线材下料优化方案
优化线材下料方案

优化线材下料方案
线材下料方案的优化可以从以下几个方面考虑:
1.材料选择:根据线材使用的具体要求,选择适当的材料。
可以考虑
使用更轻、更耐磨、更高强度的材料,以减少材料的使用量和成本。
2.下料方式:根据线材的形状、长度和数量,选择合适的下料方式。
可以考虑使用自动下料机器,以提高下料的速度和精度。
3.下料尺寸控制:根据线材的实际使用情况,合理确定下料尺寸。
可
以通过合理的计算和分析,减少浪费材料和提高利用率。
4.下料工艺优化:根据线材的具体要求和下料机器的性能,优化下料
工艺。
可以考虑采用更高的下料速度,减少下料时间和成本。
5.在线监测和优化:通过在线监测下料过程,及时调整下料参数,以
优化下料效果。
可以通过传感器和控制系统,实时监测下料质量,并进行
反馈调整。
6.优化工作流程:优化线材下料方案还可以从工作流程的角度考虑。
可以优化和简化下料过程中的工作环节,减少人工操作和物料移动,提高
工作效率和减少材料浪费。
7.数据分析和决策支持:通过收集和分析线材下料过程中的数据,可
以为决策提供支持。
可以通过数据分析,了解线材的使用情况和下料效果,以及材料的浪费情况,从而优化下料方案。
综上所述,优化线材下料方案可以从材料选择、下料方式、下料尺寸
控制、下料工艺优化、在线监测和优化、优化工作流程以及数据分析和决
策支持等方面入手,以减少材料浪费、提高效率和降低成本。
节材与材料资源利用措施 (绿色建筑)

节材与材料资源利用措施(绿色建筑)1、就地取材:根据就地取材的原则,除设计指定和本地不生产的材料、设备及半成品外,其余必须选择生产地500km范围内的,并有实施记录,统计重量,与总重量的比例大于70%。
2、制度健全:必须有健全的机械保养、限额领料、建筑垃圾再生利用等制度。
现场机械保养、限额领料、废弃物排放和再生利用等制度健全,做到有据可查,有责可究。
3、材料的选择:3.1、施工应选用绿色、环保材料。
其材料必须符合下列要求:1)符合《民用建筑工程室内环境污染控制规范》GB50325 要求。
2)符合GB18580~18588的要求。
3)混凝土外加剂应符合《混凝土外加剂中释放氨的限量》GB18588 的要求。
3.2、临建设施采用可拆迁、可回收材料。
1)、本工程所有办公、会议室、厨房、厕所、浴室、库房等临建设施,均采用可拆迁的复合彩钢板活动用房,2)、各类加工棚、固定机械防护棚,均采用自制工具式,计划200㎡。
3)、办公区的道路,使用混凝土硬化路面,可收集雨水经沉淀池后可用于洗车,浇灌等用途,可有效控制扬尘、并节约水资源。
4)、各种隔离护栏,均采用工具式金属制品。
3.3 应利用粉煤灰、矿渣、外加剂等新材料降低混凝土和砂浆中的水泥用量;粉煤灰、矿渣、外加剂等新材料掺量应按供货单位推荐掺量、使用要求、施工条件、原材料等因素通过试验确定。
4、材料节约规定:4.1、本工程采满堂红脚手架和支撑体系。
4.2、模板采用可重复使用20次以上的的竹胶板模板,计划配置三层,在模板配置到位后对每一块模板进行编号,可有效减少位错位导致模板损失较大,这样可有效节省材料节省资源。
本工程模板:1)、本工程由于剪力墙较少且形状不统一,故模板采用散拼。
2)、框架结构多为框架柱,同样采用散拼模板。
4.3 、材料运输方法应科学,应降低运输损耗率。
材料运输工具适宜,装卸方法得当,防止损坏和遗洒。
根据现场平面布置情况就近卸载,避免和减少二次搬运。
使用AUTOCAD插件MSTEEL做线材优化(铝材备料)

使用AUTOCAD插件MSTEEL做线材优化1.前期数据统计2.按MSTEEL的格式插入3.根据铝材厂家对长度的要求(一般在3000~6000间)输入原料信息,切割缝宽4.点击计算查看利用率,当利用率不高时,可以增加原料的长度规格5.重复计算,直到利用率达到97%以上注:利用率=余长+切割缝宽×(N−1)原料长度由于铝材备料要考虑铝材两端挂钩长度(40mm),以及工厂加工模数(50mm),想要提高利用率,应尽量使原料长度大一点。
附:下料优化输出结果所用原料总长216000所用原料总数41原料利用率98.5%序号原料长度数量利用率余长规格下料组合1 5700 1 98.2% 82 SYHTW24 1x3164 + 1x24342 5100 1 99.5% 7 SYHTW24 1x2998 + 1x20753 5100 22 98.2% 62 SYHTW24 1x2998 + 2x10054 5400 1 99.4% 13 SYHTW24 1x2998 + 1x23695 5700 1 99.4% 12 SYHTW24 1x2998 + 1x26706 5700 1 98.7% 54 SYHTW24 1x2998 + 1x26287 5700 1 99.4% 2 SYHTW24 1x2998 + 2x13358 5700 1 99.4% 6 SYHTW24 1x2855 + 1x1474 +1x13359 5100 1 98.1% 65 SYHTW24 1x2282 + 1x1388 + 1x133510 5700 1 96.1% 181 SYHTW24 1x1474 + 3x133511 5400 10 98.9% 20 SYHTW24 4x1335所用原料统计序号原料长度数量利用率规格1 5700 6 98.5% SYHTW242 5100 24 98.2% SYHTW243 5400 11 98.9% SYHTW24。
节材与材料资源管理制度及措施

节材与材料资源利用制度1、图纸会审时,应审核节材与材料资源利用的相关内容,达到材料损耗率比定额损耗率降低30%。
2、根据施工进度、库存情况等合理安排材料的采购、进场时间和批次,减少库存。
3、现场材料堆放有序。
储存环境适宜,措施得当。
保管制度健全,责任落实。
4、材料运输工具适宜,装卸方法得当,防止损坏和遗洒。
根据现场平面布置情况就近卸载,避免和减少二次搬运。
5、通过技术优化、下料优化提高模板、脚手架等的周转次数。
6、就地取材,施工现场500公里以内生产的建筑材料用量占建筑材料总重量的70%以上。
7、本工程采用商品混凝土。
准确计算采购数量、供应频率、施工速度等,在施工过程中动态控制。
8、推广使用高强钢筋和高性能混凝土,减少资源消耗。
9、推广钢筋专业化加工和配送。
10、优化钢筋配料和钢构件下料方案。
钢筋及钢结构制作前应对下料单及样品进行复核,无误后方可批量下料。
11、优化钢结构制作和安装方法。
大型钢结构采用工厂制作,现场拼装;宜采用分段吊装、整体提升、滑移、顶升等安装方法,减少方案的措施用材量。
12、采取数字化技术,对大体积混凝土、大跨度结构等专项施工方案进行优化。
13、门窗、屋面、外墙等围护结构选用耐候性及耐久性良好的材料,施工确保密封性、防水性和保温隔热性。
14、门窗采用密封性、保温隔热性能、隔音性能良好的型材和玻璃等材料。
15、根据建筑物的实际特点,优选屋面或外墙的保温隔热材料系统和施工方式,例如保温板粘贴、保温板干挂、聚氨酯硬泡喷涂、保温浆料涂抹等,以保证保温隔热效果,并减少材料浪费。
16、加强保温隔热系统与围护结构的节点处理,尽量降低热桥效应。
针对建筑物的不同部位保温隔热特点,选用不同的保温隔热材料及系统,以做到经济适用。
17、贴面类材料在施工前,应进行总体排版策划,减少非整块材的数量。
18、采用非木质的新材料或人造板材代替木质板材。
19、防水卷材、壁纸、油漆及各类涂料基层必须符合要求,避免起皮、脱落。
建筑线材下料方案

建筑线材下料方案建筑线材下料方案为了保证建筑工程的质量和进度,建筑施工中线材的下料是至关重要的一环。
下料方案的合理性和准确性将直接影响到施工的效率和质量,因此,我们需要制定一套完善的线材下料方案。
1. 收集施工图纸和工程要求在制定线材下料方案之前,首先需要收集施工图纸和工程要求。
施工图纸可以帮助我们了解整个工程的结构和设计,工程要求则可以指导我们制定合理的下料方案。
2. 编制线材清单根据收集到的施工图纸和工程要求,我们需要编制一份详细的线材清单。
线材清单应包括所有需要使用的线材的种类、规格、长度等信息,以及相应的数量。
3. 确定下料方式和工具在制定下料方案时,需要确定下料的方式和所需使用的工具。
根据线材的种类和规格,可以选择手工下料或机械下料。
对于大批量的线材下料,机械下料更为合适,可以提高工作效率和准确性。
4. 制定下料方案根据线材清单和施工要求,制定详细的下料方案。
下料方案应包括下料的顺序、方法以及每根线材的具体尺寸。
需要特别注意的是,在下料过程中要考虑到线材的浪费和余料的利用,以减少资源的浪费和成本的增加。
5. 质量控制在下料过程中,需要加强质量控制。
在下料前,对线材进行检查,确保线材的质量符合要求。
对于有明显磨损、生锈或其他质量问题的线材,应及时进行更换。
另外,在下料时需要严格按照方案进行操作,保证线材的尺寸和长度的准确性。
6. 记录和报备下料完成后,需要对下料的线材进行记录和报备。
记录下料线材的种类、规格和数量,并将报备给相关部门,以备后续的追溯和跟踪。
总结:建筑线材下料方案的制定是一个复杂而重要的工作,它直接影响到建筑工程的质量和进度。
通过收集施工图纸和工程要求,编制线材清单,并确定下料方式和工具,制定下料方案,并加强质量控制,能够提高下料的准确性和效率。
在操作过程中,要注意质量的控制,并及时记录和报备,以确保施工的质量和安全。
线材下料优化方案

线材下料优化方案
一、线材的定义
线材是指直径为5-22mm的热轧圆钢或者相当此断面的异形钢。
因以盘条形式交货,故又通称为盘条。
本工程涉及的线材规格有Φ6、Φ8、Φ10三种规格
二、用途
本工程所有的梁、柱箍筋;楼板的分布筋均使用以上线材。
三、操作要求
根据《混凝土结构工程施工质量验收规范》中5.3.3条及说明中规定:钢筋调直宜采用机械方法,也可采用冷拉方法。
当采用冷拉方法调直钢筋时,HPB235级钢筋的冷拉率不宜大于4%
四、具体措施
2、下料长度的确定
如:截面为200*500的梁(保护层25mm),箍筋为Φ8的计算长度(取上表)
=(200+500)*2-8*25+4*8+6.25*8
=1282mm
冷拉率控制为4%时,下料长度为1232mm
节约长度为50mm。
五、方案效益分析
方案实施后,根据本工程钢筋线材总量,可节约Φ6钢筋线材1.2T,Φ8钢筋线材5.7T,Φ10钢筋线材6.3T。
实现成本节约6万元。
优化线材下料方案

优化线材下料方案编制人:审核人:审批人:年月日目录1、编制依据................................................................................................ 错误!未定义书签。
2、工程概况................................................................................................ 错误!未定义书签。
2.1工程基本概况___________________________________________________________ 错误!未定义书签。
2.2建筑设计概况___________________________________________________________ 错误!未定义书签。
3、基础设计及要求.................................................................................... 错误!未定义书签。
3.1基础设计 _______________________________________________________________________________ 8 3.2基础的确定 _____________________________________________________________ 错误!未定义书签。
3.3基础的验收要求_________________________________________________________ 错误!未定义书签。
3.4防雷接地 _______________________________________________________________ 错误!未定义书签。
优化下料流程提高下料效率和材料利用率
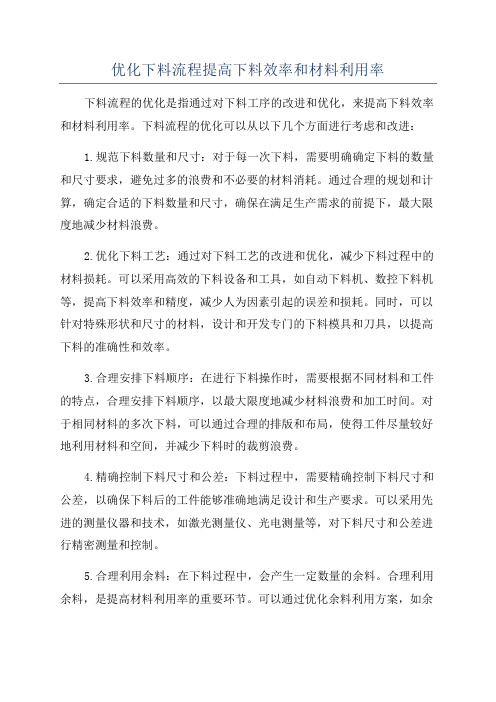
优化下料流程提高下料效率和材料利用率下料流程的优化是指通过对下料工序的改进和优化,来提高下料效率和材料利用率。
下料流程的优化可以从以下几个方面进行考虑和改进:1.规范下料数量和尺寸:对于每一次下料,需要明确确定下料的数量和尺寸要求,避免过多的浪费和不必要的材料消耗。
通过合理的规划和计算,确定合适的下料数量和尺寸,确保在满足生产需求的前提下,最大限度地减少材料浪费。
2.优化下料工艺:通过对下料工艺的改进和优化,减少下料过程中的材料损耗。
可以采用高效的下料设备和工具,如自动下料机、数控下料机等,提高下料效率和精度,减少人为因素引起的误差和损耗。
同时,可以针对特殊形状和尺寸的材料,设计和开发专门的下料模具和刀具,以提高下料的准确性和效率。
3.合理安排下料顺序:在进行下料操作时,需要根据不同材料和工件的特点,合理安排下料顺序,以最大限度地减少材料浪费和加工时间。
对于相同材料的多次下料,可以通过合理的排版和布局,使得工件尽量较好地利用材料和空间,并减少下料时的裁剪浪费。
4.精确控制下料尺寸和公差:下料过程中,需要精确控制下料尺寸和公差,以确保下料后的工件能够准确地满足设计和生产要求。
可以采用先进的测量仪器和技术,如激光测量仪、光电测量等,对下料尺寸和公差进行精密测量和控制。
5.合理利用余料:在下料过程中,会产生一定数量的余料。
合理利用余料,是提高材料利用率的重要环节。
可以通过优化余料利用方案,如余料利用方案的设计和规划,余料的再加工和利用等,有效地提高材料利用率,减少浪费。
6.加强质量管理:在下料生产过程中,加强质量管理是保证下料效率和材料利用率的关键。
通过建立和完善质量管理体系,加强对下料工艺和质量要求的控制和监督,及时发现和解决问题,以确保下料的质量和效率。
综上所述,通过规范下料数量和尺寸、优化下料工艺、合理安排下料顺序、精确控制下料尺寸和公差、合理利用余料和加强质量管理等措施,可以有效地提高下料效率和材料利用率,降低生产成本,提高企业竞争力。
优化钢筋下料方案,增加企业经济效益

优化钢筋下料方案,增加企业经济效益第一篇:优化钢筋下料方案,增加企业经济效益优化钢筋下料方案,增加企业经济效益摘要:钢筋材料是建筑工程常用的材料,其性能的好坏将对建筑工程的整体质量产生重要影响。
如何优化钢筋下料的方案,使钢筋的性能得到充分的发挥,成为建筑行业重点研究的课题。
通过采取有效的管理措施,降低钢筋的损耗率,来满足日常工程建设施工的要求,同时达到减少资源浪费、增加企业经济效益的目的。
关键词:钢筋材料;耗损率;下料方案;企业效益随着经济的飞速发展和社会的不断进步,人们的生产生活水平得到了很大的提高,对建筑工程的需求量也越来越大。
在建筑施工中,钢筋的使用量非常庞大,造价也非常昂贵,因此钢筋下料方案合理与否与钢筋损耗率的大小,可能直接决定了工程建设的质量。
由于工程建设的内容不同、钢筋材质的功用各异,因此钢筋的下料方案也是多种多样,合理优化钢筋的下料方案,是提高钢筋使用性能的重要环节,这就需要保证钢筋的存储质量、下料的过程当中注意减少钢筋的损耗,以最小的破损完成更大的施工作业,实现钢材的使用价值,以取得更好的企业效益。
一、优化钢筋下料方案的重要性(一)钢筋下料的含义分析钢筋下料是指在制作某一钢筋产品或者产品所需的钢筋材料形状时,在整批钢筋材料中截取一定形状、质量或者数量的钢筋的操作过程。
而要想顺利完成这一系列的操作,必须按照以下步骤操作:首先,钢筋下料人员能够看懂建筑工程结构施工图,这样才能准确的进行钢筋下料工作。
其次,能够计算钢筋下料的长度,掌握钢筋的保护层、量度值以及箍筋调整值等数据。
再次依据前面的准备工作,来进行钢筋的剪切和使用。
(二)优化钢筋下料方案的重要作用钢筋的下料方案是为了获得优质、高效的钢筋材料,按照建筑工程的施工图纸,结合库存材料的规格、数量以及每一编号的下料长度,填写钢筋的配料单并进行钢材切割的方案。
钢筋下料是建筑工程施工的第一步,优质的下料方案是提高工程建设质量的前提,因为它不仅提供了建筑工程所需的钢筋材料,同时也对钢筋材料的库存、使用和废料有了清晰的认识,为接下来的工程施工提供了数据支撑。
基于线性规划模型钢材下料问题最优切割方案

02
03
参考文献3
作者2,论文标题2,期刊名称2 ,发表时间2
作者3,论文标题3,期刊名称3 ,发表时间3
THANKS
感谢观看
限度地减少浪费和提高材料利用率的问题。随着制造业的不断发展,钢
材下料问题在实际生产中越来越受到关注。
02
现有研究的不足
尽管已经有一些研究针对钢材下料问题进行了探讨,但是仍存在一些问
题没有得到很好的解决,例如如何处理复杂的约束条件、如何优化切割
顺序等。
03
研究意义
本研究旨在通过建立一种基于线性规划模型的优化方法,解决现有研究
结果分析
根据实验结果,对不同切割方案进行对比分析,评估各方案的优劣
结果比较与讨论
结果比较
将最优切割方案与其他传统下料方案进 行比较,分析各自的优势与劣势
VS
结果讨论
探讨最优切割方案在实际生产中的应用与 局限性,为进一步优化提供参考依据
07
结论与展望
研究结论与贡献
线性规划模型的有效性
通过建立线性规划模型,成功解决了钢材下料问题的最优切割方案,证明了线性规划模型在该问题上的应用价值。
基于遗传算法的求解流程
01
初始化种群
随机生成一组染色体,组成初始 种群。
03
评估最优解
在迭代过程中,不断评估当前种 群中的最优解,记录最优解及其
对应的染色体。
02
迭代优化
通过选择、交叉和变异等操作, 逐步优化种群中的染色体。
04
终止条件
根据终止条件(如达到最大迭代 次数或最优解满足精度要求等)
,终止算法并输出最优解。
钢材下料问题建模
钢材下料问题是指如何将一块或多块钢材切割 成指定形状和尺寸的小块,以满足客户需求。
一种简便的下料优化方法
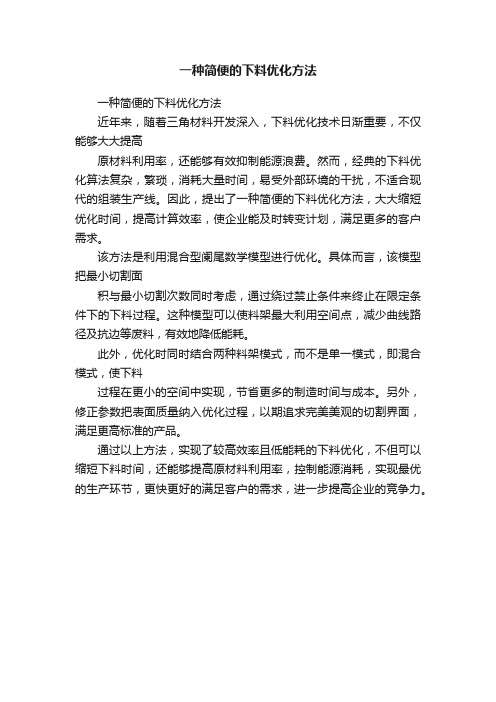
一种简便的下料优化方法
一种简便的下料优化方法
近年来,随着三角材料开发深入,下料优化技术日渐重要,不仅能够大大提高
原材料利用率,还能够有效抑制能源浪费。
然而,经典的下料优化算法复杂,繁琐,消耗大量时间,易受外部环境的干扰,不适合现代的组装生产线。
因此,提出了一种简便的下料优化方法,大大缩短优化时间,提高计算效率,使企业能及时转变计划,满足更多的客户需求。
该方法是利用混合型阑尾数学模型进行优化。
具体而言,该模型把最小切割面
积与最小切割次数同时考虑,通过绕过禁止条件来终止在限定条件下的下料过程。
这种模型可以使料架最大利用空间点,减少曲线路径及抗边等废料,有效地降低能耗。
此外,优化时同时结合两种料架模式,而不是单一模式,即混合模式,使下料
过程在更小的空间中实现,节省更多的制造时间与成本。
另外,修正参数把表面质量纳入优化过程,以期追求完美美观的切割界面,满足更高标准的产品。
通过以上方法,实现了较高效率且低能耗的下料优化,不但可以缩短下料时间,还能够提高原材料利用率,控制能源消耗,实现最优的生产环节,更快更好的满足客户的需求,进一步提高企业的竞争力。
浅谈如何优化下料方法
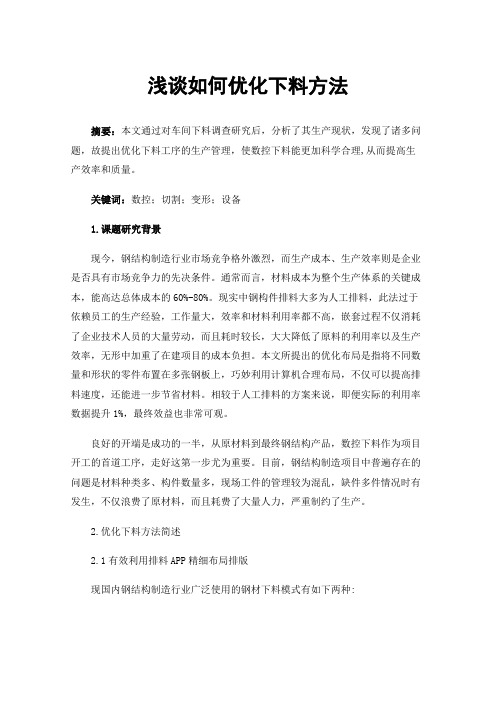
浅谈如何优化下料方法摘要:本文通过对车间下料调查研究后,分析了其生产现状,发现了诸多问题,故提出优化下料工序的生产管理,使数控下料能更加科学合理,从而提高生产效率和质量。
关键词:数控;切割;变形;设备1.课题研究背景现今,钢结构制造行业市场竞争格外激烈,而生产成本、生产效率则是企业是否具有市场竞争力的先决条件。
通常而言,材料成本为整个生产体系的关键成本,能高达总体成本的60%-80%。
现实中钢构件排料大多为人工排料,此法过于依赖员工的生产经验,工作量大,效率和材料利用率都不高,嵌套过程不仅消耗了企业技术人员的大量劳动,而且耗时较长,大大降低了原料的利用率以及生产效率,无形中加重了在建项目的成本负担。
本文所提出的优化布局是指将不同数量和形状的零件布置在多张钢板上,巧妙利用计算机合理布局,不仅可以提高排料速度,还能进一步节省材料。
相较于人工排料的方案来说,即便实际的利用率数据提升1%,最终效益也非常可观。
良好的开端是成功的一半,从原材料到最终钢结构产品,数控下料作为项目开工的首道工序,走好这第一步尤为重要。
目前,钢结构制造项目中普遍存在的问题是材料种类多、构件数量多,现场工件的管理较为混乱,缺件多件情况时有发生,不仅浪费了原材料,而且耗费了大量人力,严重制约了生产。
2.优化下料方法简述2.1有效利用排料APP精细布局排版现国内钢结构制造行业广泛使用的钢材下料模式有如下两种:(1)人工排料。
对特定项目而言,依据设计图开展细节的结构拆分,捕捉相应的下料信息,依托人工方法开展排料,再结合排料方案进行板材切割的处理。
若构件数量很少时,此法简单快捷。
但若某一类型的构件数量较多,外形较为复杂时,单靠员工凭经验完成下料工作,原材料利用率和工作效率都很低。
需求的材料以及工时,都很难精准把控,有碍材料的管理以及生产计划的调整。
(2)发展软件辅助排料。
将最优化理论应用于实践场景,配合计算机的辅助方案,进而取代人工排料。
钢管下料优化方案
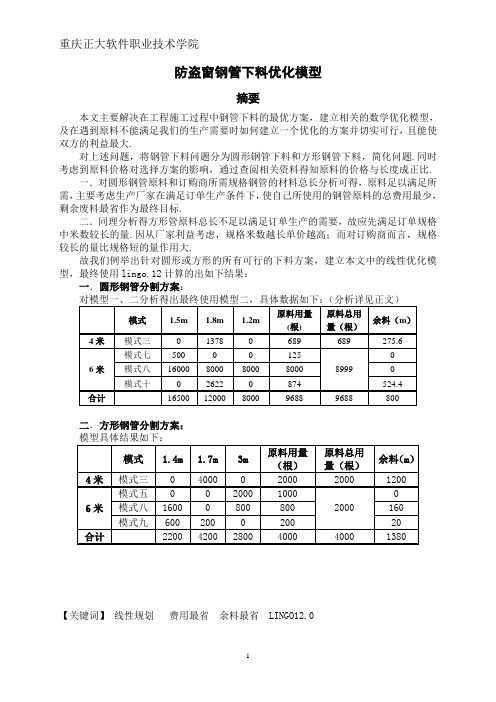
防盗窗钢管下料优化模型摘要本文主要解决在工程施工过程中钢管下料的最优方案,建立相关的数学优化模型,及在遇到原料不能满足我们的生产需要时如何建立一个优化的方案并切实可行,且能使双方的利益最大.对上述问题,将钢管下料问题分为圆形钢管下料和方形钢管下料,简化问题.同时考虑到原料价格对选择方案的影响,通过查阅相关资料得知原料的价格与长度成正比.一.对圆形钢管原料和订购商所需规格钢管的材料总长分析可得,原料足以满足所需,主要考虑生产厂家在满足订单生产条件下,使自己所使用的钢管原料的总费用最少,剩余废料最省作为最终目标.二.同理分析得方形管原料总长不足以满足订单生产的需要,故应先满足订单规格中米数较长的量.因从厂家利益考虑,规格米数越长单价越高;而对订购商而言,规格较长的量比规格短的量作用大.故我们例举出针对圆形或方形的所有可行的下料方案,建立本文中的线性优化模型,最终使用lingo.12计算的出如下结果:一.圆形钢管分割方案:对模型一、二分析得出最终使用模型二,具体数据如下:(分析详见正文)模式 1.5m 1.8m 1.2m 原料用量(根)原料总用量(根)余料(m)4米模式三0 1378 0 689 689 275.66米模式七500 0 0 12589990 模式八16000 8000 8000 8000 0 模式十0 2622 0 874 524.4合计16500 12000 8000 9688 9688 800二.方形钢管分割方案:模型具体结果如下:模式 1.4m 1.7m 3m 原料用量(根)原料总用量(根)余料(m)4米模式三0 4000 0 2000 2000 12006米模式五0 0 2000 100020000 模式八1600 0 800 800 160 模式九600 200 0 200 20合计2200 4200 2800 4000 4000 1380 【关键词】线性规划费用最省余料最省 LINGO12.0一.问题的提出某不锈钢装饰公司承接了一住宅小区的防盗窗安装工程,为此购进了一批型号为304的不锈钢钢管,分为方形管和圆形管两种,具体数据如下表:表1-1规格长4m 长6m方形管25×25×1.2(mm) 5000根9000根圆形管Φ19×1.2(mm) 2000根2000根根据小区的实际情况,需要截取钢管的规格与数量如下:表1-2圆形管规格 1.5m 1.8m 1.2m 方形管规格 1.4m 1.7m 3m 数量(根)16500 12000 8000数量(根)6000 4200 2800根据上述的实际情况建立数学模型,寻找经济效果最优的下料方案,使得厂家在满足订购商的订单需要的同时还能节约原料.二.问题的分析通过题目可知,要求我们在题目所给定的条件下,找寻最佳下料方案,使满足各种需要的前提下所使用的原材料的费用、所使用的量和所剩的余料最省.圆形钢管原材料的总长:()45000+69000=74000 m⨯⨯,订单产品的总长:()1.516500+1 .812000+1.28000=55950m⨯⨯⨯.方形钢管原材料的总长:()42000+ 62000=20000m⨯⨯,订单产品的总长:()1.46000+1.74200+32800=23940m⨯⨯⨯.通过计算,分析得出问题中的圆形钢管原料足够多,在使用时主要考虑所使用的原材料的费用、使用量和切割之后的余料最少;而方形管的原材料明显不能满足生产需要,此时应首先考虑切割不同长度的钢管的优先问题.通过查阅网络资料可得网络上对于304不锈钢钢管的单价是50元/公斤,而相应的不锈钢管重量公式:⨯⨯外径-壁厚)壁厚]0.0249每米的重量(千克/米)[(=又因为在我们的原材料中,规格都为Φ19×1.2(mm),所以可得每米的重量都是一定的,故我们可以得到每根钢管的单价与原材料的长度成正比,比例系数为k,即6米管的单价是6k,4米的单价是4k,所以6米管的单价是4米管的6k/4k=1.5倍.因此在处理这个问题时对于生产厂家而言,应考虑所生产的成品规格越长利益越大;对于订购商而言,规格长度越大材料的使用性越大.通过上诉分析可得,应该在原有材料使用完的情况下先满足规格为3米的钢管,其次是1.7米的钢管,再次生产1.4米的钢管.然而此类问题属于数学中最优解的求解问题,这是典型的线性优化,故该问题可以建立线性优化方程解决.三.模型假设1.假设钢管切割过程中无原料损耗或损坏;2.假设所生产的各种规格的钢管不能通过焊接产生;3.假设同种钢管采用的切割模式数量不限;4.假设每种钢管的单价相同且与长度成正比.四.符号说明x表示采用第i种模式下切割的钢管数id表示第i中模式下的第j种规格下的根数ijc表示第i种模式下的余料ia表示第j种规格的需求量jy表示使用4米的原料所以使用的根数1y表示使用6米的原料所以使用的根数2y表示生产规格为1.5米的钢管总数3y表示生产规格为1.8米的钢管总数4y表示生产规格为1.2米的钢管总数5y为满足生产需求产生的余料总和6k表示单位长度或者单位公斤数钢管原料的价格五.模型的建立与求解针对题目的要求我们将钢管下料方案分为圆形钢管和方形钢管两类,简化问题,并建立相关数学模型.首先根据题目已知条件可得要先给4米和6米不同规格的原材料进行分割,因此产生了不同的切割模式,选取最佳切割模式才是所要求的下料方案.其中切割所剩的余料必须小于所需切割的最小长度,在条件满足的不同组合的情况下,得知圆形管的切割方案有17种;方形钢管的切割方案有11种,具体切割方案如下:5.1 圆形钢管5.1.1圆形钢管的切割方案表5-1模式 1.5m 1.8m 1.2m 余料(m) 圆形`4 米 切 割 模 式模式一 0 0 3 0.4 模式二 2 0 0 1 模式三 0 2 0 0.4 模式四 0 1 1 1 模式五 1 0 2 0.1 模式六 1 1 0 0.7 6 米 切 割 模 式模式七 4 0 0 0 模式八 2 1 1 0 模式九0 0 5 0 模式十 0 3 0 0.6 模式十一 0 1 3 0.6 模式十二 1 0 3 0.9 模式十三 1 2 0 0.9 模式十四 0 2 2 0 模式十五 3 0 1 0.3 模式十六 2 0 2 0.6 模式十七1120.35.1.2圆形钢管的下料模型建立针对圆形管的切割方案,我们假设原材料采用模式i 切割的数量为x i (x i 必须为大于1的正整数),那么目标函数即为使生产厂家在完成订单需要的情况下所使用的原材料最少,同时所使用的原料的费用最少,且又因6米管的原料单价是4米管的1.5倍,所以目标函数是:min z (4)+1.5(6)k k =⨯⨯原料中米的总根数原料中米的总根数又由已知条件可得,所生产的量必须满足订购商的需要,即1.5m 圆管16500根,1.8m 圆管12000根,1.2m 圆管8000根,因此产生以下三个目标函数的约束条件:≤生产规格中所有的1.5米的总根数16500 ≤生产规格中所有的1.8米的总根数12000 8000≤生产规格中所有的1.2米的总根数因此可得如下数学模型:617176117717117311min k 1.550009000..0()i ii i i i i i i ii ij i j i j z x k x x x S T x x d x a ========+⎧≤⎪⎪⎪≤⎪⎪⎨⎪≥⎪⎪⎪≥⎪⎩∑∑∑∑∑∑∑为整数 利用lingo12.0编程运算得出最终结果如下表:(程序代码详见附录1)表5-2模式 1.5 1.8 1.2 原料用量 原料总用量 余料 4米模式三 0 1378 0 689 689275.6 6米模式七500 0 0 125 8999 0 模式八 16000 8000 8000 8000 0 模式十0 2622 0 874 524.4 合计1650012000800096889688 800且对于模型中钢管每米的单价k 进行不同程度改变,得知k 的值不会影响生产过程中我们对模式的选择,只会相应的改变原料成本,影响相应的利润.通过对上表的结果进行分析得,该模型已经满足生产不同规格钢管的需要,且没有多余的生产量,但该模型只考虑到所用的原料费用最省,不一定满足所要求的生产订单过后的余料最省,也就是不一定满足原料的使用率最大,故我们对模型进一步优化检验,把目标函数变为:min z 4(4)+6(6=⨯⨯⨯原料中米的总根数原料中米的总根数) -(订单中所有规格长)(订单中相应规格的根数)最终可得模型如下:617176117717117311min 465595050009000..0()i i i i i i i i i ii ij i j i j z x x x x s t x x d x a ========+-⎧≤⎪⎪⎪≤⎪⎪⎨⎪≥⎪⎪⎪≥⎪⎩∑∑∑∑∑∑∑为整数同样用lingo12.0编程运算得出结果如下:(程序代码详见附录2)表5-3模式 1.5m 1.8m 1.2m 原料用量(根) 原料总用量(根) 余料(m ) 4米模式三 0 1378 0 689 689275.6 6米模式七500 0 0 125 8999 0 模式八 16000 8000 8000 8000 0 模式十0 2622 0 874 524.4 合计1650012000800096889688 800从表一和表二相应结果可得,两张表结果一模一样.相应的证明了该切割方案是最优的切割方案,同时也满足最初的假设,即生产厂家在完成订购商的订单需要的情况下,原材料的使用最少,所产生的费用最少,并在生产过程种产生的废料最少,废料的总和才800米,同时也满足原料的使用率最大.故最佳的切割方案是使用用689根4米的原材料采用模式三进行切割,125根6米的原材料采用模式七进行切割,8000根6米的原材料采用模式八进行切割,874根6米的原材料采用模式十进行切割.5.2 方形钢管5.2.1方形钢管的切割方案表5-4模式 1.4m 1.7m 3m 余料(m)方形管4米切割模式模式一0 0 1 1模式二 2 0 0 1.2模式三0 2 0 0.6模式四 1 1 0 0.96米切割模式模式五0 0 2 0模式六 4 0 0 0.4模式七0 3 0 0.9模式八 2 0 1 0.2模式九 3 1 0 0.1模式十 1 2 0 1.2模式十一0 1 1 1.35.2.1方形钢管余料最少由于方型钢管所能提供的原材料远远不能满足生产所需,该情况下,如果还继续限制所用的材料,那么我们就无法满足生产方管的订单需要.根据问题分析中原材料的单价与它的长度成正比,并对于生产厂家而言,成品规格越长利益越大;对于订购商而言,规格长度越大材料的使用性越大.又因为:方管的总量为:42000+62000=20000m⨯⨯(),方管中的规格为1.7米和3米的钢管总长为:1.74200+32800=15540m⨯⨯().所以得出方管足以满足生产规格为3米和1.7米的钢管,即严格要求生产规格为3米和1.7米的钢管,对于规格为1.4米的钢管实在无法满足需要,只限制它的量必须大于0即可.故可得:3=2800生产出的规格为米的总根数1.7=4200生产出的规格为米的总根数1.4生产出的规格为米的总根数>0又因为总量本身不够生产,所以要求方管的所有材料必须用于生产,所以可得:=原料方管中所使用的4米的总根数2000综上分析可得关于余量最省的优化数学模型如下:()1114111511111312111111min 20002000..00i ii i i i i i i ij i j i j i i i x c x x S T x d x a d x a a ========⎧=⎪⎪⎪=⎪⎪⎪⎪≥⎨⎪⎪=⎪⎪⎪⎪≥=⎪⎩∑∑∑∑∑∑∑同样使用lingo12.0软件编程运算得出如下结果:(程序代码详见附录3) 表5-5模式 1.4m 1.7m 3m原料用量(根) 原料总用量(根) 余料(m )4米 模式三0 4000 0 2000 20001200 6米 模式五0 2000 1000 2000 0 模式八 16000 800 800 160 模式九600 200 0 200 20 合计22004200280040004000 1380对模型结果分析可得,该切割方案已是最优,没有成品钢管的浪费,又能满足生产厂家利润最大,同时还能满足订购商的长料利用率较大.并且在生产过程中总共产生1380米废弃材料.因此最优切割方案是用2000根4米的原材料采用模式三进行切割,1000根6米的原材料采用模式五进行切割,800根6米的原材料采用模式八进行切割,200根6米的原材料采用模式九进行切割.六.模型的分析与推广通过线性规划的应用,可以更好的求解一定约束条件下的最优值的求解问题,能够得出最佳合理的答案.同时线性规划对实际问题的分析与应用较为普遍,容易查找相关资料,同时可见其适于现实问题的求解,例如:对水管的下料,钢材的切割,电线的切割等,优化之后还能解决玻璃的切割问题等等.同时枚举法的运用是问题的求解思路更清晰的呈现,此为该模型的优点.但是切割模式较多,枚举法加大了运算量同时导致问题的解答相对繁杂,也是该模型的明显缺点.参考文献:[1] 颜文勇,数学建模,高等教育出版社,2011.6[2] 谢金星、薛毅,优化建模与LINDO/LINGO软件,北京,清华大学出版社,2009.12[3] /view/1266775.htm(钢管每米重量计算公式)附录附录1:MODEL:MIN=k*(X1+X2+X3+X4+X5+X6)+1.5*k*(X7+X8+X9+X10+X11+X12+X13+X14+X15+X16+X17);k=50;2*X2+X5+X6+4*X7+2*X8+X12+X13+X17>=16500;2*X3+X4+X6+X8+3*X10+X11+2*X13+2*X14+X17>=12000;X4+2*X5+X8+5*X9+3*X11+3*X12+X15+2*X16+2*X17>=8000; X1+X2+X3+X4+X5+X6<=5000;X7+X8+X9+X10+X11+X12+X13+X14+X15+X17<=9000;y1=x1+x2+x3+x4+x5+x6; !y1是使用4米长的原料所用的根数;y2=x7+x8+x9+x10+x11+x12+x13+x14+x15+x17; !y2是使用6米长的原料所用的根数;y3=2*x2+x5+x6+4*x7+2*x8+x12+x13+3*15+2*16+x17; !y3是切得规格为1.5米钢管的总数;y4=2*x3+x4+x6+x8+3*x10+x11+2*x13+2*x14+x17;!y4是切得规格为1.8米钢管的总数;y5=x4+2*x5+x8+5*x9+3*x12+3*x11+2*14+x15+2*x16+2*x17;!y5是切得规格为1.2米钢管的总数;y6=x1*0.4+x2+x3*0.4+x4+x5*0.1+x6*0.7+x7*0+x8*0+x9*0+x10*0.6+x11*0.6+x12*0.9+x13*0.9+x14*0+x15*0.3+x16*0.6+x17*0.3;!为满足生产需求产生的余料总和;@GIN( X1); @GIN( X2); @GIN( X3); @GIN( X4); @GIN( X5); @GIN( X6); @GIN( X7);@GIN( X8); @GIN( X9); @GIN( X10); @GIN( X11); @GIN( X12); @GIN( X13);@GIN( X14); @GIN( X15); @GIN( X16); @GIN( X17);END附录2:MODEL:MIN=4*X1+4*X2+4*X3+4*X4+4*X5+4*X6+6*X7+6*X8+6*X9+6*X10+6*X11+6*X12+6*X13+6*X14+6*X15+6*X16+6*X17-55950; 2*X2+X5+X6+4*X7+2*X8+X12+X13+X17>=16500;2*X3+X4+X6+X8+3*X10+X11+2*X13+2*X14+X17>=12000;X4+2*X5+X8+5*X9+3*X11+3*X12+X15+2*X16+2*X17>=8000; X1+X2+X3+X4+X5+X6<=5000;X7+X8+X9+X10+X11+X12+X13+X14+X15+X17<=9000;y1=x1+x2+x3+x4+x5+x6; !y1是使用4米长的原料所用的根数;y2=x7+x8+x9+x10+x11+x12+x13+x14+x15+x17; !y2是使用6米长的原料所用的根数;y3=2*x2+x5+x6+4*x7+2*x8+x12+x13+3*15+2*16+x17; !y3是切得规格为1.5米钢管的总数;y4=2*x3+x4+x6+x8+3*x10+x11+2*x13+2*x14+x17;!y4是切得规格为1.8米钢管的总数;y5=x4+2*x5+x8+5*x9+3*x12+3*x11+2*14+x15+2*x16+2*x17;!y5是切得规格为1.2米钢管的总数;y6=x1*0.4+x2+x3*0.4+x4+x5*0.1+x6*0.7+x7*0+x8*0+x9*0+x10*0.6+x11*0.6+x12*0.9+x13*0.9+x14*0+x15*0.3+x16*0.6+x17*0.3;!为满足生产需求产生的余料总和;@GIN( X1); @GIN( X2); @GIN( X3); @GIN( X4); @GIN( X5); @GIN( X6); @GIN( X7);重庆正大软件职业技术学院@GIN( X8); @GIN( X9); @GIN( X10); @GIN( X11); @GIN( X12); @GIN( X13);@GIN( X14); @GIN( X15); @GIN( X16); @GIN( X17);END附录3:MODEL:MIN=4*X1+4*X2+4*X3+4*X4+4*X5+4*X6+6*X7+6*X8+6*X9+6*X10+6*X11+6*X12+6*X13+6*X14+6*X15+6*X16+6*X17-55950; 2*X2+X5+X6+4*X7+2*X8+X12+X13+X17>=16500;2*X3+X4+X6+X8+3*X10+X11+2*X13+2*X14+X17>=12000;X4+2*X5+X8+5*X9+3*X11+3*X12+X15+2*X16+2*X17>=8000; X1+X2+X3+X4+X5+X6<=5000;X7+X8+X9+X10+X11+X12+X13+X14+X15+X17<=9000;y1=x1+x2+x3+x4+x5+x6; !y1是使用4米长的原料所用的根数;y2=x7+x8+x9+x10+x11+x12+x13+x14+x15+x17; !y2是使用6米长的原料所用的根数;y3=2*x2+x5+x6+4*x7+2*x8+x12+x13+3*15+2*16+x17; !y3是切得规格为1.5米钢管的总数;y4=2*x3+x4+x6+x8+3*x10+x11+2*x13+2*x14+x17;!y4是切得规格为1.8米钢管的总数;y5=x4+2*x5+x8+5*x9+3*x12+3*x11+2*14+x15+2*x16+2*x17;!y5是切得规格为1.2米钢管的总数;y6=x1*0.4+x2+x3*0.4+x4+x5*0.1+x6*0.7+x7*0+x8*0+x9*0+x10*0.6+x11*0.6+x12*0.9+x13*0.9+x14*0+x15*0.3+x16*0.6+x17*0.3;!为满足生产需求产生的余料总和;@GIN( X1); @GIN( X2); @GIN( X3); @GIN( X4); @GIN( X5); @GIN( X6); @GIN( X7);@GIN( X8); @GIN( X9); @GIN( X10); @GIN( X11); @GIN( X12); @GIN( X13);@GIN( X14); @GIN( X15); @GIN( X16); @GIN( X17);END11。
基于python的钢筋下料优化算法

基于python的钢筋下料优化算法关于基于Python的钢筋下料优化算法摘要:本文将介绍一种基于Python的钢筋下料优化算法。
钢筋下料是指根据建筑施工图纸中的钢筋需求,将钢筋材料按照一定规则进行切割和制造加工,以适应具体施工需要。
传统的钢筋下料通常是根据经验和人工计算来进行,效率较低且容易出错。
而基于Python的优化算法可以通过数学模型和计算机技术,快速准确地计算出最优方案,实现钢筋材料的有效利用。
本文将分为三个部分来详细介绍基于Python的钢筋下料优化算法。
首先,我们将介绍算法的原理和基本思想,包括数学模型的构建和优化目标的设定。
其次,我们将详细介绍算法的实现过程,包括算法流程图和具体的代码实现。
最后,我们将通过一个具体的案例来验证算法的有效性,并对算法的优缺点进行分析和讨论。
通过本文的介绍,读者将能够了解和掌握基于Python的钢筋下料优化算法的原理和实现方法,从而提高钢筋下料的效率和准确性。
关键词:Python;钢筋下料;优化算法;数学模型;效率;准确性一、算法的原理和基本思想1.1 数学模型的构建钢筋下料问题可以看作一种组合优化问题。
首先,我们需要将建筑施工图纸中的钢筋需求转化为数学模型。
通常,钢筋的规格和长度是已知的,我们需要根据建筑施工图纸中的需求,将规格和长度进行匹配,以确定需要使用的钢筋数量和长度。
同时,我们还需要考虑到钢筋的切割和制造加工的限制条件,如最大切割长度、加工时间等。
基于以上考虑,我们可以构建如下的数学模型:- 变量:- Xi:第i根钢筋的数量;- Lij:第i根钢筋经过某一切割方案后得到的第j段长度;- Yij:第i根钢筋经过某一切割方案后得到的第j段长度是否需要加工;- Xij:第i根钢筋经过某一切割方案后得到的第j段长度的数量;- 目标函数:- min ∑(∑Xij),i=1...n,j=1...m;- 约束条件:- ∑Lij=XiLi,i=1...n;- ∑Xij≤Xijmax,i=1...n,j=1...m;- ∑Yij=Yijmax,i=1...n,j=1...m;- Xij≤∑Lij,i=1...n,j=1...m;- Yij≤Xij,i=1...n,j=1...m;其中,n表示钢筋的种类数量,m表示切割得到的钢筋段数,Li表示钢筋i的长度,Xijmax表示第i根钢筋切割后得到的第j段长度的最大数量,Yijmax表示第i根钢筋切割后得到的第j段长度需要经过加工的最大数量。
钢筋下料长度优化

(1)优化背景:|常规钢筋工程下料。
(2)优化实施:做一个正方形方格表,取原点记为 o,相邻两轴为x、y,
在边 ox_oy 上标记 1.2、3、...表示下料的根数。
以供应钢筋长度为 14m,下料钢筋长度为 1.9m、2.3m、3.3m 为例,一根 14m 钢筋下 1.9m 长的钢筋
为 7.37 根,下 2.3m 长的钢筋为 6.09 根,下 3.3m 长的钢筋为 4.24 根。
在 ox 边上,取 1.9m 下料根数 7.37 根处,标记点 A;在 oy 边上,取 2.3m
下料根数 6.09 根处,标记点 B;在 ox 边上,取 3.3m 下料根数 4.24 根处,标
记点 C;在 oy 边上,取 3.3m 下料根数 4.24 根处,标记点 D。
连接 AB、AD、BC,在△0AB、△0AD、△0BC 中,距离 AB、AD、BC 最近的点为最佳组合。
(3)实施效果:AB 段:1×1.9+5×2.3=13.4m 和 7×1.9=13.3m,对比可节约0.1m;AD 段:2×1.9+3×3.3=13.7m)和 3.3×4=13.2m,对比可节约 0.5m;BC 段
:2×3.3+3×2.3=13.5m 和 3.3×4=13.2m 对比可节约 0.3m。
将以,上搭配方
法进行比较,可以根据下料数量,找出余料数量最小的搭配组合。
(4)提示:提高钢筋放样人员综合能力,对钢筋剩余短料用途做到心中有数,如梁垫铁马凳、洞口侧面附加筋等零量构件可以利用短料加工。
一种输送带转载漏斗下料系统优化方案

一种输送带转载漏斗下料系统优化方案何晓涛㊀惠刚刚㊀肖龙飞广州港集团有限公司㊀㊀摘㊀要:针对输送带转载漏斗下料系统存在的物料拥堵㊁物料对设备冲击过大等问题,应用离散元仿真方法模拟系统的物理过程和运行状态,并依据仿真实验结果提出一种优化方案,对输送带头部漏斗㊁三通分料器㊁落煤溜管㊁开口处承接匙等开展优化设计㊂应用表明,该优化方案可提高系统的生产效率与稳定性,对提高输送带转载漏斗下料系统的整体性能具有技术参考价值㊂㊀㊀关键词:离散元仿真;输送带;漏斗Optimization Scheme for Feeding System of Conveyor Belt Transfer FunnelHe Xiaotao㊀Hui Ganggang㊀Xiao LongfeiGuangzhou Port Group Co.,Ltd.㊀㊀Abstract:Based on the problems of material congestion and excessive impact of materials on equipment in the feeding system of the conveyor belt transfer funnel,the discrete element simulation method is applied to simulate the physical process and operation state of the system.Based on the simulation experiment results,an optimization plan is proposed to optimize the design of the conveyor belt head funnel,tee distributor,coal chute,and opening receiving key.The application shows that this optimization scheme can improve the production efficiency and stability of the system,and has technical reference value for improving the overall performance of the conveyor belt transfer funnel feeding system.㊀㊀Key words:discrete element simulation;conveyor belt;funnel1㊀引言输送带转载漏斗下料系统作为一种常见的固体散货物料输送手段,广泛应用于物流㊁矿山㊁化工等领域㊂输送带转载漏斗连接流程上下游的输送带,实现物料的转向和分流㊂由于散货物料作业工况的复杂性㊁漏斗下料系统设计不合理等原因,在作业过程中,漏斗往往会存在物料拥堵㊁物料对设备冲击过大等问题,导致生产流程故障停止㊁物料洒漏㊁生产效率降低,装卸成本增加㊂因此需要对输送带转载漏斗下料系统进行优化设计㊂2㊀优化方案2.1㊀问题分析某港口煤矿装卸系统转载房漏斗为2个一通二分叉结构,给料输送带和受料输送带之间落差达到7.2m㊂原漏斗下料系统设计存在的主要问题表现为:在煤炭下落过程中,物料直接冲击漏斗面,导致漏斗衬板磨损加剧;给料输送带头部漏斗为方形结构,在锥角部位容易粘黏较湿的煤炭,继而缩小漏斗通径,导致漏斗物料拥堵甚至完全阻塞;下料溜管为方形直筒,物料通过溜管垂直落入受料输送带上,对受料输送带及其托辊承受强大而持续的冲击,加剧输送带跑偏和托辊的损坏,并在受料输送带上产生大量扬尘,煤炭颗粒因高坠产生剧烈弹跳现象,导致煤粒从输送带尾部洒漏,增加了人工清理量㊂2.2㊀优化目标与优化步骤(1)优化目标根据煤炭的颗粒特性,优化系统构造,以控制物料流动的方向和速度,使漏斗在使用过程中保持畅通,避免漏斗体和受料输送带承受剧烈冲击㊂(2)优化步骤①对煤炭物料的颗粒特性进行测验㊂②对漏斗新的下料系统进行3D建模㊂③将煤炭物料颗粒模型数据㊁输送带参数㊁漏斗下料系统3D模型输入EDEM仿真软件,动态模拟漏斗下料系统的物料传送过程㊂④根据模拟仿真结果,对下料系统3D模型进一步修改优化㊂⑤进行漏斗的制作㊁安装和调试㊂41Port Operation㊀2024.No.2(Serial No.275)2.3㊀煤炭颗粒物料的材料模型测验为更好地进行EDEM 仿真模拟,需对煤炭颗粒的材料模型进行测验,如对煤炭颗粒堆积休止角进行测验,用于控制颗粒的堆积方式,从而模拟真实的煤炭堆积情况,反映散体颗粒群综合作用的宏观特征[1]㊂材料模型主要包括煤炭颗粒的密度㊁煤粒堆积角㊁含水量等对物料运动规律影响的参数㊂通过煤炭堆积密度测验㊁干燥箱含水率测试㊁振动式筛分仪尺寸分布测验㊁静动安息角测验等,得到煤炭颗粒的参数(见表1)㊂表1㊀煤炭颗粒的参数表参数名称煤炭颗粒参数堆积密度/(kg ㊃L -1)0.8~0.9静堆积角/ʎ45动堆积角/ʎ20含水量/%8~12粒度/m3~202.4㊀漏斗下料系统设计2.4.1㊀漏斗下料系统整体设计根据物料下落的抛物线特性使用曲面型漏斗设计方案㊂煤炭颗粒在曲面型漏斗的引导下,能够形成更为流畅的运动轨迹,避免物料在漏斗内堵塞和滞留,保证物料的连续输送,减轻物料对漏斗体和受料输送带的冲击负荷,有助于延长设备的使用寿命㊂曲面型漏斗具有较好的适应性,可以适用于多种煤炭颗粒的输送㊂对于不同颗粒大小和物理特性的煤炭物料,可通过调整曲面形状和角度来满足不同的需求㊂漏斗下料系统整体设计见图1㊂1.导液挡板㊀2.头部护罩㊀3.头部漏斗㊀4.三通㊀5.曲线落料管6.曲线落料管-纠偏箱㊀7.曲线落料管-纠偏卸料罩㊀8.承接匙图1㊀漏斗下料系统整体设计2.4.2㊀头部漏斗曲面导流挡板设计在给料输送带头部漏斗中安装曲面导流挡板,改变传统的漏斗衬板直接受冲击的方式,合理改变物料流的方向㊂新设计的导流挡板为3D 曲面结构,采用非常小的冲击角度调整物料运动轨迹,曲面结构能够收拢分散的物料,无锥角的设计可避免因煤颗粒粘黏而发生堵煤现象(见图2)㊂图2㊀3D 曲面导流挡板结构2.4.3㊀曲线溜管设计使用3D 曲线溜管设计,能有效控制煤炭物料流动速度和形态(见图3)㊂在溜管下端设置纠偏箱和调料挡板,可对末端料流进行方向调整,使之能够准确落在出口处的承接匙中㊂出口处3D 曲面物料承接匙的设计,确保将物料以较小冲击角度和速度差卸载到受料输送带上,并使煤炭的冲击方向与受料输送机运行方向相同,有效减少粉尘和冲击的产生,避免洒漏㊂下料过程中,不同落料高度会出现不同程度的落料不均匀现象,需将出料口落料高度设计在1m 以内[2]㊂3D 曲面溜管和承接匙设计能有效减少对受料输送机及其下方缓冲托辊的冲击,提升输送机的整体寿命㊂1.3D 曲线溜管㊀2.出口处3D 曲面承接匙图3㊀曲线溜管-出口承接匙设计2.5㊀仿真验证本方案中,使用ROCKY 三维离散单元法仿真软件,根据煤炭物料测验参数,模拟煤炭粒子组在输送机漏斗下料系统特定边界条件下的流动状况,包括物料的速度㊁轨迹和分布情况㊂该分析有助于识别潜在的问题,如物料堵塞㊁剧烈冲击㊁洒漏和粉尘生成等㊂通过仿真结果,可以评估漏斗下料系统的(下转第29页)51港口装卸㊀2024年第2期(总第275期)图7㊀传感器数据界面4㊀结语通过开发港口起重机运行状态监测平台,模拟起重机堆场作业流程,对起重机运行状态进行实时监测,评估起重机重要结构的健康状态,可提升码头工作人员的管理水平和管理效率㊂参考文献[1]㊀李娜,刘关四,王志杰,等.港口起重机械运行状态监测数据集成分析系统开发及应用[J].中国特种设备安全,2022,38(9):1-4+30.[2]㊀李毅,陈松.基于PLC 的起重机安监管理系统设计[J].电气时代,2021(7):24-27.[3]㊀李益波,肖炳林,何威誉,等.大数据驱动的港口机械状态监测平台研究[J].港口装卸,2020(1):1-5+48.唐现琼:411105,湖南省湘潭市雨湖区湘潭大学机械工程与力学学院收稿日期:2024-03-07DOI:10.3963/j.issn.1000-8969.2024.02.010(上接第15页)性能,并针对存在的问题进行优化设计,例如调整漏斗的形状㊁角度和尺寸,以改善物料的流动性和分布均匀性,优化溜管的设计,以减少物料的冲击和磨损,降低设备的维护量㊂将物料模型数据㊁优化设计的漏斗三维模型㊁输送带参数输入仿真软件并进行模拟验证,结果见图4㊁5㊂图4㊀BC34下BC36/BC37漏斗物料颗粒运动模拟仿真情况图5㊀BC33下BC36/BC37漏斗物料颗粒运动模拟仿真情况从图4和图5可以看出,煤炭物料以3.15m /s的速度均匀下料,正中落于承接匙中,并平缓进入受料输送带,漏斗下料系统的模型设计满足设计要求,表现出良好的性能特点㊂(1)物料在冲击点的表现符合设计目标,冲击角小于20ʎ,没有出现剧烈冲击或煤炭颗粒的严重反弹现象,可以有效地降低扬尘和洒漏,同时减轻漏斗体的磨损㊂(2)落料点与下方的受料输送机实现了对中,使得物料能够轻冲击地送料到受料输送带上,避免了落料不正和皮带跑偏的问题㊂(3)解决了锥角积料问题㊂通过3D 曲面挡板和溜管的设计,有效地避免了锥角粘黏煤炭颗粒继而缩小下料系统通径的问题,避免了堵料问题的发生㊂根据仿真验证得到最佳漏斗下料系统模型后,重新制作和安装了新的漏斗系统㊂重载调试结果显示,重建后下料系统的运行效果良好㊂漏斗下料系统溜管内㊁出口处的受料输送带受煤的冲击力减小,落料点集中在输送带中间无跑偏,洒漏量和粉尘也显著减少㊂3㊀结语优化后的输送带转载漏斗采用曲线下料系统设计,解决了漏斗易堵塞和设备承受剧烈冲击的问题,保证了装卸系统设备的平稳运行,减少了粉尘和洒漏的产生,提高了煤炭输送设备的寿命,在港口㊁矿场等行业具有推广意义㊂参考文献[1]㊀李艳洁,徐泳.用离散元模拟颗粒堆积问题[J].农机化研究,2005(2):57-59.[2]㊀许强.皮带输送机安装维护对跑偏问题的影响及处理措施[J].机械管理开发,2023(7):253-254.何晓涛:510100,广东省广州市越秀区东山口沿江东路406号收稿日期:2024-01-18DOI:10.3963/j.issn.1000-8969.2024.02.00692港口装卸㊀2024年第2期(总第275期)。
集中下料实施方案
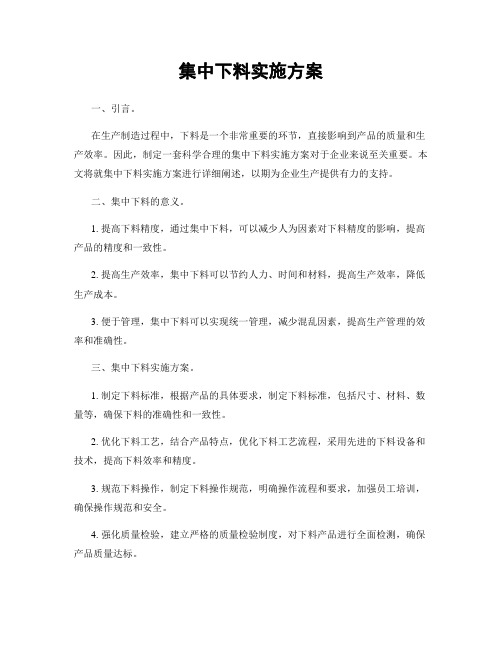
集中下料实施方案一、引言。
在生产制造过程中,下料是一个非常重要的环节,直接影响到产品的质量和生产效率。
因此,制定一套科学合理的集中下料实施方案对于企业来说至关重要。
本文将就集中下料实施方案进行详细阐述,以期为企业生产提供有力的支持。
二、集中下料的意义。
1. 提高下料精度,通过集中下料,可以减少人为因素对下料精度的影响,提高产品的精度和一致性。
2. 提高生产效率,集中下料可以节约人力、时间和材料,提高生产效率,降低生产成本。
3. 便于管理,集中下料可以实现统一管理,减少混乱因素,提高生产管理的效率和准确性。
三、集中下料实施方案。
1. 制定下料标准,根据产品的具体要求,制定下料标准,包括尺寸、材料、数量等,确保下料的准确性和一致性。
2. 优化下料工艺,结合产品特点,优化下料工艺流程,采用先进的下料设备和技术,提高下料效率和精度。
3. 规范下料操作,制定下料操作规范,明确操作流程和要求,加强员工培训,确保操作规范和安全。
4. 强化质量检验,建立严格的质量检验制度,对下料产品进行全面检测,确保产品质量达标。
5. 数据化管理,采用信息化手段,实现下料数据的实时监控和管理,及时发现问题并进行调整。
四、实施效果评估。
1. 下料精度提高,经过集中下料实施方案的实施,产品下料精度得到显著提高,产品质量得到有效保障。
2. 生产效率提升,集中下料方案的实施,使得生产效率得到明显提升,生产成本得到有效控制。
3. 管理效果明显,集中下料实施方案的实施,使得生产管理变得更加规范和高效,管理效果得到明显提升。
五、结语。
集中下料实施方案的制定和实施,对于企业生产具有重要意义。
通过本文的介绍,相信大家对于集中下料实施方案有了更深入的了解。
希望企业能够根据自身情况,制定出更加科学合理的集中下料实施方案,为企业的发展提供有力的支持。
优化下料流程提高下料效率和材料利用率
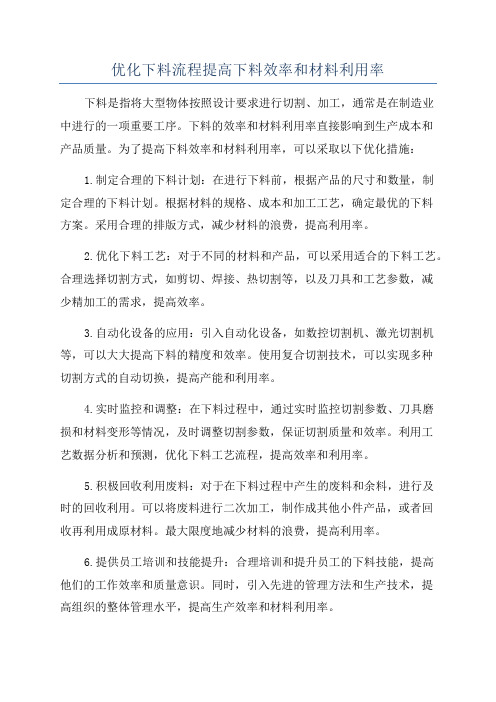
优化下料流程提高下料效率和材料利用率下料是指将大型物体按照设计要求进行切割、加工,通常是在制造业中进行的一项重要工序。
下料的效率和材料利用率直接影响到生产成本和产品质量。
为了提高下料效率和材料利用率,可以采取以下优化措施:1.制定合理的下料计划:在进行下料前,根据产品的尺寸和数量,制定合理的下料计划。
根据材料的规格、成本和加工工艺,确定最优的下料方案。
采用合理的排版方式,减少材料的浪费,提高利用率。
2.优化下料工艺:对于不同的材料和产品,可以采用适合的下料工艺。
合理选择切割方式,如剪切、焊接、热切割等,以及刀具和工艺参数,减少精加工的需求,提高效率。
3.自动化设备的应用:引入自动化设备,如数控切割机、激光切割机等,可以大大提高下料的精度和效率。
使用复合切割技术,可以实现多种切割方式的自动切换,提高产能和利用率。
4.实时监控和调整:在下料过程中,通过实时监控切割参数、刀具磨损和材料变形等情况,及时调整切割参数,保证切割质量和效率。
利用工艺数据分析和预测,优化下料工艺流程,提高效率和利用率。
5.积极回收利用废料:对于在下料过程中产生的废料和余料,进行及时的回收利用。
可以将废料进行二次加工,制作成其他小件产品,或者回收再利用成原材料。
最大限度地减少材料的浪费,提高利用率。
6.提供员工培训和技能提升:合理培训和提升员工的下料技能,提高他们的工作效率和质量意识。
同时,引入先进的管理方法和生产技术,提高组织的整体管理水平,提高生产效率和材料利用率。
7.数据化管理和优化:建立下料过程的数据化管理系统,对各项参数进行全面监控和分析。
通过对数据的统计和分析,了解下料的瓶颈和问题所在,进行相应的优化和改善,提高下料效率和材料利用率。
综上所述,通过制定合理的下料计划,优化下料工艺,应用自动化设备,实时监控和调整,积极回收利用废料,提供员工培训和技能提升,以及数据化管理和优化等措施,可以有效提高下料效率和材料利用率,降低生产成本,提高产品质量。
- 1、下载文档前请自行甄别文档内容的完整性,平台不提供额外的编辑、内容补充、找答案等附加服务。
- 2、"仅部分预览"的文档,不可在线预览部分如存在完整性等问题,可反馈申请退款(可完整预览的文档不适用该条件!)。
- 3、如文档侵犯您的权益,请联系客服反馈,我们会尽快为您处理(人工客服工作时间:9:00-18:30)。
线材下料优化方案
一、线材的定义
线材是指直径为5-22mm的热轧圆钢或者相当此断面的异形钢。
因以盘条形式交货,故又通称为盘条。
本工程涉及的线材规格有Φ6、Φ8、Φ10三种规格
二、用途
本工程所有的梁、柱箍筋;楼板的分布筋均使用以上线材。
三、操作要求
根据《混凝土结构工程施工质量验收规范》中5.3.3条及说明中规定:钢筋调直宜采用机械方法,也可采用冷拉方法。
当采用冷拉方法调直钢筋时,HPB235级钢筋的冷拉率不宜大于4%
四、具体措施
2、下料长度的确定
如:截面为200*500的梁(保护层25mm),箍筋为Φ8的计算长度(取上表)
=(200+500)*2-8*25+4*8+6.25*8
=1282mm
冷拉率控制为4%时,下料长度为1232mm
节约长度为50mm。
五、方案效益分析
方案实施后,根据本工程钢筋线材总量,可节约Φ6钢筋线材1.2T,Φ8钢筋线材5.7T,Φ10钢筋线材6.3T。
实现成本节约6万元。