硬质合金低压热等静压烧结工艺
烧结-热等静压法制取wc-co系硬质合金

烧结-热等静压法制取wc-co系硬质合金众所周知,硬质合金制品经真空(或氢气)烧结后,可以消除压制型坯中的孔洞,基本完成了致密化过程。
不过,为了进一步提高硬质合金的密度和抗弯强度,仍需进行后续热等静压处理,以消除微孔,并使残留石墨溶解于液相,通过扩散来消除石墨相。
但是,热等静压处理过程中,如果温度、压力、时间等参数选择不当,会有部分WC晶粒长大,而粗大的WC和微孔一样,往往成为工件破坏的裂纹源。
从80年代开始,烧结-热等静压工艺悄然兴起,在同一台设备里可依次进行脱蜡、预烧、最终烧结和热等静压工序,这样不仅节省了大量的设备投资,而且与传统的真空烧结+后续热等静压工艺相比,硬质合金产品的性能也有所提高<1>。
为了开发及推广这一新工艺,作者进行了WC-Co系列硬质合金的实验,测定了抗弯强度、硬度( HRA)和密度,并做了光学显微镜金相观察及断口SEM观察。
通过对真空烧结、真空烧结后续热等静压及烧结-热等静压这3种状态的WC- Co合金组织和性能的比较,阐述了烧结-热等静压工艺的优越性,并探讨了其提高合金性能的原因。
1实验材料及方法实验所用原料为市售产品,其化学成分(质量分数,下同)见表 1 ,采用不掺胶冷等静压方法成形(压力为2× 1 0 2 MPa)。
真空烧结制度:温度1 360℃,保温40 min;热等静压制度:氩气介质,压力1 0 0 MPa,温度 1 340℃,保温保压 1 .5h;烧结-热等静压制度示于图1。
烧结-热等静压炉为钢铁研究总院自行设计制造的第一台国产SIP30 0 - I型(卧式)烧结-热等静压炉,主要参数为:最高工作温度 1 60 0℃,最高真空度 1 .33Pa,最高工作压力6MPa,工作室有效空间30 0 mm×30 0 mm×1 2 0 0 mm。
工艺流程:装料表1WC- 15 Co混合粉的化学成分/ %Table 1Com positions of WC- 15 Co mixed powder/ %元素C总C游Fe O2 Co WC含量5 .2 0 0 .0 2 2 0 .0 2 40 .3 714 .84余图1烧结-热等静压工艺制度Fig.1Schematic diagram of sinter- HIP process—抽真空—升温—烧结温度保温—充氩气加压—保温保压—降压冷却—出料。
硬质合金烧结实验

硬质合金的烧结一、实验目的了解硬质合金烧结的基本知识及烧结特点二、实验原理烧结是指在高温作用下,坯体发生一系列物理化学变化,由松散状态逐渐致密化,且机械强度大大提高的过程。
在烧结过程中包括有机物的挥发、坯体内应力的消除、气孔率的减少;在烧结气氛作用下,粉末颗粒表面氧化物的还原、原子的扩散、粘性流动和塑性流动;烧结后期还可能出现二次再结晶过程和晶粒长大过程。
三、烧结方式及特点真空烧结与低压烧结真空烧结:在低于大气压力条件下进行的粉末烧结。
主要用于烧结活性金属和难熔金属铍、钍、钛、锆、钽、铌等;烧结硬质合金、磁性合金、工具钢和不锈钢;以及烧结那些易于与氢、氮、一氧化碳等气体发生反应的化合物。
优点是:(1)减少了气氛中有害成分(水、氧、氮)对产品的不良影响。
(2)对于不宜用还原性或惰性气体作保护气氛(如活性金属的烧结),或容易出现脱碳、渗碳的材料均可用真空烧结。
(3)真空可改善液相对固相的润湿性,有利于收缩和改善合金的组织。
(4)真空烧结有助于硅、铝、镁、钙等杂质或其氧化物的排除,起到净化材料的作用。
(5)真空有利于排除吸附气体、孔隙中的残留气体以及反应气体产物,对促进烧结后期的收缩有明显作用。
如真空烧结的硬质合金的孔隙度要明显低于在氢气中烧结的硬质合金。
(6)真空烧结温度比气体保护烧结的温度要低一些,如烧结硬质合金时烧结温度可降低100~150℃。
这有利于降低能耗和防止晶粒长大。
不足是:(1)真空烧结时,常发生金属的挥发损失。
如烧结硬质合金时出现钴的挥发损失。
通过严格控制真空度,即使炉内压力不低于烧结金属组分的蒸气压,也可大大减少或避免金属的挥发损失。
(2)真空烧结的另一个问题是含碳材料的脱碳。
这主要发生在升温阶段,炉内残留气体中的氧、水分以及粉末内的氧化物等均可与碳化物中的化合碳或材料中的游离碳发生反应,生成一氧化碳随炉气抽出。
含碳材料的脱碳可用增加粉末料中的含碳量以及控制真空度来解决。
低压烧结:低压烧结的“低压”是相对…热等静压‟的压力来说的,二者都是在等静压力下烧结,前者的压力约为5Mpa 左右,后者的压力高达70~100MPa 。
烧结一热等静压工艺
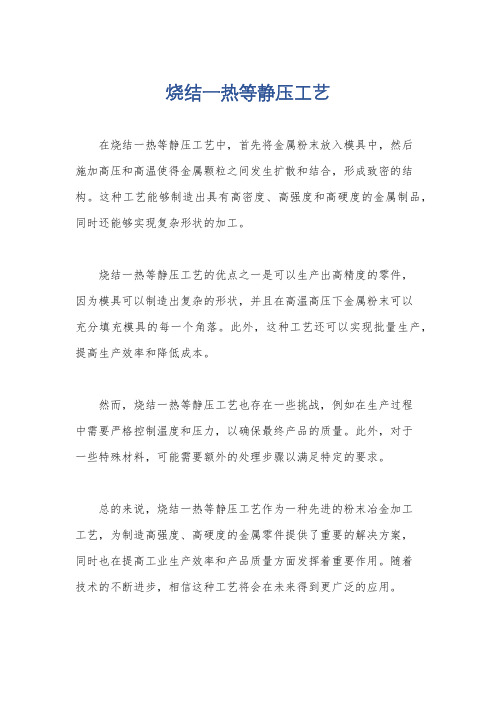
烧结一热等静压工艺
在烧结一热等静压工艺中,首先将金属粉末放入模具中,然后
施加高压和高温使得金属颗粒之间发生扩散和结合,形成致密的结构。
这种工艺能够制造出具有高密度、高强度和高硬度的金属制品,同时还能够实现复杂形状的加工。
烧结一热等静压工艺的优点之一是可以生产出高精度的零件,
因为模具可以制造出复杂的形状,并且在高温高压下金属粉末可以
充分填充模具的每一个角落。
此外,这种工艺还可以实现批量生产,提高生产效率和降低成本。
然而,烧结一热等静压工艺也存在一些挑战,例如在生产过程
中需要严格控制温度和压力,以确保最终产品的质量。
此外,对于
一些特殊材料,可能需要额外的处理步骤以满足特定的要求。
总的来说,烧结一热等静压工艺作为一种先进的粉末冶金加工
工艺,为制造高强度、高硬度的金属零件提供了重要的解决方案,
同时也在提高工业生产效率和产品质量方面发挥着重要作用。
随着
技术的不断进步,相信这种工艺将会在未来得到更广泛的应用。
硬质合金烧结工艺
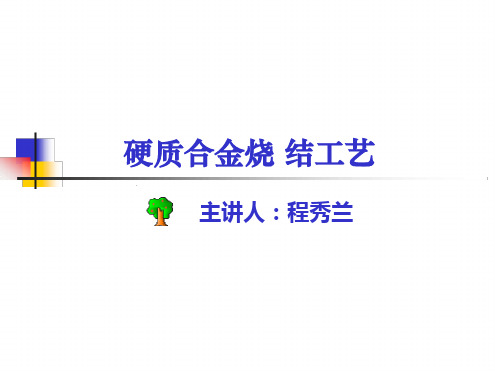
2) 影响碳化钨晶粒长大的因素
1.液相数量 影响液相数量的主要因素是: a. 烧结温度
影响液相数量的主要因素是:
a.烧结温度
b.含钴量 c.含碳量
②混合料的状态
? a.原始粉末的粒度 ? b.粒度分布均匀性 ? c.磨碎程度
相;碳量过剩,则为WC+C+ 液相;碳适量,则为WC+ 液相。
? 1.1.4. 冷却阶段(烧结温度~室温)
? 冷却速度只影响γ 相成分,不影响组织,最终组织为 WC+ γ。 ? WC-TiC- CO合金的烧结:与WC – CO 合金的烧结基本类似 。其主要区别表现 在液相的成分,出现液相的温度和所得 合金组织的不同。
? 烧结主要是物理过程,烧结体 致密化,碳化物晶粒长大,粘 结相成分的变化以及合金结构 的形成等。
图1W-C-C O系状态图在凝固温度下的等温切面
1. 1 烧结过程四阶段及相应的组织转变
1.1.1. 脱蜡预烧阶段(<800℃) 1) 成形剂的脱除 2) 粉末表面氧化物还原 3) 粉末颗粒相互之间的状态发生变化 1.1.2. 固相烧结阶段(800℃~共晶温度) ? 共晶温度是指缓慢升温时,烧结体中开始出现共晶液相的温度,对
图3 YG15合金烧结时试样长度为 50.5毫米的收缩过程 1—舟皿上层试样 2—舟皿下层试 样
? 1.2烧结体的致密化
? 1.2.1.致密化机理:致密化机理是流动过程 。
? 1) 固相烧结时的扩散与塑性流动 ? 2)液相烧结时的重排、溶解——析出与界面结构的形成 ? ①重排: ? 必要前提: ? ② 溶解-析出 ? ③界面结构的形成
硬质合金的烧结工艺

硬质合金的烧结工艺 Revised by Chen Zhen in 2021硬质合金烧结工艺硬质合金是由各种碳化物和铁族元素组成,例如WC-Co、WC-TiC-TaC-NbC-Co或是TiC-MoC-Ni。
这些材料的典型特点就是,通过液相烧结可以达到几乎100%理论密度,烧结后,低的残余孔隙度是成功应用硬质合金于金属切削、石油开采钻头或者金属成形模具等高应力使用工况的关键。
此外,必须仔细控制烧结工艺,以获得希望的显微组织和化学成分。
在很多应用场合,硬质合金都是以烧结态应用的。
烧结态合金表面经常承受条件苛刻的摩擦和应力,在大多数的切削金属应用中,刀头表面的磨耗深度只要超过0.2~0.4mm,工具就被判定报废,所以,提高硬质合金的表面性能是相当重要的。
烧结硬质合金的两种基本方法:一种是氢气烧结——在氢气中与常压下通过相反应动学来控制零件成分,另一种是真空烧结——采用真空环境或降低环境气体压强,通过减缓反应动力学来控制硬质合金成分。
真空烧结有着更为广泛的工业应用。
有时,还采用烧结热等静压和热等静压,这些技术都对硬质合金的生产有着重要的影响。
氢气烧结:氢气是还原性的气氛,但当氢气与烧结炉壁或承载装置发生反应时会改变其他成分,提供合适的碳化势以维持与硬质合金的热力学平衡。
在传统的硬质合金烧结中,要将混合料中的碳化物的含碳量调节到理论值,并在整个氢气烧结过程中维持这个值不变。
例如,烧结94WC-6CO硬质合金时,入炉时,碳含量为5.70~5.80%(质量分数),出炉时,则要维持在5.76+0.4%氢气烧结工艺的气氛控制能力对于钨钴类硬质合金来说是足够的,但是对于切钢工具用含碳化钛碳化钽或碳化铌的合金来说,气氛的氧化势太高,导致合金的成分变化,通常用真空烧结来减低这些,合金氧化物的含量,氢气烧结一般用机械推舟的方式,通过连续烧结来完成,可用一个单独的预烧炉除去润滑剂防止挥发物污染后的高烧结过程。
预烧结还可以调高生胚强度,使能对其进行粗切削加工,例如,进行车削和钻孔,预烧结温度在500~800摄氏度间,这主要取决于润滑剂除去的是否彻底及所需生胚强度。
碳纤维增强碳化钨硬质合金的烧结方法和研究进展

碳纤维增强碳化钨硬质合金的烧结方法和研究进展1.引言碳化钨-钴(WC-Co)硬质合金是以碳化钨粉末为主要原料,Co做粘结剂而制成的一种合金。
因碳化钨-Co硬质合金具有高硬度、高强度和优良的耐磨性及抗氧化性,而被广泛的用于机械加工、采矿钻探、模具和结构耐磨件等领域[1]。
超细碳化钨-钴硬质合金是指合金中碳化钨晶粒平均尺寸为0.1~0.6μm,这使其具有高强度、高硬度和高韧性,有效地解决了传统硬质合金硬度与强度之间的矛盾。
碳化钨晶粒在100nm 以下的纳米硬质合金应当有更优良的性能。
1959年,Shindo A首先发明了用聚丙烯腈(PAN)纤维制造碳纤维。
美国在21世纪革命性的12项材料技术中,则将“新一代碳纤维、纳米碳管”排在第四位[2]。
碳纤维具有高强度、高模量、密度小,比强度高、耐高温、耐摩擦、导电、导热、膨胀系数小等优良性能。
正因如此,将碳纤维与树脂、金属、陶瓷等基体复合后得到的碳纤维复合材料,同样具有高的比强度、比模量、耐疲劳、耐高温、抗蠕变等特点。
近年来它们被广泛地应用于航空航天、汽车构件、风力发电叶片、油田钻探、体育用品、建筑补强材料等领域[3]。
超细碳化钨-钴硬质合金和碳纤维在某些方面的优异性能和在工业上的广泛应用,使得国内外很多研究学者对这两种材料进行了深入研究。
本文将主要从超细碳化钨-钴硬质合金的烧结手段及其对硬质合金性能的影响、致密化方式和效果,碳纤维增强复合材料的性能等方面对国内外文献进行综述。
2. 烧结方法目前国内外研发了许多制备超细碳化钨粉末的方法,主要有直接碳化法[4]、氢气还原WO X碳化法、流化床还原碳化法、气相沉积法、有机盐热分解碳化法、等离子电弧法、熔盐法和机械球磨法、液相还原法[5]等,目前应用于工业化规模生产的主要是前三种方法。
要使超细碳化钨粉末具备特殊性能,必须经过烧结这一关键步骤,烧结技术的不同将对硬质合金的性能产生重要影响。
而如何有效控制碳化钨晶粒在烧结过程中的长大行为成为制备超细晶和纳米晶硬质合金的关键技术。
热等静压(hip)技术在硬质合金及陶瓷材料中的应用
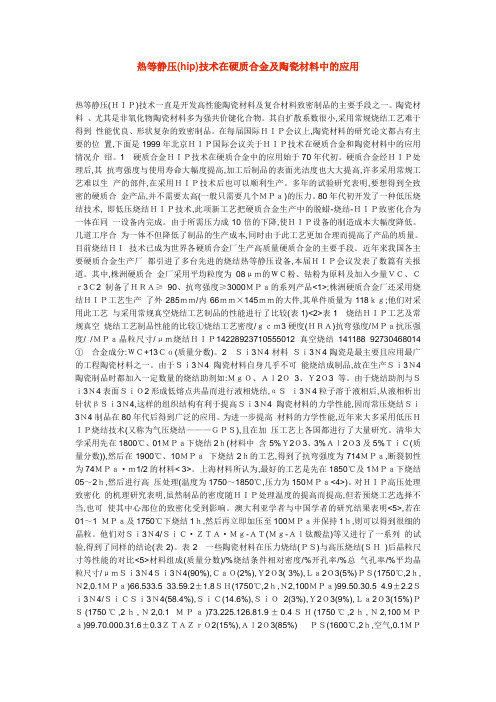
热等静压(hip)技术在硬质合金及陶瓷材料中的应用热等静压(HIP)技术一直是开发高性能陶瓷材料及复合材料致密制品的主要手段之一。
陶瓷材料、尤其是非氧化物陶瓷材料多为强共价键化合物。
其自扩散系数很小,采用常规烧结工艺难于得到性能优良、形状复杂的致密制品。
在每届国际HIP会议上,陶瓷材料的研究论文都占有主要的位置,下面是1999年北京HIP国际会议关于HIP技术在硬质合金和陶瓷材料中的应用情况介绍。
1硬质合金HIP技术在硬质合金中的应用始于70年代初。
硬质合金经HIP处理后,其抗弯强度与使用寿命大幅度提高,加工后制品的表面光洁度也大大提高,许多采用常规工艺难以生产的部件,在采用HIP技术后也可以顺利生产。
多年的试验研究表明,要想得到全致密的硬质合金产品,并不需要太高(一般只需要几个MPa)的压力。
80年代初开发了一种低压烧结技术, 即低压烧结HIP技术,此项新工艺把硬质合金生产中的脱蜡-烧结-HIP致密化合为一体在同一设备内完成。
由于所需压力成10倍的下降,使HIP设备的制造成本大幅度降低。
几道工序合为一体不但降低了制品的生产成本,同时由于此工艺更加合理而提高了产品的质量。
目前烧结HI技术已成为世界各硬质合金厂生产高质量硬质合金的主要手段。
近年来我国各主要硬质合金生产厂都引进了多台先进的烧结热等静压设备,本届HIP会议发表了数篇有关报道。
其中,株洲硬质合金厂采用平均粒度为08μm的WC粉、钴粉为原料及加入少量VC、Cr3C2制备了HRA≥90、抗弯强度≥3000MPa的系列产品<1>;株洲硬质合金厂还采用烧结HIP工艺生产了外285mm/内66mm×145mm的大件,其单件质量为118kg;他们对采用此工艺与采用常规真空烧结工艺制品的性能进行了比较(表1)<2>表1烧结HIP工艺及常规真空烧结工艺制品性能的比较①烧结工艺密度/gcm3硬度(HRA)抗弯强度/MPa抗压强度/ /MPa晶粒尺寸/μm烧结HIP14228923710555012真空烧结141188 92730468014①合金成分:WC+13Co(质量分数)。
硬质合金生产技术之压制和烧结

硬质合金生产技术之压制和烧结第一节压制机理一,压制过程:粉末压制成型是粉末冶金生产的基本成型方法;在压摸中填装粉末,然后在压力机下加压,脱模后得到所需形状和尺寸的压坯制品,,粗略分三阶段:1,压块密度随压力增加而迅速增大;孔隙急剧减少。
2,压块密度增加缓慢,因孔隙在1阶段中大量消除,继续加压只是让颗粒发生弹性屈服变形。
3,压力的增大可能达到粉末材料的屈服极限和强度极限,粉末颗粒在此压力下产生塑性变形或脆性断裂。
因颗粒的脆性断裂形成碎块填入孔隙,压块密度随之增大。
二,压制压力:压制压力分二部分;一是没有摩擦的条件下,使粉末压实到一定程度所需的压力为“静压力”(P1);二是克服粉末颗粒和压模之间摩擦的压力为“侧压力”(P2)。
压制压力P=P1+P2侧压系数=侧压力P2÷压制压力P=粉末的泊松系数u÷(1-u)=tg2(45o-自然坡度角Φ÷2)侧压力越大,脱模压力就越大,硬质合金粉末的泊松系数一般为0.2-0.25之间。
三,压制过程中的压力分布:引起压力分布不匀的主要原因是粉末颗粒之间以及粉末与模壁之间的摩擦力。
压块高度越高,压力分布越不均匀。
实行双向加压或增大压坯直径,能减少压力分布的不均匀性。
四,压块密度分布:越是复杂的压块,密度分布越不均匀;除压力分布的不均匀(压力降)外,装粉方式不正确,使压块不同部位压缩程度不一致,也会造成压块密度不均匀。
1,填充系数:是指压块密度Y压与料粒的松装密度Y松的比值;压缩比:是指粉末料粒填装高度h粉与压块高度h压之比;在数值上填充系数和压缩比是相等的。
K=Y压÷Y松=h粉÷h压2,为了减少压块密度分布的不均匀性:(1)提高模具的表面光洁度;(2)减少摩擦阻力;(3)提高料粒的流动性;(4)采用合理的压制方式;3,粉末粒度对压制的影响;(1)粉末分散度越大(松装越小),压力越大。
压块密度越小;有较大的强度值,成型性好。
热等静压技术
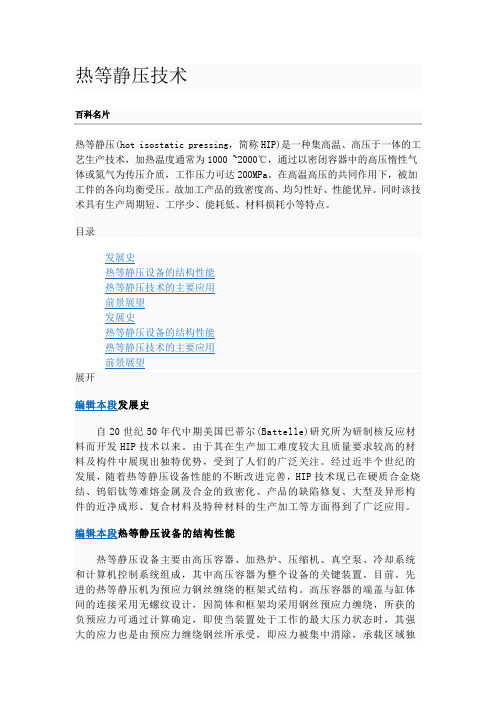
热等静压技术百科名片热等静压(hot isostatic pressing,简称HIP)是一种集高温、高压于一体的工艺生产技术,加热温度通常为1000 ~2000℃,通过以密闭容器中的高压惰性气体或氮气为传压介质,工作压力可达200MPa。
在高温高压的共同作用下,被加工件的各向均衡受压。
故加工产品的致密度高、均匀性好、性能优异。
同时该技术具有生产周期短、工序少、能耗低、材料损耗小等特点。
目录发展史热等静压设备的结构性能热等静压技术的主要应用前景展望发展史热等静压设备的结构性能热等静压技术的主要应用前景展望展开编辑本段发展史自20世纪50年代中期美国巴蒂尔(Battelle)研究所为研制核反应材料而开发HIP技术以来。
由于其在生产加工难度较大且质量要求较高的材料及构件中展现出独特优势,受到了人们的广泛关注。
经过近半个世纪的发展,随着热等静压设备性能的不断改进完善,HIP技术现已在硬质合金烧结、钨铝钛等难熔金属及合金的致密化、产品的缺陷修复、大型及异形构件的近净成形、复合材料及特种材料的生产加工等方面得到了广泛应用。
编辑本段热等静压设备的结构性能热等静压设备主要由高压容器、加热炉、压缩机、真空泵、冷却系统和计算机控制系统组成,其中高压容器为整个设备的关键装置。
目前。
先进的热等静压机为预应力钢丝缠绕的框架式结构。
高压容器的端盖与缸体间的连接采用无螺纹设计,因简体和框架均采用钢丝预应力缠绕,所获的负预应力可通过计算确定,即使当装置处于工作的最大压力状态时,其强大的应力也是由预应力缠绕钢丝所承受,即应力被集中消除,承载区域独立安全。
同时钢丝缠绕还起到防爆和屏障的作用。
因此,这种结构的热等静压机在高温高压(2000摄氏度200MPa)的工作条件下,无需外加任何特殊的防护装置,与老式的螺纹连接结构(端盖与缸体间)的热等静压机相比,不但设备的结构紧凑,而且有效地保证了生产的安全性。
加热炉负责提供热等静压所必需的热量,通常为电阻式加热炉,可视不同温度档的要求,采用不同的电阻材料,如最高工作温度为1450℃条件时可用钼丝加热炉,为2000%条件时可用石墨加热炉。
硬质合金真空烧结

硬质合金真空烧结硬质合金的烧结为液相烧结,即再黏结相呈液相的条件下进行。
将压坯在真空炉中加热到1350℃—1600℃。
烧结时压坯的线收缩率约为18%,体积收缩在50%左右,收缩量的准确值取决于粉末的粒度和合金的成分。
硬质合金的烧结是一个复杂的物理化学过程,株洲三鑫硬质合金生产有限公司友情出品。
这一过程包括增塑剂脱除、脱气、固相烧结、液相烧结、合金化、致密化、溶解析出等过程。
压坯在特定烧结条件下形成具有一定化学成分、组织结构、性能和形状尺寸的制品。
这些工艺条件依不同的烧结装置具有较大的差异。
硬质合金真空烧结是在低于1atm(1atm=101325Pa)下进行烧结的工艺过程。
在真空条件下烧结,大大降低了粉末表面吸附气体和封闭孔隙内气体对致密化的阻碍作用,有利于扩散过程和致密化的进行,避免了烧结过程中金属与气氛中某些元素的反应,可显著改善液体黏结相与硬质相的湿润性,但真空烧结要注意防止钴的蒸发损失。
真空烧结一般可以分为四个阶段,即增塑剂脱除阶段、预烧阶段、高温烧结阶段、冷却阶段。
增塑剂脱除阶段是从室温开始升温到200℃左右,压坯中粉末颗粒表面吸附的气体在热的作用下脱离颗粒表面,不断从压坯中逃逸出来。
压坯中的增塑剂受热化逸出压坯。
保持较高的真空度有利于气体的解除和逸出。
不同种类增塑剂受热变化的性能不尽相同,制定增塑剂脱除工艺要根据具体情况进行试验确定。
一般增塑剂的气化温度在550℃以下。
预烧阶段是指高温烧结前进行预烧结,使粉末颗粒中的化合氧与碳发生还原反应,生成一氧化碳气体离开压坯,如果这种气体在液相出现时不能排除,将成为封闭孔隙残留在合金中,即使加压烧结,也难以消除。
另一方面,氧化存在会严重影响液相对硬质相的湿润性,最终影响硬质合金的致密化过程。
在液相出现前,应充分得脱气,并采用尽可能高得真空度。
高温烧结阶段是硬质合金压坯发生致密化得关键阶段,而烧结温度及烧结时间是压坯实现致密化、形成均匀得组织结构、获得所要求性能的重要工艺参数。
低压烧结
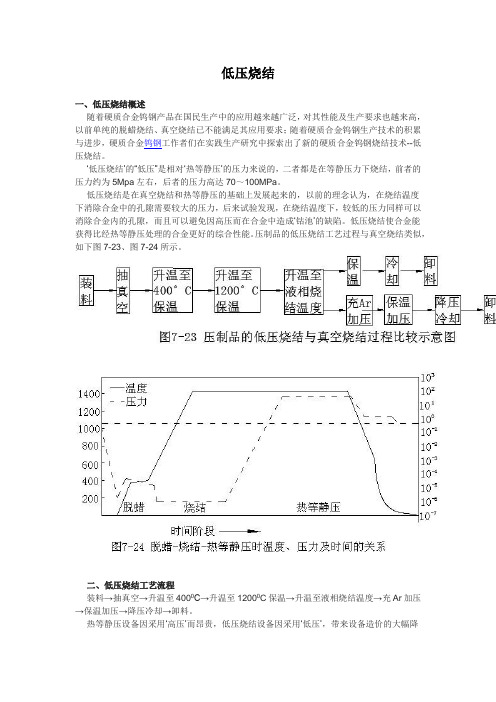
低压烧结一、低压烧结概述随着硬质合金钨钢产品在国民生产中的应用越来越广泛,对其性能及生产要求也越来高,以前单纯的脱蜡烧结、真空烧结已不能满足其应用要求;随着硬质合金钨钢生产技术的积累与进步,硬质合金钨钢工作者们在实践生产研究中探索出了新的硬质合金钨钢烧结技术--低压烧结。
…低压烧结‟的“低压”是相对…热等静压‟的压力来说的,二者都是在等静压力下烧结,前者的压力约为5Mpa左右,后者的压力高达70~100MPa。
低压烧结是在真空烧结和热等静压的基础上发展起来的,以前的理念认为,在烧结温度下消除合金中的孔隙需要较大的压力,后来试验发现,在烧结温度下,较低的压力同样可以消除合金内的孔隙,而且可以避免因高压而在合金中造成…钴池‟的缺陷。
低压烧结使合金能获得比经热等静压处理的合金更好的综合性能。
压制品的低压烧结工艺过程与真空烧结类似,如下图7-23、图7-24所示。
二、低压烧结工艺流程装料→抽真空→升温至4000C→升温至12000C保温→升温至液相烧结温度→充Ar加压→保温加压→降压冷却→卸料。
热等静压设备因采用…高压‟而昂贵,低压烧结设备因采用…低压‟,带来设备造价的大幅降低,使低压烧结炉能很快普及,现已成为生产高、中档硬质合金的常规生产设备。
热等静压烧结与低压烧结的比较热等静压设备因采用…高压‟而昂贵,低压烧结设备因采用…低压‟,带来设备造价的大幅降低,使低压烧结炉能很快普及,现已成为生产高、中档硬质合金的常规生产设备。
三、低压烧结的作用现代低压烧结炉兼容了脱蜡、真空烧结、低压烧结、低压处理、气氛烧结等多项功能。
目前主要用于:压制品的低压烧结;烧结产品的低压处理;压制品的调碳烧结。
低压烧结的主要功能是减少硬质合金中的显微孔隙。
烧结体内的孔隙在真空烧结阶段已经消除。
加压阶段主要是消除显微孔隙。
低孔隙是高质量硬质合金的重要标志,在生产中尽量降低硬质合金中的孔隙,是硬质合金工作者的主要追求之一。
硬质合金致密化与毛细管力、液相对固相的湿润性和液体的表面张力都有着息息相关的关联,在烧结过程中随着温度升高,当出现液相时,由于毛细管压力,使液相向WC表面移动,由于液相对WC相有很好的湿润性,使液相很好的附在WC表面,由于液相的表面张力,驱使被液相包裹的WC移动,强烈的收缩就此发生。
硬质合金烧结方法的新进展

硬质合金烧结方法的新进展1前言烧结是硬质合金生产过程的最后一道工序,也是最基本、最关键的一道工序,烧结前工序中的某些缺陷在一定范围内可以通过调整烧结工艺加以纠正,而由烧结造成的废品一般无法通过以后的工序来挽救,因此烧结工艺和装备选择是否恰当,对烧结产品的质量有着决定性的影响。
长久以来,在实际生产中逐渐形成了多种烧结方法,较为传统的包括氢气烧结、真空烧结、热等静压烧结、真空后续热等静压、烧结热等静压等。
80年代纳米结构问世之后,又逐渐形成了新型烧结方法,如微波烧结、放电等离子烧结等。
下面就这几种烧结技术特别是纳米硬质合金烧结技术做一综合介绍。
2氢气烧结将压坯装在石墨舟中,再充填一定含碳量的氧化铝填料或石墨颗粒填料,通常是装入连续推进式的钼丝炉内,在氢气保护下进行烧结,这个过程就是氢气烧结<1 > 。
氢气烧结的特点是:能够提供还原性气氛;需要预烧结来清除压制时添加的成形剂。
氢气烧结虽然曾在较长时期内被广泛采用,甚至目前还有少数厂家采用它,但经过长期实践,人们发现它存在许多不足。
钼丝刚玉管炉的优点是结构简单、炉子功率小、炉管寿命长,但是炉温控制不准、炉内气氛变化大、产品容易渗碳、脱碳。
另外,其烧结过程是在正压下进行的,产品内部的孔隙不能充分得到消除,留有残余孔隙,一些氧化物杂质也不能较好地挥发排除掉<2 > 。
3真空烧结硬质合金的真空烧结始于上世纪三十年代,而到六十年代才获得较大的发展。
所谓真空烧结,就是在负压的气(汽)体介质中烧结压制的过程。
真空烧结与氢气烧结相比,可以提高炉气纯度,同时负压改善了粘结相对硬质相的润湿性。
真空烧结具有如下优点:(1 )能够更好地排除烧结体中Si、Mg、Ca等微量氧化物杂质,从而提高硬质合金的纯度;(2 )真空下气相的渗碳、脱碳作用大大减少,易于保证最终合金的碳含量,控制合金的组织结构;(3)可以降低烧结温度或保温时间,防止碳化物晶粒的不均匀长大;(4)烧结品残留孔隙比氢气烧结少,可提高合金的密度和机械性能;(5 )烧结时产品不用填料隔开和保护,操作简单,而且产品表面无粘附物和白亮的金属铝沉积物。
硬质合金低压烧结工艺的探索

硬质合金低压烧结工艺的探索背景介绍硬质合金是一种具有优异性能的材料,广泛应用于切削工具、磨料工具、钻头等领域。
然而,传统的硬质合金烧结工艺存在一些问题,如高温烧结过程中易产生裂纹、粉末不易压实等。
为了解决这些问题,近年来,低压烧结工艺被引入硬质合金的生产中,取得了良好的效果。
本文将对硬质合金低压烧结工艺进行探索。
低压烧结工艺的原理低压烧结工艺是在传统的高温烧结工艺基础上进行的改进。
该工艺是在相对较低的温度和压力下进行的,能够有效降低硬质合金烧结过程中的应力,减少裂纹的产生。
具体工艺流程如下:1.硬质合金粉末的制备:首先,根据所需的产品要求,将合适的金属粉末混合,并加入适量的粘结剂和稳定剂,经过混合、湿法粉碎、干燥等工序得到合适的硬质合金粉末。
2.模具填充与压实:将制备好的硬质合金粉末填充至模具中,然后施加一定的压力进行初步压实。
这一步骤旨在保证硬质合金粉末的均匀分布和初步的固结。
3.低压烧结过程:将填充好硬质合金粉末的模具放入低压烧结炉中,根据设计要求,控制合适的温度和压力进行烧结过程。
相对于传统高温烧结工艺,低压烧结的温度和压力要求更低,从而减少了产生裂纹的可能性。
4.冷却与脱模:低压烧结过程结束后,将烧结好的硬质合金模具从炉中取出,进行冷却。
待冷却后,使用合适的方法将硬质合金产品从模具中取出,完成脱模操作。
优势与挑战低压烧结工艺相比传统高温烧结工艺具有以下优势:1.减少裂纹的产生:传统高温烧结工艺中,由于温度和压力较高,易导致硬质合金产生内应力,从而产生裂纹。
低压烧结工艺通过降低温度和压力,减小了硬质合金内应力的产生,有效减少了裂纹的发生。
2.增加硬质合金的致密度:低压烧结工艺在初步压实的基础上,通过烧结过程进一步压实硬质合金粉末,提高了硬质合金的致密度,从而提高了其力学性能和耐磨性。
3.环保节能:相对于高温烧结工艺,低压烧结工艺不需要经过高温环境,减少了能源的消耗,同时也减少了对环境的污染。
热等静压和烧结热等静压对消除硬质合金孔洞的作用

热等静压和烧结热等静压对消除硬质合金孔洞的作用
谭文生
【期刊名称】《稀有金属与硬质合金》
【年(卷),期】1989()4
【摘要】一、前言世界上第一台热等静压机(简称HIP)1955年诞生于美国巴特尔—哥伦布研究所,六十年代末这项技术得到了很大发展。
目前,世界上各大硬质合金生产厂都相继采用了热等静压技术,作为提高产品最终性能的手段。
1983年江汉钻头厂从美国AE公司引进了一台螺纹式结构热等静压机。
【总页数】4页(P14-17)
【关键词】硬质合金;孔洞;热等静压;烧结
【作者】谭文生
【作者单位】江汉钻头厂
【正文语种】中文
【中图分类】TF125
【相关文献】
1.硬质合金烧结-热等静压炉石墨筒内温度场的数值仿真与结构优化 [J], 刘余庆;时章明;陈祎;刘志强
2.硬质合金烧结-热等静压炉的优化 [J], 陈袆;罗永浩;时章明;段佳;季俊杰
3.硬质合金低压热等静压烧结工艺 [J], 印红羽;盛挺;汪海宽
4.烧结-热等静压法制取WC-Co系硬质合金 [J], 贾佐诚;强劲熙;陈飞雄
5.现代硬质合金烧结炉——西德Degussa公司VKPgr真空烧结热等静压炉 [J], 姜回龙
因版权原因,仅展示原文概要,查看原文内容请购买。
硬质合金制备过程中的基本原理烧结工艺及应用

一般为颗粒的凹陷处和大颗粒表面。
溶解在液相中固相组分的原子在这些部位析出
精选ppt
13
液相烧结原理
结果:
ቤተ መጻሕፍቲ ባይዱ
固相颗粒表面光滑化和球化
降低颗粒重排列阻力
有利于颗粒间的重排
进一步提高致密化效果
精选ppt
14
液相烧结原理
小颗粒的溶解速度遵循公式: dr / dt=2DCγLVΩ(r-R)/(kTr2R)
PS:完成球磨过程的混合料经320目过筛网筛后,一般要沉淀8h,以便酒精充分挥发,然后进
行干燥。
将干燥后的混合料用180目网筛进行筛分,其目的是除去浆料干燥时产生的氧化结块料,
并使混合料拓散,易于散热。
精选ppt
32
压制成形
模压成形工艺过程:掺胶→筛分→制粒→压制→加工和清理
成形剂的制备
1、溶剂:航空汽油或溶剂汽油。
精选ppt
25
液相烧结原理
粉末颗粒内开孔隙
降低颗粒重排的液相数量: 减小固相颗粒之间的液膜厚度
增加固相颗粒之间的接触机会
增加颗粒重排阻力
精选ppt
26
液相烧结原理
除此之外,添加剂的分布均匀性、添加剂的数量(直接影响液相数量)、 压坯密度、加热与冷却速度、杂质、温度、时间、气氛都将会影响液相烧 结效果。
17
液相烧结原理
溶解-再析出机构
小颗粒或表面曲率大的部位溶解较多,在大颗粒表面或具有负表面曲率的 部位析出。 具有表面曲率r的颗粒它的平衡溶解度与平面(r为无穷大)上的平衡浓度只 差遵循公式:
△L=Lr-L∞=2γSLδ³/kT×1/r×L∞ △L和r成反比,小颗粒先于大颗粒溶解。 溶解-再析出机构使得颗粒外形趋于球形,小颗粒减小或消失,大颗粒逐渐 长大。
硬质合金制备过程中的基本原理、烧结工艺及应用培训
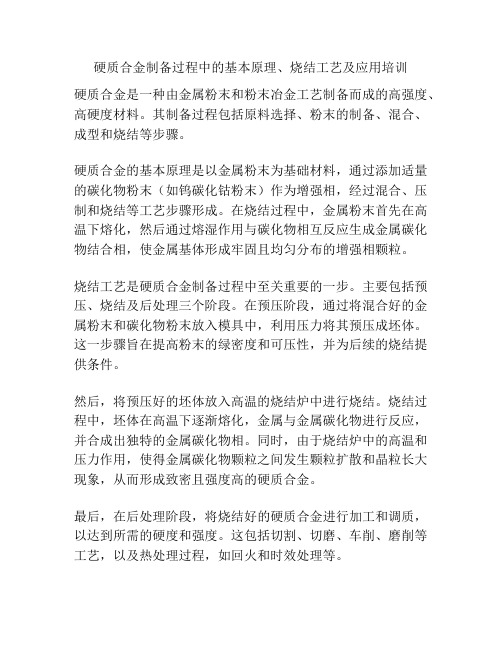
硬质合金制备过程中的基本原理、烧结工艺及应用培训硬质合金是一种由金属粉末和粉末冶金工艺制备而成的高强度、高硬度材料。
其制备过程包括原料选择、粉末的制备、混合、成型和烧结等步骤。
硬质合金的基本原理是以金属粉末为基础材料,通过添加适量的碳化物粉末(如钨碳化钴粉末)作为增强相,经过混合、压制和烧结等工艺步骤形成。
在烧结过程中,金属粉末首先在高温下熔化,然后通过熔湿作用与碳化物相互反应生成金属碳化物结合相,使金属基体形成牢固且均匀分布的增强相颗粒。
烧结工艺是硬质合金制备过程中至关重要的一步。
主要包括预压、烧结及后处理三个阶段。
在预压阶段,通过将混合好的金属粉末和碳化物粉末放入模具中,利用压力将其预压成坯体。
这一步骤旨在提高粉末的绿密度和可压性,并为后续的烧结提供条件。
然后,将预压好的坯体放入高温的烧结炉中进行烧结。
烧结过程中,坯体在高温下逐渐熔化,金属与金属碳化物进行反应,并合成出独特的金属碳化物相。
同时,由于烧结炉中的高温和压力作用,使得金属碳化物颗粒之间发生颗粒扩散和晶粒长大现象,从而形成致密且强度高的硬质合金。
最后,在后处理阶段,将烧结好的硬质合金进行加工和调质,以达到所需的硬度和强度。
这包括切割、切磨、车削、磨削等工艺,以及热处理过程,如回火和时效处理等。
硬质合金的应用非常广泛,常见的应用包括切削工具、矿业工具、电子元件等领域。
由于硬质合金具有极高的硬度、耐磨性和耐腐蚀性,因此在切削加工领域被广泛应用于车削、钻孔、铣削和切割等工艺中。
同时,在矿业工具领域,硬质合金可以用作凿岩钻头、矿山钻头等,因为它的耐磨性和强度能够满足严苛的工况要求。
在电子元件领域,由于硬质合金具有优异的导热性和耐腐蚀性能,因此常用于制造散热器、金属工具接触点等。
总之,硬质合金的制备是一个复杂的过程,包括原料选择、混合、成型和烧结等多个步骤。
通过控制工艺参数和多次迭代优化,可以获得具有优异性能的硬质合金材料,满足不同领域的应用需求。
硬质合金的烧结
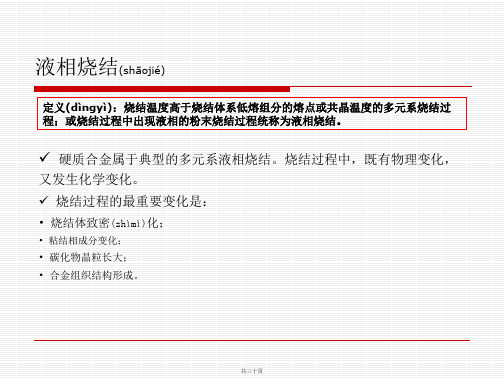
硬质合金致密(zhìmì)化的影响因 素
✓ 液-固相间的润湿角,液体的毛细管力随其对碳化物颗粒的润湿角减小而
提高。
✓ 液相数量不超过50%时,毛细管力随液相数量的增加而提高。相比较,碳化物
颗粒的流动阻力(zǔlì)随其增加而降低。 ✓ 影响液相出现的温度和数量的烧结体含碳量。含碳量较高的烧结体,液相出 现的温度较低。
✓ 固定产品及保护压坯不被碰坏;
✓ 保护底层产品在出现液相对不致受上层产品的重量而变形; ✓ 低温下作为碳氢化合物气体分解的接触剂而吸收碳,保护产品不过分增
碳;高温时,碳又与氢气及水蒸汽作用保护产品不过分脱碳。
共三十页
硬质合金(yìnɡ zhì hé jīn)的致密化过程
1. WC-10.5%Co; 2. WC- 6%Co
✓ 液相烧结阶段(共晶温度~烧结温度):出现液相后,烧结体收缩很快完成,碳
化物晶粒长大并形成骨架及合金的基本组织结构。
✓ 冷却阶段(烧结温度~室温):合金的组织和黏结相成分随冷却条件的不同而产生某些变
化。冷却后,得到最终组织结构的合金。
共三十页
WC-Co合金的平衡烧结过程
当混合料纯度极高且达到理想的均匀(jūnyún)程度且烧结时升温极其缓慢,则认为烧结体处于平衡 烧结状态。
✓ 固相颗粒的表面状态。固相颗粒的粗糙度增加,提高固-气界面 能。液固润湿过程易于进行;
✓ 烧结气氛:液相或固相氧化膜的形成导致润湿性下降。
共三十页
溶解(róngjiě)-再析出阶 段
✓ 固相在液相中具有(jùyǒu)一定溶解度的体系;
✓ 化学位差异,化学位高的部位将发生优先溶解并在附近的液相中形成浓度梯度;
共三十页
烧结(shāojié)的微观过 程
- 1、下载文档前请自行甄别文档内容的完整性,平台不提供额外的编辑、内容补充、找答案等附加服务。
- 2、"仅部分预览"的文档,不可在线预览部分如存在完整性等问题,可反馈申请退款(可完整预览的文档不适用该条件!)。
- 3、如文档侵犯您的权益,请联系客服反馈,我们会尽快为您处理(人工客服工作时间:9:00-18:30)。
硬质合金低压热等静压烧结工艺
硬质合金低压热等静压烧结工艺印红羽盛挺汪海宽(北京市粉末冶金研究所,100078)摘要低压热等静压烧结工艺技术能最大限度地消除合金内部残余孔隙、细化晶粒,克服常规热等静压给合金造成的粗晶、钴池和表面成分改变的缺陷,显著提高硬质合金物理-力学性能,并能有效校正合金碳含量。
主题词硬质合金低压热等静压烧结组织性能1前言低压热等静压烧结(Sinter-HIP)工艺[1~3],或称过压烧结(OverPresureSin-tering)工艺,是在低于常规热等静压的压力(大约6MPa)下对工件同时进行热等静压和烧结的工艺。
自1984年德国Degusa公司设计和制造出第一台真空烧结热等静压炉以来,这一工艺已逐渐为世界上很多硬质合金厂家所采用,并已开始步入我国硬质合金生产领域。
低压热等静压烧结工艺目前是硬质合金生产中最先进的致密化技术,克服了常规热等静压造成的粗晶、钴池和表面成分改变的缺陷,能最大限度地消除内部残余孔隙,提高合金性能,并且能够通过调节炉内气氛,修正合金碳含量、消除合金组织中的η相。
2硬质合金低压热等静压烧结的典型工艺硬质合金的低压热等静压烧结工艺是将工件装入真空烧结等静压炉,于较低温度下低压载气(如氢气等)脱蜡后,在1350~1450℃进行真空烧结30min,接着在同一炉内进行热等静压,采用氩气作压力介质,压制压力为6MPa左右,时间为30min[4~5]。
其典型的生产工艺见图1。
低压热等静压烧结工艺的排蜡、烧结和在压力下的致密化等生产过程在同一炉内一次完成[6],免去了传统工艺所必需的两次或多次的装料及加热生产工序,降低了热等静压时的压力(由多100MPa降至6MPa),既简化了操作程序,又节省了能耗。
同时,由于生产过程中的烧结、热等静压两个主要工序不再分步进行,避免了工件在生产中途与空气的接触而造成的难以控制的碳含量变化。
低压热等静压炉内的特定装置在每道工序后能及时排除所产生的水蒸汽、CO2和其它气体,不会在下一过程引起工件某些部分表面成分和碳含量的变化。
3低压热等静压工艺对合金性能的影响对含不同种类和不同量的粘结剂(Co或Ni)、以及添加Ta、Ti等元素的各种硬质合金曲线A为温度-时间曲线;曲线B为压力-时间曲线。
图1载气(氢气)脱蜡低压热等静压烧结典型生产工艺系列,分别进行了低压热等静压烧结(SH)、真空烧结(NS)和真空烧结后再热等静压(SH)的试验,其试验结果见表1和表2。
这些数据证明,与传统的真空烧结工艺以及真空烧结后再进行热等静压的工艺相比,低压热等静压烧结工艺能使硬质合金的强度以及矫顽磁力等各项性能都有不同程度的提高,显示了低压热等静压烧结工艺的优越性。
表1低压热等静压烧结工艺和传统工艺对不同牌号硬质合金性能的影响[4]牌号工艺密度抗弯强度硬度矫顽磁力g/cm3×103MPaHRA×103A/mP30NS12.701.6591.516.16NS+HIP12.701.9891.114.24SH12.771.9891.916.80K-05NS14.411.5892.528.96NS+HIP14.421.9092.627.20SH14.461.9894.227.20K-10NS14.561.6091.619.04NS+HIP14.572.2091.217.76SH14.612.2092.219.60K-20NS14.912.4590.716.80NS+HIP14.913.1890.415.04SH14.953.0090.817.60注:1.烧结温度1460℃,压力5MPa,低压热等静压烧结时间30min。
2.NS:常规真空烧结;NS+HIP:常规真空烧结后进行热等静压;SH:低压热等静压烧结。
3.P30含TiC、TaC;K-05、K-10和K-20含TaC。
表2低压热等静压烧结工艺和传统工艺对不同颗粒尺寸WC的硬质合金性能的影响[5]Co含量WC颗粒低压热等静压烧结+热等静压真空烧结%尺寸分等密度g/cm3硬度HRA抗弯强度MPa密度g/cm3硬度HRA抗弯强度MPa密度g/cm3硬度HRA抗弯强度MPa4中15.292.7396015.292.6340015.292.225007中14.990.6
327514.990.6313014.990.8274010中14.690.2351014.690.2337014.589.9275016中14.088.0350014.087.8343014.087.9346010细14.593.0378514.593.0371014.593.0165016细13.991.6439013.991.5423013.990.038258*中14.890.8334014.890.5285014.790.51920注:*为Ni作粘结剂;“中”为中颗粒;“细”为细颗粒。
我国学者在实际生产中对大尺寸硬质合金顶锤进行了上述三种工艺试验,其结果见表3。
由抗弯强度值可以明显看出低压热等静压烧结工艺的有效作用,加之低压热等静压烧结炉的造价远低于热等静压设备[8],因此在生产中有很高的推广应用价值。
4低压热等静压对合金组织的影响低压热等静压烧结工艺能有效改善合金的性能,主要原因之一是这种工艺能在硬质合金烧结温度之下直接对工件施加压力,可表3不同烧结工艺对大尺寸硬质合金顶锤性能的影响[7]烧结工艺种类工艺参数密度g/cm3抗弯强度MPa硬度HRA孔隙度真空烧结1400℃2h14.702000~240089.3A04低压热等静压烧结1400℃真空1h1400℃+6MPa1h14.732800~310089.5<A02真空烧结后再进行热等静压1400℃真空,2h出炉100MPa,1380℃1h14.712700~305089.5<A02表4加压压力对合金性能的影响[7]合金牌号烧结温度℃加压压力MPa抗弯强度MPa硬度HRA孔隙度YG81400(30min)4(30min)300289.3<A025(30min)301589.2<A02YG101390(30min)4(30min)308088.1<A025(30min)312087.9<A02YG151370(30min)4(30min)317087.2<A025(30min)321087.4<A02a.真空烧结;b.低压热等静压烧结。
(未侵蚀,低倍照片)图2WC-2%Co合金在不同工艺下的孔隙分布[9]以在很低的压力之下闭合合金内部的孔隙,从而有效地消除孔隙。
表4为加压压力对合金性能和孔隙度的影响。
由表中数据可知,在所论范围内,压力大小对合金孔隙度影响不太大。
在烧结温度下,即使对合金施加很小的压力,也可通过压力介质均衡地传递到合金的各个方向上,加之液相的存在,使WC颗粒能有效地通过液相的流动进行颗粒重排,填充孔隙。
图2为含钴2%的WC-Co硬质合金未腐蚀抛光表面的孔隙分布,可见常规真空烧结工艺与低压热等静压烧结工艺在合金孔隙度上所造成的差异是非常明显的。
常规真空烧结后再热等静压的工艺温度高、压力大(80~100MPa)、时间长。
在进行热等静压时会产生又一次的WC聚晶过程,容易使一些粗大的烧结WC晶粒更为粗化,引起合金中WC晶粒的不均匀长大。
低压热等静压则避免了这种倾向(见图3)。
此外,常规烧结后热等静压的工艺,容易使钴池增多,造成合金内粘结相分布不均匀而影响合金的性能。
如果保温时间长,钴池中的粘结相还可能流出而形成孔隙[9],图4a中呈黑色的孔隙即属于这种情况。
低压热等静压烧结工艺则能有效地防止这种情况的产生(见图4b)。
5利用低压热等静压工艺校正合金碳含量由于低压热等静压烧结工艺的专用烧结图3不同工艺对硬质合金组织的影响[10]图4含6%Co硬质合金中Co的流失[11]表5低压热等静压烧结对钨钴硬质合金的碳校正[12]工艺批号47596061656871真空烧结金相组织η相η相η相η相η相正常η相磁饱和值Ms115129128127126136120(×10-4T-cm3/g)低压热等静压金相组织正常正常正常正常正常正常正常校正碳含量磁饱和值Ms138151147153147150153(×10-4T-cm3/g)设备是载气脱蜡,因此还可以对WC+Co硬质合金中的碳含量进行校正[11]。
成形后的硬质合金压坯发生缺碳或碳过量时,可以采用低压热等静压工艺及设备,在制品中尚未产生液相、而其内部的成形剂已脱净的某一高温下,通入一定压力、一定组成比例的CH4/H2气体,使合金内部的η相或游离石墨得以消除,成为正常的WC+两相合金。
该气体进入工件内部尚未封闭的连通孔,对缺碳产品产生增碳反应:W+CH4—→WC+2H2↑
对碳过量的合金产生脱碳反应:C+2H2—→CH4↑生产中混合料存放时间过长而导致氧含量过高时,若采用常规真空烧结,则会在制品内产生明显的η相,严重时即使采用含碳量较多的填料在氢气烧结炉中返烧也无济于事。
通过低压热等静压烧结工艺及设备,一次碳校正烧结便可获得正常的两相组织。
表5所列的数据即为实际生产中的几批不同程度氧化的混合料,经过常规真空烧结和经低压热等静压碳校正烧结后的制品的金相组织和磁饱和值(Ms)。
这些结果表明了低压热等静压烧结工艺在校正碳含量方面的有效作用。
6结语低压热等静压烧结工艺简化操作程序,节省能耗,在硬质合金生产中,既能达到真空烧结后进行热等静压工艺所取得的良好效果,还能克服常规热等静压处理后易于出现的“钴池”,“粗晶”等组织缺陷。
与真空烧结工艺相比,可以减少合金内部孔隙,对其强度、硬度等性能指标有不同程度的提高。
因此,低压热等静压烧结工艺有极大的推广应用价值。
7参考文献1WorldFirstforPferfer'sPressureSinteringFurnac。