零件加工工艺流程图
生产机加工件工艺流程图

一、制造工艺流程表
NO
工程名称
作业内容
管理项目
记录
操作人员
1
原材料入库
原材料入库
先入Hale Waihona Puke 出原材料出库表仓库检验
保管员
2
原材料进口检查
实施进口检查
N/A
外部采购合同书,输入检验报告
3
原材料储存
移动至原材料仓库保管
分规格保管
作业日志
4
原材料分类
加工前原材料分类
按加工工艺分
原材料出库表
5
原材料加工
产品的加工
按顺序进行
作业日志
精工车间
技术人员
6
CNC加工
产品的精密加工
尺寸
生产作业指导书
7
零部件尺寸检验
测量零件尺寸
尺寸
生产作业指导书
8
氧化、着色、抛光
表面处理
表面管理
生产作业指导书
9
产品组装
产品组装
产品的结合性
作业日志
10
成品检查
最终检查
产品检验达标
检验报告
检验员
链条、齿轮等七个机械零件的加工工艺
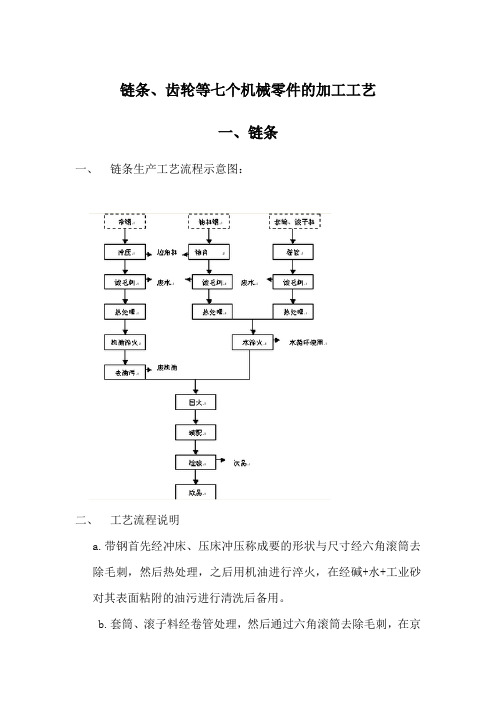
链条、齿轮等七个机械零件的加工工艺一、链条一、链条生产工艺流程示意图:二、工艺流程说明a.带钢首先经冲床、压床冲压称成要的形状与尺寸经六角滚筒去除毛刺,然后热处理,之后用机油进行淬火,在经碱+水+工业砂对其表面粘附的油污进行清洗后备用。
b.套筒、滚子料经卷管处理,然后通过六角滚筒去除毛刺,在京哈热处理之后用水淬火,然后对其表面的油污进行去除。
c.轴料钢首先经轴销机处理制成需要的形状与尺寸,然后通过六角滚筒去除毛刺,再经热处理后用水淬火,然后对其表面的油污进行去除。
d.最后将个零件进行回火,最后装配成型。
经检验合格后即为成品。
三、工艺1、热处理:在热处理设备中,在高温下采用各种辅助介质,改善零件的组织结构,提高各种物品性能。
2、渗碳:将零件置在热处理设备中加热至一定温度并保温一定时间,再通入含碳介质,将碳渗入零件表面,以提高链条硬度和耐磨性能。
3、淬火:零件在热处理设备中加热到一定温度后,保温一定时间,然后按照要求在不同的介质中冷却,从而提高零件硬度。
4、回火:经过淬火后的零件在热处理设备中以一定的温度进行加热,并保温一定时间后冷却。
零件经过回火可以降低淬火硬度,消除淬火应力,提高韧性。
5、发黑:采用高分子有机聚合原理,利用热处理工艺过程中回火余热成膜发黑。
发黑后工件带有光泽,耐腐蚀,防锈性能强;降低劳动强度,改善生产环境。
6、发蓝:把零件加热至一定的温度后,经过化学水溶液冷却,皂化,使零件表面颜色呈现蓝色。
经过发蓝处理的链条外观美观,还有防锈的作用。
不足之处就是这些化学水溶液对环境造成很大的污染。
7、磷化:将零件浸置在一定温度的磷化液内,使零件表面形成磷化层,可使零件表面颜色呈现黑色或灰色,提高链条美观的同时达到防腐的目的。
这些磷化液可循环利用,对环境污染较轻。
8、镀镍:采用电镀或化学镀镍的方法,在零件表面形成镀镍层,镀镍层既可以美观链条,又可以防腐。
镀镍链条一般用在露天场合。
9、镀锌:采用电镀或化学镀锌的方法,在零件表面形成镀锌层,镀锌层既可以美观链条,又可以防腐。
生产机加工件工艺流程图

机加工制造工艺流程图
一、
制造工艺流程表
二、注:在工艺流程图中带☆标记是主要控制项目和控制点及关键和特殊工序
三、有关制造工艺流程图的详细说明
○使用了通过STM F136机械性能和物理性能验证的不锈钢(17-4 PH)。
○将原材料切割成所需的大小及形状。
○利用切割机分料初步加工之后,再利用加工中心(机床)或者车床进行精密加工;加工尺寸要达到容许误差范围。
接着利用攻螺丝机加工螺孔,然后再用研磨机实施研磨加工。
该工艺属主要控制项目和控制点。
○加工后的材料做为产品以成形,但为了提高表面粗度,进行抛光。
○抛光后进行表面研磨,使表面变得柔和。
○实施抛光处理。
○表面研磨后通过后处理,激光打标完成加工及进行最终检查。
○完成最终检查之后,再用超声波洗涤,成品检查然后结束包装,贴标签入库。
该工艺属关键
和特殊工序。
※从原料入库到成品出库,根据产品标准书,ISO9001及YY/T0287标准要求的规定,全程
记录及管理。
扭力扳手管体机加工件工艺流程图

管体加工制造工艺流程图
二、注:在工艺流程图中带☆标记是主要控制项目和控制点及关键和特殊工序
三、有关制造工艺流程图的详细说明
○使用了通过STM F136机械性能和物理性能验证的不锈钢(17-4 PH)。
○将原材料切割成所需的大小及形状。
○利用切割机分料初步加工之后,再利用加工中心(机床)或者车床进行精密加工;加工尺寸要达到容许误差范围。
接着利用攻螺丝机加工螺孔,然后再用研磨机实施研磨加工。
该工艺属主要控制项目和控制点。
○加工后的材料做为产品以成形,但为了提高表面粗度,进行抛光。
○抛光后进行表面研磨,使表面变得柔和。
○实施抛光处理。
○表面研磨后通过后处理,激光打标完成加工及进行最终检查。
○完成最终检查之后,再用超声波洗涤,成品检查然后结束包装,贴标签入库。
该工艺属关键和特殊工序。
※从原料入库到成品出库,根据产品标准书,ISO9001及YY/T0287标准要求的规定,全程记录及管理。
模具零件加工工艺流程图(底盖)
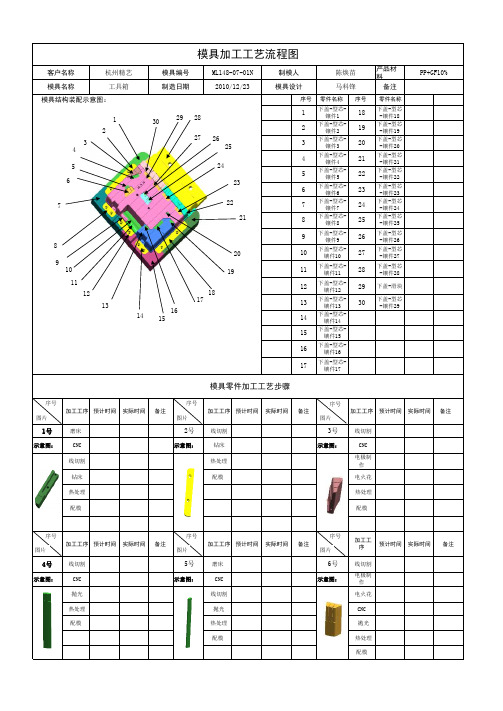
产品材料备注序号 零件名称序号零件名称1下盖-型芯-镶件118下盖-型芯-镶件182下盖-型芯-镶件219下盖-型芯-镶件193下盖-型芯-镶件320下盖-型芯-镶件204下盖-型芯-镶件421下盖-型芯-镶件215下盖-型芯-镶件522下盖-型芯-镶件226下盖-型芯-镶件623下盖-型芯-镶件237下盖-型芯-镶件724下盖-型芯-镶件248下盖-型芯-镶件825下盖-型芯-镶件259下盖-型芯-镶件926下盖-型芯-镶件2610下盖-型芯-镶件1027下盖-型芯-镶件2711下盖-型芯-镶件1128下盖-型芯-镶件2812下盖-型芯-镶件1229下盖-滑块13下盖-型芯-镶件1330下盖-型芯-镶件2914下盖-型芯-镶件1415下盖-型芯-镶件1516下盖-型芯-镶件1617下盖-型芯-镶件17加工工序 预计时间 实际时间备注加工工序 预计时间 实际时间备注加工工序 预计时间 实际时间 备注1号磨床 2号线切割 3号线切割示意图:CNC 示意图:钻床示意图:CNC 线切割 热处理 电极制作 钻床配模电火花 热处理 热处理配模配模加工工序 预计时间 实际时间备注加工工序 预计时间 实际时间备注加工工序 预计时间 实际时间备注4号线切割 5号磨床 6号线切割示意图:CNC 示意图:CNC 示意图:电极制作 抛光 线切割 电火花 热处理 抛光CNC配模热处理 抛光配模热处理配模制模人模具设计模具零件加工工艺步骤模具结构装配示意图:陈焕苗马科锋杭州精艺模具加工工艺流程图PP+GF10%ML148-07-01N 2010/12/23客户名称模具名称模具编号工具箱制造日期234578910111213141719202425262723222118166图片序号图片序号图片序号图片序号图片序号图片序号129302815。
完整版)生产机加工件工艺流程图

完整版)生产机加工件工艺流程图制造工艺流程图如下:1.原材料入库:将原材料送入仓库。
2.原材料检查:检查原材料是否符合要求。
3.原材料储存:将原材料分别放置在不同的仓库中。
4.原材料分类:根据加工工艺将原材料进行分类。
5.原材料粗加工:将原材料进行初步加工。
C加工:使用CNC机床进行加工。
7.精加工:对产品进行精密加工。
8.线切割加工:使用线切割机进行加工。
9.零部件尺寸检验:对零部件的尺寸进行检验。
10.氧化、着色、抛光:进行表面处理。
11.零件组装:将零部件组装成产品。
12.产品装配:将产品进行组装。
13.激光打标:使用激光进行打标。
14.成品检验:对成品进行检验。
制造工艺流程表如下:NO 工程名称作业内容管理项目记录操作人员1 原材料入库将原材料送入仓库先入先出原材料出库表仓库检验2 原材料检查检查原材料是否符合要求 N/A 外部采购合同书,输入检验报告保管员3 原材料储存将原材料分别放置在不同的仓库中分规格保管作业日志精工车间4 原材料分类根据加工工艺将原材料进行分类按加工工艺分原材料出库表技术人员5 原材料粗加工将原材料进行初步加工按顺序进行作业日志精工车间6 CNC加工使用CNC机床进行加工尺寸生产作业指导书技术人员7 精加工对产品进行精密加工尺寸生产作业指导书技术人员8 线切割加工使用线切割机进行加工尺寸生产作业指导书技术人员9 零部件尺寸检验对零部件的尺寸进行检验尺寸检验报告技术人员10 氧化、着色、抛光进行表面处理表面管理作业日志精工车间11 零件组装将零部件组装成产品产品的结合性生产作业指导书技术人员12 产品装配将产品进行组装产品的结合性生产作业指导书技术人员13 激光打标使用激光进行打标作业日志技术人员14 成品检验对成品进行检验产品检验达标检验报告技术人员以上是机加工制造工艺流程图和制造工艺流程表。
我们将原材料进行分类、加工、精加工、线切割加工、零部件尺寸检验、氧化、着色、抛光、零件组装、产品装配、激光打标和成品检验。
生产工艺流程图
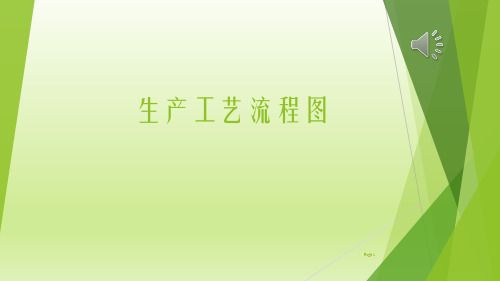
Page 1
生产工艺流程图
FLOW CHART 进料 IQC
CHECK ITEM
1.材料规格厂牌数量
1.PCB/PCBA 2.电子/机构/包材检验 3.依AQL或客户要求
印刷 贴装
1.锡膏厂牌 2.冰箱温度/印刷厚度 1.置件正确性 2.首件/外观
回流焊 FQC目检
1.溫度 2.链条速度
100% 100% 100%
100% 100%
EQVR
放大镜 罩板
NOTE
检验日报表 PCBA外观检验标准
包装材料
制程稽核表 产品包装作业指导书
零件加工设 备
不良標簽
比重計 测温仪
烙铁温度测 试仪
a.75欧负载 电压表 b.电视机, 毫伏表
自动组装线 测试台
制程稽核表 零件加工作业指导书 机种插件作业指导书
目检报表 锡炉Q.A.P.S检查表 錫波高度检查表 制程管制图-Per contorl chart 作业指导书 维修记录表
产品维修SOP 维修日報表
测试SOP 测试记录表
生产工艺流程图
FLOW CHART
CHECK ITEM FREQ
EQVR
NOTE
老化 FUNCTION
QA抽驗
1.负载老化 1.各項功能测试 a.高压测试 b.LNB电压测试 c.升级串口测试 d.机身LED显示按键功 能 e.图像AV1AV2音频LR 声道切换,遥控,信号 频点测试 2.不良品的标示 1.外观检验; 2.功能测试;
1.零件规格 2.零件外观 3.零件數
维修
1.外观不良 2.不良报表的列印 3.检验标记
FREQ
每次领料 FOR机种 抽检
机加工工艺流程图
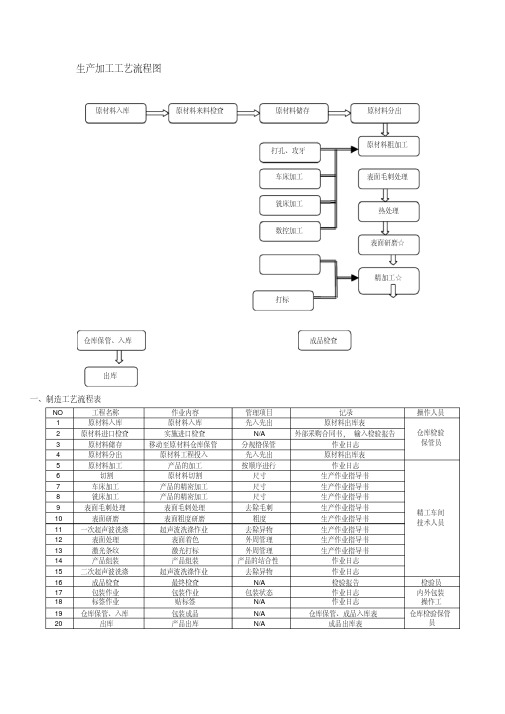
生产加工工艺流程图一、制造工艺流程表NO 工程名称作业内容管理项目记录操作人员1 原材料入库原材料入库先入先出原材料出库表仓库检验保管员2 原材料进口检查实施进口检查N/A 外部采购合同书,输入检验报告3 原材料储存移动至原材料仓库保管分规格保管作业日志4 原材料分出原材料工程投入先入先出原材料出库表5 原材料加工产品的加工按顺序进行作业日志精工车间技术人员6 切割原材料切割尺寸生产作业指导书7 车床加工产品的精密加工尺寸生产作业指导书8 铣床加工产品的精密加工尺寸生产作业指导书9 表面毛刺处理表面毛刺处理去除毛刺生产作业指导书10 表面研磨表面粗度研磨粗度生产作业指导书11 一次超声波洗涤超声波洗涤作业去除异物生产作业指导书12 表面处理表面着色外周管理生产作业指导书13 激光条纹激光打标外周管理生产作业指导书14 产品组装产品组装产品的结合性作业日志15 二次超声波洗涤超声波洗涤作业去除异物作业日志16 成品检查最终检查N/A 检验报告检验员17 包装作业包装作业包装状态作业日志内外包装操作工18 标签作业贴标签N/A 作业日志19 仓库保管、入库包装成品N/A 仓库保管、成品入库表仓库检验保管员20出库产品出库N/A成品出库表原材料来料检查原材料粗加工精加工☆成品检查打标打孔、攻牙车床加工出库仓库保管、入库铣床加工原材料入库原材料储存原材料分出热处理表面研磨☆表面毛刺处理数控加工二、注:在工艺流程图中带☆标记是主要控制项目和控制点及关键和特殊工序三、有关制造工艺流程图的详细说明○使用了通过STM F136机械性能和物理性能验证的不锈钢(17-4 PH)。
○将原材料切割成所需的大小及形状。
○利用切割机分料初步加工之后,再利用加工中心(机床)或者车床进行精密加工;加工尺寸要达到容许误差范围。
接着利用攻螺丝机加工螺孔,然后再用研磨机实施研磨加工。
该工艺属主要控制项目和控制点。
○加工后的材料做为产品以成形,但为了提高表面粗度,进行抛光。
机械制造工艺流程图范例
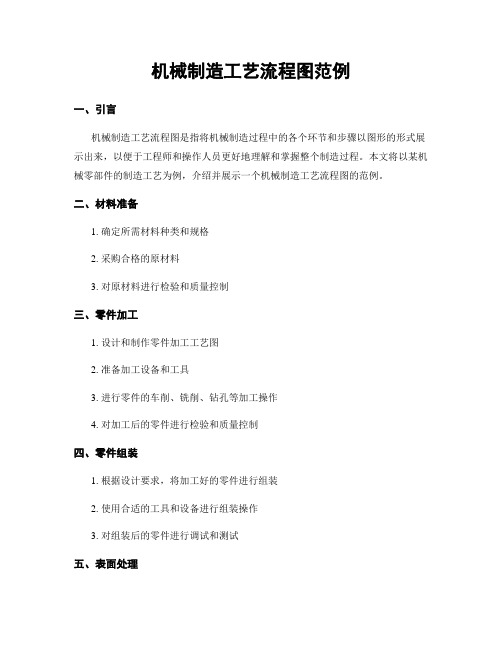
机械制造工艺流程图范例一、引言机械制造工艺流程图是指将机械制造过程中的各个环节和步骤以图形的形式展示出来,以便于工程师和操作人员更好地理解和掌握整个制造过程。
本文将以某机械零部件的制造工艺为例,介绍并展示一个机械制造工艺流程图的范例。
二、材料准备1. 确定所需材料种类和规格2. 采购合格的原材料3. 对原材料进行检验和质量控制三、零件加工1. 设计和制作零件加工工艺图2. 准备加工设备和工具3. 进行零件的车削、铣削、钻孔等加工操作4. 对加工后的零件进行检验和质量控制四、零件组装1. 根据设计要求,将加工好的零件进行组装2. 使用合适的工具和设备进行组装操作3. 对组装后的零件进行调试和测试五、表面处理1. 根据产品要求,选择合适的表面处理方法,如喷涂、镀铬等2. 进行表面处理操作3. 对表面处理后的产品进行检验和质量控制六、成品检验1. 对成品进行全面的检验和测试2. 检查产品的尺寸、外观和性能等方面是否符合要求3. 对不合格品进行返工或报废处理七、包装和出货1. 根据产品特点和运输方式,选择合适的包装材料和方法2. 进行产品的包装和标识3. 准备出货文件和相关手续4. 安排产品的运输和交付八、质量控制1. 在整个制造过程中,严格执行质量控制标准和流程2. 对每个环节和步骤进行记录和检查3. 及时发现和解决质量问题,确保产品质量九、总结机械制造工艺流程图是机械制造过程中的重要工具,能够帮助工程师和操作人员更好地理解和掌握制造过程。
通过本文所展示的机械制造工艺流程图范例,我们可以清晰地了解到机械制造的各个环节和步骤,从材料准备到成品出货,每个环节都有相应的操作和质量控制要求。
在实际生产中,我们可以根据具体产品的特点和要求,进行相应的调整和改进,以提高产品质量和生产效率。
机加工工艺流程图

创建日期: 责任人:工序号/SN 制造◇/MFG 搬运○/Transit 储存△/Store 检验□/Inspect过程特性控制/Process control point 示意图 / Picture 端面粗加工 (80° Nr1.2)A (外径粗加工)B端面精加工 (80° Nr0.8)A(外径精加工)B 内径粗加工(80° Nr0.8)C 内径精加工(55° Nr0.4)C Dia.18钻头加工D*430注意零件碰伤端面粗加工 (80° Nr1.2)E (外径粗加工)F端面精加工 (80° Nr0.8)E(外径精加工)F内径粗加工(80° Nr0.8)G(内径粗加工)H内径精加工(55° Nr0.4)G (内径精加工)H60注意零件碰伤钻孔(H1101 - H1111)钻孔(H3101 - H3104)钻孔(H3001 - H3002)钻孔(H3201)钻孔(H3201)钻孔(H3301)钻孔(H3201)倒角(H1101 - H1111)倒角(H3101 - H3104)倒角(H3001 - H3002)倒角(H3201)倒角(H3301)攻丝(H3101 - H3104)攻丝(H3201)立式车床车削加工90△上挂架80成品检验按抽样标准检验图纸尺寸/Inspect dimension per our AQL.吊装零件至下一道工序行车70钻孔+攻丝/Drilling and tapping加工中心50尺寸检验/FQC 3D 按抽样标准检验图纸尺寸/Inspect dimension per our AQL.吊装并将零件翻身行车40过 程 流 程 图Process flow chart零件号(料号)版本号/Part No.RVE.零件描述(品名)/Description:过程描述/ Process description 车削加工立式车床20设备/Equipment 按抽样标准检验图纸尺寸10尺寸检验/FQC 3D。
轴承加工工艺流程(附图)

轴承加工工艺流程(附图)轴承就是当代机械设备中一种重要零部件。
它得主要功能就是支撑机械旋转体,降低其运动过程中得摩擦系数,并保证其回转精度.按运动元件摩擦性质得不同,轴承可分为滚动轴承与滑动轴承两大类.轴承可同时承受径向负荷与轴向负荷。
能在较高得转速下工作。
接触角越大,轴向承载能力越高。
那么轴承就是怎么加工出来得呢?轴承制造加工基本过程(以套圈制造基本流程为重点,材料选用高碳铬轴承钢Gcr15SiMn)〈1>滚动体(钢球)制造基本流程:原材料——冷镦—-光磨——热处理—-硬磨——初研——外观—-精研<2〉保持架(钢板)制造基本流程:原材料——剪料——裁环-—光整——成形——整形-—冲铆钉孔〈3>套圈(内圈、外圈)制造基本流程:原材料——锻造——退火——车削——淬火--回火——磨削--装配汇普轴承加工流程图(1)锻造加工:锻造加工就是轴承套圈加工中得初加工,也称毛坯加工。
套圈锻造加工得主要目得就是:(a)获得与产品形状相似得毛坯,从而提高金属材料利用率,节约原材料,减少机械加工量,降低成本。
(b)消除金属内在缺陷,改善金属组织,使金属流线分布合理,金属紧密度好,从而提高轴承得使用寿命。
锻造方式:一般就是在感应加热炉、压力机、扩孔机与整形机组成连线得设备体进行流水作业(2)退火:套圈退火得主要目得就是:高碳铬轴承钢得球化退火就是为了获得铁素体基体上均匀分布着细、小、匀、圆得碳化物颗粒得组织,为以后得冷加工及最终得淬回火作组织准备.Gcr15SiMn退火基本工序:在790—810℃保温2—6h,以10—30℃/h,冷至600℃以下,出炉空冷(3)车削加工:车削加工就是轴承套圈得半成品加工,也可以说就是成型加工.车削加工得主要目得就是:(a)使加工后得套圈与最终产品形状完全相同。
(b)为后面得磨削加工创造有利条件。
车削加工得方法:集中工序法:在一台设备上完成所有车削工序得小批量生产。
分散工序法:在一台设备上完成某一种车削工序得大批量生产。
工艺流程图(模板)
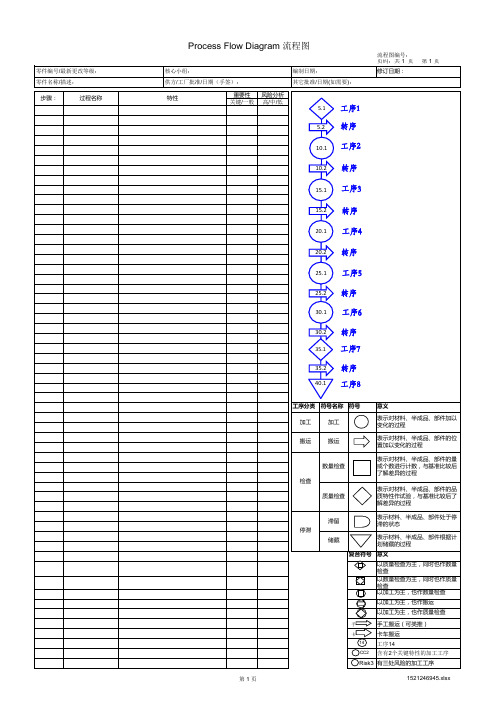
步骤:
过程名称
Process Flow Diagram 流程图
核心小组: 供方/工厂批准/日期(手签):
编制日期: 其它批准/日期(如需要):
特性
重要性 风险分析 关键/一般 高/中/低
5.1 工序1
5.2 转序
10.1 工序2
流程图编号: 页码:共 1 页
修订日期:
第1页
10.2 转序
15.1 工序3
15.2 转序
20.1 工.1 工序6
30.2 转序 35.1 工序7 35.2 转序 40.1 工序8
第1页
工序分类 符号名称 符号
加工
加工
搬运
搬运
意义
表示对材料、半成品、部件加以 变化的过程
表示对材料、半成品、部件的位 置加以变化的过程
以加工为主,也作搬运
以加工为主,也作质量检查
手
手工搬运(可类推)
卡
卡车搬运
14 工序14
CC2 含有2个关键特性的加工工序
Risk3 有三处风险的加工工序
1521246945.xlsx
数量检查 检查
质量检查
表示对材料、半成品、部件的量 或个数进行计数,与基准比较后 了解差异的过程
表示对材料、半成品、部件的品 质特性作试验,与基准比较后了 解差异的过程
停滞
滞留 储藏
表示材料、半成品、部件处于停 滞的状态
表示材料、半成品、部件根据计 划储藏的过程
复合符号 意义
以质量检查为主,同时也作数量 检查 以数量检查为主,同时也作质量 检查 以加工为主,也作数量检查
模具零件加工步骤流程图

产品材料ABS
备注
⑴ 前模
序号
⑵ A 板
图号
⑶ 面板
11钳工⑷ 后模
示意图
2CNC ⑸ B 板3线割⑹顶针板顶针4电火花⑺ 底板
5深孔钻⑻ 滑块
6省模⑼ 测压块7钳工
⑽ 耐磨块8
⑾序号
⑿图号
⒀21钳工⒁示意图
2CNC ⒂3深孔钻⒃
4钳工5678
序号
图号
31钳工示意图
2CNC 3钳工
45678
序号
图号
141钳工2示意图
2CNC 33线割44电火花55深孔钻66省模77钳工
8
8
制表人:
钻螺丝孔及装配
5示意图
省胶位拆模架,打字码开粗后精加工钻运水钻螺丝孔及装配
钻运水省胶位钻运水 加工内容
装配
加工内容
拆模架,打字码开粗后精加工钻运水开粗后精加工料位和做
电极铜公
加工工序
加工内容
装配
倒C角,钻工艺螺丝孔开粗后精加工料位和做
电极铜公
线割顶针孔清角及加工骨位
清角及加工骨位
备注
加工内容
序号CNC 深孔钻钳工
图号
加工工序
加工工序
序号
备注
拆模架,打字码开粗后精加工钻螺丝孔及装配
序号
备注
备注
模具零件加工步骤加工工序
备注
序号序号序号钳工中昇模具加工步骤流程图
2015/11/10
客户名称模具名称
模具编号模具设计
模具结构装配示意图:
加工工序
线割唧嘴孔制造日期
制模人 加工内容
倒C角,钻工艺螺丝孔。
生产机加工件工艺流程图
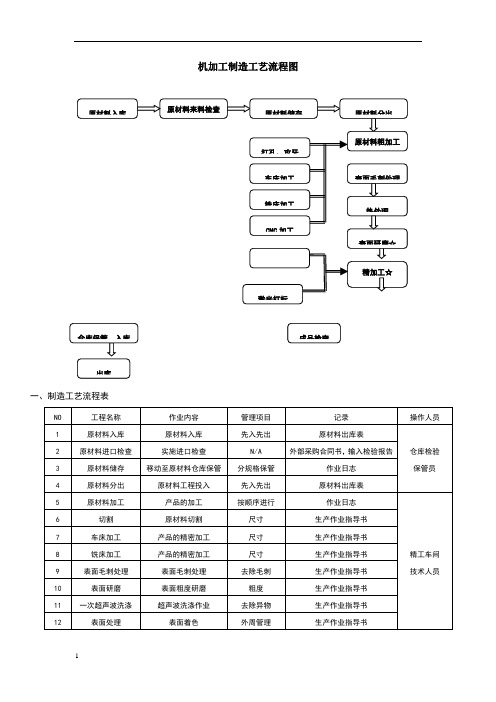
机加工制造工艺流程图
一、制造工艺流程表
二、注:在工艺流程图中带☆标记是主要控制项目和控制点及关键和特殊工序
三、有关制造工艺流程图的详细说明
○使用了通过STM F136机械性能和物理性能验证的不锈钢(17-4 PH)。
○将原材料切割成所需的大小及形状。
○利用切割机分料初步加工之后,再利用加工中心(机床)或者车床进行精密加工;加工尺寸要达到容许误差范围。
接着利用攻螺丝机加工螺孔,然后再用研磨机实施研磨加工。
该工艺属主要控制项目和控制点。
○加工后的材料做为产品以成形,但为了提高表面粗度,进行抛光。
○抛光后进行表面研磨,使表面变得柔和。
○实施抛光处理。
○表面研磨后通过后处理,激光打标完成加工及进行最终检查。
○完成最终检查之后,再用超声波洗涤,成品检查然后结束包装,贴标签入库。
该工艺属关键和特殊工序。
※从原料入库到成品出库,根据产品标准书,ISO9001及YY/T0287标准要求的规定,全程记录及管理。
- 1、下载文档前请自行甄别文档内容的完整性,平台不提供额外的编辑、内容补充、找答案等附加服务。
- 2、"仅部分预览"的文档,不可在线预览部分如存在完整性等问题,可反馈申请退款(可完整预览的文档不适用该条件!)。
- 3、如文档侵犯您的权益,请联系客服反馈,我们会尽快为您处理(人工客服工作时间:9:00-18:30)。
零件加工工艺流程图
零件加工工艺流程图主要是指将原材料通过一系列加工工艺和工序加工成最终产品的过程。
下面是一个典型的零件加工工艺流程图,包含以下几个关键工艺和工序。
第一步:原材料准备
1. 初步检查原材料质量和规格是否符合要求;
2. 使用机械设备将原材料进行截断,确保尺寸符合工艺要求;
3. 为了提高材料的切削性能,可以对原材料进行火焰热处理。
第二步:粗加工
1. 使用加工中心或车床将原材料进行初步加工,包括车削、铣削、钻孔等工序;
2. 根据设计要求,进行粗磨和刨削,以形成基本的几何形状;
3. 进行相关表面处理,如打磨、抛光等。
第三步:精加工
1. 进一步进行车削、铣削、钻孔等精细加工工序;
2. 对产品进行精磨和研磨,以提高几何和尺寸精度;
3. 进行光洁度检测和表面质量检查。
第四步:热处理
1. 对零件进行热处理,包括淬火、回火、退火等工艺;
2. 通过热处理改变零件的物理和化学性质,提高其强度和耐磨性。
第五步:表面处理
1. 零件经过镀铬、电镀、镀镍等表面处理;
2. 通过表面处理提高零件的抗腐蚀性能、耐磨损性能等。
第六步:装配和焊接
1. 将多个零件进行装配,使用螺栓、焊接等方法进行固定;
2. 进行装配过程中的调试和检测,确保零件装配正确。
第七步:质量检验
1. 对加工完成的零件进行质量检验,包括尺寸检测、硬度测试、金属组织分析等;
2. 检查零件表面的光洁度、毛刺等。
第八步:包装和运输
1. 将加工完成的零件进行包装,以防止零件在运输过程中受到损坏;
2. 运输零件到目的地。
以上是一个典型的零件加工工艺流程图,包括原材料准备、粗加工、精加工、热处理、表面处理、装配和焊接、质量检验、包装和运输等关键工艺和工序。
不同的零件加工流程可能会有所不同,但大致流程是相似的。
通过合理的工艺流程和工序控制,可以确保零件加工的质量和精度,提高零件的整体性能和寿命。