层压工序作业指导
层压操作规程

层压操作规程1 准备工作1.1 穿好工作衣、工作鞋,戴好工作帽、隔热手套。
1.2 清洁、整理工作场地、设备和工具。
2 对上道工序来料进行检验。
检验要求如下:A 组件内不能漏放EVA。
B TPT一定要盖满钢化玻璃。
3 层压操作过程3.1 按《层压机组操作规程》启动层压机组。
3.2 根据快速EVA的特性调整层压机设定温度为125~130℃,设定抽空计时4~5min,使层压机上三个真空表指针小于-0.09Mpa;加压计时15sec左右,使2#真空表指针在-0.07~-0.04MPa之间;层压计时20~25min。
在操作记录单上填写温度、压力等参数。
3.3 在层压机加热板上放置1~2层水发布。
3.4 将拼接好的组件钢化玻璃朝下送入层压机加热板中央。
3.5 在组件上覆盖一层高温水发布,再覆盖一块环氧树脂板。
3.6 按下合盖按钮关上层压机上盖。
3.7 待层压自动完成后,取出组件修边,整齐堆放,做好标识。
3.8 操作结束后,进行自检。
自检要求如下:A 组件内芯片无碎片、裂纹。
B 组件内0.5~1mm2气泡不超过3个,1~1.5mm2气泡不超过1个。
C 组件内无碰片现象。
3.9 符合要求,流入下道工序,并在随工单上做好记录。
3.10 发现有批质量问题,立即报告技术人员或生产主管。
4 注意事项4.1 组件放入层压机时,芯片、TPT、EVA不能移位,并且轻拿轻放。
4.2 逐车做好清洁工作,保持层压机加热板、气囊、水发布清洁。
4.3 如不符合3.8条,填写返工单,按不合格组件进行返修。
4.4 操作时要戴隔热手套,并小心操作,以防止被烫伤。
4.5 移动拼接完好的组件进入层压机时必须保持基本水平,不得倾斜移动。
4.6 美工刀非常锋利,应小心使用。
5 停电异常处理5.1 放入组件不超过1分钟,应立即人工向下室充气至大气压,按双控气动阀开盖按钮打开机盖,取出组件另行处理;5.2 放入组件超过1分钟但未加压,利用加热板余热加热数分钟后人工向上气室充气至所需压力,加压数分钟后按5.1的方法处理;5.3 组件已经加压但未完成整个程序,可再加压数分钟后按5.1的方法处理。
WI-751-MFG-14_01 Laminator Work Instruction(CA module)层压工序作业指导书(CA组件)
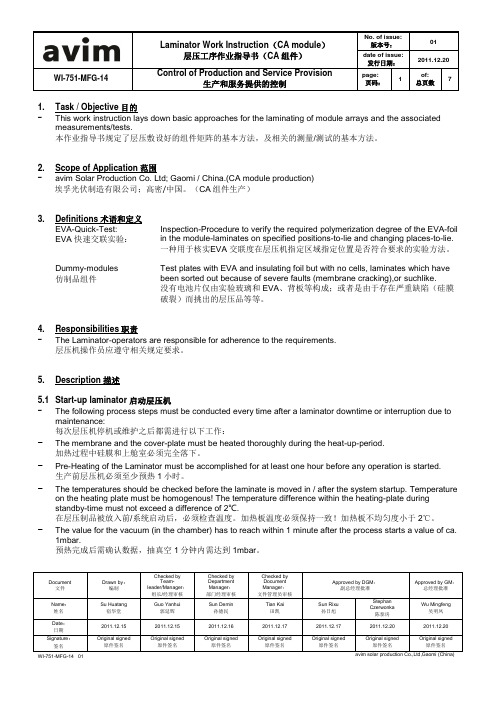
WI-751-MFG-141. Task / Objective 目的-This work instruction lays down basic approaches for the laminating of module arrays and the associated measurements/tests.本作业指导书规定了层压敷设好的组件矩阵的基本方法,及相关的测量/测试的基本方法。
2. Scope of Application 范围- avim Solar Production Co. Ltd; Gaomi / China.(CA module production) 埃孚光伏制造有限公司;高密/中国。
(CA 组件生产)3.Definitions 术语和定义 EVA-Quick-Test: EVA 快速交联实验: Inspection-Procedure to verify the required polymerization degree of the EVA-foil in the module-laminates on specified positions-to-lie and changing places-to-lie.一种用于核实EVA 交联度在层压机指定区域指定位置是否符合要求的实验方法。
Dummy-modules 仿制品组件Test plates with EVA and insulating foil but with no cells, laminates which have been sorted out because of severe faults (membrane cracking),or suchlike. 没有电池片仅由实验玻璃和EVA 、背板等构成;或者是由于存在严重缺陷(硅膜破裂)而挑出的层压品等等。
4. Responsibilities 职责- The Laminator-operators are responsible for adherence to the requirements. 层压机操作员应遵守相关规定要求。
组件层压准备作业指导书

组件层压准备作业指导书工位名称所用工具/工装作业步骤编号名称双手需要1.标准组件将玻璃绒面朝上放置、108客户OEM 按产品要求放置),检查玻璃清洁程度,方法:A 按模板要求排放电池片放电池片时要看清正负极EV A 铺设要平整,不能有褶皱.不能有翘起,鼓包。
检查玻璃清洁状况,若有杂质和脏污,用无尘布加酒精擦拭掉;如无,可以不擦拭工位名称所用工具/工装名称数量轻抬汇流条使其与EV A 隔开子捏住接触处的边缘焊接汇流条两端留的余量要对称,两端距离之差≤1mm 电池片:灰色面引出线为正极蓝色面引出线为负极时)引出线要求在汇流条上方(从组件背面看时)剪刀面要保证与所剪焊带水平,被剪组件上的焊带头不允许带左手要持住待剪焊带,防止扯动电池片或者剪去的焊带落到组件里工位名称所用工具/工装编号名称数量1 直尺2 1.固定点在汇流条与焊带焊接处2 手指套数个汇流条美观.3 恒温烙22.固定点要清洁没有毛刺、锡堆常规组件固定汇流条的示意图,红色为固定位置固定规则:每一串电池串都有固定位置组件下手固定示意图,红色为固定位置.绝缘条上下翻转1800按工装要求贴条形码工位名称所用工具/工装绝缘长称且不超出玻璃常规组件绝缘方块到下部相近汇条与电池片之间组件长绝缘条一定压在绝缘方块上,交叠1mm 区域为绝缘方块固长绝缘条固定位置EV A 要平整铺在电池片上,和玻璃四周边缘大小要一致。
组件绝缘方块到翻折焊带处件绝缘方块固定位置绝缘条之间的固定点,固定时间控制在1s 内,要求工位名称所用工具/工装背板开口与EV A用工装剪裁切口从EV A下面掏出引出线,要保证引出线平整。
用工装贴组件外条码,条码方向正确,不可偏斜按工装要求在背板上贴条形码,此为正向。
太阳能板层压工序注意事项

太阳能板层压工序注意事项太阳能板层压是太阳能板制造过程中的关键一环,能够确保太阳能板的结构牢固、功能稳定。
在进行太阳能板层压时,需要注意以下几个方面:1. 材料准备:层压过程中需要使用复合材料,如玻璃纤维等。
在层压前,需要检查材料的质量和规格,确保符合制造要求,并储存在干燥、清洁的环境中,以防止材料受潮、污染。
2. 设备检查:层压设备必须定期进行检查和维护,保证其正常运行。
特别是加热装置、液压系统等关键部位,需要定期检查温度传感器和液压管路,确保其准确性和安全性。
3. 工艺参数设置:层压过程中需要设置合适的工艺参数,如温度、压力、时间等。
这些参数会直接影响太阳能板的质量和性能。
应根据具体材料和层压要求,合理设置参数,并进行实时监控和调整,保证太阳能板的质量稳定。
4. 表面处理:在层压前,需要对太阳能板的表面进行处理,以提高材料的附着力和表面平整度。
常见的表面处理方法包括清洗、打磨、涂覆等。
应根据具体需求选择合适的处理方法,并注意控制处理过程中的环境和工艺参数,确保处理效果符合要求。
5. 真空处理:在层压过程中,需要进行真空处理,以排除杂质和气泡,确保太阳能板内部的结构和性能。
在真空处理前,需要清洗和净化加热室和真空室,确保无尘、无杂质,在真空处理过程中,要操作准确、谨慎,避免真空泄漏和污染。
6. 层压顺序:太阳能板层压通常采用多层结构,如背板、封装层等。
在层压前,需要明确层压顺序,按照从内到外、从下到上的顺序进行层压,以确保各层之间的粘接牢固、无杂质。
7. 层压压力控制:在层压过程中,需要控制压力的大小和均匀性。
过高的压力会导致材料破裂,过低的压力则会导致粘接不牢。
应根据材料和制造要求,选择合适的压力,并保持压力均匀,避免出现局部压力不足或过高的情况。
8. 层压温度控制:在层压过程中,温度对材料的粘接和性能有很大影响。
过高的温度会导致材料烧损或变形,过低的温度则会影响粘接质量。
应根据材料和制造要求,选择合适的温度,并严格控制温度的均匀性。
PE-010层压作业规范

层压机作业规范1.目的本文适用于本公司使用LHV.120.8层压机进行层压的过程。
2.适应范围本作业规范了该工序的作业要求、标准。
3.安全须知3.1压机的夹平台及排水气管道在工作时温度很高,注意不要被烫伤3.2层压机控制箱内带高压电,非专业人员不要随意触摸,以免触电3.3控制开关由层压员工操作,外来人员不得操作。
4.设备和材料4.1 LHV.120.8层压机4.2 24(inch)*24(inch)、22(inch)*22(inch)镜面钢板4.3 待层压柔性电路板4.4 分离膜4.5 硅橡胶5.生产程序5.1前准备工作:5.1.1准备好一字螺丝刀、耐高温手套、高温薄膜、碎布、酒精;5.1.2用酒精清理钢板、硅胶;5.1.3检查层压机是否正常;5.2层压机的开机、关机程序:5.2.1开机程序:先接外部电源打开机内总电源打开控制回路开关依次打开4个开口的加热开关进行加热将压力调到2Mpa合上闭模开关(快速升温)5.2.2关机程序:依次关闭4个开口的加热开关关闭控制回路开关关闭机内总电源打开自来水4个开口进行冷却达到工艺温后关闭自来水开关打开机内总电源打开控制回路开关打开开模开关进行卸料关闭控制回路开关关闭机内总电源关闭外部总电源。
5.3摆料的作业要求:5.3.1检查钢板及硅胶是否干净。
5.3.2摆料方式严格按下列图示进行摆料:5.3.3摆料时注意:板、薄膜不允许有打皱及重叠现象,钢板有1个开口偏小一些,分开摆料。
5.4层压的作业要求:5.4.1按指定的开口,摆放待压板。
(即第一个开口必须指定)5.4.2上料时,戴好高温手套,批量板必须由两人抬起待压板,确定待压板的中心位置时,双手必须抓紧钢板向内推不允许有滑动现象。
滑动即摆料会错位,造成报废。
5.4.3按闭模开关,合上4个开口进行预压段压制。
试样板需预压:15分钟。
批量板需预压:15分钟。
5.4.4待预压段结束,依照参数表将压力调至工艺压力。
进行成形段压制。
层压机作业指导书2
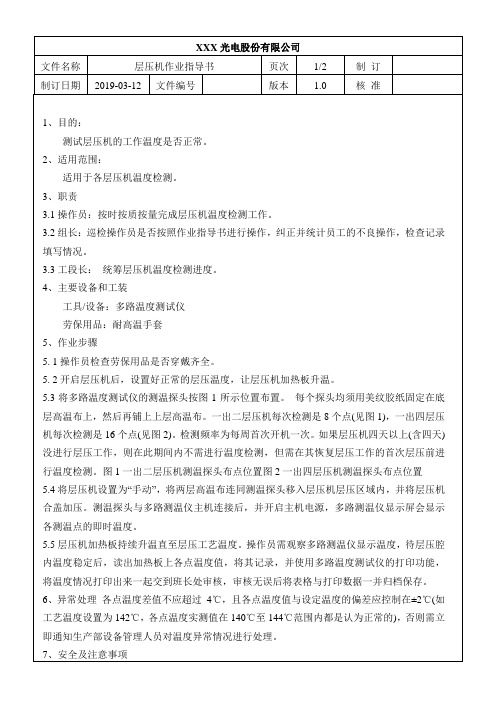
7.3多路测温仪必须进行定期外校。
1、目的:
测试层压机的工作温度是否正常。
2、适用范围:
适用于各层压机温度检测。
3、职责
3.1操作员:按时按质按量完成层压机温度检测工作。
3.2组长:巡检操作员是否按照作业指导书进行操作,纠正并统计员工的不良操作,检查记录填写情况。
3.3工段长:统筹层压机温度检测进度。
4、主要设备和工装
工具/设备:多路温度测试仪
劳保用品:耐高温手套
5、作业步骤
5. 1操作员检查劳保用品是否穿戴齐全。
5. 2开启层压机后,设置好正常的层压温度,让层压机加热板升温。
5.3将多路温度测试仪的测温探头按图1所示位置布置。每个探头均须用美纹胶纸固定在底层高温布上,然后再铺上上层高温布。一出二层压机每次检测是8个点(见图1),一出四层压机每次检测是16个点(见图2)。检测频率为每周首次开机一次。如果层压机四天以上(含四天)没进行层压工作,则在此期间内不需进行温度检测,但需在其恢复层压工作的首次层压前进行温度检测。图1一出二层压机测温探头布点位置图2一出四层压机测温探头布点位置
5.4将层压机设置为“手动”,将两层高温布连同测温探头移入层压机层压区域内,并将层压机合盖加压。测温探头与多路测温仪主机连接后,并开启主机电源,多路测温仪显示屏会显示各测温点的即时温度。
5.5层压机加热板持续升温直至层压工艺温度。操作员需观察多路测温仪显示温度,待层压腔内温度稳定后,读出加热板上各点温度值,将其记录,并使用多路温度测试仪的打印功能,将温度情况打印出来一起交到班长处审核,审核无误后将表与打印数据一并归档保存。
6、异常处理各点温度差值不应超过4℃,且各点温度值与设定温度的偏差应控制在±2℃(如工艺温度设置为142℃,各点温度实测值在140℃至144℃范围内都是认为正常的),否则需立即通知生产部设备管理人员对温度异常情况进行处理。
层压工艺指导书

7.2.1上室或下室处于真空状态时,检查真空表是否达到99.OKPa以上,充气状态时真空表是否接近0
7.2.2出现异常情况时,检查报警原因,通过紧急开盖处理故障
7.3作业后检查:
7.3.1检查组件是否有气泡;
7.3.2检查组件表面有无异物、裂片、缺角;
7.3;
8.4开盖后,迅速拿出层压完的组件
9、相关实验
9.1交联度试验
9.1.1用废片或碎片代替组件送入层压机进入层压
9.1.2层压完成后,在每块玻璃的四条边各取一个EVA试样每个试样约1g左右
9.1.3将试样送入化实验室进行分析,测出EVA交联度
9.1.4将各项分析数据进行记录,填写实验报告
7.3.4检查互连条汇流条是否弯曲,表面是否有锡渣、焊疤;
7.3.5检查TPT上是否有EVA及杂质,如有可用酒精清除。
7.3.6检查合格后流入下道工序。
8、工艺要求
8.1组件内单片无碎裂、无明显移位
8.2层压作业前,必须让层压机自动运行几次空循环,以清除腔体内残余气体
8.3放入铺好的叠层组件时,要迅速进入层压状态
6.9此时可将A级再次放入组件等待
6.10层压完毕后上盖自动打开,然后C级将组件送出,同时A级将另一炉组件送入,进
行下一个层压循环
6.11每次层压完毕必须迅速将组件取出,待冷却后用美工刀修边
7、作业检查:
7.1作业前检查:
7.1.1检查叠层好的组件进入机前是否完全被布遮盖
7.1.2检查温度是否已达设定值,若温度已达到,检查真空泵开关是否已打开
6.4打开热油泵开关,打开加热开关
6.5温度到达设定值后,打开真空泵开关
6.6在手动状态下将上盖打开到位,并将B级手动运行到停止位,然后进入自动工作状态
组件层压工艺作业规程
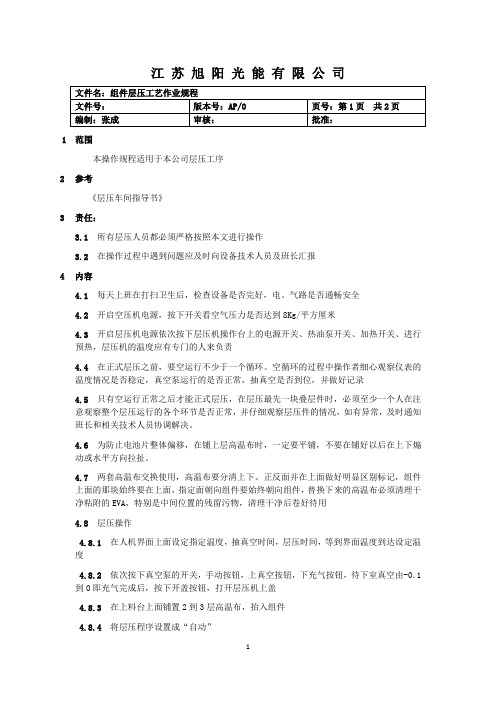
江苏旭阳光能有限公司1 范围本操作规程适用于本公司层压工序2参考《层压车间指导书》3责任:3.1所有层压人员都必须严格按照本文进行操作3.2在操作过程中遇到问题应及时向设备技术人员及班长汇报4内容4.1 每天上班在打扫卫生后,检查设备是否完好,电、气路是否通畅安全4.2 开启空压机电源,按下开关看空气压力是否达到8Kg/平方厘米4.3 开启层压机电源依次按下层压机操作台上的电源开关、热油泵开关、加热开关、进行预热,层压机的温度应有专门的人来负责4.4在正式层压之前,要空运行不少于一个循环。
空循环的过程中操作者细心观察仪表的温度情况是否稳定,真空泵运行的是否正常,抽真空是否到位,并做好记录4.5 只有空运行正常之后才能正式层压,在层压最先一块叠层件时,必须至少一个人在注意观察整个层压运行的各个环节是否正常,并仔细观察层压件的情况,如有异常,及时通知班长和相关技术人员协调解决。
4.6为防止电池片整体偏移,在铺上层高温布时,一定要平铺,不要在铺好以后在上下煽动或水平方向拉扯。
4.7两套高温布交换使用,高温布要分清上下、正反面并在上面做好明显区别标记,组件上面的那块始终要在上面,指定面朝向组件要始终朝向组件,替换下来的高温布必须清理干净粘附的EVA,特别是中间位置的残留污物,清理干净后卷好待用4.8层压操作4.8.1在人机界面上面设定指定温度,抽真空时间,层压时间,等到界面温度到达设定温度4.8.2 依次按下真空泵的开关,手动按钮,上真空按钮,下充气按钮,待下室真空由-0.1到0即充气完成后,按下开盖按钮,打开层压机上盖4.8.3在上料台上面铺置2到3层高温布,抬入组件4.8.4将层压程序设置成“自动”4.8.5点击“自动进料”由一个人扶持进料,观察仪表真空度有没有到达,进入层压阶段。
4.8.6出料时由两个人引导出料,并及时了解层压件的情况4.9关机4.9.1所有组件层压完毕后,保持上盖打开状态,关闭加热,机器停止加热,关闭真空泵,做好关机准备4.9.2等待机器降温到80℃以下。
层压机操作规程范文
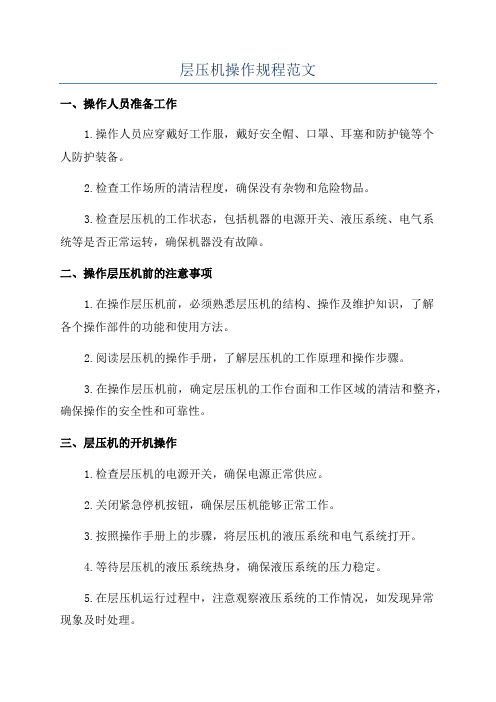
层压机操作规程范文一、操作人员准备工作1.操作人员应穿戴好工作服,戴好安全帽、口罩、耳塞和防护镜等个人防护装备。
2.检查工作场所的清洁程度,确保没有杂物和危险物品。
3.检查层压机的工作状态,包括机器的电源开关、液压系统、电气系统等是否正常运转,确保机器没有故障。
二、操作层压机前的注意事项1.在操作层压机前,必须熟悉层压机的结构、操作及维护知识,了解各个操作部件的功能和使用方法。
2.阅读层压机的操作手册,了解层压机的工作原理和操作步骤。
3.在操作层压机前,确定层压机的工作台面和工作区域的清洁和整齐,确保操作的安全性和可靠性。
三、层压机的开机操作1.检查层压机的电源开关,确保电源正常供应。
2.关闭紧急停机按钮,确保层压机能够正常工作。
3.按照操作手册上的步骤,将层压机的液压系统和电气系统打开。
4.等待层压机的液压系统热身,确保液压系统的压力稳定。
5.在层压机运行过程中,注意观察液压系统的工作情况,如发现异常现象及时处理。
四、层压机的操作步骤1.将待加工的材料放置在层压机的工作台面上,并根据需要进行定位和固定。
2.根据操作手册上的要求,调整层压机的工作参数,包括温度、压力和时间等。
3.打开加热系统,根据需要进行预热,待材料达到预定温度后,进行下一步操作。
4.打开层压机的压力系统,根据操作手册上的要求进行压力调整。
5.启动层压机进行加工,根据工艺要求控制加工时间。
6.在层压机加工过程中,注意观察加工情况,如发现异常情况及时停机检查,防止事故发生。
7.加工完成后,关闭层压机的加热和压力系统,并将加工好的产品取出。
五、层压机的停机操作1.关闭层压机的加热系统和压力系统,并等待层压机冷却。
2.关闭层压机的液压系统和电气系统,切断电源。
3.检查层压机的运转状态,确保层压机处于停机状态。
4.清理工作区域和层压机的工作台面,确保工作区域的整洁和安全。
六、层压机的维护保养1.定期对层压机进行润滑和清洁,保持机器的正常运行状态。
整理--层压工序

层压知识整理水洗段去除酸洗、碱洗、棕化过程中板面残留的药水,避免污染下一道工序水或DI水DI水电导率,水洗时间,喷淋压力喷淋压力:14-20 psi,纯水电导率:≤ 20 μs/cm预浸段活化铜表面以利于棕化处理快速均匀,增强结合力活化剂(成分为苯并三唑、乙二醇单异丙基醚和水)活化剂浓度,温度,时间温度:40±5oC,BondFilmActivator浓度:15-25 mL/L棕化段粗化铜面并在铜面形成一层均匀的棕色有机金属转化膜,从而增强多层板内层结合力2Cu+H2SO4+H2O2+nA+nB →CuSO4+2H2O+Cu[A+B]n棕化剂MS-100、H2SO4和双氧水H2SO4浓度、H2O2浓度、棕化剂浓度、Cu2+浓度、温度、时间温度:35±5o C,BondFilmMS-100浓度:60-75 mL/L,30%H2O2浓度:35-45mL/L ,98%H2SO4浓度:40-50 mL/L,微蚀速率:45-65u”(2)棕化过程机理图示在棕化过程中,主要作用物料为乙二醇单异丙基醚和苯并三唑。
其中,乙二醇单异丙基醚(有机物A)的作用有:(1)参与环氧树脂的聚合;(2)与有机物B和金属铜形成化学键。
苯并三唑(有机物B)的作用有:(1)与基体铜结合;(2)通过与A的桥键与环氧树脂结合;(3)化合物B分子间通过配位键的形式连接。
在压合过程中,棕化膜上带有的-OH(有机物A提供)会与半固化片中的环氧基团发生反应,两者通过共价键进行结合,因此棕化有利于增强铜面与半固化片之间的结合力。
(3)棕化生产控制要点:控制项参数备注板厚度0.05-3.0 mm 板厚<0.1 mm需要带板条生产,避免卡板(1)压合工步流程:入板→选择或设置压板程序→过程参数检查→压板→出板→拆板(2)主要设备:压机,型号/供应商:精科压机(热油),设备能力—热板平整度:≤0.086 mm,温度均匀性:±1.5o C,升温速率:40-180o C升温速率8o C/min,降温速率:180-70o C 降温速率8o C/min。
层压作业指导
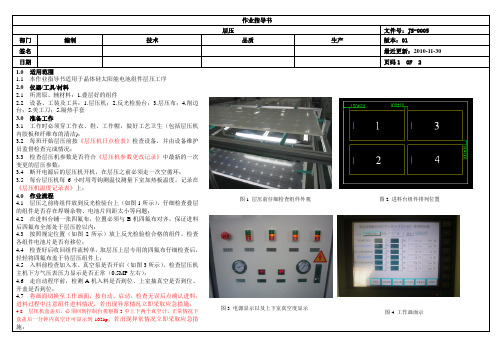
图 3 电源显示以及上下室真空度显示
图 4 工作画面示
施;
石光光伏 层压 部门 签名 日期 4.9 抽真空正常后,操作员工利用中间时间完成 A 机上料以及成品削 边工作,过程中需时刻关注层压机的出料时间和运行状况; 4.10 出料时不需有员工在 BC 机连接处,以保证组件从 B 机顺利过渡 到 C 机出料台,若出现异常情况立即采取应急措施; 4.11 组件出层压机后取掉上层层压布,观察背面是否也有凹坑,并轻 轻的将最外面一块组件翻转玻璃向上检验,如果没有异常则确认进料, 组件放在出料台需冷却 5 分钟; 4.12 层压布必须打卷回收,回收过程中注意清理层压布上残留的 EVA; 4.13 冷却后放置到削边台上仔细检查,目检合格后将流转单贴在组件 背面(注意条形码编号一致) ; 4.14 如图 7 所示进行削边,削边时玻璃朝下,刀片以 45°向前推; 4.15 不合格品请巡检确认, 做好流转单记录, 并放置在指定不良品区; 4.16 削边后的组件放置在指定位置的周转托盘上,玻璃面向下,并且 每个托盘最多叠放不超过 25 块; 4.6 满 25 块后,用叉车将组件移动到指定半成品区; 5.0 检验 5.1 层压前仔细检验组件外观,包括组件内的异物、焊锡、电池片间 距、隔离条位置等; 5.1 层压后的组件按《组件外观检验标准》要求进行外观目检; 6.0 注意事项 6.1 搬运组件时,应由两人四手护住组件四角,平拿平放 ,手指不要压在 背板上面; 6.2 每班开始之前注意清理硅胶皮上残留的杂物和硅胶; 6.3 层压前必须观察压力表显示,进料后特别注意上下室真空计显示 变化情况; 6.4 盒盖过程中注意不要挡住光幕,更不要将手放在层压腔内; 6.5 出料时注意戴手套放置烫伤; 6.6 削边时严禁将两块组件叠放在一起作业; 6.7 削边时戴手套,防止割伤手,若有受伤情况发生及时处理就医; 编制 技术 品质
层压操作规程

层压操作规程
1准备工作
1-1穿好工作衣,工作鞋,戴好工作帽和隔热手套。
1-2清洁、整理工作场地,检查设备和工具。
2对上道工序来料进行检验
2-1组件内不能漏放EVA。
2-2TPT和EVA一定要覆盖住钢化玻璃。
3层压操作过程
3-1按《层压机组操作规程》启动层压机。
3-2根据EVA特性调整层压机设定温度和抽空时间,在操作记录单上填写温度压力等技术参数。
3-3在层压机内加热板上放1-2层水发布,将拼接好的组件钢化玻璃朝下送入层压机加热板中间,再放上一层高温水发布,盖上环氧树脂板。
3-4按下合盖按钮(此时为自动状态),层压机进入自动控制系统。
3-5当层压结束后,层压机自动开盖,取出组件(视EVA性质决定对组件是否进行修边)。
3-6对组件进行自检,组件内内芯片无垃圾、碎片、裂纹、并片,组件内0.5~1mm²气泡不超过3个,1~1.5
mm²气泡不超过一个。
3-7如果返修则在随工单上做好返修原因记录,符合要求的流入下道工序在随工单上做好记录。
3-8如发现压出的扳子连续出现同样的错误则停产报告相关技术人员。
4注意事项
4-1层压机内部温度很高,在拿取组件时要戴好隔热手套避免被烫伤。
4-2修边时用的美工刀非常锋利,小心使用避免划伤。
避免划伤TPT表面。
4-3组件要轻轻放入层压机,保证放入后组件的芯片TPT、EVA不能移位。
编制: 审批: 实施日期:。
层压检验作业指导

层压后检验标准1、目的:本规范描述了太阳能电池组件产品层压后检验的要求,作为判断组件合格产品依据。
2、适用范围:本规范适用于125/156单多晶电池片生产的组件产品的层压后检验要求。
3.检验基础:条件:色差在室内光线不小于800Lx下,离样本约0.6m,目视。
4.检验项目1 层压工序:A、层压结束后,削边操作人员将冷却好的组件放置到削边台上,进行削边后;层压检验员检查层压件背面质量,有无凹痕,凸点、破损等。
2 背面外观:A、背板长短边脱层向内延伸不能大于2mm,长度不能大于5cm,在四角处脱层距玻璃角部向内延伸不能超过5mm。
B、允许表面有未深入背板基层的轻微压痕(用手摸感觉不到的) 不允许有任何深入背材基层的划伤(距边处6mm除外,以装框后不可视)。
C、焊点凸出高度≤0.8mm面积≤1.5mm2的缺陷不超过5个,面积≤2mm2的缺陷不超过2个,总数量≤6个。
D、长条形凹槽深度≤0.3mm宽度≤3mm长度≤20mm的不超过3个,长度≤50mm的不超过2个,总数量≤ 5个。
E、圆形凹陷深度≤0. 3mm,面积≤10 mm2的不超过3个,面积≤50mm2的缺陷不超过2个,总数量≤5个3.移位:A、背板移位:上下、左右移位均不能超过3mm。
B、电池片移位:单片移位在1.5mm-2.5mm的范围之内,串距在2mm-3mm的范围之内;整体移位上下、左右均不能超过3mm。
C.裂片、破片必须返修,组件内0.5-1 mm2的气泡不超过2个,1-1.5 mm2的气泡不超过1个,超过此标准的气泡必须返修,返修件仍然按标准检验。
D.检验员使用钢尺等工具,检查A面(正面)质量:裂片、杂物、气泡等。
以上各项有一项不合格即判定不合格;若产品合格,应在《工艺流程卡》上”层压检验员签字,流入下道工序,并在《层压检验记录》上作相关记录。
4. 电池片质量:A、缺角崩边:单片电池允许轻微崩边,面积≤2mm2;缺角必须是U形≤1mm2;缺陷部分距离主栅线不小于5mm,单片电池不允许超过2处不良,每个组件内不允许超过2处不良。
层压工序作业指导(精).doc
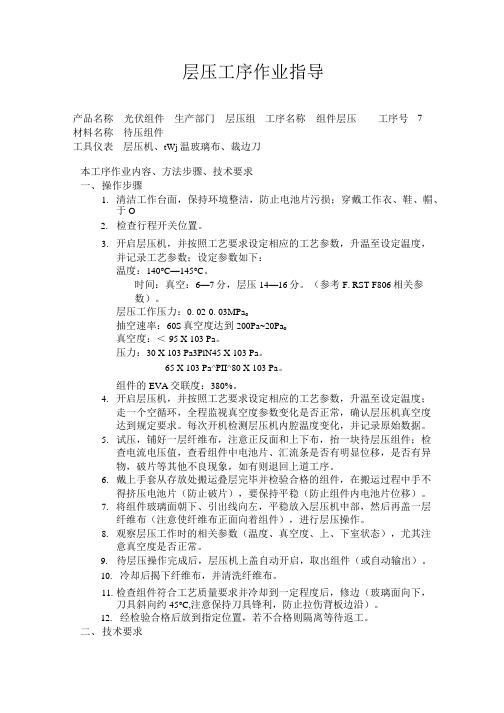
层压工序作业指导产品名称光伏组件生产部门层压组工序名称组件层压工序号7材料名称待压组件工具仪表层压机、tWj温玻璃布、裁边刀本工序作业内容、方法步骤、技术要求一、操作步骤1.清洁工作台面,保持环境整洁,防止电池片污损;穿戴工作衣、鞋、帽、于O2.检查行程开关位置。
3.开启层压机,并按照工艺要求设定相应的工艺参数,升温至设定温度,并记录工艺参数;设定参数如下:温度:140°C—145°C。
时间:真空:6—7分,层压14—16分。
(参考F. RST F806相关参数)。
层压工作压力:0. 02-0. 03MPa o抽空速率:60S真空度达到200Pa~20Pa o真空度:<-95 X 103 Pa。
压力:30 X 103 Pa3PlN45 X 103 Pa。
65 X 103 Pa^PII^80 X 103 Pa。
组件的EVA交联度:380%。
4.开启层压机,并按照工艺要求设定相应的工艺参数,升温至设定温度;走一个空循环,全程监视真空度参数变化是否正常,确认层压机真空度达到规定要求。
每次开机检测层压机内腔温度变化,并记录原始数据。
5.试压,铺好一层纤维布,注意正反面和上下布,抬一块待层压组件;检查电流电压值,查看组件中电池片、汇流条是否有明显位移,是否有异物,破片等其他不良现象,如有则退回上道工序。
6.戴上手套从存放处搬运叠层完毕并检验合格的组件,在搬运过程中手不得挤压电池片(防止破片),要保持平稳(防止组件内电池片位移)。
7.将组件玻璃面朝下、引出线向左,平稳放入层压机中部,然后再盖一层纤维布(注意使纤维布正面向着组件),进行层压操作。
8.观察层压工作时的相关参数(温度、真空度、上、下室状态),尤其注意真空度是否正常。
9.待层压操作完成后,层压机上盖自动开启,取出组件(或自动输出)。
10.冷却后揭下纤维布,并清洗纤维布。
11.检查组件符合工艺质量要求并冷却到一定程度后,修边(玻璃面向下,刀具斜向约45°C,注意保持刀具锋利,防止拉伤背板边沿)。
04-层压工序操作规范及注意事项
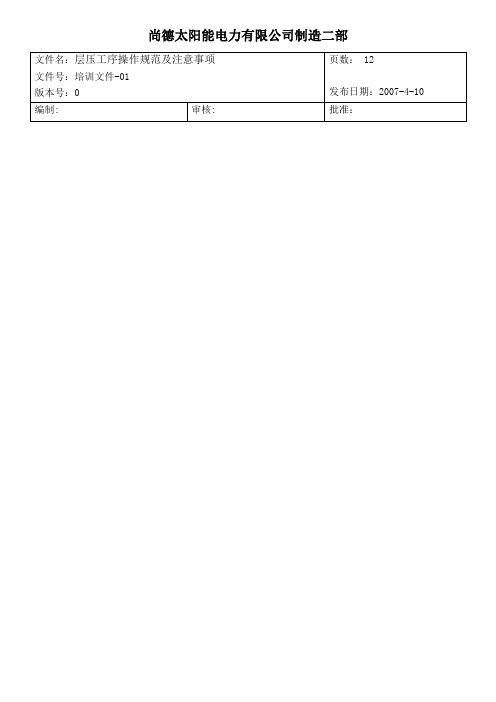
尚德太阳能电力有限公司制造二部15Quality is the conformance to standards.质量是完全符合相应的标准。
When our product meets the requirement of the standard set , it is of good quality and our product can be use for it ’s intended function.当我们的产品完全符合标准,也就是确保了质量得到了保证;在质量得到保证的条件下,我们就能满足产品性能和可靠性的要求。
遇到异常情况及时向工序长、领班汇报。
Report to your leader immediately if any abnormality isencountered!目的:层压的过程是将层叠件通过在145℃的温度下将EVA 熔融后初步固化的过程待压组件 已压组件14 压机操作规范及注意事项操作规范:一、操作前准备工作:1. 正确穿戴方法及要求2.生产前工具的准备工具要求:美工刀(见下图)美工刀 .二、申科层压机操作要求及步骤:1.1 打开真空泵冷却水及压缩空气开关,当进入自动运行时真空泵会自动启工号牌佩戴在左臂,正面朝外正确穿戴工作服、鞋、帽15动。
1.2 首先打开电源总开关(见图1),再打开左侧的(传动控制)三相空气开关和右侧的(控制系统)单相空气开关(见图2),此时热油泵开始运行,并且电脑会自动进入操作程序。
(如果电脑没有自动进入操作程序,立即通知设备部门)。
此画面顶部有一条中文菜单栏分别为:File 、运行显示、内部参数设置及手动控制(图3)。
图1 图2 图31.3 自动运行:选择“运行显示” 。
1.4.1 由组件研发部专职工艺员按工艺要求设置热板表面温度、上腔室放气速度、下腔室放气速度、上腔室抽真空时间、上腔室停抽真空时间、加温加压时间、下腔室放气时间(图4)。
层压组合预叠操作规程(3篇)
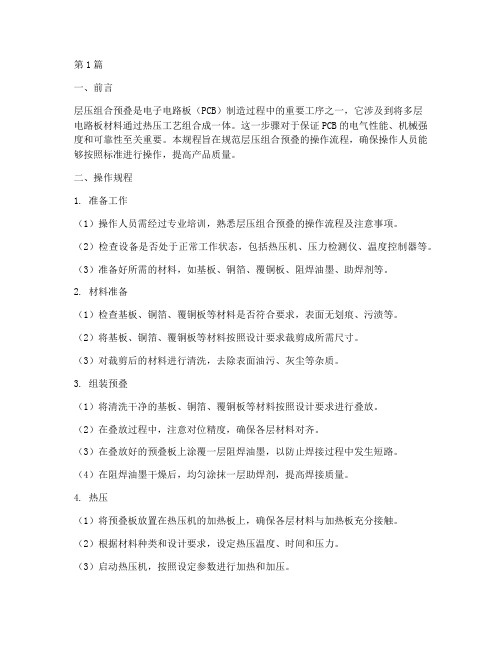
第1篇一、前言层压组合预叠是电子电路板(PCB)制造过程中的重要工序之一,它涉及到将多层电路板材料通过热压工艺组合成一体。
这一步骤对于保证PCB的电气性能、机械强度和可靠性至关重要。
本规程旨在规范层压组合预叠的操作流程,确保操作人员能够按照标准进行操作,提高产品质量。
二、操作规程1. 准备工作(1)操作人员需经过专业培训,熟悉层压组合预叠的操作流程及注意事项。
(2)检查设备是否处于正常工作状态,包括热压机、压力检测仪、温度控制器等。
(3)准备好所需的材料,如基板、铜箔、覆铜板、阻焊油墨、助焊剂等。
2. 材料准备(1)检查基板、铜箔、覆铜板等材料是否符合要求,表面无划痕、污渍等。
(2)将基板、铜箔、覆铜板等材料按照设计要求裁剪成所需尺寸。
(3)对裁剪后的材料进行清洗,去除表面油污、灰尘等杂质。
3. 组装预叠(1)将清洗干净的基板、铜箔、覆铜板等材料按照设计要求进行叠放。
(2)在叠放过程中,注意对位精度,确保各层材料对齐。
(3)在叠放好的预叠板上涂覆一层阻焊油墨,以防止焊接过程中发生短路。
(4)在阻焊油墨干燥后,均匀涂抹一层助焊剂,提高焊接质量。
4. 热压(1)将预叠板放置在热压机的加热板上,确保各层材料与加热板充分接触。
(2)根据材料种类和设计要求,设定热压温度、时间和压力。
(3)启动热压机,按照设定参数进行加热和加压。
(4)在热压过程中,密切观察温度、压力和加热时间,确保预叠板充分固化。
5. 冷却(1)热压完成后,关闭热压机,待预叠板自然冷却至室温。
(2)避免突然冷却,以免预叠板出现应力变形。
6. 检验(1)检查预叠板外观,确保无气泡、翘曲、裂纹等现象。
(2)使用万用表等仪器检测预叠板的电气性能,如绝缘电阻、介电常数等。
(3)对预叠板进行机械性能测试,如弯曲强度、冲击强度等。
(4)检查预叠板的尺寸精度,确保符合设计要求。
7. 记录(1)记录层压组合预叠的操作过程,包括材料规格、设备参数、操作时间等。
层压工艺原理及过程

层压工艺原理及过程一、原理介绍层压工艺是一种将多层材料通过压力和热力相结合的方式进行粘合的工艺。
它主要利用了材料在高温下容易变形的特性,通过压力将多层材料紧密地粘合在一起,形成一个坚固的复合材料结构。
层压工艺广泛应用于制造各种复合材料制品,如电路板、玻璃钢制品、船舶制品等。
二、层压工艺过程1. 准备工作:首先,需要准备好所需的材料和工具。
根据产品的要求选择合适的基材和粘合剂,同时准备好压力机和加热设备。
2. 材料处理:将所选材料按照产品的要求进行切割和处理。
通常情况下,材料需要按照一定的尺寸和形状进行切割,并进行表面处理以增强粘合性能。
3. 堆叠层压:将处理好的材料按照一定的顺序和层次进行堆叠。
在堆叠过程中,需要根据产品要求在不同层之间加入粘合剂。
粘合剂可以是固态的或液态的,根据不同的粘合剂,可以采用不同的加热方式。
4. 加热压实:将堆叠好的材料放入预热好的压力机中,施加一定的压力并加热。
加热的目的是使粘合剂能够在高温下熔化,从而使材料能够更好地粘合在一起。
压力的作用是使材料能够更加紧密地结合在一起,并消除可能存在的气泡和空隙。
5. 冷却固化:在加热压实过程完成后,需要将材料冷却至室温。
冷却的过程中,粘合剂会逐渐固化,形成坚固的粘合点。
冷却时间的长短取决于所使用的粘合剂的特性和产品的要求。
6. 后续处理:在层压工艺完成后,还需要进行后续的处理。
这可能包括修整、打磨、涂漆等步骤,以使最终产品符合要求。
三、层压工艺的优点1. 强度高:层压工艺可以使多层材料紧密地结合在一起,形成一个坚固的结构。
这样可以提高产品的强度和稳定性。
2. 轻量化:由于层压工艺可以在不增加材料重量的情况下提高产品强度,因此可以实现产品的轻量化设计。
这对于一些对重量要求较高的领域,如航空航天、汽车等行业具有重要意义。
3. 多样性:层压工艺可以灵活地应用于不同的材料和产品。
通过选择不同的基材和粘合剂,可以满足各种不同产品的要求。
4. 可靠性:层压工艺可以提供可靠的粘合点,使产品具有较好的耐久性和抗冲击性。
层压机操作规程范文(二篇)

层压机操作规程范文一、操作前的准备工作1. 查询生产工艺流程,了解层压机的操作要求与步骤;2. 检查层压机设备的工作状态及安全装置是否正常;3. 准备所需的原材料,并确保其质量符合要求;4. 穿戴好个人防护用品,如工作服、安全鞋、防尘口罩等。
二、启动与停机操作1. 启动操作:a. 按下主电源开关,确认机器处于待机状态;b. 打开润滑系统,确保设备正常润滑;c. 按下启动按钮,层压机开始工作。
2. 停机操作:a. 先按下急停按钮,立即切断电源;b. 关闭润滑系统;c. 断开设备与电源的连接。
三、操作层压机1. 调整层压机参数:a. 根据生产工艺要求,设置合适的温度、压力、速度等参数;b. 通过观察屏幕上的仪表和指示灯,确保参数调整到位。
2. 将原材料放入层压机:a. 将原材料切割成适当的尺寸;b. 将原材料放置在层压机的工作台上,确保放置平整。
3. 安装模具:a. 根据生产工艺要求,选取合适的模具;b. 将模具安装在层压机上,并固定好。
4. 开始层压:a. 按下“开始”按钮,层压机开始工作;b. 在层压过程中,保持观察,并及时调整参数以保持层压质量;c. 当层压结束时,及时停止层压机工作。
四、维护与保养1. 维护层压机:a. 定期清洁层压机设备,并消除设备上的杂质;b. 检查设备各部件的紧固情况,并及时调整松紧;c. 定期检修设备的电气系统、液压系统,确保其正常工作。
2. 保养层压机:a. 定期更换设备所需的润滑油,保证设备的正常润滑;b. 定期清理润滑系统,并检查其工作是否正常;c. 定期检查设备的皮带、链条等易损件,如有磨损及时更换。
五、安全注意事项1. 在操作层压机时,应先确保自己的安全,不得随意接近机器运转部件;2. 禁止用手直接触摸加热部件,以免烫伤;3. 在操作层压机时,严禁穿插手或其他物品进入层压区域;4. 如遇异常情况,切勿擅自操作,应及时报告相关人员;5. 操作层压机时应注意机器的工作状态,如有异常应立即停机并进行处理;6. 不得擅自改动或拆卸层压机设备,必要时应找专业人员进行维修。
制作木质层压板的工艺流程
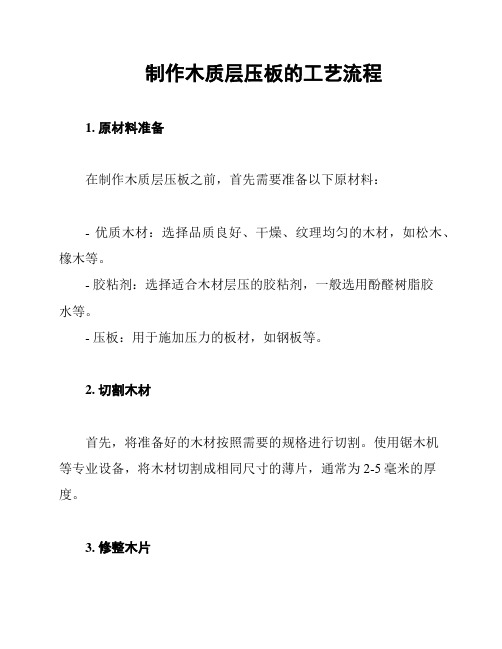
制作木质层压板的工艺流程1. 原材料准备在制作木质层压板之前,首先需要准备以下原材料:- 优质木材:选择品质良好、干燥、纹理均匀的木材,如松木、橡木等。
- 胶粘剂:选择适合木材层压的胶粘剂,一般选用酚醛树脂胶水等。
- 压板:用于施加压力的板材,如钢板等。
2. 切割木材首先,将准备好的木材按照需要的规格进行切割。
使用锯木机等专业设备,将木材切割成相同尺寸的薄片,通常为2-5毫米的厚度。
3. 修整木片将切割好的木材薄片进行修整。
使用平整机等设备,将木材薄片的两面修整得平整、光滑,确保木材表面没有任何凹凸或刺。
4. 涂胶将修整好的木片表面均匀地涂上胶粘剂。
可使用刮胶刀或刷子等工具,确保每个木片表面均匀涂覆胶粘剂。
5. 层压将涂胶的木片按照一定的层次堆叠在一起。
每层之间要涂上胶粘剂,确保木片之间粘合紧密。
6. 施加压力将层压好的木材放置在预热好的层压机中。
通过施加压力,使木片之间的胶粘剂充分结合,并且木材的厚度变薄。
压力和温度要根据具体的木材和胶粘剂进行调节,确保质量稳定。
7. 平整与修边经过压力的作用,制作出的木质层压板会略微变形。
在制作结束后,对木质层压板进行平整和修边的处理,使其达到一定的平整度和美观度。
8. 切割成型根据客户需求,将制作好的木质层压板切割成标准尺寸或特定形状,以便后续的应用。
9. 砂光和涂漆最后,对木质层压板进行必要的砂光和涂漆处理,以增加木材的质感和保护层压板的表面。
以上所述为制作木质层压板的一般工艺流程,具体操作还需根据实际制作情况进行调整。
制作过程中需要注意安全操作,并且在选择原材料和胶粘剂时,要根据需求选择合适的材料,以确保最终产品的质量和使用效果。
太阳能板层压工序注意事项

太阳能板层压工序注意事项太阳能板的层压工序是太阳能板制造过程中非常重要的一步。
在层压工序中,太阳能电池片、EVA膜和玻璃等材料被压合在一起,形成一个坚固的太阳能板。
以下是太阳能板层压工序的注意事项。
1.清洁工作:在层压工序开始之前,必须确保所有材料和设备表面的清洁。
任何灰尘、油脂或杂质都可能影响层压过程的质量和效果。
2.温度控制:在层压工序中,温度对于保证太阳能板质量至关重要。
在进行层压之前,需要将电池片和EVA膜预热至适当的温度,以确保层压后的太阳能板具有较高的结合强度。
3.压力控制:在层压工序中,适当的压力控制对于保证太阳能板的结合效果至关重要。
过低的压力可能导致太阳能板层之间存在空隙,影响太阳能吸收效率;过高的压力则可能导致太阳能板损坏或破裂。
因此,需要根据具体的材料和工艺要求,调整合适的压力值。
4.粘性剂的使用:在层压工序中,粘性剂(如EVA膜)的选择和使用对于太阳能板的质量和性能具有重要影响。
要选择具有良好粘接性和耐候性的粘性剂,并确保其均匀涂布在电池片和玻璃的表面上。
5.气泡排除:在层压过程中,必须确保太阳能电池片和EVA膜之间没有气泡产生,以免影响太阳能板的质量和效能。
为了排除气泡,可采用真空处理或针对性的压力调节措施。
6.层压时间:层压时间是太阳能板质量的一个重要参数。
层压时间过短可能导致太阳能板层之间的结合不紧密,影响太阳能板的使用寿命;层压时间过长则会增加生产周期和成本。
因此,需要根据具体情况确定合适的层压时间。
7.检验质量:完成层压后,需要进行太阳能板质量的检验。
包括检查太阳能板表面是否平整、无气泡,太阳能电池片与EVA膜之间的粘接是否牢固等。
同时,还应使用专业仪器对太阳能板的光电转换效率进行测试,以确保太阳能板的性能符合要求。
在太阳能板层压工序中,上述的注意事项能够确保太阳能板制造过程中的质量控制和技术可靠性。
只有实施严格的质量管理、合理的工艺流程和有效的检验控制,才能生产出高质量、高效能的太阳能板。
- 1、下载文档前请自行甄别文档内容的完整性,平台不提供额外的编辑、内容补充、找答案等附加服务。
- 2、"仅部分预览"的文档,不可在线预览部分如存在完整性等问题,可反馈申请退款(可完整预览的文档不适用该条件!)。
- 3、如文档侵犯您的权益,请联系客服反馈,我们会尽快为您处理(人工客服工作时间:9:00-18:30)。
层压工序作业指导
本工序作业内容、方法步骤、技术要求
一、操作步骤
1.清洁工作台面,保持环境整洁,防止电池片污损;穿戴工作衣、鞋、帽、
手套。
2.检查行程开关位置。
3.开启层压机,并按照工艺要求设定相应的工艺参数,升温至设定温度,
并记录工艺参数;设定参数如下:
①温度:140℃—145℃。
②时间:真空:6—7分,层压14—16分。
(参考F.RST F806相关参
数)。
③层压工作压力:0.02~0.03MPa。
④抽空速率:60S真空度达到200Pa~20Pa。
⑤真空度:≤-95 X 103 Pa。
⑥压力:30 X 103 Pa≥PI≥45 X 103 Pa。
65 X 103 Pa≥PII≥80 X 103 Pa。
⑦组件的EVA交联度:≥80%。
4.开启层压机,并按照工艺要求设定相应的工艺参数,升温至设定温度;
走一个空循环,全程监视真空度参数变化是否正常,确认层压机真空度
达到规定要求。
每次开机检测层压机内腔温度变化,并记录原始数据。
5.试压,铺好一层纤维布,注意正反面和上下布,抬一块待层压组件;检
查电流电压值,查看组件中电池片、汇流条是否有明显位移,是否有异
物,破片等其他不良现象,如有则退回上道工序。
6.戴上手套从存放处搬运叠层完毕并检验合格的组件,在搬运过程中手不
得挤压电池片(防止破片),要保持平稳(防止组件内电池片位移)。
7.将组件玻璃面朝下、引出线向左,平稳放入层压机中部,然后再盖一层
纤维布(注意使纤维布正面向着组件),进行层压操作。
8.观察层压工作时的相关参数(温度、真空度、上、下室状态),尤其注
意真空度是否正常。
9.待层压操作完成后,层压机上盖自动开启,取出组件(或自动输出)。
10.冷却后揭下纤维布,并清洗纤维布。
11.检查组件符合工艺质量要求并冷却到一定程度后,修边(玻璃面向下,
刀具斜向约45℃,注意保持刀具锋利,防止拉伤背板边沿)。
12.经检验合格后放到指定位置,若不合格则隔离等待返工。
二、技术要求
1.加热器技术参数:
①油加热器控温精度:±1℃。
②加热板温度均匀性:±3℃。
③加热器运行压力:0.2~0.6MPa。
2.层压机设定温度校准:在层压机达到设定温度后,使用经过计量检测机
构定期校准的点温计,并记录校准结果。
合格标准:相对设定温度不超
过±3℃。
3.放入组件时,应检查部件:
①组件引出的正负极(一般左正右负);组件引出线长度不能打折;
②TPT是否有划痕、划伤、褶皱、凹坑、是否完全覆盖玻璃、正反面
是否正确。
③EVA的正反面、大小、有无破裂、污物等;玻璃的正反面、气泡、
划伤等。
④组件内的锡渣、焊花、破片、缺角、头发、黑点、纤维、焊带的残
留等。
⑤隔离TPT是否到位、焊带是否剪齐或未剪。
⑥各个间距是否达到技术要求,组件间间隔大于10cm,组件四周边角
无翘起。
4.层压过程中应检查:
①开层压机上盖,上室真空表为-0.1MPa、下室真空表为0.00MPa,确
认温度、参数。
②符合工艺要求后进料;组件完全进入层压机内部后点击下降;上、
下室真空表都要达到-0.1MPa(抽真空)(如发现异常按“急停”,
改手动将组件取出,排除故障后再试压一块组件)等待设定时间走
完后上室充气(上室真空表显示)0.00MPa。
③下室真空表仍然保持-0.1MPa开始层压。
层压时间完成后下室放气
(下室真空表变为0.00MPa、上室真空表仍为0.00MPa)放气时间完
成后开盖(上室真空表变为-0.1MPa、下室真空表不变)出料;接
着四氟布自动返回至原点。
④组件放入至合盖,应在60秒内完成。
5.层压完成后应及时清理不粘布上的残余粘连物。
三、检验标准(具体参考组件出厂检验规范)
1.TPT是无划痕、划伤、正反面要正确。
2.组件内无头发、纤维等异物,无气泡、碎片。
3.组件内部电池片无明显位移,间隙均匀,最小间距不得小于1mm。
4.组件背面无明显凸起或者凹陷。
5.组件汇流条之间间距不得小于10mm。
6.EV A的凝胶率不能低于75%。
四、管理重点:
1.每次层压间断后,首次开机层压前,做一次层压温度校准。
2.层压机由专人操作,其他人员不得进入红线区域内。
3.修边时注意安全。
4.玻璃纤维布上无残留EV A、杂质等。
5.钢化玻璃四角易碎,抬放时须小心保护。
6.摆放组件,应平拿平放,手指不得按压电池片。
7.检查冷却水位、行程开关和真空泵是否正常。
8.区别画面状态和控制状态,防止误操作。
9.出现异常情况按“急停”后退出,排除故障后,首先恢复下室真空。
10.下室放气速度设定后,不可随意改动,经设备主管同意后方可改动,并
相应调整下室放气时间,层压参数由技术部来定,不得随意改动。
11.上室橡胶皮属贵重易耗品,进料前应仔细检查,避免利器、铁器等物混
入,划伤胶皮。
12.开盖前必须检查下箱充气是否完成,否则不允许开盖,以免损伤设备。
13.更换参数后必须走1-2次空循环,试压一块组件后,检测组件无异常,
开始层压。