铸造工艺设计注意问题.pptx
合集下载
压铸件产品设计注意规范 PPT

二、铸造圆角与脱模斜度
1)铸造圆角 压铸件各部分相交应有圆角(分型面处除
外),使金属填充时流动平稳,气体容易排出, 并可避免因锐角而产生裂纹。对于需要进 行电镀与涂饰得压铸件,圆角可以均匀镀 层,防止尖角处涂料堆积。 压铸件得圆角半径R一般不宜小于1mm,最 小圆角半径为0、5 mm,见表2。铸造圆角 半径得计算见表3。
配合面得最小脱模 非配合面得最小脱
斜度
模斜度
α
外表面α 内表面β 外表面α 内表面β
锌合金
0°10′ 0°15′ 0°15′ 0°45′
β
铝、镁合金 0°15′ 0°30′ 0°30′
1°
铜合金
0°30′ 0°45′
1°
1°30′
说明:①、由此斜度而引起得铸件尺寸偏差,不计入尺寸公差值内。 ②、表中数值仅适用型腔深度或型芯高度≤50mm,表面粗糙度在Ra0、1,大端 与小端尺寸得单面差得最小值为0、03mm。当深度或高度>50mm,或表面 粗糙 度超过Ra0、1时,则脱模斜度可适当增加。
2
0
8
7
3
M6
5、 58~ 5、70
5、 38~ 5、50
≥10
M8
7、45 ~ 7、
60
7、15 ~ 7、
30
≥13、 3
旋入深度t
t≥1、5d
我司现较为常用得自攻螺钉规格为M4与M5, 其采用得底孔直径如下表:
d2
d3
t
M4
3、84
0 -0、1
3、59 +0、1 0
10
M5
4、84
0 -0、1
表5 最小孔径与最大孔深
孔 合金 径
类别
铸造缺陷及其对策.pptx

第25页/共28页
4、防止方法:
1、优化铸件结构设计,壁厚均匀,过渡平滑,肋板 厚度和分布的合理化; 2、优化浇注系统,控制浇温、浇速使铸件各部位冷 却速度趋于一致; 3、降低有害元素,合理控制合金元素添加量; 4、合理设定开箱时间。
5、补救措施:
1、开止裂孔后焊补; 2、采用工业修补剂; 3、如在重要面,报废重铸。
第16页/共28页
4、防止方法: 1、优化工艺设计,合理设置浇注系统; 2、考虑使用保温冒口、发热冒口; 3、优化铸件结构设计; 4、模拟分析(CAE); 5、调整成份; 6、控制炉料.
第17页/共28页
5、补救措施: 1、轻者焊补或采用工业修补剂; 2、重者报废重铸.
第18页/共28页
2.夹砂
的不同大小、形状的 孔洞缺陷的总称
缩孔 缩松
形状不规则,孔壁粗糙,常伴有粗大 树枝晶.夹杂物.裂纹等缺陷;
是细小的分散缩孔,断口呈海绵状;
疏松(显微缩松) 不作严格区分;
第3页/共28页
气 孔
第4页/共28页
针孔
2、裂纹、冷隔类缺陷
定义
缺陷名 称
特征
宏观(肉眼、PT、R T、MT、UT)或微 观(显微镜)判断发现 有开裂状纹络
1、铸件内部裂纹可采用超声波探伤(UT)、 磁粉探伤(MT)或射线探伤法(RT)进行检验; 2、铸件表面的裂纹可采用染色探伤法(PT)来 帮助确定,大部份是肉眼可直接发现的。
第24页/共28页
3、形成原因:
1、铸件结构或浇注系统设计不合理壁厚相差悬殊, 过渡圆角小; 2、铸造合金中有害元素(P、S等)超标,珠光体 元素过量; 3、铸件开箱过早,冷却过快; 4、合金收缩率大; 5、肋板设计不合理。
4、防止方法:
1、优化铸件结构设计,壁厚均匀,过渡平滑,肋板 厚度和分布的合理化; 2、优化浇注系统,控制浇温、浇速使铸件各部位冷 却速度趋于一致; 3、降低有害元素,合理控制合金元素添加量; 4、合理设定开箱时间。
5、补救措施:
1、开止裂孔后焊补; 2、采用工业修补剂; 3、如在重要面,报废重铸。
第16页/共28页
4、防止方法: 1、优化工艺设计,合理设置浇注系统; 2、考虑使用保温冒口、发热冒口; 3、优化铸件结构设计; 4、模拟分析(CAE); 5、调整成份; 6、控制炉料.
第17页/共28页
5、补救措施: 1、轻者焊补或采用工业修补剂; 2、重者报废重铸.
第18页/共28页
2.夹砂
的不同大小、形状的 孔洞缺陷的总称
缩孔 缩松
形状不规则,孔壁粗糙,常伴有粗大 树枝晶.夹杂物.裂纹等缺陷;
是细小的分散缩孔,断口呈海绵状;
疏松(显微缩松) 不作严格区分;
第3页/共28页
气 孔
第4页/共28页
针孔
2、裂纹、冷隔类缺陷
定义
缺陷名 称
特征
宏观(肉眼、PT、R T、MT、UT)或微 观(显微镜)判断发现 有开裂状纹络
1、铸件内部裂纹可采用超声波探伤(UT)、 磁粉探伤(MT)或射线探伤法(RT)进行检验; 2、铸件表面的裂纹可采用染色探伤法(PT)来 帮助确定,大部份是肉眼可直接发现的。
第24页/共28页
3、形成原因:
1、铸件结构或浇注系统设计不合理壁厚相差悬殊, 过渡圆角小; 2、铸造合金中有害元素(P、S等)超标,珠光体 元素过量; 3、铸件开箱过早,冷却过快; 4、合金收缩率大; 5、肋板设计不合理。
XX第二章铸造铸造工艺设计

PPT文档演模板
XX第二章铸造铸造工艺设计
PPT文档演模板
XX第二章铸造铸造工艺设计
2、应尽量减少使用活块
PPT文档演模板
XX第二章铸造铸造工艺设计
PPT文档演模板
XX第二章铸造铸造工艺设计
3、铸件内腔设计--应尽量不用或少用型芯
•实例1
•实例2
PPT文档演模板
XX第二章铸造铸造工艺设计
铸件内腔设计
➢影响因素:造型方式;合金种类;铸件尺寸;加工面与基准面距离;浇注位置等。 ➢一般查手册。 ➢表示方法:
PPT文档演模板
XX第二章铸造铸造工艺设计
(1) 机加工余量与最小铸出孔:
➢在铸件上为切削加工而加大的尺寸称为机械加工余量。 ➢加工余量必须认真选取,余量过大,切削加工费工,且浪费金属材料;余 量过小,制品会因残留黑皮而报废,或者,因铸件表层过硬 而加速刀具磨损。
应使铸件有最少的分型面,并尽量做到只 有一个分型面 这是因为:①多一个分型面多 一份误差,使精度下降;② 分型面多,造型工 时大,生产率下降;③机器造型只能两箱造型, 故分型面多,不能进行大批量生产。
PPT文档演模板
XX第二章铸造铸造工艺设计
•b •零件图---三通分型面的确定 •b
•a
•实例1
•c
➢影响因素:造型方式;合金种类;铸件尺寸;加工面与基准面距离;浇注位置等。 ➢一般查手册。
PPT文档演模板
XX第二章铸造铸造工艺设计
§ 铸孔及铸槽 铸件上的孔和槽类这部分结构是否铸出,取决于工 艺的可行性和必要性。
▪ 孔处理:最小孔直径和经济性原则。 § 一般来说,尺寸较小的孔不铸出反而经济。
设计时查手册。
PPT文档演模板
铸造工艺介绍ppt课件.ppt

胶)的池中并待乾,使以蜡制的复制品覆上一层陶瓷外膜,一直 重复步骤直到外膜足以支持铸造过程(约1/4寸到1/8寸),然后熔 解模型中的蜡,并抽离铸模。对铸模多次加以高温焙烧,增强硬 度浇入熔融物质凝固冷却后形成铸件的铸造方法。
2014-8-28
9
病原体侵入机体,消弱机体防御机能 ,破坏 机体内 环境的 相对稳 定性, 且在一 定部位 生长繁 殖,引 起不同 程度的 病理生 理过程
铸造简介
《考工记》是中国战国时期记述官营手工业各工种规范和制造工艺的文献。 这部著作记述了齐国关于手工业各个工种的设计规范和制造工艺。
《考工记》中记载了六种器物的不同含锡量,称之为“六齐”。
合金名称 钟鼎之齐 斧斤之齐 戈戬之齐 大刃之齐 削杀矢之齐 鉴燧之齐
含铜比例 5╱6 4╱5 3╱4 2╱3 3╱5 1╱2
14
病原体侵入机体,消弱机体防御机能 ,破坏 机体内 环境的 相对稳 定性, 且在一 定部位 生长繁 殖,引 起不同 程度的 病理生 理过程
浇注位置的选择原则
①铸件的重要加工面应朝下或位于侧面 ②铸件宽大平面应朝下 ③面积较大的薄壁部分应置于铸型下部或垂直 ④易形成缩孔的铸件,较厚部分置于上部或侧面 ⑤应尽量减少型芯的数量 ⑥要便于安放型芯、固定和排气
在高压作用下,使液态或半液态金属以较高的速度充填压铸 型(压铸模具)型腔,并在压力下成型和凝固而获得铸件的方法。 2.4离心铸造
离心铸造是将液体金属注入高速旋转的铸型内,使金属液在 离心力的作用下充满铸型和形成铸件的技术和方法。
2014-8-28
10
病原体侵入机体,消弱机体防御机能 ,破坏 机体内 环境的 相对稳 定性, 且在一 定部位 生长繁 殖,引 起不同 程度的 病理生 理过程
2014-8-28
9
病原体侵入机体,消弱机体防御机能 ,破坏 机体内 环境的 相对稳 定性, 且在一 定部位 生长繁 殖,引 起不同 程度的 病理生 理过程
铸造简介
《考工记》是中国战国时期记述官营手工业各工种规范和制造工艺的文献。 这部著作记述了齐国关于手工业各个工种的设计规范和制造工艺。
《考工记》中记载了六种器物的不同含锡量,称之为“六齐”。
合金名称 钟鼎之齐 斧斤之齐 戈戬之齐 大刃之齐 削杀矢之齐 鉴燧之齐
含铜比例 5╱6 4╱5 3╱4 2╱3 3╱5 1╱2
14
病原体侵入机体,消弱机体防御机能 ,破坏 机体内 环境的 相对稳 定性, 且在一 定部位 生长繁 殖,引 起不同 程度的 病理生 理过程
浇注位置的选择原则
①铸件的重要加工面应朝下或位于侧面 ②铸件宽大平面应朝下 ③面积较大的薄壁部分应置于铸型下部或垂直 ④易形成缩孔的铸件,较厚部分置于上部或侧面 ⑤应尽量减少型芯的数量 ⑥要便于安放型芯、固定和排气
在高压作用下,使液态或半液态金属以较高的速度充填压铸 型(压铸模具)型腔,并在压力下成型和凝固而获得铸件的方法。 2.4离心铸造
离心铸造是将液体金属注入高速旋转的铸型内,使金属液在 离心力的作用下充满铸型和形成铸件的技术和方法。
2014-8-28
10
病原体侵入机体,消弱机体防御机能 ,破坏 机体内 环境的 相对稳 定性, 且在一 定部位 生长繁 殖,引 起不同 程度的 病理生 理过程
6铸造工艺基础.pptx

金属液在冷凝过程中,其液态收缩和凝固过程若得不到有效补充,铸件将 产生缩孔或松动缺陷。
铸件的凝固过程:
在铸件的凝固过程中, 其截面一般存在三个区 域,即液相区、凝固区、 固相区。对铸件质量影 响较大的主要是液相和 固相并存的凝固区的宽 窄。铸件的凝固方式就 是依据凝固区的宽窄来 划分的。
凝固方式有:
2.1 铸造工艺基础
什么是金属的液态成形:
即将液态金属浇入与零件形状相适应的铸型空腔中,待其冷却凝固, 以获得毛坯或零件的工艺方法,亦称铸造.
金属的液态成形的作用:
金属的液态成形是制造毛坯、零件的重要方法之一。按铸型材料的 不同,金属液态成形可分为砂型铸造和特种铸造(包括压力铸造、金属型 铸造等).其中砂型铸造是最基本的液态成形方法,所生产的铸件要占铸 件总量的80%以上.
合金的收缩
合金的收缩的过程:
合金从液态冷却至室温的过程中,其体积或尺寸缩减的 现象。合金的收缩给液态成形工艺带来许多困难,会造成许 多铸造缺陷。(如:缩孔、缩松、裂纹、变形等)。
合金收缩的三个阶段
缩孔与缩松的形成
液态合金在冷凝过程中,若其液态收缩和凝固收缩所减少的体积得不到有效补 充,则铸件最后凝固的部位形成空洞,按空洞大小、分布,可分为缩孔和缩松。
缩孔与缩松的形成演示
判断缩孔出现的方法
A等温线法
B内截圆法
消除缩孔和缩松的方法
原理
定向凝固原则
是铸件让远离冒口的地方先凝 固,靠近冒口的地方次凝固, 最后才是冒口本身凝固。实现 以厚补薄,将缩孔转移到冒口 中去。
方法
合理布置内浇道及确定浇铸工艺。 合理应用冒口、冷铁和补贴等工艺措施。
解决缩孔的方法演示: 冒口和冷铁
缩孔的形成: 纯金属、共晶成分和凝固温度范围窄的合金,浇注后在型腔内是由表
铸件的凝固过程:
在铸件的凝固过程中, 其截面一般存在三个区 域,即液相区、凝固区、 固相区。对铸件质量影 响较大的主要是液相和 固相并存的凝固区的宽 窄。铸件的凝固方式就 是依据凝固区的宽窄来 划分的。
凝固方式有:
2.1 铸造工艺基础
什么是金属的液态成形:
即将液态金属浇入与零件形状相适应的铸型空腔中,待其冷却凝固, 以获得毛坯或零件的工艺方法,亦称铸造.
金属的液态成形的作用:
金属的液态成形是制造毛坯、零件的重要方法之一。按铸型材料的 不同,金属液态成形可分为砂型铸造和特种铸造(包括压力铸造、金属型 铸造等).其中砂型铸造是最基本的液态成形方法,所生产的铸件要占铸 件总量的80%以上.
合金的收缩
合金的收缩的过程:
合金从液态冷却至室温的过程中,其体积或尺寸缩减的 现象。合金的收缩给液态成形工艺带来许多困难,会造成许 多铸造缺陷。(如:缩孔、缩松、裂纹、变形等)。
合金收缩的三个阶段
缩孔与缩松的形成
液态合金在冷凝过程中,若其液态收缩和凝固收缩所减少的体积得不到有效补 充,则铸件最后凝固的部位形成空洞,按空洞大小、分布,可分为缩孔和缩松。
缩孔与缩松的形成演示
判断缩孔出现的方法
A等温线法
B内截圆法
消除缩孔和缩松的方法
原理
定向凝固原则
是铸件让远离冒口的地方先凝 固,靠近冒口的地方次凝固, 最后才是冒口本身凝固。实现 以厚补薄,将缩孔转移到冒口 中去。
方法
合理布置内浇道及确定浇铸工艺。 合理应用冒口、冷铁和补贴等工艺措施。
解决缩孔的方法演示: 冒口和冷铁
缩孔的形成: 纯金属、共晶成分和凝固温度范围窄的合金,浇注后在型腔内是由表
铸造工艺设计 ppt课件

图为起重臂分型面的选择,按图 (a)分型,必须采
用挖砂造型;采用图(b)方案分开,可采用分模造型,
使造型工艺简化。
ppt课件
12
轮形铸件在批量不大
的生产条件下,多采用三
箱造型;但在大批量生产
条件下,采用机器造型时,
需采用环状型芯。
ppt课件
13
避免使用活块
未延伸凸台
延伸凸台
如图(a)所示凸台均妨碍起模,必须采用活块或增
ppt课件
18
拔模斜度---为便于起模,凡垂直于分型面的立壁在制 造模型时必需留拔模斜度。
ppt课件
19
型芯头---型芯端头的延伸部位,芯头须留有一定斜 度。
最小铸出孔及槽---铸件的孔、槽是否铸出,应从工 艺、质量及经济上考虑。较大的孔、槽应当铸出, 以减少切削加工工时,节约金属材料,同时也可减 小铸件上的热节;孔、槽较小而壁较厚,则不易铸 出,直接加工。
ppt课件
9
床身铸件pp的t课件分型方案
10
应尽量减少分型面的数ppt量课件
铸件图所示的三通铸件 其内腔必须采用一个T字 型芯来形成;
当中心线ab呈垂直时, 铸型必须有三个分型面;
当中心线cd呈垂直时, 铸型有两个分型面,
当中心线ab与cd都呈水 平位置时,铸型只有一个 分型面。
11
分型面应尽量平直
+3 +3
10 30
ø66
+3
非加工表面拔摸斜度30’~1o
2oபைடு நூலகம்
铸造圆角R3~5
收缩率1%
铸钢件表面粗糙、变形较大,其加工余量应比铸铁件大;
有色合金铸件表面较光洁、平整,其加工余量要小些;
铸造工艺设计培训.pptx

它是制造模样和铸型,进行生产准备 和铸件检验的依据——基本工艺文件 。
铸造工艺设计是根据铸件结构特
点、技术要求、生产批量、生产条 件等,确定铸造方案和工艺参数, 绘制图样和标注符号,编制工艺卡 和工艺规范等。
1.浇注位置的选择原则
浇注位置是指浇注时铸件在铸型中 所处的空间位置。
选择正确与否,对铸件质量影响很大 。 选择时应考虑以下原则:
,砂芯形状、数量及
芯头大小等
是制造模样、模底板 、芯盒等工装以及进行 生产准备和验收的依据
适用于各种批量的生 产
①产品零件的技术条件 和结构工艺性分析
②选择铸造及造型方法 ③确定浇注位置和分型
面 ④选用工艺参数 ⑤设计浇冒口、冷铁和
铸肋 ⑥型芯设计
铸 件 图
把经过铸造工艺设计后 ,改变了零件形状、尺 寸的地方都反映在铸件 图上
⑥使型腔和主要型芯位于下箱
使型腔和主要芯位于下箱,便于下 芯、合型和检查型腔尺寸。
3.铸造工艺参数的确定
铸造工艺参数包括收缩余量、 加工余量、起模斜度、铸造圆角 、芯头、芯座等。
①收缩余量:
为了补偿收缩,模样比铸件图纸尺寸 增大的数值称收缩余量。收缩余量的大小 与铸件尺寸大小、结构的复杂程度和铸造 合金的线收缩率有关,常常以铸件线收缩 率表示:
零件上的孔与糟是否铸出,应考虑 工艺上的可行性和使用上的必要性。
一般说来,较大的孔与槽应铸出, 以节约金属、减少切削加工工时,同 时可以减小铸件的热节;较小的孔, 尤其是位置精度要求高的孔、槽则不 必铸出,留待机加工反而更经济。( 表1-3)
③起模斜度
为使模样容易地从铸型中取出或型芯 自芯盒中脱出,平行于起模方向在模样或 芯盒壁上的斜度,称为起模斜度。
铸造工艺设计是根据铸件结构特
点、技术要求、生产批量、生产条 件等,确定铸造方案和工艺参数, 绘制图样和标注符号,编制工艺卡 和工艺规范等。
1.浇注位置的选择原则
浇注位置是指浇注时铸件在铸型中 所处的空间位置。
选择正确与否,对铸件质量影响很大 。 选择时应考虑以下原则:
,砂芯形状、数量及
芯头大小等
是制造模样、模底板 、芯盒等工装以及进行 生产准备和验收的依据
适用于各种批量的生 产
①产品零件的技术条件 和结构工艺性分析
②选择铸造及造型方法 ③确定浇注位置和分型
面 ④选用工艺参数 ⑤设计浇冒口、冷铁和
铸肋 ⑥型芯设计
铸 件 图
把经过铸造工艺设计后 ,改变了零件形状、尺 寸的地方都反映在铸件 图上
⑥使型腔和主要型芯位于下箱
使型腔和主要芯位于下箱,便于下 芯、合型和检查型腔尺寸。
3.铸造工艺参数的确定
铸造工艺参数包括收缩余量、 加工余量、起模斜度、铸造圆角 、芯头、芯座等。
①收缩余量:
为了补偿收缩,模样比铸件图纸尺寸 增大的数值称收缩余量。收缩余量的大小 与铸件尺寸大小、结构的复杂程度和铸造 合金的线收缩率有关,常常以铸件线收缩 率表示:
零件上的孔与糟是否铸出,应考虑 工艺上的可行性和使用上的必要性。
一般说来,较大的孔与槽应铸出, 以节约金属、减少切削加工工时,同 时可以减小铸件的热节;较小的孔, 尤其是位置精度要求高的孔、槽则不 必铸出,留待机加工反而更经济。( 表1-3)
③起模斜度
为使模样容易地从铸型中取出或型芯 自芯盒中脱出,平行于起模方向在模样或 芯盒壁上的斜度,称为起模斜度。
ch06铸造工艺设计124页PPT

合金类别 铸件内壁比外壁厚度应
减少的相对值/%
铸铁 铸钢 铸铝 铸铜 10~20 20~30 10~20 15~20
所谓铸件壁厚均匀性,是为了使铸件各处的冷却速度相近, 并非要求铸件所有的壁厚完全相同。铸件的外壁、内壁和筋 的厚度比约为: 1:0.8:0.6
(4)铸件壁的过渡和连接
通常情况下,铸件壁的厚度并不完全一致。因此,在壁 的过渡处应参考表中壁的过渡形式和尺寸进行设计。
(1) 机加工余量 造型方式;合金种类;铸件尺寸;加工面与基准面距离;
浇注位置等。一般查手册。孔处理:最小孔直径和经济性原 则。在铸件上为切削加工而加大的尺寸称为机械加工余量。 加工余量必须认真选取,余量过大,切削加工费工,且浪费 金属材料;余量过小,制品会因残留黑皮而报废,或者,因 铸件表层过硬 而加速刀具磨损。
设计肋时,要尽量分散和减少热节点,避免多条肋互相 交叉,肋与肋和肋与壁的连接处要有圆角过渡,垂直于 分型面的肋应有铸造斜度。
除此之外,应考虑:应用肋提高铸件品质和载荷性能。 大平面铸件,按原设计,在浇注时因金属液的烘烤,平 面A处砂型膨胀较大易裂开脱落,产生夹砂类缺陷。增 加肋后不易产生夹砂类缺陷。
砂型铸造铸铁件的最小壁厚/mm
铸件种类
灰铸铁 孕育铸铁 球墨铸铁
碳素钢 低合金结构钢
高锰钢 不锈钢 耐热钢
<200
3~4 5~6 3~4
8 8~9 8~9 8~10 8~10
铸件最大轮廓尺寸
200~400
400~800
800~1250
4~5 6~8 4~8
9 9~10
10 10~12 10~12
5~6 8~10 8~10
(a)不合理的
(b)合理的
铸造工艺学习.pptx
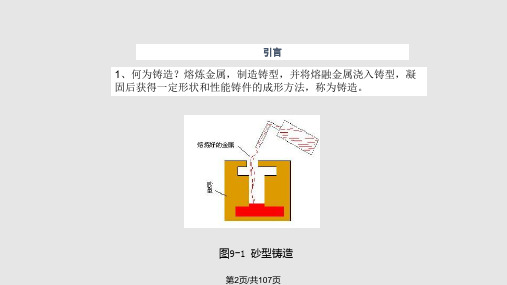
(3)铸件的变形和防止 铸件的变形包括铸件凝固后所发生的变形以及随后的切削 加工变形。防止铸件变形有以下几种方法: a) 采用反变形法 可在模样上做出与铸件变形量相等而方 向相反的预变形量来抵消铸件的变形,此种方法称为反变 形法。 b) 进行去应力退火 铸件机加工之前应先进行去应力退火, 以稳定铸件尺寸,降低切削加工变形程度。 c) 设置工艺肋 为了防止铸件的铸态变形,可在容易变形 的部位设置工艺肋。
图9-8 定向凝固原则
第18页/共107页
b)合理确定铸件的浇注位置、内浇道位置及浇注工艺 浇 注位置的选择应服从定向凝固原则;内浇道应开设在铸件 的厚壁处或靠近冒口;要合理选择浇注温度和浇注速度, 在不增加其它缺陷的前提下,应尽量降低浇注温度和浇注 速度。
第19页/共107页
2. 铸造应力、变形和裂纹 在铸件的凝固以及以后的冷却过程中,随温度的不断降低,收缩 不断发生,如果这种收缩受到阻碍,就会在铸件内产生应力,引 起变形或开裂,这种缺陷的产生,将严重影响铸件的质量。 (1) 铸造应力的产生 铸造应力按其产生的原因可分为三种: a)热应力 铸件在凝固和冷却过程中,不同部位由于不均衡的收 缩而引起的应力。 b)固态相变应力 铸件由于固态相变,各部分体积发生不均衡变 化而引起的应力。 c)收缩应力 铸件在固态收缩时,因受到铸型、型芯、浇冒口、 箱挡等外力的阻碍而产生的应力。 铸件铸出后存在于铸件不同部位的内应力称为残留应力。
•(三) 影响合金收缩的因素 1. 化学成分 不同成分的合金其收缩率一般也不相同。在常用铸造合 金中铸刚的收缩最大,灰铸铁最小。 2. 浇注温度 合金浇注温度越高,过热度越大,液体收缩越大。 3. 铸件结构与铸型条件 铸件冷却收缩时,因其形状、尺寸的不同, 各部分的冷却速度不同,导致收缩不一致,且互相阻碍,又加之铸 型和型芯对铸件收缩的阻力,故铸件的实际收缩率总是小于其自由 收缩率。这种阻力越大,铸件的实际收缩率就越小。Biblioteka 图9-3 不同结晶特征的合金的流动性
铸造加工技术.pptx

低压铸造、连续铸/共190页
第5页/共190页
❖ 铸造是历史上最悠久的一 种工艺,在我国已有6000多 年历史了。从殷商时期就有灿 烂的青铜器铸造技术。河南安 阳出土的殷朝祭器司母戊鼎, 重达700多公斤,长、高都超 过1m(见右图),四周饰有 精美的蟠龙纹及饕餮(古代传 说中的一种凶恶的野兽)。
型砂的组成
型(芯)砂是由原砂、旧砂(回用砂)、粘结剂、附加物和水组 成的。经混制后,符合造型要求的混合料。
第28页/共190页
1. 原砂 原砂是型(芯)砂的主体。最常用的是二氧化硅含量较高
的硅砂。还有一些不常用的特种砂(如锆砂、镁砂、橄榄石砂、 铬铁矿砂、钛铁矿砂、刚玉砂等。 2. 粘结材料
用来粘结砂粒的材料称为粘结剂。常用的有粘土、水玻璃、 油类粘结剂、合成树脂粘结剂等。目前使用最普遍的是粘土, 粘土分为铸造用粘土和铸造用膨润土。 3. 辅助材料
车床
铣床
刨床
第19页/共190页
磨床
(一)砂型铸造生产过程简介
铸造按生产方式不同,可分为砂型铸造和特种铸造。用砂型 铸造生产铸件的方法,目前约占铸件总产量的80% 以上。其 生产过程的工艺流程如图所示:
型砂配制
造型
烘型 金属熔炼
工装准备
合型
浇注
落砂清理
检验
芯砂配制
造芯
烘芯
第20页/共190页
(二)铸造生产的特点: (1)砂型铸造生产的优点
所谓辅助材料是指制造砂型(芯)过程中所用各种材料中 除原砂、粘结剂(如粘土、树脂、水玻璃等)、水之外的材料。 常用的辅助材料有煤粉、锯屑、石墨粉、滑石粉、重油和脱模 剂等。
第29页/共190页
(三)型(芯)砂的性能 生产中为了获得优质的铸件和良好的技术经济效果,要求型
第5页/共190页
❖ 铸造是历史上最悠久的一 种工艺,在我国已有6000多 年历史了。从殷商时期就有灿 烂的青铜器铸造技术。河南安 阳出土的殷朝祭器司母戊鼎, 重达700多公斤,长、高都超 过1m(见右图),四周饰有 精美的蟠龙纹及饕餮(古代传 说中的一种凶恶的野兽)。
型砂的组成
型(芯)砂是由原砂、旧砂(回用砂)、粘结剂、附加物和水组 成的。经混制后,符合造型要求的混合料。
第28页/共190页
1. 原砂 原砂是型(芯)砂的主体。最常用的是二氧化硅含量较高
的硅砂。还有一些不常用的特种砂(如锆砂、镁砂、橄榄石砂、 铬铁矿砂、钛铁矿砂、刚玉砂等。 2. 粘结材料
用来粘结砂粒的材料称为粘结剂。常用的有粘土、水玻璃、 油类粘结剂、合成树脂粘结剂等。目前使用最普遍的是粘土, 粘土分为铸造用粘土和铸造用膨润土。 3. 辅助材料
车床
铣床
刨床
第19页/共190页
磨床
(一)砂型铸造生产过程简介
铸造按生产方式不同,可分为砂型铸造和特种铸造。用砂型 铸造生产铸件的方法,目前约占铸件总产量的80% 以上。其 生产过程的工艺流程如图所示:
型砂配制
造型
烘型 金属熔炼
工装准备
合型
浇注
落砂清理
检验
芯砂配制
造芯
烘芯
第20页/共190页
(二)铸造生产的特点: (1)砂型铸造生产的优点
所谓辅助材料是指制造砂型(芯)过程中所用各种材料中 除原砂、粘结剂(如粘土、树脂、水玻璃等)、水之外的材料。 常用的辅助材料有煤粉、锯屑、石墨粉、滑石粉、重油和脱模 剂等。
第29页/共190页
(三)型(芯)砂的性能 生产中为了获得优质的铸件和良好的技术经济效果,要求型
最新1.3铸造工艺设计课件教学讲义ppt
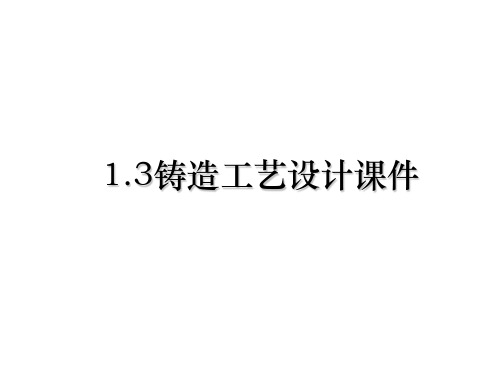
✓指合金液能充满型腔的最小厚度,小于最小壁 厚易产生浇不足、冷隔等缺陷。
✓铸件最小壁厚与 合金种类、铸件尺 寸等因素有关。
19
1.3 铸造工艺设计 铸件壁厚不易过厚 ✓ 过大的壁厚会引起铸件晶粒粗大,强度下降,
产生缩孔、缩松等缺陷
20
1.3 铸造工艺设计 ➢2、铸件壁厚尽量均匀 ✓壁厚不均易产生缩孔和缩松,内应力和变形、开 裂等缺陷。
30
1.3 铸造工艺设计
❖ 浇注位置选择原则 ➢ 重要面朝下 ➢ 大平面朝下 ➢ 薄壁部分置于铸型下部或使其处于垂直或 倾斜位置 ➢ 厚大部分朝上或侧面 ➢ 型芯少而稳定
31
1.3 铸造工艺设计 ➢ 重要面朝下 ✓ 铸件上部易产生砂眼、气孔、夹渣等缺陷,且晶
粒较粗大。重要加工面应朝下或位于侧面;重要 加工面有数个时,应将较大的平面朝下。
➢ 选择浇注系统类型。 ➢ 确定内交道在铸件上的位置、数目和金属液引入方
向。 ➢ 决定直浇道的位置和高度。 ➢ 计算浇注时间并核算金属上升速度。 ➢ 计算阻流截面积S阻。 ➢ 确定浇口比并计算各组员截面积。 ➢ 绘出浇注系统图。
42
1.3 铸造工艺设计 2.铸件分型面的选择 ✓ 指上、下、左、右砂型间的接触面,应能在保
简化内腔自带型芯
13
1.3 铸造工艺设计
框形与肋板结构
肋板与框架立体图
14
✓ 型芯在铸型中应支撑牢固
1.3 铸造工艺设计
内腔是否连通立体图 内腔连通不连通零件图
内腔连通不连通型芯放置
15
1.3 铸造工艺设计
✓ 增加型芯头或工艺孔,以固定型芯,同时便于 型芯固排清
封闭内腔立体图
封闭内腔零件图 封闭内腔型芯无法取出
➢ 浇口杯 ➢ 直浇道 ➢ 横浇道 ➢ 内浇道
✓铸件最小壁厚与 合金种类、铸件尺 寸等因素有关。
19
1.3 铸造工艺设计 铸件壁厚不易过厚 ✓ 过大的壁厚会引起铸件晶粒粗大,强度下降,
产生缩孔、缩松等缺陷
20
1.3 铸造工艺设计 ➢2、铸件壁厚尽量均匀 ✓壁厚不均易产生缩孔和缩松,内应力和变形、开 裂等缺陷。
30
1.3 铸造工艺设计
❖ 浇注位置选择原则 ➢ 重要面朝下 ➢ 大平面朝下 ➢ 薄壁部分置于铸型下部或使其处于垂直或 倾斜位置 ➢ 厚大部分朝上或侧面 ➢ 型芯少而稳定
31
1.3 铸造工艺设计 ➢ 重要面朝下 ✓ 铸件上部易产生砂眼、气孔、夹渣等缺陷,且晶
粒较粗大。重要加工面应朝下或位于侧面;重要 加工面有数个时,应将较大的平面朝下。
➢ 选择浇注系统类型。 ➢ 确定内交道在铸件上的位置、数目和金属液引入方
向。 ➢ 决定直浇道的位置和高度。 ➢ 计算浇注时间并核算金属上升速度。 ➢ 计算阻流截面积S阻。 ➢ 确定浇口比并计算各组员截面积。 ➢ 绘出浇注系统图。
42
1.3 铸造工艺设计 2.铸件分型面的选择 ✓ 指上、下、左、右砂型间的接触面,应能在保
简化内腔自带型芯
13
1.3 铸造工艺设计
框形与肋板结构
肋板与框架立体图
14
✓ 型芯在铸型中应支撑牢固
1.3 铸造工艺设计
内腔是否连通立体图 内腔连通不连通零件图
内腔连通不连通型芯放置
15
1.3 铸造工艺设计
✓ 增加型芯头或工艺孔,以固定型芯,同时便于 型芯固排清
封闭内腔立体图
封闭内腔零件图 封闭内腔型芯无法取出
➢ 浇口杯 ➢ 直浇道 ➢ 横浇道 ➢ 内浇道
铸造工艺设计注意问题PPT文档共65页
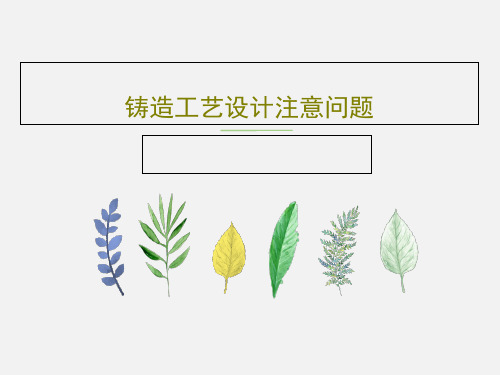
、死去何所道,托体同山阿。 57、春秋多佳日,登高赋新诗。 58、种豆南山下,草盛豆苗稀。晨兴 理荒秽 ,带月 荷锄归 。道狭 草木长 ,夕露 沾我衣 。衣沾 不足惜 ,但使 愿无违 。 59、相见无杂言,但道桑麻长。 60、迢迢新秋夕,亭亭月将圆。
61、奢侈是舒适的,否则就不是奢侈 。——CocoCha nel 62、少而好学,如日出之阳;壮而好学 ,如日 中之光 ;志而 好学, 如炳烛 之光。 ——刘 向 63、三军可夺帅也,匹夫不可夺志也。 ——孔 丘 64、人生就是学校。在那里,与其说好 的教师 是幸福 ,不如 说好的 教师是 不幸。 ——海 贝尔 65、接受挑战,就可以享受胜利的喜悦 。——杰纳勒 尔·乔治·S·巴顿
61、奢侈是舒适的,否则就不是奢侈 。——CocoCha nel 62、少而好学,如日出之阳;壮而好学 ,如日 中之光 ;志而 好学, 如炳烛 之光。 ——刘 向 63、三军可夺帅也,匹夫不可夺志也。 ——孔 丘 64、人生就是学校。在那里,与其说好 的教师 是幸福 ,不如 说好的 教师是 不幸。 ——海 贝尔 65、接受挑战,就可以享受胜利的喜悦 。——杰纳勒 尔·乔治·S·巴顿
- 1、下载文档前请自行甄别文档内容的完整性,平台不提供额外的编辑、内容补充、找答案等附加服务。
- 2、"仅部分预览"的文档,不可在线预览部分如存在完整性等问题,可反馈申请退款(可完整预览的文档不适用该条件!)。
- 3、如文档侵犯您的权益,请联系客服反馈,我们会尽快为您处理(人工客服工作时间:9:00-18:30)。
内腔或便于外形起模。
分块:便于操作、搬
运、烘干和简化芯盒。
共型芯:增加型芯稳定性、提高模
板和砂箱利用率。
§4-2 工艺参数的确定
铸造工艺参数的确定: 铸造工艺参数包括加工余
量、起模斜度、铸造圆角、芯 头、芯座、收缩余量等。
一、机械加工余量和铸孔
机械加工余量:在铸件上为切削 加工而加大的尺寸。
铸型中设置的一个储存金属液的空 腔作用,提供体收缩时所需的金属液。
对其进行补缩,防止产生缩孔、缩 松等(冒口清除)。
冒口的设置:铸件热节圆直径较大 的部位。
冒口尺寸计算:比例法。(表4-6)(图4-
18)
§4-4 铸造工艺设计
主要是画铸造工艺图、铸件毛坯图、 铸型装配图和编写工艺卡片等。 一般大量生产的定型产品、特殊重 要的单件生产的铸件,铸造工艺设计 订得细致,内容涉及较多。
余量过大,切削加工费工,且浪 费材料;
余量过小,制品会因残留黑皮而 报废,或因铸件表层过硬而加速 刀具磨损。
加工余量应根据铸件生产批量、 合金种类、造型方法、加工要 求、铸件的形状、尺寸及浇注 位置等来确定。
大量生产:机器造型,精度高,余 量小。 铸钢件:表面粗糙,余量比铸铁大 非铁合金:价贵,表面光滑,余量 小。
三、铸造圆角
防止在夹角处产生冲砂及裂纹; 圆角半径约为相交两壁平均厚度 的1/3~1/2。
四、铸造收缩率
铸件冷却后的尺寸比型腔尺寸 略为缩小,为保证铸件的应有 尺寸,模样尺寸必须比铸件放 大一个该合金的收缩率。
铸造收缩率K 表达式为:
灰铸铁:0.7%~1.0%; 铸造碳钢:1.3%~2.0%; 铝硅合金:0.8%~1.2%; 锡青铜:1.2%~1.4%。
如下表面致密。
车床床身的浇注位置
起重机卷扬筒的浇 注位置方案(采用 立式浇注)
2)铸件的大平面应朝下
大平面还常产生夹砂缺陷,故对平 板、圆盘类铸件,大平面应朝下。
3)面积较大的薄壁部分置于铸型下 部或使其处于垂直或倾斜位置。
防止铸件产生浇不足或冷隔等缺陷。
√
×
薄壁件的浇注位置
4)对于容易产生缩孔 的铸件,应使厚的部 分放在分型面的上部 或侧面,厚处直接安 放冒口,实现自下而 上的顺序凝固。
②改用方案II时,
可省去活块,仅在
A处稍加挖砂即可。
□大批量生产条件下,采用机器造 型,需要改用图中所示的环状型芯, 使铸型简化成只有一个分型面。
使用型芯减少分型面
2)尽量使铸件 全部或大部置于 同一砂箱,以保 证铸件精度。
车床床身铸件
3)尽量使型腔及主要型芯位于下型
便于造型、下芯、 合箱和检验铸件壁 厚。但下型型腔也 不宜过深,并尽量 避免使用吊芯和大 的吊砂。
第四章 铸造工艺设计
要求:①掌握铸造工艺方案的制定,
铸造工艺参数确定的原则;② 熟悉浇注系统的组成以及冒口的作用; ③了解冒口尺寸的计算方法。
重点:砂型铸造工艺图的绘制; 难点:浇注位置及分型面的选择。
砂型铸造工艺设计:
为获得好的铸件,减少工 作量,降低成本,合理制订铸 造工艺方案,绘制铸造工艺图。
√
×
2.分型面的选择原则
重要性:
①恰当与否会影响铸件质量; ②使制模、造型、造芯、合箱或清理 等工序复杂化; ③甚至还可增大切削加工的工作量。
1)便于起模,使造型工艺简化
尽量使分型面平直、数量少,避 免不必要的活块和型芯。 √
×
起重臂的分型面
√
□避免用活块。支架
注意:选择分型面的上述诸原则, 对于某个具体的铸件来说难以全面 满足,有时甚至互相矛盾。
因此,必须抓住主要矛盾、全面 考虑,至于次要矛盾,则应从工艺 措施上设法解决。
工艺设计步骤:
先定浇注位置,再选分型 面,在定分型面时,应尽可能 与浇注位置相一致。
三、砂芯形状、个数及分块
砂芯作用:形成铸件
五、芯头及芯座
型芯头可分为垂直芯头和水平芯 头两大类。
§4-3 浇、冒口系统
一、浇注系统 引导金属液流入铸型型腔的一系 列通道的总称。 组成:浇口杯(外浇口)、直浇 道、横浇道、内浇道。
1.尺寸的确定:根据铸件形状、尺寸, 查表确定。
2.常见浇注系统的类型
3.内浇道与铸件型腔连接位置的选择
二、冒口
加工表面上的起模斜度应结合加工 余量直接表示出,而不加工表面上的 斜度(结构斜度)仅需用文字注明。
起模斜度的大小:根据立壁的高度、
造型方法和模样材料来确定。
立壁愈高,斜度愈小;外壁斜度比内 壁小;机器造型的一般比手工造型的 小;金属模斜度比木模小。
具体数据可查有关手册。
一般外壁为15º-3º,内壁为3º-10°。
(表4-2) (表4-3)——说明
铸件的孔、槽是否铸出,不仅取 决于工艺上的可能性,还须考虑其 必要性。
较大的孔、槽应铸出,可减小加 工工时,减小热节;
较小的孔、槽不必铸出,留待加 工更经济。
不加工的特形孔、价格较贵的非 铁金属铸孔,尽量铸出。
二、起模斜度(拔模斜度)
使模型样(或型芯)易于从砂型 (或芯盒)中取出,应在模样或芯盒 的起模方向带有一定的斜度。
支座的铸造工艺图、模样图及合型图
一、工艺符号及其表示方法(表4-1)
二、浇注位置及分型面的选择
浇注位置:浇注时铸件在砂型中
所处的空间位置。
分型面:砂箱间的接触表面。 重要性:影响铸件质量、工艺难
易程度。
1.浇注位置的选择原则
1)铸件的重要加工面 应朝下或位于侧面。
上表面易产生砂眼、
气孔、夹渣等缺陷,不
§4-1 铸造工艺方案的确定
铸造工艺方案:
①选择铸件的浇注位置及分型面。 ②型芯的数量、形状及其固定方法。 ③确定工艺参数:加工余量、起模斜
度、圆角、收缩率。 ④浇冒口、冷铁形状、尺寸及其布置。
铸造工艺图:
在零件图上用各种工艺符号 表示出铸造工艺方案的图形。
作用:
它是制造模样和铸型,进行 生产准备和铸件检验的依据(基 本工艺文件)。
单件、小批生产的一般性产品, 铸造工艺设计内容可以简化。
在最简单的情况下,只须绘制一 张铸造工艺图即可。
铸造工艺设计的内容和一般程序
以C6140车 床进给箱体 为例分析毛 坯的铸造工 艺方案如下:
质量约 35Kg。
车床进给箱体零件图
该零件没有特殊质量要求的表面,仅 要求尽量保证基准面D不得有明显铸 造缺陷,以便进行定位。
分块:便于操作、搬
运、烘干和简化芯盒。
共型芯:增加型芯稳定性、提高模
板和砂箱利用率。
§4-2 工艺参数的确定
铸造工艺参数的确定: 铸造工艺参数包括加工余
量、起模斜度、铸造圆角、芯 头、芯座、收缩余量等。
一、机械加工余量和铸孔
机械加工余量:在铸件上为切削 加工而加大的尺寸。
铸型中设置的一个储存金属液的空 腔作用,提供体收缩时所需的金属液。
对其进行补缩,防止产生缩孔、缩 松等(冒口清除)。
冒口的设置:铸件热节圆直径较大 的部位。
冒口尺寸计算:比例法。(表4-6)(图4-
18)
§4-4 铸造工艺设计
主要是画铸造工艺图、铸件毛坯图、 铸型装配图和编写工艺卡片等。 一般大量生产的定型产品、特殊重 要的单件生产的铸件,铸造工艺设计 订得细致,内容涉及较多。
余量过大,切削加工费工,且浪 费材料;
余量过小,制品会因残留黑皮而 报废,或因铸件表层过硬而加速 刀具磨损。
加工余量应根据铸件生产批量、 合金种类、造型方法、加工要 求、铸件的形状、尺寸及浇注 位置等来确定。
大量生产:机器造型,精度高,余 量小。 铸钢件:表面粗糙,余量比铸铁大 非铁合金:价贵,表面光滑,余量 小。
三、铸造圆角
防止在夹角处产生冲砂及裂纹; 圆角半径约为相交两壁平均厚度 的1/3~1/2。
四、铸造收缩率
铸件冷却后的尺寸比型腔尺寸 略为缩小,为保证铸件的应有 尺寸,模样尺寸必须比铸件放 大一个该合金的收缩率。
铸造收缩率K 表达式为:
灰铸铁:0.7%~1.0%; 铸造碳钢:1.3%~2.0%; 铝硅合金:0.8%~1.2%; 锡青铜:1.2%~1.4%。
如下表面致密。
车床床身的浇注位置
起重机卷扬筒的浇 注位置方案(采用 立式浇注)
2)铸件的大平面应朝下
大平面还常产生夹砂缺陷,故对平 板、圆盘类铸件,大平面应朝下。
3)面积较大的薄壁部分置于铸型下 部或使其处于垂直或倾斜位置。
防止铸件产生浇不足或冷隔等缺陷。
√
×
薄壁件的浇注位置
4)对于容易产生缩孔 的铸件,应使厚的部 分放在分型面的上部 或侧面,厚处直接安 放冒口,实现自下而 上的顺序凝固。
②改用方案II时,
可省去活块,仅在
A处稍加挖砂即可。
□大批量生产条件下,采用机器造 型,需要改用图中所示的环状型芯, 使铸型简化成只有一个分型面。
使用型芯减少分型面
2)尽量使铸件 全部或大部置于 同一砂箱,以保 证铸件精度。
车床床身铸件
3)尽量使型腔及主要型芯位于下型
便于造型、下芯、 合箱和检验铸件壁 厚。但下型型腔也 不宜过深,并尽量 避免使用吊芯和大 的吊砂。
第四章 铸造工艺设计
要求:①掌握铸造工艺方案的制定,
铸造工艺参数确定的原则;② 熟悉浇注系统的组成以及冒口的作用; ③了解冒口尺寸的计算方法。
重点:砂型铸造工艺图的绘制; 难点:浇注位置及分型面的选择。
砂型铸造工艺设计:
为获得好的铸件,减少工 作量,降低成本,合理制订铸 造工艺方案,绘制铸造工艺图。
√
×
2.分型面的选择原则
重要性:
①恰当与否会影响铸件质量; ②使制模、造型、造芯、合箱或清理 等工序复杂化; ③甚至还可增大切削加工的工作量。
1)便于起模,使造型工艺简化
尽量使分型面平直、数量少,避 免不必要的活块和型芯。 √
×
起重臂的分型面
√
□避免用活块。支架
注意:选择分型面的上述诸原则, 对于某个具体的铸件来说难以全面 满足,有时甚至互相矛盾。
因此,必须抓住主要矛盾、全面 考虑,至于次要矛盾,则应从工艺 措施上设法解决。
工艺设计步骤:
先定浇注位置,再选分型 面,在定分型面时,应尽可能 与浇注位置相一致。
三、砂芯形状、个数及分块
砂芯作用:形成铸件
五、芯头及芯座
型芯头可分为垂直芯头和水平芯 头两大类。
§4-3 浇、冒口系统
一、浇注系统 引导金属液流入铸型型腔的一系 列通道的总称。 组成:浇口杯(外浇口)、直浇 道、横浇道、内浇道。
1.尺寸的确定:根据铸件形状、尺寸, 查表确定。
2.常见浇注系统的类型
3.内浇道与铸件型腔连接位置的选择
二、冒口
加工表面上的起模斜度应结合加工 余量直接表示出,而不加工表面上的 斜度(结构斜度)仅需用文字注明。
起模斜度的大小:根据立壁的高度、
造型方法和模样材料来确定。
立壁愈高,斜度愈小;外壁斜度比内 壁小;机器造型的一般比手工造型的 小;金属模斜度比木模小。
具体数据可查有关手册。
一般外壁为15º-3º,内壁为3º-10°。
(表4-2) (表4-3)——说明
铸件的孔、槽是否铸出,不仅取 决于工艺上的可能性,还须考虑其 必要性。
较大的孔、槽应铸出,可减小加 工工时,减小热节;
较小的孔、槽不必铸出,留待加 工更经济。
不加工的特形孔、价格较贵的非 铁金属铸孔,尽量铸出。
二、起模斜度(拔模斜度)
使模型样(或型芯)易于从砂型 (或芯盒)中取出,应在模样或芯盒 的起模方向带有一定的斜度。
支座的铸造工艺图、模样图及合型图
一、工艺符号及其表示方法(表4-1)
二、浇注位置及分型面的选择
浇注位置:浇注时铸件在砂型中
所处的空间位置。
分型面:砂箱间的接触表面。 重要性:影响铸件质量、工艺难
易程度。
1.浇注位置的选择原则
1)铸件的重要加工面 应朝下或位于侧面。
上表面易产生砂眼、
气孔、夹渣等缺陷,不
§4-1 铸造工艺方案的确定
铸造工艺方案:
①选择铸件的浇注位置及分型面。 ②型芯的数量、形状及其固定方法。 ③确定工艺参数:加工余量、起模斜
度、圆角、收缩率。 ④浇冒口、冷铁形状、尺寸及其布置。
铸造工艺图:
在零件图上用各种工艺符号 表示出铸造工艺方案的图形。
作用:
它是制造模样和铸型,进行 生产准备和铸件检验的依据(基 本工艺文件)。
单件、小批生产的一般性产品, 铸造工艺设计内容可以简化。
在最简单的情况下,只须绘制一 张铸造工艺图即可。
铸造工艺设计的内容和一般程序
以C6140车 床进给箱体 为例分析毛 坯的铸造工 艺方案如下:
质量约 35Kg。
车床进给箱体零件图
该零件没有特殊质量要求的表面,仅 要求尽量保证基准面D不得有明显铸 造缺陷,以便进行定位。