玻璃定位、检测系统
基于PLC的玻璃原片上料系统设计
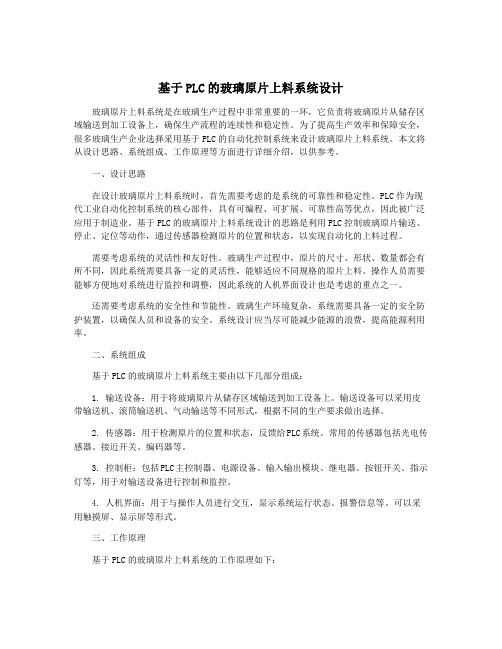
基于PLC的玻璃原片上料系统设计玻璃原片上料系统是在玻璃生产过程中非常重要的一环,它负责将玻璃原片从储存区域输送到加工设备上,确保生产流程的连续性和稳定性。
为了提高生产效率和保障安全,很多玻璃生产企业选择采用基于PLC的自动化控制系统来设计玻璃原片上料系统。
本文将从设计思路、系统组成、工作原理等方面进行详细介绍,以供参考。
一、设计思路在设计玻璃原片上料系统时,首先需要考虑的是系统的可靠性和稳定性。
PLC作为现代工业自动化控制系统的核心部件,具有可编程、可扩展、可靠性高等优点,因此被广泛应用于制造业。
基于PLC的玻璃原片上料系统设计的思路是利用PLC控制玻璃原片输送、停止、定位等动作,通过传感器检测原片的位置和状态,以实现自动化的上料过程。
需要考虑系统的灵活性和友好性。
玻璃生产过程中,原片的尺寸、形状、数量都会有所不同,因此系统需要具备一定的灵活性,能够适应不同规格的原片上料。
操作人员需要能够方便地对系统进行监控和调整,因此系统的人机界面设计也是考虑的重点之一。
还需要考虑系统的安全性和节能性。
玻璃生产环境复杂,系统需要具备一定的安全防护装置,以确保人员和设备的安全。
系统设计应当尽可能减少能源的浪费,提高能源利用率。
二、系统组成基于PLC的玻璃原片上料系统主要由以下几部分组成:1. 输送设备:用于将玻璃原片从储存区域输送到加工设备上。
输送设备可以采用皮带输送机、滚筒输送机、气动输送等不同形式,根据不同的生产要求做出选择。
2. 传感器:用于检测原片的位置和状态,反馈给PLC系统。
常用的传感器包括光电传感器、接近开关、编码器等。
3. 控制柜:包括PLC主控制器、电源设备、输入输出模块、继电器、按钮开关、指示灯等,用于对输送设备进行控制和监控。
4. 人机界面:用于与操作人员进行交互,显示系统运行状态、报警信息等。
可以采用触摸屏、显示屏等形式。
三、工作原理基于PLC的玻璃原片上料系统的工作原理如下:1. 系统初始化:当系统上电后,PLC主控制器首先对系统进行初始化,确认各部件的连接状态和工作状态。
玻璃缺陷在线检测系统设计

中国矿业大学科研创新论文玻璃缺陷在线检测系统设计姓名:连清学号:03101257专业:测控技术与仪器导师:刘万里摘要传统的玻璃质量检测主要采用人工检测的方法。
人工检测不仅工作量大,而且易受检测人员主观因素的影响,容易对玻璃表面缺陷造成漏检,尤其是变形较小、畸变不大的夹杂缺陷漏检,极大降低了玻璃的表面质量,从而不能够保证检测的效率与精度u。
目前,玻璃缺陷检测系统主要是利用激光检测和摩尔干涉原理的方法。
激光检测易受到外界干扰,影响检测精度。
摩尔干涉原理由于光栅内的莫尔条纹比较细,为保证莫尔条纹有很强的对比度便于计算机进行分析处理,就必须要求光栅有很高的明暗对比度,通过复杂计算机图形处理技术对干涉图形进行处理,占用大量的检测时间,检测周期非常缓慢而在实际检验中并无实用效果。
近年来,迅速发展的以图像处理技术为基础的机器视觉技术恰恰可以解决这一问题。
机器视觉主要是采用计算机来模拟人的视觉功能,从客观事物的图像中提取信息,进行处理并加以理解,最终用于实际检测、测量和控制。
本文介绍的玻璃表面缺陷检测系统采用机器视觉技术,完成对玻璃缺陷的提取、识别,为玻璃分级打标提供信息,满足玻璃表面缺陷检测的要求。
关键字:玻璃表面检测;图像处理;系统设计目录1、玻璃缺陷在线检测系统设计课题的提出 (4)1.1课题研究的背景 (4)1.2课题研究的意义及目的 (5)2、国内外玻璃缺陷在线检测系统的研究现状 (5)3、测量系统的简要介绍 (7)3.1检测系统的基本结构 (7)3.2检测系统原理 (8)3.3玻璃表面缺陷图像的处理(简介) (9)4、系统设计中重要的检测参数和部分要求 (9)5、课题研究的步骤及各阶段完成目标 (10)相关文献 (11)1、玻璃缺陷在线检测系统设计课题的提出1.1课题研究的背景玻璃在生产过程中,会产生各种各样的缺陷,比如:气泡、条纹和结石。
这些缺陷都会影响玻璃的外观质量,降低玻璃的透光性、机械强度和热稳定性,造成大量的废品和次品。
一种玻璃缺陷检测方法

一种玻璃缺陷检测方法
玻璃缺陷检测是一种常见的工业检测问题,以下是一种常见的玻璃缺陷检测方法:
1. 视觉检测:使用高分辨率的摄像头和图像处理算法来检测玻璃表面的缺陷,例如裂纹、气泡等。
该方法通常可以自动化进行,但对摄像头的精准定位和图像处理算法的优化需要一定的技术支持。
2. 超声波检测:使用超声波振荡器将声波传递到玻璃表面,通过测量声波的传播时间和反射强度来检测玻璃内部的缺陷,例如空洞、裂纹等。
这种方法可以非破坏性地检测玻璃缺陷,并且可以应用于任意形状和尺寸的玻璃制品。
3. 激光光谱检测:使用激光器将激光光束照射到玻璃表面,通过测量反射光谱和干涉图案来检测玻璃表面和内部的缺陷,例如划痕、晶粒等。
这种方法需要精确的光学测量和数据处理算法,但可以提供更详细的缺陷信息。
4. 热红外检测:使用红外热像仪来测量玻璃表面的温度分布,通过热传导和辐射的特性来检测玻璃内部的缺陷,例如不均匀的密度分布、断裂等。
这种方法对玻璃材料的热性质要求较高。
以上是一些常见的玻璃缺陷检测方法,每种方法都有各自的适用范围和优缺点,选择合适的方法需要考虑具体的应用场景和要求。
《基于机器视觉与深度学习的挡风玻璃雨滴检测方法研究》
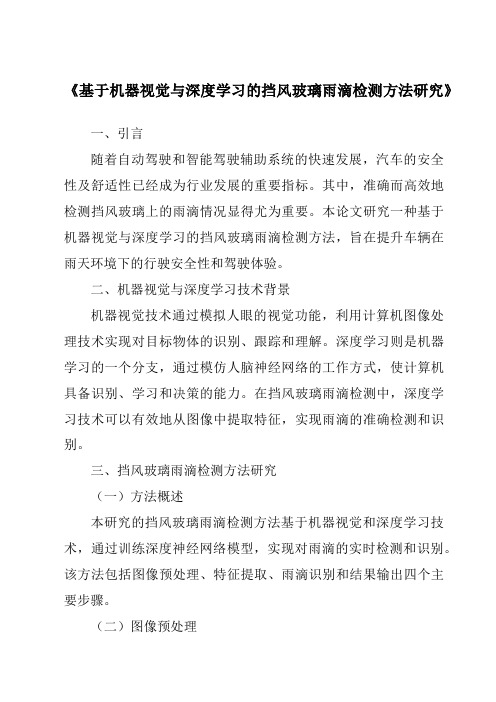
《基于机器视觉与深度学习的挡风玻璃雨滴检测方法研究》一、引言随着自动驾驶和智能驾驶辅助系统的快速发展,汽车的安全性及舒适性已经成为行业发展的重要指标。
其中,准确而高效地检测挡风玻璃上的雨滴情况显得尤为重要。
本论文研究一种基于机器视觉与深度学习的挡风玻璃雨滴检测方法,旨在提升车辆在雨天环境下的行驶安全性和驾驶体验。
二、机器视觉与深度学习技术背景机器视觉技术通过模拟人眼的视觉功能,利用计算机图像处理技术实现对目标物体的识别、跟踪和理解。
深度学习则是机器学习的一个分支,通过模仿人脑神经网络的工作方式,使计算机具备识别、学习和决策的能力。
在挡风玻璃雨滴检测中,深度学习技术可以有效地从图像中提取特征,实现雨滴的准确检测和识别。
三、挡风玻璃雨滴检测方法研究(一)方法概述本研究的挡风玻璃雨滴检测方法基于机器视觉和深度学习技术,通过训练深度神经网络模型,实现对雨滴的实时检测和识别。
该方法包括图像预处理、特征提取、雨滴识别和结果输出四个主要步骤。
(二)图像预处理在图像预处理阶段,对输入的图像进行灰度化、降噪和归一化等处理,以提高后续特征提取和识别的准确性。
(三)特征提取利用深度神经网络模型提取图像中的特征信息,包括雨滴的形状、大小、位置等信息。
特征提取是挡风玻璃雨滴检测的关键步骤,对于提高检测准确率具有重要意义。
(四)雨滴识别通过训练好的深度神经网络模型对提取的特征进行分类和识别,实现雨滴的准确检测。
该阶段采用多尺度、多方向的识别策略,以适应不同大小和形状的雨滴。
(五)结果输出将检测到的雨滴信息以图像或数据的形式输出,为后续的驾驶辅助系统提供决策支持。
四、实验与结果分析(一)实验数据集为了验证本研究的挡风玻璃雨滴检测方法的准确性和有效性,我们收集了多种不同环境、不同光线条件下的雨天驾驶图像作为实验数据集。
(二)实验过程与结果我们采用深度学习框架训练深度神经网络模型,对实验数据集中的图像进行雨滴检测实验。
实验结果表明,本研究的挡风玻璃雨滴检测方法具有较高的准确性和实时性,能够有效地识别和定位雨滴。
汽车挡风玻璃涂胶系统配置研究与优化

汽车挡风玻璃涂胶系统配置研究与优化摘要:在汽车挡风玻璃的涂胶过程中,涂胶系统需要完成玻璃运输、定位、玻璃辨识、涂胶及仿形作业。
因此,在涂胶系统中必须包涵玻璃运输设备、定位装置、玻璃辨识装置、机器人仿形设备、供胶系统设备、胶料保压系统等。
本文根据现场使用经验,对涂胶系统中的设备配置以及plc对设备间的连锁控制进行研究总结,并提出优化配置及控制方案,以满足汽车挡风玻璃涂胶装配的质量要求。
关键词:机器人仿形;涂胶系统;挡风玻璃;plc;连锁控制;配置优化;在上汽通用五菱总装车间中,累积使用五套涂胶系统设备,然而,涂胶系统的结构原理大致相同。
涂胶机主要包括玻璃上料与下料的运输系统、玻璃定位于玻璃类型辨识系统、机器人仿形与涂胶系统、胶泵供胶系统、胶料保压系统、电控连锁系统、安全保护系统等。
1 涂胶系统配置现状及研究1.1 涂胶系统组成概念1.2 玻璃运输系统在上汽通用五菱总装车间的5条生产线中,玻璃运输系统主要有以下几个方式:一是链条输送玻璃配合真空拾取的玻璃下料装置;二是双面转台配合机器人运输玻璃的形式组合。
在链条运输系统中,包括上料工位、移动工位、涂胶及仿形工位、下料工位,使玻璃在不断的改变工位状态,进而实现玻璃间续不断的进行涂胶仿形作业,实现连续生产的循环。
而在转台输送系统中,转台两面相互180度的角度切换,对转台两面命名为上料位与工作位,转台转动过程中,不断的切换上料位与工作位,实现连续作业的循环。
但是,当使用转台运输玻璃时,需要机器人配合搬运挡风玻璃,具体需要在涂胶仿形作业中阐述。
1.3 玻璃定位装置目前,玻璃定位、对中原理大致相同,均采用夹具定位。
驱动元件主要选择气缸,有的使用气缸驱动齿轮齿条夹具配合固定断档,有的使用气缸配合活动断档等玻璃定位对中方式。
由于选择玻璃运输方式的不同,导致玻璃定位方式也有差异,最终将决定玻璃涂胶仿形作业的形式。
1.4 玻璃类型辨识方式汽车制造混装线中,要求涂胶系统具有一定的兼容性,具有对多种玻璃进行涂胶作业的能力,因此,根据玻璃外形及尺寸识别玻璃是一项必不可少的作业过程。
玻璃缺陷检测

玻璃片缺陷视觉检测1.玻璃缺陷特征玻璃片生产过程中,常见的缺陷有:气泡、划痕、结石、夹杂物,翘曲等。
各类缺陷的主要特点分:(1)气泡,该类缺陷是由于玻璃生产材料含有气体、外界环境气泡、金属铁丝等引起,主要特点为整体轮廓近似于圆形、线形、中空、具有光透射性等。
(2)结石,由于其热胀系数和外界环境热胀系数的差异,该类缺陷严重影响玻璃质量。
主要分为:原材料结石、耐火材料结石以及玻璃析晶结石等。
(3)夹锡,夹锡主要分为粘锡和锡结石,其特点是呈暗黑色、具有光吸收性。
(4)划伤,该缺陷主要是玻璃原板与硬质介质间的相互摩擦产生,外表呈线性。
(5)表面裂纹及线道,其特点表面呈线性。
具体的缺陷图如图1-1所示:(a)无缺陷玻璃图像(b)含气泡玻璃图像(c)含结石玻璃图像(d)含裂纹玻璃图像(e)含夹杂物的玻璃图像(f)划痕的玻璃图像图 1-1 玻璃典型缺陷图像2玻璃缺陷视觉监测系统工作原理2.1 玻璃缺陷视觉检测原理玻璃生产过程大体可分为:原料加工、备制配合料、熔化和澄清、冷却和成型及切裁等。
在各生产过程中,由于制造工艺、人为等因素,在玻璃原板的生产任一过程中都有可能产生缺陷,根据玻璃现行标准中的规定,玻璃常见的缺陷主要包括:气泡、粘锡、划伤、夹杂等。
无缺陷的玻璃其特点是质地均匀、表面光洁且透明。
玻璃质量缺陷检测是采用先进的CCD 成像技术和智能光源。
系统照明采用背光式照明,其原理如图2-1所示,即在玻璃的背面放置光源,光线经待检玻璃,透射进入摄像头[1]。
图 2-1 检测原理图示意图光线垂直入射玻璃后,当玻璃中没有杂质时如图2-2(a)所示,出射的方向不会发生改变,CCD 摄像机的靶面探测到的光也是均匀的;当玻璃中含有杂质时,出射的光线会发生变化,CCD 摄像机的靶面探测到的光也要随之改变。
玻璃中含有的缺陷主要分为两种:一是光吸收型(如沙粒,夹锡等夹杂物)如图2-2(b)所示,光透射玻璃时,该缺陷位置的光会变弱,CCD 摄像机的靶面上探测到的光比周围的光要弱;二是光透射型(如裂纹,气泡等)如图2-2(c)所示,光线在该缺陷位置发生了折射,光的强度比周围的要大,因而CCD 摄像机的靶面上探测到的光也相应增强。
擦玻璃机器人设计方案

擦玻璃机器人设计方案一、引言玻璃清洁是一项繁琐的任务,尤其是在高楼大厦的外墙上。
为了解决这个问题,我们设计了一种擦玻璃机器人,旨在提高清洁效率、降低工作风险。
本文将详细介绍该机器人的设计方案。
二、机器人结构设计1.底盘设计机器人底盘采用轮式结构,以提高运动灵活性和平稳性。
底盘采用防滑材质,以确保机器人在玻璃表面行驶时更加稳定。
2.擦拭装置擦拭装置由一对可旋转的擦拭臂和擦拭垫组成。
擦拭臂的材质选择耐磨损的合成纤维,以确保长时间使用不会导致擦拭效果下降。
擦拭垫采用微纤维材质,具有较强的吸水性和吸附力,能够快速并有效地清洁玻璃表面。
3.导航系统机器人配备先进的导航系统,采用激光雷达和摄像头进行环境感知和位置识别。
通过激光雷达和摄像头的数据融合,机器人能够准确地感知到玻璃表面的位置和障碍物,并根据预先设定的路径规划进行移动。
4.能源供应机器人搭载高能效锂电池,确保持续工作时间较长,并可通过充电站进行充电。
充电站可根据机器人的当前位置和电池电量智能调配,提供稳定可靠的能源供应。
三、机器人工作流程1.定位与路径规划机器人首先通过导航系统识别玻璃表面的位置,并根据预设的清洁路径规划合理的擦拭路线,确保全面覆盖。
2.擦拭过程机器人依次移动至不同位置,并将擦拭臂伸展到玻璃表面。
擦拭臂旋转后,擦拭垫能够有效清除玻璃表面的污垢和灰尘。
3.障碍物识别与规避如果机器人在擦拭过程中感知到突出的障碍物,导航系统会通过实时计算和分析,调整移动路径以绕过障碍物,保证机器人的正常工作。
4.清洁结果反馈机器人清洁完成后,导航系统会发送清洁结果给操作人员。
同时,机器人还能够记录清洁过程中的异常情况,并生成报告,以便后续处理和分析。
四、安全性设计1.紧急停止装置机器人配备紧急停止按钮,一旦出现异常情况,操作人员可以立即按下按钮,停止机器人的运动,确保人员和设备的安全。
2.防坠落装置机器人底盘装有重力传感器和倾斜传感器,一旦检测到机器人越过安全边界和倾斜角度,相应的报警机制将触发,防止机器人坠落。
基于PLC的玻璃原片上料系统设计
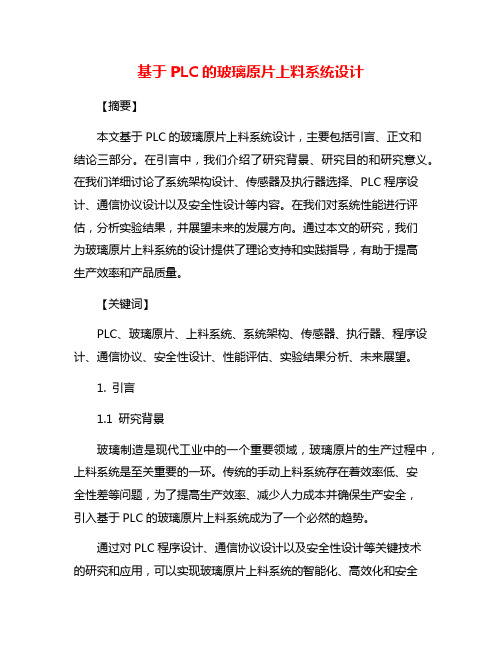
基于PLC的玻璃原片上料系统设计【摘要】本文基于PLC的玻璃原片上料系统设计,主要包括引言、正文和结论三部分。
在引言中,我们介绍了研究背景、研究目的和研究意义。
在我们详细讨论了系统架构设计、传感器及执行器选择、PLC程序设计、通信协议设计以及安全性设计等内容。
在我们对系统性能进行评估,分析实验结果,并展望未来的发展方向。
通过本文的研究,我们为玻璃原片上料系统的设计提供了理论支持和实践指导,有助于提高生产效率和产品质量。
【关键词】PLC、玻璃原片、上料系统、系统架构、传感器、执行器、程序设计、通信协议、安全性设计、性能评估、实验结果分析、未来展望。
1. 引言1.1 研究背景玻璃制造是现代工业中的一个重要领域,玻璃原片的生产过程中,上料系统是至关重要的一环。
传统的手动上料系统存在着效率低、安全性差等问题,为了提高生产效率、减少人力成本并确保生产安全,引入基于PLC的玻璃原片上料系统成为了一个必然的趋势。
通过对PLC程序设计、通信协议设计以及安全性设计等关键技术的研究和应用,可以实现玻璃原片上料系统的智能化、高效化和安全化,为玻璃制造行业的发展提供有力支持。
对基于PLC的玻璃原片上料系统的研究具有重要的理论和实践意义。
1.2 研究目的本次研究的目的是设计一套基于PLC的玻璃原片上料系统,旨在实现自动化的玻璃原片上料过程,提高生产效率和产品质量。
通过引入PLC技术,可以实现对上料系统的精确控制和监测,提高生产线的稳定性和可靠性。
通过对传感器及执行器的选择和PLC程序的设计,可以实现对玻璃原片的准确捕捉和放置,确保上料过程的准确性和安全性。
设计合理的通信协议和安全性措施,可以保证系统的稳定运行并避免潜在的安全风险。
通过本次研究,可以为玻璃制造行业提供一套先进的上料系统设计方案,为企业的生产运营带来显著的改善。
还能为相关领域的学术研究提供有益的参考和借鉴,推动自动化技术在工业生产中的应用和发展。
1.3 研究意义本文着重探讨基于PLC的玻璃原片上料系统设计,旨在解决传统人工上料存在效率低下、易出错的问题,提高生产效率和产品质量。
保特罗玻璃切割机BCMSWin软件操作使用说明

保特罗玻璃切割机B C M S W i n软件操作使用说明集团标准化工作小组 #Q8QGGQT-GX8G08Q8-GNQGJ8-MHHGN#切割机BCMSWin软件操作使用说明340/352BCS Classics 机器操作说明一.开机步骤:1. 检查外来主电源(AC 380~420V);2. 检查气源(主气源6Bar,油压1Bar);3. 打开主电源开关(在控制柜后), 启动电脑,此时控制电源关闭灯会亮;4. 确定设备正常后启动控制电源按钮;5. 确认设备操作环境(包括导轨,台面及操作区域)安全后,将选择开关(钥匙)顺时针扭动一下;6. 然后再次确认人员安全,按下带有人形标志的按钮;7. 释放紧急开关,完成以上步骤后,机器显示器上会显示待机状态;8. 按下归零键,机器处于待机工作状态.二.关机步骤:1. 按下紧急开关 ;2. 按下控制电源关闭键,关闭电脑;3. 关闭主电源(在控制柜后)。
注:电控柜必须在电源开关关闭之后,才可以打开和关闭.否则会造成电源开关损坏。
三. 切割操作步骤1.按下F6,输入原片参数之后按或确定;2. 切割版面输入;切割版式面输入方式有三种方法:1) 手动输入:在切割输入区,按如下方法直接输入切割命令。
a) 直线:竖线X 、Z 和Q ,横线Y 、W 和 R ,按X->Y->Z->W->Q->R 的秩序输入,例如:X1200 Y1000 Z800 W600 Q400 R200; b) 斜线类A ,B ,C ,D ,两组数据形成一斜线,如:A100,B100;第一象限 第二象限c) 异形类S ,*,P (来源于BCMSWin 图库,CAD 绘图,异形扫描等),输入异形时,必须先输入异形外框尺寸(须大于异形外框),如切割一个直径500MM 圆时,须输入X560 Y560 P1,然后设定圆半径250MM ,指定图形文件名。
AB CDB CAD切割排版命令异形文件名称直线外框命令◆ S 调用图形画面;◆ *直接调用图形,‘*’号后面必须输入图形文件名; ◆ P 调用图库菜单;d) 控制命令:重复命令M ,格式:M*,*表标重次数;e) 输入完毕后,按F2或输入文件名保存版面,以便以后使用。
光伏玻璃压延缺陷位置精确定位方法

英文回答:The method of precise defect positioning in roll-to-roll production of photovoltaic glass entails a series of crucial steps. Firstly, advanced imaging technology is utilized to meticulously scan the glass surface and detect any potential defects. This technology epasses high-resolution cameras, infrared cameras, and sophisticated laser scanning systems, all of which yield detailed information regarding the size, shape, and precise location of any defects present on the glass surface.光伏玻璃生产中精确的缺陷定位方法涉及一系列关键步骤。
利用先进的成像技术仔细扫描玻璃表面并发现任何潜在的缺陷。
这项技术通过高分辨率照相机、红外照相机和精密的激光扫描系统,所有这些系统都提供关于玻璃表面任何缺陷的大小、形状和准确位置的详细信息。
So, the next step in our super accurate positioning method is to use fancyputer vision stuff to look at all the data we collected from the cameras. These algorithms can figure out what kind of problems there are, like scratches or bubbles, and make a detailed map showing exactly where these issues are on the glass. Then we can use this map to make sure everything gets fixed up just right during the roll-to-roll production process.Cool, huh?我们超级精确定位方法的下一步是使用花哨的视觉材料来观察我们从摄像机中收集的所有数据。
轻松看到玻璃中硫化镍颗粒不再遥不可及

轻松看到玻璃中硫化镍颗粒,不再遥不可及玻璃,这种透明而坚硬的材料,广泛应用于建筑、家居、汽车等各个领域,给我们的生活带来了极大的便利和美感。
然而,随着玻璃应用的不断扩大,其安全问题也日益凸显。
钢化玻璃自爆事件时有发生,给人们的生命财产安全带来了极大的威胁。
为了解决这一问题,一款新型筱豹玻璃自爆检测设备的研发成功让您轻松看到玻璃中的硫化镍颗粒,不再遥不可及!一、钢化玻璃自爆的罪魁祸首——硫化镍颗粒钢化玻璃自爆的原因有很多,其中玻璃上墙后发生最主要的就是玻璃中的硫化镍颗粒。
硫化镍颗粒是玻璃生产过程中不可避免的杂质,当玻璃受到温度变化或外力冲击时,硫化镍颗粒会发生变化,导致玻璃内部应力失衡,从而引发自爆。
因此,准确检测和定位玻璃中的硫化镍颗粒,对于预防钢化玻璃自爆具有重要意义。
二、传统检测方法的局限性传统的钢化玻璃检测方法主要依赖于人工目视检查和破坏性实验。
人工目视检查受限于人的视力和经验,很难准确识别和定位微小的硫化镍颗粒。
而破坏性热浸实验虽然可以准确检测玻璃的强度,但会对玻璃造成不可逆的损伤,且成本较高。
因此,传统检测方法在准确性和效率上都存在较大的局限性。
三、新型检测设备——让硫化镍颗粒无处遁形针对传统检测方法的局限性,一款新型的钢化玻璃风险检测设备研发成功。
该设备采用了先进的激光扫描技术和高精度图像处理算法,能够在短时间内对整块玻璃进行全面、准确的检测。
具体优势如下:1.高精度检测:设备采用高分辨率激光扫描仪,可以对玻璃表面进行微米级别的精确测量,有效识别和定位硫化镍颗粒。
2.非破坏性检测:该设备采用非接触式测量方法,不会对玻璃造成任何损伤,保证了玻璃的完整性和美观性。
3.高效便捷:设备具备自动化检测功能,只需简单设置参数,即可实现全自动检测。
同时,设备还配备了直观的操作界面和强大的数据处理能力,大大提高了检测效率。
4.多功能性:除了检测硫化镍颗粒外,该设备还可以检测玻璃的其他缺陷,如气泡、裂纹等,为玻璃质量提供全面保障。
玻璃表面缺陷检测系统原理

玻璃表面缺陷检测系统原理玻璃是一种常见的建筑材料,广泛应用于建筑、汽车、家电等领域。
然而,由于制造过程中的各种原因,玻璃表面可能会出现各种缺陷,如划痕、气泡、脱附等。
这些缺陷不仅影响玻璃的美观度,还可能降低其强度和耐久性。
因此,开发一种高效、准确的玻璃表面缺陷检测系统对于保证产品质量和提高生产效率至关重要。
玻璃表面缺陷检测系统的原理是基于图像处理和机器视觉技术。
首先,将待检测的玻璃放置在特定的检测平台上,并通过传感器获取玻璃表面的图像。
然后,利用图像处理算法对图像进行预处理,去除噪声和背景干扰,增强图像的对比度和清晰度,以便更好地识别缺陷。
在预处理完成后,接下来是缺陷的检测和分类。
通常,玻璃表面的缺陷可以分为几个主要类别,如划痕、气泡、脱附等。
针对不同的缺陷类型,需要设计相应的检测算法和模型。
例如,对于划痕缺陷,可以利用边缘检测算法和形态学处理方法来提取划痕的轮廓和边界信息;对于气泡缺陷,可以利用图像分割算法和形状特征提取方法来检测和定位气泡的位置和大小。
在检测和分类完成后,系统还需要进行缺陷的评估和判定。
这一步骤通常涉及到特征提取和模式识别技术。
通过提取缺陷区域的纹理、颜色、形状等特征,并利用机器学习算法训练分类模型,可以对缺陷进行定量评估和判定。
例如,可以利用支持向量机(SVM)算法对不同类型的缺陷进行分类,并给出缺陷的严重程度和优先级。
玻璃表面缺陷检测系统还需要提供可视化的结果和报告。
通过将检测结果以图像、表格或报告的形式呈现给操作人员,可以帮助他们直观地了解玻璃表面的缺陷情况,并及时采取相应的措施进行修复或处理。
此外,系统还可以将检测结果保存和记录,用于质量追溯和生产过程的改进。
玻璃表面缺陷检测系统是基于图像处理和机器视觉技术的一种高效、准确的自动检测方法。
通过对玻璃表面图像的处理、缺陷的检测和分类、缺陷的评估和判定,以及结果的可视化呈现,可以实现对玻璃表面缺陷的快速、准确的检测和分析,提高产品质量和生产效率,为各行业的玻璃应用提供可靠的质量保证。
- 1、下载文档前请自行甄别文档内容的完整性,平台不提供额外的编辑、内容补充、找答案等附加服务。
- 2、"仅部分预览"的文档,不可在线预览部分如存在完整性等问题,可反馈申请退款(可完整预览的文档不适用该条件!)。
- 3、如文档侵犯您的权益,请联系客服反馈,我们会尽快为您处理(人工客服工作时间:9:00-18:30)。
机器人堆垛机视觉系统
北京嘉恒图像技术有限公司
2011年4月
机器人堆垛机视觉系统
一、检测项目:
1、检测对象:实时检测辊道上随辊道运动的玻璃。
2、玻璃最大规格:3300mm*2600mm (单片)
1650mm*2134mm (同时出双片、并列)
3、玻璃在辊道上最大速度:1.5米/秒
4、辊子的直径为130mm,辊道的宽度为近4米;
二、视觉系统要求:
1、视觉检测系统需架设在玻璃生产线滚辊道上方。
2、应能在线检测(即玻璃随辊道一起运动)玻璃的规格尺寸,精度为±1mm。
3、完整性检测。
玻璃是否有破损、缺边、缺角情况。
4、等级识别。
应能识别玻璃上的标记。
标记为打点(喷墨点)或划道。
5、还应能检测玻璃在辊道上的偏转角度的大小情况。
6、图像软件应能处理以上数据。
数据经交换机通过以太网传给上位机。
三、系统原理
作为一个完整的计算机视觉检测系统,玻璃检测系统包括硬件系统和相应的图像采集处理软件;其中硬件部分又分为光学系统、CCD传感装置和控制/处理单元(计算机)组成,软件为图像采集处理、控制;在被测玻璃上打背光,该视觉检测系统组成如下图所示。
系统的工作原理为,首先对摄像机参数标定,建立摄像机坐标系统与空间坐标系统的关系,本摄像机模型近似为针孔模型,摄像机标定需要一个放在摄像机前的特制标定参照物或基准,摄像机获取该物体的图像,并由此计算摄像机的内外参数。
1#、2#摄像机采集的图像传送至处理单元,由于图像的多样性和不规则性,并不能直接进行检测,而系统在检测之前需要对每一幅图片都要进行预处理。
预处理包括滤波去噪、边缘增强、二值化、形态学处理等,通过这些预处理来改善图像质量,便于后面图像分析。
图像分析实现以下功能:
1.计算玻璃的尺寸,长、宽,精度为1mm;
2.定义世界坐标系,给出玻璃的其中一条边和世界坐标系x轴的偏角;
3.玻璃缺陷检测,缺陷包括破损、缺边、缺角,对于有缺陷的产品进行输出报警;
4.玻璃等级检测,识别玻璃上的标记,标记为墨点、划道;
5.处理软件把检测结果输出给上位机;
四、主要部件组成
部件名称数量单位
线扫描相机 2 个
采集卡 2 个
控制卡 1 个
镜头 2 个
光源 2 个
计算机 1 个
报警器 1 个
脉冲编码器 1 套
相机密闭箱 2 个
机箱柜 1 套。