烧结
材料烧结的主要作用
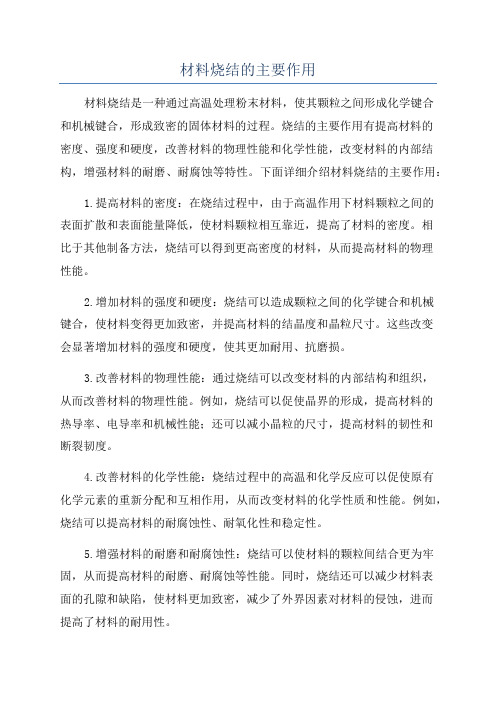
材料烧结的主要作用材料烧结是一种通过高温处理粉末材料,使其颗粒之间形成化学键合和机械键合,形成致密的固体材料的过程。
烧结的主要作用有提高材料的密度、强度和硬度,改善材料的物理性能和化学性能,改变材料的内部结构,增强材料的耐磨、耐腐蚀等特性。
下面详细介绍材料烧结的主要作用:1.提高材料的密度:在烧结过程中,由于高温作用下材料颗粒之间的表面扩散和表面能量降低,使材料颗粒相互靠近,提高了材料的密度。
相比于其他制备方法,烧结可以得到更高密度的材料,从而提高材料的物理性能。
2.增加材料的强度和硬度:烧结可以造成颗粒之间的化学键合和机械键合,使材料变得更加致密,并提高材料的结晶度和晶粒尺寸。
这些改变会显著增加材料的强度和硬度,使其更加耐用、抗磨损。
3.改善材料的物理性能:通过烧结可以改变材料的内部结构和组织,从而改善材料的物理性能。
例如,烧结可以促使晶界的形成,提高材料的热导率、电导率和机械性能;还可以减小晶粒的尺寸,提高材料的韧性和断裂韧度。
4.改善材料的化学性能:烧结过程中的高温和化学反应可以促使原有化学元素的重新分配和互相作用,从而改变材料的化学性质和性能。
例如,烧结可以提高材料的耐腐蚀性、耐氧化性和稳定性。
5.增强材料的耐磨和耐腐蚀性:烧结可以使材料的颗粒间结合更为牢固,从而提高材料的耐磨、耐腐蚀等性能。
同时,烧结还可以减少材料表面的孔隙和缺陷,使材料更加致密,减少了外界因素对材料的侵蚀,进而提高了材料的耐用性。
总之,材料烧结是一种重要的制备方法,其主要作用包括提高材料的密度、强度和硬度,改善材料的物理性能和化学性能,改变材料的内部结构,增强材料的耐磨、耐腐蚀等特性。
这些作用使得烧结成为一种广泛应用于各个领域的材料制备技术。
材料的烧结名词解释
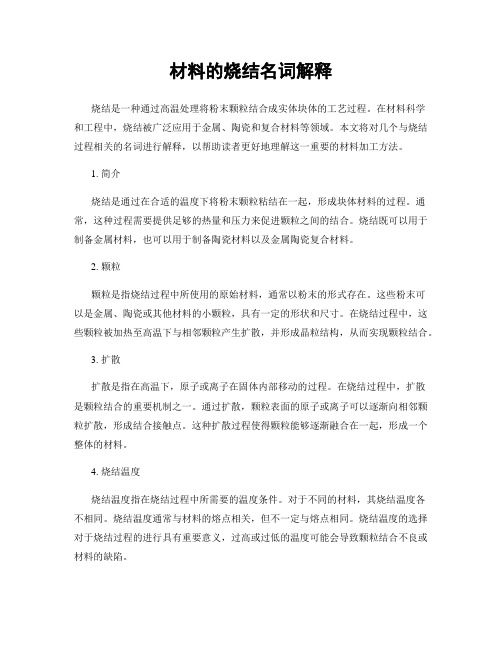
材料的烧结名词解释烧结是一种通过高温处理将粉末颗粒结合成实体块体的工艺过程。
在材料科学和工程中,烧结被广泛应用于金属、陶瓷和复合材料等领域。
本文将对几个与烧结过程相关的名词进行解释,以帮助读者更好地理解这一重要的材料加工方法。
1. 简介烧结是通过在合适的温度下将粉末颗粒粘结在一起,形成块体材料的过程。
通常,这种过程需要提供足够的热量和压力来促进颗粒之间的结合。
烧结既可以用于制备金属材料,也可以用于制备陶瓷材料以及金属陶瓷复合材料。
2. 颗粒颗粒是指烧结过程中所使用的原始材料,通常以粉末的形式存在。
这些粉末可以是金属、陶瓷或其他材料的小颗粒,具有一定的形状和尺寸。
在烧结过程中,这些颗粒被加热至高温下与相邻颗粒产生扩散,并形成晶粒结构,从而实现颗粒结合。
3. 扩散扩散是指在高温下,原子或离子在固体内部移动的过程。
在烧结过程中,扩散是颗粒结合的重要机制之一。
通过扩散,颗粒表面的原子或离子可以逐渐向相邻颗粒扩散,形成结合接触点。
这种扩散过程使得颗粒能够逐渐融合在一起,形成一个整体的材料。
4. 烧结温度烧结温度指在烧结过程中所需要的温度条件。
对于不同的材料,其烧结温度各不相同。
烧结温度通常与材料的熔点相关,但不一定与熔点相同。
烧结温度的选择对于烧结过程的进行具有重要意义,过高或过低的温度可能会导致颗粒结合不良或材料的缺陷。
5. 烧结压力烧结压力是指在烧结过程中施加在颗粒上的压力。
通过施加适当的压力,可以促进颗粒之间的结合,提高烧结的效率和质量。
烧结压力的大小取决于烧结过程中所使用的设备和材料的性质。
通常情况下,较高的烧结压力可以达到更密实的结构。
6. 烧结时间烧结时间是指颗粒在高温下进行烧结过程所需要的时间。
对于不同的材料和烧结条件,烧结时间各不相同。
烧结时间的选择应综合考虑烧结温度、压力和材料的性质等因素。
较长的烧结时间可以提高材料的致密性和结合强度,但过长的时间可能会导致颗粒生长过大或发生异常晶粒长大。
烧结的工艺流程
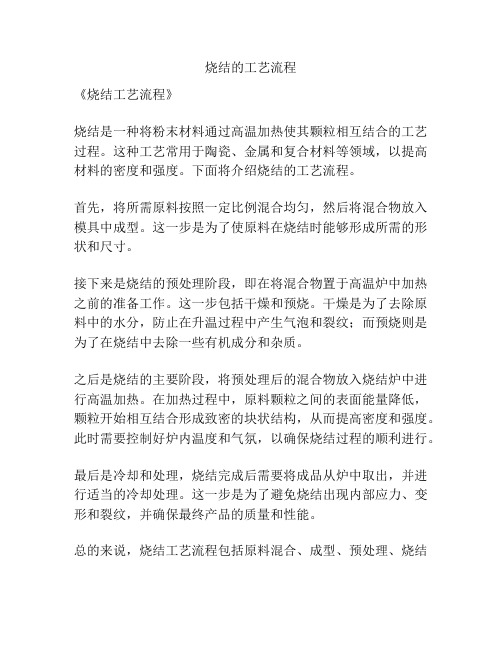
烧结的工艺流程
《烧结工艺流程》
烧结是一种将粉末材料通过高温加热使其颗粒相互结合的工艺过程。
这种工艺常用于陶瓷、金属和复合材料等领域,以提高材料的密度和强度。
下面将介绍烧结的工艺流程。
首先,将所需原料按照一定比例混合均匀,然后将混合物放入模具中成型。
这一步是为了使原料在烧结时能够形成所需的形状和尺寸。
接下来是烧结的预处理阶段,即在将混合物置于高温炉中加热之前的准备工作。
这一步包括干燥和预烧。
干燥是为了去除原料中的水分,防止在升温过程中产生气泡和裂纹;而预烧则是为了在烧结中去除一些有机成分和杂质。
之后是烧结的主要阶段,将预处理后的混合物放入烧结炉中进行高温加热。
在加热过程中,原料颗粒之间的表面能量降低,颗粒开始相互结合形成致密的块状结构,从而提高密度和强度。
此时需要控制好炉内温度和气氛,以确保烧结过程的顺利进行。
最后是冷却和处理,烧结完成后需要将成品从炉中取出,并进行适当的冷却处理。
这一步是为了避免烧结出现内部应力、变形和裂纹,并确保最终产品的质量和性能。
总的来说,烧结工艺流程包括原料混合、成型、预处理、烧结
和冷却处理这几个主要阶段。
通过精确地控制每个环节,可以获得致密、坚固和具有优良性能的烧结制品。
烧结工艺流程

烧结工艺流程烧结是指将粉煤灰、粉煤、石灰石、矿渣等原料通过一定的热处理工艺,使其在高温下结合成块状的固体材料的工艺过程。
烧结工艺是冶金、化工、建材等行业中常见的生产工艺之一,其产品广泛应用于水泥生产、冶金工业、建筑工程等领域。
下面将介绍烧结工艺的流程及其关键步骤。
1. 原料准备。
烧结工艺的第一步是原料的准备。
通常情况下,原料包括粉煤灰、粉煤、石灰石、矿渣等。
这些原料需要经过粉碎、混合等处理,以确保其颗粒大小和化学成分的均匀性,从而保证烧结后的产品质量。
2. 配料混合。
经过原料准备后,需要将各种原料按照一定的配比进行混合。
混合的目的是使各种原料充分混合,确保烧结后产品的化学成分均匀,并且提高烧结料的透气性和流动性。
3. 成型。
混合好的原料需要进行成型,通常采用压制成型或浇铸成型的方式。
压制成型是将原料放入成型机中,通过一定的压力将原料压制成一定形状的块状体。
浇铸成型则是将原料熔化后倒入模具中进行成型。
4. 预烧。
成型后的块状体需要进行预烧处理。
预烧是指将成型体在较低温度下进行热处理,以去除其中的水分和一些有机物,提高其强度和耐火性。
5. 烧结。
经过预烧处理后的块状体需要进行烧结。
烧结是将预烧后的块状体在高温下进行加热,使其在颗粒间发生化学反应,形成坚固的结合。
烧结的温度和时间是影响产品质量的重要因素。
6. 冷却。
烧结后的产品需要进行冷却处理。
冷却是将烧结后的产品缓慢降温,以避免产生内部应力和裂纹,确保产品的完整性和稳定性。
7. 成品。
经过冷却处理后,烧结产品即成为最终的成品。
成品可以根据需要进行包装、储存和运输,以满足不同领域的需求。
总结。
烧结工艺流程包括原料准备、配料混合、成型、预烧、烧结、冷却和成品等关键步骤。
每个步骤都对产品的质量和性能有着重要影响,需要严格控制和管理。
烧结工艺的优化和改进,可以提高产品的品质,降低生产成本,促进工艺的可持续发展。
烧结过程及机理

气氛
气氛对烧结过程的 影响
气氛是烧结过程中的一个重要 因素。气氛中的气体成分可以 与材料发生化学反应,从而影 响烧结过程和材料的性能。
气氛对材料相变的 影响
在烧结过程中,气氛中的气体 成分可以与材料发生化学反应 ,导致材料发生相变。这种相 变可以改变材料的物理和化学 性质,因此控制气氛可以实现 对材料相变和性能的调控。
压力
压力对烧结过程的影响
压力是烧结过程中的另一个重要参数。在适宜的压力范围内,随着压力的增加,烧结速率 加快,材料的致密度和强度增加。
压力对材料结构的影响
在烧结过程中,压力可以改变材料的结构。例如,在高温高压条件下,某些材料会发生晶 体结构的改变或相变,从而改变材料的性能。
压力对扩散的影响
压力可以影响材料内部原子或分子的扩散速度。在烧结过程中,扩散速度决定了材料的致 密化程度和显微结构,因此控制压力可以实现对材料结构和性能的调控。
烧结的重要性
烧结是材料制备过程中的重要环节,通过 烧结可以获得高性能的材料,广泛应用于 航空航天、汽车、电子、能源等领域。
通过优化烧结工艺参数和添加合金元 素等方法,可以进一步改善材料的性 能,提高其综合性能和应用价值。
烧结过程可以改变材料的物理和化学性质 ,如密度、硬度、电导率、热导率等,从 而满足不同领域对材料性能的需求。
陶瓷材料的烧结机理主要包括扩散传质和流动传质,扩散 传质是材料内部质点通过热运动进行迁移的过程,流动传 质则是气体在压力作用下通过材料孔隙的流动过程。
金属材料
金属材料的烧结过程是在一定的温度和压力下,通过原子或分子的扩散和流动,使松散的金属粉末颗 粒紧密结合在一起,形成致密的金属块体。金属材料具有高强度、高导电性、高导热性等优点,广泛 应用于机械、电子、航空航天等领域。
烧结工艺介绍

烧结工艺介绍烧结工艺是一种常见的冶金工艺,用于将粉末状物质加热至接触点熔融,形成固态结合体的过程。
本文将介绍烧结工艺的原理、应用范围以及工艺流程。
一、原理烧结是通过热量作用使粉末颗粒表面融合,而形成较强的固态接触的过程。
烧结过程中,粉末颗粒相互接触,颗粒表面由于温度升高而软化或熔化,粒子间形成了弥散相和连续相,使颗粒间形成了较强的结合力。
通过控制加热温度、时间以及加压力度等工艺参数,使颗粒状物质在相互接触的同时,形成致密且高强度的结构体。
二、应用范围烧结工艺在冶金、陶瓷、粉末冶金、高分子材料等领域有着广泛的应用。
1. 冶金领域烧结工艺在冶金领域广泛应用于粉末冶金制品的制备,如金属粉末冶金零件、冶金陶瓷、高合金材料等。
2. 陶瓷领域烧结是陶瓷领域中常用的制备工艺之一,通过烧结工艺可以制备出具有高强度和良好耐磨性的陶瓷制品,如瓷砖、陶瓷碗碟等。
3. 粉末冶金领域粉末冶金是一种以粉末为原料,通过烧结工艺制备制品的工艺。
烧结工艺可以将金属粉末制备成各种零件,如齿轮、凸轮等。
4. 高分子材料领域烧结工艺在高分子材料领域中用于制备具有特殊性能的塑料制品,如高强度塑料零件、高耐磨塑料制品等。
三、工艺流程烧结工艺的基本流程包括原料制备、粉末颗粒的装填、加热烧结和冷却等步骤。
1. 原料制备:首先需要根据所需制品的要求,选择合适的原料并对其进行加工和处理。
这一步骤可以包括粉末的混合、筛分以及添加特定添加剂等。
2. 粉末颗粒的装填:将经过处理的粉末颗粒通过特定的装填方式填入烧结模具中。
装填要求均匀且适量,以确保烧结过程中的热量传导均匀。
3. 加热烧结:将装有粉末颗粒的模具放入烧结炉中,加热至一定温度并保持一定时间。
温度和时间的选择根据所需制品的要求来确定。
4. 冷却:烧结结束后,需要进行冷却处理。
冷却可以通过自然冷却或者采用特殊的冷却方法来进行。
四、工艺优势烧结工艺相对于其他加工方式具有以下优势:1. 提高材料的致密度和强度。
烧结的基本过程

《烧结的基本过程》同学们,今天咱们来了解一下烧结的基本过程。
你们可能会问,什么是烧结呀?其实,烧结就是把一些粉末状的东西变成一个坚固的整体。
那它是怎么做到的呢?简单说,就是先把粉末堆在一起,然后加热。
就好像我们做饼干,把面粉等材料混合好,再放进烤箱里烤。
比如说,制造砖头的时候,就会用到烧结。
把泥土弄成粉末,然后放进一个特别的炉子里加热,出来就是坚硬的砖头啦。
有个小工厂,专门生产零件,他们就用烧结的方法。
把一些金属粉末加热后,就变成了结实好用的零件。
同学们,现在是不是对烧结有点概念啦?《烧结的基本过程》同学们呀,咱们来聊聊烧结的基本过程。
烧结这个词,听起来有点陌生,其实很有趣。
想象一下,有一堆小小的粉末,它们分散着,没什么力气。
但是经过烧结,它们就能团结在一起,变得很强壮。
比如制作陶瓷,把陶土粉末弄好,经过高温烧结,就成了漂亮的陶瓷碗、陶瓷杯。
我听说过一个故事,有个小朋友好奇地看着爸爸工作,爸爸就是在做烧结,把一些材料变成有用的东西。
小朋友觉得太神奇啦!同学们,烧结是不是很有意思呢?《烧结的基本过程》同学们,今天咱们说一说烧结的基本过程。
你们知道吗?烧结能让一些小小的粉末变得很厉害。
一开始,粉末们松松散散的。
然后给它们加热,它们就开始发生变化啦。
就像一群小伙伴,本来各自玩耍,后来一起努力,变成了一个强大的团队。
比如说,制造铁锅的时候,也是用烧结。
把铁的粉末加热,就有了我们家里用的铁锅。
有一次,我去工厂参观,看到了烧结的过程,那场面可壮观啦!同学们,烧结是不是很神奇呀?。
烧结工艺知识点总结大全

烧结工艺知识点总结大全一、烧结原理1. 烧结是指将粉末材料在一定温度下加热,使其颗粒间发生结合,形成致密的块状产品。
烧结的基本原理是固相扩散,即热力学上的固相之间的扩散过程。
2. 烧结过程中主要有三种力学过程,分别为颗粒间的原子扩散、颗粒间的表面扩散和颗粒间的体扩散。
这三种扩散方式相互作用,共同促进颗粒间发生结合。
3. 烧结过程中温度、时间和压力是影响烧结效果的重要因素。
通过控制这些参数,可以使烧结过程更加均匀和有效。
二、烧结设备1. 烧结设备主要包括热处理炉、烧结炉、烧结机等。
不同的烧结设备适用于不同的烧结材料和工艺要求。
2. 烧结设备的主要部件包括燃烧室、加热炉、炉膛、热风循环系统、控制系统等。
这些部件共同作用,实现对粉末材料的加热和烧结作用。
3. 热处理炉是常见的烧结设备之一,主要通过电阻加热、气体燃烧等方式对粉末材料进行加热处理,适用于各种金属和非金属材料的烧结工艺。
三、烧结工艺控制1. 烧结工艺控制是烧结过程中的关键环节,可以通过控制温度、时间、压力等参数,实现对烧结过程的精确控制。
2. 烧结工艺控制的主要方法包括PID控制、自适应控制、模糊控制等。
这些控制方法通过对烧结过程中的各个参数进行实时监测和调整,以实现对烧结过程的精确控制。
3. 在实际生产中,烧结工艺控制可以通过计算机控制系统实现自动化,提高生产效率和产品质量。
四、烧结材料选型1. 烧结工艺适用于各种粉末材料,包括金属粉末、陶瓷粉末、粉末冶金材料等。
根据不同的材料性质和要求,选择合适的烧结工艺和设备。
2. 烧结材料的选型考虑因素包括原料种类、粒度、成分、形状等。
根据不同的要求,选择合适的烧结材料,可以有效提高产品质量和生产效率。
3. 在烧结材料选型过程中,也需要考虑成本、资源利用率和环境保护等方面的因素,以实现经济、环保和可持续发展。
五、烧结工艺的应用1. 烧结工艺广泛应用于金属、陶瓷、粉末冶金、电子材料等行业。
在金属制品生产中,烧结工艺可以用于制造各种粉末冶金制品、焊接材料、钎焊材料等。
烧结理论及工艺要求

烧结理论及工艺要求
一、烧结理论
烧结,它是一种特殊的金属加工方法,是将金属粉末或粒子因加热及
压实而聚结成固态或凝固态的工艺。
烧结过程一般分为三个阶段,疏松期、烧结期和结晶期。
烧结期包括加热期、热压期和持热期。
1、疏松期:粉末在温度小于熔点时,它的聚结能力较低,它的表面
比较滑,一般称为粉末状态,它既可以形成颗粒和宏观结构。
2、烧结期:当温度上升到金属熔点以上时,粉末微粒之间的聚结能
力增强,它的表面光滑,此时粉末形成了小的颗粒,并可以粘合在一起,
形成较大的烧结体。
3、结晶期:当温度上升到金属晶体化温度时,粉末发生晶体结构,
进一步烧结,形成金属晶体。
二、烧结工艺要求
1、烧结温度:烧结温度是控制烧结成果的重要参数,一般来说,烧
结温度应高于金属的熔点,低于其晶体化温度。
2、压力:压力也是影响烧结成果的重要参数。
如果压力太低,烧结
质量就会受到影响,这时就需要使用较高的压力,以保证烧结质量。
3、时间:在烧结过程中,烧结时间也是一个重要的参数,如果烧结
时间不足,就可能导致金属的结晶不匀,从而影响烧结的成果。
烧结的概念——精选推荐

第十二章烧结(Sinter)第一节基本概念一、烧结1、烧结的意义烧结是粉末冶金、陶瓷、耐火材料、超高温材料等部门的一个重要工序。
烧结的目的是把粉状物料转变为致密体。
这种烧结致密体是一种多晶材料,其显微结构由晶体、玻璃相和气孔组成,烧结过程直接影响显微结构中晶粒尺寸和分布,气孔尺寸和分布以及晶界体积分数….。
烧结过程可以通过控制晶界移动而抑制晶粒的异常生长或通过控制表面扩散、晶界扩散和晶格扩散而充填气孔,用改变显微结构方法使材料性能改善。
因此,当配方、原料粒度、成型等工序完成以后,烧结是使材料获得预期的显微结构以使材料性能充分发挥的关键工序。
2、烧结的定义宏观定义:一种或多种固体(金属、氧化物、氮化物等)粉末经过成型,在加热到一定温度后开始收缩,在低于熔点温度下变成致密、坚硬的烧结体,这种过程称为烧结。
微观定义:由于固态中分子(或原子)的相互吸引,通过加热,使粉末体产生颗粒粘结,经过物质迁移使粉末体产生强度并导致致密化和再结晶的过程。
由于烧结体宏观上出现体积收缩,致密度提高和强度增加,因此烧结程度可以用坯体收缩率、气孔率、吸水率或烧结体密度与理论密度之比(相对密度)等指标来衡量。
3、与烧结有关的一些概念A.烧结与烧成(firing):烧成:包括多种物理和化学变化。
例如脱水、坯体内气体分解、多相反应和熔融、溶解、烧结等。
而烧结仅仅指粉料经加热而致密化的简单物理过程,烧结仅仅是烧成过程的一个重要部分。
B.烧结和熔融(Melt):烧结是在远低于固态物质的熔融温度进行的。
泰曼发现烧结温度(T S)和熔融温度(T M)的关系有一定规律:金属粉末 T S=(0.3~0.4)T M盐类 T S=0.57T M硅酸盐 T S=(0.8~0.9)T M烧结和熔融这两个过程都是由原子热振动而引起的,但熔融时全部组元都为液相,而烧结时至少有一组元是处于固态。
C.烧结与固相反应:两个过程均在低于材料熔点或熔融温度之下进行的。
烧结工艺的目的和原理

烧结工艺的目的和原理烧结工艺是一种制备陶瓷、金属、合金等材料的工艺方法,其主要目的是将粉末材料在高温下加热,使其粒子之间产生相互结合和颗粒增大,从而形成致密的固体材料。
通过烧结,可以改善材料的力学性能和化学稳定性,提高材料的密度、硬度、强度和导电性等性能,并增加其使用寿命和可靠性。
1.粒子结合:烧结过程中,粉末颗粒间通过热作用力和压缩力相互结合,形成颗粒间的连接。
该连接可以是颗粒间的摩擦力和间隙力,也可以是颗粒间的化学键和晶格力。
当温度升高时,形成颗粒结合的力逐渐增强,使得粉末材料的孔隙度减小,粒径增大,颗粒之间的接触面积增大,从而提高材料的强度和致密度。
2.晶粒生长:烧结过程中,晶体表面的原子或分子在高温下扩散,并产生结晶生长。
这种晶粒生长包括晶核生成、晶体生长和晶界融合等过程。
随着温度的升高,晶粒生长速度加快,晶粒尺寸增大,从而使材料的晶界面积减少,晶格结构更加密集,提高材料的力学性能。
3.成分调整:烧结过程中,材料的成分会发生改变。
例如,由于一些元素会在高温下发生氧化、还原和挥发等反应,材料的成分可能发生偏离,从而改变材料的性能。
通过调整烧结条件,可以控制材料的成分,以获得所需的性能和化学稳定性。
4.特殊效应:在烧结工艺中,还存在一些特殊的效应,如颗粒饱满、表面收缩、孔隙扩散等。
这些效应通过烧结过程中的物理和化学变化,导致材料的结构和性能发生变化。
根据材料的需求,可以通过调整烧结条件来控制这些效应,以实现所需的材料性能。
总的来说,烧结工艺的目的是通过高温加热粉末材料,使其粒子间相互结合和颗粒增大,形成致密的固体材料;其原理主要包括粒子结合、晶粒生长、成分调整和特殊效应等。
通过控制烧结条件和方法,可以实现对材料性能的调控和优化,满足不同领域的应用需求。
烧结过程的三个阶段
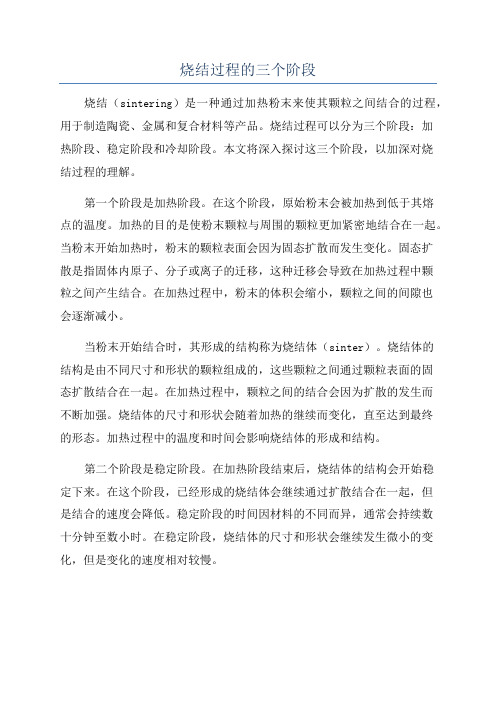
烧结过程的三个阶段烧结(sintering)是一种通过加热粉末来使其颗粒之间结合的过程,用于制造陶瓷、金属和复合材料等产品。
烧结过程可以分为三个阶段:加热阶段、稳定阶段和冷却阶段。
本文将深入探讨这三个阶段,以加深对烧结过程的理解。
第一个阶段是加热阶段。
在这个阶段,原始粉末会被加热到低于其熔点的温度。
加热的目的是使粉末颗粒与周围的颗粒更加紧密地结合在一起。
当粉末开始加热时,粉末的颗粒表面会因为固态扩散而发生变化。
固态扩散是指固体内原子、分子或离子的迁移,这种迁移会导致在加热过程中颗粒之间产生结合。
在加热过程中,粉末的体积会缩小,颗粒之间的间隙也会逐渐减小。
当粉末开始结合时,其形成的结构称为烧结体(sinter)。
烧结体的结构是由不同尺寸和形状的颗粒组成的,这些颗粒之间通过颗粒表面的固态扩散结合在一起。
在加热过程中,颗粒之间的结合会因为扩散的发生而不断加强。
烧结体的尺寸和形状会随着加热的继续而变化,直至达到最终的形态。
加热过程中的温度和时间会影响烧结体的形成和结构。
第二个阶段是稳定阶段。
在加热阶段结束后,烧结体的结构会开始稳定下来。
在这个阶段,已经形成的烧结体会继续通过扩散结合在一起,但是结合的速度会降低。
稳定阶段的时间因材料的不同而异,通常会持续数十分钟至数小时。
在稳定阶段,烧结体的尺寸和形状会继续发生微小的变化,但是变化的速度相对较慢。
稳定阶段的主要目的是确保烧结体的稳定性和一致性。
稳定阶段的结束标志是燃料在烧结体中完全燃尽。
当燃料燃尽时,烧结体的温度会开始降低,以进入第三个阶段。
第三个阶段是冷却阶段。
在冷却阶段,加热源会被移除,并且烧结体会开始冷却。
烧结体的冷却速度会影响其最终的性能和结构。
如果冷却速度过快,可能会导致烧结体的内部产生应力,从而引起开裂或变形。
因此,冷却过程需要在控制的条件下进行,以确保烧结体的质量。
综上所述,烧结过程的三个阶段是加热阶段、稳定阶段和冷却阶段。
加热阶段是使粉末颗粒结合的起始阶段,通过固态扩散来形成烧结体。
陶瓷烧结原理
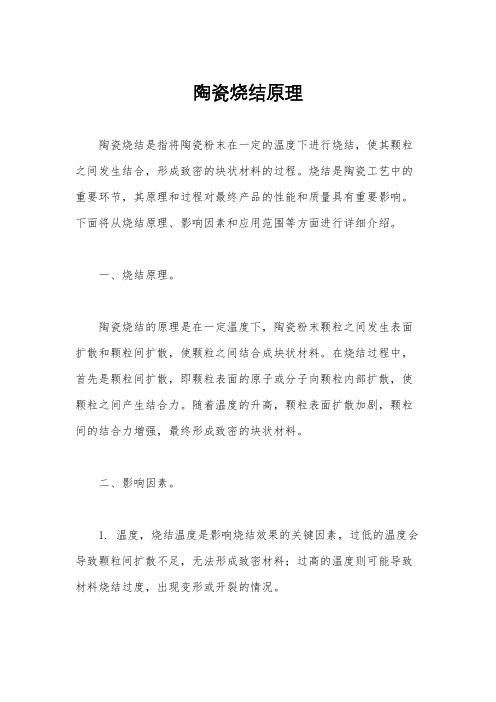
陶瓷烧结原理陶瓷烧结是指将陶瓷粉末在一定的温度下进行烧结,使其颗粒之间发生结合,形成致密的块状材料的过程。
烧结是陶瓷工艺中的重要环节,其原理和过程对最终产品的性能和质量具有重要影响。
下面将从烧结原理、影响因素和应用范围等方面进行详细介绍。
一、烧结原理。
陶瓷烧结的原理是在一定温度下,陶瓷粉末颗粒之间发生表面扩散和颗粒间扩散,使颗粒之间结合成块状材料。
在烧结过程中,首先是颗粒间扩散,即颗粒表面的原子或分子向颗粒内部扩散,使颗粒之间产生结合力。
随着温度的升高,颗粒表面扩散加剧,颗粒间的结合力增强,最终形成致密的块状材料。
二、影响因素。
1. 温度,烧结温度是影响烧结效果的关键因素,过低的温度会导致颗粒间扩散不足,无法形成致密材料;过高的温度则可能导致材料烧结过度,出现变形或开裂的情况。
2. 时间,烧结时间也是影响烧结效果的重要因素,过短的时间会导致烧结不完全,材料性能不达标;过长的时间则可能造成能耗浪费和生产效率低下。
3. 压力,在烧结过程中施加一定的压力可以促进颗粒间的结合,提高烧结效率和材料密度。
4. 添加剂,适量的添加剂可以改善陶瓷粉末的流动性和烧结性能,提高最终产品的质量。
三、应用范围。
陶瓷烧结广泛应用于陶瓷制品的生产过程中,如陶瓷砖、陶瓷器皿、陶瓷瓷砖等。
通过烧结工艺,可以使陶瓷制品具有较高的强度、硬度和耐磨性,满足不同领域的需求。
总结,陶瓷烧结是一项重要的陶瓷加工工艺,其原理是在一定温度下实现颗粒间的结合,影响因素包括温度、时间、压力和添加剂等,应用范围广泛,可用于生产各种陶瓷制品。
掌握烧结原理和技术,对于提高陶瓷制品的质量和性能具有重要意义。
烧结 原理

烧结原理
烧结是一种将金属或非金属粉末通过热处理使其结合变硬的工艺。
它广泛应用于制造陶瓷、金属件和复合材料等产品。
烧结的原理是将粉末在高温下加热,使其表面熔化并黏合在一起。
在烧结过程中,粉末颗粒之间发生热扩散,使得颗粒接触面积增大。
随着温度升高,金属或非金属颗粒之间的原子迁移速度增加,有利于形成更密实的结合。
同时,由于粉末之间存在表面张力,烧结过程中颗粒表面逐渐熔化并形成颗粒间的接触点。
烧结的过程分为初烧结和返炉烧结两个阶段。
初烧结阶段,通过升高温度使颗粒间的结合更紧密,但仍然存在空隙。
返炉烧结阶段是在初烧结的基础上继续加热并施加压力,以进一步减小颗粒间的空隙,达到更高的密度和硬度。
烧结工艺的优势包括高材料利用率、高生产效率和良好的产品均匀性。
同时,烧结还可以用于制造复杂形状的产品,如陶瓷模具和金属零件。
然而,烧结过程中也存在一些问题,例如颗粒间的烧结不均匀、气孔和缺陷的产生等,这些问题需要在工艺设计和优化中加以解决。
总之,烧结是一种通过高温加热将粉末熔结在一起的工艺。
通过烧结,可以制造出高密度、硬度和耐磨的材料,广泛应用于各个领域。
烧结名词解释

烧结是指将粉状或颗粒状原料在一定条件下加热至一定温度,使其颗粒之间发生结合并形成固体块状的过程。
在材料工程和冶金学中,烧结通常是用于制造陶瓷、金属和合金等材料的一种常见加工方法。
烧结过程中,原料颗粒表面的一小部分会熔化,形成一种称为熔液的液体相。
这些熔液在高温下具有表面张力,可以使颗粒之间产生结合力。
当温度升高时,熔液会在颗粒之间扩散,并在冷却过程中形成固体相。
这种固体相由于颗粒之间的结合而形成坚固的结构。
烧结的主要目的是增强材料的力学性能、改善材料的密实性和减少孔隙率。
通过烧结,原料颗粒之间的结合力得以增强,从而提高了材料的强度和硬度。
此外,烧结还可以消除原料颗粒之间的间隙,减少材料的孔隙率,提高材料的密实性和耐久性。
烧结技术在多个领域得到广泛应用。
例如,在陶瓷工业中,烧结用于制造陶瓷瓷砖、陶瓷器具和陶瓷零件。
在金属工业中,烧结常用于制造金属粉末冶金零件、硬质合金和磁性材料等。
此外,烧结还可以用于制造复合材料、矿石的烧结还原等多个领域。
烧结是一种通过加热原料颗粒使其结合形成块状固体的加工方法,广泛应用于材料工程和冶金学中,以提高材料的力学性能、密实性和耐久性。
烧结
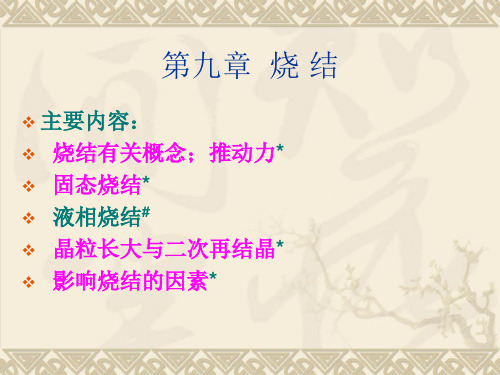
Ⅰ.烧结时间:
如NaF和Al2O3 试块的烧结收缩曲线
x 5 Ⅱ.原料的起始粒度: r 粒度与接触颈部增长关系图 r 在扩散传质的烧结过程中,起始粒度的控制相当重要 3
Ⅲ.温度对烧结过程的决定性作用
温度升高,自扩散系数 D* D0 exp( Q RT )
D*明显增大,故升高温度必然加快烧结的进行。
对球形曲率:弯曲表面由于表面张力而造成的压差
1 1 P ( ) 对非球形曲面: r1 r2
烧结的推动力:
2 P r
G VP
结论:弯曲表面上的附加压力与球形颗粒 ( 或曲面 ) 曲率
半径成反比,与粉料表面张力成正比,故粉料越细,由 曲率引起的烧结推动力越大
x 160D * 5 5 5 ( ) r t r kT
1 3 1
扩散传质初期动力学方程可以写成:
Y
P
1 Kt log Y log t K ' P
Y — 烧结收缩率 K — 烧结速率常数 t — 烧结时间
logY—t作图为一直线,截矩 =K’(随T升高而升高),斜率=1/P(不 随T变化)
颈表面 颗粒接触点 空位扩散方向: 颈表面 颗粒内部
扩散方式:表面扩散、晶界扩散、体积扩散
2. 扩散传质的动力学 (1) 烧结初期 烧结初期物质迁移路线图 坯体变化:以表面扩散为主,气孔率大,收缩约在 1%左右 动力学方程:
颈部增长速率:
x 160 D * 5 5 5 ( ) r t r kT
第九章 烧 结
主要内容:
烧结有关概念;推动力* 固态烧结* 液相烧结# 晶粒长大与二次再结晶* 影响烧结的因素*
烧结工艺的操作方法
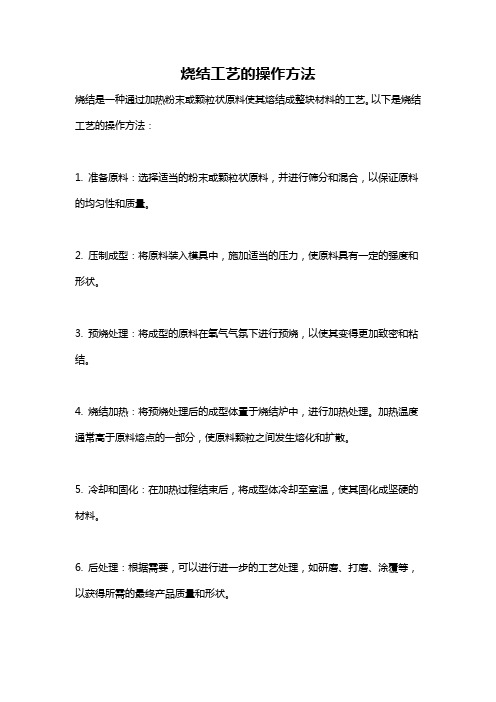
烧结工艺的操作方法
烧结是一种通过加热粉末或颗粒状原料使其熔结成整块材料的工艺。
以下是烧结工艺的操作方法:
1. 准备原料:选择适当的粉末或颗粒状原料,并进行筛分和混合,以保证原料的均匀性和质量。
2. 压制成型:将原料装入模具中,施加适当的压力,使原料具有一定的强度和形状。
3. 预烧处理:将成型的原料在氧气气氛下进行预烧,以使其变得更加致密和粘结。
4. 烧结加热:将预烧处理后的成型体置于烧结炉中,进行加热处理。
加热温度通常高于原料熔点的一部分,使原料颗粒之间发生熔化和扩散。
5. 冷却和固化:在加热过程结束后,将成型体冷却至室温,使其固化成坚硬的材料。
6. 后处理:根据需要,可以进行进一步的工艺处理,如研磨、打磨、涂覆等,以获得所需的最终产品质量和形状。
需要注意的是,不同的烧结工艺可能存在一些差异,具体的操作方法可能会有所不同。
因此,在实际操作中需要根据具体的工艺要求和设备条件进行调整和优化。
一烧结基本原理

一烧结基本原理烧结是一种将粉末状物质通过加热处理,使其颗粒间发生结合,形成致密坚固固体的加工工艺。
烧结的基本原理是利用粉末颗粒间的表面扩散和粘结现象。
粉末颗粒间的表面扩散是指在高温下,粉末颗粒表面的原子或离子因能量梯度而发生位移,从而扩散到颗粒表面。
在颗粒接触面上,颗粒表面扩散相遇时,就会发生粒间结合。
而粘结是颗粒间相互吸附,并形成新的键合力。
烧结的主要工艺分为两个阶段:初级焙烧和二次烧结。
初级焙烧是将粉末颗粒在升温的重力作用下接触、聚结和烧结的过程。
通过初级焙烧可以使粉末颗粒间的结合力增强,颗粒之间的间隙减小,从而增加烧结体的密实性。
在初级焙烧过程中,粉末颗粒表面的扩散使颗粒间形成颗粒接触,再通过粘结力增强颗粒间的粘结,并最终使粉末颗粒相互结合成为一体。
二次烧结是在初级焙烧的基础上进行的再烧结过程。
在初级焙烧中已形成的颗粒结合体在二次烧结中会继续收缩,使得颗粒之间的间隙进一步减小,从而提高烧结体的致密性。
在二次烧结的过程中,粉末颗粒表面扩散再次发生,使得原本疏松的颗粒结合体进一步密实与凝结。
烧结的基本原理在于高温下的颗粒表面扩散和粘结,这些现象使粉末颗粒相互结合成为一体,从而形成坚固致密的烧结体。
烧结常用于金属和陶瓷等材料的加工过程中,可以改善材料的强度、致密性、耐磨性和导热性等性能。
烧结还可以制备各种复杂形状和高精度的工件,广泛应用于航空航天、汽车、机械、电子等领域。
同时,烧结也是一种高效的资源利用方式,可以回收再利用废弃粉末,减少资源浪费。
总之,烧结的基本原理是利用粉末颗粒间的表面扩散和粘结现象,在高温下使粉末颗粒相互结合成为一体,从而形成致密坚固的固体。
烧结是一种重要的材料制备工艺,具有广泛的应用前景和重要的经济意义。
烧结的原理

烧结的原理烧结是一种重要的冶金工艺,广泛应用于铁矿石、铬矿石、锰矿石等矿石的加工过程中。
烧结的原理是通过矿石颗粒之间的结合作用,将散乱的矿石颗粒烧结成块状物,以便于后续的冶炼和加工。
本文将从烧结的原理入手,对烧结过程中所涉及的关键原理进行介绍。
首先,烧结的原理涉及到矿石颗粒之间的结合作用。
在烧结过程中,矿石颗粒经过高温热处理,表面会产生一层熔融的物质,这些物质能够在颗粒之间形成一种粘结作用,使得颗粒能够相互结合。
同时,烧结过程中还会产生一些气体,这些气体会在颗粒之间形成一种“填隙”作用,使得颗粒之间的结合更加牢固。
其次,烧结的原理还涉及到热传导和热膨胀。
在烧结过程中,矿石颗粒会受到高温的加热,从而导致颗粒内部温度升高。
当颗粒内部温度升高时,颗粒会发生热膨胀,使得颗粒之间的接触面积增大,从而促进颗粒之间的结合。
同时,热传导也会使得矿石颗粒表面的熔融物质能够向颗粒内部传导,进一步增强颗粒之间的结合作用。
另外,烧结的原理还与矿石颗粒的化学成分和结构特性有关。
不同种类的矿石在烧结过程中会产生不同的熔融物质,这些熔融物质的性质会影响矿石颗粒之间的结合情况。
同时,矿石颗粒的结构特性,如颗粒的形状、大小、表面粗糙度等也会影响烧结的效果。
最后,烧结的原理还与烧结工艺参数的选择有关。
在实际的烧结过程中,烧结温度、烧结时间、烧结气氛等参数的选择会直接影响烧结的效果。
合理选择这些参数,可以使烧结过程更加有效,提高烧结块的质量和产量。
总之,烧结的原理是一个复杂的物理化学过程,涉及到矿石颗粒之间的结合作用、热传导和热膨胀、化学成分和结构特性以及烧结工艺参数等多个方面。
只有深入理解烧结的原理,才能更好地指导烧结工艺的实际应用,提高烧结产品的质量和产量。
- 1、下载文档前请自行甄别文档内容的完整性,平台不提供额外的编辑、内容补充、找答案等附加服务。
- 2、"仅部分预览"的文档,不可在线预览部分如存在完整性等问题,可反馈申请退款(可完整预览的文档不适用该条件!)。
- 3、如文档侵犯您的权益,请联系客服反馈,我们会尽快为您处理(人工客服工作时间:9:00-18:30)。
1
又烧结初期 x >>ρ,故上式可写成:
ΔP
γMp0 dRTρ
△P - 颈部与颗粒表面的饱和蒸气压之差。
此式反映了颗粒大小与蒸气压差的定量关系。由于颗粒表面有 正曲率半径,蒸气压比平表面的蒸气压大些,因此,颈部与颗粒 表面的蒸气压差实际上比上式表示的要大。
常用γGB晶界能和γSV表面能之比值来衡量烧结的难易, γGB/γSV愈小→→愈容易烧结,
为了促进烧结,必须是γSV>γGB。一般Al2O3粉的表面能约为 1 J/m2,而晶界能为0.4 J/m2,两者之差较大,比较易烧结; 而Si3N4、SiC、AlN等,γGB/γSV比值高,烧结推动力小,因而 不易烧结。
烧结时,由于传质机理的不同而使双球模型的中心 距离会出现两种情况:一种是颈部增长而两球中心距 离不变;另一种是随着颈部的增长两球间中心距离缩 短。
以下介绍几种模型,并列出了由简单几何关系计算得到的颈部 曲率半径 ρ、颈部体积 V、颈部表面积 A 与颗粒半径 r 和接触颈 部半径 x 之间的关系(假设烧结初期r变化很小,x>>ρ)。 (A) 模型是球型颗粒的点接触,烧结过程中心距离不变。
4、蒸发-凝聚传质的特点 • 1)凸面蒸发,凹面凝聚。烧结时颈部扩大,球的
形状改变为椭圆,气孔形状改变,但球与球之间
的中心距不变,也就是在这种传质过程中坯体不 发生收缩,△L/L→0(线收缩接近0)。 • 2)坯体密度不变。气孔形状的变化对坯体一些宏 观性质有可观的影响,但不影响坯体密度。
二、扩散传质
单组元,也可以是两组元或更多组元参加,但组元间不发生化学
反应,仅仅是在表面能驱动下,由粉体变成致密体。 实际生产中烧结、固相反应往往是同时穿插进行的。
四、烧结过程推动力
从热力学观点,烧结前的粉料与烧结体相比是处 于热力学不稳定状态,它将自发地向能量降低的状 态变化。
粉状物料的表面能大于多晶烧结体的晶界能, 二者的差值是烧结过程的推动力。烧结推动力 约为4-20 J/g。
开尔文公式表达了弯曲液面的曲率 半径对蒸气压影响的定量关系:
pr 2M 1 ln p0 dRT r
当r>0时,即曲面为凸面时,pr>p0 ( 即液体凸液面上的饱和 蒸气压大于水平液面上的饱和蒸气压);当r<0时,即曲面为凹 液面时,pr<p0。 也即曲率不同的液面饱和蒸汽压关系为:p凸>p平>p凹。 据此可解释毛细管现象:在一定的温度下,对于水平液面尚未 达到饱和的蒸气而对毛细管内的凹液面可能达到过饱和状态,蒸 气将凝结成液体,这种现象称毛细管凝结。
• 无机材料的性能不仅与材料的组成(化学组成和矿 物组成)有关,还与材料的显微结构有密切关系。
• 例如配方相同而晶粒尺寸不同的两个烧结体,由于
晶粒长度或宽度方向上某些参数的叠加,晶界出现 频率不同而引起材料性能的差异: • 材料的断裂强度(σ )与晶粒直径(d)之间有以 下函数关系:σ= σ0 + kd
在大多数固体材料中,由于高温下蒸气压低,则传质更易 通过固态内质点扩散过程来进行。
烧结的推动力是如何使质点在固态中发生迁移的呢?
1. 颈部应力模型 (假定晶体是各向同性的)。
在烧结前的粉末体如果是由同径颗粒堆积而成的理想紧密堆积,颗粒接 触点上最大压应力相当于外加一个静压力。在真实系统中,由于球体尺寸不 一,颈部形状不规则,堆积方式不相同等原因,使接触点上应力分布产生局 部剪应力。
• 气孔又是光散射中心而使材料不透明;
• 气孔又对畴壁运动起阻碍作用而影响铁电性和磁性
等。 • 在特定条件下,气孔的存在具有有利的一面,如在 存在高的应力梯度时(比如热震引起的应力),气 孔能起到容纳变形,阻止裂纹扩散的作用。
显微结构对无机材料性能的影响
• 烧结过程可以通过控制晶界移动抑制晶粒的异常生 长或通过控制表面扩散、晶界扩散和晶格扩散而充
σ2
△P
△P(σP)
x γ
γ
一、蒸发一凝聚传质
固体颗粒表面曲率不同,在高温时必然在系统
的不同部位有不同的蒸气压。质点通过蒸发,再凝
聚实现质点的迁移,促进烧结。 氧化铍和氧化铁的烧结。 这种传质过程仅 仅在高温下蒸气压较大的系统内进行,如氧化铅、
1、传质模型 双球 - 中心距不缩短,如图。 2、传质机理
• 宏观定义仅仅描述了坯体宏观上的变化,而对烧结本质揭示仍是不够 的。学者们认为必须强调粉末颗粒表面的粘结和粉末内部物质的传递 和迁移。因为只有物质的迁移才能使气孔充填和强度增加。
• 微观定义:由于固态中分子(或原子)的相互吸 引,通过加热,使粉末体产生颗粒粘结,经过物 质迁移使粉末体产生强度并导致致密化和再结晶 的过程称为烧结。 • 即烧结过程可分为两个过程:1)颗粒的粘附作用;2)
3、动力学方程
由郎格缪(Langmuir)公式(由气体分子运动 认推出物质在单位面积上凝聚速率正比与平衡气压 和大气压差)、凝聚速率等于颈部体积增长时及以 上理论可以导出颈部生长速率:
3 π γM 2 p 3 2 1 2 1 x 3 3 0 r 3 t 3 kr t r 2 R 3 2T 3 2 d 2
烧结温度(TS)和熔点(TM)关系: 金属粉末:TS≈(0.3~0.4)TM 盐 类:TS ≈0.57 TM 硅酸盐 :TS ≈0.8~0.9 TM
烧结与固相反应区别:
相同点:两个过程均在低于材料熔点或熔融温度之下进行, 并且在过程的自始至终都至少有一相是固态。 不同点:固相反应发生化学反应,固相反应必须至少有两组元 存在,产物的组成、结构与性能不同反应物。而烧结可以是只有
ρ=x2/(2r) A=π2x3/r V=πx4/(2r)
ρ=x2/(4r) A=π2x3/(2r) V=πx4/(4r)
ρ=x2/(2r) A=πx3/r V=πx4/(2r)
(B) 模型是球型颗粒的点接触,但是烧结过程中心距离变小 (C) 模型是球型颗粒与平面的点接触,烧结过程中心距离也变小。
颗粒表面和颈部的蒸气压关系可用开尔文公式表示:
p1 γM 1 1 ln p0 dRT ρ x
式中:p1 - 颈表面的饱和蒸气压;p0 - 颗粒(球)表面的饱和蒸 气压;d - 烧结材料的密度;x、ρ - 颈部两主曲率半径。
上式中,由于压力差(p0-p1 )很小(凝聚体的蒸气压一般 很小),所以 p ΔP ΔP
0.3
x/r
0.2
lg x/r
斜率1/3
0.1 0 10 20 时间/s 30 lg t
图:NaCl烧结时颈部相对增长速率与时间的关系
• 从工艺控制考虑,两个重要的变量是原料
起始粒度(r)和烧结温度(T)。 • 粉末的起始粒度愈小,烧结速率愈大;由 于蒸汽压(P0)随温度而呈指数地增加,
因而提高温度对烧结有利。
传质过程同时伴随着晶界移动、晶粒生长。
衡量烧结程度指标:
(烧结体宏观上出现体积收缩,致密度提高
和强度增加,因此)
烧结程度可以用坯体收缩率、气孔率、吸水 率或烧结体密度与理论密度之比(相对密度) 等指标来表示。
三、相关概念
烧成:在多相系统内产生的一系列物理和化学变 化。例如脱水、坯体内气体分解、多相反应和熔融、 溶解、烧结等。 烧结:指粉料受压成型后,经加热而致密化的简 单物理过程,不包括化学变化。 烧结仅仅是烧成过 程的一个重要部分。烧结是在低于固态物质的熔融温 度下进行的。 熔融:固体融化成熔体过程。烧结和熔融这两个过 程都是由原子热振动而引起的,但熔融时全部组元都 转变为液相,而烧结时至少有一组元是处于固态。
五、烧结模型
为了定量地研究烧结过程和烧结机理,必须建立合 理的简化模型。G.C.Kuczynski(库金斯)提出粉末压 块由等径球体堆积为模型。随着烧结的进行,各接触点 开始形成颈部,并逐渐扩大,最后烧结成一个整体。 由于各颈部所处的环境和几何条件相同,所以只需确 定两个颗粒形成的颈部的增长速率就基本代表了整个 烧结初期的动力学关系。
固体的升华过程和液体的蒸发过程相类似,故开尔 文公式同样适用于固体物质:即凸面(固体颗粒)的饱 和蒸气压大于平面的;凹面的饱和蒸气压小于平面的。
pr γM 1 1 对于非球形曲面, 表示为 ln p0 dRT r1 r2
即颗粒表面(凸面)的蒸气压必大于颈部表面(凹 面)的蒸气压,也即颗粒表面和颈部表面存在着压差, 这种压差使物质从蒸气压高的颗粒表面蒸发,通过气相 传递而凝聚在蒸气压低的颈部表面,如图所示,以此传 质过程使颈部逐渐被填满。
粒中心距逼近→ →形成晶界→ →气
孔形状变化,体积缩小→ →最后气 孔部分或全部从晶体中排除,这就
是烧结所包含的主要物理过程。
同时,粉末压块的性质也随这些物理过
程的进展而出现坯体收缩、气孔率下降、 电阻率下降、强度升高等变化
二、烧结定义
• 宏观定义:粉体原料经过成型,在加热到一定的 温度后开始收缩,在低于熔点的温度下变成致密、 坚硬的烧结体,这种过程称为烧结。
任何系统降低能量是一种自发趋势、粉体经烧结后, 晶界能取代了表面能,这是多晶材料稳定存在的原因。
粒度为 1μm的材料烧结时所发生的自由焓降低约 8.3 J/g (Al2O3烧结时所发生的自由焓降低约为0.846 kJ/mol ); 而 α-石英转变为β-石英时能量变化为1.7 kJ/mol; 一般化学反应前后能量变化> 200 kJ/mol; 因此烧结推动力与相变前后或化学反应前后的能量变化相 比还是极小的。 烧结推动力很小,不足以使物质的质点迁移,烧结必须在 高温作用下进行。
以上三个模型对烧结初期一般是适用的,但随烧结 的进行,球形颗粒逐渐变形,因此在烧结中、后期应 采用其它模型。
11.2 固相烧结
固相烧结完全是固体颗粒之间的高温固结过程, 没有液相参与。固态烧结过程包括: 1)高温粘附,形成颈部结构(弯曲面),产生附 加压力,指向中心 (由于切线方向表面张力作用 的结果),引起颗粒重排; 2)传质(充填颈部); 3)晶界移动,晶粒生长。 固态烧结的主要传质方式有: 蒸发一凝聚和扩散传质。 另外还有塑性流变。