齿轮热处理复习课程
齿轮零件的预备热处理工艺

齿轮零件的预备热处理工艺
齿轮零件的预备热处理工艺包括以下几个步骤:
1.清洗:将齿轮零件进行清洗,去除表面的油污或脏物。
2.均热:将齿轮零件放入炉内进行均热处理,使整个零件达到相同的温度,以便进行下一步的加热。
3.加热:将齿轮零件加热到所需的温度,一般为860-900的温度。
4.保温:将齿轮零件在所需温度下保持一定时间,以让零件内部充分均匀地达到所需温度,以便进行淬火处理。
5.淬火:将齿轮零件迅速放入淬火介质中,使其迅速冷却,以改善其力学性能。
6.回火:对淬火后的齿轮零件进行回火处理,以改善其韧性和耐磨性能,一般回火温度为300-600。
7.清洗:最后将齿轮零件进行清洗,以去除表面的氧化物和脏物。
以上是齿轮零件的预备热处理工艺。
齿轮材料热处理的讲义

(2) 渗碳炉的参数控制
对渗碳炉最基本的性能要求是碳势和炉温的有效控制。
目前碳势的间接测量大都通过一次仪表(传感器)在线连续测量渗碳
气氛的有关成分参数和温度,再由二次仪表(碳势控制仪)根据一次仪表
测得的参数和建立的气氛碳势数学模型自动计算得到气氛的实时碳势。
根据测定原理和采用测量气氛成分仪器的数量,一般有以下几种方法
表87 9CrSi、CrWMn和Cr钢淬火冷却条件与马氏体含碳量的关系 (试样尺寸为Ф10~15mm圆棒)
钢号
淬火温度 /℃
冷却介质
9CrSi
20℃的水 875 30℃的油
170℃的硝盐,空冷
CrWM n
20℃的水 840 30℃的油
170℃的硝盐,空冷
20℃的水
Cr
850 30℃的油
170℃的硝盐,空冷
在金相观察中,马氏体针与残余奥氏体密切相关,粗大的马氏体针总是伴随关大 量的残余奥氏体存在。
在齿轮的渗碳和C-N共渗中常常在表面产生非马氏体黑色组织,当其深度 达到一定程度时就会对接触疲劳寿命产生不利影响,表89是一试验结果。
表89 黑色组织对接触疲劳寿命的影响
C-N共渗层深 (mm)
黑色组织层深 (mm)
用于自适应 法工艺控制 和工艺过程
记录管理
一般
○
较高
○
○
连 续炉
一般
○
较高
○
3.5.3 淬火冷却
渗碳后的齿轮对淬火冷却的要求:达到要求的表面硬度和心部硬度; 达到要求的有效硬化层深度;尽量小的淬火变形。
(1) 淬火介质 为了达到以上三条要求,合理选择淬火介质就显得尤为重要,通常可 按以下原则选用: a)钢材的含碳量 齿轮钢材含碳量与心部硬度有关,心部含碳量越低 ,要求淬火油的冷却速度就越高。 b)钢材的淬透性 齿轮钢材淬透性越高,淬火油的冷却速度就可以低 些。 c)齿轮有效厚度 齿轮有效厚度越大,要求淬火介质冷却速度就越高 。 d)齿轮结构形状 齿轮结构形状越复杂,要求淬火介质的最高冷却速 度越低。
2024版《机械设计基础》第六章齿轮传动

安全系数
在强度计算中引入安全系数,以保证齿轮 在极端工况下仍能安全可靠地工作。
齿轮疲劳寿命预测方法
疲劳寿命概念
齿轮在循环载荷作用下,经过一定次 数的应力循环后发生疲劳破坏的寿命。
影响因素
齿轮的疲劳寿命受多种因素影响,如 材料性能、制造工艺、润滑条件和使 用环境等。
预测方法
基于疲劳累积损伤理论,结合齿轮的 受力分析和材料特性,采用试验或数 值模拟等方法预测齿轮的疲劳寿命。
确定合理的齿轮参数
包括模数、齿数、压力角、螺旋角等, 以满足传动比、承载能力和传动平稳 性等要求。
保证齿轮的精度和强度
通过合理的制造工艺和材料选择,确 保齿轮具有足够的精度和强度,以承 受传动过程中的载荷和冲击。
考虑润滑和冷却
为齿轮传动装置提供适当的润滑和冷 却,以减少磨损、降低温度和防止腐 蚀。
典型齿轮传动装置实例分析
齿轮热处理工艺选择及优化
退火
消除齿轮内部应力,降低硬度,便 于加工。
正火
提高齿轮硬度和强度,改善切削性 能。
淬火
使齿轮获得高硬度和高耐磨性,提 高齿轮使用寿命。
回火
消除淬火产生的内应力,稳定齿轮 尺寸,提高韧性。
齿轮制造工艺流程简介
01
02
齿轮毛坯加工
包括锻造、铸造、焊接等工艺, 获得齿轮的基本形状。
齿轮传动具有传动比准确、效率高、结构紧凑、工作可靠、寿命长等 优点。同时,齿轮传动也具有制造和安装精度要求高、成本较高等缺 点。
齿轮传动分类及应用
分类
根据齿轮的轴线相对位置,齿轮传动可分为平行轴齿轮传动、 相交轴齿轮传动和交错轴齿轮传动。根据齿轮的齿形,齿轮传 动又可分为直齿、斜齿、人字齿、圆弧齿等。
20CrMnMo齿轮热处理工艺设计课程设计(Word最新版)

20CrMnMo齿轮热处理工艺设计课程设计通过整理的20CrMnMo齿轮热处理工艺设计课程设计相关文档,希望对大家有所帮助,谢谢观看!20CrMnMo齿轮热处理目录1 绪论1 1.1 热处理工艺课程设计的目的1 1.2 课程设计的任务1 1.3 热处理工艺设计的方法1 2 热处理工艺课程设计内容和步骤 1 2.1 课题工件简图 1 2.2 技术要求:2 2.3 特点2 2.4 适用范围2 2.5 齿轮的性能要求及为何选用20CrMnMo 2 2.6 化学成分作用3 2.7 20CrMnMo钢的淬透性曲线4 2.8 淬透性5 2.9 渗碳热处理工艺规范5 2.10 钢的等温转变和连续冷却转变 5 3 热处理工艺方案以及参数论述 6 3.1 热处理工艺流程 6 3.2 热处理工艺方案论证 6 3.2.1 20CrMnMo处理温度以及冷却方式6 3.2.2 热处理方案制定6 3.3 热处理方案6 3.3.1 正火7 3.3.2 正火工艺曲线7 3.3.3 正火冷却8 3.4 20CrMnMo的渗碳工艺8 3.4.1 渗碳的目的8 3.4.2 渗碳过程8 3.5 20CrMnMo的淬火工艺9 3.5.1 渗碳后一次重新加热淬火的目的9 3.5.2 淬火事项9 3.6 低温回火工艺10 3.6.1 回火的目的10 3.6.2 回火温度11 3.6.3 加热介质11 3.6.4 保温时间11 3.6.5 回火工艺曲线11 3.6.6 冷却方式12 4 总的热处理工艺曲线12 4.1 热处理总工艺曲线12 4.2 选择加热设备12 4.2.1 装置选择:井式电阻炉12 4.2.2井式炉示意图13 4.3.1 井式气体渗碳炉型号规格及技术数据13 5 工装图14 5.1 工装图及装件14 6 工序质量检验15 7 热处理工艺过程中常见缺陷分析15 7.1 常见的淬火及防护措施15 7.2 常见的渗碳缺陷及防护措施16 8 心得体会17 9 参考文献17 20CrMnMo齿轮热处理工艺设计1 绪论1.1 热处理工艺课程设计的目的热处理工艺课程设计是高等工业学校金属材料工程专业一次专业课设计练习,是热处理原理与工艺课程的最后一个教学环节。
工程齿轮的材料选择与热处理技术

工程齿轮的材料选择与热处理技术工程齿轮作为机械传动系统中重要的零部件之一,其材料选择和热处理技术影响着齿轮的强度、硬度和耐磨性等性能指标。
本文将就工程齿轮的材料选择和热处理技术展开讨论,帮助读者更好地理解和应用于实际工程中。
一、工程齿轮的材料选择工程齿轮的材料选择主要考虑以下几个因素:1. 强度要求:工程齿轮在传动系统中承受较大的载荷,因此材料的强度是选择的首要考虑因素。
常用的工程齿轮材料有合金钢、碳钢和铸铁等。
合金钢具有较高的强度和硬度,适用于对强度和耐磨性较高的场合。
碳钢适用于载荷较小的场合,成本较低。
铸铁适用于低速低载的场合,但其硬度较低。
2. 耐磨性要求:工程齿轮在传动过程中会发生摩擦和磨损,因此对材料的耐磨性要求较高。
合金钢具有较好的耐磨性,因此在对耐磨性要求较高的工程齿轮中应用较多。
对于低速低载的场合,碳钢和铸铁也能满足耐磨性要求。
3. 制造成本:工程齿轮的制造成本也是材料选择的一个重要考虑因素。
合金钢相对于碳钢和铸铁而言,制造成本较高。
因此,在经济性要求较高的场合,碳钢和铸铁更具优势。
二、工程齿轮的热处理技术工程齿轮的热处理技术主要包括淬火、回火和渗碳等。
热处理可以提高工程齿轮的硬度、强度和耐磨性等性能。
1. 淬火:淬火是将工程齿轮材料加热至临界温度,经过快速冷却使其组织发生变化,从而获得较高的硬度和强度。
淬火过程中,要控制冷却速度和温度,以避免产生过高的应力和变形。
2. 回火:回火是通过将淬火后的工程齿轮材料加热至较低的温度,使其硬度降低,同时提高韧性。
回火过程中,要控制回火温度和时间,以获得理想的硬度和韧性组织。
3. 渗碳:渗碳是将工程齿轮材料放入渗碳剂中,在高温下进行温度保持一定时间,使渗碳剂中的碳元素渗入工程齿轮表面,从而提高其表面硬度和耐磨性。
渗碳过程中,要控制温度、温度保持时间和碳含量,以获得理想的渗碳层。
总结:工程齿轮的材料选择和热处理技术对其性能有着重要影响。
在材料选择时,需要考虑强度要求、耐磨性要求和制造成本等因素。
常用齿轮材料选择及其热处理工艺
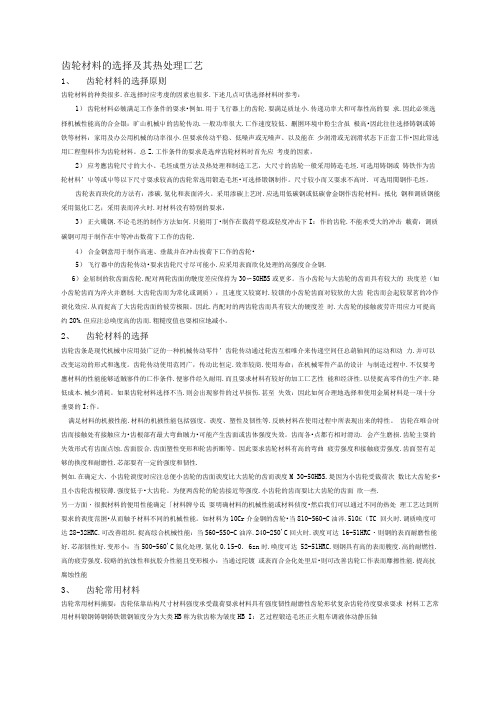
齿轮材料的选择及其热处理匸艺1、齿轮材料的选择原则齿轮材料的种类很多.在选择时应考虔的因素也很多.下述几点可供选择材料时参考:1)齿轮材料必皴满足工作条件的耍求•例如.用于飞行器上的齿轮.耍满足质址小.传递功率大和可靠性高的耍求.因此必须选择机械性能高的合佥银:旷山机械屮的齿轮传动.一般功率很大.匸作速度较低、删圉环境中粉尘含虽极高•因此往往选择铸钢或铸铁等材料:家用及办公用机械的功率很小.但要求传动平稳、低噪声或无噪声、以及能在少润滑或无润滑状态下正當工作•因此常选用匸程塑料作为齿轮材料。
总Z.工作条件的耍求是选痒齿轮材料时首先应考虔的因素,2)应考應齿轮尺寸的大小、毛坯成型方法及热处理和制造工艺,大尺寸的齿轮一般采用铸造毛坯.可选用铸钢或铸铁作为齿轮材料’屮等或屮等以下尺寸耍求较高的齿轮常选用锻造毛坯•可选择锻钢制作。
尺寸较小而又耍求不高时. 可选用閲钢作毛坯,齿轮表而玦化的方法有:渗碳.氨化和表面淬火。
采用渗碳上艺时.应选用低碳钢或低碳會金钢作齿轮材料:抵化钢和调质钢能采用氮化匸艺;采用表而淬火时.对材料没有特别的耍求,3)正火磯钢.不论毛坯的制作方法如何.只能用丁•制作在裁荷平稳或轻度冲击下I:作的齿轮.不能承受大的冲击載荷:调质碳钢可用于制作在中等冲击数荷下工作的齿轮.4)合金钢當用于制作高速、垂裁并在冲击拔荷下匸作的齿轮•5)飞行器中的齿轮传动•耍求齿轮尺寸尽可能小.应采用表面欣化处理的高强度合佥钢.6)金屈制的软齿面齿轮.配对两轮齿面的駛度差应保持为30〜50HBS或更多。
当小齿轮与大齿轮的齿而具有较大的玦度差(如小齿轮齿而为淬火并磨制.大齿轮齿而为常化或调质):且速度又较窩时.较锁的小齿轮齿面对较软的大齿轮齿而会起较眾茗的冷作谀化效应.从而捉高了大齿轮齿面的彼劳极限。
因此.肖配对的两齿轮齿而具有较大的硬度差时.大齿轮的接触疲劳许用应力可提高约20%.但应注总唤度高的齿而.粗糙度值也耍相应地减小。
标准齿轮的加工课程设计
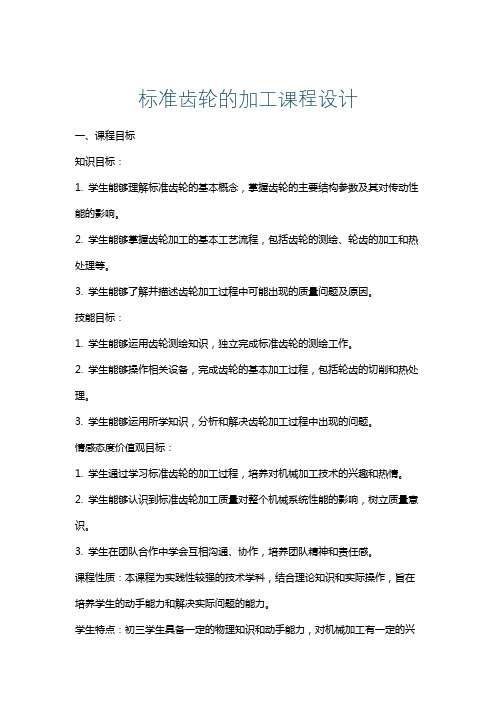
标准齿轮的加工课程设计一、课程目标知识目标:1. 学生能够理解标准齿轮的基本概念,掌握齿轮的主要结构参数及其对传动性能的影响。
2. 学生能够掌握齿轮加工的基本工艺流程,包括齿轮的测绘、轮齿的加工和热处理等。
3. 学生能够了解并描述齿轮加工过程中可能出现的质量问题及原因。
技能目标:1. 学生能够运用齿轮测绘知识,独立完成标准齿轮的测绘工作。
2. 学生能够操作相关设备,完成齿轮的基本加工过程,包括轮齿的切削和热处理。
3. 学生能够运用所学知识,分析和解决齿轮加工过程中出现的问题。
情感态度价值观目标:1. 学生通过学习标准齿轮的加工过程,培养对机械加工技术的兴趣和热情。
2. 学生能够认识到标准齿轮加工质量对整个机械系统性能的影响,树立质量意识。
3. 学生在团队合作中学会互相沟通、协作,培养团队精神和责任感。
课程性质:本课程为实践性较强的技术学科,结合理论知识和实际操作,旨在培养学生的动手能力和解决实际问题的能力。
学生特点:初三学生具备一定的物理知识和动手能力,对机械加工有一定的兴趣,但缺乏系统性的齿轮加工知识。
教学要求:结合学生特点,注重理论与实践相结合,充分调动学生的积极性,引导他们通过实际操作掌握齿轮加工的基本技能。
在教学过程中,关注学生的个体差异,提供针对性的指导,确保每位学生都能达到课程目标。
通过课程学习,使学生能够将所学知识应用于实际工作中,提高其综合素养。
二、教学内容1. 齿轮基本概念:齿轮的分类、结构参数(齿数、模数、压力角等)及其对传动性能的影响。
2. 齿轮测绘:测绘工具的使用、齿轮的测量方法、数据处理及齿轮图的绘制。
3. 齿轮加工工艺:齿轮加工的基本工艺流程、轮齿的切削加工(滚齿、插齿、剃齿等)、热处理工艺及其对齿轮性能的影响。
4. 齿轮加工设备:认识齿轮加工的主要设备及其功能,如滚齿机、插齿机、磨齿机等。
5. 齿轮加工质量控制:分析齿轮加工过程中可能出现的质量问题(如齿面磨损、齿形误差等)及其原因,探讨提高加工质量的措施。
20crmnti 齿轮 热处理

题目:20crmnti 齿轮热处理一、20crmnti 齿轮的特性和用途20crmnti 钢是一种具有优良机械性能和热处理性能的中碳合金结构钢,常用于制造重载齿轮、轴、连杆、轴承和齿条等零部件。
其主要特点包括高强度、高硬度、耐磨性好、疲劳强度高、具有一定的韧性和可塑性等。
在重载、高速、高温和频繁启动等要求苛刻的工作条件下,20crmnti 齿轮表现出色,被广泛应用于工程机械、汽车、船舶、轨道交通等领域。
二、20crmnti 齿轮热处理工艺热处理是指通过控制材料的加热、保温和冷却等过程,改变材料的组织结构和性能。
对于20crmnti 钢制造的齿轮来说,合理的热处理工艺对其性能和使用寿命起着至关重要的作用。
一般的20crmnti 齿轮热处理工艺包括淬火和回火两个主要过程。
1. 淬火淬火是热处理的重要工艺环节之一。
通过高温加热至奥氏体区,然后迅速冷却至马氏体区,以获得高硬度和高强度的组织结构。
对于20crmnti 齿轮来说,淬火工艺的温度、保温时间和冷却介质的选择都会对最终的性能产生重要影响。
合理的淬火工艺能够使齿轮表面获得较高的硬度,提高其耐磨性和疲劳强度,同时保持一定的韧性。
2. 回火回火是淬火后的齿轮进行的第二次热处理工艺。
通过对淬火后的齿轮进行中温加热一段时间,然后再空冷或油冷,以调整其组织结构和性能。
合理的回火工艺能够降低淬火时产生的残余应力,提高齿轮的韧性和塑性,使其在工作过程中不易产生变形和开裂。
三、20crmnti 齿轮热处理的注意事项在进行20crmnti 齿轮热处理时,需要注意以下几点:1. 温度控制:热处理温度是影响齿轮性能的重要因素,需严格控制在设计要求的范围之内。
2. 冷却介质选择:不同的冷却介质会对齿轮的硬度和残余应力产生影响,需要根据具体情况选择合适的冷却介质。
3. 工艺参数优化:包括加热温度、保温时间、冷却速度等工艺参数需要根据齿轮的实际情况进行优化调整。
4. 试样取样:进行热处理前需要取样进行试验,以确定最佳的热处理工艺。
齿轮零件的材料、毛坯及热处理(精)

齿面热处理
为了提高齿面硬度、 增加齿轮的承载能力和 耐磨性,通常在滚、插、 剃齿之后,珩、磨齿之 前安排齿面高频感应加 热淬火、渗碳淬火、氮 碳共渗和渗氮等热处理 工序。
精密机械制造基础 四、课程总结
1
齿轮零件的材料
课 程 总 结
3
2
齿轮的毛坯
齿轮的热处理
精密机械制造基础 五、思考题
现要设计一个用于矿山带式输送机上的双级减速器中的低速级直
40Cr、球墨铸铁
精密机械制造基础 二、齿轮的毛坯 齿轮常用的毛坯是铸铁件、棒料、锻坯和铸钢坯。
棒料 铸铁件 锻坯
铸钢坯
精密机械制造基础 三、齿轮的热处理
在齿轮加工工艺中,热处理工序的位置安排十分重要,它直接影响 齿轮的力学性能及切削加工的难易程度。
毛坯热处理
为了消除铸造、 锻造和粗加工造成的 残余应力,改善齿轮 材料内部的金相组织 和切削加工性能,通 常在齿轮毛坯加工前 后安排调质或正火等 预热处理。
齿轮零件材料、毛坯及热处理
主讲教师:时虹 副教授
精密机械制造基础
目 录
01
02
齿轮零件的材料 齿轮的毛坯
03
04
齿轮一、齿轮零件的材料
齿轮应根据使用要求和工作条件选取合适的材料,普通齿轮选用中碳钢 和中碳合金钢,如40、45、40Cr、42SiMn等;强度要求高的齿轮可选取 20Mn2B、18CrMnTi、20Cr等低碳合金钢;对于低速轻载的开式传动的齿 轮可选取ZG40、ZG45等铸钢材料或灰铸铁;非传力齿轮可选取尼龙、夹 布胶木或塑料等。
齿圆柱齿轮传动机构,已知低速级小齿轮功率p1=29kw,输入转速 n1=242.2r/min,传动比 i=3.5,工作机载荷有轻微冲击,每天工作 12小时,结构紧凑,输送机单向运转,可靠性一般,试选择该低速级 齿轮传动机构中齿轮的材料、毛坯及热处理方式。
齿轮所有热处理总结-

--齿轮热处理例如:30CrMnTi 调质275~310HB,齿轮表面淬火58~63HRC,淬火深度1~2mm一、工作条件以及材料与热处理要求1.条件: 低速、轻载又不受冲击要求: HT200 HT250 HT300 去应力退火2.条件: 低速(<1m/s)、轻载,如车床溜板齿轮等要求: 45 调质,HB200-2503.条件: 低速、中载,如标准系列减速器齿轮--要求: 45 40Cr 40MnB (5042MnVB) 调质,HB220-2504.条件: 低速、重载、无冲击,如机床主轴箱齿轮要求: 40Cr(42MnVB) 淬火中温回火HRC40-455.条件: 中速、中载,无猛烈冲击,如机床主轴箱齿轮要求: 40Cr、40MnB、42MnVB 调质或正火,感应加热表面淬火,低温回火,时效,HRC50-556.条件: 中速、中载或低速、重载,如车床变速箱中的次要齿轮要求: 45 高频淬火,350-370℃回火,HRC40-45(无高频设备时,可采用快速加热齿面淬火)7.条件: 中速、重载要求: 40Cr、40MnB(40MnVB、42CrMo、40CrMnMo、40CrMnMoVBA)淬火,中温回火,HRC45-50.8.条件: 高速、轻载或高速、中载,有冲击的小齿轮要求: 15、20、20Cr、20MnVB渗碳,淬火,低温回火,HRC56-62.38CrAl 38CrMoAl 渗氮,渗氮深度0.5mm,HV900 9.条件: 高速、中载,无猛烈冲击,如机床主轴轮.要求: 40Cr、40MnB、(40MnVB)高频淬火,HRC50-55.10.条件: 高速、中载、有冲击、外形复杂和重要齿轮,如汽车变速箱齿轮(20CrMnTi淬透性较高,过热敏感性小,渗碳速度快,过渡层均匀,渗碳后直接淬火变形较小,正火后切削加工性良好,低温冲击韧性也较好)要求: 20Cr、20Mn2B、20MnVB渗碳,淬火,低温回火或渗碳后高频淬火,HRC56-62.18CrMnTi、20CrMnTi(锻造→正火→加工齿轮→局部镀同→渗碳、预冷淬火、低温回火→磨齿→喷丸)渗碳层深度1.2-1.6mm,齿轮硬度HRC58-60,心部硬度HRC25-35.表面:回火马氏体+残余奥氏体+碳化物.中心:索氏体+细珠光体11.条件: 高速、重载、有冲击、模数<5要求: 20Cr、20Mn2B 渗碳、淬火、低温回火,HRG56-62.12.条件: 高速、重载、或中载、模数>6,要求高强度、高耐磨性,如立车重要螺旋锥齿轮要求: 18CrMnTi、20SiMnVB 渗碳、淬火、低温回火,HRC56-6213.条件: 高速、重载、有冲击、外形复杂的重要齿轮,如高速柴油机、重型载重汽车,航空发动机等设备上的齿轮.要求: 12Cr2Ni4A、20Cr2Ni4A、18Cr2Ni4W A、20CrMnMoVBA(锻造→退火→粗加工→去应力→半精加工→渗碳→退火软化→淬火→冷处理→低温回火→精磨)渗碳层深度1.2-1.5mm,HRC59-62.14.条件: 载荷不高的大齿轮,如大型龙门刨齿轮要求: 50Mn2、50、65Mn 淬火,空冷,HB≤24115.条件: 低速、载荷不大,精密传动齿轮.要求: 35CrMO 淬火,低温回火,HRC45-5016.条件: 精密传动、有一定耐磨性大齿轮.要求: 35CrMo 调质,HB255-302.17.条件: 要求抗磨蚀性的计量泵齿轮.要求: 9Cr16Mo3VRE 沉淀硬化18.条件: 要求高耐磨性的鼓风机齿轮.要求: 45 调质,尿素盐浴软氮化.19.条件: 要求耐、保持间隙精度的25L油泵齿轮。
热处理期末考试复习资料
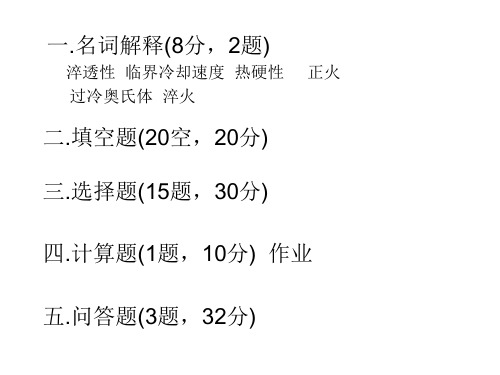
1. 完全退火主要适用于( A. 亚共析钢 B. 共析钢 2. 扩散退火的目的为(
)。 C. 过共析钢 )。
A. 消除和改善晶内偏析 B. 消除冷塑性变形后产生的加工硬化 C. 降低硬度以便加工 3. 球化退火的温度是( 火温度为( ) A. 550-650 ℃ B. AC1-AC3线之间 C. AC3线以上 )。去应力退
27. 下列组织硬度最高的是( )。 A.回火马氏体 B.回火托氏体 C.回火索氏体 28. 小齿轮的表面热处理用的方法是( )。 A.高频感应加热 B.中频感应 C.工频感应加热 29. 化学热处理与其他热处理方法的基本区别是( )。 A· 加热温度 B.组织变化 C.改变表面化学成分 30. 用l5钢制造的齿轮,要求齿轮表面硬度高而心部具有良好的综 合力学性能,应采用( )处理。
)。
11、含碳量在0.5-0.75%的碳钢,应采用(
A.退火 B.回火C.淬火 D正火12、ya共析钢的正常淬火加热温度是(
A.Acm十(30—50℃) B.Ac3十(30—50℃) C.Ac1十(30—50℃) D.Ac1一(30—50℃)
)。
13 某工件形状简复杂,截面尺寸小,采用( 淬火介质可以减小变形和开裂。
A.淬火+低温回火 B.表面淬火+低温回火 C.渗碳+淬火+低温回火
31. 经过热处理过后的刀具,如锯条,其硬度指标应用 ( )表示。
A.HV B.HB C.HRC
32.用45钢制造的齿轮,要求齿轮表面硬度高而心部具有良好的 综合力学性能,应采用( )处理 。
A.淬火+低温回火 B.调质+表面淬火+低温回火 C.表面淬火+低温回火
33.零件渗碳后一般必须经( 耐磨。
陈国民:齿轮材料和热处理1

(3)金相组织 淬火钢表层含有5%的非马氏体(体积分数)组织时,弯曲疲劳 极限将降低10%。图3是非马氏体组织对弯曲疲劳极限的影响。对于马氏体组织, 只有经过适当回火后才有良好的疲劳性能。
疲 劳 极 限
40Mn2 42MnMo 40CrNiMo 40Cr 40B
图3 非马氏体组织对疲劳极限的影响
σ-1/MPa
平均寿命周 次(×106)
寿命 比
3.15~4.41
3.85
1.00
1.88~2.21
2.08
0.54
4.89~5.20
5.06
1.31
注:
1.喷丸工艺:喷丸在转台喷丸机上进行,铁丸尺寸为Ф0.6~Ф1.0mm,喷射速度为58.3m/s,转台每转一 圈,将零件转90°,一般喷丸共喷四圈,强化喷丸喷八圈。 2.齿轮用20Mn2TiB钢制造,经气体渗碳(层深1.0~1.3mm),淬火及回火。 3.试验在封闭式变速箱试验台上进行,中间轴挂一档作运转试验,以中轴一档齿轮的损伤为寿命的标准。
5 8 ~ 6 4 HRC 或 7 5 . 7 ~ 81.1HR30N,同炉热处理件数 ≤5时全部检查,否则抽查
7.2
模 数 ≥ 1 2 mm 时 齿 宽 中线齿根区域的表面
不规定
满足图样要求,抽查代 满足图样要求,全部检
8 心部硬度
21HRC以上
25HRC以上
推荐测量位置:齿宽中部齿根30°切线的 法向上,深度为5倍硬化层深,但不小于1 倍模数。可按技术条件要求,或采用供需 双方协议的检查方法进行检测。
GB/T 10561方法B检验Ⅱ区纯度,检验面积近200mm2.下表为夹杂物
3
纯度及冶炼
级别。
A
B
陈国民齿轮材料和热处理PPT课件

△ ▲晶间脆裂 ▲ ◎ -
抗磨损能力 ◎硬度高较好 △
▲硬度降低 ○硬度提高 ▲硬度下降 -
第4页/共90页
3.2.3 钢材的淬火冷却 (1)钢材的淬透性表示方法
表37 钢材的淬透性表示方法
方法名称
方法要点
表示法
末端淬 火法
采用一种端淬试样,在标准条件下淬火,测 量从水冷端开始的硬度梯度,测量方法细则 可参见GB225-88
a)42CrMo钢的淬透性曲线
3
第15页/共90页
b)硬度分布曲线
c.齿轮毛坯的求法 齿轮毛坯件调质后截面硬度的分布求法,其关 键是截面尺寸的确定。实际使用中可根据各种齿轮的结构特点归并为圆 形截面和板状截面两种,然后再按上述两种截面的硬度分布求法来求作。 表45列举了7种典型结构齿轮截面尺寸的确定方法,可供参考。
163~192HBS 179~212HBS 201~229HBS
45~50HRC
269~302HBS 201~229HBS
56~62HRC
269~302HBS 201~229HBS
齿面硬度大致相同
45~50HRC 56~62HRC
第11页/共90页
3.3.2 齿轮钢材调质硬度的确定 调质齿轮淬火后的最低硬度主要决定于所要求的强度,并考虑具有
30
以20℃水为标准的相对冷却强 度H
650~550℃
300℃
1.00
1.00
0.79
1.00
0.54
0.82
0.19
0.06
0.30
0.07
0.40
0.11
0.69
0.94
0.60
0.53
0.52
航空齿轮的选择和热处理方法

航空齿轮的选择和热处理方法
1、选材方法
航空齿轮是用以传递动力和改变运行速度的,对齿轮的要求是齿面应耐磨损,抗接触疲劳强高,而齿根应抗弯曲疲劳破坏。
航空上常用w(C)为0.10%~0.20%的高淬透性钢,渗碳后进淬火、低温回火使用。
渗碳层深度可取模数的15%~20%,或取节圆处齿厚的10%~20%。
航齿轮加工工艺路线:
(1)锻件毛坯→正火或调质→机械加工→渗碳及淬火→低温回火→机械加工至成品。
(2)锻件毛坯→正火或调质→机械加工→镀铜(非渗碳表面)→渗碳→除铜→淬火→低温火→机械加工至成品。
(3)锻件毛坯→正火或调质→机械加工→渗碳→机械加工→淬火→低温回火→机械加工成品。
(4)锻件毛坯→正火+调质→机械加工→镀锡或镀铜→渗氮→机械加工至成品。
航空齿轮常用材料及技术要求见表1。
表1. 航空齿轮常用材料及技术要求
2、航空齿轮热处理方法
(1)15CrA渗碳、二次淬火、低温回火。
(2)12CrNi3A渗碳、二次淬火、低温回火。
(3)12Cr2Ni4A渗碳、二次淬火、低温回火。
(4)14CrMnSiNi2MoA渗碳、淬火、低温回火。
(5)18Cr2Ni4WA渗碳、淬火、低温回火。
(6)38CrMoAlA正火、调质,渗氮。
设计者应该注意:齿轮图样上应该有最终表面硬度、心部硬度、有效硬化层深、至心部硬度降、表面碳(氮)浓度,金相组织中有渗层碳化物级别、马氏体和残留奥氏体级别,硬化层和半硬化层占整个硬化层的比例。
还应该有预备热处理的表面硬度、金相组织、晶粒度等。
- 1、下载文档前请自行甄别文档内容的完整性,平台不提供额外的编辑、内容补充、找答案等附加服务。
- 2、"仅部分预览"的文档,不可在线预览部分如存在完整性等问题,可反馈申请退款(可完整预览的文档不适用该条件!)。
- 3、如文档侵犯您的权益,请联系客服反馈,我们会尽快为您处理(人工客服工作时间:9:00-18:30)。
齿轮热处理1 齿轮热处理概述众所周知,齿轮是机械设备中关键的零部件,它广泛的用于汽车、飞机、坦克、轮船等工业领域。
它具有传动准确、结构紧凑使用寿命长等优点。
齿轮传动是近代机器中最常见的一种机械振动是传递机械动力和运动的一种重要形式、是机械产品重要基础零件。
它与带、链、摩擦、液压等机械相比具有功率范围大,传动效率高、圆周速度高、传动比准确、使用寿命长、尺寸结构小等一系列优点。
因此它已成为许多机械产品不可缺少的传动部件,也是机器中所占比例最大的传动形式。
由于齿轮在工业发展中的突出地位,使齿轮被公认为工业化的一种象征. 得益于近年来汽车、风电、核电行业的拉动,汽车齿轮加工机床、大规格齿轮加工机床的需求增长十分耀眼。
据了解,随着齿轮加工机床需求的增加,近年来涉及齿轮加工机床制造的企业也日益增多。
无论是传统的汽车、船舶、航空航天、军工等行业,还是近年来新兴的高铁、铁路、电子等行业,都对机床工具行业的快速发展提出了紧迫需求,对齿轮加工机床制造商提出了新的要求。
据权威部门预测2012 年将达到200 万吨。
但我国齿轮的质量与其他发达国家的同类产品相较还是具有一定的差距,主要表现在齿轮的平均使用寿命、单位产品能耗、生产率这几方面上。
本设计是在课堂学习热处理知识后的探索和尝试,其内容讨论如何设计齿轮的热处理工艺,重点是制定合理的热处理规程,并按此设计齿轮的热处理方法。
齿轮是机械工业中应用最广泛的重要零件之一。
其主要作用是传递动力,改变运动速度和方向。
是主要零件。
其服役条件如下:(1)齿轮工作时,通过齿面的接触来传递动力。
两齿轮在相对运动过程中,既有滚动,又有滑动。
因此,齿轮表面受到很大的接触疲劳应力和摩擦力的作用。
在齿根部位受到很大的弯曲应力作用;⑵高速齿轮在运转过程中的过载产生振动,承受一定的冲击力或过载;⑶在一些特殊环境下,受介质环境的影响而承受其它特殊的力的作用。
因此,齿轮的表面有高的硬度和耐磨性,高接触疲劳强度,有较高的齿根抗弯强度,高的心部抗冲击能力。
齿轮常用材料有20Cr ,20CrMnTi, 18Cr2Ni4WA。
①20Cr有较高的强度及淬透性,但韧性较差。
渗碳时有晶粒长大倾向,降温直接淬火对冲击韧性影响较大,因而渗碳后进行二次淬火提高零件心部韧性;可切削性良好,但退火后较差;20Cr为珠光体,焊接性较好,焊后一般不需热处理。
②20CrMnTi20CrMnTi是性能良好的渗碳钢,淬透性较高,经渗碳淬火后具有高的强度和韧性,特别是具有较高的低温冲击韧性,切削加工性良好,加工变形小,抗疲劳性能好。
③18Cr2Ni4WA18Cr2Ni4WA属于高强度中合金渗碳钢。
18Cr2Ni4WA钢常用于合金渗碳钢,强度,韧性高,淬透性良好,也可在不渗碳而调质的情况下使用,一般用做截面较大,载荷较高且韧性良好的重要零件。
对于汽车来说,由于其使用条件复杂,采用调质钢不能保证要求,选用渗碳钢较为合适。
20CrMnTi钢采用渗碳+淬火+低温回火,齿轮表面可以获得55~63HRC的高硬度,因淬透性较高,齿心部具有较高的强度和韧性。
因而选用20CrMnTi钢。
2预氧化的作用与目的2.1预氧化的作用预氧化使工件表面获得一层致密结构的氧化薄膜(3Fe+2o2→Fe3O4),其再随后的渗碳初期被渗碳气氛还原,生成洁净的初生态的铁(Fe3O4+2[C] →3Fe+2CO2),呈现出很高的化学活性,产生大量能够吸附渗剂的活性位置。
同时,工件表面轻度氧化,可适当提高工件表面粗糙度,形成微孔,人为增加表面缺陷,还可提供位错露头、台阶和各种表面缺陷,形成具有较低“势垒”的活性中心,使渗剂的被吸附概率和吸附量大大增加,从而加快活性碳原子渗入过程和表面碳浓度梯度的形成,有效地提高零件的吸碳活性,适应新型渗碳工艺要求,获得合格的渗碳性能。
2.2渗碳前预处理目的①零件进炉渗碳前加以预热,同时还能烧掉未清洗掉的油脂,不容易形成炭黑;②使氧气与铁发生反应,生成Fe3O4膜,提高渗碳零件表面活性,加快钢件表面吸附碳原子速度,可以提高渗碳速度和均匀性;③Fe3O4是一层致密氧化膜,可以防止进一步的氧化和脱碳。
④消除应力,减少变形(500时效果不明显,550-600去应力较好,超过500易被氧化,造成氧化脱碳。
预氧化本身不是为了去应力。
间接如果为了去应力,应该选用较高⑤Fe3O4是一层致密氧化膜,可以防止进一步的氧化和脱碳。
⑥消除应力,减少变形(500时效果不明显,550-600去应力较好,超过500易被氧化,造成氧化脱碳。
预氧化本身不是为了去应力。
间接如果为了去应力,应该选用较高温度、加保护气体氮气好些)3渗碳的工艺介绍及原理3.1渗碳的工艺介绍渗碳:是对金属表面处理的一种,采用渗碳的多为低碳钢或低合金钢,具体方法是将工件置入具有活性渗碳介质中,加热到900--950摄氏度的单相奥氏体区,保温足够时间后,使渗碳介质中分解出的活性碳原子渗入钢件表层,从而获得表层高碳,心部仍保持原有成分。
相似的还有低温渗氮处理。
这是金属材料常见的一种热处理工艺,它可以使渗过碳的工件表面获得很高的硬度,提高其耐磨程度。
图 1渗碳工艺介绍也是使低碳钢的工件具有高碳钢的表面层,再经过淬火和低温回火,使工件的表面层具有高硬度和耐磨性,而工件的中心部分仍然保持着低碳钢的韧性和塑性。
渗碳工件的材料一般为低碳钢或低碳合金钢(含碳量小于0.25%)。
渗碳后﹐钢件表面的化学成分可接近高碳钢。
工件渗碳后还要经过淬火﹐以得到高的表面硬度﹑高的耐磨性和疲劳强度﹐并保持心部有低碳钢淬火后的强韧性﹐使工件能承受冲击载荷。
渗碳工艺广泛用于飞机﹑汽车和拖拉机等的机械零件﹐如齿轮﹑轴﹑凸轮轴等。
渗碳工艺在中国可以上溯到2000年以前。
最早是用固体渗碳介质渗碳。
液体和渗碳是在20世纪出现并得到广泛应用的。
美国在20年代开始采用转筒炉进行气体渗碳。
30年代﹐连续式气体渗碳炉开始在工业上应用。
60年代高温(960~1100℃)气体渗碳得到发展。
3.2渗碳的原理1. 渗碳与其他化学热处理一样﹐也包含3个基本过程。
2.1 分解:渗碳介质的分解产生活性碳原子。
2.2 吸附:活性炭原子被钢件表面吸收后即溶到表层奥氏体中﹐使奥氏体中含碳量增加。
2.3 扩散:表面含碳量增加便与心部含碳量出现浓度差﹐表面的碳遂向内部扩散。
碳在钢中的扩散速度主要取决于温度﹐同时与工件中被渗元素内外浓度差和钢中合金元素含量有关。
渗碳零件的材料一般选用低碳钢或低碳合金钢(含碳量小於0.25%)。
渗碳后必须进行淬火才能充分发挥渗碳的有利作用。
工件渗碳淬火后的表层显微组织主要为高硬度的马氏体加上残余奥氏体和少量碳化物﹐心部组织为韧性好的低碳马氏体或含有非马氏体的组织﹐但应避免出现铁素体。
一般渗碳层深度范围为0.8~1.2毫米﹐深度渗碳时可达2毫米或更深。
表面硬度可达HRC58~63﹐心部硬度为HRC30~42。
渗碳淬火后﹐工件表面产生压缩内应力﹐对提高工件的疲劳强度有利。
因此渗碳被广泛用以提高零件强度﹑冲击韧性和耐磨性﹐借以延长零件的使用寿命。
3.3碳浓度的高低及防止方法1.碳浓度过高和防止方法产生原因及危害:如果渗碳时急剧加热,温度又过高或固体渗碳时用全新渗碳剂,或用强烈的催渗剂过多都会引起渗碳浓度过高的现象。
随着碳浓度过高,工件表面出现块状粗大的碳化物或网状碳化物。
由于这种硬脆组织产生,使渗碳层的韧性急剧下降。
并且淬火时形成高碳马氏体,在磨削时容易出现磨削裂纹。
防止的方法:①不能急剧加热,需采用适当的加热温度,不使钢的晶粒长大为好。
如果渗碳时晶粒粗大,则应在渗碳后正火或两次淬火处理来细化晶粒。
②严格控制炉温均匀性,不能波动过大,在反射炉中固体渗碳时需特别注意。
渗碳零件的材料一般选用低碳钢或低碳合金钢(含碳量小於0.25%)。
渗碳后必须进行淬火才能充分发挥渗碳的有利作用。
工件渗碳淬火后的表层显微组织主要为高硬度的马氏体加上残余奥氏体和少量碳化物﹐心部组织为韧性好的低碳马氏体或含有非马氏体的组织﹐但应避免出现铁素体。
一般渗碳层深度范围为0.8~1.2毫米﹐深度渗碳时可达2毫米或更深。
表面硬度可达HRC58~63﹐心部硬度为HRC30~42。
渗碳淬火后﹐工件表面产生压缩内应力﹐对提高工件的疲劳强度有利。
因此渗碳被广泛用以提高零件强度﹑冲击韧性和耐磨性﹐借以延长零件的使用寿命。
2.碳浓度过低和防止方法产生的原因及危害:温度波动很大或催渗剂过少都会引起表面的碳浓度不足。
最理想的碳浓度为0.9—1.0%之间,低于0.8%C,零件容易磨损。
由于在实际生产中几乎不会出现碳浓度过低现象,即使出现后期也很难处理,冷冻处理可以提高硬度。
3.渗碳的工艺发展渗碳工艺是一个十分古老的工艺,在中国,最早可上溯到2000年以前。
起先是用固体渗碳介质渗碳。
在20世纪出现液体和气体渗碳并得到广泛应用。
后来又出现了真空渗碳和离子渗碳。
到现在,渗碳工艺仍然具有非常重要的实用价值,原因就在于它的合理的设计思想,即让钢材表层接受各类负荷(磨损、疲劳、机械负载及化学腐蚀)最多的地方,通过渗入碳等元素达到高的表面硬度﹑高的耐磨性和疲劳强度耐蚀性﹐而不必通过昂贵的合金化或其它复杂工艺手段对整个材料进行处理。
4.气体渗碳的目的气体渗碳是为了增加钢件表层的含碳量和一定的碳浓度梯度,将钢件在渗碳介质中加热并保温使碳原子渗入钢件表层的化学热处理工艺称为渗碳,渗碳钢一般采用普通碳钢、优质碳素结构钢和低碳合金结构钢,也可采用Q235钢。
开炉前的准备:(1)渗碳工件表面不应有锈蚀、污垢、裂纹及伤痕等缺陷。
(2)工件表面不需渗碳部分可采用表面镀铜或涂防渗碳涂料防止渗碳,也可在渗碳后,对不需要渗碳的部分切削去渗碳层。
镀铜层的厚度一般应大于0.03mm;防渗碳涂料的厚度一般应大于0.3mm,要求涂层致密。
(3)采用滴注式渗碳时,渗碳剂一般是RX(形成载气)RX;煤油或丙酮、醋酸乙酯(形成富化气),有条件时也可以采用其他方式的可控气氛渗碳。
5.开炉前的注意事项①开炉前检查设备②根据停炉时间和炉罐情况,按工艺文件规定,进行炉罐渗碳。
炉罐渗碳时间,对于新炉罐一般为6-12h,对于旧炉罐一般为2-4h左右。
③装炉:a.将材质相同、渗碳层技术要求相同、渗碳后热处理方式相同的工件,放在同一炉生产。
试样放在料筐的有代表性的位置。
每炉装载量和装料高度应小于设备规定的最大装载量和装料高度。
b.为保证炉内渗碳气氛的循环畅通,使渗碳层均匀,工件间应留有纵横大于5mm 的间隙。
c.料筐装入炉内时,要垂直摆放,各层料筐应齐整,不得有间隙,同时悬吊放入中间试样棒。
d.工件入炉后,将炉盖盖紧,不允许有漏气现象,滴入渗碳剂后,应保持炉内压力为196-490Pa。
4变速器齿轮的热处理工艺分析4.1变速器齿轮的淬火淬火是把合金加热到固溶体溶解曲线上,保温一段时间,然后以大于临界冷却速度急速冷却,从而得到过饱和固溶体的热处理方法。