铝硅合金的熔炼
AlSi合金的细化
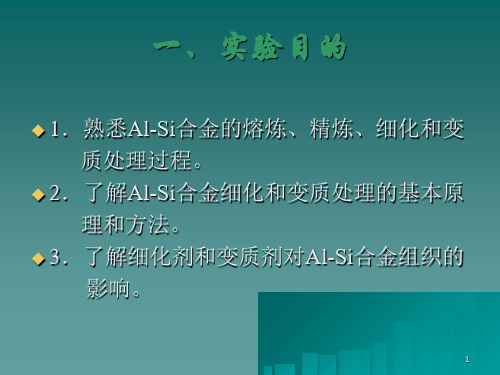
三、实验设备及材料
井式坩埚电阻炉,石墨坩埚,钟罩, Al-7Si合金,Al-5Ti-1B中间合金, Al-10Sr中间合金,C2Cl6, 金相试样预磨机和抛光机,HF,王水, 砂纸等。
9
四、实验步骤与方法
1.在经预热发红的两个石墨坩埚中分别加入 1000g的Al-7Si合金原料,升温至 720℃,熔化后 保温1h以促进成分的均匀化;所有参加实验的学 生在实验教师指导下在熔融Al-7Si合金中加入0.6 %的C2Cl6进行精炼除气。
晶粒细化剂的加入量与合金种类、化学成分、 加入方法、熔炼温度以及浇铸时间等有关。若加 入量过大,则形成的异质形核颗粒会逐渐聚集, 由于其密度比铝熔体大,因此会聚集在熔池底部, 丧失晶粒细化能力,产生细化效果衰退现象。
3
晶粒细化剂加入合金熔体后要经历孕育期和 衰退期两个时期。在孕育期内中间合金完成熔化 过程并使起细化作用的异质形核颗粒均匀分布并 与合金熔体充分润湿,逐渐达到最佳的细化效果。 此后,由于异质形核颗粒的溶解而使细化效果下 降;同时异质固相颗粒会逐渐聚集而沉积在熔池 底部,出现细化效果衰退现象。当细化效果达到 最佳值时进行浇注是最为理想的。随合金的熔炼 温度和加入的细化剂种类的不同,达到最佳细化 效果所需的时间也有所不同,通常存在一个可接 受的保温时间范围。
5.以4~6人为一组,每隔30min以组为单位浇铸 试样。应保证经细化处理和变质处理的试样分别 最少浇铸4组。
6.各组对浇铸出的试样进行切割、粗磨、细磨、 抛光、腐蚀处理,然后在光学金相显微镜下观察, 评价合金的细化和变质效果。
11
五、实验报告要求
1.简述实验目的、实验内容与实验原理和 步骤。
2.评价Al-7Si合金的细化和变质效果,并 分析影响合金细化和变质效果的主要因 素。
铝硅合金压铸常见问题分析
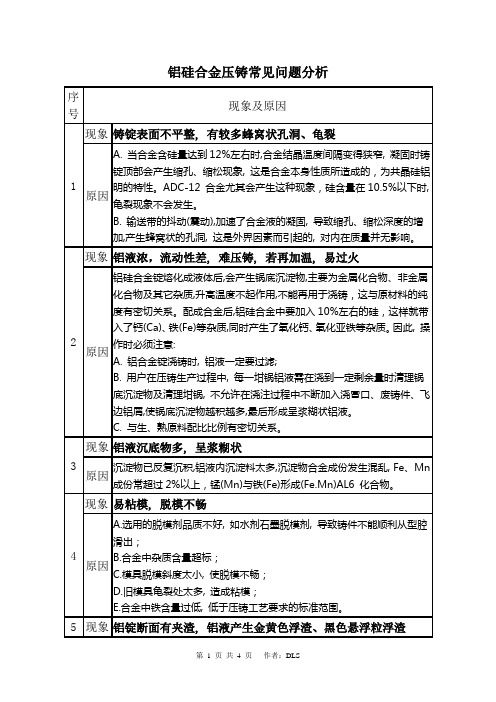
B. 用户在压铸生产过程中, 每一坩锅铝液需在浇到一定剩余量时清理锅底沉淀物及清理坩锅, 不允许在浇注过程中不断加入浇冒口、废铸件、飞边铝屑,使锅底沉淀物越积越多,最后形成呈浆糊状铝液。
C. 与生、熟原料配比比例有密切关系。
3
现象
铝液沉底物多, 呈浆糊状
原因
沉淀物已反复沉积,铝液内沉淀料太多,沉淀物合金成份发生混乱,Fe、Mn成份常超过2%以上,锰(Mn)与铁(Fe)形成(Fe.Mn)AL6 化合物。
原因
A.用户在合金精炼时除气不彻底, 模具排气溢流槽分布须合理;
B.压铸时填充速度过快。
18
现象
铸件断面有大量孔隙, 有时有大空洞,学术名称为“缩孔”
原因
A.铝合金锭熔炼温度偏高;
B.比压太低;
C.溢流槽容量太小, 溢口偏薄;
D.铸件壁厚不均匀, 有热节;
E.冒口太小;
F.压铸时铝液容量不充足。
19
C.铸造斜度放得太小;
D.顶杆位置布置不当;
E.清除浇口方法不当等。
22
现象
铸件有硬点,有时是黑色颗粒,有时是发亮晶体,精加工时打刀
原因
与沉淀物有密切联系, 解决方法参照题2、题3
23
现象
铸件喷砂处理时表面会翘皮
原因
A.铸件硬度与喷砂机拋头转速不匹配,转速太急、太猛;
B.铸件内部有气孔、缩松, 铸件体各处软硬不一致。
7
现象
铸造时, 活塞成品靠近冒口处有大量孔隙发生
原因
此乃铸造工艺、模具设计不当造成。对于活塞铸造工艺,早已形成一套完整的设计(JINGREN 法), 即鹅颈式浇口系统。根据活塞直径大小、壁厚, 按一侧或两侧,设单个或两个冒口(侧冒口)。有的生产厂家为节约铝液,只设计小浇口及小冒口, 从而形成冒口过小, 补缩不良, 产生孔隙。
铝合金的熔炼规范
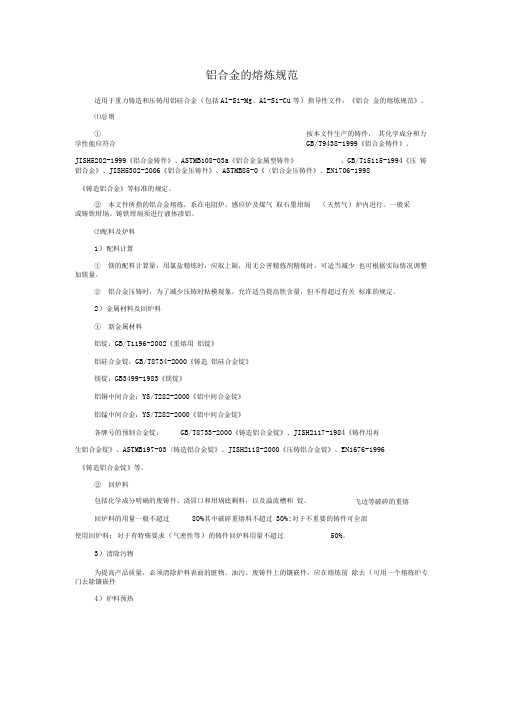
铝合金的熔炼规范适用于重力铸造和压铸用铝硅合金(包括Al-Si-Mg 、Al-Si-Cu 等)指导性文件:《铝合 金的熔炼规范》。
⑴总则 ①按本文件生产的铸件, 其化学成分和力学性能应符合GB/T9438-1999《铝合金铸件》、JISH5202-1999《铝合金铸件》、ASTMB108-03a 《铝合金金属型铸件》 、GB/T15115-1994《压 铸铝合金》、JISH5302-2006《铝合金压铸件》、ASTMB85-0《〈铝合金压铸件》、EN1706-1998《铸造铝合金》等标准的规定。
② 本文件所指的铝合金熔炼,系在电阻炉、感应炉及煤气 取石墨坩埚或铸铁坩埚。
铸铁坩埚须进行液体渗铝。
⑵配料及炉料1)配料计算① 镁的配料计算量:用氯盐精炼时,应取上限,用无公害精炼剂精炼时,可适当减少 也可根据实际情况调整加镁量。
② 铝合金压铸时,为了减少压铸时粘模现象,允许适当提高铁含量,但不得超过有关 标准的规定。
2)金属材料及回炉料① 新金属材料铝锭:GB/T1196-2002《重熔用 铝锭》铝硅合金锭:GB/T8734-2000《铸造 铝硅合金锭》 镁锭:GB3499-1983《镁锭》铝铜中间合金:YS/T282-2000《铝中间合金锭》 铝锰中间合金:YS/T282-2000《铝中间合金锭》 各牌号的预制合金锭:GB/T8733-2000《铸造铝合金锭》、JISH2117-1984《铸件用再生铝合金锭》、ASTMB197-03〈铸造铝合金锭》、JISH2118-2000《压铸铝合金锭》、EN1676-1996 《铸造铝合金锭》等。
② 回炉料包括化学成分明确的废铸件、浇冒口和坩埚底剩料,以及溢流槽和 锭。
回炉料的用量一般不超过80%其中破碎重熔料不超过 30%;对于不重要的铸件可全部使用回炉料;对于有特殊要求(气密性等)的铸件回炉料用量不超过50%。
3)清除污物为提高产品质量,必须清除炉料表面的脏物、油污、废铸件上的镶嵌件,应在熔炼前 除去(可用一个熔炼炉专门去除镶嵌件4)炉料预热(天然气)炉内进行。
铝合金及其熔炼

铝合金及其熔炼一、铝合金的系列:铝合金共有三个系列根据与其形成合金的元素而有些区别。
1、铝硅系:合金中硅含量在共晶点附近,合金的流动性好,铸造性能好,不易产生裂纹,致密性好,热膨胀量小,导热性好,耐腐蚀,适合压铸大型薄壁复杂铸件。
但是其机械性能不够高,切削性稍差,阳极氧化不理想。
2、铝硅铜系:合金具有最佳综合性能,应用广泛,尤其在汽摩行业。
3、铝镁系:合金的强度、塑性、耐蚀性和表面质量最佳,但收缩和膨胀量大,铸造性能差。
二、合金元素的作用:1、硅:铝与硅的共晶点在11.7%,共晶合金的凝固温度范围最小,补缩及抗热裂性最好,共晶点附近的合金都有良好的流动性,适合铸造薄壁,复杂大型的铸件。
随着含硅量的提高,强度与硬度也有所提升,但伸长力下降,切削性能变差,而合金对坩埚的熔蚀也增加。
2、铜:铜对于铝合金可提高机械性能改善切削性,但耐蚀性降低,热裂倾向增大。
3、镁:铝镁合金耐蚀性好,但由于凝固温度范围大,有热脆性故铸件易于产生裂纹,其流动性随着镁含量的提高而改善,但相应收缩也增加。
对于铝硅系合金而言,镁有强化效能,提高耐蚀性,改善电镀,阳极氧化的性能及铸件表面质量。
但对铝硅铜而言,必须控制其含量,因为镁会造成热裂,冷脆降低伸长率和冲击韧性。
4、铁:铁能缓解铝与模具的亲和力,通常控制在0.6% ~ 1%之间,过高的含铁量在铸件中产生FeAl3针状相,降低性能。
在铝硅系及铝硅铜系里过量的Fe形成金属间化合物造成脆性在切削时会影响表面粗糙度。
5、锰:适量锰能中和过量铁的不利影响,但不大于0.5%。
6、锌可提高流动性,改善机械性能,但高温脆性大,产生热裂。
7、锡:改善切削性能,降低强度和耐蚀性,有高温脆性。
8、镍:少量的镍能改善机械性能,对耐蚀性不利。
9、铅:改善切削性能,但有损耐蚀性。
10、铬:改善耐蚀性。
11、钛:细化结晶,改善性能。
三、铝合金的熔炼:铝合金的熔炼对压铸企业而言是个重要环节,一般均有熔炼及保温二种过程,一边压铸一边熔炼是不被容许的。
6班-铝硅合金的细化和变质处理实验报告

1.实验目的1)熟悉铸造铝硅合金的熔炼、精炼、细化和变质处理的过程;2)掌握铸造铝硅合金精炼、细化和编制处理的基本原理及方法;3)掌握细化剂和变质剂对铸造铝硅合金的影响。
2.实验内容1)对熔融的Al-7Si合金进行细化处理;2)对熔融的Al-7Si合金进行变质处理;3)在光学显微镜下观察,评价合金的细化和变质处理效果。
3.实验原理3.1 铝硅合金晶粒细化技术及其机理铸造铝合金铸态时通常呈现三种不同的晶粒状态:等轴晶、柱状晶和枝状晶。
有目的地一直柱状晶和枝状晶生长,促进细小等轴晶形成,这种工艺过程就叫做晶粒细化处理。
晶粒细化是通过控制晶体的形核和长大来实现的。
细化处理的最基本原理是促进形核,抑制长大。
而形核质点主要有两种来源:一是包括快速凝固法、动力学方法和成分过冷法等的内生形核质点,二是向熔体中添加晶粒细化剂的外来形核质点。
目前,添加细化剂成为生产过程中最有效、最实用的方法。
对于铝硅合金,通常将细化元素Ti、B以中间合金的形式加入熔体来实现晶粒的细化。
3.2 铝硅合金变质处理技术及其机理铝硅合金中,由于Si相在自然生长条件下会长成块状或片状的脆性相,严重的割裂基体,降低合金的强度和塑性,因而必须采用变质处理工艺,使共晶硅形貌发生变化,提高合金性能。
4.实验步骤1)在两个Al2O3坩埚中分别加入1000g的铝硅合金原料,在电阻炉中升温至720℃,溶化后保温1小时以促进成分的均匀化;2)对精炼处理后的Al-7Si合金教主一组试样;3)向一个坩埚中加入0.03%的B进行晶粒细化处理;4)向另一个坩埚中加入0.03%的Sr进行变质处理;5)1-2人为一组,每个20-30分钟以组为单位浇注试样,为充分观察细化和变质处理的孕育期和衰退期,应至少浇注4组试样;6)对各组试样进行处理,在光学显微镜下观察,评价合金的变质效果,观察晶粒尺寸。
5.实验结果分析5.1 晶粒细化效果分析将实验分成三个实验组,第1组为未加细化剂处理的原料铸型,第2组为加入细化剂处理20min后的原料铸型,第3组为加入细化剂处理40min后的原料铸型。
铝合金熔炼规范

铝合金熔炼规范文稿归稿存档编号:[KKUY-KKIO69-OTM243-OLUI129-G00I-FDQS58-铝合金的熔炼规范适用于重力和压铸用铝硅(包括Al-Si-Mg、Al-Si-Cu等)指导性文件:《铝的熔炼规范》。
(1)总则①按本文件生产的铸件,其化学成分和力学性能应符合GB/T 9438-1999《铝铸件》、JISH 5202-1999《铝铸件》、ASTM B 108-03a《铝金属型铸件》、GB/T 15115-1994《压铸铝》、JISH 5302-2006《铝》、ASTM B 85-03《铝》、EN1706-1998《铝》等标准的规定。
②本文件所指的铝熔炼,系在电阻炉、感应炉及煤气(天然气)炉内进行。
一般采取石墨或铸铁。
铸铁须进行液体渗铝。
(2)配料及炉料1)配料计算①镁的配料计算量:用氯盐精炼时,应取上限,用无公害精炼剂精炼时,可适当减少;也可根据实际情况调整加镁量。
②铝压铸时,为了减少压铸时粘模现象,允许适当提高铁含量,但不得超过有关标准的规定。
2)金属及回炉料①新金属铝锭:GB/T 1196-2002《重熔用铝锭》铝硅锭:GB/T 8734-2000《铝硅锭》镁锭: GB 3499-1983《镁锭》铝铜中间:YS/T 282-2000《铝中间锭》铝锰中间:YS/T 282-2000《铝中间锭》各牌号的预制锭:GB/T 8733-2000《铝锭》、JISH 2117-1984《铸件用再生铝锭》、ASTM B 197-03《铝锭》、JISH 2118-2000《压铸铝锭》、EN1676-1996《铝锭》等。
②回炉料包括化学成分明确的废铸件、浇冒口和底剩料,以及溢流槽和飞边等破碎的重熔锭。
回炉料的用量一般不超过80%,其中破碎重熔料不超过30%;对于不重要的铸件可全部使用回炉料;对于有特殊要求(气密性等)的铸件回炉料用量不超过50% 。
3)清除污物为提高产品质量,必须清除炉料表面的脏物、油污、废铸件上的镶嵌件,应在熔炼前除去(可用一个熔炼炉专门去除镶嵌件)。
铝合金熔炼工艺流程和操作工艺

铝合金熔炼工艺流程和操作工艺(一)装料熔炼时,装入炉料的顺序和方法不仅关系到熔炼的时间、金属的烧损、热能消耗,还会影响到金属熔体的质量和炉子的使用寿命。
装料的原那么有:1、装炉料顺序应合理。
正确的装料要根据所参加炉料性质与状态而定,而且还应考虑到最快的熔化速度,最少的烧损以及准确的化学成分控制。
装料时,先装小块或薄片废料,铝锭和大块料装在中间,最后装中间合金。
熔点易氧化的中间合金装在中下层。
所装入的炉料应当在熔池中均匀分布,防止偏重。
小块或薄板料装在熔池下层,这样可减少烧损,同时还可以保护炉体免受大块料的直接冲击而损坏。
中间合金有的熔点高,如AL-NI和AL-MN合金的熔点为750-800℃,装在上层,由于炉内上部温度高容易熔化,也有充分的时间扩散;使中间合金分布均匀,那么有利于熔体的成分控制。
炉料装平,各处熔化速度相差不多这样可以防止偏重时造成的局部金属过热。
炉料应进量一次入炉,二次或屡次加料会增加非金属夹杂物及含气量。
2、对于质量要求高的产品〔包括锻件、模锻件、空心大梁和大梁型材等〕的炉料除上述的装料要求外,在装料前必须向熔池内撒20-30kg粉状熔剂,在装炉过程中对炉料要分层撒粉状熔剂,这样可提高炉体的纯洁度,也可以减少损耗。
3、电炉装料时,应注意炉料最高点距电阻丝的距离不得少于100mm,否那么容易引起短路。
熔化炉料装完后即可升温。
熔化是从固态转变为液态的过程。
这一过程的好坏,对产品质量有决定性的影响。
A、覆盖熔化过程中随着炉料温度的升高,特别是当炉料开始熔化后,金属外层外表所覆盖的氧化膜很容易破裂,将逐渐失去保护作用。
气体在这时候很容易侵入,造成内部金属的进一步氧化。
并且已熔化的液体或液流要向炉底流动,当液滴或液流进入底部聚集起来时,其外表的氧化膜就会混入熔体中。
所以为了防止金属进一步氧化和减少进入熔体的氧化膜,在炉料软化下塌时,应适当向金属外表撒上一层粉状熔剂覆盖,其用量见表。
这样也可以减少熔化过程中的金属吸气。
铝合金的精炼
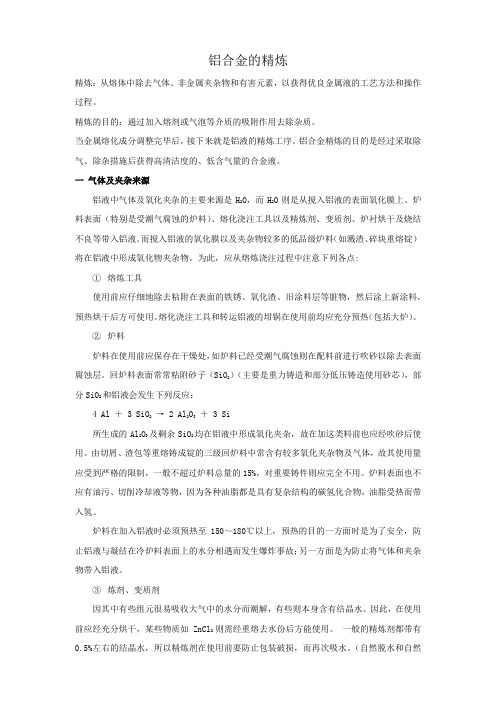
铝合金的精炼精炼:从熔体中除去气体、非金属夹杂物和有害元素,以获得优良金属液的工艺方法和操作过程。
精炼的目的:通过加入熔剂或气泡等介质的吸附作用去除杂质。
当金属熔化成分调整完毕后,接下来就是铝液的精炼工序。
铝合金精炼的目的是经过采取除气、除杂措施后获得高清洁度的、低含气量的合金液。
一气体及夹杂来源铝液中气体及氧化夹杂的主要来源是H2O,而H2O则是从搅入铝液的表面氧化膜上、炉料表面(特别是受潮气腐蚀的炉料)、熔化浇注工具以及精炼剂、变质剂、炉衬烘干及烧结不良等带入铝液。
而搅入铝液的氧化膜以及夹杂物较多的低品级炉料(如溅渣、碎块重熔锭)将在铝液中形成氧化物夹杂物。
为此,应从熔炼浇注过程中注意下列各点:①熔炼工具使用前应仔细地除去粘附在表面的铁锈、氧化渣、旧涂料层等脏物,然后涂上新涂料,预热烘干后方可使用。
熔化浇注工具和转运铝液的坩锅在使用前均应充分预热(包括大炉)。
②炉料炉料在使用前应保存在干燥处,如炉料已经受潮气腐蚀则在配料前进行吹砂以除去表面腐蚀层。
回炉料表面常常粘附砂子(SiO2)(主要是重力铸造和部分低压铸造使用砂芯),部分SiO2和铝液会发生下列反应:4 Al + 3 SiO2→ 2 Al2O3+ 3 Si所生成的Al2O3及剩余SiO2均在铝液中形成氧化夹杂,故在加这类料前也应经吹砂后使用。
由切屑、渣包等重熔铸成锭的三级回炉料中常含有较多氧化夹杂物及气体,故其使用量应受到严格的限制,一般不超过炉料总量的15%,对重要铸件则应完全不用。
炉料表面也不应有油污、切削冷却液等物,因为各种油脂都是具有复杂结构的碳氢化合物,油脂受热而带入氢。
炉料在加入铝液时必须预热至150~180℃以上,预热的目的一方面时是为了安全,防止铝液与凝结在冷炉料表面上的水分相遇而发生爆炸事故;另一方面是为防止将气体和夹杂物带入铝液。
③炼剂、变质剂因其中有些组元很易吸收大气中的水分而潮解,有些则本身含有结晶水。
因此,在使用前应经充分烘干,某些物质如ZnCl2则需经重熔去水份后方能使用。
探究铝合金熔炼工艺与质量控制
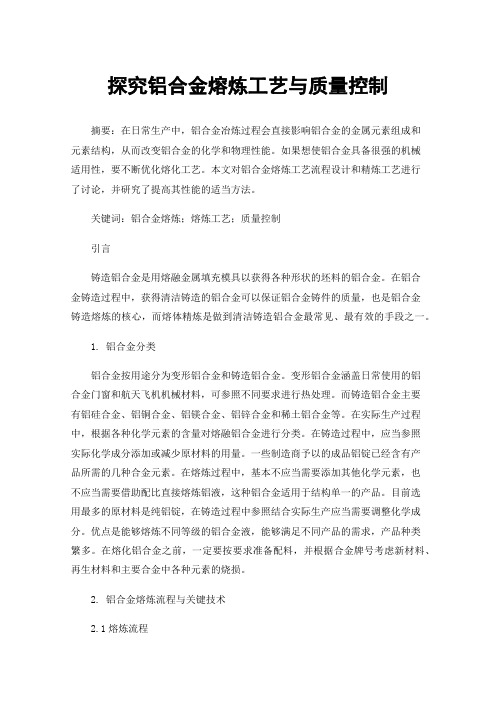
探究铝合金熔炼工艺与质量控制摘要:在日常生产中,铝合金冶炼过程会直接影响铝合金的金属元素组成和元素结构,从而改变铝合金的化学和物理性能。
如果想使铝合金具备很强的机械适用性,要不断优化熔化工艺。
本文对铝合金熔炼工艺流程设计和精炼工艺进行了讨论,并研究了提高其性能的适当方法。
关键词:铝合金熔炼;熔炼工艺;质量控制引言铸造铝合金是用熔融金属填充模具以获得各种形状的坯料的铝合金。
在铝合金铸造过程中,获得清洁铸造的铝合金可以保证铝合金铸件的质量,也是铝合金铸造熔炼的核心,而熔体精炼是做到清洁铸造铝合金最常见、最有效的手段之一。
1. 铝合金分类铝合金按用途分为变形铝合金和铸造铝合金。
变形铝合金涵盖日常使用的铝合金门窗和航天飞机机械材料,可参照不同要求进行热处理。
而铸造铝合金主要有铝硅合金、铝铜合金、铝镁合金、铝锌合金和稀土铝合金等。
在实际生产过程中,根据各种化学元素的含量对熔融铝合金进行分类。
在铸造过程中,应当参照实际化学成分添加或减少原材料的用量。
一些制造商予以的成品铝锭已经含有产品所需的几种合金元素。
在熔炼过程中,基本不应当需要添加其他化学元素,也不应当需要借助配比直接熔炼铝液,这种铝合金适用于结构单一的产品。
目前选用最多的原材料是纯铝锭,在铸造过程中参照结合实际生产应当需要调整化学成分。
优点是能够熔炼不同等级的铝合金液,能够满足不同产品的需求,产品种类繁多。
在熔化铝合金之前,一定要按要求准备配料,并根据合金牌号考虑新材料、再生材料和主要合金中各种元素的烧损。
2. 铝合金熔炼流程与关键技术2.1熔炼流程在铸造过程中,添加的Mg、Zn和Cd元素会与合金精炼过程中形成的C2Cl6(六氯乙烷)发生反应,将Mg元素与Cl元素一起稀释,Cd元素会随着时间的推移高温精炼而不断减少。
为保证ZL109A铝合金中合金化微量元素含量,可在C2Cl6静置半小时后再开展后续操作,整个操作过程不超过2小时。
在整个铸造过程中,鉴于炉料的高温和铸造坩埚等铸造工具的各种化学反应,不可避免地会导致铸造合金重量中的各种杂质。
铝合金熔炼

Fe、Mg及冷却对材料性能的影响
Fe、Mg及冷却对材料性能的影响
Fe、Mg及冷却对材料性能的影响
常用名词解释
• 合金:是两种或两种以上的金属或金属元素与非金属元素熔合在一起 所得到的具有金属特性的物质。组成合金的各元素称组元。它们交互 作用形成多种相,即合金中具有同一化学成份、同一结构和原子聚集 状态的均匀部分。不同相之间有明显的界线分开。相的结构可分为固 溶体和化合物两大类。 • 固溶体:是指溶质原子溶入溶剂晶格中而仍保持溶剂晶格类型的一种 金属晶体。大多数溶质原子在溶剂晶格中溶解度是有一定限度的,过 量会形成新相。 • 固溶强化:通过溶入某种溶质元素形成固溶体,使晶格常数变化越大, 其强化效果也越大。这种现象称固溶强化。 • 金属化合物(中间相):是合金元素间发生相互作用而生成的一种新 相(溶质含量越过溶解度),当合金中出现金属化合物时,通常能提 高合金的强度、硬度和耐磨性,但会降低塑性。 • 共晶是在低于任一种组成物金属熔点的温度下所有成分的融合。在大 多数例子中,共晶合金中组成物金属的熔点与它在纯金属状态下的熔 点相差100℃。共晶合金直接从固态变到液态,而不经过塑性阶段。其 熔化温度称共晶温度。 • 烧损:熔炼过程中,熔体由于氧化而变成某些不能回收的金属化合物 时,这种损失统称为烧损,其大小与炉型、炉料状态、生产工艺等有 关。
铝及铝硅金
铝的主要性能:比重小,纯铝约2.7g/cm3,大约只有 钢和铜的三分之一,导电、热性高,仅次于银和铜, 耐腐蚀性好,加工性好,无毒,铝合金比强度(强 度与比重的比值)高,还有良好的低温反射性能, 无磁性,不起火花,表面光泽美观,能表面涂饰等 多种特殊性能。 工业上使用的纯铝纯度为99.7%,溶点660.37℃。 具有面心立方格,无同素异晶转变,在空气中易在 表面形成致密的氧化膜。沸点2450℃。 ZL101合金: 在700℃时比重为2.4g/cm3,阻力系数µ 为1.27,动力 粘度η为0.023g/Cm· S,固态理想 密度为2.68克/立方 厘米,固相线温度及液相线温度555℃-615℃。
铸造铝合金熔炼、浇注操作规程

铸造铝合金熔炼、浇注操作规程«1铝合金的熔化1.1坩埚、锭模及熔炼工具的预备1. 1. 1石墨坩埚的预备:1. 1. 1. 1根据熔化量的多少选用容量适当的坩埚;1 . 1 . 1. 2新坩埚使用前,应由室温缓慢升温至900C进行焙烧,以去除坩埚的水分并防止炸裂;1 . 1 . 1. 3旧坩埚(注重同一个坩埚不能用于熔化不同牌号的合金)使用前应检查是否损坏,清除表面熔渣和其它脏物,装料前预热到250~300 C。
1 . 1 . 2铁质坩埚一般采用球铁坩埚,也可用铸钢(或钢板焊接)坩埚。
为提高坩埚使用寿命,其外表面可进行液体渗铝处理。
1 . 1 . 3坩埚、锭模及熔炼工具,使用前应将残余的金属、氧化皮等杂物清除干净。
1 . 1 . 4新坩埚及有锈蚀污物的旧坩埚,使用前应吹砂或用其它方法清除干净,并加热到700〜800 C,保温2〜4小时,以除去坩埚吸附的水分及其它化学物质。
1 . 1 . 5铝镁系合金的熔炼工具,使用前应在光卤石等溶剂中洗涤干净。
1 . 1 . 6坩埚、锭模、熔炼工具使用前应涂防护涂料。
搪衬的保温坩埚重复使用时,可不涂防护涂料。
1 . 1 . 6. 1涂料成分可按表1中的规定:表1坩埚和工具用涂料1 . 1 . 6. 2涂料的配制:涂料成分中的所有固体组元,配制前应磨碎,并经过100〜140目过筛,然后混合均匀。
使用时,先将水玻璃倒入80〜100 C的热水中搅拌均匀,加入固体组元后再搅拌均匀,冷却后备用。
配好后的涂料停放时间一般不超过8小时。
1 . 1 . 6. 3将坩埚、锭模、熔炼工具预热到180〜250C,涂以防腐涂料。
1. 1. 7用于保温的碳素钢板焊接坩埚,其内表应用耐火材料搪衬。
耐火材料可按表2中的规定:表2耐火材料成分配比1 . 2原材料1.2.1配制铝合金所用的金属材料应符合QB004《原材料技术条件及验收标准》中的规定。
1 .2 . 2配制涂料、搪衬、精炼用剂所用的辅助材料也应符合QB004中的规定。
矿热炉的冶炼铝硅合金工艺-定义说明解析
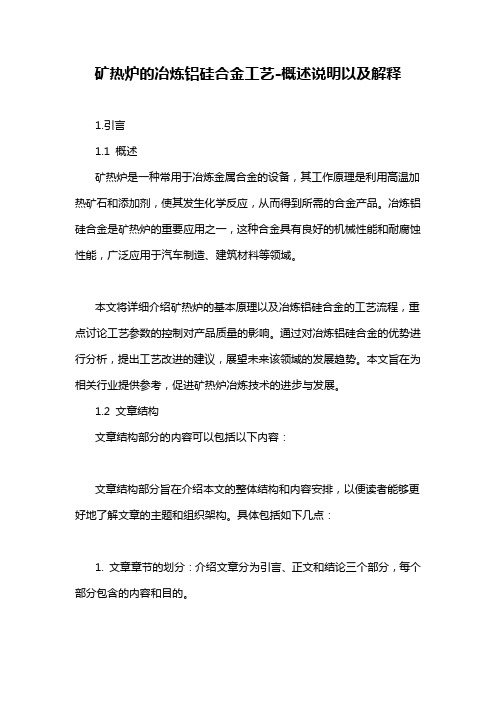
矿热炉的冶炼铝硅合金工艺-概述说明以及解释1.引言1.1 概述矿热炉是一种常用于冶炼金属合金的设备,其工作原理是利用高温加热矿石和添加剂,使其发生化学反应,从而得到所需的合金产品。
冶炼铝硅合金是矿热炉的重要应用之一,这种合金具有良好的机械性能和耐腐蚀性能,广泛应用于汽车制造、建筑材料等领域。
本文将详细介绍矿热炉的基本原理以及冶炼铝硅合金的工艺流程,重点讨论工艺参数的控制对产品质量的影响。
通过对冶炼铝硅合金的优势进行分析,提出工艺改进的建议,展望未来该领域的发展趋势。
本文旨在为相关行业提供参考,促进矿热炉冶炼技术的进步与发展。
1.2 文章结构文章结构部分的内容可以包括以下内容:文章结构部分旨在介绍本文的整体结构和内容安排,以便读者能够更好地了解文章的主题和组织架构。
具体包括如下几点:1. 文章章节的划分:介绍文章分为引言、正文和结论三个部分,每个部分包含的内容和目的。
2. 各部分之间的逻辑关系:说明每个部分之间的内在联系和逻辑关系,确保文章的结构清晰、条理分明。
3. 各章节之间的过渡:提及在文章中各个章节之间的过渡和连接,确保文章的内容流畅、连贯。
4. 文章整体主旨:概括概述文章的主要观点和重点,引导读者对文章的整体内容和主题有一个整体性的把握。
文章结构部分的内容应该简明扼要,清晰地说明文章整体的安排和组织,为读者提供一个全面的预览,帮助读者更好地理解全文内容。
1.3 目的目的部分:本文旨在探讨矿热炉在冶炼铝硅合金过程中的应用,通过分析矿热炉的基本原理、工艺流程以及工艺参数的控制,深入探讨冶炼铝硅合金的优势及存在的问题,并提出改进的建议,最终展望未来对该工艺的发展方向。
通过本文的研究,旨在为相关行业提供更好的冶炼铝硅合金工艺方法,推动行业技术的进步和提高产品品质,从而促进整个行业的健康发展。
2.正文2.1 矿热炉的基本原理矿热炉是一种特殊类型的冶炼设备,通常用于熔炼金属或合金。
其基本原理是利用燃料的燃烧产生的热能进行金属或合金物质的加热熔融,然后通过控制燃烧的强度和温度来控制冶炼过程。
熔炼的五个准备
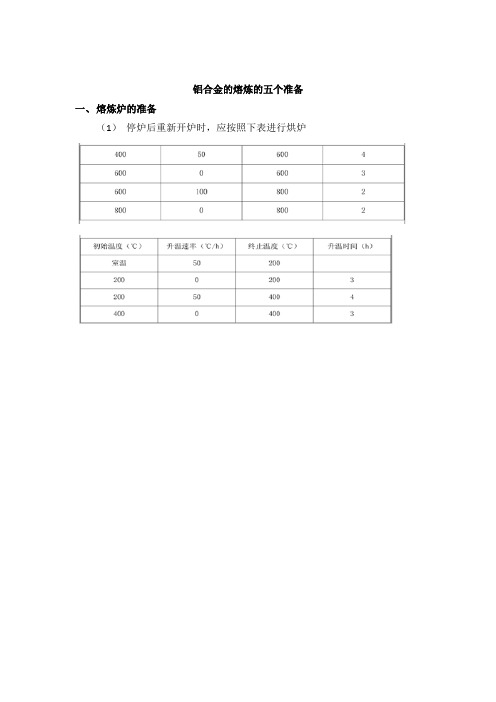
铝合金的熔炼的五个准备一、熔炼炉的准备(1)停炉后重新开炉时,应按照下表进行烘炉二、坩埚、锭模及熔炼工具的准备1石墨坩埚的准备:(1)新坩埚使用前,应由室温缓慢升温至900℃进行焙烧,以去除坩埚的水分并防止炸裂;(2)旧坩埚(注意同一个坩埚不能用于熔化不同牌号的合金)使用前应检查是否损坏,清除表面熔渣和其它脏物,装料前预热到250~300℃。
(3)铁质坩埚一般采用球铁坩埚,也可用铸钢(或钢板焊接)坩埚。
为提高坩埚使用寿命,其外表面可进行液体渗铝处理。
(4)坩埚、锭模及熔炼工具,使用前应将残余的金属、氧化皮等杂物清除干净。
(5)新坩埚及有锈蚀污物的旧坩埚,使用前应吹砂或用其它方法清除干净,并加热到700~800℃,保温2~4 小时,以除去坩埚吸附的水分及其它化学物质。
(6)铝镁系合金的熔炼工具,使用前应在光卤石等溶剂中洗涤干净。
(7)坩埚、锭模、熔炼工具使用前应涂防护涂料。
搪衬的保温坩埚重复使用时,可不涂防护涂料。
(8)涂料成分可按表 1 中的规定:(9)涂料的配制:涂料成分中的所有固体组元,配制前应磨碎,并经过100~140 目过筛,然后混合均匀。
使用时,先将水玻璃倒入80~100℃的热水中搅拌均匀,加入固体组元后再搅拌均匀,冷却后备用。
配好后的涂料停放时间一般不超过8 小时。
(9)将坩埚、锭模、熔炼工具预热到180~250℃,涂以防腐涂料。
三、炉料的准备(1)铝锭、纯合金锭、中间合金锭、一二三级回炉料都要去除表面上的锈迹、泥沙、油腻等杂质;(2)回炉料分为三级,用法、用量要依照表二注:(1)当铸件有特殊要求时(如针孔度等),回炉料的用量应酌情减少,如气缸铸件应低于40%;(2)当各级回炉料搭配使用时,回炉料的总量≤80%,其中,三级回炉料≤10%,二级回炉料≤50%。
(3)回炉料应按牌号分开堆放,成分不清的需经重熔后分析成分方可用于配料。
(3)所有使用的炉料都要进行化学分析并做好存档记录,以便进行准确的计算、技术分析和复查核实;(4)各炉料的用量比例要进行准确科学的分析计算,以减少理化试验的次数,缩短熔炼的时间,提高生产效率;(5)炉料加入的先后要符合以下原则;1 当用铝锭和中间合金熔化时,首先装入铝锭,然后加入中间合金;2 当用预制合金锭进行熔炼时,首先装入预制合金锭,然后补加所需的铝和中间合金;3 当炉料为回炉料和铝锭组成时,首先加入炉料中最多的那一部分;4 当熔炉容量足以同时装入几种炉料时,则应首先装入熔点相近的成分;5 容易烧损和低熔点的炉料,如镁和锌,应在最后加入;6 在连续熔化时坩埚内应剩余一部分铝液以加速下一炉的熔化;7 采用覆盖剂时,应在炉料开始熔化时就加入熔剂。
铝合金的熔炼与铸造

针孔应在三级以内,局部(不超过受检面积的25%)不应超过三级,超过三级者必须采取重熔炼的办法以减少针孔度。重熔精炼方法与一般铝合金熔炼相同,浇铸温度不宜超过660℃,对于那些原始晶粒大的铝锭、合金锭等,应先用较低的锭模温度,使它们快速凝固,细化晶粒。
2、炉料处理
(二)熔炼工具的准备
钟罩、压瓢、搅拌勺、浇包
锭模等使用前均应预热,并在150度---200度温度下涂以防护性涂料,并彻底烘干,烘干温度为200--400度,保温时间2小时以上,使用后应彻底清除表面上附着的氧化物、氟化物,(最好进行吹砂)。
3、熔炼温度的控制
熔炼温度过低,不利于合金元素的溶解及气体、夹杂物的排出,增加形成偏析、冷隔、欠铸的倾向,还会因冒口热量不足,使铸件得不到合理的补缩,有资料指出,所有铝合金的熔炼温度到少要达705度并应进行搅拌。熔炼温度过高不仅浪费能源,更严重的是因为温度愈高,吸氢愈多,晶粒亦愈粗大,铝的氧化愈严重,一些合金元素的烧损也愈严重,从而导致合金的机械性能的下降,铸造性能和机械加工性能恶化,变质处理的效果削弱,铸件的气密性降低。
5、熔体的转送和浇注
尽管固态氧化铝的密度近似于铝熔体的密度,在进入铝熔体内部后,经过足够长的时间才会沉至坩埚底陪。而铝熔体被氧化后形成的氧化铝膜,却仅与铝熔体接触的一面是致密的,与空气接触的一面疏松且有大量直径为60--100A的小孔,其表面积大,吸附性强,极易吸附在水汽,反有上浮的倾向。因此,在这种氧化膜与铝熔体的比重差小,将其混入熔体中,浮沉速度很慢,难以从熔体中排除,在铸件中形成气孔太夹杂。所以,转送铝熔体中关键是尽量减少熔融金属的搅拌,尽量减少熔体与空气的接触。
(五)即将浇注时,应扒净浇包的渣子,以免在浇注中将熔渣、氧化皮等带入铸型中。
铝及铝合金熔炼工艺操作规程
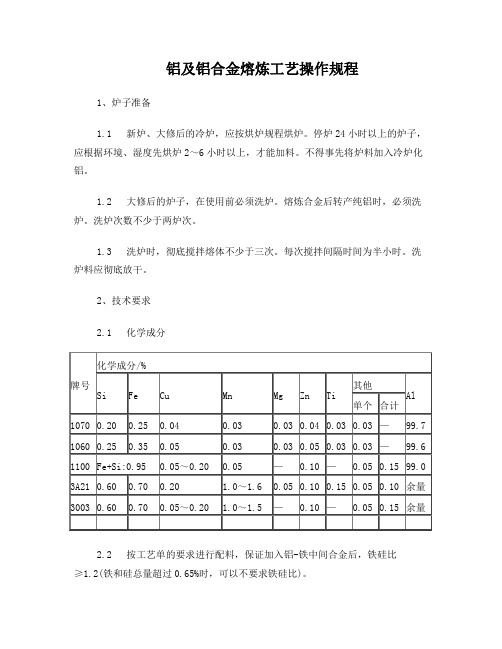
铝及铝合金熔炼工艺操作规程1、炉子准备1.1 新炉、大修后的冷炉,应按烘炉规程烘炉。
停炉24小时以上的炉子,应根据环境、湿度先烘炉2~6小时以上,才能加料。
不得事先将炉料加入冷炉化铝。
1.2 大修后的炉子,在使用前必须洗炉。
熔炼合金后转产纯铝时,必须洗炉。
洗炉次数不少于两炉次。
1.3 洗炉时,彻底搅拌熔体不少于三次。
每次搅拌间隔时间为半小时。
洗炉料应彻底放干。
2、技术要求2.1 化学成分2.2 按工艺单的要求进行配料,保证加入铝-铁中间合金后,铁硅比≥1.2(铁和硅总量超过0.65%时,可以不要求铁硅比)。
3、加料3.1 对炉料的要求3.1.1 配料所使用的原料,必须符合公司内部原材料验收标准的规定,必须有化学成分单方可使用。
3.1.2 外购卷废料成分符合要求,且加工性能合格,方可使用。
3.1.3 铝屑之类的炉料应先铸成锭后,才能加入,并应掺含50%以上的新料(可以是剪切边角料)加入。
3.1.4 所使用的原材料必须清洁、干燥,不得粘有泥、砂,不得混入其他金属和非金属夹杂物。
粘有泥、砂的炉料,应清洗晾干后,才能加入炉内。
3.2 炉料的加入顺序和原则3.2.1 为了保护炉底,加料前先用小块料铺一层底料。
3.2.2 炉膛内加料分布均匀,保持重心不偏移。
3.2.3 炉料在炉膛内的平均高度不允许超过烧嘴的位置,炉料最高处不允许超过烧嘴位置8cm,要保持烧嘴喷射火焰空间畅通,空气流通,防止冒浓烟,减少热损失。
为保证装炉量,分二次加料,开火待一次加料软化、炉料高度下降后,再进行二次加料。
3.3 安全要求3.3.1 凡粘有水和油的废料,不得直接加入未放尽铝液的炉内。
3.3.2 凡粘有润滑油的炉料,不得直接加入保温炉,应在柴油炉内加热蒸发,烧去油污和水分。
3.3.3 加废料前,应先打开烟道闸门,加完后再开烧嘴一刻钟,然后适当关烟道闸门进行升温。
4、熔化4.1 柴油炉点火,应严格遵守安全操作规程,先开风,后开油,先停油,后关风。
铝合金精炼
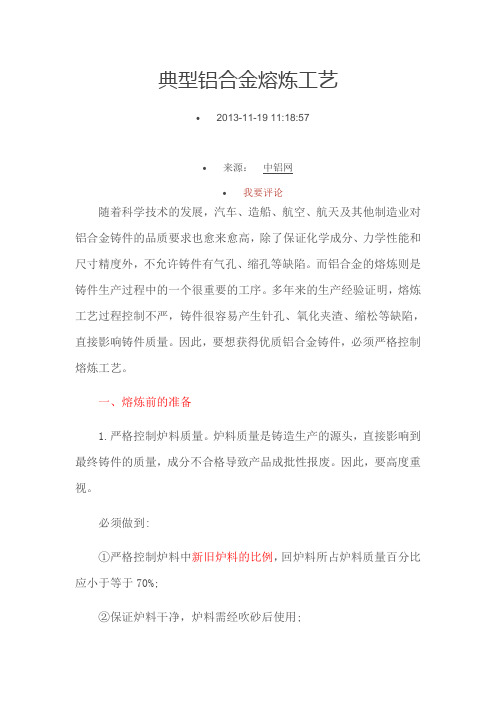
典型铝合金熔炼工艺∙2013-11-19 11:18:57∙来源:中铝网∙我要评论随着科学技术的发展,汽车、造船、航空、航天及其他制造业对铝合金铸件的品质要求也愈来愈高,除了保证化学成分、力学性能和尺寸精度外,不允许铸件有气孔、缩孔等缺陷。
而铝合金的熔炼则是铸件生产过程中的一个很重要的工序。
多年来的生产经验证明,熔炼工艺过程控制不严,铸件很容易产生针孔、氧化夹渣、缩松等缺陷,直接影响铸件质量。
因此,要想获得优质铝合金铸件,必须严格控制熔炼工艺。
一、熔炼前的准备1.严格控制炉料质量。
炉料质量是铸造生产的源头,直接影响到最终铸件的质量,成分不合格导致产品成批性报废。
因此,要高度重视。
必须做到:①严格控制炉料中新旧炉料的比例,回炉料所占炉料质量百分比应小于等于70%;②保证炉料干净,炉料需经吹砂后使用;③三等回炉料枷浇冒口匀使用前应经重熔精炼处理;④炉料应充分预热,去除水分、油污等杂质;⑤由于铭合金有铝硅类、铝铜类、铝镁类等合金,合金牌号较多,使用的元素也比较多,且互相影响,要求严格管理,不可混料;⑥配料、称量要准确,比如ZL104合金,考虑到除气、排渣及变质过程中的损耗,Mg元素应在实际配料时多加炉料质量的0.02%-0.03%,才能保证铸件的化学成分。
2.熔炼工具。
熔炼使用的址涓及熔炼工具须清理干净且涂上涂料,以保证使用时与铝合金有效隔离,减少合金液受到杂质污染,并且需要充分预热,址涓要烘烤至暗红色再加入炉料熔炼,以防水蒸气带入合金中使合金的气体增加、针孔度增加。
3.其他工作。
严格按已制订好的工艺规范作好覆盖剂、精炼剂及变质剂的准备工作。
二、熔炼操作熔炼步骤如下。
①装料。
在预热后的柑A中装入预制合金锭、优质回炉料,再加中fol合金,最后加合金元素。
②温度控制。
严格控制铝合金熔炼的温度,只有合适的温度才能获得高质量的合金液,避免过热。
若温度过高,会加大合金中各种元素的氧化烧损,引起合金中化学成分的变化。
电热法熔炼铝硅合金

由于铝比较容易和氯生成低价氯化铝,而低价氯化铝只在高温下稳定,在低温下就歧化为三氯化铝和金属铝。据此可在高温下使铝合金中的铝转化为AlCl气,然后在低温下使AlCl歧化分解出铝和三氯化铝,三氯化铝再返回与铝硅合金反应。在坡化分解过程中,铝硅合金中的Si、Fe、Ti很少参与反应,但Zn、Mg随之进入铝液。
低价氯化铝歧化法包括5个环节:(1)电热法制取粗合金;(2)铝硅合金和AlCl3气体在反应炉内发生反应,温度为1300℃;(3)卤化物同低价卤化物在分馏室内蒸发分离;(4)用氯气与高铝硅合金反应得到AlCl3;(5)在冷凝器内,AlCl歧化解得到纯铝和AlCl3,后者返回使用。
低价氯化铝歧化法在工业上从铝硅合金中提取纯铝是有效的方法。在真空条件下,AlCl的分解率很高,在1kPa时的分解率接近100%。低价氯化铝歧化过程还可以在熔盐中进行,AlCl3通入铝硅合金与KCl组成的熔盐中返应,生成的AlCl溶于高温熔体中而不挥发,当熔体冷却时AlCl就歧化分解出纯铝。
中国抚顺铝厂于20世纪60年代进行了电热法熔炼铝硅合金以及从铝硅合金中提取纯铝的研究。电热法熔炼铝合金是非电解法,它的原理就是碳还原,即用碳还原含铅和硅的矿石,得到铝硅合金。
一、电热法熔炼铝硅合金的原理
在电炉中,铝矿加热到2000℃,碳就可以夺取氧化铝中的氧,还原出金属铝。而矿中的SiO2在1700℃下就还原为硅,形成铝硅合金。SiO2和Al2O3共同被碳还原的反应分为三步:
铝硅合金是应用最广的铸造铝合金,目前世界各国所用的铝硅合金均是纯铝与纯硅混熔掺兑生产的. 生产纯铝需要高品位的铝土矿,我国铝土矿的静态保障年限只有十多年[1],且该方法生产铝硅合金工艺流程长而复杂,能耗高. 用碳电热还原法生产铸造用一次铝硅合金不仅可大大降低能耗,缩短流程,而且可以使用储量丰富的低品位铝土矿和其他铝矿资源[2],因此越来越受到重视.
- 1、下载文档前请自行甄别文档内容的完整性,平台不提供额外的编辑、内容补充、找答案等附加服务。
- 2、"仅部分预览"的文档,不可在线预览部分如存在完整性等问题,可反馈申请退款(可完整预览的文档不适用该条件!)。
- 3、如文档侵犯您的权益,请联系客服反馈,我们会尽快为您处理(人工客服工作时间:9:00-18:30)。
铝硅合金的熔炼前言:从20世纪韧铝合金用于铸造工业以来,合金的成分有了很大的发展,合金的品种越来越丰富。
早期使用的铸造铝台金含t3%2n和3%cu。
这种合金在第一次世界大战前后用量很大,后来由于金屑型铸造的发展而被铝铜合金取代。
同时,铝硅台金开始得到应用.铝镁合金也随之推出。
1919年,美国生产的铝合金铸件,97%以上由含8%cu的铝合金铸造。
1933年,用这种合金生产的铸件仍占铝合金铸件的50%左右。
除了在铸态下使用的合金外,后来又开发出可以热处理的铝锅台金,含大约4%cu o随着金屑型铸造和压铸工艺的发展,铝硅合金得到广泛应用。
近年来,在铸造领域应用的铝合金,除了铝硅系列合金之外,还有铝锅系列、铝镁系列、铝锌系列和其他系列的铝合金。
在这些系列的合金中,除了少数的二元合金外,大多数都是添加多种合金元素的多元合金。
摘要:铝硅合金熔炼性质工艺流程正文:铝硅系列合金具有良好的铸造性能,较小的线胀系数,耐磨性能好,气密性也很好。
这种合金被广泛地应用于铸造复杂的铸件,如汽车发动机铸件等。
铝的国家标准铸造铝合金生产中所用的铝包括电解原铝重熔用铝锭和一定数量的再生铝。
有些牌号的铸造铝合金要以电解原铝为原料,有些牌号则可以用大部分再生铝和小部分电解原铝作原料.有些牌号甚至可以完全用再生铝作原料。
电解原铝是用冰品石—氧化铝熔融盐电解法生产的。
自中华人民共和国成立以来,我国的电解铝工业从无到有p生产技术和铝产量都有很大发展。
1999年我国铝的总产量已达265万吨,跃居世界第三位,仅次于美国和俄罗斯。
2003年我国铝的总产量达到542万吨,居世界首位。
但是.我国铝的人均占有量还很少。
硅的国家标准我国工业硅必须符合国家标憋哪288l一91,工业硅厂工业硅的内控标准如表2.4,2.5所示。
硅铝二元相图铝相硅很容易形成合金。
A1—si二元相图如图2—1所示。
从si二元相图可以看作简单的二元共晶型状态图,共品成分为12.6%s1(有的文献为11.6%s1),共品温度为577℃,共晶反应为L1。
’Po。
相是硅溶解于铝的固溶体,在577℃时固涪度最大,为1.65%,在室温下大约为o.05%。
P相是铝溶于硅的固溶体,由于固溶度极小,在577℃时仅为o.17%,因此可以把它看作硅相。
工业中应用的铸造铝硅合金台si量大干4%,有的高达26%。
工业上台sl量小于10%的铝硅合金称为亚共晶型铝硅合金,含S1量10%一14%的铝硅合金称为共晶型铝硅合金,含st量大子14%的铝硅合金称为过共晶型铝硅合金。
认真学习和掌握从Si二元相固十分重要,有助于分析和大致预副铝硅合金的某些待性。
一般生产工艺流程铸造铝合金生产的一般工艺流程如图1.1所示原料准备:包括原料外观检查,化学成分分济,配料和按配料计算结果称量各种原料。
另外,还包括精炼剂、变质剂的烘干和称量。
熔炼:按一定的加料顺序把原料加入炉内,将其熔化成化学成分均匀的合金。
炉前化验:合金熔化均匀后,取样化验,检查各种化学成分是否符合技术标准要求。
调整成分:经化验,如果发现合金中某种或几种化学成分超出技术标准的规定,则要进行调整,使化学成分达到技术标准。
精炼:化学成分符合要求后,要用精炼刑清除合金中溶解的气体和夹带的固体颧粒。
细化变质:向铝合金液中汤加适量的细化剂和变质剂,改善合金力学性能和机械切削加工性能等。
浇铸:将化学成分合格、变质效果好,含气量和含渣量均达到要求的铝合金铸或锭,打成包捆。
检查入库;经过检验,化学成分、含气量、夹杂物、变质效果、力学性能和外观都合格的铝合金锭作为合格产品入库。
熔炉熔炼铸造铝合金炉的容量范围较大,有几百公斤的小型炉,也有60一80t的大型萨。
小型炉为增蜗炉、工顾感应炉相中顾感应炉等,大型炉则为备式各样的反射炉。
例如,电阻加热反射炉,燃泊加热反射炉,燃气加热反射炉和燃煤加热反射炉等。
由于反射萨容量大,适合于大规模生产,所以现代化铸造侣合金厂均采用反射炉。
气体燃料可以是煤气,也可以是天然气。
铸造铝合金厂所用的煤气一般为热煤气,低发热量约为5652U/m3,天然气的低发热量约为35170U/m3。
煤气的单耗为500一700m3/t,天然气的单耗为80—90m3/to燃气加热反射护可以做成圆形也可以砌成矩形,圆形炉的特点是,当炉子容量相同时,炉子的外表面最小。
同时,烧嘴喷出的火焰可以沿炉子内壁切线方向流动,能提高加热效果。
炉组在铸造铝合金厂,除了用单体炉进行生产外,常常将上妒和下妒组成炉组进行生产。
上炉的主要任务是熔化废铝炉料,然后将掖态炉料放人下炉.进行调整化学成分和精炼变质等操作。
当上炉液态炉料全部故人下妒后.可以颠利地将妒底上留下的铁固定件扒出来。
因此可以降低铝合金液的台Fe量.提高废铝利用率。
炉组一般是一台上炉对一台下炉,也可以是一台上炉对两台或更多台下炉。
田3.6是妒组示意图。
当上妒中的掖态铝炉料不需要全部放出,只需放出一部分到下炉进行配村时,应该放出的合金数量可以由配科计算确定。
但是,打开上妒炉眼,经过一段时间后,流到下炉中的铝妒科量,一方固可以由有经验的工人大致估计,另一方面也可以根据铝合金中的某一种合金素的含量按式计算:熔炼前的准备焙炼前的准备包括炉料准备、精炼剂淮备、变质剂淮备、各种工具准备和始炼炉准备。
铸造铝硅系合金生产所用的原料包括工业纯金屑、中间合金和回收的废铝及废旧铝件等。
①工业纯金屑。
例如,工业硅、工业纯铝、电解铜、工业纯镁、电解镭……②中间合金。
高熔点或易氧化的合金元素,有时事先配成中间合金使用。
另外,撤为铸造铝合金变质对或绍化剂的金屑元素也以中问合金的形式使用。
③再生铝。
回收的废铝和废旧铝件的化学成分复杂,混杂的其他金属较多。
因此.在使用前要进行预处理,包括人工分选、破碎、磁选和脱漆等。
除气除渣在熔融状态下,铸造铝合金很容易被氧化和吸气,在铝合金锭内部形成灾渣和针孔。
如果铝合金铸件内部存在大量夹渣和针孔,会使铸件的抗拉强度和伸长率下降,气密性遭到破坏,刀具磨损加快甚至断裂。
铝合金的氧化和吸气发生在熔炼和浇铸的各个环节之中。
在每一项操作中都要尽量创造减少氧化和吸气的工作条件。
虽然针孔是气体溶解于铝合金所致,氧化物夹渣是由于氧化物残留在铝合金中引起的,但是二者往往相互关联。
在生产实践中可以发现,氧化物夹渣多的铝合金往往含气量高。
这是由于某些氧化物,如yl从03,其外表面有许多95—910咖的摄孔强烈地吸附气体的结果。
吸附气体后的Y—d203密度下降,与铝合金液的密度差减小,悬浮在铝合金液中,增加了铝合金的含气量和夹渣量。
因此,为了提高铝合金的质量.在净化处理铝台金液的过程中要同时考虑除气和除渣,不可偏皮。
踌造铝合金炉内沉渣的产生和预防在铸造铝合金和铝合金铸件生产厂,保温炉内液态铝合金停留时间较长时,常常有固体微鞍向炉底沉积,称之为“沉渣(studp)”。
如果炉底上有大量沉渲长时间沉积,它会逐渐形成硬块.影电炉子的正常操作.也会给生产带来其他不良影璃。
对沉渲进行化学分桥表明,沉渲是由铝、枝和铁元家组成的.即是A1—57Fe金属问化合物。
如果铝合金中还含有锤和锗,那么沉渣是由铝、枝、铁和锤以及铝、硅、快、镭和锗元家组成的,即是A1—SLPrMn和A1—Si—PrMn·cr金属问化合物。
这些化合物的组分不固定而且很硬,它们的密度比液态铝合金密度大得多,熔点较高,所以在铝合金液的保温过程中它们会以固体微较的形态向炉底沉降,并在那里积聚。
在铝合金铸件生产厂,特别不希望有从s6。
Fe,从SI—PrMn和从sI—PrMncr等金屑间化合物形成的沉渣。
如果颊鞍较大的这类沉渣落入铸件里,它们合成为铸件里的硬质点,在铸件加工过程中会使车刀磨损加快,甚至断裂。
如果是自动化流水线,由于车刀断裂会影响整个流水线。
铝合金祷件中的硬质点在铝合金涛件加工的过程中,有时在加工面上发现有硬度很大的小颗粒,有的发亮,有的较暗。
加工铸件时有的可能从加工磨损,甚至可能使刀具断裂,造成整个流水线停止工作。
人们把铝台金涛件中硬度很高的微小颗粒称为硬质点。
铝合金铸件中的硬质点,大体上有:氧化物,如。
AI,ck(刚玉),MsJLl04(尖品石)和炉衬脱落的耐火枝科颐较等;金屑间化合Qt如从龄PrAh金屑闯化合物或从3I—FrMLCr金屑间化古物和碳化物等。
这些物质在铝台金涛件中出现概率最多的是刚玉和金屑问化合物。
它们很硬,前者的布氏硬度为250一350,后考为500以上.面铸造铝硅合金的硬度为100左右。
硅酸盐和尖品石的硬度为250左右,碳化物的硬度与刚五相当。
从03(刚五)主要是在保温炉里形成炉结,又脱落进入铝合金液中,浇涛时混入铸件里形成硬质点。
金屑间化合物主要是A1—sLFLMn,它的熔点较高,密度较大,当Fe和Mn在铝台金中的含量一定时,即沉渣系数一定,需要保温炉有一定混度才能保证AL31—FrMn 化合物不大量聚集和下沉。
如果炉混过低,它将聚集和下沉,当浇包取铝合金液时被带入铸件内形成发亮的硬质点。
参考文献:中国机械工程学会铸造专业学会铸造手册:铸造非铁合金.3顺北京:机械工业出版社,1994:7.孙业赞,等.铁在铝硅合金中存在的形态及其作用分析.铸造,1998(7)42陈存中.有色金樱熔炼与铸锭.北京:冶金工业出版社,1991。