(抽样检验)抽样标准最全版
(抽样检验)第七章整群抽样最全版
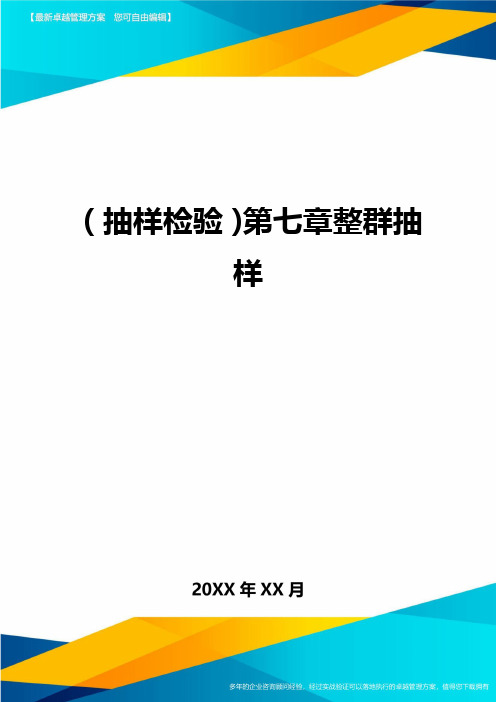
(抽样检验)第七章整群抽样第七章整群抽样第壹节整群抽样概述壹、整群抽样的概念整群抽样是先将总体各单元划分成若干群(组),然后以群为单位,从中随机抽取壹部分群,对中选群内的所有单元进行全面调查。
确切地说,这种抽样组织形式应称为单级整群抽样。
如果总体中的单元能够分成多级,则能够对前几级单元采用多阶抽样,而在最后壹阶中对该阶抽样单元所包含的全部个体(最基本单元)进行调查,这种抽样称作多级整群抽样。
本章只讨论单级整群抽样。
设总体被划分为N群,第i群含有Mi个次级单元,全部总体次级抽样单元数记为M0,即M0=∑M i。
当诸Mi都相等时,称为等群;否则,称为不等群。
采用整群抽样的俩个理由:-抽选群能大大降低数据收集的费用,当总体的分布比较广且调查采用面访时更是如此;-从总体中直接抽选个体在实际中且不总是可行的(没有关于个体的抽样框);有时,抽选单元组成群体组更简便易行(如整个住户)。
整群抽样包括俩步:首先,总体被分为群;然后,在总体中抽取群的样本且访问群中的所有单元。
如果总体单元是自然分成组或群的,创建壹个这种关于群的抽样框且对它们进行抽样比创建总体中所有单元的名录框更为容易。
或者,无法得到关于总体中所有单元的名录框,但却有这些单元分布地域的地图,因而能够创建地域框。
群的抽取能够采用简单随机抽样、系统抽样或PPS抽样等各种不同的方法。
二、群的划分问题整群抽样策略的统计效率取决于群内单元的相似程度有多大,每个群中有多少单元,及抽中群的数量。
同分层抽样壹样,整群抽样的前提是先要对总体进行分群。
关于群的划分,有俩个问题:壹是如何定义群,即当群且非是壹个自然形成的单位时,确定每个群的组成;二是如何确定群的规模即群的大小。
分层抽样是在各层都进行随机抽样,“层是缩小了的总体”,抽样单元仍然是总体基本单元。
这决定了分层的原则是:尽量缩小层内差异,而扩大层间差异。
而整群抽样只是在各群之间抽取壹部分群进行调查,且在抽中的群内作全面调查。
(抽样检验)AQL抽样介绍最全版

(抽样检验)AQL抽样介绍AQL抽样方法介绍AQL的定义AQL原来叫“合格质量水平(AcceptableQualityLevel)”,在新版国家标准《GB/T2828.1-2003计数抽样检验程序第1部分:按接收质量限(AQL)检索的逐批检验抽样计划》中,AQL的全称被改为了“接收质量限(AcceptanceQualityLimit)”,其定义为“当壹个连续系列批被提交验收抽样时,可允许的最差过程平均质量水平”。
检验水平在AQL中,有三种壹般检验水平(Ⅰ、Ⅱ、Ⅲ)和四种特殊检验水平(S-1、S-2、S-3、S-4)。
在三种壹般检验水平中,LEVELⅡ是常规水平,也是最经常采用的水平。
从LEVELⅠ到LEVELⅢ抽样的数量逐渐增加。
LEVELⅠ的抽样数是LEVELⅡ的40%,适用于品质较为稳定或产品出现不壹致可能性极小的状况。
LEVELⅢ的抽样数是LEVELⅡ的160%,加大检验的样本数量能够降低接受不合格产品的可能性。
四种特殊检验水平的特点是抽样数量少,因为在某些情况下,例如检验的成本高、检验所花费的时间长、货物的品质比较稳定(单壹产品的重复加工),通过少量的抽样检验就能够反应总体的品质水平。
从S-1到S-4抽样检验数逐步增加。
在服装辅料的检验中有时会采用特殊检验水平,例如拉链、纽扣等的检验。
抽样方案AQL有壹次、二次、多次(五次)3种抽样方案。
确定抽样方案能够从下面几个方面来考虑:1)简便易行:壹次优于二次,二次优于五次。
2)平均样本量:五次少于二次,二次少于壹次。
3)管理难度:五次难于二次,二次难于壹次。
4)取样的难易程度:取样麻烦时,壹次优于二次,二次优于五次。
5)试验时间的长短:根据单个试验时间的长短和是否能够多个样品同时进行试验来确定总的试验时间。
严格程度AQL中制定了三种严格程度:正常(NORMAL)、加严(TIGHTENED)、放宽(REDUCED)。
正常检验是最常用的检验水平,刚开始检验新的供应商生产的货物时,应采用正常检验。
统计抽样标准大全

統計抽樣標準大全之宇文皓月创作AQL的意义及其确定方法※ 产品检验的概念和分类单位产品:为了实施检验的需要而划分的基本单元。
如一辆卡车、1M棉布、1KG水泥、一双鞋等。
检验批:需要进行检验的一批单位产品。
简称批。
构成检验批的单位产品不该有实质的不同,只能有随机的动摇。
因此,一个检验批应当由在基底细同的生产条件下并在大约相同的时期内,所生产的同类型、同等级的单位产品所组成。
批量:需要检验的一批产品所包含的单位产品数。
致命缺陷:对使用和维护产品或对与此有关的人员可能造成危害或不服安状况的缺陷;或损坏产品重要的、最终的基本功能的缺陷。
重缺陷:分歧于致命缺陷,但能引起失效或显著降低产品预期性能的缺陷。
轻缺陷:不会显著降低产品的预期性能的缺陷,或偏离尺度但只轻微影响产品有效使用或操纵的缺陷。
产品检验可分为全数检验、抽样检验、购入检验、中间检验、成品检验、出厂检验、库存检验、监督检验、计数检验、计量检验、破坏性检验、非破坏性检验等。
抽样检验经经常使用于下列情况:a) 检验是破坏性的;b) 检验时,被检对象是连续体;c) 产品数量多;d) 检验项目多;e) 希望检验费用小;f) 作为生产过程工序控制的检验。
随机抽样方法:简单随机抽样:随机数表法、掷骰法。
周期系统抽样:采取一定间隔进行抽样的方法。
分层抽样:从一个可以分为分歧子批(或称层)的检验批中,按规定的比例从分歧层中抽取样本※ 抽样检验尺度及其体系1、计数和计量抽样检验尺度计数抽样检验尺度是以计数抽样检验的结果作为判定质量特性指标的,已经制订了国家尺度的有:a) GB2828-1987《逐批检查计数抽样程序及抽样表(适用于连续批的检查)》b) GB2829-1987《周期检查计数抽样程序及抽样表(适用于生产过程稳定性的检查)》c) GB8051-1987《计数序贯抽样检查程序及表》d) GB8052-1987《单水平和多水平计数连续抽样检查程序及表》计量抽样检验尺度是以计数抽样检验的结果作为判定质量特性指标的,已经制订了国家尺度的有:2AG8$INa) GB6378-1986《分歧格品率的计量抽样检查程序及表》b) GB8053-1987《分歧格品率的计量尺度型一次抽样检查程序及表》c) GB/T8054-1995《平均值的计量尺度型一次抽样检查程序及表》2、调整型与非调整型抽样检验尺度调整型抽样检验尺度,如GB2828-1987,GB6378-1986,可以根据连续批的质量变更来调整抽样检验方案的宽严程度,以达到包管批质量的情况下,引导生产方重视产品质量或减少抽样费用。
原材料抽样检验标准

#3一、织物疵点评分标准:织物疵点按“四分制”(FOUR POINT SYSIEM)评分1、评分方法疵点在3寸或以下评一分疵点超过3英寸而到6英寸评二分疵点超过6英寸到9英寸评三分疵点超过9英寸评四分2、连续性疵点,每1码计四分:3、较大的疵点(有破洞等)不计大小,每1码计四分;4、横档、中边色、不对色、幅不足、幅不同、有皱、整理不良等,连续发生时,每1码计四分。
二、以平方码为单位的计算方法1、每匹布:(常用)总评分数×36×100 评分=码数×有效幅度(寸)100平方码2、每单货:(整批布)每码总分数×36×100 评分=总码数×有效幅度100平方码三、验收标准(以100平方码为基准)适用欧洲、美国、日本等国家。
每匹布1组15分/100平方码2组20分/100平方码3组25分/100平方码4组40分/100平方码5组60分/100平方码现通用标准是选用2组、3组、4-5组不用四、全面疵点的评分标准☆连续性疵点1、连续有规律性疵点,1码计四分2、连续性3码以上,作不合格品对待。
☆整幅疵点3、合格品内不允许有以下疵点存在:A.长度超过6英寸全幅疵点。
B.较细小的全幅疵点,100码内超过5处。
C.以100码为单位,每10码中严重疵点平均2处以上。
D.布头、布尾3码内有严重疵点或整幅疵点的。
E.在平放裁床时,有边绉、预缩皱、波浪皱、折皱、皱条等疵布。
☆幅宽4、每匹布最少测三次。
5、达不到加工要求幅宽,则计不合格,6、幅宽计算:整幅度:两布边之间距有效幅度:去除布边、针洞、无印花部分的幅宽。
7、对色:分色最多接常受3个LOT色,每LOT色最小码数为500码以上,每LOT色之间色差按AATCC灰色卡4-5级。
8、每匹布中边、头尾色差不能低于4-5级。
9、工厂检验时,应取6英寸匹头,编号后留给客人。
10、客人QC来验货时,若色不板(4-5级以下)则该单货不合格,要重新检查、翻修。
(抽样检验)第三章抽样检验最全版

(抽样检验)第三章抽样检验第三章抽样检验大纲要求和内容提要壹、基本概念1、掌握抽样检验、计数检验、计量检验、单位产品、(检验)批、不合格、不合格品、批质量、过程平均、接收质量限及极限质量的概念1.1抽样检验(p130)——按照规定的抽样方案,随机从壹批或壹个过程中抽取少量个体(作为样本)进行的检查,根据样本检验结果判定壹批产品或壹个过程是否能够被接收。
1.2计数检验(pp.130-131)——包括计件和计点抽样检验。
计件抽样检验——根据被检样本中的不合格产品数,推断整批产品的接收和否。
计点抽样检验——根据被检样本中的产品包含的不合格数,推断整批产品的接收和否。
1.3计量检验(p131)——通过被检样本中的产品质量特性的具体数值且和标准进行比较,进而推断整批产品的接收和否。
1.4单位产品(p131)——为实施抽样检验需要而划分的基本产品单位。
……在抽样标准中定义为可单独描述和考察的事物。
……1.5(检验)批(p131)——提交检验的壹批产品,亦为检验对象而汇集的壹批产品。
——它应由同型号、同等级和同种类(尺寸、特性、成分等),且生产条件和生产时间基本相同的单位产品组成。
——又分为孤立批和连续批:孤立批——指脱离已生产或汇集的批而不属于当前检验批系列的批;连批批——指待检批可利用最近已检批所提供质量信息的连续提交检验批。
1.6批量(p131)——检验批中单位产品的数量,常用N表示。
1.7不合格(p132)——单位产品的任壹质量特性不满足规范要求。
常据不合格的严重程度必要时将其由重到轻分类为A、B、C类不合格。
1.8不合格品(p132)——具有壹个或壹个之上不合格的单位产品。
对应于不合格分类而为A、B、C类不合格品。
1.9批质量(p132)——单个提交检验批产品的质量。
由于质量特性值——计数值、计量值的属性不同而对之表示方法有别。
a.计数值有:i)批不合格品率(计件)——批的不合格品数D除以批量N:P=D/N,ii)批不合格品百分数(计件)100piii)批每百单位产品不合格数(计点):批的不合格数D除以批量N:u=D/N b.计量值有:i)批中所有单位产品的某个特性的平均值;ii)批中所有单位产品的某个特性的标准差或变异系数等。
抽样检验标准完整版

抽样检验标准HUA system office room 【HUA16H-TTMS2A-HUAS8Q8-HUAH1688】抽样检验标准1. 目的:为使进料检验、过程检验、成品检验时有正确之抽样方法及判定依据。
2. 范围:进料检验、过程检验、成品检验均适用本规范。
3. 权责:由进料、过程、成品检验员负责实施之。
4. 定义:4. 1 单位产品: 为实施抽样检查的需要而划分的基本单位,称为单位产品。
4. 2 检查批: 为实施抽样检查汇集起来的单位产品称之为检查批,简称为批。
4. 3 批量: 批中所包含的单位产品数,称为批量。
4. 4 样本单位: 从批中抽取用检查的单位产品,称为样本单位。
4. 5 样本: 样本单位的全体,称为样本。
4. 6 样本大小: 样本中所包含的样本单位数,称为样本大小。
4. 7 抽样检验:依照批量大小,抽出不同数量的样本,将该样本按其规格进行检验,并将检验的结果与预先决定的品质标准比较,以决定个别的样品是否合格。
4. 8 不良率: 不良品的表示方法。
任何已知数量的制品不良率,为制品中所含的不良品数除以单位产品的总数再乘以100%即得:不良率=? 不良品个数 *100%检验单位产品总数4. 9 检验方法: 用检验、量测、试验或其它方式将单位产品和其规定的要求加以比较的方法。
4. 10 抽样计划: 样本大小和判定数组结合在一起,称为抽样计划。
4. 11 抽样程序: 使用抽样计划判断批合格与否的过程,称为抽样程序。
4. 12类别:根据产品质量性能和使用过程的重要程度,由高到低依次分为A、B、C 三类。
A类:成品及构成产品的最主要原料。
其质量直接影响最终产品的质量性能,严重的可能直接导致产品报废。
B类:半成品及重要原材料。
其质量直接影响产品的质量性能,导致产品重要性能指标的下降。
C类:一般原材料,可以根据情况进行检测,备案。
不会对产品的主要性能产生影响,不直接影响产品的应用性能。
说明:原材料分级规定详见附件《原材料分类》5作业内容:5.1 A类原材料需100%检测,B类抽检,C类凭合格证检验,抽样比率如下:5.2 采购回的物品必须检测其产品合格证,检测其产品规格或技术参数是否符合本公司采购的要求,强制性产品必须检查是否印有3C标志及合格证。
MIL-STD-105E抽样标准(可编辑修改word版)

次品数﹥基准:拒收次品数≤基数:允收MIL —STD —105E 抽样标准1、AQL 是什么?AQL 是指工厂按抽样检验方式实施检验,通常叫品质允收标准。
AQL :ACCEPTABLE QUALITY LEVEL 品质允收标准最原是美国的军方标准:M I L — S T D— 1 0 5 D / E2、抽样检验方式:版次号序号 标 准军事从批次货中随机抽取一定数量的样本,经过外观检验、功能测试后,将结果与标准作比较,然后判定此批货是合格或不合格的方法就是抽样检验。
抽样检验的原理:3、抽样检验标准:● 决定抽取样本数量和判定标准的数据表就是抽样检验标准; ● MIL —STD —105D/E 分别是最常用的两种抽样标准,见 AQL 表:良品ACCEPTABLE QUALITY LEVELS 品质允收水准MIL—STD—105E3AQL 表内容解释如下:第一列是样品数据分类;第二列是一般检验水准:ⅠⅡⅢ;第三列是样本的代号,用A、B、C……表示;第四列是赋予代号的抽取样本数量;以后各列是不同级别的QAL 值;要注意表中的箭头和其所指的方向,以防判错。
4、AQL 使用步骤:1)确定要抽样的产品和抽样检验特性;2)确定检验级别,一般为“Ⅱ”级;3)确定AQL 值,如:主要不良取“0.65”,次要不良去“1.5”,或主要与次要均去“1.5”。
4)根据要检查产品的数量确定样本代码,即行与列的交汇处的字母;如:2000 个产品,查的代码为“K”;5)查表K 代码的行对应的抽样数量为125 个;6)检查125 个样本,并对不良品分类;如:共检出7 个不良品,其中主要不良品数2 个,次要不良品数5 个;7)对比AQL 表上基准进行判定;判定结果:因不良品数量小于Re 的值,所以,该批产品判定合格;8)如果出现对应到箭头的情况,则沿着箭头的方向读取箭头所值的第一个“Ac、Re”值,然后由此值回查对应的检查样本值,以新查到的样本值为准,同时,原查到的样本值作废。
(抽样检验)抽样与参数估计最全版

(抽样检验)抽样与参数估计最全版(抽样检验)抽样与参数估计抽样和参数估计推断统计:利⽤样本统计量对总体某些性质或数量特征进⾏推断。
从数据得到对现实世界的结论的过程就叫做统计推断(statisticalinference)。
这个调查例⼦是估计总体参数(某种意见的⽐例)的壹个过程。
估计(estimation)是统计推断的重要内容之壹。
统计推断的另壹个主要内容是本章第⼆节要介绍的假设检验(hypothesistesting)。
因此本节内容就是由样本数据对总体参数进⾏估计,即:学习⽬标:了解抽样和抽样分布的基本概念理解抽样分布和总体分布的关系了解点估计的概念和估计量的优良标准掌握总体均值、总体⽐例和总体⽅差的区间估计第⼀节抽样和抽样分布回顾相关概念:总体、个体和样本抽样推断:从所研究的总体全部元素(单位)中抽取壹部分元素(单位)进⾏调查,且根据样本数据所提供的信息来推断总体的数量特征。
总体(Population):调查研究的事物或现象的全体参数个体(Itemunit):组成总体的每个元素样本(Sample):从总体中所抽取的部分个体统计量样本容量(Samplesize):样本中所含个体的数量壹般将样本单位数不少于三⼗个的样本称为⼤样本,样本单位数不到三⼗个的样本称为⼩样本。
壹、抽样⽅法及抽样分布1、抽样⽅法(1)、概率抽样:根据已知的概率选取样本①、简单随机抽样:完全随机地抽选样本,使得每壹个样本都有相同的机会(概率)被抽中。
注意:在有限总体的简单随机抽样中,由抽样是否具有可重复性,⼜可分为重复抽样和不重复抽样。
⽽且,根据抽样中是否排序,所能抽到的样本个数往往不同。
②、分层抽样:总体分成不同的“层”(类),然后在每壹层内进⾏抽样③、整群抽样:将壹组被调查者(群)作为壹个抽样单位④、等距抽样:在样本框中每隔壹定距离抽选壹个被调查者(2)⾮概率抽样:不是完全按随机原则选取样本①、⾮随机抽样:由调查⼈员⾃由选取被调查者②、判断抽样:通过某些条件过滤来选择被调查者(3)、配额抽样:选择壹群特定数⽬、满⾜特定条件的被调查者2、抽样分布壹般地,样本统计量的所有可能取值及其取值概率所形成的概率分布,统计上称为抽样分布(samplingdistribution)。
通用抽样检验规范标准

通用抽样检验规范编制:审核:批准:日期:1.范围:适用于除冷加工外的产品检验抽样。
2.依据:GB/T 2828.1 《计数抽样检验程序第1部分:按接受质量限(AQL)检索的逐批检验抽样计划》3.定义3.1 单位产品:为实施抽样检查的需要而划分的基本单位,称为单位产品。
3.2 检查批:为实施抽样检查汇集起来的单位产品称之为检查批,简称批。
3.3 批量:批中包含的单位产品数,称为批量。
3.4 样本单位:从批中抽取用检查的单位产品,称为样本单位。
3.5 样本:样本单位的全体称为样本。
3.6样本大小:样本中所含的样本单位数称为样本大小。
3.7 抽样检验:依照批量大小,抽出不同数量的样本,将该样本按其规格进行检验,并将检验的结果与预先决定的品质标注比较,以决定个别样品是否合格。
3.8 不良率:不良品的表示方法。
任何已知数量的制品不良率,为制品中所含的不良品数除以单位产品的总数再乘以100%即得:不良品率=不良品数/检验单位产品总数×100%3.9 检验方法:用检验、测量、试验或其他方式将单位产品和其规定的要求加以比较的方法。
3.10 抽样计划:样本大小和判定数组和在一起,称为抽样计划。
3.11 抽样程序:使用抽样计划判定批合格与否的过程。
3.12 符号:N:批量n:样本大小Ac:合格判定数(允收数)Re:不合格判定数(拒收数)II:检验水准AQL:合格质量水准(允收品质水准)4.抽样标准4.1 本公司产品采用GB2828.1正常检验一次抽样计划,一般水平II级抽样方法抽样。
4.2 转移规则:A 从正常检验→加严检验。
当进行正常检验时,若在连续五批产品中有两批检验不合格,则后续来料转为加严检验。
B 从加严检验→正常检验当进行加严检验时,若连续五批来料合格,则后续来料转为正常检验。
C 从正常检验→放宽检验当进行正常检验时,若连续10批来料检验合格,后续来料转到放宽检验D从放宽检验→正常检验当放宽检验时,若有一批来料检验不合格,则后续来料转为正常检验。
检验抽样标准
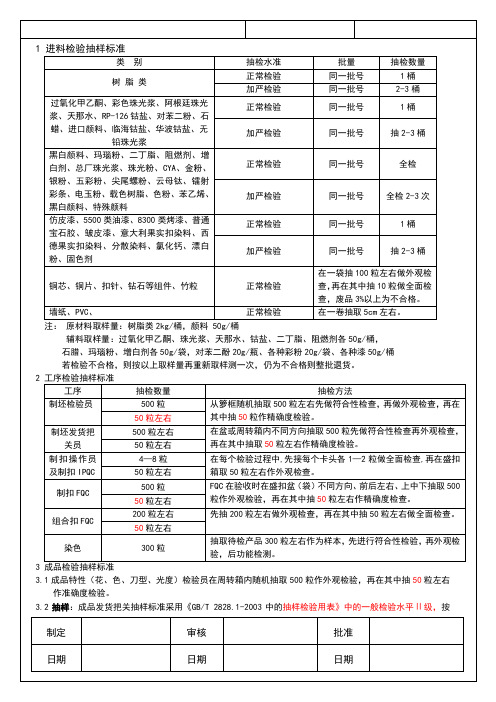
批量范围
AQL值
致命
缺陷
严重缺陷(一类)
严重缺陷(二类)
一般缺陷
A
1250以上
(1250以内全检)
00.01允许拒收0.065允许
拒收
0.4
允许
拒收
0粒
1粒
2粒(0.16%)
3粒
10粒(0.8%)
11粒
B
1250以上
(1250以内全检)
0
0.025
0粒
1粒
0.25
7粒(0.56%)
8粒
2.5
1进料检验抽样标准
类别
抽检水准
批量
抽检数量
树脂类
正常检验
同一批号
1桶
加严检验
同一批号
2-3桶
过氧化甲乙酮、彩色珠光浆、阿根廷珠光浆、天那水、RP-126钴盐、对苯二粉、石蜡、进口颜料、临海钴盐、华波钴盐、无铅珠光浆
正常检验
同一批号
1桶
加严检验
同一批号
抽2-3桶
黑白颜料、玛瑙粉、二丁脂、阻燃剂、增白剂、总厂珠光浆、珠光粉、CYA、金粉、银粉、五彩粉、尖尾螺粉、云母钛、镭射彩条、电玉粉、载色树脂、色粉、苯乙烯、黑白颜料、特殊颜料
4.3致命缺陷:三只眼、一只眼、无眼
4.4严重缺陷(一类):单边废、大崩扣、大气泡、大缺角、正面崩扣、明显不圆、脏扣、花糊、
缺字、字不完整。(参考实样)
4.5严重缺陷(二类):比一类要稍不严重一些,大崩扣、大气泡、大缺角、正面崩扣、明显不圆、脏扣、花糊、缺字、字不完整。(参考实样)
4.6一般缺陷:钻头划、芯子顶、扣不圆、单边厚、字体深浅不一、珠光花、珠光脏点、反面小崩扣、反面小气泡、薄扣、严重刀纹、严重烧扣、严重中一点、花走形。
(抽样检验)AATCC检验及抽样标准最全版

(抽样检验)AATCC检验及抽样标准AATCC检验及抽样标准1.抽样数量:总码数的平方根乘以八。
2.抽箱数:总箱数的平方根。
一.四分制检验1.1”-3”扣1分;3”-6”扣2分;6”-9”扣3分;9”之上扣4分2.疵点的评分原则:A.同壹码中所有经纬向的疵点扣分不超过4分。
B.破洞不问大小扣4分。
C.布边壹英寸内不扣分。
D.连续性疵点须开裁或降等外品。
E.任何大于针孔的洞均扣4分。
F.无论经向或纬向,无论何病疵,都以见的见为原则,且按疵点评分给予正确扣分。
G.除了特殊规定(比如涂层上胶布),通常只检验布的正面。
3.等级计算方法有俩种:A.以线长度为基准计算:100M扣分不超过50分为A级(为可接受范围)。
100M扣分超过50分为B级。
(为不可接受范围)。
B.以平方码为基准计算:每百平方码四十分(为可接受范围)总疵点评分*3600被查布匹实际长度*实际布匹门幅(英寸)拒收标准:A.壹匹布疵点评分超过四十分。
B,整匹大货的标准疵点超过20分。
C,疵点连续出当下三米或之上,不论疵点评分多少。
二.十分制检验1.经向疵点扣分法:1”以下扣1分;1”-5”扣3分;5”-10”扣5分;10”-36”之间扣10分。
2.纬向扣分法:1”以下扣1分;1”-5”扣3分;5”-半门幅之间扣5分;半门幅之上扣10分。
疵点的评分原则:A:同壹码中所有经纬向的疵点扣分10分。
B,破洞不问大小扣10分。
C,布边半英寸内不扣分。
D,连续性疵点须开裁或降等外品。
E,任何大于针孔的洞均扣10分。
F,无论经向或纬向,无论何病疵,都以见得见为原则,且按疵点评分给予正确扣分。
G,除了特殊规定(比如涂层上胶布),通常只需检验布的正面。
三.等级计算方法1.可接受范围=总分数小于总码数;2.百码扣分不得超过壹百分四.布匹检验标准布匹的检验方法常见的是“四分制评分法”。
在这个“四分制评分法”中,对于任何单壹疵点的最高评分为四分。
无论布匹存在多少疵点,对其进行的每直线码数(linearyard)疵点评分都不得超过4分。
抽样检验标准

抽样检验标准1.目的为包材,半成品和成品的抽样检验符合质量体系要求,保证抽样方案的合理性,以国家标准GB/T2828.1为引用依据,特制订本标准。
2.范围2.1仅适用于上海浩韵化妆品有限公司检验包材,半成品和成品检验取样作业。
2.2若客户的抽样标准与本标准有出入,则应在符合中华人民共和国法律法规的前提下,按照各户的要求进行抽样检测。
3.权责3.1采购部按此标准采购包装材料。
3.2质量部按此标准检验包材,半成品和成品。
4操作依据4.1本公司所有包材来料与完成品的取样检验按GB/T2828.1-2003正常检验一次抽样方案一般检验水平II级进行,尺寸与功能检验取样按一次抽样方案特殊检验水平S3级进行。
4.2本公司包材与完成品采用正常检验一次抽样方案与加严检验一次抽样方案,不采用放宽检验抽样方案:A)无特殊要求,一般开始采用正常检验一次抽样方案;B)当正常检验抽样连续5批中有2批不合格时,应及时转入加严检验一次抽样方案;C)当加严检验抽样连续5批合格后方可转入正常检验。
4.3批次定义4.3.1 来料检验批次定义:同一批来料,具有相同规格型号的商品为一个检验批次。
4.3.2 制程检验批次定义:制造:由同一生产者在相同生产条件下制造一定量的料体作为一个检验批次;灌装与包装:由同一生产者在相同生产条件下生产的一定数量的同种定量包装商品作为一个检验批次。
4.3.3 成品出货检验批次定义:同一个灌装包装商品作为一个检验批次。
4.4 抽样检验的判定水平(AQL):4.4.1严重缺陷(CR),AQL=0.654.4.2一般缺陷(MA),AQL=1.54.4.3轻微缺陷(MI),AQL=4.05. 操作步骤5.1 确定抽样的箱数:抽样箱数X= N+1 ,N 为总箱数,X 为小数点后第一位数四舍五入的整数值,例:109=10.4,则抽样箱数为10+1=11箱,111=10.5,则抽样箱数为11+1=12箱,箱子的选取要平均分散选取。
抽样检验标准简介
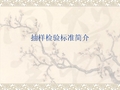
10.1开始时实行“正常”,除非负责部门另有规定。 10.2正常→加严:初次检验中连续5批或少于5批中有2批是不可接收的, 则转移到加严。 10.3加严→正常:加严时接连5批已接收,则恢复正常检验。 10.4正常→放宽: 10.4.1正在采用正常检验时,下列条件同时满足,则从正常转移到放宽 检验。 a:当前的转移得分至少30分; b:生产稳定; c:负责部门同意。 10.4.2转移得分:正常检验开始时,转移得分设定为0,而在检验每个后 续的批以后应更新转移得分: a:一次抽样方案(1)当接收数≥2时,如AQL加严一级后该批被接收, 则转物得分加2分;否则仍为0。(2)当接收数为0或1时,如果该批被 接收,则转物得分加2分;否则仍为0。 b:二次和多次抽样方案(1)当使用二次抽样方案时,如该批在检验第 一样本后被接收,则转移得分加3分;否则仍为0。(2)当使用多次抽 样方案时,如果该批在检验第一样本或第二样本后被接收,则转移得分 加3分,否则仍为0。
分别为正常、加严、放宽三种严格度的α表。
14、使用方风险表
列于GB/T2828.1-2003标准中表6及表7,其
中表6-A、B、C为适用于不合格品率为正常、 加严、放宽严格度的β表;表7为适用于每百 单位产品不合格数的正常、加严、放宽严格 度的β表。
15、分数接收数一次抽样方案(供选择)
GB/T13263—1991 跳批计数抽样程序及抽样表(计数、连续批、 跳批、与GB/T2828.1—2003一起使用)。 GB/T13264—1991 不合格品率的小批计数抽样检查程序及抽样 表(计数,N=10~250,连续批和孤立批,一次、二次)。 GB/T13393—1992 抽样检查导则。 GB/T13546—1992 挑选型计数抽样检查程序及抽样表(计数、 连续批、挑选型)。 GB/T13732—1992 粒度均匀散料抽样检验通则(计量,散料)。 GB/T14162—1993 产品质量监督计数抽样程序及抽样表(计数、 监督抽样、一次)。 GB/T14437—1997 产品质量计数一次监督抽样检验程序及抽样 表(计数、监督抽样、一次、N>250)。 GB/T14900—1994 产品质量平均值的计量一次监督抽样检验程 序及抽样表(计量、监督抽样、一次)。 GB/T15239—1994 孤立批计数抽样检验程序及抽样表(计数、 孤立批、A、B两种模式)。
抽样检验标准

GB2828-2003抽样标准part21 范围1.1 GB/T2828的本部分规定了一个计数抽样检验系统。
本部分采取术语接收质量限(AQL)来检索。
本部分的目的是通过批不接收使供方在经济上和心里上产生的压力,促使其将过程平均至少保持在和规定的接收质量限一样好,而同时给使用方偶尔接收劣质批的风险提供一个上限。
GB/T2828的部分指定的抽样计划可用于(但不限于)下述检验:――最终产品;――零部件和原材料;――操作;――在制品;――库存品;――维修操作;――数据和记录;――管理程序。
1.2 这些抽样计划主要用于连续系列批。
连续系列批的系列的长度足以允许使用转移规则(见9.3)。
这些规则为;a) 一旦发现质量变劣,通过转移到加严检验或暂停抽样检验给使用方提供一种保护;b) 一旦达到一致好的质量,经负责部门决定,通过转移到放宽检验提供一种奖励,以减少检验费用对孤立批的检验也可使用本部分的抽样方案,但在此情况下,为找到一个能给予所期望保护的抽样方案,特别建议使用者查阅抽样方案的抽检特性曲线(见12.1)。
使用者也可参阅在GB/T15239-1994中给出的按极限质量(LQ)检索的抽样方案。
详细介绍:GB2828-2003抽样标准part21 范围1.1 GB/T2828的本部分规定了一个计数抽样检验系统。
本部分采取术语接收质量限(AQL)来检索。
本部分的目的是通过批不接收使供方在经济上和心里上产生的压力,促使其将过程平均至少保持在和规定的接收质量限一样好,而同时给使用方偶尔接收劣质批的风险提供一个上限。
GB/T2828的部分指定的抽样计划可用于(但不限于)下述检验:――最终产品;――零部件和原材料;――操作;――在制品;――库存品;――维修操作;――数据和记录;――管理程序。
1.2 这些抽样计划主要用于连续系列批。
连续系列批的系列的长度足以允许使用转移规则(见9.3)。
这些规则为;a) 一旦发现质量变劣,通过转移到加严检验或暂停抽样检验给使用方提供一种保护;b) 一旦达到一致好的质量,经负责部门决定,通过转移到放宽检验提供一种奖励,以减少检验费用对孤立批的检验也可使用本部分的抽样方案,但在此情况下,为找到一个能给予所期望保护的抽样方案,特别建议使用者查阅抽样方案的抽检特性曲线(见12.1)。
抽样检验标准

记d为样本中的不合格(品)数。实际抽样检验对批 质量的判断也即对批接收性的判断规则是:若d小于等于 接收数Ac,则接收该批产品;若d大于Ac,则拒收该批产 品。Ac称为合格判定数,计数型一次抽样检验判断过程如 图5-1所示。
5.3 计数型抽样方案及对批可接收性的判断
图5-1 一次抽样方案的程序图
5.3 计数型抽样方案及对批可接收性的判断
5.3 计数型抽样方案及对批可接收性的判断
抽样检验的对象是一批产品,一批产品的可接收性 指通过抽样检验判断批的接收与否,可以通过样本批的质 量指标来衡量。
在实际抽样检验过程中,将上述批质量判断规则转 换为一个具体的抽样方案。最简单的一次抽样方案由样本 量n和用来判定批接收与否的接收数Ac组成,记为(N,n, Ac)。
5.3 计数型抽样方案及对批可接收性的判断
交验批总体N 抽样
抽取一个样本n1 检验
统计样本中不合格(品)数d1
d1≤AC1
AC1<d1≤AC2 抽取第二个样本n2 统计样本中不合格品数d2
d1>AC2
d1+d2≤AC2
d1+d2>AC2
批接收
批不接收
图5-2 二次抽样方案的程序图
5.4 计数调整型抽样检验
5.4.2 GB/T2828.1的使用程序
图5-3 GB/T2828.1的使用步骤
5.4.2 GB/T2828.1的使用程序
1. 质量标准和不合格分类的确定
首先需要明确待检产品的质量特性指标,该指标应 该符合的标准或规范,以及不合格分级。
(抽样检验)抽样检验方案最全版

(抽样检验)抽样检验方案抽样检验方案第四节抽样检验方案(大纲要求熟悉)壹、抽样检验的几个基本概念(基础知识)1.抽样检验方案是根据检验项目特性所确定的抽样数量、接受标准和方法。
如在简单的计数值抽样检验方案中,主要是确定样本容量n和合格判定数,即允许不合格品件数c,记为方案(n,c)。
2.检验.检验是对检验项目中的性能进行量测、检查、试验等,且将结果和标准规定要求进行比较,以确定每项性能是否合格所进行的活动。
3.检验批4.批不合格品率是指检验批中不合格品数占整个批量的比重。
5.过程平均批不合格品率是指对k批产品首次检验得到的k个批不合格品率的平均数。
6.接受概率(又称批合格概率)接受概率是根据规定的抽样检验方案将检验批判为合格而接受的概率。
壹个既定方案的接受概率是产品质量水平,即批不合格品率P的函数,用L(p)表示,检验批的不合格品率p越小,接受概率L(p)就越大。
二、抽样检验方案类型(壹)抽样检验方案的分类(二)常用的抽样检验方案(大纲要求熟悉)1.标准型抽样检验方案(1)计数值标准型壹次抽样检验方案计数值标准型壹次抽样检验方案是规定在壹定样本容量n时的最高允许的批合格判定数c,记作(n,c),且在壹次抽检后给出判断检验批是否合格的结论。
c也可用Ac表示。
c值壹般为可接受的不合格品数,也能够是不合格品率,或者是可接受的每百单位缺陷数。
若实际抽检时,检出不合格品数为d,则当:d≤c时,判定为合格批,接受该检验批;d>c定为不合格批,拒绝该检验批。
(2)计数值标准型二次抽样检验方案(之上俩种标准型抽样检验程序见图7-16、7-17)(3)多次抽样检验方案(★适当位置加图7-16和7-17)2.分选型抽样检验方案3.调整型抽样检验方案[例题]当采用计数值标准型壹次抽样检验方案实际抽检时,检验出的不合格品数d,当(),判定为不合格批,拒绝该检验批。
A.d<cB.d>cC.d=cD.d=r答案:B抽样检验方案参数的确定三、抽样检验方案参数的确定(大纲要求了解)实际抽样检验方案中也都存在俩类判断错误。
- 1、下载文档前请自行甄别文档内容的完整性,平台不提供额外的编辑、内容补充、找答案等附加服务。
- 2、"仅部分预览"的文档,不可在线预览部分如存在完整性等问题,可反馈申请退款(可完整预览的文档不适用该条件!)。
- 3、如文档侵犯您的权益,请联系客服反馈,我们会尽快为您处理(人工客服工作时间:9:00-18:30)。
(抽样检验)抽样标准
抽样检验标准
1.0目的
对入厂外协件进行有效的质量控制,防止未经检验合格的产品投入使用和加工,确保入厂外协件能最大限度地满足X公司产品的质量要求,规范品管来料检验作业,保证来料符合X公司的质量要求。
2.0范围
适用于X公司采购零部件的检验和质量监督,不包括合格供应商的新品或新供应商的样品。
3.0权责
3.1质量部长:外协厂家的质量控制和反馈
3.2外检班长:检验作业的安排和督导
3.3检验员:外协件的检验
4.0作业内容
4.1检验实物和《检验通知单》是否壹致
4.2检索AQL值和样本量
4.3按外协件抽样方案随机抽取样品
4.4根据图纸要求检验规格尺寸
4.5根据检验结果如实填写《检验通知单》
4.6如来料检验合格,检验员将《检验通知单》交仓管办理入库手续;若不合格做不合格标识交由采购退货
5.0抽样方案
采用计数调整型抽样方案,检验水平为壹般检验水平Ⅱ,抽样类型为二次抽样,初始抽样方案为正常检验二次。
5.1AQL取值检索表
根据零部件的不同供应商和类型,在表5-1壹般附件AQL值、5-2壹般加工零件AQL值、5-3毛坯件及半成品件AQL值中检索相应的AQL值
5.2选取样本量
根据《检验通知单》上提供的产品数量,查找相应的样本量字码。
当批产品总数在1-小批中时,采用全检。
根据相应的样本量字码在表5-5正常检验二次抽样方案、5-6加严检验二次抽样方案、5-7放宽检验二次抽样方案中查找相应的样本数和Ac、Re值。
表5-5正常检验二次抽样方案
*——使用相应的壹次抽样方案,见表5-8正常壹次检验抽样方案
表5-6加严检验二次抽样方案
*——使用相应的壹次抽样方案,见表5-9加严壹次检验抽样方案
*——使用相应的壹次抽样方案,见表5-10放宽壹次检验抽样方案
表5-8正常壹次检验抽样方案
表5-9加严壹次检验抽样方案
5.3正常检验二次、加严检验二次和放宽检验二次的抽样方案和相互转换
转换条件:
正常检验转为加严检验:连续五批中有俩批不合格;
加严检验转为正常检验:连续五批全部合格;
正常检验转为放宽检验:连续五批全部合格;
放宽检验转为正常检验:有任意壹批不合格;
返修件全部使用加严检验但不参和条件转换;;
暂停检验:自加严检验累计俩次批不合格。
5.4二次检验程序
d1:壹次抽检不合格数; d2:二次抽检不合格数;
Ac1/Re1
:壹次抽检接受数和拒收数; Ac2/Re2
:二次抽检接受数和拒收数。