矿用用回柱绞车
回柱绞车结构及技术标准
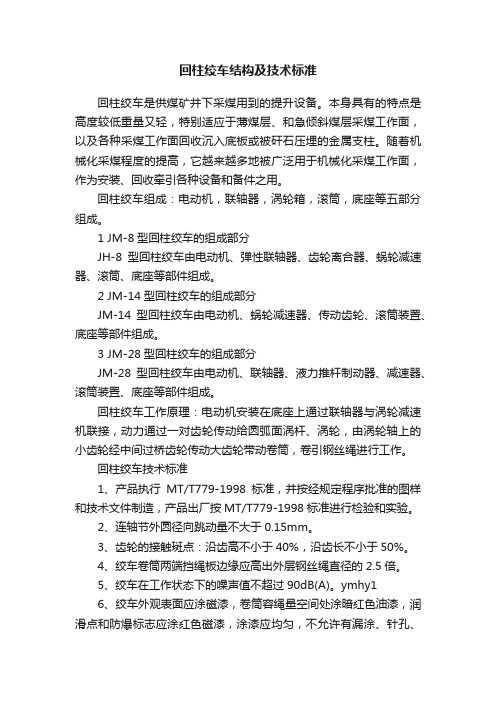
回柱绞车结构及技术标准回柱绞车是供煤矿井下采煤用到的提升设备。
本身具有的特点是高度较低重量又轻,特别适应于薄煤层、和急倾斜煤层采煤工作面,以及各种采煤工作面回收沉入底板或被矸石压埋的金属支柱。
随着机械化采煤程度的提高,它越来越多地被广泛用于机械化采煤工作面,作为安装、回收牵引各种设备和备件之用。
回柱绞车组成:电动机,联轴器,涡轮箱,滚筒,底座等五部分组成。
1 JM-8型回柱绞车的组成部分JH-8型回柱绞车由电动机、弹性联轴器、齿轮离合器、蜗轮减速器、滚筒、底座等部件组成。
2 JM-14型回柱绞车的组成部分JM-14型回柱绞车由电动机、蜗轮减速器、传动齿轮、滚筒装置、底座等部件组成。
3 JM-28型回柱绞车的组成部分JM-28型回柱绞车由电动机、联轴器、液力推杆制动器、减速器、滚筒装置、底座等部件组成。
回柱绞车工作原理:电动机安装在底座上通过联轴器与涡轮减速机联接,动力通过一对齿轮传动给圆弧面涡杆、涡轮,由涡轮轴上的小齿轮经中间过桥齿轮传动大齿轮带动卷筒,卷引钢丝绳进行工作。
回柱绞车技术标准1、产品执行MT/T779-1998标准,并按经规定程序批准的图样和技术文件制造,产品出厂按MT/T779-1998标准进行检验和实验。
2、连轴节外圆径向跳动量不大于0.15mm。
3、齿轮的接触斑点:沿齿高不小于40%,沿齿长不小于50%。
4、绞车卷筒两端挡绳板边缘应高出外层钢丝绳直径的2.5倍。
5、绞车在工作状态下的噪声值不超过90dB(A)。
ymhy16、绞车外观表面应涂磁漆,卷筒容绳量空间处涂暗红色油漆,润滑点和防爆标志应涂红色磁漆,涂漆应均匀,不允许有漏涂、针孔、气泡、裂纹、脱落、留痕等缺陷。
JH-5回柱绞车7、绞车出厂前进行正、反方向各15分钟的空运转实验,并符合一下要求:(1)运转平稳、无异常声响、无冲击性噪音。
山东中煤集团回柱绞车(2)所有连接件、紧固件连接应可靠,无松动现象,卷筒上的螺钉不得高出卷筒圆周表面。
调度绞车 回柱绞车
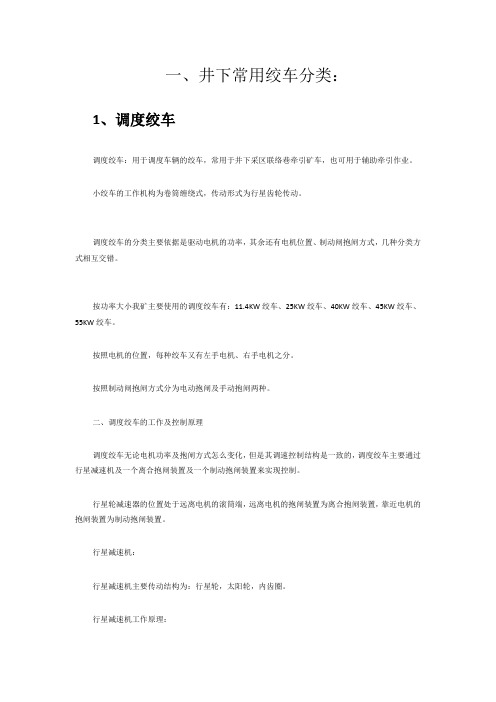
一、井下常用绞车分类:1、调度绞车调度绞车:用于调度车辆的绞车,常用于井下采区联络巷牵引矿车,也可用于辅助牵引作业。
小绞车的工作机构为卷筒缠绕式,传动形式为行星齿轮传动。
调度绞车的分类主要依据是驱动电机的功率,其余还有电机位置、制动闸抱闸方式,几种分类方式相互交错。
按功率大小我矿主要使用的调度绞车有:11.4KW绞车、25KW绞车、40KW绞车、45KW绞车、55KW绞车。
按照电机的位置,每种绞车又有左手电机、右手电机之分。
按照制动闸抱闸方式分为电动抱闸及手动抱闸两种。
二、调度绞车的工作及控制原理调度绞车无论电机功率及抱闸方式怎么变化,但是其调速控制结构是一致的,调度绞车主要通过行星减速机及一个离合抱闸装置及一个制动抱闸装置来实现控制。
行星轮减速器的位置处于远离电机的滚筒端,远离电机的抱闸装置为离合抱闸装置,靠近电机的抱闸装置为制动抱闸装置。
行星减速机:行星减速机主要传动结构为:行星轮,太阳轮,内齿圈。
行星减速机工作原理:由一个内齿环紧密结合於齿箱壳体上,环齿中心有一个自外部动力所驱动之太阳齿轮,介於两者之间有一组由4颗齿轮等分组合於托盘上之行星齿轮组,该组行星齿轮浮游於内齿环及太阳齿之间;行星减速机当电机驱动太阳齿时,可带动行星齿轮自转,并依循著内齿环之轨迹沿著中心公转,游星之旋转带动连结於托盘之出力轴输出动力。
绞车控制原理:电机与太阳轮直接相连,电机滚筒与组合于托盘上的行星齿轮组直接相连,当制动闸拉紧,离合闸松开时,电机带动太阳轮转动,行星轮组不动,行星轮组各齿轮转动从而带动内齿圈转动;当离合闸拉紧,制动闸松开时,电机带动太阳轮转动,内齿圈不动,行星轮组各齿轮转动,从而带动行星轮组托盘转动带动滚筒转动。
调度绞车操作方式:1、调度绞车的操作整个动作就是启动和关闭电动机及用手交替操纵两个刹车把。
2、在启动电动机时,滚筒上的制动闸把手应拉紧,离合闸把手应松开,这样滚筒不转动,仅大内齿轮回转。
3、缓缓压紧离合闸把,同时缓缓松开制动闸把,使滚筒慢转,平稳起动加速,压紧离合闸,松开制动闸,达到正常运行速度。
矿用调度绞车、回柱绞车规格型号
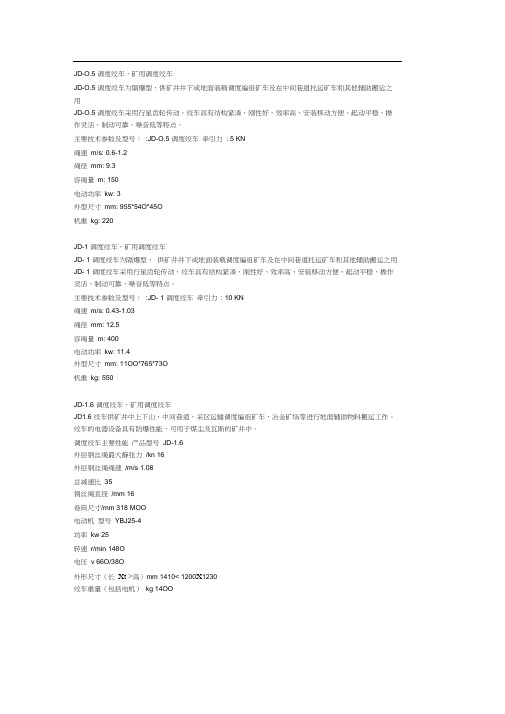
JD-O.5 调度绞车为隔爆型,供矿井井下或地面装载调度编组矿车及在中间巷道托运矿车和其他辅助搬运之用JD-O.5 调度绞车采用行星齿轮传动,绞车具有结构紧凑、刚性好、效率高、安装移动方便、起动平稳、操作灵活、制动可靠、噪音低等特点。
主要技术参数及型号::JD-O.5 调度绞车牵引力: 5 KN绳速m/s: 0.6-1.2绳径mm: 9.3容绳量m: 150电动功率kw: 3外型尺寸mm: 955*54O*45O机重kg: 220JD-1 调度绞车,矿用调度绞车JD- 1 调度绞车为隔爆型,供矿井井下或地面装载调度编组矿车及在中间巷道托运矿车和其他辅助搬运之用JD- 1 调度绞车采用行星齿轮传动,绞车具有结构紧凑、刚性好、效率高、安装移动方便、起动平稳、操作灵活、制动可靠、噪音低等特点。
主要技术参数及型号::JD- 1 调度绞车牵引力: 10 KN绳速m/s: 0.43-1.03绳径mm: 12.5容绳量m: 400电动功率kw: 11.4外型尺寸mm: 11OO*765*73O机重kg: 550JD-1.6 调度绞车,矿用调度绞车JD1.6 绞车供矿井中上下山,中间巷道,采区运输调度编组矿车,冶金矿场等进行地面辅助物料搬运工作。
绞车的电器设备具有防爆性能,可用于煤尘及瓦斯的矿井中。
调度绞车主要性能产品型号JD-1.6外层钢丝绳最大静张力/kn 16外层钢丝绳绳速/m/s 1.08总减速比35钢丝绳直径/mm 16卷筒尺寸/mm 318 MOO电动机型号YBJ25-4功率kw 25转速r/min 148O电压v 66O/38O外形尺寸(长Xt >高)mm 1410< 1200X1230绞车重量(包括电机)kg 14OOJD2.5 绞车供矿井中上下山,中间巷道,采区运输调度编组矿车,冶金矿场等进行地面辅助物料搬运工作。
绞车的电器设备具有防爆性能,可用于煤尘及瓦斯的矿井中。
调度绞车主要性能产品型号JD-2.5外层钢丝绳最大静张力/kn 25外层钢丝绳绳速/m/s 1.52总减速比40.1钢丝绳直径/mm 20卷筒尺寸/mm 450 X56O电动机型号YBJ40-4功率kw 40转速r/min 1480JD-4 调度绞车,矿用调度绞车JD-4 绞车供矿井中上下山,中间巷道,采区运输调度编组矿车,冶金矿场等进行地面辅助物料搬运工作绞车的电器设备具有防爆性能,可用于煤尘及瓦斯的矿井中。
矿用调度绞车、回柱绞车规格型号
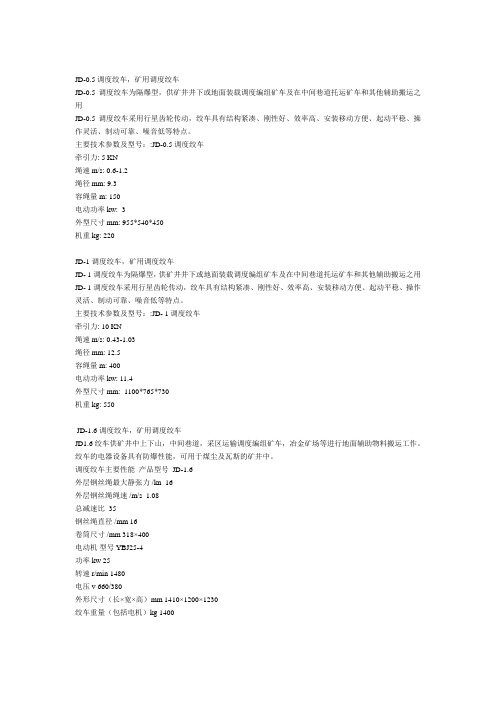
JD-0.5调度绞车,矿用调度绞车JD-0.5调度绞车为隔爆型,供矿井井下或地面装载调度编组矿车及在中间巷道托运矿车和其他辅助搬运之用JD-0.5调度绞车采用行星齿轮传动,绞车具有结构紧凑、刚性好、效率高、安装移动方便、起动平稳、操作灵活、制动可靠、噪音低等特点。
主要技术参数及型号::JD-0.5调度绞车牵引力: 5 KN绳速m/s: 0.6-1.2绳径mm: 9.3容绳量m: 150电动功率kw: 3外型尺寸mm: 955*540*450机重kg: 220JD-1调度绞车,矿用调度绞车JD- 1调度绞车为隔爆型,供矿井井下或地面装载调度编组矿车及在中间巷道托运矿车和其他辅助搬运之用JD- 1调度绞车采用行星齿轮传动,绞车具有结构紧凑、刚性好、效率高、安装移动方便、起动平稳、操作灵活、制动可靠、噪音低等特点。
主要技术参数及型号::JD- 1调度绞车牵引力: 10 KN绳速m/s: 0.43-1.03绳径mm: 12.5容绳量m: 400电动功率kw: 11.4外型尺寸mm: 1100*765*730机重kg: 550JD-1.6调度绞车,矿用调度绞车JD1.6绞车供矿井中上下山,中间巷道,采区运输调度编组矿车,冶金矿场等进行地面辅助物料搬运工作。
绞车的电器设备具有防爆性能,可用于煤尘及瓦斯的矿井中。
调度绞车主要性能产品型号 JD-1.6外层钢丝绳最大静张力 /kn 16外层钢丝绳绳速 /m/s 1.08总减速比 35钢丝绳直径 /mm 16卷筒尺寸 /mm 318×400电动机型号 YBJ25-4功率 kw 25转速 r/min 1480电压v 660/380外形尺寸(长×宽×高)mm 1410×1200×1230绞车重量(包括电机)kg 1400JD-2.5调度绞车,矿用调度绞车JD2.5绞车供矿井中上下山,中间巷道,采区运输调度编组矿车,冶金矿场等进行地面辅助物料搬运工作。
煤矿回柱和调度绞的安全使用要求

回柱和调度绞车的安全使用要求
(一)回柱绞车
又称慢速绞车,是用来拆除和回收采煤工作面支柱的一种绞车。
常用的回柱绞车有JH—5型、JH—8型、JH—14型和JH—20型等。
(二)调度绞车
调度绞车是用来调度车辆及进行辅助作业的一种绞车,一般用于平巷,在不太长的距离内拖运矿车,或在采掘工作面拖运设备。
常用调度绞车有JD—4.5型、 JD—11.4型、 JD—22型、 JD—40型等。
(三)回柱和调度绞车的安全使用要求
(1)绞车司机必须经过培训,经考试合格,持证上岗
(2)开车前,认真检查现场的支护情况及绞车固定情况
(3)严格按信号操作绞车,并与回柱工或挂链工密切配合,接到停车信号后立即停车。
(4)回柱绞车启动前,必须先松开手闸。
(5)调度绞车启动前,必须将滚筒制动闸闸住,将大内齿轮上的制动闸松开,然后按启动按钮,使电动机空转。
之后,严禁两个制动闸把手同时制动,也不允许在两个制动闸把手处于制动状态下按启动按钮。
(6)绞车启动后,松闸与施闸必须平稳,不得动作过快,突然加速或减速。
(7)运行中,应注意绞车的声音,各部位温升、钢丝绳的缠绕情况和张紧状态。
(8)运行中,司机的两手应不离开制动把手,精神集中,严禁与他人交谈。
(9)严禁超载运行。
(10)停车后,应施闸、停电并闭锁。
回柱绞车说明书

回柱绞车说明书JH-5、JH-8绞车一、用途JH系列回柱绞车主要供煤矿井下回柱放顶之用。
特别适用于薄煤层和急倾斜煤层采煤工作面,亦可用来拖运重物和调度车辆。
绞车配有隔爆电气设备,可用于有煤尘及瓦斯的矿井。
二、主要技术参数JH-8 JH-5牵引力最大千牛80 牵引力最大千牛57 最小69 最小42 卷筒尺寸直径×宽度毫米280×230卷筒尺寸直径×宽度毫米276×272钢丝绳直径毫米15.5 钢丝绳直径毫米16 绳速最大米/秒0.12 绳速最大米/秒0.199 最小0.083 最小0.141 减速比181.17 减速比157 容绳比米80 容绳比米80电动机功率千瓦7.5电动机功率千瓦7.5 转速转/分970 转速转/分1450 使用电压伏380/660 使用电压伏380/660外形尺寸长度毫米1550外形尺寸长度毫米1450 宽度530 宽度512 高度570 高度515绞车重量包括电机千克650 绞车重量包括电机千克620 配套电器QC83-80N隔爆可逆磁力启动器配套电器QC83-80N隔爆可逆磁力启动器LA81-3隔爆控制按钮LA81-3隔爆控制按钮三、传动系统概述1、传动系统图2、主要组成部件及其结构特征本绞车是由隔爆电动机、弹性联轴节(JH-5使用一对斜齿轮,不用联轴节)、蜗轮减速机、过桥齿轮、卷筒、底座等部件组成。
绞车传动零件的支承、分别采用滑动轴承和滚动轴承。
绞车传动零件的主要技术参数和滚动轴承的型号、数量按传动系统图排号列于下表。
JH-8齿轮一览表序号名称模数齿数6 蜗杆 6 14 蜗轮 6 4012 徘徊齿轮 6 1711 过桥齿轮 6 2210 大齿轮 6 7713 内齿离合器 6 17JH-8滚动轴承一览表序号型号名称数量旧型号7 30313 圆锥滚子轴承173****0215圆锥滚子轴承 1 7215 15 30312 圆锥滚子轴承 1 7312 14 32215 圆锥滚子轴承 1 7515 9 NJ318 内圈单挡边圆柱滚子轴承 2 42318 JH-5齿轮一览表序号名称模数齿数数量2 斜齿轮(左旋) 4 34 1 2 斜齿轮(右旋)4 34 1 6 蜗杆 6.5 1 1 4 蜗轮 6.5 37 1 12 齿轮 6 17 1 11 过桥齿轮 6 28 1 10 大齿轮 6 72 1JH-5滚动轴承一览表序号型号名称数量旧型号3、7 51314 推力球轴承2 8314 3、7 6214 深沟球轴承 2 2145 6312 深沟球轴承 1 31214 22314 调心滚子轴承 1 36149 30313 圆锥滚子轴承 2 7313各部件的结构及其特征:1)电动机绞车采用专用隔爆电动机、电动机为F级绝缘。
矿用回柱绞车
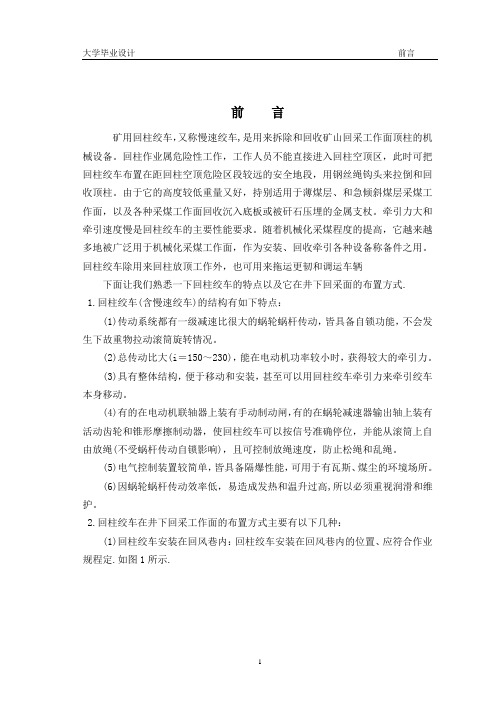
前言矿用回柱绞车,又称慢速绞车,是用来拆除和回收矿山回采工作面顶柱的机械设备。
回柱作业属危险性工作,工作人员不能直接进入回柱空顶区,此时可把回柱绞车布置在距回柱空顶危险区段较远的安全地段,用钢丝绳钩头来拉倒和回收顶柱。
由于它的高度较低重量又好,持别适用于薄煤层、和急倾斜煤层采煤工作面,以及各种采煤工作面回收沉入底板或被矸石压埋的金属支杖。
牵引力大和牵引速度慢是回柱绞车的主要性能要求。
随着机械化采煤程度的提高,它越来越多地被广泛用于机械化采煤工作面,作为安装、回收牵引各种设备称备件之用。
回柱绞车除用来回柱放顶工作外,也可用来拖运更韧和调运车辆下面让我们熟悉一下回柱绞车的特点以及它在井下回采面的布置方式.1.回柱绞车(含慢速绞车)的结构有如下特点:(1)传动系统都有一级减速比很大的蜗轮蜗杆传动,皆具备自锁功能,不会发生下故重物拉动滚筒旋转情况。
(2)总传动比大(i=150~230),能在电动机功率较小时,获得较大的牵引力。
(3)具有整体结构,便于移动和安装,甚至可以用回柱绞车牵引力来牵引绞车本身移动。
(4)有的在电动机联轴器上装有手动制动闸,有的在蜗轮减速器输出轴上装有活动齿轮和锥形摩擦制动器,使回柱绞车可以按信号准确停位,并能从滚筒上自由放绳(不受蜗杆传动自锁影响),且可控制放绳速度,防止松绳和乱绳。
(5)电气控制装置较简单,皆具备隔爆性能,可用于有瓦斯、煤尘的环境场所。
(6)因蜗轮蜗杆传动效率低,易造成发热和温升过高,所以必须重视润滑和维护。
2.回柱绞车在井下回采工作面的布置方式主要有以下几种:(1)回柱绞车安装在回风巷内:回柱绞车安装在回风巷内的位置、应符合作业规程定.如图1所示.图1 在回风巷布置回柱绞车1回风巷2 回柱绞车3 导向轮Fig 1--In return air back-alley layout winch1 Lane2 to wind back to the winch-round 3-oriented回柱绞车安装在回风巷内布置方式的优点有:①回栓绞车不需经常搬迁;②适合于煤层倾角较大、顶板破碎、压力较大的工作面。
煤矿综采队回柱绞车安全技术操作规程

煤矿综采队回柱绞车安全技术操作规程
煤矿综采队回柱绞车安全技术操作规程
一、一般规定
1、绞车司机必须经过专业技术培训,懂得设备性能和工作原理,经考试取得合格证,持证上岗。
2、绞车司机应具备独立的操作技能,会检查、会操作、会排除一般故障。
二、开车前的检查内容
1、钢丝绳排列整齐,断丝、磨损均不超限、无打结、无死弯等现象。
2、“四压两戗”齐全紧固。
3、电动机风叶罩内无阻碍转动的物件、电缆悬挂整齐、无破损、电气设备隔爆性能良好。
4、连接装置、钩头插接等符合要求。
5、减速机油质合格、油量合适。
6、传动齿轮箱内清洁无杂物,各种防护罩齐全、紧固。
7、信号系统灵敏可靠。
三、运转操作
1、用钩头将被拉运的柱子或物件连接好,打铃通知绞车司机开车。
2、司机接到信号后,按“松绳”或“紧绳”的信号开车。
3、当司机接到停车信号或遇有紧急情况时,应及时停车。
4、信号规定如下:
(1)停车:一声长铃;
(2)起动(紧绳):二声短铃;
(3)起动(松绳):三声短铃。
四、注意事项
1、操作人员必须认真监视绞车的运转情况,发现故障或异常,应立即停车。
2、绞车运行中,严禁任何人靠近牵引钢丝绳和物件,严禁在牵引区域内行人。
3、绞车不得过负荷运行。
4、绞车工作时滚筒钢丝绳不可全部放完,至少应保留3~4圈。
5、设备使用完毕后,必须将其磁力启动器隔离手柄置于停电位置,并闭锁。
20t回柱绞车技术参数

20t回柱绞车技术参数
摘要:
1.JH-20 回柱绞车说明书概述
2.JH-20 回柱绞车的技术参数
3.JH-20 回柱绞车的组成
4.JH-20 回柱绞车的应用场景
5.JH-20 回柱绞车的安全使用要求
正文:
JH-20 回柱绞车是一种矿用回柱绞车,主要应用于煤矿井下回柱放顶的工作。
它具有牵引力大、稳定性好、操作简单等优点,特别适用于薄煤层和急倾斜采煤工作面,以及在各种采煤工作面上回收沉入底板或被矸石长结的金属支柱。
此外,它还可用作移溜槽、搬移皮带运输机头等辅助牵引工作。
JH-20 回柱绞车的技术参数主要包括钢丝绳平均静张力、电动机功率、涡轮传动箱速比等。
其中,钢丝绳平均静张力为200KN,电动机功率为
15KW,涡轮传动箱速比为1:16。
JH-20 回柱绞车由电动机、涡轮传动箱、卷筒装置、底座等组成。
电动机驱动涡轮传动箱,通过减速器将动力传递到卷筒装置,从而实现绞车的牵引和回柱操作。
在使用JH-20 回柱绞车时,需要遵守一些安全使用要求。
例如,周围空气中的煤尘、甲烷爆炸性气体不得超过《煤矿安全规程》中所规定的安全含量。
此外,工作制为低速重载非连续型,空负荷运转时,应使绞车连续正反转
各30 分钟,以确保绞车运转正常。
总之,JH-20 回柱绞车在煤矿井下回柱放顶工作中具有重要作用。
回柱绞车安全技术操作规程

卷扬机安全技术操作规程
1、矿柱回采绞车安装在工作面上下车头上、机尾最远不得超过
30米,最小不得低于6米,顶板完好,不影响安全的地方。
2、绞车压紧时安装牢固可靠。
3、为了安全,防止断绳碰伤司机,绞车前应设置两道防护栏,
在出绳上方钉上木板挡好。
4、必须由经过培训的合格驾驶员操作,司机必须熟知设备性能、结构和工作原理。
5、工作前先检查钢丝绳、绳头、绞车有无异常声响,运转要灵
活可靠,如果有问题,应在工作前及时处理。
6、运行中,司机不准离开绞车,不要用手和脚触摸钢丝绳。
7、开始go南瓜子前,检查信号是否清晰可靠,如无信号不准作业,按规定负荷工作。
8、钢丝绳应按要求整齐地排列在卷筒上,工作中不可完全放出
至少要保留3~5圈留在滚筒上。
9、运行中发现异常声音和轴承温度急剧上升,必须停车检查,
排除故障后方可工作。
10、如停车时间太长,应将电动机关闭,下班后切断电源,做好
文明生产。
矿用调度绞车回柱绞车规格型号
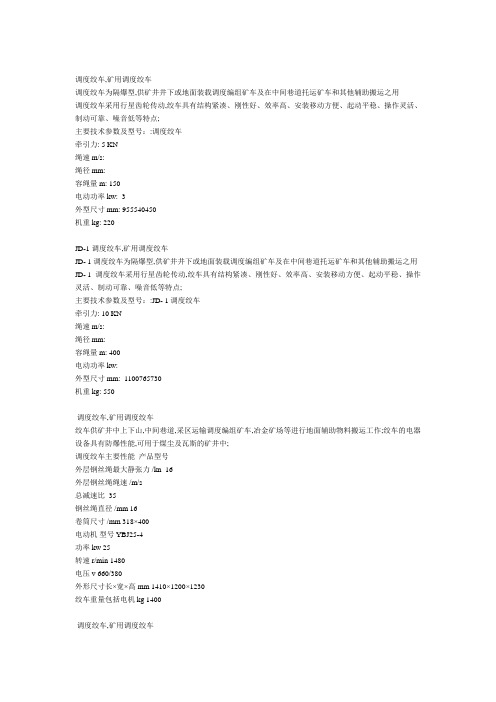
调度绞车,矿用调度绞车调度绞车为隔爆型,供矿井井下或地面装载调度编组矿车及在中间巷道托运矿车和其他辅助搬运之用调度绞车采用行星齿轮传动,绞车具有结构紧凑、刚性好、效率高、安装移动方便、起动平稳、操作灵活、制动可靠、噪音低等特点;主要技术参数及型号::调度绞车牵引力: 5 KN绳速m/s:绳径mm:容绳量m: 150电动功率kw: 3外型尺寸mm: 955540450机重kg: 220JD-1调度绞车,矿用调度绞车JD- 1调度绞车为隔爆型,供矿井井下或地面装载调度编组矿车及在中间巷道托运矿车和其他辅助搬运之用JD- 1调度绞车采用行星齿轮传动,绞车具有结构紧凑、刚性好、效率高、安装移动方便、起动平稳、操作灵活、制动可靠、噪音低等特点;主要技术参数及型号::JD- 1调度绞车牵引力: 10 KN绳速m/s:绳径mm:容绳量m: 400电动功率kw:外型尺寸mm: 1100765730机重kg: 550调度绞车,矿用调度绞车绞车供矿井中上下山,中间巷道,采区运输调度编组矿车,冶金矿场等进行地面辅助物料搬运工作;绞车的电器设备具有防爆性能,可用于煤尘及瓦斯的矿井中;调度绞车主要性能产品型号外层钢丝绳最大静张力 /kn 16外层钢丝绳绳速 /m/s总减速比 35钢丝绳直径 /mm 16卷筒尺寸 /mm 318×400电动机型号 YBJ25-4功率 kw 25转速 r/min 1480电压v 660/380外形尺寸长×宽×高mm 1410×1200×1230绞车重量包括电机kg 1400调度绞车,矿用调度绞车绞车供矿井中上下山,中间巷道,采区运输调度编组矿车,冶金矿场等进行地面辅助物料搬运工作;绞车的电器设备具有防爆性能,可用于煤尘及瓦斯的矿井中;调度绞车主要性能产品型号外层钢丝绳最大静张力 /kn 25外层钢丝绳绳速 /m/s总减速比钢丝绳直径 /mm 20卷筒尺寸 /mm 450×560电动机型号 YBJ40-4功率 kw 40转速 r/min 1480JD-4调度绞车,矿用调度绞车JD-4绞车供矿井中上下山,中间巷道,采区运输调度编组矿车,冶金矿场等进行地面辅助物料搬运工作.绞车的电器设备具有防爆性能,可用于煤尘及瓦斯的矿井中;调度绞车主要性能产品型号 JD-4外层钢丝绳最大静张力 /kn 40外层钢丝绳绳速 /m/s总减速比钢丝绳直径 /mm 22卷筒尺寸 /mm 580×600电动机型号 YBk2-280M-6功率 kw 55转速 r/min 980电压v 660/380或660/1140外形尺寸长×宽×高mm 2500×1965×1425绞车重量包括电机kg 3800电压v 660/380外形尺寸长×宽×高mm 1805×1358×1480绞车重量包括电机kg 2755JH-5回柱绞车,矿用回柱绞车JH-5回柱绞车具有隔爆性能,主要用于矿井下回柱放顶,亦可作运料、移溜槽等辅助牵引工作;H-5回柱绞车彩用球面蜗轮副传动,结构紧凑、外形尺寸小,能整机下井,结构对称,呈长条形,底座呈雪撬状,在井下自移平稳灵便;重心低,底座刚性好,既可打顶柱,可安设地锚,安装方便、运转平稳、安全可靠;卷筒直径 mm 260 钢丝绳直径 mm宽度 mm 272 平均静张力 KN 50容绳量 m 80 平均绳速 m/s电动机型号结构绳 6×19功率 kW 公称抗拉强度 MPa 1550电压 v 380/660 传动比 i 157机器总重量 kg 648 外形尺寸 mm 1640×624×695JH-8回柱绞车,矿用8吨回柱绞车JH-8回柱绞车具有隔爆性能,主要用于矿井下回柱放顶,亦可作运料、移溜槽等辅助牵引工作;JH-8回柱绞车彩用球面蜗轮副传动,结构紧凑、外形尺寸小,能整机下井,结构对称,呈长条形,底座呈雪撬状,在井下自移平稳灵便;重心低,底座刚性好,既可打顶柱,可安设地锚,安装方便、运转平稳、安全可靠;卷筒直径 mm 300 钢丝绳直径 mm 17宽度 mm 240 平均静张力 KN 80容绳量 m 100 平均绳速 m/s电动机型号 YBK2-160L-6 结构绳 6×19功率 kW 11 公称抗拉强度 MPa 1550电压 v 380/660 传动比 i机器总重量 kg 650 外形尺寸 mm 1540×533×630JH-14回柱绞车,矿用14吨回柱绞车JH-14回柱绞车具有隔爆性能,主要用于矿井下回柱放顶,亦可作运料、移溜槽等辅助牵引工作;JH-8回柱绞车彩用球面蜗轮副传动,结构紧凑、外形尺寸小,能整机下井,结构对称,呈长条形,底座呈雪撬状,在井下自移平稳灵便;重心低,底座刚性好,既可打顶柱,可安设地锚,安装方便、运转平稳、安全可靠卷筒直径 mm 400 钢丝绳直径 mm宽度 mm 302 平均静张力 KN 140容绳量 m 130 平均绳速 m/s电动机型号 YBK2-225S-8 结构绳 6×19功率 kW 公称抗拉强度 MPa 1550电压 v 730 传动比 i 188机器总重量 kg 1415 外形尺寸 mm 2050×680×830JH-20回柱绞车,矿用20吨回柱绞车JH-20回柱绞车具有隔爆性能,用于矿井下回柱放顶,亦可作运料、移溜槽等辅助牵引工作;采用球面蜗轮副传动,具有结构紧凑、外形尺寸小,均能整机下井,绞车结构对称,呈长条形,底座呈雪撬状,在井下自移平稳灵便;绞车重心低,底座刚性好,可打顶柱,可安设地锚,安装方便、运转平稳、安全可靠;技术参数:卷筒直径 mm 440 钢丝绳直径 mm宽度 mm 400 平均静张力 KN 200容绳量 m 170 平均绳速 m/s电动机型号 YBK2-200l2-6 结构绳 6×19功率 kW 22 公称抗拉强度 MPa 1550电压 v 380/660 传动比 i 181机器总重量 kg 1710 外形尺寸 mm 1891×1026×908。
jh回柱绞车技术参数
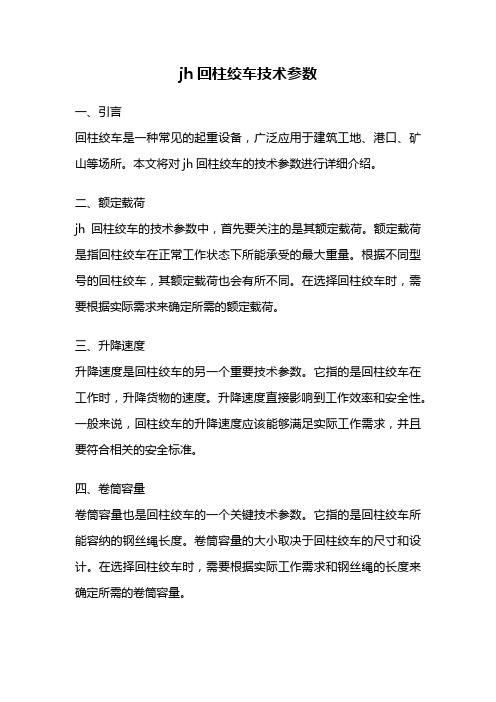
jh回柱绞车技术参数一、引言回柱绞车是一种常见的起重设备,广泛应用于建筑工地、港口、矿山等场所。
本文将对jh回柱绞车的技术参数进行详细介绍。
二、额定载荷jh回柱绞车的技术参数中,首先要关注的是其额定载荷。
额定载荷是指回柱绞车在正常工作状态下所能承受的最大重量。
根据不同型号的回柱绞车,其额定载荷也会有所不同。
在选择回柱绞车时,需要根据实际需求来确定所需的额定载荷。
三、升降速度升降速度是回柱绞车的另一个重要技术参数。
它指的是回柱绞车在工作时,升降货物的速度。
升降速度直接影响到工作效率和安全性。
一般来说,回柱绞车的升降速度应该能够满足实际工作需求,并且要符合相关的安全标准。
四、卷筒容量卷筒容量也是回柱绞车的一个关键技术参数。
它指的是回柱绞车所能容纳的钢丝绳长度。
卷筒容量的大小取决于回柱绞车的尺寸和设计。
在选择回柱绞车时,需要根据实际工作需求和钢丝绳的长度来确定所需的卷筒容量。
五、工作级别工作级别是回柱绞车的另一个重要技术参数。
它表示回柱绞车的使用频率和工作强度。
常见的工作级别有M3、M4、M5等。
在选择回柱绞车时,需要根据实际工作需求和工作环境来确定所需的工作级别。
六、起升高度起升高度是回柱绞车的另一个关键技术参数。
它指的是回柱绞车能够起升的最大高度。
起升高度的大小与回柱绞车的臂长和设计有关。
在选择回柱绞车时,需要根据实际工作需求和起升高度来确定所需的回柱绞车型号。
七、电源要求回柱绞车通常需要外部电源供应。
电源要求是回柱绞车的另一个重要技术参数。
它包括电压、频率和相数等方面。
在选择回柱绞车时,需要根据现场电源情况和回柱绞车的电源要求来确定适合的型号。
八、安全保护装置安全保护装置是回柱绞车不可或缺的一部分。
它包括限位器、过载保护器、行程开关等。
安全保护装置的设计和性能直接关系到回柱绞车的安全性能。
在选择回柱绞车时,需要关注其安全保护装置的类型和性能,确保工作环境和人员的安全。
九、外观尺寸和重量外观尺寸和重量是回柱绞车的另一个重要技术参数。
矿用回柱绞车滚筒及主轴的设计

矿用回柱绞车滚筒及主轴的设计【摘要】我国矿用小绞车主要是指调度绞车和回柱绞车,它经历了仿制、自行设计两个阶段。
回柱绞车大体上也是经历了仿制和自行设计的两个阶段,八十年代以前一直使用的是仿制的老产品,八十年代中期才开始设计新型的回柱绞车,其滚筒和主轴在产品的不断更新换代中,在设计和加工制造上逐步完善和改进,本文就滚筒和主轴的设计进行研究。
【关键词】回柱绞车滚筒和主轴设计加工回柱绞车用于煤矿井下回柱放顶,特别适用于立槽煤层、薄煤层,中厚煤层顶板压力较小的采掘工作面,综合采煤设备的搬迁及工作面安装的牵引动力,亦可做运料、移滑槽、搬移皮带运输机机头等辅助工作的牵引绞车,特别适用于薄煤层和倾斜采煤工作面,以及在各种采煤工作面上回收沉入底板或被矸石卡结的金属支柱。
1 滚筒材料及壁厚确定选用A3钢作为滚筒材料,焊接而成.查手册知其厚度在20~40mm之间,根据经验公式,最后确定滚筒壁厚为。
2 滚筒尺寸的确定已知滚筒的尺寸:(1)滚筒直径:280mm(2)钢绳直径:14mm(3)最大缠绕层数:4(4)最大容绳量:80mm2.1 确定滚筒的宽度B由公式可以算出每层的缠绕圈数,取,所以滚筒的宽度为:2.2 确定绳筒各直径(1)滚筒最小缠绕直径——滚筒的最小外径——钢丝绳直径(2)滚筒最大缠绕直径——钢丝绳每层厚度降低系数,取(3)滚筒平均缠绕直径(4)滚筒结构外径3 滚筒主轴的设计3.1 滚筒主轴设计应考虑的问题主轴是绞车的主要部件之一,对于它的设计和使用,必须给予足够的重视。
主轴的结构设计应考虑如下几点:(1)便于起吊、安装和加工;(2)卷筒子轴上的固定方式,不论用键或热装固定,都应力求可靠、不松动,因为松动后不仅影响传动,而且回在轴上磨出沟槽,以至引起断轴事故;(3)轴的断面变化不应太剧烈,并要防止其它类型的、过大的应力集中;(4)轴的加工和热处理需严格遵守规程,并于机械加工情在轴头切样检验,此外还要进行探伤检验;(5)对轴不仅有强度要求,而且还有刚度要求,通常挠度应小于轴跨距的1/3000;(6)主轴的材料一般采用45号钢。
JH—14回柱绞车
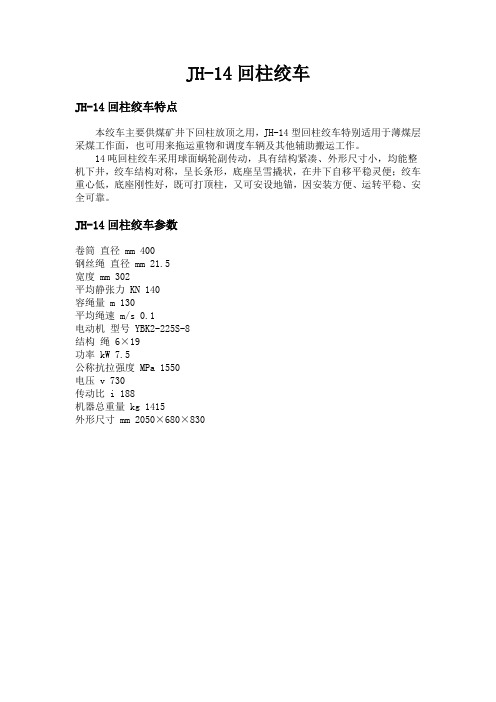
JH-14回柱绞车
JH-14回柱绞车特点
本绞车主要供煤矿井下回柱放顶之用,JH-14型回柱绞车特别适用于薄煤层采煤工作面,也可用来拖运重物和调度车辆及其他辅助搬运工作。
14吨回柱绞车采用球面蜗轮副传动,具有结构紧凑、外形尺寸小,均能整机下井,绞车结构对称,呈长条形,底座呈雪撬状,在井下自移平稳灵便;绞车重心低,底座刚性好,既可打顶柱,又可安设地锚,因安装方便、运转平稳、安全可靠。
JH-14回柱绞车参数
卷筒直径 mm 400
钢丝绳直径 mm 21.5
宽度 mm 302
平均静张力 KN 140
容绳量 m 130
平均绳速 m/s 0.1
电动机型号 YBK2-225S-8
结构绳6×19
功率 kW 7.5
公称抗拉强度 MPa 1550
电压 v 730
传动比 i 188
机器总重量 kg 1415
外形尺寸mm 2050×680×830。
煤矿回柱绞车司机安全技术操作规程

煤矿回柱绞车司机安全技术操作规程煤矿回柱绞车司机操作规程一、先进行2-3次正反车试转,并与回柱工用信号连系,试验其准确性。
二、集中精力,听取信号,按回柱信号进行开车、停车、倒车等操作。
三、正常情况停车时,应断电后用机械闸停车,不准打反车停车,相对湿度电动机轮轴温度下降后方准开车。
四、看滑轮工应在滑轮柱上方0.5米外靠采空区端部工作;松主绳时,在轮轴下方钢丝绳,外侧密切配合下给绳,以防咬绳。
五、看滑轮工必须用哨子与回柱绞车司机联络,发现滑轮卡绳、柱子松动、咬绳销子过热等情况时,必须立即吹哨停车。
六、不论开车或停车,看滑轮工都必须集中精力,且注教育工作范围动态,严禁打瞌睡或离开工作岗位。
运行时,滑轮内侧不准钢丝人员存留或通过。
七、信号工(打点工)必须听从回柱工的指挥,精力集中,密切注意钢丝绳方向,当发觉钢丝绳方向有误时,应立即发出停车信号。
发信号要迅速、准确。
八、信号工始终要和回柱位置继续保持5-8米距离,随回柱位置彻底改变推延改变工作位置,并收盘好电缆;调整工作位置时,应手持信号装置,不得悬捉信号线,以免损坏信号线接头;造成事故。
九、发现有卡绳时,按以下要求操作。
1、在回柱工、看轮工等协助下取出钢丝绳。
2、用撬棍或其他工具螺丝刀剔拔撬起卡住的钢丝绳,恰当时可辅以人力撩绳。
3、将钢丝绳拉展好,用绳头的大钩(或卡子)拴(卡)在牢固支柱上时再上时再以再开倒车,或使卡住钢丝绳松开。
4、开倒车处理卡绳时候,如钢丝绳拉倒绞车滚筒边绳子仍未松开,应停车,以免损坏,折断钢丝绳。
十、开倒车处理卡绳事故这时,现场其他值班人员人员必须退到安全目的地。
十一、回柱工作结束后,把钢制全部缠在滚筒上,把开关手把打在跳闸断电位置上,锁紧闭锁螺栓,切断电源。
JH-14回柱绞车说明书
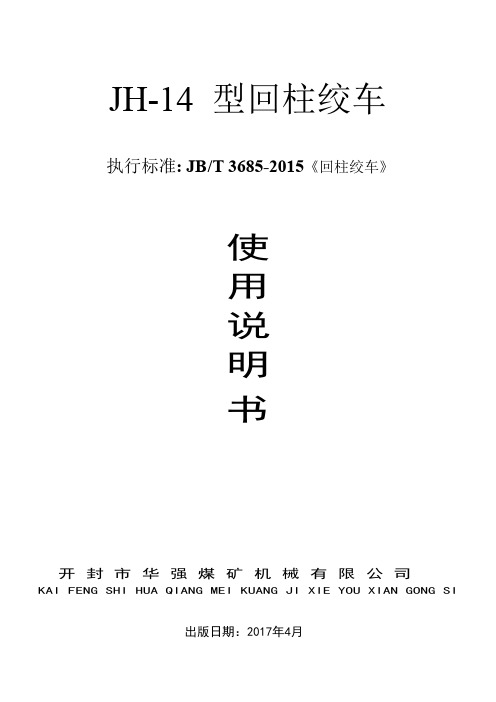
停车检查
--7--
7.3 工作后的注意事项: 7.3.1 工作结束后,应将钢丝绳整齐地缠绕在卷筒上,切断电源,封闭开关。 7.3.2 清楚机器上的灰尘、杂物。 7.3.3 交班时必须把本班发现的不正常情况向下一班交代清楚 。
8. 绞车的维护、拆卸与修理
8.1 绞车的操作人员必须严格遵守操作规程。 8.2 绞车必须按第四节的规定及时加注润滑油(脂)。 8.3 绞车如长时间搁置不用,必须选择干燥通风的地方存放,防止电器设备受潮,绞车的 裸漏部分应涂以保护油。
KAI FENG SHI HUA QIANG MEI KUANG JI XIE YOU XIAN GONG SI
出版日期:2017年4月
示语
a 严禁用于载人或提升,严禁超载; b 绞车所配的电器产品必须要有在有效期内的安全认证标志; c 操作之前必须熟读本说明书,并按要求操作 c 绞车在使用时发现声音异常、发热等情况,立即进行检查,在排除后发
绞车在装配前应清查零件数量,并将所有零件清洗干净,严防铁屑、灰尘带人;所有滚 动轴承宜在油中加热后(一般加热温度为 120-140°C)进行装配,不得硬打硬砸,以防零件受 力变形。
绞车应先进行部装,然后再进行总装,总装前应先装成以下几个部分。 6.1 蜗轮箱部分:
在装配该部分时,可按以下装配程序: 6.1.1 将蜗杆和轴承装入蜗轮箱盖内。 6.1.2 将调整盖、蜗轮轴承、轴承盖、密封圈、“O”型圈油封、小齿轮等零件均装在蜗轮轴 上,然后将装配好的蜗轮轴装置在蜗轮箱底座内。 6.1.3 将过桥齿轮、铜套装在过桥轴上,然后再一齐装在蜗轮箱底内,使其与小齿轮啮合。 其接触斑点,沿齿高不小于 40%,沿齿长于 50%。 6.14 将蜗轮箱盖与蜗轮箱底装在一起,此时利用调整盖上的调整螺丝、轴承盖、对蜗轮进 行轴向调整,同时可确定调整圈的厚度并确保调整圈与蜗轮箱有 0.1-0.25 毫米的间隙。利用 染色法选择蜗杆两端轴承压盖的调整垫的厚度,对蜗杆进行轴向调整,使蜗杆和蜗轮啮合正 确,蜗轮轮齿上的接触斑点,沿齿高不小于 70%,沿齿长不小于 25%。(跑合后)。蜗杆螺 牙的接触斑点为:其长度是整个螺牙长度的 40%以上,且蜗杆螺纹接触斑点不应达到接近 螺纹长度 10%的螺纹入口端(即在上述规定的范围内在入口处不允许有接触斑点)。
JH系列回柱绞车使用说明
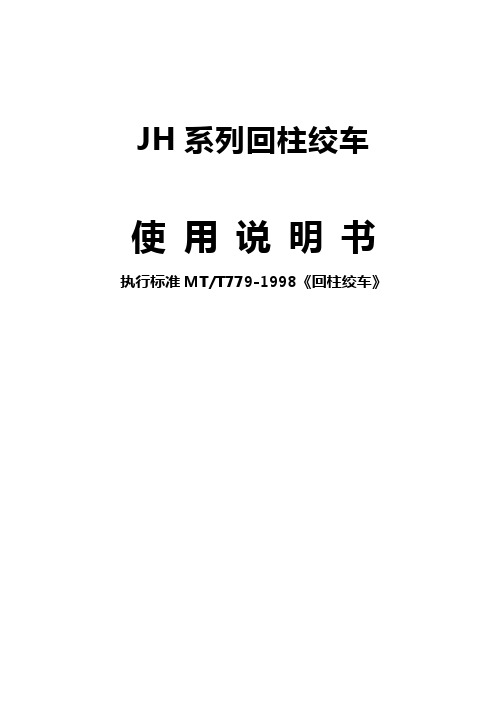
JH系列回柱绞车使用说明书执行标准MT/T779-1998《回柱绞车》目录1、概述 (2)2、主要技术参数 (3)3、结构特征………..……….………………………......………..3-104、绞车的润滑………..…………..……………….....…………10-115、绞车的安装、调试和试运转…….....………………......……11-166、绞车的操作规程 (16)7、常见故障与分析 (17)8、绞车的维护与修理 (17)9、电器控制系统…..………….…………………………....…..18-1910、备件与易损件 (20)11、运输与贮存 (21)12、验收与检查 (21)13、质量保证 (21)一、概述1.用途和适用范围JH系列回柱绞车主要用于煤矿井下回柱放顶,特别适用于立槽煤层、薄煤层、中层煤层顶板压力较小的采掘工作面。
2.品种和规格我公司共生产五种规格的回柱绞车,分别是JH-5、JH-8、JH-14、JH-20、JH-30。
其中JH-8与JH-14结构与工作原理相同;JH-20与JH-30结构与工作原理相同。
3.工作条件⑴环境温度为-10~+40℃;⑵环境相对湿度不超过95%(+25℃),海拔高度不超过1000m 的情况下工作;对于海拔高度超过1000 m,需要考虑到空气冷却作用和介电强度的下降,选用的电器设备应根据制造厂和用户的协议进行设计或使用;⑶周围空气中的甲烷、煤尘和硫化氢、二氧化碳等不得超过《煤矿安全规定》中所规定的安全含量;⑷工作制为低速重载非连续型。
4.型号编制J H □——□修改序号钢丝绳平均静张力,单位10kN回柱绞车标记示例:钢丝绳平均静张力为80KN的回柱绞车为:JH-8绞车电机、电器设备具有隔爆性能,可用于含有沼气及煤尘的矿井中。
5.警示语本绞车严禁用于载人或提升。
绞车所配的电机和电器设备,必须要有在有效期内的安标证。
二、主要技术参数JH系列回柱绞车主要技术参数见表一三结构特征(一)JH-5回柱绞车1.主要结构及工作原理绞车由电动机、蜗轮减速机、中间轴、卷筒、底座等部件组成。
JH-14型回柱绞车使用说明书

JH-14型回柱绞车使用说明书1、概述1.1 主要用途及适用范围1.1.1 JH-14型回柱绞车(以下简称绞车)主要供煤矿回采工作面回柱放顶用,亦可用于拖运重物和调度车辆。
1.1.2 本绞车的电动机和电气控制设备具有隔爆性能,适用于有煤层及瓦斯的矿井。
1.2产品型号及含义:1.2.1 型号含义1.3安全绞车严禁载人及提升。
绞车所配备的电气产品必须要有在有效期内的安标证!绞车准备运行工作前,所有人必须远离危险区域,禁止任何人停留,以免发生人身伤亡事故!禁止带电检修和保养!1.4工作条件绞车应在环境温度为-10℃~+40℃,环境相对温度不超过95%(+25℃),海拔高度不超过1000m的情况下工作。
对于海拔高度超过1000m,需要考虑到空气冷却作用和介电强度的下降,选用的电器设备应根据制造厂和用户的协议进行设计或使用。
隔爆型绞车用于煤矿井下时,周围空气中的甲烷、煤尘和硫化氢、二氧化碳等不得超过《煤炭安全规程》中所规定的安全含量。
2结构特征与工作原理2.1 传动系统2.1.1涡轮、蜗杆和齿轮参数见表1。
2.1.2在绞车中使用的滚动轴承见表2。
2.2各部件的结构及特征2.2.1本绞车由制动器、联轴器、涡轮减速器、齿轮罩、中间轴装置、卷筒装置、齿轮罩、底座和电动机组成。
2.2.2电气设备如下:2.2.2.1电动机a)型号 YBJ18.5-8b)额定功率 kw 18.5c)额定转速 r/min 735d)额定电压 v 380/6602.2.2.2隔爆磁力启动器 BQD7-80N2.2.2.3隔爆控制按钮 BZA2-32.2.3弹性联轴器电动机与涡轮箱之间装有弹性联轴器,可以补偿两轴线的相对误差,亦可起缓冲、减振的作用。
2.2.4手动带式制动器制动带由铜丝石棉带与钢板铆接而成,其两端铰接于三星枴臂上。
通过杆系在绞车后部进行操作。
制动带与制动轮的间隙用钢带接头螺栓调整。
2.2.5减速机构由涡轮减速器和两对圆柱齿轮组成2.2.6钢丝绳为直径22、蔴芯、6股19丝,钢丝破断拉力总和为312.6KN。
煤矿井下常用调度绞车、回柱绞车、无极绳绞车(顺槽连续牵引车)技术参数及基础图集
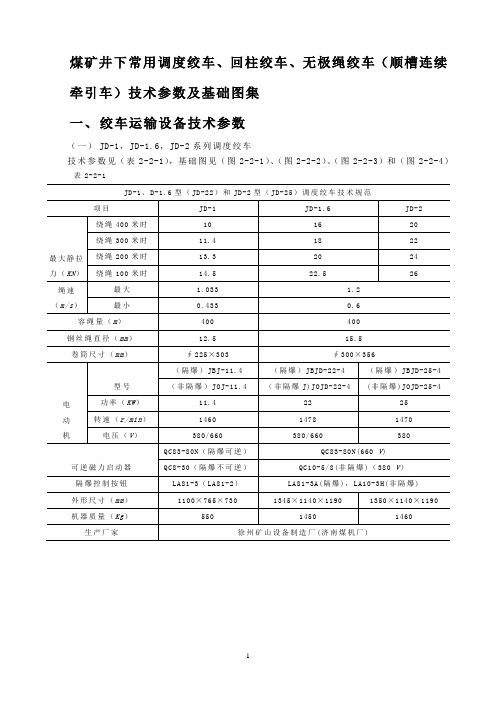
煤矿井下常用调度绞车、回柱绞车、无极绳绞车(顺槽连续牵引车)技术参数及基础图集一、绞车运输设备技术参数(一)JD-1,JD-1.6,JD-2系列调度绞车技术参数见(表2-2-1),基础图见(图2-2-1)、(图2-2-2)、(图2-2-3)和(图2-2-4)表2-2-1JD-1、D-1.6型(JD-22)和JD-2型(JD-25)调度绞车技术规范(二)JD-2.5,JD-3系列调度绞车技术参数见(表2-2-2),基础图见(图2-2-5)、(图2-2-6)、(图2-2-7)、(图2-2-8)表2-2-2JD-2.5型(JD-40)和JD-3型(JD-45)调度绞车技术规范(三)JY-4系列调度绞车技术参数见(表2-2-3),基础图见(图2-2-9)、(图2-2-10)、(图2-2-11)表2-2-3执行标准:JB/T9028-1999《运输绞车》(四)JH-8系列回柱机技术参数见(表2-2-4)表2-2-4JH-8系列回柱绞车技术规范(五)JH-14C和JH-20A回柱机技术参数见(表2-2-5),基础图见(图2-2-12)表2-2-5JH-14C和JH-20A型回柱绞车技术规范(六)SDJ系列回柱机技术参数见(表2-2-6),基础图见(图2-2-13)、(图2-2-14)、(图2-2-15)表2-2-6SDJ系列多用途绞车技术规范二、 顺槽连续牵引车技术规范(一) SQ-1200型顺槽连续牵引车 见表2-2-7表2-2-74.运输能力连续牵引车牵引能力可根据验算程序计算确定,对适应坡度和牵引重量进行计算,一般情况可参考表2-2-7选用,在1500m 运距工况条件下连续牵引车运输能力见表2-2-8表2-2-8绞车、张紧装置及尾轮基础图见(图2-2-17)、(图2-2-18)、(图2-2-19)、(图2-2-20)、(图2-2-21)、(图2-2-22)。
三、 绞车基础图集JD-2.5绞车基础图(济南煤机厂)绞车铸铁底座,厚350mm,孔径30mm,使用螺栓直径26mm。
回柱绞车司机操作规程
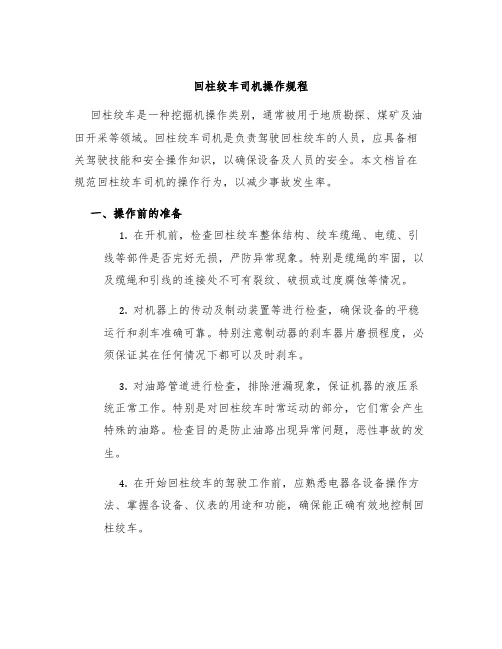
回柱绞车司机操作规程回柱绞车是一种挖掘机操作类别,通常被用于地质勘探、煤矿及油田开采等领域。
回柱绞车司机是负责驾驶回柱绞车的人员,应具备相关驾驶技能和安全操作知识,以确保设备及人员的安全。
本文档旨在规范回柱绞车司机的操作行为,以减少事故发生率。
一、操作前的准备1.在开机前,检查回柱绞车整体结构、绞车缆绳、电缆、引线等部件是否完好无损,严防异常现象。
特别是缆绳的牢固,以及缆绳和引线的连接处不可有裂纹、破损或过度腐蚀等情况。
2.对机器上的传动及制动装置等进行检查,确保设备的平稳运行和刹车准确可靠。
特别注意制动器的刹车器片磨损程度,必须保证其在任何情况下都可以及时刹车。
3.对油路管道进行检查,排除泄漏现象,保证机器的液压系统正常工作。
特别是对回柱绞车时常运动的部分,它们常会产生特殊的油路。
检查目的是防止油路出现异常问题,恶性事故的发生。
4.在开始回柱绞车的驾驶工作前,应熟悉电器各设备操作方法、掌握各设备、仪表的用途和功能,确保能正确有效地控制回柱绞车。
二、操作方法1.操作前先切断所有的电源,并在红色开关上挂上“禁止通电”的标志。
操作人员必须保证车辆稳定,不能使车辆发生侧翻等倾倒危险。
2.确保回柱绞车的电气系统被正确地连接到电源。
不能将绞车缆绳沉下机器脚架,因此必须在进行实际操作前,把机架向上提,同时将绞车钢缆牢固地固定在顶头。
3.模拟使用场景后进行操作。
如果回柱绞车驾驶人员在操作前能够清楚的知道将要面对何种情况,就能够提高操作的准确性。
这是因为多年来,各类经验不充足的驾驶人员都因操作不当而造成了众多不必要的事故。
4.确定吊钩形式和吊重比例。
回柱绞车的绞车缆绳牢固地绑紧,颜色清晰可见。
牢固的固定意味着更大的重量,所以一定要确认使用正确的钩子类型。
钩子尺寸和类型应该能够完全承载要吊起的石头或矿物。
5.开始吊装。
操作人员必须保证车辆稳定,不能使车辆发生侧翻等倾倒危险。
操作员要时刻观察吊物状态,同时判断是否存在钩在吊物下,来避免不必要的危险。
- 1、下载文档前请自行甄别文档内容的完整性,平台不提供额外的编辑、内容补充、找答案等附加服务。
- 2、"仅部分预览"的文档,不可在线预览部分如存在完整性等问题,可反馈申请退款(可完整预览的文档不适用该条件!)。
- 3、如文档侵犯您的权益,请联系客服反馈,我们会尽快为您处理(人工客服工作时间:9:00-18:30)。
前言矿用用回柱绞车,又称慢速绞车,是用来拆除和回收矿山回采工作面顶柱的机械设备。
回柱作业属危险性工作,工作人员不能直接进入回柱空顶区,此时可把回柱绞车布置在距回柱空顶危险区段较远的安全地段,用钢丝绳钩头来拉倒和回收顶柱。
由于它的高度较低重量又好,持别适用于薄煤层、和急倾斜煤层采煤工作面,以及各种采煤工作面回收沉入底板或被矸石压埋的金属支杖。
牵引力大和牵引速度慢是回柱绞车的主要性能要求。
随着机械化采煤程度的提高,它越来越多地被广泛用于机械化采煤工作面,作为安装、回收牵引各种设备称备件之用。
回柱绞车除用来回柱放顶工作外,也可用来拖运更韧和调运车辆下面让我们熟悉一下回柱绞车的特点以及它在井下回采面的布置方式.1.回柱绞车(含慢速绞车)的结构有如下特点:(1)传动系统都有一级减速比很大的蜗轮蜗杆传动,皆具备自锁功能,不会发生下故重物拉动滚筒旋转情况。
(2)总传动比大(i=150~230),能在电动机功率较小时,获得较大的牵引力。
(3)具有整体结构,便于移动和安装,甚至可以用回柱绞车牵引力来牵引绞车本身移动。
(4)有的在电动机联轴器上装有手动制动闸,有的在蜗轮减速器输出轴上装有活动齿轮和锥形摩擦制动器,使回柱绞车可以按信号准确停位,并能从滚筒上自由放绳(不受蜗杆传动自锁影响),且可控制放绳速度,防止松绳和乱绳。
(5)电气控制装置较简单,皆具备隔爆性能,可用于有瓦斯、煤尘的环境场所。
(6)因蜗轮蜗杆传动效率低,易造成发热和温升过高,所以必须重视润滑和维护。
2.回柱绞车在井下回采工作面的布置方式主要有以下几种:(1)回柱绞车安装在回风巷内:回柱绞车安装在回风巷内的位置、应符合作业规程定.如图1所示.图1 在回风巷布置回柱绞车1回风巷2 回柱绞车3 导向轮Fig 1--In return air back-alley layout winch1 Lane2 to wind back to the winch-round 3-oriented回柱绞车安装在回风巷内布置方式的优点有:①回栓绞车不需经常搬迁;②适合于煤层倾角较大、顶板破碎、压力较大的工作面。
缺点有;①回栓绞车可能影响回风巷人员行走和材料运输工作;②钢丝绳牵引时要绕过一个拐直角的导向轮,钢丝绳受力大容易损坏;②要求固定拐角导向轮的柱子或锚杆等必须牢固.(2)回柱绞车安装在回采工作面上端;回柱绞车布置在紧靠回风巷,且在工作面的上端相密集支柱之间.如图2所示。
图2 在回采工作面上布置回柱绞车1 回风巷2 回柱绞车3 钢丝绳Fig 2 --Recovery work surface layout in the back-winch1 Lane2 to wind back 3-wire rope winch回柱绞车安装在回采工作面上端布置方式的优点有:①钢丝绳牵引不必拐弯,直线牵引,钢丝绳运行阻力小,不易损坏;②不影响回风巷内人员走动和材料运输工作。
缺点有:①每进行一次循环都要移动回柱绞车;⑧要求在顶板条件较好和煤层倾角较小的条件下采用。
当顶板压力较大时,机座受力后易变形;②顶板严重冒落,可能埋住绞车,移设和检修都很困难。
这种布置方式很少采用。
(3)回柱绞车直接安装在工作面:回柱绞车直接安装在工作面的多台布置,方式如图3所示.回柱绞车直接安装在工作面的多台绞车布置方式的优点有:①多台同时回柱,加快回柱进度,特别适合需要回柱的普通机械化采煤工作面,如使用刨煤机的回采工作面;②不影响回风巷内的人员走动和材料运输工作;⑧钢丝绳牵引不必拐弯,直线牵引,钢丝绳运行阻力小,不易损坏。
缺点有,①每进行—次循环都要移动回柱绞车;②要求在顶板条件较好和煤层倾角较小的条件下采用;②顶板冒落,可能埋住绞车,移设和检修都很困难。
这种布置方式是在回柱工艺时间大大超过来煤工艺时间的情况下采用,可提高采煤工作面生产能力和经济效益,但应在确保安全的前提下谨慎推广使用图 3 在工作面上布置数台绞车1 回风巷2 回柱绞车3 刮板输送Fig 3--In the work surface layout several winch1 Lane2 to wind back to the winch-3 AFC1.回柱绞车的概况与方案的初步拟定1.1.国内外回柱小绞车的概况我国矿用小绞车主要是指调度绞车和回柱绞车,它经历了仿制、自行设计两个阶段。
解放初期使用的矿用小绞车有日本的、苏联的,因此当时生产的矿用小绞车也是测绘仿制日本和苏联的产品。
1958年后这些产品相继被淘汰,并对苏联绞车进行了改进,于1964年进入了自行设计阶段.回柱绞车大体上也是经历了仿制和自行设计的两个阶段,八十年代以前一直使用的是仿制的老产品,八十年代中期才开始设计新型的回柱绞车,主要针对效率极低的球面蜗轮副、慢速工作和快速回绳等环节进行根本的改进。
矿用小绞车标准化方面,1967年制定了调度绞车部标准,1971年制定了回柱绞车部标准.1982年对上述两个标准都进行了修订,其标准方为JB965-83. JB1409-83.国外矿用小绞车使用很普通,生产厂家也很多。
苏联、日本、美国、瑞典等国都制造矿用小绞车。
国外矿用小绞车的种类、规格较多.工作机构有单筒、双筒和摩擦式.传动型式有皮带传动、链式传动、齿轮传动、蜗轮传动、液压传动、行星齿轮传动和摆线齿轮传动等。
其中采用行星齿轮传动的比较多。
发展趋势向标准化系列方向发展,向体积小、重量轻、结构紧凑方向发展;向高效、节能、寿命长、低噪音、一机多能通用化、大功率、外形简单、平滑、美观、大方方向发展。
国外矿用小绞车规格比较多,适用不同场合,我国矿用小绞车的规格少,品种型号多而乱,也较繁杂,没有统一标准。
从工作机构上分,国外有单筒、双筒及摩擦式三种,我国只有单筒一种型式。
从原动力上分,国外有电动的、风动的及液压驱动,我国只有电动的和少量风动的。
例如回柱绞车的薄弱环节是球面蜗轮副传动,回柱绞车的主传动均采用了蜗轮副传动,这是因为蜗轮副传动比大,又具有自锁性,故其传动效率较低,一般只有0. 4~0.45,回柱绞车的总传动效率更低。
回绳速度慢,所有的回柱纹车回绳速度和工作牵引速度相同.不论绞车用于回柱放顶,还是搬运设备,工作效率太低。
随着采煤机械化的发展,综采设备的频繁搬迁,又由于回柱绞车搬运,工作时间长占用人工多,因此这类绞车均应设置快速回绳。
我国矿用小绞车在寿命、噪音、可靠性等综合指标与苏联有着一定的差距。
苏联矿用小绞车使用寿命规定在5年以上,我国目前不具备测试手段寿命无法考核,但从对用户的访问中得知,寿命达不到5年.噪音也稍大。
虽然我国矿用小绞车参数系列水平优于国外,但在标准化和通用化方面远不如发达采煤机械制造国。
比如牵引力14000kg·f这一档回柱绞车就有四种型号. JHC-14型一级减速为蜗轮副传动、二级为行星齿轮传动(少齿差传动)。
JHZ-14型二级减速为蜗轮副传动,一级和三级减速为圆柱齿轮传动。
JM-14型是在一级蜗轮副减速之后,其二级、三级减速为直齿圆柱齿轮传动。
JH-14型是在一级蜗轮副减速之后,其二级减速为直齿圆柱齿轮传动,也是传动系统最简单的一种。
回柱绞车以电动使用最广,传动型式以球面蜗轮副居多,该机主要结构型式为电动机悬装在蜗轮副减速器的后部,蜗轮副减速器为第一级减速,第二级和第三级为圆柱齿轮传动,分别安装在机器的两侧对称机体的中心布置,该机呈长条形适应并下巷道的空间,体积小,底座呈雪橇形,安装搬运方便。
纵观国外矿用小绞车的发展情况其发展趋势有以下几个特点。
(1)向标准化系列化方向发展,苏联月本、美国、德国、英国已有矿用小绞车国家标准.并且这些国家的各制造公司有自己的产品系列型谱。
在这些国家标准和系列型谱中,对绞车的性能、参数做了明确的规定,并强力推行和实施,给设计和制造、使用、维护带来极大方便。
(2)向体积小、重量轻、结构紧凑方向发展。
由于煤矿井下狭窄的工作环境要求绞车体积小、重量轻,各国都在力求将绞车的原动机、传动装置、工作滚筒、制动操作等部分及底座等主要部件综合在一个系统中加以统筹布局,充分利用空间提高紧凑程度,做好外形封闭。
为此有的将传动部分置于滚筒内部,有的紧贴滚筒端部,有的将电机埋入滚筒内部,有的将底座支架减速器铸为一体。
(3)向高效节能方向发展。
世界工业发达的国家如苏联、日本在纹车各种参数的设置上进行优化设计,选取最佳参数,最大限度提高产品功能。
在传动机构上尽量采用较先进的传动型式,并采用合理的制造精度,以提高生产效率。
在产品节能方面各国各公司都很重视。
苏联和日本在绞车设计方面为节约电耗,对电机功率在全面分析绞车的实际工作情况的基础上确定。
使电机的功率保证绞车的功能(牵引力、牵引速度)等,又能使电机功率得以充分利用。
(4)向寿命长、低噪音方向发展。
寿命和噪音是衡量产品的综合性能指标,是产品质量的综合性反应。
寿命长,经济效益才能高;噪音低,有利工人身心健康。
(5)向一机多能、通用化方向发展。
矿用小绞车在使用过程中不仅做调度用,而且还做运输及其他辅助工作。
使用范围扩大,要求绞车有比较强的适应能力。
把调度、运输、辅助绞车归纳为一个标准。
三种绞车结构相近,大同小异。
即主机相近而制动操作部分则根据各自的使用条件有所区别。
有的国家已经打破了行业界限,把各行业的卷扬机设备统归为卷扬机类。
这样便于生产使用和维护。
便于提高产品质量和社会经济效益。
随着管理水平的提高,产品通用化程度也必然的不断提高,这是今后产品发展的必然趋势。
(6)向大功率方向发展。
随着生产的发展,原来的产品越来越不能满足用户的要求。
长期的生产实践的成功经验表明,调度绞车除调度矿车外,也用于运搬设备,又如回柱绞车除用于回柱放顶外,有时也用于运搬综采及各类机电设备时,运距一般较长,牵引和回绳用一种速度,且目前的回柱绞车牵引速度太慢,回绳速度更慢,因此解决上述问题的同时要加大绞车的功率,满足用户的要求。
(7)向外形简单、平滑、美观、大方方向发展。
由于各国力求使产品的结构紧凑、体积小、重量轻、大都采用了机电合一的综合机构。
外表只能看到滚简和制动操纵部分。
整个绞车近似一个圆形,显得线条简单外形平滑,为了争夺市场,各国绞车在外形上巧妙的构思,使得产品造型美观,操作者感到舒适。
1.2.回柱绞车的主要传动方式类型我国常用的回柱绞车类型及其传动方式有下列几种:1.25JH-型回柱绞车,其传动方式为:一组斜齿轮,一组蜗轮,一组直齿轮2.8JH-型回柱绞车,其传动方式为:一组蜗轮,一组直齿轮3.214JM-回柱绞车,其传动方式有两种,一种为:一组蜗轮,两组直齿轮;一组为一组斜齿轮,一组蜗轮,一组直齿轮.4.214JH-型回柱绞车,其,传动方式为:一组斜齿轮,一组蜗轮,一组内齿轮5.14JHC-型回柱绞车,其传动方式为:一组蜗轮,一组少齿差行星齿轮6.20JH A-型回柱绞车,其传动方式为:一组直齿轮,一组蜗轮,一组直齿轮7.28JM-型回柱绞车,其传动方式为:一组圆锥齿轮,一组变速直齿轮,一组行星齿轮,一组直齿轮1.3.设计任务与方案的初步拟定矿用回柱绞车传动装置设计1.设计条件:1)机器用途:煤矿井下回收支柱用的慢速绞车;2)工作情况:工作稳定、平稳,间歇工作(工作与停歇时间比为1:2),绳筒转向定期变换;3)运动要求:绞车绳筒转速误差不超过8%;4)工作能力:储备余量10%;2.原始数据见表1-1:表1-1绞车原始数据图Table 1-1 winch raw data plans题号 J1钢绳牵引力(kn) 50钢绳最大速度(m/min) 5绳筒直径(mm) 280钢绳直径(mm) 14最大缠绕层数 4绳筒容绳量(mm) 803.方案的初步拟定根据设计要求,所给原始数据,经过对回柱绞车常用型号的传动方式比较,最后选用一级为蜗杆传动,一级齿轮传动的传动方式.其传动结构图如图1-1:图1-1回柱绞车传动方式Fig.1-1 Drive back to the winch-way该结构简单,而且占用的空间小,适合井下狭窄空间.第一级采用蜗杆机构,也符合回柱绞车传动比大的要求,所以经过比较,最终我选择此种传动方案.2.传动装置设计2.1 传动方案的拟定已知条件:钢绳牵引力F=50kN,最大速度V=5m/min,绳筒直径D=280mm,钢绳直径d=14mm ,则6010006010005/606/min 3.141280v nr w Dπ⨯⨯⨯===⨯ 初步拟定出二级传动的传动方案。