变速器挡传动比;η为变速器传动效率,取96%。
货车的变速器中心距在80~170mm范围内变化。
对于本中型货车,可取=9.0,其余取值按照已有参数计算3-11式可得A≈120.07mm。
2.2.5 外形尺寸设计货车变速器壳体的轴向尺寸与挡数有关,4挡为(2.2~2.7)A。
当变速器选用的常啮合齿轮对数和同步器多时,应取给出范围的上限。
本中型货车,4挡变速器壳体的轴向尺寸取2.7A,即324.20mm,取整得L=325mm。
2.2.6 齿轮参数2.2.6.1.模数的选取变速器齿轮模数选取的一般原则如下1)为了减少噪声应合理减小模数,同时增加齿宽;2)为使质量小些,应该增加模数,同时减少齿宽;3)从工艺方面考虑,各档齿轮应该选用同一种模数;4)从强度方面考虑,格挡齿轮应该选用不同模数;5)对于货车,减少质量比减小噪声更加重要,因此模数应该选得大一些;6)抵挡齿轮选用大一些的模数,其他档位选用另一种模数。
查表可知,中型货车变速器齿轮法向模数范围为3.5~4.5,所选模数应该符合国家标准GB/T 1357—1987 《渐开线圆柱齿轮模数》的规定。
优先选用第一系列的模数,尽量不选括号内的模数。
遵照以上原则,1挡直齿齿轮选用模数m=4.0mm,其余档位斜齿齿轮选=4.00mm。
同步器与啮合套的结合齿多采用渐开线齿形,出于工艺性考虑,同一变速器中的结合齿模数相同,其取值范围如下表。
选取较小的模数可是齿数增多,有利于换挡,在此取2.0。
2.2.6.2 压力角α压力角较小时,重合度较大,传动平稳,噪声较低;压力角较大时,可提高齿轮的抗弯强度和表面接触强度。
对货车,为提高齿轮强度应选用22.5°或25°等大些的压力角。
国家规定的标准压力角为20°,所以普遍采用的压力角为20°。
啮合套或同步器的压力角有20°、25°、30°等,普遍采用30°压力角。
遵照国家规定取齿轮压力角为20°,啮合套或同步器压力角为30°。
2.2.6.3 螺旋角β齿轮的螺旋角对齿轮工作噪声、齿轮强度、轴向力有影响。
选用大些的螺旋角时,可使齿轮啮合的重合度增加,因而平稳工作、噪声降低。
从提高抵挡齿轮的抗弯强度出发,以15°~25°为宜,从提高高档齿轮的接触强度和重合度出发,应当选用大些的螺旋角。
斜齿轮螺旋角选用范围为货车变速器是18°~26°。
2.2.6.4 齿宽b齿宽对变速器的轴向尺寸、齿轮工作平稳性、齿轮强度和齿轮工作时受力的均匀程度等均有影响。
选用较小的齿轮可以缩短变速器的轴向尺寸和减少质量,但齿宽减少使斜齿轮传动平稳的优点削弱,齿轮工作应力增加;选用较大的齿宽,工作时会因轴的变形导致齿轮倾斜,是齿轮沿齿宽方向受力不均匀,并在齿宽方向磨损不均匀。