零件毛刺的工艺要求准则
冲压件毛刺检验指导书
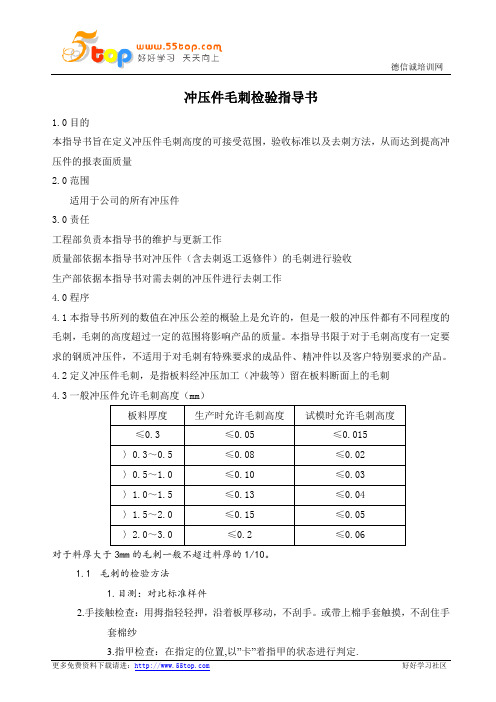
冲压件毛刺检验指导书1.0 目的本指导书旨在定义冲压件毛刺高度的可接受范围,验收标准以及去刺方法,从而达到提高冲压件的报表面质量2.0 范围适用于公司的所有冲压件3.0 责任工程部负责本指导书的维护与更新工作质量部依据本指导书对冲压件(含去刺返工返修件)的毛刺进行验收生产部依据本指导书对需去刺的冲压件进行去刺工作4.0 程序4.1 本指导书所列的数值在冲压公差的概验上是允许的,但是一般的冲压件都有不同程度的毛刺,毛刺的高度超过一定的范围将影响产品的质量。
本指导书限于对于毛刺高度有一定要求的钢质冲压件,不适用于对毛刺有特殊要求的成品件、精冲件以及客户特别要求的产品。
4.2 定义冲压件毛刺,是指板料经冲压加工(冲裁等)留在板料断面上的毛刺4.3 一般冲压件允许毛刺高度(mm)板料厚度生产时允许毛刺高度试模时允许毛刺高度≤0.3 ≤0.05 ≤0.015〉0.3~0.5 ≤0.08 ≤0.02〉0.5~1.0 ≤0.10 ≤0.03〉1.0~1.5 ≤0.13 ≤0.04〉1.5~2.0 ≤0.15 ≤0.05〉2.0~3.0 ≤0.2 ≤0.06对于料厚大于3mm的毛刺一般不超过料厚的1/10。
1.1毛刺的检验方法1.目测:对比标准样件2.手接触检查:用拇指轻轻押,沿着板厚移动,不刮手。
或带上棉手套触摸,不刮住手套棉纱3.指甲检查:在指定的位置,以”卡”着指甲的状态进行判定.确认位置以各表面进行.不可”卡”着指甲4.过纸检查:在指定的位置,以A4纸作R部,约45o倾斜,以前端部”卡”着状态移动,进行判定..前端不可”卡”着F5.卡尺测量(毛刺较大),4.5毛刺的清除1、对于小毛刺可以先用锉刀或刮刀修锉,然后用砂纸进行精砂;对于较大毛刺先采用旋转研磨机去除毛刺,然后用抛光轮抛光但注意造成零件的变形量,更不能伤到产品其它表面。
注意在使工具手工去刺时,工具防向要与毛刺方向成一定的倾角。
2、喷砂冲压件外观缺陷检验标准项目描述关键件判定(整车区域)A B C D裂纹1、封闭裂纹:长度≥50mm宽度≥3mm2、不封闭裂纹:长度≥30mm宽度≥2mm/所有件下同报废1、封闭裂纹:10mm≤长度<50mm宽度<3mm2、不封闭裂纹:10mm≤长度<30mm宽度<2mm是报废报废报废报废非报废返修返修返修1、封闭裂纹:长度<10mm宽度<3mm2、不封闭裂纹:长度<10mm宽度<2mm/ 返修返修返修返修缩颈缩颈部位材料厚度:厚度≥料厚的80%;缩颈部位长度≥60mm/ 报废缩颈部位材料厚度:料厚的50%≤厚度<料厚的80%;缩颈部位长度:30mm≤长度<60mm;是报废报废报废报废非报废报废返修返修缩颈部位材料厚度:厚度<料厚的50%缩颈部位长度:长度<30mm/ 返修坑包面积≥8m㎡;长度≥10mm;高度≥1.5mm/ 报废报废返修返修面积<8m㎡;长度L<10mm;高度<1.5mm/ 返修返修返修合格变形零件表面出现明显起伏;目视明显;严重影响外观及装配/ 报废零件表面出现起伏;目视不明显;手感/ 返修返修返修合格明显零件表面出现起伏;手感不明显;油石检验明显/ 返修返修合格合格麻点零件2/3面积上能看到麻点或小凸包/ 报废零件表面用油石磨件之前用手感觉明显的麻点或麻点群;麻点面积<2/3零件面积;/ 报废报废返修合格材料缺陷料厚明显不符合要求;表面有明显的桔皮滑移线、镀锌层疏松;锌脱落长度≥300mm;宽度≥5mm/ 报废报废报废合格轻微的材料缺陷;磨件后可见的材料缺陷;/ 返修返修合格合格锈蚀锈蚀厚度≥料厚的40%;锈蚀面积≥全部面积的25%;型面比较复杂无法消除锈迹;/ 报废锈蚀厚度:料厚的20%≤厚度<料厚的40%;锈蚀面积:全面积5%≤厚度<全面积25%;是报废非报废报废返修返修表面质量受锈蚀影响但可通过打磨修复;/ 返修起皱肉眼能看出的严重皱折、棱线错位,严重影响焊接及装配;/棱线、弧度不够清晰光顺;肉眼可见的皱纹、波纹、棱线错位;是报废报废返修返修非报废报废返修合格毛刺毛刺高度H大于料厚的40%;有操作危险性的粗毛刺;/ 返修毛刺高度:料厚的20%≤高度<料厚的40%;毛刺影响定位、装配、焊接、压一般孔合格定位孔装返修合的;配孔一般料边合格压合/焊接料边返修毛刺高度:高度<料厚的20%;/ 合格拉毛压痕划伤深度≥料厚的30%;宽度≥2mm;长度≥5mm;是报废非报废报废返修合格料厚的10%≤深度<料厚的30%;宽度<2mm;长度<5mm/ 返修返修返修合格深度<料厚的10%;/ 返修返修合格合格圆角不顺圆角半径不均匀,未达到要求;明显地不清晰、不光顺;配合间隙达2mm以上;/ 报废报废返修返修圆角半径不均匀,不够清晰光顺;配合间隙达2mm以下/ 返修返修合格合格叠料板料重叠宽度:宽度≥8mm / 报废板料重叠宽度:3mm≤宽度<8mm是报废非报废报废报废返修板料重叠宽度:宽度<3mm / 报废返修返修合格其他能引起严重功能障碍的缺陷报废对使用有明显影响的缺陷返修9.2尺寸缺陷检验判定标准尺寸缺陷检验判定标准项目描述零件与检具的间隙用d 表示, 平度用h 表示,单位mm判定结果压合料边面 定位面特殊料边面 -0.5≤h ≤0.5;2.5≤d ≤3.5 合格焊缝搭接边 -1.0≤h ≤1.0;2.0≤d ≤4.0点焊搭接边 涉及外观\装配面料边 -0.5≤h ≤0.5;2.0≤d ≤4.0 定位孔0≤直径≤0.2;-0.5≤d ≤0.5; -0.5≤圆心位置偏移量≤0.5; 装配孔-0.2≤直径≤0.2;-0.5≤d ≤0.5; -0.5≤圆心位置偏移量≤0.5; 一般过孔 -0.5≤直径≤0.5;-1.0≤d ≤1.0; -1.0≤圆心位置偏移量≤1.0 一般边缘 1.5≤d ≤4.5;-1.0≤h ≤1.0一般型面2.0≤d ≤4.0说明:1、表中数值为制件检具测量的平度、间隙大小。
零件毛刺的工艺要求准则

零件毛刺的工艺要求通则
DSLBJ-JS-ZZ-002各工序除毛刺以图纸工艺要求为依据,未标尺寸工件棱边及孔边缘倒钝(倒角≥45°)为原则,且倒边打磨后,表面光滑平整。
毛刺判定以以下原则判定。
(1)各工种在加工过程中出现尖角毛刺的控制尺度以以下工艺要求作参考
A、根据生产批量采取合理的套裁方法,先下大料,后下小料,尽量提高材料的利用率。
B、零件为弯曲件或有料纹要求的,应按其料纹、轧展的方向进行裁剪。
C、钢板剪切截断的毛刺应符合表1的规定:
表1
对于气割下料或仿形下料的产品,毛刺的要求符合表2的规定
表2
钻孔加工的产品,毛刺的要求符合表3
表3
冲压类工件,毛刺的要求符合表4
(2)质量检查
A、对图纸和工艺卡片未注垂直度公差的零件,应测量对角线之差在≤550 毫米的对角线之差不大于1.5 毫米,在>550 毫米以上的对角线之差不大于3 毫米(按短边长度决定)。
B、逐件检查所裁的板料,应符合工艺卡或图纸的要求。
表4
剪切面长上
偏
差板厚
3-5 6-12 12-20 上偏差
300-600 -1 +0.5 +0.5 +1 >600-1000 +1 +1 +1.2 >1000-1500 +1.2 +1.5 +1.5 >1500-2000 +1.5 +2 +2 >2000-2800 +2 +2 +2.5 >2800-3500 -2 +2 +2 +2.5 >3500-5000 +2 +2.5 +2.5 5000以上+3 +3 +3.5。
剪板冲压毛刺控制标准

剪板冲压毛刺控制标准文件管理序列号:[K8UY-K9IO69-O6M243-OL889-F88688]QS/ZG电梯有限公司企业标准版本号:A0 ZG-CS62-2017发放部门:质管部持有部门:总经办、生产部、质管部剪板冲压毛刺控制标准编制:审核:批准:2017年06月15日发布 2017年07月01日实施电梯有限公司批准评审会签记录版本记录1.目的为标准规定了钣金冲裁加工毛刺长度标准,确定生产过程毛刺质量的控制标准。
2.范围本规范适用于公司所有的冲裁产品毛刺质量控制。
3.管理职责由制造部负责对冲裁产品进行自检工作,超出标准及时对隐患点处理。
由质管部负责对冲裁产品做好监控工作,并妥善保管相关检验记录。
4.冲裁件毛刺的极限值说明4.1冲裁件毛刺超过一定的高度是不允许的,冲压件毛刺高度的极限值(mm)见下表。
* f级(精密级)适用于较高要求的零件;m级(中等级)适用于中等要求的零件;g级(粗糙级)适用于一般要求的零件。
表1 冲压件毛刺高度的极限值4.2等级要求:技术图纸未注则按m级控制4.3毛刺的方向要求:毛边方向:朝里(朝使用时不可视的方向或折弯方向)。
4.4需要压毛边(毛刺打磨)的部位:对暴露在外面的断口;人手经常触摸到的锐边;需要过线缆的孔或槽;有相对滑动的部位需要对毛刺增加打磨工序,具体按图纸技术要求执行。
4.5常用材料抗拉强度参考(具体需查材料手册):冷轧钢板08F:295MPa; 1Cr18Ni9(SUS304不锈钢):≥520MPa;热轧钢板Q215:335~410mpa;热轧钢板Q235:375~500MPa;热轧钢板Q345:490~620MPa.5.不合格品控制按QSE-QP24-2017《不合格品控制程序》执行。
6.相关文件6.1 JB/T4129 -1999《冲压件毛刺高度》6.2 QSE-QP24-2017《不合格品控制程序》7.相关记录。
机械毛刺的控制和去除工艺
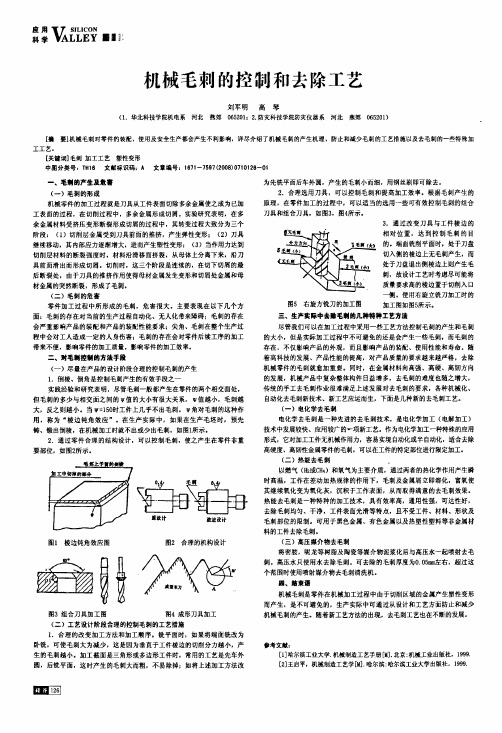
蠹墨弘渊_豁机械毛刺的控制和去除工艺刘军明(1.华北科技学院机电系河北燕郊06520l;高琴2.防灾科技学院防灾仪器系河北燕郊065201)[摘要】机械毛刺对零件的装配、使用及安全生产都会产生不利影响,详尽介绍了机械毛刺的产生机理、防止和减少毛刺的工艺措施以及去毛刺的一些特殊加工工艺。
【关键词]毛刺加工工艺塑性变形中图分类号:T H l6文献标识码:^文章编号:1671—7597(2008)0710126—01一、毛捌的产生及危謇(一)毛刺的形成机械零件的加工过程就是刀具从工件表面切除多余金属使之成为已加工表面的过程,在切削过程中,多余金属形成切屑。
实验研究表明,在多余金属材料受挤压变形断裂形成切屑的过程中,其转变过程大致分为三个阶段:(1)切削层金属受到刀具前面的推挤,产生弹性变形;(2)刀具继续移动,其内部应力逐渐增大,进而产生塑性变形;(3)当作用力达到切削层材料的断裂强度时,材料沿滑移面挤裂,从母体上分离下来,沿刀具前面滑出而形成切屑。
切削时,这三个阶段是连续的,在切下切屑的最后断裂处,由于刀具的推挤作用使得母材金属发生变形和切屑处金属和母材金属的突然断裂,形成了毛刺。
(二)毛刺的危害零件加工过程中所形成的毛刺,危害很大。
主要表现在以下几个方面:毛刺的存在对当前的生产过程自动化、无人化带来障碍:毛刺的存在会严重影响产品的装配和产品的装配性能要求;尖角、毛刺在整个生产过程中会对工人造成一定的人身伤害;毛刺的存在会对零件后续工序的加工带来不便,影响零件的加工质量。
影响零件的加工效率。
二、对毛朝控翻的方法手段(一)尽量在产品的设计阶段合理的控制毛刺的产生1.倒棱、倒角是控制毛刺产生的有效手段之一实践经验和研究表明,尽管毛刺一般都产生在零件的两个相交面处,但毛刺的多少与相交面之间的v值的大小有很大关系,v值越小,毛刺越大,反之则越小。
当v=150时工件上几乎不出毛刺。
v角对毛刺的这种作用,称为“棱边钝角效应”。
去毛刺作业规范

2、去毛刺方法分类
无毛刺或少毛刺设计和加工
零部件经过加工后在其相交棱边处会产生大小不同的毛刺,通过改变设计结构
和加工工艺,可以达到零件无或少毛刺,从而提高生产效率、减少成本和人工去毛
刺强。因此,无毛刺或少毛刺设计及加工是一种主动去毛刺方法。表1为无或少
毛刺设计及加工典型实例。
改进结构,减少毛刺影响 改进焊接零件设计,减少和消 除焊缝对装配使用的影响。
增加槽边缘倒角,去除毛刺。 在挡圈槽和阶梯轴处加工倒 角,倒角15。或0°最佳,可以 去除挡圈槽与内孔交接处棱 角以及阶梯轴交汇处棱角的 毛刺。
增加加工工序去除毛刺 阶梯孔系在不同尺寸孔交接 处、挡圈槽入口处、偏心孔入 口处易产生毛刺(如左图箭头 所示)。在保证尺寸精度的前 提下,采用两次精镗加工,可 以有效减少或去除毛刺。
有指导意义。由于产品的特殊性,不适用本标准的,允许制定相应作业指导书。
二、引用标准
JB4129冲压件毛刺高度
DIN6784各种工件的棱边标注
GB/T立式砂轮机用去毛刺和荒磨砂轮
三、去毛刺定义及方法分类
1、去毛刺定义
广义去毛刺流程如图1所示,是包含从设计去毛刺、机加工去毛刺、过程去毛 刺、专门去毛刺到清洗工艺的一个完整过程。 狭义去毛刺工艺主要指专门去毛刺工 序。
改变加工顺序去除毛刺
(a)先加工工作面,后加工 孔,工作面毛刺大;
(b)先加工孔,后加工面,
工作面无毛刺。
改变加工刀具,
减少工作面毛刺。
用端铣刀加工平面,毛刺多; 用圆柱铣刀加工平面,毛刺 少。
改变刀具刃口形状去除毛刺
文件编号
IQMS/JLW-JS-066A
去毛刺作业规范
(试行)
钣金冲压件毛刺高度标准及检验方法
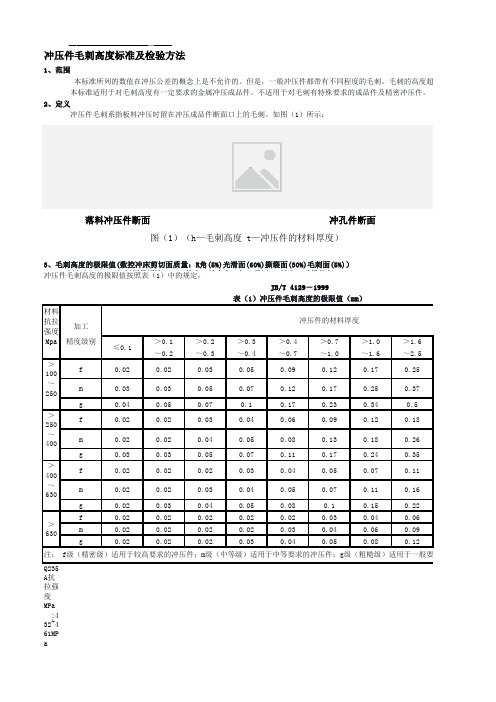
材料抗拉强度加工Mpa 精度级别>0.1>0.2>0.3>0.4>0.7>1.0>1.6~0.2~0.3~0.4~0.7~1.0~1.6~2.5>100f 0.020.020.030.050.090.120.170.25~250m 0.030.030.050.070.120.170.250.37g 0.040.050.070.10.170.230.340.5>250f 0.020.020.030.040.060.090.120.18~400m 0.020.020.040.050.080.130.180.26g 0.030.030.050.070.110.170.240.35>400f 0.020.020.020.030.040.050.070.11~630m 0.020.020.030.040.050.070.110.16g0.020.030.040.050.080.10.150.22f 0.020.020.020.020.020.030.040.06m 0.020.020.020.020.030.040.060.09g0.020.020.020.030.040.050.080.12Q235A抗拉强度MPa :432~461MP a本标准适用于对毛刺高度有一定要求的金属冲压成品件。
不适用于对毛刺有特殊要求的成品件及精密冲压件。
2、定义冲压件毛刺高度标准及检验方法1、范围本标准所列的数值在冲压公差的概念上是不允许的。
但是,一般冲压件都带有不同程度的毛刺。
毛刺的高度超过用性能。
冲压件毛刺系指板料冲压时留在冲压成品件断面口上的毛刺。
如图(1)所示:落料冲压件断面冲孔件断面图(1)(h—毛刺高度 t—冲压件的材料厚度)3、毛刺高度的极限值(数控冲床剪切面质量:R角(5%)光滑面(60%)撕裂面(30%)毛刺面(5%))(30%)毛刺面(5%),可切板厚最厚达4MM.。
特点:精度高,加工灵活.。
缺点:受模具限冲压件毛刺高度的极限值按照表(1)中的规定。
冲裁零件毛刺方向的控制

冲裁零件毛刺方向的控制一、引言-介绍冲裁零件毛刺问题的背景和重要性-阐述本论文的目的和意义二、毛刺的形成机理-毛刺的定义和特点-毛刺形成的原因-毛刺与金属材料的性质关系三、常见的毛刺控制方法-机械去毛刺-化学处理去毛刺-电化学去毛刺-激光去毛刺四、冲裁零件毛刺方向的控制-定义毛刺方向的概念-毛刺方向对产品质量的影响-控制毛刺方向的措施和方法五、未来的发展和应用-探讨新的去毛刺技术的发展趋势-未来在工业生产中对毛刺控制的需求-对冲裁技术的未来发展提出建议六、结论-总结本论文的内容和创新点-总结冲裁零件毛刺方向的控制对产品质量和工业生产的重要性-展望未来的研究方向和应用价值。
第一章引言随着制造业的发展,冲裁技术已经成为了工业生产中不可缺少的一部分,尤其在焊接、冲压和模具制造等行业中得到了广泛应用。
然而,在冲裁过程中,一些不可避免的因素会导致零件表面产生毛刺,从而影响产品质量和性能。
毛刺不仅会降低产品的美观度和整体质量,更会增加产品的摩擦阻力和润滑难度,进而引发一系列的问题。
因此,控制冲裁零件毛刺方向是重要的研究领域,目前国内外已经出现了许多相关的研究成果。
本论文主要围绕冲裁零件毛刺方向的控制展开研究,旨在提出一些有效的控制方法和技术路线,从而提高冲裁零件表面质量,进一步推动制造业的发展。
第二章毛刺的形成机理2.1 毛刺的定义和特点毛刺是冲压加工过程中在零件边缘和孔洞处产生的边缘材料扭曲的小尖刺,因为其形状呈现尖锐、颗粒状,给操作者带来触感上的不适,影响到人的舒适感;及对机器的损坏,甚至是对操作者的伤害。
毛刺常常形成在薄板的裂口处、小弯曲处、开口的边缘以及锐利的孔洞或切割区域等地方。
毛刺通常在冲裁后就形成,因此在制造和配件加工过程中已经成为了一个需要解决的问题。
2.2 毛刺的形成原因毛刺产生的原因非常多,常见的因素包括材料的硬度、摆动角度、冲模磨损、裁切模具的半径、冲压力等一系列因素。
其中,材料硬度、摆动角度和冲压力的大小是构成毛刺形成的最重要因素。
五金冲压件毛刺标准
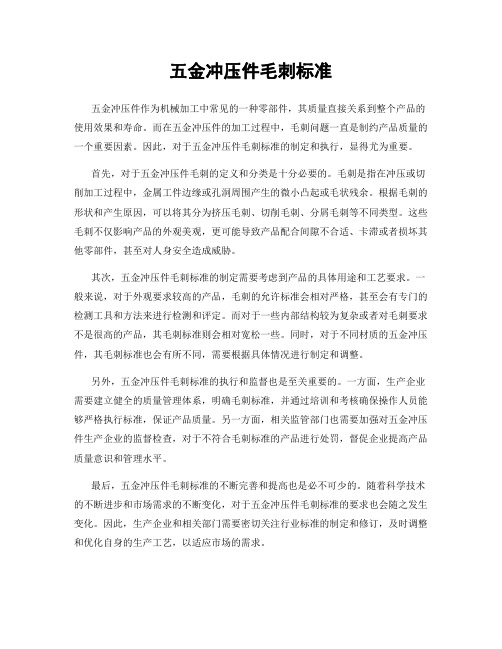
五金冲压件毛刺标准五金冲压件作为机械加工中常见的一种零部件,其质量直接关系到整个产品的使用效果和寿命。
而在五金冲压件的加工过程中,毛刺问题一直是制约产品质量的一个重要因素。
因此,对于五金冲压件毛刺标准的制定和执行,显得尤为重要。
首先,对于五金冲压件毛刺的定义和分类是十分必要的。
毛刺是指在冲压或切削加工过程中,金属工件边缘或孔洞周围产生的微小凸起或毛状残余。
根据毛刺的形状和产生原因,可以将其分为挤压毛刺、切削毛刺、分屑毛刺等不同类型。
这些毛刺不仅影响产品的外观美观,更可能导致产品配合间隙不合适、卡滞或者损坏其他零部件,甚至对人身安全造成威胁。
其次,五金冲压件毛刺标准的制定需要考虑到产品的具体用途和工艺要求。
一般来说,对于外观要求较高的产品,毛刺的允许标准会相对严格,甚至会有专门的检测工具和方法来进行检测和评定。
而对于一些内部结构较为复杂或者对毛刺要求不是很高的产品,其毛刺标准则会相对宽松一些。
同时,对于不同材质的五金冲压件,其毛刺标准也会有所不同,需要根据具体情况进行制定和调整。
另外,五金冲压件毛刺标准的执行和监督也是至关重要的。
一方面,生产企业需要建立健全的质量管理体系,明确毛刺标准,并通过培训和考核确保操作人员能够严格执行标准,保证产品质量。
另一方面,相关监管部门也需要加强对五金冲压件生产企业的监督检查,对于不符合毛刺标准的产品进行处罚,督促企业提高产品质量意识和管理水平。
最后,五金冲压件毛刺标准的不断完善和提高也是必不可少的。
随着科学技术的不断进步和市场需求的不断变化,对于五金冲压件毛刺标准的要求也会随之发生变化。
因此,生产企业和相关部门需要密切关注行业标准的制定和修订,及时调整和优化自身的生产工艺,以适应市场的需求。
总之,五金冲压件毛刺标准的制定和执行对于提高产品质量、保障产品安全具有重要意义。
只有建立科学合理的毛刺标准体系,加强执行和监督,不断完善和提高标准,才能更好地满足市场需求,推动五金冲压件行业的健康发展。
毛刺标准
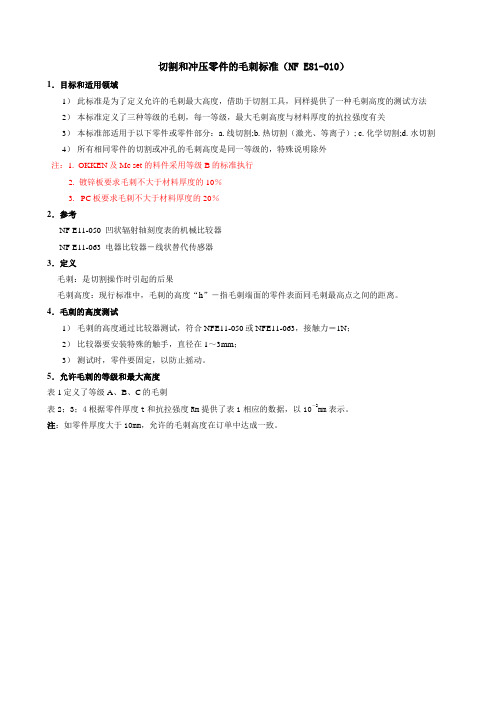
切割和冲压零件的毛刺标准(NF E81-010)
1.目标和适用领域
1)此标准是为了定义允许的毛刺最大高度,借助于切割工具,同样提供了一种毛刺高度的测试方法2)本标准定义了三种等级的毛刺,每一等级,最大毛刺高度与材料厚度的抗拉强度有关
3)本标准部适用于以下零件或零件部分:a. 线切割;b. 热切割(激光、等离子); c. 化学切割;d. 水切割4)所有相同零件的切割或冲孔的毛刺高度是同一等级的,特殊说明除外
注:1. OKKEN及Mc set 的料件采用等级B的标准执行
2. 镀锌板要求毛刺不大于材料厚度的10%
3. PC板要求毛刺不大于材料厚度的20%
2.参考
NF E11-050 凹状辐射轴刻度表的机械比较器
NF E11-063 电器比较器-线状替代传感器
3.定义
毛刺:是切割操作时引起的后果
毛刺高度:现行标准中,毛刺的高度“h”-指毛刺端面的零件表面同毛刺最高点之间的距离。
4.毛刺的高度测试
1)毛刺的高度通过比较器测试,符合NFE11-050或NFE11-063,接触力=1N;
2)比较器要安装特殊的触手,直径在1~3mm;
3)测试时,零件要固定,以防止摇动。
5.允许毛刺的等级和最大高度
表1定义了等级A、B、C的毛刺
表2;3;4根据零件厚度t和抗拉强度Rm提供了表1相应的数据,以10-2mm表示。
注:如零件厚度大于10mm,允许的毛刺高度在订单中达成一致。
表1:毛刺等级
表2:等级A 允许的最大毛刺高度;单位:10-2mm
表3. 等级B 允许的最大毛刺高度;单位:10-2mm
表4. 等级C 允许的最大毛刺高度;单位:10-2mm。
车间毛刺管理制度
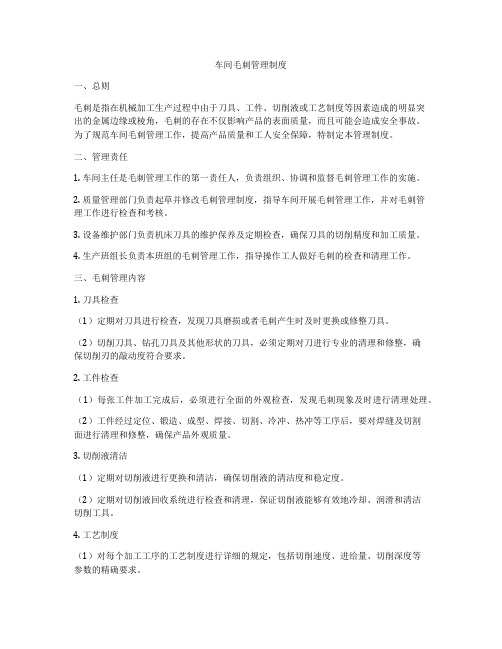
车间毛刺管理制度一、总则毛刺是指在机械加工生产过程中由于刀具、工件、切削液或工艺制度等因素造成的明显突出的金属边缘或棱角,毛刺的存在不仅影响产品的表面质量,而且可能会造成安全事故。
为了规范车间毛刺管理工作,提高产品质量和工人安全保障,特制定本管理制度。
二、管理责任1. 车间主任是毛刺管理工作的第一责任人,负责组织、协调和监督毛刺管理工作的实施。
2. 质量管理部门负责起草并修改毛刺管理制度,指导车间开展毛刺管理工作,并对毛刺管理工作进行检查和考核。
3. 设备维护部门负责机床刀具的维护保养及定期检查,确保刀具的切削精度和加工质量。
4. 生产班组长负责本班组的毛刺管理工作,指导操作工人做好毛刺的检查和清理工作。
三、毛刺管理内容1. 刀具检查(1)定期对刀具进行检查,发现刀具磨损或者毛刺产生时及时更换或修整刀具。
(2)切削刀具、钻孔刀具及其他形状的刀具,必须定期对刀进行专业的清理和修整,确保切削刃的敲动度符合要求。
2. 工件检查(1)每张工件加工完成后,必须进行全面的外观检查,发现毛刺现象及时进行清理处理。
(2)工件经过定位、锻造、成型、焊接、切割、冷冲、热冲等工序后,要对焊缝及切割面进行清理和修整,确保产品外观质量。
3. 切削液清洁(1)定期对切削液进行更换和清洁,确保切削液的清洁度和稳定度。
(2)定期对切削液回收系统进行检查和清理,保证切削液能够有效地冷却、润滑和清洁切削工具。
4. 工艺制度(1)对每个加工工序的工艺制度进行详细的规定,包括切削速度、进给量、切削深度等参数的精确要求。
(2)针对容易产生毛刺的工件和工序,要制定专门的清理工艺制度,确保产品的加工质量。
5. 操作规范(1)操作工人必须严格按照操作规程和作业指导书的要求进行生产操作,确保操作规范和安全生产。
(2)操作工人需经过专业培训,熟练掌握毛刺的检查和清理技术,提高工人的技术水平和质量意识。
四、管理措施1. 定期检查(1)质量管理部门定期对各个生产班组进行毛刺管理工作的检查,发现问题及时通知相关部门进行整改。
零件毛刺的产生和改善

【干货】零件毛刺的产生和改善01什么是毛刺毛刺的定义是指加工金属或树脂等材料时,产生的突出物,通常在镜像过程中或过程之后产生。
常用毛刺的高度、厚度和长度来表示。
在本文中,我们使用毛刺厚度来表示毛刺尺寸。
毛刺如果不去除,极有可能会导致零件无法正常运作。
至于外观方面,毛刺也会划伤其他产品,组装过程中也会出现测量问题,以及操作者安全问题。
02毛刺的大小和方向毛刺的大小和方向取决于工艺。
例如在金属加工工艺中,表面的外围会产生水平毛刺。
在这种情况下,刀具入口侧的毛刺尺寸与刀具的另一侧不同:在入口侧,毛刺往往较小;在出口侧,毛刺往往较大。
入口侧产生的毛刺称为初始毛刺,末端产生的毛刺称为翻边毛刺。
这种机制在钻孔过程中也是一样,在钻孔过程中,入口侧产生垂直毛刺,产生小的初始毛刺,在外面产生大的翻边毛刺。
03如何测量毛刺的尺寸测量毛刺尺寸的一些常用方法是使用千分尺和卡尺或数码显微镜。
使用表面粗糙度测试仪测量毛刺尺寸的方式与测量表面粗糙度相同,但这种方法只能测量非常小的毛刺。
选择合适的测量工具很重要,有很多方法可以测量毛刺大小或边缘状况,因此在选择工具之前,最好先决定如何评估毛刺或形状。
04如何检查已去除的毛刺2018年开始,我们对300多家加工企业进行的一项调查显示:61%的加工企业会通过手指触摸或使用放大镜目视检查的方式进行检查;此外还调查了询问操作员如何量化“去除所有毛刺”,其中34%表示低于10-50μm的毛刺是可以接受的,26%表示介于50μm-0.1mm之间。
05如何最小化毛刺尺寸如何控制毛刺方向最小化毛刺尺寸很重要,因为毛刺越大,需要去除它们的刀具就越少。
毛刺大小是由边缘的角度引起的,角度对毛刺大小至关重要。
大多数情况下,刃角为90度且锋利时,毛刺越大;反之,刃角越小,毛刺越小。
如果刃角精确到150度,则不会产生毛刺。
有时可能会遇到非常大的毛刺,这时建议改变切削刀具的刃角以减小毛刺尺寸。
至于边角毛刺差异,有时改变模具的形状并不容易,可以通过在切削条件上做一些改变来尝试。
工件去毛刺要求
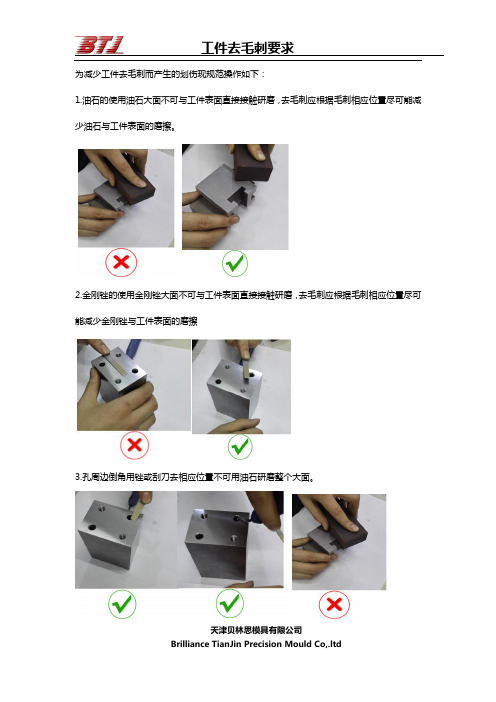
为减少工件去毛刺而产生的划伤现规范操作如下:
1.
油石的使用油石大面不可与工件表面直接接触研磨,
去毛刺应根据毛刺相应位置尽可能减少油石与工件表面的磨擦。
2.金刚锉的使用金刚锉大面不可与工件表面直接接触研磨,去毛刺应根据毛刺相应位置尽可能减少金刚锉与工件表面的磨擦
3.孔周边倒角用锉或刮刀去相应位置不可用油石研磨整个大面。
天津贝林思模具有限公司
天津贝林思模具有限公司
未按要求去毛刺造成工件划伤:
造成此类划伤按人为处理首次处罚200元,再犯直接终止与贝林思的劳动关系,如未发现责任者将处罚部门主管,请各部门主管执行监督。
冲压件毛刺高度标准
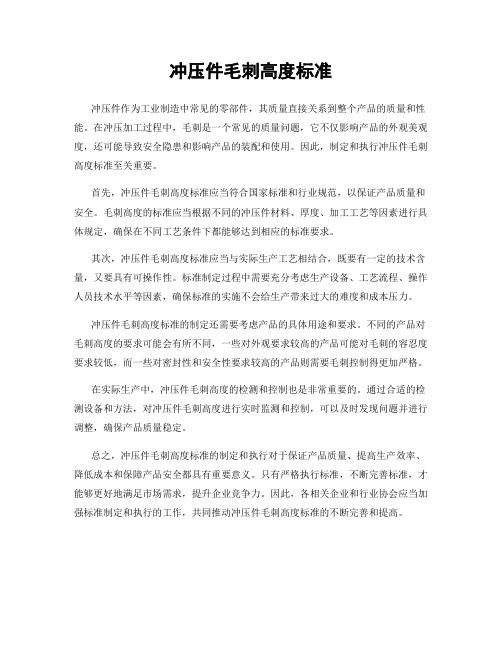
冲压件毛刺高度标准
冲压件作为工业制造中常见的零部件,其质量直接关系到整个产品的质量和性能。
在冲压加工过程中,毛刺是一个常见的质量问题,它不仅影响产品的外观美观度,还可能导致安全隐患和影响产品的装配和使用。
因此,制定和执行冲压件毛刺高度标准至关重要。
首先,冲压件毛刺高度标准应当符合国家标准和行业规范,以保证产品质量和安全。
毛刺高度的标准应当根据不同的冲压件材料、厚度、加工工艺等因素进行具体规定,确保在不同工艺条件下都能够达到相应的标准要求。
其次,冲压件毛刺高度标准应当与实际生产工艺相结合,既要有一定的技术含量,又要具有可操作性。
标准制定过程中需要充分考虑生产设备、工艺流程、操作人员技术水平等因素,确保标准的实施不会给生产带来过大的难度和成本压力。
冲压件毛刺高度标准的制定还需要考虑产品的具体用途和要求。
不同的产品对毛刺高度的要求可能会有所不同,一些对外观要求较高的产品可能对毛刺的容忍度要求较低,而一些对密封性和安全性要求较高的产品则需要毛刺控制得更加严格。
在实际生产中,冲压件毛刺高度的检测和控制也是非常重要的。
通过合适的检测设备和方法,对冲压件毛刺高度进行实时监测和控制,可以及时发现问题并进行调整,确保产品质量稳定。
总之,冲压件毛刺高度标准的制定和执行对于保证产品质量、提高生产效率、降低成本和保障产品安全都具有重要意义。
只有严格执行标准,不断完善标准,才能够更好地满足市场需求,提升企业竞争力。
因此,各相关企业和行业协会应当加强标准制定和执行的工作,共同推动冲压件毛刺高度标准的不断完善和提高。
冲压件毛刺高度标准及检测方法
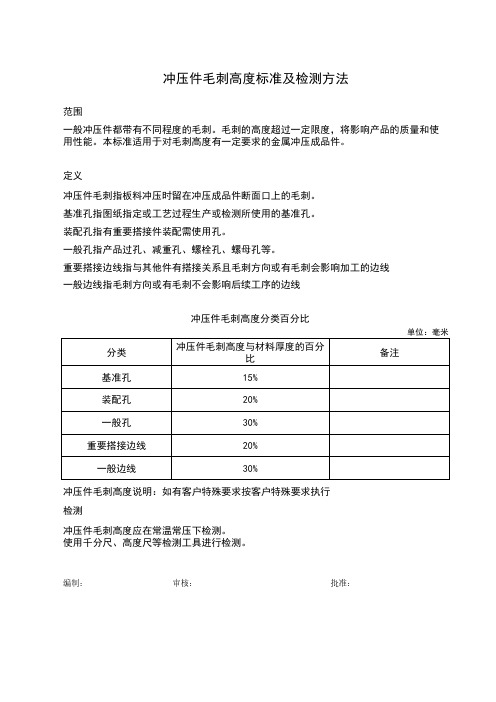
冲压件毛刺高度标准及检测方法
范围
一般冲压件都带有不同程度的毛刺。
毛刺的高度超过一定限度,将影响产品的质量和使用性能。
本标准适用于对毛刺高度有一定要求的金属冲压成品件。
定义
冲压件毛刺指板料冲压时留在冲压成品件断面口上的毛刺。
基准孔指图纸指定或工艺过程生产或检测所使用的基准孔。
装配孔指有重要搭接件装配需使用孔。
一般孔指产品过孔、减重孔、螺栓孔、螺母孔等。
重要搭接边线指与其他件有搭接关系且毛刺方向或有毛刺会影响加工的边线
一般边线指毛刺方向或有毛刺不会影响后续工序的边线
冲压件毛刺高度分类百分比
单位:毫米
分类冲压件毛刺高度与材料厚度的百分
比
备注
基准孔15%
装配孔20%
一般孔30%
重要搭接边线20%
一般边线30%
冲压件毛刺高度说明:如有客户特殊要求按客户特殊要求执行
检测
冲压件毛刺高度应在常温常压下检测。
使用千分尺、高度尺等检测工具进行检测。
编制:审核:批准:。
除毛刺工艺验规范

除毛刺工艺检验规范
目的:
指导品质检验人员了解除毛刺要求并能作出判定,减少客户投诉提升品质。
适用范围:
川信品质检验人员及打毛刺操作人员
定义:
A级面:具有装饰性重要表面,在产品开启或关闭状态,在正面可直视的面。
B 级面:具有半装饰性,但可经常可看到的处观面,日常维护时可视面。
C级面:不以装饰为目的,不能轻易观察到的内外表面。
操作步骤:
数冲加工完成后,转入下工序前必须除毛刺节点,工程在生产工艺清单上按客户要求增加去毛刺工艺,现场品检按工艺要求检验,判定合格后方可转序,如下工序发现未按工艺操作时可拒绝生产,并通知上工序返工,完成后品检用绿标标示。
质量要求:
A级面:不允许有任何毛刺节点,检测方式可采用戴细纱手套触摸,如有抽纱判定为不合格。
B 级面:用手指触及时无刮伤刺破感情用等危险,且不影性能判定为OK。
C 级面:不影响装配及性能时不作要求
以上要求仅指在本厂内完成组装,如客户要求为散件出货时,全部视为A级面,验收标准也将按A级面要求检验;针对圆孔或方孔及其它异形孔时,特别是以蚕蚀加工时,按正常表面等级要求;如有特殊要求,请工程必须标注说明,不允许毛刺,节点,利边等。
对毛刺部有什么安全要求
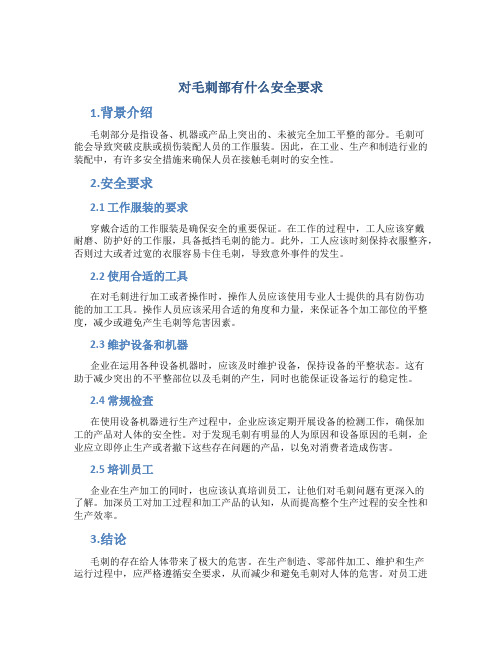
对毛刺部有什么安全要求1.背景介绍毛刺部分是指设备、机器或产品上突出的、未被完全加工平整的部分。
毛刺可能会导致突破皮肤或损伤装配人员的工作服装。
因此,在工业、生产和制造行业的装配中,有许多安全措施来确保人员在接触毛刺时的安全性。
2.安全要求2.1 工作服装的要求穿戴合适的工作服装是确保安全的重要保证。
在工作的过程中,工人应该穿戴耐磨、防护好的工作服,具备抵挡毛刺的能力。
此外,工人应该时刻保持衣服整齐,否则过大或者过宽的衣服容易卡住毛刺,导致意外事件的发生。
2.2 使用合适的工具在对毛刺进行加工或者操作时,操作人员应该使用专业人士提供的具有防伤功能的加工工具。
操作人员应该采用合适的角度和力量,来保证各个加工部位的平整度,减少或避免产生毛刺等危害因素。
2.3 维护设备和机器企业在运用各种设备机器时,应该及时维护设备,保持设备的平整状态。
这有助于减少突出的不平整部位以及毛刺的产生,同时也能保证设备运行的稳定性。
2.4 常规检查在使用设备机器进行生产过程中,企业应该定期开展设备的检测工作,确保加工的产品对人体的安全性。
对于发现毛刺有明显的人为原因和设备原因的毛刺,企业应立即停止生产或者撤下这些存在问题的产品,以免对消费者造成伤害。
2.5 培训员工企业在生产加工的同时,也应该认真培训员工,让他们对毛刺问题有更深入的了解。
加深员工对加工过程和加工产品的认知,从而提高整个生产过程的安全性和生产效率。
3.结论毛刺的存在给人体带来了极大的危害。
在生产制造、零部件加工、维护和生产运行过程中,应严格遵循安全要求,从而减少和避免毛刺对人体的危害。
对员工进行安全培训,并定期检查和维护设备和机器等方面,都是非常必要的工作,能够从根本上保障工人和消费者的健康和安全。
- 1、下载文档前请自行甄别文档内容的完整性,平台不提供额外的编辑、内容补充、找答案等附加服务。
- 2、"仅部分预览"的文档,不可在线预览部分如存在完整性等问题,可反馈申请退款(可完整预览的文档不适用该条件!)。
- 3、如文档侵犯您的权益,请联系客服反馈,我们会尽快为您处理(人工客服工作时间:9:00-18:30)。
零件毛刺的工艺要求通则
DSLBJ-JS-ZZ-002各工序除毛刺以图纸工艺要求为依据,未标尺寸工件棱边及孔边缘倒钝(倒角≥45°)为原则,且倒边打磨后,表面光滑平整。
毛刺判定以以下原则判定。
(1)各工种在加工过程中出现尖角毛刺的控制尺度以以下工艺要求作参考
A、根据生产批量采取合理的套裁方法,先下大料,后下小料,尽量提高材料的利用率。
B、零件为弯曲件或有料纹要求的,应按其料纹、轧展的方向进行裁剪。
C、钢板剪切截断的毛刺应符合表1的规定:
表1
对于气割下料或仿形下料的产品,毛刺的要求符合表2的规定
表2
钻孔加工的产品,毛刺的要求符合表3
表3
冲压类工件,毛刺的要求符合表4
(2)质量检查
A、对图纸和工艺卡片未注垂直度公差的零件,应测量对角线之差在≤550 毫米的对角线之差不大于1.5 毫米,在>550 毫米以上的对角线之差不大于3 毫米(按短边长度决定)。
B、逐件检查所裁的板料,应符合工艺卡或图纸的要求。
表4
剪切面长上
偏
差板厚
3-5 6-12 12-20 上偏差
300-600 -1 +0.5 +0.5 +1 >600-1000 +1 +1 +1.2 >1000-1500 +1.2 +1.5 +1.5 >1500-2000 +1.5 +2 +2 >2000-2800 +2 +2 +2.5 >2800-3500 -2 +2 +2 +2.5 >3500-5000 +2 +2.5 +2.5 5000以上+3 +3 +3.5。