精馏塔论文
精馏塔毕业论文

精馏塔毕业论文精馏塔毕业论文精馏塔是化学工程领域中一种重要的设备,广泛应用于石油化工、化学制药、食品加工等行业。
在精馏塔的设计和操作中,涉及到许多理论和实践问题,因此,本文将探讨精馏塔的原理、设计和优化方法,以及一些实际应用案例。
一、精馏塔的原理精馏塔是一种用于分离液体混合物的设备,其基本原理是利用不同组分的挥发性差异,在塔内进行蒸馏和冷凝,从而实现分离。
在精馏塔内,液体混合物被加热至沸腾,产生蒸汽,然后通过填料层或板层进行传质和传热,最终在冷凝器中冷却并分离为不同的组分。
二、精馏塔的设计精馏塔的设计是一个复杂的过程,需要考虑许多因素,如物料性质、操作条件、分离效率等。
常见的设计方法包括理论计算方法和经验公式方法。
在理论计算方法中,常用的有McCabe-Thiele图、Ponchon-Savarit图等,这些图形方法可以帮助工程师快速估算精馏塔的塔板数、回流比等参数。
而在经验公式方法中,常用的有Fenske方程、Underwood方程等,这些公式基于实验数据和经验公式,适用于一些常见的分离系统。
三、精馏塔的优化精馏塔的优化是为了提高分离效率、节约能源和降低成本。
常见的优化方法包括改变操作条件、优化塔板结构和填料选型等。
改变操作条件是一种常见的优化方法,例如调整回流比、塔顶温度和塔底温度等,可以改善分离效果。
此外,优化塔板结构也是一种重要的方法,例如改变塔板孔径、增加塔板数目等,可以提高传质和传热效率。
填料选型也是一个关键的优化因素,合适的填料可以提高液体和气体的接触面积,从而提高分离效率。
四、精馏塔的实际应用精馏塔在许多领域都有广泛的应用。
以石油化工行业为例,精馏塔被用于原油分馏、石油化学产品的提纯等过程。
在化学制药行业,精馏塔用于药物的纯化和提纯。
在食品加工行业,精馏塔则用于酒精的提纯和饮料的生产。
总结精馏塔作为一种重要的分离设备,在化学工程领域具有广泛的应用。
其设计和优化是一个复杂而关键的过程,需要考虑多个因素。
填料精馏塔设计毕业论文

填料精馏塔设计毕业论文目录前言 (1)第一章文献综述 (2)1.1甲醇 (2)1.1.1 甲醇的来源 (2)1.1.2 苯的性质[3] (3)1.2 水 (4)1.2.1 水的来源 (4)1.2.2 甲苯的性质 (5)1.3 精馏的介绍及精馏原理 (6)1.4 精馏塔的介绍 (7)1.5精馏技术的进展 (8)第二章设计部分 (9)2.1 设计任务 (9)2.2 设计方案的确定 (10)2.2.1 装置流程的确定 (10)2.2.2 操作压力的选择 (11)2.2.3 进料热况的选择 (11)2.2.4 加热方式的选择 (12)2.2.5 回流比的选择 (12)2.3精馏塔的工艺计算 (13)2.3.1精馏塔的物料衡算 (13)2.3.2理论板层数NT的求取 (14)2.3.3实际板层数的求取 (15)2.3.4精馏塔的工艺条件及有关物性数据的计算 (15)2.3.5精馏塔的塔体工艺尺寸计算 (19)2.3.6塔板主要工艺尺寸的计算 (20)2.3.7筛板的流体力学验算 (22)2.3.8 塔板负荷性能图 (24)第三章结论 (29)致谢 (31)参考文献 (32)附录 (33)前言化工操作单元中甲醇-水混合液的筛板分离塔是最常见的分离操作之一。
根据资料显示:甲醇沸点80.1度,而水是100度,两样物质化学性质相近,故只能采用沸点不同进行分离,可将混合物置于水浴中,进行蒸馏,这种方法只能得到的纯度不可能达到百分之九十九,故可参考酒精和水分离方法,当用普通的蒸馏方法提纯达到97.6%(体积分数)之前,挥发系数K大于1,但到了97.6%这个点时,挥发系数K就会等于1,这时酒精再也不能从混合液中挥发出来,于是就再下不能往下得到纯度更高的酒精溶液,同样,甲苯和苯混合物中,当用常规方法提取苯达到一定浓度时,即苯的纯度达到了像97.6%这样的这个点时,就再也不能往下提纯了,只有用负压精蒸的方法才能进行分离,才能得到更高浓度。
乙醇精馏塔设计毕业论文

乙醇精馏塔设计毕业论文目录摘要................................................. 错误!未定义书签。
Abstract .............................................. 错误!未定义书签。
第一章绪论 (1)1.1 设计的目的和意义 (1)1.2 产品的性质及用途 (1)1.2.1 物理性质 (1)1.2.2 化学性质 (2)1.2.3 乙醇的用途 (2)第二章工艺流程的选择和确定 (3)2.1 粗乙醇的精馏 (3)2.1.1 精馏原理 (3)2.1.2 精馏工艺和精馏塔的选择 (3)2.2 乙醇精馏流程 (5)第三章物料和能量衡算 (7)3.1 物料衡算 (7)3.1.1 粗乙醇精馏的物料平衡计算 (7)3.1.2 主塔的物料平衡计算 (8)3.2 主精馏塔能量衡算 (9)3.2.1 带入热量计算 (9)3.2.2 带出热量计算 (10)3.2.3 冷却水用量计算 (10)第四章精馏塔的设计 (11)4.1 主精馏塔的设计 (11)4.1.1 精馏塔全塔物料衡算及塔板数的确定 (11)4.1.2 求最小回流比及操作回流比 (12)4.1.3 气液相负荷 (12)4.2 求操作线方程 (12)4.3 图解法求理论板 (13)4.3.1 塔板、气液平衡相图 (13)4.3.2 板效率及实际塔板数 (14)4.4 操作条件 (14)4.4.1 操作压力 (14)4.4.2 混合液气相密度 (15)4.4.3 混合液液相密度 (16)4.4.4 表面力 (16)4.5 气液相流量换算 (19)第五章塔径及塔的校核 (21)5.1 塔径的计算 (21)5.2 溢流装置 (23)5.2.1 堰长 (23)5.2.2 出口堰高 (23)5.2.3 弓形降液管的宽度和横截面积 (23)5.2.4 降液管底隙高度 (24)5.3 塔板布置 (24)5.4 浮阀数目与排列 (24)5.5 气相通过浮阀塔板的压降 (26)5.6 淹塔 (27)5.7 塔板负荷性能图 (28)5.7.1 雾沫夹带线 (28)5.7.2 液泛线 (29)5.7.3 液相负荷上限线 (30)5.7.4 漏液线 (30)5.7.5 液相负荷下限线 (31)第六章塔附件设计 (34)6.1 接管设计 (34)6.2 壁厚 (35)6.3 封头 (35)6.4 裙座 (35)6.5 塔高的计算 (35)6.5.1 塔的顶部空间高度 (35)6.5.2 塔的底部空间高度 (36)6.5.3 塔立体高度 (36)第七章总结 (37)致谢 (38)参考文献.............................................. 错误!未定义书签。
丙烯精馏塔论文-工程师

优化控制方案,提高丙烯产品质量第一节概述精馏是化工,炼油生产中应用极为广泛的传质传热过程,其目的是将混合物中各组份分离,达到规定的纯度。
例如,石油化工生产中的中间产品裂解气,需要通过精馏操作进一步分离成纯度要求很高的乙烯、丙烯、丁二烯及芳烃等化工原料。
精馏过程的实质,就是利用混合物中各组份具有不同的挥发度,即在同一温度下各组份的蒸汽压不同这一性质,使液相中的轻组份转移到汽相中,而汽相中的重组份转移到液相中,从而实现分离的目的。
乙烯装臵分离工段的主要任务是通过精馏操作将裂解气分离成纯度要求很高的乙烯、丙烯等产品,这就要求对各个精馏塔实施有效的自动调节。
精馏塔是分离系统的关键设备,它的操作将直接影响产品的质量。
因此,了解精馏塔的自动控制情况很有必要。
一.精馏塔的调节要求精馏塔的自动控制应满足以下几方面的要求:(1)质量指标塔顶或塔底产品之一应该保证合乎规定的纯度,另一产品的成分亦应维持在规定范围,或者塔顶和塔底的产品均应保证一定的纯度。
就二元组分精馏塔来说,质量指标的要求就是使塔顶产品中的轻组份含量和塔底产品中重组份的含量符合规定的要求。
分离热区的丙烯精馏塔(DA-406,DA-1406)就是二元精馏塔。
(2)物料平衡塔顶馏出液和塔底釜液的平均采出量之和应该等于平均进料量,而且这两个采出量的变动应该比较平稳,以利于上、下工序的平稳操作。
塔内及顶、底容器的蓄液量应介于规定的上、下限之间。
此外,塔内压力恒定与否,对塔的平稳操作有很大影响。
(3)热平衡全塔的热平衡是指进入精馏塔各物料带走的热量和离开系统带走的热量相等。
(4)约束条件为了使塔正常操作,必须满足一些约束条件。
例如,塔压必须稳定,否则破坏物料平衡。
为此,除正常压力调节系统外,还需设臵一些保护系统。
又如,有些塔在低温条件下工作,还有些塔容易产生聚合现象,可能使塔发生堵塞,为了判断这种情况,则设臵塔顶、中部、塔底间的压差指示仪表。
二.精馏塔的干扰因素精馏塔塔身,冷凝器,回流罐及再沸器的物料流程如图1-1所示。
化工精馏毕业设计论文
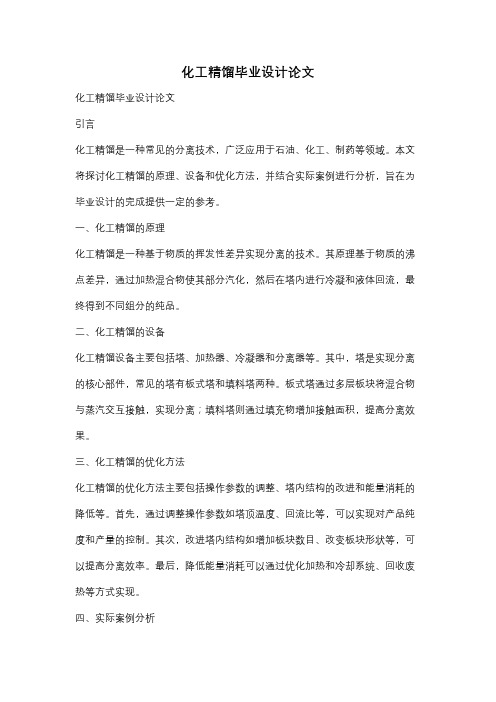
化工精馏毕业设计论文化工精馏毕业设计论文引言化工精馏是一种常见的分离技术,广泛应用于石油、化工、制药等领域。
本文将探讨化工精馏的原理、设备和优化方法,并结合实际案例进行分析,旨在为毕业设计的完成提供一定的参考。
一、化工精馏的原理化工精馏是一种基于物质的挥发性差异实现分离的技术。
其原理基于物质的沸点差异,通过加热混合物使其部分汽化,然后在塔内进行冷凝和液体回流,最终得到不同组分的纯品。
二、化工精馏的设备化工精馏设备主要包括塔、加热器、冷凝器和分离器等。
其中,塔是实现分离的核心部件,常见的塔有板式塔和填料塔两种。
板式塔通过多层板块将混合物与蒸汽交互接触,实现分离;填料塔则通过填充物增加接触面积,提高分离效果。
三、化工精馏的优化方法化工精馏的优化方法主要包括操作参数的调整、塔内结构的改进和能量消耗的降低等。
首先,通过调整操作参数如塔顶温度、回流比等,可以实现对产品纯度和产量的控制。
其次,改进塔内结构如增加板块数目、改变板块形状等,可以提高分离效率。
最后,降低能量消耗可以通过优化加热和冷却系统、回收废热等方式实现。
四、实际案例分析以石油精炼过程中的脱硫装置为例,探讨化工精馏在实际工程中的应用。
脱硫装置中,石油中的硫化物需要被去除,而硫化物与其他组分的沸点接近,难以通过传统的精馏方法实现分离。
因此,可以采用辅助剂的方式,如添加氨水,与硫化物反应生成易挥发的氨基硫化物,再通过精馏将其分离出来。
结论化工精馏作为一种常见的分离技术,在石油、化工、制药等领域具有广泛应用。
通过了解其原理、设备和优化方法,可以更好地应用于实际工程中。
在毕业设计中,可以选择适当的案例进行分析和研究,以提高设计的质量和实用性。
参考文献:[1] Smith R. Chemical Process Design and Integration[M]. John Wiley & Sons, 2005.[2] Henley E J, Seader J D. Equilibrium-Stage Separation Operations in Chemical Engineering[M]. John Wiley & Sons, 1981.。
精馏塔毕业设计论文

第一章概论1.1 塔设备在化工生产中的作用和地位塔设备是化工、石油化工和炼油等生产中最重要的的设备之一。
它可使气(或汽)液或液液两相之间进行紧密接触,达到相际传质及传热的目的。
可在塔设备中完成的常见的单元操作有:精馏、吸收、解吸和萃取等。
此外,工业气体的冷却与回收、气体的湿法净制和干燥,以及兼有气液两相传质和传热的增湿、减湿等。
在化工厂、石油化工厂、炼油厂等中,塔设备的性能对于整个装置的产品产量、质量、生产能力和消耗定额,以及三废处理和环境保护等各个方面,都有重大的影响。
据有关资料报道,塔设备的投资费用占整个工艺设备投资费用的较大比例;它所耗用的钢材重量在各类工艺设备中也属较多。
因此,塔设备的设计和研究,受到化工、炼油等行业的极大重视。
1.2 塔设备的分类及一般构造塔设备经过长期发展,形成了型式繁多的结构,以满足各方面的特殊需要。
为了便于研究和比较,人们从不同的角度对塔设备进行分类。
例如:按操作压力分为加压塔、常压塔和减压塔;按单元操作分为精馏塔、吸收塔、解吸塔、萃取塔、反应塔和干燥塔;按形成相际接触界面的方式分为具有固定相界面的塔和流动过程中形成相界面的塔;也有按塔釜型式分类的。
但是长期以来,最常用的分类是按塔的内件结构分为板式塔和填料塔两大类,还有几种装有机械运动构件的塔。
在板式塔中,塔内装有一定数量的塔盘,气体以鼓泡或喷射的形式穿过塔盘上的液层使两相密切接触,进行传质。
两相的组分浓度沿塔高呈阶梯式变化。
在填料塔中,塔内装填一定段数和一定高度的填料层,液体沿填料表面呈膜状向下流动,作为连续相的气体自下而上流动,与液体逆流传质。
两相的组分浓度沿塔高呈连续变化。
人们又按板式塔的塔盘结构和填料塔所用的填料,细分为多种塔型。
装有机械运动构件的塔,也就是有补充能量的塔,常被用来进行萃取操作,液有用于吸收、除尘等操作的,其中以脉动塔和转盘塔用得较多。
塔设备的构件,除了种类繁多的各种内件外,其余构件则是大致相同的。
1200mm精馏塔机械设计毕业论文.doc

1200mm精馏塔机械设计毕业论文第一章概述1.1 塔设备概论塔设备是化工、石油化工和炼油、医药、环境保护等工业部门的一种重要的单元操作设备。
它的作用是实现气(汽)——液相或液——液相之间的充分接触,从而达到相际间进行传质及传热的目的。
可在塔设备中完成的常见的单元操作有:精馏、吸收、解吸和萃取等。
在化工或炼油厂中,塔设备的性能对于整个装置的产品产量、质量、生产能力和消耗定额以及三废处理和环境保护等各个方面都有重大的影响。
因此,塔设备的设计和研究受到化工、炼油行业的极大重视。
为了使塔设备能更有效、更经济地运行,除了要求它满足特定的工艺条件外,还应满足以下要求:1.气液两相充分接触,相际间传热面积大;2.生产能力大,即气液处理量大;3.操作稳定,操作弹性大;4.阻力小;5.结构简单,制造、安装、维修方便,设备的投资及操作费用低;6.耐腐蚀,不易堵塞。
塔设备的分类:1.按操作压力分有加压塔、常压塔及减压塔;2.按单元操作分有精馏塔、吸收塔、介吸塔、萃取塔、反应塔、干燥塔等;3.按内件结构分有填料塔、板式塔。
1.2常压塔的工作原理及工艺路在产品生产工艺中,在蒸馏前必须进行严格的脱盐、脱水,脱盐后TSC换热到81℃进初馏塔(又称预汽化塔),塔顶出半成品或者成品。
本次设计的是常压塔,常压塔的基本结构和工作原理如下图:1.3精馏塔的主要结构在塔设备的类别中,由于目前工业上应用最广泛的是填料塔及板式塔,所以主要考虑这两种类别。
考虑到设计条件,在初馏塔中STC的分离程度要求不高,成分复杂,而且板式塔较填料塔而言其效率更高,更稳定,液——气比适用范围大,持液量较大,安装、检修更容易,造价更低,故选用板式塔更为合理。
板式塔是一种逐级(板)接触的气液传质设备。
塔内以塔板作为基本构件,气体自塔底向上以鼓泡或喷射的形式穿过塔板上的液层,使气——液相密切接触而进行传质与传热,两相的组分浓度呈阶梯式变化。
塔盘采用浮阀型式。
因为浮阀塔在石油、化工、等工业部门应用最为广泛,具有优异的综合性能,在设计和选用时常作为首选的板式塔型式。
乙醇与水精馏塔设计论文
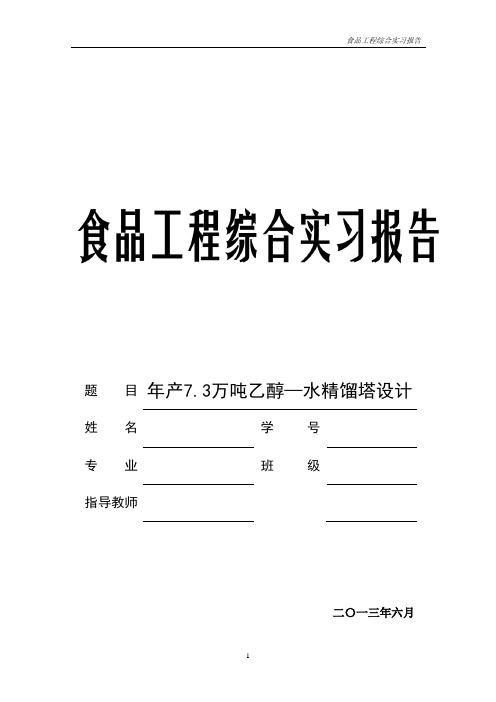
题目年产7.3万吨乙醇—水精馏塔设计姓名学号专业班级指导教师二〇一三年六月目录第1章综合实习课题—课程设计任务------------------------------------------3 第2章设计简介---------------------------------------------------------------------------------------------4 第3章筛板精馏塔设计方案的确定及计算------------------------------------------------------------53.1 物料衡算---------------------------------------------------------------------------------------------53.2 塔板数的确定---------------------------------------------------------------------------------------53.3 精馏段的工艺条件及有关物性数据的计算---------------------------------------------------63.4 精馏塔的塔体工艺尺寸计算---------------------------------------------------------------------83.5 塔板主要工艺尺寸的计算------------------------------------------------------------------------93.6 筛板的流体力学验算----------------------------------------------------------------------------113.7 塔板负荷性能图----------------------------------------------------------------------------------133.8 设计结果概要或设计一览表---------------------------------------------------------------17 第4章辅助设备的计算及选型-------------------------------------------------------------------------18 第5章对本设计的评述----------------------------------------------------------------------------------21 第6章参考文献-------------------------------------------------------------------------------------------22 第7章符号说明-------------------------------------------------------------------------------------------231 2010级食品科学与工程专业——《食品工程原理》课程设计任务书1.1 设计课题:乙醇—水分离过程板式精馏塔的设计1.2 课题原始数据及设计条件1、生产能力原料(乙醇水溶液)处理量:1万吨—10万吨/年(年开工率为280天/年,一天24h计物料(原料)为乙醇-水溶液中乙醇含量为15% (质量分数,下同)2、分离提纯工艺要求塔顶馏出物乙醇含量 90%塔底残液乙醇含量:不超过1%3、操作条件三、设计要求:1、设计一套满足上述工艺要求的筛板精馏塔精馏工艺装置,用于乙醇水溶液中乙醇的提纯(包括塔设备本体、及料液输送系统的选型配套设计和辅助设备的选择)。
精馏塔自控系统设计毕业论文

精馏塔自控系统设计毕业论文目录精馏塔自控系统设计 (I)摘要......................................................... 错误!未定义书签。
Monitoring and Controlling System Design of Distillation....... 错误!未定义书签。
Abstract ....................................................... 错误!未定义书签。
Keywords: automation; batch distillation system; DCS; computer control system . 错误!未定义书签。
第一章绪论 (1)1.1 精馏塔控制的研究背景及意义 (1)1.2 精馏塔控制的研究现状 (1)1.3精馏塔控制存在的问题及最新发展 (2)第二章精馏塔控制的原理和工艺要求 (4)2.1 精馏塔分馏原理 (4)2.2 精馏塔的控制要求及主要扰动 (5)2.2.1 精馏塔的控制要求 (5)2.2.2 精馏塔的干扰因数特性 (6)2.3 精馏塔的控制目标 (8)2.3.1 质量指标 (8)2.3.2 产品产量和能量消耗 (9)2.4 精馏塔装置的工艺流程 (11)第三章精馏塔控制方案设计 (13)3.1 精馏塔控制方案 (13)3.1.1提馏段参数控制 (13)3.1.2精馏段参数控制 (14)3.1.3精馏塔的温差控制及双温差控制 (16)3.2 乙烯精馏塔装置的控制方案 (19)3.3 精馏塔工艺因数影响及系统维护 (23)3.3.1工艺因数影响 (23)3.3.2故障分析及系统维护 (24)第四章 DCS系统选型 (26)4.1 DCS系统概述 (26)4.2 DCS系统的结构与特点 (26)4.2.1 DCS系统的基本组成 (26)4.2.2 DCS系统的特点 (28)4.2.3 DCS系统的传输媒介 (29)4.2.4 DCS通讯网络 (29)4.2.5 JX-300XP系统简介 (31)4.2.6测控仪表选型 (39)第五章控制系统在DCS中的实现 (42)5.1控制站及操作站组态 (44)5.1.1控制站组态 (44)5.1.2操作站组态 (45)第六章控制系统的设计 (48)6.2塔釜液位控制系统的设计 (63)6.2塔釜温度控制系统的设计 (65)6.3冷却水流量控制系统的设计 (69)6.3.1涡流流量计的工作原理 (69)6.4回流比自动控制系统的设计 (70)6.4.1比值系统组成原理 (70)6.4.2工作原理 (71)6.5 精馏塔的监控测试点的确定 (73)6.6其他控制量的控制趋势图 (75)6.6.1系统总貌图 (75)6.6.2塔釜压力趋势图 (76)6.6.3塔节温度趋势图 (77)6.6.4进料温度趋势图 (79)第七章结论.................................................... 错误!未定义书签。
精馏热量衡算精馏塔全塔效率操作弹法论文

精馏热量衡算精馏塔全塔效率操作弹法论文摘要本次设计是针对二元物系的精馏问题进行分析、选取、计算、核算、绘图等,是较完整的精馏设计过程。
我们对此塔进行了工艺设计,包括它的进出口管路的计算,画出了塔板负荷性能图,并对设计结果进行了汇总。
此设计的精馏装置包括精馏塔,再沸器,冷凝器等设备,热量自塔釜输入,物料在塔内经多次部分气化与部分冷凝进行精馏分离,由塔顶产品冷凝器中的冷却介质将余热带走。
本文是精馏塔及其进料预热的设计,分离摩尔分数为0.42的苯—甲苯溶液,使塔顶产品苯的摩尔含量达到98%,塔底釜液摩尔分数为3.5%。
综合工艺操作方便、经济及安全等多方面考虑,本设计采用了筛板塔对苯-甲苯进行分离提纯,塔板为碳钢材料,按照逐板计算求得理论板数为14。
根据经验式算得全塔效率为53.72%。
塔顶使用全凝器,部分回流。
精馏段实际板数为14,提馏段实际板数为14。
实际加料位置在第15块板。
精馏段弹性操作为3.02,提馏段操作弹性为3.12。
全塔塔径为1.4m。
通过板压降、漏液、液泛、液沫夹带的流体力学验算,均在安全操作范围内。
确定了操作点符合操作要求。
关键词:苯-甲苯、精馏、热量衡算、精馏塔设计、全塔效率、操作弹性第一章绪论筛板精馏塔是炼油、化工、石油化工等生产中广泛应用的气液传质设备。
它的出现仅迟于泡罩塔20年左右,当初它长期被认为操作不易稳定,在本世纪50年代以前,它的使用远不如泡罩塔普遍。
其后因急于寻找一种简单而价廉的塔型,对其性能的研究不断深入,已能作出比较有把握的设计,使得筛板塔又成为应用最广的一种类型。
1.1精馏流程设计方案的确定本设计任务为分离苯-甲苯混合物。
对于二元混合物的分离,应采用连续精馏流程。
设计中采用气液混合物进料,将原料液通过预热器加热至温度后送入精馏塔内。
塔顶上升蒸气采用全凝器冷凝,冷凝液在泡点下一部分回流至塔内,其余部分作为塔顶产品冷却后送至储罐。
该物系属易分离物系,最小回流比较小,故操作回流比取最小回流比的1.45倍。
(强烈推荐)苯-甲苯精馏塔的设计毕业论文
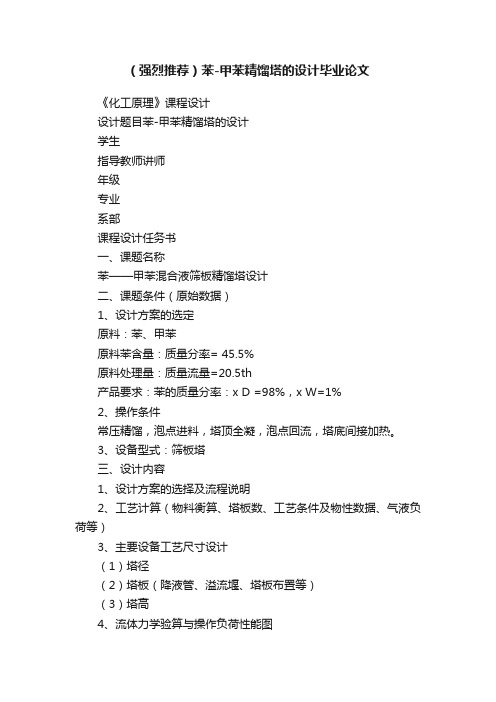
(强烈推荐)苯-甲苯精馏塔的设计毕业论文《化工原理》课程设计设计题目苯-甲苯精馏塔的设计学生指导教师讲师年级专业系部课程设计任务书一、课题名称苯——甲苯混合液筛板精馏塔设计二、课题条件(原始数据)1、设计方案的选定原料:苯、甲苯原料苯含量:质量分率= 45.5%原料处理量:质量流量=20.5th产品要求:苯的质量分率:x D =98%,x W=1%2、操作条件常压精馏,泡点进料,塔顶全凝,泡点回流,塔底间接加热。
3、设备型式:筛板塔三、设计内容1、设计方案的选择及流程说明2、工艺计算(物料衡算、塔板数、工艺条件及物性数据、气液负荷等)3、主要设备工艺尺寸设计(1)塔径(2)塔板(降液管、溢流堰、塔板布置等)(3)塔高4、流体力学验算与操作负荷性能图5、辅助设备选型(冷凝器、再沸器、泵、管道等)6、结果汇总表7、设计总结8、参考文献9、塔的设计条件图(A2)10、工艺流程图(A3)四、图纸要求1、带控制点的工艺流程图(2#图纸);2、精馏塔条件图(1#图纸)。
摘要:本设计对苯—甲苯分离过程筛板精馏塔装置进行了设计,主要进行了以下工作:1、对主要生产工艺流程和方案进行了选择和确定。
2、对生产的主要设备—筛板塔进行了工艺计算设计,其中包括:①精馏塔的物料衡算;②塔板数的确定;③精馏塔的工艺条件及有关物性数据的计算;④精馏塔的塔体工艺尺寸计算;⑤精馏塔塔板的主要工艺尺寸的计算。
3、绘制了生产工艺流程图和精馏塔设计条件图。
4、对设计过程中的有关问题进行了讨论和评述。
本设计简明、合理,能满足初步生产工艺的需要,有一定的实践指导作用。
关键词:苯—甲苯;分离过程;精馏塔目录目录 (1)1 文献综述 (3)1.1概述 (3)1.2方案的确定及基础数据 (3)2 塔物料衡算 (5)2.1原料液及塔顶、塔底产品的摩尔分率 (5)2.2原料液及塔顶、塔底产品的平均摩尔质量 (6)2.3物料衡算 (6)3 塔板数的确定 (6)3.1理论板层数的求取 (6)3.2求精馏塔气液相负荷 (7)3.3操作线方程 (8)3.4逐板计算法求理论板层数 (8)3.5全塔效率估算 (8)3.6求实际板数 (9)4 精馏塔的工艺条件及有关物性数据的计算 (9)4.1操作压力计算 (9)4.3平均摩尔质量计算 (10)4.4平均密度计算 (11)4.5液体平均表面张力计算 (12)4.6液体平均粘度计算 (13)4.7气液负荷计算 (14)5 精馏塔塔体工艺尺寸的计算 (15)塔径的计算 (15)6 塔板主要工艺尺寸的计算 (16)6.1溢流装置计算 (16)6.2塔板布置 (18)6.3筛孔数n与开孔率: (19)7 筛板的流体力学验算 (19)7.1气体通过筛板压强相当的液柱高度计算(精馏段) (19)7.2气体通过筛板压强相当的液柱高度计算(提馏段) (21)8 塔板负荷性能图 (22)8.1精馏段: (22)8.2提馏段: (26)9 设备设计 (30)9.2再沸器 (31)10 各种管尺寸确定 (31)10.1进料管 (31)10.2出料管 (31)10.3塔顶蒸汽管 (32)10.4回流管 (32)10.5再沸返塔蒸汽管 (32)11 塔高 (32)12.设计体会 (33)13.参考文献 (34)分离苯-甲苯混合液的筛板精馏塔1.文献综述1.1概述在常压操作的连续精馏塔内分离苯-甲苯混合液,已知原料液的处理量为20.5th,组成为45.5%(苯的质量分率),要求塔顶馏出液的组成为98%(苯的质量分率)塔底釜的组成为1%。
精馏塔论文
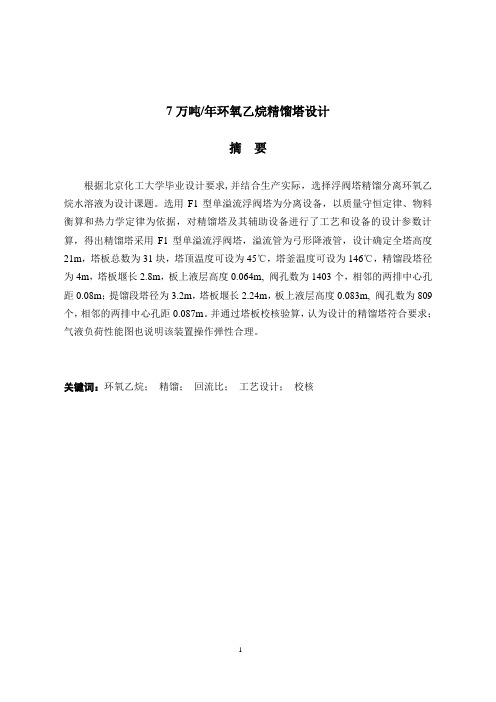
7万吨/年环氧乙烷精馏塔设计摘要根据北京化工大学毕业设计要求,并结合生产实际,选择浮阀塔精馏分离环氧乙烷水溶液为设计课题。
选用F1型单溢流浮阀塔为分离设备,以质量守恒定律、物料衡算和热力学定律为依据,对精馏塔及其辅助设备进行了工艺和设备的设计参数计算,得出精馏塔采用F1型单溢流浮阀塔,溢流管为弓形降液管,设计确定全塔高度21m,塔板总数为31块,塔顶温度可设为45℃,塔釜温度可设为146℃,精馏段塔径为4m,塔板堰长2.8m,板上液层高度0.064m, 阀孔数为1403个,相邻的两排中心孔距0.08m;提馏段塔径为3.2m,塔板堰长2.24m,板上液层高度0.083m, 阀孔数为809个,相邻的两排中心孔距0.087m。
并通过塔板校核验算,认为设计的精馏塔符合要求;气液负荷性能图也说明该装置操作弹性合理。
关键词:环氧乙烷;精馏;回流比;工艺设计;校核目录第1章前言 (4)第1.1节环氧乙烷概述 (4)第1.2节环氧乙烷生产方法 (5)1.2.1 氯醇法 (5)1.2.2 直接氧化法 (5)第1.3节设计任务及目标 (6)第2章设计内容框架 (7)第3章设计简介 (8)第3.1节精馏原理 (8)第3.2节装置流程的确定 (8)第3.3节操作压力的选择 (8)第3.4节浮阀标准 (9)第4章精馏塔设计参数确定 (10)第4.1节物料衡算 (10)4.1.1 精馏塔的物料衡算 (10)4.1.2 精馏塔塔顶、塔釜、进料板温度的计算 (11)4.1.3 塔顶温度的求取 (12)4.1.4 塔釜温度的求取 (12)4.1.5 进料板温度的确定 (13)第4.2节回流比、操作线方程、实际板数的确定 (14)4.2.1 相对挥发度 (14)4.2.2 最小回流比的求取 (14)4.2.3 适宜回流比 (14)4.2.4 操作线方程 (14)4.2.5 理论板的计算和实际塔板数的确定 (14)4.2.6 实际塔板数的确定 (16)第4.3节塔径的计算 (16)4.3.1 精馏段 (16)4.3.2 提馏段 (17)第4.4节塔高的计算 (19)第4.5节塔板结构尺寸及溢流装置的确定 (19)4.5.1 堰长 (19)4.5.2 溢流堰高 (19)4.5.3 弓形降液管的宽度和面积:Wd 和Af (20)4.5.4 降液管底隙高度:ho (21)第4.6节塔板的布置 (21)4.6.1 塔板分布 (21)4.6.2 浮阀的数目与排列 (22)4.6.3 鼓泡区面积 (22)4.6.4 阀孔分布 (23)4.6.5 孔速及动能因数:0u 和0F (23)4.6.6 开孔面积和开孔率 ............................................ 23 第4.7节 塔板校核 (24)4.7.1 气体通过浮阀塔板的压降:hp (24)4.7.2 液泛 (24)4.7.3 雾沫夹带 .................................................... 25 第4.8节 负荷性能图的计算 . (26)4.8.1 雾沫夹带线 (26)4.8.2 液泛线 (27)4.8.3 液相负荷上限线 (28)4.8.4 漏液线 (28)4.8.5 液相负荷下限线 (28)4.8.6 操作弹性 .................................................... 29 第4.9节 热量衡算 (29)4.9.1 塔顶冷凝器换热面积的确定 (29)4.9.2 冷却水消耗量 (29)4.9.3 冷凝器 (29)4.9.4 再沸器 (30)第5章 辅助设备及选型与计算 .......................................... 31 第5.1节 管道尺寸的确定 (31)5.1.1 塔顶蒸汽馏出管线 (31)5.1.2 塔顶冷凝液管线 (31)5.1.3 原料入口管尺寸 (31)5.1.4 再沸器升气管 ............................................... 32 第5.2节 回流罐的确定 ............................................... 32 第5.3节 回流泵的选择 ............................................... 32 第5.4节 安全附件 (33)第6章 结 论 (35)重要符号一览表 (37)参考文献 (39)致 谢 (40)第1章前言第1.1节环氧乙烷概述环氧乙烷是重要的石油化工产品,是乙烯工业衍生物中仅次于聚乙烯和聚氯乙烯的重要有机化工原料。
化工机械毕业论文-1脱丙烷精馏塔设计
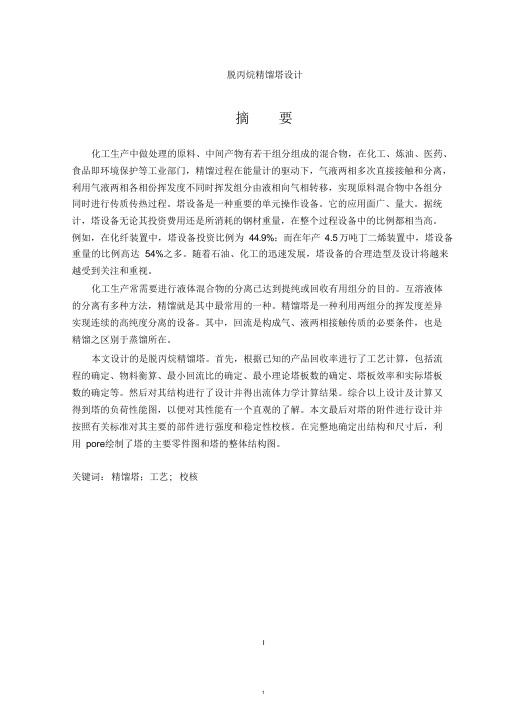
脱丙烷精馏塔设计摘要化工生产中做处理的原料、中间产物有若干组分组成的混合物,在化工、炼油、医药、食品即环境保护等工业部门,精馏过程在能量计的驱动下,气液两相多次直接接触和分离,利用气液两相各相份挥发度不同时挥发组分由液相向气相转移,实现原料混合物中各组分同时进行传质传热过程。
塔设备是一种重要的单元操作设备。
它的应用面广、量大。
据统计,塔设备无论其投资费用还是所消耗的钢材重量,在整个过程设备中的比例都相当高。
例如,在化纤装置中,塔设备投资比例为44.9%;而在年产4.5 万吨丁二烯装置中,塔设备重量的比例高达54%之多。
随着石油、化工的迅速发展,塔设备的合理造型及设计将越来越受到关注和重视。
化工生产常需要进行液体混合物的分离已达到提纯或回收有用组分的目的。
互溶液体的分离有多种方法,精馏就是其中最常用的一种。
精馏塔是一种利用两组分的挥发度差异实现连续的高纯度分离的设备。
其中,回流是构成气、液两相接触传质的必要条件,也是精馏之区别于蒸馏所在。
本文设计的是脱丙烷精馏塔。
首先,根据已知的产品回收率进行了工艺计算,包括流程的确定、物料衡算、最小回流比的确定、最小理论塔板数的确定、塔板效率和实际塔板数的确定等。
然后对其结构进行了设计并得出流体力学计算结果。
综合以上设计及计算又得到塔的负荷性能图,以便对其性能有一个直观的了解。
本文最后对塔的附件进行设计并按照有关标准对其主要的部件进行强度和稳定性校核。
在完整地确定出结构和尺寸后,利用pore绘制了塔的主要零件图和塔的整体结构图。
关键词:精馏塔;工艺; 校核IAbstractTower is an important unit operation equipment in industries such as chemical engineering, o il refining, medicine, food and environmental protection. It is used widely. According to statistics, tower equipment, regardless of their investment costs or the amount of steel or the weight of equipment in the process, accounts for very . For example, in the fiber installations, the tower facility investment ratio is 44.9%. In an annual output of 45,000 tons of butadiene units, the ratio of the weight of tower equipment is as much as 54%.With the development of the petroleum, chemical industry is developing rapidly, reasonable design of the power will become more and more concerned.Chemical production often requires the separationof liquid mixtures that or recovery purposes. There are many ways of liquid separating. Distillation is one of the most commonly used. The use of distillation column is a two-point difference in the achievement of continuous volatility of the separation of constitutes a gas, liquid two-phase mass transfer contact with the necessary conditions for the distillation is distilled from theis designed in this article. First ofall, the basis of known products of the process is used to calculate the recovery rate. Including the identification process, material balance, the determination of the minimum reflux ratio, the minimum theoretical plate number of the identified tray efficiency and the actual determinationof the number plate. And then calculation of bear fruit designing carried out and reaching structure. The function designing and calculating the load getting a tower above synthesis is pursued. Finally, the tower accessories are designed and proofread according to carrying out the intensity and the stability on those main components in connection with the standard the main body of a book. Overall structural drawing in the picture and tower ascertaining out structure and the dimension queendrawn by making use of pore.Key Words:distillation; technology;check毕业设计(论文)原创性声明和使用授权说明原创性声明本人郑重承诺:所呈交的毕业设计(论文),是我个人在指导教师的指导下进行的研究工作及取得的成果。
精馏塔设计摘要范文

精馏塔设计摘要范文英文回答:Abstract.Distillation is a process that separates components of a liquid mixture by selective evaporation and condensation. Distillation towers are used in a wide variety of industries, including the chemical, pharmaceutical, and food and beverage industries.The design of a distillation tower is a complex process that involves a number of factors, including the type of feed, the desired separation, and the operating conditions. The following is a summary of the key steps involved in the design of a distillation tower:1. Feed characterization: The first step in the design of a distillation tower is to characterize the feed. This includes determining the composition of the feed, theboiling points of the components, and the relativevolatility of the components.2. Selection of tower type: The next step is to select the type of distillation tower that will be used. There are a number of different types of distillation towers, each with its own advantages and disadvantages. The most common type of distillation tower is the packed tower.3. Determination of operating conditions: The operating conditions of the distillation tower must be determined in order to achieve the desired separation. The operating conditions include the temperature, pressure, and reflux ratio.4. Design of the tower: The tower must be designed to meet the operating conditions and to achieve the desired separation. The design of the tower includes the selection of the packing material, the height of the tower, and the diameter of the tower.5. Control of the tower: The distillation tower must becontrolled in order to maintain the operating conditionsand to achieve the desired separation. The control of the tower includes the use of temperature controllers, pressure controllers, and reflux controllers.Conclusion.The design of a distillation tower is a complex process that involves a number of factors. By following the steps outlined above, engineers can design distillation towersthat meet the specific needs of their application.中文回答:摘要。
关于浅析萃取精馏技术的研究论文[5篇范文]
![关于浅析萃取精馏技术的研究论文[5篇范文]](https://img.taocdn.com/s3/m/a0e5becefbb069dc5022aaea998fcc22bcd143ee.png)
关于浅析萃取精馏技术的研究论文[5篇范文]第一篇:关于浅析萃取精馏技术的研究论文1、萃取精馏的原理在基本有机化工生产中,经常会遇到组分的相对挥发度比较接近,组分之间也存在形成共沸物的可能性。
若采用普通精馏的方法进行分离,将很困难,或者不可能。
对于这类物系,可以采用特殊精馏方法,向被分离物系中加入第三种组分,改变被分离组分的活度系数,增加组分之间的相对挥发度,达到分离的目的。
如果加入的溶剂与原系统中的一些轻组分形成最低共沸物,溶剂与轻组分将以共沸物形式从塔顶蒸出,塔底得到重组分,这种操作称为共沸精馏;如果加入的溶剂不与原系统中的任一组分形成共沸物,其沸点又较任一组分的沸点高,溶剂与重组分将随釜液离开精馏塔,塔顶得到轻组分,这种操作称为萃取精馏。
2、溶剂筛选原理由于萃取精馏混合物多为强非理想性的系统,所以工业生产中选择适宜溶剂时主要应考虑以下几点:(1)选择性:溶剂的加人要使待分离组分的相对挥发度提高显著,即要求溶剂具有较高的选择性,以提高溶剂的利用率;2)溶解性:要求溶剂与原有组分间有较大的相互溶解度,以防止液体在塔内产生分层现象,但具有高选择性的溶剂往往伴有不互溶性或较低的溶解性,因此需要通过权衡选取合适的溶剂,使其既具有较好的选择性,又具有较高的溶解性;(3)沸点:溶剂的沸点应高于原进料混合物的沸点,以防止形成溶剂与组分的共沸物。
但也不能过高,以避免造成溶剂回收塔釜温过高。
目前萃取精馏溶剂筛选的方法有实验法、数据库查询法、经验值方法、计算机辅助分子设计法用实验法筛选溶剂是目前应用最广的方法,可以取得很好的结果,但是实验耗费较大,实验周期较长。
实验法有直接法、沸点仪法、色谱法、气提法等。
实际应用过程中往往需要几种方法结合使用,以缩短接近目标溶剂的时间。
溶剂筛选的一般过程为:经验分析、理论指导与计算机辅助设计、实验验证等。
若文献资料和数据不全,则只有采取最基本的实验方法,或者采取颇具应用前景的计算机优化方法以寻求最佳溶剂。
关于精馏的论文总结范文

摘要:精馏作为化工生产中常用的分离技术,在提高产品质量、降低能耗、减少污染等方面发挥着重要作用。
本文对精馏技术的原理、应用及优化进行了综述,分析了当前精馏技术的研究热点和发展趋势,以期为相关领域的研究和实践提供参考。
一、引言精馏是一种基于组分沸点差异,通过加热、蒸发、冷凝和再冷凝等过程,实现混合物中各组分分离的技术。
随着化工产业的快速发展,精馏技术在石油、化工、医药、食品等领域得到了广泛应用。
提高精馏效率、降低能耗、减少污染成为当前研究的热点。
二、精馏原理与应用1. 精馏原理精馏过程主要包括加热、蒸发、冷凝和再冷凝等步骤。
加热使混合物中的低沸点组分蒸发,蒸汽通过冷凝器冷凝成液体,再通过再冷凝器进一步冷凝,最终实现各组分分离。
2. 精馏应用(1)石油化工:在石油化工领域,精馏技术广泛应用于石油馏分、汽油、柴油、煤油等产品的生产。
(2)医药行业:在医药行业中,精馏技术用于提取、分离和纯化药物中间体及原料。
(3)食品工业:在食品工业中,精馏技术用于生产食醋、酒精、果汁等产品。
三、精馏优化技术1. 优化精馏塔结构(1)优化塔径:合理确定塔径,提高传质效率。
(2)优化塔板结构:采用新型塔板,如浮阀塔板、筛板等,提高传质面积。
2. 优化操作参数(1)优化回流比:合理调整回流比,提高分离效果。
(2)优化进料位置:优化进料位置,提高分离效率。
3. 节能减排技术(1)采用节能型加热设备,如红外加热器、微波加热器等。
(2)优化冷却系统,降低冷却水用量。
四、研究热点与发展趋势1. 精馏塔结构优化研究新型塔板、塔填料等,提高传质效率。
2. 优化操作参数研究智能控制技术,实现精馏过程的自动化、智能化。
3. 节能减排技术研究新型节能设备,降低能耗。
五、结论精馏技术在化工生产中具有重要意义,通过优化精馏塔结构、操作参数和节能减排技术,可提高精馏效率、降低能耗、减少污染。
随着科学技术的不断发展,精馏技术将在化工、医药、食品等领域得到更广泛的应用。
论文资料精馏塔的结构和工作原理

基本功能:形成气液两相充分接触的相界面,使质、热的传递快速有效 地进行,接触混合与传质后的气、液两相能及时分开,互不夹带。
精馏塔分类:精馏塔的种类很多,按接触方式可分为连续接触式(填料 塔)和逐级接触式(板式塔)两大类在吸收和蒸馏操作中应用极广 。
板式塔
在圆柱形壳体内按一定间距水平设 置若干层塔板,液体靠重力作用自 上而下流经各层板后从塔底排出, 各层塔板上保持有一定厚度的流动 液层;气体则在压强差的推动下, 自塔底向上依次穿过各塔板上的液 层上升至塔顶排出。气、液在塔内 逐板接触进行质、热交换,故两相 的组成沿塔高呈阶跃式变化。
较小 对液量有一定要求 较难 金属及非金属材料均可 新型填料投资较大
板式塔塔板类型
溢流
板式塔
无溢流
降液管
液
相
堰
液相
气相
• 错流式:泡罩、浮阀、筛板 • 喷射式:舌型、浮舌、浮动喷射式
气相
• 穿流塔板、逆流塔板
板式塔塔板类型
溢流塔板 :塔板间有专供液体溢流的降液管 (溢流管),横向流过塔板的 流体与由下而上穿过塔板的气体呈错流或并流流动。 板上液体的流径与液层的高度可通过适当安排降液管的位置及堰的高度 给予控制,从而可获得较高的板效率,但降液管将占去塔板的传质有效 面积,影响塔的生产能力。
气体出 液体进
气体进
液体出
填料塔
在圆柱形壳体内装填一定高度的填 料,液体经塔顶喷淋装置均匀分布 于填料层顶部上,依靠重力作用沿 填料表面自上而下流经填料层后自 塔底排出;气体则在压强差推动下 穿过填料层的空隙,由塔的一端流 向另一端。气液在填料表面接触进 行质、热交换,两相的组成沿塔高 连续变化。
逆流塔板(穿流式塔板):塔板间没有降液管,气、液两相同时由塔板 上的孔道或缝隙逆向穿流而过,板上液层高度靠气体速度维持。 优点:塔板结构简单,板上无液面差,板面充分利用,生产能力较大; 缺点:板效率及操作弹性不及溢流塔板。
精馏塔设计实例范文

精馏塔设计实例范文以下是一个关于精馏塔设计的实例。
精馏塔是用于在化学过程中分离液体混合物的设备,它利用了不同组分的沸点差异来实现分离。
这里我们将讨论一种设计精馏塔的实例,以进一步说明其原理和应用。
1.设计目标:我们的设计目标是将含有甲醇和乙醇的混合物进行分离,以获得高纯度的乙醇。
2.设计原理:甲醇和乙醇的沸点分别为64.7℃和78.4℃,因此我们可以利用精馏塔将两种醇分离。
在精馏塔中,混合物首先被加热到使其汽化,然后通过塔体中不同的级别进行分离。
3.塔体设计:我们将采用两级塔体来进行分离。
首先是一个加热塔,用于将混合物加热到汽化温度。
在这个加热塔中,混合物被加热器加热,然后进入塔体。
然后,混合物在塔体中沿着塔底向上流动,同时在塔体的底部注入蒸汽。
4.分离过程:在塔体中,甲醇和乙醇混合物会按照其沸点温度升序分离。
甲醇在较低的温度下汽化并上升,而乙醇则在较高温度下汽化并上升。
在塔体内部的多个级别上,我们设置了板和塔盘,用于进一步促使两者分离。
5.产品收集:在塔体的顶部,乙醇的纯度已经很高。
因此,我们可以从顶部收集乙醇产品。
甲醇则较重,会沉入塔体的底部,并通过塔底排出。
6.控制系统:为了确保高效的分离和操作,我们需要一个控制系统来实时监测和调整操作参数,如加热器温度、蒸汽压力和料液流量等。
7.安全性考虑:精馏塔操作需要高温和高压,因此必须采取安全措施以防止意外事故。
例如,我们需要设置安全阀,以确保塔体内部的压力不超过合理范围。
总结:精馏塔是一种用于液体混合物分离的重要设备。
在本实例中,我们设计了一个用于分离甲醇和乙醇的精馏塔,并介绍了其原理、结构和操作。
通过适当的控制和安全措施,我们可以获得高纯度的乙醇产品。
同时,这个实例也说明了精馏塔在化学工业中的广泛应用。
FF浮阀式精馏塔毕业设计论文

FF浮阀式精馏塔毕业设计论文目录第1章工艺综述 (1)1.1催化裂化工艺流程 (1)1.2压缩机润滑油工艺流程 (1)1.3工艺流程图 (2)第2章工艺设计计算 (3)2.1塔板的工艺设计 (3)2.1.1精馏塔设计题目 (3)2.1.2全塔物料衡算 (3)2.1.3物性参数计算 (4)2.1.4 塔板数的确定 (11)2.1.5 塔径的初步设计 (12)2.1.6 溢流装置 (14)2.1.7 塔板分布、浮阀数目与排列 (16)2.2塔板的流体力学计算 (17)2.2.1气相通过浮阀塔板的压降 (17)2.2.2 淹塔 (18)2.2.3 雾沫夹带 (19)2.2.4 塔板负荷性能图 (20)第3章结构设计 (22)3.1塔总体高度计算 (22)3.1.1 塔顶封头 (23)3.1.2 塔顶空间 (23)3.1.3 塔底空间 (23)3.1.4 进料板处板间距 (23)3.1.5 裙座 (23)3.2塔的接管 (24)3.2.1 进料管 (24)3.2.2 回流管 (24)3.2.3 塔底出料管 (24)3.2.4 塔顶蒸气出料管 (25)3.2.5 塔底蒸气进气管 (25)第4章强度校核 (25)4.1塔的强度校核 (25)4.1.1 塔体和封头的壁厚计算 (25)4.1.2 确定危险截面位置 (27)4.1.3 质量计算 (27)4.2塔的自振周期计算 (29)4.3风载荷计算 (30)4.3.1 水平风压 (30)4.3.2 各危险截面风弯矩计算 (31)4.4地震载荷计算 (31)4.5各危险截面地震弯矩计算 (32)4.6裙座应力验算 (33)4.6.1裙座厚度确定 (33)4.6.2操作时裙座中应力验算 (33)4.6.3 水压试验裙座应力验算 (35)4.7圆筒轴向应力校核 (35)4.7.1 圆筒轴向应力计算 (35)4.7.2 圆筒稳定性校核 (36)4.7.3 圆筒拉应力校核 (36)4.8容器液压试验时压力校核 (37)4.8.1 壳体应力校核 (37)4.8.2 应力校核 (37)4.9基础环设计 (38)4.9.1 基础环内外径计算 (38)4.9.2 基础环厚度计算 (38)4.10地脚螺栓的设计 (39)4.11裙座与壳体的对接焊缝验算 (40)第5章全塔工艺设计结果 (40)参考文献 (44)第1章工艺综述1.1 催化裂化工艺流程原料油由罐区或其他装置(常减压、润滑油装置)送来,进入原料油罐,由原料泵抽出,换热至200—300℃左右,分馏塔来的回炼油和油浆一起进入提升管的下部,与由再生器再生斜管来的650~700℃再生催化剂接触反应,然后经提升管上部进入分馏塔(下部);反应完的待生催化剂进入沉降器下部汽提段。
- 1、下载文档前请自行甄别文档内容的完整性,平台不提供额外的编辑、内容补充、找答案等附加服务。
- 2、"仅部分预览"的文档,不可在线预览部分如存在完整性等问题,可反馈申请退款(可完整预览的文档不适用该条件!)。
- 3、如文档侵犯您的权益,请联系客服反馈,我们会尽快为您处理(人工客服工作时间:9:00-18:30)。
7万吨/年环氧乙烷精馏塔设计摘要根据北京化工大学毕业设计要求,并结合生产实际,选择浮阀塔精馏分离环氧乙烷水溶液为设计课题。
选用F1型单溢流浮阀塔为分离设备,以质量守恒定律、物料衡算和热力学定律为依据,对精馏塔及其辅助设备进行了工艺和设备的设计参数计算,得出精馏塔采用F1型单溢流浮阀塔,溢流管为弓形降液管,设计确定全塔高度21m,塔板总数为31块,塔顶温度可设为45℃,塔釜温度可设为146℃,精馏段塔径为4m,塔板堰长2.8m,板上液层高度0.064m, 阀孔数为1403个,相邻的两排中心孔距0.08m;提馏段塔径为3.2m,塔板堰长2.24m,板上液层高度0.083m, 阀孔数为809个,相邻的两排中心孔距0.087m。
并通过塔板校核验算,认为设计的精馏塔符合要求;气液负荷性能图也说明该装置操作弹性合理。
关键词:环氧乙烷;精馏;回流比;工艺设计;校核目录第1章前言 (4)第1.1节环氧乙烷概述 (4)第1.2节环氧乙烷生产方法 (5)1.2.1 氯醇法 (5)1.2.2 直接氧化法 (5)第1.3节设计任务及目标 (6)第2章设计内容框架 (7)第3章设计简介 (8)第3.1节精馏原理 (8)第3.2节装置流程的确定 (8)第3.3节操作压力的选择 (8)第3.4节浮阀标准 (9)第4章精馏塔设计参数确定 (10)第4.1节物料衡算 (10)4.1.1 精馏塔的物料衡算 (10)4.1.2 精馏塔塔顶、塔釜、进料板温度的计算 (11)4.1.3 塔顶温度的求取 (12)4.1.4 塔釜温度的求取 (12)4.1.5 进料板温度的确定 (13)第4.2节回流比、操作线方程、实际板数的确定 (14)4.2.1 相对挥发度 (14)4.2.2 最小回流比的求取 (14)4.2.3 适宜回流比 (14)4.2.4 操作线方程 (14)4.2.5 理论板的计算和实际塔板数的确定 (14)4.2.6 实际塔板数的确定 (16)第4.3节塔径的计算 (16)4.3.1 精馏段 (16)4.3.2 提馏段 (17)第4.4节塔高的计算 (19)第4.5节塔板结构尺寸及溢流装置的确定 (19)4.5.1 堰长 (19)4.5.2 溢流堰高 (19)4.5.3 弓形降液管的宽度和面积:Wd 和Af (20)4.5.4 降液管底隙高度:ho (21)第4.6节塔板的布置 (21)4.6.1 塔板分布 (21)4.6.2 浮阀的数目与排列 (22)4.6.3 鼓泡区面积 (22)4.6.4 阀孔分布 (23)4.6.5 孔速及动能因数:0u 和0F (23)4.6.6 开孔面积和开孔率 ............................................ 23 第4.7节 塔板校核 (24)4.7.1 气体通过浮阀塔板的压降:hp (24)4.7.2 液泛 (24)4.7.3 雾沫夹带 .................................................... 25 第4.8节 负荷性能图的计算 . (26)4.8.1 雾沫夹带线 (26)4.8.2 液泛线 (27)4.8.3 液相负荷上限线 (28)4.8.4 漏液线 (28)4.8.5 液相负荷下限线 (28)4.8.6 操作弹性 .................................................... 29 第4.9节 热量衡算 (29)4.9.1 塔顶冷凝器换热面积的确定 (29)4.9.2 冷却水消耗量 (29)4.9.3 冷凝器 (29)4.9.4 再沸器 (30)第5章 辅助设备及选型与计算 .......................................... 31 第5.1节 管道尺寸的确定 (31)5.1.1 塔顶蒸汽馏出管线 (31)5.1.2 塔顶冷凝液管线 (31)5.1.3 原料入口管尺寸 (31)5.1.4 再沸器升气管 ............................................... 32 第5.2节 回流罐的确定 ............................................... 32 第5.3节 回流泵的选择 ............................................... 32 第5.4节 安全附件 (33)第6章 结 论 (35)重要符号一览表 (37)参考文献 (39)致 谢 (40)第1章前言第1.1节环氧乙烷概述环氧乙烷是重要的石油化工产品,是乙烯工业衍生物中仅次于聚乙烯和聚氯乙烯的重要有机化工原料。
2009年,全世界环氧乙烷产能已达到2200万吨,产量约为2000万吨。
由于近年来对环氧乙烷的需求旺盛,每年环氧乙烷产能的增长量都在100万吨左右。
环氧乙烷常温常压下为无色气体,气味似醚,在低于10.7℃时是无色易流动的液体,其蒸汽对眼和鼻粘膜有刺激性,与水、酒精、乙醚相互混溶,化学性质非常活泼,能与许多化合物起加成反应。
环氧乙烷为易燃、易爆、有毒液体,沸点在10.5℃,闪点-17.8℃,易溶于水和有机溶剂,与空气形成爆炸性混合物,爆炸极限为2.6%-100%(体积),爆炸危险性极大。
环氧乙烷特殊的三元环结构决定了环氧乙烷的特殊反应活性,能与许多物质发生开环反应,遇水则缓慢反应生成乙二醇,在精馏过程中会发生聚合反应,异构化反应和水合反应,高温下发生分解反应。
在生产、储存、运输、使用过程中,防火防爆工作极为重要,必须进行全面危害识别、风险评估,制定并落实可靠安全措施,确保安全生产。
表1-1 环氧乙烷的物性数据环氧乙烷是一种重要的有机合成原料,主要用于生产乙二醇;其次也用于生产非离子型表面活性剂、聚醚多元醇、乙醇胺类、环氧乙烷醚类、多胺类、羟乙基纤维素、氯化胆碱和具有特殊功能的液体等,主要应用于洗涤、印染、电子、医药、农药、纺织、造纸、汽车、石油开采与炼制等众多领域。
近年来,在需求持续增加的带动下,国内环氧乙烷新项目不断上马,环氧乙烷生产能力稳步增加。
第1.2节环氧乙烷生产方法环氧乙烷的工业化生产已经有近1个世纪的历史,在其生产发展过程中,生产技术和工艺过程都有不断的改进和革新最早的工业化生产方法是氯醇法,由于其存在产量低、质量差、腐蚀设备、污染环境和耗氯量大等一系列问题,现在己基本上被淘汰了,取而代之的是直接氧化法。
到目前为止,世界上几乎所有的环氧乙烷都是用乙烯直接氧化法生产的。
直接氧化法中,首先出现的是空气氧化法,而后氧气氧化法问世,二者并行,其主要区别在于乙烯的氧化剂各不相同。
1.2.1 氯醇法环氧乙烷氯醇法生产分两步进行:首先氯气与水反应生成次氯酸,再与乙烯反应生成氯乙醇;然后氯乙醇用石灰乳皂化生成环氧乙烷。
氯醇法生产环氧乙烷,由于装置小、产量少、质量差、消耗高,因而成本也高,与大装置氧化法生产的高质量产品相比已失去了市场竞争能力。
1.2.2 直接氧化法乙烯直接氧化法,分为空气直接氧化法和氧气直接氧化法。
这两种氧化方法均采用列管式固定床反应器。
反应器是关键性设备,与反应效果密切相关,其反应过程基本相同,都包括反应、吸收、汽提和蒸馏精制等工序。
(1)空气氧化法此方法用空气为氧化剂,因此必须有空气净化装置,以防止空气中有害杂质带入反应器而影响催化剂的活性。
空气法的特点是有两台或多台反应器串联,即主反应器和副反应器,为使主反应器催化剂的活性保持在较高水平(63~75%),通常以低转化率进行操作,保持在20~50%范围内。
(2)氧气氧化法氧气法不需要空气净化系统,而需要空气分离装置或有其它氧源。
由于用纯氧作氧化剂,连续引入系统的惰性气体大为减少,未反应的乙烯基本上可完全循环使用。
从吸收塔顶出来的气体必须经过脱碳以除去二氧化碳,然后循环返回反应器,二氧化碳的摩尔分数超过15%,将严重影响催化剂的活性。
氧气氧化法无论是在生产工艺、生产设备、产品收率、反应条件上都具有明显的优越性,因此目前世界上的环氧乙烷/乙二醇装置普遍采用氧气氧化法生产。
但是由于氧气氧化法采用纯氧作原料,因此在氧气价格上涨时,对氧气法生产环氧乙烷的生产总费用会有一定的影响,而空气法就不存在氧气价格变动带来的总费用变动问题,而且氧气法对原料的纯度要求很高,如氧气纯度低,就会显著增加含烃放空气体的数量,造成乙烯单耗提高。
尽管如此,通常氧气氧化法的生产成本要比空气氧化法低10%左右近几十年来,许多厂家都采用氧气氧化法生产环氧乙烷,因为氧气氧化法不需要空气净化系统,并且氧气氧化法的环氧乙烷收率高于空气氧化法,乙烯单耗较低。
由于用纯氧作氧化剂,连续引入系统的惰性气体大为减少,未反应的乙烯基本上可完全循环使用。
国内环氧乙烷的生产始于20世纪60年代,采用以乙醇为原料的氯醇法工艺生产环氧乙烷。
20世纪70年代后期,随着北京燕山石油化工公司和辽阳石油化纤公司分别引进了美国SD公司和美国UCC公司的两套环氧乙烷/乙二醇联产生产装置的建成投产,国内环氧乙烷的生产改为以乙烯为原料进行生产。
第1.3节设计任务及目标本毕业设计是依据北京化工大学成人教育学院毕业设计大纲和设计任务书,选择6.1万吨/年环氧乙烷精馏塔设计为课题,采用氧气直接氧化法生产环氧乙烷,以操作简单、能耗低、操作弹性大的浮阀塔为分离设备,确定环氧乙烷提纯单元工艺流程,并进行物料衡算、热量衡算及相关设备工艺计算,力求使精馏塔塔顶温度、塔釜、进料板及泡点温度,塔顶、塔釜物料流量,塔板数、操作回流比等相关设计参数达到最佳理想操作状态。
第2章设计内容框架本设计的年产6.1万吨环氧乙烷精馏塔设计内容框架如下:(1) 精馏塔的物料衡算;(2) 塔板数的确定;(3) 精馏塔的工艺条件及有关物件数据的计算;(4) 精馏塔的塔体工艺尺寸计算;(5) 塔板主要工艺尺寸的计算;(6) 塔板的流体力学验算;(7) 塔板负荷性能图;(8) 精馏塔接管尺寸计算;(9) 绘制生产工艺流程图;(10)总结。
第3章设计简介第3.1节精馏原理精馏之所以能使液体混合物得到较完全的分离,关键在于回流的应用。
回流包括塔顶高浓度易挥发组分液体和塔底高浓度难挥发组分蒸气两者返回塔中。
汽液回流形成了逆流接触的汽液两相,从而在塔的两端分别得到相当纯净的单组分产品。
塔顶回流入塔的液体量与塔顶产品量之比,称为回流比,它是精馏操作的一个重要控制参数,它的变化影响精馏操作的分离效果和能耗。
精馏装置包括精馏塔、原料预热器、釜液冷凝器、蒸馏釜(再沸器)和产品冷凝器等设备,蒸馏过程按操作形式分为间歇蒸馏和连续蒸馏多种流程,间歇蒸馏具有操作灵活,适应性强的优点,适用于小规模,多品种或多组分物系的初步分离;连续蒸馏具有生产能力大,产品质量稳定的特点,工业中以连续蒸馏为主。